工艺路线方案一
实施方案 工艺路线

实施方案工艺路线工艺路线是指在生产过程中,为了达到预期的生产目标,按照一定的流程和方法进行操作和管理的具体方案。
在制定工艺路线时,需要考虑到生产设备、原材料、生产工艺、人力资源等因素,以确保生产过程的顺利进行和产品质量的稳定提升。
首先,确定产品需求和规格。
在制定工艺路线之前,必须明确产品的需求和规格,包括产品的功能特点、外观要求、尺寸规格等。
只有明确了产品的需求和规格,才能有针对性地制定工艺路线,确保生产出符合要求的产品。
其次,分析原材料和生产设备。
在确定产品需求和规格后,需要对原材料和生产设备进行全面的分析。
原材料的选择和质量直接影响产品的质量和成本,而生产设备的性能和稳定性则决定了生产效率和产品质量。
因此,在制定工艺路线时,必须充分考虑原材料和生产设备的特点,以确保生产过程的顺利进行。
然后,优化生产工艺。
在分析原材料和生产设备的基础上,需要对生产工艺进行优化。
生产工艺的优化包括工艺流程的设计、生产参数的确定、工艺操作的规范等方面。
通过优化生产工艺,可以提高生产效率、降低生产成本,同时确保产品质量的稳定提升。
接着,制定生产计划和管理控制。
在确定产品需求和规格、分析原材料和生产设备、优化生产工艺之后,需要制定详细的生产计划和管理控制方案。
生产计划包括生产周期、生产数量、生产进度等方面,而管理控制则包括生产过程的监控、质量控制、安全管理等方面。
通过制定生产计划和管理控制,可以有效地组织和管理生产过程,确保产品按时按量生产,并且保证产品质量和安全。
最后,建立质量管理体系和持续改进机制。
在制定工艺路线之后,需要建立完善的质量管理体系和持续改进机制。
质量管理体系包括质量标准的制定、质量检测的实施、质量问题的处理等方面,而持续改进机制则包括对生产过程的不断优化和改进。
通过建立质量管理体系和持续改进机制,可以不断提升产品质量和生产效率,确保企业的持续发展和竞争优势。
综上所述,制定工艺路线是生产过程中至关重要的一环,只有制定了科学合理的工艺路线,才能确保生产过程的顺利进行和产品质量的稳定提升。
杠杆零件的加工工艺及夹具毕业设计

