减薄、划片工艺介绍
晶圆减薄研磨工艺
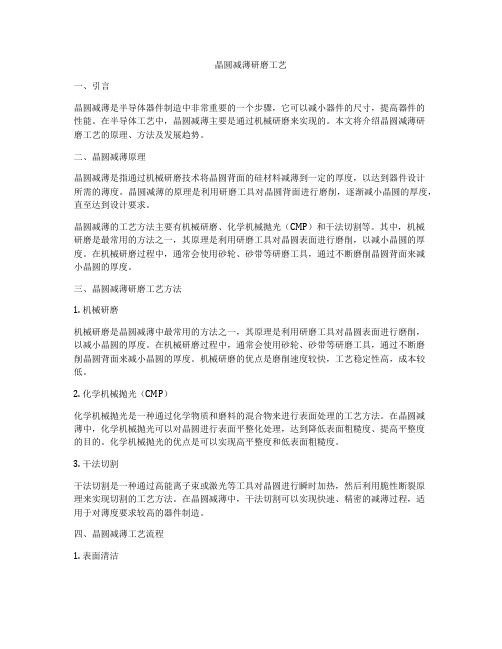
晶圆减薄研磨工艺一、引言晶圆减薄是半导体器件制造中非常重要的一个步骤,它可以减小器件的尺寸,提高器件的性能。
在半导体工艺中,晶圆减薄主要是通过机械研磨来实现的。
本文将介绍晶圆减薄研磨工艺的原理、方法及发展趋势。
二、晶圆减薄原理晶圆减薄是指通过机械研磨技术将晶圆背面的硅材料减薄到一定的厚度,以达到器件设计所需的薄度。
晶圆减薄的原理是利用研磨工具对晶圆背面进行磨削,逐渐减小晶圆的厚度,直至达到设计要求。
晶圆减薄的工艺方法主要有机械研磨、化学机械抛光(CMP)和干法切割等。
其中,机械研磨是最常用的方法之一,其原理是利用研磨工具对晶圆表面进行磨削,以减小晶圆的厚度。
在机械研磨过程中,通常会使用砂轮、砂带等研磨工具,通过不断磨削晶圆背面来减小晶圆的厚度。
三、晶圆减薄研磨工艺方法1. 机械研磨机械研磨是晶圆减薄中最常用的方法之一,其原理是利用研磨工具对晶圆表面进行磨削,以减小晶圆的厚度。
在机械研磨过程中,通常会使用砂轮、砂带等研磨工具,通过不断磨削晶圆背面来减小晶圆的厚度。
机械研磨的优点是磨削速度较快,工艺稳定性高,成本较低。
2. 化学机械抛光(CMP)化学机械抛光是一种通过化学物质和磨料的混合物来进行表面处理的工艺方法。
在晶圆减薄中,化学机械抛光可以对晶圆进行表面平整化处理,达到降低表面粗糙度、提高平整度的目的。
化学机械抛光的优点是可以实现高平整度和低表面粗糙度。
3. 干法切割干法切割是一种通过高能离子束或激光等工具对晶圆进行瞬时加热,然后利用脆性断裂原理来实现切割的工艺方法。
在晶圆减薄中,干法切割可以实现快速、精密的减薄过程,适用于对薄度要求较高的器件制造。
四、晶圆减薄工艺流程1. 表面清洁在进行晶圆减薄之前,首先需要对晶圆表面进行清洁处理,以确保研磨过程中不受到杂质的干扰。
2. 粗磨经过表面清洁处理后,将晶圆放入研磨设备中进行粗磨。
在粗磨过程中,通常会选择适当的研磨工具和磨料,以尽快减小晶圆的厚度。
3. 精磨粗磨完成后,再将晶圆放入研磨设备中进行精磨。
集成电路封装工艺
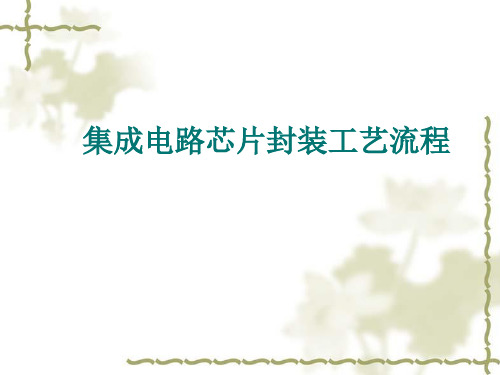
根据材料性能,膜材料分四类 根据材料性能,膜材料分四类:
1.导体膜:主要用于形成电路图形,为电阻电容, 半导体元件和半导体芯片等部件提供电极电学连接 2.电阻膜:形成电路中的电阻, 电阻率:100-2000µΩ.cm 方块阻值:10-1000Ω/□ 3.介质膜:形成电容膜和实现绝缘和表面钝化 4.功能膜:特殊功能膜
打线键合技术
超声波键合: - 振幅20- 超声波键合:20-60kHz,振幅 -200µm超声波 振幅 超声波
铝线和金线是常见材料 优点:温度低,键合尺寸小, 优点:温度低,键合尺寸小,适合键合点间 距小,密度高的芯片连接 距小, 缺点: 缺点:必须沿金属线回绕方向排列
热压键合:预热300- 度 电子点火, 热压键合:预热 -400度,电子点火,
去飞边毛刺
塑料封装中,塑料树脂溢出、贴带毛边,引 线毛刺等统称为飞边毛刺 毛刺的厚度薄于10µm,对后面工序有影响
去飞边毛刺的工艺:介质去飞边毛刺
溶剂去飞边毛刺 水去飞边毛刺
上锡焊
该工序是在框架外引脚上做保护性镀层,以 加可焊性
方法:电镀
浸锡 电镀:清洗-电镀槽电镀-冲洗-吹干-烘干 浸锡:清洗-浸助焊剂-热浸焊-清洗-烘干
丝网印刷 基板清洗 丝网印刷:丝网孔板制备 干燥 烧成
刮板
浆料
玻璃胶贴装法:玻璃胶是低成本芯片粘贴材料 玻璃胶贴装法:
冷却降温注意速度 优点:无空隙,热稳定好, 优点:无空隙,热稳定好,低结合应力 缺点: 缺点:胶中有机成分和溶剂要去除 多用于陶瓷封装, 多用于陶瓷封装,玻璃胶在特殊处理的铜合金 引脚架上才能键合
芯片互连
芯片互连:将芯片焊区与电子封装外壳的 芯片互连:将芯片焊区与电子封装外壳的I/O 引线或基板上的金属布线区相连 常见的方法:打线键合WB(Wire Bonding) 常见的方法:打线键合 载带自动键合TAB(Tape Automated Bonding) 载带自动键合 倒装芯片键合FCB(Flip Chip Bonding) C4 倒装芯片键合 WB:4<n<257 n为I/O数 TAB:10<n<600 FCB:5<n<16000
(完整版)减薄、划片工艺介绍
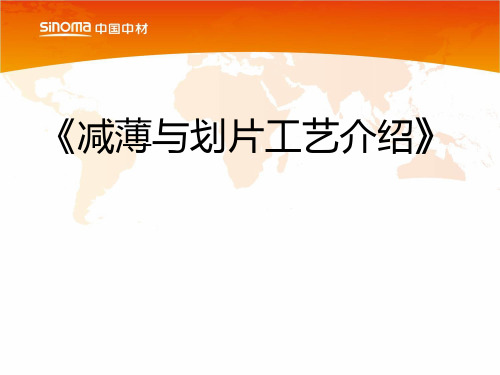
扩张
• 步骤:
• 扩张前准备
开机,打开电源,查看引伸盘控温器上的温 度显示值是否为40℃± 5℃,异常红灯会亮。
划片 贴片 切割 裂片 倒膜 扩张
放扩张环 ,打开压盖,将扩张环的内环 放入底盘中,注意光滑面朝上,将扩张环的 外环放入压环盘中,注意光滑面朝下。
划片 贴片 切割 裂片 倒膜 扩张
430μm
80μm
上蜡
减薄
• 定义:
将芯片固定在陶瓷盘上便于减薄的过程 。
上蜡 研磨 抛光
卸片
清洗
上蜡
减薄
• 步骤:
• 清洁陶瓷盘
上蜡贴片前,首先需要保证陶瓷盘的 洁净程度,LED芯片减薄是属于微米量 级的操作,任何细微的杂质都可能导 致意想不到的异常状况。
上蜡 研磨 抛光 卸片
清洗
上蜡
• 步骤:
上蜡 研磨 抛光 卸片
清洗
研磨
• 步骤:
• 镶盘 将锡盘上均匀布满钻石液的过程。
减薄 上蜡 研磨 抛光 卸片 清洗
