哈工大版金属切削原理与刀具课件第10章-刀具合理几何参数的选择
金属切削原理 10第十章 刀具合理几何参数的选择
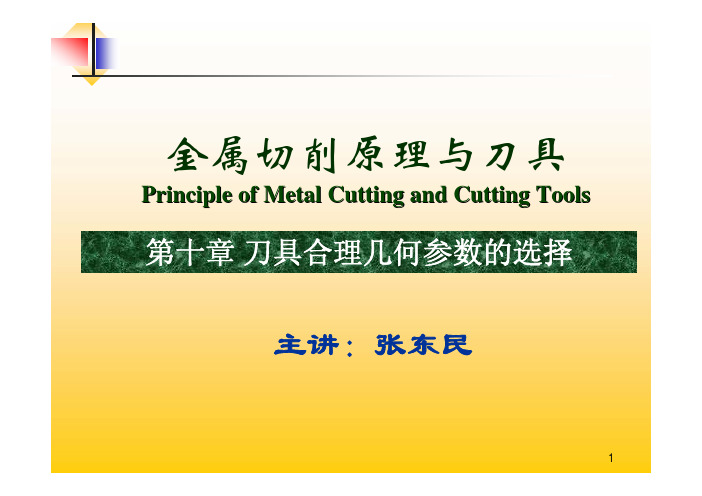
主讲:张东民金属切削原理与刀具Principle of Metal Cutting and Cutting Tools第十章刀具合理几何参数的选择10.1前角及前刀面形状的选择10.2后角的选择10.3主偏角、副偏角及刀尖形状的选择10.4刃倾角的选择刀具的几何参数(γo、αo、κr 、κr′、λs ),对切削变形、切削力、切削温度、刀具寿命等有显著的影响。
选择合理的刀具几何参数,对保证加工质量、提高生产率、降低加工成本有重要的意义。
所谓刀具合理几何参数,是指在保证加工质量的前提下,能够满足较高生产率、较低加工成本的刀具几何参数。
由于刀具几何参数和刀具结构改进,刀具耐用度每隔十年提高2倍(CIRP)。
刀具合理前角取决于刀具材料和工件材料1. 刀具材料刀具材料抗弯强度和冲击韧性较高时,应取较大的前角。
如高速钢刀具的前角比硬质合金刀具的前角要大;陶瓷刀具的韧性差,其前角应更小。
2. 工件材料(1) 加工塑性材料时,为减小切削变形,降低切削力和和切削温度,应选较大的前角;加工脆性材料时,为增加刃口强度,应取较小的前角。
(2)工件材料强度低,硬度低,应选较大的前角,反之,应取较小的前角。
(3)用硬质合金刀具切削特硬材料或高强度钢时,应取负前角。
不同工件材料的刀尖受力点(a)塑性材料(b)脆性材料不同刀具前角的刀尖受力情况3. 选择合理前角考虑具体加工条件9粗加工、断续切削时,为提高切削刃的强度,应选用较小的前角。
9精加工时,为使刀具锋利,提高表面加工质量,应选用较大的前角。
9当机床的功率不足或工艺系统的刚度较低时,应取较大的前角。
9对于成形刀具和在数控机床、自动线上不宜频繁更换的刀具,为了保证工作的稳定性和刀具耐用度,应选较小的前角或零度前角。
二、倒棱及其参数选择倒棱主要作用是增强切削刃,减小刀具磨损。
刀刃钝圆增强切削刃方法,减少刀具早期磨损,提高刀具耐用度200%。
前刀面的形式a)平面型b)带倒棱型c)带断屑槽型d)负前角平面型e)双平面型三、带卷屑槽的前刀面形状及其参数选择增大后角,可减小刀具后刀面与已加工表面间的摩擦,减小磨损,还可使切削刃钝圆半径减小,提高刃口锋利程度,改善表面加工质量。
金属切削刀具与原理教材

第三篇刀具知识第十章金属切削加工的基本概念§10.1切削运动和形成的表面一、切削过程中的运动机器零件的形状虽然多种多样,但总是由一些基本的表面如平面、外圆柱(锥)面、内圆柱(锥)面和具有一定规律的曲面所组成的。
这些基本表面的形成,是通过机床上的工件和刀具作相对运动来实现的。
工件与刀具的相对运动称为切削运动,这包括主运动和进给运动。
1.主运动由机床或人力提供的主要运动,它促使刀具和工件之间产生相对运动,从而使刀具前面接近工件。
主运动的速度可用 c表示。
通常主运动的速度较高,消耗的切削功率也较大。
一般一种切削加工中的主运动只有一个。
主运动可以由工件来完成,如车削时工件的回转运动(图10-1);可也以由刀具来完成,如铣削时铣刀的回转运动。
主运动可以是回转运动,也可以是直线往复运动,如刨削时刨刀的运动。
