SIR878DP-T1-GE3;中文规格书,Datasheet资料
SIC762CD-T1-GE3;中文规格书,Datasheet资料

Integrated DrMOS Power StageDESCRIPTIONThe SiC762CD is an integrated solution that contains PWM optimized n-channel MOSFETs (high side and low side) and a full featured MOSFET driver IC. The device complies with the Intel DrMOS standard for desktop and server V core power stages. The SiC762CD delivers up to 35 A continuous output current and operates from an input voltage range of 3 V to 27 V. The integrated MOSFETs are optimized for output voltages in the ranges of 0.8 V to 2.0 V with a nominal input voltage of 24 V. The device can also deliver very high power at 5 V output for ASIC applications.The SiC762CD incorporates an advanced MOSFET gate driver IC. This IC accepts a single PWM input from the V R controller and converts it into the high side and low side MOSFET gate drive signals. The driver IC is designed to implement the skip mode (SMOD) function for light load efficiency improvement. Adaptive dead time control also works to improve efficiency at all load points. The SiC762CD has a thermal warning (THDN) that alerts the system of excessive junction temperature. The driver IC includes an enable pin, UVLO and shoot through protection.The SiC762CD is optimized for high frequency buck applications. Operating frequencies in excess of 1 MHz can easily be achieved.The SiC762CD is packaged in Vishay Siliconix high performance PowerP AK MLP6 x 6 package. Compact co-packaging of components helps to reduce stray inductance, and hence increases efficiency. •FEATURES•Integrated Gen III MOSFETs and DrMOScompliant gate driver IC•Enables V core switching at 1 MHz•Easily achieve > 90 % efficiency in multi-phase, low output voltage solutions•Low ringing on the VSWH pin reduces EMI•Pin compatible with DrMOS 6 x 6 version 3.0•Tri-state PWM input function prevents negative output voltage swing• 5 V logic levels on PWM•MOSFET threshold voltage optimized for 5 V driver bias supply•Automatic skip mode operation (SMOD) for light load efficiency•Under-voltage lockout•Built-in bootstrap schottky diode•Adaptive deadtime and shoot through protection •Thermal shutdown warning flag•Low profile, thermally enhanced PowerPAK® MLP 6 x 640 pin package•Halogen-free according to IEC 61249-2-21 definition •Compliant to RoHS directive 2002/95/ECAPPLICATIONS•CPU and GPU core voltage regulation•Server, computer, workstation, game console, graphics boards, PCSIC762CD APPLICATION DIAGRAMMa.T A = 25 °C and all voltages referenced to P GND = C GND unless otherwise noted.Stresses beyond those listed under "Absolute Maximum Ratings" may cause permanent damage to the device. These are stress ratings only,and functional operation of the device at these or any other conditions beyond those indicated in the operational sections of the specifications is not implied. Exposure to absolute maximum rating/conditions for extended periods may affect device reliability.Note:a.Recommended operating conditions are specified over the entire temperature range, and all voltages referenced to P GND = C GND unless otherwise noted.ORDERING INFORMATIONPart Number Package SiC762CD-T1-GE3PowerPAK MLP66-40SiC762DBReference boardRECOMMENDED OPERATING CONDITIONSParameter Symbol Min.Typ.Max.UnitInput Voltage V IN 3.01224VControl Input Voltage V CIN 4.5 5.5Drive Input Voltage V DRV 4.55.5Switch NodeV SW_DC1224THERMAL RESISTANCE RATINGSParameterSymbol Typ.Max.Unit Maximum Power Dissipation at T PCB = 25 °C P D_25C 25W Maximum Power Dissipation at T PCB = 100 °C P D_100C 10Thermal Resistance from Junction to T op R th_J_TOP 15°C/WThermal Resistance from Junction to PCBR th_J_PCB5Notes:a.Typical limits are established by characterization and are not production tested.b.Guaranteed by design.ELECTRICAL SPECIFICATIONSParameter Symbol Test Conditions Unless SpecifiedV DSBL# = V SMOD = 5 V ,V IN = 12 V , V VDRV = V VCIN = 5 V ,T A = 25 °C Min.Typ.a Max.UnitPower SuppliesV CIN Control Input Current I VCIN V DSBL# = 0 V , no switching21µAV DSBL# = 5 V , no switching 350V DSBL# = 5 V , f s = 300 kHz, D = 0.1500Drive Input Current (Dynamic)I VDRV f s = 300 kHz, D = 0.11418mAf s = 1000 kHz, D = 0.14054Bootstrap SupplyBootstrap Switch Forward Voltage V BS Diode V VCIN = 5 V, forward bias current 2 mA0.600.75VControl Inputs (PWM, DSBL#, SMOD)PWM Rising Threshold V th_pwm_r 3.5 3.9 4.2VPWM Falling Threshold V th_pwm_f 0.8 1.0 1.2PWM T ristate Rising Threshold V th_tri_r 0.9 1.3 1.8PWM T ristate Falling ThresholdV th_tri_f 3.43.74.0PWM T ristate Rising Threshold Hysteresis V hys_tri_r 280mV PWM T ristate Falling Threshold Hysteresis V hys_tri_f 180T ristate Hold-Off Time b t TSHO 150ns PWM Input CurrentI PWM V PWM = 5 V 250µA V PWM = 0 V - 250SMOD, DSBL# Logic Input Voltage V LOGIC_LH Rising (low to high) 2.0V V LOGIC_LH Falling (high to low)0.8Pull Down Impedance R THDN 5 k Ω resistor pull-up to V CIN40ΩTHDN Output Low V THDNL0.04V ProtectionThermal Warning Flag Set 150°CThermal Warning Flag Clear 135Thermal Warning Flag Hysteresis 15Under Voltage Lockout V CIN V UVLO Rising, on threshold 3.3 3.9V Under Voltage Lockout V CINFalling, off threshold 2.32.95Under Voltage Lockout Hysteresis V CIN V UVLO_HYST 400mV High Side Gate Discharge ResistorbR HS_DSCRGV VDRV = V VCIN = 0 V; V IN = 12 V20.2k ΩNote:a. Min. and Max. are not 100 % production tested.TIMING DEFINITIONSNote:GH is referenced to the high side source. GL is referenced to the low side source.TIMING SPECIFICATIONSParameter Symbol Test Conditions Unless Specified V VDRV = V VCIN = V DSBL# = 5 V ,V VIN = 12 V , T A = 25 °C Min. Typ.Max.UnitTurn Off Propagation DelayHigh Side at d_off_HS 25 % of PWM to 90 % of GH102035nsRise Time High Side t r_HS 10 % to 90 % of GH 10Fall Time High Side t f_HS 90 % to 10 % of GH 8Turn Off Propagation Delay Low Side at d_off_LS 75 % of PWM to 90 % of GL103745Rise Time Low Side t r_LS 10 % to 90 % of GL 6Fall Time Low Side t f_LS 90 % to 10 % of GL 5Dead Time Rising t dead_on 10 % of GL to 10 % of GH 27Dead Time Fallingt dead_off10 % of GH to 10 % of GL19Region DefinitionSymbol 1T urn off propagation delay LSt d_off_LS 2Fall time LS t f_LS 3Dead time rising t dead_on 4Rise time HSt r_HS 5T urn off propagation delay HSt d_off_HS 6Fall time HS t f_HS 7Dead time falling t dead_off 8Rise time LSt r_LSP W MGHGLS W1234 567810%90%10%90%75%25%SIC762CD BLOCK DIAGRAMDETAILED OPERATIONAL DESCRIPTIONPWM Input with Tristate FunctionThe PWM input receives the PWM control signal from the V R controller IC. The PWM input is designed to be compatible with standard controllers using two state logic (H and L) and advanced controllers that incorporate Tristate logic (H, L and Tristate) on the PWM output. For two state logic, the PWM input operates as follows. When PWM is driven above V th_pwm_r the low side is turned off and the high side is turned on. When PWM input is driven below V th_pwm_f the high side turns off and the Low side turns on. For Tristate logic, the PWM input operates as above for driving the MOSFETs.However, there is an third state that is entered into as the PWM output of Tristate compatible controller enters its high impedance state during shut-down. The high impedance state of the controller's PWM output allows the SiC762CD to pull the PWM input into the Tristate region (see the Tristate Voltage Threshold Diagram below). If the PWM input stays in this region for the Tristate Hold-Off Period, t TSHO , both high side and low side MOSFETs are turned off. This function allows the V R phase to be disabled without negative output voltage swing caused by inductor ringing and saves a Schottky diode clamp. The PWM and Tristate regions are separated by hysteresis to prevent false triggering. The SiC762CD incorporates PWM voltage thresholds that are compatible with 5 V logic.Disable (DSBL#)In the low state, the DSBL# pin shuts down the driver IC and disables both high-side and low-side MOSFET. In this state,the standby current is minimized. If DSBL# is left unconnected an internal pull-down resistor will pull the pin Diode Emulation Mode (SMOD) Skip ModeWhen SMOD pin is low the diode emulation mode is enabled.This is a non-synchronous conversion mode that improves light load efficiency by reducing switching losses. Conducted losses that occur in synchronous buck regulators when inductor current is negative are also reduced. Circuitry in the gate drive IC detects when inductor current crosses zero and automatically stops switching the low side MOSFET. See SMOD Operation Diagram for additional details. This function can also be used for a pre-biased output voltage. If SMOD is left unconnected, an internal pull up resistor will pull the pin up to V CIN (Logic High) to disable the diode emulation function.Thermal Shutdown Warning (THDN)The THDN pin is an open drain signal that flags the presence of excessive junction temperature. Connect a maximum of 20 k Ω to pull this pin up to V CIN . An internal temperature sensor detects the junction temperature. The temperature threshold is 150 °C. When this junction temperature is exceeded the THDN flag is set. When the junction temperature drops below 135 °C the device will clear the THDN signal. The SiC762CD does not stop operation when the flag is set. The decision to shutdown must be made by an external thermal control function.Voltage Input (V IN )This is the power input to the drain of the high-side Power MOSFET. This pin is connected to the high power intermediate BUS rail.Switch Node (V SWH and PHASE)The Switch node V SWH is the circuit PWM regulated output.Figure 2U V LOV DR VGHGLC G N DP G N DV S W HBOOTV I N V CI NP W MDSBL#THD NSMOD Thermal W arningT ristate P W MAST C N TL DCM DETECTPHASEregulated high output for the buck converter. The PHASE pin is internally connected to the switch node V SWH . This pin is to be used exclusively as the return pin for the BOOT capacitor. A 20.2 k Ω resistor is connected between GH and PHASE to provide a discharge path for the HS MOSFET in the event that V CIN goes to zero while V IN is still applied.Ground connections (C GND and P GND )P GND (power ground) should be externally connected to C GND (control signal ground). The layout of the Printed Circuit Board should be such that the inductance separating the C GND and P GND should be a minimum. Transient differences due to inductance effects between these two pins should not exceed 0.5 V.Control and Drive Supply Voltage Input (V DRV ,V CIN )V CIN is the bias supply for the gate drive control IC. V DRV is the bias supply for the gate drivers. It is recommended to separate these pins through a resistor. This creates a low pass filtering effect to avoid coupling of high frequency gate drive noise into the IC.Bootstrap Circuit (BOOT)The internal bootstrap switch and an external bootstrap capacitor form a charge pump that supplies voltage to the BOOT pin. An integrated bootstrap diode is incorporated so that only an external capacitor is necessary to complete the bootstrap circuit. Connect a boot strap capacitor with one leg tied to BOOT pin and the other tied to PHASE pin.Shoot-Through Protection and Adaptive Dead Time (AST)The SiC762CD has an internal adaptive logic to avoid shoot through and optimize dead time. The shoot through protection ensures that both high-side and low-side MOSFET are not turned on the same time. The adaptive dead time control operates as follows. When PWM input goes high the LS gate starts to go low after a few ns. When this signal crosses through 1.7 V the logic to switch the HS gate on is activated. When PWM goes low the HS gate goes low. When the HS gate-to-source drive signal crosses through 1.7 V the logic to turn on the LS gate is activated.This feature helps to adjust dead time as gate transitions change with respect to output current and temperature.Under Voltage Lockout (UVLO)During the