杠杆零件的加工工艺及夹具设计绪论加工工艺及夹具毕业设计是对所学专业知识的一次巩固,是在进行社会实践之前对所学各课程的一次深入的综合性的总复习,也是理论联系实际的训练;机床夹具已成为机械加工中的重要装备,同时是机械加工不可缺少的部件,在机床技术向高速、高效、精密、复合、智能、环保方向发展的带动下,夹具技术正朝着高精、高效、模块、组合、通用、经济方向发展;机床夹具的设计和使用是促进生产发展的重要工艺措施之一;随着我国机械工业生产的不断发展,机床夹具的改进和创造已成为广大机械工人和技术人员在技术革新中的一项重要任务;2 杠杆加工工艺规程设计零件的作用题目给出的零件是等臂的杠杆;它的主要的作用是用来支承、固定的;要求零件的配合要符合要求;传统的杠杆加工由于加工比较粗糙加工过程比较简单,既耗时又没有科学性此杠杆如果按传统加工工艺来加工由于没有考虑到工件材料及脆塑性能将会影响加工结果,再有加工工艺过程顺序选择也将会影响加工结果;为此,此夹具就是要克服这些缺点;零件的工艺分析由分析零件图可知,杠杆中间的两平面和左右两边的端面要进行切削加工,Φ25、Φ10、Φ8孔的端面为平面,这样可以防止加工的过程中钻头钻偏,可以保证加工的精度和配合的精度;另外,除了Φ10孔以外,对其余的三孔的孔内表面要求较高;要采取必要的措施以保证其表面精度;但这些加工精度可以在正常的生产条件下采用经济的方法保质保量的加工出来;端面和孔的加工可以通过通用的铣床和钻床保证加工精度,而不需要使用高精度的机床,通过钻削、铣削的加工就可以达到要求;杠杆加工的主要问题确定毛坯的制造形式零件的材料灰铸铁HT200,考虑到杠杆零件在工作中的载荷平稳并且处于润滑状态,因此选择润滑效果较好的铸铁,以使金属纤维尽量不被裁断,保证零件工作可靠;由于年产量为4000件,达到大批生产的水平,而且零件的轮廓尺寸不大,铸造表面质量的要求高,故可采用铸造质量稳定的,适合大批生产的金属模铸造;便于铸造和加工工艺过程,而且还可以提高生产率;基面的选择1粗基准的选择;对于本零件而言,按照粗基准的选择原则,选择本零件的加工表面就是宽度为Ф40mm的肩面表面作为加工的粗基准,可用压板对肩台进行加紧,利用一组V形块支承Φ40mm的外轮廓作主要定位,以消除z、z、y、y四个自由度;再以一面定位消除x、x两个自由度,达到完全定位,就可加工Φ25H7的孔;2精基准的选择;主要考虑到基准重合的问题,和便于装夹,采用Φ25H7的孔作为精基准;确定工艺路线1、工艺路线方案一:铸造时效涂底漆工序1:粗精铣宽度为Ф40mm的上下平台和宽度为30mm的平台工序2:粗精铣宽度为Φ30mm的凸台表面工序3:钻孔Ф25H9使尺寸达到Ф23mm;工序4:扩孔钻钻孔Ф25H9使尺寸达到Ф;工序5:铰孔Ф25H9使尺寸达到Ф25H9;工序6 :钻Φ10H7的内孔使尺寸达到;工序7:粗铰Φ10H7内孔使尺寸达到;工序8:精铰Φ10H7内孔使尺寸达到Φ10H7mm;工序9:钻、粗、精铰2×Φ8H7小孔使尺寸达到Φ8H7;工序10:检验入库;2、工艺路线方案二:铸造时效涂底漆工序1:粗精铣宽度为Ф40mm的上下平台和宽度为30mm的平台; 工序2:粗精铣宽度为Φ30mm的凸台表面工序3:钻孔Ф25H9使尺寸达到Ф23mm;工序4:钻2×Ф8H7的小孔使尺寸;工序5:扩孔钻钻孔Ф25H9使尺寸达到Ф;工序6:铰孔Ф25H9使尺寸达到Ф25H9;工序7 :钻Φ10H7的内孔使尺寸达到;工序8:粗铰Φ10H7内孔使尺寸达到;工序9:精铰Φ10H7内孔使尺寸达到Φ10H7mm;工序10:粗铰2×Φ8H7小孔使尺寸达到;工序11:精铰2×Φ8H7小孔使尺寸达到Φ8H7;工序12:检验入库;上述两种工艺方案的特点是:方案一是根据宽度为40mm的上下肩面作为粗基准,Ф25H7孔作为精基准,所以就要加工Ф25孔时期尺寸达到要求的尺寸,那样就保证了2×Ф8小孔的圆跳动误差精度等;而方案二则先粗加工孔Ф25,而不进一步加工就钻Ф8H7,那样就很难保证2×Ф8的圆度跳动误差精度;所以决定选择方案一作为加工工艺路线比较合理;结合方案一的工艺路线,根据工序集中的加工原则,最终制定下面工艺路线:工序一:毛坯准备工步1:铸造毛坯工步2:表面时效热处理工步3:涂底漆工序二:粗精铣宽度为Ф40mm的上下平台和宽度为30mm的平台;工步1:粗精铣宽度为Ф40mm的上平台和宽度为30mm的平台;工步2:粗精铣宽度为Ф40mm的下平台工序三:粗精铣宽度为Φ30mm的凸台表面工序四:钻、扩、粗铰、精铰Ф25H9孔工步1:钻Ф25H9孔工步2:扩Ф25H9孔工步3:粗铰Ф25H9孔工步4:精铰Ф25H9孔工序五:钻、粗铰、精铰2×Ф8H7孔工步1:钻2×Ф8H7孔工步2:粗铰2×Ф8H7孔工步3:精铰2×Ф8H7孔工序六:钻、粗铰、精铰Φ10H7孔工步1:钻Φ10H7孔工步2:粗铰Φ10H7孔工步3:精铰Φ10H7孔工序七:表面去毛刺工序八:检验入库本零件的加工表面有:粗精铣宽度为Φ40mm的上下平台、钻Φ10H7孔、钻2×Ф8+的小孔、粗精铣Φ30凸台的平台;材料为HT200,加工方法选择如下:1、Φ40mm圆柱的上平台:公差等级为IT8~IT10,表面粗糙度为,采用粗铣→精铣的加工方法,并倒R3圆角;2、Φ40mm圆柱的下平台:公差等级为IT8~IT10,表面粗糙度为,采用采用粗铣→精铣的加工方法,并倒R3圆角;3、30mm的凸台上下表面:公差等级为IT13,表面粗糙度为,采用粗铣→精铣的加工方法;4、钻Φ10H7内孔:公差等级为IT7~IT8,表面粗糙度为,平行度为μmA,采用钻孔→粗铰→精铰的加工方法;5、钻Φ25H9内孔:公差等级为IT6~IT8,表面粗糙度为,采用钻孔→扩孔钻钻孔→精铰的加工方法,并倒1×45°内角;6、钻Φ8H7内孔:公差等级为IT6~IT8,表面粗糙度为,采用钻孔→粗铰→精铰的加工方法;由于生产类型为大批生产,故加工设备宜以采用通用机床为主,辅以少量专用机床;其生产方式为以通用机床加专用夹具为主,辅以少量专用机床的流水生产线;工件在各级床上的装卸及各机床间的传送均由人工完后;粗精铣宽度为Ф40mm的上下平台和宽度为30mm的平台;考虑到工件的定位夹紧方案及夹具结构设计等问题,采用立铣,选择X5012立式铣床参考文献:机械制造工艺设计简明手册,主编:李益民,机械工业出版社,刀具选D=2mm的削平型立铣刀参考文献:机械制造工艺设计简明手册,主编:李益民,机械工业出版社、专用夹具、专用量具和游标卡尺;粗精铣宽度为Φ30mm的凸台表面;采用X5021立式铣床,刀具选D=2mm的削平型铣刀,专用夹具、专用量检具和游标卡尺;钻孔Ф25H9使尺寸达到Ф23mm;采用Z535型钻床,刀具选莫氏锥柄麻花钻莫氏锥柄2号刀D=23mm,专用钻夹具,专用检具;扩孔钻钻孔Ф25H9使尺寸达到Ф;采用立式Z535型钻床,刀具选D=的锥柄扩孔钻莫氏锥度3号刀,专用钻夹具和专用检具;铰孔Ф25H9使尺寸达到Ф25H9;采用立式Z535型钻床,刀具选D=25mm的锥柄机用铰刀,并倒1×45°的倒角钻用铰夹具和专用检量具;钻2×Ф8H7的小孔使尺寸达到;采用立式Z518型钻床,刀具选用D=的直柄麻花钻,专用钻夹具和专用检量具;钻Φ10H7的内孔使尺寸达到Φ;采用立式Z518型钻床,刀具选用D=的直柄麻花钻,专用的钻夹具和量检具;粗铰Φ10H7内孔使尺寸达到Φ;采用立式Z518型钻床,刀具选用D=10mm的直柄机用铰刀,专用夹具和专用量检具;精铰Φ10H7内孔使尺寸达到Φ10H7mm;采用立式Z518型钻床,选择刀具D=10mm的精铰刀,使用专用夹具和量检具;粗铰2×Φ8H7小孔使尺寸达到Φ;采用立式Z518型钻床,选择刀具为D=8mm直柄机用铰刀,使用专用夹具和专用量检具;精铰2×Φ8H7小孔使尺寸达到Φ8H7;采用立式Z518型钻床,选择刀具为D=8mm的直柄机用铰刀,使用专用的夹具和专用的量检具参考文献:机械制造工艺设计简明手册,主编:李益民,机械工业出版社; 工序一:毛坯准备工步1:铸造毛坯工步2:表面时效热处理由于毛坯铸造内应力较大,为了消除内应力,减小变形,保证精度的稳定性,铸造后要安排人工时效处理;工步3:涂底漆工序二:粗精铣宽度为Ф40mm的上下平台和宽度为30mm的平台;工步1:粗精铣宽度为Ф40mm的上平台和宽度为30mm的平台;工件材料:HT200,铸造加工要求:粗铣φ40上下端面和宽度为30的平台面机床:XA6132万能立式升降铣床机械加工工艺师手册表刀具:高速钢圆柱型铣刀机械加工工艺师手册表切削用量1确定切削深度根据高速钢圆柱型铣刀GB1115-85,选择铣刀直径50mm,粗铣齿数Z=6,精铣齿数Z=8;查金属机械加工工艺人员手册有,粗铣平面选择ap=3~8mm,精铣平面选择ap=~1mm,因为切削量较小,粗铣平面选择ap=3mm,精铣平面选择ap=1mm;2确定进给量查金属切削手册选取圆柱铣刀铣削铸造件的进给量粗铣fz=z,精铣fz=z;3 确定切削速度由于粗铣铸造件时,切削负荷和载荷较大,查金属切削手册得,粗铣 Vc=15m/min,精铣 Vc=26m/min;4确定铣刀直径和工作台的进给量查金属切削手册得D=50mm,由n=1000V/ πd 得,粗铣:ns=1000×15/×50=min,取ns=96r/min,按机床选取nw=95r/min;由V=nπd/1000=×95×50/1000=min当nw=95r/min时,工作台每分钟的进给量:fm=fz×z×nw=×6×95=min精铣:ns=1000×26/×50=min,取ns=166r/min,按机床选取nw=150r/min;由V=nπd/1000=×50×150/1000=min当nw=150r/min时,工作台每分钟的进给量:fm=fz×z×nw=×8×150=72m/min5计算基本工时查金属切削手册得l=83mm,l1=,l2=3mm粗铣:t=l+l1+l2/fm=83++3/=精铣:t=l+l1+l2/fm=83++3/72=工步2:粗精铣宽度为Ф40mm的下平台工件材料:HT200,铸造加工要求:粗精铣宽度为Ф40mm的下平台机床:XA6132万能立式升降铣床机械加工工艺师手册表刀具:高速钢圆柱型铣刀机械加工工艺师手册表切削用量1确定切削深度根据高速钢圆柱型铣刀GB1115-85,选择铣刀直径50mm,粗铣齿数Z=6,精铣齿数Z=8;查金属机械加工工艺人员手册有,粗铣平面选择ap=3~8mm,精铣平面选择ap=~1mm,因为切削量较小,粗铣平面选择ap=3mm,精铣平面选择ap=1mm;2确定进给量查金属切削手册选取圆柱铣刀铣削铸造件的进给量粗铣fz=z,精铣fz=z;3 确定切削速度由于粗铣铸造件时,切削负荷和载荷较大,查金属切削手册得,粗铣 Vc=15m/min,精铣 Vc=30m/min;4确定铣刀直径和工作台的进给量查金属切削手册得D=50mm,由n=1000V/ πd 得,粗铣:ns=1000×15/×50=min,取ns=96r/min,按机床选取nw=95r/min;由V=nπd/1000=×95×50/1000=min当nw=95r/min时,工作台每分钟的进给量:fm=fz×z×nw=×6×95=min精铣:ns=1000×26/×50=min,取ns=166r/min,按机床选取nw=190r/min;由V=nπd/1000=×50×190/1000=min当nw=190r/min时,工作台每分钟的进给量:fm=fz×z×nw=×8×190=min5计算基本工时查金属切削手册得l=30mm,l1=,l2=3mm粗铣:t=l+l1+l2/fm=30++3/=精铣:t=l+l1+l2/fm=30++3/=工序三:粗精铣宽度为Φ30mm的凸台表面工件材料:HT200,铸造加工要求:粗精铣宽度为Ф40mm的下平台机床:XA6132万能立式升降铣床机械加工工艺师手册表刀具:高速钢圆柱型铣刀机械加工工艺师手册表切削用量1确定切削深度根据高速钢圆柱型铣刀GB1115-85,选择铣刀直径50mm,粗铣齿数Z=6,精铣齿数Z=8;查参考文献有,粗铣平面选择ap=3~8mm,精铣平面选择ap=~1mm,因为切削量较小,粗铣平面选择ap=3mm,精铣平面选择ap=1mm;2确定进给量查金属切削手册选取圆柱铣刀铣削铸造件的进给量粗铣fz=z,精铣fz=z;3 确定切削速度由于粗铣铸造件时,切削负荷和载荷较大,查金属切削手册得,粗铣 Vc=15m/min,精铣 Vc=26m/min;4确定铣刀直径和工作台的进给量查金属切削手册得D=50mm,由n=1000V/ πd 得,粗铣:ns=1000×15/×50=min,取ns=96r/min,按机床选取nw=95r/min;由V=nπd/1000=×95×50/1000=min当nw=95r/min时,工作台每分钟的进给量:fm=fz×z×nw=×6×95=min精铣:ns=1000×26/×50=min,取ns=166r/min,按机床选取nw=150r/min;由V=nπd/1000=×50×150/1000=min当nw=150r/min时,工作台每分钟的进给量:fm=fz×z×nw=×8×150=72m/min5计算基本工时查金属切削手册得l=30mm,l1=,l2=3mm粗铣:t=l+l1+l2/fm=30++3/=则粗铣2Φ30凸台表面:2t=×2=精铣:t=l+l1+l2/fm=30++3/72=则精铣2Φ30凸台表面:2t=×2=工序四:钻、扩、粗铰、精铰Ф25H9孔1、加工余量的确定由参考文献得钻孔余量为,扩孔的余量为,粗铰的余量为,精的余量为;2、切削用量的计算1 钻孔工步由于该材料为HT200,进给量的确定由机械制造技术基础课程设计课程设计指南选取该工步的每转进给量为f= mm/r,背吃刀量的确定 ap= mm;切削速度的计算:由机械制造技术基础课程设计课程设计指南初选切削速度为V=20 m/min由公式:n=1000V/πd得该工序的钻头转速n= r/min,参照机械制造技术基础课程设计课程设计指南所列Z550型立式钻床的主轴转速,取转速n=250 r/min,得该工序的实际钻削速度:V=ndπ/1000=250××23/1000=18m/min2扩孔工步由于该材料为HT200,进给量的确定由机械制造技术基础课程设计课程设计指南选取该工步的每转进给量为f=r,背吃刀量的确定ap= mm;切削速度的计算:由机械制造技术基础课程设计课程设计指南初选切削速度为V=4m/min由公式:n=1000V/πd得该工序的钻头转速n=min,参照机械制造技术基础课程设计课程设计指南所列Z550型立式钻床的主轴转速,取转速n=47 r/min,得该工序的实际钻削速度: V=ndπ/1000=47××1000=min3 粗铰工步由于该材料为HT200,进给量的确定由机械制造技术基础课程设计课程设计指南选取该工步的每转进给量为f=r,背吃刀量的确定 ap=;切削速度的计算:由机械制造技术基础课程设计课程设计指南初选切削速度为V=3m/min由公式:n=1000V/πd得该工序的钻头转速n=min,参照机械制造技术基础课程设计课程设计指南所列Z550型立式钻床的主轴转速,取转速n=47r/min,得该工序的实际钻削速度:V=ndπ/1000=47××1000=min4 精铰工步由于该材料为HT200,进给量的确定由机械制造技术基础课程设计课程设计指南选取该工步的每转进给量为f=r,背吃刀量的确定 ap=;切削速度的计算:由机械制造技术基础课程设计课程设计指南初选切削速度为V=5m/min由公式:n=1000V/πd得该工序的钻头转速n=min,参照机械制造技术基础课程设计课程设计指南所列Z550型立式钻床的主轴转速,取转速n=63r/min,得该工序的实际钻削速度:V=ndπ/1000=63××25/1000=min3、基本工时的计算1基本时间的计算1钻孔工步由机械制造技术基础课程设计课程设计指南表2-26得:T=L/fn=l+l1+l2/fn其中1=54 mm,l2=1 mml1=D×cotkr/2+1~2=×cot56/2+1~2=;f= mm/r n=250 r/min将上述结果代入公式,可得到该公序的基本时间:T=54++1/×250=2扩孔工步由机械制造技术基础课程设计课程设计指南表2-26得:T= L/fn=l+l1+l2/fn其中1=54 mm,l3=3 mml1=D-d1 cotkr/2+1~2= f= mm/r n=47r/min将上述结果代入公式,可得到该公序的基本时间:T=54++3/×47=3粗铰工步由机械制造技术基础课程设计课程设计指南表2-26得:T= L/fn=l+l1+l2/fn其中l1=;l2=15mm由机械制造技术基础课程设计课程设计指南表2-27得:kr=150、ap=D-d/2=查得l=54mm;f= mm/r;n=47r/min;将上述结果代入公式,可得到该公序的基本时间:T=54++15/×47=4精铰工步由机械制造技术基础课程设计课程设计指南表2-26得:T= L/fn=l+l1+l2/fn其中l1=;l2=13mm由机械制造技术基础课程设计课程设计指南表2-27得:kr=150、ap=D-d/2=/2=查得l=54mm;f=r;n=63r/min将上述结果代入公式,可得到该公序的基本时间:T=54++13/×63=2辅助时间的计算由机械制造技术基础课程设计课程设计指南得,辅助时间Ta与基本时间T的关系为:Ta=~T取Ta=,则本工序的辅助时间为:钻孔工步的辅助时间Ta==×=扩孔工步的辅助时间Ta==×=粗铰工步的辅助时间Ta==×=精铰工步的辅助时间Ta==×=3其他时间的计算除了基本时间和辅助时间外,每道工序的单件时间还包括布置工地时间、休息时间和准备时间和终结时间等的总时间Tb,与基本时间和辅助时间的关系为:Tb=×T+Ta则本工序的辅助时间为:钻孔工步Tb=×T+Ta=×+=扩孔工步Tb=×T+Ta=×+=粗铰工步Tb=×T+Ta=×+=精铰工步Tb=×T+Ta=×+=(4)单件总时间的计算钻孔工步总时间Tz=T+Ta+Tb=++=扩孔工步总时间Tz=T+Ta+Tb=++=粗铰工步总时间Tz=T+Ta+Tb=++=精铰工步总时间Tz=T+Ta+Tb=++=即工序四的所用总时间T=+++=工序五:钻、粗铰、精铰2×Ф8H7孔1、加工余量的确定由参考文献得钻孔余量为,粗铰的余量为,精的余量为;2、切削用量的计算1 钻孔工步由于该材料为HT200,进给量的确定由机械制造技术基础课程设计课程设计指南选取该工步的每转进给量为f=r,背吃刀量的确定ap= mm;切削速度的计算:由机械制造技术基础课程设计课程设计指南初选切削速度为V=22m/min由公式:n=1000V/πd得该工序的钻头转速n=1000 r/min,参照机械制造技术基础课程设计课程设计指南所列Z550型立式钻床的主轴转速,取转速n=1000 r/min,得该工序的实际钻削速度: V=ndπ/1000=10××1000=22m/min2 粗铰工步由于该材料为HT200,进给量的确定由机械制造技术基础课程设计课程设计指南选取该工步的每转进给量为f=r,背吃刀量的确定 ap=;切削速度的计算:由机械制造技术基础课程设计课程设计指南初选切削速度为V=11m/min由公式:n=1000V/πd得该工序的钻头转速n=438/min,参照机械制造技术基础课程设计课程设计指南所列Z550型立式钻床的主轴转速,取转速n=450r/min,得该工序的实际钻削速度: V=ndπ/1000=450××1000=min3 精铰工步由于该材料为HT200,进给量的确定由机械制造技术基础课程设计课程设计指南选取该工步的每转进给量为f=r,背吃刀量的确定 ap=;切削速度的计算:由机械制造技术基础课程设计课程设计指南初选切削速度为V=18m/min由公式:n=1000V/πd得该工序的钻头转速n=717/min,参照机械制造技术基础课程设计课程设计指南所列Z550型立式钻床的主轴转速,取转速n=720r/min,得该工序的实际钻削速度: V=ndπ/1000=720××8/1000=min3、基本工时的计算1基本时间的计算1钻孔工步由机械制造技术基础课程设计课程设计指南表2-26得:T= L/fn=l+l1+l2/fn其中1=15 mm,l2=2mml1=D×cotkr/2+1~2=×cot56/2+1~2=8mm;f=r n=1000 r/min将上述结果代入公式,可得到该公序的基本时间:T=15+8+1/×1000=则2T=2粗铰工步由机械制造技术基础课程设计课程设计指南表2-26得:T= L/fn=l+l1+l2/fn其中l1=;l2=15mm由机械制造技术基础课程设计课程设计指南表2-27得:kr=150、ap=D-d/2=查得l=54mm;f=r;n=450r/min将上述结果代入公式,可得到该公序的基本时间:T=15++15/×450=则2T=1min3精铰工步由机械制造技术基础课程设计课程设计指南表2-26得:T= L/fn=l+l1+l2/fn其中l1=;l2=13mm由机械制造技术基础课程设计课程设计指南表2-27得:kr=150、ap=D-d/2=/2=查得l=15mm;f=r;n=720r/min将上述结果代入公式,可得到该公序的基本时间:T=515++13/×720=则2T=2辅助时间的计算由机械制造技术基础课程设计课程设计指南得,辅助时间Ta与基本时间T的关系为:Ta=~T取Ta=,则本工序的辅助时间为:钻孔工步的辅助时间Ta==×=粗铰工步的辅助时间Ta==×1=精铰工步的辅助时间Ta==×=3其他时间的计算除了基本时间和辅助时间外,每道工序的单件时间还包括布置工地时间、休息时间和准备时间和终结时间等的总时间Tb,与基本时间和辅助时间的关系为:Tb=×T+Ta则本工序的辅助时间为:钻孔工步Tb=×T+Ta=×+=粗铰工步Tb=×T+Ta=×1+=精铰工步Tb=×T+Ta=×+=(5)单件总时间的计算钻孔工步总时间Tz=T+Ta+Tb=++=粗铰工步总时间Tz=T+Ta+Tb=1++=精铰工步总时间Tz=T+Ta+Tb=++=即工序四的所用总时间T=++=工序六:钻、粗铰、精铰Φ10H7孔1、加工余量的确定由参考文献得钻孔余量为,粗铰的余量为,精的余量为;2、切削用量的计算1 钻孔工步由于该材料为HT200,进给量的确定由机械制造技术基础课程设计课程设计指南选取该工步的每转进给量为f=r,背吃刀量的确定ap=;切削速度的计算:由机械制造技术基础课程设计课程设计指南初选切削速度为V=22m/min由公式:n=1000V/πd得该工序的钻头转速n=1000 r/min,参照机械制造技术基础课程设计课程设计指南所列Z550型立式钻床的主轴转速,取转速n=1000 r/min,得该工序的实际钻削速度: V=ndπ/1000=10××1000=30m/min2 粗铰工步由于该材料为HT200,进给量的确定由机械制造技术基础课程设计课程设计指南选取该工步的每转进给量为f=r,背吃刀量的确定 ap=;切削速度的计算:由机械制造技术基础课程设计课程设计指南初选切削速度为V=11m/min由公式:n=1000V/πd得该工序的钻头转速n=438/min,参照机械制造技术基础课程设计课程设计指南所列Z550型立式钻床的主轴转速,取转速n=450r/min,得该工序的实际钻削速度: V=ndπ/1000=450××1000=min3 精铰工步由于该材料为HT200,进给量的确定由机械制造技术基础课程设计课程设计指南选取该工步的每转进给量为f=r,背吃刀量的确定 ap=;切削速度的计算:由机械制造技术基础课程设计课程设计指南初选切削速度为V=18m/min由公式:n=1000V/πd得该工序的钻头转速n=717/min,参照机械制造技术基础课程设计课程设计指南所列Z550型立式钻床的主轴转速,取转速n=720r/min,得该工序的实际钻削速度: V=ndπ/1000=720××10/1000=min3、基本工时的计算1基本时间的计算1钻孔工步由机械制造技术基础课程设计课程设计指南表2-26得:T= L/fn=l+l1+l2/fn其中1=54 mm,l2=1mml1=D×cotkr/2+1~2=×cot56/2+1~2=;f=r n=250r/min将上述结果代入公式,可得到该公序的基本时间:T=54++1/×250=2粗铰工步由机械制造技术基础课程设计课程设计指南表2-26得:T= L/fn=l+l1+l2/fn其中l1=;l2=15mm由机械制造技术基础课程设计课程设计指南表2-27得:kr=150、ap=D-d/2=/2=查得l=54mm;f=r;n=47r/min将上述结果代入公式,可得到该公序的基本时间:T=54++15/×47=3精铰工步由机械制造技术基础课程设计课程设计指南表2-26得:T= L/fn=l+l1+l2/fn其中l1=;l2=13mm由机械制造技术基础课程设计课程设计指南表2-27得:kr=150、ap=D-d/2=查得l=54mm;f=r;n=63r/min将上述结果代入公式,可得到该公序的基本时间:T=54++15/×63=2辅助时间的计算由机械制造技术基础课程设计课程设计指南得,辅助时间Ta与基本时间T的关系为:Ta=~T取Ta=,则本工序的辅助时间为:钻孔工步的辅助时间Ta==×=粗铰工步的辅助时间Ta==×=精铰工步的辅助时间Ta==×=3其他时间的计算除了基本时间和辅助时间外,每道工序的单件时间还包括布置工地时间、休息时间和准备时间和终结时间等的总时间Tb,与基本时间和辅助时间的关系为:Tb=×T+Ta则本工序的辅助时间为:钻孔工步Tb=×T+Ta=×+=粗铰工步Tb=×T+Ta=×+=精铰工步Tb=×T+Ta=×+=(6)单件总时间的计算钻孔工步总时间Tz=T+Ta+Tb=++=粗铰工步总时间Tz=T+Ta+Tb=++=精铰工步总时间Tz=T+Ta+Tb=++=即工序四的所用总时间T=++=工序七:表面去毛刺工序八:检验入库根据该零件的生产纲量为每年产4000件;按一年360天,每天总工作时间为8小时;则每个零件所需的额定时间为:t=360×8×60÷4000=;根据计算所得的机动时间加上每道工序间的辅助时间;所用是实际时间为所以该方案满足生产要求;3 夹具的设计本次的夹具为—工序9:钻、粗、精铰2×Φ8H7小孔使尺寸达到Φ8H7而设计的;本工序所加工的孔是位于Φ30凸台平面内,孔径不大,工件重量较轻、轮廓尺寸不是很大等原因,采用翻转式钻模;确定设计方案这道工序所加工的孔在Φ30凸台平面上,且与土台面垂直,平行度△A=;根据工件结构特点,其定位方案有:工件以Φ25+孔及端面和水平面底、Φ30的凸台分别在台阶定位销、支承钉上实现完全定位;钻Φ8H7mm孔时工件为悬臂,为防止工件加工时变形,采用了螺旋辅助支承,当辅助支承与工件接触后,用螺母锁紧;选择定位元件1选择带台阶面的定位销,作为以φ 25H9孔及其端面的定位元件,定位副配合取基孔值配合;2选择可调支承钉为φ8H7孔外缘毛坯一侧防转定位面的定位元件 ,用锁紧螺母将其锁紧,防止在加工孔时出现扭转,限制工件六个自由度;为增加刚性,在φ8H7的端面增设一螺旋辅助支承,辅助支承与工件接触后,用螺母将其锁紧;计算夹紧力并确定螺杆直径由机床夹具设计手册,实际所需夹紧力K W 与切削力W 之间的关系为: K W WK =,式中的K 为安全系数,0123456 2.8K K K K K K K K == ,M10的六角螺母夹紧力W=3550N;所以,K W WK ==3550×=9940N,选择一个M30的螺旋辅助支承;一是为了承受切削力的冲击,二是为了防止工件在加工时变形,因为钻φ8H7孔时,工件为悬臂定位误差计算1加工φ8H7时孔距尺寸 84± 的定位误差计算,由于基准重合,故 :+=,,上下公差为:=,符合尺寸要求;而基准位移误差为定位孔 φ25H9 与定位销的最大间隙,故:定位销取直径为φ25H9,尽量减少位移误差;故:25-25=0,最大间隙:=,最小间隙:0-0=0 mm;其基准也符合设计要求;由此可知此定位方案能满足尺寸 84± 的定位要求;2加工φ8H7孔时轴线平行度 的定位误差计算,由于基准重合,故 :+=而基准位移误差是定位孔φ25H9与定位面间的垂直度误差;。
机械加工工艺过程

