金属熔炼与铸锭—第二章
铜合金重力铸造教程(第二部分)
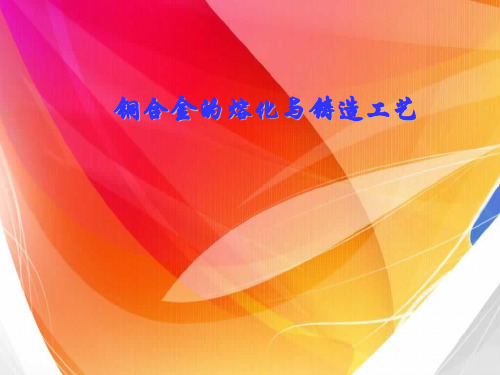
③沸腾除气法:沸腾除气是在工频有芯感 应电炉熔炼高锌黄铜时常用的一种特殊除气方 法。如熔化黄铜时锌的蒸发就可以将溶解在合 金液体中的气体去除。由于熔化温度较高超过 锌的沸点(907℃),因此在熔炼后期会出现 喷火现象,即锌的沸腾,这样有利于气体的排 除。
• (2)除渣精炼 ①静置澄清法:静置澄清过程一般是让熔 体在精炼温度下,保持一段时间使氧化及熔渣 上浮或下沉而除去。 ②浮选除渣法:浮选除渣是利用熔剂或惰 性气体与氧化物产生的某种物理化学作用,即 吸附或部分溶解作用,造成浮渣而将氧化物除 去。 ③熔剂除渣法:在熔体中加入熔剂,通过 对氧化物的吸附、溶解、化合造渣,将渣除去, 熔剂的造渣能力越强,除渣精炼的效果越好。
• 5.4.铜合金的配比
根据铁模尺寸大小要求合金配料总量为1200g
(1)黄铜(H68) 纯铜:1200g×68%=816g 锌: 1200g×32%=384g (需考虑烧损量 1.5~2%)
(2)铝青铜(QAl10) 纯铜: 1200g×90%=1080g 铝: 1200g×10%=120g
重铸基础知识
1,调整模具,清理砂筒 2,调整气压 3,漏气处贴胶 4,对准射砂口
1,增加固化时间 2,提高固化温度 3,严格按照参数混砂 1,减少固化时间 2,降低固化温度 1,仔细刮砂芯 2,射砂道小心掰掉或用锯条锯掉
夹生
焦酥
1,固化时间过长 2,固化温度过高 1,刮砂芯不仔细 2,连接射砂道敲掉后型砂表面有凹坑
4.影响铸模铸锭质量的主要因素
• (1)浇铸温度:浇铸温度过高或过低都是不 利的,因为采用较高的浇铸温度,势必就要使 炉内熔体的温度作相应的提高,这将引起铜合 金在熔化和保温过程中大量的吸气,同时也会 增加烧损,在浇铸时会使氧化加剧。此外,过 高的浇铸温度也会对铸模的寿命产生不利影响, 尤其是平模浇铸时模底板更容易遭到破坏。当 浇铸温度偏低时,熔体流动性变差,不利于气 体和夹渣上浮,也易使铸锭产生冷隔缺陷。因 此,必需根据合金的性质,结合具体的工艺熔炼时金属的损耗和氧化
有色金属熔炼与铸锭 ppt课件

1.熔体温度
2.金属及合金元素
3.炉膛压力
4.其他因素
夹渣和除渣精练
1.非金属夹渣物的种类和来源
氧化物、氮化物、硫化物、硅酸盐等非金属化合物在金属 中都以独立相存在—统称为非金属夹杂物。(简称夹杂或夹 渣)
▲按化学成分可分为:氧化物、复杂氧化物、氮化物、硫 化 物、氯化物、氟化物、硅酸盐、碳化物、氢化物、磷 化物等;
(1)脱氧剂与氧的亲和力应明显地大于基体金属与氧的亲和力
(2)脱氧剂在金属中的残留量应不损害金属性能
(3)脱氧剂要有适当的熔点和比重
(4)脱氧产物应不溶于金属熔体中,易于凝聚、上浮而被除去
(5)脱氧剂不稀贵,且无毒
2.脱氧方法及特点:
沉淀脱氧:5[Cu2O]+2[P]=P2O3+10[Cu] 扩散脱氧:脱氧剂加在金属熔体表面或炉渣中,脱氧反应 仅在炉渣-金属熔体界面上进行(溶于金属中的氧会不断地 按分配定律向界面扩散而脱氧
影响氧化烧损的因素及降低氧化烧损的方法