start up cycle, the UVLO disables the gate drive holding high-side and low-side MOSFET gate low until the input voltage rail has reached a point at which the logic circuitry can be safely activated. The SiC762CD also incorporates logic to clamp the gate drive signals to zero when the UVLO falling edge triggers the shutdown of the device. As an added precaution, a 20.2 k Ω resistor is connected between GH and PHASE to provide a discharge path for the HS MOSFET.TRISTATE PWM VOLTAGE THRESHOLD DIAGRAMDEVICE TRUTH TABLEDSBL#SMOD PWM GH GL Open X X L L L X X L L H L L L H (I L > 0), L (I L ≤ 0)H L H H L H H H H L HHLLHFigure 3V th_tri_f V th_p w m_r V th_tri_rV th_p w m_fP W MGHGL t TSHOt TSHOSMOD OPERATION DIAGRAMPIN CONFIGURATIONFigure 4DSBLSMODP W MGHGLV S WI L > 0I L = 0t d(O N)t d(OFF)Figure 5 - PowerPAK MLP 6 x 6 40P Pin Out - Top ViewV I NP2A G N DP1V S W HP330V S W H29V S W H28 P G N D27 P G N D26 P G N D25 P G N D24 P G N D23 P G N D22 P G N D21 P G N D4PWM39DSBL#38THDN37CGND36GL35VSWH34VSWH33VSWH32VSWH31VSWHSMOD 1V CI N 2V DR V 3BOOT 4C G ND 5GH 6PHASE 7V I N8V I N 9V I N 1020 PGND19 PGND18PGND17 PGND16 PGND15VSWH14VIN13VIN12VIN11VINPIN DESCRIPTIONPin Number Symbol Description1SMOD Disable low side gate operation. Active low.2V CIN This will be the bias supply input for control IC (5 V).3V DRV IC bias supply and gate drive supply voltage (5 V).4BOOT High side driver bootstrap voltage pin for external bootstrap capacitor.5, 37, PAD1C GND Control signal ground. It should be connected to P GND externally. All pins internally connected.6GH Gate signal output pin for high side MOSFET. Pin for monitoring.7PHASE Return pin for the HS bootstrap capacitor. Connect a 0.1 µF ceramic capacitor from this pin to the boot pin (4).8 to 14, PAD2V IN Input voltage for power stage. It is the drain of the high-side MOSFET.15, 29 to 35,PAD3VSWHIt is the phase node between high side MOSFET source and low side MOSFET drain. It should be connected to an output inductor. All pins internally connected.16 to 28P GND Power ground.36GL Gate signal output pin for low side MOSFET. Pin for monitoring.38THDN Thermal shutdown open drain output. Use a 10K pull up resistor to V CIN.39DSBL#Disable pin. Active low.ELECTRICAL CHARACTERISTICSI CIN (mA) vs. Temperature at Frequency = 300 kHzD = 10 %, V CIN = V DRV = 5 VPWM Falling Threshold (V) vs. Temperature (°C)V CIN = V DRV = 5 VDSBL Falling Threshold (V) vs. Temperature (°C)I DRV (mA) vs. Temperature at Frequency = 300 kHzD = 10 %, V CIN = V DRV = 5 VPWM Rising Threshold (V) vs. Temperature (°C)V CIN = V DRV = 5 VDSBL Rising Threshold (V) vs. Temperature (°C)ELECTRICAL CHARACTERISTICSSMOD Falling Threshold (V) vs. Temperature (°C)V CIN = V DRV = 5 VI CIN + I DRV (mA) vs. Temperature at Frequency = 1 MHzD = 10 %, V CIN = V DRV = 5 VPWM Falling Tristate (V) vs. Temperature (°C)SMOD Rising Threshold (V) vs. Temperature (°C)V CIN = V DRV = 5 VI DRV (mA) vs. Temperature at Frequency = 1 MHzD = 10 %, V CIN = V DRV = 5 VPWM Rising Tristate Threshold (V) vs. Temperature (°C)ELECTRICAL CHARACTERISTICSCINSMOD Falling Threshold vs. V CINPWM Falling Threshold vs. VCINSMOD Rising Threshold vs. V CINPWM Rising Threshold vs. V分销商库存信息: VISHAYSIC762CD-T1-GE3。
GE Sensing TransPort PT878 Panametrics 肥沃式流量计说明书

GESensingTransPort ®PT878Panametrics PortableUltrasonic Liquid FlowmeterTransPort PT878 is a Panametrics product. Panametrics has joined other GE high-technology sensing businesses under a new name _GE Industrial, Sensing.ApplicationsThe TransPort PT878 portable liquid flowmeter is a complete portable ultrasonic flow metering system for measurement of:•Potable water •Wastewater•Cooling and heating water •Ultrapure water and liquids •Water/glycol solutions •Crude oil•Refined hydrocarbons •Diesel and fuel oils •Lubricating oils •Chemicals •Beverages •Other liquidsgFeatures•Small, lightweight and easy to use •Non-intrusive flow measurement •Velocity, volumetric and energy flow rates •Totalized flow and trend data •Large, backlit LCD display •Alphanumeric and graphic formats •Multiple-language user interface •Rechargeable battery pack •Logs over 100,000 flow data points •Submersible package •32 site locations •Optional thickness gauge •Optional energy measurement•Suitable for most pipe sizes and materials, including lined pipe1981Portable Flow Metering at Its BestThe TransPort PT878 flowmeter is a highly versatile,self-contained, portable transit-time system with options and accessories to meet all your liquid flow measurement needs. Its compact size; lightweight, rechargeable internal battery pack; and universal power supply charger make it the ideal go-anywhere flowmeter.Accurate with Two-Phase and Perfectly Clean LiquidsThe TransPort PT878’s patented CorrelationTransit-Time™ digital signal processing (DSP) technique greatly increases its signal-to-noise ratio for accurate, drift-free flow measurement in liquids that contain a second phase of entrained solids or gas bubbles. The TransPort flowmeter operates in these and other difficult applications where conventional transit-time flowmeters fail.The TransPort PT878 flowmeter also accurately measures flow rate in perfectly clean liquids containing no “scatterers,” where Doppler-type flowmeters cannot work. The TransPort flowmeter is suited for all standard transit-time applications, plus many that would prevent other transit-time flowmeters from working.Quick and Easy to UseIt’s possible to make your first flow measurement within minutes of opening the box—the TransPort flowmeter is that easy to use. Simply input the site parameters, clamp the transducers onto the pipe, adjust the spacing, and you’re under way. No ancillary equipment is needed, and there’s no need to break into the pipeline. An experienced user can make scores of different measurements in a single day. The TransPort PT878 flowmeter is ideal for all kinds of flow survey work.Flow Transducers and Clamping FixturesUsing clamp-on transducers, the TransPort PT878 flowmeter measures flow rate through metal, plastic or even concrete-lined pipes, without penetrating the pipe wall. From ultra-pure water to corrosive and toxic liquids, the TransPort PT878 flowmeter ensuresnon-contaminating, leak-free measurement withdrift-free accuracy. The TransPort PT878 flowmeter has no moving parts to wear or orifices to clog. It can’t be fouled, and it requires no routine maintenance.A wide variety of transducers are available with different operating frequencies, materials of construction, operating temperatures and sizes to meet the requirements of rugged industrial environments.To hold clamp-on transducers in contact with the pipe, a variety of clamping fixtures are available to accommodate different pipe and transducer sizes. These fixtures use a variety of attachment methods including chain, metal strap, Velcro® strap and magnetic clamps. Alphanumeric and Graphic Liquid Crystal Display Completes the PictureA large, multifunction LCD presents measured data in both alphanumeric and graphic forms. In addition, it helps make programming easy by presenting a software menu that walks you through data entry and function selection.Standard alphanumeric functions include flow velocity, volumetric or energy flow rates, and totalized flow in either English (U.S.) or metric units.In graphic mode, the LCD shows both real time and logged data. The result is a chart recording right on the display, which is very useful for reviewing data and observing trends while on the site.Submersible, Rugged Electronics HousingYour investment in this flowmeter is protected from the day-to-day rigors of industrial usage. The TransPortPT878 is equipped with a rubber boot that provides protection against vibration and shock. The completely sealed housing and ports meet IP67 requirements, so the unit will withstand submersion in up to 3 ft (1 m) of water for limited periods of time. It will continue to function safely even if it is dropped in water.The complete TransPort PT878flowmeter system f its in a compact carrying case.Optional Energy MeasurementThe TransPort PT878 flowmeter combines proven ultrasonic flow measurement with precise RTDtemperature measurement to determine the energy flow rate in liquid heating and cooling systems.With this option, the TransPort flowmeter comesequipped with a built-in power supply for loop-powered RTD temperature sensors, as well as all necessary circuitry and software to make energy flow ratemeasurements. GE offers a variety of optional clamp-on and wetted RTD temperature sensors.Optional Pipe Wall Thickness Gauge TransducerPipe wall thickness is a critical parameter used by the TransPort flowmeter for clamp-on flow measurements.The thickness-gauge option allows accurate wall thickness measurement from outside the pipe.Infrared PortThe TransPort PT878 contains an infrared port forcommunication with your PC. If your laptop or desktop PC does not have infrared capability, an adapter isavailable that can be plugged into your PC’s serial port.Optional Infrared Thermal Printer and AccessoriesWhen you need a permanent record of your work, live measurements, logged data and site parameters can be sent to a variety of printers by beaming data directly from the TransPort PT878’s infrared port. A compact,lightweight, hand-held, infrared thermal printer isavailable. This printer is powered by a lithium ion battery.Built to Be Economical and Stay EconomicalTo be of real value, a portable flowmeter must be as economical to own and operate as it is capable in the field. The TransPort PT878 flowmeter is built to stay in service for many years. Completely solid state, the device rarely wears out or needs servicing, resulting in little downtime and low maintenance costs.The TransPort PT878 Flowmeter Uses the Transit-Time Flow Measurement TechniqueIn this method, two transducers serve as both ultrasonic-signal generators and receivers. Whenmounted on a pipe, they are in acoustic communication with each other, meaning that the second transducer can receive ultrasonic signals transmitted by the first transducer and vice versa.In operation, each transducer functions as a transmitter,generating a certain number of acoustic pulses, and then as a receiver for an identical number of pulses.The time interval between transmission and reception of the ultrasonic signals is measured in both directions.When the liquid in the pipe is not flowing, the transit-time downstream equals the transit-time upstream. When the liquid is flowing, the transit-time downstream is less than the transit-time upstream.The difference between the downstream and upstream transit times is proportional to the velocity of the flowing liquid, and its sign indicates the direction of flow.Ultrasonic Signal PathTransit-time flow measurement technique11AC charger2LEMO®-BNC transducer interconnection cable 3Input/output cable4IR-to-serial port adapter 5Small-pipe transducers 6Thickness gauge7Transducers with universal clamping fixture 8IR thermal printer9Printer AC power supply 10Printer battery chargerTransPort PT878 Accessories2345678910PT878SpecificationsFluid TypesAcoustically conductive fluids, including most clean liquids, and many liquids with entrained solids or gas bubbles. Maximum void fraction depends on transducer,interrogation carrier frequency, path length and pipe configuration.Pipe Sizes0.5 in to 300 in (12.7 mm to 7.6 m) and larger Pipe Wall Thickness Up to 3 in (76.2 mm)Pipe MaterialsAll metals and most plastics. Consult GE for concrete,composite materials, and highly corroded or lined pipes.Clamp-On Flow Accuracy (Velocity)•Pipe ID>6 in (150 mm): ±1% to 2% of reading typical •Pipe ID<6 in (150 mm): ±2% to 5% of reading typical Accuracy depends on pipe size and whethermeasurement is one-path or two-path. Accuracy to ±0.5%of reading may be achievable