抛光
减薄
• 步骤:
• 抛光
通过抛光液中的钻石颗粒,缓慢减薄 芯片。
上蜡 研磨 抛光
卸片
清洗
卸片
减薄
• 定义:
将减薄后的芯片从陶瓷盘上卸下来的过 程。
上蜡 研磨 抛光
卸片
清洗
卸片
减薄
• 步骤:
• 浸泡
将抛光后的陶瓷盘放入去蜡锅中,加 热浸泡5min左右,使芯片从陶瓷上剥 离。
上蜡 研磨 抛光 卸片
清洗
卸片
减薄
• 步骤:
• 夹取
用平口镊小心将减薄后的芯片夹只提 篮中以便于清洗。由于芯片很薄夹取 过程中需非常小心。
封装工艺流程(1)

焊区与微电子封装的I/O引线或基板上的金属
布线焊区(Pad)用金属细丝连接起来的工
艺技术。
WB技术作用机理
❖
提供能量破坏被焊表面的氧化层和污染物,
使焊区金属产生塑性变形,使得引线与被焊
面紧密接触,达到原子间引力范围并导致界
面间原子扩散而形成焊合点。引线键合键合
❖ 铜:近年来,大量用于集成电路互连。铜比
铝有较高的导电率;铜丝相对于金丝具有成
本低、强度和刚度高、适合于细间距键合的
优点。
❖
引线键合的关键工艺
❖
❖
关键工艺:温度控制、精确定位控制、工作
参数设定。
应用对象:低密度连线封装(<300个接点)
引线键合的技术缺陷
1.
2.
3.
多根引线并联产生邻近效应,导致电流分布
对芯片的影响,同时还可以屏蔽电磁干扰。
③各向异性导电聚合物:电流只能在一个方向流动。
❖ 导电胶功能:(形成化学结合、具有导电功能)
❖
2.3.4 玻璃胶粘贴法
与导电胶类似,玻璃胶也属于厚膜导体材料(后面
我们将介绍)。不过起粘接作用的是低温玻璃粉。它
是起导电作用的金属粉(Ag、Ag-Pd、Au、Cu等)
出现废品。
Chipping Die
崩边
2.3 芯片粘贴
芯片贴装:也称芯片粘贴,是将芯片固定
于封装基板或引脚架芯片的承载座上的工
艺过程。
贴装方式4种:
❖ 共晶粘贴法(Au-Si合金)
❖ 焊接粘贴法(Pb-Sn合金焊接)
❖ 环氧树脂粘结(重点)
❖ 玻璃胶粘贴法
引线框架
装
架
引线
芯片减划工艺 中电智能卡
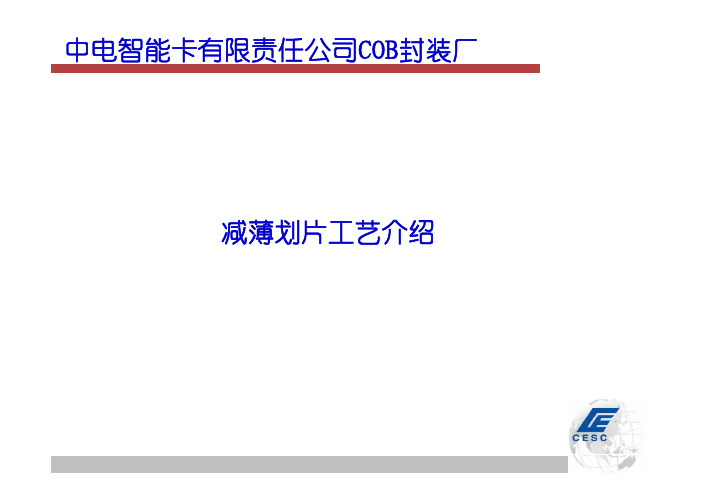
中电智能卡有限责任公司COB封装厂减薄划片工艺介绍减薄划片工艺介绍—生产流程减薄划片工艺介绍背面减薄 贴磨片膜 抛光 贴划片膜 揭磨片膜 划片团队协作,共创辉煌!减薄划片工艺介绍—贴磨片膜Chuck table CCD Alignme ntRobotDouble load portWork flow:Wafer load Wafer alignmentBG tape laminatingW f unload Wafer l d团队协作,共创辉煌!减薄划片工艺介绍—贴磨片膜Machine specification: 1.Wafer size 8 inch O.F., 8 inch V-notch, 12 inch wafer thickness ≧300μm;V-notchO.F.团队协作,共创辉煌!减薄划片工艺介绍—贴磨片膜2.Load port 8 inch wafer: wafer cassette, FOSB 12 inch wafer: FOUP, FOSBWafer cassetteFOUP团队协作,共创辉煌!减薄划片工艺介绍—贴磨片膜3. 磨片膜型号 Tape Type: UV tape, blue tape, bump tape; Tape Width:230~340mm; Tape Thickness:100~300 μm;团队协作,共创辉煌!减薄划片工艺介绍—背面减薄和贴划片膜Machine model: DGP8761+DFM2800 DFM2800 DGP8761 3 主轴,4磨片平台团队协作,共创辉煌!减薄划片工艺介绍—背面减薄和贴划片膜生产流程:1) ) Cassette 2) Transfer with robot pick 3) Alignment at the position table 4) To C/T with transfer arm 1 5) Rough grinding with Z1‐axis 6) Fine grinding with Z2‐axis 7) Dry ry polish with Z3 3‐axis 8) Wafer cleaning at C/T 9) To Spinner with transfer arm 2 10) Wafer cleaning / dry at spinner section 11) To DFM2800 UV irradiation 12)Transfer to the mounting table 13) Dicing tape mounting using ring 14) Transfer to the peeling table 15) Back grinding tape peeling 16) Load wafer to the frame cassette团队协作,共创辉煌!减薄划片工艺介绍—背面减薄和贴划片膜1. Z1/Z2 Spindle: Diamond wheel, Φ300mm; Z3 Spindle: Dry polishing wheel,为海绵,Φ450mm; 同时选配 G tti DP Getting DP, 可以有效防止memory wafer f 的电迁移效应; 的电迁移效应2. Damage of back side#2000 Dry yp polishTEM (x 106)团队协作,共创辉煌!减薄划片工艺介绍—背面减薄和贴划片膜Wafer厚度控制1. Z1 axis配置1套Inline process gauge Z1 axis i 配置2个Inline li process gauge, 厚度检测范围为0~1800um;Z1轴磨片速度分为 3段, 速度范围:0.1um/s~80um/s。
