直流电镀在微孔、盲孔镀中的重大突破
不到半根头发粗的镀铜盲孔(下)——拆解iPhone XR的多种发现

2021年1月第1期102使用A11芯片的i-XS 其最大特色是将长条型十层主板折半,中间另插入双面板然后再上下焊成为22层板,如此省下的面积可用以加大L 型电池。
主板正面头号元件PoP 的A12正是笔者详加探讨的重心,也正是电业从芯片、封装、组装最先进技术之所在。
不到半根头发粗的镀铜盲孔(下)——拆解 iPhone XR 的多种发现TPCA 资深技术顾问 白蓉生(接上期)3.6 SAP(Semi-Additive Process)半加成法的真正面貌日商大运味之素大改行并量产多年ABF(Ajinomoto Bond Film)的白色膜材,已成为全球高阶大型载板SAP 增层用无玻纤的膜材,其关键技术就是所掺加的nm 级SiO 2 小球。
当增层的ABF 膜材打出盲孔后接下来的除胶渣会咬掉表面小球,所留下众多球坑则可用以抓牢起步用的化铜层,进而得以在大排板上做出10~15μm 的牢固细线。
通常ABF 的超小盲孔可采UV 雷射绕锯成孔,较大盲孔则可用更快速的CO 2烧孔。
其化铜也较一般厚出50%。
(图20)3.7 SAP法与mSAP法两者细线的不同SAP 半加成法的流程是先对高价ABF 膜材执行孔内与板面两者总体性除胶渣,如此即可清洁盲壁盲底又可咬掉表面微球而留下1μm 的球坑,于是后续铺满较厚的化铜层时就具备了绝佳的抓地力。
有了较厚的化铜层才可用以代替铜箔进行后续流程;经光阻、电图20铜、去光阻,全面咬蚀(Differential Etching)后即得到已削角宽度仅10~20μm 的细线(图21中②)。
从画面下端见到传统蚀刻有尖角的内层板与上端无尖角细线看来,两者完全不同。
图21中①③④是用3~5μm UTC 取代高价SAP 的mSAP 工法所量产的载板细线。
注意载板与类载板两者流程也有差异。
3.8 载板用SAP半加成法与mSAP模拟半加成法两者的对比SAP 半加成法仅指ABF 膜材经全面除胶渣咬掉微球留下微坑后;再过PTH 化钯化铜湿流程的金属化——光阻及成像——电镀铜成线及填盲孔——去光阻并全面性蚀剂而完工。
PCB盲孔镀铜填孔添加剂研究进展

稳 定性。文章介 绍 了盲孔 电镀 工艺中常用的四种 添加剂 ,并对 国内外填铜添加剂的研究进展进行 了概述。
中图 分 类 号 :T 4 N 1
R e e r h pr g e so dd tve e o i d s a c o r s fa ii sus d f rbln vi upe li n PCB a uf c urng as rf lng i i m n at i
该 类添 加 剂 的分 子 内含 有 共 轭 结 构 , 这增 强 了它 在 阴 极表 面 的吸 附 强 度 ,所 以该 类 分 子 可 以有 效抑 制
( S MP ),加 速 剂 单 独 使用 不 能在 盲 孔 底 部起 到加 速 的 作用 ,反 而 会 阻化 金 属 铜 的沉 积 ,只有 在 复 合 添加 剂 中才 能起 到加 速盲 孔 底部 沉铜 的 作用 。黄 令 等 以S S 研究 对象 ,运 用循 环 伏 安法和 计 时 安培法 P为 研 究 了S S 为添 加剂对 铜 电沉 积 的影 响 ,他们 发现 P作 S S 整个 体 系 的扩散 系数 降低 ,阻化 了铜 的电沉 积 P使 过程 。S S P 的加 入 有利 于 晶核 的形 成 ,使 晶核 分布 更 加 致 密 ,促 使镀 铜 层 变 得 更 加 平 滑 并 得 以反 光 ,故 该 类化 合物 又 被称 为光 亮剂 。钟琴 口 过研 究指 出 等通
铜 离 子 在 阴 极 的还 原 。 常 用 的 整 平 剂 有 詹 纳 斯 绿 (G )和苯 并三氮 唑等 。 JB 李 亚冰 过 电化学 测试 法 、质谱 法和 液体 核 磁 通
共 振法 对J 在 电镀 过程 中的作用 进行 了研 究 ,他 们 GB 指 出J 在 较低 的 阴极 极化 电位下 会通 过 加氢 还原 断 GB 开. N 键 ,得 到产 物A,A的 结构 图 如 图1 N= 双 所示 , 在该 过程 中J GB从 电极 表 面脱 附 。产 物A比较 稳 定 ,
电镀铜配方工艺、盲孔电镀配方工艺及电镀处理技术开发

电镀系列之二:电镀铜工艺及配方技术开发线路板在制作过程中,通孔经过孔金属化后往往要经过电镀铜来加厚孔铜,增强电路的耐候性能。
通常涉及到的镀铜过程包括普通电镀铜以及盲孔填孔。
线路板中使用的电镀铜技术主要还是酸铜,其镀液组成为硫酸、硫酸铜、氯离子、光亮剂(B)、整平剂(L)以及载运剂(C)。
B L C B B C B C B C B B B B L B L C B B C B C B C B B B B L B C L B C L B C LB C L图1、添加剂B、C、L 的作用机理光亮剂(B):吸附于低电流密度区并提高沉积速率;整平剂(L):快速地吸附到所有受镀表面并均一地抑制电沉积;载运剂(C):携带光剂进入低电流密度区,提高低电流密度区的沉积速率;三剂一起作用,达到铜面、孔铜一起电镀,产生光亮镀层。
(1)PCB 普通电镀铜禾川化学经过研究,开发出一款适用于PCB 孔电镀铜药水,具有以下特点:(1)镀液容易控制,镀层平整度高;(2)镀层致密性好,不易产生针孔;(3)可快速获得镜面光亮及整平特性;(4)添加剂消耗量稳定,消耗量少;(5)通孔电镀效果好,TP 值大于80%,延展性,热应力等参数符合PCB标准。
图2、PCB电镀铜效果图(2)FPC普通电镀铜禾川化学经过研究,开发出一款适用于FPC孔铜电镀的药水,具有以下特点:(1)镀液容易控制,镀层平整度高;(2)镀层延展性好,耐折度好;(3)可快速获得镜面光亮及整平特性;(4)添加剂消耗量稳定,消耗量少;(5)通孔电镀效果好,TP值大于120%,延展性,热应力等参数符合PCB 标准。
图3、FPC电镀铜效果图(3)盲孔填空电镀填孔电镀添加剂的组成:光亮剂(B又称加速剂),其作用减小极化,促进铜的沉积、细化晶粒;载运剂(C又称抑制剂),增加阴极极化,降低表面张力,协助光亮剂作用;整平剂(L),抑制高电流密度区域铜的沉积。
微盲孔孔底和孔内沉积速率的差异主要来源于添加剂在孔内不同位置吸附分布,其分布形成过程如下:a、由于整平剂带正电,最易吸附在孔口电位最负的位置,并且其扩散速率较慢因此在孔底位置整平剂浓度较低;b、加速剂最易在低电流密度区域富集,并且其扩散速率快,因此,孔底加速剂浓度较高;c、在孔口电位最负,同时对流最强烈,整平剂将逐渐替代抑制剂加强对孔口的抑制,最终使得微孔底部的铜沉积速率大于表面沉积速率,从而达到填孔的效果。
盲孔填孔不良分析