图10-1 主运动与进给运动1—主运动2—进给运动3—待加工表面4—加工表面5—已加工表面2.进给运动由机床或人力提供的运动,它使刀具与工件之间产生附加的相对运动,即可不断地或连续地切除切屑,并得出具有所需几何特性的已加工表面。
进给运动可以是连续性的,如车削时车刀的连续进给;也可以是间歇性的,如刨削加工时,工件的横向间歇移动。
一种切削加工中,进给运动可以是一个也可能是多个。
图10-1所示为几种常见的切削加工方法的主运动和进给运动。
二、切削过程形成的表面切削时,在工件上会形成待加工工表面、加工表面和已加工表面这三个表面(图10-1)。
1.待加工表面工件上有待切除的表面。
2.加工表面工件上由切削刃形成的那部分表面,它在下一切削行程,刀具或工件的下一转里被切除,或者由下一切削刃切除。
3.已加工表面工件上经刀具切削后产后的表面。
§10.2刀具切削部分的基本定义金属切削刀具种类很多,其中车刀比较典型,其它各种刀具的切削部分都是以车刀为基本形态演变而成的。
下面以外圆车刀为例分析刀具切削部分的结构。
金属切削原理及刀具课件
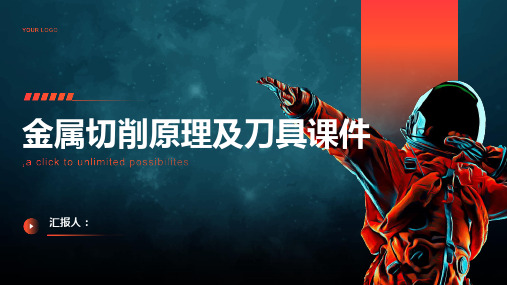
刀具的磨损与破损
刀具磨损的形式与机理
刀具磨损的形式:前刀面磨损、后刀面磨损、边界磨损
刀具磨损的机理:磨料磨损、热磨损、化学磨损、疲劳磨损
刀具磨损的影响因素:切削参数、切削材料、刀具材料、刀具结构
刀具磨损的预防措施:合理选择切削参数、选用合适的切削材料、选用高耐磨损的刀具材料、优 化刀具结构
刀具磨损的监测与控制
刀具磨损的监测方法:通过观察、测量和检验等方法对刀具磨损情况进行实时监测。
刀具磨损的控制策略:采用合理的切削参数、刀具材料和涂层技术等手段,有效控制刀具磨 损。
刀具磨损的预防措施:通过改进刀具设计、提高刀具制造质量和使用高性能刀具等方法,减 少刀具磨损的可能性。
刀具磨损的应对措施:一旦发现刀具磨损,应及时采取更换刀具、调整切削参数等措施,避 免影响加工质量和效率。
刀具的维护与保养 :正确的使用和维 护刀具,可以延长 刀具的使用寿命, 提高加工效率。
刀具的几何参数与选择
刀具的几何参数:包括前角、后角、主偏角、副偏角等,这些参数对切削 力和切削热有重要影响。
刀具的选择:根据加工材料、加工要求、刀具材料和加工条件等因素选择 合适的刀具,以确保加工质量和效率。
刀具的刃磨:刃磨可以改变刀具的几何参数,从而调整切削力和切削热, 提高加工质量和效率。
刀具的基本知识
刀具的分类与用途
刀具的分类:根据刀具的结构可分为整体式、镶嵌式和特殊形式;根据刀具的使用范围可 分为车刀、铣刀、钻头、铰刀等。
刀具的用途:刀具是机械制造中用于切削加工的工具,又称切削工具。绝大多数的刀具是 机用的,但也有手用的,如刻刀、木工刨刀、木工铣刀等。
刀具的发展趋势:随着制造业的发展,刀具行业正朝着高效化、智能化、精细化方向发展。
刀具几何参数的合理选择

重点
掌握前角后角的选择
难点
掌握前后刀面的形式及选择
[复习]
1、衡量材料切削加工性的指标
2、影响材料切削加工性的因素
3、改善材料切削加工性的途径
[新课]
1、前角:尽量大
考虑:①刀具材料:脆性↑→γo↓(高速钢→γo↑,硬质合金→γo↓,陶瓷→γo↓)
②工件材料:塑性材料→γo↑,脆性材料→γo↓,强度→γo↓,硬度→γo↓
