硬质合金挤压产品变形因素的探讨
浅析硬质合金棒材压制模具的设计

管理及其他M anagement and other 浅析硬质合金棒材压制模具的设计彭 聪摘要:硬质合金是由难熔性金属的硬化物与黏结金属通过一定技术手段制成的合金材料,它的硬度高,耐磨性和韧性都非常好,即便是在1000℃的温度中,硬度依然很高。
由于此类材料的优势突出,因此在我国的汽车、钢铁以及交通运输等众多行业中都有非常广泛的应用。
但是由于我国硬质合金工业的起步比较晚,在压制模具方面还有很多不足,需要不断提升自身的技术水平,为我国工业发展提供技术支持。
本文主要介绍了硬质合金棒材压制模具的原理,并对模具设计的关键因素和内容进行了重点分析,以此来改进模具结构,提高工艺水平,延长模具的使用寿命。
关键词:硬质合金;棒材;压制模具硬质合金凭借自身的优势,在机床道具、采掘工具以及各种成型装置中的应用都非常广泛,其中应用比较多的就是机床刀具材料,例如车刀、刨刀等,它们能够完成各种钢材的切割。
例如自蔓延高温合成技术,已经作为新的材料制备技术而深受大家关注。
该技术的应用合成过程更加简单,耗能低,不需要额外再提供其他能量,而且反应温度比较高,能够将反应物中的杂质充分挥发出去,获得性能更好的原材料。
我国也要在各种先进方法的基础上,不断提升硬质棒材的加工质量,为我国工业发展做出更多贡献。
1 硬质合金棒材压制模具的成型原理当混合材料通过模拟鉴定没有任何问题之后,就可以正式进入硬质压制成型的阶段,由于硬质合金的主要成分是WC和TiC等硬质相,它们的硬度和抗压强度都很高,在压制过程中很难成型,需要添加成型机,以此来提高材料的流动性和润滑性,加速粉末的黏结,使压坯密度分布更加均匀,以便于后期的加工。
当压坯脱模时,即是将压力除去,由于弹性内应力产生的松弛作用而造成体积膨胀现象,统称为弹性后效。
压坯的三大缺陷分别是分层、裂纹和未压好,是对于工作人员而言,尽量降低缺陷问题十分重要。
首先是混合料的成分,弹性后效值会随着粉末硬度的提高而提升;如果粉末粒度比较细、颗粒之间黏结性比较差等都会导致弹性后效增大。
铝合金挤压缺陷分析及质量控制方法

铝合金挤压缺陷分析及质量控制方法铝合金挤压是一种常见的金属加工方法,可以制造出各种形状复杂、尺寸准确的铝合金材料。
在挤压过程中,可能会出现一些缺陷,如裂纹、畸变、气泡等。
这些缺陷对最终产品的性能和质量产生重要影响。
因此,对铝合金挤压缺陷进行分析和质量控制非常重要。
首先,我们来分析一些铝合金挤压可能出现的缺陷:1.裂纹:裂纹是挤压过程中最常见的缺陷之一,可能是由于材料的拉伸、压缩或应力过大引起的。
裂纹通常位于材料的边缘或内部,严重影响材料的强度和耐久性。
2.畸变:挤压过程中,材料受到强烈的变形力,可能导致其形状发生畸变。
这可能是由于模具设计不当、材料不均匀或挤压温度过高等原因引起的。
畸变会影响产品的精度和外观质量。
3.气泡:在挤压过程中,可能会产生气泡,这通常与气体溶解度、挤压温度、模具设计等因素有关。
气泡会降低材料的强度和断裂韧性。
为了控制和避免上述铝合金挤压缺陷,可以采取以下质量控制方法:1.优化模具设计:合理的模具设计可以减少挤压过程中的应力集中和变形,降低裂纹和畸变的风险。
通过对挤压参数和材料性能的充分了解,可以设计出适合的模具几何形状和尺寸。
2.选择合适的挤压温度:挤压温度对铝合金挤压过程中的材料流动性和冷却速率具有重要影响。
选择适宜的挤压温度可以避免材料的过度损伤和缺陷的产生。
3.控制挤压速度:挤压速度对挤压过程中的应力分布和微观组织形成有影响。
过高的挤压速度可能引起过度的应力和快速冷却,增加裂纹和畸变的风险。
因此,需要控制挤压速度,使之适应材料的性质和模具的要求。
4.严格控制材料质量:合格的原材料是制造高质量铝合金挤压材料的基础。
需要严格遵守材料规格和标准,进行材料化学成分和物理性能的检测,确保材料的可靠性和稳定性。
5.加强挤压过程监控:挤压过程中需要不断监控挤压力、温度、速度等参数,及时反馈调整,并进行质量检验。
通过合理的挤压工艺和检测控制方法,可以最大限度地避免缺陷的出现。
以上是针对铝合金挤压缺陷的分析及质量控制方法的简要介绍。
硬质合金的变形及断裂

境。疲劳是造成硬质合金工件破坏的一个主要原因。 腐蚀的原因主要是粘结相的迁移导致硬质相的相互分
疲劳种类一般来说有机械疲劳、热疲劳和腐蚀疲劳等。 机械疲劳是指材料在循环载荷下即使应力未能达到硬 质合金强度极限,但在交变的拉压和冲击作用下,产
离。PUGSLEY 等[39−40]在对用于伐木和金属切削的两 种 YW 牌号硬质合金刀具在水和酸性腐蚀环境下的力 学性能和疲劳性能进行的研究中发现:暴露在腐蚀环
YW 系列
研究了在静载荷、递增载荷和循环载荷下的合金的性能。指出合金的抗 疲劳性能不能从静载荷力学性能推导出来,因为即使常规强度相当的 材料其疲劳性能差距可能很大,这是由于材料的破坏机制不同,在疲劳 载荷下,材料的破坏是由临界裂纹扩展引起的。同时由于在裂纹扩展中 其裂纹尖端和韧性变形区的演变很复杂,所以很难根据合金成分进行预 测。在疲劳断裂中,临界裂纹扩展是在 Co 相中进行的,Co 相吸收大 部分的变形能并会引起面心相向密排相的相变,这种相变会降低塑性, 特别是在裂纹尖端部分的相变会阻碍裂纹的闭合效应,从而导致硬质合 金高的疲劳敏感性。
硬质合金工具的服役状况一般比较恶劣,常常需 要承受循环载荷、冷热交替的温度变化以及腐蚀的环
