第四章 机械加工工艺规程设计学习资料
机械加工工艺规程设计教材

粗基准的选择(xuǎnzé)原则
3. 对于(duìyú)所有表面都要加工的表面,选取余量和公差最小的表面作 粗基准,以避免余量不足而造成废品。
第二十四页,共50页。
粗基准的选择(xuǎnzé)原则
4.选取光洁、平整、面积大的表面作粗基准; 5.粗基准不应重复使用。一般(yībān)情况下,粗基准只允许使用一次。
➢ 几何关系:视图完整、正确,表达清楚无歧义,几何元素的 关系应明确,避免在图纸上可能出现加工轮廓的数据不充分、 尺寸模糊不清及尺寸封闭干涉等缺陷。
第二页,共50页。
零件(línɡ jiàn)加工工 艺性分析
➢ 精度与技术要求:包括尺寸精度、形位公差和表面粗糙度。 在满足使用要求的前提下若能降低精度要求,则可降低加工 难度,减少加工次数(cìshù),提高生产率,降低成本。
第二十五页,共50页。
精基准的选择(xuǎnzé)原则
对于形位公差精度要求较高的零件,应采用已加工 过的表面作为定位基准。这种定位基准面叫做精基准。 精基准的选择原则(yuánzé): 1. 基准重合原则(yuánzé):选用定位基准与设计基准重 合
的原则(yuánzé)
第二十六页,共50页。
精基准(jīzhǔn)的选择原则
零件(línɡ jiàn) 工零艺件结性构包形括状:的合理性、几何(jǐ hé)图素关系的确定性、精度及
技术要求的可实现性、工件材料的可切削性能等
➢ 结构形状:在满足使用要求的前提下加工的可行性和经济性。 尽量避免悬臂、窄槽、内腔尖角以及刚性不稳的薄壁、细长杆 之类的结构,减少或避免采用成型刀具加工的结构,孔系、内 转角半径等尽量按标准刀具尺寸统一以减少换刀次数,深腔处 窄槽和转角尺寸要充分考虑刀具的刚性等等。
第4章机械加工工艺规程设计a
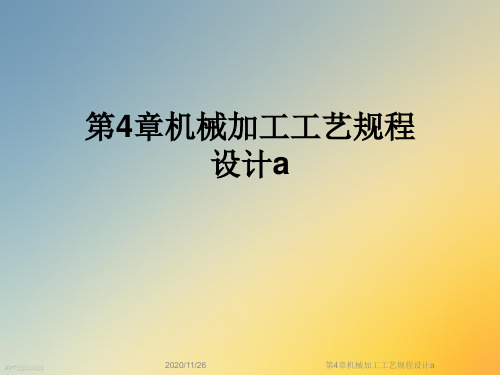
工序
0 5 10
PPT文档演模板
工种
车 车 钳
工步的基本要素:
加工面、刀具、切
削用量(不含背吃
工序内容
工作地点 刀量)均不变
(机床)
车端面,打中心孔,掉头, 车另一端面,打中心孔
粗车各外圆;半精车各外圆, 倒角,去毛刺
车床1 车床2
几个工步 ?
划线
钳工台 第4章机械加工工艺规程设计a
带回转刀架的机床(转塔车床,加工中心) ,回转刀架的一次转位所完成的 工位内容属一个工步;若有多把刀具同时参与切削,该工步称为复合工步。
第4章机械加工工艺规程设计a
加工工艺过程
工序
安装 工位 工步 走刀
PPT文档演模板
第4章机械加工工艺规程设计a
工序
一个(或一组)工人,在同一个个工工作作地地点点(或机床)对一个 (或一组)工件进行加工,所连续续完成的那部分工艺过程。
工序
0 5 10
PPT文档演模板
工种
车 车 钳
工序内容
工作地点 (机床)
零件结构形状应尽量简单和布局合理,方便加工和测量 尽量减少加工表面的数量和面积,合理规定零件的精度和 表面粗糙度,减少切削加工量 结构设计方便在夹具中安装、定位和夹紧 零件应具有足够的刚度,能承受夹紧力和切削力 结构设计便于提高生产率、保证加工质量
PPT文档演模板
第4章机械加工工艺规程设计a
安装
在同一个工序中,工件每定位和夹紧一次所完成的那部分工 序内容称为一个安装。
一个工序中,工件可安装一次或数次。
工序 工种
工序内容
0
车 车端面,打中心孔,掉头,
车另一端面,打中心孔
工作地点 (机床)
机械制造工艺学第四章 机械加工工艺规程设计
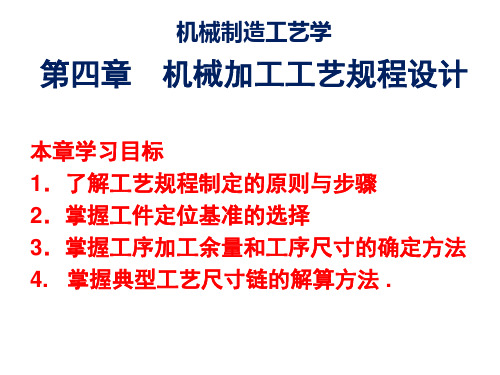
(3)应尽量减小加工面积 支座底面设计为中凹可减少加工量,提高支撑精度和稳定性。
三、要考虑生产类型与加工方法
箱体零件: 单件小批时(a),其同轴孔的直径应设计成单向递减的,以便 在镗床上通过一次安装就能逐步加工出各孔。 大批生产时(b),为提高生产率,一般用双面联动组合机床加 工,这时应采用双向递减的孔径设计,用左、右两镗杆各镗两 端孔,以缩短加工工时。
床身导轨面自为基准