②设修光刃:Krε′= 0
bε'= (1.2~1.8)f
5、刃倾角:使刀具刃口锋利,切削平稳
原则:1)粗加工λS< 0(保护刀尖)精加工λS> 0(使FP小些)
2)断续切削:λS< 0(保护刀尖)
3)工件σb、HB大:λS< 0(保护刀尖)
4)系统刚性差:λS> 0(使FP小些)
5)微量切削:λS取大值(使刀具实际刃口半径↓)
金属切削原理与刀具教案
课题
§5、2刀具几何参数的合理选择
授课日期
教材
分析
1、前角后角的选择
2、前后刀面的形Байду номын сангаас及选择
3、主、副偏角、刃倾角的选择
学情
分析
这部分内容前面已经接触过一部分,现在再系统的学习,且学生在实习过程中自己也试着选择过,比较容易掌握。
教学
目标
1、掌握前角后角的选择
2、掌握前后刀面的形式及选择
③加工要求:粗加工→γo↓,断续切削→γo↓,精加工→γo↑
④机床功率和系统刚度:功率大刚度高γο↓,数控机床、自动线:γο↓
2、后角:尽量小
原则:①粗加工:ao↓,精加工:ao↓
②塑性材料:ao↑,脆性材料:ao↓,硬度高:ao↓,强度高ao↓
第十章 刀具合理几何参数的选择

第一节 前角及前刀面形状的选择
三、带卷屑槽的前刀面形状及其参数的选择
2、直线形卷屑槽 直线形卷屑槽的槽底角,对切屑的卷曲变形由直接 的影响。 一般取槽底角等于 110°~130° 3、全圆弧形卷屑槽 可获得较大的前角,而不至于使切削刃部分强度影 响很大。 4、卷屑槽长度Wn对切屑变形影响很大影响: Wn小,易断屑,太小,切屑飞溅; Wn大, 不易断屑。 一般取Wn=(7~10)f
后刀面
刀面
第二节 后角的选择
减小后角、设臵消振棱,可提高工艺系统刚性、提 高加工表面粗糙度的主要原因: a :增加了后刀面与已加工表面之间的接触面积, 可以产生同振动位移方向相反的摩擦阻力; b:对已加工表面起一定的烫压作用。
(3)对尺寸精度要求较高的刀具,宜采用较小的 后角。原因:NB一定时,较小的后角可使刀具 耐用度提高(如前图10-8所示),切削尺寸稳定。 车削钢和铸铁时,后角一般取4°~ 6°;切断刀副后 角一般取1°~ 2°。见图10-10所示。
第二节 后角的选择
后角数值合理与否直接影响已加工表面 的质量、刀具使用寿命和生产率。 后角的功用 ①影响后刀面与加工表面之间的摩擦
② 影响加工工件的精度 ③影响刀具耐用度和刃口的强度
第二节 后角的选择
一、增大后角,可提高刀具耐用度的原因
1、增大后角,可减小弹性恢复层与后到面的接触 长度,因而减小后刀面的摩擦与磨损; 2、后角增大,楔角减小,刀刃钝圆半径减小,可 减小工件表面的弹性恢复; 3、在磨损标准VB一定的情况下,后角的增大,可 使刀具磨去较大体积的刀具材料,因而增加了刀 具寿命。 后角太大时,由于楔角的减小,将消弱切削刃 的强度。 如下图所示
下,能够获得最高刀具耐用度,达到提高效率或
降低生产成本的几何参数。
刀具切削部分几何参数的选择概要课件

03
副偏角的选择应根据工件材料、切削速度和刀具强 度进行确定。
刃倾角的选择
刃倾角的大小影响切削部分的切屑流 向和刀尖强度。
刃倾角的选择应根据工件材料、切削 速度和刀具强度进行确定。
刃倾角增大,切屑流向改变,刀尖强 度降低,刀具耐用度降低。
03