with process calibration.Repeatability±0.1% to 0.3% of reading Range (Bidirectional)–40 to 40 ft/s (–12.2 to 12.2 m/s)Rangeability (Overall)400:1Specif ications assume a fully developed flow prof ile (typically 10 diameters upstream and 5 diameters downstream of straight pipe run) and flow velocity greater than 1 ft/s (0.3 m/s).Measurement ParametersVolumetric flow, totalized flow and flow velocityOperation and PerformanceFlow MeasurementPatented Correlation Transit-Time mode EnclosureSubmersible IP67DimensionsWeight 3 lb (1.36 kg),size (h x w x d) 9.4 in x 5.5 in x 1.5 in (238 mm x 138 mm x 38 mm)Display240 x 200 pixel backlit LCD graphic display Keypad25-key rubberized tactile membrane keypadInternal BatteryRechargeable battery: 9 to 11 hr of continuous operation Battery Charger Input100 to 250 VAC, 50/60 Hz, 0.38 A MemoryFLASH memory, field-upgradable Operating Temperature –4°F to 131°F (–20°C to 55°C)Storage Temperature–40°F to 158°F (–40°C to 70°C)To ensure maximum battery life, storage temperature exceeding 35°C (95°F) is not recommended for more than one month.Standard Inputs/Outputs•One 0/4 to 20 mA current output•One user-selectable pulse (solid state, 5 V maximum) or frequency (5 V square wave, 100 to 10,000 Hz)•Two 4 to 20 mA analog inputs with switchable power supply for loop-powered temperature transmitters Digital InterfaceInfrared communication port for printer or PC interface Site-Parameter Programming•Menu-driven operator interface using keypad and “soft” function keys•Online help functions including pipe tables •Storage for saving site parametersElectronicsPT878 thickness-gauge optionPT878SpecificationsClamp-On Ultrasonic Flow TransducersTemperature Ranges•Standard: –40°F to 300°F (–40°C to 150°C)•Optional (overall range): –310°F to 572°F (–190°C to 300°C)MountingsStainless steel chain or strap, welded or magnetic clamping fixturesArea Classifications•Standard: General purpose•Optional: Weatherproof Type 4/IP65•Optional: Submersible IP67/68PT878 electronics are designed for general purpose areas.Thickness-Gauge OptionTransducerPanametrics dual-element transducer Pipe-Thickness Range0.05 in to 3 in (1.3 mm to 76.2 mm)Pipe MaterialsMost standard metal and plastic pipe materials Accuracy±1% typical or ±0.002 in (±0.05 mm)Thermal ExposureContinuous operation to 100°F (37°C); intermittentoperation to 500°F (260°C) for 10 sec followed by 2 min air coolingTransducer Cables•Standard: One pair of LEMO® coaxial transducer connectors with 25-ft (8-m) cables•Optional: 1,000-ft (305-m) extension cables available for most transducersData Logging•Memory capacity to log over 100,000 flow data points •Keypad programmable for log units, update times, and start and stop timeDisplay Functions•Graphic display shows flow in numerical or graphic format•Displays logged data•Extensive diagnostic parameters•Supports multiple languages: Dutch, English, French, German, Italian, Japanese, Portuguese, Russian, Spanish, Swedish and othersEuropean ComplianceBattery-powered system complies with EMC Directive 89/336/EEC and transducers comply with PED 97/23/EC for DN<25PT878 Specifications Energy MeasurementEnergy MeasurementCalculates energy flow rate and totalized energy. Requires optional dual-RTD, loop-powered transmitter. Temperature TransducersLoop-powered, three-wire platinum RTDs; clamp-on and wetted (thermo-well) types are availableAccuracy±0.15°C with wetted RTDs (matched pairs)Range–4°F to 500°F (–20°C to 260°C)The accuracy of the energy measurement is a combination of the accuracy of the associated flow and temperature measurements. 1% to 2% of reading is typical for calibrated systems. Not all extremes of parameters can be achieved simultaneously.Additional OptionsPanaView™ PC-Interface SoftwareThe TransPort PT878 communicates with a PC through the infrared interface and Windows® operating systems. Consult the manual for details on sites, logs and other operations with a PC.Printer•Infrared, portable, thermal printer with rechargeable battery and 120 to 240 VAC power supply/recharger •Weight 13 oz (370 g), size 6.3 in x 6.5 in x 2.3 in (160 x mm 164.2 mm x 59 mm), print width 4 in (104 mm)RS232-to-InfraredInfrared adapter plugs into any available serial port to give desktop PCs infrared capability.PanaView software links your TransPort flowmeter to your PC.©2005 GE. All rights reserved.920-039BAll specifications are subject to change for product improvement without notice. TransPort®is a registered trademark of GE. Correlation Transit-Time™ is a trademark of GE. GE®is a registered trademark of General Electric Co. Other company or product names mentioned in this document may be trademarks or registered trademarks of their respective companies, which are not affiliated with GE.g 。
SI7116DN-T1-GE3;中文规格书,Datasheet资料

Vishay SiliconixSi7116DNN-Channel 40-V (D-S) Fast Switching MOSFETFEATURES•Halogen-free Option Available •TrenchFET ® Power MOSFET•New Low Thermal Resistance PowerPAK ®Package with Low 1.07 mm Profile •PWM Optimized •100 % R g TestedAPPLICATIONS•Synchronous Rectification •Intermediate Switch •Synchronous BuckPRODUCT SUMMARYV DS (V)R DS(on) (Ω)I D (A)Q g (Typ.)400.0078 at V GS = 10 V 16.415 nC0.010 at V GS = 4.5 V14.5Notes:a.Surface Mounted on 1" x 1" FR4 board.b.See Solder Profile (/ppg?73257). The PowerPAK 1212-8 is a leadless package. The end of the lead terminal is exposed copper (not plated) as a result of the singulation process in manufacturing. A solder fillet at the exposed copper tip cannot be guaranteed and is not required to ensure adequate bottom side solder interconnection.c.Rework Conditions: manual soldering with a soldering iron is not recommended for leadless components. ABSOLUTE MAXIMUM RATINGS T A = 25 °C, unless otherwise notedParameterSymbol 10 sSteady StateUnit Drain-Source Voltage V DS 40VGate-Source VoltageV GS ± 20Continuous Drain Current (T J = 150 °C)a T A = 25 °C I D16.410.5AT A = 70 °C13.18.4Pulsed Drain CurrentI DM 60Continuous Source Current (Diode Conduction)a I S 3.21.3Avalanche Current L = 0 1 mH I AS 15Avalanche EnergyE AS 11mJ Maximum Power Dissipation aT A = 25 °C P D 3.8 1.5W T A = 70 °C 2.00.8Operating Junction and Storage T emperature Range T J , T stg- 55 to 150°CSoldering Recommendations (Peak Temperature)b, c260THERMAL RESISTANCE RATINGSParameter Symbol T ypical Maximum UnitMaximum Junction-to-Ambient a t ≤ 10 s R thJA 2433°C/WSteady State 6581Maximum Junction-to-Case (Drain)Steady StateR thJC1.92.4Vishay SiliconixSi7116DNNotes:a. Pulse test; pulse width ≤ 300 µs, duty cycle ≤ 2 %.b. Guaranteed by design, not subject to production testing.Stresses beyond those listed under “Absolute Maximum Ratings” may cause permanent damage to the device. These are stress ratings only, and functional operation of the device at these or any other conditions beyond those indicated in the operational sections of the specifications is not implied. Exposure to absolute maximum rating conditions for extended periods may affect device reliability.MOSFET SPECIFICATIONS T J = 25 °C, unless otherwise notedParameter Symbol T est Conditions Min.T yp.Max.UnitStaticGate Threshold Voltage V GS(th) V DS = V GS , I D = 250 µA 1.52.5VGate-Body LeakageI GSS V DS = 0 V , V GS = ± 20 V ± 100 nAZero Gate Voltage Drain Current I DSS V DS = 40 V , V GS = 0 V 1µA V DS = 40 V, V GS = 0 V , T J = 55 °C5On-State Drain Current aI D(on) V DS ≥ 5 V , V GS = 10 V 40A Drain-Source On-State Resistance a R DS(on) V GS = 10 V , I D = 16.4 A 0.00650.0078ΩV GS = 4.5 V, I D = 14.5 A 0.00830.010Forward T ransconductance a g fs V DS = 15 V , I D = 16.4 A 68S Diode Forward Voltage a V SDI S = 3.2 A, V GS = 0 V0.81.2VDynamic bTotal Gate Charge Q g V DS = 20 V , V GS = 4.5 V , I D = 16.4 A1523nCGate-Source Charge Q gs 6.7Gate-Drain Charge Q gd 5.1Gate Resistance R g f = 1 MHz0.71.42.1ΩTurn-On Delay Time t d(on) V DD = 20 V , R L = 20 ΩI D ≅ 1 A, V GEN = 10 V , R g = 6 Ω1015ns Rise Timet r 1015Turn-Off Delay Time t d(off) 3655Fall Timet f 1015Source-Drain Reverse Recovery Time t rr I F = 3.2 A, di/dt = 100 A/µs 3060Body Diode Reverse Recovery ChargeQ rrI F = 3.2 A, di/dt = 100 A/µs 2652nc Output Characteristics Transfer CharacteristicsVishay SiliconixSi7116DNTYPICAL CHARACTERISTICS 25°C, unless otherwise notedGate ChargeSource-Drain Diode Forward VoltageCapacitanceOn-Resistance vs. Gate-to-Source VoltageSafe Operating AreaVishay SiliconixSi7116DNTYPICAL CHARACTERISTICS 25°C, unless otherwise notedVishay Sil iconix maintains worl dwide manufacturing capabil ity. Products may be manufactured at one of several qual ified l ocations. Rel iabil ity data for Sil icon Technology and Package Reliability represent a composite of all qualified locations. For related documents such as package/tape drawings, part marking, and reliability data, see /ppg?73139.Normalized Thermal Transient Impedance, Junction-to-CaseVishay SiliconixAN822PowerPAK ® 1212 Mounting and Thermal ConsiderationsJohnson ZhaoMOSFETs for switching applications are now available with die on resistances around 1 m Ω and with the capability to handle 85 A. While these die capabilities represent a major advance over what was available just a few years ago, it is important for power MOSFET packaging technology to keep pace. It should be obvi-ous that degradation of a high performance die by the package is undesirable. PowerPAK is a new package technology that addresses these issues. The PowerPAK 1212-8 provides ultra-low thermal impedance in a small package that is ideal for space-constrained applications. In this application note, the PowerPAK 1212-8’s construction is described. Following this,mounting information is presented. Finally, thermal and electrical performance is discussed.THE PowerPAK PACKAGEThe PowerPAK 1212-8 package (Figure 1) is a deriva-tive of PowerPAK SO-8. It utilizes the same packaging technology, maximizing the die area. The bottom of the die attach pad is exposed to provide a direct, low resis-tance thermal path to the substrate the device is mounted on. The PowerPAK 1212-8 thus translates the benefits of the PowerPAK SO-8 into a smaller package, with the same level of thermal performance.