影响金属氧化烧损的因素:
一、金属及氧化物的性质
纯金属氧化烧损取决于金属与氧的亲和力和金属表面氧 化膜的性质 Mg、Li与氧亲和力大,而且a<1,氧化烧损大 Al、Be 与氧亲和力大,但a>1,氧化烧损小 Au、Ag、Pt与氧亲和力小,a>1,故很难氧化
例外情况:a>1,但线膨胀系数与基体金属不相适应则 易产生分层,断裂而脱落—显然也属于易氧化烧损金属
1.氧由气相通过边界层向氧-氧化膜界面扩散(即外扩散)
VD=DA/δ *(C0O2-CO2)
D—氧在边界层中的扩散系数,A、δ—边界层面积和 厚度
C0O2、CO2—边界层外和相界面上氧的浓度
图1-2
铝合金的熔炼与铸造
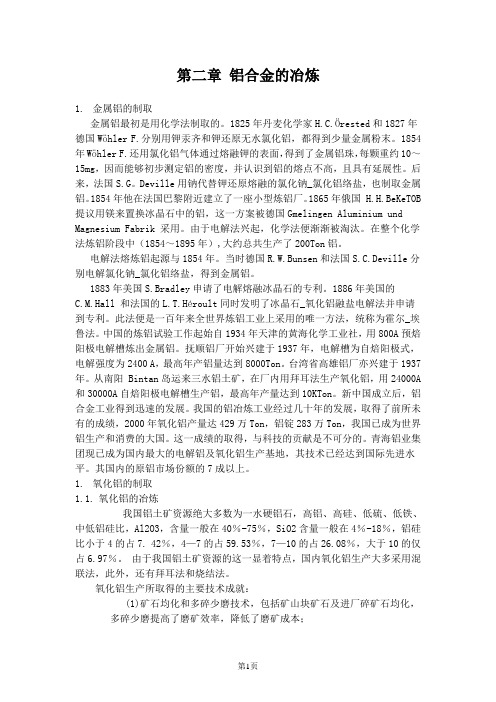
第二章铝合金的冶炼1.金属铝的制取金属铝最初是用化学法制取的。
1825年丹麦化学家H.C.Örested和1827年德国Wöhler F.分别用钾汞齐和钾还原无水氯化铝,都得到少量金属粉末。
1854年Wöhler F.还用氯化铝气体通过熔融钾的表面,得到了金属铝珠,每颗重约10~15mg,因而能够初步测定铝的密度,并认识到铝的熔点不高,且具有延展性。
后来,法国S.G。
Deville用钠代替钾还原熔融的氯化钠_氯化铝络盐,也制取金属铝。
1854年他在法国巴黎附近建立了一座小型炼铝厂。
1865年俄国 H.H.BeKeTOB 提议用镁来置换冰晶石中的铝,这一方案被德国Gmelingen Aluminium und Magnesium Fabrik 采用。
由于电解法兴起,化学法便渐渐被淘汰。
在整个化学法炼铝阶段中(1854~1895年),大约总共生产了200Ton铝。
电解法熔炼铝起源与1854年。
当时德国R.W.Bunsen和法国S.C.Deville分别电解氯化钠_氯化铝络盐,得到金属铝。
1883年美国S.Bradley申请了电解熔融冰晶石的专利。
1886年美国的C.M.Hall 和法国的L.T.Héroult同时发明了冰晶石_氧化铝融盐电解法并申请到专利。
此法便是一百年来全世界炼铝工业上采用的唯一方法,统称为霍尔_埃鲁法。
中国的炼铝试验工作起始自1934年天津的黄海化学工业社,用800A预焙阳极电解槽炼出金属铝。
抚顺铝厂开始兴建于1937年,电解槽为自焙阳极式,电解强度为2400 A,最高年产铝量达到8000Ton。
台湾省高雄铝厂亦兴建于1937年。
从南阳 Bintan岛运来三水铝土矿,在厂内用拜耳法生产氧化铝,用24000A 和30000A自焙阳极电解槽生产铝,最高年产量达到10KTon。
新中国成立后,铝合金工业得到迅速的发展。
我国的铝冶炼工业经过几十年的发展,取得了前所未有的成绩,2000年氧化铝产量达429万Ton,铝锭283万Ton,我国已成为世界铝生产和消费的大国。
第二章 纯金属的结晶
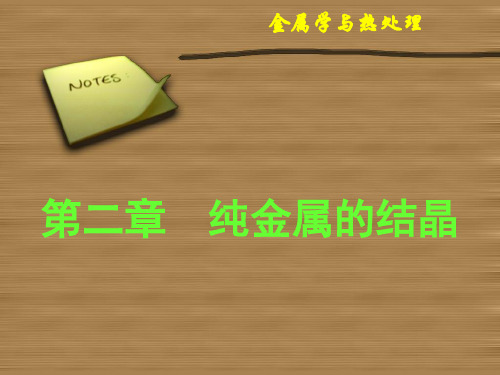
•=180o, GK’= GK. 均匀形核与非均匀形核所需要的能量起伏相同. •0< < 180o, GK’< GK. 越小, 非均匀形核越容易, 需要的过冷度也越
小.