(4)互为基准原则
对工件上的两个相互位置精度要求很高的表面,互相作为 定位基准,反复进行加工。
优点: 可使两个加工表面间获得高的位置精度。 如:内外圆面同轴度要求比较高的套类零件的加工安排
第二节 机械加工工艺路线的制订
一、定位基准的选择
2、粗基准的选择原则 (1)保证位置精度原则
0.16-0.01
加工方法 钻 扩
铰 拉
镗
孔的加工方法
加工性质
加工经济精度(IT)
实心材料
12-11
粗扩
12
精扩
10
半精铰
11-10
精铰
9-8
细铰
7-6
粗拉
10-9
精拉
9-7
粗镗
12
半精镗
11
精镗
10-8
细镗
7-6
表面粗糙度Ra
20-2.5 20-10 10-2.5 10-5 5-1.25 1.25-0.32 5-2.5 2.5-0.63 20-10 10-5 5-1.25 1.25-0.32
加工方法
外圆加工的方法
加工性质
加工经济精度(IT) 表面粗糙度Ra(um)
车 外磨 研磨 超精加工
粗车 半精车
精车 金刚石车
第四章 机械加工工艺规程设计(二-装夹与基准)

(5)几何结构原则 *精基准部位的面积,一般应大于被加工表面 的面积,以保证定位准确,夹紧可靠; *精基准部位的技术要求,一般应高于被加工 表面的技术要求,以减少定位误差;
精基准的选择原则: (1)基准重合原则 选择设计基准(或工序基准)作为精基准, 消除基准不重合误差。 在轴上加工键 槽时,工序尺寸为 t,若以下母线为 定位基准,则定位 基准与工序基准重 合,无基准不重合误差;而若以中心线为定位基 准,则定位基准与工序基准不重合,工序尺寸为 t = R+L,R与L的误差都会影响加工精度。
*测量基准:测量时所采用的基
准。(检测钻套B面的端面跳 动和φ40H6外圆的径向跳动时 以φD内孔为测量基准) *装配基准:机器装配时,用以确定零件(或部 件)在产品中的相对位置所采用的基准。 齿轮装配时以内 孔和左端面确定其在 轴上的位置,内孔和 左端面就是齿轮的装 配基准。
四. 工件定位基准的选择 1.粗基准的选择 (1)保证相互位置要求的原则:如果必须保证 工件上毛坯面与加工面之间的位置要求时,应 选择毛坯面为粗基准。
§5Байду номын сангаас2
工件加工时的装夹与基准
一. 工件的装夹 1. 装夹的概念:将工件在机床上或夹具中定位、 夹紧的过程,称为装夹。 定位 — 使工件在机床上或夹具中占据正确的 位置。 夹紧 — 工件定位后将其固定,使其在加工过 程中保持定位位置不变的操作。
2. 装夹的方法:
1)直接找正装夹法
是用百分表、划针或用目测,在机床上 直接找正工件,使工件获得正确位置的 方法。
二. 工件的定位 1. 六点定位原理: 工件在空间的位置相当于刚体在空间直角坐 标系中的位置。工件没有定位时,可看作在空间 处于自由状态的刚体(在 空间有六个自由度)。限 制这六个自由度,使工件 在空间的位置得以确定, 就是六点定位原理。
第四章机械加工工艺规程的制定

在毛坯制造方面 在加工方面 在装配方面
•铸件:便于造型、拔模斜度 •璧厚均匀、无尖边、尖角 •锻件:形状简单、无尖边、 尖角、飞刺,便于出模
•合理标注零件的技术 要求 •便于加工、减少加工
•便于装配、减少修配量
在加工方面 在装配方面
•减轻零件重量 •保证加工的可行性、经济性 •零件尺寸、规格、结构要素 标准化 •正确标注图纸尺寸及加工技 术要求。
环——尺寸链中的每一个尺寸。它可以是长度或角度。
封闭环——在零件加工或装配过程中间接获得或最后形 成的环。
组成环——尺寸链中对封闭环有影响的全部环。
组成环又可分为增环和减环。 增环——若该环的变动引起封闭环的同向变动,则该 环为增环. 减环——若该环的变动引起封闭环的反向变动。则该 环为减环。
4、增、减环判别方法
1.极值法
(1) 极值法各环基本尺寸之间的关系
封闭环的基本尺寸A0等于增环的基本尺寸之和减去减环的 基本尺寸之和,即
m
n1
A A A 0基
i基
i基
i1
•便于分解独立装配单元 •便于平行、流水作业 •调整方便、减轻装配劳动 •便于达到装配精度