针对硬质合金刀具在切削中遇到的腐蚀环境问 题,关于硬质合金刀具的耐腐蚀性和在腐蚀环境下的 力学性能和疲劳性能也有一些研究。例如 WENTZEL 和 ALLEN[38]对几种添加不同粘结剂成分的 YG 合金 进行了腐蚀性能的研究,结果表明:纯 Co 或纯 Ni 粘 结相合金可以通过合金化的方法提高其耐腐蚀性能, NiCrCo 和 NiCr 的混合粘结相合金的腐蚀速率很 低。硬度越低,合金其腐蚀速度越快,造成硬质合金
硬质合金的品种很多,按化学成分可分为 3 类, 各类硬质合金因其成分和性能的不同,有着不同的应
压铸件变形的解决措施有哪些
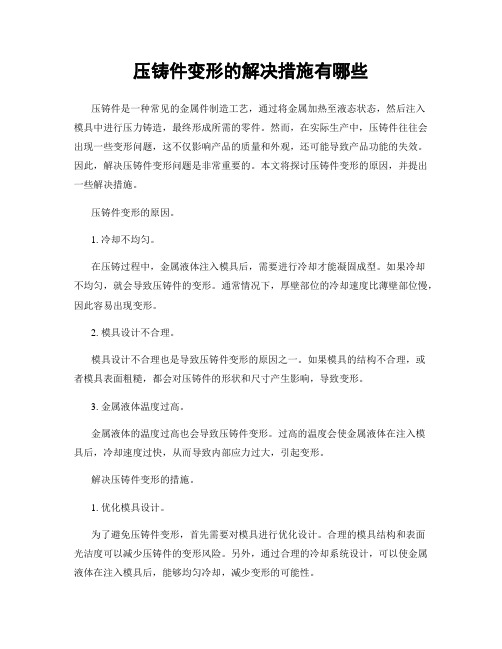
压铸件变形的解决措施有哪些压铸件是一种常见的金属件制造工艺,通过将金属加热至液态状态,然后注入模具中进行压力铸造,最终形成所需的零件。
然而,在实际生产中,压铸件往往会出现一些变形问题,这不仅影响产品的质量和外观,还可能导致产品功能的失效。
因此,解决压铸件变形问题是非常重要的。
本文将探讨压铸件变形的原因,并提出一些解决措施。
压铸件变形的原因。
1. 冷却不均匀。
在压铸过程中,金属液体注入模具后,需要进行冷却才能凝固成型。
如果冷却不均匀,就会导致压铸件的变形。
通常情况下,厚壁部位的冷却速度比薄壁部位慢,因此容易出现变形。
2. 模具设计不合理。
模具设计不合理也是导致压铸件变形的原因之一。
如果模具的结构不合理,或者模具表面粗糙,都会对压铸件的形状和尺寸产生影响,导致变形。
3. 金属液体温度过高。
金属液体的温度过高也会导致压铸件变形。
过高的温度会使金属液体在注入模具后,冷却速度过快,从而导致内部应力过大,引起变形。
解决压铸件变形的措施。
1. 优化模具设计。
为了避免压铸件变形,首先需要对模具进行优化设计。
合理的模具结构和表面光洁度可以减少压铸件的变形风险。
另外,通过合理的冷却系统设计,可以使金属液体在注入模具后,能够均匀冷却,减少变形的可能性。
2. 控制金属液体温度。
控制金属液体的温度也是避免压铸件变形的关键。
在生产过程中,需要严格控制金属液体的温度,确保其在合适的范围内,避免过高的温度导致变形。
3. 优化冷却系统。
优化冷却系统可以帮助金属液体均匀冷却,减少变形的风险。
通过改进冷却系统的设计,可以使冷却速度更加均匀,从而减少压铸件的变形。
4. 采用合适的材料。
选择合适的材料也可以减少压铸件的变形。
一些具有良好流动性和凝固性能的金属材料,可以减少变形的可能性。
此外,还可以通过添加一些合金元素来改善金属的性能,减少变形的风险。
5. 控制冷却速度。
控制冷却速度是避免压铸件变形的关键。
在生产过程中,需要合理控制冷却速度,避免过快或过慢的冷却速度导致压铸件的变形。
硬质合金的质量影响因素研究与对策
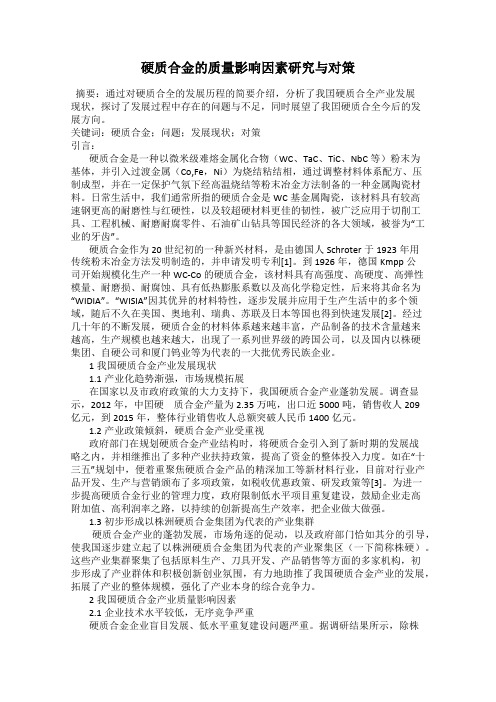
硬质合金的质量影响因素研究与对策摘要:通过对硬质合全的发展历程的简要介绍,分析了我囯硬质合全产业发展现状,探讨了发展过程中存在的问题与不足,同时展望了我囯硬质合全今后的发展方向。
关键词:硬质合金;问题;发展现状;对策引言:硬质合金是一种以微米级难熔金属化合物(WC、TaC、TiC、NbC等)粉末为基体,并引入过渡金属(Co,Fe,Ni)为烧结粘结相,通过调整材料体系配方、压制成型,并在一定保护气氛下经高温烧结等粉末冶金方法制备的一种金属陶瓷材料。
日常生活中,我们通常所指的硬质合金是WC基金属陶瓷,该材料具有较高速钢更高的耐磨性与红硬性,以及较超硬材料更佳的韧性,被广泛应用于切削工具、工程机械、耐磨耐腐零件、石油矿山钻具等国民经济的各大领域,被誉为“工业的牙齿”。
硬质合金作为20世纪初的一种新兴材料,是由德国人Schroter于1923年用传统粉末冶金方法发明制造的,并申请发明专利[1]。
到1926年,德国Kmpp公司开始规模化生产一种WC-Co的硬质合金,该材料具有高强度、高硬度、高弹性模量、耐磨损、耐腐蚀、具有低热膨胀系数以及高化学稳定性,后来将其命名为“WIDIA”。
“WISIA”因其优异的材料特性,逐步发展并应用于生产生活中的多个领域,随后不久在美国、奥地利、瑞典、苏联及日本等国也得到快速发展[2]。
经过几十年的不断发展,硬质合金的材料体系越来越丰富,产品制备的技术含量越来越高,生产规模也越来越大,出现了一系列世界级的跨国公司,以及国内以株硬集团、自硬公司和厦门钨业等为代表的一大批优秀民族企业。
1我国硬质合金产业发展现状1.1产业化趋势渐强,市场规模拓展在国家以及市政府政策的大力支持下,我国硬质合金产业蓬勃发展。
调查显示,2012年,中囯硬质合金产量为2.35万吨,出口近5000吨,销售收人209亿元,到2015年,整体行业销售收人总额突破人民币1400亿元。
1.2产业政策倾斜,硬质合金产业受重视政府部门在规划硬质合金产业结构时,将硬质合金引入到了新时期的发展战略之内,并相继推出了多种产业扶持政策,提高了资金的整体投入力度。
压铸件变形的解决措施是什么
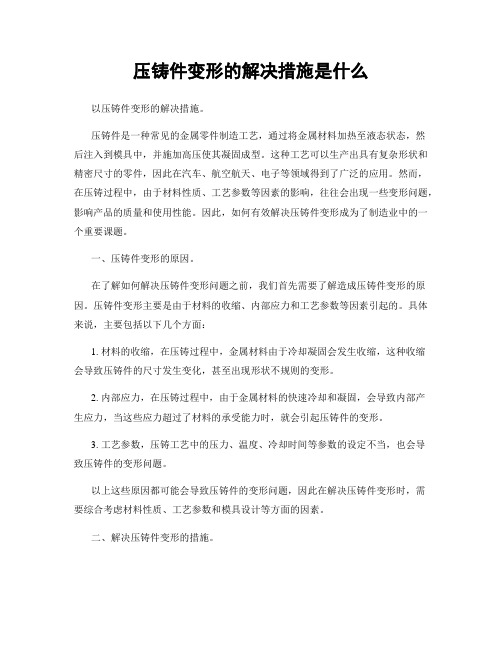
压铸件变形的解决措施是什么以压铸件变形的解决措施。
压铸件是一种常见的金属零件制造工艺,通过将金属材料加热至液态状态,然后注入到模具中,并施加高压使其凝固成型。
这种工艺可以生产出具有复杂形状和精密尺寸的零件,因此在汽车、航空航天、电子等领域得到了广泛的应用。
然而,在压铸过程中,由于材料性质、工艺参数等因素的影响,往往会出现一些变形问题,影响产品的质量和使用性能。