芯片封装设备有哪些 芯片封装工艺流程
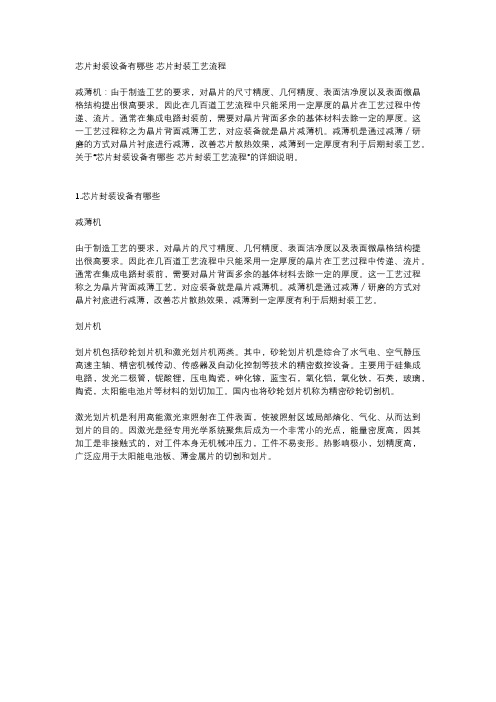
芯片封装设备有哪些芯片封装工艺流程减薄机:由于制造工艺的要求,对晶片的尺寸精度、几何精度、表面洁净度以及表面微晶格结构提出很高要求。
因此在几百道工艺流程中只能采用一定厚度的晶片在工艺过程中传递、流片。
通常在集成电路封装前,需要对晶片背面多余的基体材料去除一定的厚度。
这一工艺过程称之为晶片背面减薄工艺,对应装备就是晶片减薄机。
减薄机是通过减薄/研磨的方式对晶片衬底进行减薄,改善芯片散热效果,减薄到一定厚度有利于后期封装工艺。
关于“芯片封装设备有哪些芯片封装工艺流程”的详细说明。
1.芯片封装设备有哪些减薄机由于制造工艺的要求,对晶片的尺寸精度、几何精度、表面洁净度以及表面微晶格结构提出很高要求。
因此在几百道工艺流程中只能采用一定厚度的晶片在工艺过程中传递、流片。
通常在集成电路封装前,需要对晶片背面多余的基体材料去除一定的厚度。
这一工艺过程称之为晶片背面减薄工艺,对应装备就是晶片减薄机。
减薄机是通过减薄/研磨的方式对晶片衬底进行减薄,改善芯片散热效果,减薄到一定厚度有利于后期封装工艺。
划片机划片机包括砂轮划片机和激光划片机两类。
其中,砂轮划片机是综合了水气电、空气静压高速主轴、精密机械传动、传感器及自动化控制等技术的精密数控设备。
主要用于硅集成电路,发光二极管,铌酸锂,压电陶瓷,砷化镓,蓝宝石,氧化铝,氧化铁,石英,玻璃,陶瓷,太阳能电池片等材料的划切加工。
国内也将砂轮划片机称为精密砂轮切割机。
激光划片机是利用高能激光束照射在工件表面,使被照射区域局部熔化、气化、从而达到划片的目的。
因激光是经专用光学系统聚焦后成为一个非常小的光点,能量密度高,因其加工是非接触式的,对工件本身无机械冲压力,工件不易变形。
热影响极小,划精度高,广泛应用于太阳能电池板、薄金属片的切割和划片。
2.芯片封装工艺流程1、封装工艺流程一般可以分为两个部分,用塑料封装之前的工艺步骤成为前段操作,在成型之后的工艺步骤成为后段操作2、芯片封装技术的基本工艺流程硅片减薄硅片切割芯片贴装,芯片互联成型技术去飞边毛刺切筋成型上焊锡打码等工序3、硅片的背面减薄技术主要有磨削,研磨,化学机械抛光,干式抛光,电化学腐蚀,湿法腐蚀,等离子增强化学腐蚀,常压等离子腐蚀等4、先划片后减薄:在背面磨削之前将硅片正面切割出一定深度的切口,然后再进行背面磨削。
SIP封装的制程工艺
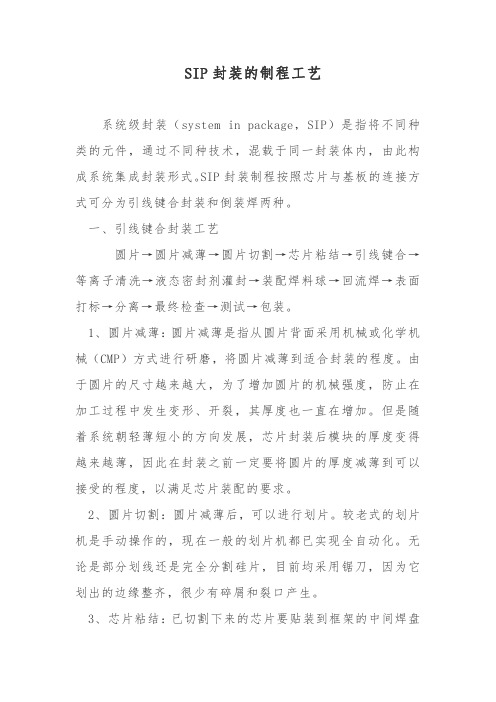
SIP封装的制程工艺系统级封装(system in package,SIP)是指将不同种类的元件,通过不同种技术,混载于同一封装体内,由此构成系统集成封装形式。
SIP封装制程按照芯片与基板的连接方式可分为引线键合封装和倒装焊两种。
一、引线键合封装工艺圆片→圆片减薄→圆片切割→芯片粘结→引线键合→等离子清洗→液态密封剂灌封→装配焊料球→回流焊→表面打标→分离→最终检查→测试→包装。
1、圆片减薄:圆片减薄是指从圆片背面采用机械或化学机械(CMP)方式进行研磨,将圆片减薄到适合封装的程度。
由于圆片的尺寸越来越大,为了增加圆片的机械强度,防止在加工过程中发生变形、开裂,其厚度也一直在增加。
但是随着系统朝轻薄短小的方向发展,芯片封装后模块的厚度变得越来越薄,因此在封装之前一定要将圆片的厚度减薄到可以接受的程度,以满足芯片装配的要求。
2、圆片切割:圆片减薄后,可以进行划片。
较老式的划片机是手动操作的,现在一般的划片机都已实现全自动化。
无论是部分划线还是完全分割硅片,目前均采用锯刀,因为它划出的边缘整齐,很少有碎屑和裂口产生。
3、芯片粘结:已切割下来的芯片要贴装到框架的中间焊盘上。
焊盘的尺寸要和芯片大小相匹配,若焊盘尺寸太大,则会导致引线跨度太大,在转移成型过程中会由于流动产生的应力而造成引线弯曲及芯片位移现象。
贴装的方式可以是用软焊料(指Pb-Sn合金,尤其是含Sn的合金)、Au-Si低共熔合金等焊接到基板上,在塑料封装中最常用的方法是使用聚合物粘结剂粘贴到金属框架上。
4、引线键合:在塑料封装中使用的引线主要是金线,其直径一般为0.025mm~0.032mm。
引线的长度常在1.5mm~3mm之间,而弧圈的高度可比芯片所在平面高0.75mm。
键合技术有热压焊、热超声焊等。
这些技术优点是容易形成球形(即焊球技术),并防止金线氧化。
为了降低成本,也在研究用其他金属丝,如铝、铜、银、钯等来替代金丝键合。
热压焊的条件是两种金属表面紧紧接触,控制时间、温度、压力,使得两种金属发生连接。
晶圆减薄工艺

晶圆减薄工艺概述晶圆减薄工艺是集成电路制造流程中的一个重要环节。
通过减薄晶圆,可以降低芯片厚度,提高芯片的性能和可靠性。
本文将详细介绍晶圆减薄工艺的原理、步骤和应用。
原理晶圆减薄工艺的原理是通过机械或化学方法将晶圆的厚度减薄至目标值。