第二节 工艺路线的制订
定位基准选择
采用毛坯上未经加工 的表面作为定位基准。
定位基准
1、粗基准 2、精基准 3、辅助基准
采用经过加工的表面 作为定位基准。
一、粗基准选择
(举例)
重点考虑: •加工表面与不加工表面的 相对位置精度; •各加工表面有足够的余量
其它工序安排
•去毛刺、倒钝锐边 •去磁 •清洗 •涂防锈油
机床加工工序的设计 一、加工余量确定
1. 加工余量概念
(1)总加工余量 (2)工序余量
《机械制造基础》第四章课后题及答案(题号可能不搭配)

第四章课后题1.什么是机械加工工艺规程?工艺规程在生产中起什么作用?制订工艺规程的原则有哪些?工艺规程是根据加工对象的具体情况和实际生产条件,拟定出比较合理的工艺过程,并按照规定的形式制定的文件。
是指导生产的主要技术文件,是生产组织和管理工作的基本依据,是新建或扩建工厂的基本资料。
2.什么是零件结构工艺性?结构工艺性是指零件所具有的结构是否便于制造、测量、装配和维修。
3.在机械加工过程中当零件的加工精度要求较高时,通常要划分为哪几个加工阶段?粗加工阶段,半精加工阶段,精加工阶段,光整加工阶段,超精密加工阶段。
划分加工阶段的目的:保证加工质量,合理使用设备,便于安排热处理工序,便于及时发现问题,保护零件。
4.什么是定位粗基准?其选取方法是什么?为什么在同一尺寸方向上粗基准一般只允许使用一次?在实际生产的第一道切削加工工艺中,只能用毛坯表面做定位基准,这种定位基准称为粗基准。
选取方法:以不加工的表面做粗基准(保证加工表面与不加工表面的位置要求)以重要表面为粗基准(保证加工余量均匀)加工余量最小的加工表面作粗基准(保证有足够的加工余量)以质量较高的表面作粗基准粗基准只能用一次:重复使用容易导致较大的基准位移误差。
5.什么是定位精基准?选取原则是什么?用已加工的表面作为定位基准,即为精基准。
选取原则:基准重合原则(选择设计基准为定位基准)基准统一原则(重复安装时,尽量选取同一表面作为定位基准)互为基准原则自为基准原则(加工表面本身作为定位基准)定位稳定原则6.工序集中和工序分散的原则分别是什么?各有什么特点?影响工序集中与工序分散的主要因素各有哪些?分别用于什么场合?工序集中原则:每道工序加工的内容较多,工艺路线短,零件加工被最大限度地集中在少数几个工序中完成。
特点:减少零件安装次数,有利于保证位置精度,减少工序间运输量,缩短加工周期;工序数少,可以采用高效机床,生产率高;减少了设备数量和占地面积,节省人力物力;所用设备结构复杂,专业化程度高。
史上最全的机械加工工艺培训课程

1.1 机械加工工艺的含义
工艺
是指制造产品的技巧、方法和程序。机械制
造过程中,凡是直接改变零件形状、尺寸、相对位
置和性能等,使其成为成品或半成品的过程,称为
机械制造工艺过程。它通常包括零件的制造与机器
的装配两部分。
1.2 机械加工工艺的作用
是指导生产的主要技术文件
1.3.6 夹具:
加工工件时,为完成某道工序,用来正确迅速安装工 件的装置。
1.4.1 机械加工中的其他术语
A. 机械制造:各种机械的制造方法和过程的总称。 B. 工艺文件:指导工人操作和用于生产、工艺管理等的各种技术文件。 C. 工艺规程:规定产品或零部件制造工艺过程和操作方法等的工艺文件。 D. 工艺参数:为了达到预期的技术指标,工艺过程中所需选用或控制的有关 量。 E. 工艺装备(工装):产品制造过程中所用的各种工具总称。包括:刀具、 夹具、模具、量具、检具、 具、钳工工具和工位器具等。 F. 工件:加工过程中的生产对象。 G. 切削加工:利用切削工具从工件上切除多余材料的加工方法。
基孔制的“表面”特征:
1.孔和轴的基本尺寸是一样的; 2.孔的下公差为0,上公差由设计需求确定(H7 H6) 3.轴的上下公差(相对地)不确定,由设计需求确定; 4.孔的配合字母大写,轴的配合字母小写(孔大轴小); 5.现实设计中,98%的情况是采用基孔制的。
基孔制举例
轴 孔 H8
+0.033 Φ 20 0
H.
