甲醇驰放气变压吸附制氢工艺控制优化
甲醇合成工艺中的驰放气回收浅谈
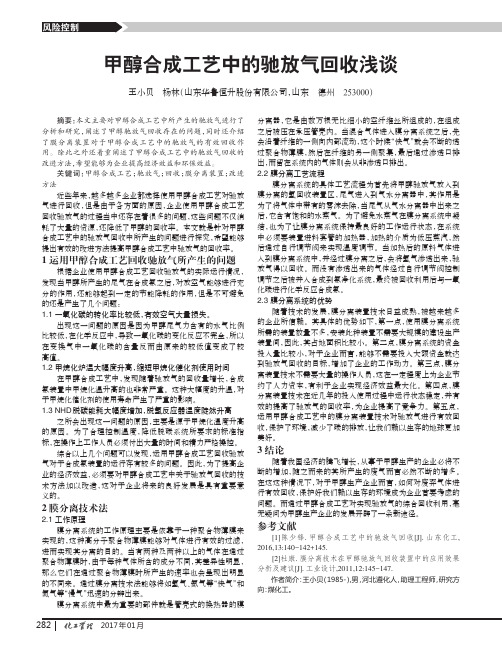
分离器,它是由数万根无比细小的空纤维丝所组成的,在组成 之后被压在承压管壳内。当混合气体进入膜分离系统之后,先 会沿着纤维的一侧向内部流动,这个时候“快气”就会不断的透 过聚合物薄膜,然后在纤维的另一侧聚集,最后通过渗透口排 出,而留在系统内的气体则会从非渗透口排出。 2.2 膜分离工艺流程
膜分离系统的具体工艺流程为首先将甲醇驰放气放入到 膜分离的氢回收装置区,尾气进入到气水分离器中,其作用是 为了将气体中带有的雾沫去除,当尾气从气水分离器中出来之 后,它含有饱和的水蒸气。为了避免水蒸气在膜分离系统中凝 结,也为了让膜分离系统保持最良好的工作运行状态,在系统 中必须要装置进料套管的加热器,加热的介质为低压蒸汽,然 后通过自行调节阀来实现温度调节。当加热后的原料气体进 入到膜分离系统中,并经过膜分离之后,会将氢气渗透出来,驰 放气得以回收。而没有渗透出来的气体经过自行调节阀控制 调节之后被并入合成到氨净化系统,最终被回收利用后与一氧 化碳进行化学反应合成氨。 2.3 膜分离系统的优势
参考文献
[1]陈少锋. 甲醇合成工艺中的驰放气回收[J]. 山东化工, 2016,13:140-142+145.
[2]杜康. 膜分离技术在甲醇驰放气回收装置中的应用效果 分析及建议[J]. 工业设计,2011,12:145-147.
作者简介:王小贝(1985-),男,河北遵化人,助理工程师,研究方 向:煤化工。
降低甲醇合成驰放气放空量的优化措施

降低甲醇合成驰放气放空量的优化措施发布时间:2021-06-07T05:50:50.326Z 来源:《中国科技人才》2021年第9期作者:陈春刘丹[导读] 我厂有四路放空点:1、打开PV5009调节阀,系统直接排放至放空总管;2、经过甲醇水洗塔洗涤甲醇回收后经驰放气压缩机加压后送往变换工段低变炉入口,弛放气放空量由驰放气压缩机一回一调节阀控制;兖矿新疆煤化工有限公司新疆乌鲁木齐 830011摘要:甲醇合成系统运行稳定后,精准找到影响驰放气放空量偏大的原因,对降低吨甲醇精制气消耗,提高甲醇产量,创造更多的经济效益,是化工企业共同关注的问题。
关键词:甲醇合成;降低;放空量;1 概述我厂甲醇生产是以多喷嘴对置式水煤浆气化炉产生的水煤气为原料,经净化工段甲醇变换、低温甲醇洗制得的精制气与甲醇合成循环气混合,进入换热器与出塔合成气换热至194~222.5℃进入合成塔,在铜基催化剂作用下低压合成甲醇经过逆流换热,冷却分离出粗甲醇,剩余未反应完全气体返回循环气压缩机,经加压后循环利用。
为防止合成系统中惰性气体的积累,要连续从系统中排放少量的循环气。
我厂有四路放空点:1、打开PV5009调节阀,系统直接排放至放空总管;2、经过甲醇水洗塔洗涤甲醇回收后经驰放气压缩机加压后送往变换工段低变炉入口,弛放气放空量由驰放气压缩机一回一调节阀控制;3、弛放气压缩机入口还有一路放空去放空总管,由放空阀的开度大小来调节弛放气的放空量,此路放空量有限,适用于气化倒炉、净化并气、合成氨停车停止回收甲醇合成弛放气时等情况;4、为保障硫回收环保装置的正常运行,将一部分驰放气经PV5015减压后并入燃料气管网以满足硫回收酸性气焚烧炉的需要。
甲醇合成系统放空不能简单地认为排放惰性气以维持入塔气组成的稳定,主要是调节入塔气中H2、CO2和惰性气的过剩程度。
驰放气的量越大,系统内的有效有效气体成分损失就越多,有效组分浪费量越多,造成甲醇产量下降,驰放气量越小,惰性气体累计量越大,系统前后压差变大,易造成催化剂粉化及压缩机超电流、压缩机喘振等不利后果。
甲醇合成装置工艺介绍及工艺指标优化调整

甲醇合成装置工艺介绍及工艺指标优化调整发布时间:2022-01-19T03:08:05.724Z 来源:《新型城镇化》2021年24期作者:张昊毛彦彬冯金喜任小永[导读] 甲醇是重要化工原料,在化工生产中被广泛应用,可用于生产制造烯烃、甲醛、苯二甲酸二甲酯、甲胺等,涉及医药、塑料、涂料、染料、农药等众多领域。
宝丰能源集团股份有限公司宁夏银川 750411摘要:甲醇是重要化工原料,在化工生产中被广泛应用,可用于生产制造烯烃、甲醛、苯二甲酸二甲酯、甲胺等,涉及医药、塑料、涂料、染料、农药等众多领域。
目前甲醇合成工艺流程大体是:原料气制备、气体净化、原料气压缩、甲醇合成。
对操作控制进行优化,可以提升生产效率、降低运行成本。
本文将针对甲醇合成工艺进行介绍以及工艺参数优化调整问题展开研究和分析。
关键词:甲醇合成;工艺调整;参数优化;一、甲醇合成装置工艺简述近些年来,随着我国化工生产水平的提高,化工生产中对甲醇需求量越来越大。
为提高甲醇生产水平,解决甲醇供求问题,研究甲醇合成工艺具有重要意义。
我国煤炭资源丰富,所以甲醇原料多采用天然气和煤,生产工艺分为:单产甲醇和联产甲醇两种。
甲醇合成工艺流程长,工艺复杂,具体生产中不同净化方式,不同原材料,工艺流程存在一定差异,所使用的设备与催化剂也会不同。
以天然气为原料的工艺技术有:气流床气化炉技术、固定床气化技术、流化床气化技术等。
