复杂硫化铜精矿微波活化预处理-加压浸出工艺
复杂硫化钴矿加压浸出工艺研究

1 3 试 验原 理 . 根据 原 矿组 成 , 加压 浸 出试 验过 程 主 要进 行 下
列反 应 : C As + 1 / O + 3 2 0一 C S 4 H3 O o S 3 4 2 / H2 o O + As 4
・
2・
有色 金属 ( 炼部分 ) 2 1 冶 0 0年 1期
复 杂 硫 化 钴 矿 加 压 浸 出工 艺研 究
黄 胜 ,张磊 ,王海 北 , 亚平 冯
( 北京矿 冶研 究总院 , 北京 1 0 4 ) 0 0 4
摘要 : 用 低 温 低 压 浸 出技 术 对 复 杂 硫 化 钻 进 行 研 究 。结 果 表 明 , 低 温 低 压 下 , 复 杂 硫 化 钴 中钴 的 采 在 该 浸 出 率 大 于 9 , 镍 的 浸 出 率 大 于 9 , 和砷 形 成 稳 定 的砷 酸铁 进 入 浸 出 渣 。 2 铜 O 铁
Ke wo d : mp e o a ts l h d r ;P e s r e c i g y r s Co l x c b l u p i e o e r s u ela hn
我 国钴 资 源 的主要特 点是 贫矿 多 、 富矿 少 , 少 缺
上小 于 0 0 4mm。试 验 所用 试 剂 如硫 酸 等 均 为分 . 7
关键 词 : 杂 硫 化 钴 矿 .日 浸 出 复 力压 中图分类号 : 86 TF 1 文献标识码 : A 文 章 编 号 :0 7 5 52 1 ) l 0 0 — 0 1 0 ~7 4 (0 0 O 一 0 2 3
Re e r ph d e s a c n t e s r a hi fCo lx Co a tS l i e Or
难浸硫化金矿的微生物氧化预处理
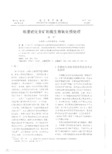
单易 行 、 成 本低 、 能耗 小 且 污 染 少 等特 点倍 受
人们 的关注 。 世纪 年代中期 , 使用氧化铁
硫 杆菌从 难选金矿 石 中获取 的高回收率 , 从而
引起 了在南 非 、 澳 大利 亚和 美 国 些地方 建起
了工 厂 , 这 些 丁 厂 大 部分取 得 了成 功 。 生 物技
术在矿物丁 程 中的应 用主 要 有 以下 个方 面
冶 金矿 资源 , 已成 为我 国黄金 工 业 发展 的一 条
原态转化 为氧化 态 , 破坏 包 裹金 的硫化矿 品格 ,
使金从 载 体布’一 物 中暴露 出 来 ,
一
刁能用 氰化法 有
效地 加 以回收 。 这种在氰化浸金前将载金矿物
氧化分解 以提 高金 暴露程度 的方法 , 称 为氧化 预处理 ‘ , 。 在生物预处理过程中, 有害组分易
于集 中处理 , 不会流 失扩散而污染环境 。
密
切相关 , 因此 , 这种作用机理称 为微 生物 的间
接作用机理 。 必 须指 出的是 , 上 述在分析硫 化
金矿微 生物氧化机理 时 , 把微生物 的直接作用
和 间接作用 分开 讨论 只 是 为 了更清楚地 说 明 问
题 , 而 在 实 际处 理刁、‘ 物 时 , 微 生物 的直接作用
和 间接作用 是 同时存 在的 , 二 者均有助 于溶解
界及 品体缺陷部位不 断地氧 化载金矿物 , 以获得
自身新陈代谢所需的能量 。
一
结 果 导致矿物 品格严
重破坏 , 矿粒形成 多孔状 , 金被 暴露 出来 。 因此 ,
微生物在难浸硫化金矿氧化预 处 理 过 程 中的作
用 , 就是它们对金属硫化矿 氧化浸 出的作用 。 包
化学—生物联合浸出次生硫化铜精矿的研究
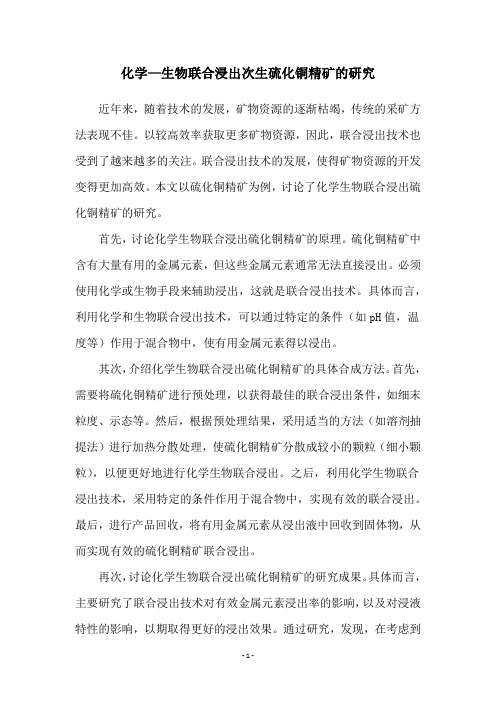
化学—生物联合浸出次生硫化铜精矿的研究近年来,随着技术的发展,矿物资源的逐渐枯竭,传统的采矿方法表现不佳。
以较高效率获取更多矿物资源,因此,联合浸出技术也受到了越来越多的关注。
联合浸出技术的发展,使得矿物资源的开发变得更加高效。
本文以硫化铜精矿为例,讨论了化学生物联合浸出硫化铜精矿的研究。
首先,讨论化学生物联合浸出硫化铜精矿的原理。
硫化铜精矿中含有大量有用的金属元素,但这些金属元素通常无法直接浸出。
必须使用化学或生物手段来辅助浸出,这就是联合浸出技术。
具体而言,利用化学和生物联合浸出技术,可以通过特定的条件(如pH值,温度等)作用于混合物中,使有用金属元素得以浸出。
其次,介绍化学生物联合浸出硫化铜精矿的具体合成方法。
首先,需要将硫化铜精矿进行预处理,以获得最佳的联合浸出条件,如细末粒度、示态等。
然后,根据预处理结果,采用适当的方法(如溶剂抽提法)进行加热分散处理,使硫化铜精矿分散成较小的颗粒(细小颗粒),以便更好地进行化学生物联合浸出。
之后,利用化学生物联合浸出技术,采用特定的条件作用于混合物中,实现有效的联合浸出。
最后,进行产品回收,将有用金属元素从浸出液中回收到固体物,从而实现有效的硫化铜精矿联合浸出。
再次,讨论化学生物联合浸出硫化铜精矿的研究成果。
具体而言,主要研究了联合浸出技术对有效金属元素浸出率的影响,以及对浸液特性的影响,以期取得更好的浸出效果。
通过研究,发现,在考虑到矿物资源本身特性的情况下,联合浸出技术可以有效地提高有效金属元素的浸出率和浸出质量,甚至有可能消除浸液中的杂质和污染物,从而改善浸出过程的效率和质量。
最后,总结了化学生物联合浸出硫化铜精矿的研究现状和前景。
随着科技的发展,化学生物联合浸出技术已成为采矿领域的一种重要技术,可以有效提高有效金属元素的浸出率,消除浸液中的杂质和污染物,并降低破坏损失。
因此,未来化学生物联合浸出技术有望实现工业应用,为矿物资源的开发带来更多的收益。
铜钴渣氧压酸浸提取铜钴试验研究
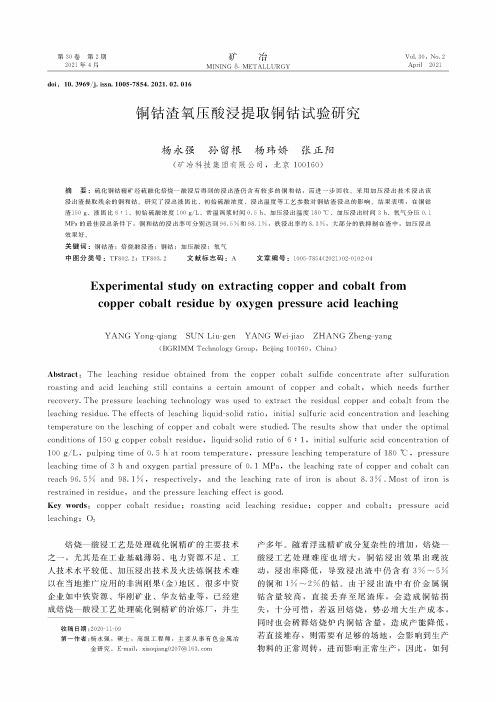
矿 冶MINING * METALLURGY第30卷第2期2021年4月Vol. 30 , No. 2April 2021doi : 10. 3969/j. issn. 1005/854. 2021. 02. 016铜钻渣氧压酸浸提取铜钻试验研究杨永强 孙留根杨玮娇张正阳(矿冶科技集团有限公司,北京100160)摘 要:硫化铜钻精矿经硫酸化焙烧一酸浸后得到的浸出渣仍含有较多的铜和钻,需进一步回收$采用加压浸出技术浸出该浸出渣提取残余的铜和钻。
研究了浸出液固比、初始硫酸浓度、浸出温度等工艺参数对铜钻渣浸出的影响$结果表明,在铜钻 渣150 g 、液固比6 : 1+初始硫酸浓度100 g/L 、常温调浆时间0.5 h 、加压浸出温度180 m 、加压浸出时间3 h 、氧气分压0. 1MPa 的最佳浸出条件下,铜和钻的浸出率可分别达到96.5%和98.1%,铁浸出率约8.3% ,大部分的铁抑制在渣中,加压浸出效果好$关键词:铜钻渣&焙烧酸浸渣&铜钻&加压酸浸&氧气中图分类号:TF802. 2& TF803. 2文献标志码:A文章编号:1005-7854(2021)02-0102-04Experimental study on extracting copper and cobalt from copper cobalt residue by oxygen pressure acid leachingYANG Yong-qiang SUN Liu-gen YANG Wei-jiao ZHANG Zheng-yang(BGRIMM TechnologyGroup ,Beijing100160,China 0Abstract : The leaching residue obtained from the copper cobatt sulfide concentrate after sulfurationroasting and acid leaching still contains a certain amount of copper and cobalt , which needs furtherrecovery.Thepressureleachingtechnology was used to extract the residual copper and cobalt from the leachingresidue.Thee f ectsofleachingliquid-solidratio ,initialsulfuricacidconcentrationandleachingtemperature on the leaching of copper and cobalt were studied. The results show that under the optimalconditionsof150gcoppercobaltresidue ,liquid-solidratioof6j1,initialsulfuricacidconcentrationof 100 g/L , pulping time of 0. 5 h at room temperature , pressure leaching temperature of 180 °C , pressureleachingtimeof3handoxygenpartialpressureof0.1 MPa !theleachingrateofcopperandcobaltcan reach 96.5% and 98. 1 % , respectively , and the leaching rate of iron is about 8.3%. Most of iron is restra8ned8nres8due !andthepressureleach8nge f ect8sgood.Key words :copper cobatt residue ; roasting acid leaching residue ; copper and cobalt ; pressure acidleaching &O 2焙烧一酸浸工艺是处理硫化铜精矿的主要技术 之一,尤其是在工业基础薄弱、电力资源不足、工人技术水平较低、加压浸出技术及火法炼铜技术难 以在当地推广应用的非洲刚果(金)地区。
刚果(金)硫化钴铜矿热活化—硫酸浸出工艺研究

消费电子产品的普及和新能源汽车产业链的迅
猛发展,促使 素成为了一种战略性 。中国
为钻消 国,9
,6
量
。随着
开采的不断,高品位、易
处理 为了
的日益减少,难处理硫化钻矿成 的热点7「2]。
前,硫 生产冰铜或
的处理工艺主要有:硫化熔炼 合金等中间品3]9 —浸
*收稿日期:206-03-6
基金项目:广东省扬帆 作者简介:张晨(677-),男,汉族,2 通信作者:黄亚祥(690-),男,6
第2 " 2012 年 8 月
矿"保护与利用
CONSERVATION AND UTILIZATION OF MINERAL RESOURCES
Nq.4 Aup. 2212
冶金工程
刚果(金)硫化钻铜矿热活化一硫酸浸出工艺研究
张晨,文定强,黄亚祥
(广东佳纳能源科技有限公司,广东清远513056 )
摘要:针对刚果(金)硫化钻铜精矿矿物组成复杂、直接酸浸效果较差等物料特性,研究了热活化-硫酸浸
和铜的高效回收利用。
关键词:硫
;
; ;硫酸;浸出
中图分类号:TD252. OTD254 文献标识码:A 文章编号:1006 - 0076(206 ) 04 - 064 - 04
DO): 10. 2772// e化0 铁U006 -0077.7412.04.042
Research on Thermal Activation Pretreatment and Sulfuric Acid Leaching of Cobalt - Copper Sulfide Conceatrctee from Congo (Kioshase)
工艺。其中,硫
微波活化铜精矿加压浸出动力学

第 2卷 第 2期
20 1 1年 4 月
有r o s Me a s c e c a d n i e r g neru tl S in e n E gn e n i
Vo. ,No2 1 2 .
