冷轧薄板罩式退火过程粘结的分析和工艺改进
八钢冷轧带钢罩式炉退火粘结缺陷原因分析及防范措施

八钢冷轧带钢罩式炉退火粘结缺陷原因分析及防范措施【摘要】本文对冷轧带钢在罩式炉中退火产生粘结缺陷的机理进行了分析,指出钢带卷径向存在温度梯度,在冷却初始阶段冷缩变形不均匀是产生粘结的主要原因,同时分析了影响粘结倾向的各种因素,并提出应对措施。
【关键词】粘结;温度梯度;冷却初始阶段1.前言冷轧带钢经罩式炉再结晶光亮退火后可消除冷变形产生的加工硬化和内应力,使带钢具有符合标准的金相组织、良好的机械性能和光亮的表面。
但带钢在退火过程中有时产生局部粘结,造成平整开卷时粘结处发生撕裂变形、凸起,经平整后形成弯月状、马蹄状或弧形的凹印。
因粘结处变形产生加工硬化、塑性降低,使带钢产生部分或整卷的废次品。
因此,如何减少粘结产生的废次品,提高成材率,降低成本是迫切需要解决的问题。
2.粘结缺陷的形成机理罩式炉中钢带卷受热主要来自内罩的热幅射和保护气体的热对流。
因钢带卷紧卷退火,保护气体经端面向层间传热明显不如内、外表面,故在钢带卷径向形成温度梯度。
因加热时钢带卷内、外层升温速度大于心部,故内、外层的热胀大于心部,使外层与心部间压应力减小,内层与心部间压应力增大。
尽管随着温度的升高,内层与心部的温度梯度增大,压应力也随之增大,但此时卷心处于回复或再结晶形核阶段,其屈服极限降低不大,层间压应力仍低于屈服极限,故不产生塑性变形。
同时氢气在600℃左右才能与氧化物有效反应,故此时钢带卷层间接触处仍存在氧化膜,可阻止粘结的产生。
随着再结晶的进行,钢带卷屈服极限迅速降低,但同时内层与心部的温度梯度逐渐减少,压应力也随之减小。
因此,在加热阶段钢带卷层间产生粘结的可能性很小。
在冷却阶段,因内外层温降速度大于心部,使外层与心部层间因冷缩不均匀产生较大压应力。
尤其在冷却初始阶段,温度梯度逐渐增大,压应力也随之增大。
当卷心温度降至一定温度时(根据大量退火曲线的统计结果,此温度在600℃左右),卷心与外层温度梯度最大,压应力也最大。
因钢带卷经再结晶后屈服极限大幅降低,故在卷心温度由峰值降至600℃过程中,钢带卷层间局部凸起处(主要由带钢浪形或同板差过大引起)在压应力作用下产生塑性变形,使层间紧密接触面积显著增大。
冷轧罩退产品缺陷分析及改进措施

冷轧罩退产品缺陷分析及改进措施摘要:冷轧罩退的粘结缺陷问题是较为常见的一种问题,冷轧罩式退火工艺可以避免受到品种规格的限制而表现出良好的应用特性,能够有效的减少粘结缺陷问题,文章就此展开分析。
关键字:冷轧;罩退;粘结1、前言冷轧罩式退火工艺在连续退火技术快速发展的过程中,依然由于其良好的应用范围和灵活的生产过程而得到了较为广泛的应用,不仅投资较少,同时能耗也相对较低,文章就此分析其生产的产品缺陷问题,以及具体的改善策略。
2、产品缺陷问题2、1刮擦冷轧钟形退火是传统的退火工艺,在后热处理技术的商业化时代,钟形退火工艺仍然存在。
它对带钢的规格和高质量品种不受各种限制。
生产非常灵活,应用的技术非常广泛。
该技术更加成熟,投资少,能耗低。
钟型退火是分批式堆叠退火,有单层堆叠和多层堆叠两种类型。
唐山钢铁集团有限责任公司的表面回流设计方法是单反应器全氢全气氛热处理。
在表面返回过程中最常见的明显缺陷是粘结。
简而言之,粘结实际上是将退火的钢带彼此粘结在一起,压扁后,发现点弧变成点棒,沿轧机方向成排的弧形折痕。
自从唐钢冷轧厂在达到生产能力以来,这种粘结不仅会影响带钢外表面的质量,而且在测试不均匀闭合线圈时甚至会造成刮擦,并成为废卷,更严重的钢粘结现象可能导致带钢产品切割损失,这将严重影响生产过程的经济效益。
2、2异物压入在热轧过程中,当粗轧道次导致具有更大孔隙率和明显缺陷的连铸板坯变形时,板坯拐角零度以下的中间位置区域已超过板坯的局部塑性极限材料在侧压力作用下变形,并确实形成了拐角裂纹。
在第一个变形过程中无法在板坯过程中焊接这样的小裂纹,然后沿着板坯方向形成断续的叠层,并随着板坯中间的翻边过程而旋转到板坯的两侧。
最后,它主要分布在距离热轧板边缘20-30mm的区域。
同时,在热轧并压入带材表面后,材料表面仍残留有疤痕,或者板坯表面发火,清洁的长宽比确实是不够的,轧制的表面更严重地被刮伤,并且坯料再次被浇铸,这也会在带钢表面形成疤痕。
碳钢冷轧罩式退火炉粘接缺陷种类及原因分析
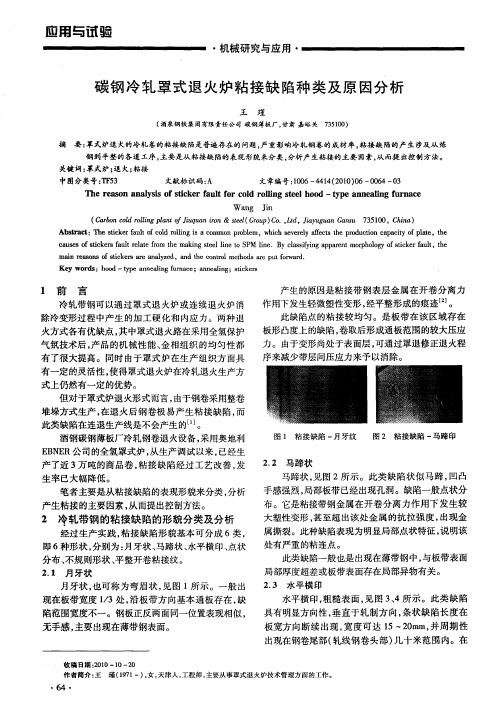
( abncl rln ln o i u ni n&s e( r p C .Id J yg a as 7 5 0 ,C i ) C ro o l gpatfJ q nG nu 3 10 h a e u z a n
火方 式各 有优 缺点 , 中罩 式退火 路在采用 全氢保 护 其 气氛 技术后 , 品 的机 械性 能 、 相组 织 的均匀 性都 产 金
产 生 的原 因是粘 接 带钢 表 层金 属 在 开卷 分 离 力 作用下 发生轻微 塑性变形 , 经平 整形 成 的痕 迹 J 。 此 缺 陷点 的粘 接 较均 匀 。是 板带 在 该 区域 存 在 板形 凸度上 的缺陷 , 卷取后形 成通 板范 围的较大 压应 力 。 由于变形 尚处 于表面层 , 可通 过罩退修 正退 火程 序 来减少 带层间压应 力来 予 以消 除 。
应用 与i 式验
・
机械研究与应用 ・
碳 钢 冷 轧 罩 式 退 火 炉 粘 接 缺 陷 种 类 及 原 因分 析
王 瑾
( 酒泉钢铁 集团有限责任公 司 碳钢薄板厂 , 甘肃 嘉峪关 75 0 ) 3 10
摘
要 : 式炉退 火的冷轧卷的粘接缺 陷是普遍存在的 问题 , 罩 严重影响冷轧钢卷的成材率 , 粘接 缺陷的产生 涉及从 炼 钢到平整的各道.序 , T 主要是从粘接缺 陷的表现形貌来分类, - 分析产生粘接 的主要 因素 , 而提 出控制方法。 从
K e o ds:h o —tpe a n ai g f r c yw r o d y n e ln una e;a ne lng;sik r n ai tc e s
