neXt安装维护手册
SUNLIKE+ERP安装维护手册
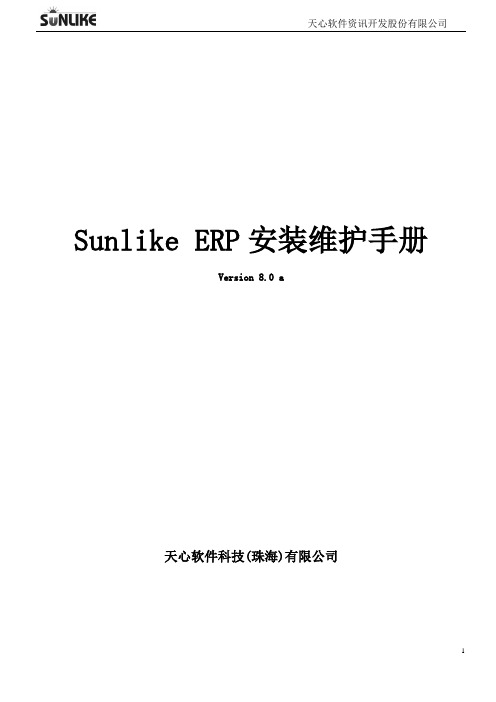
Sunlike ERP安装维护手册Version 8.0 a天心软件科技(珠海)有限公司尊敬的客户:非常感谢您选购了天心软件的企业管理软件产品!天心坚持着“优质软件,真心服务”的企业宗旨,提倡互相尊重、真诚合作和团队精神,致力于一流ERP软件和服务供应商的建设。
Sunlike ERP是一个集成化的计算机系统管理软件,是参照美国生产与库存控制协会(APICS)颁布的MRPII标准,同时吸收现代营销管理、现代物流管理、生产管理、准时制生产(JIT)、物料管理、全面质量管理、财务管理、人力资源管理等先进管理方式的优点,结合企业自身特点,以企业运作过程中的信息流、资金流和物流为核心进行系统结构设计和软件开发,可对企业的生产制造资源、财务资源和人力资源等进行全程监控和管理。
因为经营活动存在着高度的关联性,资料环环相扣。
与之相适应的Sunlike ERP模块之间均紧密集成,数据高度共享,所有模块数据间无缝衔接,可自由地实现双向往返追踪。
符合制造工业标准和工业界普遍接受的原则,同时为企业提供了一种先进、高效的业务运作管理模式,使企业能实施科学的管理。
解决目前手工管理所不能解决的许多问题,最终提高企业的整体经济效益。
Sunlike ERP C/S版本具备从会计总帐、进销存、MRPII到人事薪资等二十多个成熟的子系统,可根据客户需求任意拆分组合,即买即用。
天心对企业管理模型全方位透彻研究,充分考虑到客户的个性化管理需求,推出多项企业解决方案,如:集团企业ERP解决方案、工业企业MRPII/ERP解决方案、商业企业解决方案、纺织染整专业解决方案、天心ERP Internet解决方案等。
将天心的标准核心模组与不同规模、不同行业的企业运作特色相结合,从而达到“量身定做”。
企业选型看中的不仅仅是产品本身的卓越性能和技术,更看中的是项目具体的实施服务能否真正实现企业的系统管理化。
天心拥有雄厚的实施和服务力量,再者经过系统不断地培养,已拥有一支综合、全面、熟悉企业管理理论与企业实际运行操作的资深应用顾问。
EX2N PLC 使用手册

时
161 TZCP 时钟数据区间比较
钟
162 TADD 时钟数据加法
运 算
163 TSUB 时钟数据减法
166 TRD 时钟数据读出
256 点 D8000 至 D8255 16 点 V0-V7 Z0-Z7 128 点 P0-P127
8 点 N0-N7 16 位:-32768 至+32768 32 位:-2147483648 至+2147483647 16 位:0000 至 FFFF 32 位:00000000 至 FFFFFFFF
注1
SET 置位
动作保持
Y,M,S
注2
RST 复位
清除动作保持,寄存器清零 Y,M,S,T,C,D,V,Z
MC 主控
公共串联点的连接线圈指令 Y,M(特殊 M 除外)
3
MCR 主控复位
公共串联点的消除指令
2
MPS 压栈
运算存储
1
MRD 读栈
存储读出
1
MPP 出栈
转
500 点 200 点 46 点 4点 6点 100 点 100 点
S500 至 S999 T0 至 T199
T200 至 T245 T246 至 T249 T250 至 T255
C0 至 C99 C100 至 C199
35 点 21 点
C200 至 C234 C235 至 C255
200 点 D0 至 D199 (乘法除法结果存于双字节寄存器中) 312 点 D500-D512 (乘法除法结果存于双字节寄存器中)
★
81 PRUN 8 进制位传送
225 LD﹥ (Sl)﹥(S2)
★
外
82 ASCI HEX 转 ASCⅡ
产品安装、操作与维护手册说明书
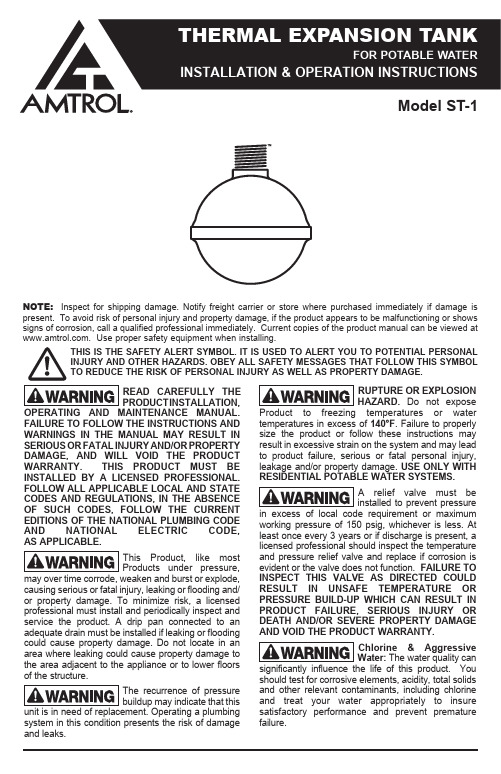
I NSTALLATION,FAILURE TO FOLLOW THE INSTRUCTIONS ANDWARNINGS IN THE MANUAL MAY RESULT INSERIOUS OR FATAL INJURY AND/OR PROPERTYDAMAGE, AND WILL VOID THE PRODUCT WARRANTY. THIS PRODUCT MUST BE INSTALLED BY A LICENSED PROFESSIONAL. FOLLOW ALL APPLICABLE LOCAL AND STATE CODES AND REGULATIONS, IN THE ABSENCE OF SUCH CODES, FOLLOW THE CURRENT EDITIONS OF THE NATIONAL PLUMBING CODE AND NATIONAL ELECTRIC CODE,causing serious or fatal injury, leaking or flooding and/or property damage. To minimize risk, a licensed professional must install and periodically inspect and service the product. A drip pan connected to an adequate drain must be installed if leaking or flooding could cause property damage. Do not locate in an area where leaking could cause property damage to the area adjacent to the appliance or to lower floorssystem in this condition presents the risk of damageand leaks.Do not expose temperatures in excess of 140°F . Failure to properly size the product or follow these instructions may result in excessive strain on the system and may lead to product failure, serious or fatal personal injury, leakage and/or property damage. USE ONLY WITHworking pressure of 150 psig, whichever is less. At least once every 3 years or if discharge is present, a licensed professional should inspect the temperature and pressure relief valve and replace if corrosion is evident or the valve does not function. FAILURE TO INSPECT THIS VALVE AS DIRECTED COULD RESULT IN UNSAFE TEMPERATURE OR PRESSURE BUILD-UP WHICH CAN RESULT IN PRODUCT FAILURE, SERIOUS INJURY OR DEATH AND/OR SEVERE PROPERTY DAMAGEThe water quality canshould test for corrosive elements, acidity, total solids and other relevant contaminants, including chlorine and treat your water appropriately to insure satisfactory performance and prevent premature failure.NOTE: Inspect for shipping damage. Notify freight carrier or store where purchased immediately if damage is present. To avoid risk of personal injury and property damage, if the product appears to be malfunctioning or shows signs of corrosion, call a qualified professional immediately. Current copies of the product manual can be viewed at . Use proper safety equipment when installing.THIS IS THE SAFETY ALERT SYMBOL. IT IS USED TO ALERT YOU TO POTENTIAL PERSONAL INJURY AND OTHER HAZARDS. OBEY ALL SAFETY MESSAGES THAT FOLLOW THIS SYMBOL TO REDUCE THE RISK OF PERSONAL INJURY AS WELL AS PROPERTY DAMAGE.Model ST-1ApplicationThe ST-1 expansion tank is for use on tankless, residential on-demand water heaters with a total water content of 2 gallons or less and a maximum set point of 140°F. Do not use with larger storage-type water heaters, as these will exceed the capacity of the ST-1.Installation1. Install the expansion tank on the cold watersupply line to the water heater at a point between the water heater and backflow preventer or other one-way device (Figure 1).2. Once the expansion tank is installed, checkthe cold water supply line for any leakage.Make repairs if necessary.3. Before the initial firing of the water heater,open a hot water fixture and draw for one minute to purge air. Next, close and open the fixture in 30 second intervals, repeating three thimes to flush the tank and piping.Finally, turn the water heater temperature control to desired ending temperature (see water heater instructions). Do not set temperature higher than the expansion tank maximum.4. To relieve initial thermal expansion, slightlyopen a hot water faucet. Continue until water heater temperature is satisfied. Once heater is at its operating range, no further bleeding of expanded water is required.5. The water heater and expansion tank willnow be operational. The expansion tank will control pressure increases caused by thermal expansion to a level below the water heater relief valve setting. FOR USE ON TANKLESS RESIDENTIAL ON DEMAND WATER HEATERS WITH A TOTAL WATER CONTENT OF 2 GALLONS OR LESS ANDA MAXIMUM SET POINT OF 140° F. NON-ADJUSTABLE PRECHARGE.PSI Volume (cu.in.)Weight (lb.).000.00.8720.00 3.92 1.0140.00 5.77 1.0760.007.43 1.1380.008.17 1.16100.008.63 1.18120.009.00 1.19140.009.27 1.20150.009.27 1.20 MaintenanceA licensed professional should check the complete system, including the expansion tank, yearly and more frequently as the system ages. WarrantyST-1 Model: Seven (7) Year Limited Warranty Visit for complete warranty details.PLEASE READ THE FOLLOWING INSTRUCTIONS CAREFULLYI MPORTANT GENERAL SAFETY INFORMATION -ADDITIONAL SPECIFIC SAFETY ALERTS APPEAR IN THE FOLLOWING INSTRUCTIONS.1400 Division Road, West Warwick, RI 02893 USA T: 800.426.8765© 2020 Worthington Industries Inc. Part #: 9013-017 (01/21) One or more features of this product are covered by U.S. patents, visit /patents for more information.。
迪纳尔(Dorner) brushless DC电机控制安装、维护与零件手册说明书

For other service manuals visit our website at:/service_manuals.aspDORNER MFG. CORP .INSIDE THE USA OUTSIDE THE USA P.O. Box 20 • 975 Cottonwood Ave.TEL: 1-800-397-8664TEL: 262-367-7600Hartland, WI 53029-0020 USA FAX: 1-800-369-2440FAX: 262-367-5827851-738 Rev. BBrushless DC Motor ControlInstallation, Maintenance and Parts ManualDorner Mfg. Corp.2851-738 Rev. BBrushless DC Motor ControlTable of ContentsIntroduction......................................................................... 2Warnings − General Safety ................................................. 3Product Description............................................................. 4Brushless DC Motor Control........................................... 4Specifications...................................................................... 52200 Light Load Gearmotors........................................... 52200 and 3200 Standard Load Gearmotors..................... 52200 Standard Load 90° Gearmotors............................... 5Controllers ....................................................................... 5Installation........................................................................... 6Required Tools................................................................. 6Conveyor Mounting......................................................... 6Stand Mounting................................................................ 7Wiring.............................................................................. 7For 1 Phase (115 Volt) Controllers:............................. 8For 3 Phase (230 Volt) Controllers:.. (9)For Remote ON/OFF Signal:...................................... 11External Input Signals................................................. 12Input Signal Connection Terminals ........................ 12Operation............................................................................ 13Controller Setup ............................................................ 13Setting Speed Acceleration and Deceleration............. 13Set Motor Direction.................................................... 15Displaying the Conveyor Belt Speed.......................... 15Setting Speed While Motor is Running...................... 17Switching the Signal Methodto Remote Signal (If Required)................................... 17Notes.................................................................................. 18Service Parts....................................................................... 19Brushless DC Motor Control.......................................... 19Return Policy. (20)IntroductionUpon receipt of shipment:•Compare shipment with packing slip. Contact factory regarding discrepancies.•Inspect packages for shipping damage. Contact carrier regarding damage.•Accessories may be shipped loose. See accessory instruc-tions for installation.The Dorner Limited Warranty applies.Dorner reserves the right to make changes at any time without notice or obligation.Dorner has convenient, pre-configured kits of Key Service Parts for all conveyor products. These time saving kits are easy to order, designed for fast installation, and guarantee you will have what you need when you need it. Key Parts and Kits are marked in the Service Parts section of thismanual with the Performance Parts Kits logo .A CAUTIONSome illustrations may show guardsremoved. DO NOT operate equipment without guards.851-738 Rev. B3Dorner Mfg. Corp.Brushless DC Motor ControlWarnings − General SafetyA WARNINGThe safety alert symbol, black triangle with white exclamation, is used to alert you to potential personal injury hazards.SEVERE HAZARD!KEEP OFF CONVEYORS. Climbing, sitting,walking or riding on conveyor will cause severe injury.EXPLOSION HAZARD!•DO NOT OPERATE CONVEYORS IN AN EXPLOSIVE ENVIRONMENT. The electric gearmotor generates heat and could ignite combustible vapors.•Failure to comply will result in death or serious injury.A WARNINGController must be properly grounded. Failure to properly ground controller may cause injury to personnel.SEVERE HAZARD!Hazardous voltage will cause severe injury or death. LOCKOUT POWER BEFOREWIRING.A WARNINGSEVERE HAZARD!Exposed moving parts can cause severe injury. DO NOT ATTEMPT ADJUSTMENTS WITH CONVEYOR RUNNING. LOCK OUT POWER before removing guards or performing maintenance.A WARNINGSEVERE HAZARD!•Dorner cannot control the physicalinstallation and application of conveyors. Taking protective measures is the responsibility of the user.•When conveyors are used in conjunction with other equipment or as part of a multiple conveyor system, CHECK FOR POTENTIAL PINCH POINTS and other mechanical hazards before system start-up.•Failure to comply could result in serious injury.Dorner Mfg. Corp.4851-738 Rev. BBrushless DC Motor ControlProduct DescriptionBrushless DC Motor ControlDorner’s Brushless DC Motor Control (Figure 1) are DC motor speed controllers for Standard and Heavy Load VFD gearmotors.Figure 1Typical Components1Mode indicator LEDsThe illuminating LED indicates the current operation mode.•MNTR: Monitor mode•F/R: Direction setting mode•LO/RE: Digital operator/external input signal set-ting mode•PRGM: Data setting mode2Unit display LEDsThe illuminating LED indicates the current display unit.•r/min: Speed of motor or gearhead output shaft •m/min: Conveyor transfer speed •%: Load factor3RUN = Start the motor operation. 4STOP = Stop the motor. 5ON/OFF Power Switch.6Use these keys to switch the mode or set data.•Switch the operation mode•Move to the next item or increase the value•Move to the previous item or decrease the value •Confirm the data 7Display8ALARM LED: A red light will come on when an alarm is generated.9RUN LED: A green light stays on during operation.NOTEFor additional information, refer to the Oriental Motor Operating Manual shipped with your controller. See Specifications table for models.134568927851-738 Rev. B5Dorner Mfg. Corp.Brushless DC Motor ControlSpecifications2200 Light Load Gearmotors2200 and 3200 Standard Load Gearmotors2200 Standard Load 90° GearmotorsControllersDorner Model NumberMax RPM*Type HP Kw FLA In-lbs N-m 62M050PLBDDEN 60A 0.0830.060See Control 768.662M020PLBDDEN 150A 0.0830.060See Control 31 3.662M015PLBDDEN200A0.0830.060See Control232.7Dorner Model NumberMax RPM*Type HP Kw FLA In-lbs N-m 62M050PSBDDEN 60B 0.250.200See Control 2402862M020PSBDDEN 150B 0.250.200See Control 10311.762M015PSBDDEN300B0.250.200See Control525.9Dorner Model NumberMax RPM*Type HP Kw FLA In-lbs N-m 62M060ESBDDEN 50B 0.250.200See Control 10612.462M040ESBDDEN 75B 0.250.200See Control 12314.362M020ESBDDEN 150B 0.250.200See Control 8910.462M010ESBDDEN 300B 0.250.200See Control 49 5.762M005ESBDDEN600B0.250.200See Control252.9Dorner Model Number Input Volt Input Phase Input Hz Max Input Amps Output Max Watts ReversingType 63MBD11B60115160 4.5BDC 60Y es A 63MBD23B60230360 1.5BDC 60Y es A 63MBD11B2001151608.8BDC 200Y es B 63MBD23B2002303603.4BDC200Y esBDorner Mfg. Corp.6851-738 Rev. BBrushless DC Motor ControlInstallationRequired Tools• 6 mm hex head wrench •Flat-blade screwdriver •Phillips screwdriverInstallation Component List (Figure 2):Figure 2Conveyor Mounting1.Install spring t-nuts (Figure 3,item 1) into conveyor t-slot.Figure 32.Attach controller (Figure 4,item 1) to conveyor with screws (Figure 4,item 2).Figure 43.Slide controller to its desired mounting location along conveyor and tighten both screws.1Controller Mounting Bar (2x)2Brushless DC Controller 3Motor Power Cord 4External Signal Cord 5Power Supply Cord6Hex Head Screws, M4 x 16 mm (4x)7T -Bar8Hex Head Screws, M6 x 16 mm (2x)1287345612851-738 Rev. B7Dorner Mfg. Corp.Brushless DC Motor ControlInstallationStand Mounting1.Install spring t-nuts (Figure 5,item 1) into stand t-slot.Figure 52.Partially thread controller mounting bar (Figure6,item 1) to lower t-nut with screw (Figure 6,item 2).Figure 63.Install second spring t-nut into stand t-slot.4.Partially thread controller mounting bar (Figure 7,item 1) to top t-nut with screw (Figure 7,item 2).Figure 75.Slide controller to its desired mounting location and tighten both screws.WiringSEVERE HAZARD!Hazardous voltage will cause severe injury or death. LOCKOUT POWER BEFOREWIRING.A WARNINGSEVERE HAZARD!Exposed moving parts can cause severe injury. DO NOT ATTEMPT ADJUSTMENTS WITH CONVEYOR RUNNING. LOCK OUT POWER before removing guards or performing maintenance.A WARNINGController must be properly grounded.Failure to properly ground control box may cause injury to personnel.NOTEFor additional specific wiring information and schematics, refer to the Oriental Motor Operating Manual shipped with your controller.Dorner Mfg. Corp.8851-738 Rev. BBrushless DC Motor ControlInstallationFor 1 Phase (115 Volt) Controllers:1.Open controller