因此,如何有效解决压铸件变形成为了制造业中的一个重要课题。
一、压铸件变形的原因。
在了解如何解决压铸件变形问题之前,我们首先需要了解造成压铸件变形的原因。
压铸件变形主要是由于材料的收缩、内部应力和工艺参数等因素引起的。
具体来说,主要包括以下几个方面:1. 材料的收缩,在压铸过程中,金属材料由于冷却凝固会发生收缩,这种收缩会导致压铸件的尺寸发生变化,甚至出现形状不规则的变形。
2. 内部应力,在压铸过程中,由于金属材料的快速冷却和凝固,会导致内部产生应力,当这些应力超过了材料的承受能力时,就会引起压铸件的变形。
3. 工艺参数,压铸工艺中的压力、温度、冷却时间等参数的设定不当,也会导致压铸件的变形问题。
以上这些原因都可能会导致压铸件的变形问题,因此在解决压铸件变形时,需要综合考虑材料性质、工艺参数和模具设计等方面的因素。
二、解决压铸件变形的措施。
针对压铸件变形的原因,我们可以采取一系列的措施来解决这一问题,主要包括以下几个方面:1. 合理选择材料,在进行压铸件的材料选择时,需要考虑材料的收缩率、热膨胀系数等因素,选择合适的材料可以降低压铸件的收缩变形。
2. 优化工艺参数,在压铸过程中,通过合理调整压力、温度、注射速度等工艺参数,可以减小内部应力的产生,降低压铸件的变形。
3. 设计合理的模具,模具的设计对于压铸件的质量和形状有着重要的影响,合理设计模具可以减小压铸件的收缩变形,减少内部应力的产生。
4. 采用热处理工艺,通过对压铸件进行热处理,可以消除内部应力,提高材料的稳定性,减少变形问题的发生。
浅谈硬质合金粉末压模设计制造中的常见问题及对策

浅谈硬质合金粉末压模设计制造中的常见问题及对策硬质合金粉末压模是一种制造高硬度和高强度零件的重要工艺。
然而,在设计和制造过程中,常常会出现一些常见问题。
本文将就这些问题及其对策进行浅谈。
问题一:压制后零件表面粗糙度过高造成表面粗糙度过高的原因可能是压模表面粗糙度太高或模具的非对称性造成的不均匀变形。
对策是先充分优化模具表面质量,保证其表面粗糙度在需要范围内,一般不超过Ra0.4μm,然后在开发模具前应通过模拟的方法寻找非对称性变形的原因,采取相应的对策,如优化压力分布等,以保证零件表面粗糙度在合理范围内。
问题二:零件误差过大零件误差大多数情况下是由模具设计不合理或者制造过程中的误差引起的。
对策是优化模具的设计,要考虑到零件的形状,尺寸和结构特征,确保模具的尺寸和精度要求在合理范围内。
在制造过程中,需要对模具进行精确加工和组装,减少模具制造中的误差,如对模具中的每个部件进行测量和校正,并且在每个步骤结束后进行全面检查。
问题三:零件的强度不均匀零件的强度不均匀可能由压模时的非对称变形和热处理不均匀引起。
对策是通过模拟工具预测和优化变形,避免非对称变形,同时在热处理过程中采取适当的温度和时间控制,确保零件中的铸造组织均匀,并且使用高精度的测量设备检查其强度。
问题四:模孔磨损模具工作时,由于力的作用及颗粒的冲击导致模孔磨损。
对策是在设计和制造时考虑到硬质合金材料的特性,选择适当的硬质合金材料,保证其硬度高,耐磨性好。
这样不仅可以延长模具寿命,而且可以减少换模次数和其它维护费用。
总之,硬质合金粉末压模设计制造中的常见问题及其对策需要从多个方面入手,如合理的设计,优化工艺参数和使用合适的材料,并始终保持高质量的制造和检测,才能确保零件的品质和稳定性。
浅谈硬质合金粉末压模设计制造中的常见问题及对策
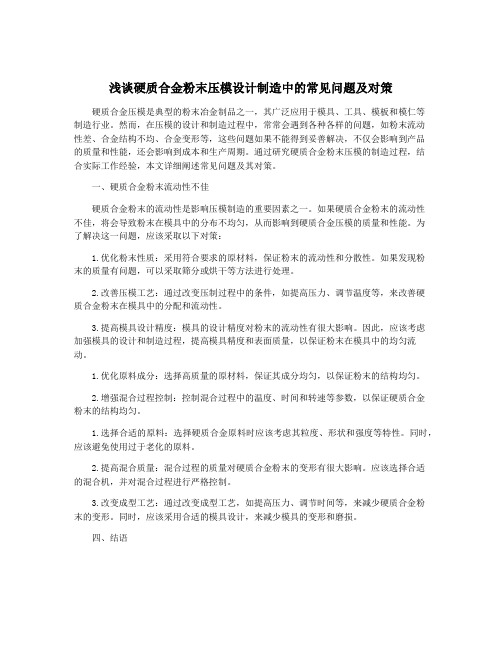
浅谈硬质合金粉末压模设计制造中的常见问题及对策硬质合金压模是典型的粉末冶金制品之一,其广泛应用于模具、工具、模板和模仁等制造行业。
然而,在压模的设计和制造过程中,常常会遇到各种各样的问题,如粉末流动性差、合金结构不均、合金变形等,这些问题如果不能得到妥善解决,不仅会影响到产品的质量和性能,还会影响到成本和生产周期。
通过研究硬质合金粉末压模的制造过程,结合实际工作经验,本文详细阐述常见问题及其对策。
一、硬质合金粉末流动性不佳硬质合金粉末的流动性是影响压模制造的重要因素之一。
如果硬质合金粉末的流动性不佳,将会导致粉末在模具中的分布不均匀,从而影响到硬质合金压模的质量和性能。
为了解决这一问题,应该采取以下对策:1.优化粉末性质:采用符合要求的原材料,保证粉末的流动性和分散性。
如果发现粉末的质量有问题,可以采取筛分或烘干等方法进行处理。
2.改善压模工艺:通过改变压制过程中的条件,如提高压力、调节温度等,来改善硬质合金粉末在模具中的分配和流动性。
3.提高模具设计精度:模具的设计精度对粉末的流动性有很大影响。
因此,应该考虑加强模具的设计和制造过程,提高模具精度和表面质量,以保证粉末在模具中的均匀流动。
1.优化原料成分:选择高质量的原材料,保证其成分均匀,以保证粉末的结构均匀。
2.增强混合过程控制:控制混合过程中的温度、时间和转速等参数,以保证硬质合金粉末的结构均匀。
1.选择合适的原料:选择硬质合金原料时应该考虑其粒度、形状和强度等特性。
同时,应该避免使用过于老化的原料。
2.提高混合质量:混合过程的质量对硬质合金粉末的变形有很大影响。
应该选择合适的混合机,并对混合过程进行严格控制。
3.改变成型工艺:通过改变成型工艺,如提高压力、调节时间等,来减少硬质合金粉末的变形。
同时,应该采用合适的模具设计,来减少模具的变形和磨损。
四、结语综上所述,硬质合金粉末压模的制造过程中存在着众多的问题。