AD . l r 20l
文章编号 :64 9 6 (0 0 —0 9 0 17 — 69 2 1)2 0 1— 5 1
略有 增 大. 当温度 低 于 4 3K 时 , 浸 出速 率较 微 波 活化前 略 有增 大 ; 2 锌 当温度 高 于 4 8K 时 , 浸 出过 3 锌 程反 而略 有放 缓 . 波活 化铜 精 矿 铜 、 浸 出反 应 的表 观 活化 能 分 别 为 5. 、9 7k/ l铜 、 浸 微 锌 6 3 4. Jmo, 锌 3 7
c mp r d wi h t f h r t ae o c n r t h l wi g c n i o s t e l a h n mp r t r sf m 0 o ae t t a e p e r td c n e tae i t e f l n o d t n : h e c i g t h o t e n o o i e e a u e i r 4 8 K o
微波活化铜精矿加压浸出动力学
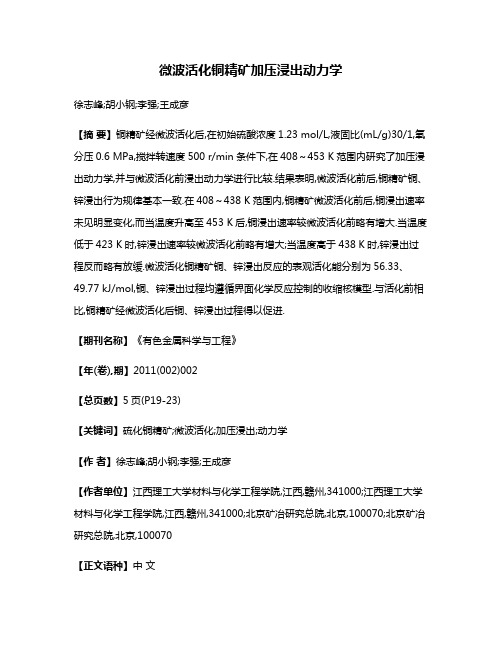
微波活化铜精矿加压浸出动力学徐志峰;胡小钢;李强;王成彦【摘要】铜精矿经微波活化后,在初始硫酸浓度1.23 mol/L,液固比(mL/g)30/1,氧分压0.6 MPa,搅拌转速度500 r/min条件下,在408~453 K范围内研究了加压浸出动力学,并与微波活化前浸出动力学进行比较.结果表明,微波活化前后,铜精矿铜、锌浸出行为规律基本一致.在408~438 K范围内,铜精矿微波活化前后,铜浸出速率未见明显变化,而当温度升高至453 K后,铜浸出速率较微波活化前略有增大.当温度低于423 K时,锌浸出速率较微波活化前略有增大;当温度高于438 K时,锌浸出过程反而略有放缓.微波活化铜精矿铜、锌浸出反应的表观活化能分别为56.33、49.77 kJ/mol,铜、锌浸出过程均遵循界面化学反应控制的收缩核模型.与活化前相比,铜精矿经微波活化后铜、锌浸出过程得以促进.【期刊名称】《有色金属科学与工程》【年(卷),期】2011(002)002【总页数】5页(P19-23)【关键词】硫化铜精矿;微波活化;加压浸出;动力学【作者】徐志峰;胡小钢;李强;王成彦【作者单位】江西理工大学材料与化学工程学院,江西,赣州,341000;江西理工大学材料与化学工程学院,江西,赣州,341000;北京矿冶研究总院,北京,100070;北京矿冶研究总院,北京,100070【正文语种】中文【中图分类】TF811;TF803.21加压浸出是一种清洁的湿法冶金新技术,具有浸取高效、流程短、无污染等优点[1],在复杂硫化铜矿浸出方面具有广阔的应用前景[2-4].但复杂硫化铜矿在硫酸浸出过程中易“钝化”[5],受该问题局限,复杂硫化铜矿加压浸出目前仅停留在实验室研究阶段.为克服矿石浸出“钝化”问题,可以采用微波预处理方法[6-9].当微波快速加热矿物时,由于微波穿过金属矿物产生很大的热应力,致使矿物边缘出现微小裂缝[10],这有可能是使矿物活性增强的原因之一.另外,在微波场中,大多数硫化矿(如黄铁矿、黄铜矿等)都能吸收微波能[11].物质吸收微波后,其晶体结构、表面性质等有可能发生显著改变[12],如黄铁矿在一定条件下经微波处理后会转变成磁黄铁矿[13].实践证明,经微波活化,原本难以浸出的铜精矿在中等温度(453 K)条件下即可顺利浸出[14].为进一步完善微波活化铜精矿加压浸出工艺,加强浸出行为及浸出过程研究是非常必要的.本文即以微波活化铜精矿为研究对象,探讨微波活化铜精矿在408~453 K 温度范围内加压浸出动力学,进而分析铜、锌浸出过程的动力学控制因素.1.1 原料与仪器实验所用铜精矿XRD谱图见图1.由图1可知,铜精矿中主要的金属矿物有闪锌矿、黄铜矿、黝铜矿、黄铁矿、方铅矿.铜精矿粒度为-44 μm占99.7%.铜精矿在微波功率82 W、每批处理量95 g条件下辐照时间120 s,过程中未见铅、锌、硫、砷的挥发损失,微波活化前后铜精矿主要元素成分见表1.硫酸及其他化学试剂均为分析纯.微波活化铜精矿加压浸出过程中通入工业纯氧.主要实验仪器:G70D20ASP-DF型微波炉(广东格兰仕微波炉电器有限公司),额定微波频率2450 MHz,额定输出功率700 W;CJF-T型高压釜(大连通达反应釜厂),内容积1.0 L.1.2 实验过程铜精矿经微波活化预处理后按一定液固比与浸出剂混合加入高压釜的钛胆中.高压釜加盖密封,通过控制箱设定加热温度.升温至设定温度时,向高压釜内通入工业纯氧并开始计时.浸出结束后通水冷却,待釜内压力降为0后开启高压釜,分别将浸出液和浸出渣送样分析.铜、锌浸出率计算均按渣计.为保证各实验点间具有可比性,控制每次实验时高压釜升温速率及降温速率相同. 为使浸出过程中,反应物(即硫酸)浓度保持相对恒定,在微波活化铜精矿加压浸出动力学实验中,选取了相对偏高的初始硫酸浓度(1.23 mol/L)以及较大的液固比(mL/g)30/1.基于大量实验可知,当搅拌转速达到500 r/min以上时,可以保证1.0 L釜内气、液、固三相充分混合和氧的传质,故在各次实验中控制搅拌转速恒定为500 r/min.本研究未考虑氧分压对微波活化铜精矿加压浸出动力学的影响,各次实验氧分压恒定为0.6 MPa.2.1 铜的浸出速率在408~453 K温度范围内,铜浸出率随浸出时间变化关系如图2所示.图2中直线为铜浸出率在一定浸出时间范围内的拟合直线.由图2可见,在铜浸出达到平衡之前,铜浸出率与浸出时间之间呈良好的直线关系,相关系数R≥0.99.进一步由图2可知,对于各浸出温度而言,在浸出达到平衡之前,铜浸出率随浸出时间延长而不断增大的规律是基本一致的.当浸出温度升高至453 K时,铜浸出达到平衡的时间缩短至150 min.与未经微波活化预处理的铜精矿加压浸出行为[15]比较可知,微波活化前后,铜浸出行为规律基本一致.铜精矿微波活化前后,铜浸出率对应浸出时间的拟合直线方程见表2.由表2可见,在408~438 K温度范围内,微波活化前后,铜浸出速率未见明显变化,当温度升高至453 K时,铜浸出速率较活化前略有增大.为保证铜的高效浸出,微波活化铜精矿浸出温度宜选择453 K.2.2 锌的浸出速率在408~453 K温度范围内,锌浸出率随浸出时间变化关系如图3所示.图3中直线为锌浸出率在一定浸出时间范围内的拟合直线.由图3可见,在锌浸出达到平衡之前,锌浸出率与浸出时间之间呈良好的直线关系,相关系数R≥0.98.进一步由图3可见,锌浸出率随浸出时间变化的规律同铜浸出.当温度升高至453 K时,锌浸出达到平衡的时间缩至120 min.相对于铜浸出而言,锌浸出更早达到平衡.与铜浸出类似,铜精矿微波活化前后锌浸出行为规律也基本一致.铜精矿微波活化前后,锌浸出率对应浸出时间的拟合直线方程见表3.由表3可见,微波活化前后,锌浸出速率随浸出温度的变化规律是相同的,即在408~438 K温度范围内,随浸出温度升高,锌浸出速率不断增大;当浸出温度进一步升高至453 K后,锌浸出速率不再明显变化.当浸出温度低于423 K时,锌浸出速率较活化前略有增大;而当浸出温度高于438 K后,虽然锌浸出率高于微波活化前,但锌浸出过程反而略有放缓.进一步比较表2、表3结果可知,在408~438 K温度范围内,锌浸出速率始终高于铜浸出速率,锌浸出优先于铜;而当温度进一步升高至453 K后,铜浸出得以明显促进,铜浸出优先于锌.上述规律同精矿微波活化前.2.3 浸出过程控制性步骤在铜精矿各金属硫化矿氧压酸浸过程中,将有单质硫固体产物生成,浸出总反应式如下:因此,反应式(1)可以用收缩核未反应模型来描述,该模型同样适用于微波活化铜精矿.浸出控制步骤可分为液体边界层扩散控制、界面化学反应控制、固体产物层扩散控制[16].在加压浸出条件下,因搅拌在气泡的作用下被强化,所以浸出速率可不受液体边界层扩散控制.经计算可知,在408~453 K温度范围内,对于微波活化铜精矿铜、锌浸出而言,只有界面化学反应控制的动力学曲线才呈现良好的线性关系,结果如图4、图5所示.1-(1-t)1/3~t之间拟合所得线性回归方程分别见表4和表5.进一步由表4、表5所示的铜、锌浸出表观速率常数(k)求得对应不同浸出温度的lnk(如表6、表7所示).进一步以lnk对1/T作图,如图6、图7所示,无论对于铜还是锌浸出而言,lnk与1/T之间均呈良好的线性关系(相关系数R≥0.97).对于铜浸出而言,所得直线斜率为-6798.88;对于锌浸出而言,所得直线斜率为-5985.74.根据阿仑尼乌斯(Arrhenius)公式,可求解浸出反应的活化能:对于铜浸出而言:对于锌浸出而言:计算所得表观活化能均处于40~300 kJ/mol范围内,由此可见,微波活化铜精矿加压浸出过程的确受界面化学反应控制,浸出控制步骤同微波活化前.铜、锌浸出反应表观活化能较微波活化前有明显降低,这说明,铜精矿经微波活化后铜、锌浸出过程得以促进.(1)在408~453 K范围内,在铜、锌浸出达到平衡之前,浸出率与浸出时间呈良好的线性关系.微波活化前后,铜精矿铜、锌浸出行为规律基本一致.(2)在408~438 K温度范围内,铜精矿微波活化前后,铜浸出速率未见明显变化,当温度升高至453 K后,铜浸出速率较活化前略有增大.当温度低于423 K时,锌浸出速率较活化前略有增大;当温度高于438 K时,锌浸出过程反而略有放缓.为保证铜的高效浸出,微波活化铜精矿浸出温度宜选择453 K.(3)在408~438 K温度范围内,锌浸出速率始终高于铜,锌浸出优先于铜;而当温度进一步升高至453 K后,铜浸出优先于锌.上述规律同精矿微波活化前一致. (4)在408~453 K范围内,微波活化铜精矿铜、锌浸出反应表观活化能分别为56.33 kJ/mol和49.77 kJ/mol,铜、锌浸出过程受界面化学反应控制,浸出控制步骤同微波活化前.经微波活化后铜精矿铜、锌浸出过程得以促进.【相关文献】[1]邱定蕃.加压湿法冶金过程化学与工业实践[J].矿冶,1994,3(4)∶55-67.[2]Habashi F.Pressure Hydrometallurgy/Past,Present and Future[C]// YangXianwan.Proceedings of the Third International Conference onHydrometallurgy’98.Kunming,China:InternationalAcademicPublishers, 1998∶27-34. [3]王海北,蒋开喜,邱定蕃,等.