石灰生产工艺操作规程
石灰工序岗位安全操作规程

石灰工序岗位安全操作规程一、总则1.1 为了保障石灰工序岗位操作人员的人身安全和设备设施的安全,制定本安全操作规程。
本规程适用于石灰生产工艺中的各岗位操作人员。
1.2 本规程的遵守是每个操作人员的责任,任何人都有权对违反本规程的行为进行指正和纠正,并有权向主管部门进行汇报。
1.3 本规程是石灰生产工序操作人员执行的基本规范,各岗位操作人员必须认真、准确、按要求进行操作,确保操作的安全、可靠、稳定。
二、岗位安全操作规程2.1 石灰石料的运输2.1.1 在运输石灰石料时,操作人员必须穿戴防护装备,包括头盔、防尘口罩、耐酸手套等。
2.1.2 在搬运石灰石料过程中,严禁石灰石料碰撞、掉落或其他不当操作,确保石灰石料的完整性和操作人员的安全。
2.1.3 石灰石料的运输车辆必须经过检查和维护,确保车辆运行的安全可靠。
2.1.4 石灰石料的搬运过程中,操作人员必须注意不要超过车辆的承载极限,确保不会因超载导致车辆翻车或损坏。
2.2 石灰窑的操作2.2.1 在石灰窑操作过程中,操作人员必须穿戴防护装备,包括耐高温工作服、防护手套、防护眼镜等。
2.2.2 在进入石灰窑之前,必须进行安全检查,确保石灰窑内无有毒有害气体和无其他安全隐患。
2.2.3 在操作石灰窑时,要严格按照操作规程进行操作,严禁擅自更改操作参数或进行其他违规操作。
2.2.4 在石灰窑操作过程中,应注意石灰窑内的温度和气体浓度,避免高温和有毒有害气体对操作人员的伤害。
2.3 石灰石的破碎和研磨2.3.1 在石灰石的破碎和研磨过程中,操作人员必须穿戴防护装备,包括防护眼镜、防尘口罩、耐酸手套等。
2.3.2 在操作石灰石破碎和研磨设备时,应按照操作规程进行操作,严禁进行不规范操作,确保设备的安全和操作人员的安全。
2.3.3 石灰石破碎和研磨设备的维护和保养应定期进行,确保设备的正常运行和安全可靠。
2.3.4 在石灰石破碎和研磨过程中,应及时清理设备周围的石灰石粉尘,避免粉尘积聚引发火灾或爆炸。
石灰烧制岗位操作规程
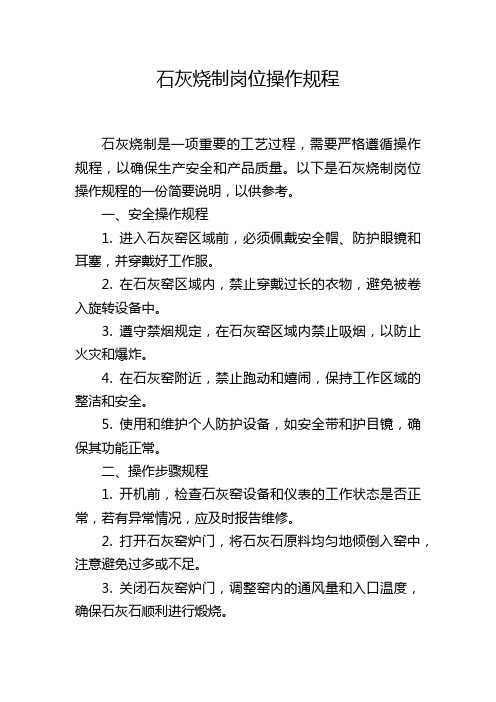
石灰烧制岗位操作规程石灰烧制是一项重要的工艺过程,需要严格遵循操作规程,以确保生产安全和产品质量。
以下是石灰烧制岗位操作规程的一份简要说明,以供参考。
一、安全操作规程1. 进入石灰窑区域前,必须佩戴安全帽、防护眼镜和耳塞,并穿戴好工作服。
2. 在石灰窑区域内,禁止穿戴过长的衣物,避免被卷入旋转设备中。
3. 遵守禁烟规定,在石灰窑区域内禁止吸烟,以防止火灾和爆炸。
4. 在石灰窑附近,禁止跑动和嬉闹,保持工作区域的整洁和安全。
5. 使用和维护个人防护设备,如安全带和护目镜,确保其功能正常。
二、操作步骤规程1. 开机前,检查石灰窑设备和仪表的工作状态是否正常,若有异常情况,应及时报告维修。
2. 打开石灰窑炉门,将石灰石原料均匀地倾倒入窑中,注意避免过多或不足。
3. 关闭石灰窑炉门,调整窑内的通风量和入口温度,确保石灰石顺利进行煅烧。
4. 定期检查窑内的煅烧温度和炉内氧气含量,确保石灰石充分煅烧,控制石灰石产量和质量。
5. 确保石灰窑的冷却系统正常运行,以保证石灰石的冷却效果。
6. 定期清理石灰窑内的积灰,保持窑内的通风畅通和设备正常工作。