然而,通过仔细分析和掌握制造过程的关键要素,采取适当的对策,我们就能够解决这些问题,提高硬质合金压模的质量和性能。
影响挤压硬质合金棒材质量的因素分析
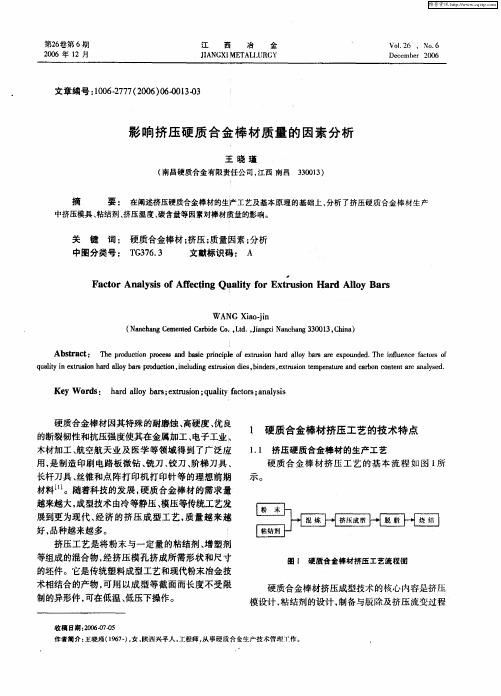
WA G X a-n N i j oi
( aca gC m n dC ri 0 Ld ,i gi aea g 3 0 3 C ia N n hn e et abd C ,t.J nx N nh n 0 1 , hn ) e e a 3
Ab t a t: T ep o u t n po es a d b sc p n il fe t in h r l y b r r x o n e 。 h n u n efcos o sr c h rd ci rc s n ai r cpe o xmso ad al asa ee p u d d T e if e c a tr f o i o l
图 I 硬质台金棒材挤压工艺流 程圈
收稿 日期 : 0 -7 5 2 6 - 0 00 作者简介 : 壬晓碰( 9 7 )女 , 16 ・ , 陕西兴平人 , = : 程师, 【 从事硬质合金生产技术管删 ‘作 。 1 :
维普资讯
・
l ・ 4
关
键
词 : 硬质合金棒材 ; 挤压 ; 质量因素; 分析
中图分类号 : T 36 3 G 7 .
文献标识鸡 : A
,
F co n ls fA et gQU lyfrE tuinHadAl yB r atrA ayi o f ci ai xrs r l a s s n t o o o
=7 d 10 1 百 2- 2× 0%
式中:-压缩 比; j , D,一分别为挤压嘴的外径和挤压嘴的内径。 d
制品端面的模孔, 在挤压筒的另一端插入挤压冲头 ,
挤压机的压力通过挤压冲头传给混合料 , 使之通过
模孑 而成为具有一定形状的制品 。棒材挤压模 L
挤压 如 图 2 所示 。
挤压变形的主要缺陷

挤压变形的主要缺陷1、模具的影响在挤压生产中,模具是在高温高压的状态下工作的,受压力和温度的影响,模具产生弹性变形。
模具工作带由开始平行于挤压方向,受到压力后,工作带变形成为喇叭状,只有工作带的刃口部分接触型材形成的粘铝,类似于车刀的刀屑瘤。
在粘铝的形成过程中,不断有颗粒被型材带出,粘附在型材表面上,造成了吸附颗粒。
随着粘铝的不断增大,模具产生瞬间回弹,就会形成咬痕缺陷。
若粘铝堆积较多,不能被型材拉出,模具瞬间回弹时粘铝不脱落,就会形成型材的表面粗糙、亮条、型材撕裂、堵模等问题。
我们现在使用的挤压模具基本是平面模,在铸棒不剥皮的情况下,铸棒表面及内在的杂质堆积在模具内金属流动的死区,随着挤压铸棒的推进及挤压根数的增多,死区的杂质也在不断的变化,有一部分被正常流动的金属带出,堆积在工作带变形后的空间内。
有的被型材拉脱,形成了吸附颗粒。
因此,模具是造成吸附颗粒的关键因素。
2、挤压工艺的影响挤压工艺参数的选择正确与否也是影响吸附颗粒的重要因素。
经过现场观察,挤压温度、挤压速度过高,吸附颗粒就越多,原因是由于温度高、速度快,型材流动速度增加,模具变形的程度增加,金属的流动加快,金属的变形抗力相对减弱,更易形成粘铝现象;对大的挤压系数来说,金属的变形抗力相对增加了,死区相对增大,提高了形成粘铝的条件,形成吸附颗粒的概率增加;铸棒加热温度与模具温度之差过大,也易造成粘铝问题,甚至堵模;工模具表面的粗糙度、工作带表面的硬度等,也是造成粘铝,形成吸附颗粒的原因之一。
3、铸棒质量的影响铸棒质量是影响铝型材表面及挤压成型的重要因素。
吸附颗粒的成因与铸棒质量有很大关系。
铸棒的组织缺陷常见的有夹渣、疏松、晶粒粗大、偏析、光亮晶粒等。
夹渣是混入铸棒的熔渣、氧化皮或其他杂质,也叫夹杂。
低倍试片上一般呈现形状不规则的黑洞,凹陷于基体,是一些不同颜色的、无定形的松软组织,破坏了铸棒的连续性。
在挤压过程中,夹渣极易从基体中分离出来,通过模具的工作带时,粘附在入口端,形成粘铝,并不断被流动的金属拉出,形成吸附颗粒;疏松是在晶界及枝晶网络出现的宏观和微观的分散性缩孔。
浅谈硬质合金粉末压模设计制造中的常见问题及对策

浅谈硬质合金粉末压模设计制造中的常见问题及对策硬质合金粉末压模设计制造中存在一些常见问题,需要采取相应的对策来解决。
以下是对这些问题及对策的简要讨论。
1. 粉末流动性不良:粉末的流动性对压模制造非常重要。
如果粉末流动性不好,会导致充填不均匀,影响成型品的质量。
对策是选择具有良好流动性的粉末,并在设计时优化充填结构,例如增加斜面和充填筒。
2. 模具磨损严重:在硬质合金粉末压模的制造过程中,模具的磨损是一个常见问题。
模具磨损会导致成型品尺寸不准确,甚至不可使用。
为了减轻模具的磨损,可以选择高硬度、高耐磨的材料制造模具,并采取合适的润滑和冷却措施,以减少磨损和延长模具使用寿命。
3. 模具冲损:在硬质合金粉末压模过程中,模具经常需要多次冲击。
长期冲击会导致模具表面出现裂纹和变形等问题,影响成型品的质量。
对策是在设计模具时考虑合适的冷却系统和支撑结构,以提高模具的耐冲击性能。
4. 成品品质不稳定:在硬质合金粉末压模制造过程中,成品品质不稳定是一个常见问题。
成品品质的不稳定可能是由于粉末配比不均匀、压力不稳定、模具失效等原因引起的。
对策是通过优化粉末配比、稳定压力和提高模具质量等方式,来提高成品的品质稳定性。
5. 模具寿命短:由于硬质合金粉末压模制造过程中的高温、高压和频繁冲击等因素,模具寿命一般较短。
