丰田汽车品牌案例分析
丰田召回门案例分析
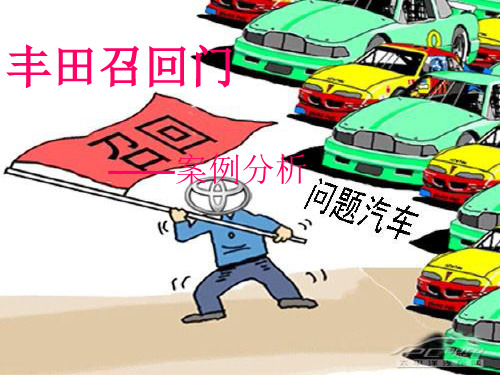
COLD LIGHT SOURCE
•
Designer:S.G.C.chen8332
海 . 水 . 正 . 作 . 品 蓝 .
严重经济损失
• 车辆召回 • 制动系统相关召回汽车 辆) 制动系统相关召回汽车(辆 • 日本: 223,000;北美: 155,000;(美国: 146,550) 欧洲: 53,000 其它: 5,000 总计: 437,000 • 油门踏板问题召回汽车 辆) SOURCE 油门踏板问题召回汽车(辆 COLD LIGHT • 美国: 2,210,000 加拿大: 270,000 欧洲: 1,710,000 中国: 75,552 *其它: 180,000 (* 中东,中美洲和南美洲,非洲) • 脚垫滑动召回汽车 辆) 脚垫滑动召回汽车(辆 • 美国: 5,350,000;加拿大: 400,000;总计: 5,750,000;注:约有210万辆车同时存在踏垫和油门踏板 问题。 • 召回总量: 约854万辆 召回总量: 万辆
COLD LIGHT SOURCE
Designer:S.G.C.chen8332
海 . 水 . 正 . 作 . 品 蓝 .
召回门对本田未来发展影响
• “召回门”很显然严重 • 丰田作为日本最大的 打击了丰田的销量。美国 汽车企业,本次“召回门” 沃德汽车信息库数据显示, 事件对日本的经济也有深 丰田汽车上月在美国销量 刻影响。日本大和综合研 下降16%,自1998年2月 究所18日发表的“丰田汽 以来首次跌破10万辆。丰 车召回对日本经济造成影 COLD LIGHT SOURCE 田公司16日宣布,打算暂 响试算结果”显示,受丰 停两家设在美国的汽车制 田召回事件影响,美国市 造厂生产,以应对销量下 场日本汽车销售下降,国 降、帮助经销商减少库存。 内乘用车产量减少30万辆, 日本GDP可能因此下降 另外,丰田成功超过通用 0.12个百分点,相关产业 成为世界头号汽车厂商的 雇用人数将减少4.9万人。 桂冠也将在以后很多年内 难以再次得到。
丰田八步法实际案例

丰田八步法实际案例【实用版】目录1.丰田八步法简介2.丰田八步法的实际案例3.丰田八步法的效果分析4.丰田八步法的应用建议正文【丰田八步法简介】丰田八步法,又称为 PDCA 循环,是一种以计划(Plan)、执行(Do)、检查(Check)和行动(Act)为核心的管理循环,被广泛应用于各种企业的质量管理中。
这个循环是一个连续不断的过程,通过不断的反馈和修正,达到提升产品质量和效率的目的。
【丰田八步法的实际案例】以丰田汽车公司为例,他们运用丰田八步法,通过不断改进,成为了全球最大的汽车制造商。
具体来说,他们会首先制定目标和计划,然后执行计划,接着检查执行结果,最后根据检查结果进行修正,以达到更好的效果。
例如,他们设定了一个目标:降低某款车型的装配时间。
他们首先进行现状分析,找出了存在的问题,然后制定了改进计划,包括重新设计流程、提高工人的操作技能等。
接着,他们执行这个计划,同时进行检查,看看改进是否达到预期效果。
最后,根据检查结果,他们进行修正,以确保改进的效果能够持续。
【丰田八步法的效果分析】丰田八步法的效果是显著的。
通过这个循环,企业可以发现并解决存在的问题,提高效率,降低成本,提升产品质量,增强竞争力。
丰田汽车公司就是最好的例子,他们的成功,很大程度上得益于丰田八步法的有效运用。
【丰田八步法的应用建议】对于想要应用丰田八步法的企业,我有以下几点建议:首先,要明确目标。
没有明确的目标,就无法进行有效的计划和执行。
其次,要进行现状分析。
只有了解现状,才能找出问题,才能制定出有效的改进计划。
再次,要设定合理的改进目标。
目标过高或过低都无法达到预期的效果。
最后,要坚持执行和检查。
只有持续的执行和检查,才能确保改进的效果能够持续。
丰田公司管理案例分析