一、工艺路线方案一工序一:粗镗、精镗孔Ø80H9(087.00 +)mm 孔的内圆 工序二:粗铣、精铣Ø80H9(087.00 +)mm 的大端端面 工序三:镗Ø80H9(087.00+)mm 大端处的2×45°倒角。
工序四:钻4-Ø13mm 的通孔,锪Ø20mm 的沉头螺栓孔。
工序五:钻2-Ø10mm 的锥销底孔,粗铰、精铰2-Ø10mm 的锥销孔。
工序六:铣削尺寸为5mm 的纵槽。
工序七:钻削通孔Ø20mm ,扩、铰孔Ø25H7(25.00+)mm,锪沉头螺栓孔Ø38mm 和Ø43mm 。
工序九:钻削M10-H7和M8-H7的螺纹底孔。
工序十:铣削尺寸为5mm 的横槽。
工序十一:攻螺纹M10-H7和M8-H7。
工序十二:终检。
二、工艺路线方案二工序一:粗铣、精铣削Ø80H9(087.00+)mm 孔的大端端面。
工序二:粗镗、精镗Ø80H9(087.00+)mm 内孔,以及倒2×45°的倒角。
工序三:钻削底板上的4-Ø13mm 的通孔,锪4-Ø20mm 的沉头螺栓孔。
工序四:钻削锥销孔2-Ø10mm 底孔,铰削锥销孔Ø10mm 。
工序五:钻削Ø21mm 的通孔,扩、铰孔Ø25H7(25.00+)mm ,锪沉头螺栓孔Ø38mm和Ø43mm 。
工序六:铣削尺寸为5mm 的纵槽。
工序七:钻削M10-H7和M8-H7的螺纹底孔。
工序八:铣削尺寸为5mm 的横槽。
工序九:攻螺纹M10-H7和M8-H7。
工序十:终检。
三、工艺方案分析工艺方案路线一:本路线是先加工孔后加工平面,再以加工后的平面来加工孔。
这样减少了工件因为多次装夹而带来的误差。
mes 工艺路线 实现方案