第四节晶核的形成
(二)形核率
1. 过冷度的影响 2. 固体杂质结构的影响 3. 固体杂质形貌的影响 4. 过热度的影响 5. 其他因素的影响
G V Gv S
结晶的驱动力
结晶的阻力
V:晶胚的体积; S: 表面积; GV:液固两相单位体积自由能差; σ: 单位面积的表面能.
第四节晶核的形成
假设晶胚为球体,半径为r,则:
G
4 3
r 3
Gv
4r 2
令 dG 0 dr
得rk
2
G vBiblioteka rk2TmH f T
T:过冷度; Tm 理论结晶温度; ΔHf 熔化潜热.
第五节晶核长大
液-固界面的微观结构
假设界面上可能的原子位置数为N,其中NA个位置为固相原子所占 据,那么界面上被固相原子占据的位置的比例为x= NA/N。 如果x=50%,即界面上有50%的位置为固相原子所占据,这样的截 面为粗糙界面;如果界面上有近于0%或100%的位置为固相原子所占 据,这样的截面为光滑界面。 界面的平衡结构应该是界面能最低的结构,在光滑界面上任意添加 原子时,其界面自由能的变化:
理论结晶温度:纯金属液体在无 限缓慢冷却条件下结晶的温度。 过冷现象:实际的结晶过程冷速都 很快,液态金属在理论结晶温度以 下开始结晶的现象。 过冷度T :理论结晶温度与实际 结晶温度的差值。
T= T0 –T1
第一节金属结晶的现象
影响过冷度的因素
过冷度随金属的本性、纯度以及冷却速度的差异 而不同。金属不同,过冷度的大小不同;金属纯度 越高,过冷度越大;冷却速度越大,过冷度越大, 实际结晶温度越低。
电子教案与课件:《铸造合金原理及熔炼》 第二章
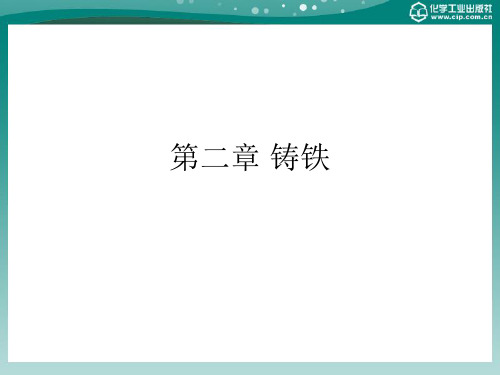
2.1.1 铸造碳钢的化学成分及性能
在铸造碳钢中,常存元素有碳、硅、锰、磷和硫。碳作为主要强化元素,硅和锰 也在一定程度上对钢起强化的作用。磷和硫降低钢的性能,是有害元素。铸造碳 钢的规格化学成分中本来是不合有合金元素的,但由于在炼钢中,可能由回炉废 钢料带入少量的合金元素成分,为了对铸造碳钢性能的控制,要求将合金元素的 含量于以控制。对应于上述 5 个牌号的化学成分要求见表 2-2。应指出,对碳、 硅和锰三元素只给出上限值而未给出下限值是为了给生产上留有较大的化学成 分调整范围。在保证达到规定的力学性能前摄下,各生产厂家可根据自己的经验 来规定各元素含量上、下限的数值。
4) 碳钢中的气体
①氢 ②氮 ③氧
①氢
在电弧炉炼钢过程中,空气中的水蒸气在电弧作用下离解,氢以原子态溶入钢液 中。氢在钢中的溶解度与温度的关系如图 2-5 所示。在钢处于液态时,能溶解大 量的氢。随着钢液温度降低,溶解度逐渐减小,而在钢凝固过程中,氢的溶解度 大幅度降低。因此,凝固时氢因过饱和而析出,形成气孔。这种气孔体积小,数 量多,常聚集在铸件表皮下形成“针孔” 在快速凝固条件下,钢液中的原子氢来不及转变为分子氢。即以极微细的质点在 铁的晶格内部析出,在晶格内部形成很高的应力状态,从而显著降低钢的塑性和 韧性,严重时会造成“氢脆”。 为了预防氢气的危害,炼钢前要作好原材料准备工作,在炼钢过程中要尽量避免 钢水吸气和氧化,并保证一定量的脱碳沸腾时间。若条件许可,还可采用真空处 理等去气措施。
③ 网状组织