国内外硫化铜矿湿法冶金发展现状[J].有色金属,2003,55(4)∶101-104.[4]郭亚惠.铜湿法冶金现状及未来发展方向[J].中国有色冶金,2006,(4)∶1-13.[5]Hackl R P,Dreisinger D B,Peters E,et al.Passivation of Chalcopyrite during Oxidative Leaching in Sulfate Media[J].Hydrometallurgy,1995, 39(1-3)∶25-48.[6]Jacobs I S,Zavitsnos P D.Microwave Handling of Mineral[J].J ApplPhys,1982,53(3)∶2730-2735.[7]张文朴.微波在稀贵金属冶金中的应用研究进展[J].稀有金属与硬质合金,2008,36(2)∶49-53.[8]Hall S T,Finch J A.New Use of Microwave[J].Miner Metall Process,1984,(11)∶179-183.[9]Standish N,Worner H.Microwave Handling of Iron Ore Powder[J]. Microwave Power and Electromagnetic Energy,1990,25(3)∶177-180.[10]Haque K E.Microwave Energy for Mineral Treatment Process A Brief Review[J].Int J Miner Process,1999,57(1):1-24.[11]Chen T T.The Relative Transparency of Minerals to Microwave Radiation[J].Can Metall Q,1984,23(1)∶349-351.[12]段爱红.晶体结构缺陷结构与物质吸收微波的能力[J].云南师范大学学报,1998,18(3):89-91.[13]崔礼生,韩跃新.微波技术在选矿中的应用[J].金属矿山,2006,(4):29-32.[14]徐志峰,李强,王成彦.复杂硫化铜精矿微波活化预处理-加压浸出工艺[J].过程工程学报,2010,10(2):256-262.[15]徐志峰,严康,李强,等.复杂硫化铜精矿加压浸出动力学[J].有色金属,2010,62(4),76-81,114.[16]华一新.冶金过程动力学导论[M].北京:冶金工业出版社,2004∶28,188.。
复杂硫化铜精矿加压浸出动力学

摘 要 : 初 始 硫 酸 浓 度 12 mo L 液 固 比 ( / )0 1氧 分 压 0 6 a 搅 拌 转 速 度 5 0/ i 件 下 , 究 以 黝 铜 矿 为 主 在 .3 l , / mL g 3/ , . MP , 0 rr n条 a 研 要矿 物 的 硫 化 铜精 矿 在 4 8~ 5 K温 度 范 围 内加 压 浸 出 动力 学 。 结 果表 明 , 浸 出 达 到平 衡 之 前 , 、 、 浸 出 率 与 浸 出 时 间 呈 0 43 在 铜 锌 铁
醇 体 系 中黄 铜 矿 浸 出 过 程 动 力 学 , 果 表 明 浸 出 反 结
48 6 K温度 条件下 氧压浸 出辉铜 矿一 黄铁 矿 型铜 精
矿 ; hls D d ePae o e 浸 出 工 艺 在 温 度 P e og.lcr D m p
4 3 氧分 压 0 7 a条件 下 浸 出 黄铜 矿 精 矿 ; n 9 K、 . MP A—
矿在酸性 氯盐 介质 中的加压 浸 出动力学 , 结果发 现 , 在浸 出初 期及 后期铜 浸 出过 程分别 遵循 界面化学 反 应 控制 与 固膜 内扩散 控 制 。M D n l 人 系 统 c oad等
第6 2卷
o . 2,No 4 16 .
No . 2 0 l 0 v
20 10年 l 1月
N ne T I ea s o f IOI M tl 8
复杂 硫 化 铜精 矿加 压 浸 出动 力学
徐 志峰 严 康 李 强。 王 成 彦 , , ,
微波活化预处理对黄铜矿加压浸出的影响

doi:10.3969/j.issn.1007-7545.2019.010.001收稿日期:2019-07-04基金项目:国家自然科学基金资助项目(51574072,51434001)作者简介:路雨禾(1992-),女,辽宁沈阳人,博士研究生;通信作者:谢锋(1970-),男,辽宁沈阳人,博士,教授.微波活化预处理对黄铜矿加压浸出的影响路雨禾1,谢锋1,白云龙1,李超1,路殿坤1,王伟1,蒋开喜1,2(1.东北大学冶金学院,沈阳110004;2.北京矿冶科技集团有限公司,北京100160)摘要:研究微波活化预处理保温时间和温度对黄铜矿加压浸出的影响,并采用X射线衍射和扫描电子显微镜表征微波活化处理前后黄铜矿及其浸出渣的形貌。
结果表明,微波活化预处理保温时间越长,活化效果越好,最适宜的活化温度为100℃。
微波活化处理能导致部分Cu-Fe-S和Fe-S键的去稳定化,并能在黄铜矿表面生成局部细小的裂缝与孔洞,从而促进黄铜矿的浸出。
微波活化可以提高铜的浸出并且抑制铁的浸出。
关键词:黄铜矿;加压浸出;微波活化中图分类号:TF811 文献标志码:A 文章编号:1007-7545(2019)10-0001-05Effect of Microwave Activation Treatment on Pressure LeachingBehavior of ChalcopyriteLU Yu-he1,XIE Feng1,BAI Yun-long1,LI Chao1,LU Dian-kun1,WANG Wei 1,JIANG Kai-xi 1,2(1.School of Metallurgy,Northeastern University,Shenyang 110004,China;2.BGRIMM Technology Group,Beijing 100160,China)Abstract:Effects of microwave activation time and activation temperature on pressure leaching behavior ofchalcopyrite were investigated.Chalcopyrite and its leaching residue before and after microwave activationtreatment were characterized by XRD and SEM.The results show that activation effect is enhanced byelongation of activation time,and the optimum activation temperature is 100℃.Microwave activationtreatment can lead to de-stabilization of Cu-Fe-S and Fe-S bonds.Local fine cracks and holes can beformed on surface of chalcopyrite,thus promoting leaching of chalcopyrite.Microwave activationtreatment can improve copper leaching and inhibit iron leaching.Key words:chalcopyrite;pressure leaching;microwave activation 加压氧化浸出技术历史悠久,在有色金属冶金领域有很多应用,黄铜矿通过加压酸浸技术可降低耗氧量,缩短浸出周期,逐渐受到冶金行业的重视[1-4]。
硫化钴铜精矿加压氧浸研究
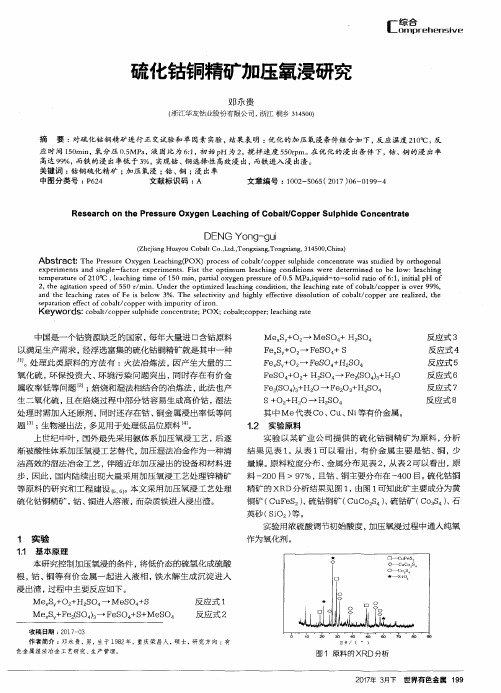
S +02 +H2 0_ ÷H 2 S O4
属 收率低 等问题 ; 焙烧和 湿法相结 合的冶炼 法 , 此法 也产
e x pe r i men t s a nd s i ng l e —f a c t or e x pe r i me nt s .F i s t t he op t i mu m l e a c h i ng c ond i t i ons we r e de t e r mi ne d t o be l ow :l e a c hi n g t e m pe r a t u r e o f21 0  ̄ ( 2,l e a c hi ng t i me of1 5 0 mi u, pa r t i a l o x yg e n pr e s s ur e of0. 5 M Pa , i q ui d—t o—s o l i d r a t i o o f6: 1 ,i ni t i a l pH of 2, t he a g i t a t i o n s pe e d o f 5 5 0 r / mi n.Und e r t h e o pt i mi z e d l e a c hi ng c o nd i t i o n,t he l e a c hi ng r a t e o f c ob a l t / c o pp e r i s o ve r 9 9%, a nd t he l e a c hi ng r a t e s o f Fe i s b e l ow 3%.Th e s e l e c t i v i t y a nd h i g h l y e fe c t i v e d i s s ol ut i o n of c o b a l t / c o p pe r a r e r e a l i z e d.t h e s e F ’ a r a t i o n e fe c t of c o ba l t / c o pp e r wi t h i m pu r i t y o f i r o n.