而以煤为原料的工艺技术有:高压技术、催化技术、粉煤纯气化工艺、水电解制氢联合成气工艺等,工艺流程包括:原料气制造、原料气净化、甲醇合成、粗甲醇精馏等工序[1]。
二、甲醇合成装置工艺介绍甲醇合成装置如操作控制不当,会造成催化剂活下下降,导致精馏不达标,影响产品合格率,增加生产成本,甚至带来一系列安全问题。
因此,有必要进行甲醇合成操作控制优化。
具体优化过程中,应从设备优化、工艺参数优化等多个方面入手,因设备优化需新增投资,且需停车工艺交出改造,故优先考虑工艺参数优化调整。
变压吸附制氢装置及工艺的改进与优化

变压吸附制氢装置及工艺的改进与优化摘要:若是想让氢气的附加值获得一定的提升,就需要应用变压吸附方面的技术,选择和装置最为契合的方法及策略,并对各种各样工艺与装置的运行情况进行分析,对变压吸附制氢装置或者是工艺做好优化,把粗氢气不断的提纯到接近于百分之百,让其变成电子光学级用氢气。
基于此,笔者将结合自己的经验,就变压吸附制氢装置及工艺的改进与优化策略进行分析,希望可以为相关人士提供一定的参考和帮助。
关键词:变压吸附;制氢装置;工艺;优化策略变压吸附方面的技术是最近新兴起的一种气体分离技术,还在整个工业产业内部获得了十分普遍的运用,其能够借助变压吸附技术来从大量的含氢废气当中对氢气进行提纯,通过变压吸附技术所拥有的循环时间短、吸附剂应用率高、吸附剂用量不多、不用装置换热设备等等的优势,来完成气体的有效分离及提纯。
为此,这就需要有关人员明确气源的基本构成、具体压力甚至是产品要求等等,利用变压吸附工艺来不断提纯氢气,对制氢装置做好有效的优化,让其可以更加顺利的运行下去。
1.变压吸附制氢装置工艺的基本概述工业内部PSA制氢装置所采用的吸附剂需要挑选表面积较大的固体颗粒,借助其本身具有的空隙大小分布情况、不一样的表面积甚至是不相同的表面性质等等,去对混合气体当中的所有组分达成吸附。
PSA制氢装置在进行吸附时的主要工作方式为物理吸附,其是利用变压吸附工艺从大量的混合气体当中不断分离出氮气、一氧化碳、甲烷、乙烯、乙烷等等有着较多杂质的组分,进而获得大量高纯度的氢气。
其主要的工作原理就是借助吸附剂在A-B段的特性真正达成气体的吸附和分离,吸附剂往往会在高温高压的条件下不断吸附所有原料气体当中除了氢气之外的各种杂质组分,接着将压力维持在B点,让各个杂质都能够获得解吸。
有关参数大致包含有:原料的气温度、吸附压力、解吸压力等等,对产品所富有的氢纯度造成一定影响的因素为原料气流量、解吸再生条件或者是均压次数等等,相关人员应该让吸附的压力不断提升,减少解吸本身的压力,让吸附的具体时间得以延长,减少产品的纯度。
甲醇驰放气制合成氨工艺分析
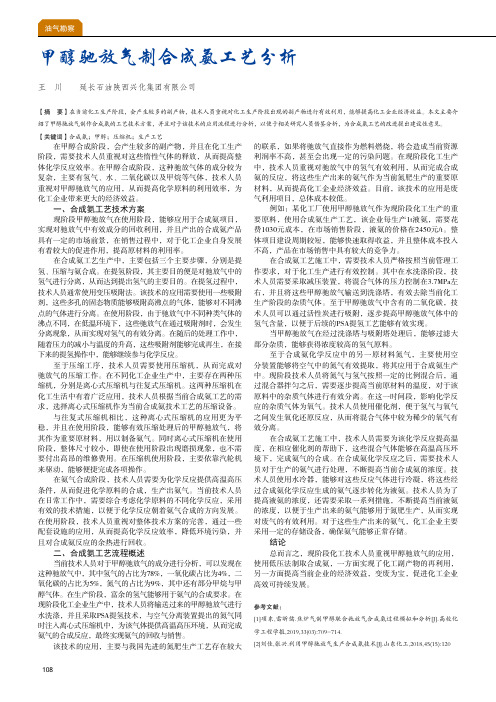
108在甲醇合成阶段,会产生较多的副产物,并且在化工生产阶段,需要技术人员重视对这些惰性气体的释放,从而提高整体化学反应效率。
在甲醇合成阶段,这种驰放气体的成分较为复杂,主要有氢气、水、二氧化碳以及甲烷等气体,技术人员重视对甲醇驰放气的应用,从而提高化学原料的利用效率,为化工企业带来更大的经济效益。
一、合成氨工艺技术方案现阶段甲醇驰放气在使用阶段,能够应用于合成氨项目,实现对驰放气中有效成分的回收利用,并且产出的合成氨产品具有一定的市场前景,在销售过程中,对于化工企业自身发展有着较大的促进作用,提高原材料的利用率。
在合成氨工艺生产中,主要包括三个主要步骤,分别是提氢、压缩与氨合成。
在提氢阶段,其主要目的便是对驰放气中的氢气进行分离,从而达到提出氢气的主要目的。
在提氢过程中,技术人员通常使用变压吸附法。
该技术的应用需要使用一些吸附剂,这些多孔的固态物质能够吸附高沸点的气体,能够对不同沸点的气体进行分离。
在使用阶段,由于驰放气中不同种类气体的沸点不同,在低温环境下,这些驰放气在通过吸附剂时,会发生分离现象,从而实现对氢气的有效分离。
在随后的处理工作中,随着压力的减小与温度的升高,这些吸附剂能够完成再生,在接下来的提氢操作中,能够继续参与化学反应。
至于压缩工序,技术人员需要使用压缩机,从而完成对驰放气的压缩工作。
在不同化工企业生产中,主要存在两种压缩机,分别是离心式压缩机与往复式压缩机。
这两种压缩机在化工生活中有着广泛应用,技术人员根据当前合成氨工艺的需求,选择离心式压缩机作为当前合成氨技术工艺的压缩设备。
与往复式压缩机相比,这种离心式压缩机的应用更为平稳,并且在使用阶段,能够有效压缩处理后的甲醇驰放气,将其作为重要原材料,用以制备氨气。
同时离心式压缩机在使用阶段,整体尺寸较小,即使在使用阶段出现磨损现象,也不需要付出高昂的维修费用。
在压缩机使用阶段,主要依靠汽轮机来驱动,能够便捷完成各项操作。
在氨气合成阶段,技术人员需要为化学反应提供高温高压条件,从而促进化学原料的合成,生产出氨气。
煤制甲醇工艺中制氢工艺的选择比较

煤制甲醇工艺中制氢工艺的选择比较摘要】本文对煤基甲醇工艺中制氢气的工艺路线进行的详细的比较分析,认为以净化气为气源经全变换后PSA制氢的工艺路线在煤基甲醇工艺制氢中具有一定的优势。
关键词:制氢;煤基甲醇;PSA;甲醇深加工1.引言随着甲醇产量的增大,甲醇产能已经出现过剩,越来越多的煤制甲醇厂开始考虑甲醇深加工项目,以便提高产品附加值。