by loosening four plastic cover screws (Figure 8,item 1), and removing controller case cover (Figure 8,item 2).Figure 82.Remove controller cover (Figure 9,item 1).Figure 93.Connect black (live side) (Figure 9,item 2) to L (Figure 9,item 3) and white (neutral side) (Figure 9,item 4) to N (Figure 9,item 5) wires on controller.4.Connect motor plugs (Figure 10,item 1) and (Figure 10,item 2).Figure 10SEVERE HAZARD!Hazardous voltage will cause severe injury or death. LOCKOUT POWER BEFORE WIRING.NOTEFor 115V controllers no wiring is required. Controller is provided with power cord. The steps 1-3 are shown for reference, only if re-wiring is required.123254121Brushless DC Motor Control Installation5.Install inner cord cover (Figure 11,item1).Figure116.Install outer cord cover (Figure 12,item1) over innercord cover (Figure 12,item2).Figure127.Twist covers (Figure 13,item1) together, as shown.Figure13 For 3 Phase (230 Volt) Controllers:1.Open controller by loosening four plastic cover screws(Figure 14,item1), and removing controller case cover (Figure 14,item2).Figure141 211A DANGERSEVERE HAZARD!Hazardous voltage will cause severe injury or death. LOCKOUT POWER BEFORE WIRING.12851-738 Rev. B9Dorner Mfg. Corp.Dorner Mfg. Corp.10851-738 Rev. BBrushless DC Motor ControlInstallation2.Install four wires (Figure 15,item 1) through cord grip opening (Figure 15,item 2) in controller assembly.Figure 153.Connect black (Figure 16,item 1), white (Figure16,item 2), red (Figure 16,item 3), and green (Figure 16,item 4) wires to mating color wires (Figure 16,item 5) on opposite end of wiring connector terminals.Figure 164.Secure wires by tightening grip (Figure 16,item 6).5.Install case cover (Figure 14,item 2). with four plastic cover screws (Figure 14,item 1).6.Connect motor plugs (Figure 17,item 1) and (Figure 17,item 2).Figure 177.Install inner cord cover (Figure 18,item 1).Figure 188.Install outer cord cover (Figure 19,item 1) over inner cord cover (Figure 19,item 2).Figure 191212345621121Brushless DC Motor Control Installation9.Twist covers (Figure 20,item1) together, as shown.Figure20For Remote ON/OFF Signal:1.Remove access plug (Figure 21,item1).Figure212.Open controller by loosening four plastic cover screws(Figure 21,item2), and removing controller case cover (Figure 21,item3).3.Remove controller cover (Figure 22,item1).Figure224.Install cord grip, not provided (Figure 22,item2).5.Insert external signal wires to terminals (Figure22,item3). See “External Input Signals” on page12.6.Be sure to configure controller for remote signals. (See“Switching the Signal Method to Remote Signal (IfRequired)” on page17 for details.)A DANGERSEVERE HAZARD!Hazardous voltage will cause severe injury or death. LOCKOUT POWER BEFORE WIRING.1231112 3851-738 Rev. B11Dorner Mfg. Corp.Dorner Mfg. Corp.12851-738 Rev. BBrushless DC Motor ControlInstallationExternal Input SignalsExternal input signals must be set in accordance with the desired application.Perform the various settings specified below using the digital operator.Input Signal Connection TerminalsConnect the input signals according to the operation method of your system. Dry contact signals are recommended. For solid state signals see Oriental Manual for details.Figure 23ApplicationNecessary settingsUse input signals connected to terminalsX1, X2 and X3Switch the operation-signal input method to “external input signals” on the digital operator. See “Switching the Signal Method to Remote Signal (If Required)” on page 17.Terminal PositionTerminal Name Signal Name DescriptionNecessary settingsLower StageC0IN-COM0Input signal common Remove the short bar and connect an external control equipment.C1IN-COM0Input signal common -X1CW input Clockwise rotationSet the operation-signal input method to “external input signals” on the digital operator.X2CCW inputCounterclockwise rotation851-738 Rev. B13Dorner Mfg. Corp.Brushless DC Motor ControlOperationController SetupWhen purchased with a gearmotor, Dorner configures Variable Speed VFD Controllers as follows:•Acceleration and Deceleration, 0.5 sec •Direction = Forward •Speed = 0 rpm•Remote Signal = Local (Lo)Proceed with the following steps to change these configurations:Setting Speed Acceleration and Deceleration1.Press MODE to switch to the data setting mode. The PRGM LED (Figure 24,item 1) will illuminate and “SPd” (Figure 24,item 2) will be displayed.Figure 242.Press SET (Figure 25,item 1). “P. no1” (Figure 25,item 2) will be displayed.Figure 253.Press SET (Figure 25,item 1). Press up or down(Figure 25,item 3) until “SPd1” (Figure 26,item 1) is displayed. Press set (Figure 26,item 2) again. “SPd1” (Figure 26,item 1) will blink and correct speed (Figure 26,item 3) will be displayed.Figure 26SEVERE HAZARD!Hazardous voltage will cause severe injuryor death. LOCKOUT POWER BEFORE WIRING.A WARNINGSEVERE HAZARD!Exposed moving parts can cause severe injury. DO NOT ATTEMPT ADJUSTMENTS WITH CONVEYOR RUNNING. LOCK OUT POWER before removing guards or performing maintenance.NOTEFor additional information or desired settings other than listed, refer to information provided by controller manufacturer.NOTEThe controller is capable of storing several speed configurations of speed programs. The following instructions are for programming one only. For further details, see the controllermanual.Dorner Mfg. Corp.14851-738 Rev. BBrushless DC Motor ControlOperation4.Press up or down (Figure 27,item 1) to change the speed (e.g., 1000 r/min) (Figure 27,item 2). Pressing and holding the key for 3 seconds or more will increase or decrease the value successively.Figure 275.After the speed has been changed, press SET (Figure 28,item 1) to confirm the new setting. The display will blink and show “Acc1” (Figure 28,item 2), after which the acceleration time (Figure 28,item 3) will be displayedFigure 286.Press up or down (Figure 29,item 1) to change the acceleration time (e.g., 5.0) (Figure 29,item 2).Pressing and holding the key for 3 seconds or more will increase or decrease the value successivelyFigure 297.After the acceleration time has been changed, press SET (Figure 30,item 1) to confirm the new setting. The display will blink and show “dEc1”(Figure 30,item 2), after which the deceleration time (Figure 30,item 3) will be displayed.Figure 308.Press up or down (Figure 31,item 1) to change the deceleration time (e.g., 5.0) (Figure 31,item 2).Pressing and holding the key for 3 seconds or more will increase or decrease the value successively.Figure 319.After the deceleration time has been changed, press SET (Figure 32,item 1) to confirm the new setting. The display will blink.Figure 3210.Press MODE to switch to the monitor mode.NOTEMinimum Speed = 100 rpm Maximum Speed = 3000 rpmBrushless DC Motor Control OperationSet Motor DirectionThe initial setting is “For” (clockwise).1.Press MODE to switch to the direction setting mode.The F/R LED (Figure 33,item1) will illuminate.Figure332.Press up or down (Figure 33,item2) to select a desireddirection. “For” (Figure 33,item3): Clockwise or“rEv”: Counterclockwise.3.Press SET (Figure 33,item4) to confirm the selection.The display will blink.Displaying the Conveyor Belt SpeedWhile the motor is operating, the speed of the motor output shaft is displayed on the digital operator. To show the speed of the conveyor belt (speed ft/minute), set the gear ratio to the conveyor gear ratio in use.1.Calculate the conveyor gear ratio using the formulabelow:•Conveyor gear ratio =•where:•Gearhead ratio = ratio of inline or 90 degree gearbox •Pulley diameter = Diameter of Drive Pulley (Ft)-2200 Series = 0.104-3200 Series = 0.25-2200 Precision Move End Drive Series = 0.125-2200 Precision Move Mid Drive Series = 0.167-3200 Precision Move End Drive Series = 0.275-2200 Modular Belt Series = 0.125-5300 Modular Belt Series = 0.325-5200 Modular Belt Series = 0.325•Drive Sprocket Teeth = Number of teeth on sprocket connected to gearmotor. Note: For all side drives = 1.•Driven Sprocket Teeth = Number of teeth on sprocket connected to conveyor shaft. Note: For all side drives = 1.•Example:-2200 Series Conveyor with a 62M015PLBDDEN Gear-motor and a light load bottom mount with a 44 tooth pulley on the gearmotor and a 22 tooth pulley on the conveyor.•Conveyor gear ratio =•Conveyor gear ratio = 21.5(Gearhead Ratio) x (Drive Sprocket T eeth)(4.28 Factor) x (Pulley Dia.) x (3.14) x (Driven Sprocket T eeth)NOTETo convert the display to meters/min., enter allpulley diameters in meters and omit the 4.28division factor in the equation.(Gearhead Ratio) x (Drive Sprocket T eeth)(4.28 Factor) x (Pulley Dia.) x (3.14) x (Driven Sprocket T eeth)(15) x (44)(4.28) x (0.104) x (3.14) x (22)851-738 Rev. B15Dorner Mfg. Corp.Dorner Mfg. Corp.16851-738 Rev. BBrushless DC Motor ControlOperation2.Press MODE to switch to the data setting mode. The PRGM LED (Figure 34,item 1) will illuminate and “SPd” (Figure 34,item 2) will be displayed.Figure 343.Press up (Figure 35,item 1) to select “Gr-r”(Figure 35,item 2) (gear ratio), and then press SET (Figure 35,item 3).Figure 354.Press up or down (Figure 36,item 1) to select the speed display mode “cv” (Figure 36,item 2), and then press SET (Figure 36,item 3):Figure 36•cv: Conveyor transfer speed display (the m/min LED will illuminate).5.Press up or down (Figure 37,item 1) to change theconveyor gear ratio (e.g., 100 (Figure 37,item 2)). Pressing and holding the key for 3 seconds or more will increase or decrease the value successively.Figure 376.After the gear ratio has been changed, press SET (Figure 37,item 3) to confirm the new setting.7.Press MODE to switch to the monitor mode. The r/min LED or m/min LED will illuminate according to the specified display mode.Brushless DC Motor Control OperationSetting Speed While Motor is Running1.While the motor is running, press MODE (Figure38,item1) with the display showing the speed (e.g.,1000 r/min) (Figure 38,item2). The MNTR LED(Figure 38,item3) will blink.Figure382.Press up or down (Figure 39,item1) to change motorspeed and set operation data to write the current speed to(e.g., SPd1) (Figure 39,item2).Figure393.Press SET (Figure 40,item1). The new speed will beset to the operation data digitally.Figure40 Switching the Signal Method to Remote Signal (If Required)1.Turn on the power.2.Set the operation method to “Remote”.The initial setting is “Lo” (digital operator).a.Press MODE to switch to the digital operator/externalinput signal setting mode. The LO/RE LED (Figure41,item1) will illuminate.Figure41b.Press up or down (Figure 41,item2) select to select“RE”(remote operator).c.Press SET (Figure 41,item3) to confirm the selection.The display will blink.851-738 Rev. B17Dorner Mfg. Corp.NotesBrushless DC Motor ControlDorner Mfg. Corp.18851-738 Rev. B851-738 Rev. B19Dorner Mfg. Corp.Brushless DC Motor ControlService PartsBrushless DC Motor ControlNOTEFor replacement parts other than those shown in this section, contact an authorized Dorner Service Center or the factory. Key Service Parts and Kits are identified by the Performance Parts Kits logo . Dorner recommends keeping these parts on hand.124536Item Part Number Description163MBD11B60Controller, 115 Volts, 60 Watts 63MBD23B60Controller, 230 Volts, 60 Watts 63MBD11B200Controller, 115 Volts, 200 Watts 63MBD23B200Controller, 230 Volts, 200 Watts 2807-2190Cord Cover3920416M Socket Head Screws, M4-0.70x16 (x4)4350292Mounting Bars (x2)5639971MK10T -Bar, Single Drop-In (x10)6920616M Socket Head Screws, M6-1.00x16 (x2)851-738 Rev. B Printed in U.S.A.Dorner Mfg. Corp. reserves the right to change or discontinue products without notice. Allproducts and services are covered inaccordance with our standard warranty. All rights reserved. © Dorner Mfg. Corp. 2012DORNER MFG. CORP .975 Cottonwood Ave., PO Box 20 Hartland, WI 53029-0020 USA TEL 1-800-397-8664 (USA)FAX 1-800-369-2440 (USA)Internet: Outside the USA:TEL 1-262-367-7600FAX 1-262-367-5827Return PolicyReturns must have prior written factory authorization or they will not be accepted. Items that are returned to Dorner without authorization will not be credited nor returned to the original sender. When calling for authorization, please have the following information ready for the Dorner factory representative or your local distributor: and address of customer.2.Dorner part number(s) of item(s) being returned.3.Reason for return.4.Customer's original order number used when ordering the item(s).5.Dorner or distributor invoice number (if available, part serial number).A representative will discuss action to be taken on the returned items and provide a Returned Goods Authorization (RMA) number for reference. RMA will automatically close 30 days after being issued. To get credit, items must be new andundamaged. There will be a return charge on all items returned for credit, where Dorner was not at fault. It is the customer’s responsibility to prevent damage during return shipping. Damaged or modified items will not be accepted. The customer is responsible for return freight.Returns will not be accep ted after 60 days from original invoice date. The return charge covers inspection, cleaning,disassembly, disposal and reissuing of components to inventory. If a replacement is needed prior to evaluation of returned item, a purchase order must be issued. Credit (if any) is issued only after return and evaluation is complete.Dorner has representatives throughout the world. Contact Dorner for the name of your local representative. Our Customer Service Team will gladly help with your questions on Dorner products.For a copy of Dorner's Warranty, contact factory, distributor, service center or visit our website at .For replacement parts, contact an authorized Dorner Service Center or the factory.Product TypeStandard ProductsEngineered to order partsProduct LineConveyors Gearmotors & Mounting Packages Support Stands Accessories Spare Parts (non-belt)Spare Belts - Standard Flat Fabric Spare Belts - Cleated & Specialty FabricSpare Belts -Plastic Chain All equipment and parts110030% return fee for all products except:50% return fee for conveyors with modular belt,cleated belt or specialty beltsnon-returnablecase-by-case22002200 Modular Belt 2200 Precision Move 23002300 Modular Belt 32003200 LPZ3200 Precision Move 4100520053006200Controls 7200 / 730050% return fee for all products7350non-returnable736074007600。
系统部署手册
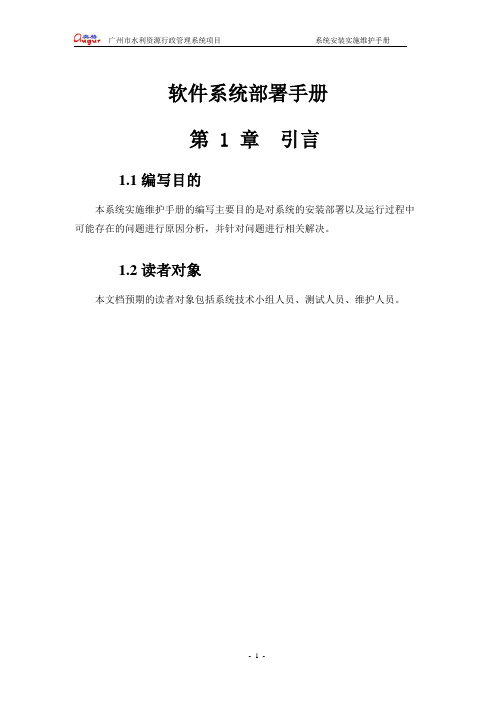
软件系统部署手册第 1 章引言1.1 编写目的本系统实施维护手册的编写主要目的是对系统的安装部署以及运行过程中可能存在的问题进行原因分析,并针对问题进行相关解决。
1.2 读者对象本文档预期的读者对象包括系统技术小组人员、测试人员、维护人员。
第 2 章JDK1.6安装1、双击2、出现安装界面如图1-1图1-13、选择接受,出现如图1-2图1-2这时要选择更改路径到C:\,路径尽可能不要出现空格(尽管很多时候有空格也不会出错)4、点击更改之后出现1-3界面图1-35、单击确定之后下一步,一直到出现图1-4图1-4 6、第5步进度条执行完毕后出现图1-5这里和第3步-第4步是一样的,更改路径7、更改路径之后出现图1-6图1-6 8、直接点击下一步出现图1-7,正在安装…..图1-79、安装完毕后出现图1-8图1-8二、配置环境变量1、安装好jdk之后我们在cmd中运行两个命令,java和javac结果如图1-9图1-9运行结果java是可以运行的,javac不是本地命令,那为什么呢?javac是将我们编写的.java代码编译为中间代码.class,再由java命令来执行.class文件2、右击我的电脑选择属性如图1-10图1-10选择“属性->高级”之后出现界面再选择高级如图1-11图1-11选择单击“环境变量”出现如图1-12图1-12单击“新建”系统变量如图1-13图1-13黄线标出来的是变量名,等会path中需要用到,变量值是你安装jdk的目录,我建议大家去安装的目录中copy过来,以免输入错误。
如图1-14图1-14单击“确定”。
3、刚才定义的那个系统环境变量名“JA V A_HOME”现在就要用上了。