工位:为了完成一定的工序部分,一次装夹工件后,工件(或装配单元)
与夹具或设备的可动部分一起相对刀具或设备的固定部分所占据的每一个 位置
I.
工艺尺寸:根据加工的需要,在工艺附图或工艺规程中所给出的尺寸。
机械制造工艺学第二版王先奎机械制造工艺学ch41机械加工工艺规程设计概述

更 改 内 容
走
程
次 背吃 数刀
量 (m m)
切削用量
进给量
( mm/r 或 mm/ min)
切削速 度 ( r/min )或双 行程数 /min
切削 速度 (m/ min )
工作定额 (min)
基 辅 工服 本 助 作务 时 时 地时 间 间 点间
刀具量具及辅助 工具
工 步 号
名规 编数 称格 号量
第四章 机械加工工艺规程设计 第一节 概述
一、机械加工工艺规程旳作用 二、机械加工工艺规程旳格式 三、机械加工工艺规程旳设计原
则、环节和内容
一、机械加工工艺规程旳作用
1)机械加工工艺规程是生产旳计划、调度,工人旳操作、 质量检验等活动旳根据。
2)机械加工工艺规程是生产准备工作(涉及技术准备工作) 旳根据。
内壁孔出 口处平整,钻 孔方便,易保 证孔中心位置 度
附加定位 基准,加工时 保证 A.B 面平 行,加工后, 将附加定位基 准去掉
图例6:
键槽设置在阶梯 17 轴 90°方向上,需两
次装夹加工
钻孔过深,加工 18 时 间 长 , 钻 头 耗 损
大,并且钻头易偏斜
进.排气(油)通 19 道设计在孔壁上,加
1)在单件小批生产中,一般只编写简朴旳机械加工工艺 过程卡片;
2)在中批生产中,多采用机械加工工艺卡片;
3)在大批大量生产中,则要求有详细和完整旳工艺文件, 要求各工序都要有机械加工工序卡;
4)对半自动及自动机床,则要求有机床调整卡,对工序 则要求有检验工序卡等。
(工厂名)
表 1-8 机械加工共序卡片
7、拟定各工序旳加工余量、计算工序尺寸和公 差。
8、拟定切削用量 a) 在单件小批生产中,切削用量多由操作 者决定,机械加工工艺过程卡中一般不作 明确要求。 b) 在中批,尤其是在大批大量生产中,为 了确保生产旳合理性和节奏均衡,要求必 须要求切削用量,并不得随意改动。
第4章机械加工工艺规程设计b
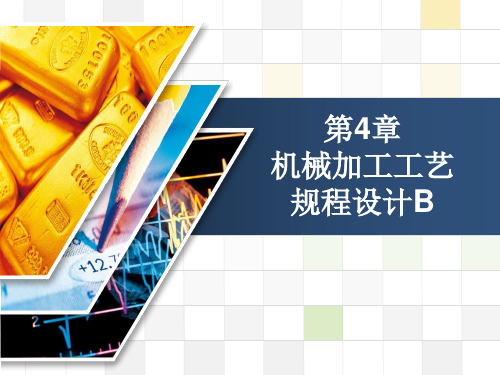
抛光 Ra 0.1~0.012
外圆加工方法
注:加工有色金属时,表面粗糙度 Ra 取小值。
内圆表面加工
内圆表面的适用范围
✓ 螺钉、螺栓的紧固孔; ✓ 套筒、法兰盘及齿轮等回转体零件上的孔; ✓ 箱体类零件上的主轴及传动轴的轴承孔; ✓ 炮筒、空心轴的深孔(一般l/d≥10); ✓ 保证零件间配合准确性的圆锥孔等。
LOGO
第4章 机械加工工艺
规程设计B
第4章 机械加工工艺规程设计
工艺过程的基本概念 零件结构工艺性分析 基准与定位 工艺路线的制订 加工余量与工序尺寸 工艺尺寸链 典型零件加工工艺分析
四、工艺路线的制定
工艺路线设计是指拟定将毛坯制成所需零件的整个加工路
线,是制订工艺规程的总体布局。
加工方法的选择
外圆表面加工
外圆表面加工的零件种类
轴类、套筒类、盘类零件
外圆表面加工的加工方法
➢ 车削、磨削和各种光整加工方法
外圆表面加工的技术要求
➢ 尺寸精度:直径 ➢ 形状精度:圆度、圆柱度 ➢ 位置精度:同轴度、垂直度、跳动 ➢ 表面质量:Ra、Rz
粗车 IT12~11 Ra 25~12.5
半精车 IT8~7 Ra 1.6~0.8
精车 IT8~7 Ra1.6~0.8 粗磨 IT8~7 Ra 0.8~0.4
金刚石车 IT6~5 Ra 0.8~0.2
精磨 IT6~5 Ra 0.4~0.2
外圆表面的典型加工工艺路线
研磨 IT5~3 Ra 0.2~0.008
超精加工 IT5 Ra 0.1~0.01
砂带磨 IT5~6 Ra 0.4~0.1
成形法 (仿形法)
•铣齿 •磨齿
机械加工工艺规程设计资料-新

(3)步骤: ①确定生产类型; ②分析研究产品的装配图和零件图,进行工艺审查;熟悉产品,性
能,用途和工作条件,零件在产品中的作用;
检查尺寸,视图及技术条件是否是否合理?