目前比较多的深加工项目有醋酸、醋酸乙烯、醋酸丁酯及MTO、MTP等,特别是MTO,在神化取得成功后,全国各地掀起了一股甲醇制烯烃的热潮。
在MTO及后续深加工工艺中,都属于石油化工范畴,需要大量的氢气,并且纯度较高(一般大于95%,甚至99%以上),氢气的制得是一个需要大家考虑的问题。
本文主要针对煤制甲醇工艺深加工中氢气的制取工艺进行讨论。
2.煤制甲醇工艺及工业制氢工艺简介2.1 煤制甲醇工艺简介一般的煤制甲醇工艺流程为煤或水煤浆加压进入气化炉然后经碳洗塔洗涤进入变换炉部分变换调节氢碳比后进入净化脱硫脱碳,之后进入合成塔合成甲醇,一般分为四个单元,气化、变换、净化、合成。
一般能够作为富氢气气源的有变换气、净化气及合成驰放气,其一般的气体成分如下:变换气气体及成分:H2:44%;CO2:34.4%;CO:19.36%;CH4:0.075%;N2:0.44%;AR:0.1%;H2S:1.3%;COS:0.063%;MEOH:0;H2O:0.181%。
净化气气体及成分:H2:67.7%;CO2:1.88%;CO:29.44%;CH4:0.11%;N2:0.69%;AR:0.15%;H2S:0;COS:0;MEOH:0.01;H2O:0。
驰放气气体及成分:H2:77%;CO2:1.62%;CO:5.96%;CH4:2.42%;N2:9.76%;AR:0.34%;H2S:0;COS:0;MEOH:0.52;H2O:0。
由上可以看出,由于气体成分的不同,需要根据气源的不同,选择不同的制氢工艺[1]。
制氢操作规程(变压吸附部分)
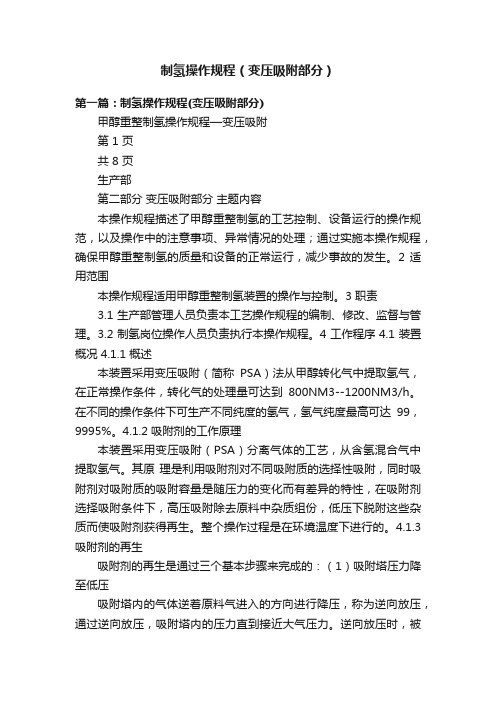
制氢操作规程(变压吸附部分)第一篇:制氢操作规程(变压吸附部分)甲醇重整制氢操作规程—变压吸附第 1 页共 8 页生产部第二部分变压吸附部分主题内容本操作规程描述了甲醇重整制氢的工艺控制、设备运行的操作规范,以及操作中的注意事项、异常情况的处理;通过实施本操作规程,确保甲醇重整制氢的质量和设备的正常运行,减少事故的发生。
2 适用范围本操作规程适用甲醇重整制氢装置的操作与控制。
3 职责3.1 生产部管理人员负责本工艺操作规程的编制、修改、监督与管理。
3.2 制氢岗位操作人员负责执行本操作规程。
4 工作程序4.1 装置概况 4.1.1 概述本装置采用变压吸附(简称PSA)法从甲醇转化气中提取氢气,在正常操作条件,转化气的处理量可达到800NM3--1200NM3/h。
在不同的操作条件下可生产不同纯度的氢气,氢气纯度最高可达99,9995%。
4.1.2 吸附剂的工作原理本装置采用变压吸附(PSA)分离气体的工艺,从含氢混合气中提取氢气。
其原理是利用吸附剂对不同吸附质的选择性吸附,同时吸附剂对吸附质的吸附容量是随压力的变化而有差异的特性,在吸附剂选择吸附条件下,高压吸附除去原料中杂质组份,低压下脱附这些杂质而使吸附剂获得再生。
整个操作过程是在环境温度下进行的。
4.1.3 吸附剂的再生吸附剂的再生是通过三个基本步骤来完成的:(1)吸附塔压力降至低压吸附塔内的气体逆着原料气进入的方向进行降压,称为逆向放压,通过逆向放压,吸附塔内的压力直到接近大气压力。
逆向放压时,被吸附的部分杂质从吸附剂中解吸,并被排出吸附塔。
(2)抽真空吸附床压力下降到大气压后,床内仍有少部分杂质,为使这部分杂质尽可能解吸,甲醇重整制氢操作规程—变压吸附第 2 页共 8 页生产部要求床内压力进一步降低,在此利用真空泵抽吸的方法使杂质解吸,并随抽空气体带出吸附床。
(3)吸附塔升压至吸附压力,以准备再次分离原料气 4.2 工艺操作本装置是有5台吸附塔(T201A、B、C、D、E)、二台真空泵(P203A、B)、33台程控阀和2个手动调节阀通过若干管线连接构成 4.2.1 工艺流程说明工艺过程是按设定好的运行方式,通过各程控阀有序地开启和关闭来实现的。
变压吸附制氢工艺的影响因素及常见问题分析
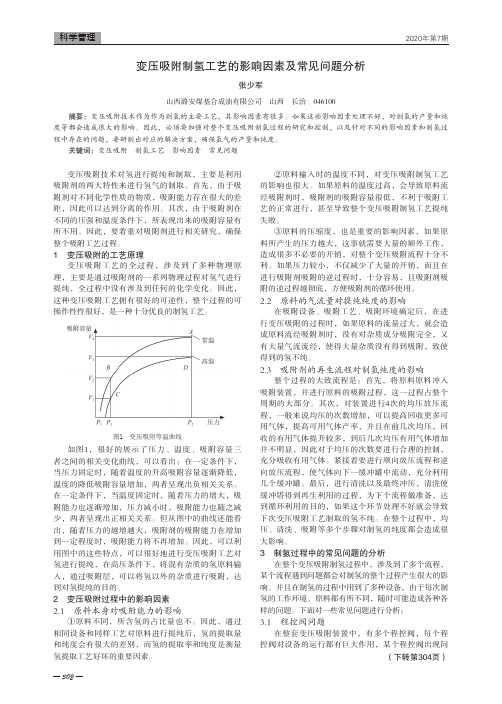
变压吸附技术对氢进行提纯和制取,主要是利用吸附剂的两大特性来进行氢气的制取。
首先,由于吸附剂对不同化学性质的物质,吸附能力存在很大的差距,因此可以达到分离的作用。
其次,由于吸附剂在不同的压强和温度条件下,所表现出来的吸附容量有所不用。
因此,要着重对吸附剂进行相关研究,确保整个吸附工艺过程。
1 变压吸附的工艺原理变压吸附工艺的全过程,涉及到了多种物理原理,主要是通过吸附剂的一系列物理过程对氢气进行提纯,全过程中没有涉及到任何的化学变化。
因此,这种变压吸附工艺拥有很好的可逆性,整个过程的可操作性性很好,是一种十分优良的制氢工艺。
图1 变压吸附等温曲线如图1,很好的展示了压力、温度、吸附容量三者之间的相关变化曲线,可以看出:在一定条件下,当压力固定时,随着温度的升高吸附容量逐渐降低,温度的降低吸附容量增加,两者呈现出负相关关系。
在一定条件下,当温度固定时,随着压力的增大,吸附能力也逐渐增加,压力减小时,吸附能力也随之减少,两者呈现出正相关关系。
但从图中的曲线还能看出,随着压力的越增越大,吸附剂的吸附能力在增加到一定程度时,吸附能力将不再增加。
因此,可以利用图中的这些特点,可以很好地进行变压吸附工艺对氢进行提纯,在高压条件下,将混有杂质的氢原料输入,通过吸附层,可以将氢以外的杂质进行吸附,达到对氢提纯的目的。