硬质合金刀具切削部分几何参数的选择
总结词
硬质合金刀具具有高硬度、高耐磨性和 良好的高温性能,适用于加工钢铁等黑 色金属材料。在选择硬质合金刀具切削 部分几何参数时,应考虑刀具的切削刃 强度、切削深度和切削宽度等因素。
VS
详细描述
硬质合金刀具的切削刃强度较高,能够承 受较大的切削力和冲击力。因此,在选择 切削部分几何参数时,应注重提高刀具的 切削效率和延长刀具使用寿命。常见的硬 质合金刀具切削部分几何参数包括前角、 后角、主偏角、副偏角和刃倾角等,这些 参数的选择将直接影响切削效果和刀具寿 命。
刀具切削部分几何参数的选择 概要课件
目录
CONTENTS
• 刀具切削部分的基本概念 • 刀具切削部分的几何参数 • 刀具切削部分几何参数的选择原则 • 刀具切削部分几何参数的选择实例 • 总结与展望
01
CHAPTER
刀具切削部分的基本概念
刀具切削部分的组成
01
02
03
04
前刀面
与切屑接触的部分,控制切屑 流出方向。
主后刀面
与工件接触的部分,控制切削 深度。
副后刀面
与工件另一侧接触的部分,辅 助主后刀面控制切削深度。
刀尖
前刀面和后刀面的交接处,通 常为圆弧形或直线形。
刀具切削部分的作用
切削
任务2.2刀具合理几何参数的选择

2.后角的选取原则
⑴根据切削厚度选取后角:
切削厚度小时,为减小切削刃的钝圆半径对切 削层的挤压,应选取较大的后角;切削厚度大 时,为保证刃口强度和改善散热条件,应选取 较小的后角;
前角的作用及选择 1.前角的作用 ⑴影响切削区的变形程度;
增加前角可减小切削层的塑性变形,从而减小切削 力、切削热和切削功率。
⑵影响刀具耐用度;
①增大前角,可减小切削力、切削热和切削功率, 提高刀具耐用度;
②前角过大则刀头强度降低,散热条件差,从而使 刀具耐用度降低。
⑶影响加工表面质量;
①增加前角可减小塑性变形,从而减少工件表面的 加工硬化,并抑制积屑瘤与鳞刺的产生;
s
2.流屑角和实际切削角度 流屑角的定义:
在刀具前刀面上,切屑流出的方向与切削刃法线 间的夹角Ψλ称为流屑角。
二、刃倾角的作用及其选择
刃倾角的作用:
⑴影响切屑的流出方向; ⑵影响实际切削前角和切削刃的锋利性;
s
oe
rne rn cos s
5.4 过渡刃与修光刃参数的选择
一、过渡刃及其参数选择 ⑴外圆车刀过渡刃参数:
ቤተ መጻሕፍቲ ባይዱ
过渡刃偏角
rs
1 2
r
过渡刃长度
bs=0.5~2mm
⑵切断刀过渡刃参数 过渡刃偏角 κrs=45° 过渡刃长度 bs=(0.20~0.25)ap
Κ 'r
Κr
3)圆弧过渡刃
⑴高速钢车刀 r 0.5 ~ 5mm ⑵硬质合金车刀 r 0.5 ~ 2mm
金属切削原理与刀具推选PPT资料

b)滚齿运动
图10-8 滚刀刀齿形状和滚刀安装
a)滚刀刀齿形状
b)滚刀安装
图10-9 滚刀的产形螺旋面
a)滚刀的切削刃在产形螺旋面上
b)滚刀经重磨前面后齿廓不变
Aγ— 前面 Aα—后面(齿顶) AαL—左齿面 AαR—右齿面
S—顶刃
SL—左切削刃
SR—右切削刃
图10-10 阿基米德螺旋面及其车削方法
a)阿基米德螺旋面形成
b)阿基米德螺旋面的车削方法
图10-11 法向直廓螺旋面及其车削方法
图10-12 加工硬齿面的硬质合金刮削滚刀
图10-13 滚刀齿轮顶后角和齿侧后角
精品课件!