1 前 言 冷轧 带钢可 以通 过 罩 式退 火 炉或 连 续退 火 炉消 除冷 变形过 程 中产 生 的加 工 硬 化 和 内应 力 。两 种退
冷轧板退火过程中的粘结问题及解决措施
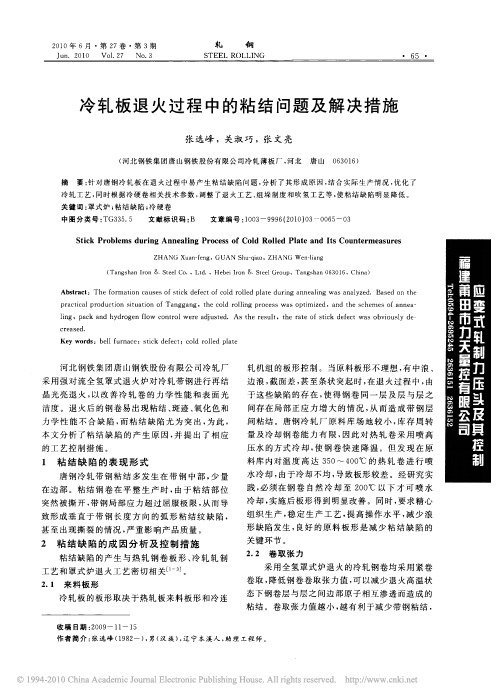
1
粘结 陷的表现形式
唐 钢冷 轧带 钢 粘 结 多 发 生 在 带 钢 中 部 , 少 量
在边 部
粘结 钢 卷 在 平 整 生 产 时 , 由于 粘 结 部 位
突然 被撕 开 , 带钢 局部 应 力超 过屈 服极 限 ,从 而 导 致 形 成垂 直 于带 钢 长 度 方 向 的弧 形 粘 结 纹缺 陷 , 甚 至 出现 撕 裂的情 况 , 严重 影 响产 品质 量
势就 越 明显 , 处 于底 部就越 易粘 结 因此 , 在 生产 h 镇0. 7m m 薄 规格 钢 卷 时 , 罩退 机 组 采 用 人 工 组
规格 的卷取 张力 制度 见表 1
冷硬卷的卷取张力
0.40 ~ 0.50 3.5 0.50~ 1.15 3.0 ) 1.15 2.7
表2
SP C C 钢 不 同 规 格 带钢 的 退 火 工 艺 制 度
热点 / 冷点 / ∃ 十缓 冷 时间 / h
700/620 + 3 7 0 0 / 6 10 + 2 6 90 / 6 10 + 2
力 , 以减少粘 结 缺 陷 表 2 为 SP CC 钢种不同规 格 带钢 的退火 工 艺制度
缘粘结 , 不 仅不 利 于后 工 序开 卷 , 而且 会降低 产 品 成材率 根 据生 产 实际 , 经过 多次调 整 , 不 同产 品
表 1
产 品 厚 度 /m m 卷 取 张 力 /M P a 毛0. 40 4 .5
别 为 6 20 7 10 0 , 经 过 跟 踪 产 品 性 能 , 厚 1. om m C 规 格退 火卷 的伸 长率 为 4 % 一4 % (标准 3 % ), 6 7 厚 1. sm m 规 格 退 火 卷 的 伸 长 率 为 4 % 一 4 % 9 (标准 3 % ) , 远 远 高 于标 准要 求 8 经统计, 唐钢
碳钢冷轧罩式退火炉粘接缺陷种类及原因分析

( 1) 通过缓冷措施, 可有效降低薄带钢的粘接缺 陷发生的几率。 ( 2) 虽然缓冷措施可以大幅减少薄带钢出现粘 接的几率, 但很难根除, 每个钢卷本身表面的条件也 决定了粘接的发生倾向, 因此需从酸轧机组及前道工 序对钢卷板面状态进行控制。 ( 3) 平整机在厚带钢出现粘接时, 应适当增加开 卷速度 , 减少平整轧机降速、 增速的时间。 ( 4) 酸轧机组需控制带钢冷轧后表面的残铁量 , 信 息
[ 3]
。
图 7 粘接缺陷 - 不规则点块状
图 8 不规则点块 状
应用与试验
机械研究与应用 4 工艺条件的影响分析及改善措施
根据在平整过程 出现的粘结缺陷, 联系酸 轧过 程、 退火过程的工艺条件, 发现当前工艺执行过程中 存在诸多不利因素, 针对不利因素, 采取了相应措施 , 以求改善粘接的发生率。具体分析见表 1 所示。
( Carbon cold rolling p lan t of J iuquan iron & steel(G roup )C o . , L td, J iayuguan Gansu 735100 , Ch ina) Abstrac t : The sticke r fau lt o f co ld ro lling is a co mmon proble m, w hich seve re ly affec ts the produc tion capacity of p late , the causes o f stickers fault relate from the m aking stee l line to SP M line . By class ify ing apparent m orpho logy o f sticker fau lt , the m a in reasons o f stickers are ana lyzed, and the control m ethods are put for w ard. K ey word s : hood- type annea ling fu rnace ; annea ling ; sticke rs
HPH退火带钢粘结问题分析和措施

HPH退火带钢粘结问题分析和措施HPH, 带钢, 措施, 退火, 粘结HPH退火带钢质量问题分析研究表明,不同类型的黏结由不同因素引发,而罩式退火工序经常被认为是产生黏结的唯一原因。
本文讨论各种类型的黏结产生机理以及预防措施。
全世界众多企业因黏结问题引起的损失高达10%。
大型轧钢厂一直致力于黏结问题及其产生过程的研究,目前已经使黏结率平均下降到1%以下。
引言现代技术的罩式退火炉中生产的退火薄钢板实现了最高的质量要求。
就拉伸性而言,材料力学性能已达到最优化,即屈服强度低、伸长率高、Lankfort系数(厚向异性)高。
同时,罩式退火炉(见图1)能够保证表面没有任何缺陷。
自低强度钢板有黏结敏感倾向后,避免黏结疤痕成为质量方面的主要目标。
一、黏结的分类“黏结”是描述材料塑性变形或流动以及扭折痕迹的综合词汇,在开卷时钢带未到达平整机轧缝前,就能清楚地看到带钢上这些流动和扭折痕迹。
黏结由金属裸露表面的压力焊合产生。
目前对焊合是否由两个面的烧结过程或其它黏结装置之间的扩散焊合过程引起,还没有明确结论。
然而,研究已经发现了各种类型的黏结现象。
而且产生此类缺陷的机理也已探明。
1.脊黏结脊黏结是带材宽度上非常有限的一些缺陷。
这些黏结主要由带材轮廓异常(如隆起)引起,从而在钢卷内部产生很高的辐射状压力。
2.点黏结点黏结只限于带材上的局部点。
产生的主要原因是局部压力过高(如钢卷夹具引起),以及无意间外来物体裹挟进钢中,这在开卷时能明显看到。
3.边部黏结顾名思义,边部黏结发生在带材边部。
它们是带材边部非常有限的裂痕,由钢卷和对流加热器平板或载流子之间的相对运动产生,结果这些部分和钢卷的加热、冷却速率产生偏差。
此外,钢卷处理上产生的破坏,如表面不平也能引起边部黏结。