三、质量控制规程1. 定期抽样检查石灰石的化学成分和物理性能,确保产品符合质量标准。
2. 定期检查石灰窑设备的运行状态,及时发现和排除设备故障,避免对产品质量的影响。
3. 关注烧结过程中产生的尾气排放情况,确保排放符合环保要求,减少对环境的污染。
4. 监测石灰石的产量,及时调整石灰石的投料量和煅烧参数,以保持生产计划和产品供应的一致性。
四、应急处理规程1. 在石灰烧制过程中,如发现设备异常响声、异味或冒烟等情况,应立即停机检修。
2. 如遇窑内温度过高或过低、石灰石产量异常等情况,应及时调整运行参数或采取紧急措施。
3. 如窑内发生火灾或其他安全事故,应立即向相关部门报警,并采取紧急撤离措施,确保人员安全。
以上是石灰烧制岗位操作规程的简要说明,实际操作应根据具体情况进行调整和完善。
石灰生产工艺操作规程
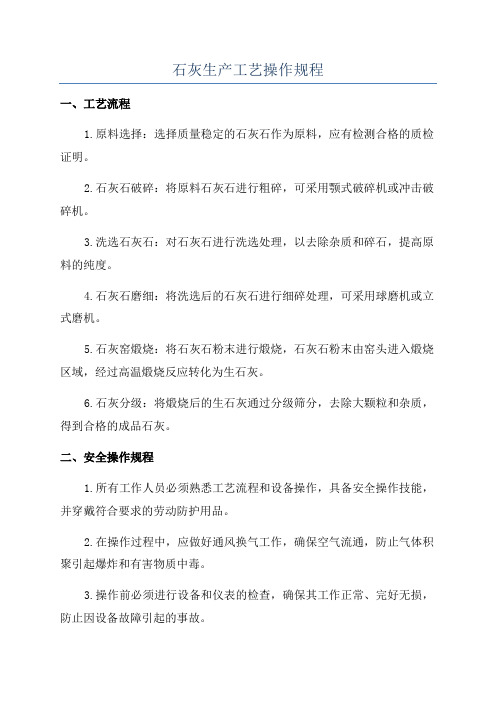
石灰生产工艺操作规程一、工艺流程1.原料选择:选择质量稳定的石灰石作为原料,应有检测合格的质检证明。
2.石灰石破碎:将原料石灰石进行粗碎,可采用颚式破碎机或冲击破碎机。
3.洗选石灰石:对石灰石进行洗选处理,以去除杂质和碎石,提高原料的纯度。
4.石灰石磨细:将洗选后的石灰石进行细碎处理,可采用球磨机或立式磨机。
5.石灰窑煅烧:将石灰石粉末进行煅烧,石灰石粉末由窑头进入煅烧区域,经过高温煅烧反应转化为生石灰。
6.石灰分级:将煅烧后的生石灰通过分级筛分,去除大颗粒和杂质,得到合格的成品石灰。
二、安全操作规程1.所有工作人员必须熟悉工艺流程和设备操作,具备安全操作技能,并穿戴符合要求的劳动防护用品。
2.在操作过程中,应做好通风换气工作,确保空气流通,防止气体积聚引起爆炸和有害物质中毒。
3.操作前必须进行设备和仪表的检查,确保其工作正常、完好无损,防止因设备故障引起的事故。
4.严禁在操作过程中闲聊、喧哗或违反规定的行为,确保工作人员专注于操作任务。
5.操作人员必须熟悉应急措施和设备停机操作,遇到异常情况或突发事件时能够及时处理。
三、质量控制规程1.原料进货前必须进行检测,检查其化学成分和物理性质是否合格,确保原料质量稳定。
2.对于石灰石的破碎、洗选和磨细工序,必须控制好破碎度、洗选效果和细度,确保原料的质量要求。
3.煅烧过程中,必须控制好煅烧温度、时间和窑炉内的气氛,确保石灰石能够完全转化为生石灰。
4.石灰的分级工序必须进行筛分分析,对不合格品进行再处理或淘汰,以确保成品的质量达标。
5.对成品石灰进行抽样检验,检测其化学成分和物理性质,确保产品的质量符合标准要求。
四、设备维护规程1.设备操作人员必须定期进行设备维护,清理设备内部的灰尘和杂物,保证其正常运行。
2.设备运行中,如发现异常情况、设备故障或机械部分有异响等现象,应及时停机进行检修,确保设备的安全和稳定运行。
3.对于易磨损的设备零部件,必须定期检测并更换,以延长设备的使用寿命和保证操作的稳定性。
石灰工序岗位安全操作规程模版

石灰工序岗位安全操作规程模版一、岗位背景与职责1.1 岗位背景:石灰工序是石灰生产过程中的重要环节,包括石灰石的运输、破碎、煅烧和石灰石粉的处理等环节。
1.2 岗位职责:- 进行石灰石的装车、装卸工作;- 进行石灰石的破碎、筛分等加工工作;- 掌握石灰石粉的处理工艺和设备操作;- 协助维护和修理石灰工序设备。