常用的减薄方法包括机械研磨、化学机械研磨和激光磨削。
机械研磨机械研磨是最早应用的晶圆减薄方法之一。
它通过在研磨盘上使用研磨液和研磨颗粒对晶圆进行研磨,从而减小晶圆的厚度。
机械研磨的优点是工艺简单、成本低,但是容易引入研磨损伤和晶圆表面不平整问题。
化学机械研磨化学机械研磨是一种结合了化学腐蚀和机械研磨的方法。
它通过在研磨液中加入化学溶液和研磨颗粒,同时进行机械研磨和化学腐蚀,从而实现高效的晶圆减薄。
化学机械研磨可以减小研磨损伤和晶圆表面不平整问题,但是其研磨液的配方和工艺参数需要进行精确控制。
激光磨削激光磨削是一种非接触的减薄方法,它利用激光束的加热和蒸发作用,将晶圆表面的材料蒸发掉,从而减小晶圆的厚度。
激光磨削具有减小研磨损伤和晶圆表面不平整问题的优点,但是需要精确控制激光参数和扫描路径。
步骤晶圆减薄工艺通常包括以下步骤:去背面设备准备在晶圆减薄前,需要对去背面设备进行准备工作。
这包括校准设备、清理器具、检查设备状态等。
粗磨粗磨是晶圆减薄的第一步,旨在快速减小晶圆的厚度。
通常使用机械研磨方法进行粗磨,选择合适的研磨颗粒和磨剂,控制研磨力和速度,使晶圆表面平整度达到要求。
中磨中磨是对粗磨后的晶圆进行进一步的减薄和平整处理。
常用的方法是化学机械研磨,通过调整化学研磨液的配方和工艺参数,控制研磨颗粒和化学反应,使晶圆表面更为平整。
精磨精磨是对中磨后的晶圆进行最后的减薄和平整处理。
常用的方法包括化学机械研磨和激光磨削。
通过精确调整研磨液的配方和工艺参数,控制研磨颗粒和化学反应的微观作用,使晶圆获得所需的薄度和表面光洁度。
清洗和检测减薄后的晶圆需要进行清洗和检测工作,以去除研磨残留物和检查减薄效果。
减薄,划片工艺处理介绍
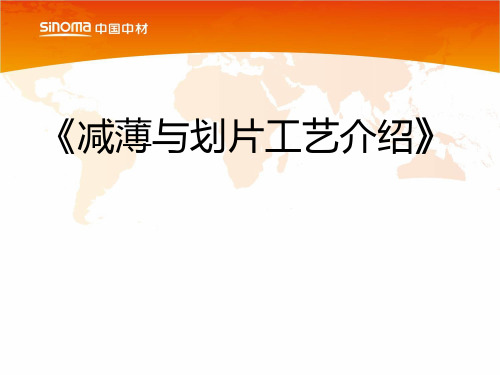
划片
在芯片正面(激光划芯片背面), 贴片
沿着激光划片的痕迹使用裂片机将 切割 管芯完全分离开。
裂片
倒膜
扩张
倒膜
• 定义:
将完全分离的管芯由正面贴膜翻转 成背面贴膜。
划片 贴片 切割 裂片 倒膜 扩张
倒膜
• 步骤:
• 去杂质 将切割与劈裂过程中产生的一些碎屑
杂质粘掉。
划片 贴片 切割 裂片 倒膜 扩张
• 步骤:
• 浸泡
将抛光后的陶瓷盘放入去蜡锅中,加 热浸泡5min左右,使芯片从陶瓷上剥 离。
上蜡 研磨 抛光 卸片
清洗
卸片
减薄
• 步骤:
• 夹取
用平口镊小心将减薄后的芯片夹只提 篮中以便于清洗。由于芯片很薄夹取 过程中需非常小心。
上蜡 研磨 抛光 卸片
清洗
清洗
• 定义:
使用一定的化学试剂通过水浴浸泡, QDR冲洗的方式将芯片上蘸有的残蜡 清洗干净。
贴片
• 步骤:
• 贴片 放铁环,需注意对准卡栓,用平口
镊子夹取芯片,放片时芯片正面朝上 ,使用白膜粘住芯片。
划片 贴片 切割 裂片 倒膜 扩张
切割
划片
使用激光在芯片背面,沿切割道划片 贴片
。不同尺寸芯片,划片深度不一, 切割 深度区间为25至40μm之间。
注意:并未将芯片划穿。
裂片
倒膜
扩张
裂片
上蜡 研磨 抛光 卸片
清洗
研磨
• 步骤:
• 镶盘 将锡盘上均匀布满钻石液的过程。
减薄 上蜡 研磨 抛光 卸片 清洗
抛光
减薄
• 步骤:
• 抛光
通过抛光液中的钻石颗粒,缓慢减薄 芯片。
晶圆划片工艺简介

晶圆划片工艺简介划片工艺流程晶圆经过前道工序后芯片制备完成,还需要经过切割使晶圆上的芯片分离下来,最后进行封装。
不同厚度晶圆选择的晶圆切割工艺也不同:厚度100um以上的晶圆一般使用刀片切割;厚度不到100um的晶圆一般使用激光切割,激光切割可以减少剥落和裂纹的问题,但是在100um以上时,生产效率将大大降低;厚度不到30um的晶圆则使用等离子切割,等离子切割速度快,不会对晶圆表面造成损伤,从而提高良率,但是其工艺过程更为复杂;刀片切割(Blade dicing or blade sawing)刀片切割(锯切)过程中,保护膜的附着与摘除(图片来自网络)为了保护晶圆在切割过程中免受外部损伤,事先会在晶圆上贴敷胶膜,以便保证更安全的“切单”。
“背面减薄(Back Grinding)”过程中,胶膜会贴在晶圆的正面。
但与此相反,在“刀片”切割中,胶膜要贴在晶圆的背面。
而在共晶贴片(Die Bonding,把分离的芯片固定在PCB或定架上)过程中,贴会背面的这一胶膜会自动脱落。
切割时由于摩擦很大,所以要从各个方向连续喷洒DI水(去离子水)。
而且,叶轮要附有金刚石颗粒,这样才可以更好地切片。
此时,切口(刀片厚度:凹槽的宽度)必须均匀,不得超过划片槽的宽度。
很长一段时间,锯切一直是被最广泛使用的传统的切割方法,其最大的优点就是可以在短时间内切割大量的晶圆。
然而,如果切片的进给速度(Feeding Speed)大幅提高,小芯片边缘剥落的可能性就会变大。
因此,应将叶轮的旋转次数控制在每分钟30000次左右。
晶圆划片机晶圆切割时,经常遇到较窄迹道(street)宽度,要求将每一次切割放在迹道中心几微米范围内的能力。
这就要求使用具有高分度轴精度、高光学放大和先进对准运算的设备。
当用窄迹道切割晶圆时,应选择尽可能最薄的刀片。
可是,很薄的刀片(20µm)是非常脆弱的,更容易过早破裂和磨损。
结果,其寿命期望和工艺稳定性都比较厚的刀片差。
芯片减薄划切过程中的UV膜与蓝膜特性简介

芯片减薄划切过程中的UV膜与蓝膜特性简介Wafer在减薄之前,会在Wafer的正面贴一层粘性膜,该层膜的作用是在Wafer正面固定芯片,便于磨片机在Wafer的背面研磨硅片。