主要:
a.审查各项技术要求是否合理;过高的精度,表 面粗糙度及其他要求会使工艺过程复杂化,成 本提高; b.审查零件的结构工艺性是否好;便于加工的 安装,尽可能减少工和装配的劳动量; c.审查材料选用是否恰当;
精基准:采用已加工表面作为定位基准。
辅助基准:(有时回遇到这种情况),工件上没有能作为定位基 准用的恰当表面,而在工件上专门设置或加工出定位表面。常 用的有工艺孔和工艺塔子。
辅助基准在零件上不起 功能作用,纯粹是为了 工艺上的需要。加工完 毕后,若有需要(如有 碍外观等)可予以去除。
工艺塔子
粗基准和精基准所起作用不同,两者的选择原则也不一样。 基本要求是:先把精基准加工出来,即基准先行
③确定毛坯的种类和尺寸;(应考虑生产批量,零件材料及毛坯 生产条件)
a.一般采用:铸件、锻件、焊接件; b.毛坯精度提高,材料利用率提高,大大节约机械加工工时, 但毛坯精度过高会使毛坯制造困难,毛坯成本增加。 因此,毛坯种类和制造方法的选择要根据生产类型和具体 生产条件而定。达到高质量,降低生产产品生产成本。
测量基准:测量时用来确定被测零件在度量工具上位置所采用的基准。 必须实际存在,不可互为基准。
装配基准:装配时用来确定零件或部件在产品中的相对位置所采用的 基准。可以是假想的
(4)定位基准对工艺规程的影响。 直接影响: a.工序的数目; b.夹具结构的复杂程度; c.零件的精度是否易于保证(如基准重合);
第4章机械加工工艺规程的设计课件

17
4.1 机械加工的基础知识
18
4.2 机械加工的工艺规程
4.2.1 机械加工工艺规程及其作用 1.机械加工工艺规程的概念
规定产品或零部件制造工艺过程和操作方法 等的工艺文件称为工艺规程。其中,规定零件机 械加工工艺过程和操作方法等的工艺文件称为机 械加工工艺规程。它是在具体生产条件下,最合 理或较合理的工艺过程和操作方法,并按规定的 形式写成工艺文件,经审批后用来指导生产的。
28
4.3 工艺审查和毛坯选择
29
4.3 工艺审查和毛坯选择
3.结构设计时应注意的几项原则
①尽可能采用标准化参数,有利于采用标准刀具和量具; ②要保证加工的可能性和方便性,加工面应有利于刀具的 进入和退出; ③加工表面形状应尽量简单,便于加工,并尽可能布置在 同一表面或同一轴线上,以减少工件装夹、刀具调整及走 刀次数; ④零件结构应便于工件装夹,并有利于增强工件或刀具的 刚度; ⑤应尽可能减轻零件质量,减少加工表面面积,并尽量减 少内表面加工; ⑥零件的结构应与先进的加工工艺方法相适应。
产品均有一定的数量,工作地的加工对象周期地重复。 单件生产:产品产量很少,品种很多,各工作地加工对象经 常改变,很少重复。
生产类型的划分主要决定于生产纲领,即年产量 。
13
4.1 机械加工的基础知识
14
4.1 机械加工的基础知识
15
4.1 机械加工的基础知识 三、工件的基准
基准是用来确定生产对象上几何要素间的几何 关系所依据的那些点、线、面。一个几何关系只有 一个基准。
(4)工序设计指机床和工艺装备选择、确定加工余 量、计算工序尺寸及公差、确定切削用量及计算工 时定额等;
第四章机械加工工艺规程设计

第四章机械加工工艺规程设计第四章第一节概述一、什么是机械加工工艺规程?是规定产品或零部件机械加工工艺过程和操作方法等的工艺文件,是一切有关生产人员都应严格执行、认真贯彻的纪律性文件。
工艺规程由一个或若干个顺序排列的工序组成二、机械加工工艺规程的作用?工艺规程是指导生产的主要技术条件。
工艺规程是生产组织和生产管理工作的依据。
(3)工艺规程是新建或扩建工厂及车间的基本资料。
三、制订工艺规程所需的原始资料?①产品的全套装配图和零件工作图②产品验收的质量标准③产品的生产纲领④毛坯资料⑤现场生产条件⑥应尽可能多了解新工艺、新方法四、工艺规程的设计原则?①技术要求必须保证②生产纲领要能够满足③工艺成本最低④尽量减轻工人劳动强度五、设计工艺规程的步骤?①阅读图纸;了解产品、熟悉零件②工艺审查③选择毛坯④拟定机械加工工艺路线⑤确定设备和相应的工艺装备⑥确定各主要工序的技术要求和检验方法⑦确定各工序的加工余量、计算工序尺寸和公差。