精品课件!
逆滚
图10-14 逆向与顺向滚削
顺滚
感谢观看
S—顶刃
SL—左切削刃
SR—右切削刃
a)交错轴斜齿轮副
b)滚齿运动
图10-11 法向直廓螺旋面及其车削方法
图10-1 齿轮铣刀铣齿
图10-6 齿轮滚刀
a)插齿刀的前角、后角
b)前角引起齿廓误差
Aγ— 前面 Aα—后面(齿顶) AαL—左齿面 AαR—右齿面
图10-5 插齿刀的前角和后角
图10-8 滚刀刀齿形状和滚刀安装
图10-11 法向直廓螺旋面及其车削方法
a)盘形齿轮铣刀
b)指形齿轮铣刀
图10-4 渐开螺旋面的形成
图10-5 插齿刀的前角和后角
a)插齿刀的前角、后角
b)前角引起齿廓误差
图10-6 齿轮滚刀
图10-6(a) 涂层齿轮滚刀实物照片
图10-7 滚刀加工齿轮相当于一对交错轴斜齿轮啮合
a)交错轴斜齿轮副
a)盘形齿轮铣刀
b)指形齿轮铣刀
第十章-刀具合理几何参数的选择PPT课件

(1) 考虑刀具材料和结构。刀具材料有高速钢、硬质合金 等;而刀具结构有整体、焊接、机夹、可转位等。
(2) 考虑工件的实际情况。如材料的物理机械性能、毛坯 情况(铸、 锻等)、形状、材质等。
(3) 了解具体加工条件。如机床、夹具情况,系统刚性、 粗或精加工、自动线等。
(4) 注意几何参数之间的关系。如选择前角,应同时考虑 卷屑槽的形状、是否倒棱、刃倾角的正、负等。
振棱。
对于尺寸精度要求较高的刀具,如拉刀,宜取较小的
αo, 因为当NB为定值时,αo小,所允许磨去金属量多,
刀具可连续使用的时间较长。
.ቤተ መጻሕፍቲ ባይዱ
20
图 后刀面的消振棱
.
21
图 αo对磨去量的影响(NB一定时)
.
22
切断刀因进给量关系,使近中心处工作后角减小,
αo应取的比外圆车刀大,常取αo=10°~12°;车削大
单件、小批量生产时,考虑到一刀多用(车外圆、 端面、
倒角),宜取通用性好的κr=45°或90°车刀。
.
29
二、副偏角κr′
1、作用
工件已加工表面靠副切削刃最终形成,κr′值影响刀尖强
度、散热条件、刀具耐用度、 振动和已加工表面的质量等。
2、选择
粗加工时,考虑到刀尖强度、散热条件等, κr′不宜太大,
③ 改变切削刃受力性质。如+γo受弯;-γo受压。
④ 影响切屑形态、断屑效果,如小的γo,切屑变形大,易
折断。
⑤ 影响已加工表面的质量, 主要是通过积屑瘤、 鳞刺、
振动等因素产生影响。
.
3
图 γo
(a) 正前角; (b) 负前角
.