难处理低品位某铜镍硫化物矿物加压浸出工艺
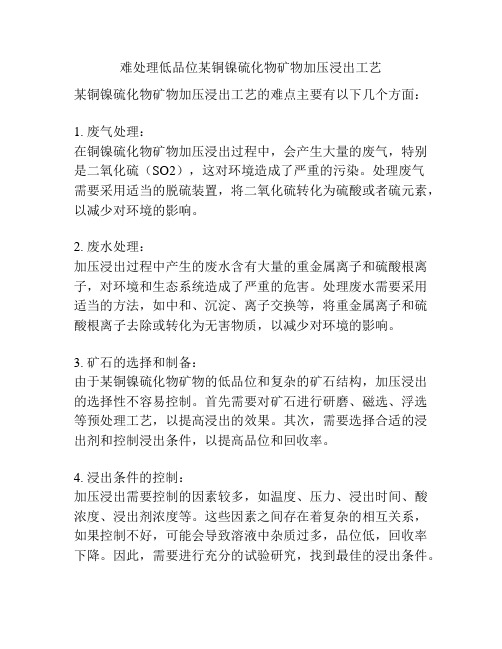
难处理低品位某铜镍硫化物矿物加压浸出工艺某铜镍硫化物矿物加压浸出工艺的难点主要有以下几个方面:1. 废气处理:在铜镍硫化物矿物加压浸出过程中,会产生大量的废气,特别是二氧化硫(SO2),这对环境造成了严重的污染。
处理废气需要采用适当的脱硫装置,将二氧化硫转化为硫酸或者硫元素,以减少对环境的影响。
2. 废水处理:加压浸出过程中产生的废水含有大量的重金属离子和硫酸根离子,对环境和生态系统造成了严重的危害。
处理废水需要采用适当的方法,如中和、沉淀、离子交换等,将重金属离子和硫酸根离子去除或转化为无害物质,以减少对环境的影响。
3. 矿石的选择和制备:由于某铜镍硫化物矿物的低品位和复杂的矿石结构,加压浸出的选择性不容易控制。
首先需要对矿石进行研磨、磁选、浮选等预处理工艺,以提高浸出的效果。
其次,需要选择合适的浸出剂和控制浸出条件,以提高品位和回收率。
4. 浸出条件的控制:加压浸出需要控制的因素较多,如温度、压力、浸出时间、酸浓度、浸出剂浓度等。
这些因素之间存在着复杂的相互关系,如果控制不好,可能会导致溶液中杂质过多,品位低,回收率下降。
因此,需要进行充分的试验研究,找到最佳的浸出条件。
5. 铜镍的分离和提纯:加压浸出后得到的溶液中含有大量的铜和镍离子,需要进行分离和提纯。
常用的方法包括溶剂萃取、离子交换、电积等。
这些方法不仅需要选择合适的分离剂和条件,还需要考虑到废液、废渣的处理和资源的利用。
总之,某铜镍硫化物矿物加压浸出工艺处理起来困难重重,需要克服废气、废水的处理问题,解决矿石选择和制备、浸出条件的控制等难题。
只有克服这些难点,才能实现高效、低污染的加压浸出工艺。
某铜镍硫化物矿物加压浸出工艺是一项复杂而困难的过程。
在这个过程中,我们需要面对的挑战包括废气处理、废水处理、矿石的选择和制备、浸出条件的控制和铜镍的分离和提纯等方面。
首先,废气处理是该工艺中的一个重要环节。
加压浸出过程中会产生大量的废气,其中主要是二氧化硫。
一种复杂难处理硫化矿的生物浸出研究
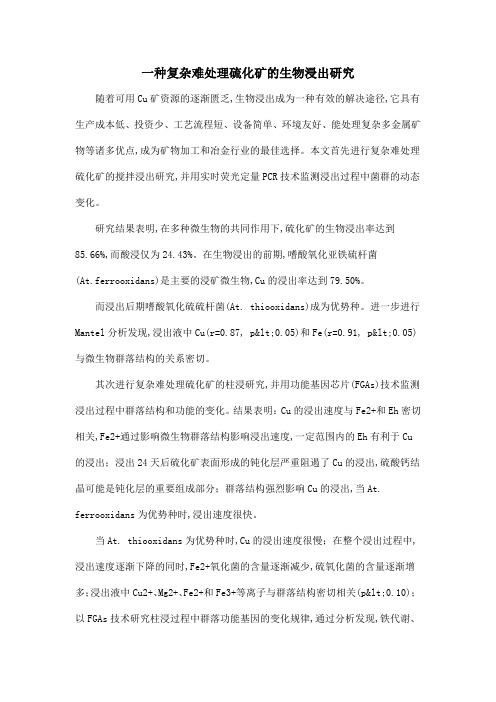
一种复杂难处理硫化矿的生物浸出研究随着可用Cu矿资源的逐渐匮乏,生物浸出成为一种有效的解决途径,它具有生产成本低、投资少、工艺流程短、设备简单、环境友好、能处理复杂多金属矿物等诸多优点,成为矿物加工和冶金行业的最佳选择。
本文首先进行复杂难处理硫化矿的搅拌浸出研究,并用实时荧光定量PCR技术监测浸出过程中菌群的动态变化。
研究结果表明,在多种微生物的共同作用下,硫化矿的生物浸出率达到85.66%,而酸浸仅为24.43%。
在生物浸出的前期,嗜酸氧化亚铁硫杆菌(At.ferrooxidans)是主要的浸矿微生物,Cu的浸出率达到79.50%。
而浸出后期嗜酸氧化硫硫杆菌(At. thiooxidans)成为优势种。
进一步进行Mantel分析发现,浸出液中Cu(r=0.87, p<0.05)和Fe(r=0.91, p<0.05)与微生物群落结构的关系密切。
其次进行复杂难处理硫化矿的柱浸研究,并用功能基因芯片(FGAs)技术监测浸出过程中群落结构和功能的变化。
结果表明:Cu的浸出速度与Fe2+和Eh密切相关,Fe2+通过影响微生物群落结构影响浸出速度,一定范围内的Eh有利于Cu 的浸出;浸出24天后硫化矿表面形成的钝化层严重阻遏了Cu的浸出,硫酸钙结晶可能是钝化层的重要组成部分;群落结构强烈影响Cu的浸出,当At. ferrooxidans为优势种时,浸出速度很快。
当At. thiooxidans为优势种时,Cu的浸出速度很慢;在整个浸出过程中,浸出速度逐渐下降的同时,Fe2+氧化菌的含量逐渐减少,硫氧化菌的含量逐渐增多;浸出液中Cu2+、Mg2+、Fe2+和Fe3+等离子与群落结构密切相关(p<0.10);以FGAs技术研究柱浸过程中群落功能基因的变化规律,通过分析发现,铁代谢、硫代谢、氮代谢、碳代谢、电子传递、金属抗性的相关基因与Cu的浸出的关系密切,群落的功能对浸出速度有较强的影响,所有功能基因的信号值呈先升后降的趋势,且当信号值较大时浸出速度较快。
硫化铜精矿加压氧化酸浸试验研究
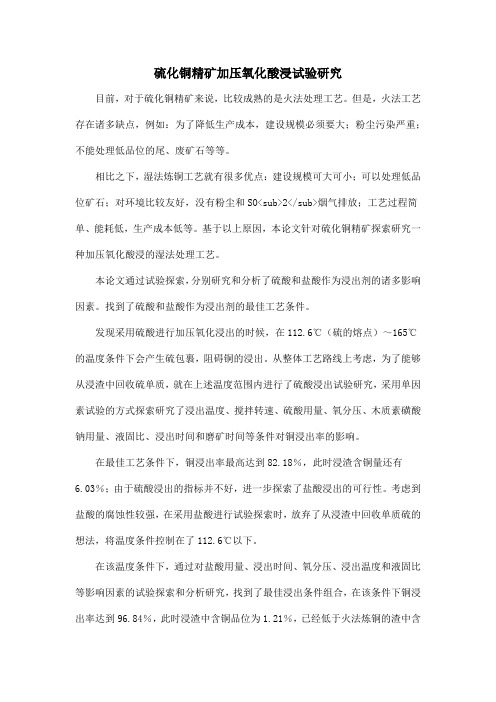
硫化铜精矿加压氧化酸浸试验研究目前,对于硫化铜精矿来说,比较成熟的是火法处理工艺。
但是,火法工艺存在诸多缺点,例如:为了降低生产成本,建设规模必须要大;粉尘污染严重;不能处理低品位的尾、废矿石等等。
相比之下,湿法炼铜工艺就有很多优点:建设规模可大可小;可以处理低品位矿石;对环境比较友好,没有粉尘和SO<sub>2</sub>烟气排放;工艺过程简单、能耗低,生产成本低等。
基于以上原因,本论文针对硫化铜精矿探索研究一种加压氧化酸浸的湿法处理工艺。
本论文通过试验探索,分别研究和分析了硫酸和盐酸作为浸出剂的诸多影响因素。
找到了硫酸和盐酸作为浸出剂的最佳工艺条件。
发现采用硫酸进行加压氧化浸出的时候,在112.6℃(硫的熔点)~165℃的温度条件下会产生硫包裹,阻碍铜的浸出。
从整体工艺路线上考虑,为了能够从浸渣中回收硫单质,就在上述温度范围内进行了硫酸浸出试验研究,采用单因素试验的方式探索研究了浸出温度、搅拌转速、硫酸用量、氧分压、木质素磺酸钠用量、液固比、浸出时间和磨矿时间等条件对铜浸出率的影响。
在最佳工艺条件下,铜浸出率最高达到82.18%,此时浸渣含铜量还有6.03%;由于硫酸浸出的指标并不好,进一步探索了盐酸浸出的可行性。
考虑到盐酸的腐蚀性较强,在采用盐酸进行试验探索时,放弃了从浸渣中回收单质硫的想法,将温度条件控制在了112.6℃以下。
在该温度条件下,通过对盐酸用量、浸出时间、氧分压、浸出温度和液固比等影响因素的试验探索和分析研究,找到了最佳浸出条件组合,在该条件下铜浸出率达到96.84%,此时浸渣中含铜品位为1.21%,已经低于火法炼铜的渣中含铜量。
文章对两种浸出剂的试验探索结果进行了综合分析,发现了一些有价值结论。
并对比研究了硫酸浸出和盐酸浸出的条件与结果,认为采用盐酸对硫化铜精矿进行加压氧化浸出有明显的优势,同时,经过工艺成本估算分析,可以认为采用盐酸对硫化铜精矿进行加压氧化浸出的工艺方案是完全可行的。
- 1、下载文档前请自行甄别文档内容的完整性,平台不提供额外的编辑、内容补充、找答案等附加服务。
- 2、"仅部分预览"的文档,不可在线预览部分如存在完整性等问题,可反馈申请退款(可完整预览的文档不适用该条件!)。
- 3、如文档侵犯您的权益,请联系客服反馈,我们会尽快为您处理(人工客服工作时间:9:00-18:30)。
本文由perfect_0319贡献 pdf文档可能在WAP端浏览体验不佳。
建议您优先选择TXT,或下载源文件到本机查看。
第 1卷第 2 0 期 2 l 年 4 月 OO 过 程 工 程 学 报 Th ne eJ u na fPr e sEngne rng eChi s o r lo oc s i ei 、0 _0 NO 2 ,ll . Ap . 01 r2 0 复杂硫化铜精矿微波活化预处理一 加压浸 出工艺 徐 志峰 李 强 王成彦 , , f. 西理 工大 学材料 与化 学工程 学院 ,江 西 赣 州 3 10 ;2 1江 4 00 .北京矿 冶研 究总 院 ,北京 10 4) 004 摘 要: 研究 了以黝铜矿为主的复杂硫化铜精矿微波活化预处理一 加压浸 出工艺.结果表 明, 该精矿在微波功率 8 、 2 w 每批处理量 9 及辐照 时间 10S 5g 2 条件下预处理后 ,矿石浸 出性能显著改善.预处理过程 中未见铅、锌、硫 、砷等元 素挥发损失.实验确定了微波活化铜精矿 加压浸 出工艺条件为:浸 出温度 4 3 5 K,氧分压 06 a .MP ,初始硫酸浓度 1 3 . 2 mo L l ,液周比 5mLg / /,浸 出时间 20 ,木质 素磺酸钙用量为精矿质量 的 1 5 .h . %,搅拌速度 5 0 / i.在此条件下, 2 0 r n r a 铜 、锌、铁浸 出率分别达到 8 . %, 2 3 63 9 . %和 2 . %.加压浸 出渣经高温煤油溶解单质硫后返回作浸出配矿使用 ,可 6 3 76 4 保 障 有 价 金 属铜 锌 收 率 . 关键 词 :复 杂铜 精 矿 ;黝 铜矿 ;微 波 活 化 ; 预 处理 ;加 压 浸 出 中图分类号:T 11 F 1 文献标 识码 :A 文章编号 :1 0— 0X(0 00 — 2 6 0 0 9 66 2 1)2 0 5— 7 1 前 言 在复杂硫 化铜精矿中,铜多以黄铜矿、黝铜矿形式 存在 ,结构稳定 ,分解困难 ,其浸 出必须经过强氧化过 波能[1 2.物质吸 收微波后 ,其晶体结构、表面性质等有 可能发生显著改变 , 如黄铁矿在一定条件下经微波处理 后会转 变成磁 黄铁矿 [ 且在 微波 场 中不 同矿物具 有 . 不同的升温特性 .] 。