2 变压吸附过程中的影响因素2.1 原料本身对吸附能力的影响①原料不同,所含氢的占比量也不。
因此,通过相同设备和同样工艺对原料进行提纯后,氢的提取量和纯度会有很大的差别,而氢的提取率和纯度是衡量氢提取工艺好坏的重要因素。
②原料输入时的温度不同,对变压吸附制氢工艺的影响也很大。
如果原料的温度过高,会导致原料流经吸附剂时,吸附剂的吸附容量很低,不利于吸附工艺的正常进行,甚至导致整个变压吸附制氢工艺提纯失败。
③原料的压缩度,也是重要的影响因素,如果原料所产生的压力越大,这事就需要大量的额外工作,造成很多不必要的开销,对整个变压吸附流程十分不利。
甲醇合成驰放气洗涤系统优化
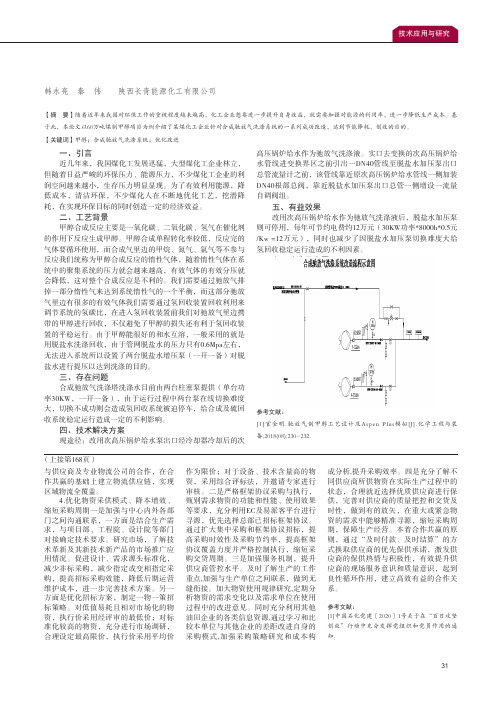
一、引言近几年来,我国煤化工发展迅猛,大型煤化工企业林立,但随着日益严峻的环保压力、能源压力,不少煤化工企业的利润空间越来越小,生存压力明显显现。
为了有效利用能源,降低成本,清洁环保,不少煤化人在不断地优化工艺,挖潜降耗,在实现环保目标的同时创造一定的经济效益。
二、工艺背景甲醇合成反应主要是一氧化碳、二氧化碳、氢气在催化剂的作用下反应生成甲醇。
甲醇合成单程转化率较低,反应完的气体要循环使用,而合成气里边的甲烷、氮气、氩气等不参与反应我们统称为甲醇合成反应的惰性气体,随着惰性气体在系统中的聚集系统的压力就会越来越高,有效气体的有效分压就会降低,这对整个合成反应是不利的。
我们需要通过驰放气排掉一部分惰性气来达到系统惰性气的一个平衡,而这部分驰放气里边有很多的有效气体我们需要通过氢回收装置回收利用来调节系统的氢碳比,在进入氢回收装置前我们对驰放气里边携带的甲醇进行回收,不仅避免了甲醇的损失还有利于氢回收装置的平稳运行。
由于甲醇能很好的和水互溶,一般采用的就是用脱盐水洗涤回收,由于管网脱盐水的压力只有0.6Mpa左右,无法进入系统所以设置了两台脱盐水增压泵(一开一备)对脱盐水进行提压以达到洗涤的目的。
三、存在问题合成驰放气洗涤塔洗涤水目前由两台柱塞泵提供(单台功率30KW,一开一备),由于运行过程中两台泵在线切换难度大,切换不成功则会造成氢回收系统被迫停车,给合成及硫回收系统稳定运行造成一定的不利影响。
四、技术解决方案现途径:改用次高压锅炉给水泵出口经冷却器冷却后的次高压锅炉给水作为驰放气洗涤液。
实口去变换的次高压锅炉给水管线进变换界区之前引出一DN40管线至脱盐水加压泵出口总管流量计之前,该管线靠近原次高压锅炉给水管线一侧加装DN40根部总阀,靠近脱盐水加压泵出口总管一侧增设一流量自调阀组。
五、有益效果改用次高压锅炉给水作为驰放气洗涤液后,脱盐水加压泵则可停用,每年可节约电费约12万元(30KW功率*8000h*0.5元/Kw =12万元),同时也减少了因脱盐水加压泵切换难度大给氢回收稳定运行造成的不利因素。
浅谈PSA变压吸附制氢工艺及优化
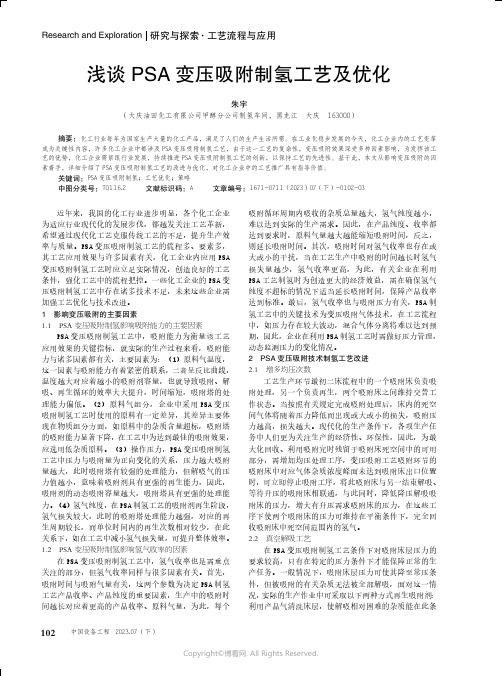
102研究与探索Research and Exploration ·工艺流程与应用中国设备工程 2023.07 (下)近年来,我国的化工行业进步明显,各个化工企业为适应行业现代化的发展步伐,都越发关注工艺革新,希望通过现代化工艺克服传统工艺的不足,提升生产效率与质量。
PSA 变压吸附制氢工艺的流程多、要素多,其工艺应用效果与许多因素有关,化工企业内应用PSA变压吸附制氢工艺时应立足实际情况,创造良好的工艺条件,强化工艺中的流程把控。
一些化工企业的PSA 变压吸附制氢工艺中存在诸多技术不足,未来这些企业需加强工艺优化与技术改进。
1 影响变压吸附的主要因素1.1 PSA 变压吸附制氢影响吸附能力的主要因素PSA 变压吸附制氢工艺中,吸附能力为衡量该工艺应用效果的关键指标,就实际的生产过程来看,吸附能力与诸多因素都有关,主要因素为:(1)原料气温度,这一因素与吸附能力有着紧密的联系,二者呈反比曲线,温度越大对应着越小的吸附剂容量,也就导致吸附、解吸、再生循环的效率大大提升,时间缩短,吸附塔的处理能力偏低。
(2)原料气组分,企业中采用PSA 变压吸附制氢工艺时使用的原料有一定差异,其差异主要体现在物质组分方面,如原料中的杂质含量超标,吸附塔的吸附能力显著下降,在工艺中为达到最佳的吸附效果,应选用低杂质原料。
(3)操作压力,PSA 变压吸附制氢工艺中压力与吸附量为正向变化的关系,压力越大吸附量越大,此时吸附塔有较强的处理能力,但解吸气的压力值越小,意味着吸附剂具有更强的再生能力,因此,吸附剂的动态吸附容量越大,吸附塔具有更强的处理能力。
(4)氢气纯度,在PSA 制氢工艺的吸附剂再生阶段,氢气损失较大,此时的吸附塔处理能力越强,对应的再生周期较长,而单位时间内的再生次数相对较少,在此关系下,如在工艺中减小氢气损失量,可提升整体效率。
1.2 PSA 变压吸附制氢影响氢气收率的因素在PSA 变压吸附制氢工艺中,氢气收率也是需重点关注的部分,但氢气收率同样与很多因素有关。
甲醇制氢变压吸附提纯工艺方案讨论

109甲醇裂解制氢在国内已经是相当成熟的工艺技术,分为甲醇裂解和变压吸附提纯两个单元。