mes 工艺路线实现方案一、MES工艺路线的基本概念MES工艺路线是制造执行系统(MES)中的重要概念,它是指将产品的生产工艺、工序、设备、物料等信息以及其之间的关系进行建模和规划,以实现生产计划的准确执行。
二、MES工艺路线的作用1. 优化生产计划:MES工艺路线可以根据产品特性和生产设备的性能,合理安排生产工序和工艺参数,从而优化生产计划,提高生产效率。
2. 提高生产质量:MES工艺路线可以明确每个工序的质量要求和检验标准,确保产品质量的稳定性和一致性。
3. 实现生产过程可视化:MES工艺路线可以将生产过程中的各个环节、状态和数据进行实时监控和记录,实现生产过程的可视化管理。
4. 支持产品溯源:MES工艺路线可以将每个产品的生产过程和相关数据进行记录和追溯,支持产品质量追溯和合规要求。
5. 提升生产决策能力:MES工艺路线可以为企业提供实时的生产数据和报表分析,帮助企业管理层做出准确的决策。
三、MES工艺路线的实施步骤1. 数据收集与整理:收集并整理产品的生产工艺、工序、设备、物料等信息,建立起完整的工艺路线数据库。
2. 工艺规划与优化:根据产品特性和生产设备的性能,对工艺路线进行规划和优化,确保生产计划的合理性和可行性。
3. 系统集成与开发:根据企业实际需求,选择合适的MES系统,并进行系统集成和开发,实现工艺路线的可视化管理和数据追溯。
4. 培训与推广:对相关人员进行培训,使其掌握工艺路线的使用方法和技巧,并在企业内部推广应用,确保工艺路线的有效实施。
四、MES工艺路线的优势1. 提高企业生产效率和产品质量,降低生产成本。
2. 支持生产过程的实时监控和数据分析,帮助企业进行持续改进。
3. 实现生产过程的可视化管理,提高生产决策的准确性和及时性。
4. 支持产品质量追溯和合规要求,提升企业的竞争力和市场信誉度。
MES工艺路线实现方案是制造企业提高生产效率、产品质量和管理水平的重要工具。
通过建立完整的工艺路线数据库,优化生产计划,实现生产过程的可视化管理和数据追溯,企业可以有效地提升竞争力,实现可持续发展。
工艺路线

1.工艺路线方案一工序1 划线在毛坯一端划中心线。
工序2 钳工按线钻φ5×60○的中心孔。
工序3 粗车1 以中心孔定位,一顶一夹,粗车外圆φ105至φ107,调头加工注意外圆的接平。
工序4 粗车2 夹外圆,中心夹托一端,粗车两端面尺寸为476±0.2至490;钻通孔φ74为φ30,扩孔φ74至φ74,粗车φ84至φ84,粗车φ90到φ88,粗车φ85至φ83,并在靠φ85孔的端面打上标号。
工序5 热处理1 调质处理,硬度达HBS257,保证圆柱度为1.5。
工序6 半精车1 夹外圆,中心架托一端,在打标号一端车割6mm的试片,工件相应端再打同样标号,试片金相组织检验合格后转入下道工序。
工序7 半精车2 车外圆φ105至φ106,调头加工要保持接刃平整,车1:10锥面工序8 半精车3 夹外圆中心中架托一端,车两端尺寸为476±0.2至476.3±0.2,车孔φ90至φ89.6,φ76至φ75.6,φ85至φ84.6,切6×φ96,6×φ94槽,车倒角60○。
工序9 粗磨1 两端60○倒角定位,粗磨外圆φ105至φ105.6,R a1.25。
工序10 探伤磁粉探伤。
工序11 铣粗精铣齿条,中径留磨量0.5,Ra5。
工序12 热处理2 高温时效,保证圆柱≤0.08(不准使用工具校正)。
工序13 粗磨2 Ra0.63。
工序14 粗磨3 粗磨φ90至φ89.9,φ76至φ75.6,φ85至φ84.9,槽内肩面磨出即可,磨60○倒角内锥面,Ra为1.25。
工序15 磨齿粗磨齿条,中径留磨量0.2,Ra1.25。
工序16 钳工用占磨定位,两端面上钻孔,攻6×M4-6H深10的螺纹,铰2×φ3深6的孔,锉刀修齿顶棱角倒圆为R0.5,其余棱角倒角0.3×45○。
工序17 精磨1 以两端60○倒角面定位,精磨外圆φ105至φ105.1,Ra0.32。
CA6140车床拨叉(831008型号)零件的机械加工工艺及夹具设计【钻M6孔】

工序一 以φ32外圆为粗基准,粗铣φ20孔上下端面。
1. 加工条件
工件材料:HT200,σb=0.16GPa HB=190~241,铸造。
加工要求:粗铣φ20孔上下端面。
机床:X6140卧式铣床。
据以上原始资料及加工路线,分别确定各家工表面的机械加工余量、工序尺寸及毛坯尺寸如下:
1. 外圆表面延轴线方向长度方向的加工余量及公差(φ20,φ50端面)。
查《机械制造工艺设计简明手册》(以下称《工艺手册》)表2.2~2.5,取φ20,φ50端面长度余量均为2.5(均为双边加工)
铣削加工余量为:
粗铣1mm
工序十一 检查。
上面工序可以适合大多数生产,但效率较低。
综合考虑以上步骤,得到我的工艺路线。
3.工艺路线方案三
工序一 以φ32外圆为粗基准,粗铣φ20孔下端面。
工序二 精铣φ20孔上下端面。
工序三 以φ20孔上端面为精基准,钻、扩、铰、精铰φ20孔,保证垂直度误差不超过0.05mm,孔的精度达到IT7。
(二)零件的工艺分析
CA6140车床共有两处加工表面,其间有一定位置要求。分述如下:
1.以φ20为中心的加工表面
这一组加工表面包括:φ20 的孔,以及其上下端面,上端面与孔有位置要求,孔壁上有一个装配时钻铰的锥孔,一个M8的螺纹孔。下端有一个47°的斜凸台。这三个都没有高的位置度要求。
2.以φ50为中心的加工表面
工序四 以φ20孔为精基准,钻、扩、铰、精铰φ50孔,保证空的精度达到IT7。
工序五 切断。
工序六 以φ20孔为精基准,粗铣φ50孔上下端面。
工序七 以φ20孔为精基准,精铣φ50孔上下端面,保证端面相对孔的垂直度误差不超过0.07。
机械制造技术基础(课程设计)减速器传动轴设计1.

