几种常见热处理工艺种类及表面渗氮的技术
三种必备化学热处理知识

一.软氮化热处理为了缩短氮化周期,并使氮化工艺不受钢种的限制,在近年间在原氮化工艺基础上发展了软氮化和离子氮化两种新氮化工艺。
软氮化实质上是以渗氮为主的低温氮碳共渗,钢的氮原子渗入的同时,还有少量的碳原子渗入,其处理结果与一般气体氮化相比,渗层硬度较氮化低,脆性较小,故称为软氮化。
1、软氮化方法分为:气体软氮化、液体软氮化及固体软氮化三大类。
目前国内生产中应用最广泛的是气体软氮化。
气体软氮化是在含有活性氮、碳原子的气氛中进行低温氮、碳共渗,常用的共渗介质有尿素、甲酰胺、氨气和三乙醇胺,它们在软氮化温度下发生热分解反应,产生活性氮、碳原子。
活性氮、碳原子被工件表面吸收,通过扩散渗入工件表层,从而获得以氮为主的氮碳共渗层。
气体软氮化温度常用560-570℃,因该温度下氮化层硬度值最高。
氮化时间常为2-3小时,因为超过2.5小时,随时间延长,氮化层深度增加很慢。
2、软氮化层组织和软氮化特点:钢经软氮化后,表面最外层可获得几微米至几十微米的白亮层,它是由ε相、γ`相和含氮的渗碳体Fe3(C,N)所组成,次层为的扩散层,它主要是由γ`相和ε相组成。
软氮化具有以下特点:(1)、处理温度低,时间短,工件变形小。
(2)、不受钢种限制,碳钢、低合金钢、工模具钢、不锈钢、铸铁及铁基粉未冶金材料均可进行软氮化处理。
工件经软氮化后的表面硬度与氮化工艺及材料有关。
3、能显著地提高工件的疲劳强度、耐磨性和耐腐蚀性。
在干摩擦条件下还具有抗擦伤和抗咬合等性能。
4、由于软氮化层不存在脆性ξ相,故氮化层硬而具有一定的韧性,不容易剥落。
因此,目前生产中软氮化巳广泛应用于模具、量具、刀具(如:高速钢刀具)等、曲轴、齿轮、气缸套、机械结构件等耐磨工件的处理。
二.长轴氮化热处理目前,国内一般细长轴(2—3m)的热处理变形量要求不大于0.03~0.05mm,按传统制造工艺是很难达到这个要求。
经过对传统制造工艺流程和工艺进行改进和完善,使长轴最终氮化处理的变形量达到国内同行业先进水平。
机械加工常见热处理工艺

渗碳渗碳热处理渗碳:是对金属表面处理的一种,采用渗碳的多为低碳钢或低合金钢,具体方法是将工件置入具有活性渗碳介质中,加热到900--950摄氏度的单相奥氏体区,保温足够时间后,使渗碳介质中分解出的活性碳原子渗入钢件表层,从而获得表层高碳,心部仍保持原有成分。
相似的还有低温渗氮处理。
这是金属材料常见的一种热处理工艺,它可以使渗过碳的工件表面获得很高的硬度,提高其耐磨程度。
概述渗碳(carburizing/carburization)是指使碳原子渗入到钢表面层的过程。
也是使低碳钢的工件具有高碳钢的表面层,再经过淬火和低温回火,使工件的表面层具有高硬度和耐磨性,而工件的中心部分仍然保持着低碳钢的韧性和塑性。
渗碳工件的材料一般为低碳钢或低碳合金钢(含碳量小于0.25%)。
渗碳后﹐钢件表面的化学成分可接近高碳钢。
工件渗碳后还要经过淬火﹐以得到高的表面硬度﹑高的耐磨性和疲劳强度﹐并保持心部有低碳钢淬火后的强韧性﹐使工件能承受冲击载荷。
渗碳工艺广泛用于飞机﹑汽车和拖拉机等的机械零件﹐如齿轮﹑轴﹑凸轮轴等。
渗碳工艺在中国可以上溯到2000年以前。
最早是用固体渗碳介质渗碳。
液体和气体渗碳是在20世纪出现并得到广泛应用的。
美国在20年代开始采用转筒炉进行气体渗碳。
30年代﹐连续式气体渗碳炉开始在工业上应用。
60年代高温(960~1100℃)气体渗碳得到发展。
至70年代﹐出现了真空渗碳和离子渗碳。
分类按含碳介质的不同﹐渗碳可分为气体渗碳、固体渗碳﹑液体渗碳﹑和碳氮共渗(氰化)。
气体渗碳是将工件装入密闭的渗碳炉内,通入气体渗剂(甲烷、乙烷等)或液体渗剂(煤油或苯、酒精、丙酮等),在高温下分解出活性碳原子,渗入工件表面,以获得高碳表面层的一种渗碳操作工艺。
固体渗碳是将工件和固体渗碳剂(木炭加促进剂组成)一起装在密闭的渗碳箱中,将箱放入加热炉中加热到渗碳温度,并保温一定时间,使活性碳原子渗人工件表面的一种最早的渗碳方法。
液体渗碳是利用液体介质进行渗碳,常用的液体渗碳介质有:碳化硅,―603‖渗碳剂等。
金属材料热处理方法有几种
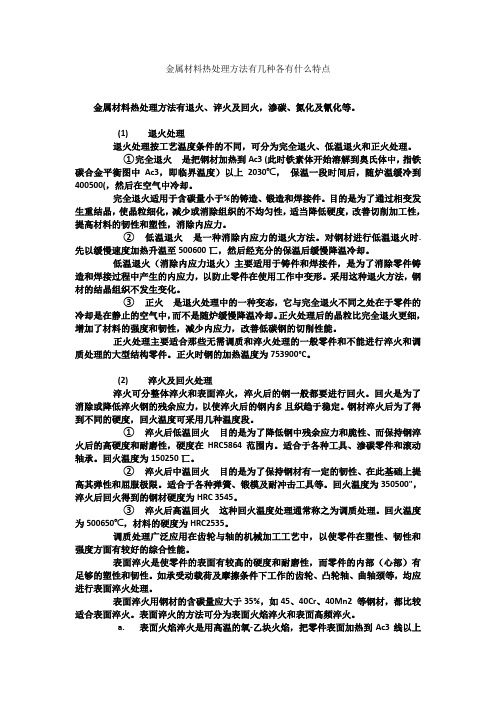
金属材料热处理方法有几种各有什么特点金属材料热处理方法有退火、谇火及回火,渗碳、氮化及氰化等。
(1) 退火处理退火处理按工艺温度条件的不同,可分为完全退火、低温退火和正火处理。
①完全退火是把钢材加热到Ac3 (此时铁素体开始溶解到奥氏体中,指铁碳合金平衡图中Ac3,即临界温度)以上2030℃,保温一段时间后,随炉温缓冷到400500(,然后在空气中冷却。
完全退火适用于含碳量小于%的铸造、锻造和焊接件。
目的是为了通过相变发生重结晶,使晶粒细化,减少或消除组织的不均匀性,适当降低硬度,改善切削加工性,提高材料的韧性和塑性,消除内应力。
② 低温退火是一种消除内应力的退火方法。
对钢材进行低温退火时.先以缓慢速度加热升温至500600匸,然后经充分的保温后缓慢降温冷却。
低温退火(消除内应力退火)主要适用于铸件和焊接件,是为了消除零件铸造和焊接过程中产生的内应力,以防止零件在使用工作中变形。
采用这种退火方法,钢材的结晶组织不发生变化。
③ 正火是退火处理中的一种变态,它与完全退火不同之处在于零件的冷却是在静止的空气中,而不是随炉缓慢降温冷却。
正火处理后的晶粒比完全退火更细,增加了材料的强度和韧性,减少内应力,改善低碳钢的切削性能。