对策是采用高强度、耐磨及耐腐蚀的材料来制造模具,并根据实际情况选择合适的表面处理方式,以延长模具的使用寿命。
硬质合金粉末压模设计制造中常见的问题包括粉末流动性不良、模具磨损严重、模具冲损、成品品质不稳定以及模具寿命短等。
通过选择适当的粉末、优化设计和加强模具材料等方面的对策,可以有效地解决这些问题,提高压模产品的质量和寿命。
挤压缺陷鉴别与原因分析及改善措施培训教材

挤压缺陷鉴别与原因分析及改善措施培训教材汇报人:日期:•挤压缺陷鉴别•挤压缺陷原因分析•挤压缺陷改善措施目•挤压缺陷案例分析录挤压缺陷鉴别01表面粗糙裂纹气泡氧化01020304挤压件表面存在不平整、凹凸不光滑现象。
挤压件表面或内部存在连续或断续的裂纹。
挤压件表面存在圆形或不规则的气泡。
挤压件表面出现黑色氧化现象。
挤压件的实际尺寸与设计尺寸存在较大差异。
尺寸超差挤压件存在扭曲变形现象,导致尺寸不直。
扭曲挤压件存在弯曲变形现象,导致尺寸不准确。
弯曲晶粒粗大偏析热处理不当挤压件组织结构中存在化学成分不均匀现象。
热处理工艺不当导致组织结构不均匀或出现缺陷。
0302 01组织结构缺陷鉴别挤压件组织结构中晶粒尺寸过大,影响材料性能。
挤压缺陷原因分析02不同批次或不同来源的原材料可能存在成分差异,如化学成分、晶粒大小等,影响挤压加工性能和产品质量。
成分差异原材料中可能含有过多的杂质,如气体、氧化物、硫化物等,影响挤压塑性和产品的机械性能。
杂质含量原材料原因挤压速度挤压速度过低或过高都可能影响制品质量,如速度过低可能导致制品不致密,速度过高则可能导致金属过热和模具磨损。
挤压温度温度过高可能导致金属塑性降低、模具磨损加剧,温度过低则可能导致金属流动性差、制品不致密。
挤压比挤压比过小或过大都可能影响制品质量和性能,如比值过小可能导致制品不致密,比值过大则可能导致金属过热和模具磨损。
挤压工艺原因如模具流速分布不均、模孔排布不当等,导致制品出现缺陷。
如模孔尺寸偏差、表面粗糙等,影响制品成型和质量。
模具原因模具制造精度差模具设计不合理如加热温度、保温时间等不当,导致金属内部结构变化不均匀,影响制品机械性能。
热处理不当如表面涂层质量、氧化处理等不当,影响制品外观和耐腐蚀性。
表面处理不当产品加工后续处理原因挤压缺陷改善措施03调整原材料成分通过调整原材料的化学成分和物理性能,可以改善挤压过程的稳定性和产品质量。
详细描述根据挤压产品的要求,对原材料的化学成分进行精细调整,控制杂质含量和微量元素比例,确保材料具有适宜的塑性和韧性,以利于挤压成型。
硬质合金烧结变形及控制方法
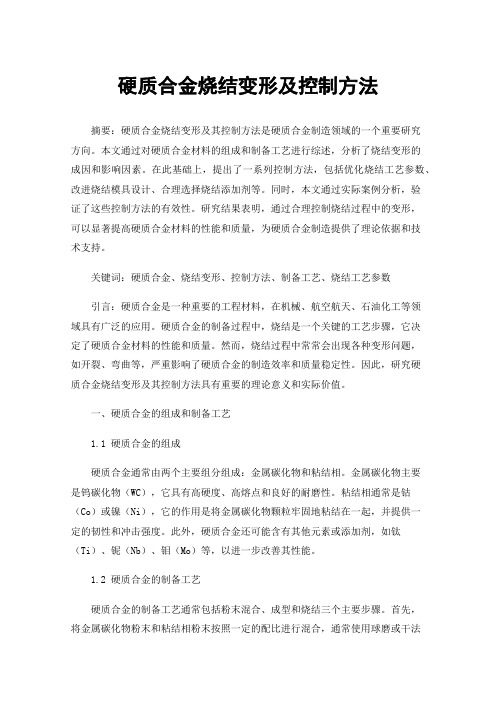
硬质合金烧结变形及控制方法摘要:硬质合金烧结变形及其控制方法是硬质合金制造领域的一个重要研究方向。
本文通过对硬质合金材料的组成和制备工艺进行综述,分析了烧结变形的成因和影响因素。
在此基础上,提出了一系列控制方法,包括优化烧结工艺参数、改进烧结模具设计、合理选择烧结添加剂等。
同时,本文通过实际案例分析,验证了这些控制方法的有效性。
研究结果表明,通过合理控制烧结过程中的变形,可以显著提高硬质合金材料的性能和质量,为硬质合金制造提供了理论依据和技术支持。
关键词:硬质合金、烧结变形、控制方法、制备工艺、烧结工艺参数引言:硬质合金是一种重要的工程材料,在机械、航空航天、石油化工等领域具有广泛的应用。
硬质合金的制备过程中,烧结是一个关键的工艺步骤,它决定了硬质合金材料的性能和质量。
然而,烧结过程中常常会出现各种变形问题,如开裂、弯曲等,严重影响了硬质合金的制造效率和质量稳定性。
因此,研究硬质合金烧结变形及其控制方法具有重要的理论意义和实际价值。
一、硬质合金的组成和制备工艺1.1 硬质合金的组成硬质合金通常由两个主要组分组成:金属碳化物和粘结相。
金属碳化物主要是钨碳化物(WC),它具有高硬度、高熔点和良好的耐磨性。
粘结相通常是钴(Co)或镍(Ni),它的作用是将金属碳化物颗粒牢固地粘结在一起,并提供一定的韧性和冲击强度。
此外,硬质合金还可能含有其他元素或添加剂,如钛(Ti)、铌(Nb)、钼(Mo)等,以进一步改善其性能。
1.2 硬质合金的制备工艺硬质合金的制备工艺通常包括粉末混合、成型和烧结三个主要步骤。
首先,将金属碳化物粉末和粘结相粉末按照一定的配比进行混合,通常使用球磨或干法混合的方法,以确保两种粉末均匀混合。
然后,将混合粉末通过成型工艺,如压制、注射成型等,制备成所需的形状,如板材、棒材、刀片等。
最后,成型体经过烧结工艺,即在高温下进行加热处理,以使金属碳化物颗粒结合成整体。
烧结过程中,首先进行预烧结,将成型体加热至金属碳化物颗粒开始颗粒间结合的温度。
硬质合金粉末压制模具设计制造中的常见问题及对策
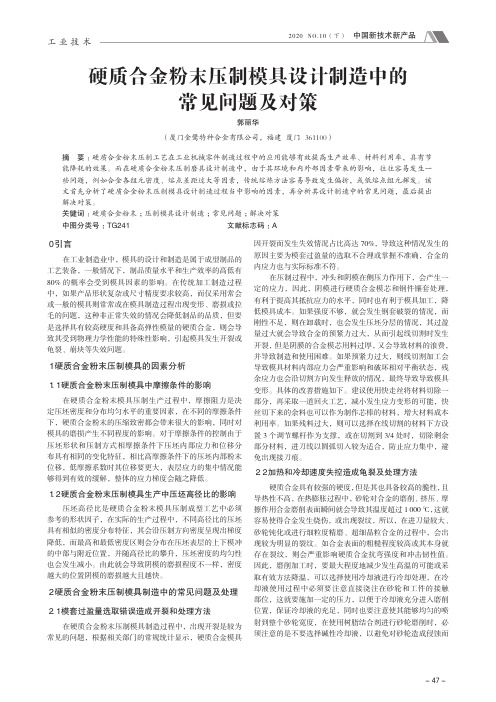
- 47 -工 业 技 术0 引言在工业制造业中,模具的设计和制造是属于成型制品的工艺装备,一般情况下,制品质量水平和生产效率的高低有80%的概率会受到模具因素的影响。
在传统加工制造过程中,如果产品形状复杂或尺寸精度要求较高,而仅采用常会或一般的模具则常常或在模具制造过程出现变形、磨损或拉毛的问题,这种非正常失效的情况会降低制品的品质,但要是选择具有较高硬度和具备高弹性模量的硬质合金,则会导致其受到物理力学性能的特殊性影响,引起模具发生开裂或龟裂、崩块等失效问题。
