材料对汽车轮辋闪光对焊成批开裂的影响
汽车车轮轮辋电阻对焊开裂原因分析

万方数据.生产碘场±严搬琢(a)轮辋中间开裂形貌(b)轮辋端缘开裂形貌图1焊缝开裂宏观形貌图5高温氧化物微观形貌图2温度不均的焊缝形貌图3对焊后轮辋端缘搭焊错边形貌裂处断面形貌见图4。
高温氧化物微观形貌见图5。
夹杂物评级:A0.B0,CO。
DO.5;AO,BO.5。
C0,D0.5。
母材金相组织见图6。
焊缝处组织见图7。
晶粒度10—11级。
检验结果表明,材料组织、夹杂物、晶粒度均未见异常。
3.焊接工艺、设备情况分析(1)从随机取样情况看,在焊接过程中,发现焊件沿焊缝方向冷热状态时的颜色均存在不一样的现象,说明加热温度不均匀。
电镜检验发现存在高温氧化物,说明未将氧化物挤出。
存在轮辋厚度方向的错边,特别是存在边部翘曲,电极压力无法对悬空状态的错边和翘曲压平,导致焊接时电流分布不均。
图4开裂处断面形貌(2)从开裂情况看,焊后去毛刺时发现轮辋端部有小裂口,占总量的比例为3.9%。
焊接接头未经过扩口等工序的塑性变形就出现开裂.表明导致轮辋焊缝开裂的原因主要是与设备调试及焊接工艺有关。
4.材料因素分析(1)合理选材。
钢的强度影响电阻焊的卷圆难度及焊接时的电极压平程度。
因此.在设备能力有限的条件下,在保证疲劳寿命的同时.尽可能选择强度级别低的牌号。
《2)硫化物的影响。
在电阻对焊过程中,若S含量过高,则将在焊缝区出现裂纹,为了防止裂纹产生,需控制Mn/S比。
另外,钢中的Mn,Si比值对电阻对焊也有重要影响,当Mn,Si在4—40之间时,焊接时形成的氧化物熔点比钢低.在电阻对焊顶锻时容易被挤出,有利于焊接质量提高。
总之.钢中的S越低越好,钢的强度越低对卷圆、焊接越有利。
从实际统计及检验的情况看,硫含量控制~般在0.010%左右,未发现硫含量与开裂率间存在对应关系,Mn,Si比的控制范围也在要求范围内。
措施及效果在原因分析的基础上.用户对相关设备进行了检测及调试,通过采取及时更换磨损严重的夹具,使加热温度均匀.并控制好错边量等措施.杜绝图6基体组织(400×图7焊缝组织(200×)假焊、搭焊,轮辋焊缝开裂率明显下降.取得了较好的效果。
汽车车轮轮辋电阻对焊开裂原因分析

滚 型 l一 滚 型 …一扩 涨 定 径 一 冲气 裂的炉次化 学成分在标准 及内控要求 决 。 l
门孔 一合成压 装一 四工 位C O 合成焊 范 围内 .其C、S、Mn Si 含量 、Al
差 ;焊 接接头错边 量的控 制。
高 。2 0 0 3年 该 用 户 三 次 出现 轮 辋 焊 缝 开 裂 质量 问题 .为 找 出开 裂 原
轮辋焊缝开裂原 因分析
1获得优质接头的基本条件及焊 .
s
材 料 方 面 :选 材 问题 ;钢 中的
n/ i S bo E
:
Hale Waihona Puke 2取样检 验分析 .图2 温 度不均 的焊缝 形貌
表 明导 致轮 辋焊 缝 开 裂 的 原 因 主要 是 与设备调试 及焊接 工艺有关 。 4材料 因素 分析 .
( )合理 选材 。钢 的强 度影响 电 1
图6 基 体组织 (0 x 4o)
阻焊 的卷 圆 难 度及 焊 接 时 的 电极 压 平程 度 。 因此 .在设 备 能 力 有 限 的 条 件 下 .在 保 证 疲 劳寿 命 的同 时 ,
区 出现 裂 纹 ,为了 防 止 裂纹 产 生 .