丰田公司管理案例分析丰田公司是全球著名的汽车制造公司,其成功的管理模式备受瞩目。
下面将对丰田公司的管理案例进行分析。
首先,丰田公司的成功得益于其创始人丰田喜一郎的领导风格。
丰田喜一郎提倡尊重员工,注重员工的意见和参与,鼓励员工敢于创新和提出改善建议。
这种领导风格创建了一种积极向上的企业文化,员工感到自己的贡献被认可和尊重,从而提高了员工的工作积极性和创造力。
其次,丰田公司以质量为中心的管理理念在汽车行业树立了良好的口碑。
丰田公司一直推崇“精益生产”管理模式,注重生产过程中的细节和品质控制。
丰田公司鼓励员工发现并解决问题,不断改进生产流程和产品质量。
这种质量导向的管理理念使丰田汽车在市场上享有较高的声誉,并赢得了消费者的信任。
另外,丰田公司注重团队合作和横向沟通。
丰田公司采用了“5S”管理方法,即整理、整顿、清洁、清扫、自制。
这种方法强调团队合作,通过组织员工的主动参与来改善工作环境和生产效率。
丰田公司还鼓励员工进行横向沟通,打破部门之间的壁垒,促进信息的自由流动,提高企业的协同效应。
此外,丰田公司不断加强供应链和供应商的管理。
丰田公司着力构建稳定可靠的供应链体系,与供应商建立长期合作关系,共同提高产品质量和供货速度。
丰田公司还通过供应商管理系统来对供应商进行评估和监控,确保供应商符合公司的要求和标准。
最后,丰田公司积极推进可持续发展和环境保护。
丰田公司致力于研发和生产绿色环保的汽车产品,推广可再生能源和节能减排技术。
丰田公司还制定了环境保护的目标和计划,不断提高企业的环境责任和可持续发展能力。
综上所述,丰田公司成功的管理案例得益于其创始人的领导风格、质量导向的管理理念、团队合作和横向沟通、供应链和供应商管理以及可持续发展和环境保护。
这些管理实践使丰田公司成为汽车行业的佼佼者,并在全球范围内树立了良好的企业形象。
案例分析:丰田:追求“零缺陷”的战术

丰田:追求“零缺陷”的战术丰田做出了一个决策,不仅改变了自己的命运,也促成了各企业的制造革命。
它走出了自己的文化,接纳了一位美国商业顾问的质量理念。
全面质量管理之父威廉-爱德华兹-戴明缺少个人魅力。
他来自农村,举止刻板,总穿着破旧的三件套式西装,授课时语言生硬。
当年,丰田公司(Toyota)决定把质量放在第一位,它的这步棋在当时并没有像今天看起来那样吸引眼球。
当时的公司深陷困境。
在20世纪50年代末,公司将第一批汽车发往美国市场,却因为质量低劣而遭到嘲笑。
身处危机之时,公司的总裁石田退三(Taizo Ishida)决定做一件对任何公司——尤其是日本公司——来说都是最难做到的事情。
丰田采纳了一位外部人士——质量大师威廉-爱德华兹-戴明(W. Edwards Deming)的创意,为了改善自己,对组织进了一次彻底的整顿。
今天,丰田的质量系统被称为“丰田之道”(Toyota Way),一直被世界各地的制造业公司甚至是服务机构奉行。
举例来说,丰田之道能帮助丰田比竞争对手更快地设计出汽车,表明这一流程对于脑力工作的重要性与对于体力工作的重要性是一样的。
然而,执行这个流程要比看上去困难许多,即使是丰田自身在近年来也受困于质量问题。
通过重新拾起对丰田之道的热忱,这家汽车公司现在再次回到了正轨。
让我们来了解一下丰田的这个秘密。
——V.H.1961年,丰田中止在美国销售汽车,不光彩地撤出了美国市场。
它关闭了位于芝加哥和旧金山的办事处,将地区总部从贝弗利山搬到了在好莱坞租下的场所。
公司完全误读了美国市场,试图销售一种低马力、高价格却非常不耐用的迷你汽车。
直到1965年,丰田才重返美国,但这回它带来了一款质量大幅提高、价格更有竞争力的新车。
此举开启了一系列的成功,至今已经持续了数十年。
丰田在美国市场上尝试、失败、再尝试的故事在管理历史上是独一无二的。
再度尝试时,它得到了一位出生于艾奥瓦州、名叫威廉。
爱德华兹。
戴明的统计学家的帮助。
丰田汽车案例分析