正火处理主要适合那些无需调质和淬火处理的一般零件和不能进行淬火和调质处理的大型结构零件。
正火时钢的加热温度为753900°C。
(2) 淬火及回火处理淬火可分整体淬火和表面淬火,淬火后的钢一般都要进行回火。
回火是为了消除或降低淬火钢的残余应力,以使淬火后的钢内纟且织趋于稳定。
钢材淬火后为了得到不同的硬度,回火温度可采用几种温度段。
① 淬火后低温回火目的是为了降低钢中残余应力和脆性、而保持钢淬火后的高硬度和耐磨性,硬度在HRC5864范围内。
适合于各种工具、渗碳零件和滚动轴承。
回火温度为150250匸。
② 淬火后中温回火目的是为了保持钢材有一定的韧性、在此基础上提高其弹性和屈服极限。
常用表面处理工艺及热处理工艺
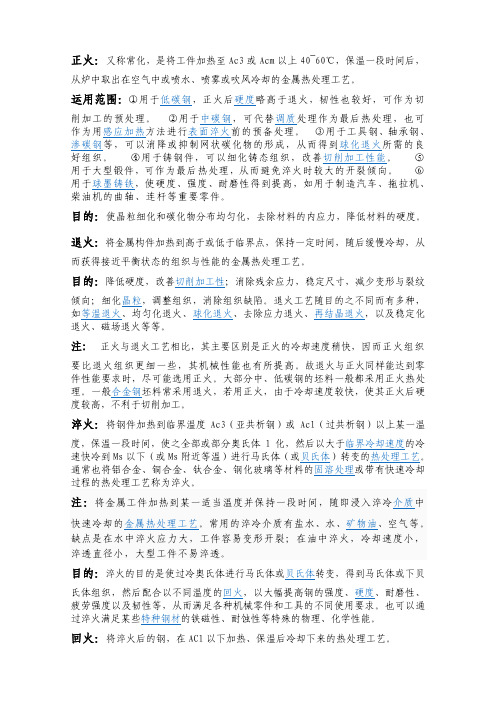
正火:又称常化,是将工件加热至Ac3或Acm以上40~60℃,保温一段时间后,从炉中取出在空气中或喷水、喷雾或吹风冷却的金属热处理工艺。
运用范围:①用于低碳钢,正火后硬度略高于退火,韧性也较好,可作为切削加工的预处理。
②用于中碳钢,可代替调质处理作为最后热处理,也可作为用感应加热方法进行表面淬火前的预备处理。
③用于工具钢、轴承钢、渗碳钢等,可以消降或抑制网状碳化物的形成,从而得到球化退火所需的良好组织。
④用于铸钢件,可以细化铸态组织,改善切削加工性能。
⑤用于大型锻件,可作为最后热处理,从而避免淬火时较大的开裂倾向。
⑥用于球墨铸铁,使硬度、强度、耐磨性得到提高,如用于制造汽车、拖拉机、柴油机的曲轴、连杆等重要零件。
目的:使晶粒细化和碳化物分布均匀化,去除材料的内应力,降低材料的硬度。
退火:将金属构件加热到高于或低于临界点,保持一定时间,随后缓慢冷却,从而获得接近平衡状态的组织与性能的金属热处理工艺。
目的:降低硬度,改善切削加工性;消除残余应力,稳定尺寸,减少变形与裂纹倾向;细化晶粒,调整组织,消除组织缺陷。
退火工艺随目的之不同而有多种,如等温退火、均匀化退火、球化退火、去除应力退火、再结晶退火,以及稳定化退火、磁场退火等等。
注: 正火与退火工艺相比,其主要区别是正火的冷却速度稍快,因而正火组织要比退火组织更细一些,其机械性能也有所提高。
故退火与正火同样能达到零件性能要求时,尽可能选用正火。
大部分中、低碳钢的坯料一般都采用正火热处理。
一般合金钢坯料常采用退火,若用正火,由于冷却速度较快,使其正火后硬度较高,不利于切削加工。
淬火:将钢件加热到临界温度Ac3(亚共析钢)或Ac1(过共析钢)以上某一温度,保温一段时间,使之全部或部分奥氏体1化,然后以大于临界冷却速度的冷速快冷到Ms以下(或Ms附近等温)进行马氏体(或贝氏体)转变的热处理工艺。
通常也将铝合金、铜合金、钛合金、钢化玻璃等材料的固溶处理或带有快速冷却过程的热处理工艺称为淬火。
渗氮工艺基本原理,特点及优缺点
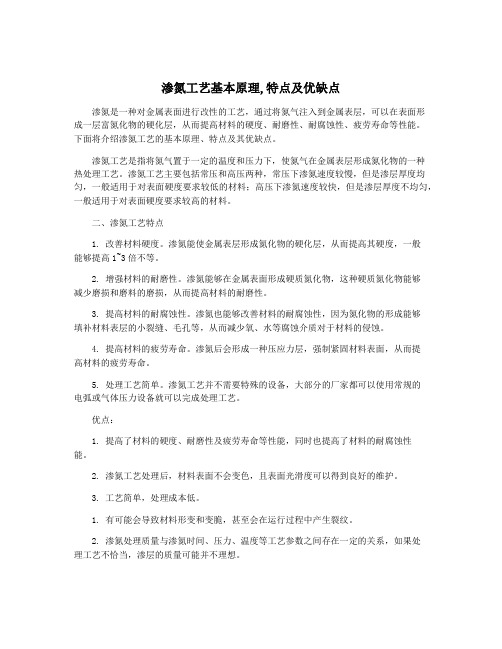
渗氮工艺基本原理,特点及优缺点渗氮是一种对金属表面进行改性的工艺,通过将氮气注入到金属表层,可以在表面形成一层富氮化物的硬化层,从而提高材料的硬度、耐磨性、耐腐蚀性、疲劳寿命等性能。
下面将介绍渗氮工艺的基本原理、特点及其优缺点。
渗氮工艺是指将氮气置于一定的温度和压力下,使氮气在金属表层形成氮化物的一种热处理工艺。
渗氮工艺主要包括常压和高压两种,常压下渗氮速度较慢,但是渗层厚度均匀,一般适用于对表面硬度要求较低的材料;高压下渗氮速度较快,但是渗层厚度不均匀,一般适用于对表面硬度要求较高的材料。
二、渗氮工艺特点1. 改善材料硬度。
渗氮能使金属表层形成氮化物的硬化层,从而提高其硬度,一般能够提高1~3倍不等。
2. 增强材料的耐磨性。
渗氮能够在金属表面形成硬质氮化物,这种硬质氮化物能够减少磨损和磨料的磨损,从而提高材料的耐磨性。
3. 提高材料的耐腐蚀性。
渗氮也能够改善材料的耐腐蚀性,因为氮化物的形成能够填补材料表层的小裂缝、毛孔等,从而减少氧、水等腐蚀介质对于材料的侵蚀。
4. 提高材料的疲劳寿命。
渗氮后会形成一种压应力层,强制紧固材料表面,从而提高材料的疲劳寿命。
5. 处理工艺简单。
渗氮工艺并不需要特殊的设备,大部分的厂家都可以使用常规的电弧或气体压力设备就可以完成处理工艺。
优点:1. 提高了材料的硬度、耐磨性及疲劳寿命等性能,同时也提高了材料的耐腐蚀性能。
2. 渗氮工艺处理后,材料表面不会变色,且表面光滑度可以得到良好的维护。
3. 工艺简单,处理成本低。
1. 有可能会导致材料形变和变脆,甚至会在运行过程中产生裂纹。
2. 渗氮处理质量与渗氮时间、压力、温度等工艺参数之间存在一定的关系,如果处理工艺不恰当,渗层的质量可能并不理想。
3. 渗氮处理的深度较浅,一般只能够处理金属的表层,如果需要提高整个材料的硬度,则需要采用其他处理工艺。
总之,渗氮工艺是一种较为常见的表面处理工艺,主要用于提高金属材料的硬度、耐磨性、耐腐蚀性等性能,工艺简单,处理成本低,但也存在一定的缺点。
渗碳渗氮、碳氮共渗和氮碳共渗,傻傻分不清楚?来看看他们的区别

渗碳渗氮、碳氮共渗和氮碳共渗,傻傻分不清楚?来看看他们的区别渗碳、渗氮、碳氮共渗和氮碳共渗,都是⾦属材料的表⾯处理⼯艺。
为了实现不同零件的⼯作条件和功能要求,需要对其表⾯进⾏不同的处理。
1. 渗碳渗碳是指使碳原⼦渗⼊到钢表⾯层的过程。
是使低碳钢的⼯件具有⾼碳钢的表⾯层,再经过淬⽕和低温回⽕,使⼯件的表⾯层具有⾼硬度和耐磨性,⽽⼯件的中⼼部分仍然保持着低碳钢的韧性和塑性。