根据GB/T 3634.2-2011要求,纯氢质量指标氢气纯度也需达到99.99%(CO+CO 2≤20ppm),并且出于经济性考虑一般要求氢气的回收率要达到95%以上,因此变压吸附提纯工艺在本工艺中就显得极为重要。
本文将探讨变压吸附提纯氢气面临的多种工艺方案选择。
一、催化剂和吸附剂的选择甲醇裂解制氢最核心的技术就是甲醇裂解用的催化剂和变压吸附用的吸附剂了。
催化剂一般采用耐毒性、活性高、使用周期长、转化率高的催化剂,吸附剂一般采用活性氧化铝、活性碳和分子筛。
由于催化剂和吸附剂都是申请了国家专利技术的,我们也是从固定的渠道购买,所以催化剂和吸附剂的选择都是公司层面的考虑,工艺人员就不用考虑了。
催化剂一般需要几年一换,而吸附剂因为可以再生,可以持续用15年左右。
二、产品气提纯大方案选择确定了催化剂和吸附剂,就需要进行提纯产品氢气工艺方案的选择了。
变压吸附提纯氢气大方案有两种选择:一种是第一级变压吸附先保氢气纯度,先回收部分纯度满足要求的氢气,第二级再保氢气收率,把纯度不够的解析气再进行提纯回收。
这种方案难点就是解析气提纯较困难,而且所有解析气都需要加压,能耗较大;另一种方案是第一级变压吸附先保证氢气收率,第一级氢气回收率一般要达到98%,一段解析气直接排放,保证氢气排出率小于2%,第二级再进行氢气提纯,保证氢气纯度达到99.99%产品气要求,二段解析气再进行回收,这种方案需要加压的解析气相当少一些,能耗低。
两种方案的工艺参数差别是比较大的,为了降低装置能耗,对于甲醇裂解制氢项目我们一般选用第二种方案。
当然这并不能说明第一种方案不好,对于原料本身杂质含量较少的原料,第一种方案是比较好的,比如普氢提纯高纯氢或超纯氢项目,我们就是选用第一种方案。
三、吸附剂再生解析方案选择由于变压吸附装置是持续稳定周期运行的,变压吸附过程分为吸附产气过程和再生解析回收过程。
甲醇裂解制氢含甲醇蒸汽转化和变压吸附制氢两部分
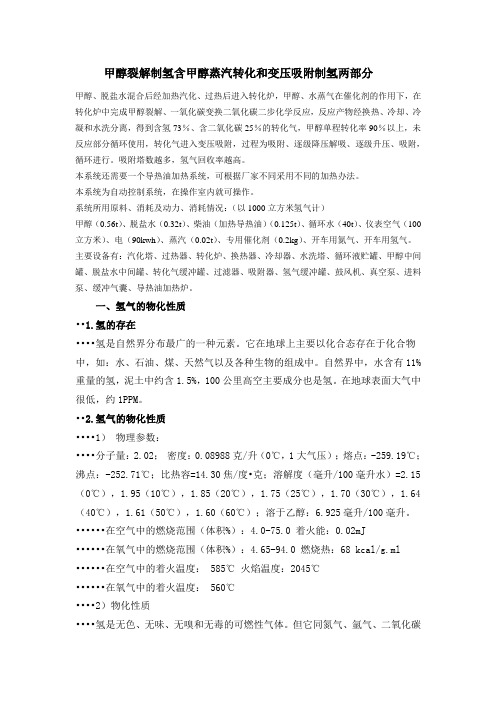
甲醇裂解制氢含甲醇蒸汽转化和变压吸附制氢两部分甲醇、脱盐水混合后经加热汽化、过热后进入转化炉,甲醇、水蒸气在催化剂的作用下,在转化炉中完成甲醇裂解、一氧化碳变换二氧化碳二步化学反应,反应产物经换热、冷却、冷凝和水洗分离,得到含氢73%、含二氧化碳25%的转化气,甲醇单程转化率90%以上,未反应部分循环使用,转化气进入变压吸附,过程为吸附、逐级降压解吸、逐级升压、吸附,循环进行。
吸附塔数越多,氢气回收率越高。
本系统还需要一个导热油加热系统,可根据厂家不同采用不同的加热办法。
本系统为自动控制系统,在操作室内就可操作。
系统所用原料、消耗及动力、消耗情况:(以1000立方米氢气计)甲醇(0.56t)、脱盐水(0.32t)、柴油(加热导热油)(0.125t)、循环水(40t)、仪表空气(100立方米)、电(90kwh)、蒸汽(0.02t)、专用催化剂(0.2kg)、开车用氮气、开车用氢气。
主要设备有:汽化塔、过热器、转化炉、换热器、冷却器、水洗塔、循环液贮罐、甲醇中间罐、脱盐水中间罐、转化气缓冲罐、过滤器、吸附器、氢气缓冲罐、鼓风机、真空泵、进料泵、缓冲气囊、导热油加热炉。
一、氢气的物化性质••1.氢的存在••••氢是自然界分布最广的一种元素。
它在地球上主要以化合态存在于化合物中,如:水、石油、煤、天然气以及各种生物的组成中。
自然界中,水含有11%重量的氢,泥土中约含1.5%,100公里高空主要成分也是氢。
在地球表面大气中很低,约1PPM。
••2.氢气的物化性质••••1)物理参数:••••分子量:2.02;密度:0.08988克/升(0℃,1大气压);熔点:-259.19℃;沸点:-252.71℃;比热容=14.30焦/度•克;溶解度(毫升/100毫升水)=2.15(0℃),1.95(10℃),1.85(20℃),1.75(25℃),1.70(30℃),1.64(40℃),1.61(50℃),1.60(60℃);溶于乙醇:6.925毫升/100毫升。
10万吨年甲醇裂解-变压吸附制氢
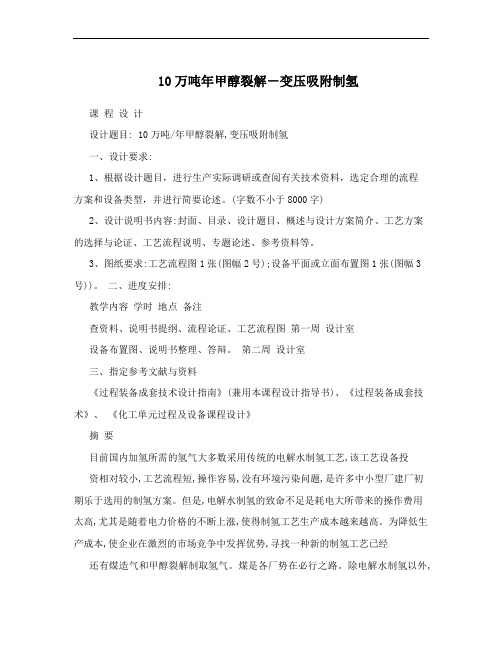
10万吨年甲醇裂解-变压吸附制氢课程设计设计题目: 10万吨/年甲醇裂解,变压吸附制氢一、设计要求:1、根据设计题目,进行生产实际调研或查阅有关技术资料,选定合理的流程方案和设备类型,并进行简要论述。
(字数不小于8000字)2、设计说明书内容:封面、目录、设计题目、概述与设计方案简介、工艺方案的选择与论证、工艺流程说明、专题论述、参考资料等。
3、图纸要求:工艺流程图1张(图幅2号);设备平面或立面布置图1张(图幅3号))。
二、进度安排:教学内容学时地点备注查资料、说明书提纲、流程论证、工艺流程图第一周设计室设备布置图、说明书整理、答辩。
第二周设计室三、指定参考文献与资料《过程装备成套技术设计指南》(兼用本课程设计指导书)、《过程装备成套技术》、《化工单元过程及设备课程设计》摘要目前国内加氢所需的氢气大多数采用传统的电解水制氢工艺,该工艺设备投资相对较小,工艺流程短,操作容易,没有环境污染问题,是许多中小型厂建厂初期乐于选用的制氢方案。
但是,电解水制氢的致命不足是耗电大所带来的操作费用太高,尤其是随着电力价格的不断上涨,使得制氢工艺生产成本越来越高。