一、案例背景P1位于美国肯塔基州的丰田汽车制造公司(美国)(TMM)乔治敦工厂于1988年开始进行大规模生产。
这家工厂所采用生产和管理系统正是丰田独特的丰田生产系统(TPS)。
1992年初,TMM将佳美的两厢版投放市场,使得座椅样式由原来的5种迅速增加为发往北美的8种、发往欧洲的10种、发往日本和中东的18种,合计36种。
此时,乔治敦工厂的装配线经理道格·弗里森遇到了急需解决的座椅问题。
P2TMM公司的独家座椅供应商是肯塔基镶框座椅公司(KFS)。
KFS以顺序拉动式系统与TMM的生产装配线保持同步。
座椅是一个柔软易损部件。
后座的垫子的后面有个钩子用于钩住车身的“眼”,钩子由于由金属材料变更为塑料材料而容易折断,从而导致了这次严重的问题——生产线的产出率在一个月内由95%下降到了85%,离线车辆库存水平激增,并且不能按照承诺准时发货。
但是,在丰田日本工厂曾使用同样的工程设计发生该问题。
二、对TPS及其基于的JIT生产模式和自动化缺陷控制的介绍P1TPS的目标是彻底的消除浪费以降低成本,而它提供了两条指导原则以简化如何识别浪费这个关键过程:一是准时(JIT)生产,二是自动化缺陷控制原则。
P2准时生产方式(Just In Time)简称JIT,是日本丰田汽车公司在20世纪60年代创立的一种生产方式:只生产需要的产品,只生产需要的数量,同时只在需要的时候生产。
JIT采取的是多品种少批量、短周期的生产方式,实现了消除库存、优化生产物流、减少浪费的目的。
它将传统生产过程中前道工序向后道工序送货,改为后道工序根据“看板”向前道工序取货,看板系统是J IT生产现场控制技术的核心,但JIT不仅仅是看板管理。
丰田案例分析报告(HBR分析法)

丰田汽车制造公司(美)分析报告2010111040006 付博文1.写作目的对丰田美国工厂座椅问题的分析2.立场陈述JIT本身是一个非常好的生产理念,但是如果没有对临时问题的合理处理办法,一味运用JIT做到准时生产,座椅问题是无法从根本上避免的。
3.证明案例中关键问题是座椅的挂钩出现容易折断的问题,直接影响了汽车的生产速率。
我们先用鱼骨图来分析这个问题。
丰田的高层也是通过这样逐个寻找原因,首先对原材料供应问题来解决,原材料是不存在问题,然后在设计方面,根据日本丰田公司也是运用同样的设计来制作的,但是却没有出现问题,最后基本确定了是生产线的问题,然后再根据生产线了解,那么确定了是员工的操作问题。
但是案例中并没有考虑有没有可能是自然环境造成的,比如湿度,气候抑或是生产线上的温度,在这方面出现问题的概率比较低,可能高层通过了调查,基本确定是人为问题,排除了自然问题。
通过最终确定下来的是原因使生产线上员工的操作问题。
这对于丰田是一个挺致命的问题。
要阐述问题的严重性,先大致了解一下丰田公司的jidoka原则——人工智能自动化质量控制。
一个帮助机器和操作员,发现异常情况并立即停止生产的方法。
它使得各工序能将质量融入生产,并且把人和机器分开,以利于更有效的工作。
jidoka突显出问题,因为当问题一出现的时候,工作就立即被停止下来。
通过消除缺陷的根源,来帮助改进质量。
如果操作员工遵循了jidoka原则,那么挂钩质量问题是可以避免的。
换一句话说,美国丰田公司的生产系统已经偏离了日本总公司的要求,这才是问题的关键。
在操作中,员工发现了这个质量问题,却没有及时停止生产,反而继续生产。
后续的生产并不知道之前的问题,继续生产,导致问题到了成品的时候才解决。
这时所耗损的成本就远远高于及时停止生产的成本,在下面一部分,我们着重来研究jidoka原则。
Jidoka原则是帮助人自动化控制质量,将质量与生产有机融合一起,在生产每个环节中改进质量。
丰田八步法实际案例