一般研磨之前硅片的厚度在700 μm左右,研磨之后,Wafer的厚度变为200 μm,甚至达到120 μm的程度,具体将视客户要求和芯片的应用环境情况而定,即Wafer减薄过程。
Wafer在划片之前,会将Wafer的背面粘一层膜,该层膜的作用是将芯片粘在膜上,可以保持晶粒在切割过程中的完整,减少切割过程中所产生的崩碎,确保晶粒在正常传送过程中不会有位移和掉落的情况,即芯片后封测环节中的划切过程。
如上所述,芯片减薄划切过程中都用到了一种用于固定Wafer和固定芯片作用的膜。
实际生产过程中,该种膜一般使用UV膜或蓝膜。
UV膜和蓝膜在芯片减薄划切过程中具有非常重要的作用,但两者特性有明显的区别。
2 UV膜和蓝膜的特性UV膜和蓝膜均具有粘性,其粘性程度使用粘性剥离度来表示,通常单位使用N/20 mm或者N/25 mm,例如1 N/20 mm的意义是测试条宽度为20 mm,用180°的剥离角度从测试版上将其剥离的力是1 N。
UV膜是将特殊配方的涂料涂布于PET薄膜基材表面,达到阻隔紫外光及短波长可见光的效果,图1所示为通用的UV膜结构图。
一般UV膜由3层构成,其基层材质为聚乙烯氯化物,粘性层在中间,与粘性层相邻的为覆层(Release film),部分UV膜型号没有该覆层。
UV膜通常叫紫外线照射胶带,价格相对较高,未使用时有效期较短,它分为高粘性、中粘性和低粘性三种,对于高粘性的UV膜而言,其未经过紫外线照射时粘性很大,粘性剥离度大约在5 000 m N/20 m m 到12 000 mN/20 mm左右,但是在紫外线灯光照射的时间延长和照射强度增加之后,剥离粘性度会降到1 000 mN/20 mm以下;对于低粘性的UV膜而言,未经过UV照射时,其剥离粘性度在1 000 mN/20 mm左右,而经过紫外线照射之后,其剥离粘性度会降到 100 mN/20 mm 左右;中粘性的UV膜的粘性剥离度介于高粘性UV膜和低粘性UV膜之间。
半导体减薄工艺

半导体减薄工艺1. 引言半导体减薄工艺是半导体制造过程中的关键步骤之一。
通过减薄,可以实现半导体器件的轻薄化,从而提高器件的性能和可靠性。
本文将深入探讨半导体减薄工艺的原理、方法以及在半导体制造中的应用。
2. 半导体减薄的原理半导体减薄的原理是通过去除半导体片的衬底或衬底一部分来减少器件的厚度。
通常使用机械研磨或化学机械抛光(CMP)工艺来实现减薄。
机械研磨是通过机械研磨机对半导体片进行研磨,而CMP工艺则是在研磨过程中加入一定的化学药液,以提高研磨效果。
3. 半导体减薄的方法在半导体减薄工艺中,常用的方法有机械研磨和化学机械抛光。
具体方法如下:3.1 机械研磨机械研磨是最早被使用的半导体减薄方法之一。
它通过使用研磨机械对半导体片进行研磨,逐渐去除衬底或衬底一部分,以达到减薄的目的。
机械研磨的优点是成本低,但存在一定的缺陷,如研磨过程中可能引入机械损伤,需要进一步的处理来修复。
3.2 化学机械抛光化学机械抛光(CMP)是一种同时结合了化学和机械作用的减薄方法。
它通过在研磨过程中加入化学药液,使半导体片表面发生化学反应,并结合研磨机械的作用进行减薄。
相比机械研磨,CMP具有更好的成品率和减薄均匀性,但也存在药液选择、处理工艺复杂等问题。
4. 半导体减薄的应用半导体减薄在半导体制造中有广泛的应用,下面以几个常见的应用为例进行介绍。
4.1 光电子器件在光电子器件制造中,半导体减薄工艺常用于减小器件的厚度,提高器件的光电转换效率。
例如,在太阳能电池制造中,通过减薄可以减少光在器件中的传播路径,提高光电转换效率。
4.2 封装工艺半导体减薄工艺在封装工艺中也发挥着重要的作用。
在芯片封装过程中,需要将芯片切割成一定的尺寸,然后将其封装在封装材料中。
半导体减薄可以使芯片达到所需的薄度,以便更好地适应封装工艺。
4.3 三维封装随着三维封装技术的发展,半导体减薄工艺也在其中发挥着关键作用。
三维封装中,多层芯片需要通过减薄来达到所需的整体厚度,并使各层芯片之间实现可靠的连接。
研磨 划片工艺技术

刀片冷却水的重要性
❖ 0.9~1.5 l/min的重 要性(为什 么修改原来 >1的标准
❖ 刀刃的晃动 是chipping 加剧的根源
划片质量的要点
❖ 贴片 贴片台异物、凸起造成芯片划伤 芯片划伤(KFJ/219 )投诉 ❖ 烘热 长时间烘热增加圆片与type的黏合力,影响DB ❖ 校正 细化操作方法的规则(划偏……)
减薄工艺参数的差别
❖ 起始高度(type+wafer+空切量) 碎片
❖ 空切量(50um)
碎边
❖ 粗磨速度1/2(5~8um/sec)
裂片
❖ 精磨起始高度(粗磨结束高度)
❖ 精磨空切量(10~20)
烧片
❖ 精磨速度1/2(0.8~0.2) TTV粗糙度
❖ 结束高度(type+spec) THICKNESS
划片设备的差异
❖ BBD功能的正确使用 防止刀片破损造成擦伤 ❖ OPT功能的合理使用 科学控制切割留深减少背面缺损和残留的方法 背面缺损的顾客投诉 ❖ Step切割方式的区别 全面采用面step切割的好处 SDIP32芯片裂纹测试投诉 ❖ 自动切割程序管理 减少人为修改对划片造成的可变因素
切割水的正确方向
b. SDIP32芯片裂纹圆片厚度280um切割过程中应力释放不均 导致裂纹280um的产品采用AS切割模式