图7 焊缝 组织 ( 0 x 2o)
DO5 .。母 材金 相组 织见 图6。焊缝 处 需控制MnS:。另外 ,钢 中的Mns /l E /i
组 织见 图7。晶粒 度 1 - 1 。检 验 比值 对 电阻 对 焊也 有 重 要 影 响 , 当 假焊 、搭 焊 ,轮 辋 焊 缝 开 裂率 明显 0 1级
轮辋用钢hz380cl闪光对焊开裂原因

CAUSE OF CRACK IN
FLASH BUTT WELDING OF RIM STEEL HZ380CL
Zhang Zhiqiangꎬ Liu Fenglinꎬ Pei Qingtaoꎬ Jia Gaifeng
( HBIS Group Hansteel Companyꎬ Handanꎬ Heibeiꎬ 056015)
能和舒适性能不断提高ꎬ无内胎深槽滚型钢制车轮
被广泛应用到各种车辆中 [1ꎬ2] ꎮ 钢制车轮的结构由
轮辋和轮辐组成ꎮ 轮辋的生产工艺一般包括下料、
闪光焊接、刨渣、切边、压边、扩口、滚压、扩涨、气密
性测试和打孔等工序ꎬ其中闪光电阻对焊是轮辋生
产的重要工艺ꎮ 如果轮辋对焊质量不高ꎬ在成型过
程的扩口、三道滚型以及扩涨工序中ꎬ容易在焊缝处
研究工作ꎬE - mail:zzqlj616@ 126. com
16
效控制ꎮ
河北冶金 2019 年第 12 期
1
钢出厂要求进行了对比ꎮ 如表 1 所示ꎬ所有成分均
uniform distributionꎬ most of which are widmanstatten. The existence of these two factors cut the continuity
of steel matrixꎬ reduce the toughness and plasticity of steelꎬ which leads to cracking. By adjusting the upset ̄
show that there are a lot of iron oxides in the weldꎬ which are the remaining foreign matters that can not be
380CL钢制轮辋焊缝开裂分析

关键词
3
焊 缝开裂
An a l y s i s o n We l d Cr a c k i n g o f 3 8 0 CL S t e e l Wh e e l Ri m
L i Mi n a n d S o n g Z h e n g u n a
c a u s e s o fma t e i r a l f a i l u r e a r e a b n o r ma l l y c o a r s e f e r r i t e g r  ̄ i n s ,r es u l i t n g i n l o w y i e l d s t r e n g t h o f w e l d s e  ̄ f l a n d p o o r
2 o %, 远大 于轮 辋 对 焊 开 裂 比率 3 % 0 的 企业 内 控 指标 。针对 这种 情况 , 济钢 利用 光学显 微镜 、 扫 描 电子显 微镜 、 能谱 仪 等检验 设备 , 对轮 辋焊缝 开 裂 部位 进行 了观察 分 析 , 以期 查 明 轮 辋焊 缝 开 裂 原 因, 并 找 出根本 的解 决办法 。
・
第 l 9卷第 4期 2 8。 2 0 1 3年 8月
宽厚板
nD E AND HE AVY P LA T E
V0 1 . 1 9. N o . 4 Au g u s t 2 0 1 3
・
技术讨论 ・
3 8 0 C L钢 制轮辋 焊 缝 开裂 分 析
李 敏 宋振 官
( J i n a n I r o n a n d S t e e l G r o u p C o .L t d )
Ab s t r a c t Mi c r o ‘ e x a mi n a i t o n a n d a n a l y s i s h a v e b e e n p e fo r r me d o n we l d c r a c k i n g b y me ns a o f t e s t i n g e q u i p me n t
C380CL钢车轮焊缝开裂原因分析