具体⽅法是将⼯件置⼊具有活性渗碳介质中,加热到900--950摄⽒度的单相奥⽒体区,保温⾜够时间后,使渗碳介质中分解出的活性碳原⼦渗⼊钢件表层,从⽽获得表层⾼碳、⼼部仍保持原有成分。
它可以使渗过碳的⼯件表⾯获得很⾼的硬度,提⾼其耐磨程度。
典型渗碳⼯艺流程 渗碳⼯件的材料⼀般为低碳钢或低碳合⾦钢(含碳量⼩于0.25%)。
渗碳后﹐钢件表⾯的化学成分可接近⾼碳钢。
⼯件渗碳后还要经过淬⽕,以得到⾼的表⾯硬度、⾼的耐磨性和疲劳强度,并保持⼼部有低碳钢淬⽕后的强韧性,使⼯件能承受冲击载荷。
渗碳⼯艺⼴泛⽤于飞机﹑汽车和拖拉机等的机械零件﹐如齿轮﹑轴﹑凸轮轴等。
⼯件渗碳淬⽕后的表层显微组织主要为⾼硬度的马⽒体加上残余奥⽒体和少量碳化物,⼼部组织为韧性好的低碳马⽒体或含有⾮马⽒体的组织,但应避免出现铁素体。
齿轮渗碳表⾯组织(马⽒体+碳化物)渗碳后⼼部组织低碳马⽒体⼀般渗碳层深度范围为0.8~1.2毫⽶,深度渗碳时可达2毫⽶或更深。
表⾯硬度可达HRC58~63,⼼部硬度为HRC30~42。
渗碳淬⽕后﹐⼯件表⾯产⽣压缩内应⼒﹐对提⾼⼯件的疲劳强度有利。
齿轮渗碳层深度按含碳介质的不同,渗碳可分为固体渗碳、液体渗碳、⽓体渗碳和碳氮共渗等。
2. 渗氮是在⼀定温度下⼀定介质中使氮原⼦渗⼊⼯件表层的化学热处理⼯艺。
常见有液体渗氮、⽓体渗氮、离⼦渗氮。
渗⼊钢中的氮⼀⽅⾯由表及⾥与铁形成不同含氮量的氮化铁,⼀⽅⾯与钢中的合⾦元素结合形成各种合⾦氮化物,特别是氮化铝、氮化铬。
渗氮处理工艺
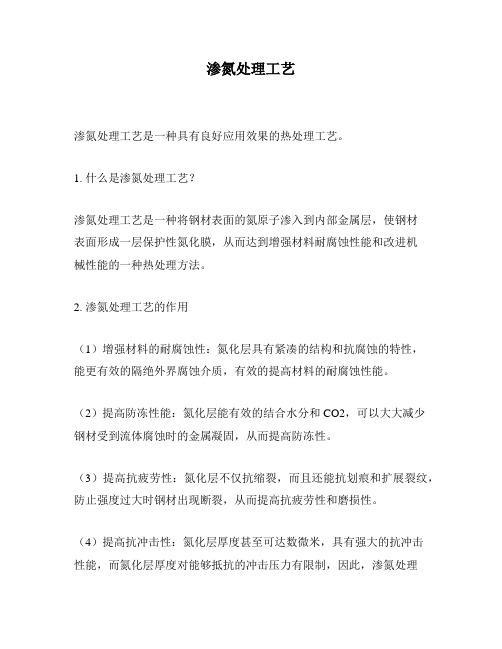
渗氮处理工艺
渗氮处理工艺是一种具有良好应用效果的热处理工艺。
1. 什么是渗氮处理工艺?
渗氮处理工艺是一种将钢材表面的氮原子渗入到内部金属层,使钢材
表面形成一层保护性氮化膜,从而达到增强材料耐腐蚀性能和改进机
械性能的一种热处理方法。
2. 渗氮处理工艺的作用
(1)增强材料的耐腐蚀性:氮化层具有紧凑的结构和抗腐蚀的特性,
能更有效的隔绝外界腐蚀介质,有效的提高材料的耐腐蚀性能。
(2)提高防冻性能:氮化层能有效的结合水分和CO2,可以大大减少
钢材受到流体腐蚀时的金属凝固,从而提高防冻性。
(3)提高抗疲劳性:氮化层不仅抗缩裂,而且还能抗划痕和扩展裂纹,防止强度过大时钢材出现断裂,从而提高抗疲劳性和磨损性。
(4)提高抗冲击性:氮化层厚度甚至可达数微米,具有强大的抗冲击
性能,而氮化层厚度对能够抵抗的冲击压力有限制,因此,渗氮处理
工艺能提高抗冲击性能。
3. 渗氮处理工艺的工艺要求
(1)渗氮处理温度一般在400~850摄氏度之间,氮化处理时间可由产品性能和渗氮处理设备特性而定;
(2)由于渗氮处理的过程中很难完全控制温度,在高温下,钢材内部的氮原子会被过多钙化,不仅会降低渗氮处理后的硬度,还会增加钢材表面的摩擦系数;
(3)上述温度段中,温度越到越高时,氮化处理性能也会越好。
4. 渗氮处理工艺的应用领域
渗氮处理技术不仅在航空、航天、汽车、风能和军工等行业有广泛应用,而且也被延伸到了电镀、化工等行业,完成机械装备配件的镀膜保护和抗腐蚀处理外观装饰,以及其他金属加工行业和机械设备加工行业等。
热处理知识——渗碳和渗氮
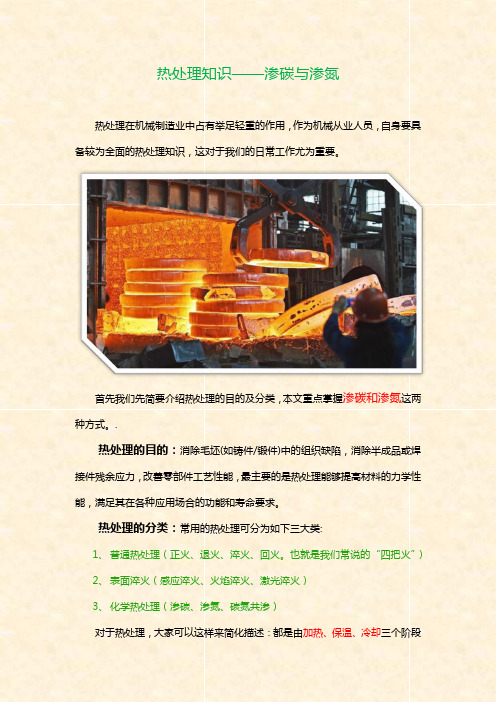
热处理知识——渗碳与渗氮热处理在机械制造业中占有举足轻重的作用,作为机械从业人员,自身要具备较为全面的热处理知识,这对于我们的日常工作尤为重要。
首先我们先简要介绍热处理的目的及分类,本文重点掌握渗碳和渗氮这两种方式。
.热处理的目的:消除毛坯(如铸件/锻件)中的组织缺陷,消除半成品或焊接件残余应力,改善零部件工艺性能,最主要的是热处理能够提高材料的力学性能,满足其在各种应用场合的功能和寿命要求。
热处理的分类:常用的热处理可分为如下三大类:1、普通热处理(正火、退火、淬火、回火。
也就是我们常说的“四把火”)2、表面淬火(感应淬火、火焰淬火、激光淬火)3、化学热处理(渗碳、渗氮、碳氮共渗)对于热处理,大家可以这样来简化描述:都是由加热、保温、冷却三个阶段组成。
不同热处理方法区别就在于这三个阶段,加热方式,加热温度或者加热的速度不同;保温方式,保温环境或者保温时间不同等;冷却的速度及冷却的环境不同等。
进入正文,主要介绍渗碳和渗氮渗碳定义:把零部件置于渗碳介质中,加热到单相奥氏体区,保温一定时间,使碳原子渗入钢表层的化学热处理工艺。
目的:使零件表面具有高硬度、耐磨及疲劳极限,心部具有较高的强度和韧性。
常用钢种:含碳量0.1%-0.25%的碳钢或合金(即低碳钢和低碳合金钢)渗碳方法:常用的气体渗碳法:工件置于密闭的加热炉中,滴入煤油、丙酮、甲苯等在高温(900-950°C)下分解出CO、CO2、CH4等,气体再分解出活性碳原子,随后活性碳原子溶于高温奥氏体中,随着时间进行,碳原子逐渐向内扩散,深度主要取决于保温时间,可大约按0.2mm/h的速度近似计算。
关键技术点:1)表面含碳量最好在0.85%-1.05%内,若含碳量过低,淬火、低温回火后得到的回火马氏体,含碳量较低,硬度低,耐磨性差。
2)在一定的渗碳层深度范围内,随渗碳层深度的增加,疲劳极限、抗弯强度及耐磨性都将增加,但渗碳层深度超过一定限度后,疲劳极限反随着渗碳层深度的增加而降低。
金属热处理中渗氮工艺常识

离子渗氮:
离子渗氮又称辉光渗氮﹐是利用辉光放电原理进行的。把金属工件作为阴极放入通有含氮介质的负压容器中﹐通电后介质中的氮氢原子被电离﹐在阴阳极之间形成等离子区。在等离子区强电场作用下﹐氮和氢的正离子以高速向工件表面轰击。离子的高动能转变为热能﹐加热工件表面至所需温度。由於离子的轰击﹐工件表面產生原子溅射﹐因而得到净化﹐同时由於吸附和扩散作用﹐氮遂渗入工件表面。