机械制造技术基础课程设计设计题目: 减速器传动轴学校: 陕西科技大学学院: 机电学院专业类别: 机械设计制造及其自动化班级: 机械046**: ***学号: ************: **起始日期: 2007年1月9 日完成日期: 2007年1月25 日成绩:传动轴零件的加工工艺规程 1机械制造课程设计题目:设计“减速器传动轴”零件的机械加工工艺规程(年产量为5000件)内容:(1)零件图 1张(A3)(2)毛坯图 1张(A3)(3)工序简图 1张(A2)(4)工序卡片 2张(5)课程设计说明书 1份班级:机械046学生:杨孟博指导教师:张斌学号: 514046272007年 1月25日陕西科技大学课程设计说明书 2目录1 设计说明 (4)1.1题目所给的零件是传动轴 (4)1.2 零件的工艺分析 (4)1.3 其主要加工表面位置要求 (4)1.4零件的材料 (4)2 工艺规程的设计 (5)2.1 零件表面加工方法的选择 (5)2.2制定工艺路线 (6)3 机械加工余量﹑工序尺寸及毛坯尺寸的确定 (6)3.1 确定加工余量 (6)3.2 确定毛坯尺寸 (7)4 确定切削用量及基本工时 (8)4.1 车两端面 (9)4.2 计算切削用量 (9)5: 选择量具 (15)5.1 选择刀具 (15)5.2 选择量具 (15)6:总结 (16)7:参考文献 (17)传动轴零件的加工工艺规程 3 机械制造基础课程设计说明书本次设计是在基本学完大学基础课,技术基础课以及大部分专业课后进行的。
是在毕业设计之前做的较全面较深入地对所学各课程进行的综合性复习及应用。
为我提供了一次理论联合实际训练的机会,在我的大学生涯中占有非常重要的地位。
我希望通过本次课程设计对自己的综合性训练,从中锻炼自己的独立思考问题,解决问题的能力,为今后的自己未来生活及工作打下一个良好的基础。
但由于能力有限,此设计难免有不宜之处。
恳请各位老师及同学给予指教。
工艺路线及工艺流程设计(一)
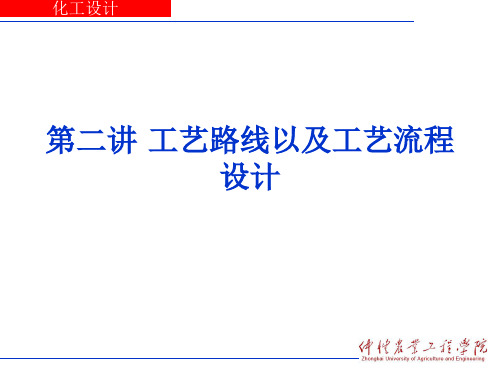
➢ 管道代号应分段编定,管道的分段可按设备到设备之间为一段, 亦可取设备到管道分支点为一段。
➢ 流程图、系统图和管道布置图上相应的管道代号必须一致。 ➢ 管道代号由设备位号及管道的顺序号组成。管径一般标注公称
2. 设备绘制方法
(1)常用设备的外形画法可参照图例绘制,如附录2表
2-1所示。有些设备外形在设计规定中没有图例 的,可绘出其象征性的简单外形,以表明该设备 的特征即可。
(2)在流程图上一律不表示设备的支脚、支架、基础 和平台。
(3)设备的布置,原则上按流程图自左至右,要求图 面饱满匀称,清晰整齐。
项目的设计条件,如对土建、电力、给排水等的要求。 9. 编制设计文件,包括设计说明书、附图(流程图、布
置图、设备图)和附表(设备一览表、材料汇总表等)
化工设计
第二讲 物料衡算与热量衡算(一)
2.1 工艺路线的确定
2.2 工艺流程 主 要 2.3 工艺流程设计方法 内 容 2.4 工艺流程图绘制方法
4. 工艺流程图:在流程草图的基础上表示出物流及
其流向,每一个过程的设备特征,物流组成变化,显 示仪表及自动控制方案、工艺操作参数、管道工程、 经济管径、辅助生产流程等。
化工设计
第二讲 物料衡算与热量衡算(一)
2.3 工艺流程设计方法
化工设计
第二讲 物料衡算与热量衡算(一)
设计中涉及的问题
1. 确定整个流程的组成
具体收集的内容主要有:
(1搜)国集内国外内生产外情同况类,型各种生生产产厂方的法及有工关艺资流料程;,(包2) 原括料来技源术及路产线品应特用点情、况工; 艺(3)参试验数研、究原报材告;料(和4)安公 全((67用种))技生 设术工技产备及技的程术劳术大单路动是型耗 线保否化护、的先及措进制产发施,造品展;生、质情(产运5)量况连输综续情合、与化况利三动、;用废向自及治等动三(8)化废理技基程处本以术度理建及经;;设各济投 资资、产料品。成本、占地面积; (9)水、电、气、燃料的
生产工艺方案

生产工艺方案生产工艺方案是指针对某一产品的生产过程,按照一定的工艺路线和操作规程制定的方案。
以下是一个关于生产工艺方案的示例,总字数为700字。
生产工艺方案一、产品概述本工艺方案针对XX产品的生产过程进行设计,旨在提高生产效率,降低生产成本,确保产品质量。
二、工艺路线1. 原材料检验所有进货原材料必须进行检验,包括外观、尺寸、化学成分等,符合标准后方可入库使用。
2. 原材料粉碎将原材料经过粉碎机进行加工,使其达到所需的粒度要求。
3. 混合搅拌将粉碎后的原材料按照一定比例进行混合,然后放入搅拌机中进行搅拌,使其充分混合均匀。
4. 压制成型将混合后的原材料放入压制机中进行成型,确保产品的外观和尺寸符合要求。
5. 烧结将成型后的产品放入烧结炉中进行烧结,烧结温度和时间根据产品材质和尺寸确定。
6. 修整加工烧结后的产品经过修整加工,去除表面的毛刺和不平整,使其表面光滑平整。
7. 质量检验对修整后的产品进行质量检验,包括外观质量、尺寸精度、物理性能等。
8. 包装合格的产品经过包装处理,标注产品规格、批号、生产日期等信息,方便后续销售和使用。
三、操作规程1. 操作人员必须参加相关的工艺培训,了解各个工序的操作规程和安全注意事项。
2. 操作人员在操作前必须戴好防护用品,包括手套、口罩、安全帽等。
3. 混合搅拌时要控制搅拌时间和搅拌速度,确保混合均匀。
4. 压制成型时要调节压制机的参数,确保产品外观和尺寸符合要求。
5. 烧结时要根据产品材质和尺寸确定烧结温度和时间,严禁超过规定的温度范围。
6. 修整加工时要使用合适的工具,保持修整后的产品表面光滑平整。
7. 质量检验时要按照规定的方法和标准进行,记录检验结果和异常情况。
8. 包装时要注意包装材料的选择和包装方法的合理性,确保产品的安全运输。
四、质量控制1. 进行原材料检验,拒绝不合格的原材料入库使用。
2. 每个工序进行自检,并在工艺流转卡上记录检验结果。
3. 建立产品质量档案,对每批产品进行追溯管理,保留合格样品和试样。
机械制造工艺及机床夹具设计毕业论文

机械制造工艺及机床夹具设计毕业论文前言机械制造工艺及机床夹具设计是大学四年来最后一次实践教学环节,此次毕业设计为了我们对所学的工艺夹具知识进一步深化,指导老师分配了《车床转盘机械制造工艺及夹具设计》的题目,为的是对所学的各课程深入的、综合性的总复习,也是一次理论联系实际的训练。
通过此次工艺夹具毕业设计,能在下述各方面得到锻炼:(1)能熟练运用机械制造工艺学课程中的基本理论,以更正确地解决一个零件在加工中的定位、夹紧以及工艺路线安排、工艺尺寸确定等问题,保证零件的加工质量。
(2)提高结构设计能力,学生通过设计夹具的训练,应当获得根据被加工零件的加工要求,设计出高效、省力、经济合理而能保证加工质量的夹具的能力。
(3)学会使用手册及图表资料。
掌握与本设计有关的各种资料的名称、出处,能够做到熟练运用。
就我个人而言,我希望能通过这次毕业设计对自己从事的工作进行一次适应性训练,从中锻炼自己分析问题、解决问题的能力,为今后工作打下一个良好的基础。
由于能力所限,设计尚有许多不足之处,恳请各位老师给予指教。
第一章零件的分析§1-1 零件的作用题目所给定的零件是普通车床转盘,它位于刀架部件的上刀架与下刀架之间,它是上刀架的导向件,当需要用小刀架车锥面时,可以通过转盘相对于下刀架的转动来调整锥角。
§1-2 零件的工艺分析从零件图上可以看出,它的加工部分可分成四部分:1、底面P及φ70h6mm外圆面N,空刀面、凹台面及倒角;2、燕尾面H及导轨面M,空刀面、凹台面及倒角;3、φ35H7mm孔;4、φ196mm圆弧面和尺寸132mm两侧面K及其端面Q;以上各部分之间的位置要求为:1、φ70h6mm外圆面N与P面有垂直度要求,垂直度公差为φ0.02mm;2、燕尾面M与P面有平行度要求,平行度公差为0.04mm;3、φ35H7mm孔与端面P有垂直度要求,垂直度公差φ0.1mm;4、燕尾槽两55°斜面平行度为0.02mm;由以上分析可知:对于头二组加工面来说,我们可以先选择其中一组表面进行加工,然后再以加工过的表面为基准,加工其他各组表面,并保证它们之间的位置精度。
工艺加工路线