(Please refer to application note “PowerPAK SO-8Mounting and Thermal Considerations.”)The PowerPAK 1212-8 has a footprint area compara-ble to TSOP-6. It is over 40 % smaller than standard TSSOP-8. Its die capacity is more than twice the size of the standard TSOP-6’s. It has thermal performance an order of magnitude better than the SO-8, and 20times better than TSSOP-8. Its thermal performance is better than all current SMT packages in the market. It will take the advantage of any PC board heat sink capability. Bringing the junction temperature down also increases the die efficiency by around 20 % compared with TSSOP-8. For applications where bigger pack-ages are typically required solely for thermal consider-ation, the PowerPAK 1212-8 is a good option.Both the single and dual PowerPAK 1212-8 utilize the same pin-outs as the single and dual PowerPAK SO-8.The low 1.05 mm PowerPAK height profile makes both versions an excellent choice for applications with space constraints.PowerPAK 1212 SINGLE MOUNTINGTo take the advantage of the single PowerPAK 1212-8’s thermal performance see Application Note 826,Recommended Minimum Pad Patterns With Outline Drawing Access for Vishay Siliconix MOSFETs. Click on the PowerPAK 1212-8 single in the index of this document.In this figure, the drain land pattern is given to make full contact to the drain pad on the PowerPAK package.This land pattern can be extended to the left, right, and top of the drawn pattern. This extension will serve to increase the heat dissipation by decreasing the ther-mal resistance from the foot of the PowerPAK to the PC board and therefore to the ambient. Note that increasing the drain land area beyond a certain point will yield little decrease in foot-to-board and foot-to-ambient thermal resistance. Under specific conditions of board configuration, copper weight, and layer stack,experiments have found that adding copper beyond an area of about 0.3 to 0.5 in 2 of will yield little improve-ment in thermal performance.Figure 1.PowerPAK 1212 DevicesVishay SiliconixAN822PowerPAK 1212 DUALTo take the advantage of the dual PowerPAK 1212-8’s thermal performance, the minimum recommended land pattern can be found in Application Note 826,Recommended Minimum Pad Patterns With Outline Drawing Access for Vishay Siliconix MOSFETs . Click on the PowerPAK 1212-8 dual in the index of this doc-ument.The gap between the two drain pads is 10 mils. This matches the spacing of the two drain pads on the Pow-erPAK 1212-8 dual package.This land pattern can be extended to the left, right, and top of the drawn pattern. This extension will serve to increase the heat dissipation by decreasing the ther-mal resistance from the foot of the PowerPAK to the PC board and therefore to the ambient. Note that increasing the drain land area beyond a certain point will yield little decrease in foot-to-board and foot-to-ambient thermal resistance. Under specific conditions of board configuration, copper weight, and layer stack,experiments have found that adding copper beyond an area of about 0.3 to 0.5 in 2 of will yield little improve-ment in thermal performance.REFLOW SOLDERINGVishay Siliconix surface-mount packages meet solder reflow reliability requirements. Devices are subjected to solder reflow as a preconditioning test and are then reliability-tested using temperature cycle, bias humid-ity, HAST, or pressure pot. The solder reflow tempera-ture profile used, and the temperatures and time duration, are shown in Figures 2 and 3. For the lead (Pb)-free solder profile, see /doc?73257.Ramp-Up Rate+ 6°C /Second Maximum Temperature at 155 ± 15 °C 120 Seconds Maximum Temperature Above 180 °C 70 - 180 Seconds Maximum T emperature240 + 5/- 0 °CTime at Maximum T emperature 20 - 40 Seconds Ramp-Down Rate+ 6 °C/Second MaximumFigure 2. Solder Reflow Temperature ProfileFigure 3.Solder Reflow Temperatures and Time DurationsVishay SiliconixAN822THERMAL PERFORMANCE IntroductionA basic measure of a device’s thermal performance is the junction-to-case thermal resistance, R θjc, or the junction to- foot thermal resistance, R θjf. This parameter is measured for the device mounted to an infinite heat sink and is therefore a characterization of the device only, in other words, independent of the properties of the object to which the device is mounted. Table 1 shows a comparison of the PowerPAK 1212-8, PowerPAK SO-8,standard TSSOP-8 and SO-8 equivalent steady state performance.By minimizing the junction-to-foot thermal resistance, the MOSFET die temperature is very close to the tempera-ture of the PC board. Consider four devices mounted on a PC board with a board temperature of 45 °C (Figure 4). Suppose each device is dissipating 2 W. Using the junc-tion-to-foot thermal resistance characteristics of the PowerPAK 1212-8 and the other SMT packages, die temperatures are determined to be 49.8 °C for the Pow-erPAK 1212-8, 85 °C for the standard SO-8, 149 °C for standard TSSOP-8, and 125 °C for TSOP-6. This is a 4.8 °C rise above the board temperature for the Power-PAK 1212-8, and over 40 °C for other SMT packages. A 4.8 °C rise has minimal effect on r DS(ON) whereas a rise of over 40 °C will cause an increase in r DS(ON) as high as 20 %.Spreading CopperDesigners add additional copper, spreading copper, to the drain pad to aid in conducting heat from a device. It is helpful to have some information about the thermal performance for a given area of spreading copper.Figure 5 and Figure 6 show the thermal resistance of a PowerPAK 1212-8 single and dual devices mounted on a 2-in. x 2-in., four-layer FR-4 PC boards. The two inter-nal layers and the backside layer are solid copper. The internal layers were chosen as solid copper to model the large power and ground planes common in many appli-cations. The top layer was cut back to a smaller area and at each step junction-to-ambient thermal resistance measurements were taken. The results indicate that an area above 0.2 to 0.3 square inches of spreading copper gives no additional thermal performance improvement.A subsequent experiment was run where the copper on the back-side was reduced, first to 50 % in stripes to mimic circuit traces, and then totally removed. No signif-icant effect was observed.TABLE 1: EQIVALENT STEADY STATE PERFORMANCEPackage SO-8TSSOP-8TSOP-8PPAK 1212PPAK SO-8ConfigurationSingleDual Single Dual Single Dual Single Dual Single Dual Thermal Resiatance R thJC (C/W)2040528340902.45.51.85.5Figure 4. Temperature of Devices on a PC BoardVishay SiliconixAN822CONCLUSIONSAs a derivative of the PowerPAK SO-8, the PowerPAK 1212-8 uses the same packaging technology and has been shown to have the same level of thermal perfor-mance while having a footprint that is more than 40 %smaller than the standard TSSOP-8.Recommended PowerPAK 1212-8 land patterns are provided to aid in PC board layout for designs using this new package.The PowerPAK 1212-8 combines small size with attrac-tive thermal characteristics. By minimizing the thermal rise above the board temperature, PowerPAK simplifies thermal design considerations, allows the device to run cooler, keeps r DS(ON) low, and permits the device to handle more current than a same- or larger-size MOS-FET die in the standard TSSOP-8 or SO-8 packages.Figure 5. Spreading Copper - Si7401DNFigure 6. Spreading Copper - Junction-to-Ambient Performance分销商库存信息: VISHAYSI7116DN-T1-GE3。
FGH40N65UFDTU;中文规格书,Datasheet资料
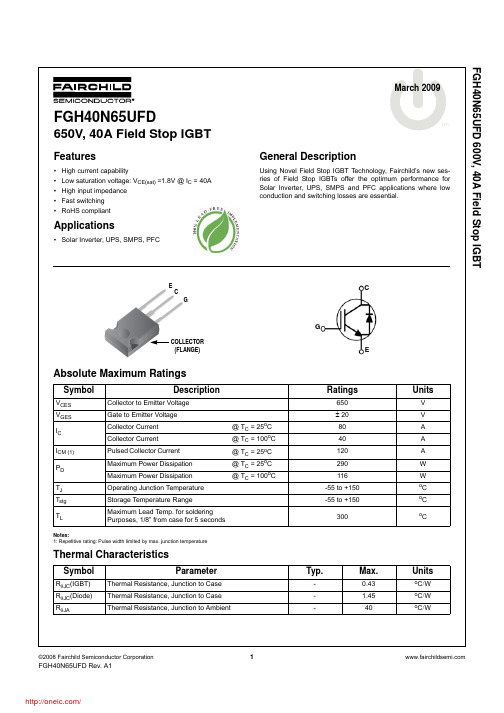
Figure 3. Typical Saturation Voltage Characteristics
120
Common Emitter
100
VGE = 15V TC = 25oC
80 TC = 125oC
20
VGE = 8V
0
0.0
1.5
3.0
4.5
6.0
Collector-Emitter Voltage, VCE [V]
0
0
1
2
3
4
Collector-Emitter Voltage, VCE [V]
Figure 5. Saturation Voltage vs. Case Temperature at Variant Current Level
3.5 Common Emitter VGE = 15V
3.0 80A
0 5 6 7 8 9 10 11 12 Gate-Emitter Voltage,VGE [V]
120 TC = 125oC
100
15V 20V
12V
Collector Current, IC [A]
Collector Current, IC [A]
80
80
60
60
10V
10V
40
40
20
VGE = 8V
0
0.0
1.5
3.0
4.5
6.0
Collector-Emitter Voltage, VCE [V]
Figure 4. Transfer Characteristics
120
Common Emitter VCE = 20V 100 TC = 25oC TC = 125oC 80
SI4459ADY-T1-GE3;中文规格书,Datasheet资料

3600
1800 Crss
Coss
0.003 0 14 28 42 ID - Drain Current (A) 56 70
0 0 6 12 18 24 VDS - Drain-to-Source Voltage (V) 30
A
mJ
Maximum Power Dissipation
PD
W
Operating Junction and Storage Temperature Range
TJ, Tstg
°C
THERMAL RESISTANCE RATINGS
Parameter Maximum Junction-to-Ambienta, c Maximum Junction-to-Foot Notes: a. Surface mounted on 1" x 1" FR4 board. b. t = 10 s. c. Maximum under steady state conditions is 80 °C/W. d. Based on TC = 25 °C. Document Number: 69979 S11-1813-Rev. B, 12-Sep-11 This document is subject to change without notice. THE PRODUCTS DESCRIBED HEREIN AND THIS DOCUMENT ARE SUBJECT TO SPECIFIC DISCLAIMERS, SET FORTH AT /doc?91000 / 1 t 10 s Steady State Symbol RthJA RthJF Typical 29 13 Maximum 35 16 Unit °C/W
PT878便携式超声波中文操作手册(修改)
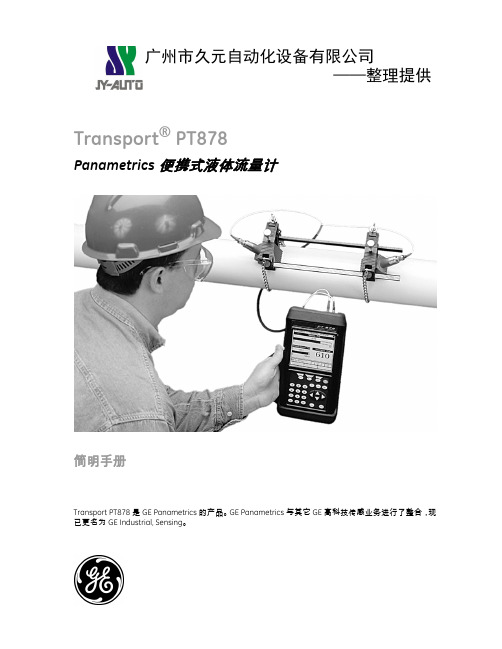
SL2.2S规格书,usb HUB大全,替换FE1.1S,GL850,GL852,PL2586

USB2.0 HUB控制器集成电路USB 2.0 HIGH SPEED 4-PORT HUB CONTROLLERSL2.2s数据手册Data Sheet内容目录第一章管脚分配 (3)1.1 SL2.2S管脚图 (3)1.2 SL2.2S管脚定义 (3)第二章 功能叙述 (5)2.1综述 (5)2.2指示灯 (5)2.2.1单灯方案 (5)2.2.2多灯方案 (6)2.2.3 LED指示定义 (6)2.3过流保护 (6)2.4充电支持 (6)2.5I2C接口 (7)2.6EEPROM设置 (7)第三章电气特性 (8)3.1极限工作条件 (8)3.2工作范围 (8)3.3直流电特性 (8)3.4HS/FS/LS电气特性 (8)3.5ESD特性 (8)附录一封装 (9)表格目录表格1: 端口LED定义 (6)表格 2 : ACTIVE LED定义 (6)表格3:EEPROM数据结构定义 (7)表格4: 最大额定值 (8)表格5: 工作范围 (8)表格6: 直流电特性 (8)插图目录图1:SSOP28 管脚图 (3)图2:单灯方案配置 (5)图3: 5灯方案配置 ............................................................................... (6)图 4:附录 封装图 ................................................................................... .9第一章管脚分配1.1SL2.2s管脚图图1:SSOP28 管脚图1.2SL2.2s管脚定义管脚名称28Die IO类型定义Pin#VSS 1 P 芯片地XOUT 2 O晶振PAD XIN 3 IDM4 4 B下行口4的USB信号DP4 5 BDM3 6 B下行口3的USB信号DP3 7 BDM2 8 B下行口2的USB信号DP2 9 BDM1 10 B下行口1的USB信号DP1 11 BVDD18 12 P 模拟1.8vVDD33 13 P 模拟3.3v - 14 NCUDM 15 B上行口的USB信号UDP 16 BRESET_N 17 I,Pu 芯片外部复位输入- 18 NCPSELF 19 I,Pu 高为自供电,低为总线供电VDD5 20 P 5v输入VDD33 21 P 3.3v输出DRV 22 B,Pu 点灯驱动信号LED1 23 B,Pu 点灯驱动信号LED2 24 B,Pu 点灯驱动信号PWRN 25 B,Pu 下行口电源输出控制,低有效OVCRN/SDA 26 B,PuI2C SDA数据线,内部上拉;芯片初始化完成后作为过流保护输入脚,低有效SCL 27 B,Pu I2C SCL时钟输出VDD18 28 P 数字1.8v注释:O,输出;I 输入;B 双向;P 电源/接地;Pu 上拉;Pd 下拉;NC 悬空;第二章 功能叙述2.1综述SL2.2s 是一颗高集成度,高性能,低功耗的USB2.0集线器主控芯片;该芯片采用STT 技术,单电源供电方式,芯片供电电压为5v , 内部集成5V 转3.3V,只需在外部电源添加滤波电容;芯片自带复位电路,低功耗技术让他更加出众。
SIP32411DNP-T1-GE4;SIP32411DR-T1-GE3;中文规格书,Datasheet资料

Notes: x = Lot code GE3 and GE4 denote halogen-free and RoHS compliant
ABSOLUTE MAXIMUM RATINGS
Parameter Supply Input Voltage (VIN) Enable Input Voltage (VEN) Output Voltage (VOUT) Maximum Continuous Switch Current (Imax.) Maximum Pulsed Current (IDM) VIN (Pulsed at 1 ms, 10 % Duty Cycle) ESD Rating (HBM) Junction Temperature (TJ) Thermal Resistance (JA)a Power Dissipation (PD)a 6 pin SC70-6b 4 pin TDFN4 1.2 mm x 1.6 mmc 6 pin SC70-6b 4 pin TDFN4 1.2 mm x 1.6 mmc SC70-6 package TDFN4 1.2 mm x 1.6 mm SC70-6 package TDFN4 1.2 mm x 1.6 mm Limit - 0.3 to 6 - 0.3 to 6 - 0.3 to VIN + 0.3 1.8 2.4 2.2 3 4000 - 40 to 125 240 170 230 324 V °C °C/W mW A V Unit
Stresses beyond those listed under "Absolute Maximum Ratings" may cause permanent damage to the device. These are stress ratings only, and functional operation of the device at these or any other conditions beyond those indicated in the operational sections of the specifications is not implied. Exposure to absolute maximum rating/conditions for extended periods may affect device reliability.
德森精密DSP-1008使用说明书
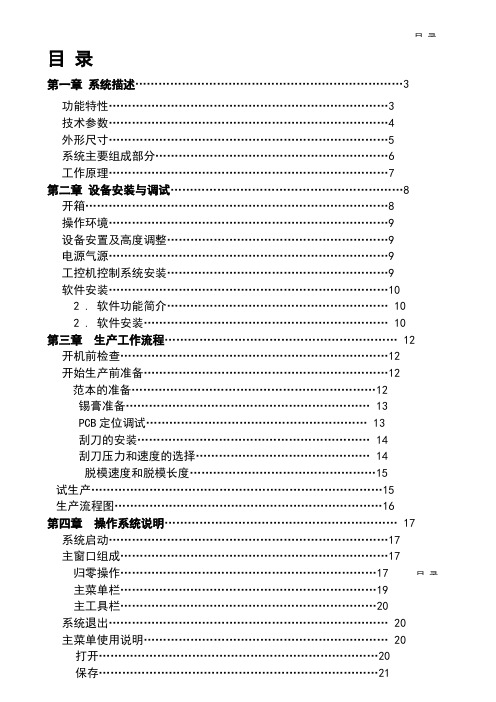
目 录目 录 目 录第一章 系统描述.....................................................................3 功能特性........................................................................3 技术参数........................................................................4 外形尺寸........................................................................5 系统主要组成部分............................................................6 工作原理........................................................................7 第二章 设备安装与调试............................................................8 开箱..............................................................................8 操作环境........................................................................9 设备安置及高度调整.........................................................9 电源气源........................................................................9 工控机控制系统安装.........................................................9 软件安装........................................................................10 2 . 软件功能简介......................................................... 10 2 . 软件安装............................................................... 10 第三章 生产工作流程............................................................ 12 开机前检查.....................................................................12 开始生产前准备...............................................................12 范本的准备...............................................................12 锡膏准备............................................................... 13 PCB 定位调试......................................................... 13 刮刀的安装............................................................ 14 刮刀压力和速度的选择............................................. 14 脱模速度和脱模长度................................................15 试生产...........................................................................15 生产流程图.....................................................................16 第四章 操作系统说明............................................................ 17 系统启动........................................................................17 主窗口组成.....................................................................17 归零操作..................................................................17 主菜单栏..................................................................19 主工具栏..................................................................20 系统退出........................................................................ 20 主菜单使用说明 (20)打开........................................................................20 保存 (21)I/O检测 (21)移动检测 (22)过板 (23)报警复位 (23)联机 (23)产量清零 (23)刮刀移动 (23)机器参数 (24)更新有效期 (24)系统密码 (24)密码设置 (24)语言 (24)设置用户产品信息及生产信息 (24)查看报警记录 (25)生产记录 (25)说明 (25)故障查询 (26)关于DESEN (26)主工具栏使用说明 (27)资料录入 (27)生产设置 (31)网板自动清洗 (32)开始生产 (32)停止生产 (33)第一章系统描述第一章系统描述功能特性采用先进的图像视觉识别系统,独立控制与调节的照明,高速移动的镜头,精确地进行PCB与模板的对准,确保印刷精度为±。