C380CL钢车轮焊缝开裂原因分析张明博;刘效云;高建国;薛启河;韩宇;程玉君【摘要】C380CL钢车轮焊接时焊缝易开裂.对焊缝开裂的原因进行了研究.结果表明:C380CL钢车轮焊缝开裂的原因为,母材采用较大量的锰进行固溶强化,导致其碳当量和裂纹敏感系数增大,焊接性能恶化;其次是焊接工艺参数不适用于母材.据此,将C380CL钢的C、Mn含量(质量分数)分别从最大0.08%和1.15%降低至最大0.07%和0.75%,并添加微量的Nb、Ti细晶强化,以使确保其力学性能不致降低.结果,钢的碳当量和裂纹敏感性指数分别降低了0.113%和0.055%.改进的焊接工艺参数为:闪光速度1.5 mm/s,顶锻留量6 mm,带电顶锻时间1.2s,焊接时间14.0 s,钳口间距30 mm.成分和焊接工艺参数优化后,焊缝开裂的C380CL钢车轮的百分率降低了近4.0%.【期刊名称】《上海金属》【年(卷),期】2019(041)003【总页数】5页(P34-38)【关键词】C380CL钢;焊接性能;显微组织;成分;焊接工艺参数【作者】张明博;刘效云;高建国;薛启河;韩宇;程玉君【作者单位】河钢股份有限公司承德分公司,河北承德670102;河钢股份有限公司承德分公司,河北承德670102;河钢股份有限公司承德分公司,河北承德670102;河钢股份有限公司承德分公司,河北承德670102;河钢股份有限公司承德分公司,河北承德670102;河钢股份有限公司承德分公司,河北承德670102【正文语种】中文车轮是汽车底盘系统中的承载和保障车辆安全行驶的重要部件[1- 4],不仅承受车辆的负重和自重,还承受横向力、驱动(制动)扭矩和行驶过程中产生的各种应力。
河钢承钢生产的C380CL钢主要用于轮辋,其工艺流程为下料、对焊、刨渣、扩口、滚压、扩张、气密性检测。
目前存在的问题是焊接接头易开裂,即焊后扩口扩张开裂[5],开裂率达4.50%,远达不到低于0.8%的要求,严重影响了车轮的生产效率和制造成本。
汽车轮辋闪光对焊焊接开裂原因分析

pat s g 3 0 L v h l w els e o i n I n ad SelC . t. hog h m cl l i 8 C e i e h e t l fQ a a r n t o,Ld,tru h c e ia nun c e n o e
YI Na N ZHOU hi i Z we CUIYa g n LIFe ZHAO n i Li L ie g IRu h n
( h eerhIstt o eh ooy ( ina rnadSel o, t. T eR sa tue f cn lg ) Qa nI n te C . Ld ) c ni T o
A s a t Ai n tt e s r u r c h n me o ftu k rm u twed n n a d me t e l b t c mi g a h e i s c a k p e o n n o c r o r i bt l i g i o si wh e c
减 重 和节 能是 汽车行 业未 来 的发展 趋 势 。为
象 。这不仅造成材料和工时的浪费 ,也相应增加 了产品成本 。因此 ,对轮辋焊接开裂成因的研究
减轻车身重量 ,汽车行业逐步增加 了高强钢板 的 使用¨ 。车轮钢具有强度和硬度高、疲劳性能以 J 及冷弯性能好的特点 ,因此被广泛应用于制造载 重卡车 、客车的轮辐和轮辋。焊接是轮辐和轮辋 生产的关键工序之一。闪光对焊因其具有省 时、 省料和省能源等诸 多优点 ] 。 ,使其在汽车轮辋 生产 中得到广泛应用。闪光对焊后 ,轮辋还须经 受扩 口、滚压成形和扩张定径等多次大的变形工 序 ,因此对焊接接头质量要求非常高。然而 ,国 内某车轮厂在使用首钢迁钢公 司 ( 称迁钢公 简 司)30 L生产轮辋时 ,尤其在扩 口及扩张工序 8C 中,发生过焊接 接头强度低 导致 焊缝 开裂 的现
汽车轮毂加工方法与工艺分析

本文以深槽轮辋为例,阐述兼具使用性能优点和加工成本优势的压力成形制造工艺。
通过分析轮毂的材料、结构及加工方法,详细介绍了轮辋生产过程及所用装备,并展望未来生产技术的特点和发展方向。
1 序言汽车作为现代化的交通工具,其数量越来越多。
车轮是汽车必须的、基本的和重要的部件,其安全性、经济性及外观质量是目前使用者关注的主要指标。
不同车辆的轮毂结构不同、材料不同,其加工工艺也不相同。
通过分析车辆轮毂常使用的材料及加工方法,着重介绍具有深槽结构的家用汽车铝合金轮毂加工工艺及其特点。
2 汽车轮毂的材料及制造现状2.1 轮毂结构与材料轮毂是汽车支撑轮胎的圆形结构,由轮辋和轮辐组成,轮辋和轮辐可以是整体式的、永久联接式的和可拆卸式的。
轮辋常使用的结构有深槽轮辋和平底轮辋,并在此结构上有不同的改进,比如对开式轮辋、半深槽轮辋、平底宽轮辋及全斜底轮辋,用于不同的场合。
深槽轮辋如图1所示,断面中部呈凹槽形,有凸缘结构,用于安放轮胎,肩部向中间倾斜4°~6°。
该结构简单,刚度大,质量较小,对于尺寸小、弹性大的轮胎安装比较方便,因此适用于轿车及轻型越野车。
平底轮辋是货车常用的结构形式。
图1 深槽轮辋常见的汽车轮毂有钢质轮毂和铝合金轮毂。