(三)制定工艺路线制定工艺路线的出发点,应当是使零件的加工精度(尺寸精度、形状精度、位置精度)和表面质量等技术要求能得到合理的保证。
在生产纲领已经确定为中批量生产的条件下,可以考虑采用通用机床配以专用夹具并尽量使工序集中来提高生产率。
除此以外,还应当考虑经济效果,以便使生产成本尽量下降。
1、工艺路线方案一:工序Ⅰ粗铣大孔3705.00+φ的两圆端面,以两端面互为粗基准,以及φ52加工圆外轮廓为定位基准。
选用卧式升降台铣床加专用夹具工序Ⅱ钻、扩、精扩3705.00+φ孔,以φ52不加工圆外轮廓为基准,对大孔3705.00+φ进行305.1o⨯的倒角工序Ⅲ铣30045.00+φ二孔内端面,以大孔3705.00+φ左端面及大孔3705.00+φ的中心轴为定位基准。
使用立式升降台加专用夹具的铣床工序Ⅳ铣30045.00+φ二孔外端面,以大孔3705.00+φ左端面及大孔3705.00+φ的中心轴为定位基准。
工序Ⅴ钻、、扩、精扩30045.00+φ二孔,以大孔3705.00+φ及30045.00+φ二孔不加工圆外轮廓为定位基准。
使用立式升降台加专用夹具的机床。
对30045.00+φ外端倒角451o⨯。
工序Ⅵ钻、扩两φ10.5的孔。
工序Ⅶ铣30045.00+φ二孔开缝,以大孔3705.00+φ及30045.00+φ二孔不加工圆外轮廓为定位基准。
工序Ⅷ终检。
2、工艺路线方案二:工序Ⅰ铣30045.00+φ二孔内端面,以两内端面互为粗基准,以及φ52加工圆外轮廓为定位基准。
使用立式升降台加专用夹具的铣床。
工序Ⅱ铣30045.00+φ二孔外端面,以两外端面互为粗基准,以及φ52加工圆外轮廓为定位基准。
使用立式升降台加专用夹具的铣床。
工序Ⅲ钻、扩两φ10.5的孔。
工序Ⅳ钻、精扩30045.00+φ二孔,以大孔3705.00+φ及30045.00+φ二孔不加工圆外轮廓为定位基准。
使用立式升降台加专用夹具的机床。
工序Ⅴ对30045.00+φ外端倒角451o⨯工序Ⅵ锯30045.00+φ二孔开缝,以大孔3705.00+φ及30045.00+φ二孔不加工圆外轮廓为定位基准工序Ⅶ粗铣大孔3705.00+φ的两圆端面,以两端面互为粗基准,以及φ52加工圆外轮廓为定位基准。
机械制造工艺学课程设计---调速杠杆
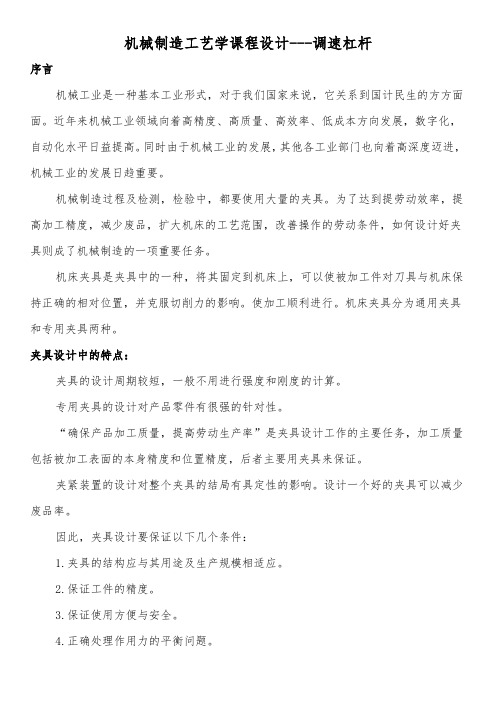
机械制造工艺学课程设计---调速杠杆序言机械工业是一种基本工业形式,对于我们国家来说,它关系到国计民生的方方面面。
近年来机械工业领域向着高精度、高质量、高效率、低成本方向发展,数字化,自动化水平日益提高。
同时由于机械工业的发展,其他各工业部门也向着高深度迈进,机械工业的发展日趋重要。
机械制造过程及检测,检验中,都要使用大量的夹具。
为了达到提劳动效率,提高加工精度,减少废品,扩大机床的工艺范围,改善操作的劳动条件,如何设计好夹具则成了机械制造的一项重要任务。
机床夹具是夹具中的一种,将其固定到机床上,可以使被加工件对刀具与机床保持正确的相对位置,并克服切削力的影响。
使加工顺利进行。
机床夹具分为通用夹具和专用夹具两种。
夹具设计中的特点:夹具的设计周期较短,一般不用进行强度和刚度的计算。
专用夹具的设计对产品零件有很强的针对性。
“确保产品加工质量,提高劳动生产率”是夹具设计工作的主要任务,加工质量包括被加工表面的本身精度和位置精度,后者主要用夹具来保证。
夹紧装置的设计对整个夹具的结局有具定性的影响。
设计一个好的夹具可以减少废品率。
因此,夹具设计要保证以下几个条件:1.夹具的结构应与其用途及生产规模相适应。
2.保证工件的精度。
3.保证使用方便与安全。
4.正确处理作用力的平衡问题。
5.注意结构的工艺性,便于制造和维修。
注意夹具与机床、辅助工具、刀具、量具之间的联系。
在机械制造中,为了适应新产品的不断发展要求。
因此,具设计过程中有朝着下列方向发展的趋势:1.发展通用夹具的新品种由于机械产品的加工精度日益提高,因此需要发展高精度通用夹具。
广泛的采用高效率夹具,可以压缩辅助时间,提高生产效率。
2.发展调整式夹具3.推广和发展组合夹具及拼拆夹具。
4.加强专用夹具的标准化和规范化。
5.大力推广和使用机械化及自动化夹具。
6.采用新结构、新工艺、新材料来设计和制造夹具。
本设计属于工艺夹具设计范围,机械加工工艺设计在零件的加工制造过程中有着重要的作用。
工艺路线调整实施方案

工艺路线调整实施方案一、背景分析。
随着市场需求的不断变化和技术的不断进步,公司的工艺路线也需要不断调整和优化,以满足客户的需求并提高生产效率。
因此,制定工艺路线调整实施方案显得尤为重要。
二、目标设定。
1. 提高生产效率,通过调整工艺路线,降低生产成本,提高生产效率。
2. 优化产品质量,通过调整工艺路线,提高产品质量,满足客户需求。
3. 减少资源浪费,通过合理调整工艺路线,减少资源浪费,提高资源利用率。
三、调查研究。
1. 调查市场需求,了解客户对产品的需求情况,为工艺路线调整提供依据。
2. 调查现有工艺路线,分析现有工艺路线存在的问题和不足,为调整提供参考。
3. 调查竞争对手,了解竞争对手的工艺路线和产品质量,为调整提供参考。
四、工艺路线调整方案。
1. 优化生产流程,根据市场需求和现有工艺路线的不足,优化生产流程,减少生产环节,提高生产效率。
2. 更新生产设备,根据调查研究结果,更新生产设备,提高生产效率和产品质量。
3. 优化原材料选用,根据市场需求和产品特性,优化原材料选用,提高产品质量,降低生产成本。
4. 设立质量检验环节,在生产流程中增加质量检验环节,提高产品质量,减少次品率。
五、实施计划。
1. 制定详细的实施计划,包括工艺路线调整的具体步骤、时间节点和责任人。
2. 提前做好准备工作,包括更新生产设备、培训操作人员等。
3. 逐步实施,分阶段实施工艺路线调整方案,确保生产不受影响。
4. 监控和评估,实施过程中,及时监控效果,对调整方案进行评估和调整。
六、风险控制。
1. 制定应急预案,针对可能出现的问题,制定相应的应急预案,保证生产不受影响。
2. 加强沟通协调,加强各部门之间的沟通协调,及时解决问题,确保工艺路线调整顺利进行。
七、总结。
工艺路线调整是一个复杂的过程,需要全公司的共同努力和配合。
只有不断优化工艺路线,提高生产效率和产品质量,才能在激烈的市场竞争中立于不败之地。
希望全体员工能积极配合,共同推动工艺路线调整实施方案的顺利进行,为公司的发展贡献力量。
工艺实施方案的格式

工艺实施方案的格式工艺实施方案。
一、概述。
工艺实施方案是指在生产过程中,根据产品特点和生产条件,确定生产工艺路线和实施步骤的详细计划。
本文档旨在对工艺实施方案进行全面的分析和规划,确保生产过程顺利进行,产品质量稳定可靠。
二、工艺流程。
1. 原料准备,首先,根据产品配方和生产计划,准备所需原料和辅助材料,确保原料的质量符合要求。
2. 制备工序,将原料按照一定的比例进行混合、搅拌、加热等操作,形成初步的产品中间体。
3. 成型工序,对初步产品中间体进行成型加工,可以采用压制、注塑、挤出等方式,将产品初步成型。
4. 烘干/固化,对成型后的产品进行烘干或固化处理,确保产品的稳定性和耐久性。
5. 表面处理,对产品进行表面处理,包括喷涂、镀层、抛光等工艺,提高产品的外观质量和使用寿命。
6. 检验/包装,对成品进行严格的检验,确保产品符合质量标准,然后进行包装,准备出厂。
三、关键工艺参数。
1. 温度控制,在制备工序和烘干/固化工序中,需要严格控制温度,确保产品质量和成型效果。
2. 压力控制,在成型工序中,需要根据产品特点和成型材料的性质,合理控制成型压力,避免产品变形或损坏。
3. 时间控制,在各个工序中,需要精确控制加工时间,避免过长或过短导致产品质量问题。
4. 化学物质使用,在表面处理工序中,需要严格控制化学物质的使用量和浓度,确保环境安全和工人健康。
四、安全生产。
1. 人员防护,在生产过程中,要求操作人员严格遵守操作规程,配备必要的防护用具,确保人身安全。
2. 设备安全,对生产设备进行定期维护和检查,确保设备运行稳定,避免发生安全事故。
3. 废物处理,对生产过程中产生的废物进行分类、处理和回收利用,严禁乱倒乱排,保护环境。
五、质量控制。
1. 过程监控,建立完善的生产过程监控体系,对关键工艺参数进行实时监测和记录,确保产品质量可控。
2. 检验标准,制定严格的产品检验标准和抽样检验方案,对成品进行全面检测,确保产品合格率达标。
工艺路线方案