SI4401DDY-T1-GE3;中文规格书,Datasheet资料
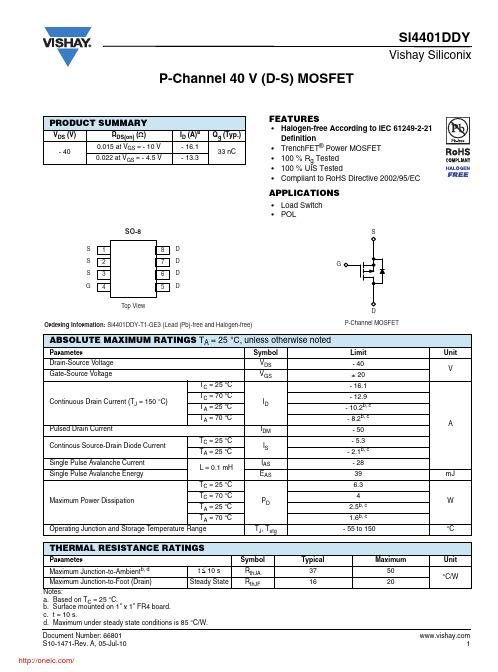
0.024 V GS = 4.5 V 0.018 V GS = 10 V 0.012
C - Capacitance (pF)
3600 Ciss 2700
1800
0.006
900
Coss Crss
0 0 10 20 30 40 50
0 0 8 16 24 32 40
ID - Drain Current (A)
0.5
1.0
1.5
2.0
VDS - Drain-to-Source Voltage (V)
VGS - Gate-to-Source Voltage (V)
Output Characteristics
0.030 4500
Transfer Characteristics
RDS(on) - On-Resistance (Ω)
50 V GS = 10 V thru 5 V 40
ID - Drain Current (A)
10
V GS = 4 V
ID - Drain Current (A)
8
30
6
20
4 T C = 25 °C 2
10 V GS = 3 V 0 0.0
T C = 125 °C 0 T C = - 55 °C 0 1 2 3 4
• Halogen-free According to IEC 61249-2-21 Definition • TrenchFET® Power MOSFET • 100 % Rg Tested • 100 % UIS Tested • Compliant to RoHS Directive 2002/95/EC
Si4401DDY
Vishay Siliconix
HCS878 8.0 使用说明书
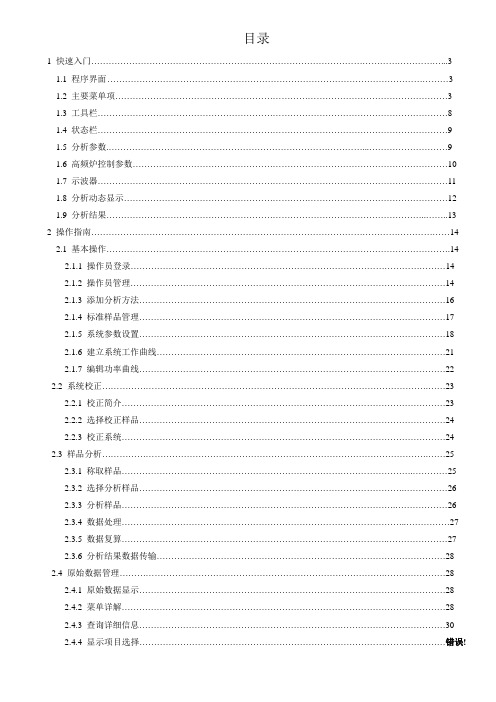
目录1 快速入门 (3)1.1 程序界面 (3)1.2 主要菜单项 (3)1.3 工具栏 (8)1.4 状态栏 (8)1.5 分析参数 (9)1.6 高频炉控制参数 (10)1.7 示波器 (11)1.8 分析动态显示 (12)1.9 分析结果 (13)2 操作指南 (14)2.1 基本操作 (14)2.1.1 操作员登录 (14)2.1.2 操作员管理 (14)2.1.3 添加分析方法 (16)2.1.4 标准样品管理 (17)2.1.5 系统参数设置 (18)2.1.6 建立系统工作曲线 (21)2.1.7 编辑功率曲线 (22)2.2 系统校正 (23)2.2.1 校正简介 (23)2.2.2 选择校正样品 (24)2.2.3 校正系统 (24)2.3 样品分析 (25)2.3.1 称取样品 (25)2.3.2 选择分析样品 (26)2.3.3 分析样品 (26)2.3.4 数据处理 (27)2.3.5 数据复算 (27)2.3.6 分析结果数据传输 (28)2.4 原始数据管理 (28)2.4.1 原始数据显示 (28)2.4.2 菜单详解 (28)2.4.3 查询详细信息 (30)2.4.4 显示项目选择……………………………………………………………………………………………错误!未定义书签。
2.4.5 数据过滤 (32)2.4.6 查询备份记录 (33)2.4.7 原始记录报表 (34)2.4.7.1 报表设计 (3)2.4.7.2 报表页面设置 (3)2.4.7.3 设置打印参数 (3)2.4.7.4 打印预览 (3)2.4.7.5 打印报表 (3)2.5 系统工具 (41)2.5.1 系统诊断 (41)2.5.2 修复/压缩数据库 (42)2.5.3 数据库备份 (42)1 快速入门1.1 程序界面系统运行后显示的主界面,包括菜单、工具栏、分析参数、高频率控制参数(*)、分析动态显示、状态栏和分析结果几个部分,对于不同的设备配置其界面也有所区别。
HI-8788中文资料

HI-8787,HI-8788 DESCRIPTIONFEATURESPIN CONFIGURATIONThe HI-8787and HI-8788are system components forinterfacing16bit parallel data to an ARINC429bus.Theycombine logic and line driver on one chip.The HI-8787hasan output resistance of37.5ohms,and the HI-8788hasoutput resistance of10ohms to facilitate external lightningprotection circuitry.The technology is analog/digitalCMOS.Both products offer high speed data bus transactions into abuffer register.After loading216-bit words,data isautomatically transferred and transmitted.The data rate isequal to the clock rate.Parity can be enabled in the32ndbit.Reset is used to initialize the logic upon startup.Wordgaps are automatically sent.The part requires+/-10volt supplies in addition to a5voltsupply.Automatically converts16bit parallel datato ARINC429or561dataHigh speed data bus interfaceOn-chip line driverAvailable in small TQFP packageMilitary processing optionslllll32-Pin Plastic TQFP package January200124-TXBOUT23-TXAOUT22-V-21-PARITY ENB20-XMT RDY19-XMIT CLK18-17-RESETWRITED4-1N/C-2D5-3D6-4D7-5D8-6D9-7D10-8HI-8787PQIHI-8787PQTHI-8788PQI&HI-8788PQT元器件交易网PARAMETER SYMBOL CONDITION MIN TYP MAX UNITS Operating Voltage V 4.755 5.25VMin.Input Voltage(HI)V 2.0 1.4VMax.Input Voltage(LO)V 1.40.7VMin.Input Current(HI)I V=4.9V280µAMax.Input Current(LO)I V=0.1V-1µAMin.Output Voltage(HI)V I=-1.6mA 2.7VMax.Output Voltage(LO)V I=1.6mA0.4VOperating Current Drain I f=100khz0.8 2.8mAInput Capacitance C Not tested20pFCCCCOperating Voltage V+9.51010.5V Operating Voltage V--9.5-1010.5VLine Driver Output Levels(Ref.To GND)ONE no load,VCC=5.0V 4.5 5.0 5.5VNULL“-0.2500.25VZERO-5.5-5.0-4.5VLine Driver Output Levels(Differential TXAOUT-TXBOUT)ONE no load,VCC=5.0V9.010.011.0VNULL“-0.500.5VZERO“-11.0-10.0-9.0V Minimum Short Circuit Sink or Source Current I momentary magnitude80mAOperating Current Drain(V+)I f=100khz620mA Operating Current Drain(V-)I f=100khz-20-6mAIHILIH IHIL ILOH OUTIH OUTINOUTDDEENOTE:Stresses above absolute maximumratings or outside recommended operatingconditions may cause permanent damage to thedevice.These are stress ratings only.Operationat the limits is not recommended.Voltages referenced to GroundSupply voltagesV+.................................................12.5VV-.................................................-12.5VDC current per input pin................+10maPower dissipation at25°plastic DIL............1.0W,derate10mW/°Cceramic DIL..........0.5W,derate7mW/°CSolder Temperature........275°C for10secStorage Temperature........-65°C to+150°CVCC (7V)ABSOLUTE MAXIMUM RATINGS RECOMMENDED OPERATING CONDITIONSSupply VoltagesV+.......................................+10V (5)V-........................................-10V (5)Temperature RangeIndustrial Screening.........-40°C to+85°CHi-Temp Screening........-55°C to+125°CMilitary Screening..........-55°C to+125°CVCC.......................................5V (5)VCC=5.0V,V=0V,V+=10V,V-=-10V,T=Operating Temperature Range(unless otherwise specified).SS ACONDITIONSTemperature ORDERING INFORMATIONHI-8787PQI YES 37.5ohm 32Pin Plastic TQFP -40°C TO +85°C I SOLDER HI-8787PQT YES 37.5ohm 32Pin Plastic TQFP -55°C TO +125°C T SOLDER HI-8788PQI YES 10.0ohm 32Pin Plastic TQFP -40°C TO +85°C I SOLDER HI-8788PQTYES10.0ohm32Pin Plastic TQFP-55°C TO +125°CTSOLDER元器件交易网w w w .c e c b 2b .c o m32PIN PLASTIC。
西门子 S7-1200 功能安全手册 - 设备手册说明书

SIMATICS7S7-1200 功能安全手册设备手册Siemens AGDigital IndustriesⓅ 10/2022 本公司保留更改的权利 Copyright © Siemens AG 2022. 保留所有权利法律资讯警告提示系统为了您的人身安全以及避免财产损失,必须注意本手册中的提示。
人身安全的提示用一个警告三角表示,仅与财产损失有关的提示不带警告三角。
警告提示根据危险等级由高到低如下表示。
危险表示如果不采取相应的小心措施,将会导致死亡或者严重的人身伤害。
警告表示如果不采取相应的小心措施,可能导致死亡或者严重的人身伤害。
小心表示如果不采取相应的小心措施,可能导致轻微的人身伤害。
注意表示如果不采取相应的小心措施,可能导致财产损失。
当出现多个危险等级的情况下,每次总是使用最高等级的警告提示。
如果在某个警告提示中带有警告可能导致人身伤害的警告三角,则可能在该警告提示中另外还附带有可能导致财产损失的警告。
合格的专业人员本文件所属的产品/系统只允许由符合各项工作要求的合格人员进行操作。
其操作必须遵照各自附带的文件说明,特别是其中的安全及警告提示。
由于具备相关培训及经验,合格人员可以察觉本产品/系统的风险,并避免可能的危险。
按规定使用 Siemens 产品请注意下列说明:警告Siemens 产品只允许用于目录和相关技术文件中规定的使用情况。
如果要使用其他公司的产品和组件,必须得到 Siemens 推荐和允许。
正确的运输、储存、组装、装配、安装、调试、操作和维护是产品安全、正常运行的前提。
必须保证允许的环境条件。
必须注意相关文件中的提示。
商标所有带有标记符号 ® 的都是 Siemens AG 的注册商标。
本印刷品中的其他符号可能是一些其他商标。
若第三方出于自身目的使用这些商标,将侵害其所有者的权利。
责任免除我们已对印刷品中所述内容与硬件和软件的一致性作过检查。
然而不排除存在偏差的可能性,因此我们不保证印刷品中所述内容与硬件和软件完全一致。
SIR426DP-T1-GE3;中文规格书,Datasheet资料

Vishay SiliconixSiR426DPN-Channel 40-V (D-S) MOSFETFEATURES•Halogen-free According to IEC 61249-2-21Definition•TrenchFET ® Power MOSFET •100 % R g Tested •100 % UIS Tested•Compliant to RoHS Directive 2002/95/ECAPPLICATIONS•DC/DC Converters- Synchronous Buck - Synchronous RectifierPRODUCT SUMMARYV DS (V)R DS(on) (Ω)I D (A)Q g (Typ.)400.0105 at V GS = 10 V 30a 9.3 nC0.0125 at V GS = 4.5 V30aNotes:a.Based on T C = 25 °C. Package limited.b.Surface Mounted on 1" x 1" FR4 board.c.t = 10 s.d. See Solder Profile (/ppg?73257). The PowerPAK SO-8 is a leadless package. The end of the lead terminal is exposed copper (not plated) as a result of the singulation process in manufacturing. A solder fillet at the exposed copper tip cannot be guaranteed and is not required to ensure adequate bottom side solder interconnection.e.Rework Conditions: manual soldering with a soldering iron is not recommended for leadless components.f.Maximum under Steady State conditions is 70 °C/W.ABSOLUTE MAXIMUM RATINGS T A = 25 °C, unless otherwise notedParameter Symbol Limit Unit Drain-Source Voltage V DS 40VGate-Source Voltage V GS ± 20Continuous Drain Current (T J = 150 °C)T C = 25 °C I D 30a AT C = 70 °C 30aT A = 25 °C 15.9b, cT A = 70 °C 12.8b, cPulsed Drain Current I DM 70Avalanche Current L = 0.1 mHI AS 20Avalanche Energy E AS 20mJ Continuous Source-Drain Diode Current T C = 25 °C I S30a A T A = 25 °C 4b, c Maximum Power DissipationT C = 25 °C P D 41.7W T C = 70 °C 26.7T A = 25 °C 4.8b, c T A = 70 °C 3.1b, cOperating Junction and Storage T emperature Range T J , T stg - 55 to 150°C Soldering Recommendations (Peak Temperature)d, e 260THERMAL RESISTANCE RATINGSParameter Symbol Typical MaximumUnitMaximum Junction-to-Ambient b, f t ≤ 10 s R thJA2126°C/WMaximum Junction-to-Case (Drain)Steady StateR thJC 2.4 3.0Vishay SiliconixSiR426DPNotes:a. Pulse test; pulse width ≤ 300 µs, duty cycle ≤ 2 %.b. Guaranteed by design, not subject to production testing.Stresses beyond those listed under “Absolute Maximum Ratings” may cause permanent damage to the device. These are stress ratings only, and functional operation of the device at these or any other conditions beyond those indicated in the operational sections of the specifications is not implied. Exposure to absolute maximum rating conditions for extended periods may affect device reliability.SPECIFICATIONS T J = 25 °C, unless otherwise notedParameter Symbol Test Conditions Min. Typ.Max.UnitStaticDrain-Source Breakdown Voltage V DS V GS = 0 V , I D = 250 µA40V V DS Temperature Coefficient ΔV DS /T J I D = 250 µA47mV/°C V GS(th) T emperature Coefficient ΔV GS(th)/T J - 5.4Gate-Source Threshold Voltage V GS(th)V DS = V GS , I D = 250 µA 1.2 2.5V Gate-Source LeakageI GSS V DS = 0 V , V GS = ± 20 V ± 100nA Zero Gate Voltage Drain Current I DSS V DS = 40 V , V GS = 0 V 1µA V DS = 40 V , V GS = 0 V , T J = 55 °C5On-State Drain Current aI D(on) V DS ≥ 5 V, V GS = 10 V 30A Drain-Source On-State Resistance a R DS(on)V GS = 10 V , I D = 15 A 0.00850.0105ΩV GS = 4.5 V, I D = 10 A 0.01040.0125Forward T ransconductance a g fsV DS = 15 V , I D = 15 A43SDynamic bInput Capacitance C iss V DS = 20 V , V GS = 0 V, f = 1 MHz1160pFOutput CapacitanceC oss 185Reverse Transfer Capacitance C rss 70Total Gate Charge Q g V DS = 20 V , V GS = 10 V , ID = 10 A 20.531nC V DS = 20 V , V GS = 4.5 V , I D = 10 A 9.314Gate-Source Charge Q gs 3.1Gate-Drain Charge Q gd 2.5Gate Resistance R g f = 1 MHz0.20.8 1.6ΩTurn-On Delay Time t d(on) V DD = 20 V , R L = 2 ΩI D ≅ 10 A, V GEN = 4.5 V , R g = 1 Ω1835ns Rise Timet r 1530Turn-Off Delay Time t d(off) 1835Fall Timet f 1020Turn-On Delay Time t d(on) V DD = 20 V , R L = 2 ΩI D ≅ 10 A, V GEN = 10 V , R g = 1 Ω918Rise Timet r 918Turn-Off Delay Time t d(off) 1835Fall Timet f816Drain-Source Body Diode Characteristics Continuous Source-Drain Diode Current I S T C = 25 °C30A Pulse Diode Forward Current I SM 70Body Diode VoltageV SD I S = 4.0 A, V GS = 0 V0.77 1.2V Body Diode Reverse Recovery Time t rr I F = 10 A, dI/dt = 100 A/µs, T J = 25 °C2345ns Body Diode Reverse Recovery Charge Q rr 1938nC Reverse Recovery Fall Time t a 14nsReverse Recovery Rise Timet b9Vishay Siliconix SiR426DPOn-Resistance vs. Drain Current and Gate VoltageGate ChargeThreshold VoltageSingle Pulse Power (Junction-to-Ambient)Vishay SiliconixSiR426DPTYPICAL CHARACTERISTICS 25 °C, unless otherwise noted* The power dissipation P D is based on T J(max) = 150 °C, using junction-to-case thermal resistance, and is more useful in settling the upper dissipation limit for cases where additional heatsinking is used. It is used to determine the current rating, when this rating falls below the package limit.Power, Junction-to-CasePower, Junction-to-AmbientSiR426DPVishay SiliconixTYPICAL CHARACTERISTICS 25 °C, unless otherwise notedVishay Siliconix maintains worldwide manufacturing capability. Products may be manufactured at one of several qualified locations. Reliability data for Silicon Technology and Package Reliability represent a composite of all