使用硬度更高的高锰含量的平板式对流加热器可减少边部黏结。
平板式对流加热器和载流子的设计也很重要。
输送面积大于50%的平板式对流加热器能够使薄带材(厚度<0.7mm)上的边部黏结最小化。
冷轧带钢的退火缺陷及原因分析
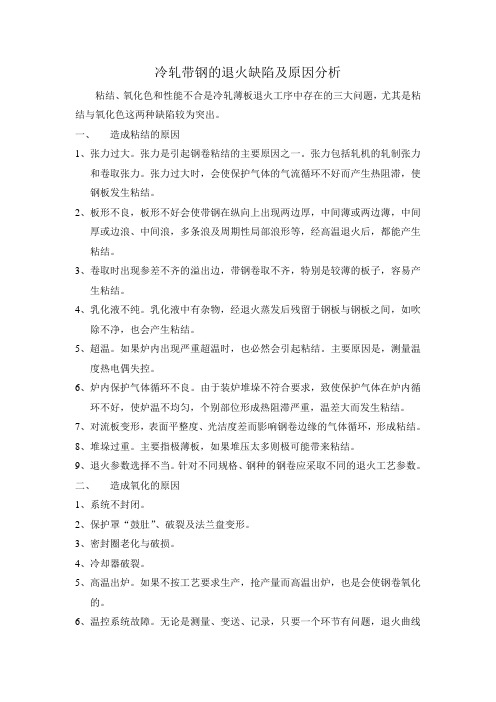
冷轧带钢的退火缺陷及原因分析粘结、氧化色和性能不合是冷轧薄板退火工序中存在的三大问题,尤其是粘结与氧化色这两种缺陷较为突出。
一、造成粘结的原因1、张力过大。
张力是引起钢卷粘结的主要原因之一。
张力包括轧机的轧制张力和卷取张力。
张力过大时,会使保护气体的气流循环不好而产生热阻滞,使钢板发生粘结。
2、板形不良,板形不好会使带钢在纵向上出现两边厚,中间薄或两边薄,中间厚或边浪、中间浪,多条浪及周期性局部浪形等,经高温退火后,都能产生粘结。
3、卷取时出现参差不齐的溢出边,带钢卷取不齐,特别是较薄的板子,容易产生粘结。
4、乳化液不纯。
乳化液中有杂物,经退火蒸发后残留于钢板与钢板之间,如吹除不净,也会产生粘结。
5、超温。
如果炉内出现严重超温时,也必然会引起粘结。
主要原因是,测量温度热电偶失控。
6、炉内保护气体循环不良。
由于装炉堆垛不符合要求,致使保护气体在炉内循环不好,使炉温不均匀,个别部位形成热阻滞严重,温差大而发生粘结。
7、对流板变形,表面平整度、光洁度差而影响钢卷边缘的气体循环,形成粘结。
8、堆垛过重。
主要指极薄板,如果堆压太多则极可能带来粘结。
9、退火参数选择不当。
针对不同规格、钢种的钢卷应采取不同的退火工艺参数。
二、造成氧化的原因1、系统不封闭。
2、保护罩“鼓肚”、破裂及法兰盘变形。
3、密封圈老化与破损。
4、冷却器破裂。
5、高温出炉。
如果不按工艺要求生产,抢产量而高温出炉,也是会使钢卷氧化的。
6、温控系统故障。
无论是测量、变送、记录,只要一个环节有问题,退火曲线所记录的温度就不会准确,这也是氧化的重要因素。
7、保护气体吹洗不充分,内罩里和外部快冷系统里的空气排除不干净。
另外,如果是残留乳化液过多或湿度较大的钢卷,则吹洗时间应比一般情况下要多一些,否则也达不到光亮退火。
8、在刚开始喷淋快速冷却时,分流的保护气体由于冷却后其体积突然缩小而造成炉内压力差引起内罩负压,而导致空气侵入。
9、保护气体露点高。
露点高的,说明保护气体中含水量高,这必然会给退火钢卷带来氧化色。
低合金钢冷轧薄板的退火工艺优化研究
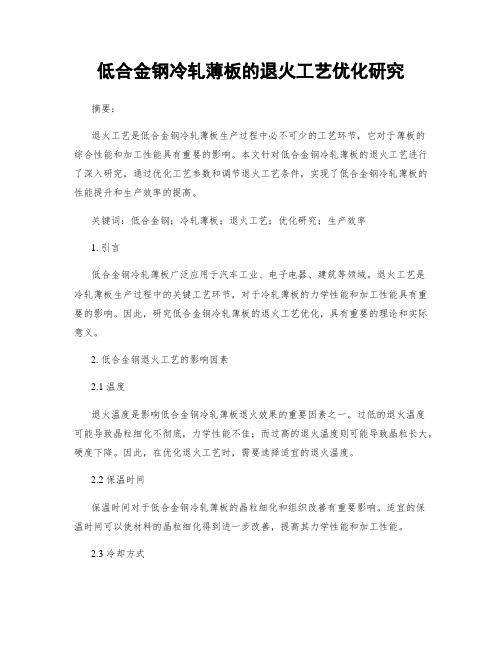
低合金钢冷轧薄板的退火工艺优化研究摘要:退火工艺是低合金钢冷轧薄板生产过程中必不可少的工艺环节,它对于薄板的综合性能和加工性能具有重要的影响。
本文针对低合金钢冷轧薄板的退火工艺进行了深入研究,通过优化工艺参数和调节退火工艺条件,实现了低合金钢冷轧薄板的性能提升和生产效率的提高。
关键词:低合金钢;冷轧薄板;退火工艺;优化研究;生产效率1. 引言低合金钢冷轧薄板广泛应用于汽车工业、电子电器、建筑等领域。
退火工艺是冷轧薄板生产过程中的关键工艺环节,对于冷轧薄板的力学性能和加工性能具有重要的影响。
因此,研究低合金钢冷轧薄板的退火工艺优化,具有重要的理论和实际意义。
2. 低合金钢退火工艺的影响因素2.1 温度退火温度是影响低合金钢冷轧薄板退火效果的重要因素之一。
过低的退火温度可能导致晶粒细化不彻底,力学性能不佳;而过高的退火温度则可能导致晶粒长大,硬度下降。
因此,在优化退火工艺时,需要选择适宜的退火温度。
2.2 保温时间保温时间对于低合金钢冷轧薄板的晶粒细化和组织改善有重要影响。
适宜的保温时间可以使材料的晶粒细化得到进一步改善,提高其力学性能和加工性能。
2.3 冷却方式冷却方式是影响低合金钢冷轧薄板组织和性能的重要因素。
不同的冷却方式对晶粒的长大和相变过程具有不同的影响。
水冷是一种常用的冷却方式,可以使晶粒得到更好的细化,提高低合金钢冷轧薄板的强度和韧性。
3. 低合金钢冷轧薄板退火工艺优化方法3.1 基于试验设计的工艺优化通过设计试验矩阵,分析不同工艺参数对低合金钢冷轧薄板性能的影响,确定最佳工艺参数组合。
采用正交试验设计等方法,有效地减少了试验次数,提高了工艺优化的效率。
3.2 数值模拟优化利用有限元数值模拟方法,对低合金钢冷轧薄板的退火工艺进行数值模拟,分析退火过程中的温度场和应力场,预测材料的织构、晶粒大小以及相变行为。
通过优化数值模拟结果,确定最佳的退火工艺参数。
3.3 综合优化方法结合试验设计和数值模拟方法,进行综合优化。
宝钢冷轧板粘结成因分析及消除对策探讨

宝钢冷轧板粘结成因分析及消除对策探讨黄皆捷吴彬摘要:分析了宝钢冷轧薄板粘结的形成缘故,与生产中各工序产生的应力和带钢本身的物理性能有关,即与轧机卷取应力、轧后冷却应力、板形应力、板凸度应力、退火过程内在热应力、平坦开卷应力、带钢表面粗糙度和带钢的强度有关.通过对相关因素的讨论,找出了实际生产中解决粘结问题的方法,实施后取得了显著成效.关键词:冷轧带钢;粘结;应力Analysis of the causes of sticking of cold rolled strip and research onelimination measuresHUANG Jie-jie,WU Bin(Cold Rolling Dept., Baoshan Iron & Steel(Group) Co., Shanghai200941,China)Abstract:The sticking of cold rolled strip is related with the physical properties of strip itself and stress, which is in~duced by coiling, cooling, harmful shape, convexity, annealing, uncoiling and the coarse degree of strip surface and strip strength. The measures of eliminating sticking are found after analyzing these factors, and the application result is effective.Keywords:cold rolled strip; sticking; tress冷轧薄板的粘结是宝钢冷轧产品的要紧质量缺陷之一,严峻阻碍了宝钢冷轧产品的收得率和O5板的质量.