形态见图 2-2c。铁素体在原奥氏体的晶界处析出。由于奥氏体晶界上晶格缺位多, 且组织疏松,故易于铁素体新相的形核和铁原子的聚集,从而为网状组织的形成 创造了条件。由于网状组织的形态特征,故称之为仿晶界形貌析出相(GBA—— Grain Boundary Allotriomorphs)。 图 2-3 表示了铸造碳钢的含碳量及冷却速度对铸态组织中铁素体形态的影响。对 于钢的力学性能最有利的是粒状组织,具有粒状铁素体和珠光体相互交错分布的 组织使钢具有良好的强度和韧性,而魏氏体和网状组织则使钢具有较低的力学性 能,特别是韧性。通过适当的热处理(退火或正火),魏氏体或网状组织即会转变 为粒状组织,从而使钢的性能得到提高。
有色金属熔炼与铸锭资料课件
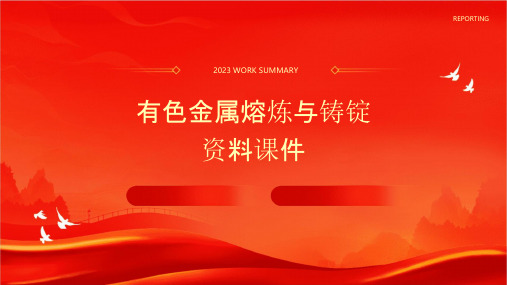
有色金属熔炼与铸锭 资料课件
REPORTING
CATALOGUE
• 有色金属熔炼基础
PART 01
有色金属熔炼基础
熔炼的基本概念
熔炼定义
熔炼是有色金属生产中重要的一步,它涉及到将原料加热至熔融状态,通过化学反应和 物理作用,将杂质去除并使金属或合金成分均匀混合的过程。
铸锭的结晶过程
01
02
03
结晶过程
金属熔体在冷却过程中, 原子或分子的排列从无序 状态逐渐变为有序状态, 形成晶体的过程。
结晶温度
金属熔体结晶速率
结晶过程中晶体生长的快 慢,受到冷却速率、过冷 度等因素的影响。
铸锭的宏观组织形成与控制
宏观组织
铸锭中晶体的分布、大小、 形状等宏观特征。
反应的可能性与方向,而动力学则研究反应速率与过程控制因素。
熔炼过程中的热力学与动力学
热力学在熔炼中的应用
热力学的主要任务是研究熔炼过程中能量的转化与物质平衡的问题。通过热力学分析,可 以确定熔炼过程的自发性和方向,以及反应的标准摩尔焓变、熵变等参数。
动力学对熔炼过程的影响
动力学研究反应速率和反应机制的问题。在熔炼过程中,动力学因素决定了反应的快慢和 进行的程度。通过控制熔炼温度、搅拌速率等参数,可以调节反应速率,优化熔炼过程。
微观偏析
金属熔体在结晶过程中,由于溶质再分配导致晶 体内部化学成分的不均匀性。
PART 04
有色金属熔炼与铸锭中的 问题及解决策略
杂质与夹杂物的控制
控制方法
选用纯净的原材料,加强原材料 的保管和运输,采用合理的熔炼 和浇注工艺,以及进行有效的精 炼处理。
实例
采用电渣重熔、真空熔炼等方法 去除杂质与夹杂物,提高金属纯 净度。
有色金属熔炼与铸锭第二章 铝合金的熔炼

2.1.3 铝合金中主要合金元素、微量元素及杂质
熔体成分控制、熔体质量控制 熔炼设备、净化设备
2.2 熔体的成分控制
2.3.1 备料 炉料一般包括: 一、新金属:电解Cu、电解Al等。品位↑,价格↑,成本↑。 二、废料:①本厂废料—几何废料、工艺废料;②厂外废料:化学废料。 三、中间合金 使用目的:在于加入某些熔点高、难溶解、易氧化、易挥发的元素,以便准确控
相:合金中具有同一化学成份、同一聚集状态并以界面互相分开的各个均匀的组成部分。 合金中所有的相可分为固溶体和金属化合物两大类。
组元:组成合金的元素(或稳定化合物)称为组元。 结晶:物质由液体状态转变为晶体状态物过程叫结晶。 过冷:液体冷却到平衡结晶温度以下某一温度才开始有效结晶的现象叫过冷。而该温度
第2章 铝合金的熔炼
2.1 概述 2.1.1 熔炼的目的
对化学成分的要求