qualified locations. For related documents such as package/tape drawings, part marking, and reliability data, see /ppg?65162.Package InformationVishay Siliconix PowerPAK® SO-8, (SINGLE/DUAL)MILLIMETERS INCHES DIM.MIN.NOM.MAX.MIN.NOM.MAX.A0.97 1.04 1.120.0380.0410.044A10.00-0.050.000-0.002b0.330.410.510.0130.0160.020c0.230.280.330.0090.0110.013D 5.05 5.15 5.260.1990.2030.207D1 4.80 4.90 5.000.1890.1930.197D2 3.56 3.76 3.910.1400.1480.154D3 1.32 1.50 1.680.0520.0590.066D40.57 TYP.0.0225 TYP.D5 3.98 TYP.0.157 TYP.E 6.05 6.15 6.250.2380.2420.246E1 5.79 5.89 5.990.2280.2320.236E2 3.48 3.66 3.840.1370.1440.151E3 3.68 3.78 3.910.1450.1490.154E40.75 TYP.0.030 TYP.e 1.27 BSC0.050 BSCK 1.27 TYP.0.050 TYP.K10.56--0.022--H0.510.610.710.0200.0240.028L0.510.610.710.0200.0240.028L10.060.130.200.0020.0050.008θ0°-12°0°-12°W0.150.250.360.0060.0100.014M0.125 TYP.0.005 TYP.ECN: T10-0055-Rev. J, 15-Feb-10DWG: 5881Vishay SiliconixAN821PowerPAK ® SO-8 Mounting and Thermal ConsiderationsWharton McDanielMOSFETs for switching applications are now available with die on resistances around 1 m Ω and with the capability to handle 85 A. While these die capabilities represent a major advance over what was available just a few years ago, it is important for power MOSFET packaging technology to keep pace. It should be obvi-ous that degradation of a high performance die by the package is undesirable. PowerPAK is a new package technology that addresses these issues. In this appli-cation note, PowerPAK’s construction is described.Following this mounting information is presented including land patterns and soldering profiles for max-imum reliability. Finally, thermal and electrical perfor-mance is discussed.THE PowerPAK PACKAGEThe PowerPAK package was developed around the SO-8 package (Figure 1). The PowerPAK SO-8 uti-lizes the same footprint and the same pin-outs as the standard SO-8. This allows PowerPAK to be substi-tuted directly for a standard SO-8 package. Being a leadless package, PowerPAK SO-8 utilizes the entire SO-8 footprint, freeing space normally occupied by the leads, and thus allowing it to hold a larger die than a standard SO-8. In fact, this larger die is slightly larger than a full sized DPAK die. The bottom of the die attach pad is exposed for the purpose of providing a direct,low resistance thermal path to the substrate the device is mounted on. Finally, the package height is lower than the standard SO-8, making it an excellent choice for applications with space constraints.PowerPAK SO-8 SINGLE MOUNTINGThe PowerPAK single is simple to use. The pin arrangement (drain, source, gate pins) and the pin dimensions are the same as standard SO-8 devices (see Figure 2). Therefore, the PowerPAK connection pads match directly to those of the SO-8. The only dif-ference is the extended drain connection area. To take immediate advantage of the PowerPAK SO-8 single devices, they can be mounted to existing SO-8 land patterns.The minimum land pattern recommended to take full advantage of the PowerPAK thermal performance see Application Note 826, Recommended Minimum Pad Patterns With Outline Drawing Access for Vishay Sili-conix MOSFETs . Click on the PowerPAK SO-8 single in the index of this document.In this figure, the drain land pattern is given to make full contact to the drain pad on the PowerPAK package.This land pattern can be extended to the left, right, and top of the drawn pattern. This extension will serve to increase the heat dissipation by decreasing the ther-mal resistance from the foot of the PowerPAK to the PC board and therefore to the ambient. Note that increasing the drain land area beyond a certain point will yield little decrease in foot-to-board and foot-to-ambient thermal resistance. Under specific conditions of board configuration, copper weight and layer stack,experiments have found that more than about 0.25 to 0.5 in 2 of additional copper (in addition to the drain land) will yield little improvement in thermal perfor-mance.Figure 1.PowerPAK 1212 DevicesFigure 2.Standard SO-8Pow erPAK SO-8Vishay SiliconixAN821PowerPAK SO-8 DUALThe pin arrangement (drain, source, gate pins) and the pin dimensions of the PowerPAK SO-8 dual are the same as standard SO-8 dual devices. Therefore, the PowerPAK device connection pads match directly to those of the SO-8. As in the single-channel package,the only exception is the extended drain connection area. Manufacturers can likewise take immediate advantage of the PowerPAK SO-8 dual devices by mounting them to existing SO-8 dual land patterns.To take the advantage of the dual PowerPAK SO-8’s thermal performance, the minimum recommended land pattern can be found in Application Note 826,Recommended Minimum Pad Patterns With Outline Drawing Access for Vishay Siliconix MOSFETs . Click on the PowerPAK 1212-8 dual in the index of this doc-ument.The gap between the two drain pads is 24 mils. This matches the spacing of the two drain pads on the Pow-erPAK SO-8 dual package.REFLOW SOLDERINGVishay Siliconix surface-mount packages meet solder reflow reliability requirements. Devices are subjected to solder reflow as a test preconditioning and are then reliability-tested using temperature cycle, bias humid-ity, HAST, or pressure pot. The solder reflow tempera-ture profile used, and the temperatures and time duration, are shown in Figures 3 and 4.For the lead (Pb)-free solder profile, see /doc?73257.Ramp-Up Rate+ 6 °C /Second Maximum Temperature at 155 ± 15 °C 120 Seconds Maximum Temperature Above 180 °C 70 - 180 Seconds Maximum T emperature 240 + 5/- 0 °CTime at Maximum T emperature 20 - 40 SecondsRamp-Down Rate+ 6 °C/Second MaximumFigure 3. Solder Reflow Temperature ProfileFigure 3.Solder Reflow Temperatures and Time DurationsVishay SiliconixAN821THERMAL PERFORMANCE IntroductionA basic measure of a device’s thermal performance is the junction-to-case thermal resistance, R θjc , or the junction-to-foot thermal resistance, R θjf . This parameter is measured for the device mounted to an infinite heat sink and is therefore a characterization of the device only, in other words, independent of the properties of the object to which the device is mounted. Table 1 shows a comparison of the DPAK, PowerPAK SO-8, and stan-dard SO-8. The PowerPAK has thermal performance equivalent to the DPAK, while having an order of magni-tude better thermal performance over the SO-8. Thermal Performance on Standard SO-8 Pad Pattern Because of the common footprint, a PowerPAK SO-8can be mounted on an existing standard SO-8 pad pat-tern. The question then arises as to the thermal perfor-mance of the PowerPAK device under these conditions.A characterization was made comparing a standard SO-8and a PowerPAK device on a board with a trough cut out underneath the PowerPAK drain pad. This configuration restricted the heat flow to the SO-8 land pads. The results are shown in Figure 5.Because of the presence of the trough, this result sug-gests a minimum performance improvement of 10 °C/W by using a PowerPAK SO-8 in a standard SO-8 PC board mount.The only concern when mounting a PowerPAK on a standard SO-8 pad pattern is that there should be no traces running between the body of the MOSFET.Where the standard SO-8 body is spaced away from the pc board, allowing traces to run underneath, the Power-PAK sits directly on the pc board.Thermal Performance - Spreading CopperDesigners may add additional copper, spreading cop-per, to the drain pad to aid in conducting heat from a device. It is helpful to have some information about the thermal performance for a given area of spreading cop-per.Figure 6 shows the thermal resistance of a PowerPAK SO-8 device mounted on a 2-in. 2-in., four-layer FR-4PC board. The two internal layers and the backside layer are solid copper. The internal layers were chosen as solid copper to model the large power and ground planes common in many applications. The top layer was cut back to a smaller area and at each step junction-to-ambient thermal resistance measurements were taken.The results indicate that an area above 0.3 to 0.4 square inches of spreading copper gives no additional thermal performance improvement. A subsequent experiment was run where the copper on the back-side was reduced, first to 50 % in stripes to mimic circuit traces,and then totally removed. No significant effect was observed.TABLE 1.DPAK and PowerPAK SO-8Equivalent Steady State PerformanceDPAKPowerPAKSO-8 Standard SO-8 Thermal Resistance R θjc1.2 °C/W1.0 °C/W16 °C/WFigure 5. PowerPAK SO-8 and Standard SO-0 Land Pad Thermal PathFigure 6. Spreading Copper Junction-to-Ambient PerformanceR th v s. Spreading Copper (0 %, 50 %, 100 % Back Copper))s t t a w /C ( e c n a d e p m I 0.0056514641360.250.500.751.001.251.501.752.000 %50 %100 %分销商库存信息: VISHAYSIR426DP-T1-GE3。
SI2343DS-T1-GE3;中文规格书,Datasheet资料

Vishay SiliconixSi2343DSP-Channel 30-V (D-S) MOSFETFEATURES•Halogen-free According to IEC 61249-2-21Available•TrenchFET ® Power MOSFETAPPLICATIONS•Load Switch •PA SwitchPRODUCT SUMMARYV DS (V)R DS(on) (Ω)I D (A)- 300.053 at V GS = - 10 V - 4.00.086 at V GS = - 4.5 V- 3.1Notes:a. Surface Mounted on 1" x 1" FR4 board.b. Pulse width limited by maximum junction temperature.* Pb containing terminations are not RoHS compliant, exemptions may apply ABSOLUTE MAXIMUM RATINGS T A = 25 °C, unless otherwise notedParameterSymbol 5 s Steady State Unit Drain-Source Voltage V DS - 30VGate-Source VoltageV GS± 20Continuous Drain Current (T J = 150 °C)a, b T A = 25 °C I D - 4.0- 3.1AT A = 70 °C- 3.2- 2.5Pulsed Drain CurrentI DM - 15Continuous Source Current (Diode Conduction)a, b I S- 1.0- 0.6Maximum Power Dissipationa, bT A = 25 °C P D 1.250.75W T A = 70 °C0.80.48Operating Junction and Storage T emperature RangeT J , T stg- 55 to 150°C THERMAL RESISTANCE RATINGSParameter Symbol T ypical Maximum UnitMaximum Junction-to-Ambient a t ≤ 5 s R thJA 75100°C/WSteady State 120166Maximum Junction-to-Foot (Drain)Steady StateR thJF4050Vishay SiliconixSi2343DSNotes:a. Pulse test: PW ≤ 300 µs, duty cycle ≤ 2 %.b. For DESIGN AID ONLY, not subject to production testing.c. Switching time is essentially independent of operating temperature.Stresses beyond those listed under “Absolute Maximum Ratings” may cause permanent damage to the device. These are stress ratings only, and functional operation of the device at these or any other conditions beyond those indicated in the operational sections of the specifications is not implied. Exposure to absolute maximum rating conditions for extended periods may affect device reliability.SPECIFICATIONS T J = 25 °C, unless otherwise notedParameter Symbol T est Conditions LimitsUnitMin.Typ.Max.StaticDrain-Source Breakdown Voltage V (BR)DSS V GS = 0 V , I D = - 250 µA - 30VGate-Threshold Voltage V GS(th) V DS = V GS , I D = - 250 µA - 1- 3Gate-Body LeakageI GSS V DS = 0 V , V GS = ± 20 V ± 100 nAZero Gate Voltage Drain Current I DSS V DS = - 24 V , V GS = 0 V - 1µA V DS = - 24 V, V GS = 0 V , T J = 55 °C- 10On-State Drain Current a I D(on) V DS ≤ - 5 V , V GS = - 10 V - 15A Drain-Source On-Resistance aR DS(on) V GS = - 10 V , I D = - 4.0 A 0.0430.053ΩV GS = - 4.5 V , I D = - 3.1 A 0.0680.086Forward T ransconductance a g fs V DS = - 5 V , I D = - 4.0 A 10S Diode Forward Voltage V SDI S = - 1.0 A, V GS = 0 V- 0.7- 1.2VDynamic bTotal Gate Charge Q g V DS = - 15 V , V GS = - 10 VI D ≅ - 4.0 A1421nCGate-Source Charge Q gs 1.9Gate-Drain Charge Q gd 3.7Input Capacitance C iss V DS = - 15 V, V GS = 0 V , f = 1 MHz540pFOutput CapacitanceC oss 131Reverse Transfer Capacitance C rss105Switching c Turn-On Time t d(on) V DD = - 15 V , R L = 15 ΩI D ≅ - 1.0 A, V GEN = - 10 VR G = 6 Ω1015nst r 1525Turn-Off Timet d(off) 3150t f2030Output CharacteristicsOn-Resistance vs. Drain CurrentGate ChargeCapacitanceOn-Resistance vs. Junction TemperatureSingle Pulse PowerVishay