丰田八步法实际案例某大型制造企业的生产线存在生产效率低下的问题,为了解决这个问题,企业决定引入丰田生产方式,并采用丰田八步法进行优化。
第一步:明确问题。
企业的目标是提高生产效率,具体指标是降低生产成本、缩短生产周期、提高产品质量。
现状是生产线存在浪费、不平衡、设备故障率高、员工技能水平不一等问题。
理想状态是实现生产线平衡、降低浪费、提高设备利用率和员工技能水平。
第二步:分析现状。
企业收集了生产线相关的数据,包括设备利用率、员工效率、产品质量等信息,并对生产线进行了现场观察。
通过数据分析,企业发现生产线存在严重的浪费问题,包括过度生产、等待时间、运输、不良品等。
同时,设备故障率高也是导致生产效率低下的重要原因。
第三步:确定要因。
经过分析,企业确定了导致生产效率低下的主要原因,包括设备故障率高、生产线不平衡、员工技能水平不一等。
第四步:制定对策。
针对要因,企业制定了相应的对策,包括建立设备维护体系、实施生产线平衡改善、开展员工技能培训等。
第五步:实施对策。
企业按照制定的对策进行了实施,包括建立设备维护体系、对生产线进行重新布局和平衡调整、开展员工技能培训等。
在实施过程中,企业采用了丰田生产方式中的看板管理、标准化作业等工具和方法。
第六步:检查效果。
经过一段时间的实施,企业对改善效果进行了检查。
通过对比改善前后的数据,企业发现生产效率得到了显著提高,生产成本降低了20%,生产周期缩短了30%,产品质量也得到了明显改善。
第七步:标准化。
为了保持改善成果并持续改进,企业将改善过程中形成的经验和方法进行了总结和归纳,形成了标准化的作业流程和规范,并在企业内部进行了推广和实施。
第八步:持续改进。
企业建立了持续改进的机制,定期对生产线进行检查和评估,发现问题及时进行处理和改进。
同时,企业还鼓励员工提出改进意见和建议,并对其进行评估和实施。
国外安全生产典型案例分析

国外安全生产典型案例分析国外安全生产典型案例分析安全生产是企业发展的重要环节,在国内外都备受重视。
本文将分析国外的一个典型案例,以了解其在安全生产方面的成功经验。
典型案例:丰田汽车安全生产丰田汽车是一家世界知名的汽车制造商,以其卓越的汽车质量和安全记录而闻名。
丰田在安全生产方面的成功经验有很多值得我们学习的地方。
首先,丰田汽车高度重视员工安全教育和培训。
公司不仅提供必要的安全培训,还鼓励员工自愿参加安全相关培训。
丰田注重将安全理念融入员工的日常工作中,并根据员工的需求制定个性化的培训计划。
这些培训涵盖了安全意识的培养、事故预防和应急处理等方面,使员工在工作中能够正确处理各种安全问题。
其次,丰田汽车强调以人为本。
公司设立了专门的安全生产部门,负责安全政策的制定和执行。
在生产车间,丰田注重人性化的设计和人因工程,确保员工的安全和舒适。
丰田还鼓励员工主动提出安全改进建议,并定期组织安全检查和审计,及时发现和解决安全隐患。
再次,丰田汽车重视技术创新和设备更新。
公司不断引进先进的安全生产技术和设备,确保员工的工作环境和条件达到最佳状态。
丰田还积极推广先进的安全生产管理方法,如“5S”管理和“PDCA”循环改进法,提高生产管理的效率和水平。
最后,丰田汽车通过建立合作伙伴关系,共同推进安全生产。
公司与供应商、经销商和客户定期举行会议,交流安全生产方面的经验和成果。
丰田鼓励合作伙伴共同参与安全生产管理和改进,共同努力打造安全可靠的汽车产品。
通过对丰田汽车的安全生产经验的分析,我们可以得出以下几个启示:首先,安全生产需要全员参与,不能仅仅依靠单一部门的努力。
其次,安全教育和培训是保障员工安全的重要手段,需要不断加强。
再次,技术创新和设备更新是保障工作环境安全的重要保证。
最后,在安全生产方面,企业需要与合作伙伴建立良好的合作关系,实现互利共赢。
总之,丰田汽车在安全生产方面的成功经验值得我们借鉴。
对于国内企业来说,建立科学、健全的安全生产体系,提高员工的安全意识和技能水平是重要的。