还有以抗蚀为目的的气体渗氮﹐渗氮温度在550~700℃之间﹐保温0.5~3小时﹐氨分解率为35~70%﹐工件表层可获得化学稳定性高的化合物层﹐防止工件受湿空气﹑过热蒸汽﹑气体燃烧產物等的腐蚀。
正常的气体渗般不影响使用。
气体参氮可採用一般渗氮法(即等温渗氮)或多段(二段﹑三段)渗氮法。前者是在整个渗氮过程中渗氮温度和氨气分解率保持不变。温度一般在480~520℃之间﹐氨气分解率为15~30%﹐保温时间近80小时。这种工艺适用於渗层浅﹑畸变要求严﹑硬度要求高的零件﹐但处理时间过长。多段渗氮是在整个渗氮过程中按不同阶段分别採用不同温度﹑不同氨分解率﹑不同时间进行渗氮和扩散。整个渗氮时间可以缩短到近50小时﹐能获得较深的渗层﹐但这样渗氮温度较高﹐畸变较大。
3.氨的分解率
渗氮是其它合金元素与初生态的氮接触而进行(初生态氮的产生,由氨气与加热中的零件接触时零件本身成为触媒而促进氨的分解),虽然在各种分解率的氨气下,皆可渗氮,但一般都采用15~30%的分解率,并按渗氮所需厚度保持4~10小时,处理温度保持在520℃左右。
4.冷却
大部份的工业用渗氮炉都有热交换机,在渗氮工作完成后冷却加热炉及被处理零件。即渗氮完成后,将加热电源关闭,使炉温降低约50℃,然后将氨的流量增加一倍后开启热交换机,此时须注重确认炉内压力为正压。等候导入炉中的氨气安定后,即可减少氨的流量至保持炉内正压为止,当炉温下降至150℃以下时,方可启开炉盖。
表面热处理工艺精选全文完整版
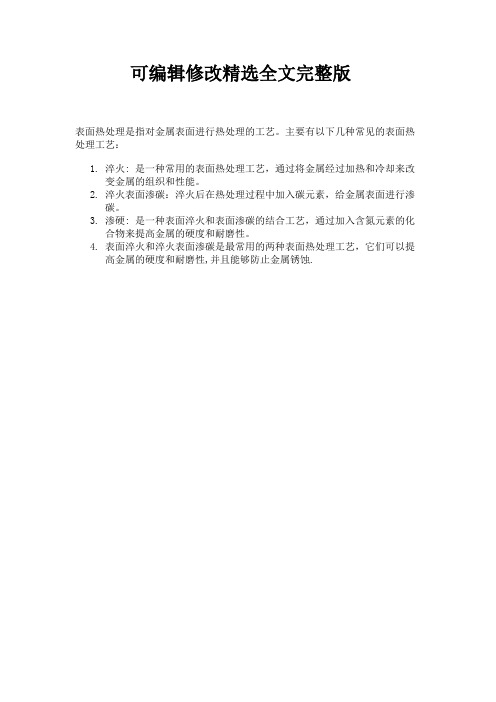
可编辑修改精选全文完整版
表面热处理是指对金属表面进行热处理的工艺。
主要有以下几种常见的表面热处理工艺:
1.淬火: 是一种常用的表面热处理工艺,通过将金属经过加热和冷却来改
变金属的组织和性能。
2.淬火表面渗碳:淬火后在热处理过程中加入碳元素,给金属表面进行渗
碳。
3.渗硬: 是一种表面淬火和表面渗碳的结合工艺,通过加入含氮元素的化
合物来提高金属的硬度和耐磨性。
4.表面淬火和淬火表面渗碳是最常用的两种表面热处理工艺,它们可以提
高金属的硬度和耐磨性,并且能够防止金属锈蚀.。
金属热处理生产工艺 渗氮工艺的技能操作 渗氮工艺的技能操作

6. 操作
(1)升温之前先检查炉子是否漏气,然后通氨气 ,按照工艺 规范加热升温 ,进行排气。
(2)为了减少变形采用阶梯升温方法 , 当炉温到达渗氮温度时, 调节好氨的分解率后开始计保温时间 。当氨分解率达到18% 左右时可点燃废气以保护环境。
(3)为了降低渗层的脆性 ,应进行退氮处理 ,此时应关闭出气 孔 , 只通入少量的氨气以保持炉内正压力。
度≥0.43mm;硬
度要求: 磨去
0. 1mm后硬度≥ 900HV; 畸变要求:
径向圆跳动≤
o.05mm。
2. 渗氮前的预备热处理
(1)调质 。粗车后加热到940 ℃保温2.5~3h ,油冷,在650~ 690 ℃回火,保温3.5h 。调质后硬度为248~280HBS。
(2)高温回火 。半精车后在610 ℃保温5~5.5h ,炉冷至≤ 350℃出炉空冷 。主要是消除机加工过程中的应力, 防止 渗氮过程中变形。
• (5)畸变 。主轴渗氮后精磨0. 1mm,径向跳动 0.03mm为合格 。如变形超差 ,主要原因是渗氮 前未很好地消除应力;温度不均匀 ,升温太快; 零件结构不合理等。
6.2.3训练3 齿轮气体渗氮(中级工)
• 1.技术要求 高速齿轮 ,30万吨合成氨离心空气压缩机的增速 器齿轮 ,材料25Cr2MoV ,渗氮层深0.45~
0.55mm。
• 2.加热设备及渗氮方式的选择 加热设备选用井式气体渗氮炉 ,采用气体渗氮方 式。
• 3.零件预备热处理 齿轮调质处理后精加工 ,精加工后进行消除应力 退火。
5. 质量检验
• (1)表面质量 。 目测氮化表面色泽 ,银灰色、不发亮为正 常 。如果发黑,说明炉内含氧量过高,零件去油污不好 。 解决的办法是检查泄漏 ,并注意清洗零件 ,清洗后一定要 干燥进炉。 (2)表面硬度。用试样检查表面硬度,再磨去0. 1mm后检 测硬度 。发现硬度低 ,说明渗氮温度过高或过低; 时间短 渗层太浅;真空度低 ,漏气造成氧化;氮势不足;材料用 错等 。解决的办法是严格执行工艺 ,检查漏气的原因 ,供 气适当 ,改正材料等。
金属热处理渗氮加工的工艺方法
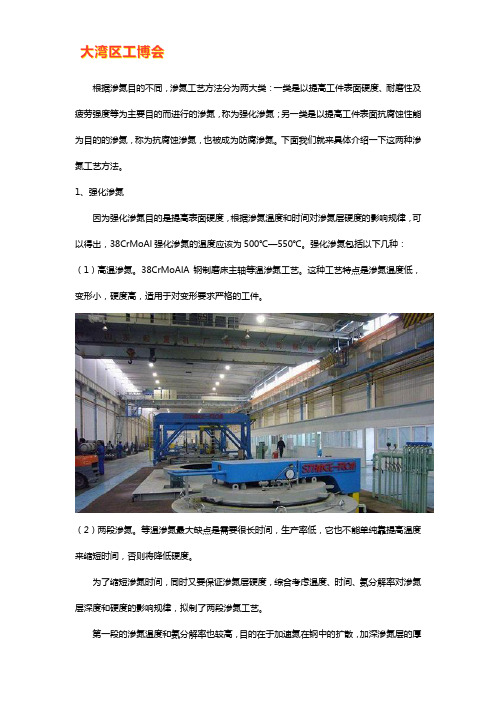
根据渗氮目的不同,渗氮工艺方法分为两大类:一类是以提高工件表面硬度、耐磨性及疲劳强度等为主要目的而进行的渗氮,称为强化渗氮;另一类是以提高工件表面抗腐蚀性能为目的的渗氮,称为抗腐蚀渗氮,也被成为防腐渗氮。
下面我们就来具体介绍一下这两种渗氮工艺方法。
1、强化渗氮因为强化渗氮目的是提高表面硬度,根据渗氮温度和时间对渗氮层硬度的影响规律,可以得出,38CrMoAl强化渗氮的温度应该为500℃—550℃。
强化渗氮包括以下几种:(1)高温渗氮。
38CrMoAlA钢制磨床主轴等温渗氮工艺。
这种工艺特点是渗氮温度低,变形小,硬度高,适用于对变形要求严格的工件。
(2)两段渗氮。
等温渗氮最大缺点是需要很长时间,生产率低,它也不能单纯靠提高温度来缩短时间,否则将降低硬度。
为了缩短渗氮时间,同时又要保证渗氮层硬度,综合考虑温度、时间、氨分解率对渗氮层深度和硬度的影响规律,拟制了两段渗氮工艺。
第一段的渗氮温度和氨分解率也较高,目的在于加速氮在钢中的扩散,加深渗氮层的厚度,从而缩短总的渗氮时间,并使渗氮层的硬度分布曲线趋于平缓。