SiliconixSi2343DSTYPICAL CHARACTERISTICS 25°C, unless otherwise notedVishay Siliconix maintains worldwide manufacturing capability. Products may be manufactured at one of several qualified locations. Reliability data for Silicon Technology and Package Reliability represent a composite of all qualified locations. For related documents such as package/tape drawings, part marking, and reliability data, see /ppg?72079.Normalized Thermal Transient Impedance, Junction-to-AmbientVishay SiliconixPackage InformationSOT-23 (TO-236): 3-LEADDimMILLIMETERS INCHESMinMaxMinMaxA 0.89 1.120.0350.044A 10.010.100.00040.004A 20.88 1.020.03460.040b 0.350.500.0140.020c 0.0850.180.0030.007D 2.803.040.1100.120E 2.10 2.640.0830.104E 1 1.201.400.0470.055e 0.95 BSC 0.0374 Ref e 1 1.90 BSC0.0748 RefL 0.400.600.0160.024L 10.64 Ref 0.025 Ref S 0.50 Ref0.020 Refq3°8°3°8°ECN: S-03946-Rev. K, 09-Jul-01DWG: 5479AN807Vishay Siliconix Mounting LITTLE FOOT R SOT-23 Power MOSFETsWharton McDanielSurface-mounted LITTLE FOOT power MOSFET s use integrated circuit and small-signal packages which have been been modified to provide the heat transfer capabilities required by power devices. Leadframe materials and design, molding compounds, and die attach materials have been changed, while the footprint of the packages remains the same.See Application Note 826, Recommended Minimum Pad Patterns With Outline Drawing Access for Vishay Siliconix MOSFET s, (/doc?72286), for the basis of the pad design for a LITTLE FOOT SOT-23 power MOSFET footprint . In converting this footprint to the pad set for a power device, designers must make two connections: an electrical connection and a thermal connection, to draw heat away from the package.The electrical connections for the SOT-23 are very simple. Pin 1 is the gate, pin 2 is the source, and pin 3 is the drain. As in the other LITTLE FOOT packages, the drain pin serves the additional function of providing the thermal connection from the package to the PC board. The total cross section of a copper trace connected to the drain may be adequate to carry the current required for the application, but it may be inadequate thermally. Also, heat spreads in a circular fashion from the heat source. In this case the drain pin is the heat source when looking at heat spread on the PC board.Figure 1 shows the footprint with copper spreading for the SOT-23 package. This pattern shows the starting point for utilizing the board area available for the heat spreading copper. T o create this pattern, a plane of copper overlies the drain pin and provides planar copper to draw heat from the drain lead and start the process of spreading the heat so it can be dissipated into the ambient air. This pattern uses all the available area underneath the body for this purpose.FIGURE 1.Footprint With Copper Spreading0.03941.00.0370.95Since surface-mounted packages are small, and reflow soldering is the most common way in which these are affixed to the PC board, “thermal” connections from the planar copper to the pads have not been used. Even if additional planar copper area is used, there should be no problems in the soldering process. The actual solder connections are defined by the solder mask openings. By combining the basic footprint with the copper plane on the drain pins, the solder mask generation occurs automatically.A final item to keep in mind is the width of the power traces. The absolute minimum power trace width must be determined by the amount of current it has to carry. For thermal reasons, this minimum width should be at least 0.020 inches. The use of wide traces connected to the drain plane provides a low-impedance path for heat to move away from the device.Application Note 826Vishay SiliconixA P P L I C A T I O N N O T RECOMMENDED MINIMUM PADS FOR SOT -23Legal Disclaimer Notice VishayDisclaimerALL PRODU CT, PRODU CT SPECIFICATIONS AND DATA ARE SU BJECT TO CHANGE WITHOU T NOTICE TO IMPROVE RELIABILITY, FUNCTION OR DESIGN OR OTHERWISE.Vishay Intertechnology, Inc., its affiliates, agents, and employees, and all persons acting on its or their behalf (collectively,“Vishay”), disclaim any and all liability for any errors, inaccuracies or incompleteness contained in any datasheet or in any other disclosure relating to any product.Vishay makes no warranty, representation or guarantee regarding the suitability of the products for any particular purpose or the continuing production of any product. To the maximum extent permitted by applicable law, Vishay disclaims (i) any and all liability arising out of the application or use of any product, (ii) any and all liability, including without limitation special, consequential or incidental damages, and (iii) any and all implied warranties, including warranties of fitness for particular purpose, non-infringement and merchantability.Statements regarding the suitability of products for certain types of applications are based on Vishay’s knowledge of typical requirements that are often placed on Vishay products in generic applications. Such statements are not binding statements about the suitability of products for a particular application. It is the customer’s responsibility to validate that a particular product with the properties described in the product specification is suitable for use in a particular application. Parameters provided in datasheets and/or specifications may vary in different applications and performance may vary over time. All operating parameters, including typical parameters, must be validated for each customer application by the customer’s technical experts. Product specifications do not expand or otherwise modify Vishay’s terms and conditions of purchase, including but not limited to the warranty expressed therein.Except as expressly indicated in writing, Vishay products are not designed for use in medical, life-saving, or life-sustaining applications or for any other application in which the failure of the Vishay product could result in personal injury or death. Customers using or selling Vishay products not expressly indicated for use in such applications do so at their own risk and agree to fully indemnify and hold Vishay and its distributors harmless from and against any and all claims, liabilities, expenses and damages arising or resulting in connection with such use or sale, including attorneys fees, even if such claim alleges that Vishay or its distributor was negligent regarding the design or manufacture of the part. Please contact authorized Vishay personnel to obtain written terms and conditions regarding products designed for such applications.No license, express or implied, by estoppel or otherwise, to any intellectual property rights is granted by this document or by any conduct of Vishay. Product names and markings noted herein may be trademarks of their respective owners.Material Category PolicyVishay Intertechnology, Inc. hereb y certifies that all its products that are identified as RoHS-Compliant fulfill the definitions and restrictions defined under Directive 2011/65/EU of The European Parliament and of the Council of June 8, 2011 on the restriction of the use of certain hazardous substances in electrical and electronic equipment (EEE) - recast, unless otherwise specified as non-compliant.Please note that some Vishay documentation may still make reference to RoHS Directive 2002/95/EC. We confirm that all the products identified as being compliant to Directive 2002/95/EC conform to Directive 2011/65/EU.分销商库存信息: VISHAYSI2343DS-T1-GE3。
sage SES878 咖啡机使用说明书.pdf the Barista Pro
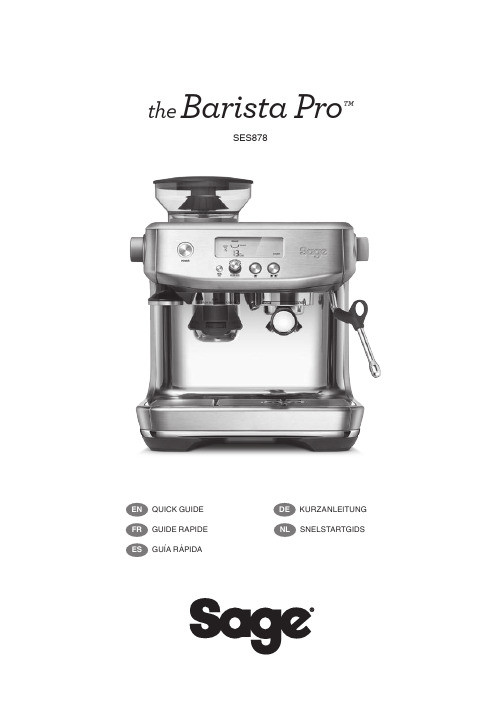
□Contents SAGE®RECOMMENDS SAFETY FIRST At Sage® 我们非常注重安全。
我们在设计和制造电器时会考虑您的安全性。
我们还要求您在使用任何电器时都要格外小心,并遵守以下预防措施。
2使用前请阅读所有说明并保存以备将来参考·上也提供了本文档的可下载版本。
首次使用前,请确保您的电源与设备底部的额定标签上的相同。
如果您有任何疑问,请联系您当地的电力公司。
·建议在安装所有电器时安装剩余电流安全开关,以提高安全性。
建议使用额定工作电流不超过30mA的安全开关。
向电工咨询专业意见。
·首次使用前,请安全地取出并丢弃所有包装材料。
·为了消除年幼儿童窒息的危险,请安全丢弃电源插头上的保护盖。
·确保在首次使用之前正确组装产品。
·本设备仅用于家用。
请勿将本设备用于其预定目的以外的用途。
请勿在移动的车辆或船上使用。
不要在户外使用。
滥用可能会造成伤害。
·将设备放置在远离柜台边缘的稳定,耐热,水平,干燥的表面上,并且请勿在热源(例如热板,烤箱或燃气灶)上或附近操作。
·在操作之前,请完全展开电源线。
·请勿将电源线悬在柜台或桌子的边缘。
请勿让电源线接触灼热的表面或打结。
·使用时请勿将设备无人看管。
·如果要使用该设备:-无人看管-清洁-移动-组装;或-存储始终通过按电源按钮将咖啡机关闭,以将其关闭。
关闭电源,然后从电源插座上拔下电源。
·定期检查电源线,插头和实际设备是否有损坏。
如果发现任何形式的损坏,请立即停止使用该设备,并将整个设备退回最近的授权Sage服务中心进行检查,更换或维修。
·保持设备和配件清洁。
请遵循本书中提供的清洁说明。
本说明手册中未列出的任何程序都应在授权的Sage服务中心进行。
·只有经过安全的监督或指导以指导他们使用本设备,并且年龄在8岁以上的儿童以及肢体,感官或心理能力较弱或缺乏经验和知识的人才能使用本设备。
SQJ964EP-T1-GE3;中文规格书,Datasheet资料
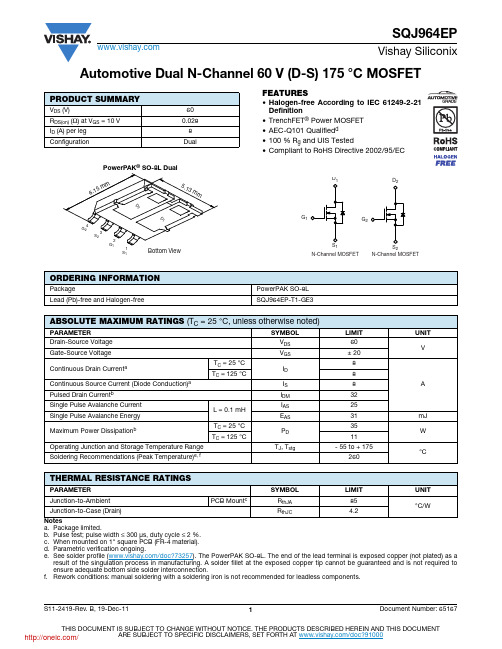
Automotive Dual N-Channel 60 V (D-S) 175 °C MOSFETFEATURES•Halogen-free According to IEC 61249-2-21Definition•TrenchFET ® Power MOSFET •AEC-Q101 Qualified d•100 % R g and UIS Tested•Compliant to RoHS Directive 2002/95/ECNotesa.Package limited.b.Pulse test; pulse width ≤ 300 μs, duty cycle ≤ 2 %.c.When mounted on 1" square PCB (FR-4 material).d.Parametric verification ongoing.e.See solder profile (/doc?73257). The PowerPAK SO-8L. The end of the lead terminal is exposed copper (not plated) as a result of the singulation process in manufacturing. A solder fillet at the exposed copper tip cannot be guaranteed and is not required to ensure adequate bottom side solder interconnection.f.Rework conditions: manual soldering with a soldering iron is not recommended for leadless components.PRODUCT SUMMARYV DS (V)60R DS(on) (Ω) at V GS = 10 V 0.028I D (A) per leg 8ConfigurationDualORDERING INFORMATIONPackagePowerPAK SO-8L Lead (Pb)-free and Halogen-freeSQJ964EP-T1-GE3ABSOLUTE MAXIMUM RATINGS (T C = 25 °C, unless otherwise noted)PARAMETER SYMBOL LIMIT UNIT Drain-Source Voltage V DS60VGate-Source Voltage V GS ± 20Continuous Drain Current aT C = 25 °C I D 8A T C = 125 °C8Continuous Source Current (Diode Conduction)a I S 8Pulsed Drain Current bI DM 32Single Pulse Avalanche Current L = 0.1 mH I AS 25Single Pulse Avalanche Energy E AS 31mJ Maximum Power Dissipation bT C = 25 °C P D 35W T C = 125 °C 11Operating Junction and Storage Temperature Range T J , T stg- 55 to + 175°C Soldering Recommendations (Peak Temperature)e, f260THERMAL RESISTANCE RATINGSARAMETER SYMBOL LIMIT UNIT Junction-to-Ambient PCB Mount cR thJA 85°C/WJunction-to-Case (Drain)R thJC4.2Notesa.Pulse test; pulse width ≤ 300 μs, duty cycle ≤ 2 %.b.Guaranteed by design, not subject to production testing.c.Independent of operating temperature.Stresses beyond those listed under “Absolute Maximum Ratings” may cause permanent damage to the device. These are stress ratings only, and functional operation of the device at these or any other conditions beyond those indicated in the operational sections of the specifications is not implied. Exposure to absolute maximum rating conditions for extended periods may affect device reliability.SPECIFICATIONS (T C = 25 °C, unless otherwise noted)PARAMETER SYMBOLTEST CONDITIONS MIN.TY P .MAX.UNITStaticDrain-Source Breakdown Voltage V DS V GS = 0, I D = - 250 μA 60--V Gate-Source Threshold Voltage V GS(th)V DS = V GS , I D = - 250 μA 3.4 3.8 4.5Gate-Source LeakageI GSS V DS = 0 V, V GS = ± 20 V--± 100nAZero Gate Voltage Drain Current I DSS V GS = 0 V V DS = 60 V --1μA V GS = 0 V V DS = 60 V, T J = 125 °C --50V GS = 0 V V DS = 60 V, T J = 175 °C--150On-State Drain Current aI D(on) V GS = 10 V V DS ≥ 5 V 30--A Drain-Source On-State Resistance a R DS(on) V GS = 10 V I D = 9.6 A -0.0200.028ΩV GS = 10 V I D = 9.6 A, T J = 125 °C -0.0330.046V GS = 10 VI D = 9.6 A, T J = 175 °C-0.0400.055Forward Transconductance b g fsV DS = 15 V, I D = 9.6 A-30-S Dynamic bInput Capacitance C issV GS = 0 V V DS = 30 V, f = 1 MHz -23602900pFOutput CapacitanceC oss -155190Reverse Transfer Capacitance C rss -7390Total Gate Charge c Q gV GS = 10 VV DS = 30 V, I D = 9.6 A -3857nC Gate-Source Charge c Q gs -12.5-Gate-Drain Charge c Q gd -8-Gate Resistance R g f = 1 MHz123ΩTurn-On Delay Time c t d(on)V DD = 20 V, R L = 20 Ω I D ≅ 1 A, V GEN = 10 