⑧确定切削用量⑨确定时间定额⑩填写工艺文件第二节工艺路线的制订制订工艺路线考虑的主要问题?(1)怎样选择定位基准?(2)怎样确定加工方法?(3)怎样安排加工顺序、热处理工序、检验等其他工序?一、定位基准的选择?粗基准―加工的起始工序中,只能用毛坯上未经加工的表面作定位基准,则该表面称为粗基准。
精基准―利用已加工过的表面做为定位基准。
1、粗基准的选择A.保证相互位置要求的原则:为保证不加工表面与加工表面之间的相互位置关系,应首先选择不加工表面作粗基准,若零件上有多个不加工表面,则应选择其中与加工表面相对位置要求较高的不加工表面为粗基准。
B.合理分配加工余量的原则:对于具有较多加工平面的工件,粗基准选择时,应考虑合理地分配各表面的加工余量。
a.应保证各加工表面有足够的余量,应选择毛坯余量最小的表面作为粗基准b.对于某些重要表面,为了尽可能使其加工余量均匀,应选择该主要毛坯面作粗基准。
C.便于装夹工件的原则:为了使定位稳定、可靠,夹具结构简单,操作方便,作为粗基准的表面应不是分型面,应尽可能平整光洁,且有足够大的尺寸。
第四章 机械加工工艺规程设计

插键槽工序采用已镗孔的下切线为基准,用试切法保证插键槽深度,此深度尺寸应是上一工序直接保证的尺寸,磨孔工序应保证磨削余量均匀,定位基准为孔的中心孔。
因此ф50+0.030mm定
53.8+0.30定位基准与设计基准不重合,因此磨孔可直接保证ф
进行余量校核,画包含余量的加工尺寸联系图(图b),列包含余量的工艺尺寸
)所示,在尺寸链中,加工中余量由加工前后的实际尺寸间接求得,为封闭环。
四.工序尺寸与加工余量计算图表法工艺尺寸图表追踪法
节小结讲解不同情况下工艺方案的技术经济问题。
对同一加工对象的几种工艺方案计算技术经济指标,再加以分析进行比较,选出最经济者。
- 1、下载文档前请自行甄别文档内容的完整性,平台不提供额外的编辑、内容补充、找答案等附加服务。
- 2、"仅部分预览"的文档,不可在线预览部分如存在完整性等问题,可反馈申请退款(可完整预览的文档不适用该条件!)。
- 3、如文档侵犯您的权益,请联系客服反馈,我们会尽快为您处理(人工客服工作时间:9:00-18:30)。
第四章机械加工工艺规程设计双边余量:零件对称结构的对称表面,其加工余量一般为双边余量。
如:内外圆柱面和回转体表面。
余量公差:工序尺寸有公差,所以加工余量也必然在某一公差范围内变化,其公差大小等于本道工序尺寸公差与上道工序尺寸公差之和。
T Z =Z max -Z min =T b +T aT Z —工序余量公差Z max —工序最大余量Z min —工序最小余量T b —本道工序的工序尺寸公差T a ——上道工序的工序尺寸公差一般情况下,工序尺寸按“入体原则”标注。
这样表示,是为了使工件以公称基本尺寸为目标尺寸加工时,仍有可切除量,避免过切产生废品。
毛坯尺寸则按双向对称偏差的形式标注。
二.工序余量的影响因素第一道粗加工工序余量与毛坯制造精度有关。
毛坯制造精度高则第一道粗加工序加工工序余量小,毛坯制造精度低则第一道粗加工工序的加工余量就大。
其它工序的工序余量的影响因素有以下几个方面:1.上工序的尺寸公差Ta :本工序应切除上道工序尺寸公差中包含的各种可能产生的误差。
2.上道工序产生的表面粗糙度Ry 和表面缺陷层深度Ha :3.上工序留下的需单独考虑的空间误差εa :这些误差可能是上工序加工方法带来的,也可能是热处理后产生的,也可能是毛坯带来的。
4.本工序的装夹误差εb :定位误差和夹紧误差。
此项误差直接影响被加工表面和切削刀具的相对位置,所以加工余量中应该包括此项误差。
5.余量计算公式单边:双边: 三.加工余量的确定⎣⎦b a a y a e H R T Z ε++++=min ⎣⎦ba a y a e H R T Z ε++++=2/min1.增环公称尺寸,上下偏差照抄;2.减环公称尺寸变号,上下偏差对调、变号;3.取其代数和,得封闭环的公称尺寸,上下偏差。
公差重新分配问题:(1)当组成环公差之和≥封闭环公差,求解一个组成环时,可能出现零公差或负公差。
机械制造中,0公差或负公差不可能制造即不能出现。
应缩减其余组成环的公差解决问题。
(2)通常设计时,由给定的封闭环的公差决定各组成环的公差。