为此,对其形成机理及防止计策进行了探讨.1 带钢粘结的应力-温度曲线带钢粘结产生的机理是:卷紧的钢卷在罩式炉退火过程中,在高温条件下由于应力作用,边界原子相互渗透因而使带钢层与层之间产生粘连和焊合现象.在实验室中,应用叠片试验,通过高温加压,可测出不同温度对带钢发生粘结的临界应力,从而绘出带钢粘结的应力-温度曲线.不同钢种,其曲线略有不同.一样强度高的钢种,在相同温度时粘结应力略高.在粘结应力-温度曲线中,温度越低,曲线变化越平缓;温度越高,应力值下降越快.用该曲线可推测粘结的发生.在退火过程中,应使带钢层与层之间的径向应力值落在曲线的下方安全区域.带钢粘结的形成与各工序产生的应力及带钢本身的物理性能有关,包括轧机卷取应力、轧后冷却应力、板形应力、板凸度应力、退火过程内在热应力、平坦开卷应力、带钢表面粗糙度和带钢的强度.图1 粘结应力-温度曲线2 带钢卷取张应力及阻碍因素2030mm冷连轧机的卷取特点:钢卷直径为Φ610~Φ1049mm时,张力为卷取设定值的150%;在Φ1050~Φ1100mm段,张力线性下降;在Φ1151~Φ2470mm 段,采纳设定张力卷取.把每层钢卷想像成理想状态,即薄壁筒,运算层与层之间的径向压应力.除去边部一小部分带钢,则中部处于平面应变状态.依照弹性力学理论,切向张应力σ1=σq,即径向应力值与卷取张应力值相等.卷取张应力的阻碍因素:(1)板形的阻碍在生产过程中,带钢不可幸免地存在局部浪形,因此沿带钢宽度方向的卷取张应力不可能处处均布,假设全宽1000mm的带钢,距两侧边100mm范畴内各有纵向间距1000mm、高4mm的边浪,则带钢中部与边部的应力差为6.40MPa;假如原带钢单位卷取张力设定为32.00MPa,则中部张应力为31.28MPa;边部张应力为24.88MPa.故带钢板形对卷取张应力的分布起到了不可忽视的作用.当板形极差,会造成浪形处卷取张应力为0,无浪形处的张应力将可能远大于单位卷取张力,即造成钢卷局部径向应力σ1较大.(2)轧后冷却的阻碍带钢在轧制过程中,其中部和边部的受热和散热状况不同,一样而言,轧辊中部温度高,故带钢中部易受热,而在末机架出口,假设乳化液吹扫极洁净,其中部散热相对较慢,故在板形测量仪处测得的板形,是带钢轧后热态板形,这时带钢中部与边部的温差一样为2~5℃,带钢卸卷冷却后,随着板温各个部位的趋同,卷取张应力的分布将有所改变,σ2表示线性温降对卷取张应力的阻碍:σ2=EαT(2) 式中,E为弹性模量,此值为200×103MPa;α为带钢的热胀系数,低碳钢为14×10-6;T表示带钢与边部点(距边部25mm)在通过板形仪时的温差.则σ2=5.6~14MPa.由此可见,带钢轧后温度的分布对卷取张应力分布的阻碍不可忽视,假如轧机设备显现专门,中间板温明显过高时,其卸卷冷却后,中部卷取张应力将成倍于轧机设定的单位卷取张力.3 钢卷在罩式炉退火过程中的应力分析(1)差不多热应力分析在罩式炉退火过程中,钢卷在炉内立放,层与层之间包紧致密,没有相对位置变化,故可先作为整体考虑.由热弹性理论可知,径向应力σr =σh+σt(3)式中,σh 为热应力;σt为弹性应力.图2 钢卷示意图关于钢卷退火,一样在800℃以下,应力应变关系不受温度阻碍,其模型可简化为热弹性准静力问题.由于带钢除边部小部格外,中部处于平面应变状态,故模型为平面应变状态下的热弹性准静力问题,则考虑钢卷外侧的边界条件:σr=0,有(4)式中,T1为钢卷内孔侧壁温度;T2为钢卷外侧温度;T3为钢卷单侧中心点温度(在加热过程中,其温度为钢卷中最低,而冷却时则为最高,一样称冷点);r1为钢卷内半径;r2为钢卷外半径;r3为冷点半径.由于宝钢罩式炉退火时,钢卷内径为Ф610mm,外径最大值为Ф2470mm,则可简化为:σn =0.056αE〔7.5(T1-T2)-2.6(T3-T2)〕(5)依照宝钢生产中试验用炉台热电偶测定值,运算冷点在加热段和冷却段热应力值,结果得出:不管在加热段依旧冷却段,热应力在冷点均为正值,但随内外温差的增大,冷却段的热应力将变得专门大,为卷取张应力的8~10倍.(2)阻碍热应力的因素从式(4)中发觉,热应力值要紧取决于T1、T2、T3的温度差.在加热段,由于罩式炉本身气流的特点,T1、T2温差可不能专门大,因此要紧依靠缩小T3、T2温差来实现减小热应力.在冷却段,三者温差均专门关键,温差越小,越有利于减小热应力.通过对加热段和冷却段的运算分析得出,由于加热段T1、T2和T3、T2的温差相互正负补偿作用明显,故其热应力值远小于冷却段,因而可知:宝钢罩式炉冷却开始时期的热应力是造成钢卷发生粘结的要紧缘故.减少T3、T2温差,使温度在钢卷中尽可能平均分布,其要紧阻碍因素有:(1)钢卷退火过程中罩式炉爱护罩内的热传导性钢卷在罩式炉退火过程中,由于层与层之间的热阻专门大,故要紧导热方式是通过上下端面进行的,上下端面导热量越大,带钢内温度分布越平均,否则将导致T3与T2的庞大温差.为增加上、下端面的导热量,最好的方法是增加流经上、下端面的爱护气体流速,从而加强端面导热.增加气流流速的方式:①增大罩式炉底循环风机功率及转速;②适当减薄对流板的厚度,使气体流速和气流热效应有效高度呈最佳组合.(2)钢卷加热和冷却的速率钢卷退火冷却段速率适当放慢,专门是冷却开始段,当钢卷温度专门高时,要保证炉内爱护气体充分循环,使钢卷内部温度分布平均.现在宝钢罩式炉作业区有3种类型的退火炉,分别为LOI3%氮氢炉、LOI全氢炉、EBNER全氢炉,其退火曲线及数学模型由外商提供.