电镀盲孔填孔不良分析目前多阶HDI板的层间互连大多采用微孔叠孔及交错连接方式设计,一般采用电镀铜填孔方式进行导通,但电镀填盲孔技术与传统电镀有一定差别,且在工艺参数,流程设计,设备方面更有严格要求,填孔过程中出现空洞、凹陷、漏填也是厂内控制的难点,下面将厂内填孔缺陷进行分析,提供些填孔不良的思路;一、填孔不良分析:针对厂内填孔不良切片分析分类,统计如下:序号缺陷分类不良图片不良比例1 凹陷75%2 漏填15%3 空洞5%二、原因分析:通过切片分析确认,不良主要为凹陷、漏填、空洞,其中凹陷、漏填比例较高,其次为空洞,现针对厂内填孔不良可能原因进行分析.2.1添加剂浓度失调:盲孔的填孔主要是通过添加剂中各组成分的协调作用、吸附差异平衡化完成,浓度失控势必会造成添加剂在盲孔内吸附平衡的破坏影响填孔效果.2.2打气喷管堵塞:填孔槽打气大小直接影响到填孔过程中孔内药水交换效果,若打气效果差必然会造成孔内药水交换导致填孔效果欠佳凹陷值偏大.2.3导电性不良:夹头或挂具损坏、飞靶和V型座接触不好,导致电流分布不均,板内电流小区域必然会出现盲孔凹陷或漏填现象.2.4填孔前微蚀异常:填孔前微蚀不足均可能导致个别盲孔孔内导电不良,孔内电阻偏高,在填孔时不利于添加剂分布导致填孔失败.2.5板子入槽时变形导致局部盲孔突起,局部盲孔漏填或凹陷.2.6泵浦吸入口漏气,必然会造成大量空气进入槽内,通过过滤泵循环过滤将起泡带入整个槽内通过气流进入盲孔,阻碍孔内药水交换导致盲孔漏填现象.三、效果验证:实验前通过对药水调整至最佳状态,检查打气管道、夹头(挂具)、打气状况,维修设备接触不良处并用稀硫酸清洗、微蚀速率控制在20—30u”,保证板为垂直状态后进行填孔测试,测试结果无异常.四、结论:通过改善前后对比可以看出:厂内填孔不良主要为药水浓度、打气、导电性、填孔前微蚀量异常及槽内有气泡导致填孔异常,当然影响盲孔填孔异常的因素还有很多,只有平时做到长期监控,细心维护设备,认真排查造成填孔不良的每一个可能因素,才能真正运用好填孔技术,解决厂内填孔异常.。
印制电路板通盲孔同镀

印制电路板通盲孔同镀随着HDI印制电路板产品市场的需求越来越大,电路板的通孔及盲孔的制作技术有待提高的必要。
高密度,小微孔板的设计需要利用盲孔、埋孔和通孔的结构来将层与层之间相连接。
制作工厂一般是先处理盲孔电镀填铜后,再进行通孔的电镀。
工艺流程过于复杂,需要经过两次电镀工序才能完成,对于需求高量产的制作工厂来说,这种工序严重浪费工时。
文章为改善这一困难,试验了将通孔和盲孔一次性制作,以达到降低生产成本,提高产品品质和缩短生产周期的效果。
标签:高密度电路板;盲孔;通盲孔同镀;降低成本Abstract:With the increasing demand of HDI printed circuit board product market,it is necessary to improve the through hole and blind hole manufacturing technology of circuit board. The design of high density,small hole plate needs to use the structure of blind hole,buried hole and through hole to connect layer to layer. The manufacture factory usually processes the blind hole electroplating to fill the copper first,and then carries on the through hole electroplating. The process is too complex and requires two electroplating processes to be completed,which is a serious waste of time for manufacturing plants that require high volume production. In order to improve this difficulty,this paper tests that the through hole and blind hole can be made in one time,so as to reduce the production cost,improve the product quality and shorten the production period.Keywords:high density circuit board;blind hole;through blind hole same plating;reduce cost1 概述电路板的通孔电镀和盲孔填铜工艺是经过两次电镀制成,电镀产线一直是高密度电路板的难产工序,产能及员工工时严重被浪费。
模具表面的电镀技术

所以要获得质量优良的镀层,还应有合理的镀液组成和合 理的工艺控制。
电镀合金
为什么要用合金镀层?
❖ 对镀层性能上的高要求 ❖ 品种远远大于单金属 ❖ 特殊的物理性能、化学性能、机械性能,使
合金镀层在各方面优于单金属镀层
5、反应生成物不妨碍镀覆过程的正常进行,即 溶液有足够的使用寿命
化学镀的特点
❖ (1)可以在由金属、半导体和非导体等各种材料制成的零件上 镀覆金属;
❖ (2)无论零件的几何形状如何复杂,凡能接触到溶液的地方都 能获得厚度均匀的镀层,化学镀溶液的分散能力优异,不受 零件外形复杂程度的限制,无明显的边缘效应,因此特别适 合于复杂零件、管件内壁、盲孔件的镀覆;
❖ 【去离子水】电镀/化学镀溶液,或配制或调整,或工件需 要特别清洗,使用经过阴阳两种离子交换的树脂处理,将其 水中存在的各种离子予以吸附除去,获得纯度极高的水。
❖ 【活性炭】由木质粉末烧制成粒度极细的木炭粉,呈多孔结 构具有极大的表面积,有高的吸附性能,能吸附大量的有机 物。用于清除电镀液的有机杂质,有粉状和颗粒状两种类型。
1、电解液中金属离子浓度的影响 (包括金属离子浓度和金属离子总浓度)
Co:-0.277V Ni: -0.246V
2、配位剂浓度的影响: 单一配位剂:氰化镀黄铜;酸性氟化物镀Sn-Ni
混合配位剂:碱性氰化物镀Cu-Sn
➢ 3、添加剂的影响
✓ 添加剂与配位剂相比,其影响要小得多 ✓ 添加剂含量达到一定值后,镀层组成可基本不变 ✓ 添加剂通常对简单盐镀液有明显影响 ✓ 添加剂对合金成分的影响常有选择性
三、在合金共沉积理论中的阴极极化曲线
盲孔电镀填平不良改善研究