选中path 后如图1-15可以单击“编辑”当然也可以双击进行编辑图1-15如图1-16在变量值的最后加上“%JA V A_HOME%\bin;(%JA V A_HOME%\bin等同于jdk中bin的文件夹路径)”,环境变量path,是操作系统查找可执行程序是要搜索的路径,在配置java时,只需要在初始值后添加“%JA V A_HOME%\bin;”即可(中间用“;”隔开)初始值:(%SystemRoot%\system32;%SystemRoot%;%SystemRoot%\System32\Wbem)图1-16单击“确定”、“确定”、“确定”。
使用手册 Use manual-BJ HY
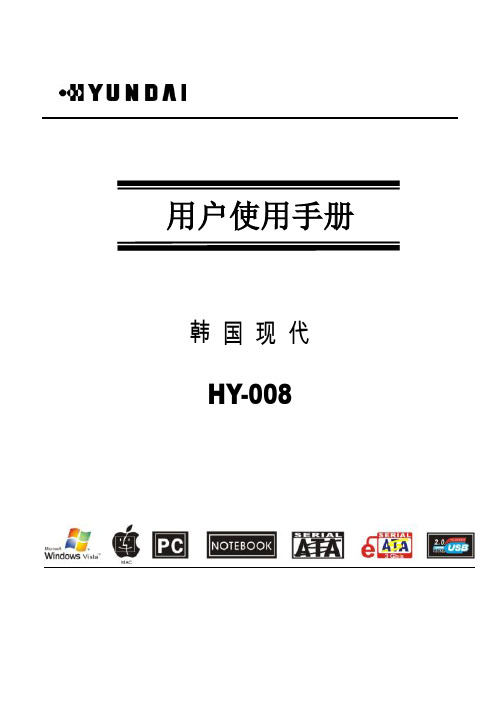
用户使用手册韩国现代HY-008一、前言感谢您选购本公司外置盒系列产品! 我们将带给您一个全新的、安全便捷的移动存贮器的新概念。
对于PC系统或MAC系统的用户,在扩充硬盘容量及提高数据的可移动性,提供了一个最佳的解决方案!在您使用之前,请您详细阅读本手册,以便更好的熟悉本产品。
二、系统要求:安装此驱动的环境条件:2.1.硬件需求:有一个空闲的USB接口的个人PC机、笔记本电脑或MAC机。
若系SATA、eSATA或1394机种,还要有相应的SATA、eSA TA或1394接口.2.2.操作系统:WIN 98/98SE、WINME、WIN2000、WINXP、VISTA,MAC OS 8.60 或以上版本。
三、性能:(1) 即插即用,支持热插拔;(2) 支持USB2.0,兼容USB1.1;(3) 支持SA TA接口(若是SATA接口机种);(4) 支持eSA TA接口(若是eSATA接口机种);(5) 硬盘所需运行环境: WIN98/SE/ME /2000/XP、VISTA,MAC OS 8.6 或以上版本。
四、包装配件:1.外置盒一台.2.驱动光盘一个3.USB数据线各一条)4.螺丝包一个5.干燥剂一包(勿食用)6. 螺丝刀一把(选配)五、SATA 接口硬盘的硬件安装:1. 从包装盒中取出产品,并打开产品面盖;2. 将内部的7PIN SA TA红色细扁数据线15P SA TA电源线, 插入SA TA硬盘上的相应7+15PIN接口。
3. 检查内部连接OK后, 装好盒子并锁紧镙丝;4. 插入USB数据电缆;最后打开电源开关.5. (1)这时电脑会识别到一个可移动硬盘.(2)点击移动硬盘图标可在您电脑的任务栏上会出现一个安全可移动硬盘的图标,点击它,在电脑依旧开机的情况下,您就可以安全移除硬盘盒。
(注: SA TA 或ESA TA有可能不会出现安全移除符号,要安全移除请在移动硬盘空闲以后,即读写灯不闪时)(3) 注意事项:本产品采用USB2.0接口,建议您使用高速USB2.0,以发挥产品的最高性能。
系统安装维护手册

服务器安装使用指南目录1.安装准备 (2)1.1文档声明 (2)1.2 安装必备 (2)1.3运行环境 (2)2.应用设置 (3)3.配置数据库 (3)3.1安装Oracle 10g (4)3.2 Oracle 10g数据库的初始化 (8)3.3安装Oracle 9i (11)3.4 Oracle 9i 数据库的初始化 (15)4.应用服务器配置 (19)4.1安装BEA9.2版 (19)4.2应用服务器的配置 (20)5.BEA系统参数设置 (25)5.1修改系统登录端口 (25)5.2 BEA性能调优 (26)6.课件服务器配置 (28)6.1创建FTP站点用户访问帐号 (28)5.2创建与访问帐号对应的目录 (29)5.3创建“用户隔离”FTP站点 (30)5.4修改IIS默认站点主目录 (31)5.5课件服务器的分配 (32)6.系统初始化 (33)7.数据库备份和恢复 (33)7.1 数据库备份 (33)7.2 数据库恢复 (34)1.安装准备1.1文档声明此系统安装维护手册适用于广东省地税教育培训学习管理系统(版本10.039)1.2 安装必备1.数据库软件: Oracle 10g2.应用服务器软件: BEA Weblogic 9.23.数据库初始化脚本:Study.sql4.系统编译包: WebRoot.rar压缩包(安装时须解压)5.数据库备份: StudyBackup.bat6.恢复数据: 恢复数据库.txt1.3运行环境注:数据库服务器和应用服务器共用一台服务器2.应用设置1.在WebRoot文件夹下,搜索sysConfig.xml,右键记事本打开进行编辑,该文件中的记录最高级单位名称,简介和初始部门名称(defaultOrganName为单位名称,defaultOrganShortName为单位简介, defaultOrganDeptName为初始部门名称),DefaultManagerActualName为系统最高权限用户名字,defaultRootUserName为最高权限用户登录账号, defaultManagerPassword为所有管理员用户登录初始密码,defaultUserPassword为普通用户登录系统的初始密码, defaultManagerNamePrefix为新建下级单位管理员登录系统账号前缀,defaultManagerNamePostfix新建下级单位管理员登录系统账号后缀,新建单位管理员的登录账号为”前缀+编号+后缀”。
Caché使用维护手册

前 言应广大用户的要求,经过InterSystems培训部及技术部等部门的共同努力,经过长时间的筹划,这本Caché5.0使用及维护手册,终于与InterSystems的朋友们见面。
本手册主要是针对Caché5.0,在Windows系统下的操作和使用指南。
本手册作为Caché的维护精粹,凝集了本公司维护及培训人员的经验结晶,通过详尽的描述,力求具体,深入,精炼,让各位用户在实际工作中能够预防问题的出现,并能够准确判断故障出现的原因进而解决问题。
由于编写人员的知识水平和收集资料所限,缺点疏漏在所难免,恳请广大用户,提出宝贵意见,以便再版时修订补充!InterSystems2006-8-24目 录1安装及卸载 (2)安装Caché (2)安装许可证(Caché License) (2)卸载Caché (3)2配置缓存..........................................................................................................4三缓存简介. (4)数据缓存配置 (4)程序缓存配置 (6)3指令日志 (8)数据库物理操作日志 (8)WIJ概述 (8)WIJ 配置方法 (9)Journaling概述 (9)Journaling配置方法 (10)Journal 文件 (12)Journal文件设置 (13)查看 Journal 文件内容方法: (14)崩溃缓冲 (14)4镜像服务 (16)镜像服务原理 (16)镜像服务的特点: (16)镜像服务的配置 (17)配置方法: (17)5备份及恢复 (21)备份种类 (21)备份流程 (21)备份方法 (21)Caché中备份数据库的方法: (21)其它外部备份方法 (23)备份的恢复 (25)恢复方法 (25)Caché中的数据恢复 (25)其他方法的数据恢复 (26)6ECP网络 (28)ECP原理 (28)ECP特点: (29)ECP配置 (29)ECP配置方法: (29)ECP 监视 (33)1 安装及卸载安装CachéCaché的安装非常简单,插入安装光盘,在Windows下,运行安装文件目录下的SETUP.EXE ,根据安装向导,即可操作完成!安装许可证(Caché License)在拿到了Cache.key文件以后,把这个文件拷贝到c:\Cachesys\mgr(c:\Cachesys\是默认的安装路径,如果你没有按照默认安装,可以更改为您Caché的路径)。
安装部署手册(范文)

密级:秘密用户手册编制:审核:批准:变更记录目录1概述 (1)1.1简介 (1)1.2运行环境 (1)1.3术语表 (2)1.4版权声明 (2)2安装与启动 (3)2.1运行环境安装 (3)2.2系统安装与配置 (4)2.3系统启动 (4)2.4系统卸载 (5)3操作说明 (5)3.1模块一 (5)3.1.1功能描述 (5)3.1.2界面图示 (5)3.1.3操作描述 (5)3.2模块二 (5)3.3功能描述 (5)3.4界面图示 (5)3.5操作描述 (5)4疑难解答 (6)4.1问题一 (6)4.2问题二 (6)5附录 (6)1概述1.1简介【对系统进行简单介绍,扼要说明系统所提供的主要功能,以及帮助用户所解决的问题,指出预期的读者】1.2运行环境【说明系统所需要的运行环境,包括:硬件设备、支持软件和数据结构等】1.硬件设备列出为运行本软件所要求的硬设备的最小配置,如:1)处理机的型号、内存容量2)所要求的外存储器、媒体、记录格式、设备的型号和台数、联机/脱机;3)I/O设备(联机/脱机);4)数据传输设备和转换设备的型号、台数2.支持软件说明运行本软件所需要的支持软件,如:1)操作系统的名称、版本号;2)程序语言的编译/汇编系统的名称和版本号3)数据库管理系统的名称和版本号4)其他支持软件。
3.数据结构列出为支持本软件的运行所需要的数据库活数据文卷。
【举例】服务器端:1)主机类型配置 WEB应用服务器/报表服务器数据库服务器(WEB Server & ApplicationServer)(DatabaseServer)型号型号自选 UNIX服务器、型号自选CPU 2.8G以上双CPUE-cache 1M以上 1M以上内存 2G以上 4G以上硬盘 80G以上 100G以上光驱普通光驱可刻录DVD光驱磁带普通磁带机普通磁带机2)网络类型§ intrant§ internet3)操作系统应用服务器用WINDOWS系统,数据库服务器用UNIX操作系统4)数据库管理系统ORACLE数据库5)其他支撑软件WebLogic、中创报表工具及备份策略客户端:CPU: PIII733或celeron1G以上。
AT Controls SY 系列霍克伏尔法驱动器安装与维护手册说明书
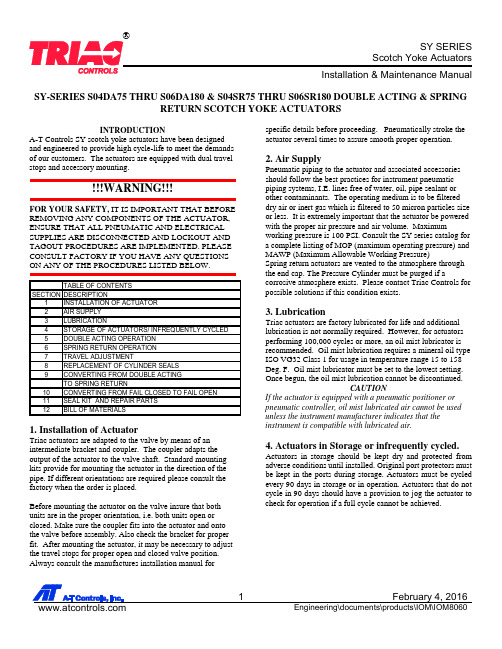
SY-SERIES S04DA75 THRU S06DA180 & S04SR75 THRU S06SR180 DOUBLE ACTING & SPRINGRETURN SCOTCH YOKE ACTUATORSINTRODUCTIONA-T Controls SY scotch yoke actuators have been designedand engineered to provide high cycle-life to meet the demandsof our customers. The actuators are equipped with dual travel stops and accessory mounting.WARNINGFOR YOUR SAFETY, IT IS IMPORTANT THAT BEFORE REMOVING ANY COMPONENTS OF THE ACTUATOR, ENSURE THAT ALL PNEUMATIC AND ELECTRICAL SUPPLIES ARE DISCONNECTED AND LOCKOUT AND TAGOUT PROCEDURES ARE IMPLEMENTED. PLEASE CONSULT FACTORY IF YOU HAVE ANY QUESTIONSON ANY OF THE PROCEDURES LISTED BELOW.1. Installation of ActuatorTriac actuators are adapted to the valve by means of an intermediate bracket and coupler. The coupler adapts theoutput of the actuator to the valve shaft. Standard mountingkits provide for mounting the actuator in the direction of the pipe. If different orientations are required please consult the factory when the order is placed.Before mounting the actuator on the valve insure that bothunits are in the proper orientation, i.e. both units open or closed. Make sure the coupler fits into the actuator and ontothe valve before assembly. Also check the bracket for proper fit. After mounting the actuator, it may be necessary to adjust the travel stops for proper open and closed valve position. Always consult the manufactures installation manual for specific details before proceeding. Pneumatically stroke the actuator several times to assure smooth proper operation.2. Air SupplyPneumatic piping to the actuator and associated accessories should follow the best practices for instrument pneumatic piping systems, I.E. lines free of water, oil, pipe sealant or other contaminants. The operating medium is to be filtered dry air or inert gas which is filtered to 50 micron particles size or less. It is extremely important that the actuator be powered with the proper air pressure and air volume. Maximum working pressure is 100 PSI. Consult the SY series catalog for a complete listing of MOP (maximum operating pressure) and MAWP (Maximum Allowable Working Pressure)Spring return actuators are vented to the atmosphere through the end cap. The Pressure Cylinder must be purged if a corrosive atmosphere exists. Please contact Triac Controls for possible solutions if this condition exists.3. LubricationTriac actuators are factory lubricated for life and additional lubrication is not normally required. However, for actuators performing 100,000 cycles or more, an oil mist lubricator is recommended. Oil mist lubrication requires a mineral oil type ISO VG32 Class 1 for usage in temperature range 15 to 158 Deg. F. Oil mist lubricator must be set to the lowest setting. Once begun, the oil mist lubrication cannot be discontinued.CAUTIONIf the actuator is equipped with a pneumatic positioner or pneumatic controller, oil mist lubricated air cannot be used unless the instrument manufacturer indicates that the instrument is compatible with lubricated air.4. Actuators in Storage or infrequently cycled. Actuators in storage should be kept dry and protected from adverse conditions until installed. Original port protectors must be kept in the ports during storage. Actuators must be cycled every 90 days in storage or in operation. Actuators that do not cycle in 90 days should have a provision to jog the actuator to check for operation if a full cycle cannot be achieved.5. Double Acting OperationApplying air pressure to the CCW Port drives the piston toward the end cap which turns the yoke counterclockwise when viewed from the accessory side of the actuator. When pressure is applied to the CW Port the piston is driven towards the adapter which turns the yoke clockwise. This is shown in Figure 1Figure 16. Spring Return OperationApplying air pressure to the CCW Port drives the piston toward the end cap as the spring is compressed. This rotates the yoke counterclockwise when viewed from the accessory side of the actuator. When pressure is relieved at the CCW Port the spring drives the piston towards the adapter which turns the yoke clockwise. This is shown in figure 2. To reverse the failure mode turn the actuator over.Figure 27. Travel AdjustmentThe Triac SY actuators have + or - 8 degree adjustment of the end of travel stops in both the open and close directions. CAUTION: DO NOT ATTEMPT TO ADJUST STOP BOLT WITH AIR PRESSURE OR SPRING FORCE APPLIED TO THE STOP BOLT. ALWAYS JOG ACTUATOR AWAY FROM STOP BOLT BEFORE ADJUSTING.The stop bolts are in the rod cover and the end cap of the actuator. Figure 3 shows the stop bolt locations loosen the lock nut and adjust stop bolt as required then retighten lock nut.Figure 3WARNINGFOR YOUR SAFETY, IT IS IMPORTANT THAT BEFORE REMOVING ANY COMPONENTS OF THE ACTUATOR, ENSURE THAT ALL PNEUMATIC AND ELECTRICAL SUPPLIES ARE DISCONNECTED AND LOCKOUT AND TAGOUT PROCEDURES ARE IMPLEMENTED.8. Replacement of Cylinder SealsWhen the cylinder seals must be replaced, because of leakage or a preventive scheduled maintenance, the following procedure must be followed. Note only the soft parts indicated on page 5 are included in a seal kit. If additional parts are required they must be ordered separately.1.Disconnect electrical supplies and shut off pneumaticsupply, vent actuator and remove from valve or damper.2.Remove any accessories mounted on top of actuator.3.For spring return actuators the spring tension must berelieved before starting. Apply air pressure until thepiston moves off the stop bolt located on the rod cover.DO NOT LOOSEN THE BOLT ON THE END CAP BYTHE SPRING CYLINDER. Loosen the hex nut (item 47)then back out the stop bolt (item 48) until the preload isrelieved. For double acting units the actuator should be inthe clockwise position with the piston next to the centerbody front flange (item 37).4.Vent all air pressure from the cylinder (item 14).5.Remove the 4 nuts (item 24) on the spring cartridge tierods (item 2). Then slide the spring cartridge out over thetie rods.6.Remove the tie rods (item 2).7.Remove the cylinder (item 21) from the front flange (item37) by pulling over the piston (item 7). Use caution not toscratch the cylinder bore when sliding over piston.8.Remove the lock nut setscrews (item 19) from the locknut (item 20). Remove the lock nut (item 20).9.Remove the piston (item 7), piston O-ring (item 34).10.Remove front flange bolt (item 35) and lock washer (item36). Remove front flange (item 37) carefully over pistonrod.11.Remove the bolts (item 11) from rod cover and carefullyslide over the piston rod.12.Remove snap ring (item 11) on yoke shaft (item39) andremove yoke shaft spacer (item 17). Slide yoke shaft(item 39) down thru body and carefully remove frombottom of actuator as not to damage the upper and lowerbearings and O-rings.13.Remove the piston rod and yoke assembly thru thepressure port opening.14.Remove the O-rings from the piston and both flanges.15.Clean all parts with a mild solvent that will not attack thecoating on the parts.16.The center body assembly should be inspected before thepressure group is rebuilt.17.Inspect the Yoke pin bushing (bronze slider) (item 4) forwear along with the slot in the yoke arm.18.Inspect the upper and lower yoke shaft bearings (item 14)for wear.19.Wipe out old grease and replace with new grease on allsliding surfaces.20.Install new O-rings to replace the old O-rings removedearlier.21.Install the piston rod and yoke assembly thru the pressureport opening.22.Then reinstall Yoke shaft into yoke aligning the key intothe keyway, then install bearings using care not to harmthe bearings or the O-rings. Reinstall the yoke washer and snap ring.23.Install front flange O-ring in groove.24.Reinstall front flange with rod bearing over piston rod andslide into position and torque bolts in a diagonal pattern.25.Install rod cover O-ring on rod cover.26.Reinstall rod cover and rod bearing over piston rod andslide into position and torque bolts in a diagonal pattern.27.Check actuator for freedom of movement before installingpressure group.28.Lightly grease the O-ring for the front flange and install inthe groove.29.Lightly grease O-ring (item 34) and slide over piston rod.Slide piston over piston rod and install lock nut Tightensecurely and install set screws.30.At this point the piston should be able to be pushed backand forth to insure that all parts are in proper alignmentand working properly. 31.Lightly grease piston grooves and install O-ring and back-up strip.32.Lightly grease cylinder completely on the inside surfaceand carefully slide over the piston until seated on theadapter.33.Lightly grease the O-ring for the end cap and install in thegroove. Place end cap over the tie rods and seat on thecylinder. Be sure to keep the original alignment of theNPT port.34.Reinstall the tie rod nuts and tighten in a diagonal pattern.35.To pressure test a double acting actuator proceed to thenext step for a spring return go the step 39.36.Connect 2 psig air to the body (CCW Port) and cycle theactuator then connect to the end cap (CW Port) and cycle the actuator several times.37.Apply 100 psig air to the Body and check for leakage atthe adapter/cylinder connection and the yoke bearings.Place a flexible tube in the end cap NPT port and checkfor leakage across the piston by checking for bubbles in a cup of water. Relieve air pressure on cylinder.38.Apply 100 psig air to the end cap and check for leakage atthe end cap/cylinder connection. Place a flexible tube inthe body NPT port and check for leakage across thepiston. Relieve air pressure on cylinder.39.Apply supply pressure to the body and check for leakageat the front flange/cylinder connection and the yokebearings. Then check for leakage across the piston byusing the method in step 37 above.40.Position stop bolts back to 90 degrees position and tightenlock nuts.41.The actuator is now ready to return to service.9. Converting from Double Acting to SpringReturnWARNINGFOR YOUR SAFETY, IT IS IMPORTANT THAT BEFORE REMOVING ANY COMPONENTS OF THE ACTUATOR, ENSURE THAT ALL PNEUMATIC AND ELECTRICAL SUPPLIES ARE DISCONNECTED AND LOCKOUT AND TAGOUT PROCEDURES ARE IMPLEMENTED.1.Disconnect electrical supplies and shut off pneumaticsupply, vent actuator and remove from valve or damper.2.Loosen the stop bolt nut on rod cover and back out.3.Remove the Tie rod nuts (item 24) and the lock washers(item 23). Remove the end cap and inspect the O-ring.4.Install Spring cartridge end cap and replace lock washersand nuts.5.Apply air pressure to compress spring and loosen nut onspring end cap to adjust travel stop as needed for the openposition.6.Apply air pressure and check for smooth operation. 10. Changing from “Spring Closed” to “Spring Open”To convert from spring closed to spring open requires that the actuator be mounted with the Triac logo towards the valve. Simply turn the actuator over. As both sides are symmetrical.11. Seal kits and Repair PartsTo order replacement seal kits or spare parts please provide the following information:Actuator Model NumberSerial NumberType of seal kit (Nitrile standard, low temperature, Viton Item Number, Description and quantity for repair parts.A-T Controls product, when properly selected, is designed to perform its intended function safely during its useful life. However, the purchaser or user of A-T Controls products should be aware that A-T Controls products might be used in numerous applications under a wide variety of industrial service conditions. Although A-T Controls can provide general guidelines, it cannot provide specific data and warnings for all possible applications. The purchaser / user must therefore assume the ultimate responsibility for the proper sizing and selection, installation, operation, and maintenance of A-T Controls products. The user should read and understand the installation operation maintenance (IOM) instructions included with the product, and train its employees and contractors in the safe use of A-T Controls products in connection with the specific application.While the information and specifications contained in this literature are believed to be accurate, they are supplied for informative purposes only. Because A-T Controls is continually improving and upgrading its product design, the specifications, dimensions and information contained in this literature are subject to change without notice. Should any question arise concerning these specifications, the purchaser/user should contact A-T Controls.For product specifications go to /A-T Controls, Inc. • 9955 International Boulevard, Cincinnati, OH 45246 • Phone: (513) 530-5175 • Fax: (513) 247-5462 • 。