宝钢认真对比研究了3种工艺退火曲线,从钢卷退火过程中升、降温平均性动身,取长补短,进行了改进,最终确定了较符合宝钢生产实际的、较合理的退火曲线.4 带钢板凸度分析带钢板凸度的分布和大小极大地改变了钢卷的径向应力分布.假如带钢呈理想状态,厚薄绝对平均,则径向力如(1)式所示,即为卷取张应力.事实上,由于存在带钢凸度,中部径向应力远大于理想状态.由于板形凸度分布的多样性和测量问题,目前尚不能对其径向应力有较合理的运算分析.由生产数据来分析,宝钢热轧来料2%的凸度是一个临界点,凸度大于2%的钢卷粘结发生率几乎为小于2%时的2倍.5 带钢表面粗糙度带钢表面粗糙度有2个表征量,一个是粗糙度大小读数Ra,另一个是单位面积峰值数PPI.相同的Ra读数会有不同的PPI值.实验测定,粗糙度Ra数值越大,越有利于幸免粘结,这是因为粗糙度值增大了钢卷层与层间界面原子间的结合阻力.实验统计结果显示,相同的Ra值时,PPI值也有较明显的阻碍力,过大或过小的PPI值,均不利于幸免粘结,这与边界微观外貌造成的界面原子间的结合能大小有关.6 平坦开卷应力平坦开卷应力要紧是指瞬时的开卷张应力.粘结尽管是带钢层与层的粘连,但适当的开卷角度专门关键,即使开卷张力不变,适宜的开卷角度仍对幸免粘结有一定作用.开卷时,应尽可能使带钢沿钢卷切向打开,使张应力中的切向重量尽可能大些,通过切向应力使带钢层与层间的附着有所松动.较大的法向开卷应力会造成粘连带钢的开卷拉损,显现粘结印迹,严峻阻碍带钢外观.在平坦过程中,增大平坦量也有利于修复发生粘连的带钢表面,但不利于产品的深冲性能.考虑到金属变形的硬化效应,可提高平坦速度,通过瞬时开卷大变形,提高带钢的抗拉强度,从而幸免带钢表面平坦时的受力损害.7 板形的再分析前面讨论了板形对钢卷径向应力的阻碍,但并不完全.上述讨论引伸出的结论是:中浪板形有利于减轻带钢中部的径向应力,从而缓和中部粘结.而宝钢的统计数据说明,中浪板形反而易引发粘结,其缘故有2点:(1)中浪板形在卷紧后,造成带钢层与层间接触面的贴合不完整,从而使径向压应力分布不均,局部径向压应力增大,而较大中浪造成的较大径向压应力促使了粘结的发生.(2)边浪板形一样使边部带钢变薄,显现微小的缝隙,有利于罩式炉内爱护气体这一导热介质进入并交换热量,而中浪板形不仅阻止了导热介质进入,同时由于中部微小缝隙的存在,增大了带钢层与层间的热阻,反而阻碍了沿内外径热量的导入,造成了较大的热应力.8 计策和成效从上述研究分析中,能够得出:在宝钢,所有形成粘结的缘故中,罩式炉加热过程中形成的热应力是专门关键的因素.从初步理论运算可知,目前其热应力相当于卷取张应力的8~10倍.因此,欲解决粘结问题,不能单纯用减小卷取张力的方法,而减小热应力是当务之急.与此同时,其它阻碍因素也不可忽视.从上述分析中可知,如当板形应力在板形极差时,其阻碍是卷取张应力的几倍.当解决了热应力问题后,其它因素会变得突出,其专门小的阻碍可能会造成较大后果.宝钢解决粘结问题采取了以下措施:(1)保证生产过程中冷轧机组末机架工作辊的粗糙度,保证轧机出口钢板表面粗糙度;(2)冷轧机出口板形必须是微边浪,不承诺中浪板形流入罩式炉.(3)规定薄料在平坦时采纳穿S辊的平坦方式.(4)提高平坦速度;(5)在罩式炉生产时,采纳新的退火工艺操作规范;(6)在保证后道机组生产的基础上,尽可能减小轧机出口卷取张力.作者简介:黄皆捷(1968~)男(汉族),上海人,高级工程师,从事冷轧综合技术主管工作.作者单位:宝山钢铁(集团)公司冷轧部,上海200941参考文献〔1〕杜庆华、余寿文,姚振汉著.弹性理论〔M〕.北京:科学出版社,1986.10. 〔2〕徐芝纶著.弹性力学简明教程(第2版)〔M〕.北京:高等教育出版社,1983.10.〔3〕陶文铨主编.传热学基础〔M〕.北京:电力工业出版社,1981.10. 〔4〕Reo T K, Barth G J, Miller J R. Computer model pre-diction of heating, soaking and cooling time in batch an-nealing[J].Iron and steel Engineering, 1983.。
SPCC冷轧薄板退火工艺的优化与性能分析(1)

致抗拉强度偏高,伸长率偏低。 工艺优化后的组织晶
粒较均匀,长大充分,基本形成了等轴晶。
(a) 改进前
(b) 改进后
×150
×150
图 3 工艺改进前后的金相组织
Fig.3 The microstructure of steel coil before and
after process improvement
172
Hot Working Technology 2010, Vol.39, No.08
下半月出版
Material & Heat Treatment 材料热处理技术
由图 3 可看出,工艺改进前金相组织(即性能不 合格钢卷金相组织)晶粒分布不均匀,长大不充分, 部分组织呈条状,较细小,未形成均匀的等轴晶,导
Abstract:The reason of low-qualifying rate of capability and growing-to-full-size rate of finished products for SPCC sheet of cold rolling were analyzed. The defect that annealing course produces is the major reason that causes useless substandard products. Through adopting the measure of optimization annealing technology, the annealing defect drops obviously. Therefore, the qualifying rate of capability and growing-to-full-size rate of finished products of cold rolling SPCC sheet are effectively raised.