第二段温度的升高,虽要发生氮化物的集聚、长大,但它与一次较高温度渗氮不同,因为在第一段渗氮时首先形成的高度弥散细小的氮化物,其集聚涨大要比直接再高温时涨大的氮化物的粗化过程慢得多,因而其硬度下降不显著。
(3)三段渗氮。
为了使两段渗氮后表面氮浓度有所提高,以提高其表面硬度,在两端渗氮后期再次降低渗氮温度和氨分解率而出现了三段渗氮法。
2、抗腐蚀渗氮经过抗腐蚀渗氮的碳钢、低合金钢及铸铁零件,在自来水、湿空气、过热蒸汽以及弱碱液中,具有良好的抗腐蚀性能。
因此已用来制造自来水龙头、锅炉汽管、水管阀门及门把手等,代替铜件和镀铬件,但是,渗氮层在酸溶液中没有抗腐蚀性。
抗腐蚀渗氮过程与强化渗氮过程基本相同,只有渗氮温度较高,有利于缩短渗氮时间。
但是温度过高,表面含氮量降低,孔隙度增大,因而抗腐蚀性降低。
金属热处理,渗碳,渗氮,发黑发蓝等处理

金属热处理,渗碳,渗氮,发黑发蓝等处理金属热处理,渗碳,渗氮,发黑发蓝等处理金属热处理:1.金属热处理是将金属工件放在一定的介质中加热到适宜的温度,并在此温度中保持一定时间后,又以不同速度冷却,通过改变金属材料表面或内部的组织结构来控制其性能的一种工艺。
2.金属热处理是机械制造中的重要工艺之一,与其他加工工艺相比,热处理一般不改变工件的形状和整体的化学成分,而是通过改变工件内部的显微组织,或改变工件表面的化学成分,赋予或改善工件的使用性能。
其特点是改善工件的内在质量,而这一般不是肉眼所能看到的。
3.钢铁的热处理是金属热处理的主要内容。
另外,铝、铜、镁、钛等及其合金也都可以通过热处理改变其力学、物理和化学性能,以获得不同的使用性能。
4.热处理工艺一般包括加热、保温、冷却三个过程,有时只有加热和冷却两个过程。
这些过程互相衔接,不可间断。
5.加热是热处理的重要工序之一。
金属热处理的加热方法很多,最早是采用木炭和煤作为热源,进而应用液体和气体燃料。
电的应用使加热易于控制,且无环境污染。
利用这些热源可以直接加热,也可以通过熔融的盐或金属,以至浮动粒子进行间接加热。
6.金属加热时,工件暴露在空气中,常常发生氧化、脱碳(即钢铁零件表面碳含量降低),这对于热处理后零件的表面性能有很不利的影响。
金属通常应在可控气氛或保护气氛中、熔融盐中和真空中加热,也可用涂料或包装方法进行保护加热。
7.加热温度是热处理工艺的重要工艺参数之一,选择和控制加热温度,是保证热处理质量的主要问题。
加热温度随被处理的金属材料和热处理的目的不同而异,但一般都是加热到相变温度以上,以获得高温组织。
另外转变需要一定的时间,因此当金属工件表面达到要求的加热温度时,还须在此温度保持一定时间,使内外温度一致,使显微组织转变完全,这段时间称为保温时间。
采用高能密度加热和表面热处理时,加热速度极快,一般就没有保温时间,而化学热处理的保温时间往往较长。
8.冷却也是热处理工艺过程中不可缺少的步骤,冷却方法因工艺不同而不同,主要是控制冷却速度。
渗氮工艺

渗氮渗氮,是在一定温度下一定介质中使氮原子渗入工件表层的化学热处理工艺。
常见有液体渗氮、气体渗氮、离子渗氮。
传统的气体渗氮是把工件放入密封容器中,通以流动的氨气并加热,保温较长时间后,氨气热分解产生活性氮原子,不断吸附到工件表面,并扩散渗入工件表层内,从而改变表层的化学成分和组织,获得优良的表面性能。
如果在渗氮过程中同时渗入碳以促进氮的扩散,则称为氮碳共渗。
常用的是气体渗氮和离子渗氮。
目录原理应用气体渗氮离子渗氮氮碳共渗辉光离子氮化渗氮前的处理渗氮前的生产准备原理应用渗入钢中的氮一方面由表及里与铁形成不同含氮量的氮化铁,一方面与钢中的合金元素结合形成各种合金氮化物,特别是氮化铝、氮化铬。
这些氮化物具有很高的硬度、热稳定性和很高的弥散度,因而可使渗氮后的钢件得到高的表面硬度、耐磨性、疲劳强度、抗咬合性、抗大气和过热蒸汽腐蚀能力、抗回火软化能力,并降低缺口敏感性。
与渗碳工艺相比,渗氮温度比较低,因而畸变小,但由于心部硬度较低,渗层也较浅,一般只能满足承受轻、中等载荷的耐磨、耐疲劳要求,或有一定耐热、耐腐蚀要求的机器零件,以及各种切削刀具、冷作和热作模具等。
渗氮有多种方法,常用的是气体渗氮和离子渗氮。
钢铁渗氮的研究始于20世纪初,20年代以后获得工业应用。
最初的气体渗氮,仅限于含铬、铝的钢,后来才扩大到其他钢种。
从70年代开始,渗氮从理论到工艺都得到迅速发展并日趋完善,适用的材料和工件也日益扩大,成为重要的化学热处理工艺之一。
气体渗氮一般以提高金属的耐磨性为主要目的,因此需要获得高的表面硬度。
它适用于38CrMoAl等渗氮钢。
渗氮后工件表面硬度可达HV850~1200。
渗氮温度低,工件畸变小,可用于精度要求高、又有耐磨要求的零件,如镗床镗杆和主轴、磨床主轴、气缸套筒等。
但由于渗氮层较薄,不适于承受重载的耐磨零件。
气体参氮可采用一般渗氮法(即等温渗氮)或多段(二段、三段)渗氮法。
前者是在整个渗氮过程中渗氮温度和氨气分解率保持不变。
渗氮及氮化处理
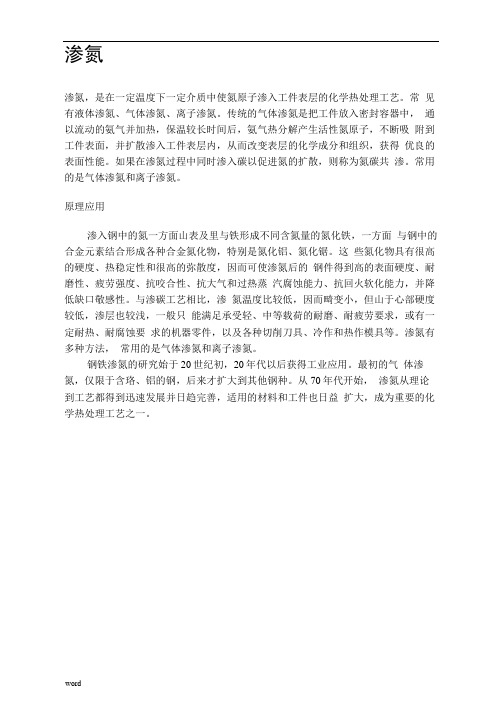
渗氮渗氮,是在一定温度下一定介质中使氮原子渗入工件表层的化学热处理工艺。
常见有液体渗氮、气体渗氮、离子渗氮。
传统的气体渗氮是把工件放入密封容器中,通以流动的氨气并加热,保温较长时间后,氨气热分解产生活性氮原子,不断吸附到工件表面,并扩散渗入工件表层内,从而改变表层的化学成分和组织,获得优良的表面性能。
如果在渗氮过程中同时渗入碳以促进氮的扩散,则称为氮碳共渗。
常用的是气体渗氮和离子渗氮。