2.1.2 相关的基本概念
合金:是两种或两种以上的金属或金属元素与非金属元素熔合在一起所得到的具有金 属特性的物质。组成合金的各元素称组元。它们交互作用形成多种相,即合金中具有 同一化学成份、同一结构和原子聚集状态的均匀部分。不同相之间有明显的界线分开。 相的结构可分为固溶体和化合物两大类。
表面张力:作用在液体表面,并力图使表面自动收缩的力。与本身性质(对液态金 属主要是成份和温度)、接触相的性质有关。是液态金属的重要物理特性之一。影 响润湿、毛细、内吸附等现象的发生。
润湿:液体在固体或液体表面铺展的性质。如接触面有扩大的趋势称润湿。如液 体成球形,在固体或液体表面不能铺开,接触面有收缩趋势称不润湿。润湿角小 于90度表示能润湿。
晶体:物质内部结构中的质点(原子、离子或分子)按一定规则次序排列的固体叫晶体。 特点:规则的外形,固定的熔点,各向异性。实际晶体由于结晶及其它加条件的影响, 使得所得到的晶体在内部结构上产生很多缺陷,称真实晶体。
有色金属熔炼与铸造
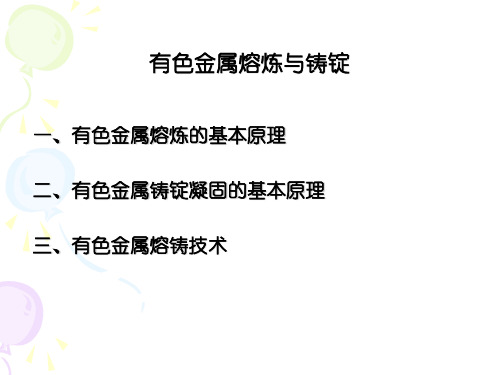
RT ln pO2 =A BT
A<0
A BT A
ln pO2
RT
B T
(2)
氧化热力学条件及判据
氧化热力学条件及判据
在标准状态下,金属的氧化趋势、氧化顺序
和可能的氧化烧损程度,一般可用氧化物的标准
生成自由焓变量ΔG,分解压pO2或氧化物的生成 热ΔH作判据。通常ΔG、 pO2或ΔH越小,元素氧 化趋势越大,可能的氧化程度越高。
Me MO MeO M
Me 为还原剂, MO为金属氧化物,作氧化剂。
例如: 4Al 3TiO2 3Ti 2Al2O3
氧化热力学条件及判据
金属Me可被炉气中的氧气直接氧化,也可被其他氧化剂(以 MO表示)间接氧化。
Me+MO=MeO+M
研究表明,上式反应的热力学条件为ΔGMeO<ΔGMO,即Me对 氧的亲和力大于M对氧的亲和力。所以位于ΔG-T图下方的金属可
决定因素:金属与氧的亲和力大小,也与合金成分、 温度和压力有关
氧化热力学条件及判据
在标准状态下,金属与一摩尔氧作用生成金属氧化物的 自由焓变量称为氧化物的标准生成自由焓变量:
2x y
Me(s,l )
O2(g)
2 y
MexO y(s,l )
G RTlnPO2
ΔG是衡量标准状态下金属氧化趋势的判据,某一金属 氧化物的ΔG值越小(越负),则该元素与氧的亲和力越大,氧 化反应的趋势亦越大,氧化物就越稳定。
即:Cu2O能够被Al还原。
G 715900J / mol 0
ΔG还是衡量标准状态下氧化物稳定性的一种判据,某一金属 氧化物的ΔG值越小(越负),则该元素可还原ΔG值较大的氧化物。
有色金属熔炼与铸锭
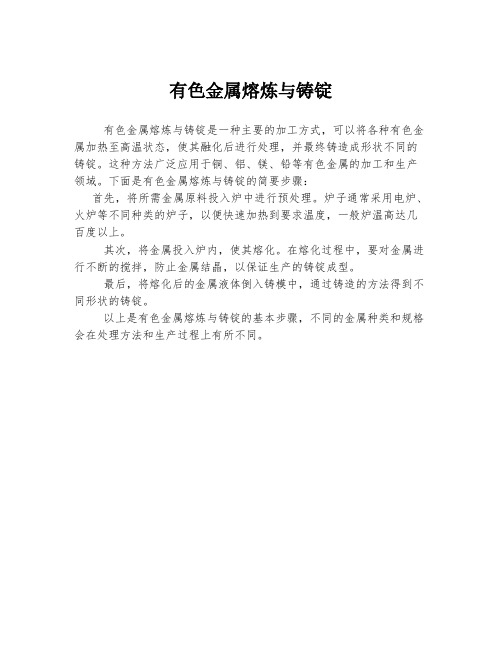
有色金属熔炼与铸锭
有色金属熔炼与铸锭是一种主要的加工方式,可以将各种有色金属加热至高温状态,使其融化后进行处理,并最终铸造成形状不同的铸锭。
这种方法广泛应用于铜、铝、镁、铅等有色金属的加工和生产领域。
下面是有色金属熔炼与铸锭的简要步骤:
首先,将所需金属原料投入炉中进行预处理。
炉子通常采用电炉、火炉等不同种类的炉子,以便快速加热到要求温度,一般炉温高达几百度以上。
其次,将金属投入炉内,使其熔化。
在熔化过程中,要对金属进行不断的搅拌,防止金属结晶,以保证生产的铸锭成型。