2,如大多数硅 酸盐 、碳酸盐 、石英 7 等脉石属热惰性[ .因此 ,在微波作用下有可能实现有 用矿物 的选择性热活化, 进而提高矿物反应活性并改善 其浸出性 能. 程. 加压浸 出是一种强化湿法冶金过程 , 具有浸取高效、 流程短、无污染等优 点,具有广 阔的应用前景Ⅲ. 目 但 前加压浸 出工艺仅在 次生辉铜矿 处理方面成 功实现工 业化『, 2 由于原生黄铜矿 、 ] 黝铜矿在硫酸介质 中浸出“ 钝 本工作开展复杂硫化 铜精矿 微波 活化预处 理一 加压 浸 出工艺研究 ,即对以黝铜矿为主体矿物 的复杂硫化铜 矿进行微波活化预处理,使硫化铜矿晶格 活化 ,从而使 原本难 以浸 出的复杂铜精矿 在 中等温 度和压力下顺 利 浸出. 预处理过程 中,铜精矿 中的硫、锌 、砷 、铅等元 素无挥发损 失. 复杂硫化铜精矿 微波活化预处理一 加压 化 ”3 [问题 尚未彻底解决 ,复杂硫化铜矿加压浸 出仍只 ] 停 留在试验研究阶段. 为克服浸出 “ 钝化 ”问题 ,在复杂硫化铜矿浸 出过 程中常引入 H O 催化氧 化[ 1 N 3 4 或实施加氯活化浸 出 ~ . , 5 1 在 H O 催化氧化浸 出条件下,精矿 中的硫将大量氧化 N 生成硫酸 ,导致后续 中和工序负荷增重 ,此外浸 出液脱 浸出工艺无 需面对 S 2 O 回收 问题,清 洁高效. 硝也是一大难题;而加氯活化浸 出工艺 中氯离子对浸 出 设备 的腐蚀不容忽视 . 为克服复杂硫化铜浸 出 “ 钝化”问题,还可采用矿 石 活化预处理方法 . 现有的矿石活化预处理研 究多集 中 于机械活化[,如 A t o 9 】 cv x铜精矿浸 出工艺的关键就在 i 于精矿细磨 】 矿石经细磨后, 出过程虽可强化[- 1 加. 浸 1 1, 15 2 买 验 2 1原料 与设备 . 复杂硫化铜精矿原料 中主要元素含量见表 1 .由铜 精矿 XR 谱 图( D 见图 1可知, ) 精矿 中主要金属矿物有闪 但机械活化有明显局 限性[,] 11,未能从根本上解 决矿物 67 钝化 问题 ,且机械活化方式能耗高、成本大 ,矿石细磨 后有可能引发浸出渣排放 困难等问题. 微波 预处理矿 石及促进精矿 浸 出 目前 已有 多项研 锌矿 、黄铜矿、黝铜矿 、黄铁矿、方铅矿及少量铜蓝和 蓝辉 铜矿 ,脉石矿物主要为石英. 显微镜 下观察可知, 铜精矿 中闪锌矿多 ,含铜矿物 中黝铜矿量多,占 3 %~ 5 4 %左右. 0 精矿粒度为一 4u 占 9 . 4 m 9 %. 7 硫酸及其他化学试剂均为分析纯. 表 1 复杂 铜 精 矿 主 要 元 素 成分 T b e 1 Elme t l o o i o f o lx c p e o c n rt a l e n a mp st n o mp e o p r n e tae c i c c 究[- 】 12.当微波快速加热矿物时 ,由于微波穿过金属矿 82 物产生很大的热应力 ,致使矿物边缘 出现微小裂缝l , 2 这有可能是使矿物活性增强 的原因之一.另外,在微波 场 中,大多数硫化矿( 如黄铁矿 、黄铜矿等) 都能吸收微 里! 型 Co t n . net 86 .3 1 .1 77 垒 ! 1 .6 8 9 2 . 1 0 5 2 3 90 4 I .6 .4 .2 收稿 刚 朗:20 — 1 1,修 回 日期 :2 1— 1 1 09 1- 8 0 0 0— 8 基 金项 目:江西 省 自然 科 学基金 资助项 目( 编号 :2 0 G C 66; 国家 重点 基础研 究发 展规划 (7) 金资助 项 目( 号 :2 0C 6 30) 0 7 Q 0 5) 9 3基 编 0 7 B 15 5 作者 简介 :徐志 峰(9 3) 17一 ,男,江 西省 南 昌市 人 ,博 士 ,教 授 ,有色 金属 冶金专 业 ;王成彦 ,通讯 联 系人 ,Emal h 30 @s a o - iwcy2 7 i . m. : nt 第 2期 ∞ 0 ∞ 0 ∞ 徐 志O 等 : 0 杂硫 化 铜 精 矿 微 波 活 化 预 处 理一 压 浸 出 工 艺 0 加 复 峰 加 Ch l p r ̄ ac y i o t 27 5 昌 () , ◆ T r edr e etah E i t } 暑 出实验 ,实验条 件为 :[ S 4 1 1mo L,液 固比 H2O ] . l = 4 / L S 4m /,氧分/ p 20 a /= Lg  ̄ o . MP ,搅拌速度 5 0 / i, , = 6 0 m n r 浸出体系中引入 1 5 木质素磺酸钙( . %( 2 相对 于精矿质 量,下 同) ,结果见表 2 . 一 o 、-, ’ 历 C l 口 ■ 表 2铜精矿直接加压浸 出实验结果 T b e2 P e s r a h n e u t f n r t a e a l r s u el c i gr s l o p e e t d e s u r co pe u fdec c nta e p rs l i on e r t 三 Ilf ◆ . I f ★ l I ZU Z5 3【 】 3 5 4U 45 5 U 5 5 2 。
( ) 图 1硫化铜精矿 XR D谱图 F g 1XRD p cr m f o p r u f ec n e tae i. set u o p e l d o c nr t c s i 主要实验 仪器:G7 D 0 PDF型微波炉( 0 2 AS . 广东格 兰仕微波炉电器 有限公司) ,额定频率 2 5 z 4 0MH ,额定 输出功率 7 0 0 W;C FT型高压釜( J— 大连通达反应釜厂) , 内容积 1 .高压釜设备连接如 图 2所示. .L 0 由表 2可见,未经任 何活化 预处理 ,复杂铜精矿直 接加压浸出时,随浸 出温 度 由 4 3K升至 4 3K,浸 出 2 5 25 .h时,铜浸 出率仅 由 1. %提高至 2 . %,即使浸 59 9 76 3 出时间延长至 6 ,铜浸 出率也仅为 6 . %,而锌浸 .h 0 82 2 出过 程相对 容易得 多, 在温度 4 3 5 K下浸 出 25 , . h 锌浸 出率可达 8 . %,调整浸 出条件 ,锌浸 出率还可进一 01 5 步提 高. 在上述实验条件下 ,铁浸 出甚微. 经浸 出动力 学分析可 知, 铜浸 出反应表观活化 能为 7 .8 J l 出过程为界面化学反应控制. 1 / ,浸 9 k mo 为解决铜 浸 出困难 ,对 复杂铜精矿进行活化预处理 ,通过增大矿 石 反应活性 ,降低浸 出反应表观活化 能,进而实现复杂 铜精矿在 中等温度及压 力条件 下较理想 地浸 出. 3 2微 波功 率的影响 . 图 2 高压 釜 设 备连 接 图 F g 2 De i eat c me t fa t c a e i . v c t h n u o l v a o 考 察 了不 同微 波功 率对微 波预 处理后铜 精矿 加压 浸 出结果 的影 响,浸 出实验条件 为:T-5 - 3K,p 20 4 o . = 6 MP ,LS 5 L g H2O ]i 1 3 l a /= /,[ S 4n . / - . h m i= 2 mo L,t2 ,木 . 0 2 2 实验过程 . 称取一定量铜精矿 , 均匀平铺于微波炉腔体 内的石 英玻璃 圆盘上 , 在一定功率及 时间下进行微波辐照预处 理.将预 处理后 的铜精矿 按一定液固 比与浸 出剂混合加 质素磺酸钙用量 1 5 ,搅拌速度 5 0 r n . %( 2 0 / ,微波 mi 预处理 时间 1 0S 2 ,每批处理量 9 5g铜精矿 ,结果见图 3 . 入高压釜 的钛胆 中.高压釜加盖密封 ,通过控制箱设定 加热温度.升温 至设定温度 时 ,向高压釜 内通入工业纯 氧并开始计时. 通过调 节控 制箱,保 持浸出过程中搅拌 、. 一 转速恒定. 出结束后通水冷却 ,待 釜内压 力降为 0后 浸 开启高压釜 ,分别将浸 出液和浸 出渣送样分析 . 为保证 各实验点间具有可 比性,控制每次实验时高压釜升温速 率及降温速 率相 同. u J 里 2 巴 0' . 曼 a ) J C 0 ∞ .. 控制各 浸出实验中搅 拌转速 恒定为 5 0 / n 以保 0 mi, r 证实验条件 下釜内气 、 、固三相充分混合和氧 的传质. 液 M co a ep we ( i w v o r W) r 3 结果与讨论 3 1直接浸 出对 比实验 . 复杂硫 化 铜精矿 未经 微波 预处理 直接 进行 加压浸 图 3微波功率对预处理后铜精矿加压浸 出的影响 Fi 3 Efe tofm ir g_ f c c owa w e n e s e la hig vepo ro pr su e c n r o m ir wa ep er a e o p r o c n a e f c o v r te t dc p e n e  ̄ t c 28 5 过 程 工 程 学 报 第l 0卷 由图 3 可见 ,经 8 功率微波辐 照后 ,铜浸 出率 2w 明显提 高至 8 . %,而锌 、铁浸出率则分别为 9 . % 66 3 23 3 和 2 . %.随微波功率进一步增大,铜 、锌 、铁浸 出率 74 6 、一 未见明显变化. 经微波预处理后,复杂铜精矿浸出性能 的确得 以极大改善,在较低微波 功率(2 即可实现较 8 w) u J _ ∞ L 0' 理想 的铜浸 出效果. 进~步考察 了微波功率对复杂铜精矿 中铅 、 、 、 锌 硫 砷等元素挥发损失的影响,结果见 图 4 .由图可见,在 微波功率 8~ 8 范围内,金属铅、锌一直稳定存在 2 60W 于精矿 中,未见挥发损 失;当微波功率大于 5 0 后 , 2 W 硫才开始挥发,损 失率达 55 . %左右 ;而当微波功率提 高至 6 0 后,砷才开始出现少量挥发,6 0 时损失 8 W 8 W . 呈 仍 ∞ J C 0 .. B thweg t f o c nrt g ac ih n e t e() oc a 图 5 批 处 理 量 对 微 波 预 处 理后 铜 精 矿 加 压浸 出 的影 响 F g 5 E e t f ac ih f c o v r t ae i . f c th weg t r wa ep er td ob o mi e 率为 5 6 . %.