为降低生产成本,使企业在激烈的市场竞争中发挥优势,寻找一种新的制氢工艺已经还有煤造气和甲醇裂解制取氢气。
煤是各厂势在必行之路。
除电解水制氢以外,造气提取纯氢技术,虽然投资比甲醇裂解制氢技术省,但占地面积大,更重要的是煤气制氢技术环境污染大,三废难以解决,随着世人对环境保护日趋重视,煤造气制氢技术逐渐被淘汰。
甲醇裂解-变压吸附制氢技术,是近几年被逐渐推广的新技术,其工艺简单,技术成熟,投资省,建设期短,无环境污染,且具有所需原料甲醇价格日渐下降,制氢成本低等优势被广大制氢厂家所看好,成为制氢工艺技改的首选方案。
关键字:甲醇裂解,变压吸附制氢目录1 前言 (I)第1章甲醇裂解-变压吸附制氢技术工艺流程论证.................. 5 1概述 (6)1.2 甲醇裂解制氢化学反应原理及工艺过程 (6)11.2. 1 甲醇、水蒸气混合物在转化器的裂解和转化反应.................61.2. 2 甲醇裂解制氢工艺流程简图 (6)1.2. 3 工艺过程简述 (6)1.3 甲醇裂解制氢在生产中应用情况 (7)1.3. 1 甲醇裂解制氢气产品质量 (7)1.3. 2 经济指标 (7)1.4 甲醇裂解制氢安全性能与环保性能 (8)1.4. 1 安全性 (8)1.4. 2 甲醇裂解制氢的环保性 (8)1.5 总结................................................ 8 第二章物料衡算与能量衡算. (8)2.1 物料衡算概念 (8)2.2 甲醇制氢物料衡算 (9)2.3 热量衡算.............................................. 10 第三章典型机器设备选型与论证. (13)3.1 设备选型的基本要求 (13)3.1.1 技术经济指标 (14)3.1.2 设备结构要求......................................... . 143.2 定型设备的选择 (14)3.2.1 泵的选择 (14)3.2.2 换热器的选择 (15)3.2.3 汽化器的选型....................................... 16 第四章总结 (17)第五章参考文献 (17)前言(1) 甲醇裂解-变压吸附制氢技术工艺原理1甲醇裂解原理 ?甲醇与水蒸气在一定的温度、压力条件下,通过催化剂作用,同时发生催化裂解反应以及一氧化碳变换反应,最终生成氢、二氧化碳及少量的一氧化碳,同时由2于副反应的作用将生成少量的甲烷、二甲醚等副产物。
甲醇生产中驰放气的综合利用
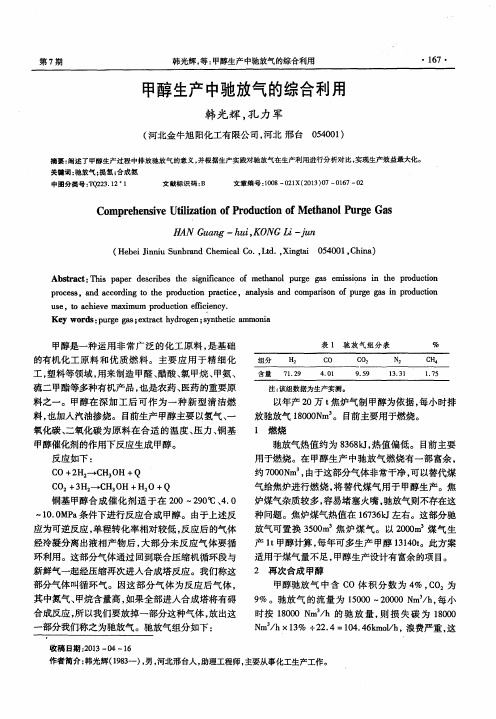
合成 系统所 产生 的 甲醇驰放 气 压力 为 6 . 5 M P a 、
温 度4 0  ̄ C、 流量为1 8 0 0 0 N m / h , 由 于 驰 放 气 具 有
6 . 5 M P a 的压力 , 故不考虑进行加压 。具体工艺流程 为: 原 合成 系统 的 甲醇 驰放 气 , 首先 在小 合成 系统 的 气气换热器的壳程与小合成塔出口的出塔气进行换
u s e ,t o a c h i e v e ma x i mu m p r o d u c t i o n e ic f i e n c y . Ke y wo r d s : p u r g e g a s ; e x t r a c t h y d r o g e n; s y n he t t i c a mmo n i a
流、 多汇 报 , 争 取 他 们 的理 解 和 支 持 。其 次 , 新《 锅
运 转带来 困难 。其 次 , 在 原 材料 、 外 协件 入厂验 收 方
规》 的贯彻 执 行 , 对 产 品监 检 单 位 同样 提 出新 的要 求, 对新《 锅规》 首先要吃准 、 吃 透 才 能履 行 好 其 监
。
氢气和氮气可合成氨。反应如下 :
3 H2 + N 2 N H 3 +Q
( 下转第 1 7 2页)
・
1 7 2 ・
山 东 化 工 S HA N D 0 N G C H E M I C A L I N D U S T R Y
2 0 1 3年第 4 2卷
些企业 存在 的主要 问题 是 : 由于技术 人 员缺乏 , 质 保 责任师 不稳定 , 经 常有 空位 的情 况 , 给质 保体 系正 常
汽包系统进行热量 回收, 产生的低压蒸气送人低压 蒸汽 管 网。
PSA变压吸附技术制氢影响因素及优化措施

摘要:本文介绍了变压吸附工作原理,并分析了影响变压吸附的主要因素,认为吸附时间与吸附压力是影响变压吸附最主要的因素;同时,在变压吸附操作中应尽量提高吸附压力、降低解吸压力、延长吸附时间、降低产品纯度,以提高氢气回收率进而提高装置的经济效益。
关键词:psa变压吸附制氢优化变压吸附氢提纯工艺过程之所以得以实现是由于吸附剂在物理吸附中的具有的两个性质:一是对不同组分的吸附能力不同,二是吸附物质在吸附剂上的吸附容量随吸附质的分压上升而增加,随吸附温度的上升而下降。
利用吸附剂的这些特性,可实现吸附剂在低温、高压下吸附而在高温、低压下解析再生,从而构成吸附剂的吸附与再生循环,达到连续分离提纯氢气的目的。