二、岗位安全操作规程2.1 装卸作业安全操作规程- 在进行装卸作业前,必须佩戴符合安全要求的头盔、防护鞋等个人防护装备。
- 在装卸操作时,要确保货物固定稳定,防止货物倾倒或滑落。
- 使用起重设备进行装卸作业时,必须检查设备的安全性和可靠性,并按照操作规程进行操作。
- 禁止超载操作,严禁人员站在货物上进行装卸作业。
- 在装卸作业结束后,要清理场地和设备,确保安全畅通。
2.2 加工工作安全操作规程- 在进行石灰石的加工工作前,必须佩戴符合安全要求的防尘口罩、护目镜等个人防护装备。
- 检查加工设备的安全性和可靠性,如发现异常情况要及时报告维修人员。
- 加工作业时,必须按照规定的设备操作步骤进行操作。
- 在加工作业过程中,严禁将手部或其他身体部位靠近机械设备,防止意外伤害。
- 在加工作业结束后,要清理设备和工作区域,保持工作环境整洁。
2.3 石灰石粉处理安全操作规程- 在进行石灰石粉处理工作前,必须佩戴符合安全要求的防尘口罩、护目镜、防护手套等个人防护装备。
- 检查石灰石粉处理设备的安全性和可靠性,如发现异常情况要及时报告维修人员。
- 进行石灰石粉处理时,要注意操作环境的通风和防尘措施,防止粉尘对人体的危害。
- 在处理石灰石粉时,严禁使用有火源的设备或工具,以防止引发火灾或爆炸事故。
- 在处理结束后,要清理设备和工作区域,保持整洁,并将废料妥善处理。
2.4 设备维护与修理安全操作规程- 在进行设备维护和修理前,必须佩戴符合安全要求的工作服、防护手套等个人防护装备。
- 关闭设备电源或切断工作介质,确保维护和修理的安全性。
石灰工序岗位安全操作规程
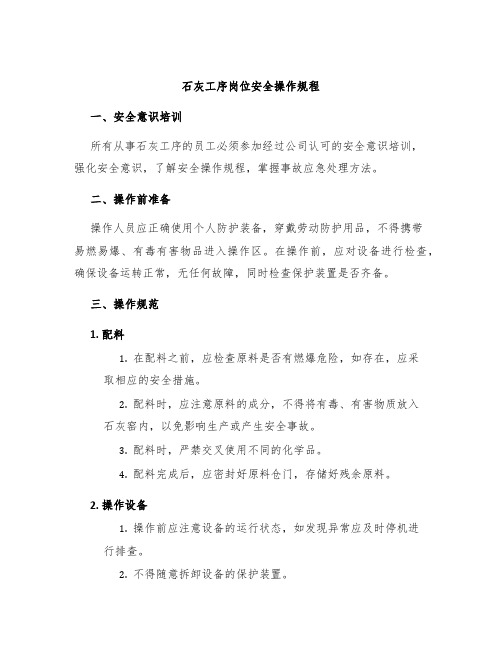
石灰工序岗位安全操作规程一、安全意识培训所有从事石灰工序的员工必须参加经过公司认可的安全意识培训,强化安全意识,了解安全操作规程,掌握事故应急处理方法。
二、操作前准备操作人员应正确使用个人防护装备,穿戴劳动防护用品,不得携带易燃易爆、有毒有害物品进入操作区。
在操作前,应对设备进行检查,确保设备运转正常,无任何故障,同时检查保护装置是否齐备。
三、操作规范1. 配料1.在配料之前,应检查原料是否有燃爆危险,如存在,应采取相应的安全措施。
2.配料时,应注意原料的成分,不得将有毒、有害物质放入石灰窑内,以免影响生产或产生安全事故。
3.配料时,严禁交叉使用不同的化学品。
4.配料完成后,应密封好原料仓门,存储好残余原料。
2. 操作设备1.操作前应注意设备的运行状态,如发现异常应及时停机进行排查。
2.不得随意拆卸设备的保护装置。
3.操作设备时,应严格按照工艺流程要求进行操作,不得擅自操作。
4.对设备进行清洁保养时,应注意个人安全,确保停车后才进行维修保养。
3. 工作区域安全1.岗位操作人员应认真遵守各项安全规程,不得擅自私自下地,行动甚至跨越到其他工作区域。
2.工作时应注意俯仰邻位存在异样动作或存在危险操作。
3.抽样检测时,应在安全的区域进行,确保个人安全。
4.严格遵守公司消防规程,不得乱丢烟蒂或进行随意的吸烟。
四、危险品处理1.在石灰窑出现危险品泄漏事件时,应及时采取措施进行处理,如打印火灭火等。
2.发现有管道泄漏、气体泄漏时,应检查泄漏的原因,及时进行紧急的排气、采取措施,保障自身安全。