盲孔电镀填平不良改善研究雷华山;于永贞;刘彬云;肖定军【摘要】The reasons which led to the quality defects of void, dimple value too large, un-iflling and so on were analyzed deeply in the process of microvia iflling for the VCP bath .At the same time, they were veriifed by using the relevant test methods and experiment.The results showed that the electrical conductivity of collect was poor and some nozzles were blocked, which was the main reason led to the void, dimple value too larger causing the un-iflling phenomenon related to the bubble in bath.%针对VCP槽填孔过程中出现的空洞、凹陷值偏大、漏填等品质缺陷问题,对其产生原因进行深入分析,并通过组织相关测试手段及试验进行验证,试验结果表明:导电性不良,喷嘴堵塞是造成空洞、凹陷值偏大的主要原因。
漏填现象发生跟槽液中的气泡有关。
【期刊名称】《印制电路信息》【年(卷),期】2014(000)012【总页数】4页(P19-22)【关键词】填孔;空洞;凹陷值;漏填【作者】雷华山;于永贞;刘彬云;肖定军【作者单位】广东东硕科技有限公司,广东广州510245;广东东硕科技有限公司,广东广州 510245;广东东硕科技有限公司,广东广州 510245;广东东硕科技有限公司,广东广州 510245【正文语种】中文【中图分类】TN411 前言随着时尚消费类电子产品的不断更新换代,给PCB行业带来了更大的发展机遇。
镀金工艺的研究进展

镀金工艺的研究进展
科技风 "#"$ 年 $$ 月
詹秀玲4徐佩琳4马 进4孙 滔4杨富国!
佛山科学技术学院环境与化学工程学院!广东佛山!"#*%%%
摘4要本文重点介绍了氰化物镀金无氰镀金工艺综述了每种镀金工艺的基本组成镀金工艺参数等因素对镀层 和镀液体系性能的影响 在无氰脉冲电镀金铜合金工艺中镀层含有铜金元素镀层表面无裂纹平整性好孔隙率低 细致均匀镀层耐蚀性强结合力好硬度高镀液稳定性好电流效率高 对相关镀液体系中金的电沉积行为进行了总 结并对未来无氰电镀金工艺的发展方向进行了展望
&"&
理论研究
科技风 "#"$ 年 $$ 月
度均匀性的因素"通过单因素对比实验"研究阴极触点数 量&电场屏蔽板 开 孔 尺 寸& 旋 转 桨 与 晶 圆 间 距 和 旋 转 桨 转 速等因素对镀金层厚度均匀性的影响及其影响机理% 当 阴极触点数量为 $) 个"电场屏蔽板开孔尺寸为 0%RR"旋 转桨与晶圆的间距为 (RR"旋转桨转速为 $<%Q*R/- 时"可 得到最优的 3 英寸'$ 英寸 h)&93RR( 晶圆双面电镀金厚 度均匀性% 当电镀工艺目标镀层厚度为 3$R时"晶圆双 面镀层厚度均匀性可控制在 9:以内% 实验结果表明"晶 圆双面挂镀设备即可满足晶圆双面同时电镀"也可满足高 端芯片封装对镀层厚度均匀性的要求%
易"钛合金最难% 不锈钢和钛合金需要先镀上一层其他金 属' 打底层( %
集成电路封装材料-电镀材料

7.1 硅通孔电镀材料
7.1.1 硅通孔电镀材料在先进封装中的应用 7.1.2 硅通孔电镀材料类别和材料特性 7.1.3 新技术与材料发展
7.1.1 硅通孔电镀材料在先进封装中的应用
三维集成,存储器的三维堆叠、多芯片集成中的硅中介转接层,RF模 组、微机电系统及图像传感器的2.5 D及3D集成与组装。 在赛灵思(Xilinx)Virtex7 FPGA和三星电子面向服务器应用的 RDIMM DDR4 SRAM中都采用硅通孔技术。
7.1.2 硅通孔电镀材料类别和材料特性
硫酸铜体系材料价格较低,但工艺窗口窄;甲基磺酸铜体系工艺窗口宽, 但材料价格较高。 甲基磺酸铜体系中铜离子含量较高。实际应用中一般采用甲基磺酸铜体系。
7.1.2 硅通孔电镀材料类别和材料特性
添加剂主要作用是在电镀过程中将添加剂材料吸附(化学吸附和物理吸 附)到电镀阴极(待镀晶圆)表面等特定位置, 通过改变表面生长点浓度、表面吸附离子浓度、扩散系数及吸附离子表 面扩散的活化能等来影响电镀沉积的动力和生长机制, 从而对铜在阴极的沉积过程和晶体生长进行精确调控,实现改善电镀质 量的目标。
7.1.1 硅通孔电镀材料在先进封装中的应用
图7-5 Xilinx Virtex®-7 2000T FPGA 组装示意图
7.1.1 硅通孔电镀材料在先进封装中的应用
硅通孔电镀主要客户,几乎囊括了所有具备三维集成技术和量产能力的 晶圆制造及封测公司:英特尔、三星电子、台积电、中芯国际、日月光、 长电科技、通富微电、华天科技、晶方科技。 电镀液材料供应商:陶氏化学(Dow Chemical)、乐思化学(Enthone Chemical)、上村(Uyemura)、安美特(Atotech)、罗门哈斯 (Rohm&hass)、Pactech(2015年被长濑Nagase收购)及上海新阳。 电镀液供应商和电镀设备供应商合作,各自确认各自匹配程度。
盲孔电镀问题分析与改善
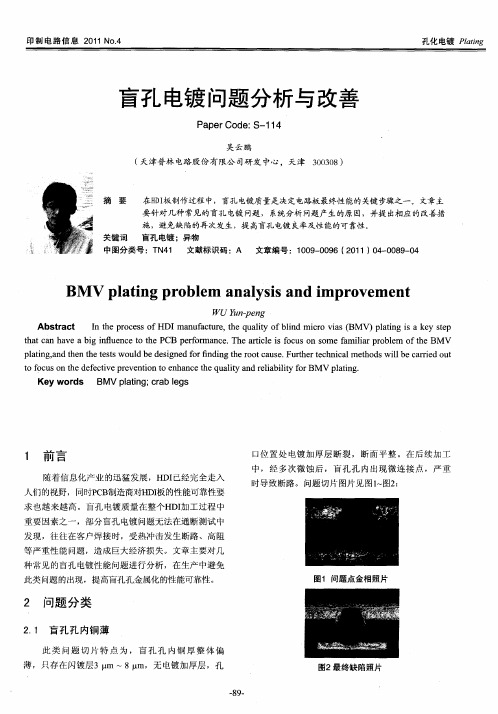
2 问题 分 类
2 1 盲子 孑 内铜薄 . LL
此 类 问 题 切 片 特 点 为 ,盲 孔 孔 内铜 厚 整 体 偏 薄 ,只存 在 闪 镀层 3 m ~8p m,无 电镀 加 厚层 ,孔
图2最终缺陷照片
图4 盲孔孔内异物
( )喷淋、循环管路 中,负压区漏气,气泡随 3
循环 管路进 入槽 电镀 液 中 。
2 3 盲子 电镀 “ . L 螃蟹脚 ”
t c s nted fciepe e t nt n a c eq ai n l bl r of u eet rv ni eh n et u lya dr i it f V lt g o o h v o o h t e a i o BM pai . y n
Key wor ds BMV a i g; r b lgs pltn c a e
求 也 越来 越 高 。盲孔 电镀质 量在 整 个H I 工 过程 中 D加
重要因素之一,部分盲孔 电镀 问题无法在通断测试中
发 现 ,往往 在 客户 焊接 时 ,受热 冲击 发生 断路 、 高阻 等 严重 性 能 问题 ,造 成 巨大 经济 损失 。文 章主 要对 几 种 常见 的 盲孔 电镀性 能 问题进 行 分析 ,在 生产 中避 免
1 前 言
随着 信 息化 产业 的迅 猛 发展 ,H I D 已经完 全走 入
人们 的视 野 ,同时P B C 制造 商对H 板 的性能可靠 性要 DI
口位 置 处 电镀 加 厚层 断裂 ,断 面 平 整 。在 后 续加 工
中 ,经 多 次 微 蚀后 , 盲孔 孔 内 出现 微 连 接 点 ,严 重 时 导致 断路 。 问题 切 片 图片 见 图 1图2 ~ :
深盲孔电镀铜填充的空洞机理研究