由于变压吸附( psa)气体分离技术是依靠压力的变化来实现吸附与再生的,因而再生速度快、能耗低,属节能型气体分离技术。
并且,该工艺过程简单、操作稳定、对于含多种杂质的混合气可将杂质一次脱除得到高纯度产品。
因而近二十年来发展非常迅速,已广泛应用于含氢气体中氢气的提纯,混合气体中一氧化碳、二氧化碳、氧气、氮气、氢气和烃类的制取、各种气体的无热干燥等。
而其中变压吸附制取纯氢技术的发展尤其令人瞩目。
一、变压吸附的操作原理变压吸附分离技术是以固定床吸附,在连续改变体系平衡的热力学参数下,加压气体组份吸附,减压被吸附组份解吸,放出该气体组份,吸附剂得到再生。
如果在吸附和解吸过程中床层的温度维持恒定,利用吸附组份的分压变化吸附剂的吸附容量相应改变,如图 1,过程沿吸附等温线t1进行,则在ab 线两端吸附量之差△q= qa- qb 为每经加压(吸附)和减压(解吸)循环组份的分离量。
如此利用压力变化进行的分离操作就是变压吸附。
如果要使吸附和解吸过程吸附剂的吸附容量的差值增加,可以同时采用减压和加热方法进行解吸再生,在实际的变压吸附分离操作中,组份的吸附热都较大,吸附过程是放热反应,随着组份的解吸,变压吸附的工作点从 e 移向 f 点,吸附时从f点返回 e 点,沿着ef 线进行,每经加压吸附和减压解吸循环的组份分离量 q= qe- qf为实际变压吸附的差值。
甲醇驰放气提氢操作规程汇总
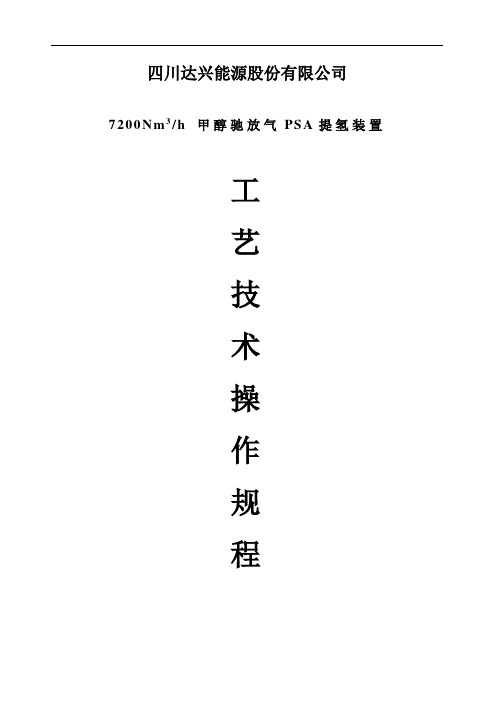
四川达兴能源股份有限公司7200N m3/h甲醇驰放气PS A提氢装置工艺技术操作规程四川达兴能源股份有限公司甲醇工段甲醇弛放气PSA提氢装置工艺技术操作规程编制:李冰审核:周卫东审定:批准:甲醇工段技术组2012年6月10日第一章装置概貌1、装置规模装置公称处理原料气能力:7200Nm3/h装置公称产氢能力:4100Nm3/h2、装置组成变压吸附(PSA)氢提纯装置由一气液分离器、六台吸附塔、一台顺放气缓冲罐和一台富氮气缓冲罐及一台解吸气缓冲罐和一台解吸气混合罐组成。
3、物料概况表 1-1组成第二章工艺过程说明第一节工艺原理1、概况本装置采用变压吸附技术(Pressure Swing Adsorption,以下简称PSA)将甲醇驰放气的组份进行分离,最终产品为:氢气、富氮气和富碳气。
氢气(纯度为96.5%)作为合成气压缩机原料气;富碳气作为焦炉气压缩机原料气;富氮气作为燃料气进入燃料管网,一部分替代驰放气作为精脱硫升温炉和转化预热炉燃料气。
2、吸附基本原理吸附是指:当两种相态不同的物质接触时,其中密度较低物质的分子在密度较高的物质表面被富集的现象和过程。
具有吸附作用的物质(一般为密度相对较大的多孔固体)被称为吸附剂,被吸附的物质(一般为密度相对较小的气体或液体)称为吸附质。
吸附按其性质的不同可分为四大类,即:化学吸附、活性吸附、毛细管凝缩、物理吸附。
PSA制氢装置中的吸附主要为物理吸附。
物理吸附是指依靠吸附剂与吸附质分子间的分子力(即范德华力)进行的吸附。
其特点是:吸附过程中没有化学反应,吸附过程进行得极快,参与吸附的各相物质间的平衡在瞬间即可完成,并且这种吸附是完全可逆的。
3、本装置所用吸附剂的特性如下1)活性氧化铝本装置所用活性氧化铝为一种物理化学性能极其稳定的高空隙Al2O3,规格为Φ3~5球状,抗磨耗、抗破碎、无毒。
对几乎所有的腐蚀性气体和液体均不起化学反应。
主要装填在吸附塔底部,用于脱除水分。
天然气制甲醇生产过程控制【模板范本】

天然气制甲醇生产过程控制1、甲醇生产采用DCS自动控制系统设定的温度、压力、流量等参数进行自动跟踪监控,此过程由岗位主操人员在中控室进行监护调节和控制。
2 、从界区来天然气压力为2。
8Mpa,总硫含量为172.9mg/Nm3,其中有机硫含量为168。
6 mg/Nm3,配入少量甲醇驰放气作为脱硫加氢来源经过预热后依次进入铁锰脱硫槽、钴钼加氢反应器、氧化锌脱硫槽作进一步的有机硫、无机硫脱硫处理,在此过程中对天然气温度、压力、流量进行监控和调节,并作好《岗位操作记录》和《设备运行记录》。
3、天然气在脱硫工序通过铁锰、钴钼加氢转化吸收和氧化锌脱硫后,将天然气中的硫含量从172。
9 mg/Nm3降至0。
1ppm,生产操作通过天然气的温度、压力进行监控和调节,并按检验计划每班对天然气中的H2S,有机硫及总硫进行取样化验,并作好分析记录.4、天然气含硫量降到0.1ppm后进入转化炉,在高温高压的条件和在催化剂的作用下,通过与水蒸汽发生化学反应后生成甲醇合成气,生产过程控制按《岗位操作规程》操作,填写《岗位操作记录》及《设备运行记录》,岗位人员对转化过程的各项温度、压力、流量等进行监控和调节,并每小时作好监测记录.每班对转炉气中CO 、CO2、H2、CH4、C2H6、N2等进行取样化验分析,并作好检验记录。
5、合成过程控制:合格的转化气通过离心压缩机压力达到7.05Mpa后进入合成工序,在此过程中对合成气温度、压力进行监控和调节并每小时作好监测记录。
DX/MS—2-09-2010 生产过程控制程序 B/1 6 、精馏生产过程控制6.1精馏工序,严格按《GB338—2004工业甲醇质量技术标准》和《岗位操作规程》进行控制,并填写好《岗位操作记录》和《设备运行记录》6.2甲醇精馏过程的操作,岗位人员对温度、压力、流量进行监控和调节,每班对粗甲醇中CH3OH含量进行两次取样检验和每班一次杂醇和甲醇残液取样检验,同时每天对精甲醇中间槽甲醇进行取样分析,并作好检验记录。