钢质轮毂强度高,常用于大型载货汽车,质量较重;铝合金轮毂质量相较要轻很多,相同体积的铝合金轮毂比钢质轮毂轻2/3左右,符合如今低碳的使用理念,且导热快,散热性能好。
图2永久联接式轮毂结构2.2 轮毂常用加工方法目前铝合金轮毂的生产方法有铸造法、锻造法、冲压法和旋压法。
我国铝合金轮毂仍然以低压铸造为主,随着技术的发展,其加工工艺不断进行变革。
铝合金的铸造工艺主要有4种:重力铸造、低压铸造、反压铸造和挤压铸造。
大部分的铝合金车轮采用低压铸造生产,这是铝合金车轮铸造工艺中的主要技术。
铸造车轮需要准备铸型,熔炼金属,浇筑冷却凝固成形后取出铸件,工序多、设备大,产品容易出现缩孔、缩松等质量缺陷,特别是铸件尺寸较薄的情况下,更容易出现质量问题。
某SUV轮罩开裂问题的分析及设计改进
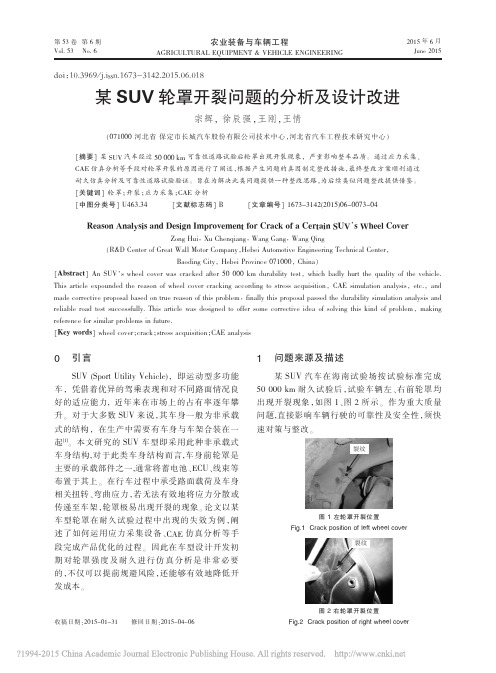
0 引言
SUV (Sport Utility Vehicle), 即运动型多功能 车, 凭借着优异的驾乘表现和对不同路面情况良 好的适应能力, 近年来在市场上的占有率逐年攀 升。 对于大多数 SUV 来说,其车身一般为非承载 式的结构, 在生产中需要有车身与车架合装在一 起[1]。 本文研究的 SUV 车型即采用此种非承载式 车身结构,对于此类车身结构而言,车身前轮罩是 主要的承载部件之一,通常将蓄电池、ECU、线束等 布置于其上。 在行车过程中承受路面载荷及车身 相关扭转、弯曲应力,若无法有效地将应力分散或 传递至车架,轮罩极易出现开裂的现象。 论文以某 车型轮罩在耐久试验过程中出现的失效为例,阐 述了如何运用应力采集设备、CAE 仿真分析等手 段完成产品优化的过程。 因此在车型设计开发初 期对轮罩强度及耐久进行仿真分析是非常必要 的,不仅可以提前规避风险,还能够有效地降低开 发成本。
表 4 仿真分析结果对比 Tab.4 Comparison of two structures’ simulative results
优化前
优化后
开裂点处应力寿命
左前轮罩 右前轮罩 左前轮罩 右前轮罩
材料
DC53D+Z
HC220YD+Z
屈服极限 / MPa
160
230
最大应力 / MPa
159
168
通过鉴定, 开裂制件的材质性能达到设计状 态,供应商所用材质与设计相符。 2.2 工艺过程控制原因排查
通过现场对开裂车辆确认及焊点剥离试验, 焊点均满足设计要求, 查焊装焊接设备参数亦满 足工艺标准。 故工艺过程控制不存在问题,可排除 人员技能不足及焊接设备的问题。 2.3 应力采集及仿真分析
(1)应 力 采 集 : 分 别 抽 取 同 一 批 次 生 产 的 车 辆 进行应力测试。 根据裂纹走向确定裂纹的主应力 方向, 沿该方向布置若干应变片, 贴片方向与裂 纹方向垂直[2]。 部分贴片的位置如图 4、图 5 所示。
汽车轮毂单元总成钢轴系工件断裂分析
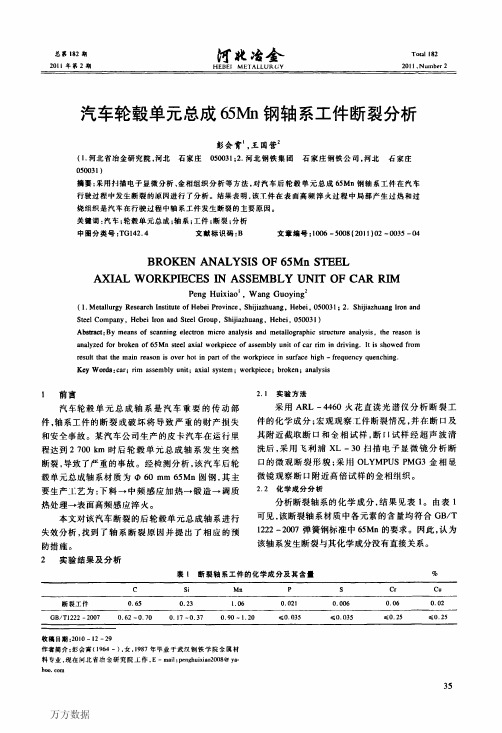
断裂,导致了严重的事故。经检测分析,该汽车后轮
毂单元总成轴系材质为①60 mm 65Mn圆钢,其主
要生产:l:艺为:下料一中频感应加热一锻造一调质 热处理一表面高频感应淬火。 本文对该汽车断裂的后轮毂单元总成轴系进行 失效分析,找到了轴系断裂原因并提出了相应的预
防措施。
2
分析断裂轴系的化学成分,结果见表l。由表1 可见,该断裂轴系材质中各元素的含量均符合GB/T 1222—2007弹簧钢标准中65Mn的要求。冈此,认为 该轴系发生断裂与其化学成分没有直接关系。
实验结果及分析
表l 断裂轴系工件的化学成分及其含量
%
收稿日期:2010—12—29
作者简介:彭会霄(1964一)。女,1987年毕业于武汉钢铁学院金属材 料专业.现在河北省冶金研究院上作.E—mail:penghuixia02008@ya—
boo.cam
35
万方数据
2
3*口%mmn
域为灰色;断口术发现明显的断裂耀。图l b为n刚 a十的断tl处所取的高倍试样,制样后观察其盒相 组织:
4
局部存在过热过烧组织,致使.【件的韧性降低,汽车 在运行过程中轴系工件在外加载荷的反复作用下, 使过热过烧区域局部熔化的孔洞逐渐扩大,最终导 致了轮毂单元总成轴系的断裂,而使汽车运行中发 生了严重的交通事故。分析认为,一般工件产生过 热过烧的原因有两个:一是在较高温度下长时间地 保温加热,另一种情况是保温时间虽然很短但加热 温度较高。该轴系工件的材质为65Mn,其液相线
裂。
(上接第8页) 3
结语
炉瓦斯灰用于烧结生产是较为合理的利用途径。 (4)由于瓦斯灰碳含量不稳定,配入烧结后对 烧结配碳量的稳定性有所影响,要求生产操作过程 中,加大除尘灰残碳量分析频次,并及时调整烧结配 碳量,做到配料混匀,保证烧结指标和烧结矿质量指 标达到最佳。