深盲孔电镀铜填充的空洞机理研究
陆敏菲;朱凯;钟荣军;王蒙蒙
【期刊名称】《印制电路信息》
【年(卷),期】2024(32)4
【摘要】电镀铜填孔技术被广泛用于高密度互连(HDI)板、封装基板和先进封装中,其中填孔的缺陷和效率问题是目前产业应用过程中最关注的两个方面。
重点研究了孔径约110μm、孔深约180μm的深盲孔电镀填孔过程中的空洞问题。
首先从理论上分析了填孔过程中镀层生长方式和空洞产生的原因;然后通过哈林槽电镀试验,结合加速剂局部预吸附技术,发现了盲孔底部加速剂和Cu^(2+)传质不足是深盲孔填孔产生空洞的关键原因。
研究表明:加速剂局部预吸附技术不仅可以缩短深盲孔电镀填孔时间,而且可以有效地降低深盲孔产生填孔空洞的风险;此外,通过提高气流量、镀液温度或Cu^(2+)浓度来加强深盲孔孔底Cu^(2+)传质对深盲孔填孔是非常必要的。
【总页数】8页(P20-27)
【作者】陆敏菲;朱凯;钟荣军;王蒙蒙
【作者单位】深南电路股份有限公司
【正文语种】中文
【中图分类】TN41
【相关文献】
1.MPS和氯离子在电镀铜盲孔填充工艺中的作用机理
2.加速剂局部预吸附提升电镀铜填充深盲孔技术研究
3.利用电镀铜填充微米盲孔与通孔之应用
4.《利用电镀铜填充微米盲孔与通孔之应用》-文彩图
5.镀铜填充盲孔的低电阻测试模块应用
因版权原因,仅展示原文概要,查看原文内容请购买。
HDI板微孔工艺介绍
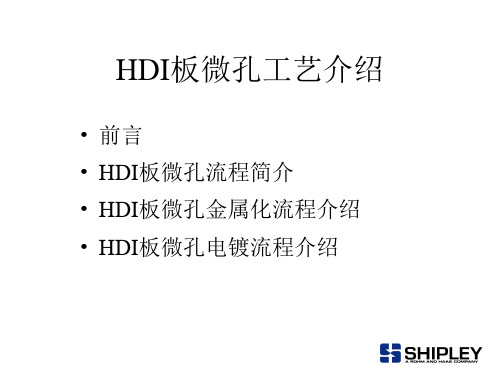
四. HDI板微孔电镀流程介绍
由于HDI板微孔特性,孔内传质效果差,所以孔内 电镀困难度较一般通孔要大。为改善孔内电镀层 品质,主要采用如下措施: • 降低电流密度,延长电镀时间。 • 优化镀液参数和电镀槽液计。 • 改垂直挂镀为水平挂镀。 • 改用反脉冲电镀。
• 碳黑基工艺(如 麦德美的BLACKHOLE)
碳黑基工艺与石墨基工艺相似。碳黑系统不需要选择 固定剂。 流程:
清洁剂
碳黑
空气刀/干燥
清洁剂
碳黑
空气刀/干燥
微蚀
• 导电聚合物(如DMS-E)
该工艺是在树脂及玻璃纤维表面上形成有机导电层。 流程:
溶剂调整
高锰酸钾
清洗
催 化剂
固定
干燥
板先在高温环境中(约90℃),以KMnO4进行氧化性的整 孔处理,使孔壁上先形成MnO2层,再浸入含Pyrrole
• 化学沉铜金属化微孔 由于化学沉铜过中,氧化还原过程中 产生H2,严重影响该工艺应用微孔金属 工艺,因为H2不是导致空洞,就是使沉 铜层变薄。
• 钯基工艺(如 Conduction DP-H)
钯基直接金属化工艺利用分散的钯的颗粒来使非导电 表面导电。 钯基工艺流程:
清洁/调整
微蚀
预浸
生产导电层
7. 改善RFI/EMI/ESD性能。 8. 提高布局效率。
二. HDI流程简介
• 华通Build up介绍 • 四种非机钻成孔方式介绍 • co2激光钻孔原理
三. HDI板微导通孔金属化流程
在HDI制作取得成功中,微导通孔金属化是保证微 孔导电及金属可靠性的关键因素。用来使导通孔 金属化的工艺有如下几种: • 化学沉铜 • 钯基直接金属化 • 石墨法 • 碳墨技术 • 导电聚合物
接插件镀金镀层常见质量问题分析