1 硬质合金粉末压制模具的因素分析1.1 硬质合金粉末压制模具中摩擦条件的影响在硬质合金粉末模具压制生产过程中,摩擦阻力是决定压坯密度和分布均匀水平的重要因素,在不同的摩擦条件下,硬质合金粉末的压缩致密都会带来很大的影响,同时对模具的磨损产生不同程度的影响。
对于摩擦条件的控制由于压坯形状和压制方式相摩擦条件下压坯内部应力和位移分布具有相同的变化特征,相比高摩擦条件下的压坯内部粉末位移,低摩擦系数时其位移要更大,表层应力的集中情况能够得到有效的缓解,整体的应力梯度会随之降低。
1.2 硬质合金粉末压制模具生产中压坯高径比的影响压坯高径比是硬质合金粉末模具压制成型工艺中必须参考的形状因子,在实际的生产过程中,不同高径比的压坯具有相似的密度分布特征,其会沿压制方向密度呈现出梯度降低,而最高和最低密度区则会分布在压坯表层的上下模冲的中部与附近位置,并随高径比的攀升,压坯密度的均匀性也会发生减小。
由此就会导致阴模的磨损程度不一样,密度越大的位置阴模的磨损越大且越快。
2 硬质合金粉末压制模具制造中的常见问题及处理2.1 模套过盈量选取错误造成开裂和处理方法在硬质合金粉末压制模具制造过程中,出现开裂是较为常见的问题,根据相关部门的常规统计显示,硬质合金模具因开裂而发生失效情况占比高达70%,导致这种情况发生的原因主要为模套过盈量的选取不合理或掌握不准确,合金的内应力也与实际标准不符。
浅谈硬质合金粉末压模设计制造中的常见问题及对策
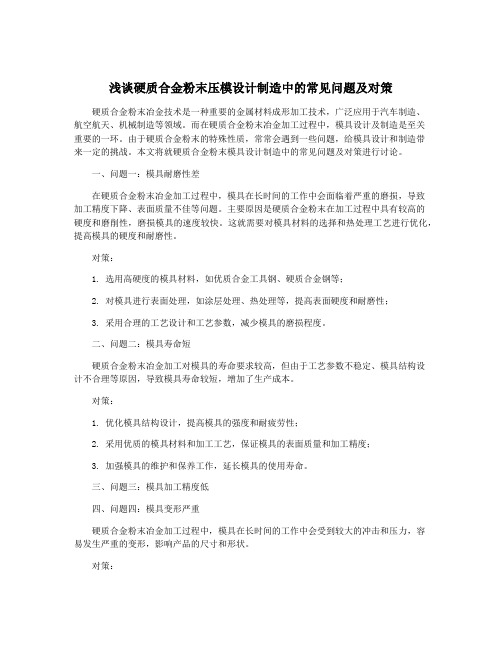
浅谈硬质合金粉末压模设计制造中的常见问题及对策硬质合金粉末冶金技术是一种重要的金属材料成形加工技术,广泛应用于汽车制造、航空航天、机械制造等领域。
而在硬质合金粉末冶金加工过程中,模具设计及制造是至关重要的一环。
由于硬质合金粉末的特殊性质,常常会遇到一些问题,给模具设计和制造带来一定的挑战。
本文将就硬质合金粉末模具设计制造中的常见问题及对策进行讨论。
一、问题一:模具耐磨性差在硬质合金粉末冶金加工过程中,模具在长时间的工作中会面临着严重的磨损,导致加工精度下降、表面质量不佳等问题。
主要原因是硬质合金粉末在加工过程中具有较高的硬度和磨削性,磨损模具的速度较快。
这就需要对模具材料的选择和热处理工艺进行优化,提高模具的硬度和耐磨性。
对策:1. 选用高硬度的模具材料,如优质合金工具钢、硬质合金钢等;2. 对模具进行表面处理,如涂层处理、热处理等,提高表面硬度和耐磨性;3. 采用合理的工艺设计和工艺参数,减少模具的磨损程度。
二、问题二:模具寿命短硬质合金粉末冶金加工对模具的寿命要求较高,但由于工艺参数不稳定、模具结构设计不合理等原因,导致模具寿命较短,增加了生产成本。
对策:1. 优化模具结构设计,提高模具的强度和耐疲劳性;2. 采用优质的模具材料和加工工艺,保证模具的表面质量和加工精度;3. 加强模具的维护和保养工作,延长模具的使用寿命。
三、问题三:模具加工精度低四、问题四:模具变形严重硬质合金粉末冶金加工过程中,模具在长时间的工作中会受到较大的冲击和压力,容易发生严重的变形,影响产品的尺寸和形状。
对策:1. 优化模具设计,提高模具的强度和刚度,减少变形的可能性;2. 采用合理的工艺参数和成形工艺,减少模具的冲击和压力;3. 优化模具的冷却系统,提高模具的散热效果,减少变形的程度。
硬质合金粉末压模设计制造中常见的问题有着复杂性和多样性,需要在实际生产中根据具体情况采取相应的对策措施。
这些措施包括对模具材料、结构设计、加工工艺等方面的优化和改进,以求提高模具的耐磨性、寿命、加工精度和强度,保证产品的质量和成形效果。
硬质合金变形需要的温度

硬质合金变形需要的温度硬质合金是由硬质材料(如碳化钨、碳化钛等)和粘结金属(如钴、镍等)通过粉末冶金工艺制成的复合材料。
它们以极高的硬度、良好的耐磨性和抗压强度而著称,广泛应用于切削工具、模具、矿山钻头等领域。
硬质合金的变形,即塑性加工,通常涉及到热处理过程,包括热压、锻造或挤压等。
硬质合金的变形温度取决于其具体成分和目标应用,但一般而言,需要在较高的温度下进行,以减少材料的脆性并提高其塑性。
这些温度通常高于室温,并且可以达到材料熔点的一定比例,但必须避免达到或超过粘结相的熔点,以防止材料的性能恶化。
硬质合金变形的典型温度范围•低温变形:在500°C到800°C之间,可以进行一些轻微的变形加工,如弯曲或校正。
这个温度范围对于硬质合金来说相对较低,变形能力有限。
•中温变形:在800°C到1000°C之间,硬质合金的塑性会有所提高,可以进行更为复杂的变形加工,如轧制或锻造。
在这个温度范围内,粘结相的塑性变形能力得到显著提升,有助于硬质颗粒的重新排列和密实。
•高温变形:在1000°C到1400°C之间,部分硬质合金可在此温度范围内进行高温挤压、热压等加工。
这个温度范围接近于一些粘结相的熔点,因此需要精确控制温度,避免材料性能下降。
需要注意的是,具体的变形温度还需根据硬质合金的成分、预期的变形量、加工速度和加工环境等因素综合考虑。
高温加工时,还需注意氧化问题,可能需要在保护气氛或真空中进行。
此外,高温变形后的硬质合金通常需要通过适当的冷却程序和后续热处理来优化其最终性能。
总之,硬质合金的变形加工是一个复杂的过程,需要根据材料特性和加工要求仔细选择适当的温度和技术。
浅谈硬质合金粉末压模设计制造中的常见问题及对策

浅谈硬质合金粉末压模设计制造中的常见问题及对策在硬质合金粉末压模设计制造过程中,常常会遇到一些常见问题,这些问题会对产品质量和生产效率造成一定的影响。
下面我将就硬质合金粉末压模设计制造中常见问题及对策进行浅谈。