2)精基准选择的原则
①尽可能用工序基准作为定位基准——基准重合的原则
②所选的精基准应该能用它定位来加工尽可能多的表面——基准统一原则
③有的精加工或光整加工工序要求加工余量小,而均匀,在加工时应选择该加工表面本身作精基准——自为基准原则。
④有时还要遵循互为基准,反复加工的原则。
工序II扩钻主销孔、倒角:中心线距离叉架部分外轮廓72mm,钻主销Φ mm。
工序III拉主销孔:拉主销孔Φ mm,并保证同轴度Φ0.012mm。
工序IV铣端面、叉窝:将轴颈右端面铣距离定位中心 mm,叉窝距离定位中心43±1。
工序V 精铣两耳外侧面:两外侧面距离 mm,上耳厚度 mm。切对于主销孔中心轴线保持0.05的垂直度。
由《工艺简明》表2.2-22
= =0.90 可由表中公式计算r
外圆角半径r=0.05H+0.5
=0.05×55+0.5
=3.25
4、确定分模线位置
本锻件形状复杂为便于起模时及时发现上下模在模锻过程中的错位,上模出耳部、下模锻出节轴部。
5、确定拔模角
为简化起邮,以节轴部φ55处毛坯尺寸为准计算
= =1≤1.5且 <1
工序VIII 钻、扩、铰φ41主销孔锪孔φ67轴承主端及钻、攻4-M6螺纹孔
工序IX铣下耳内侧端面
工序X铣上、下耳部朝外端面
工序XI拉锥孔键槽8+0.098 +0.040达要求
工序XII车螺纹M30×1.5-6h
工序XIII铣平台26mm
比较之下,方案一工序更加集中,而方案二工序则工序分散,在此之下综合考虑,选择方案一。
根据《工艺手册》中表3-28,查得 =0.08mm/z
工艺技术路线
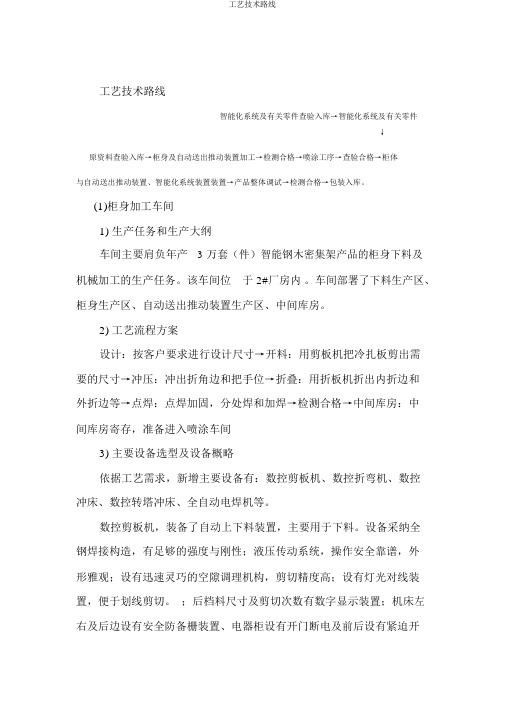
工艺技术路线智能化系统及有关零件查验入库→智能化系统及有关零件↓原资料查验入库→柜身及自动送出推动装置加工→检测合格→喷涂工序→查验合格→柜体与自动送出推动装置、智能化系统装置装置→产品整体调试→检测合格→包装入库。
(1)柜身加工车间1)生产任务和生产大纲车间主要肩负年产 3 万套(件)智能钢木密集架产品的柜身下料及机械加工的生产任务。
该车间位于 2#厂房内。
车间部署了下料生产区、柜身生产区、自动送出推动装置生产区、中间库房。
2)工艺流程方案设计:按客户要求进行设计尺寸→开料:用剪板机把冷扎板剪出需要的尺寸→冲压:冲出折角边和把手位→折叠:用折板机折出内折边和外折边等→点焊:点焊加固,分处焊和加焊→检测合格→中间库房:中间库房寄存,准备进入喷涂车间3)主要设备选型及设备概略依据工艺需求,新增主要设备有:数控剪板机、数控折弯机、数控冲床、数控转塔冲床、全自动电焊机等。
数控剪板机,装备了自动上下料装置,主要用于下料。
设备采纳全钢焊接构造,有足够的强度与刚性;液压传动系统,操作安全靠谱,外形雅观;设有迅速灵巧的空隙调理机构,剪切精度高;设有灯光对线装置,便于划线剪切。
;后档料尺寸及剪切次数有数字显示装置;机床左右及后边设有安全防备栅装置、电器柜设有开门断电及前后设有紧迫开关装置,带有防备罩脚踏开关,以保证工作时操作安全。
数控折弯机,装备了自动上下料装置,主要实现原料折弯工艺。
设备采纳了全闭环数控系统、两把光栅尺、一个光电编码器及时检测反应,步进电机驱动丝杆构成全闭环控制。
两把光栅尺;一把对后挡料、一把对滑块的地点及时检测反应纠正;光电编码器对油缸死挡块的地点进行检测反应给数控系统。
数控冲床,装备了自动上下料装置。
J21S 系列压力机其喉深超出同规格一般压力机的二倍,所以其属深喉口类压力机。
合用于板料冲孔,落料,曲折和浅拉伸等工艺。
数控转塔冲床主要实现产品板料加工。
设备采纳钢板焊接的闭式O 型机身,刚性好,稳固性高;简单易学的人性化控制系统,操作方便(入口冲压专用系统,功能强盛); CAD自动编程,辨别 Procam 变换代码,实现现场编程,后台编程;夹钳躲让功能,实现板材无死区加工;冲压速度可调,加强设备的柔性能力;传动系统采纳入口的高精度、大导程滚珠丝杠、直线导轨,精度高,性能好;主要气动元件、电器元件采纳稳固的入口品牌产品,使机床性能更趋完美;集中润滑装置,减少各无能运动副的摩擦,提升机器使用寿命;转塔采纳日本技术薄转塔,长导向并经热办理去内应力,刚性好、精度稳固、抗冲击能力强;模具采纳先进的加工及热办理工艺,使用寿命长,型号国际通用;高性能全自动浮动夹钳,万向球、毛刷混淆构造工作台。
厂房工艺路线布置方案

厂房工艺路线布置方案1. 引言在设计和建造厂房时,工艺路线的合理布置对于生产效率和生产流程的顺利进行至关重要。
本文将探讨一种厂房工艺路线布置方案,旨在最大程度地优化生产流程和提高生产效率。
2. 布置原则在制定布置方案时,我们应考虑以下原则:•优化生产流程:最小化不必要的物料和人员移动,减少生产时间和能源的浪费。
•确保安全性:合理布置生产区域和通道,保证人员和设备的安全。
•提高可操作性:确保操作人员能够方便地接触到设备和物料,减少操作难度和疏忽。
•灵活性和可扩展性:考虑到未来可能的生产线扩展和设备替换,布置方案应具有一定的灵活性和可扩展性。
3. 厂房布局3.1. 生产区域生产区域应根据不同的生产过程进行划分,并且按照生产流程的顺序进行布置。
在不同的生产区域之间,应提供足够的空间和通道,以便物料的流动和工艺的转换。
3.2. 辅助区域辅助区域包括原料储存区、成品仓储区、设备维护区等。
这些区域应与生产区域相对应,以便提供必要的支持和服务。
3.3. 办公区域在厂房中设置办公区域,提供管理和指导生产过程的工作空间。
办公区域应尽量与生产区域和辅助区域相邻,方便管理人员的监督和沟通。
4. 工艺路线布置4.1. 物料流动根据生产流程,确定物料在厂房内的流动路径。
物料流动路径应尽量简化和直观,以减少物料的移动和处理时间。
4.2. 设备布置根据工艺路线和设备之间的关系,布置各个设备的位置。
设备之间应保留足够的间距,以方便操作和维护。
4.3. 通道和辅助设施为了确保设备和物料的顺利流动,应设计合理的通道,并提供必要的辅助设施,如输送带、吊运设备等。
4.4. 安全考虑在工艺路线布置中,安全是一个重要的考虑因素。
通道和工作台应设定标准尺寸,以确保人员和设备的安全。
5. 布置方案示例下面是一个布置方案示例,仅供参考:办公区生产流程生产区域辅助区域6. 结论综上所述,厂房工艺路线的合理布置对于生产效率和生产流程的顺利进行至关重要。
配气机构摇臂轴”零件的机械加工工艺规程
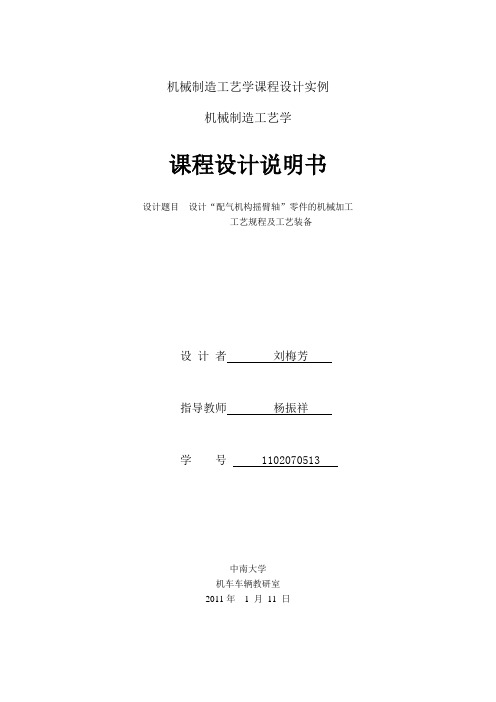
机械制造工艺学课程设计实例机械制造工艺学课程设计说明书设计题目设计“配气机构摇臂轴”零件的机械加工工艺规程及工艺装备设计者刘梅芳指导教师杨振祥学号 1102070513中南大学机车车辆教研室2011年 1 月11 日内容:1. 零件图 1张2. 毛坯图 1张3. 课程设计任务书 1份4. 机械加工工艺工程卡片 1张5. 机械加工工序卡 8张6. 夹具装配图 1张7.课程设计说明书 1份序言机械制造工艺学课程设计是在我们学完了大学的全部基础课、技术基础课以及大部分专业课之后进行的。
这是我们在进行毕业设计之前对所学各课程的一次深入的综合性的总复习,也是一次理论联系实际的训练,因此,它在我们四年的大学生活中占有重要的地位。
就个人而言,我希望能通过这次课程设计对自己未来将从事的工作进行一次适应性的训练,希望在设计中能锻炼自己分析问题、解决问题的能力,为自己今后参加祖国的“四化”建设打下一个良好的基础。
由于能力所限,设计尚有许多不足之处,希望各位老师给予指教。
一、零件的分析(一)零件的作用及技术要求1、零件的作用配气机构是进、排气管道的控制机构,它按照发动机的作功次序和每一缸的工作循环的要求,适时地开闭进、排气门、向气缸供给可燃混合气(汽油机)或新鲜空气(柴油机)并及时排出废气。
一般由凸轮轴、气门推杆、挺柱、气门摇臂、摇臂控制轴、气门导管以及气门等部件构成。
摇臂轴是一空心圆轴,用数个支座安装在气缸盖上,摇臂套装在摇臂轴上,并能在轴上作圆弧摆动。
轴内孔与主油道相通,供给配气机构润滑油2。
主要技术要求零件图上主要的技术要求为:1)摇臂轴调质硬度为HB255-302;B 表面淬火硬度HRC55-60,硬化深度1-1.5mm ; 2)探伤检查。
(二)零件的工艺性分析配气机构摇臂轴这个零件从附图1上可以看出,它一共有以下7组加工表面,分述如下:1、 Φ50h8轴:轴径039.050-mm ,表面粗糙度为Ra6.3μm ,端倒角2mm ×45°。
主要工艺技术路线