最后,将熔化后的金属液体倒入铸模中,通过铸造的方法得到不同形状的铸锭。
以上是有色金属熔炼与铸锭的基本步骤,不同的金属种类和规格会在处理方法和生产过程上有所不同。
熔炼与铸锭

(3) 熔剂法:利用熔剂被夹渣的吸附、溶解、化
合作用来除渣。
A
11
a、上熔剂法:适用夹渣比重小的情况,如Al青 铜、Al黄铜;
b、下熔剂法:适用夹渣比重大的情况,如Mg及 合金; c、全体熔炼法:适用夹渣比重差不较大的情况。
如Al及合金。 (4) 过滤法:通过过滤器,利用过滤作用原理。 主要有网状过滤法、填充床过滤法和刚性微孔过
体,还能与W、Ti、Zr、Ce、V、Li、K、Na形 成氢化物。
O2——能溶解于Cu、Ni、Co、Ag、V、T等, 以氧化物的形式存在,也能与Al、Ag、Si等形 成不溶性,稳定的氧化物。
N2——能与Al、Mg、Ti、Zr、W、Mo等在高温 下形成氮化物(700℃以下量少),在Cu、Ni、 Pb、Sn、Zn、Cr等中不溶或少溶解。
2、熔剂脱气法
3、真空脱气法
真空脱气法分为静态真空脱气法和动态真空 脱气法。静态真空脱气法是将熔体置于10~30托 的真空度下,保持一段时间。动态真空脱气是将 金属液经流槽导入抽至10托的真空炉内,使金属 液以分散的液滴喷落在熔池中。其特点是脱气速 度和程度高,并且铜、镍、铝及其合金也愈来愈 多的采和真空熔炼及真空处理脱气法。
证某些合金纯度的要求。 3、火焰炉应选用低硫燃料 4、所有与金属炉料接触A 的工具,尽可能采用不6
会带入杂质的材料制作,或用适当涂料保护好。
5、变料或转换合金时,应根据前后两种合金的 纯度和性能的要求,对熔炉进行必要的清洗处理。
6、注意辅助材料的选用。
7、加强炉料管理,杜绝混料现象。
三、金属的脱氧
铜用磷脱氧的反应如下: 5[Cu2O]+2[P]=P2O5(g)+10[Cu] 6[Cu2O]+2[P]=2CuPO3(L)+10[Cu]
有色金属熔炼与铸造02

王华 工学院材料系
第二章 熔体净化技术
熔体净化技术
本章要点: 介绍熔体净化的基本原理和对应的净化处理技术, 包括: (1) 熔体脱气和除渣精炼的几种基本原理; (2) 铝、镁、铜合金熔体净化处理技术; (3) 不同金属的熔体保护措施。
第一节 熔体净化原理
4
除渣精炼
氧化夹杂
非金属夹杂物的种类和来源
金属中的非金属化合物,如氧化物、氮化物、 等,统称为非金属夹杂物,一般简称为夹杂或 夹渣。
形成的夹渣若不在浇 根据夹渣的形态可分为:薄膜状、团状和颗粒 注前去除,将在铸锭 状。 中形成氧化夹杂。
夹渣的来源不同分为:外来夹渣和内生夹渣。
如,铝镁合金常见的有Al2O3、MgO、SiO2等 ,铜合金、镍合金中通常为Cu2O、NiO、ZnO 、SnO2、SiO2、Al2O3等,钢铁中有硫化物、 氢化物等。
除渣精炼
• 静置澄清除渣(密度差作用)
当金属熔体在高温静置时,非金属夹杂物与金属熔体比重不同 因而产生上浮或下沉。球形固体夹杂颗粒在液体中下沉或上浮的 速度服从Stokes定律: 2 g ( 2 1 ) 2 v r 9 T ↑ ,η↓,则:v↑,τ↓ 上升或下沉时间:
9 H 2 2r ( 2 1 ) g
方法一:分压差脱气
气体溶解度与金属液/气体接触处该气体分 压的平方根成正比。
S K1 P