c.芯片划伤(KFJ/219)贴片台异物造成芯片划伤
d.制造异常DAD3350划偏设备异常改善设备排风和Y轴部件更 换 软件预防措施不足升版升版软件、改进校正方法、增加 图像检查
e.芯片粘污、变色压焊块切割后腐蚀采用清洁剂划片 清洁剂 粘污清理设备管道,清楚清洁剂的残留物
❖ 抛光时间(90sec) 背面粗糙度和TTV
芯片减划工艺 中电智能卡
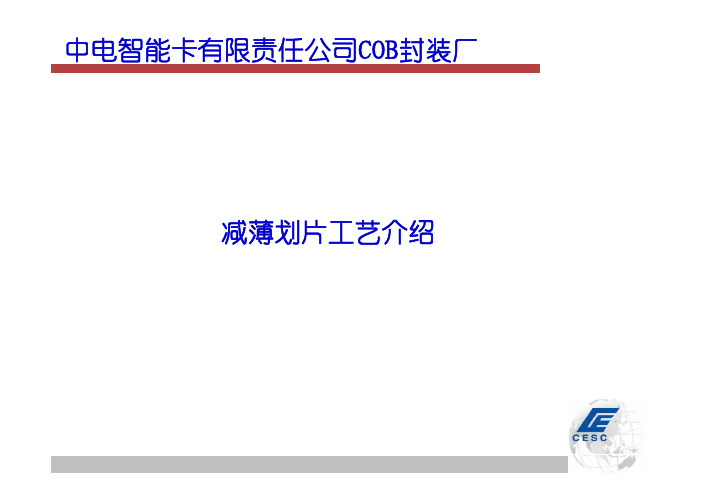
中电智能卡有限责任公司COB封装厂减薄划片工艺介绍减薄划片工艺介绍—生产流程减薄划片工艺介绍背面减薄 贴磨片膜 抛光 贴划片膜 揭磨片膜 划片团队协作,共创辉煌!减薄划片工艺介绍—贴磨片膜Chuck table CCD Alignme ntRobotDouble load portWork flow:Wafer load Wafer alignmentBG tape laminatingW f unload Wafer l d团队协作,共创辉煌!减薄划片工艺介绍—贴磨片膜Machine specification: 1.Wafer size 8 inch O.F., 8 inch V-notch, 12 inch wafer thickness ≧300μm;V-notchO.F.团队协作,共创辉煌!减薄划片工艺介绍—贴磨片膜2.Load port 8 inch wafer: wafer cassette, FOSB 12 inch wafer: FOUP, FOSBWafer cassetteFOUP团队协作,共创辉煌!减薄划片工艺介绍—贴磨片膜3. 磨片膜型号 Tape Type: UV tape, blue tape, bump tape; Tape Width:230~340mm; Tape Thickness:100~300 μm;团队协作,共创辉煌!减薄划片工艺介绍—背面减薄和贴划片膜Machine model: DGP8761+DFM2800 DFM2800 DGP8761 3 主轴,4磨片平台团队协作,共创辉煌!减薄划片工艺介绍—背面减薄和贴划片膜生产流程:1) ) Cassette 2) Transfer with robot pick 3) Alignment at the position table 4) To C/T with transfer arm 1 5) Rough grinding with Z1‐axis 6) Fine grinding with Z2‐axis 7) Dry ry polish with Z3 3‐axis 8) Wafer cleaning at C/T 9) To Spinner with transfer arm 2 10) Wafer cleaning / dry at spinner section 11) To DFM2800 UV irradiation 12)Transfer to the mounting table 13) Dicing tape mounting using ring 14) Transfer to the peeling table 15) Back grinding tape peeling 16) Load wafer to the frame cassette团队协作,共创辉煌!减薄划片工艺介绍—背面减薄和贴划片膜1. Z1/Z2 Spindle: Diamond wheel, Φ300mm; Z3 Spindle: Dry polishing wheel,为海绵,Φ450mm; 同时选配 G tti DP Getting DP, 可以有效防止memory wafer f 的电迁移效应; 的电迁移效应2. Damage of back side#2000 Dry yp polishTEM (x 106)团队协作,共创辉煌!减薄划片工艺介绍—背面减薄和贴划片膜Wafer厚度控制1. Z1 axis配置1套Inline process gauge Z1 axis i 配置2个Inline li process gauge, 厚度检测范围为0~1800um;Z1轴磨片速度分为 3段, 速度范围:0.1um/s~80um/s。
晶圆划片工艺分析
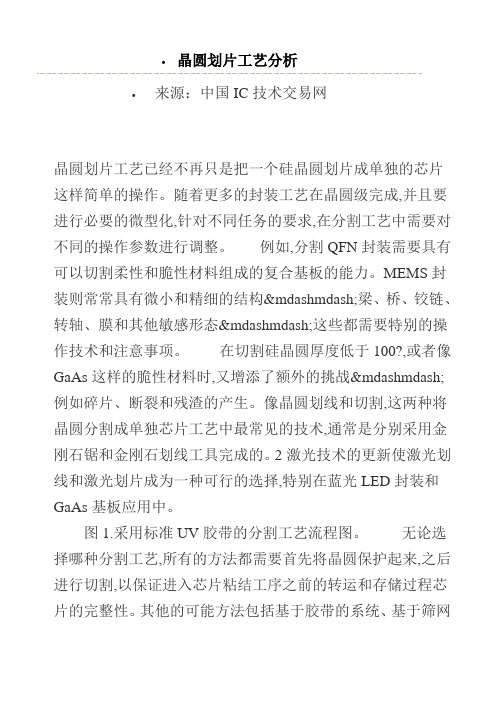
•晶圆划片工艺分析•来源:中国IC技术交易网晶圆划片工艺已经不再只是把一个硅晶圆划片成单独的芯片这样简单的操作。
随着更多的封装工艺在晶圆级完成,并且要进行必要的微型化,针对不同任务的要求,在分割工艺中需要对不同的操作参数进行调整。
例如,分割QFN封装需要具有可以切割柔性和脆性材料组成的复合基板的能力。
MEMS封装则常常具有微小和精细的结构&mdashmdash;梁、桥、铰链、转轴、膜和其他敏感形态&mdashmdash;这些都需要特别的操作技术和注意事项。
在切割硅晶圆厚度低于100?,或者像GaAs这样的脆性材料时,又增添了额外的挑战&mdashmdash;例如碎片、断裂和残渣的产生。
像晶圆划线和切割,这两种将晶圆分割成单独芯片工艺中最常见的技术,通常是分别采用金刚石锯和金刚石划线工具完成的。
2 激光技术的更新使激光划线和激光划片成为一种可行的选择,特别在蓝光LED封装和GaAs基板应用中。
图1.采用标准UV胶带的分割工艺流程图。