Parker Balston 72-007气接收器安装、操作和维护手册说明书
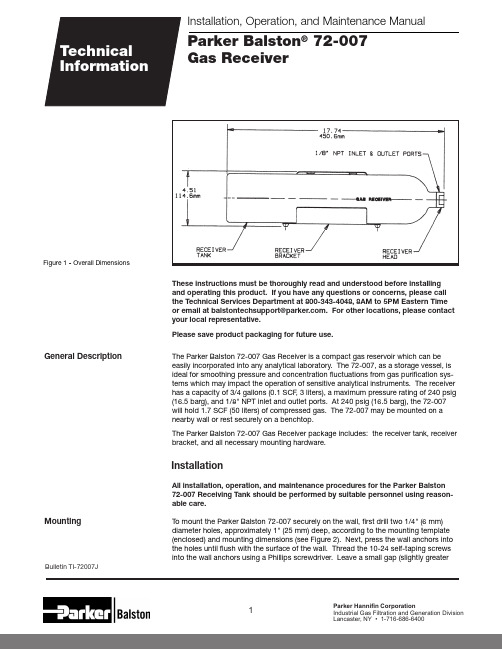
Parker Hannifin Corporation Industrial Gas Filtration and Generation Division Lancaster, NY • 1-716-686-64001All installation, operation, and maintenance procedures for the Parker Balston 72-007 Receiving Tank should be performed by suitable personnel using reason-able care.To mount the Parker Balston 72-007 securely on the wall, first drill two 1/4" (6 mm)diameter holes, approximately 1" (25 mm) deep, according to the mounting template (enclosed) and mounting dimensions (see Figure 2). Next, press the wall anchors into the holes until flush with the surface of the wall. Thread the 10-24 self-taping screws into the wall anchors using a Phillips screwdriver. Leave a small gap (slightly greaterFigure 1 - Overall DimensionsThese instructions must be thoroughly read and understood before installing and operating this product. If you have any questions or concerns, please call the Technical Services Department at 800-343-4048, 8AM to 5PM Eastern Time **************************************.Forotherlocations,pleasecontact your local representative.Please save product packaging for future use.The Parker Balston 72-007 Gas Receiver is a compact gas reservoir which can beeasily incorporated into any analytical laboratory. The 72-007, as a storage vessel, is ideal for smoothing pressure and concentration fluctuations from gas purification sys-tems which may impact the operation of sensitive analytical instruments. The receiver has a capacity of 3/4 gallons (0.1 SCF , 3 liters), a maximum pressure rating of 240 psig (16.5 barg), and 1/8" NPT inlet and outlet ports. At 240 psig (16.5 barg), the 72-007 will hold 1.7 SCF (50 liters) of compressed gas. The 72-007 may be mounted on a nearby wall or rest securely on a benchtop.The Parker Balston 72-007 Gas Receiver package includes: the receiver tank, receiver bracket, and all necessary mounting hardware.General Description Mounting Bulletin TI-72007JInstallationBulletin TI-72007JInstallation, Operation and Maintenance ManualTechnical Information Parker Balston ® Model 72-007 Gas Receiver Parker Hannifin Corporation Industrial Gas Filtration and Generation Division Lancaster, NY • 1-716-686-64002Piping Figure 2Mounting Dimensions Figure 3Sample InstallationNOTE: RECEIVER SHOULD BE CENTERED ONBRACKET DURING USE AND STORAGE.Principal Specifications Model Number72-007Material of Construction3003 Aluminum Max. Temperature130°F (54°C)****************************240 psig (16.5 barg) Capacity @ Atmospheric Pressure0.1 SCF (3 liters)Capacity @ 60 psig (4.1 barg)0.5 SCF (14 liters)Capacity @ 80 psig (5.5 barg)0.7 SCF (18 liters)Capacity @ 100 psig (6.9 barg)0.8 SCF (22 liters)Dimensions 5" dia. x 18" length (12 cm x 45 cm)Shipping Weight 4 lb. (2 Kg)than the thickness of the bracket) between the head of the screw and the surface of the wall. Hang the receiver bracket on the wall, lining up the keyhole slots and the installed screws. Finally, tighten the self-tapping screws until the receiver bracket is snug against the wall. Do not over-tighten. Over-tightening may strip the wall anchors.Check the epoxy bead which has been deposited at the interface of the receiver head andreceiver body to ensure proper alignment and seal integrity. (The epoxy bead was depos-ited at the factory after seal integrity was assured.) If the epoxy bead is not intact, tighten receiver head until the bead is aligned and pressure test for leaks. If unit continues to leak after tightening, consult the factory.Place the 72-007 receiver tank in the bracket, either on the wall or on the benchtop. Pipe the supply gas to the 1/8" NPT inlet port (use PTFE tape as needed), labeled “1”, on thehead of the receiver. (Note: The inlet and outlet ports are interchangeable, if needed, forease of installation). Pipe the gas from the outlet port, labeled “2”, to the instrument or analyzer (see Figure 3). Re-check the epoxy bead on the receiver.Do not rotate the receiver head relative to the body. Rotation of the receiver head may loosen the seal and cause the gas receiver to leak.Purge the receiver and downstream piping for 5 to 10 minutes prior to initial startup of analytical equipment to ensure gas purity throughout the system.Copyright© Parker Hannifin Corporation 2001, 2011 Printed in U.S.A. Bulletin TI-72007J Parker Hannifin (UK) Ltd Gas Separation & Filtration Division EMEA Dukesway, Team Valley Trading Estate Gateshead, Tyne & Wear, NE11 0PZ United Kingdom Ph: +44 (0)191 402 /gsfeParker Hannifin CorporationIndustrial Gas Filtration and Generation Division 4087 Walden Avenue Lancaster, NY 14086Tel: 716-686-6400 Fax: 。
科特斯spa热水器安装、使用和维护手册说明书
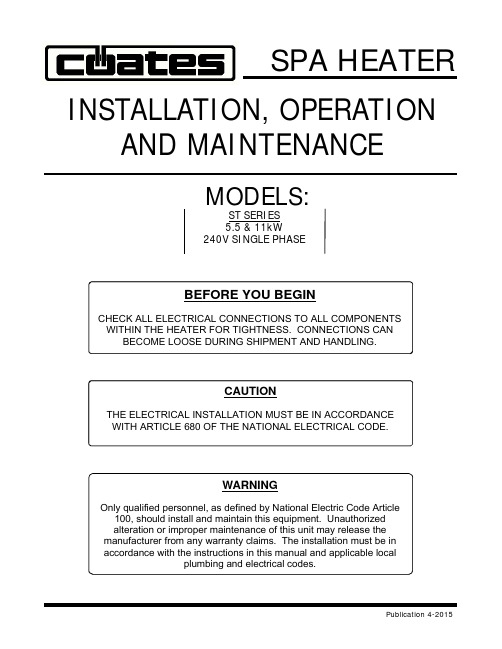
SPA HEATERMODELS:ST SERIES 5.5 & 11kW240V SINGLE PHASEWARNINGOnly qualified personnel, as defined by National Electric Code Article 100, should install and maintain this equipment. Unauthorized alteration or improper maintenance of this unit may release the manufacturer from any warranty claims. The installation must be in accordance with the instructions in this manual and applicable localplumbing and electrical codes.CAUTIONTHE ELECTRICAL INSTALLATION MUST BE IN ACCORDANCE WITH ARTICLE 680 OF THE NATIONAL ELECTRICAL CODE.BEFORE YOU BEGINCHECK ALL ELECTRICAL CONNECTIONS TO ALL COMPONENTS WITHIN THE HEATER FOR TIGHTNESS. CONNECTIONS CANBECOME LOOSE DURING SHIPMENT AND HANDLING.INSTALLATION, OPERATIONAND MAINTENANCEPublication 4-20151.0 DESCRIPTIONCoates Spa Heaters are intended for use on spas or hot tubs having a forced water circulation system. The water flow through the heater should be at least 15 GPM but should not exceed 80 GPM. Higher flow may damage the heater. An external bypass should be installed to limit the flow to within this range.2.0 INSTALLATIONCHECK ELECTRICAL CONNECTIONS TO ALL COMPONENTS within the heater for tightness. These can become loose during shipment and handling.2.1 PHYSICAL PLACEMENTThe Coates Spa Heater is suitable for indoor or outdoor installation. See Figure 1 for piping connections and Figures 3A or 3B for electrical connections. The heater should be securely mounted to a smooth, flat surface. It may be conveniently located next to the filtration equipment. Leave minimum clearances of 9 inches on the left for element removal, 12 inches on the front for maintenance, 6 inches on the back for service entrance and the right side will be determined by the plumbing configuration used.2.2 ELECTRICAL INSTALLATIONThe electrical supply power must be single phase,2 wire, 240 VAC. The supply must be protected by a ground fault circuit interrupter (GFCI) in accordance with NEC Article 680. An electrical disconnect with over-current protection must be provided. An insulated ground conductor must be provided. See Figures 3A or 3B and Table 1 for supply wire and circuit sizing. A lug has been provided for attachment of the BONDING wire per the NEC Article 680-22, (a)(4). This lug is located between the inlet and outlet pipes of the heaterRefer to Table 2 for part description.CAUTIONTHE ELECTRICAL INSTALLATION MUST BE IN ACCORDANCE WITH ARTICLE 680 OF THE NATIONAL ELECTRICAL CODE (NEC).** NOTICE **NO PRESSURE RELIEF VALVE IS SHIPPED WITH THIS HEATER AND NONE IS REQUIRED PER UL STD 1261. DO NOT INSTALL SHUT OFF VALVE BETWEEN THE HEATER AND POOL OR SPA. A CHECK VALVE IS ACCEPTABLE AND IN ACCORDANCE TO UL STD 1261 REVISED JULY 1983.3.0 CONTROL PANELA. INDICATOR LIGHTSThe control has two indicator lights. The lights are as follows:STATUS LIGHTSLIGHT DESCRIPTION (when Illuminated ) FLOW Sufficient water flow through heater. ELEMENTHeating elements are powered.B. DIGITAL THERMOSTAT CONTROL For heaters equipped with a digital thermostat. The digital thermostat control which measures the temperature of the water as it enters the heater has a MENU button, up and down adjustment buttons, and an LED display. The desired water temperature (set point) is controllable between 40°F and 104°F (5°C and 40°C). The set point may differ from the actual water temperature at the pool or spa due to heat loss in the piping.MENU:The MENU button cycles through the three menu items: Measured Water Temperature (default), SET POINT and °F/°C.ADJUSTING THE SET POINT:Press one of the following buttons; MENU,or . The display will momentarily blank and then the current set point will be displayed. Press the or button to change the set point. Hold the button down for rapid temperature changes.The set point will be saved and the display will return to the measured temperature after two seconds of inactivity.OPERATION:In the measured temperature mode, the water temperature in the heater is displayed. The LED corresponding to the current temperature scale will be illuminated. If the heater is calling for heat the HEATING LED will be illuminated.FAHRENHEIT TO CELCIUS:Press the MENU button twice and the current temperature scale will be displayed ( F or C ). Press the or buttons to toggle between F and C.The temperature scale will be saved and the display will return to the measured temperature after two seconds of inactivity.ERROR CODE:The display will read “Err” when it detects a problem with the temperature sensor. This can be caused by a faulty sensor or a loose connection between the sensor and the temperature controller.3.1 CAUTIONS AND WARNINGS1. Be sure to check all cautions andwarnings in this manual and as displayed on the heater labels before operating or performing and maintenance on these heaters. 2. Do not remove the heater cover whileelectrical power is applied to the heater. Power must be interrupted at the heater supply circuit breaker or disconnect switch. 3. The MIN setting on the temperaturecontrol dial is an OFF position. The heater will not operate at this setting regardless of water temperature.3.2 STARTING THE HEATER - CAUTION -Do not operate heater without water.1. Ensure that heater case is properlygrounded, and bonded.2. Fill the system with water and start thecirculating pump.3. Turn on electrical power at the heatersupply circuit breaker.4. Set the temperature control to desiredwater temperature and adjust accordingly after the temperature has stabilized. DO NOT EXCEED 104°F.3.3 STOPPING THE HEATERTurn off electrical power at the heater supply circuit breaker before stopping the circulating pump.4.0 MAINTENANCE1. Keep the heater clean.2. If high temperature causes the limitthermostat to cut off the electrical power, turn off power at disconnect switch and determine the cause before resetting the switch. A water temperature drop is required to allow resetting of the manual reset high temperature limit. 3. If leaks develop in the heater orconnecting piping, shut down the heater and repair defective connections. 4. If heating elements are removed forreplacement, use only Coates elements, see Table 2.Wiring Diagram NOT LESS THAN # 12 AWG. 12411STTABLE 1MODEL NO. HEATERKW/VOLTRATING NO. & KW OFHEATINGELEMENTSHEATERCURRENTRATINGRECOMMENDEDCIRCUIT RATINGRECOMMENDEDSUPPLY WIRINGCOPPER @ 60° C12406ST 5.5 @ 240VAC *******23 AMPS 30 AMPS #10 AWG12411ST 11 @ 240 VAC *******46 AMPS 60 AMPS #4 AWGTABLE 2ITEM PARTNUMBER DESCRIPTION QTY1 – CON1 21000100 CONTACTOR, 2P, 50 AMP, 240VAC 22 - TC 22002150 DIGITAL TEMPERATURE CONTROL 13 - FLOW 23000105 FLOW SWITCH, 20 GPM 14 - HTL 22003820 HIGH TEMPERATURE LIMIT, MANUAL RESET 15 - RLY 21006010 FLOW RELAY, 30AMP, 240V 16 – PL1,2 29034620 PILOT LIGHTS for ELEMENT and FLOW 27 62002620VESSEL ASSEMBLY, STAINLESS STEEL 18 20005061 HEATING ELEMENT, 5.5KW, 240 VOLTS *929020025GROUNDLUG,LA-21 1029020035BONDINGLUG,SAU-701 1132705010UNIONASSEMBLY2 *SEE TABLE 1 FOR ELEMENT QUANTITYWhen ordering parts from your dealer, provide the model number and serial number of your heater.WARNING:Only qualified personnel should attempt maintenance on this equipment. (NEC Article 100)HEATER TROUBLE SHOOTING GUIDE- CAUTION -This heater incorporates 240 volt electrical circuits.Do not open the case unless unit is disconnected from electrical power. Use only manufacturer's parts, or UL listing and warranty may be void.Elements can be checked with an Ohm meter only when power is disconnected from heater and all wires have been removed from the element terminals. Each element should read approximately 10.5 Ohms.Ambient temperatures above 120°F will cause the high temperature limit to trip prematurely.Proper water balance is important to extending the life of your Coates Heater. While pH control is critical, the control of alkalinity and calcium hardness will protect against scaling and also help to prevent corrosion.ACID ALKALINE HEATER CAN BE DAMAGEDCORROSIVE WATERIDEAL RANGEALKALINE WATER0 1 2 3 4 5 6 7 7.2-7.88 9 10 11 12 13 14HEATER CAN BE DAMAGEDThe correct level of sanitizer, pH, total alkalinity and calcium hardness will very, depending on the type of pool (plaster, fiberglass or vinyl) and the chemical content of the fill water. Water that is out of balance can damage your pool heater and void the warranty. Thisheater is not for use in salt water pools.PROTECTING YOUR COATES HEATER WITH PROPER WATER CHEMISTRYIMPORTANT SAFETY INSTRUCTIONSWhen using this electrical equipment, basic safety precautions should always be followed, including the following.1) READ AND FOLLOW ALL INSTRUCTIONS.2) To reduce the risk of injury.A) The water in a pool or tub should never exceed 104°F (40°C). A water temperature in excess of104°F is considered unsafe for all persons. Lower water temperatures are recommended forextended use (exceeding 10-15 minutes) and for young children. SEE “STARTING THEHEATER” IN THE OPERATIONS & MAINTENANCE MANUAL FOR INSTRUCTIONS ON HOW TO ADJUST THE TEMPERATURE CONTROL.B) Since excessive water temperatures have a high potential for causing fetal damage during theearly months of pregnancy, pregnant or possibly pregnant women should limit pool or tub water temperatures to 100°F (38°C).C) Before entering a pool or tub, the user should measure the water temperature at several occupantlocations using an accurate thermometer since the tolerance of water temperature-regulatingdevices may vary as much as ± 5°F (± 3°C).D) Alcohol, drugs or medications should not be used before or during pool or tub use since their usemay lead to unconsciousness with the possibility of drowning.E) Obese persons and persons with a medical history of heart disease, low or high blood pressure,circulatory system problems, or diabetes should consult a physician before using a pool or tub.F) Persons using medication should consult a physician before using a pool or tub since somemedication may induce drowsiness while other medication may affect heart rate, blood pressure, and circulation.3) SAVE THESE INSTRUCTIONS.