汽车轮辋焊接区裂纹分析_赵玉梅

赵玉梅1赵红利1张红霞1杨坤21.湖北汽车工业学院材料工程系湖北十堰442002;2.东风汽车车轮有限公司湖北十堰442000摘要:汽车滚型轮辋闪光对焊后焊接区域发现裂纹,通过对有裂纹的轮辋进行了化学成分分析和宏、微观检验。
并对焊接工艺过程进行了研究,结果表明,焊接过程形成了焊缝表层氧化物夹杂,刮渣工艺不良造成焊缝表层毛刺状撕裂,通过调整焊接和刮渣工艺,可避免焊接区裂纹的发生。
主题词:轮辋闪光对焊裂纹夹杂物1引言作为汽车行驶系重要组成部分的车轮,要求其轮辋的焊接质量可靠,外形正确,有足够的抗疲劳断裂能力。
其制造质量的好坏直接影响到车轮乃至整车的各项性能。
某汽车车轮厂生产的大型载货汽车滚型轮辋在成型后采用磁力探伤发现存在裂纹。
其生产工序流程是将剪切板弯曲,然后通过闪光对接焊制成的。
具体为:剪条料→滚边→卷圆→压平→闪光对焊→刮渣→滚压焊缝→切端头→校圆→扩口→一次滚型→二次滚型→三次滚型→扩张精整→冲气门孔等。
本文对生产工序中产生裂纹的轮辋进行分析。
2理化检验2.1母材化学成分分析从裂纹件母材上截取试样进行化学分析,分析结果列于表1。
该车轮生产厂选择的是材料牌号为B380CL的汽车用车轮钢,其供货状态为热轧后正火的板材。
化学成分分析结果表明,该轮辋的化学成分符合B380CL标准。
汽车轮辋焊接区裂纹分析2.2金相检测轮辋焊接区域裂纹宏观形貌见图一,由图中可见焊缝处略高出基体。
裂纹位于基体和焊缝的边缘处,不是正焊缝的位置。
金相试样取样部位如图一箭头所示,轮辋裂纹微观形貌如图二所示,裂纹起源于表面,并位于近表面延伸,长度较长,大于2毫米,但深度浅,离表层深度约0.2毫米。
轮辋裂纹采用金相显微镜进一步放大后,末端形貌及裂纹附近显微组织如图三所示。
裂纹中间形貌及裂纹附近显微组织如图四所示。
焊缝显微组织见图五,远离焊缝的基体处组织见图六。
从图三中可清晰见到裂纹末端有细小开叉,近裂纹处显微组织皆为因受外力变形后拉长的铁素体(右侧),更远处(左侧)是趋于等轴状的铁素体和极少量小块状珠光体。
车轮钢闪光对焊工艺参数对焊接接头性能的影响
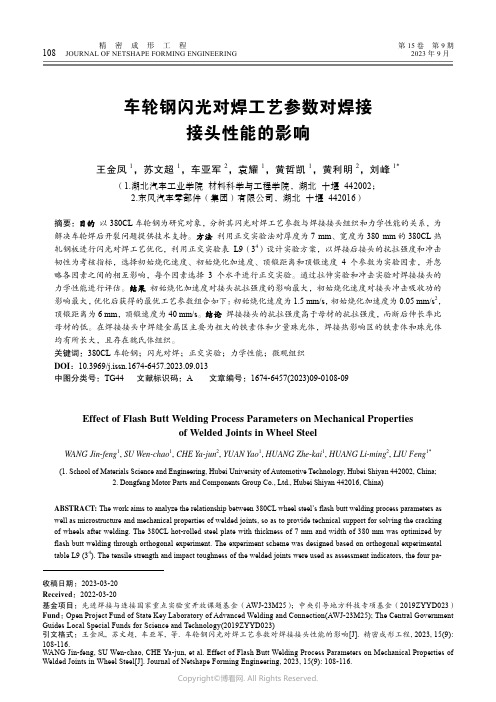
精 密 成 形 工 程第15卷 第9期108 JOURNAL OF NETSHAPE FORMING ENGINEERING2023年9月收稿日期:2023-03-20 Received :2022-03-20基金项目:先进焊接与连接国家重点实验室开放课题基金(AWJ-23M25);中央引导地方科技专项基金(2019ZYYD023) Fund :Open Project Fund of State Key Laboratory of Advanced Welding and Connection(AWJ-23M25); The Central Government Guides Local Special Funds for Science and Technology(2019ZYYD023)引文格式:王金凤, 苏文超, 车亚军, 等. 车轮钢闪光对焊工艺参数对焊接接头性能的影响[J]. 精密成形工程, 2023, 15(9): 108-116.WANG Jin-feng, SU Wen-chao, CHE Ya-jun, et al. Effect of Flash Butt Welding Process Parameters on Mechanical Properties of Welded Joints in Wheel Steel[J]. Journal of Netshape Forming Engineering, 2023, 15(9): 108-116.车轮钢闪光对焊工艺参数对焊接接头性能的影响王金凤1,苏文超1,车亚军2,袁耀1,黄哲凯1,黄利明2,刘峰1*(1.湖北汽车工业学院 材料科学与工程学院,湖北 十堰 442002;2.东风汽车零部件(集团)有限公司,湖北 十堰 442016)摘要:目的 以380CL 车轮钢为研究对象,分析其闪光对焊工艺参数与焊接接头组织和力学性能的关系,为解决车轮焊后开裂问题提供技术支持。
闪光对焊各参数对焊接质量的影响及调整方法
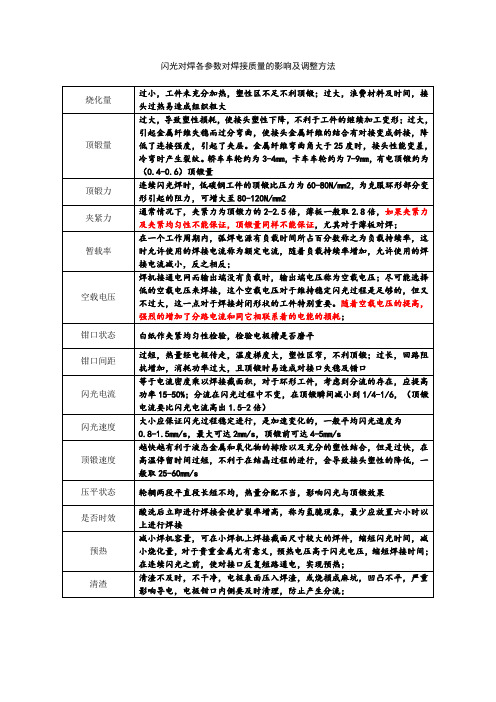
连续闪光焊时,低碳钢工件的顶锻比压力为60-80N/mm2,为克服环形部分变形引起的阻力,可增大至80-120N/mm2
夹紧力
通常情况下,夹紧力为顶锻力的2-2.5倍,薄板一般取2.8倍,如果夹紧力及夹紧均匀性不能保证,顶锻量同样不能保证,尤其对于薄板对焊;