无论选择哪种分割工艺,所有的方法都需要首先将晶圆保护起来,之后进行切割,以保证进入芯片粘结工序之前的转运和存储过程芯片的完整性。
其他的可能方法包括基于胶带的系统、基于筛网的系统以及采用其他粘结剂的无胶带系统。
工艺标准的切割工艺中首先是将减薄的晶圆放置好,使其元件面朝下,放在固定于钢圈的释放胶带上。
这样的结构在切割过程中可以保证晶圆,并且将芯片和封装继续保持在对齐的位置,方便向后续工艺的转运。
工艺的局限来自于减薄晶圆的应用,在存储之后很难从胶带上取下晶圆,采用激光的话容易切到胶带,同时在切割过程中冷却水的冲击也会对芯片造成损伤。
基于胶带的分割图2.可处理200或300 mm晶圆的UV固化单元可以放置在桌子上,采用365 nm波长的激光每个小时可以处理50片晶圆。
采用基于胶带的系统时,需要重点考虑置放系统,以及所采用的条带类型是不是适合要切割的材料。
金属渐薄处理

金属渐薄处理
金属渐薄处理,或称金属减薄处理,是一种工艺过程,旨在通过去除金属的一部分材料来减少其厚度。
这种处理常用于各种应用,包括材料研究、电子显微镜样品的制备、以及某些特定工业应用。
以下是金属渐薄处理的一些主要方法和步骤:
机械减薄:
使用研磨机、抛光机或切割机等机械设备来去除金属的部分材料。
此方法适用于较大和较厚的金属片材。
可以通过控制研磨或抛光的参数来实现精确的厚度调整。
化学减薄:
使用化学腐蚀剂与金属表面发生反应,从而去除部分材料。
适用于某些特定的金属和合金。
需要精确控制腐蚀剂的浓度、温度和处理时间,以防止过度腐蚀。
电解减薄:
通过电解过程,在电解质溶液中去除金属的部分材料。
通常用于制备透射电子显微镜(TEM)样品。
需要精确控制电解参数,如电流、电压和处理时间。
离子束减薄:
使用高能离子束轰击金属表面,从而去除部分材料。
是一种高精度和高效率的减薄方法,常用于制备高质量的TEM样品。
需要昂贵的设备和高度的操作技术。
等离子刻蚀:
使用等离子体与金属表面反应,从而去除部分材料。
适用于某些特定的金属和合金。
可以实现精确的厚度控制和高度均匀的减薄效果。
在选择金属渐薄处理方法时,需要考虑金属的类型、所需的减薄量、所需的精度和可行性等因素。
此外,还需要注意处理过程中可能出现的问题,如表面粗糙度、变形和应力等。
研磨减薄工艺

研磨减薄工艺研磨减薄工艺是一种常用的表面处理工艺,广泛应用于金属材料的加工中。
它通过磨削材料表面,使其达到一定的平整度和光洁度,以满足特定的工艺要求。
本文将从工艺原理、设备与工具、加工参数等方面介绍研磨减薄工艺的相关内容。
一、工艺原理研磨减薄工艺主要基于磨削原理,通过磨削材料表面的方式,将材料的高点磨掉,使其表面平整度和光洁度得到提高。
该工艺能够消除材料表面的缺陷和氧化皮,去除材料表面的残余应力,提高材料的耐腐蚀性能和力学性能。
二、设备与工具研磨减薄工艺需要使用到一些特定的设备与工具。
常见的设备包括研磨机、研磨头、研磨盘等。
研磨机是研磨减薄工艺的核心设备,其通过电机带动研磨头进行高速旋转,磨削材料表面。
研磨头是用来磨削材料表面的工具,常见的有砂轮、砂带等。
研磨盘用于支撑材料,在研磨过程中起到稳定材料的作用。
三、加工参数研磨减薄工艺的加工参数对于加工效果至关重要。
其中包括研磨速度、研磨压力、研磨深度等。
研磨速度的选择应根据材料的硬度和磨削头的特性进行合理调节,过高的速度容易导致材料热变形,过低的速度则会降低加工效率。
研磨压力的选择应根据材料的硬度和研磨头的特性进行合理调节,过大的压力容易导致研磨头磨损过快,过小的压力则会降低研磨效果。
研磨深度的选择应根据材料的要求和加工精度进行合理调节,过大的研磨深度容易导致材料变形,过小的研磨深度则会影响加工效果。
四、工艺流程研磨减薄工艺的一般流程包括材料准备、研磨加工和检测等步骤。
首先需要对材料进行准备,包括清洗、去除氧化皮等工序,以保证研磨效果的稳定性。
然后进行研磨加工,根据具体要求选择合适的研磨头和研磨盘,调节好加工参数,进行研磨操作。
最后进行检测,通过表面粗糙度仪、金相显微镜等工具对加工后的材料进行检测,以验证加工效果是否符合要求。
五、应用领域研磨减薄工艺广泛应用于金属材料的加工中。
例如,在半导体制造领域,研磨减薄工艺被用于晶圆的研磨和薄化,以满足芯片制造的要求。
- 1、下载文档前请自行甄别文档内容的完整性,平台不提供额外的编辑、内容补充、找答案等附加服务。
- 2、"仅部分预览"的文档,不可在线预览部分如存在完整性等问题,可反馈申请退款(可完整预览的文档不适用该条件!)。
- 3、如文档侵犯您的权益,请联系客服反馈,我们会尽快为您处理(人工客服工作时间:9:00-18:30)。
减薄 上蜡 研磨 抛光 卸片
清洗
清洗
• 定:
使用一定的化学试剂通过水浴浸泡, QDR冲洗的方式将芯片上蘸有的残蜡清 洗干净。
减薄 上蜡 研磨 抛光
卸片
清洗
清洗
• 步骤:
去蜡液—ACE—IPA—QDR—IPA—烘干
减薄 上蜡 研磨
抛光
卸片
清洗
之间的蜡均匀分布,并凝固将芯片固 定。
减薄 上蜡 研磨 抛光 卸片 清洗
研磨
• 定义:
使用钻石砂轮将芯片快速减薄到一 定厚度,研磨后芯片厚度值为 120±5μm,此步骤大约耗时15min。
430μm
15min
120μm
减薄 上蜡 研磨 抛光 卸片 清洗
研磨
• 步骤:
• 修盘 每次研磨前需使用油石将钻石砂
使用激光在芯片背面,沿切割道划 片。不同尺寸芯片,划片深度不一 ,深度区间为25至40μm之间。 注意:并未将芯片划穿。