---WARNING---DANGER OF HYPERTHERMIAHyperthermia occurs when the internal temperature of the body reaches a level several degrees above the normal body temperature of 98.6°F. The symptoms of hyperthermia include dizziness, fainting, drowsiness, lethargy and an increase in the internal temperature of the body. The effects of hyperthermia include:a) Unawareness of impending hazard;b) Failure to perceive heat;c) Failure to recognize the need to exit pool or tub; d) Physical inability to exit pool or tub;e) Fetal damage in pregnant women;f ) Unconsciousness resulting in a danger ofdrowning.WARNING--- The use of alcohol, drugs or medications can greatly increase the risk of fatal hyperthermia in pools and tubs.6THIS PAGE INTENTIONALLY LEFT BLANKLIMITED WARRANTYThe company extends this limited warranty to the original purchaser of a Coates Electric Spa Heater.Coates warrants the electrical components* and wiring (excluding enclosure, enclosure parts, knobs and accessories) in this new Spa Heater to be free from defects in materials and workmanship for one (1) year from the provable date of purchase, or eighteen (18) months from date of factory shipment, whichever occurs first. Coates further warrants the stainless steel water containment vessel to be free from defects in materials and workmanship for two (2) years from the provable date of purchase or thirty (30) months from the factory shipment, whichever occurs first. Enclosure, enclosure parts, knobs and accessories have no warranty whatsoever.*Exception: Factory installed heating elements are warranted for ninety (90) days from the date of heater installation, or one (1) year from date of factory shipment, whichever occurs first.COATES will repair or replace at its option, defective component parts as explained above, during the warranty period provided such parts are returned to the factory, freight prepaid. Factory authorization MUST BE OBTAINED under this warranty before returning such defective parts.Limited Warranty Does Not Cover1. New products purchased outside the United States of America and Canada.2. Uncrating, unpacking, set-up, installation and / or startup of this unit.3. Adjustments to controls normally operated by consumer, purchaser or installer.4. This limited warranty does not extend to any defect, malfunction or failure caused by, or resulting from improperservice, maintenance or repair, abuse, neglect, accident, corrosion caused by improper water chemistry or byequipment that use salt to create a sanitizer, lack of water, or any other cause beyond the control of CoatesHeater Company, Inc. or to any product where the nameplate shall have been removed, altered, replaced, defaced or rendered illegible.5. This limited warranty is void if the Heater is used in a salt water system or under any extreme or unusualcorrosive condition for which stainless steel metals would not be recommended.6. This limited warranty does not extend to the repair or replacement of defective components except at COATES or aservice facility authorized by COATESIMPLIED WARRANTIES, WHEN APPLICABLE, SHALL COMMENCE UPON THE SAME DATE AS THE EXPRESS WARRANTY PROVIDED ABOVE, AND SHALL, EXCEPT FOR WARRANTIES OF TITLE, EXTEND ONLY FOR THE DURATION OF THE EXPRESS WARRANTY. SOME STATES DO NOT ALLOW LIMITATIONS ON HOW LONG AN IMPLIED WARRANTY LASTS, SO THE ABOVE LIMITATION MAY NOT APPLY TO YOU. THE ONLY REMEDY PROVIDED TO YOU UNDER AN APPLICABLE IMPLIED WARRANTY AND THE EXPRESS WARRANTY SHALL BE THE REMEDY PROVIDED UNDER THE EXPRESS WARRANTY, SUBJECT TO THE TERMS AND CONDITIONS CONTAINED THEREIN.COATES SHALL NOT BE LIABLE FOR INCIDENTAL AND CONSEQUENTIAL LOSSES AND DAMAGES, UNDER THE EXPRESS WARRANTY, ANY APPLICABLE IMPLIED WARRANTY, OR CLAIMS FOR NEGLIGENCE, EXCEPT TO THE EXTENT THAT THIS LIMITATION IS FOUND TO BE UNENFORCEABLE UNDER APPLICABLE STATE LAW.SOME STATES DO NOT ALLOW THE EXCLUSION OF LIMITATION OF INCIDENTAL OR CONSEQUENTIAL DAMAGES, SO THE ABOVE LIMITATION OR EXCLUSION MAY NOT APPLY TO YOU.THIS WARRANTY GIVES YOU SPECIFIC LEGAL RIGHTS, AND YOU MAY ALSO HAVE OTHER RIGHTS WHICH VARY FROM STATE TO STATE.HEATER COMPANY, INC.P.O. Box 1750Kent, WA 9803590007000 4-2015P/N。
ORBINOX RB模型溜堰门安装、运行和维护手册说明书
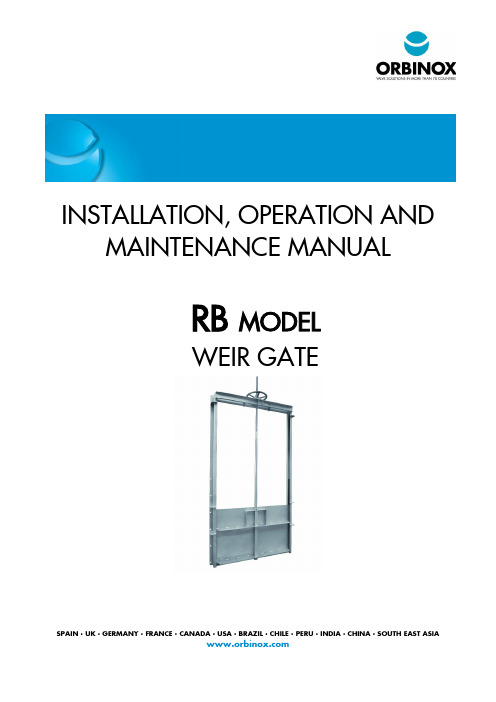
SPAIN · UK · GERMANY · FRANCE · CANADA · USA · BRAZIL · CHILE · PERU · INDIA · CHINA · SOUTH EAST ASIAINSTALLATION, OPERATION ANDMAINTENANCE MANUALRB MODELWEIR GATEINDEX Page0. Introduction (2)1. Handling and s torage (2)2. Equipment main components (3)3. Installation (4)3.1. Installation: Concrete wall mounted (4)3.2. Installation: Stem extension, stem guides and floor stand (when applicable) (6)4. Operation (8)5. Maintenance (9)5.1. Cleaning and lubrication (9)5.2. Vertical and bottom seals r eplacement (10)6. Trouble shooting (12)7. Environmental considerations (12)0.INTRODUCTION•This manual describes the recommended procedures for installation, operation, maintenance and safety precautions for ORBINOX RB model weir gates•Please read thoroughly all the instructions in the manual prior to installation and contact an ORBINOX representative in case of any questions•The manual makes reference to the “General Arrangement Drawing” (GAD). The GAD is the drawing that is sent to and approved by the customer prior to the production of the weir gate•ORBINOX assumes no responsibility or liability if the slide gate is not installed, operated and maintained in strict accordance to the procedures described in this manual1.HANDLING AND STORAGEStandard safety procedures should be followed to prevent personal injury or equipment damage. Additionally, the following instructions shall be followed during handling and storage to prevent any damage of the product: •Stems have precision surfaces and should never be used as a mean to lift the slide gate•Equipment shall be stored in a dry, clean and even area on a raised even wood surface to prevent distortion of the frame•Do not stack slide gates•Stems and extensions that are shipped separately shall be supported over their entire length to prevent any bending or distortion while in storage2.EQUIPMENT MAIN COMPONENTS3.INSTALLATIONThis section describes the different installation methods3.1. Installation: concrete wall mounted▶ Required Materials:•ORBINOX RB Weir Gates are installed by means of Anchor Bolts. Depending on the size and working conditions they shall be either of the mechanical or chemical type. In order to get the expected performance of the anchor bolts, the minimum concrete strength shall be 25 MPa (3,625 PSI)•In order to avoid leakage between the concrete wall and the frame, construction sealant shall be used. (Sikabond/Sikaflex 11FC Sealant or equivalent, 200ml per meter of opening perimeter). As an alternative, self-adhesive commercial sponge EPDM strips, approximately 20mm/0,80” wide by 10mm/0,40” thick, can be used and glued to the slide gate around the hole•For detailed information about the type, size and quantity of the re-quired anchor bolts, or any other specific instal lation notes or materials, please refer to the notes on the …General Arrangement Drawing‟▶ Installation procedure:Step 1: Concrete wall surface inspection•The concrete construction shall be flat, level and plumb, and shall be in accordance to DIN 18202 or ACI 117-06 standards. If necessary, use non-shrink grout in order to meet the specified standard•Concrete wall surface shall be dry (so the construction sealant sets effectively). If it is necessary, the wall can be dried with the help of a blowtorch or a hot air fanStep 2: Pre-installation of the weir gate•Position the weir gate against the wall and line up with the channel•Drill and install an anchor bolt on each side of the gate (see Figure 2). After installing the first anchor bolt, and prior to drilling the hole of the other side, make sure the frame is perfectly leveledFigure 1Step 3: Construction sealant application• In order to avoid leakage between the frame and the wall, construction sealant shall be applied on the frame:o Remove the weir gate from the wall (first remove the nuts of the anchor bolts).o Apply construction sealant all around the perimeter of the frame. Sikabond/Sikaflex 11FC (200 ml/m) or equivalent construction sealant shall be used. Be sure not to get sealant on the gate ’s seals, guides, and/or stem, as this may cause leakage or damage.Figure 2Step 4: Final installation• Place back the gate on the wall at the previously installed anchors • Drill and install the rest of the anchor boltsCAUTION!: If the weir gate is not completely in contact with the wall, do not over-tighten the anchor bolts. Over tightening may bend or distort the frame. If the wall flatness and levelness is according to the specified standards, the construction sealant will fill in the remaining void• Apply construction sealant around the frame in order to fill in any existing gap between the wall and the frame (this step is only for esthetics). Wipe away the excess sealant to leave a smooth finish.Back side of the frame (Side in contact with the wall)Construction sealant (Sikaflex11FC (200ml/m))Figure 33.2. Installation: stem extension, stem guides and floor stand (when applicable)•Some RB weir gates include stem extensions, extension guides and floor stand (depending on the configuration of the civil works)•Once the gate is installed, the rest of the elements must be installed:o Connect the stem extension (item 3) to the shaft (item 1) on top of the yokeo Insert all stem guides from the top of the stem extension (when applicable). Align stem extension, and especially make sure that it is aligned with the vertical axis of the openingo Next, install all stem guides (drill and tighten anchor bolts). Refer to General Arrangement Drawing for dimensionso Position the floor stand and the operator. Engage the shaft of the stem extension with the operator.Make sure that the stem extension is perfectly aligned and parallel to the wall surface, adjusting theoffset if necessary, of the Stem-Guides‟(U)HMWPE inserts. Once, the stem extension is perfectlyaligned, install the floor stand (drill and tighten anchor bolts)Figure 4Operator Floor StandStem GuideConnect the Extension to the Slide Gate Adjust offset distancefrom wallAdjust Stem Extension Aligment4.OPERATIONInitial Operation:Before cycling the weir gate, make sure there are no foreign deposits or materials on the seals, guides or sealing area. Gate seals could be damaged if the area is not cleaned and coated with a light grease. Please refer to section “Materials needed for maintenance and seal replacement” for detailed informat ion about the grease type.•ManualApply a light grease on the stem before initial operation after the installation. If the operation is difficult due to high torque, stop operation of the gate and check stem alignment.•Electric actuatoro Refer to the electric actuator manufacturer instruction manual before commissioning the weir gateo Electric actuators must be limited with limit and torque switches. Electric actuators without these limiters shall not be used with ORBINOX weir gate. Electric actuators must be adjusted at the time of installation on site (except in the case of a self-contained frame and yoke-mounted actuators; in this case the motor is factory-set). To adjust the limit switches, follow the next instructions using values of the GAD:▪Position the slide in the nearly closed position (leave 10mm /0,40” open). From thisposition, manually (using the handwheel) operate the slide until it is completely closed(check tightness with a 0,05mm/0,002” gauge). In this position, set the limit switch for theCLOSED position▪Position the slide in the nearly open position (leave 10mm /0,40” closed). From thisposition, manually (using the handwheel) operate the slide until it is completely open. Inthis position, set the limit switch for the OPEN positiono Be aware when the gate is almost fully OPEN or CLOSED. If the gate does not stop once the fully open or fully closed position is reached, stop immediately and correct adjusting again the limit and torque switches Operation:• CAUTION! Do not force the operator to close the gate, as it may cause damage to the stem and it does not improve the sealing system. The maximum applicable force on the handwheel is 25 kg /55 lbs• The RB weir gate is closed by a clockwise rotation, and opened (downwards) by a counter-clockwise rotation of the operator• The RB weir gate is designed to be self-locking, so that the slide maintains its position in open, close or intermediate positions5.MAINTENANCE5.1. Cleaning and lubricationORBINOX model RB weir gates need practically no maintenance. In order to assure maximum performance of the weir gate, the following maintenance inspections shall be carried out periodically (every 6 months):•Stem and stem nut shall be cleaned and greased. In some configurations, the stem may be in contact with water and dirt. Under these conditions, the threads of the stem and/or stem nut may wear, and they shall be checked every 3 months.•Clean the gate with clear water and remove any deposits, especially on the seals and in the guides•Check the seals and make sure they are not damaged. Seals shall be replaced if damaged. See section …Maintenance: Seal Replacement‟ for detailed procedures about seal replacement•Seals shall be wet while operating. If the weir gate has not been used for a long period of time under dry conditions, the seals shall be wetted with clear water before operating the weir gate. Operating the gate with dry seals may damage the seals. Additionally, more torque may be required to operate the weir gate Spare parts:ORBINOX does not recommend stocking any spare parts by the owner of the equipment as the weir gates are designed for a very long life cycle. If a repair part is required, please contact an ORBINOX representative and provide the following information:•ORBINOX S/O number•“O RBINOX General Arrangement Drawing” number•Project name (if applicable)•Vendor’s company nameMaterials needed for maintenance and seal replacement:5.2. Vertical and bottom seals replacementThe procedure for replacing the seal is described below. Please note that in any case, the slide must be first removed from the frame. It is not necessary to remove the frame from the wallWeir gates (200 x 200mm/8”x8” to 1200 x 1200mm/48”x48”)•From the closed position unscrew the nuts and remove the washers of the lateral anchor bolts•Unscrew bolts (item 3). CAUTION! the slide is no longer secured•Remove frame guides (item 4), (U)HMWPE guides (item 5) and slide (item 7)•Unscrew bolts and remove retainers (items 10 and 11)•Remove seal (item 12) and replace it by the new seal. After installing the new seal, apply grease on it to ease operation NOTE: the shaft must be completely empty to carry out this maintenance operation as the seals are bolted to the frameFigure 5Weir gates (1250x1250mm/49”x49” to 2000 x 2000mm /80”x80”)•Start from the open position•Remove the yoke (upper part of frame, item 2), the stem (item 3) and the slide (item 5) as a single assembly. To do this, first loosen the bolts and nuts on the yoke•Remove the seal retainer (items 7 and 8)•Remove seal (item 9) and replace it by the new seal. After installing the new seal, apply grease on it to ease operation.Figure 66.TROUBLE SHOOTING7.ENVIRONMENTAL CONSIDERATIONS• The packaging is made from environmentally friendly materials. Dispose of the packaging through the available recycling channels• The valve is designed and manufactured with materials that can be recycled by specialised recycling firms. Once the life of the product is expired, you have to consider a proper disposal of the product in order to prevent any negative impact on the environment and allows for the recycling of valuable commodities• Please follow the local environmental rules in your country for proper disposal。