原理应用渗入钢中的氮一方面山表及里与铁形成不同含氮量的氮化铁,一方面与钢中的合金元素结合形成各种合金氮化物,特别是氮化铝、氮化锯。
这些氮化物具有很高的硬度、热稳定性和很高的弥散度,因而可使渗氮后的钢件得到高的表面硬度、耐磨性、疲劳强度、抗咬合性、抗大气和过热蒸汽腐蚀能力、抗回火软化能力,并降低缺口敬感性。
与渗碳工艺相比,渗氮温度比较低,因而畸变小,但山于心部硬度较低,渗层也较浅,一般只能满足承受轻、中等载荷的耐磨、耐疲劳要求,或有一定耐热、耐腐蚀要求的机器零件,以及各种切削刀具、冷作和热作模具等。
渗氮有多种方法,常用的是气体渗氮和离子渗氮。
钢铁渗氮的研究始于20世纪初,20年代以后获得工业应用。
最初的气体渗氮,仅限于含珞、铝的钢,后来才扩大到其他钢种。
从70年代开始,渗氮从理论到工艺都得到迅速发展并日趋完善,适用的材料和工件也日益扩大,成为重要的化学热处理工艺之一。
气体渗氮——相艮而反用的扩隸算层 ----------------------L— _________ T砒2(吸附)亠~N 他吸附)亠3H (吸附)一N (吸附)—N? I-H ,EJ 5-33-1?渗氯层形成过襄示疡图:-1 一血沪内不晰输人劉气②•一氨分子向金雋表庇迁密③一氨分子被金展炭面吸附 々一慫分子在相界面上不斷增加、形成氮原子和氨原子 ⑤-恬性原子复合成分 :P ,经栩界囱反应的扩散层界不斯夙炉内排出⑥一表面吸附的氮原于浴解干a —Fe 中7:'-KM 子由金凤表面向內部扩散.井产生一定的侬度分布⑧一当氮超过在 "E 屮的落解度后,表层开集形成亂化物⑨一眾优樹沿金属表面的垂直方向利平 彳『方向K 大 询~烹面依次琏成y 相剤w 用 ⑪一氮化层不断增序 ⑫一氮从氮化 利向舍厲内部tr 敌一般以提高金属的耐磨性为主要U 的,因此需要获得高的表面硬度。
热处理知识——渗碳和渗氮
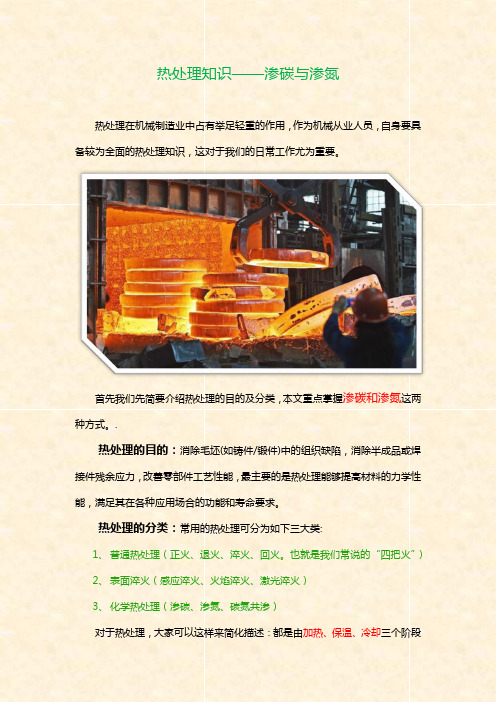
热处理知识——渗碳与渗氮热处理在机械制造业中占有举足轻重的作用,作为机械从业人员,自身要具备较为全面的热处理知识,这对于我们的日常工作尤为重要。
首先我们先简要介绍热处理的目的及分类,本文重点掌握渗碳和渗氮这两种方式。
.热处理的目的:消除毛坯(如铸件/锻件)中的组织缺陷,消除半成品或焊接件残余应力,改善零部件工艺性能,最主要的是热处理能够提高材料的力学性能,满足其在各种应用场合的功能和寿命要求。
热处理的分类:常用的热处理可分为如下三大类:1、普通热处理(正火、退火、淬火、回火。
也就是我们常说的“四把火”)2、表面淬火(感应淬火、火焰淬火、激光淬火)3、化学热处理(渗碳、渗氮、碳氮共渗)对于热处理,大家可以这样来简化描述:都是由加热、保温、冷却三个阶段组成。
不同热处理方法区别就在于这三个阶段,加热方式,加热温度或者加热的速度不同;保温方式,保温环境或者保温时间不同等;冷却的速度及冷却的环境不同等。
进入正文,主要介绍渗碳和渗氮渗碳定义:把零部件置于渗碳介质中,加热到单相奥氏体区,保温一定时间,使碳原子渗入钢表层的化学热处理工艺。
目的:使零件表面具有高硬度、耐磨及疲劳极限,心部具有较高的强度和韧性。
常用钢种:含碳量0.1%-0.25%的碳钢或合金(即低碳钢和低碳合金钢)渗碳方法:常用的气体渗碳法:工件置于密闭的加热炉中,滴入煤油、丙酮、甲苯等在高温(900-950°C)下分解出CO、CO2、CH4等,气体再分解出活性碳原子,随后活性碳原子溶于高温奥氏体中,随着时间进行,碳原子逐渐向内扩散,深度主要取决于保温时间,可大约按0.2mm/h的速度近似计算。
关键技术点:1)表面含碳量最好在0.85%-1.05%内,若含碳量过低,淬火、低温回火后得到的回火马氏体,含碳量较低,硬度低,耐磨性差。
2)在一定的渗碳层深度范围内,随渗碳层深度的增加,疲劳极限、抗弯强度及耐磨性都将增加,但渗碳层深度超过一定限度后,疲劳极限反随着渗碳层深度的增加而降低。
渗碳+渗氮+碳氮共渗表面处理工艺详解
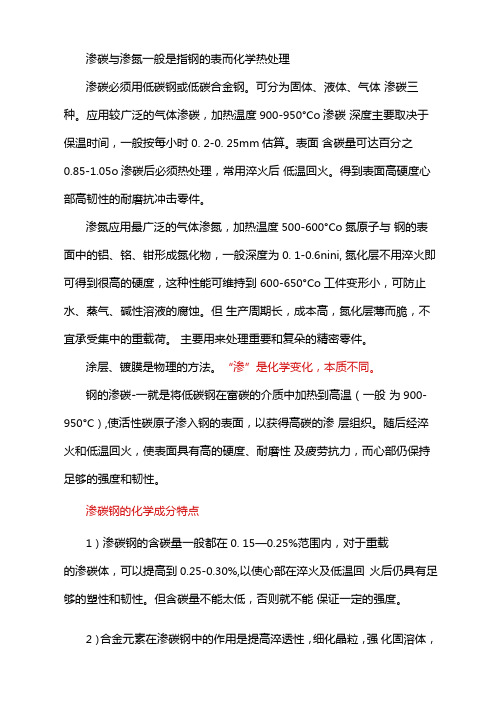
渗碳与渗氮一般是指钢的表而化学热处理渗碳必须用低碳钢或低碳合金钢。
可分为固体、液体、气体渗碳三种。
应用较广泛的气体渗碳,加热温度900-950°Co渗碳深度主要取决于保温时间,一般按每小时0. 2-0. 25mm估算。
表面含碳量可达百分之0.85-1.05o渗碳后必须热处理,常用淬火后低温回火。
得到表面高硬度心部高韧性的耐磨抗冲击零件。
渗氮应用最广泛的气体渗氮,加热温度500-600°Co氮原子与钢的表面中的铝、铭、钳形成氮化物,一般深度为0. 1-0.6nini, 氮化层不用淬火即可得到很高的硬度,这种性能可维持到600-650°Co工件变形小,可防止水、蒸气、碱性溶液的腐蚀。
但生产周期长,成本高,氮化层薄而脆,不宜承受集中的重载荷。
主要用来处理重要和复朵的精密零件。
涂层、镀膜是物理的方法。
“渗”是化学变化,本质不同。
钢的渗碳-一就是将低碳钢在富碳的介质中加热到高温(一般为900-950°C),使活性碳原子渗入钢的表面,以获得高碳的渗层组织。
随后经淬火和低温回火,使表面具有高的硬度、耐磨性及疲劳抗力,而心部仍保持足够的强度和韧性。
渗碳钢的化学成分特点1)渗碳钢的含碳量一般都在0. 15—0.25%范围内,对于重载的渗碳体,可以提高到0.25-0.30%,以使心部在淬火及低温回火后仍具有足够的塑性和韧性。
但含碳量不能太低,否则就不能保证一定的强度。
2)合金元素在渗碳钢中的作用是提高淬透性,细化晶粒,强化固溶体,影响渗层中的含碳量、渗层厚度及组织。