第一个常见问题是模具设计时出现的粉末堆积问题。
硬质合金粉末在模具中的堆积会导致压制过程中出现气孔或者不均匀的密度分布,从而影响产品的机械性能。
解决这一问题的对策是根据不同的产品形状和工艺要求,设计合理的模具结构,确保粉末能够均匀分布,避免堆积现象的发生。
第二个常见问题是模具磨损问题。
在硬质合金粉末压模的制造过程中,模具会受到高压和摩擦的作用,容易出现磨损现象。
模具的磨损会导致产品尺寸不稳定、形状偏差增大等问题。
为了解决这一问题,可以采取以下对策:在模具材料的选择上尽量选择硬度高、耐磨性好的材料;在模具的表面上添加一层涂层,以增加模具的使用寿命;定期对模具进行维护保养,及时修复磨损。
第三个常见问题是模具结构设计不合理导致成型瑕疵。
硬质合金粉末压模制造过程中,模具的结构设计不合理可能导致产品成型瑕疵,比如出现裂纹、扭曲等问题。
为了避免这些问题的发生,应该根据产品的具体要求,合理设计模具结构,确保产品的成型质量。
第四个常见问题是模具加工精度不高。
模具加工精度的高低直接影响到产品的尺寸精度和形状精度。
在硬质合金粉末压模制造过程中,如果模具加工精度不高,将会导致产品的尺寸偏差过大,形状精度下降。
为了提高模具加工精度,可以采取以下对策:选用加工设备和工具要求精度高;制定严格的加工工艺规范,确保每个加工环节的准确性;进行工装夹具的检测和校验,确保模具加工的准确性。
在硬质合金粉末压模设计制造过程中,常见的问题包括粉末堆积、模具磨损、模具结构不合理和模具加工精度不高等。
针对这些问题,可以采取一些对策,如设计合理的模具结构、选择耐磨性好的模具材料、定期进行模具维护保养以及严格控制模具加工工艺等。
这样可以有效地解决这些问题,提高硬质合金粉末压模制造的生产效率和产品质量。
硬质合金压制过程中的几个基本知识点

压制过程中的几个基本知识点1、压制过程中粉末的位移与变形1.1 位移粉末装填在刚性模具中时,由于表面不规则,以及相互间的摩擦,颗粒间相互搭架而形成拱桥孔洞的现象叫做“拱桥效应”。
当施加压力时,拱桥效应被破坏,粉末受到压力的作用而发生相对的位移,其位移情况如下图。
1.2 变形粉末在发生位移的同时也发生着变形,变形主要有弹性变形、塑性变形和脆性断裂,基本情况图下图。
2、单位压制压力计算单位压制压力=总压制压力/产品的受压面积,以硬质合金的B型(20mm×6.5mm×5.25mm)试样为例:注:①单位为KN/mm2;②收缩系数以1.2为例,不同的粉末取不同的收缩系数值;③通常情况下,收缩系数随着压制压力的增加而下降,增加压制单重亦可使得收缩系数的下降。
图压制压力与压坯密度的关系3、弹性后效粉末冶金类产品在去除压制压力,将压坯脱模以后,由于弹性内应力的松弛作用而引起压坯体积膨胀的现象,称之为弹性后效,其定量的表示式如下:%100001⨯-=L L L δ 式中:δ——压坯高度或直径方向的弹性后效值;L0——压坯脱模前的高度或直径;L1——压坯脱模后的高度或直径。
一般来说,高度方向上的弹性后效要比直径方向上的大得多(即弹性后效具有明显的方向性),脱模的一瞬间是弹性后效最为显著的时刻,是压坯最容易出现分层、裂纹的时刻。
弹性后效是导致压坯出现分层、裂纹废品的主要原因。
其影响因素有以下几点。
① 混合料成分的影响:硬度高的粉末在压制时所产生的弹性后效大,弹性后效值随着粉末的硬度提高而提高。
WC-Co 合金混合料的弹性后效值一般比WC-TiC-Co 合金混合料的低。
高钴合金混合料的弹性后效值比低钴混合料的低,粉末氧化物和杂质含量高也会使得弹性后效值提高。
② 粉末物理性能的影响:粉末粒度细,颗粒粗糙程度降低,颗粒间结合强度降低,会增加压坯的弹性后效。
混合料的料粒干燥过度变硬时,也会使得弹性后效增加。
- 1、下载文档前请自行甄别文档内容的完整性,平台不提供额外的编辑、内容补充、找答案等附加服务。
- 2、"仅部分预览"的文档,不可在线预览部分如存在完整性等问题,可反馈申请退款(可完整预览的文档不适用该条件!)。
- 3、如文档侵犯您的权益,请联系客服反馈,我们会尽快为您处理(人工客服工作时间:9:00-18:30)。
硬 质合 金 挤 压 产 品变 形 因 素 的探 讨
蠢 明 友
( 昌硬质 台金厂 ) 南
本 文 从 挤 压 法 的生 产 实 际 出 发 , 对 工 艺 ,操 作 、 环 境 方面 影 响挤 压 产 品变 形 的主 要 因素 进 行 了讨论 。
一
c d 示 。 由 图 l 见 。 ① 当 碳 含 量在 5 8 、 所 可 .5
大而增 大。挤压速度控制 不均匀会使压坯 的
密 度 不 一, 烧 结 时 收 缩 量 不 同。 导 致 产 品 变 形 。 而 装 舟 不 当 和牯 舟会 使 制 品 出 现 凹 凸 不
平。
试验 结果表 明。各 种因素对 于制 品变形 量 的影 响不 同, 碳 含 量和 氧含 量 的 影 响 比较 明显・ 次是装舟 不当程度 、 其 成形 液加入量、 挤压 速度控制 的不 均匀程度,室温 和干燥 时
程 1 r m; 冲程 数I a 3 / n}驱动 电 机 功率 }1 k 8 a 6  ̄ 0 mi W 1 ’
联 系人 t孙 鲴周 }地址 比 阳 东北 工 学院 材料 系 ; 电话 t 9 7 4 3 0 . 3 3 0 - 2 3 } 电报挂 号 } 3 l 4 — 2 6 9 00 57
的某一部位与舟皿 粘在一起 在 收缩过程 中
造成制 品拉弯变形。为 了防止制 品发生碳的.