由此可见 , 8 微波功率下, 3 在 2 w 复杂铜精 矿活化预 处理过程 中不会产 生砷 、铅 、锌 元素挥 发及 S2 O 烟气污染 问题 ,该工艺过程清洁,对环境友好. c p e o c nr t n i r s u el a h n o p rc n e tae o s e s r c i g tp e 矿石微波预处理过程 中,微波辐射能量( 波一部 ) 分被物料吸收而使其升温( )另一部分 则损耗( ) Q , Q , 即 . = 吸+ ,其 中 Q ̄= m rc为矿石 比热 ,m 微 QI Q 波 cA( 为矿石质量 , △ 为经微波预处理后矿石温度升 高值) .微 波功率一定 , 即 . 为常数 的条件下 , 镦 物料质量较小时, 、- , a ) 0) C 虽然较物料质量大时用 于升高相 同温 度所需热量更小, 8 器 o J 但热损耗更大;而物料质量较大时 ,虽然 单位质量物料 向外 界散热减少 ,但用 于升高相 同温度所 需热量增加. 所 以,只有物料 质量在某个适 当值时,其温度才能升至 最高 ,从而达到活化矿 石并最终促进矿石浸 出的 目的. 综上所述,在本实验条件下,每批物料处理量选择 M co a ep w rW ) i w v o e ( r 9 5 g较适宜 , 工艺放大 时,可能需要重新调整微波功 但 率及预处理时间等条件 . 图 4微波功率对铜精矿中元素挥发损失 的影响 F g 4 E e t f c o v o r nt el s f e d i . f c r wa ep we so a , o mi o h o l zn , u f r n r e i ec p e o c nr t ic s l d a s n c i t o p r n e ta e u a nh c 3 4预处理时 间 . 在微波功率 8 、每批处理量 9 条件下 ,考察 2w 5g 了微波预处理时间对活化铜精矿加压浸出结果 的影响, 3 3物料质量 的影响 . 在微波功率 8 2 W、预处理时问 10 的条件下 , 2 S 考 浸 出实验条件 同 3 . ,结果见图 6 2节 . 察 了批处 理量对微波预 处理后铜 精矿加压浸 出结果 的 影响,浸 出实验条件 同 3 . 2节,结果见 图 5 . 由图 5可见,在本实验条件下,批处理量在 10g 0 、- , 范围内, 微波辐照能起到活化铜精矿 并有效促进矿物浸 出的效果 ;批处理量进一步增大,特别是增大至 15 g 5 时, 微波辐 照不仅对铜精矿无 活化作用 , 反而使铜、 、 锌 铁浸 出明显受到抑制 , 铜、 锌浸 出率分别降低 至 1 . % 26 4 u J 0' . 兰 £ 0 a ) J 和 1. %, 81 0 铁浸 出完全受到抑制.随批处理量进一步增 大,铜精矿石预处理后浸 出性能反而恶化,与蔡超君【 2 引 的研究相 同. 进一步考察 了批 处理量对铜精矿中硫挥发 损失率 的影响. 结果发现,在微波功率 8 2 w、预处理时 间 10S 2 条件下 , 在批处理量 5 ~ 5 围内未见硫挥 5 15 g范 发损 失. Mco aeperam nt e() i w v rt t e ti S r e m 图 6 微 波 预 处 理 时 间对 活 化 铜 精 矿 加 压浸 出 的影 响 F g 6Efe t f c o v r te t n meo r s u e i . f c r wa ep e r ame t i np e s o mi t r l a h n f ci ae o p rc n e tae e c i g o t td c p e o c n r t a v 第 2期 徐志峰等 : 复杂硫化铜精矿微波活化预处理一 加压浸 出工 艺 29 5 由图 6 可见 , 6 ~ 0 范围 内, 在 0 30S 微波预 处理 时间 对铜浸 出无 明显影响 ,铜浸 出率保持在 8%~ 8 6 8%左右. 随预处理 时间延长 ,锌 、铁浸 出率均呈 降低趋势 ,原 因 可 能是硫化铁矿石具有 良好 的微波吸收性 能, 如磁黄铁 矿微波加热升温速率就高达 1 . /凹 , 6 3 s 】在微波加热条 4 K [ 件下铁矿物较短时间 内能迅速达到高温 , 易造成铁矿物 与锌矿物之间局部 “ 烧结 ”现 象 ,且随微波预处理 时间 3 6浸 出温度 的影响 . 在 4 8 4 3K范围 内, 0 — 7 考察 了浸 出温度对微波活化 铜 精 矿 加 压 浸 出 的影 响 .浸 出实 验 条 件 为 :P 2O6 0 . = MP ,LS 5 /,【 2O ]i 1 3 l a /= g H S 4n . / = .h mL i= 2 mo L,t2 ,木 - 0 质素磺酸钙用量 1 5 c ,搅拌速度 5 0 r n . %( ) 2 o 0 / ,结果 mi 见图 8 . 延长和矿物 持续升温 ,“ 结 ”现象有可 能趋于严重 , 烧 最终表现为锌 、 铁浸 出率 随微波预 处理时间延长而降低 . 进一步考察 了微波功率 8 条件下预处理时间对 2w 铜精矿 中易挥发元素铅、锌 、硫 、砷损 失率 的影响,发 现在本实验条件下,铜精矿 中铅 、锌、硫 、砷无挥发损 . 、_ 一 山 - c a L 0) E 0 c a ∞ J 失.因此 ,在微波功率 8 2 w、每批 处理量 9 5g的条件 下 ,微波预处理时间选择 10 S为宜. 2 在上述实验条件 下 ,铜、锌浸 出率可分别达 8 . %和 9 . %,铁浸 出 66 3 23 3 率为 2 . %. 73 4 3 5浸出剂用量的影响 . [ .. T K () 考 察 了浸 出剂硫 酸用 量对微 波活化 铜精矿 加压浸 出的影响.以硫酸与精矿 中铜 、铅、锌金属 的摩尔 比( 以 图 8浸 出温 度 对 微 波 活化 铜精 矿 加 压 浸 出 的影 响 F g 8Ef c f e c i g tmp r t r np e s e la h n i . f t a h n e e au eo r s u c i g e o l r e o c o v — c i ae o p r u fd o c n r t f mi r wa e a t td c p e l ec n e tae v s i 下简称酸 比1 表征浸 出剂硫酸 的用量. 出实验条件 为: 浸 T 4 3K,p  ̄0 a /= Lg = . h = 5 o . MP ,LS 5m /,t 0 ,木质素 = 6 2 磺酸钙用量 1 5 c ,搅拌速度 5 0 r n . %( ) 2 o 0 / ,结果见图 mi 7 .由图可见 ,随酸 比由 0 . 8增大至 1 ,即[ 2O ] 由 . 4 HS 4 08 l . mo/ 2 L增大至 1 4 m l ,铜 、锌浸 出率略呈增 大 . o/ 4 L 趋势, 铁浸 出率在 2 %~ 0 0 3 %之间波动.当酸 比为 1 ( . 即 2 由图 8可见,随浸出温度 由 4 8K升高至 4 3K, 0 5 铜浸出率 由 3 .8 9 %增大至 8 . %, 9 63 6 锌浸 出率 由 3 - % 11 3 增大 至 9 . %,浸 出温度进一步升高至 4 3 23 3 7 K,铜、锌 浸 出率均略有升高,分别达 8 .1 91%和 9 . %. 3 9 随浸 出 7 温度 由 4 8K 升高至 4 8 K,铁浸 出率 由 4 .0 0 3 70 %降至 2 . %, 64 8 这可能是 由于高温 下溶出的铁 易水解沉淀入渣 [ 2O ] 1 3 o L 时,锌浸 出率达 9 . %,铜浸 出 HS 4 = . l ) 2t / o 23 3 率为 8 . %. 6 6 若进一步提高浸 出剂硫酸用量 , 3 不仅 未能 明显提高铜 、锌浸 出率 ,反而提 高浸 出终酸浓度 ,降低 了酸利用率 . 因此 ,酸 比取 1 . 2为宜,即[ 2O ]i 1 3 H S 4r . i= 2 I . m o& l . 浸出温 度进 一步升高 ,铁浸 出率保持相对平衡.因此 , 浸出温 度选 择 4 3K为宜. 5 3 7添加剂用量的影响 . 单质硫 为硫化 铜精矿 氧压酸浸的产 物之一.当浸 出 温度 高于硫熔 点(9 时 , 32 K1 熔融硫 易包裹未反应矿 , 将 严 重影响有 价金属浸 出率. 常用 的硫分散剂有木质素 、 木质素磺酸盐 、丹 宁化 合物( 白雀木及其他 树皮提取 如 物) 及烷基 芳基磺酸 盐等[ ,其 中,木质 素磺酸盐为工 3 们 、- , u J ● 业上最常用的硫分散剂. 考察 了木质 素磺酸钙作添加剂 旦 窭 0) . 时其用量对 微波活化铜精 矿加压浸 出的影响. 出实验 浸 条件 为: = 5 p 206 a LS 5 /,H S 4 T 4 3K, o . MP , /= g [ 2O ]i = mL i= . 1 3 I ,t20 ,搅 拌速度 5 0 / n . / = .h 2 mo L 0 mi,结果见 图 9 r . 由图 9可见 ,在用量 0 %~ . 范围内,木质 . 08 2 %( 呈 t - o 弼 a ) . 一 素磺 酸钙对 铜浸出无 明显影响, 铜浸 出率保持在 5 %左 5 M l t f 2 O / b Z + u o rai o S 4 P + n C ) ar o H ( 右. 木质素磺酸钙用量 由 0 %增至 08 c ,锌浸 出率 . 2 .%( ) o 由 8 . %略增至 8 . %, 26 9 9 5 而铁浸 出率则 由 6 . %略降 2 78 4 至 6 . %. 