主要工艺技术路线主要工艺技术路线:在现代工业生产中,工艺技术路线是指将原材料经过一系列工序加工,最终制成产品的全部流程和步骤。
一个科学合理的工艺技术路线,可以提高产品的生产效率和质量,降低生产成本,进而增加企业的竞争力。
在制定主要工艺技术路线时,需要考虑以下几个方面:1. 原材料准备:包括原材料的筹备、储存和处理等工艺流程。
这个环节的重点是确保原材料的质量和供应稳定性,以及降低原材料的损耗。
2. 加工工序选择:根据产品的特性和要求,确定需要哪些加工工序以及它们的顺序。
同时,还要考虑加工工序的安全性、效率和可行性等因素。
3. 设备选择与布置:根据每个加工工序的特点,选择适合的设备,并合理布置各个工序的设备,以确保生产流程的连续性和高效性。
4. 工艺参数与控制:确定每个加工工序的工艺参数,包括温度、压力、速度等。
同时,要建立相应的监测和控制系统,及时掌握生产过程中的各项参数,并对其进行调整和控制,以确保产品的质量和一致性。
5. 危险源控制与防护:在工艺技术路线中,需要充分考虑可能存在的危险源,如高温、高压、有害物质等,并采取相应的防护措施,确保工人的安全和健康。
6. 副产品处理:在生产过程中,可能会产生一些副产品或废弃物,需要制定相应的处理方案,以减少对环境的影响,并实现资源的最大利用。
7. 质量控制与检测:在工艺技术路线中,需要建立一套完整的质量控制和检测体系,确保产品的质量符合标准和客户的要求。
总之,制定一个科学合理的工艺技术路线,需要全面考虑产品特性、原材料、工艺流程、设备和质量控制等多个因素,并进行适当的优化和经验总结。
只有通过不断改进和优化工艺技术路线,才能不断提高产品的品质,满足客户需求,促进企业的可持续发展。
- 1、下载文档前请自行甄别文档内容的完整性,平台不提供额外的编辑、内容补充、找答案等附加服务。
- 2、"仅部分预览"的文档,不可在线预览部分如存在完整性等问题,可反馈申请退款(可完整预览的文档不适用该条件!)。
- 3、如文档侵犯您的权益,请联系客服反馈,我们会尽快为您处理(人工客服工作时间:9:00-18:30)。
目录
第一章前言
第二章零件的工艺分析
第三章定位基准的选择
第四章工艺路线的拟定
第五章加工余量的确定
第六章工序尺寸及公差的确定
第七章机床与工艺装备的选择
第八章参考文献
第九章结束语
图1-1填料箱盖
(一)确定毛坯的制造形式零件材料为H T200。
考虑在运行过程中所受冲击不大,零件结构又比较简单,故选择铸件毛坯。
(二)零件的工艺分析共填料箱盖有两处加工表面,其间有一定位置要求。
分述如下:
1.φ65等一组外圆柱面及端面这一组加工表面包括:
φ的外圆面,φ80m m及以φ75m m的外圆面,φ的阶梯外轮廓面,及的密封环槽。
2.以φ50为中心的加工表面这一组加工表面包括:φ
的孔,以及其上下两个端面。
这两组表面有一定的位置度要求,即φ的孔上下两个端面与φ的孔有垂直度要求。
由上面分析可知,加工时应先加工一组表面,再以这组加工后表面为基准加工另外一组
(三)基面的选择基面选择是工艺规程设计中的重要工作之一。
基面选择得正确与合理可以使加工质量得到保证,生产率得以提高。
否则,加工工艺过程中回问题百出,更有甚者,还会造成零件的大批报废,是生产无法正常进行。
(1)粗基准的选择。
对于零件而言,尽可能选择不加工表面为粗基准。
而对有若干个不加工表面的工件,则应以与加工表面要求相对位置精度较高的不加工表面作粗基准。
(2)精基准的选择。
主要应该考虑基准重合的问题。
当设计基准与工序基准不重合时,应该进行尺寸换算,这在以后还要专门计算,此处不再重复。
(四)制定工艺路线按照先加工基准面,先面后孔、先粗后精的原则
工艺路线方案一
1、工序1:粗车外圆
并车左右端面。
2、工序2:半精车外圆
80m m,
3、工序3:钻扩孔
4、工序4:以右端面为基准粗镗—半精镗—精镗孔
5、工序5:粗磨,精磨,研磨孔的右端面
6、工序6:精车外圆
7、工序7:攻螺纹4X m10-6H T20
8、工序8:冲箭头
工序9:终检
工艺路线方案二
工序1:车铸件的两端面
工序2:钻扩孔
工序3:粗镗,半精镗,精镗左边孔
工序4:粗磨,精磨,研磨孔的右端面
工序5:粗车,半精车,精车外圆
工序6:攻螺纹4X M10-6H T20
工序7:冲箭头
工序8:终检
工艺方案的比较与分析
上述两个工艺方案的特点在于:方案一是以铸件外圆为粗基准,然后加工外圆、孔,而方案二则是以内孔为粗基准,先加工内孔,再加工外圆。
经比较可见,以外圆为粗基准,孔的余量不均,但加工后壁厚均匀,而以内孔为粗基准,孔的余量均匀,但加工后壁厚不均匀。
这时,根据要求,方案一的位置精度易保证,所以应选择方案一,具体的加工路线如下:
工序1:粗车端面及外圆
工序2:半精车外圆
工序3:以外圆为粗基准,钻扩孔,
并忽倒角45°,再钻孔,选用C365L转塔车床
工序4:以右端面及圆为基准,选用T740型卧式金刚镗床及专用夹具加工,粗镗,半精镗,精镗的孔工序5:磨孔的右端面,为保证表面粗糙度0.4,应先粗磨,精磨,再研磨
工序6:选用C A6140卧式车床和专用夹具精车外圆,91m m,
工序7:攻螺纹4X M10-6H T20
工序8:冲箭头
工序9:终检
(四)机械加工余量,工序尺寸及毛坯尺寸的确定根据上述原始资料及加工工艺,分别确定各加工表面的机械加工余量,工序尺寸及毛坯尺寸如下:
1、外圆表面ø155m m的外圆面取加工余量为4m m,ø100m m 的外圆取加工余量为 4.0m m,考虑到铸造的难易程度,ø78m m的外圆在铸造时直径与的外圆直径相同,同样的ø80m m的外圆的加工余量为 4.0m m,ø75m m的外圆铸造时与ø80m m直径相同,ø65m m的外圆加工余量为3m m
2、外圆表面沿轴线长度方向的加工余量及公差查《机械加工工艺手册》表 2.3-13;锻件轮廓尺寸(长度方向)>120-260m m,宽度>150m m故长度方向偏差为 1.8长度方向的余量规定为3m m,故取为3m m
3、内孔
(1)毛坯铸造了一个的内孔,精度在I T7—I T8之间,查表可知其加工余量为:
扩孔:
半精镗:55.9m m2z=0.2m m
精镗:2z=0.1m m
(2)的内孔和中间孔在铸造时为实心的,查表可知
两孔工序尺寸和余量为:
47的内孔:
钻孔:
钻孔:
钻孔:
扩孔:
粗镗:
半粗镗:
中间孔没有固定尺寸,故加工后保持I T8—I T9就可以满足要求了。
(五)选择加工设备与工艺装备1、选择机床①工序I、I I、I I I、V I是粗车和半精车。
选用卧式车床就能满足要求。
本零件尺寸不大,精度要求不高,选用最常用的C620-1型卧式车床即可。
②工序V、V I是精车和精细车还有精镗。
由于要求的精度较高,表面粗糙度较小选用精密的车床能满足要求。
故选用C616A型车床。
③工序V I I钻孔。
可采用专用的分度夹具在立式钻床上加工,可选用Z518型立式钻床。