PM500 电压调节器安装,操作和维护手册说明书
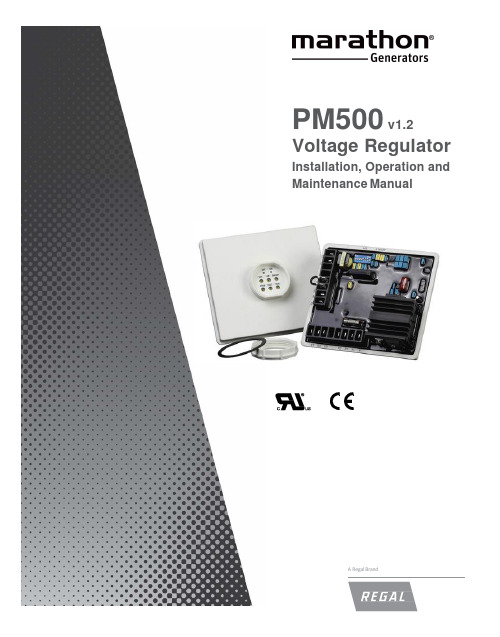
Maintenance ManualA Regal BrandIntroductionThe PM500 is an encapsulated electronic voltage regulator intended for use with the Marathon PMG systemand most Marathon AC generators. The PM500 controls the output of a brushless AC generator by regulating the DC current input to the exciter field. The PM500 is designed as a three phase or single phasetrue RMS sensing regulator that is capable of accepting analog voltage adjustment input. The PM500 is UL Recognized and UL Certified for Canada – Component per UL File E222903. The PM500 bears the CE markfor the European Union.SpecificationsSensing Input175 - 600Vac, True RMS, 60/50Hz, 3 Phase/1 PhasePower Input 175 - 260Vac, 300Hz PMG, 60/50Hz ShuntPower Output, Continuous 85Vdc at 3.5Adc with 240Vac input powerPower Output, Forcing 170Vdc at 7Adc for 10 sec. with 240Vac input powerFuse 5 x 20mm S505-5A, Slow Blow TypeVoltage Regulation ± 0.25%, with 4% engine governingExcitation Resistance9 ohms, minimumOver Excitation Protection Excitation exceeds 190Vdc or 7Adc for more than 10 seconds Manual Voltage Adjustment Range ± 20% with 2000 ohm rheostat± 10% with 1000 ohm rheostatAnalog Voltage Input A1 & A2 ± 20% with 0-10Vdc or ± 5Vdc biasUnder Frequency Factory Setting 58Hz preset for 60Hz operation and 48Hz preset for 50Hz operation Voltage Build-up Voltage build up from input voltage ≥ 5Vac at 25Hz.Response Time<1 CycleWeight16.6 oz.Operating Temperature -40°C to +60°CStorage T emperature -40°C to +85°CPower Dissipation12 watts, maximumSize 5.9” L x 5.3” W x 2.2” HThermal Drift 0.05% / °C change in AVR ambient temperature Electromagnetic Compatibility TestsImmunityIEC61000-4-2 - Electrostatic DischargeIEC61000-4-3 - Radiated RFIEC61000-4-4 - Electrical Fast TransientIEC61000-4-5 - SurgeIEC61000-4-6 - Conducted RFIEC61000-4-11EmissionEN61204-3 - Conducted RFCISPR 22IEC61000-3-2 - Harmonic IECIEC61000-3-3 - Flicker IEC2InstallationMOUNTINGThe PM500 is mounted through a keyed hole in the generator conduit box and secured with a plastic mounting nut.The PM500 should be mounted directly to the conduit box panel with the rubber gasket positioned between the outside of the conduit box panel and the mounting nut.Protect front panel adjustment pots by installing clear or black plastic cover.Mounting nut torque is 26 – 43 lbf-in. Refer to the Figure 1 for dimensions.Wiring and ConnectionsEXCITER FIELD POWER CIRCUITThe exciter field resistance must be ≥ 9 ohms.If the exciter field resistance is less than 9 ohms andthe full load field current does not exceed 3.5 amps, add a resistor in series of sufficient wattage to increase the total resistance to 9 ohms.Connect the generator F+ (F1) field lead to the regu- lator F+ terminal. Connect the generator F- (F2) field lead to the regulator F- terminal. Refer to Figure 3 for typical connection points.POWER I NPUT C IRCUITThe PM500 is designed to be powered by a PMG and capacitor. A 7.5µƒ capacitor is connected in parallel between the PMG leads and the regulator power input terminals.The regulator power input terminals are labeled P1 and P2. Connect leads from P1 and P2 to the capacitor terminals.Connect regulator terminals P1 & P2 to generator leads that will provide 240Vac output. No capacitor is used with the PM500 in shunt mode.Refer to Figure 3 for typical connection points.Figure 23TO PREVENT PERSONAL INJURY OR EQUIPMENT DAMAGE, ONLY QUALIFIED PERSONNEL SHOULD INSTALL, OPERATE OR SERVICE THIS DEVICE.Figure 1Wiring and Connections (cont’d)Figure 3a – Three PhaseFigure 3b – Single PhaseSENSING CIRCUITSSensing input range is 175 - 600Vac. DIP switch SW1 and SW2 must be set appropriately. Refer to Figures 3a & 3b for typical connections.Single Phase SensingConnect PM500 terminal E1 to output lead L1 and E2 to output lead L2. PM500 terminal E3 is jumpered to E2. 3 Phase SensingConnect PM500 terminal E1 to output lead L1, E2 to output lead L2 and E3 to output lead L3.If used in a paralleling application, a paralleling CT will be required in the generator B phase. Paralleling CT must be sized to provide either a 1A or 5A signal when the generator is under full load.4Wiring and Connections (cont’d)DIP SWITCH PROGRAMMINGEight DIP switches located on the back of the regulator must be set appropriately for correct regulator operation and generator control. Refer to Figure 4.Switches 1 & 2 set the regulator sensing range.Switches 3 – 8 Configure multiple functions: 3 or Single Phase Sensing, Frequency, Over Excitation Protection, kW Range and Paralleling CT Range.SW1 : OFF SW2 : OFF Volts ≤ 280VacSW1 : OFF SW2 : ON Volts ≤ 480VacSW1 : ON SW2 : ON Volts ≤ 600VacOFF ONSW3 : 3 Phase Sensing 1 Phase SensingSW4 :60 Hz 50 HzSW5 :O/E Protect On O/E Protect OffSW8 :CT 1A CT 5ASW6 : OFF SW7 : OFF< 90kWSW6 : ON SW7 : OFF90 - 500kWSW6 : ON SW7 : ON> 500kW PROTECTION F UNCTIONSThe PM500 has built in protection functions for Over Excitation, Under Frequency and Over Voltage Protection.Over ExcitationThe Over Excitation function protects the PM500 and generator components in the event the excitation system demands excessive levels of voltage and/or current to maintain output.The Over Excitation function will trip when excitation output exceeds 190Vdc or 7Adc for more than 10 sec. with 220Vac input power.The Over Excitation O/E LED on the front panel will be illuminated when thePM500 when the OverExcitation system has tripped. Replace the fuse on theback panel if required and inspect the generator. ThePM500 will reset when power is cycledUnder FrequencyUnder Frequency protection allows the generatorvoltage to decrease when the output frequency dropsbelow the Roll-Off point. This reduces the load on theengine, allowing engine RPM to recover. This is normaloperation and no reset is required.5 Figure 4Operating AdjustmentsSix adjustable potentiometers are accessible on the front panel of the PM500. These are: VOLT, STAB, U/F, DIP, DROOP and TRIM.Figure 6VOLTAGE ADJUST (VOLT)Set PointOutput voltage may be adjusted via the VOLT poten- tiometer on the front panel of the regulator. The set point range is 175 - 600Vac.Remote Voltage AdjustA 2000 ohm, 2 watt rheostat may be connected to VR1 and VR2 - replacing the factory jumper, providing a ±10% voltage adjustment range. T erminals A1 & A2 may not be used when a rheostat is installed.Analog Voltage AdjustRegulator terminals A1 & A2 may be connected to the analog output of a gen-set controller. The allowable voltage input range is 0-10Vdc or ± 5Vdc will provide a 20% range. Jumper VR1 & VR2 when analog voltage adjustment terminals are used.TRIM ADJUST (TRIM)The analog bias range is adjusted via the TRIM potenti-ometer on the front panel. Set the TRIM potentiometer fully clockwise to provide a ± 20% adjustment range. DROOP ADJUST (DROOP)Requires a 1A or 5A CT in the B Phase.DIP switch SW8 must be set appropriately.In a paralleling system, the PM500 adjusts the genera- tor output voltage when the B phase current leads or lags the B phase voltage.The adjustment range may be preset via the DROOP potentiometer. The default setting is full counter clock-wise for minimum range. Maximum range is ±7% at 1.7 PF lagging to 0.7 PF leading.UNDER FREQUENCY ROLL-OFF ADJUST (U/F) The Roll-Off point is the frequency at which the gen- erator output voltage is allowed to decrease and is factory preset at 57Hz for 60Hz operation and at 47Hz for 50Hz operation.When the U/F LED on the front panel it lit, the PM500 is operating in Under Frequency mode.To change the roll-off point, first verify that the gen-set is operating at the intended speed and voltage.Fixed Engine RPMOn most new engines (Tier 4i and up), the engine speed is fixed at 1800RPM or 1500RPM.Adjust the roll-off point by block loading the genera-tor and observing the U/F LED on the front panel. To ensure the generator maintains voltage under a given block load, adjust U/F potentiometer until the U/F LED remains off during the block load test.Adjustable Engine RPMAdjust engine speed to the new roll-off point. Verify that the output voltage still matches the intended set-point voltage.Next, adjust the U/F potentiometer clockwise until the voltage starts to drop off, then slightly adjust the poten- tiometer counterclockwise until the voltage returns to rated voltage. Re-adjust engine speed to rated speed. U/F DIP ADJUST (DIP)When Under Frequency (U/F) protection is activated, the voltage dip follows a linear Volts / Hertz curve. The voltage dip ratio may be adjusted via the DIP potentiometer with an adjustable range of 3-10V/Hz. The default setting is full clockwise for 10V/Hz. STABILITY ADJUST (STAB)Stability is the ability of the generator to respond to load changes. Decreasing the stability setting allows the generator to respond faster to load changes. If the stability setting is too low, the generator voltage will tend to hunt under steady state conditions.Correct stability adjustment must be conducted while the generator is operating unloaded.Adjust the STAB potentiometer clockwise until the voltage becomes unstable, then slightly adjust coun- terclockwise (Approximately 1/5 turn) until the voltage becomes stable.6Warnings & CautionsIMPORTANT INFORMATIONPlease Read CarefullyThis document is not intended to provide operational instructions. Appropriate Marathon Electric instructions provided with the generator and precautions attached to the generator should be read carefully prior to installation, operations and/or maintenance of the equipment. Injury to personnel or generator failure may be caused by improper installation, maintenance or operation.The following and information is supplied to you for your protection and to provide you with many•Buyer shall be solely responsible for determining the adequacy of the product for any and all uses to which Buyer shall apply the product. The application by Buyer shall not be subject to any implied warranty of fitness for a particular purpose.•For safety, Buyer or User should provide protective guards over all shaft extensions and any moving apparatus mounted thereon. The User is responsible for checking all applicable safety codes in his area and providingsuitable guards. Failure to do so may result in bodily injury and/or damage to equipment.•Hot oil can cause severe burns. Use extreme care when removing lubrication plugs.•Disconnect power and lock out drive equipment before working on a generator.•Always keep hands and clothing away from moving parts.•The lifting eyes on the generator are not to be used to lift the entire generator set. Only the generator may be safely lifted by the lifting eyes. Do not use the conduit box for lifting or support of the generator.•Install and ground the generator per local and national codes.•Discharge all capacitors before servicing the generator.•Misapplication of a generator in a hazardous environment can cause fire or an explosion and result in serious injury.•Never attempt to measure the temperature rise of a generator by touch. Temperature rise must be measured by thermometer, resistance, imbedded detector or thermocouple.•Operation of a generator at higher than its nameplate ratings may result in fire, damage to equipment or serious injury to personnel.•Do not apply any force to the generator fan when rotating the generator rotor.•Generators should not be operated faster than their rated speed.•The following statement is only applicable to high voltage generators (above 5000 V). A grounding strap is supplied from the generator neutral to ground. This grounding strap not only bleeds off any voltage potential on the main statorafter the high potential test, but also bleeds off any static charge that can build-up on the main stator during shipmentand storage. THIS GROUND STRAP IS NOT A PERMANENT PART OF THE GENERATOR CONSTRUCTION. REMOVETHIS GROUND STRAP ONLY AFTER A PERMANENT GROUND IS INSTALLED ON THE GENERATOR MAIN STATOR(not supplied by Marathon Electric), OR THE GENERATOR FINAL INSTALLATION IS COMPLETE.•Mounting bolts should be routinely checked to ensure that the unit is firmly anchored for proper operation.•Consult qualified personnel with questions. All electrical repairs must be performed by trained and qualified personnel only.•For inverter applications, follow the inverter manufacturer’s installation guidelines.•Make sure the generator is properly secured and aligned before operation.•When installing the generator, insure that loose parts or tools do not fall inside the generator.•When connecting the generator, be sure to follow the correct wiring diagram for the desired voltage. Insure that the voltage regulator is connected per the wiring diagram.RESALE OF GOODSIn the event of the resale of any of the goods, in whatever form, Resellers/Buyers will include the following language in a conspicuous place and in a conspicuous manner in a written agreement covering such sale:The manufacturer makes no warranty or representations, express or implied, by operation of law or otherwise, as to the merchantability or fitness for a particular purpose of the goods sold hereunder. Buyer acknowledges that it alone has deter- mined that the goods purchased hereunder will suitably meet the requirements of their intended use. In no event will the manufacturer be liable for consequential, incidental or other damages. Even if the repair or replacement remedy shall be deemed to have failed of its essential purpose under Section 2-719 of the Uniform Commercial Code, the manufacturer shall have no liability to Buyer for consequential damages.Resellers/Buyers agree to also include this entire document including the cautions and warnings above in a conspicuous place and in a conspicuous manner in writing to instruct users on the safe usage of the product.This information should be read together with all other printed information supplied by Marathon Electric.For more information contact: Regal Beloit America, Inc., 100 E. Randolph St., Wausau, WI 54401Phone: 715-675-3311 or Fax: 715-675-80267A Regal Brand100 E. Randolph Street PO Box 8003Wausau, WI 54402-8003 U.S.A. PH: 715-675-3359 FAX: 715-675-8026 ©2019 Regal Beloit Corp GPN056 v1.2100/11-19/FSPrinted in the U.S.A.。