浅谈罩式退火粘结的产生原因及控制措施

浅谈罩式退火粘结的产生原因及控制措施罩式退火钢带粘结缺陷是指冷轧退火钢卷相邻层之间相互粘和在一起,造成钢卷开平时钢板表面变形、损伤、甚至撕裂的缺陷。
为了生产出高质量的冷轧薄带钢,有效控制粘结的产生是极其重要的生产环节。
罩式退火粘结缺陷一般是在冷却阶段初期产生的,产生的机理是由于带钢卷层间在高温度、高应力下长时间相互压合,形成类似压力焊接的条件产生局部焊合,形成钢带表面粘结。
罩式退火工艺参数如加热温度、高温阶段冷却速度、保护气体种类;冷轧工艺如卷曲张力、板形、粗糙度、表面残留物;钢卷材质和规格都对罩式退火粘结产生影响,粘结程度是各方面综合作用的结果。
合理控制诸因素可以减轻或消除粘结。
退火工艺对粘结的影响是直接通过温度和时间的作用,但间接地是通过钢卷中由温度场产生的热应力来影响粘结的形成。
退火工艺中采用的保护气体种类,也是影响钢带表面粘结的因素。
目前罩式退火炉使用的保护气体主要是氮氢型保护气体和全氢型保护气体。
对于强对流全氢罩式退火炉来讲,使用全氢型保护气体,由于氢气的热导率是氮氢型保护气体的数倍,加上强烈的对流热交换,可大大缩短退火周期。
同时由于氢的高渗透性,全氢又可改变钢卷温度场分布,降低钢卷内外温差,使钢卷在实现光亮再结晶退火的同时有效地减少了钢卷的粘结。
为了保证产品质量应尽可能选用全氢罩式退火炉退火。
而表面残余的氧化铁粉在全氢高温还原气氛下将被还原成微细的纯铁粉颗粒,反应式为FeO + H2 = H2O + Fe。
这些微细纯铁粉颗粒在层卷间充当“焊接剂”使得紧紧压合在一起的卷层更容易“焊合”在一起,形成粘结。
降低卷曲张力,增加层间间隙,可以改善传热条件,缩小钢卷内外加热、冷却时的速度差,降低钢卷内外温差。
因此降低轧钢卷取张力值,可以有效减少退火高温状态下钢卷层与层之间边部原子相互渗透而造成的粘结。
卷取张力值越小对减少粘结越有好处,但过小会造成钢卷卷形不好,扁卷、松卷、散卷等,同时影响平整生产,平整时易产生钢卷层间滑动造成擦伤缺陷。
冷轧罩式退火炉设备改进与工艺技术优化
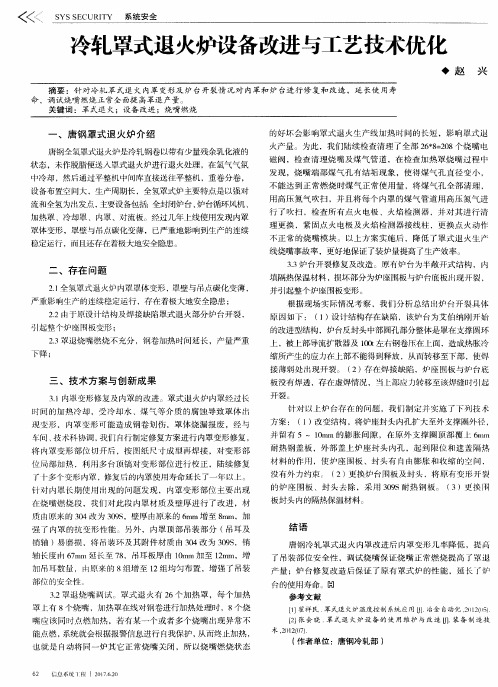
缩所产生 的应力在上部 不能得到释放 ,从而 转移至下部 ,使 焊 接 薄弱处 现开 裂。 ( 2 )存 在焊接 缺 陷 ,炉座 围板 与炉 台底 板没有 焊透 ,存在虚焊情况 ,当 部应 力转 移至 陔焊缝 时引起
开裂 。
三 、 技 术 方 案 与创 新 成 果
3 . 1内罩变形 修复及 内罩的改进 。罩式退火 炉 内罩经 过长
S YS S E CUR I T Y 系统 安 全
冷聋 L 罩式退火炉设备改进 与工艺技术优化
◆ 赵 兴
摘 要 :针 对 冷轧 罩 式退 火 内罩 变形及 炉 台开 裂情 况对 内罩和 炉 台进行 修 复和 改造 ,延 长使 用寿 命 ,调 试烧嘴 燃烧 正常全 面提 高罩退产量 。 关键词 :罩 式退 火;设 备改进 ;烧嘴 燃烧
行 了 吹扫 ,检查所 有 点火 电极 、火焰 检 测器 ,并对 其 进行 清 理 更换 ,紧固点 火 电极及 火焰 检测 器接 线柱 ,更 换点 火 动作
流和全氢为m发点 , 主要设备包括:全封 闭炉 台 、 炉 台循环风机 、 』 J 口 热罩 、冷却罩 、内罩 、对 流板。经过几年上线使用 发现 内罩 罩体变形 ,罩壁 与吊点碳化变薄 ,已严重地影 响到生产 的连续
稳定运行 ,而且还存在着极大地安全隐患 。
不正 常 的烧 嘴模 块 。 以一 k方案 实施 后 ,降低 了罩 式退 火 生产 线烧 嘴事故率 ,更 好地保证 了装 炉量提高 了生产效率 。
3 3炉 台开 裂修 复及改造 。原有炉 台为半 敞开式结构 ,内
二 、存在 问题
2 . 1 令氢罩式退 火炉内罩罩体变形 , 罩壁与 吊点碳 化变薄 ,
住烧 嘴燃 烧 段 ,我 们对 此段 内罩材 质及 壁 厚进行 了改进 ,材
冷轧带钢退火粘结缺陷原因分析及控制措施

冷轧带钢退火粘结缺陷原因分析及控制措施摘要:本文针对八钢公司冷轧带钢3种不同位置的粘结缺陷产生的原因进行了系统性分析,并采取了针对性的措施,效果明显。
关键词:冷轧带钢;退火;粘结Cause analysis and control measures of bonding defects in coldrolled strip annealingXu Jian- sheng,Wang Gong ping,Jiao-dong li(Xinjiang Bayi Iron&steel Co.,Ltd.,Baosteel Group,Urumqi830022,xinjiang ,China)Abstract: t This paper systematically analyzes the reasons of bond defects in three different positions of cold rolled strip steel in Basteel company, and adopts the targeted measures with obvious effect。
Key words:cold roled steel strip;annealing;sticking1.引言八钢公司冷轧分厂使用EBNER强对流全氢型保护气体单垛式罩式炉对冷轧卷直接进行再结晶光亮退火,罩退前无脱脂处理工艺,退火后在后序生产过程中因粘结缺陷封闭降级量大。
粘结严重时,2小时只能生产1卷钢,且发生多次因带钢撕裂而引发断带的事故,严重影响生产节奏及生产成本。
为了进一步提高生产节奏,降低粘结缺陷量,本文对针对八钢公司冷轧带钢三种不同位置的粘结缺陷产生的原因进行了分析,并提出改进措施。
2全氢罩式炉退火工艺规程将炉料装好,清理炉台密封圈及内罩法兰的杂物,吊扣内罩,液压压紧到位(炉内保护气体出口阀自动关闭),在工作负载空间室温条件下,进行N2试漏15min,试漏合格后用流量为120 m3/h N2清洗45min,使O2≤1%。