五、安全事故处理在公司认为本身产生过安全事故,会进行相关的记录报警,有专人进行事故原因的调查,对于事故成因或者事故发现的原因及时进行整改,避免同类事故再次发生,以确保工作场所的安全。
六、其他注意事项1.产品开箱入库时,应对产品外包装进行检查,如有破损、密封不良等,应及时向上级汇报。
2.禁止任何非法活动和品行不端的行为。
3.其他事项以相关规程为准。
石灰生产工艺流程
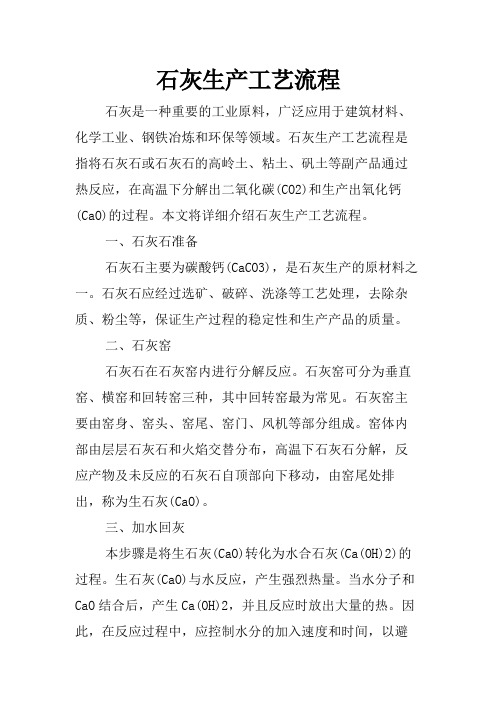
石灰生产工艺流程石灰是一种重要的工业原料,广泛应用于建筑材料、化学工业、钢铁冶炼和环保等领域。
石灰生产工艺流程是指将石灰石或石灰石的高岭土、粘土、矾土等副产品通过热反应,在高温下分解出二氧化碳(CO2)和生产出氧化钙(CaO)的过程。
本文将详细介绍石灰生产工艺流程。
一、石灰石准备石灰石主要为碳酸钙(CaCO3),是石灰生产的原材料之一。
石灰石应经过选矿、破碎、洗涤等工艺处理,去除杂质、粉尘等,保证生产过程的稳定性和生产产品的质量。
二、石灰窑石灰石在石灰窑内进行分解反应。
石灰窑可分为垂直窑、横窑和回转窑三种,其中回转窑最为常见。
石灰窑主要由窑身、窑头、窑尾、窑门、风机等部分组成。
窑体内部由层层石灰石和火焰交替分布,高温下石灰石分解,反应产物及未反应的石灰石自顶部向下移动,由窑尾处排出,称为生石灰(CaO)。
三、加水回灰本步骤是将生石灰(CaO)转化为水合石灰(Ca(OH)2)的过程。
生石灰(CaO)与水反应,产生强烈热量。
当水分子和CaO结合后,产生Ca(OH)2,并且反应时放出大量的热。
因此,在反应过程中,应控制水分的加入速度和时间,以避免出现爆炸等安全事故。
水合石灰(Ca(OH)2)的制备条件是:温度越高,溶解度越大;加水速度越慢,反应越充分。
四、石灰产品制备水合石灰(Ca(OH)2)可以用于水泥、建材、建筑和环保等行业。
常见的石灰产品制备方法有石灰乳、熟料水泥等。
其中,石灰乳为一种半流体状态的混合物,由水合石灰和水混合后形成。
石灰乳可以用于钢铁冶炼、矿柱充填和土壤改良等方面。
熟料水泥则将制备好的石灰与硅酸盐等材料烧成熟料,再经过磨捣、混合等工艺制成,是建筑和工程领域最常用的材料之一。
总的来说,石灰生产工艺的流程主要分为四步:石灰石准备、石灰窑、加水回灰和石灰产品制备。
在每个步骤中,都需要严格控制生产条件和流程,以确保生产产品的质量和提高生产效率。
同时,石灰生产过程中要注意安全,避免出现事故和环境破坏等问题,保障生产的安全和可持续发展。
石灰生产工艺说明及质量保证措施

汇报人:日期:contents•石灰生产工艺说明•石灰生产质量保证措施目录•石灰生产环境保护与安全•石灰生产经济效益分析•石灰生产工艺改进与发展趋势石灰生产工艺说明生石灰粉磨将消化后的生石灰进行粉磨,使其成为细粉状,方便使用。
生石灰消化将煅烧后的生石灰进行消化,去除其中的杂质和未反应的石灰石。
石灰石煅烧将破碎后的石灰石放入石灰窑中进行高温煅烧,使其发生化学反应,生成生石灰。
石灰石开采石灰石开采是石灰生产的第一步,将矿石从地下或山上开采出来。
石灰石破碎将开采出来的石灰石进行破碎,使其成为小块或粉末。
石灰生产工艺流程石灰窑破碎机消化器粉磨机01020304用于高温煅烧石灰石,产生生石灰。