两种方法: Ⅰ、等公差法:取各组成环的公差值相等。
然后根据各环的加工难易程度适当调整。
Ⅱ、等精度法:按各组成环精度相等的原则求其组成环公差,可使尺寸大的公差大,尺寸小的组成环公差小。
避免等公差法缺点,但也是调整个别公差。
Ⅲ、经验确定法:组成环公差按工艺特点,根据具体情况而选。
无论哪种方法均需保证: 三.直线尺寸链在工艺过程中应用(一)工艺基准和设计基准不重合时工艺尺寸计算1.测量基准和设计基准不重合例:下图所示的车床主轴箱,两孔Ⅲ、Ⅳ中心距127±0.07mm 不便测量,只能用游标卡尺直接测量两孔内侧或外侧母线之间的距离来间接保证中心距之间的尺寸要求。
现采用测量两孔内侧母线的方法决定,求该测量尺寸应为多少,才能满足孔心距的要求。
求解:1)建立尺寸链,如图b 所示2)判断增环和减环,其中L0为封闭环。
L1、L2、L3为增环3)计算127=40+L2+32.50.07=0.002+ES2+0.015-0.07=-0.009+EI2+0得 只要实测结果在L2的公差范围内,就一定能保证Ⅲ、Ⅳ中心线的设计要求。
假废品问题:053.0061.025.54+-=L ∑-==11n i i o T T直线尺寸链极值算法是极限情况下的各尺寸之间的尺寸联系。
从保证封闭环的尺寸要求看,是保守算法。
计算结果可靠,但可能出现误判,出现假废品。
上例中若两孔的直径尺寸都取上限,即L1=40.002,L3=32.515时,L2做成L2 =54.5-0.087 时,则L1+L2+L3=126.93为中心距设计尺寸的下限尺寸,工件合格。
应用:为避免假废品的产生,发现实例尺寸超差时,应实测其他组成环的实际尺寸,然后在尺寸链中重新计算封闭环的实际尺寸。
原因:测量基准和设计基准不重合,组成环环数愈多,公差范围愈大,出现假废品的可能性越大。
因此应尽量使测量基准和设计基准重合。
2.定位基准和设计基准不重合例1:如下图所示某零件高度方向的设计尺寸12-0.070,,生产中用调整法加工A,B,C 面,前面工序A 、B 面已加工好,本工序以A 面定位基准加工C 面,问本工序调整尺寸应是多少?解题:C 面的设计基准(工序基准)为B 面,定位基准为A 面。
1)画尺寸链:如图b 所示。
2)确定封闭环,增环和减环:本尺寸链中调整法加工能直接保证尺寸为L2,L0间接保证。
则L0封闭环,L1增环,L2减环3)计算:L1是未注公差,为保证L0的计算,必须把L0公差分配给L1和L2。
采用等公差法分配:按入体原则标注L1公差为 计算L2的基本尺寸和偏差为(公式计算和竖式计算)……..(二)一次加工满足多个设计尺寸要求的工艺尺寸计算(工序间尺寸及尺寸链 ) 工序间尺寸链:机械加工过程中,零件尺寸的获得由一个先后的顺序,就某一尺寸而言,它是在加工过程中通过若干个工序,逐步切除余量而最后达到图纸设计要求的。
工序尺寸及其公差是根据设计要求考虑到加工中心的基准,工序间的余量以及工序的经济精度等条件,对各工序提出的尺寸要求。
工序间尺寸链是零件加工后最终尺寸及其公差和有关的工序尺寸和工序公差,以及工序间的余量有关尺寸联系构成一种工艺尺寸链。
035.02021===T T T 0035.0130-=L例1:一个带有键槽的内孔,设计尺寸如图a)所示,该内孔由淬火处理要求,因此有以下加工工艺安排:1.镗内孔至ф49.8+0.046mm2.插键槽3.淬火处理4.磨内孔,保证内孔直径ф50+0.030mm 和键槽深度53.8+0.30mm 两个设计尺寸的要求求淬火前插键槽的深度L2分析:插键槽工序采用已镗孔的下切线为基准,用试切法保证插键槽深度,此深度尺寸应是上一工序直接保证的尺寸,磨孔工序应保证磨削余量均匀,定位基准为孔的中心孔。
因此ф50+0.030mm 定位基准和设计基准重合,键槽深度53.8+0.30定位基准与设计基准不重合,因此磨孔可直接保证ф50+0.030mm ,而53.8+0.30则间接保证。
解算:…….说明:1) 本例把上工序镗孔和本工序磨孔的定位基准看作是同一中心线是近似要求,因为磨孔和镗孔是连两次装夹下完成,存在同轴度误差,若同轴度误差不是很小,则应将同轴度也作为一个组成环画在尺寸链中。
2)按设计要求键槽深度公差范围为0—0.30mm 。