2 2 木质素磺 酸钙用量 由 08 进一步提高至 7 . %( 1 5 ,虽然锌 浸 出率增 幅不 明显 ,但 铜浸 出率 由 . %( 2 图 7 硫 酸 用 量 对 微 波 活 化 铜 精 矿 加 压 浸 出 的影 响 F g 7 Ef c f o a eo l rca i np e s r a h n i . f t s g f u f i cd o r s u el c i g e o d s u e o i r w a e a tva e op rc ce r t fm c o v — c i t dc pe on nta e 过 程 工 程 学 报 第 1 0卷 5 . %明显增至 8 . %,而铁浸出率则 由 6 . %显著 68 0 66 3 27 2 降低至 2 . %. 76 4 木质素磺 酸钙用量进一步增 大, 、 、 铜 锌 铁 浸 出基 本保持 平衡.因此 ,木质 素磺酸钙 用量选 择 1 5 为宜. . %( 2 响 ,浸出实验条件 为:T 4 3 K, o O6MP ,LS 5 = 5 p 2 . = a /= mLg, [ 2O = . l / H S 4 1 3 mo L, 木 质 素 磺 酸 钙 用 量 2 / 1 5 ,搅 拌速度 5 0 / n . %( 2 0 mi,结果见 图 1 . r 1 由图 1 可见,随浸 出时间由 1 l . 0h延长至 20 , .h 铜 浸 出率由 7 . %增至 8 . %, 59 3 6 6 锌浸 出率 由 8 . %增至 3 67 3 9 . %,浸 出时间进一步延长 ,铜 、锌浸 出率无明显变 23 3 化. 2 在 . h范围 内,铁浸 出率保持在 2 %左右,浸 出 0 7 、 . , 时间进 一步延长 , 铁浸 出率有 明显增长, 浸出时间为 30 . h时,铁浸出率 高达 4 . %.鉴于此 ,为减轻后续 中和 35 7 旦 巴 0) . ∈ 除铁工序 的负荷 ,在保证铜、锌 高效浸 出的前提下尽可 能缩短浸 出时间,浸 出时间取 2 . h为宜. 0 £ c) c 6 a ) J D s g f a im I n s I o ae %, o a eo l u g o u h n t ( cc I p 、一 图 9 木 质 素 磺 酸 钙用 量 对 微 波 活化 铜 精 矿 加 压 浸 出 的影 响 F g9 E f c f o a eo ac u l n s l h n t np e s r i . fe t s g f li m g o u p o aeo r s u e od c i l a hn f c o v ? ci a e o p rc n e t t e c i g o mi r wa e a t td c p e o c n r e v a u J ‘ 口 0) . C o 3 8氧分压 的影响 . c 口 ∞ . _ J 考察 了氧分压对微波活化铜精矿加压浸出的影 响, 浸 出实验条件为: = 5 LS 5 /’H S 4 = . T43 K, /= g [2O 1 3 mL 2 mo L - . h l ,t20 ,木质素磺酸钙用量 1 5 ,搅拌速 / . %( 2 th () 度 50r i,结果见 图 1. 0 r n / a 0 图1 1浸 出 时 间对 微 波 活 化 铜 精矿 加压 浸 出 的影 响 F g 1 fe t f e c i gt np e s e la h n f i .1Ef c a h n me o r s u c ig o o l i r e mir wa e a t a e o p r o c n ae c o v - ci t dc p e n e t t v c r 31 .0液 固 比的影 响 、- 一 u J - 考 察了液 固比对微波活化铜精矿加压浸出的影响 , 浸 出实验条件为 := 5 P 206 a[ 2O ]i1 3 T43 K, o .MP , S 4n . = H i= 2 . mo/ ,t2 ,木质素磺酸钙用 量 1 5 c ,搅拌速 l L -. h 0 . %( ) 2 o 度 50/ n 0 mi,结果见图 1. r 2 巴 0 妄 0 c a ∞ J £ — Ox g rp ra pe s r MP ) y el at l rs ue( a i 、- 一 u J 图1 0氧分压对微波活化铜精矿加压浸 出的影响 F g 1 fe t f x g np ri l r s u eo a h n i .0Ef c y e a t e s r n l c i g o o ap e o mir wa e a t ae o p r o c n r t f c o v - ci td c p e n e ta e v c . c 口 L o' 三 0 £ o ‘ o J 由图 1 可见 ,随氧 分压 由 02 a 0 .MP 增至 0 MP , . 6 a 铜浸 出率 由 7 . %增至 8.6 43 3 63%,铁浸出率 由 1 . %增 06 2 至 2 . %,氧分压进一步增至 0 a 76 4 .MP ,铜浸 出趋于平 7 衡 ,浸 出率不再 明显变化 ,而铁浸 出率则显著提 高至 5 . %. 0 ~ . MP 68 5 在 . 0 a范围内,氧分压变化对锌浸 出 2 7 率无 明显影 响.综合考虑 ,氧分压取 0 a为宜. . MP 6 3 9浸出时间的影晌 . R t fi i t l ( /) a oo l u s i mL i do od q g 图1 2液固比对微波活化铜精矿加压浸 出的影 响 F g 1 f c f ai f i u dt o i n p e s e la h n i .2 Ef t r t o l i s l o r s u c i g e o o q o d r e o ir wa e a t ae o p r o c n a e f c o v — c i td c p e n e t t m v c r 考察 了浸 出时 间对微 波活化 铜精矿加 压浸 出的影 由图 1 可见 ,随液 固比由 3m / 2 Lg增至 5 /, g 铜 mL 第 2期 徐志峰等 : 复杂硫化铜精矿微波活化预处理一 加压浸 出工艺 状 [] 有色金属, 0 3 5 ()1 1 0 . J_ 2 0 , 54:0 —14 2l 6 浸 出率 由 4 . %增至 8 . %, 30 1 6 6 锌浸 出率 由 8 . %增至 3 68 4 9 . %, 2 3 铁浸 出率不断增大至 2 . %. 3 76 4 液固 比进一步增 大 ,铜 、锌浸 出率无 明显变化 ,而铁浸 出率则呈 明显增 大趋势.因此 ,液 固 比取 5 / g为宜. mL 3 1 工 艺 优 化 . 1 【]刘大星.湿法炼铜 的发展与前景 [】 有色金属再生与利用,2 0 , 2 J_ 05 () 3 — 9 7 :7 3 . [] c l , es g r B, ees , t 1P siaino h l p re 3 Hak P Drin e R i D Ptr e . as t f ac yi E a v o C o t d r gOxd t eL ahn n S l t da[] Hy rme l ry ui iai ec ig i uf eMe i J. do t l g , n v a au 1 9 , 913: 5 4 . 9 5 3 (/)2 — 8 【] ve S L ud r R E S i e a. tc S l r ec ig 4 Dais D , e ees , pt RA,t 1Nii— ufi L ahn z r uc 由上述实验结果可知 ,以黝铜矿为主体矿物的复杂 硫化铜 矿经微 波活 化预处 理后 可初步 取得较 理想 的加 压浸 出结果 , 、 铜 锌浸出率可 分别达到 8 . %和 9 . %. 66 3 23 3 但浸出渣 中铜 、锌含量仍偏高 ,分别 为 1 8 . %和 2 0 7 . %. 2 为进一步提高有 价金属 铜、 锌收率 , 行工艺优 化实验 , 进 P oesmpo e nsJ. n rE g, 9 13 () 15 — 2 9 rcs rv met [】Mie. n .1 8, 38:2 2 15 . I []王永 慧. 矿石 及精矿 氮类 物催化 加压 浸出 的应用与经 济估算 5 铜 [】 J_中国有色冶金, 0 9 ()6 14 . 2 0 ,1: -l, 3 [J ko inM, vi , k s Efc o C o cnrt nad 6 rba Ha l T U ai M. f t f S k k e Na 1 n et i n C ao Pa t l i e o a c p r t a h n n Cu rc Ch o d l t n ri e S z n Ch lo y i Le c i g i p l r e So u i c e i i o [ . y rmealry2 0 , 71 ) 19 1. J H do tl g , 0 5 7 (/ : 0 一l4 J u 2 即浸出渣 经高温煤 油溶解单质硫 处理 , 脱硫渣进行第二 段浸出,第二段 浸出工艺条件 同第一段. 煤油脱硫实验 条件 为: 油温度 3 3K, 煤 5 煤油与浸 出渣液 固比 2 L g 0 /, m 混合时间 05h . ,搅拌速度 5 0 r n 在上述 实验条件 0 / . mi []L Jf e I L wsn F f c o ho d o s0 h 7 u z Y, ef y M , a o .E f t fC lr e In 1 te r e i 1 Di ouino h l p r enAcdcS lt n [1Hy rmeaug , s l o f ac yi ii oui sJ. do tl ry s t C o ti o l 2 0 ,62: — 0 . 