- 1、下载文档前请自行甄别文档内容的完整性,平台不提供额外的编辑、内容补充、找答案等附加服务。
- 2、"仅部分预览"的文档,不可在线预览部分如存在完整性等问题,可反馈申请退款(可完整预览的文档不适用该条件!)。
- 3、如文档侵犯您的权益,请联系客服反馈,我们会尽快为您处理(人工客服工作时间:9:00-18:30)。
甲醇驰放气变压吸附制氢工艺控制优化
在甲醇过程中产生了一些惰性气体聚集在系统中,对于甲醇的合成过程有着不利的影响,为此就要进行驰放气。
而在甲醇驰放气中氢气的含量较高,只要通过科学、有效的变压吸附技术,就可将氢气有效的收集起来,还能起到增产、节能的功效,本文主要对甲醇驰放气变压吸附的相关概论进行详细的阐述,并对制氢工艺优化进行了深入的分析,继而确保其发挥更高的效用。
标签:甲醇驰放气;变压吸附技术;制氢工艺
1 变压吸附制氢工艺原理分析
在变压吸附制氢过程中,吸附剂发挥的作用至关重要,其主要有两个特性:其一是在特定的条件下,吸附剂对于不同的吸附质发出的效力也不尽相同;其二是在不同的条件下,吸附剂对吸附质的吸附容量也存在较大差异。
随着吸附质分压的不断增加,其吸附量也会随之上升;随着吸附温度的不断升高,其吸附量便会不断地减小。
所以吸附剂的其中一个特性就是能够将氢气中的大颗粒杂质预先吸附出来,这样就能够确保氢气提取的纯度;吸附剂的第二个特性是在低温、高压条件下大量吸附杂质,在高温、低压条件下,就可进行吸附质解析、吸附剂再生的实现,如此反反复复就可达到氢气的提纯。
2 甲醇驰放气变压吸附工艺流程
将原料气混合后置于3.2-3.5MPa及零下40℃的条件下,通过气液分离器将液态物质清除掉送入PSA系统进行氢气的提纯。
在甲醇驰放气制氢工艺中,每台吸附装置需要经过吸附过程、多挤压力降低过程、顺放过程、逆放过程、冲洗过程、多挤压力上升过程、升压过程等环节。
在逆放环节中将吸附装置中残留的杂质排出,然后通过冲洗环节将剩余杂质完全解吸掉。
在逆放环节前期压力较大时,气体进入缓冲罐,在不经过逆放或冲洗气较小的时候输送到混合罐,确保混合罐中进气始终保持均匀性,继而确保混合罐压力的稳定性;在逆放环节的末期,压力较低部位的气体及冲洗环节的气体均送入到解吸气混合罐中。
解吸气通过对应的缓冲罐、混合罐压力稳定后输送到甲醇装置中炉燃料气管网。
最后通过将原料气中的氢气提纯,并与氮气进行有效的混合后,通过干燥处理便能够得到氨原料气。
3 变压吸附制氢工艺优化分析
3.1 程序方案及氢回收率分析
在化工生产过程中,12台吸附塔运行的均压次数、吸附时间、解析时间均有着密切的联系,通常认为均压次数多多益善,在确保吸附时间、解吸时间的基础上,还要保证均压次数的合理性、有效性。
针对12塔流程有两种方案,在此
方案中各个流程均设置有2个吸附塔同时进行吸附操作,但是第一种方案均压次数设置为6次;第二种方案均压次数设置为5次,在进行方案的选择过程中,不仅要确保吸附时间、解吸时间,还要很大程度上确保均压,继而确保原料气产量与氢气回收率得到提升。
通过以上两种方案的实施结果显示:方案1氢气平均回收率约为87%,方案2氢气平均回收率为83%。
可见方案1相比于方案2更加优异,其主要是方案2均压次数少一次,无法将再生过程中形成的氢气有效的应用,而且在后续的过程中所需的时间相对较长,促使解吸气中的杂质又流入吸附塔中,导致氢气回收率降低。
3.2 吸附时间与氢气回收率的关联性
在确保原料气量、生产温度、生产压力等工艺参数固定不变的基础上,增加甲醇驰放气的吸附时间,继而降低吸附剂的再生次数,使得氢气的消耗量也相对减少,如此便能提高其回收率。
然而当吸附时间延长后,杂质进入的数量就会不断的增加,难以保障氢气提取的纯度。
为了确保甲醇驰放气变压吸附技术运行的成本得到合理的控制,在确保氢气纯度的基础上增加吸附时间,从而来增加氢气的回收率。
在实际的甲醇制氢运行过程中,增加吸附时间氢气的纯度也会随之减少,通过程控设计启动工艺阀门,促使部分原料气未通过吸附塔就进入解吸气中,促使氢气回收率下降显著。
通過上图显示,随着吸附时间的上升氢气回收率降低,所以当吸附时间设置为15s,氢气回收率可升至90%。
3.3 吸附时间与产气量关系
在运行温度、运行压力、吸附时间、解吸次数等保持不变的前提下,甲醇驰放气的变化很大程度会影响氢气纯度,但是甲醇驰放气越多其中杂质越多,为了确保氢气的纯度,就要相对的减少吸附时间;反之甲醇驰放气下降时,为了提升氢气的纯度,就要适当的增加吸附时间。
4 结束语
通过以上研究发现,甲醇驰放气变压吸附制氢工艺极为的复杂、繁琐,在氢气的制取过程中,不仅要保障能够获得氢气回收率,还要确保氢气回收的纯度。
由于以上两个指标很大程度上会受到吸附时间、均压次数、原料产气量的影响,必须要是对各个影响因素进行详细的了解,才能对其进行合理、有效的调节,如此才能促使甲醇驰放气变压吸附制氢工艺更加的高效、实用。
参考文献:
[1]阴国平.甲醇驰放气变压吸附制氢工艺控制优化[J].当代化工研究,2015(1):55-56.。