4
显然γo大或小,各有利弊。如γo大,切削变形小,可降 低温度,但刀具散热条件差,温度可能上升;γo小,甚至负值,
- 1、下载文档前请自行甄别文档内容的完整性,平台不提供额外的编辑、内容补充、找答案等附加服务。
- 2、"仅部分预览"的文档,不可在线预览部分如存在完整性等问题,可反馈申请退款(可完整预览的文档不适用该条件!)。
- 3、如文档侵犯您的权益,请联系客服反馈,我们会尽快为您处理(人工客服工作时间:9:00-18:30)。
4.刀面型式及参数
IS0标准确立了多棱面前、后刀面的定义,标 志着切削刀具刀面型式的发展和多样性。 前刀面上的卷屑槽、断屑槽,后刀面的双重 刃磨、铲背以及波形刀面等,都是常见的刀 面型式。 选择合理的刀面型式及其参数值,对切屑的 变形、卷曲和折断,对切削力、切削热、刀 具磨损及使用寿命,有着直接的影响,其中 前刀面的影响和作用更大。
4.要考虑具体的加工条件
选择合理几何参数,也要考虑加工条件,这就是 机床、夹具的情况,工艺系统刚度及功率大小,切 削用量和切削液性能等。 一般地说,粗加工时,着重考虑保证生产效率, 精加工时,主要考虑保证加工精度和已加工表面质 量的要求;对于自动线生产用的刀具,主要考虑刀 具工作的稳定性,有时需要着重解决断屑问题;机 床刚性和动力不足时,刀具应力求锋利(如增大前角 和主偏角,减小切削刃钝圆半径等),以减小切削力 和振动。
10.1硬质合金车刀合理前角参考值
4.采用负倒棱强化切削刃
倒棱的主要作用是增强刃口强度,减少刀 具破损。 正的前刀面加上负倒棱,可以大大提高刀 具的强度。见图10.4。
10.2.2后角的功用及合理后角值的选择
后角数值合理与否直接影响已加工表面的质量、刀具使 用寿命和生产率。 1.后角的功用 (1)后角的主要功用是减小后刀面与过渡表面之间 的摩擦。由于切屑形成过程中的弹性、塑性变形和切 削刃钝圆半径rn的作用,在过渡表面上有一个弹性恢 复层。后角越小,弹性恢复层同后刀面的摩擦接触长 度越大,它是导致切削刃及后刀面磨损的直接原因之 一。从这个意义上来看,增大后角能减小摩擦,可以 提高已加工表面质量和刀具使用寿命。
由图10.6可看出, 切削厚度越小,后角越大,反之,切削厚度越大, 则后角越小,这是因为切削厚度较小时,后刀面的 磨损比较显著,而前刀面上的月牙洼磨损较轻微, 增大后角可以减少后刀面磨损。相反,切削厚度较 大时,前刀面月牙洼磨损较显著,而后刀面磨损相 对下降,这时用较小的后角可以增大刀头散热体积 ,减少前刀面月牙洼磨损。
(3)影响切屑形态和断屑效果:若减小前角, 可以增大切屑的变形,使之易于脆化断裂。 (4)影响已加工表面质量:前角与表面质量的 关系,在第九章已有论述。 值得注意的是,前角大小同切削过程中的振 动现象有关,减小前角或者采用负前角时, 振幅急剧增大。
2.合理前角的概念
从上述前角的作用可知,增大或减小前角,各有其 有利和不利两方面的影响。例如,从切削热的产生 和散热来说,增大前角,可以减小切削热的产生, 切削温度不致太高;但如果前角太大,则因刀头导 热面积和容热体积减小,切削温度反而升高。在切 削很硬的材料时,应用较小的前角,甚至选用适宜 的负前角,以加强切削刃,并改善刀头容热和散热 条件;但若是前角太小,或取很大的负前角,则因 切削变形严重,产生热量多,来不及散逸,结果还 会使切削温度上升。可见,在一定的条件下,前角 有一个合理的数值。
副后角的作用是减少副后 刀面与已加工表面的摩擦 。一般车刀的副后角等于 主后角,切断刀和切槽刀 的副后角由于受结构强度 和刃磨后尺寸变化的影响 ,只能取得很小,一般取 1—2度。见图10.8.