用于破碎大块的石灰石,使其成为小块或粉末。
用于消化生石灰,去除其中的杂质和未反应的石灰石。
用于粉磨消化后的生石灰,使其成为细粉状。
石灰石是石灰生产的主要原料,通常来自矿山或采石场。
石灰石通常使用煤炭作为燃料,用于提供煅烧石灰石所需的热量。
燃料用于消化生石灰,去除其中的杂质和未反应的石灰石。
水根据需要添加其他添加剂,以改善生石灰的性能或提高产品质量。
其他添加剂石灰生产质量保证措施选择质量稳定、信誉良好的供应商,并确保原料的产地来源可靠。
原料产地选择原料检测原料储存对进厂的原料进行严格的质量检测,包括化学成分、含水量、粒度等指标,确保符合生产要求。
建立科学的原料储存管理制度,保持原料的干燥、防潮和清洁,避免原料的质量下降。
030201原料质量控制严格监控生产过程中的各个工艺环节,确保工艺参数符合要求,及时调整和处理异常情况。
工艺流程监控对生产现场的环境进行监控,包括温度、湿度、粉尘浓度等指标,确保生产环境的稳定和安全。
生产环境监控定期对生产设备进行检查和维护,确保设备的正常运行,避免因设备故障影响产品质量。
设备维护与检查生产过程监控对生产出的石灰产品进行化学成分的检测,包括氧化钙、氧化镁等主要成分,确保产品质量符合标准。
石灰厂生产工艺流程
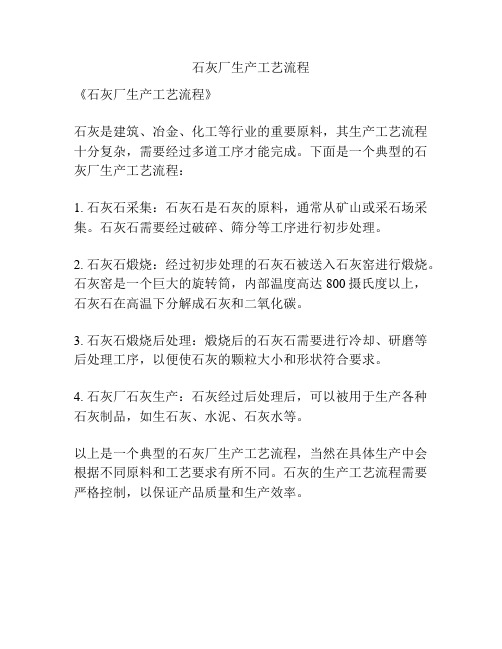
石灰厂生产工艺流程
《石灰厂生产工艺流程》
石灰是建筑、冶金、化工等行业的重要原料,其生产工艺流程十分复杂,需要经过多道工序才能完成。
下面是一个典型的石灰厂生产工艺流程:
1. 石灰石采集:石灰石是石灰的原料,通常从矿山或采石场采集。
石灰石需要经过破碎、筛分等工序进行初步处理。
2. 石灰石煅烧:经过初步处理的石灰石被送入石灰窑进行煅烧。
石灰窑是一个巨大的旋转筒,内部温度高达800摄氏度以上,石灰石在高温下分解成石灰和二氧化碳。
3. 石灰石煅烧后处理:煅烧后的石灰石需要进行冷却、研磨等后处理工序,以便使石灰的颗粒大小和形状符合要求。
4. 石灰厂石灰生产:石灰经过后处理后,可以被用于生产各种石灰制品,如生石灰、水泥、石灰水等。
以上是一个典型的石灰厂生产工艺流程,当然在具体生产中会根据不同原料和工艺要求有所不同。
石灰的生产工艺流程需要严格控制,以保证产品质量和生产效率。
- 1、下载文档前请自行甄别文档内容的完整性,平台不提供额外的编辑、内容补充、找答案等附加服务。
- 2、"仅部分预览"的文档,不可在线预览部分如存在完整性等问题,可反馈申请退款(可完整预览的文档不适用该条件!)。
- 3、如文档侵犯您的权益,请联系客服反馈,我们会尽快为您处理(人工客服工作时间:9:00-18:30)。
一、石灰生产工艺流程图二、主要参数1 窑体主要参数1)有效高度 21.7 m 。
2)有效容积 150 m3 。
3)窑衬外径 4.6 m 。
4)窑衬内径 3 m 。
5)高径比 7.58 。
6)焙烧带高度 5 m 。
7)烧嘴:低压套筒式。
8)烧嘴数量:2排共28只。
9)上下排烧嘴距离:2.5M。
10)上下排烧嘴布置:平面对称、上下错排。
2、煤气与助燃空气参数1)煤气热值:850~950KCaL/NM32)空气过剩系数:1.05~1.15三、技术要求1 石灰石(执行YB/T5279-1999 二级石灰石标准)1)粒度规格:40~80 mm。