划片 贴片 切割 裂片 倒膜 扩张
裂片
在芯片正面(激光划芯片背面) ,沿着激光划片的痕迹使用裂片机 将管芯完全分离开。
划片 贴片 切割 裂片 倒膜 扩张
倒膜
• 定义:
将完全分离的管芯由正面贴膜 翻转成背面贴膜。
研磨机
抛光机
减薄、划片工艺中主要使用的机台
激光划片机
裂片机
减薄、划片工艺流程图
减薄 划片 上蜡 贴片 研磨 切割 抛光 裂片 卸片 倒膜 清洗 扩张
减薄定义
减薄:顾名思义是通过特定的工艺手法将物体由厚变薄的 过程。
我司减薄的过程是要将厚度约为430μm的COW片(chip on wafer)减薄至 80μm±5μm左右
薄芯片。
减薄 上蜡 研磨 抛光
卸片
清洗
卸片
• 定义:
将减薄后的芯片从陶瓷盘上卸下来的 过程。
减薄 上蜡 研磨
抛光
卸片
清洗
卸片
• 步骤:
• 浸泡 将抛光后的陶瓷盘放入去蜡锅中,
加热浸泡5min左右,使芯片从陶瓷上 剥离。
减薄 上蜡 研磨 抛光 卸片
清洗
卸片
• 步骤:
• 夹取 用平口镊小心将减薄后的芯片夹只
划片定义
划片:是采用激光切割与劈刀裂片配合的方式,将连在一 起的管芯分割开来
划片
贴片
• 定义:
使用蓝膜或白膜将减薄后芯片 固定的过程。
划片 贴片 切割 裂片 倒膜 扩张
贴片
• 步骤:
• 准备工作 用IPA加至无尘布上擦拭chuck
表面和滚轮。把vacuum开至off。减薄 后80μm芯片很脆弱,需要注重每一个 细节。
划片 贴片 切割 裂片 倒膜 扩张
贴片
• 步骤:
• 取片 把贴片机vacuum开至off处。小
心将贴好的芯片取下。
划片 贴片 切割 裂片 倒膜 扩张
贴片
• 步骤:
• 贴片 放铁环,需注意对准卡栓,
用平口镊子夹取芯片,放片时芯片正 面朝上,使用白膜粘住芯片。
划片 贴片 切割 裂片 倒膜 扩张
切割
《减薄与划片工艺介绍》
减薄与划片流程图 减薄工艺简介 划片工艺简介
外延片
芯片生产工艺流程图
下料清洗
蒸镀
黄光作业
刻蚀
分选
测试
划片
减薄
合金
减薄、划片位于芯片生产工艺的中游。
COW(chip on wafer)
减薄、划片
COT (chip on wafer)
减薄、划片
减薄、划片工艺中主要使用的机台
划片 贴片 切割 裂片 倒膜 扩张
扩张
• 定义:
通过扩张蓝膜的方式,增大管 芯之间距离,以便于目检作业
划片 贴片 切割 裂片 倒膜 扩张
扩张
• 步骤:
• 扩张前准备
开机,打开电源,查看引伸盘控温器上的温度显示值是 否为40℃± 5℃,异常红灯会亮。
划片 贴片 切割 裂片 倒膜 扩张
扩张
• 步骤:
430μm
80μm
上蜡
• 定义:
将芯片固定在陶瓷盘上便于减薄的过 程。
减薄 上蜡 研磨
抛光
卸片
清洗
上蜡
• 步骤:
• 清洁陶瓷盘 上蜡贴片前,首先需要保证陶瓷
盘的洁净程度,LED芯片减薄是属于微 米量级的操作,任何细微的杂质都可 能导致意想不到的异常状况。
减薄 上蜡 研磨 抛光 卸片
清洗
上蜡
• 步骤:
清洗
抛光
• 定义:
如果说研磨是快速减薄的过程,抛光 则是一个缓慢减薄的过程,同时使芯 片表面粗糙度降低,以获得光亮、平 整表面。
减薄 上蜡 研磨 抛光 卸片
清洗
研磨
• 步骤:
• 镶盘 将锡盘上均匀布满钻石液的过程。
减薄 上蜡 研磨
抛光
卸片
清洗
抛光
• 步骤:
• 抛光 通过抛光液中的钻石颗粒,缓慢减
轮修整一遍。此动作意义类似于切菜 的前磨刀。
减薄 上蜡 研磨 抛光 卸片 清洗
研磨
• 步骤:
• 归零 归零实际是设置研磨起始点,归
零又分为手动归零和自动归零。
减薄 上蜡 研磨 抛光 卸片 清洗
研磨
• 步骤:
• 研磨 砂轮高速自转(1050rpm)并以一
定的规律进给将芯片减薄到指定厚度 。
减薄 上蜡 研磨 抛光 卸片
划片 贴片 切割 裂片 倒膜 扩张
倒膜
• 步骤:
• 去杂质 将切割与劈裂过程中产生的一些
碎屑杂质粘掉。
划片 贴片 切割 裂片 倒膜 扩张
倒膜
• 步骤:
• 贴膜 剪一方形蓝膜(大小为
20cm*20cm,长宽误差不大于2cm),将 Wafer背面贴于蓝膜中间位置
划片 贴片 切割 裂片 倒膜 扩张
倒膜
• 步骤:
• 加压 蓝膜在下,白膜在上放于倒膜
机加热平台上,盖上硅胶片,硅胶片 需覆盖整个片子区域,按下下降按钮 ,加压盘下降,等待4秒后加压盘自动 上升,即加压一次完成。
划片 贴片 切割 裂片 倒膜 扩张
倒膜
• 步骤:
• 撕膜 从加热平台上取下,左手按住
贴有Wafer的蓝膜,右手贴着膜平撕下 表面的白膜,倒膜完成,管芯由正面 贴膜变成了背面贴膜
• 扩张前准备
放扩张环 ,打开压盖,将扩张环的内环放入底盘中 ,注意光滑面朝上,将扩张环的外环放入压环盘中,注意光
滑面朝下。
划片 贴片 切割 裂片 倒膜 扩张
扩张
• 步骤:
• 放蓝膜
将贴有芯片的蓝膜平铺于底盘上,贴有芯片的一面 朝上。
划片 贴片 切割 裂片 倒膜 扩张
扩张
• 步骤:
• 扣紧压盖
• 涂蜡 将陶瓷盘加热至140℃,保证蜡条
能迅速融化,涂蜡过程中需注意要使 蜡均匀分布在陶瓷盘表面。
减薄 上蜡 研磨 抛光
卸片
清洗
上蜡
• 步骤:
• 贴片 将需要减薄的芯片小心放置于陶
瓷盘上,注意需要赶走芯片与蜡层之 间的气泡。
减薄 上蜡 研磨 抛光 卸片 清洗
上蜡
• 步骤:
• 加压冷却 通过加压的方式使,陶盘与芯片