I电流、h板厚、k电导率、d孔径 上式说明电流越小电位差越小,降低电流密度 可使孔内镀层均匀。 我们通过生产实践:在加厚镀铜时我们延长时 间至35分钟,电流密度为1.7A/dm2,使铜层厚度为 12微米左右,图形镀铜把电流密度降至1.3A/din2, 电镀时间延长至90分钟,板厚为1.6毫米、孔径为 0.3毫米的印制电路板,经金相剖析厚度均为25~28 微米之间。
2.镀金层质量问题的产生原因
2 1金层颜色不正常 接插件镀金层的零件的金层颜色出现差 异,出现这种问题的原因是: 2.1 I镀金原材料杂质影响
当加入镀液的化学材料带进的杂质超过镀金液 的忍受程度后会很快影响金层的颜色和亮度。如果
是有机杂质影响会出现金层发暗和发花现象,郝尔 槽试片检查发暗和发花位置不固定。若是金属杂质 干扰则会造成电流密度有效范围变窄,郝尔槽试验 显示是试片电流密度低端镀不亮或是高端镀不亮低 端镀不上。反映到镀件上是镀层发红甚至发黑,其 孔内的颜色变化较明显。 2.1.2镀金电流密度过大
2.会议论文 沈涪 电镀质量问题分析处理案例 2008
对电镀质量问题的分析,首先应从电镀工序查找自身的原因,在排除了电镀所有条件(电镀设备、操作方式、工艺参数)的影响后,要向上工序逐级倒推一直查到镀件使用的基体材料的质量。近些年来,由于市场竞争激烈,而各种原材料又在不断涨价的情况下,镀件的基材加工厂会在降低材料等级和减少生产工序上想办法,实际上现在好多电镀质量问题也 确实跟基材质量有关。对于产品用户提出的电镀质量问题,除了要在电镀上工序查找原因外,还要在电镀的下工序查找原因,例如大家关注的镀金层变色问题就跟镀件的装配、运输、包装有一定的关系。
1)综合评述了国内军用电子设备中电接触元件在质量上存在的一些问题和镍打底镀金工艺的发展与应用,提出了与国外电连接器行业存在的差距,总结了电连接器接触体镀金常见质量问题并对其产生原因和解决办法进行了分析探讨,并论述电连接器接触体镍打底镀金工艺的宗旨和思想。 2)详细论述了镍打底镀金工艺的理论和方法。首先,介绍了镍打底镀金工艺研究的目的和理论依据;其次,对镀镍工艺进行了选择与优化,对镀镍机理、低应力镍机理和镀金阻挡层的选择原则进行了阐述。通过几种不同镀镍溶液中所获得镍镀层的物理性质及镀层孔隙率的对比,得出氨基磺酸盐镀镍是电连接器接触体镀镍的理想镀镍体系,并通过氨基磺酸 盐镀镍层内应力的影响因素分析及试验,对镀镍工艺进行了优化,得到了最佳电解液组成和工艺条件,同时对镀液的配制、维护和控制进行了阐述;最后对镀金机理和常用镀金工艺进行了分析,确定了适合本研究的镀金工艺,同时介绍了镀液的配制及镀液组成对镀液性能的影响。 3)介绍了镍打底镀金工艺流程,并从化学除油、酸洗、活化I、中和、预镀铜、活化II、氨盐镀镍、浸柠檬酸、柠檬酸盐镀金、镀后处理共10个方面对其主要工序进行了详细说明。 4)阐述了镀金层的质量检验与性能测试。从镀金层的质量要求、镀金层的质量检验和性能测试方法及试验结果3个方面进行了详细介绍,并对本章进行了小结。 5)阐述了镀金溶液的维护纯化和故障分析。从镀金溶液的维护和控制、镀金溶液的纯化和镀金溶液的常见故障及排除方法共3个方面进行了详细介绍。 6)最后,对全文进行总结。
高电流密度通孔电镀铜影响因素的研究

高电流密度通孔电镀铜影响因素的研究陈杨;程骄;王翀;何为;朱凯;肖定军【摘要】印制电路板在垂直连续电镀生产线上镀铜,通过改进电镀槽结构,引入喷流加强溶液交换等措施,能够使用更大的电流密度,大幅度提高产能.由于搅拌强度、电流密度和阴阳极距离等工艺条件发生改变,为了使微通孔电镀铜效果达到最优,对镀液成分配比进行优化实验.通过对镀铜层切片分析,确定光亮剂浓度和电流密度为影响电镀的显著因素.在优化控制条件下,采用的电镀液对厚径比为6.4∶1.0的通孔(d =0.25 mm)镀铜,铜层的均镀能力达到80%以上,具有很好的实用价值.【期刊名称】《电镀与精饰》【年(卷),期】2015(037)008【总页数】5页(P23-27)【关键词】印制电路板;高速电镀铜;优化实验设计;添加剂;均镀能力【作者】陈杨;程骄;王翀;何为;朱凯;肖定军【作者单位】电子科技大学应用化学系,四川成都610054;广东光华科技股份有限公司,广东汕头515061;广东东硕科技有限公司,广东广州510663;电子科技大学应用化学系,四川成都610054;广东光华科技股份有限公司,广东汕头515061;电子科技大学应用化学系,四川成都610054;广东光华科技股份有限公司,广东汕头515061;电子科技大学应用化学系,四川成都610054;广东光华科技股份有限公司,广东汕头515061【正文语种】中文【中图分类】TQ153.14引言随着印制线路板(PCB)向着“短、小、轻及薄”的快速演进,对微小通孔和高厚径比板件电镀制作要求也越来越高[1],目前高厚径比微通孔和精细线路的电镀铜是一大难题[2]。
尽管脉冲电镀能较好地解决高厚径比微通孔的电镀问题,但也存在明显的缺陷[3]:1)脉冲电源昂贵,投资大,维护成本高;2)脉冲电源与电镀槽之间连接要求高,连接不当或接触不好都会影响电镀效果;3)脉冲电镀需要使用特殊化学添加剂。
因此,直流电镀仍然是PCB电镀铜最常用的方法。
导电聚合物用于微盲孔直接电镀工艺的常见问题与对策

导电聚合物用于微盲孔直接电镀工艺的常见问题与对策刘彬云;肖亮;何雄斌【摘要】The conductive polymer film was applied to direct electroplating process for metallization of microvias in fabrication of printed circuit board (PCB). The main process flow including smear removal, conductive organic film formation, and copper electroplating was introduced. The common problems occurred during experiments and production were summarized and some countermeasures were given.%将导电聚合物膜应用于印制电路板(PCB)制造的微盲孔金属化直接电镀工艺中.介绍了主要工艺流程,包括除胶渣、有机导电膜工艺和电镀铜.总结了实验和生产过程中的常见问题,并给出了相应的解决对策.【期刊名称】《电镀与涂饰》【年(卷),期】2018(037)008【总页数】6页(P350-355)【关键词】印制电路板;微盲孔;金属化;直接电镀铜;导电聚合物膜;除胶渣【作者】刘彬云;肖亮;何雄斌【作者单位】广东东硕科技有限公司,广东广州 510288;广东东硕科技有限公司,广东广州 510288;广东东硕科技有限公司,广东广州 510288【正文语种】中文【中图分类】TQ153.14;TG178在印制电路板(PCB)制造工艺中,层间电路导通是靠通孔或盲孔金属化来完成的。
传统工艺一般都采用以甲醛为还原剂的化学镀铜层为底层。
但甲醛毒性大,是一种致癌物质,并且含有铜离子、镍离子、钯离子和配位剂的化学镀铜废液难以处理。
机械表零件电镀常见故障类型分析与改进