新版asapnext generation手册
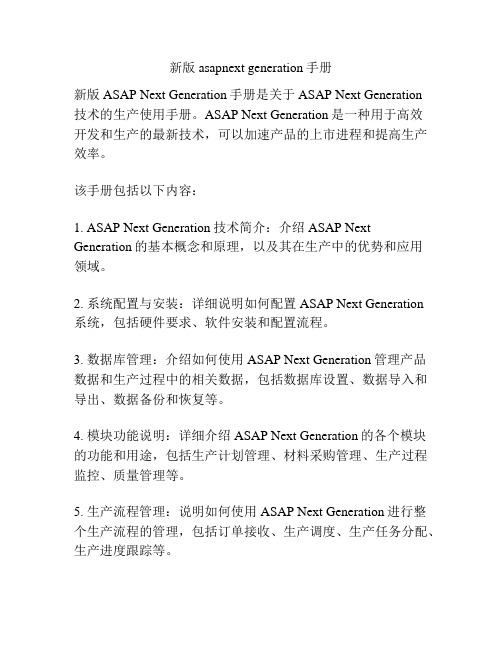
新版asapnext generation手册新版ASAP Next Generation手册是关于ASAP Next Generation技术的生产使用手册。
ASAP Next Generation是一种用于高效开发和生产的最新技术,可以加速产品的上市进程和提高生产效率。
该手册包括以下内容:1. ASAP Next Generation技术简介:介绍ASAP Next Generation的基本概念和原理,以及其在生产中的优势和应用领域。
2. 系统配置与安装:详细说明如何配置ASAP Next Generation系统,包括硬件要求、软件安装和配置流程。
3. 数据库管理:介绍如何使用ASAP Next Generation管理产品数据和生产过程中的相关数据,包括数据库设置、数据导入和导出、数据备份和恢复等。
4. 模块功能说明:详细介绍ASAP Next Generation的各个模块的功能和用途,包括生产计划管理、材料采购管理、生产过程监控、质量管理等。
5. 生产流程管理:说明如何使用ASAP Next Generation进行整个生产流程的管理,包括订单接收、生产调度、生产任务分配、生产进度跟踪等。
6. 故障排除与维护:提供ASAP Next Generation系统故障排除和维护的常见问题和解决方法,以及系统升级和更新的步骤和注意事项。
7. 最佳实践指南:给出在使用ASAP Next Generation时的最佳实践建议,包括如何优化生产效率、提高产品质量和降低生产成本等方面的经验分享。
新版ASAP Next Generation手册的目标是帮助企业更好地理解和使用ASAP Next Generation技术,实现高效和卓越的生产过程。
ECONX - 安装说明说明书

0 ECONX –FIT OFF INSTRUCTIONSbelling2.Fit Off –Alarm Sensors3.Fit Off –Smoke Sensors4.Fit of Siren and Sounder5.Partitioning, Night Arm and Panic Buttons6.Fit Off Temperature SensorsFIT OFF -LABELLINGTo ensure commissioning is straight forward we recommend completing the form included in the instructions and following your project scope.Alarm circuits must be identified so Entry and Exit delays can be applied.1Relay ControlsRelay1Hot water cylinderRelay2Instant Water Heater or In Floor HeatingRelay3Under tile Heating EnsuiteRelay4Under Tile Heating BathroomsRelay5Heated Towel RailsRelay6Outdoor Entry LightsRelay7Indoor NightRelay8Relay9Security and Safety1Smoke or Sensor Smoke-Hallway2Smoke or Sensor Smoke-Hallway3Smoke or Sensor Smoke-Living4Smoke or Sensor PIR-Entry5Smoke or Sensor PIR–Garage6Smoke or Sensor PIR–Laundry Door7Smoke or Sensor PIR–Hallway18Smoke or Sensor PIR–Hallway29Smoke or Sensor PIR–Master Bedroom10Smoke or Sensor11Smoke or Sensor12Smoke or SensorPanic ButtonKey SwitchTemperature Input1BathroomTemperature Input2EnsuiteAccessControl/Misc.0Garage DoorControl/Misc.1Automatic GateControl/Misc.2Blinds UpControl/Misc.3Blinds DownControl/Misc.4Control/Misc.5Control/Misc.6Control/Misc.7Control/Misc.8Heating and CoolingIR Output0Heat Pump LivingIR Output1Heat Pump HallwayIR Output2IR Output3IR Output42 FIT OFF –PIR SENSORWe recommend one sensor per zone. If additional inputs are required we suggest doubling up the smoke detector zones.Alarm sensors require a positive, negative and an input into the Econx. Common practice is the 4 wire method. Econx provides the option of 24hr monitored tamper with separate wiring of the tamper input.End of Line Resistors (EOL) must be a minimum of 1K. Econx recommends 2K -10K. Econx will learn whatever is installed, different resistors throughout a single installation is acceptable.3 FIT OFF –SMOKEWe recommend one sensor per zone.These require a positive, negative and a input into the Econx. Common practice is the 4 wire method. End of Line Resistors (EOL) must be a minimum of 1K. Econx recommends 2K -10K. Econx will learn whatever is installed, different resistors throughout a single installation is acceptable.Econx prefers the resistors are installed in parallel with the N/O contact. This provides the ability to fault find should you have damaged wires or a faulty smoke detector.4 FIT OFF –OUTDOOR & INDOOR SIRENPlease Note the siren and strobe are wired separately. The Strobe will flash when disarming and arming as a visual indicator.The tamper is 24hr monitored and no other configuration is required5 FIT OFF –PARTITIONING, NIGHT ARM & PANICPartitioning/ Night Arming and disarming is typically operated by the clients smart phone App. Manual push buttons can be installed if preferred.Key Switch input –This can be used to Arm and Disarm the system. This is a momentary action. Should this feature be used no personalised logging is possible.6 TEMPERATURE SENSOR CONNECTIONEconx is pre-configured to operate with1.DEVI floor, indoor and outdoor temperature sensors.2.Hot wire 10K and 100K under tile heating probesAny of the Smoke 1 –3, PIR 1 –9 plus AIN 1 & 2 can be configuredas a Temperature inputs.One room sensor can be used to control multiple outputsE.G One Living Room sensor could control7 FIT OFF –LIGHT SWITCHESEconx recommends Auto/ Manual/ Off Mechs are installedfor all lighting loads connected to Econx, This providesmanual operation and the ability to isolate when required.N/O wiring into Econx is recommended. This ensures lightswill be off if the Econx system is isolated.Outdoor Motion sensors can be installed in Parallel withEconx –Econx will NOT be effected by parallel switching.Light switches, where auto/man/off is NOT8 FIT OFF –DEDICATED CIRCUITSThe following is recommended to ensure operationbefore commissioning and protection from non-essential heating loads be left On.Econx recommends N/C connection is used for thefollowinga)Hot waterb)Heated Towel Railsc)Pool Pumpsd)Water FeaturesFIT OFF –HEAT PUMPS9Heat Pump control is via infra red, Each Econx cancontrol up to 5 zones from one system. The Econxsoftware includes most major brands IR codes, newmodels and other brands can be added at any time.Functionality includesa)On/Offb)Heating and Coolingc)Set Temperaturesd)Automation of OperationTestingand the codes on the remote do not match any in theTo Test –Econx panel, you will see 5 LED’s flash On then Off. Go10 FIT OFF –GARAGE DOORS, GATES & FRONT DOORSThese 9 miscellaneous inputs and outputs canbe configured to operate Garage Doors,Automatic Gates, Mortice or Mag Locks,Electric blinds, Irrigation and ……….The inputs and outputs are linked within theEconx software.PLEASE NOTE Inputs and outputs must11 FIT OFF –ELECTRIC BLINDS AND WINDOWSThese 9 miscellaneous inputs and outputs can beconfigured to operate electric blinds and windows.Functionality includes full opening and closing viathe browser, smart phone app and schedules.Manual push buttons are installed for part openingand closing.Should more than 3 –4 zones be required werecommend the installation of the manufacturesSUPPORT 12Support Contact Anthony Tucker **************.nz PH 0272 666 329More wiring Informationa)Wiring diagrams are supplied with your Econx system and are available at /technical-information b)Step by Step Fit Off and Configuration Guides are available at /technical-information。
SCHOLD LMX-3-DC MIXER 安装、操作和维护手册说明书
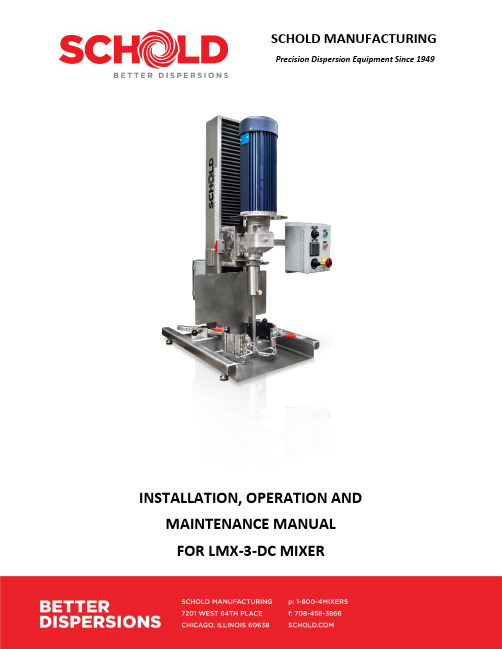
SCHOLD MANUFACTURINGPrecision Dispersion Equipment Since 1949INSTALLATION, OPERATION ANDMAINTENANCE MANUALFOR LMX-3-DC MIXERTABLE OF CONTENTS _____________________________________________________________________________________PAGE 1.INTRODUCTION31.1TECHNICAL SERVICE 32.SAFETY 43.DESCRIPTION 54.TRANSPORTATION AND HANDLING 64.1 UNPACKING 64.2 TRANSPORTING 65.INSTALLATION 75.1 INSTALLATION – MECHANICAL 75.2 INSTALLATION – ELECTRICAL 8FIELD WIRING DIAGRAM5.3 DIRECTION OF ROTATION 96.OPERATION 106.1 MIXING TIPS 126.2 CLEANING 127.MAINTENANCE 137.1 GENERAL MAINTENANCE 137.2 ASSEMBLY AND DISASSEMBLY OF MIX BLADE 147.3 RECOMMENDED SPARE PARTS 14BELED PARTS 15INTRODUCTION _____________________________________________________________________________________ 1 INTRODUCTIONThe purpose of this manual is to provide you with the information needed to setup and operate your Schold LMX mixer.IMPORTANT: Please read this manual carefully before attempting to set up or operate your machine. Neither Schold Manufacturing nor its representatives can acceptresponsibility for damage or injury resulting from improper set up or use.If you have any questions, please contact Schold Manufacturing at 1-800-4-MIXERS.1.1 TECHNICAL SERVICESpare or replacement parts and advice regarding the operation of your machine can be obtained from the Technical Service Department by calling 1-800-4-MIXERS.SAFETY _____________________________________________________________________________________ 2 SAFETYPlease observe the Health and Safety regulations applicable to your location; these vary from place to place but their substance is the same – avoid all hazards to personnel and property.Throughout the manual you will find WARNINGS and CAUTIONS associated with certain procedures.WARNINGS ARE PROVIDED WHERE THERE MAY BE PHYSICAL DANGER TO PERSONNEL IF THE WARNING IS IGNORED.CAUTIONS Indicate that the machine may be damaged if care is not taken whenperforming the procedure.WARNING: DO NOT USE THE MACHINE IN A HAZARDOUS AREA WHERE A FLAMMABLE OR EXPLOSIVE ATMOSPHERE MAY BE PRESENT UNLESS THE MACHINE IS FITTED WITH AN EXPLOSION PROOF MOTOR RATED TO THE RELEVANT STANDARD FOR THAT AREA AND WIRED BY A QUALIFIED ELECTRICIAN TO THE APPLICABLE AREA.WARNING: ALWAYS DISCONNECT OR LOCK OUT THE MACHINE FROM THE ELECTRICITY SUPPLY BEFORE CARRYING OUT ANY MAINTENANCE WORK. SEE WARNINGS.Any electrical operation should only be carried out by a qualified electrician.Always use a lifting anchor where necessary; some components are heavy and can bedangerous to handle without the proper equipment.When using solvents to clean components use in a well-ventilated area and avoidinhalation of fumes. Keep away from sources of ignition.WARNING: NEVER TOUCH ROTATING PARTS. FAILURE TO OBSERVE THIS MAY RESULT IN BODILY INJURY.THE NOISE LEVEL GENERATED BY THE MIXER WILL DEPEND ON VARIOUS FACTORS.THESE INCLUDE THE NATURE OF THE PRODUCT BEING PROCESSED, THEINSTALLATION, THE VESSEL CHARACTERISTICS AND SUPPORT STRUCTURE, THEACOUSTIC CHARACTERISTICS OF THE BUILDING, THE MOTOR SPECIFIED, AND THEBLADE FITTED.IF THE NOISE LEVEL EXCEEDS 85 dBA, ATTENTION MUST BE GIVEN TO PREVAILINGHEALTH AND SAFETY LEGISLATION TO LIMIT THE EXPOSURE OF OPERATORS TO THENOISE.DESCRIPTION _____________________________________________________________________________________The LMX mixer has the following components:•Table mounted “H-style” frame design• 3 HP 1780 RPM output TEFC DC motor•Electrical supply required: 220V/1Ph/60Hz•Electric lift actuator•Dual torque tube design•Removeable backsplash tray•Adjustable shaft guard•Stainless steel wetted parts•Low speed bow tie blade assembly•Remote mounted VFD panel, NEMA 12 rated•Operator station with motor load readout•Adjustable hinged style tub holder•Safety switch and ultrasonic sensorTRANSPORTATION AND HANDLING_____________________________________________________________________________________ 4.1 UNPACKINGCAUTION: The mixer must not be lifted directly by the motor under anycircumstances. To lift the mixer, attach a lifting anchor to the top of the rectangular,metal frame. A ½”-13 threaded hole is located on the top plate, and is intended to be used to attach a lifting anchor for lifting purposes. The lifting anchor is not supplied by Schold Manufacturing.Ensure that the mixer has not been damaged in transit and is clean.1.Remove the shipping anchor bolts from the wooden frame/pallet.2.Attach a lifting anchor to the top of the rectangular, metal frame. A ½”-13 threadedhole is located on the top plate, and is intended to be used to attach a lifting anchorfor lifting purposes. (See figure below)3.Lift and move the mixer to the desired area.4.2 TRANSPORTINGTo avoid damage, the mixer must not be transported without being packed securely. It is recommended that the mixer is attached to a wooden skid, and securely bolted down with anchor bolts using the four 3/8” through holes at the base of the “H-style” frame.Make sure to cover the mixer completely with plastic to prevent water damage.If any major fault develops, the mixer should be returned for repair and/or service. The mixer must be shipped suitably packed and with the approval of Schold Manufacturing.If you have any questions, please contact Schold Manufacturing at 1-800-4-MIXERS.INSTALLATION _____________________________________________________________________________________ 5.1 INSTALLATION - MECHANICALEnsure that the mixer has not been damaged in transit and is clean.CAUTION: The mixer must not be lifted directly by the motor under anycircumstances. To lift the mixer, attach a lifting anchor to the top of the rectangular,metal frame. A ½”-13 threaded hole is located on the top plate, and is intended to be used to attach a lifting anchor for lifting purposes. The lifting anchor is not supplied by Schold Manufacturing.1.Make sure the base of the mixer is level. To adjust the level, loosen the four jam nutslocated at the base of the “H-style” frame. Then, adjust each foot to achieve level,and tighten the four jam nuts. (See figure below)2.Mount the base securely in place using the four 3/8” through holes located at thebase of the “H-style” frame after leveling.5.2 INSTALLATION - ELECTRICALWARNING: ANY ELECTRICAL WORK SHOULD ONLY BE CARRIED OUT BY A QUALIFIEDELECTRICIAN. ALL NATIONAL, LOCAL, AND SITE REGULATIONS SHOULD BE OBSERVED.WHEN MAKING ELECTRICAL CONNECTIONS THE SUPPLY SHOULD BE ISOLATED, FUSES REMOVED, AND THE FUSE BOX LOCKED SHUT WITH THE FUSES AND THE KEY IN THEPOSSESSION OF THE ELECTRICIAN UNTIL THE WORK IS COMPLETE.1.Before connecting the mixer to the electrical supply, the followingchecks/precautions must be taken.2.Check that the voltage phases and cycles (Hz) on the name plate attached to themotor are compatible with the available electricity supply.3.All cables, starters, etc. should be sized according to the relevant regulations andcodes of practice.4.Always follow the motor manufacturer’s instructions and wiring diagram whenconnecting three phase motors to the mains. The instructions are generally providedin the form of a printed sheet situated inside the terminal box, but they aresometimes printed on the terminal box itself or on the terminal box cover.5.The field wiring diagram is shown on the next page. If you have any questionsregarding the field wiring diagram, please contact Schold Manufacturing at1-800-4-MIXERS.5.3 DIRECTION OF ROTATIONWARNING: NEVER TOUCH ROTATING PARTS. FAILURE TO OBSERVE THIS MAY RESULTIN BODILY INJURY.WARNING: USE SPECIAL CARE WHEN HANDLING THE MIXING ASSEMBLY – THE BLADE AREA MAY BE SHARP!The mixer must be wired to ensure that it runs in the correct direction. The direction should be clockwise when viewed from the top of the motor. (See figure below) WARNING: ENSURE THAT THE MIXER IS ISOLATED FROM THE ELECTRICAL SUPPLYBEFORE CARRYING OUT THE FOLLOWING PROCEDURE:1.Before attempting to start the machine, ensure the drive shaft can be turned freely.This is carried out by carefully rotating the mixer shaft clockwise by hand. Make sure to avoid the sharp blade area. If the drive shaft does not turn freely, consult Schold Manufacturing.2.If everything is in order, reconnect the electrical supply and check for direction ofrotation.3.To jog, press the START button on the starter and IMMEDIATELY press the STOPbutton. This will make the motor turn only two or three revolutions – sufficient to view the direction of rotation. The direction should be clockwise when viewed from the top of the motor.4.If the motor rotates in the wrong direction, swap any two of the input phase linesand repeat the procedure given above. Changing the input leads into the VFDtypically will not change the rotation. Wiring must be changed between the VFD output and motor input.OPERATION _____________________________________________________________________________________ 6 OPERATIONWARNING: DO NOT USE THE MACHINE IN A HAZARDOUS AREA WHERE A FLAMMABLE OR EXPLOSIVE ATMOSPHERE MAY BE PRESENT UNLESS THE MACHINE IS FITTED WITH AN EXPLOSION PROOF MOTOR RATED TO THE RELEVANT STANDARD FOR THAT AREA.WARNING: USE SPECIAL CARE WHEN HANDLING THE MIXING ASSEMBLY – THE BLADE AREA MAY BE SHARP!1.Secure vessel in place with the tub holder arm and chain. Extend the tub holder armand wrap the chain tightly around it the vessel. Make sure it is centered with respectto the mixing blade and it is rigid in place.2.The operation panel (See figure below) consists of the following components:• A lever to move the mixer up and down• A knob to adjust the rotational speed of the mixer shaft.