暂载率
在一个工作周期内,弧焊电源有负载时间所占百分数称之为负载持续率,这时允许使用的焊接电流称为额定电流,随着负载持续率增加,允许使用的焊接电流减小,反之相反;
钳口间距
过短,热量经电极传走,温度梯度大,塑性区窄,不利顶锻;过长,回路阻抗增加,消耗功率过大,且顶锻时易造成对接口失稳及错口
闪光电流
等于电流密度乘以焊接截面积,对于环形工件,考虑到分流的存在,应提高功率15-50%;分流在闪光过程中不变,在顶锻瞬间减小到1/4-1/6,(顶锻电流要比闪光电流高出1.5-2倍)
空载电压
焊机接通电网而输出端没有负载时,输出端电压称为空载电压;尽可能选择低的空载电压来焊接,这个空载电压对于维持稳定闪光过程是足够的,但又不过大,这一点对于焊接封闭形状的工件特别重要。随着空载电压的提高,强烈的增加了分路电流和同它相联系着的电能的损耗;
钳口状态
白纸作夹紧均匀性检验,检验电极槽是否磨平
闪光对焊各参数对焊接质量的影响及调整方法
烧化量
过小,工件未充分加热,塑性区不足不利顶锻;过大,浪费材料及时间,接头过热易造成组织粗大
顶锻量
过大,导致塑性损耗,使接头塑性下降,不利于工件的继续加工变形;过大,引起金属纤维失稳而过分弯曲,使接头金属纤维的结合有对接变成斜接,降低了连接强度,引起了夹层。金属纤维弯曲角大于25度时,接头性能变差,冷弯时产生裂纹。轿车车轮约为3-4mm,卡车车轮约为7-9mm,有电顶锻约为(0.4-0.6)顶锻量
380CL
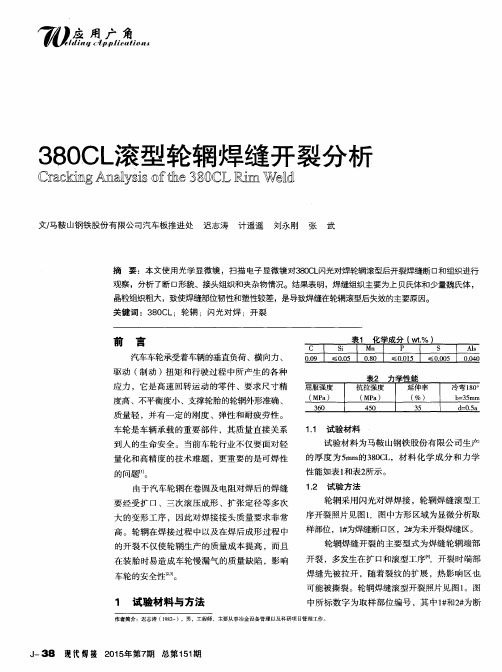
1.1 试 验 材 料 试验材料为马鞍山钢铁股份有 限公 司生产
的厚度 为5r am的380CL,材料 化学 成分 和力学 性 能如 表 1和表 2所示 。 1_2 试 验 方法
轮辋采用 闪光对焊焊接 ,轮辋焊缝滚型工 序开裂照片见图1,图中方形 区域为显微分析取 样部 位 ,1#为焊缝 断 口区 ,2#为未 开裂 焊缝 区 。
轮辋焊缝开裂的主要 型式为焊缝轮辋端部 开裂 ,多发生在扩 口和滚型工序 ,开裂时端部 焊缝先被拉 开 ,随着裂纹 的扩展 ,热影响 区也 可能被撕 裂。轮辋焊缝滚型开裂照片见图 1。图
1 试验材料与方法
中所标数字为取样部位编号 ,其 中1#和2#为断
作者简 介:迟 志涛 (1982一),男 ,工程师 ,主要从事冶金设备管理 以及科研项 目管理工作。
刖 昌
汽车车 轮承受 着 车辆过程 中所产生 的各种
应力 ,它是高速 回转运动的零件 、要求 尺寸精 度高 、不平衡度小 、支撑轮胎的轮辋外形准确、 质量轻 ,并有一定的刚度 、弹性 和耐疲 劳性 。
屈服强度 l 抗拉强度 l 延伸率 l 冷弯180。
J一38 现代焊接 2015年第7期 总第151期
(MPa) l (MPa) 『 (% ) l b=35mm
35
车轮是车辆承载的重要部件 ,其 质量直接关 系 到人 的生命安全 。当前车轮行业不仅要面对轻 量化和高精度 的技术难题 ,更重要的是可焊性 的问 题川。
由于汽车轮辋在卷圆及 电阻对焊后 的焊缝 要经受 扩 口、三次滚压成形 、扩张定径等多次 大的变形 工序 ,因此对焊接接头质量要求非常 高。轮辋 在焊接过程 中以及在焊后成形过程 中 的开裂不仅使 轮辋 生产的质量成本 提高 ,而且 在装胎时易造成车轮慢漏气 的质量 缺陷 ,影响 车 轮 的安 全 ∞ 。
乘用车轮辋用钢SPFH590闪光焊失效分析及改进

0.34
0.17
C
0.31
0.32
0.15
注:Ceq(IIW) =C + Mn/6 + ( Cr + Mo + V)/5 + ( Cu + Ni) / 15 ;Ceq( JIS) =C + Mn/6 + Si/24 + Cr/5 + NV40 + Mo/4 + V/ 14;Pcm-C + S/30 + ( Mn + Cu + C/ /20 + N/60 + Mo/15 + V/ 10+5B&
闪光对焊属于固相焊接方法[1],是能实现 整个端面一次性连接的高效率焊接方法。闪光 焊几乎不要求待焊工件表面清理,不需添加其 他焊接材料,也是相比其它焊接方法所独有的 优势。闪光对焊方法的特点:材料结合面处已 达到金属液化温度,在随后的顶锻过程中,界面 附近的金属发生了较大的塑性变形,焊接接头 是在热、电、机械力的综合作用下形成的。考虑 到接头不同位置处经历的加热温度及发生的塑 性变形量均不同,相应的微观组织和力学性能 也有较大差异,正是由于闪光焊的上述特点,对 材料提出了更高的要求。
状组织A为2级,B为0.5级,C为1.0级。
表4 A-C夹杂物、带状、晶粒度和金相组织类型
样品标识 夹杂物 带状级别 晶粒度
金相组织
A
A0.5,D0.5
2
12 铁素体+珠光体
B
D0.5
0.5