罩退冷轧钢带粘结缺陷分析及工艺优化

Ab s t r a c t : T a k e t h e c o l d—r o l l e d s t r i p o f 0 . 8 mm S P C C a s a n e x a mp l e , p r o c e s s t e mp e r a t u r e a n d i n t e r l a mi n a r s t r e s s d i s t r i b u t i o n
o f F u l l —h y d r o g e n Be l l —t y p e An n e a l i n g F u r n a c e
Li Pi ng
( S h a n d o n g I r o n& S t e e l G r o u p C o . , L t d .J i n a n C o mp a n y , J i n a n 2 5 0 1 0 1 S h a n d o n g , C h i n a )
要问题 , 月改判率最高达 1 . 4 %。
面的辐射换热 、 加热罩外表面散热 、 加热罩壁 的导 热。冷却罩内的传热主要是空气与内外罩的对流换 热、 内外罩表面的辐射换热 、 冷却罩外表面散热 、 冷 却 罩 内部 导热 。
罩 退冷 轧 钢 带粘 结缺 陷分 析及 工 艺优 化
李 平
2 5 0 1 0 1 )
( 山东钢铁股份有限公司济南分 公司 , 山东 济南
摘
要: 以厚度规格为 0 . 8 m m的 S P C C冷轧钢带为例 , 利用 A N S Y S 有限元分析软件分析了钢卷在全氢罩式炉
退 火过程 的温度 和层 间压应力分布情况 , 得 出在冷却 阶段卷心温度为 6 5 0℃左右和 4 5 0 o C左右 , 层 间压应力分别大 于 3 0 M P a
CSP冷轧薄板罩式退火过程粘结的分析和工艺改进

( tr n tl ryS h o,In rMo g l nv ri fS in ea d T c n lg ,B oo 1 0 0; 1 Maei a d Meal g c ol n e n oi U iest o ce c n eh oo l a u a y y atu0 4 1
poe s-fra ec oigt 6 ℃ ,arc l gt 8 ℃ te trc l g n n raigH2p r , rc s u c ol 5 0 n n o i o i o3 0 n h nwae o i ;a dicesn ui n y t
M a e ilI d x CS o d Ro ig S e t tra n e P C l l n h e ,Be y u n c ,A n ai g t k n l T p F r ae e n e n ,S i ig l c
经过 罩式炉退 火 的冷轧 钢 卷 在平 整 开 卷时 , 有
表 2 包钢 S C P C钢冷轧薄板粘结数据统计
Ta l S a it a a a f c l ol d s e t s c i g o be2 t tsi l d t o o d r l h t k n f c e i S CC t la o o t l P se tBa t u S e
时会出现局部粘结 , 粘结是冷轧带钢经过罩式炉退 火产生 的一种质量 缺 陷 , 目前在粘结 造成
平整开卷 时产生很 大 的开 卷 阻 力 , 使粘 结 处 发 生撕 裂变形 、 凸起 , 经平 整 后 形成 弯 月 状 、 蹄状 或 弧形 马 的 凹印, 带钢产 生部 分或 整 卷 的废 次 品 。为 了生 使 产 出高质 量的冷 轧带 钢 , 制粘 结 的产 生是 重 要手 控
冷轧带钢粘结缺陷的影响因素及控制措施

冷轧带钢粘结缺陷的影响因素及控制措施摘要本文结合冷轧薄板厂生产实际情况,对通过罩式退火炉退火后钢带产生的粘结缺陷的形成机理、影响因素进行了分析,提出了相应的控制和补救措施。
关键词冷轧带钢;粘结;因素;措施AbstractIn this paper, the actual situation of cold-rolled sheet plant, through the annealing furnace for annealing steel strip produced by the formation mechanism of bond defects, affecting factors were analyzed, the corresponding control and remedial measures.Key wordsold-rolled strip of adhesive Measure前言强对流全氢罩式退火炉具有生产灵活性大、效率高、产品退火后表面好、机械性能优等特点。
冷轧带钢经罩式炉退火后消除了因冷轧变形产生的硬化和内应力,使带钢具有良好的力学性能和光亮的表面。
但是冷轧钢带粘结是经过罩式退火炉后钢带一种常见的表面质量缺陷。
为了提高产品质量及成材率,本文对粘结缺陷的产生机理进行了分析,找出影响带钢粘结的各类因素,提出控制及改进措施。
形成机理粘结缺陷是冷轧钢卷层与层之间接触过分紧密,经过退火后成为一体,在平整中撕开后产生的常见的冷轧缺陷。
截取粘结部位试样在显微镜下观察,可以看到在两层钢板板之间有共生晶粒出现,在共生晶粒中有共生碳化物。
这表明,两层钢板在粘结处已成为同一金属休。
冷轧后钢卷层间压力随张力的增加而加大,也受局部显微应力变化的影响。
当层间压应力超过一定极限后,在退火条件合理的情况下层间金属离子相互扩散,形成共生晶粒,甚至出现共生碳化物,使局部形成粘结。
当钢卷加热到一定温度、保温一定时间后,钢板表面粒子获得了用于克服周围粒子约束和层间势能的能力,以带钢层间贴合面为桥梁,扩散到另一个钢板表面上去。
冷轧带罩式炉退火后容易出现的问题原因及解决措施

冷轧带钢经罩式炉退火后容易出现的问题原因及解决措施退火后容易出现氧化,高温氧化及保护气体不纯氧化。