变 化 和 牯 舟 , 烧 结 体 的装 舟 , 通 常采 用事 先 在 舟 皿 上 与制 品接 触 部 位 涂 一 层 既可 以 防 止
・
信息・
5 T全 自动 册 束 冶金 压 机 正 在 进 行 国 产 化 O
预烧 阶段 因需排 除成 形剂,烧绪体会发 生一
定 量 的收 缩 , 制 品 间 因 产生 不 同 的 收缩 应力 而 出 现不 同程 度 的 变 形 。 在 真 空烧 结 过 程 中, 制 品装 在 石 墨舟 上 , 制 品 与 舟 皿接 触 部 位 含 碳量 往 往 比 其 它部 位 高 , 产生 局 部 渗 碳 , 引起 收缩 不 均 。 还 会 因硬 质 台 金 中钴 的 蒸 发 ,在 石 墨 舟 皿 上 形 成 绕 瘤, 蝴 者 使 制 品
2 6 邮政 编码 ; 10 0 18 1C 6 : 、
提高高 薯度册末冶金零件可 机加工 性的新方法
加拿大Qu b e e e金属粉末公 使用氮化硼改善了耕 末 金零件的可机加工性。在 ATOME T铁粉 中添
加 少于 0 1 嘶的氮 化 硼颗 粒 ,得 蓟 " .wt TATOM ET2 M 及ATOMET2 M 两 种 粉 末 . 以ATOMET2 M 茸 9 9
、
壹 形 因 素与 壹 形 结 果
试 样 成 分 为 w c一 6 %Co 经 真 空烧 结 。
丽 成 。 尺 寸为 3 5×6 。 . 0
试 样 的含 碳 量 、 含 氧 量 , 干燥 时 间及 成
形液 加 入量 对于变形量 的影响如 图 1 、b a 、
}/ I /l
h 7 5.8 5. 5 5 95
~
5 9 时 。 变 形 量 较 小 , 当碳 含 量 小 于 或 .5
大于该范 围时变形量都较 太I@ 随氧含 量的 升高。变形量 增大J⑧ 随干燥时 间的延 长和 成 形液加入量 的增加。变 形量增大。另 外。 由于碳含 量过 高或 过低 以及氧含 量过高所 } 【 起 的变形呈 S ・千燥 时间过长以及成形液 形 加入 量过大所 引起的变形呈 拱形。
C . %
4 - )
b )
c )
d )
田 1 壤 含■ 、l含 ■ 、干曩 时问豆 成 形液 加^ 量 对 于捌量 变形■ 的髟 响
d b c d 特蜊 l 碳 古量 ,氧古 量 .干燥 时问与 戚形 浪加^ 量对 于制 品 变形 量的 影响 )、 ), ), ) 为
挤压 时室温对于制 品变形 量也 有不可忽
为 侧 ,其与 ATOME 9 T ̄ 相比 ,前 者可钻 孔 14 . 4个 后者 仅钻 孔 5个 . 机 加工 性大 大 提 高 此 种方 法适 用于 6 可
需 要 机 加工 的 高强 度 粉 末冶 金零 件 .优于 常 用的 硫 和M n 添 加剂 S 。 ’
( 庆辰译自 Mea o d rR p r。19 4( ) ~16 郭 tlP l e e o t 90 5 3 }l e 83
视 的 影 响 。 将 室 温 控 制在 2 ' 右 较 好 。 过 0C左 :
二、 生形 盈素 讨 论
1 工 艺 冯 案 .
高过低都 会导 致制 品变 形, 中部拱起。或左
右 弓弯 。
在硬质 台金曲生 产中 ・ 、 碳 氧含量 的控 制 是 生 产工 艺 过 程 中的 重 要 环 节 。 无 论 是 原 料
3 环 境 因素 .
主 要 是 讨 论 室 温 的影 响 。 掺 有 成 形 液 的 泥 团料 , 成 形 液 中 的某 些 成 分容 易 自然 挥 发 出来 , 压 墉 口和 压坯 暴 露 于 空气 中, 室 温 的 过 高 或 过低 影 响 挤 压 压 力 和 挤 压 速度 的均 匀 性 , 引 起 压 坯 的 密 度不 均 。 室 温 过高 ,成 形 液 粘 度 低 , 挤 压 压力 也 降 低 , 压 坯 膨 胀 , 挤 压 速 度 减 慢 , 与 接坯 速 度 不 一 致 , 给 压 坯 密 度 的控 制 带 来 不 利 。 压 坯 在 自然 干 燥 过 程
中还 是 由成 形 剂 ,保 护 气 体 等 带 入 的碳 和 氧
另 外, 制 品 的 变 形 量 随挤 压 速 度控 制 的 不 均 匀程 度 , 装舟 不 当 程 度 和 粘 舟 程 度前 增
都会改 变半成 品的碳 , 氧含 量 。 从而影 响制 品
的外 形 质 量 。 最理 想 的 合金 制 品 是 希 望 既无 游离 碳 相 也 无 缺 碳 柑 。 由 于 各 种 因素 所 造 成 的 碳量 增 加 ,使 碳 鲥 过 剩 量 增 l 并 聚 集 在 一 起, 导 致 拥 制 品 的 某 个 部 位 成 为 高 碳 区域 。 造 成 烧 结 ,
f。 H j
凝 固时该部位碳 的析 出,则该部位 的体积 收 缩 不 完 垒 , 形 成 局 部 凸起 。 另 外 , 当 合金 原
料 中混 入 了过 多 的氧 , 加 半 成 品 在 预 烧 过
程 中局部吸 收 了较多 的氧。 在烧 结时就会使
No
实 践 经 验
氧 罱 高 的局 部 损 碳 最 更 大 , 致 使 制 品 出现 局
粘 舟 又 能 保 持 碳 稳 定 的 物 质 , 以 减少 制 品 变
形。
部 缺 碳 , 泼部 位 出现 液 相 的 温 度 会 更 高 , 液 相 量 会 更 少 , 体 积 收 缩就 会 不 完 全 , 从 而 出 现局 部体 积 过 大 。
成 形 液 的过 量 加 入 , 过稀 挤 出来 的 料 使
2 操 作 因 素 .
挤 压 速 度 均 匀 程 度 的 影响 已如 前 述 。 硬 质 合 金 管 、 棒 、 带 材 的烧 结 装舟 。在
中, 成形液挥发快, 收缩 也加 快,使压坯产
生弯 曲 现 象 , 烧 结 过 程 中 难 以 矫 正 。 室 温 过 低 , 掺 有 成 形掖 的料 冷 凝 变 硬 , 需 要 更 大 的 挤 压 压 力 ,在 固 定 的 机 械 控 速 下 , 产生 拉 应 力 , 使 压 坯 密 度不 均而 变 形 。 另 外 , 压 坯 在 自然 干 燥 过 程 中, 由 于 压 坯 变 硬 , 成 形 液 的 挥 发 在 横 向与 纵 向不 能 同 步 进 行 , 两 端 比 中 部 挥 发快 ,使 之 收 缩 更 加不 均 , 导 致变 形 。 另 外 , 中 间 品 的所 有 转 移 过 程 都 是 在 空 气 中进行 ,特 别 是 预 烧 后 的 半 成 品, 若 空气 的湿 度 过 大, 会 吸 收较 多 的 水 份 , 增 加 含 氧 量 , 而 且 两端 要 比 中 间 部位 的 吸 氧 量 多 , 造 成 烧 结 过 程 中 的收 缩 不 均 匀 而 使 制 品变 形 。
压 坯 容 易 产 生 流 动变 形 } 成 形 液 的 挥 发 , 形 成 收 缩 应 力 , 使 压 坯 形 状 改变 。 另 外 , 在 空 气 中 干燥 的 压 坯 , 压 坯 随 之吸 收 氧 份 , 特 别 是 在 湿 度 大 的 季 节 里 更 加 明 显 ,使 在 烧 结 中 产 生 局 部 失 碳 , 导 致 制 品 变形 。
5 T垒 自动 籽末 冶 金压 机 ,由东 北 工 学 院孙 绍周 副教 授 负 责立 项 . 德国 DoR T公 司 sT垒 自 粉 o S o 动
末 冶金压 机 为样 机 进 行 仿制 , 现已 掌握 其技 术 关键 .正在 进 行 l 产工 作 .该 压机 的 技术数 据为 投 最 大压 制压 力 }6 t 0 =最大 脱模 力 。3 t 0 ;最 大 回 程力 ,3 2 } 上 冲头 冲程 2 0 m) 上 冲 头位 置调 整 .t 0r a 范 围 2 0 2 mm; 最大 装料 高度 } l 5  ̄ mm} 最 大压 制行 程 }9 r mI 最大 脱 模 行程 } 9 t m}最大 顶 压行 5 a 0i l