第49卷第9期2021年5月广州化工Guangzhou Chemical IndustryVol.49No.9May.2021机械表零件电镀常见故障类型分析与改进朱敬洪(杭州手表有限公司,浙江杭州311108)摘要:电镀是机械手表厂的一个非常重要的部门,制作机械手表机芯零件所用的材料多为黄铜和碳钢,为达到美观、防腐、抗磨损的艺术和物理效果,通常都需要进行电镀处理.手表零件本身具有形状复杂、盲孔多、加工方式多、零件小、精度要求高等特点。
同时国内机芯厂多为原来的国营老厂,电镀车间普遍具有规模小,镀种多,多种操作方式混合的特点。
本文主要讨论了手表零件在电镀过程中产生的典型故障类型,并介绍了一些改进方法。
关键词:前处理;盲孔电镀;热处理;超声波中图分类号:TQ153.1文献标志码:A文章编号:1001-9677(2021)09-0146-02Analysis and Improvement of Common Faults in Electroplatingof Mechanical Watch PartsZHU Jing-Hong(Hangzhou Watch Co.,Ltd.,Zhejiang Hangzhou311108,China)Abstract:Electopiating is a very important department in mechanical watch ually the materials of mechanical watch movement parts are brass and carbon steel.In onlei*to achieve beautiful,anticorrosive,anti-wear art and physical effects,it usually needs to be electroplated treatment.The watch part itself has the characteristics of shape complex,many blind holes,many of processing,small parts,precision required.At the same time,most of the domestic core factory for the original state-owned old factory,electroplating workshop generally has the charactertics of small scale, more kinds of plating and mixed operation.The typical faults in the process of electroplating and analysis were mainly discussed,some improvement methods were introduced・Key words:pre-processing;blind hole plating;heat-treat;ultrasonic在制造机械表机芯零件过程中,电镀是不可或缺的一个部门,由于国内机芯制造厂一般为原国营单位延续而来,工艺设备普遍比较陈旧,但镀液维护普遍比较规范,电镀问题的产生一般在其它原因,本文主要针对对零件本身形状特点和机械加工的特点对于电镀问题产生进行粗浅的分析,并谈谈自己的一些看法O制作机械表机芯零件的常用材料有:铅黄铜,皱青铜,碳钢,不锈钢。
高纵横比盲孔电镀铜填孔技术改进

高纵横比盲孔电镀铜填孔技术改进夏海;谢慈育;丁杰;郝意【摘要】随着盲孔填孔产品及工艺的发展,越来越多的注意力被放在了高纵横比微盲孔的填孔技术开发上.目前高纵横比微盲孔填孔中经常出现包芯,面铜厚等问题.本文研究了通过特殊的分子结构设计以及工艺改进,极大的改善了高纵横比微盲孔的填孔表现.【期刊名称】《印制电路信息》【年(卷),期】2018(026)012【总页数】4页(P31-34)【关键词】盲孔填孔;高纵横比;电镀铜;添加剂【作者】夏海;谢慈育;丁杰;郝意【作者单位】深圳市板明科技有限公司,广东深圳 518105;深圳市板明科技有限公司,广东深圳 518105;深圳市板明科技有限公司,广东深圳 518105;深圳市板明科技有限公司,广东深圳 518105【正文语种】中文【中图分类】TN410 前言印制电路板在电子设备中提供电子元器件电气沟通的渠道,由它们构成的三维铜线路网络为每一个芯片、电容及电阻等器件能够正常工作提供了可靠保证[1]。
水平方向的铜线路可以由加减铜来完成,垂直方向的铜线路则一般依靠通盲孔以及相互的叠孔来实现[2]。
针对孔径较小的微孔,目前通孔的填孔是业界的一个重点,如果需要实现多层之间在垂直方向的电气相通,一般是采用叠孔的方式来实现,然而多层的叠孔会出现成本大且孔对位等问题。
盲孔填孔技术一般是针对厚径比小于0.8的“浅”盲孔,而厚径比大于0.8,甚至大于1的“深”盲孔填孔是业界急切想要开发的一项技术[3]。
目前填孔技术虽然可以实现纵横比大于1:1的高纵横比微盲孔填孔,但在一定程度上要解决叠孔还可能存在如何有效的降低企业生产成本及孔对位产生的安全隐患问题。
1 添加剂材料设计与作用原理1.1 包芯出现的原因在盲孔的电镀填孔过程中,特别是高纵横比的盲孔填孔实验中,经常会出现包芯(空洞void)现象。
包芯的存在会降低信号传输速率并降低导线的电致迁移耐力,同时存在一定的机械强度方面的隐患[4]。
石墨烯孔金属化制程的重大突破