三、主偏角及副偏角的功用和选择
1、主偏角的功用 一、主偏角的功用及选用 ① 主偏角κr的变化,影响各切削分力的大小比 值与产生振动的可能性。 减小主偏角κr,则吃力抗力Fy增大,走刀抗力 Fx减小,反之加大主偏角κr,则可使Fy减小, Fx增大。当工艺系统刚度较差时,若过于减小 κr,Fy显著减小,就可能引起振动,造成损坏 刀具,顶弯工件。
(3)工艺系统刚度较差时,为适当增大刀 具后刀面和加工表面之间的接触面积,以达 到阻尼消振的目的,也应取较小的后角。( 图10.7消振棱) (4)对于定尺寸刀具,即尺寸精度要求高 的精加工用刀具(如拉刀、铰刀等)为了保 证较高的尺寸耐用度,后角也应取得较小。 合理后角的选择具体值见表10.2。
第十章 刀具合理几何参数的选择
第十章 刀具合理几何参数的选择
中国谚语:“工欲善其事,必先利其器”, 国际生产工程科学院(CIRP,The International Academy for Production Engineering, CIRP是法语的 缩写Collège International pour la Recherche en Productique ) 的一项研究报告指出: “由于刀具材料的改进,刀具的允许切削速度每隔 十年几乎提高一倍;由于刀具结构和几何参数的改进, 刀具使用寿命每隔十年几乎提高二倍。”
图10.2为刀具前角对使用 寿命影响的示意曲线。可 见前角太大、太小都会使 刀具使用寿命显著降低。 对于不同的刀具材料,各 有其对应着刀具最长使用 寿命的前角,称为合理前 角γopt。 硬质合金的抗弯强度较低 ,抗冲击韧性差,其γopt 也就小于高速钢刀具的
工件材料对刀具的合理前角影响图10.3
3.合理前角的选择原则 (1)工件材料的强度、硬度低,可以取较大 的甚至很大的前角;工件材料强度、硬度高 ,应取较小的前角;加工特别硬的工件(如淬 硬钢)时,前角很小甚至取负值。 (2)加工塑性材料时,尤其是冷加工硬化严重 的材料,应取较大的前角;加工脆性材料时 ,可取较小的前角。
(3)粗加工,特别是断续切削,承受冲击性 载荷,或对有硬皮的铸锻件粗切时,为保 证刀具有足够的强度,应适当减小前角; 但在采取某些强化切削刃及刀尖的措施之 后,也可增大前角至合理的数值。 (4)成形刀具和前角影响刀刃形状的其它刀 具,为防止刃形畸变,常取较小的前角, 甚至取γ。=0,但这些刀具的切削条件不 好,应在保证切削刃成形精度的前提下, 设法增大前角,例如有增大前角的螺纹车 刀和齿轮滚刀等。
从实验曲线可以看出,加工塑性材料 比加工脆性材料的合理前角值大,加 工低强度钢比加工高强度钢的合理前 角值大。 这是因为切削塑性大的金属材料产生 的切屑,在切削过程中,它同前刀面 接触长度(刀—屑接触长度)较大,由于 塑性变形的缘故,刀—屑之间的压力 和摩擦力很大,为了减少切削变形和 切屑流动阻力,应取较大的前角。加 工材料的强度硬度较高时,由于单位 切削力大,切削温度容易升高,为了 提高切削刃强度,增加刀头导热面积 和容热体积,需适当减小前角。
说明:选择刀具合理几何参数具有重要意义。
刀具的合理(或最佳)几何参数
在保证加工质量的前提下,能够保证 刀具使用寿命、生产效率、成本低的刀具 几何参数,称为刀具的合理几何参数。
10.1 概述
刀具的合理几何参数包含四个方面基本内容: 1.刀具角度 前角γ。、 后角α。、 主偏角kr、副偏角kr’ 刃倾角λs 副后角α。’。