2)成分: CaO > 52 % MgO < 3 %SiO < 2.2 % S < 0.10 % P < 0.02 % 3)石灰石应具备良好的热稳定性,加热过程无爆裂。
4) 石灰石中不得混入杂质。
2 燃料1)高、焦混合煤气2)高炉煤气热值:≥ 740 KCaL/M33)焦炉煤气热值:≥ 4000 KCaL/M34)焦炉煤气比例: 3~5 %3 石灰主要指标(执行厂内控标准 JGN52-1999 )CaO > 88 % MgO < 5 % SiO < 3 % S < 0.07 % 灼减:6% 活性度:300ML4 烘窑1)新窑衬烘窑烘炉时间不小于168小时原则:驱除水分、烧结好炉衬。
2)新窑烘窑要求升温速度:每小时不大于10~15℃。
保温:150℃、350℃、600℃进行保温,保温时间20~24小时。
烘炉终结温度:850~900℃。
烘窑前加入1米厚的石料保护炉底。
石灰窑烘炉曲线图(后附)5 操作控制要求A、焙烧温度控制:1)焙烧带温度:1050~1150℃。
2)预热带温度:400~900℃。
3)冷却带温度:900~200℃。
4)窑顶烟气出口温度:≤ 600℃。
5)出窑石灰温度:≤ 200℃。
B、风气配比1)煤气量:8500~10000 Nm3/h2)空气量:6800~8000 Nm3/h3)空气过剩系数:1.05-1.154)一次助燃空气与二次空气比:4:6~3:75)煤气压力:14000~18000 Pa6)空气压力:13000~15000 PaC、装料、出料1)先上料再出料2)每小时装料一次,每次6-9吨。
3)每小时出料一次,上多少出多少,保持料线高度1.5~2米。
D、焙烧检验项目1)石灰窑烟气成分(CO CO2 O2 ...)。
2)石灰产品的生烧量、过烧量、活性度及化学成分。
E、休风操作要点1)煤气降压操作,由加压煤气降至常压煤气。
2)空气压力,随煤气压力的降低相应的进行降压操作,保持空气与煤气压力差 < 3000 Pa 。
3)煤气压力由高压降至常压后,关闭烧嘴阀门。
4)烧嘴阀门关闭5分钟后,关闭二次风阀门,再停风机。
F、复风操作要点1)启动风机,将风压与煤气压力匹配得当。
2)先送二次风,5分钟后再开烧嘴风气阀,进入煤气常压焙烧。
3)调整煤气、空气的流量、压力配比,使之运行稳定。
4)转入加压操作,根据煤气压力的升高,随时提升空气压力,稳定风气压力配比。
5)转入正常生产操作。
G、停窑1)先休风操作。
2)切断煤气主管道阀门。
3)打开窑体围管放散阀并吹扫管道。
6、开新窑1) 根据烘窑曲线进行烘窑,将焙烧带温度升到850℃保温8小时后转入开窑操作.2) 将石料加至下排烧嘴下0.5米。
3)加大块(树根或道木<0.5米)底柴0.8米厚,加柴前关闭烧嘴阀和炉底门,将下排烧嘴窥视镜隔一个打开一个。
4)视底柴燃烧红火后,连续投入木柴灰石混料(1:9)10斗。
5)关闭烧嘴窥视镜,送少量底风(200-300m3/h)。
6)视烧嘴处烧红火后,隔一开一个烧嘴,空气、煤气比2:1,总风流量 < 1500 m3/h。
7)连续加(1:9)混合料50斗,并逐步开全下排烧嘴,将总风流量增加到3000 m3/h,空气煤气比例调整为1.5:1。
8)通知煤气加压站启动煤气加压机,煤气压力控制在12000Pa。