石墨烯孔金属化制程的重大突破方景礼;陈伟元【摘要】石墨烯是一种集多功能优异特性于一身,可使各种制造业发生革命性变格的新材料.我们克服了石墨烯难以剥离、难溶于水、难以稳定地分散在水溶液中等难题,系统完成了各种柔性和刚性印制板直接用石墨烯水溶液进行孔金属化的小试、中试和工业化生产的考核,实现了用石墨烯工艺取代污染严重和成本高昂的化学镀铜工艺,使我国成为石墨烯金属化工艺应用于工业化生产的第一个国家.本文详细介绍了石墨烯的结构、性能、制造方法以及化学镀铜、直接电镀、氧化石墨烯和石墨烯孔金属化等工艺的流程、性能和优缺点.【期刊名称】《印制电路信息》【年(卷),期】2019(027)004【总页数】7页(P33-39)【关键词】石墨烯;氧化石墨烯;印制电路板;孔金属化【作者】方景礼;陈伟元【作者单位】南京大学化学系,江苏南京210093;赛姆烯金科技有限公司,广东深圳518000【正文语种】中文【中图分类】TN411 石墨烯概念1.1 石墨烯的发现石墨烯的概念早在1947年提出[1],它本来就存在于石墨中,只是难以剥离出单层结构。
2004年英国曼彻斯特大学物理学家在实验室中,从高定向热解石墨中剥离出石墨片,然后将薄片的两面粘在一种特殊的胶带上,撕开胶带,就能把石墨片一分为二。
不断重复这一操作,薄片就变得越来越薄,最后得到了仅由一层碳原子构成的薄片,这就是石墨烯。
随后石墨烯材料的研究受到世界各国的高度关注,大都启动了相关研究计划和项目,力争把石墨烯材料技术和产业革命的主动权和先机掌控在手。
1.2 石墨烯的定义与结构在国家标准《石墨烯材料的术语、定义及代号》中对石墨烯定义如下:石墨烯是指由一个碳原子与周围三个近邻碳原子结合形成蜂窝状结构的碳原子单层;石墨烯材料则是由石墨烯作为结构单元堆垛而成的,层数少于10层,可独立存在或进一步组装而成的碳材料的统称。
单层石墨烯材料只有一个碳原子厚,即0.335 nm,1 mm厚的石墨中约有150万层左右的单层石墨烯材料。
- 1、下载文档前请自行甄别文档内容的完整性,平台不提供额外的编辑、内容补充、找答案等附加服务。
- 2、"仅部分预览"的文档,不可在线预览部分如存在完整性等问题,可反馈申请退款(可完整预览的文档不适用该条件!)。
- 3、如文档侵犯您的权益,请联系客服反馈,我们会尽快为您处理(人工客服工作时间:9:00-18:30)。
直流电镀在微孔、盲孔镀中的重大突破林金堵随着PCB高密度的快速发展与进步,特别是微小孔的高厚径比孔电镀、盲孔电镀和填孔电镀等的要求,传统直流电镀便受到了致命的挑战,它似乎解决不了这些‘高端’孔的电镀和填孔镀问题,因此,近10年来,脉冲电镀工艺技术便在PCB工业中迅速推广应用开来。
尽管脉冲电镀工艺技术能够很好地解决微小孔的高厚径比孔电镀、盲孔电镀和填孔电镀的问题,但是,脉冲电镀工艺技术存在着明显的缺点:(一)脉冲电源昂贵,投资很大;(二)脉冲电源到电镀槽之间的连接要求高,连接不当或接触不好,会严重延长脉冲前沿时间(t r,rise time),从而影响电镀效果;(三)在脉冲电镀过程中仍然需要特殊化学填加剂,才能获得好的微小孔的高厚径比的孔电镀、盲孔电镀和填孔电镀的效果。
因此,在传统直流电镀的基础上,能否通过新的电镀化学添加剂和合适的电镀参数(如搅拌方法与方式等)来改变铜离子在镀液中的运动与分布,从而获得良好的高厚径比孔电镀、盲孔镀和填孔镀呢!这是业界十分关注的一大问题。
近几年来,在这些方面的研究、实验和应用的事实已经证明,采用特种电镀填加剂和合适的电镀参数的直流电镀,能够克服传统直流电镀的缺点,完全能很好地满足微小孔的高厚径比孔电镀、盲孔电镀和填孔电镀等的要求。
因此,采用新型的化学添加剂的直流电镀在PCB 工业中将会迅速推广应用开来,直流电镀仍然是PCB工业主要和根本的方法。
1 传统直流电镀面临的挑战传统直流电镀在印制电(线)路板的应用历史已经超过50多年了,传统直流电镀在PCB 的层间、表面涂(镀)覆所起作用是极其重要的,PCB有今天,传统直流电镀功不可没!但是,传统直流电镀存在着致命缺点,特别是在20世纪80年代中期以来,PCB组装技术从通孔插装(THT)技术走上表面安装技术(SMT)后,导通孔尺寸迅速的减小,特别是出现HDI/BUM板以来,传统直流电镀受到越来越严厉的挑战和压力!⑴传统直流电镀在孔内电流密度分布呈‘梯度’递减在通孔电镀铜时,由于电流密度分布的原因,传统直流电镀的致命缺点是从孔口到中心处,其镀层厚度成‘梯度’方式而减薄,使孔中心处形成最薄的镀层,影响PCB质量和可靠性。
尽管,可采用传统的化学添加剂(如分散剂、整平剂等)、降低电流密度值(牺牲生产率为代价,往往是不合算的)和搅拌等方式来减小这个镀层厚度‘梯度’。
但是,这些努力远跟不上孔径微小化的发展要求。
⑵高厚径比微小孔电镀难题在酸性硫酸铜镀液中,传统直流电镀所造成的板面与孔内镀层厚度差别主要是由板的厚度(孔的深度)和孔径尺寸来决定的。
即直流电镀时,通孔内的欧姆电阻E为E=JL2/2Kd-------------------(1)式中:J-----阴极电流密度;L-----孔的深度(板厚度);K-----电导率(受H2SO4影响最大,H2SO4浓度大,K就大);d-----孔的直径。
还可导出孔的电镀‘难度系数’D。
D=L2/d------------------------(2)从这两个公式中可以看到:(一)若通孔的深度L(板厚)不变,则孔内的欧姆电阻E将随着孔径微小化而提高,阻止Cu2+离子向孔内沉积将越来越大,则孔内电镀铜越来越困难;(二)传统直流电镀通孔时,电镀‘难度系数’D是与孔深度的平方成正比,跟孔直径成反比,或者更直观地说,传统直流电镀的‘系数难度’D是与孔的深度(L,板厚)和厚径比(L/d)成正比。
因此,传统直流电镀通孔时,其孔内的铜镀层厚度‘梯度’将随着孔的深度(板厚度)和厚径比(孔径微小化)的增加而急剧严重化起来!对于传统直流电镀常规的PCB,其厚径比≤6:1的通孔镀,电镀分散能力为65%到85%。
一般说来,这种电镀分散能力还是可以保证通孔连接的可靠性。
而对于厚径比≥8:1的通孔镀,传统直流电镀的电镀分散能力≤50%,这是很难保证导通孔的连接可靠性的。
⑶微小盲孔电镀的要求随着表面安装技术的深化发展,PCB板已开始由常规多层板(含埋/盲孔结构)走向HDI/BUM 板,其积层(a+n+b,n为芯板的层数,a和b为高密度积层的层数)的层数越来越多,因而盲孔镀将越来越多。
采用盲孔结构和盲孔电镀方式是常规PCB走向更高密度的HDI/BUM板的必由之路。
盲孔结构和盲孔电镀是不同于通孔电镀的。