在渗碳钢中通常加入的合金元素有镭、铭、操、钳、钩、帆、硼等。
常用渗碳钢可以分碳素渗碳钢和合金渗碳钢两大类1)碳素渗碳钢中,用得最多的是15和20钢,它们经渗碳和热处理后表而硬度可达56—62HRCo但由于淬透性较低,只适用于心部强度要求不高、受力小、承受磨损的小型零件,如轴套、链条等。
2)低合金渗碳钢如20Cr、20Cr2MnVB、20Mn2TiB等,其渗透性和心部强度均较碳素渗碳钢高,可用于制造一般机械中的较为重要的渗碳件,如汽车、拖拉机中的齿轮、活塞销等。
渗氮热处理工艺

渗氮热处理工艺引言渗氮热处理是一种常用的金属表面处理方法,通过在金属表面加热和注入氮气的过程中,使得金属表面形成一层含氮的固溶体。
这种处理工艺可以提高材料的硬度、耐磨性和耐腐蚀性能,广泛应用于汽车、航空、冶金等行业。
渗氮热处理的原理渗氮热处理是通过将金属材料暴露在高温和高氮气氛中,使氮气通过表面扩散作用渗透到金属内部。
在高温下,氮原子与金属原子发生反应,形成固溶体。
这种固溶体中含有大量的氮原子,可以极大地提高材料的硬度和耐磨性能。
渗氮热处理的工艺参数渗氮热处理的效果受到多个工艺参数的影响,包括温度、时间、氮气流量等。
以下是一些常用的工艺参数:1.温度:温度是影响渗氮效果的主要因素之一,一般在800℃至1050℃之间进行。
温度过高可能导致材料结构不稳定,而温度过低则可能无法达到预期的渗氮效果。
2.时间:渗氮的时间也是一个重要的参数。
通常情况下,渗氮时间在5至48小时之间,过短的时间可能无法达到足够的渗透深度,而过长的时间则可能导致过度渗氮,使材料变脆。
3.氮气流量:氮气流量是控制渗氮过程中氮气浓度的关键因素。
较大的氮气流量可以加快氮气的扩散速度,但过大的流量可能造成能耗过高。
4.渗氮介质:常见的渗氮介质有氨气、氮气和氨氮混合物。
不同介质对渗氮效果有一定影响,根据材料的不同选择合适的介质非常重要。
渗氮热处理的应用渗氮热处理广泛应用于以下领域:1. 汽车工业汽车发动机零部件、齿轮、曲轴等往往需要具有较高的硬度和耐磨性能,以应对高速、高温、高载荷的工作条件。
通过渗氮热处理,可以提高这些零部件的表面硬度,延长使用寿命。
2. 航空航天工业航空航天工业对材料的要求非常严格,需要具有优异的高温和耐磨性能。
通过渗氮热处理,可以改善航空发动机叶片、气门和航空零部件的性能,提高其在高温高速工况下的使用寿命。
3. 冶金工业渗氮热处理也广泛应用于冶金工业中的钢铁制品。
通过渗氮可以提高钢材的强度和硬度,使其具有更好的耐磨性和耐腐蚀性能,适用于制造耐磨零件和高强度工具。
- 1、下载文档前请自行甄别文档内容的完整性,平台不提供额外的编辑、内容补充、找答案等附加服务。
- 2、"仅部分预览"的文档,不可在线预览部分如存在完整性等问题,可反馈申请退款(可完整预览的文档不适用该条件!)。
- 3、如文档侵犯您的权益,请联系客服反馈,我们会尽快为您处理(人工客服工作时间:9:00-18:30)。
几种常见热处理工艺种类及其基本概况_技术资料
时间:2010-05-08 17:07来源:作者:点击: 2次
1.正火:将钢材或钢件加热到临界点AC3或ACM以上的适当温度保持一定时间后在空气中冷却,得到珠光体类组织的热处理工艺。
2.退火annealing:将亚共析钢工件加热至AC3以上20—40度,保温一段时间后,随炉缓慢冷却(或埋在砂中或石灰中冷却)至500度以下在空
1.正火:将钢材或钢件加热到临界点AC3或ACM以上的适当温度保持一定时间后在空气中冷却,得到珠光体类组织的热处理工艺。
2.退火annealing:将亚共析钢工件加热至AC3以上20—40度,保温一段时间后,随炉缓慢冷却(或埋在砂中或石灰中冷却)至500度以下在空气中冷却的热处理工艺。
3.固溶热处理:将合金加热至高温单相区恒温保持,使过剩相充分溶解到固溶体中,然后快速冷却,以得到过饱和固溶体的热处理工艺。
4.时效:合金经固溶热处理或冷塑性形变后,在室温放置或稍高于室温保持时,其性能随时间而变化的现象。
5.固溶处理:使合金中各种相充分溶解,强化固溶体并提高韧性及抗蚀性能,消除应力与软化,以便继续加工成型。
6.时效处理:在强化相析出的温度加热并保温,使强化相沉淀析出,得以硬化,提高强度。
7.淬火:将钢奥氏体化后以适当的冷却速度冷却,使工件在横截面内全部或一定的范围内发生马氏体等不稳定组织结构转变的热处理工艺。
8.回火:将经过淬火的工件加热到临界点AC1以下的适当温度保持一定时间,随后用符合要求的方法冷却,以获得所需要的组织和性能的热处理工艺。
9.钢的碳氮共渗:碳氮共渗是向钢的表层同时渗入碳和氮的过程。
习惯上碳氮共渗又称为氰化,目前以中温气体碳氮共渗和低温气体碳氮共渗(即气体软氮化)应用较为广泛。
中温气体碳氮共渗的主要目的是提高钢的硬度,耐磨性和疲劳强度。
低温气体碳氮共渗以渗氮为主,其主要目的是提高钢的耐磨性和抗咬合性。
10.调质处理quenching and tempering:一般习惯将淬火加高温回火相结合的热处理称为调质处理。
调质处理广泛应用于各种重要的结构零件,特别是那些在交变负荷下工作的连杆、螺栓、齿轮及轴类等。
调质处理后得到回火索氏体组织,它的机械性能均比相同硬度的正火索氏体组织为优。
它的硬度取决于高温回火温度并与钢的回火稳定性和工件截面尺寸有关,一般在HB200—350之间。
11.钎焊:用钎料将两种工件粘合在一起的热处理工艺。
回火的种类及应用
根据工件性能要求的不同,按其回火温度的不同,可将回火分为以下几种:
(一)低温回火(150-250度)
低温回火所得组织为回火马氏体。