12 铁素体+珠光体
C
D0.5
1
12 铁素体+珠光体
图3 A金相组织
图4 B金相组织
-26 -
SAE1018盘条闪光对焊后接头脆断原因分析_刘章满

2012年第6期ANGANG TECHNOLOGY 总第378期刘章满,工程师,1995年毕业于辽宁科技学院炼钢及铁合金专业,现任本钢集团北营钢铁(集团)股份有限公司总工程师。
SAE1018盘条闪光对焊后接头脆断原因分析刘章满,胡建伟,康冬梅,徐志强(本溪北营钢铁(集团)股份有限公司,辽宁本溪117017)摘要:对SAE1018热轧盘条连续闪光对焊后接头出现的脆断现象进行了分析。
结果表明,焊接头脆断是热影响区过热引起的。
采取降低焊接二次电压、高温区快冷、降低钢中S 含量等措施,可使SAE1018盘条闪光对焊焊接接头过热倾向明显改善。
关键词:SAE1018盘条;闪光对焊;过热;接头脆断中图分类号:TG407文献标识码:A文章编号:1006-4613(2012)06-0051-04Analysis on Causes Leading to Brittle Failure at Joints ofSAE1018Wire Rod after Flash Butt WeldingLiu Zhangman ,Hu Jianwei ,Kang Dongmei ,Xu Zhiqiang(Benxi Beiying Iron &Steel (Group )Co.,Ltd.,Benxi 117017,Liaoning,China )Abstract :Analysis on the causes leading to brittle failure at joints of the SAE1018hot-rolled wire rod after continuous flash butt welding is carried out.The results show that the brittle failure is caused by overheating at the heat affected zone.The tendency of overheating occurred at welded joints of the SAE 1018wire rod after flash butt welding is obviously improved by adopting such measures as lowering the secondary voltage for welding,rapidly cooling at high temperature zone and lowering the content of sulphur in the steel.Key words :SAE1018wire rod;flashing butt welding;overheating;brittle failure at joint本溪北营钢铁股份有限公司生产的Φ14.0mm 热轧SAE1018盘条经过拉拔加工用于制造螺杆。
2A14_合金轮毂疲劳开裂成因分析

0前言轮毂是飞机起落架、机轮的重要组成构件,是飞机起飞、滑行降落的主要受力构件。
轮毂的强度对飞机的安全和性能至关重要[1]。
高强度的受力、复杂多变的服役环境,都对飞机轮毂的制造工艺及材料特性,提出了较高的要求。
资料表明,目前飞机机轮使用过程中,80%的飞机轮毂故障原因为疲劳失效,它是引起飞机轮毂结构失效的最主要原因之一[2]。
2A14铝合金属Al-Cu-Mg-Si 系锻铝,是锻铝中的典型合金,具有高强度、髙硬度的特点。
该合金的铜元素含量和硬铝相当,所以也叫高强度硬铝合金。
2A14合金是目前用于制造飞机轮毂的主要合金之一。
某公司生产的2A14-T6合金飞机轮毂在进行疲劳滚转实验时,发生了开裂现象。
本文主要对此类2A14合金轮毂开裂原因进行了综合分析,并根据分析结果,对该公司2A14轮毂锻件的生产工艺进行了优化。
1试验方法断口面分析:观察轮毂开裂部位,切取开裂部位断口,置于酒精溶液中进行超声清洗。
清洁后用HitachiS-400扫描电镜进行微观断口观察,加速电压为20kV;采用牛津X-Max能谱仪进行成分分析。
显微组织分析:切取开裂处裂纹源部位,镶样,采用自动磨样机磨制纵截面,采用凯勒试剂进行浸蚀;采用Leica DM 4000M 光学显微镜进行金相组织观察;采用HitachiS-400扫描电镜进行微观观察,加速电压为20kV;采用牛津X-Max 能谱仪进行成分分析。
2试验结果及分析2.1断口面分析图1为2A14-T6飞机轮毂疲劳失效宏观形貌图。
经宏观观察分析,图1(a )中方框部位为轮毂疲劳开裂部位,开裂部位的裂纹源为图1(b )中圆圈标注部位。