切削脆性材料时,塑性变形不大,切出的 崩碎切屑,与前刀面的接触长度很小,压 力集中在切削刃附近,为了保护切削刃, 宜取较小的前角。
在某些情况下,这样选定的γopt未必是最适宜 的, 例如在出现振动的情况下,为了减小振动的振 幅或消除振动,除采取其他措施外,有时需增 大前角;在精加工条件下,往往需要考虑加工 精度和已加工表面的粗糙度要求,选择某一适 宜的前角;有些刀具需考虑其重磨次数最多而 选择某一前角,等等。
1.前角的主要功用 (1)影响切削区域的变形程度:若增大刀 具前角,可减小前刀面挤压切削层时的塑 性变形,减小切屑流经前刀面的摩擦阻力 ,从而减小了切削力、切削热和功率。前 角γ。对三个切削分力的影响,当前角增大 时,Fc、Fp、Ff力均显著减小,这是增大 前角的有利方面。
(2)影响切削刃与刀头的强度、受力性质和散 热条件:增大刀具前角,会使切削刃与刀头 的强度降低,刀头的导热面积和容热体积减 小;过分加大前角,有可能导致切削刃处出 现弯曲应力过大,造成崩刃。这些都是增大 前角的不利方面。
② 主偏角κr的变化,影响切削截面的形状。在切 削深度和进给量一定的情况下,随着κr角的减 小,切削厚度将减小,切削宽度增加,切削刃 参加工件的长度增加,切削刃单位长度的负荷 减轻,刀尖角增大,这就会提高刀尖强度,改 善散热条件,因而可提高刀具使用寿命。 ③ 主偏角κr影响工件表面形状,当车削阶梯轴时 ,应选用κr=90º ,而当车削外圆端面及倒角时 ,则可选κr=45º 。
10.1.2选择刀具合理几何参数的一般性原则
1.要考虑工件的实际情况 选择刀具合理几何参数,要考虑工件的实 际情况,主要是工件材料的化学成分、制造 方法、热处理状态、物理、机械性能(包括硬 度、抗拉强度、延伸率、冲击韧性、导热系 数等),还有毛坯表层情况、工件的形状、尺 寸、精度和表面质量要求等。
5.考虑刀具锋利性与强度关系
考虑刀具锋利性与强度矛盾关系 保证强度前提下,力求锋利
10.2 刀具合理几何角度及其选择
一、前角的功用及合理前角值的选择 从金属切削的变形规律可知, 前角(γ。) 大小直接影响切削力、切削温度 和切削功率,影响刃区和刀头的强度、容 热体积和导热面积,从而影响刀具使用寿 命和切削加工生产率。
2、合理后角的概念
后角增大虽可减小刃口钝圆半径rn,减少后刀面 与加工表面之间的摩擦,减少磨损。 提高刀具 使用寿命和加工表面质量,但后角过大则将削弱 刃口强度,恶化散热条件,刀具使用寿命反而降 低。因此,后角α过大、过小,对切削过程和刀 具使用寿命都是不利的。在一定的切削条件下, 它有一个合理的数值。 通常合理的后角值是根据切削厚度来选择的, 图10.6为不同切削厚度时的合理后角值αopt。
2.刃形 刃形即是指切削刃的形状。 直线刃 折线刃、 圆弧刃、 月牙弧刃、 波形刃、 阶梯刃 空间曲线刃,
3.切削刃刃区的剖面及其参数
切削刃的剖面型式,我们通常将它简称为刃区 型式,会影响切削加工效率、质量和成本。 图10.1所示为五种刃区型式,其合理参数值的 选择见有关资料。
(2)后角越大,切削刃钝圆半径rn值越小,切削刃 越锋利。 (3)在同样的磨钝标准VB下,后角大的刀具由新 用到磨钝,所磨去的金属体积较大见图10.5,这 也是增大后角可以延长刀具使用寿命的原因之一 。但它带来的问题是刀具后角过大,楔角β减小, 则将削弱刃口强度,减少散热体积,磨损反而加 剧,导致刀具使用寿命下降,且易发生颤振 。 NB一定时, 后角越小越耐磨,寿命越长。