其目的是在保持淬火钢的高硬度和高耐磨性的前提下,降低其淬火内应力和脆性,以免使用时崩裂或过早损坏。
它主要用
于各种高碳的切削刃具,量具,冷冲模具,滚动轴承以及渗碳件等,回火后硬度一般为HRC58-64。
(二)中温回火(350-500度)
中温回火所得组织为回火屈氏体。
其目的是获得高的屈服强度,弹性极限和较高的韧性。
因此,它主要用于各种弹簧和热作模具的处理,回火后硬度一般为HRC35-50。
(三)高温回火(500-650度)
高温回火所得组织为回火索氏体。
习惯上将淬火加高温回火相结合的热处理称为调质处理,其目的是获得强度,硬度和塑性,韧性都较好的综合机械性能。
因此,广泛用于汽车,拖拉机,机床等的重要结构零件,如连杆,螺栓,齿轮及轴类。
回火后硬度一般为HB200-330。
(责任编辑:admin)
金属热处理:渗氮_技术资料
时间:2010-05-08 17:07来源:作者:点击: 2次
使氮原子渗入钢铁工件表层内的化学热处理工艺。
传统的气体渗氮是把工件放入密封容器中﹐通以流动的氨气并加热﹐保温较长时间后﹐氨气热分解產生活性氮原子﹐不断吸附到工件表面﹐并扩散渗入工件表层内﹐从而改变表层的化学成分和组织﹐获得优良的表面性能。
使氮原子渗入钢铁工件表层内的化学热处理工艺。
传统的气体渗氮是把工件放入密封容器中﹐通以流动的氨气并加热﹐保温较长时间后﹐氨气热分解產生活性氮原子﹐不断吸附到工件表面﹐并扩散渗入工件表层内﹐从而改变表层的化学成分和组织﹐获得优良的表面性能。
如果在渗氮过程中同时渗入碳以促进氮的扩散﹐则称为氮碳共渗。
钢铁渗氮的研究始於20世纪初﹐20年代以后获得工业应用。
最初的气体渗氮﹐仅限於含铬﹑铝的钢﹐后来才扩大到其他钢种。
从70年代开始﹐渗氮从理论到工艺都得到迅速发展并日趋完善﹐适用的材料和工件也日益扩大﹐成为重要的化学热处理工艺之一。
渗入钢中的氮一方面由表及裡与铁形成不同含氮量的氮化铁﹐一方面与钢中的合金元素结合形成各种合金氮化物﹐特别是氮化铝﹑氮化铬。
这些氮化物具有很高的硬度﹑热稳定性和很高的弥散度﹐因而可使渗氮后的钢件得到高的表面硬度﹑耐磨性﹑疲劳强度﹑抗咬合性﹑抗大气和过热蒸汽腐蚀能力﹑抗回火软化能力﹐并降低缺口敏感性。
与渗碳工艺相比﹐渗氮温度比较低﹐因而畸变小﹐但由於心部硬度较低﹐渗层也较浅﹐一般只能满足承受轻﹑中等载荷的耐磨﹑耐疲劳要求﹐或有一定耐热﹑耐腐蚀要求的机器零件﹐以及各种切削刀具﹑冷作和热作模具等。
渗氮有多种方法﹐常用的是气体渗氮和离子渗氮。
气体渗氮一般以提高金属的耐磨性为主要目的﹐因此需要获得高的表面硬度。
它适用於38CrMnAc等渗氮钢。
渗氮后工件表面硬度可达HV850~1200。
渗氮温度低﹐工件畸变小﹐可用於精度要求高﹑又有耐磨要求的零件﹐如鏜床鏜杆和主轴﹑磨床主轴﹑气缸套筒等。
但由於渗氮层较薄﹐不适於承受重载的耐磨
零件。
气体参氮可採用一般渗氮法(即等温渗氮)或多段(二段﹑三段)渗氮法。
前者是在整个渗氮过程中渗氮温度和氨气分解率保持不变。
温度一般在480~520℃之间﹐氨气分解率为15~30%﹐保温时间近80小时。
这种工艺适用於渗层浅﹑畸变要求严﹑硬度要求高的零件﹐但处理时间过长。
多段渗氮是在整个渗氮过程中按不同阶段分别採用不同温度﹑不同氨分解率﹑不同时间进行渗氮和扩散。
整个渗氮时间可以缩短到近50小时﹐能获得较深的渗层﹐但这样渗氮温度较高﹐畸变较大。
还有以抗蚀为目的的气体渗氮﹐渗氮温度在 550~700℃之间﹐保温0.5~3小时﹐氨分解率为35~70%﹐工件表层可获得化学稳定性高的化合物层﹐防止工件受湿空气﹑过热蒸汽﹑气体燃烧產物等的腐蚀。
正常的气体渗氮工件﹐表面呈银灰色。
有时﹐由於氧化也可能呈蓝色或黄色﹐但一般不影响使用。
离子渗氮又称辉光渗氮﹐是利用辉光放电原理进行的。
把金属工件作为阴极放入通有含氮介质的负压容器中﹐通电后介质中的氮氢原子被电离﹐在阴阳极之间形成等离子区。
在等离子区强电场作用下﹐氮和氢的正离子以高速向工件表面轰击。
离子的高动能转变为热能﹐加热工件表面至所需温度。
由於离子的轰击﹐工件表面產生原子溅射﹐因而得到净化﹐同时由於吸附和扩散作用﹐氮遂渗入工件表面。
与一般的气体渗氮相比﹐离子渗氮的特点是﹕①可适当缩短渗氮週期﹔②渗氮层脆性小﹔③可节约能源和氨的消耗量﹔④对不需要渗氮的部分可屏蔽起来﹐实现局部渗氮﹔⑤离子轰击有净化表面作用﹐能去除工件表面钝化膜﹐可使不锈钢﹑耐热钢工件直接渗氮。
⑥渗层厚度和组织可以控制。
离子渗氮发展迅速﹐已用於机床丝杆﹑齿轮﹑模具等工件。
氮碳共渗又称软氮化或低温碳氮共渗﹐即在铁-氮共析转变温度以下﹐使工件表面在主要渗入氮的同时也渗入碳。
碳渗入后形成的微细碳化物能促进氮的扩散﹐加快高氮化合物的形成。
这些高氮化合物反过来又能提高碳的溶解度。
碳氮原子相互促进便加快了渗入速度。
此外﹐碳在氮化物中还能降低脆性。
氮碳共渗后得到的化合物层韧性好﹐硬度高﹐耐磨﹐耐蚀﹐抗咬合。
常用的氮碳共渗方法有液体法和气体法。
处理温度530~570℃﹐保温时间1~3小时。
早期的液体盐浴用氰盐﹐以后又出现多种盐浴配方。
常用的有两种﹕中性盐通氨气和以尿素加碳酸盐为主的盐﹐但这些反应產物仍有毒。
气体介质主要有﹕吸热式或放热式气体(见可控气氛)加氨气﹔尿素热分解气﹔滴注含碳﹑氮的有机溶剂﹐如甲醯胺﹑三乙醇胺等。
氮碳共渗不仅能提高工件的疲劳寿命﹑耐磨性﹑抗腐蚀和抗咬合能力﹐而且使用设备简单﹐投资少﹐易操作﹐时间短和工件畸变小﹐有时还能给工件以美观的外表。
低碳钢在渗氮后可进行高频淬火处理,以提高表面的硬度,及疲劳强度等。