K1 S0 exp[H / 2RT ]
K1:与金属及溶解气体的性质、温度和气体溶解度量单位选择有关的 常数,西维尔常数。 T:金属的热力学温度 S:溶解度 △H:气体在金属中的溶解热 p:气相中溶解气体的分压 S0:常数
除渣精炼
• 过滤除渣:
所谓机械过滤作用,是指当金属熔体通过过滤
《金属熔炼与铸锭》课程实验指导书
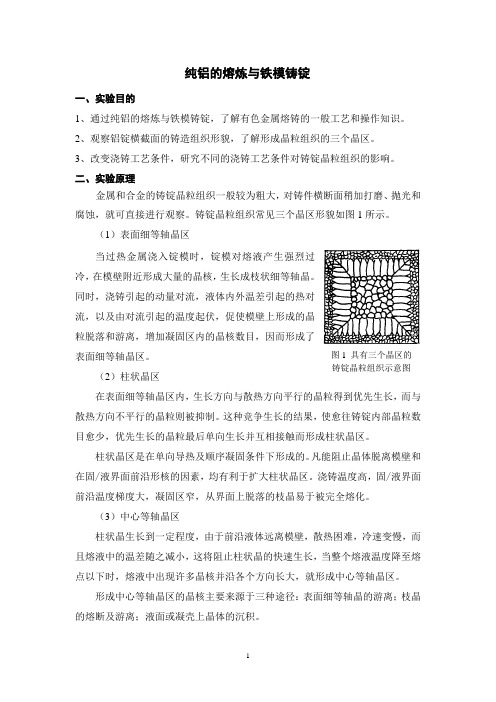
图1 具有三个晶区的 铸锭晶粒组织示意图 纯铝的熔炼与铁模铸锭一、实验目的1、通过纯铝的熔炼与铁模铸锭,了解有色金属熔铸的一般工艺和操作知识。
2、观察铝锭横截面的铸造组织形貌,了解形成晶粒组织的三个晶区。
3、改变浇铸工艺条件,研究不同的浇铸工艺条件对铸锭晶粒组织的影响。
二、实验原理金属和合金的铸锭晶粒组织一般较为粗大,对铸件横断面稍加打磨、抛光和腐蚀,就可直接进行观察。
铸锭晶粒组织常见三个晶区形貌如图1所示。
(1)表面细等轴晶区当过热金属浇入锭模时,锭模对熔液产生强烈过冷,在模壁附近形成大量的晶核,生长成枝状细等轴晶。
同时,浇铸引起的动量对流,液体内外温差引起的热对流,以及由对流引起的温度起伏,促使模壁上形成的晶粒脱落和游离,增加凝固区内的晶核数目,因而形成了表面细等轴晶区。
(2)柱状晶区 在表面细等轴晶区内,生长方向与散热方向平行的晶粒得到优先生长,而与散热方向不平行的晶粒则被抑制。
这种竞争生长的结果,使愈往铸锭内部晶粒数目愈少,优先生长的晶粒最后单向生长并互相接触而形成柱状晶区。
柱状晶区是在单向导热及顺序凝固条件下形成的。
凡能阻止晶体脱离模壁和在固/液界面前沿形核的因素,均有利于扩大柱状晶区。
浇铸温度高,固/液界面前沿温度梯度大,凝固区窄,从界面上脱落的枝晶易于被完全熔化。
(3)中心等轴晶区柱状晶生长到一定程度,由于前沿液体远离模壁,散热困难,冷速变慢,而且熔液中的温差随之减小,这将阻止柱状晶的快速生长,当整个熔液温度降至熔点以下时,熔液中出现许多晶核并沿各个方向长大,就形成中心等轴晶区。
形成中心等轴晶区的晶核主要来源于三种途径:表面细等轴晶的游离;枝晶的熔断及游离;液面或凝壳上晶体的沉积。
凡能阻止游离到铸锭中心的晶粒完全熔化的因素,均有利于促进中心等轴晶区的形成。
铸锭的结晶过程及其组织与金属的冷却条件、浇铸时熔体的温度、变质处理条件等因素有关。
改变金属的浇铸温度对结晶过程有影响作用。
当液态金属过热越多时,浇筑后沿铸锭截面的温差越大,越有利于按顺序凝固的方式结晶,形成柱状晶组织。
第二部分熔炼与铸锭

线收缩率:
L
L0 L1 L1
100%
其中 V0,L0表示铸件在高温T0时的体积和一维方向的长度;
V1,L1表示铸件在高温T1时的体积和一维方向的长度。
三 铸锭缺陷
缩孔:
定义:缩孔是指金属液在铸模中冷却和凝固时,在铸件
的厚大部位及最后凝固部位形成一些容积较大的孔洞。
产生原因:
先凝固区域堵 住液体流动的 通道,后凝固 区域收缩所缩 减的容积得不 到补充。
工艺过程:如右图所示。
特点和应用:
1、冷却速度快,组织致密, 机械性能好;
2、工艺简单,生产效率高; 3、适于横截面一定的钢材、
铝材和铸铁管等铸件的生产。
连续铸造工艺过程示意图
五、凝固理论的实际应用举例
一、铸锭(铸件)的宏观组织控制:三层典型组
织 1.激冷层(表面细晶区) 2.柱状晶区3.中心等轴晶区