由于盲孔仅一面孔口与镀液接触,镀液很难在盲孔内流动和进行新旧溶液交换。
加上在HDI/BUM板中,其积层的盲孔直径很小≤0.2mm,厚径比0.5∽1.5之间。
所以,传统直流电镀是很难胜任盲孔电镀的。
⑷微小盲孔填孔镀的挑战在‘多阶’(a+n+b)结构的HDI/BUM板的盲孔的叠层连接(特别是叠孔连接结构)上,无论从可靠性、导热和加工技术等角度上,目前都要求采用填孔镀技术。
盲孔填孔镀铜技术,就是要求做到在盲孔的底部和孔内的电沉积铜的速度要远大于板表面的沉积铜的速度才行。
实际上,由于HDI结构和今后三维结构的要求,不仅盲孔结构需要填孔,而且通孔结构也需要填孔,才能保证GDI/BUM板和IC基(载)板的导热性、可靠性的基本要求。
首先是PCB的高多层(如20层以上)化,接着的是通孔微小(如孔径≤φ0.3mm,高厚径比大于≥6时)化,加上近10年来的盲孔镀和盲孔填孔镀等要求,传统直流电镀受到越来越严厉的挑战和压力!一段时间以来,脉冲(周期性反向)电流电镀、导电胶(膏)填孔等有取代之势。
但是,任何事物总是在矛盾中向前发展着,由于科学技术的持续发展与进步,看似不可能达到的事情,通过人们的能力和工艺技术的创新,把原来认为‘不可能’的事情变成了活生生的现实!如数控钻床曾经怀疑过,对直径小于Ф300µm不能进行钻孔或成本太高等问题。
但是,近10年来,数控钻床的转速已由10年前12万转/分提高到现在18、20或25万转/分,甚至达到35万转/分,加上钻床主轴和移动台面的稳定性提以及微小钻头技术(特别是纳米技术)的解决,现在的数控钻孔直径可达到Ф100µm,甚至达到Ф50µm。
同理,直流电镀对高厚径比的通孔、特别是盲孔镀和盲孔填孔镀等似乎不能胜任的,但是现在已经能够完全解决了这个问题。
近几年来,在这些方面的研究、实验和应用的事实已经证明,采用特种电镀填加剂和合适的电镀参数的直流电镀,能够克服传统直流电镀的缺点,完全能很好地满足微小孔的高厚径比孔电镀、盲孔电镀和填孔电镀等的要求。
如我在江南计算技术研究所于2005年就看到采用直流电镀来解决HDI的盲孔镀和盲孔填孔镀的技术课题,并用于批量生产。
在2007年的《Circuitree》,NO1的杂志上也报道了美国UYEMURA公司的酸性铜‘直流电镀’的效果;同期《Circuitree》杂志上,George Milad在“Innovative solutions for leading edge design”也提到采用‘直流电镀’在高厚径比通孔镀、盲孔镀和盲孔填孔镀等方面取得了良好的效果,其性能/价格比脉冲电镀要好得多,而且质量也可与之相媲美,比起导电胶等填孔的导通性能就好多了。
因此,采用新型的化学添加剂的电镀方法应该是最根本的出路!正是在直流电镀中采用了新型化学添加剂,才使传统直流电镀也能在高厚比的微小通孔、盲孔上实现电镀铜和填孔镀铜。
因此,采用新型的化学添加剂的直流电镀在PCB 工业中将会迅速推广应用开来,直流电镀仍然是PCB工业主要和根本的方法。
2 直流电镀的突破机理在高密度安装的HDI/BUM板、IC封装基(载)板中,总是存在着大量的盲孔结构和少量的通孔结构的,由于HDI结构和今后三维结构的要求,不仅盲孔结构需要填孔,而且通孔结构也需要填孔,才能保证HDI/BUM板和IC基(载)板的工艺(可制造)性、导热性、可靠性的基本要求。
但是,由于盲孔结构与通孔结构是不同的。
在通孔中,在搅拌等条件下,镀液在板的两面形成‘压力差’(日如搅拌、喷射等)下可进行流动和新、旧溶液交换,有可能得到较好的铜沉积厚度。
而在盲孔中的镀液,由于镀液在孔中的流动和新、旧溶液交换,完全仅靠板面的一个‘开口’来进行,特别是盲孔的底部靠搅拌、喷射等动态冲击力来达到目的是困难的。
因此,盲孔镀和盲孔填孔镀必须采用其它方法(式),或者说采用与通孔镀和通孔填孔镀不同的方法,才能达到目的。
实际上,不管是盲孔、还是通孔进行直流电镀(含填孔镀),在一定直流电镀(参数)条件下,主要是通过化学添加剂(如抑制剂、整平剂和加速剂等)的控制(吸附)而完成的,其次是适当进行搅拌(机械的或物理的)辅助完成的。
(1)通孔直流电镀和填孔镀在通孔(TH)直流电镀和填孔镀中,抑制剂(又有整平剂作用,也可含另类整平剂)等在适当搅拌条件下,主要是依靠通孔的形貌(feature profile)的电位E{见公式(1)和(2),E将随着孔径微小化、厚径比增加而提高的,其电流密度将减少}高低而进行吸附的,而以添加的抑制剂具有强烈吸附高电流密度部位(区域)的,不仅使PCB板面吸附抑制剂厚度或数量远大与孔内,而且使孔内的抑制剂的吸附形成从孔口到孔中心处形成浓度差,并且在电镀过程中应该迅速建立起这种浓度差分布,所以,在PCB中,最快的铜沉积速度发生在孔中心处。
在通孔(TH)直流电镀和填孔镀中,调整合适的镀液的流动速度(搅拌或喷射等方法)可以保证添加剂(主要是抑制剂)最合理的吸附厚度与浓度梯度分布,才能达到效果。
过大的镀液的流动速度(搅拌或喷射等方法),会破坏添加剂(主要是抑制剂)最合理的吸附厚度与浓度梯度分布,将达不到预定的效果。
同样,太小的镀液的流动速度(搅拌或喷射等方法),不能满足添加剂(主要是抑制剂)最合理的迁移速度的要求,难于吸附到高密度区域和形成浓度梯度分布,因此也难达到预期的效果。
实验研究表明:(一)添加的抑制剂,其吸附高电位的部位程度,不仅与电位E高低有关,而且还与镀液流动速度有关,这就是说,除了添加适当的抑制剂含量外,还可以通过调整镀液的流动速度来改善通孔直流电镀和填孔镀;(二)由于是通孔结构,不像盲孔有底部的结构,因而不必加入加速剂,因为加入加速剂容易在通孔的两个孔口部位聚集加速剂,从而在通孔的填孔镀中的孔中心形成‘空洞’问题,参见图1的(a)。
后者,实际上是可以通过加速剂的添加量和调整镀液流动速度(搅拌程度)来解决的。
(2)盲孔直流电镀和填孔镀由于目前的HDI/BUM板、特别是IC基板的导通孔(即盲孔)的直径已经微小化到25μm ∽50μm尺寸范围,对于这样微小的盲孔尺寸,仅仅在孔壁上形成金属化的传统电镀方法是难于满足技术指标和性能要求的,必须采用电镀填孔镀铜才行。
在盲孔直流电镀和填孔镀中,同理,抑制剂(又有整平作用,也可含另类整平剂)等在适当搅拌条件下,主要是依靠通孔的形貌(feature profile)的电位E{见公式(1)和(2),E将随着孔径微小化、厚径比增加而提高的,其电流密度将减少}高低而进行吸附的,而以添加的抑制剂具有强烈吸附高电流密度部位(区域)的,不仅使PCB板面吸附抑制剂厚度或数量远大与孔内,而且使孔内的抑制剂的吸附形成从孔口到孔中心处形成浓度差,因此孔壁能够得到最快的铜沉积速度。