图1飞机轮毂开裂部位宏观形貌图切取图1(b )的断口面进行扫描电镜形貌分析和能谱分析,裂纹源部位扫描电镜形貌见图2。
图2(c )圈内为裂纹源,图2(a )为裂纹源部位2A14合金轮毂疲劳开裂成因分析孙娜,何勇,黄启波,李霜(西南铝业(集团)有限责任公司,重庆401326)摘要:采用光学显微镜、扫描电镜及能谱仪等检测仪器,对2A14合金轮毂锻件开裂部位进行了断口面分析、组织分析和能谱分析,讨论了疲劳开裂的成因。
汽车轮毂法兰旋铆裂纹影响因素分析
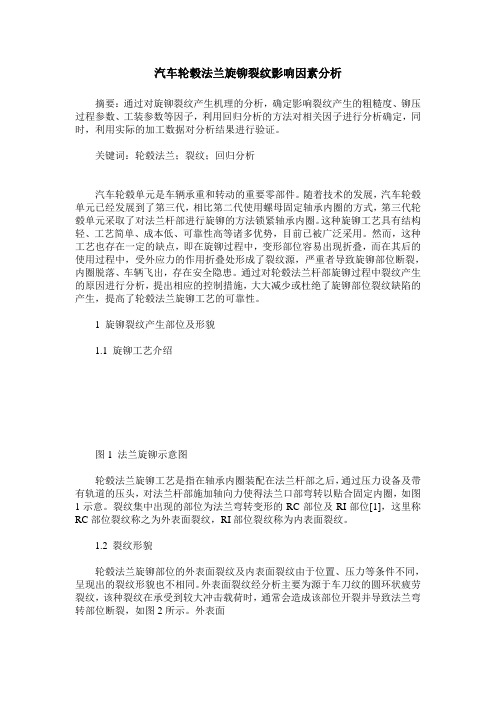
汽车轮毂法兰旋铆裂纹影响因素分析摘要:通过对旋铆裂纹产生机理的分析,确定影响裂纹产生的粗糙度、铆压过程参数、工装参数等因子,利用回归分析的方法对相关因子进行分析确定,同时,利用实际的加工数据对分析结果进行验证。
关键词:轮毂法兰;裂纹;回归分析汽车轮毂单元是车辆承重和转动的重要零部件。
随着技术的发展,汽车轮毂单元已经发展到了第三代,相比第二代使用螺母固定轴承内圈的方式,第三代轮毂单元采取了对法兰杆部进行旋铆的方法锁紧轴承内圈。
这种旋铆工艺具有结构轻、工艺简单、成本低、可靠性高等诸多优势,目前已被广泛采用。
然而,这种工艺也存在一定的缺点,即在旋铆过程中,变形部位容易出现折叠,而在其后的使用过程中,受外应力的作用折叠处形成了裂纹源,严重者导致旋铆部位断裂,内圈脱落、车辆飞出,存在安全隐患。
通过对轮毂法兰杆部旋铆过程中裂纹产生的原因进行分析,提出相应的控制措施,大大减少或杜绝了旋铆部位裂纹缺陷的产生,提高了轮毂法兰旋铆工艺的可靠性。
1 旋铆裂纹产生部位及形貌1.1 旋铆工艺介绍图1 法兰旋铆示意图轮毂法兰旋铆工艺是指在轴承内圈装配在法兰杆部之后,通过压力设备及带有轨道的压头,对法兰杆部施加轴向力使得法兰口部弯转以贴合固定内圈,如图1示意。
裂纹集中出现的部位为法兰弯转变形的RC部位及RI部位[1],这里称RC部位裂纹称之为外表面裂纹,RI部位裂纹称为内表面裂纹。
1.2 裂纹形貌轮毂法兰旋铆部位的外表面裂纹及内表面裂纹由于位置、压力等条件不同,呈现出的裂纹形貌也不相同。
外表面裂纹经分析主要为源于车刀纹的圆环状疲劳裂纹,该种裂纹在承受到较大冲击载荷时,通常会造成该部位开裂并导致法兰弯转部位断裂,如图2所示。
外表面图2 外表面裂纹形貌图3 内表面裂纹形貌裂纹的产生一般是在旋铆过程中,由于材料延展拉伸,导致材料表面原有的车刀痕发生扩展,从而引起表面的裂纹,裂纹形态一般较容易发现,在低倍显微镜或肉眼即可发现。
内表面裂纹通常为旋铆过程中由于材料发生挤压,当材料流动不畅或遇到杂质时,发生材料折叠,进而表现为微裂纹状态,如图3所示。
汽车铝合金轮毂深轮唇凹槽圆角开裂分析及解决方法

汽车铝合金轮毂深轮唇凹槽圆角开裂分析及解决方法发布时间:2021-06-15T16:00:19.973Z 来源:《基层建设》2021年第7期作者:耿家勤[导读] 摘要:对铝合金轮毂深轮唇凹槽圆角开裂形成原因进行分析,通过优化凹槽结构,解决了轮毂深轮唇圆角开裂的问题,提高了产品的良品率,获得了良好的经济效益。
广东省佛山市南海奔达模具有限公司摘要:对铝合金轮毂深轮唇凹槽圆角开裂形成原因进行分析,通过优化凹槽结构,解决了轮毂深轮唇圆角开裂的问题,提高了产品的良品率,获得了良好的经济效益。
这些措施对于相同类型产的同类缺陷具有同样的效果,对解决复杂铝合金金属型铸件裂纹具有指导意义。
关键词:铝合金轮毂、深轮唇凹槽、结构优化、解决措施前言:在铝合金轮毂的制造生产中,发现深轮唇凹槽处的圆角开裂有普遍现象。
本次研究内容是针对于此展开的。
通常铝合金裂纹主要可分为两种,一种是冷裂,一种是热裂。
冷裂纹是指合金在低于合金固相线温度时形成的裂纹。
而热裂指的是合金在高于合金固相线温度时形成的裂纹。
通俗地说,冷裂是铸件冷却到低温时,作用在铸件上的铸造应力超过铸件本身强度或塑性所允许的程度而产生的。
因此,凡是增加铸造应力,降低强度和塑性的因素都将促使冷裂纹的产生。
而热裂则是合金在固相线温度以上的固液区间冷却时,由于收缩受阻而产生的应力超过了当时金属的强度,就会导致热裂纹的产生[1]。
首先,本研究旨在弄清轮毂裂纹究竟是属于冷裂还是热裂;其次,通过分析裂纹区域的金相组织,获得产生裂纹的主要原因;最后根据主要原因寻求找到解决办法,减少或根除轮辐R裂纹。
1.问题的描述部分产品在生产过程中出现小R角开裂现象,课题统计深轮唇凹槽圆角易开裂的轮毂产品共26款,出现模具开裂的产品数量为17款,占总数的65.4%。
2.铝合金轮毂裂纹缺陷的组织分析 2.1分析铸件样品选取及金相试样如图2.1所示,选取生产现场开裂的铸件样品,裂纹缺陷存在于R角位置的铸件。