9)连续加混合料(0.5:9.5)至料线,并逐步将总风流量增加到7500 m3/ h,底风流量调整到3000 m3/h,空气煤气比例调整为1 :1。
10)将煤气压力提到16000 Pa,空气压力15400 Pa。
11)停混合料,投石灰石料每小时7斗。
12)出料:A:料线未达到前,每半小时出一次料,每次5分钟;B:料线达到后,每半小时出一次料,上多少出多少,保持料线高度。
13)根据煅烧温度、烟气温度调整煤气量。
14)混合料完全排出后,检测烟气成份,根据烟气成份调整风气比例。
15)炉窑三带温度工况形成后,转入正常生产操作。
7、故障情况处理1)烘窑时出现熄火关闭煤气阀门,用底风吹扫炉膛5分钟后,重新点火。
2)悬料煅烧带出现悬料时,立即关闭底风和煤气,用侧风进行冷吹处理,风口前不得有红料,以免降低冷吹效果,吹落后恢复生产。
3)挂壁料煅烧带出现挂壁料,关闭底风和煤气,用侧风进行冷吹处理,吹冷后即转入正常生产。
4)炉底结瘤发现炉底结瘤块影响正常出灰时,立即休风,打开炉门用钢钎进行处理。
5)出灰系统故障出灰系统故障,影响出灰时间1.5小时以上时,应休风处理,避免炉料烧结。
6)上料设备故障上料设备故障影响上料时间1.5小时,应休风处理,避免烟气温度过高。
1、司炉工岗位操作规程1.1 接班事项1.1.1 提前十五分钟接班,开班前会。
并接受任务。
1.1.2 详细询查上一班生产运行情况。
1.1.3 详细询查设备运行情况,并试车确认。
1.1.4 进行设备动态检查,发现问题及时处理。
1.1.5 确认煤气、空气的压力、流量及压差参数。
1.1.6 确认炉前仓石灰石质量。
1.1.7 确认出窑石灰产品的生过烧量。
1.1.8 确认窑温参数和烧嘴的控制使用状况1.2 操作要点1.2.1 随时掌握上料量、煤气量、窑温和石灰生过烧情况。
1.2.2 根据产量调整上料量和煤气量。
1.2.3 根据石灰质量,适量调整上料量和煤气量。
1.2.4 稳定焙烧温度 1050~1150 ℃1.2.5 调整炉窑平面温度,平面温度差小于 50 ℃。
1.2.6 观察炉料焙烧状况,及时调整异常情况。
1.2.7 按时、按量出料,炉料焙烧的时间不得大于1.5小时,否则必须动料操作。
1.2.8 复风时,先低压复风操作,确认稳定并具备加压条件后转入加压操作。
1.2.9 开启烧嘴,煤气阀门和空气阀门要交替分阶段操作,低压操作保持围管压力不低于 3000 Pa; 高压操作围管压力不低于 12000 Pa1.2.10 随时与仪表工协调,纠正控制焙烧参数。
1.2.11 作好记录1.3 安全要点1.3.1 复风操作,先送底风再送一次风和煤气。
1.3.2 休风操作,先关烧嘴煤气阀和一次空气阀,再停二次风。
1.3.3 低压复风,烧嘴煤气法阀和空气阀门要交替分阶段操作,严禁操作过快出现负压现象。
1.4 交班事项1.4.1 提前做好交班准备,符合交班标准要求。
1.4.2 向下一班交清生产情况、设备运行情况。
1.4.3 交清工具。
1.4.4 所属卫生区域清理清洁。
1.4.5 交班签字。
2、仪表控制岗位操作规程2.1 接班事项2.1.1 提前十五分钟接班,开班前会。
并接受任务。
2.1.2 详细询查上一班生产运行情况。
2.1.3 详细询查仪表、设备运行情况,并确认仪表显示情况,发现问题及时处理。