但插键槽工序却只允许按计算出的尺寸公差进行,而计算值小于原键槽深度公差要求,即增加了加工难度。
原因是工艺基础与设计基准不重合。
因此在考虑工艺安排时,应尽量使工艺基准和设计基准重合。
(三)表面淬火,渗碳层表面及镀层,涂层厚度工艺尺寸链。
1.表面淬火、渗碳:对那些要求淬火或渗碳处理,加工精度要求又比较高的表面,常在淬火或渗碳处理之后安排磨削加工,为保证磨后有一定厚度的淬火或渗碳层,需要进行有关的工艺尺寸计算。
例:一轴类零件,外圆柱P 表面要求渗碳处理,t=0.5~0.8mm ,工艺安排如下:1.精车P ,保证 2.渗碳,控制渗碳层的深度3.精磨P ,保证尺寸 ,同时保证渗碳层的深度0.5~0.8mm 。
问渗碳层的深度及其公差应为多少?01.038-Φ0016.038-Φ2.电镀有些零件要求表面涂(镀)一层耐磨或装饰材料,完成后不再加工但有一定精度要求。
这时镀层厚度只通过控制电镀时间直接保证。
例:如下图所示,轴套类零件外表面需要镀铬,规定t=0.025—0.04mm ,镀层不加工,外圆尺寸 ,求电镀前磨削工序的工序尺寸。
(四)余量校核工艺过程中,加工余量过大会影响生产率,浪费材料,并且对精加工工序还会影响加工质量,但是加工余量也不能过小,过小可能造成零件表面局部加工不到产生废品。
因此,校核加工余量,对加工余量进行必要的调整是制定工艺规程时不可缺少的工艺工作。
例1:如图所示零件。
其轴向尺寸的30±0.02mm 的工艺安排为:1)精车A 面,B 处切断,保证两端面距离尺寸L1=31±0.1mm2)以A 定位,精车B 面,保证两端面距离尺寸L2=30.4±0.05mm ,精车余量为Z23)以B 定位磨A 面,保证两端距离尺寸L3=30.15±0.02mm ,磨削余量为Z34)以A 定位磨B 面。
保证两端距离尺寸L1=30±0.02mm ,磨削余量为Z4对Z2、Z3、Z4进行余量校核,画包含余量的加工尺寸联系图(图b ),列包含余量的工艺尺寸链,如上图(图C )所示,在尺寸链中,加工中余量由加工前后的实际尺寸间接求得,为封闭环。
四.工序尺寸与加工余量计算图表法工艺尺寸图表追踪法当零件在同一方向上加工尺寸较多,并需多次转换工艺基准时,建立工艺尺寸链,进行余量校核都会遇到,并且易出错。
图表法能准确查找全部工艺尺寸链,并且能把一个复杂的工艺过程用箭头直观的在表内表示出来。
列出有关计算结果清晰、明了,信息量大。
(一)尺寸追踪法(图表追踪法):就是将零件的加工过程建立工序尺寸之间的联系并用符号形象来描绘各个尺寸发生变化的情况,将其全部反映在一种图表上,利用这张图表来解决所要解决的问题。
(二)图表绘制的方法1.在图表上方绘制加工工件的轮廓简图,并用双点划线画出毛坯轮廓。
045.028-Φ课时安排 1课时 教学方法讲授法教学内容:第四章 机械加工工艺规程设计§4.5时间定额与提高生产效率的途径一、时间定额1、时间定额概念 在一定生产条件下,规定生产一件产品或完成一道工序所需消耗的时间。
2、时间定额组成基本时间t 基:直接改变生产对象的性质,使其成为合格产品或达到工序要求所需时间(包括切入、切出时间)。
以外圆车削为例:基本时间是切去金属所消耗的机动时间,可用公式计算,一般包括切入,切削加工和切出时间。
t 基= 其中:L —加工长度L1—切刀长度L2—切出长度f —进给量n —转速辅助时间t 辅:为实现工艺过程必须进行的各种辅助动作时间,如装卸工件、启停机床、改变切削用量及进退刀等。
确定方法:(1)大批量生产:先将各辅助工作分解,然后查表确定各动作所需消耗的时间、再累加。
(2)中小批量生产中,按基本时间的百分比估算,并在实际中保证。
操作时间=基本时间+辅助时间 t 操作= t 基+ t 辅布置工作地时间t 布置:为使加工正常进行,工人照管工作地所消耗的时间(包括更换刀具、润滑机床、清理切屑、收拾工具等)。
t 布置= (2%—7%)t 操作休息和生理需要时间t 休:在工作班内,为恢复体力和满足生理需要所需时间,t 布置=2% t 操作准备终结时间t 准终:工人为了生产一批产品和零部件,进行准备和结束工作所消耗的时间,包括:熟悉工艺文件、领取毛坯、安装夹具、调整机床、发送成品等。