0 0 5 () l9 2 2 8 【】V aa , ae ao i I , eo i . ec igo o pr )i 8 rcr Z P rzn vc C rvcK P L ahn f p e( n R S C I C lim C lr e ouin [ . H do t lry 2 0 , 5 () acu ho d S lt i o J ] y rmea ug , 0 0 83: l 2 —2 7 61 6 . 下, 脱硫率达 7 . %. 9 6 煤油经冷却 降温可使溶解其 中的 9 单质硫 结晶析 出,煤油 可返 回使用 . 脱硫渣经第二段浸 出,最终渣含铜 、锌量可分别降至 O 5 . %和 00 5 2 . %,经 6 []C ra sIJ n o e JE 9 orn ,A g v .Ula n ln rte R c vr f ri t f e Miig f h eo ey o l u R f c r l J. ie. n .19 , (/1: 6— 7 . er ty God[]M nrE g, 9 1 471)7 3 7 6 ao [0 1】朱 屯l现代铜湿法冶金 [ .北京:冶金工业 出版社, 0 2 2 6 M】 20.2. 【1 Weh m JMehn ce cl rcsigo n ri C 3 S)J. 1】 la N . c ao h mia Po es f agt uAs4 [ n E e( ] H do tl ry 2 0 , 23: 6 一 7 . y rmeal g , 0 1 6 () 15 l 3 u 两段浸 出, 、 总浸 出率可分别高达 9 . %和 9 . %. 铜 锌 83 7 96 8 微波活化铜精矿经加压浸 出, 出渣经煤油脱硫后 浸 可返 回作浸 出配矿使用 ,以保障有价金属铜 、锌 的收率 并达到优化浸 出工艺 的 目的. [2 B lz . c a i l t aini do tl ry[]ItJMie. 1] aa Meh nc i t Hy rmeal g Jln.. n r P a Ac v o n u Poes 2 0 ,214: 4 — 5 . rcs. 0 3 7 (/)3 13 4 , [3 1】赵中伟 ,赵 天从,李洪桂 ,等.机械 活化对硫化锌精矿浸 出动力 学 的 影 响 [】 有 色 金 属 , 9 5 4 ()8 — 3 J. 1 9 , 72: 1 8 . [4 1]李洪桂 ,赵中伟,赵天从.机械活化黄铁矿的物 理化学性质 [ l J ] 中 南 工 业 大 学 学 报 ,9 52 ()3 9 3 2 1 9 , 63: 4 — 5 . 4 结 论 f) 1以黝铜矿 为主 体矿物 的复杂硫 化铜矿 难 以直 接 [5 1】杨家红,李洪桂 ,赵中伟,等 . 矿物机械活化基础理论的研究进 展 [】 稀 有 金 属 与 硬 质 合 金 , 9 6 ()3 _ 3 J. 1 9 ,4: 8 4 . 高效浸 出,经微波活化预处理后 ,可初步实现较理想的 加压浸出结果.实验确定 的微波 活化预 处理的较优 工艺 条件为 :微波功率 8 、每批处理量 9 ,微波预处 2w 5g 理时间 10 . 2 在微热活化预处理过程 中,铜精矿 中铅 、 S 锌 、砷等元素未见挥发损失 ,也不产 出 S O 有害气体. () 2实验确 定的微波 活化铜 精矿加 压浸 出工艺条件 为 :浸 出温度 4 3K,氧分压 06MP ,初始硫酸浓度 5 . a 13 l . / 2 mo L,液固 比 5 /,浸 出时间 20 ,木质 素磺 g mL .h 酸钙用 量为精矿质量 的 1 5 . %,搅拌速度 5 0r n 在 2 0 mi. / 上述 条件下,铜 、锌浸 出率 分别达 8 . %和 9 . %, 63 6 23 3 铁浸 出率为 2 . %. 74 6 [6 1]黎铉海 ,黄祖强 ,刘雄民,等.机械活化作用下载金矿物的形貌 特 征 [] 金属矿 山, 0 1()3 一 3 Jl 2 0 ,1: l 3 . (7 1]李 春 ,梁 斌 ,梁 小 明.钛 铁 矿 的 机 械 活 化 及 其 浸 出动 力 学 [】 J.四 川 大 学 学报 ( 程 科 学 版 )2 0 , 71: 5 3 . 工 , 0 53 ()3 ~ 8 [8 1]张文朴 微波 在稀贵金属冶 金中的应用研 究进 展 [] J.稀有金属 与 硬 质 合 金 ,0 8 3()4 — 3 2 0 ,62: 9 5 . [9 YintsJB, no uc V. lb e i o cnrt enn y 1] aao A tn ci Moy d nt C n et eClaigb e a Co prS l t nAciae y Mirwa e【J Mie. n .2 0 , p e uf i t tdb co v J. n r E g, 0 1 ao v 1 (l: 4 1 1 . 4 11 1 1- 4 9 1 [0 Jcb , ai n sP D. co v n l go iea []J 2 ] a o sIS Z vt o Mi waeHadi f nrl J . s r n M . Ap 1P y.18 , 33:7 0 2 3 . p. h s 9 2 5 ()2 3 — 7 5 , [1 alS T Fnh JA. w eo co a ef] Mie. e l 2 ]H l , ic Ne Us fMirw v J. nr M t 1 a. Po es 1 8 ,1) 19 1 3 rc s. 9 4 ( 1: 7 — 8 . , f) 波活化铜 精矿加 压浸 出渣煤 油脱 硫 实验条件 3微 为:煤 油温度 3 3K,煤 油与浸 出渣液 固 比 2 L g 5 0m /, 【2 S n i W o r Mi o v n l go o e o e [] 2 ] t ds N, me a h H. c wa e r Ha di f rnOr wdr J n I P . Mir w v P we a d lc o g ei E eg , 1 9 , 2 () co a e o r n E e t ma n t n ry 0 r c 9 5 3: 17 8 . 7 -l 0 混合 时间 0 , .h 搅拌速度 5 0r i. 高温煤 油溶解单 5 0 r n 经 / a 质硫 处理 后 ,脱硫 渣经 第二段 浸 出可使最 终浸 出渣 中 铜 、锌含量分别低至 O2 % ̄ . 5 . 5 DO 6 %.为保障有价金属 0 铜锌收率 , 微波活化铜精矿加压浸 出渣经煤油脱硫处理 后可返 回作浸 出配矿使用. 参考文献: 『 1 1王海北 ,蒋 开喜 ,邱定蕃 ,等.国内外硫 化铜矿湿法冶金 发展现 [3 Hau . co v n ry frMiea Tet n rcs- A 2 ] q eK E MirwaeE eg o nrl ramet o es- P - B e Reiw [ .n.. n rPoes 19 , 71:- 4 i r f ve J ItJMie. rcs. 9 9 5 ()1 2 . ] , 【4 h nT T h eaieTa sae c fMieast co v 2 ]C e .T eR l v rnprny o nrl o Mirwa e t Rait n[】C n Mea . ,9 4 2 ()3 9 3 dai J_ a . tl Q.1 8, 3 1:4 — 5 . o 1 1 【5 2 ]崔礼生 ,韩跃 新. 微波技 术在选矿 中的应用 [ .金属矿 山, 0 6 J ] 20, ()2 - 2 4: 9 3 . [6 2 】彭金辉 , 刘纯鹏. 微波场 中矿物及其化合物的升温特性 [ .中国 J ] 有色金属学报, 9 7 73: 0 5 . 19 , () 5— 2 【7 2 ]段 爱红.晶体结 构缺 陷结构与物质 吸收微波 的能力 [] J_云南师 22 6 范大学学报, 9 8 1 ()8 — 1 19 , 83: 9 9 . 过 程 工 程 学 报 第 1 卷 O [0 3 ]Ka la只 Ha e dnW , c i Reoey o icf m wa k f n e J Makw V N. cv r f n r Z o Zn up ie yDi cP esr e cig[ ]USP t US 87 6 , icS lhd s r t rsueL ahn P. a. 36 2 8 b e : 1 7 - 2 8 9 5 0 -1 . [8 2 ]蔡超 君 . 化 铜 矿 微 波 辅 助 焙 烧 工 艺 及 机理 研 究 [ .昆 明 : 昆 硫 D] 明 理 工大 学 , 04 3— 9 2 0 .3 3 . [9 2 ]金钦汉.微波化学 【 .北京:科学出版社, 9 92 4 M] 19.8. M ir wa eAc i a i n P er am e t n r s u eLe c i fCo l x Co p rS l d n e ta e c o v tv to r te t n d P e s r a h ngo mp e p e u f eCo c n r t a i XUZ ieg, L a g, WA hn .a h. n f I n Qi NGC e gy n ( co lf t ila dC e ia n ier g Jag i nvri S i c n eh ooy G nh u J nx 4 0 4 C ia Sh o Mae as n hm cl gnei , inx i syo c n e dTc n l , az o。