V, R g = 6.0 Ω-1725ns Rise Time ct r-1116Turn-Off Delay Time c t d(off) -3745Fall Time c t f -1015Source-Drain Diode Ratings and Characteristics bPulsed Current a I SM --32A Forward VoltageV SDI F = 2.9 A, V GS = 0-0.81.1VTYPICAL CHARACTERISTICS(T A = 25 °C, unless otherwise noted)Output Characteristics TransconductanceCapacitanceTransfer CharacteristicsOn-Resistance vs. Drain CurrentGate ChargeTYPICAL CHARACTERISTICS(T A = 25 °C, unless otherwise noted)On-Resistance vs. Junction Temperature On-Resistance vs. Gate-to-Source VoltageSource Drain Diode Forward VoltageDrain-Source Breakdown vs. Junction Temperature Threshold VoltageTHERMAL RATINGS(T A = 25 °C, unless otherwise noted)Safe Operating AreaNormalized Thermal Transient Impedance, Junction-to-AmbientTHERMAL RATINGS(T A = 25 °C, unless otherwise noted)Normalized Thermal Transient Impedance, Junction-to-CaseNote•The characteristics shown in the two graphs- Normalized Transient Thermal Impedance Junction-to-Ambient (25 °C)- Normalized Transient Thermal Impedance Junction-to-Case (25 °C)are given for general guidelines only to enable the user to get a “ball park” indication of part capabilities. The data are extracted from single pulse transient thermal impedance characteristics which are developed from empirical measurements. The latter is valid for the part mounted on printed circuit board - FR4, size 1" x 1" x 0.062", double sided with 2 oz. copper, 100 % on both sides. The part capabilities can widely vary depending on actual application parameters and operating conditions.Vishay Silico nix maintains wo rldwide manufacturing capability. Pro ducts may be manufactured at o ne o f several qualified lo catio ns. Reliability data fo r Silico n Technology and Package Reliability represent a composite of all qualified locations. For related documents such as package/tape drawings, part marking, and reliability data, see /ppg?65167.PowerPAK® SO-8L Case OutlineNote•Millimeters will goverLIMETERSINCHESMIN.NOM.MAX.MIN.NOM.MAX.A 1.00 1.07 1.140.0390.0420.045A10.00-0.1270.00-0.005b 0.330.410.480.0130.0160.019b10.440.510.580.0170.0200.023b2 4.804.905.000.1890.1930.197b30.0940.004b40.470.019c 0.200.250.300.0080.0100.012D 5.00 5.13 5.250.1970.2020.207D1 4.80 4.90 5.000.1890.1930.197D2 3.86 3.96 4.060.1520.1560.160D3 1.63 1.73 1.830.0640.0680.072e 1.27 BSC 0.050 BSC E 6.05 6.15 6.250.2380.2420.246E14.27 4.37 4.470.1680.1720.176E2 (for Al product) 2.75 2.85 2.950.1080.1120.116E2 (for other product)3.18 3.28 3.380.1250.1290.133F --0.15--0.006L 0.620.720.820.0240.0280.032L10.921.07 1.220.0360.0420.048K 0.510.020W 0.230.009W10.410.016W2 2.820.111W3 2.960.1170°-10°0°-10°ECN: C12-0026-Rev. B, 27-Aug-12DWG: 5976Legal Disclaimer Notice VishayDisclaimerALL PRODU CT, PRODU CT SPECIFICATIONS AND DATA ARE SU BJECT TO CHANGE WITHOU T NOTICE TO IMPROVE RELIABILITY, FUNCTION OR DESIGN OR OTHERWISE.Vishay Intertechnology, Inc., its affiliates, agents, and employees, and all persons acting on its or their behalf (collectively,“Vishay”), disclaim any and all liability for any errors, inaccuracies or incompleteness contained in any datasheet or in any other disclosure relating to any product.Vishay makes no warranty, representation or guarantee regarding the suitability of the products for any particular purpose or the continuing production of any product. To the maximum extent permitted by applicable law, Vishay disclaims (i) any and all liability arising out of the application or use of any product, (ii) any and all liability, including without limitation special, consequential or incidental damages, and (iii) any and all implied warranties, including warranties of fitness for particular purpose, non-infringement and merchantability.Statements regarding the suitability of products for certain types of applications are based on Vishay’s knowledge of typical requirements that are often placed on Vishay products in generic applications. Such statements are not binding statements about the suitability of products for a particular application. It is the customer’s responsibility to validate that a particular product with the properties described in the product specification is suitable for use in a particular application. Parameters provided in datasheets and/or specifications may vary in different applications and performance may vary over time. All operating parameters, including typical parameters, must be validated for each customer application by the customer’s technical experts. Product specifications do not expand or otherwise modify Vishay’s terms and conditions of purchase, including but not limited to the warranty expressed therein.Except as expressly indicated in writing, Vishay products are not designed for use in medical, life-saving, or life-sustaining applications or for any other application in which the failure of the Vishay product could result in personal injury or death. Customers using or selling Vishay products not expressly indicated for use in such applications do so at their own risk and agree to fully indemnify and hold Vishay and its distributors harmless from and against any and all claims, liabilities, expenses and damages arising or resulting in connection with such use or sale, including attorneys fees, even if such claim alleges that Vishay or its distributor was negligent regarding the design or manufacture of the part. Please contact authorized Vishay personnel to obtain written terms and conditions regarding products designed for such applications.No license, express or implied, by estoppel or otherwise, to any intellectual property rights is granted by this document or by any conduct of Vishay. Product names and markings noted herein may be trademarks of their respective owners.Material Category PolicyVishay Intertechnology, Inc. hereb y certifies that all its products that are identified as RoHS-Compliant fulfill the definitions and restrictions defined under Directive 2011/65/EU of The European Parliament and of the Council of June 8, 2011 on the restriction of the use of certain hazardous substances in electrical and electronic equipment (EEE) - recast, unless otherwise specified as non-compliant.Please note that some Vishay documentation may still make reference to RoHS Directive 2002/95/EC. We confirm that all the products identified as being compliant to Directive 2002/95/EC conform to Directive 2011/65/EU.分销商库存信息: VISHAYSQJ964EP-T1-GE3。
PT878GC中文说明书
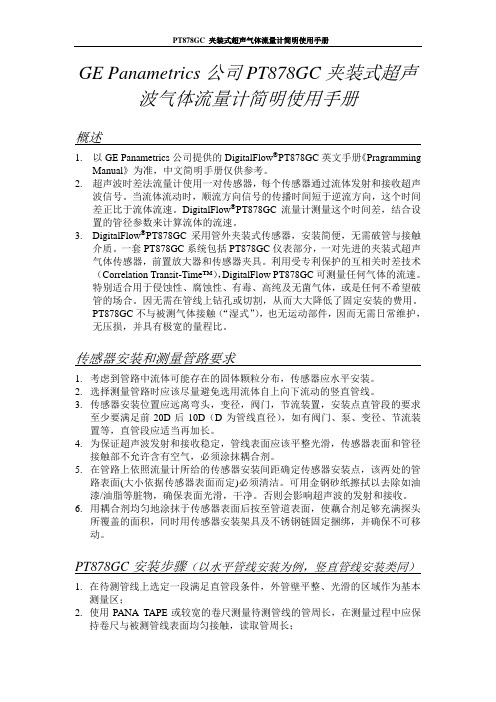
GE Panametrics公司PT878GC夹装式超声波气体流量计简明使用手册概述1.以GE Panametrics公司提供的DigitalFlow®PT878GC英文手册《PragrammingManual》为准,中文简明手册仅供参考。
2.超声波时差法流量计使用一对传感器,每个传感器通过流体发射和接收超声波信号。
当流体流动时,顺流方向信号的传播时间短于逆流方向,这个时间差正比于流体流速。
DigitalFlow®PT878GC流量计测量这个时间差,结合设置的管径参数来计算流体的流速。
3.DigitalFlow®PT878GC采用管外夹装式传感器,安装简便,无需破管与接触介质。
一套PT878GC系统包括PT878GC仪表部分,一对先进的夹装式超声气体传感器,前置放大器和传感器夹具。
利用受专利保护的互相关时差技术(Correlation Transit-Time™),DigitalFlow PT878GC可测量任何气体的流速。
特别适合用于侵蚀性、腐蚀性、有毒、高纯及无菌气体,或是任何不希望破管的场合。
因无需在管线上钻孔或切割,从而大大降低了固定安装的费用。
PT878GC不与被测气体接触(“湿式”),也无运动部件,因而无需日常维护,无压损,并具有极宽的量程比。
传感器安装和测量管路要求1.考虑到管路中流体可能存在的固体颗粒分布,传感器应水平安装。
2.选择测量管路时应该尽量避免选用流体自上向下流动的竖直管线。
3.传感器安装位置应远离弯头,变径,阀门,节流装置,安装点直管段的要求至少要满足前20D后10D(D为管线直径),如有阀门、泵、变径、节流装置等,直管段应适当再加长。
4.为保证超声波发射和接收稳定,管线表面应该平整光滑,传感器表面和管径接触部不允许含有空气,必须涂抹耦合剂。
5.在管路上依照流量计所给的传感器安装间距确定传感器安装点,该两处的管路表面(大小依据传感器表面而定)必须清洁。
- 1、下载文档前请自行甄别文档内容的完整性,平台不提供额外的编辑、内容补充、找答案等附加服务。
- 2、"仅部分预览"的文档,不可在线预览部分如存在完整性等问题,可反馈申请退款(可完整预览的文档不适用该条件!)。
- 3、如文档侵犯您的权益,请联系客服反馈,我们会尽快为您处理(人工客服工作时间:9:00-18:30)。
SiR878DP
Vishay Siliconix
N-Channel 100 V (D-S) MOSFET
PRODUCT SUMMARY
VDS (V) 100 RDS(on) () 0.014 at VGS = 10 V 0.0148 at VGS = 7.5 V 0.019 at VGS = 4.5 V ID (A)a 40 38 34 13.6 nC Qg (Typ.)
Min. 100
Typ.
Max.
Unit V
50 - 5.5 1.2 2.8 ± 100 1 10 30 0.0114 0.012 0.0152 34 0.014 0.0148 0.019
mV/°C V nA µA A S
Input Capacitance Output Capacitance Reverse Transfer Capacitance Total Gate Charge Gate-Source Charge Gate-Drain Charge Gate Resistance Turn-On Delay Time Rise Time Turn-Off Delay Time Fall Time Turn-On Delay Time Rise Time Turn-Off Delay Time Fall Time Drain-Source Body Diode Characteristics Continuous Source-Drain Diode Current Pulse Diode Forward Body Diode Voltage Body Diode Reverse Recovery Time Body Diode Reverse Recovery Charge Reverse Recovery Fall Time Reverse Recovery Rise Time Currenta
Qg Qgs Qgd Rg td(on) tr td(off) tf td(on) tr td(off) tf IS ISM VSD trr Qrr ta tb
A V ns nC ns
Notes: a. Pulse test; pulse width 300 µs, duty cycle 2 %. b. Guaranteed by design, not subject to production testing.
d, e
Symbol VDS VGS ID
Limit 100 ± 20 40 32 13.3b, c 10.6b, c 80 40 4.5b, c 20 20 44.5 28.5 5.0b, c 3.2b, c -Drain Current (TJ = 150 °C)
1250 VDS = 50 V, VGS = 0 V, f = 1 MHz VDS = 50 V, VGS = 10 V, ID = 10 A 680 50 28.3 21.6 13.6 3.7 6.4 f = 1 MHz VDD = 50 V, RL = 5 ID 10 A, VGEN = 10 V, Rg = 1 0.5 2.3 9 11 28 10 12 VDD = 50 V, RL = 5 ID 10 A, VGEN = 7.5 V, Rg = 1 13 27 7 TC = 25 °C IS = 4 A 0.76 45 IF = 10 A, dI/dt = 100 A/µs, TJ = 25 °C 50 21 24 4.6 18 22 55 20 24 26 50 14 40 80 1.1 90 100 ns 43 33 20.5 nC VDS = 50 V, VGS = 7.5 V, ID = 10 A VDS = 50 V, VGS = 4.5 V, ID = 10 A pF
b
Symbol VDS VDS/TJ VGS(th)/TJ VGS(th) IGSS IDSS ID(on) RDS(on) gfs Ciss Coss Crss
Test Conditions VGS = 0 V, ID = 250 µA ID = 250 µA VDS = VGS, ID = 250 µA VDS = 0 V, VGS = ± 20 V VDS = 100 V, VGS = 0 V VDS = 100 V, VGS = 0 V, TJ = 55 °C VDS 5 V, VGS = 10 V VGS = 10 V, ID = 15 A VGS = 7.5 V, ID = 12 A VGS = 4.5 V, ID = 10 A VDS = 10 V, ID = 15 A
80 V GS = 10 V thru 5 V I D - Drain Current (A) 10
64 I D - Drain Current (A)
8
48
V GS = 4 V
6
32
4 T C = 25 °C 2 T C = 125 °C
16 V GS = 3 V 0 0.0
0 0.5 1.0 1.5 2.0 2.5 0 1 2 3
G
Bottom View Ordering Information: SiR878DP-T1-GE3 (Lead (Pb)-free and Halogen-free)
S N-Channel MOSFET
ABSOLUTE MAXIMUM RATINGS (TA = 25 °C, unless otherwise noted)
Pulsed Drain Current Continuous Source-Drain Diode Current Single Pulse Avalanche Current Single Pulse Avalanche Energy
IDM IS IAS EAS PD
A
mJ
Maximum Power Dissipation
W
Operating Junction and Storage Temperature Range Soldering Recommendations (Peak Temperature)
TJ, Tstg
°C
THERMAL RESISTANCE RATINGS
Symbol Typical Maximum Unit RthJA t 10 s 20 25 Maximum Junction-to-Ambientb, f °C/W RthJC Steady State Maximum Junction-to-Case (Drain) 2.1 2.8 Notes: a. Based on TC = 25 °C. b. Surface mounted on 1" x 1" FR4 board. c. t = 10 s. d. See solder profile (/ppg?73257). The PowerPAK SO-8 is a leadless package. The end of the lead terminal is exposed copper (not plated) as a result of the singulation process in manufacturing. A solder fillet at the exposed copper tip cannot be guaranteed and is not required to ensure adequate bottom side solder interconnection. e. Rework conditions: manual soldering with a soldering iron is not recommended for leadless components. f. Maximum under steady state conditions is 70 °C/W. Document Number: 65939 S10-2685-Rev. B, 22-Nov-10 1 Parameter
PowerPAK® SO-8
APPLICATIONS
5.15 mm
6.15 mm
S 1 2 3 S S
• DC/DC Primary Side Switch • Telecom/Server 48 V, Full/Half-Bridge dc-to-dc • Industrial D
G 4
D 8 7 6 5 D D D
FEATURES
• Halogen-free According to IEC 61249-2-21 Definition • TrenchFET® Power MOSFET • 100 % Rg Tested • 100 % UIS Tested • Compliant to RoHS Directive 2002/95/EC
2
Document Number: 65939 S10-2685-Rev. B, 22-Nov-10
/
New Product
SiR878DP
Vishay Siliconix
TYPICAL CHARACTERISTICS (25 °C, unless otherwise noted)
T C = - 55 °C 4 5
V DS - Drain-to-Source Voltage (V)
V GS - Gate-to-Source Voltage (V)
Output Characteristics
0.035 2200
Stresses beyond those listed under “Absolute Maximum Ratings” may cause permanent damage to the device. These are stress ratings only, and functional operation of the device at these or any other conditions beyond those indicated in the operational sections of the specifications is not implied. Exposure to absolute maximum rating conditions for extended periods may affect device reliability.