例:三个成份相同,但铸造温度和 铸模材料不同的铸件得到三种横截 面: A.粗等轴晶 B.细等轴晶 C. 典型三层晶带组织,试解释为何产 生不同的组织。
A 高的浇注温度,导热性差的砂模
B 低的浇注温度,导热性差的砂模
C 适中的浇注温度,导热性好的砂模
铸锭的宏观组织控制:控制晶粒的大小
a.增加过冷度 过冷度增大,N/V0增加 实际结晶时,过冷度是由冷却速度来控制的
裂纹与变形:
在铸锭的固态收缩阶段会引起铸造应力。
铸造应力:
铸造应力
铸锭收缩受阻
机械应力
锭铸因V冷却、温度不同, 各部位收缩不一致产生
铸锭组织发生相变时,因温 度差异出现体积变化不一致
热应力 相变应力
四 连续铸造:
定义:是指将熔融金属连续不断地浇注到被成为结晶
- 1、下载文档前请自行甄别文档内容的完整性,平台不提供额外的编辑、内容补充、找答案等附加服务。
- 2、"仅部分预览"的文档,不可在线预览部分如存在完整性等问题,可反馈申请退款(可完整预览的文档不适用该条件!)。
- 3、如文档侵犯您的权益,请联系客服反馈,我们会尽快为您处理(人工客服工作时间:9:00-18:30)。
第二章
1
冶金工程学院
第2章 有色金属及合金材料
主要内容
2.1 熔铸的基本任务 2.2 熔铸的基本要求 2.3 熔铸工艺规程制定
2
冶金工程学院
2.1 熔铸的基本任务
3
冶金工程学院
2.2 熔铸的基本要求
4
冶金工程学院
2.2 熔铸的基本要求
5
冶金工程学院
2.2 熔铸的基本要求
2.3 熔铸工艺规程的制定
20
冶金工程学院
作业思考题
1.熔铸的基本任务是什么? 2.熔铸的六点要求是什么? 3.为什么在熔铸之前要制定熔铸工艺规程?
21
冶金工程学院
15
冶金工程学院
2.3 熔铸工艺规程的制定
水、电(油)、气、料
Байду номын сангаас
16
冶金工程学院
2.3 熔铸工艺规程的制定
17
冶金工程学院
18
冶金工程学院
• 铸造用(废钢熔解)里面的原材料覆盖剂在废钢熔炼过程 中覆盖在钢水表面,起到了保温、吸附夹杂物,防止钢水 氧化等作用。主要成分为C、CaO、SiO2、Al2O3等。对于 有特殊要求的,还要添加合金粉、膨胀材料等,以提高保 温、吸附夹杂的性能。 • 铸造熔炼精炼添加剂的作用及特性 熔炼精炼添加剂能加快 合金的熔化,降低熔化能耗,节省用电量,减 少电能耗损 净化 钢(铁)液,减少渣孔、气孔,提高铸件成品... • 打渣剂和清渣剂应该是一样的东西 铝合金在温度达到720度左右时加入精炼剂,用工具压到底 部缓慢移动直到不冒泡为止,主要是用来清除铝液中的氢 精炼后加入打渣剂,用工具充分搅拌后捞出渣子,主要是用 19 来清除铝液中的杂质 冶金工程学院 清渣结束后在表面撒上覆盖剂,防止空气中的氢进入铝液中
6
冶金工程学院
2.2 熔铸的基本要求
7
冶金工程学院
8
冶金工程学院
9
冶金工程学院
铸造后的工件稍受一定力后就出现裂纹或断裂,在断口出现氧化夹杂物,或者 没有融合到一起。
10
冶金工程学院
11
冶金工程学院
12
冶金工程学院
13
冶金工程学院
14
冶金工程学院
2.3 熔铸工艺规程的制定
熔铸质量最难控制的环节主要有两个:一是熔体中的 气体、微量杂质及夹杂的定量控制;二是大规格铸锭中的缩 松、裂纹、偏析及组织不均的控制。