带钢过硬或软,带钢粘结可以降低出炉温度,Q料易氧化。
保温时间短升温速度快都会导致带钢硬。
轧机张力大会影响粘接,还有板型卷型等都有影响冷轧带钢在退火过程中发生哪些组织性能变化?退火:将金属缓慢加热到一定温度,保持足够时间,然后以适宜速度冷却(通常是缓慢冷却,有时是控制冷却)的一种金属热处理[1]工艺。
目的是使经过铸造、锻轧、焊接或切削加工的材料或工件软化,改善塑性和韧性,使化学成分均匀化,去除残余应力,或得到预期的物理性能。
退火工艺随目的之不同而有多种,如重结晶退火、等温退火、均匀化退火、球化退火、去除应力退火、再结晶退火,以及稳定化退火、磁场退火等等。
1、金属工具使用时因受热而失去原有的硬度。
2、把金属材料或工件加热到一定温度并持续一定时间后,使缓慢冷却。
退火可以减低金属硬度和脆性,增加可塑性。
也叫焖火。
退火的一个最主要工艺参数是最高加热温度(退火温度),大多数合金的退火加热温度的选择是以该合金系的相图为基础的,如碳素钢以铁碳平衡图为基础(图1)。
各种钢(包括碳素钢及合金钢)的退火温度,视具体退火目的的不同而在各该钢种的Ac3以上、Ac1以上或以下的某一温度。
各种非铁合金的退火温度则在各该合金的固相线温度以下、固溶度线温度以上或以下的某一温度。
重结晶退火应用于平衡加热和冷却时有固态相变(重结晶)发生的合金。
其退火温度为各该合金的相变温度区间以上或以内的某一温度。
加热和冷却都是缓慢的。
合金于加热和冷却过程中各发生一次相变重结晶,故称为重结晶退火,常被简称为退火。
这种退火方法,相当普遍地应用于钢。
钢的重结晶退火工艺是:缓慢加热到Ac3(亚共析钢)或Ac1(共析钢或过共析钢)以上30~50℃,保持适当时间,然后缓慢冷却下来。
通过加热过程中发生的珠光体(或者还有先共析的铁素体或渗碳体)转变为奥氏体(第一回相变重结晶)以及冷却过程中发生的与此相反的第二回相变重结晶,形成晶粒较细、片层较厚、组织均匀的珠光体(或者还有先共析铁素体或渗碳体)。
退火粘接分析

罩式退火粘接分析及治理1、前言退火是冷轧钢带不可缺少的一个重要生产工序,其主要目的:消除钢带冷轧变形产生的加工硬化和内应力,使带钢具有客户要求的金相组织、良好的机械性能和光亮的表面。
退火炉有罩式退火和连续退火两种形式,其中罩式退火以投资省、占地面积小、生产组织灵活、适合品种钢开发等优点在中小企业得到广泛的应用,但罩式退火的生产特点决定了在罩式退火过程中容易出现粘结缺陷,使得产品质量降级甚至判废。
莱芜市泰山冷轧板有限公司950产线以SPCC为主,产品规格主要集中在0.15-0.5mm*712-830mm,退火采用的是罩式退火,产品质量稳定。
但进入2011年后粘接缺陷在冷轧内部缺陷中一直处于首位,严重影响了产品质量的提升和企业的信誉和效益,因此有必要对造成粘接缺陷的因素进行系统分析并彻底根治。
2、粘接缺陷机理分析关于罩式炉中产品粘接的机理在国内外众多刊物上都有介绍和分析,究其根本原因是:在退火过程中钢卷内部存在温度梯度和压应力,高温作用下局部压应力过大超过屈服极限而产生塑性变形,处于热激活状态的铁原子发生跨金属界面迁移在界面处形成共生晶粒而产生粘接。
钢卷内部的压应力主要是由两部分组成:一部分是退火温度变化而带来的热应力,主要取决于退火工艺制度;另外一部分则是钢卷进入退火炉之前的原始内应力,主要取决于轧机或脱脂机组卷取张力的设定。
在加热阶段,钢卷内外层升温速率大于芯部,造成外层与芯部间压应力减小,内层与芯部间压应力增大,使得内层与芯部之间的钢带存在粘接趋势。
在冷却阶段,内外层降温速率大于芯部.造成外层与芯部间因冷缩不均匀产生较大压应力。
尤其在冷却初始骱段,温度梯度逐渐增大,压应力也随之增大。
当卷芯温度降至一定温度时,卷芯与外层温度梯度最大,压应力也最大,使得外层与芯部之间的钢带存在粘接趋势。
在高温作用下带卷的屈服强度大幅降低,带卷层与层之间在压应力作用下局部(厚度不均、凸起部位)会产生塑性变形,使层间接触面积显著增大,界面间铁原于扩散速度加快,当扩散层达到一定深度,即形成粘结。
冷轧钢卷退火过程粘结原因分析及预防

图 2 带卷退火曲线图
4 粘结的预防措施
通过对带卷退火曲线进行对照分析,可以发现粘结最 易发生在钢卷的冷却阶段。另外,轧制和平整工艺等因素 也对粘结产生重要影响。预防粘结可采取以下主要措施: (1)优化退火工艺。在退火工艺的冷却阶段,冷却速度越 快,钢卷内外温差△ 越大,形成的压应力也越大。在 420 ~ 620 ℃温度段容易形成粘结,因此在冷却阶段带钢温度 高于 420 ℃时,冷却速度不能过快。可以采用带加热罩冷 却到 420 ℃,然后换冷却罩进行风冷和水冷。(2)控制轧 制工艺。包括表面清洁度和粗糙度、卷取张力以及板形 等。由于粘结是在高温状态下钢卷层与层间原子相互渗透 的结果,因此表面清洁度在很大程度上影响了原子的这种 渗透能力,而带钢表面清洁度过高或过低都不利于粘结的 控制,可采取合理选配乳化液和设定适当的喷吹压力等措 施。带钢表面粗糙度适当大一些,有利于避免粘结,因此 适当提高轧机工作辊原始粗糙度有利于避免粘结。适当降 低轧钢卷取张力值,可以减少退火高温状态下钢卷层与层 之间边部原子相互渗透而造成的粘结。控制轧制参数和轧 后冷却,获得良好带钢板形,避免在退火过程中由于钢卷 同一层及层与层之间都存在不同的应力值造成钢卷粘结。 (3)控制平整工艺。包括开卷力和开卷角度、开卷速度和 平整延伸率等。钢卷打开时,粘结的层与层间存在相互的 作用力,较大的钢卷法向应力会造成粘结带钢表面拉伤, 出现严重的粘结缺陷,应控制适当的开卷角度,尽可能使 带钢沿钢卷切向打开,从而减少粘结 2 。保持较大的开卷 速度可使带钢强度迅速越过屈服区域,从而避免或减轻粘 结缺陷的产生。采用恒延伸率控制,尤其较大的延伸率, 有利于对粘结的挽救。
5结语 冷轧钢卷退火时即使采用全氢罩式退火替代常规罩
式退火仍然存在局部粘结现象,可通过优化退火工艺、控 制轧制工艺、控制平整工艺等措施减轻粘结现象,从而 改善表面质量和提高钢卷成材率。