1.1.4 确认炉前仓石灰石质量。
1.1.5 确认出窑石灰产品的生过烧量。
1.1.6 确认窑温参数和风气的压力、流量、配比控制状况2.2 操作要点2.2.1 随机掌握煤气、空气的压力、流量波动变化,控制进窑风、气总量及配比。
2.2.2 掌握窑温参数的变化。
调节进窑风气量或上料量稳定焙烧温度。
2.2.3 依据窑温、料柱状况或石灰质量情况,调整烧进速度。
2.2.4 稳定焙烧温度 1050 ~1150℃。
2.2.5 及时调整一次风和二次风的比例,稳定炉窑三带温度。
2.2.6 按时、按量上料、出料,出料间隔时间不大于1.5小时。
2.2.7 随时与司炉工协调,纠正、控制焙烧参数。
2.2.8 作好记录2.3 安全要点2.3.1 复风操作,先送底风再送一次风和煤气;先低压复风操作再加压转入正常生产操作。
2.3.2 休风操作,先关停煤气和一次风,再停二次风。
2.3.3 控制风气压差≤ 3000 Pa 。
2.3.4 窑顶烟气温度≤ 600℃。
2.3.5 出灰温度≤ 200℃。
2.3.6 控制出灰频率和各点的最高焙烧温度,避免烧结、棚料。
2.4 交班事项2.4.1 提前做好交班准备,符合交班标准要求。
2.4.2 向下一班交清生产情况、设备运行情况。
2.4.3 所属卫生区域清理清洁。
2.4.4 交班签字。
3、出灰岗位操作规程3.1 接班事项3.1.1 提前十五分钟接班,开班前会。
并接受任务。
3.1.2 详细询查上一班生产、设备运行情况。
3.1.3 检查设备运行情况,发现问题及时处理。
3.2 操作要点3.2.1 随机掌握设备运行、润滑情况。
3.2.2 出灰过程拣选生烧石灰块、过烧块和杂物。
3.2.3 掌握石灰质量、温度和出灰量。
3.2.4 随时向主控室通报产品质量、温度和链板机上的石灰量。
3.2.5 作好记录3.3 安全要点3.3.1 保持润滑,及时更换有隐患的销、轴、板、轮。
3.3.2 保持身体与运转设备的距离。
3.3 交班事项3.4.1 提前做好交班准备,符合交班标准要求。
3.4.2 向下一班交清生产情况、设备运行情况。
3.4.3 所属卫生区域清理清洁。
3.4.4 交班签字。
4、成品岗位操作规程4.1 接班事项4.1.1 提前十五分钟接班,开班前会。
并接受任务。
4.1.2 详细询查上一班生产、设备运行情况。
4.1.3 确认料仓库存灰量。
4.2 操作要点4.2.1 随时掌握各仓库存量。
4.2.2 各石灰料仓循环使用,避免石灰贮存时间过长。
4.2.3 装车前检查灰车马槽,避免异物混入。
4.2.4 及时清理场地物料。
4.2.5 作好记录4.3 安全要点4.3.1 装车前检查灰车马槽,避免异物混入。
4.4 交班事项4.4.1 提前做好交班准备,符合交班标准要求。
4.4.2 向下一班交清生产情况、设备运行情况。
4.4.3 所属卫生区域清理清洁。
4.4.4 交班签字。
5、筛分岗位操作规程5.1 接班事项5.1.1 提前十五分钟接班,开班前会。
并接受任务。
5.1.2 详细询查上一班生产、设备运行情况。
5.1.3 试车确认设备动态检查,发现问题及时处理。
5.2 操作要点5.2.1 按品种、品位分别筛分、定置存放。
5.2.2 筛分前检查各级筛的技术情况。
5.2.3 开机操作,设备由末端9号皮带向一号原料仓给料器依次启动。