• A green button to start the mixer, a red button to stop the mixer•An emergency stop button to stop the mixer.WARNING: MAKE SURE THE SAFETY SWITCHES ARE WORKING3.The amps readout of the motor is shown from the readout above the operationpanel. It is displayed as a percentage.4.Do not operate without guards. The height of the shaft guard is adjustable toaccommodate various vessel sizes. Adjust the shaft guard height by unscrewing theknob, sliding the shaft guard to the desired location, and finally screwing the knobtightly back in place. (See figure below)5.Make sure the supplied air is a minimum of 80 PSIG. Lower the blade completelyinto the vessel. Start rotating the blade at a low speed. Do not attempt to start theblade in high or max speed setting. Never allow the blades to rotate above theproduct.6.Always turn the mixer down to the lowest speed setting before shutting off.6.1 MIXING TIPS•Always start the mixer at a low rotational speed setting.•Ramp up the speed to the desired speed, but make sure to never exceed 100% on the motor readout.•If high motor loading is hindering mixing, then run at a low speed setting until the product heats up. This decreases its viscosity, and allows higher speeds of mixing.6.2 CLEANINGThe LMX mixer is in most cases self-cleaning, a short run between successive mixingoperations in water, detergent or an appropriate solvent should be all that is necessary to clean the wetted parts. For more thorough cleaning, dismantling is easy anddowntime minimal.WARNING: THE MIXER MUST BE ISOLATED ELECTRICALLY BEFORE IT IS DISMANTLEDFOR INSPECTION OR CLEANING.The wetted parts can be cleaned with plant standard cleaning agents provided that they are non-scratching. Do not scour the parts with sharp objects.If the machine is to be left idle for any length of time it should first be thoroughlyflushed by running for a short time in a suitable cleaning agent to wash any solids from the blade and shaft end.WARNING: IF IT IS NECESSARY TO USE FLAMMABLE SOLVENTS TO CLEAN MIXEDPRODUCT OFF THE WETTED PARTS, THEN THE MIXING ASSEMBLY MUST BE REMOVED AND CLEANED IN A SAFE AREA, AWAY FROM THE MOTOR AND FRAME.WARNING: THE COMPLETE MACHINE ASSEMBLY SHOULD NEVER BE SPRAYED WITHWATER NOR IMMERSED IN WATER.The materials of construction of the wetted parts are compatible with all commonlyused cleaning chemicals.Most sanitizing chemicals, such as those that contain active chlorine, iodine, etc. arecorrosive, to some extent to stainless steel. Where these chemicals are used, 316Stainless Steel should be specified.WARNING: SUITABLE PROTECTIVE CLOTHING SHOULD BE WORN WHEN HANDLINGAND USING CLEANING CHEMICALS. NATIONAL, LOCAL, AND SITE REGULATIONSSHOULD BE OBSERVED.MAINTENANCE _____________________________________________________________________________________ 7.1 GENERAL MAINTENANCEMachines should always be cleaned after use. As a general guideline, where a machine is being used repeatedly to process the same material it will be sufficient to run themachine for a short time with water, detergent or a suitable solvent or flushing agent.If the machine is to be left idle for any length of time it should first be thoroughlyflushed by running for a short time in a suitable liquid to wash any solids from the blade and shaft end.7.2 ASSEMBLY AND DISASSEMBLY OF MIX BLADEWARNING: BEFORE PERFORMING ANY ASSEMBLY/DISASSEMBLY PROCEDURE,ISOLATE THE UNIT ELECTRICALLY. THIS OPERATION SHOULD BE CARRIED OUT BY AQUALIFIED ELECTRICIAN.WARNING: USE SPECIAL CARE WHEN HANDLING THE MIXING ASSEMBLY – THE BLADE AREA MAY BE SHARP!The LMX mixer’s blade assembly can be removed. To remove the blade assembly,unscrew it from the bottom of the shaft by twisting it clockwise when viewed fromabove. (See figure below)If any major fault develops, the mixer should be returned for repair and/or service. The mixer must be shipped suitably packed and with the approval of Schold Manufacturing.If you have any questions, please contact Schold Manufacturing at 1-800-4-MIXERS.7.3 RECOMMENDED SPARE PARTSThe LMX mixer’s blade can be easily replaced, and it is recommended to store a spare low speed bow tie blade assembly.LABELED PARTS_____________________________________________________________________________________ 9 DRAWING WITH LABELED PARTS。
WEM XEM系列电动阀电机TMC3服务卡安装与维护手册说明书

TMC3-115 QUICK CALIBRATION PROCEDUREThe WEM / XEM series electric actuators come standard with the TMC3 servo card already factory installed and calibrated. No additional settings need to be set prior to standard operation. This quick calibration procedure has been provided as a resource for information on calibration of the TMC3 servo card. For more detailed information, please see IOM8031.Wire TerminationThe Triac TMC3-115’s are typically mounted inside a Triac WEM series electric actuator. Theincoming power and control signal should be terminated per the actuators wiring diagram. The wiring diagram below illustrates the terminal connections on the TMC3-115 circuit board.WARNINGTAKE VALVE OUT OF SERVICE PRIOR TO CALIBRATION. CALIBRATION WILL CAUSE THE VALVE TO MOVE. PLEASE MAKE SURE VALVE IS ISOLATED FROM PROCESS AND VALVEMOVEMENT WILL NOT CAUSE SAFETY ISSUES.SIGNALOUTPUT 1234INTERNAL WIRINGACTUATOR FACTORY 10987654321NLN N L1234567TS2TS1FEEDBACKPOTENTIOMETERCW+5VWIPERGND NEUTRALLS1LS28910N-+1-5mA 4-20mA 1-5VDC-+0-10VDC SH.+-TRANSMITTER 4-20 mALINENEUTRALINPUT SIGNALCCWPOTENTIOMETER0 - 135 ohmCUSTOMER CONNECTIONS(STANDARD INPUTS)POWERHEATER21THERMOSTATTEMPSIGNALOPTIONAL MOTOR SIGNALPOWER12HEATERTEMPSIGNALTEMP SENSORInput signalThe TMC3-115 can accept various input signals, with the factory default set at 4-20mAdc. The chart below shows all of the input configurations with the jumper locations. Please check input signal termination when moving input jumpers from factory settings.Auto CalibrationThe TMC3-115 / WEM series electric actuator are factory calibrated, and no further calibration is required. The TMC3-115 / WEM series electric actuator can be field calibrated if necessary. The Auto Cal will set the open and closed position just before the limit switch trips at the end of travel. If a specific open or closed position is required, please see the Manual Calibration section.∙ Push DIP switch #1 and #6 to the ON position. When the PGM button is pressed, the TMC3-115 will start the automatic calibration procedure. The actuator will stop and the green light will turn on when the auto cal is complete.∙ Push DIP switch #1 and #6 to the OFF position will change the state to RUN MODE. Once in RUN MODE the actuator is ready for service.Manual Calibration∙ Push DIP switch #1 to the ON position will change the state from RUN MODE to CAL MODE.(NOTE: MAKE SURE DIP SWITCHES #2 - #7 ARE OFF WHEN PROGRAMMING TRAVEL POSITION)o When in CAL MODE the actuator will rotate clockwise when the CW button is pressedand counter clockwise when the CCW button is pressed.o To program the CW position, push the CW button to rotate the actuator to the desiredclosed position. Ensure that the close limit switch does not engage. Apply theminimum input signal and push the red PGM button. The red CW light and the yellow PGM light should flash confirming action.o To program the CCW position, push the CCW button to rotate the actuator to thedesired open position. Ensure that the open limit switch does not engage. Apply the maximum input signal and push the red PGM button. The green CCW light and the yellow PGM light should flash confirming action.∙ Push DIP switch #1 to the OFF position will change the state to RUN MODE. Once in RUN MODE the actuator is ready for service. Note:DIP #4 & DIP #5 are not active when input jumper is on 10V / SWReverse Acting∙ Push DIP switch #3 to the ON position will reverse the direction the actuator will rotate when a minimum signal is applied. This change will take place the next time the input moves or the power is cycled.Fail Position∙ The factory setting will rotate the actuator to the full clockwise direction when in direct actingmode (DIP #3 is OFF). The actuator will rotate to the full counter clockwise direction when in the reverse acting mode (DIP #3 is ON). The fail position can be controlled with DIP # 4 and DIP #5.Transmitter Adjustment∙ There is additional capability to adjust the 4-to-20 mA transmitter output. The adjustment range is about ±0.5 mA at the 4 mA end and ±1 mA at the 20 mA end. To adjust the output, start at the 4mA end by moving the actuator to the position that corresponds to a 4mA output (typically the fully closed position). Turn on switches 1, 3 and 4 (and only those switches), which puts the card in CAL mode and the 4 mA adjustment setting. Turn the calibrationpotentiometer while observing the 4mA output. When you have obtained the desired output, push the red PGM button to save the setting.∙ Move the actuator to the position that corresponds to a 20 mA output. (You can stay in CALmode and use the push buttons or switch to RUN mode and use the input to drive the actuator. Changing to run mode will necessitate turning off switch 3 unless you are operating in Reverse mode.) When you have reached the 20 mA position, make sure that only switches 1, 3 and 5 are on and turn the calibration potentiometer for the desired output. When the output iscorrect, use the red PGM button to save the setting. From now on, the card will use the new settings for the 4-to-20 mA transmitter.∙ To revert to the factory settings, repeat the above calibration procedure but set the calibrationpotentiometer to an approximate center position. For ease of centering the potentiometer, there is a “dead zone” in the center where the transmitter output does not change.Slide Wire InstallationConnect the slide-wire (135 ohm potentiometer)1. Connect the Low Water Level side of the slide-wire to terminal 1. Connect the wiper of the slide-wire to terminal2. Connect the High Water Level side of the slide-wire to terminal 4. 2. Put the INPUT jumper in the 10V/SW position. Put the GAIN jumper in the SW position. FAIL CCWFAIL CWFAIL IN PLACE1234567Note:DIP #4 & DIP #5 are not active when input jumper is on10V / SWCalibrating the span with a slide-wire. (An example of a slide-wire would be a McDonnell & Miller water feeder)1. Move the actuator to the fully closed position (using the black push buttons). Set the wiper ofthe slide-wire to the High Water Level side. Push the red PGM/AUTO CAL push button. The red and yellow LEDs should flash.2. Move the actuator to the fully open position (using the black push buttons). Set the wiper ofthe slide-wire to the Low Water Level side. Push the red PGM/AUTO CAL push button. The green and yellow LEDs should flash.3. Please note that for a somewhat less accurate calibration it is possible to perform theprocedure without the slide-wire connected.Running the actuator with a slide-wire1. Turn off DIP-switch 1 (run mode). In slide-wire mode filtering can be applied to the signal fromthe slide-wire. There are four possible settings for the filtering: slow, medium, fast and no-filter.2. The slow setting is activated by turning DIP-switches 6 and 7 off. This will yield a first orderfilter response with a time constant of about 16 seconds (to 63%). This is the default setting.3. The medium setting is activated by turning on DIP-switch 6. This will yield a first order filterresponse with a time constant of about 4 seconds (to 63%).4. The fast setting is activated by turning on DIP-switch 7. This will yield a first order filterresponse with a time constant of about 4 seconds (to 63%).5. The no-filter setting is activated by turning on DIP-switches 6 and 7. This will yield a responsewith no filtering.6. When in the slide-wire mode, square and square root responses are not available (DIP-switches 6 and7 are used for filtering options).Using Dual Gain Feedback Input on the TMC3 BoardSelecting the proper gain for the Feedback Input.1. Determine the rotation in degrees of the feedback potentiometer. The rotation equals theactuator shaft rotation (typically 90°) times the gear ration of the actuator shaft-to-potentiometer gear.2. If the potentiometer rotates less than 120° (this would typically indicate a 1:1 gear ratio on theshaft-to-potentiometer gear), use the H position on the FB jumper.3. If the potentiometer rotates more than 120° (this would typically indicate a 2:1 or 3:1 gear ratioon the shaft-to-potentiometer gear), use the L position on the FB jumper.A-T Controls product, when properly selected, is designed to perform its intended function safely during its useful life. However, the purchaser or user of A-T Controls products should be aware that A-T Controls products might be used in numerous applications under a wide variety of industrial service conditions. Although A-T Controls can provide general guidelines, it cannot provide specific data and warnings for all possible applications. The purchaser / user must therefore assume the ultimate responsibility for the proper sizing and selection, installation, operation, and maintenance of A-T Controls products. The user should read and understand the installation operation maintenance (IOM) instructions included with the product, and train its employees and contractors in the safe use of A-T Controls products in connection with the specific application.While the information and specifications contained in this literature are believed to be accurate, they are supplied for informative purposes only. Because A-T Controls is continually improving and upgrading its product design, the specifications, dimensions and information contained in this literature are subject to change without notice. Should any question arise concerning these specifications, the purchaser/user should contact A-T Controls.For product specifications go to /A-T Controls, Inc. • 9955 International Boulevard, Cincinnati, OH 45246 • Phone: (513) 530-5175 • Fax: (513) 247-5462 • 。
软件系统运维手册
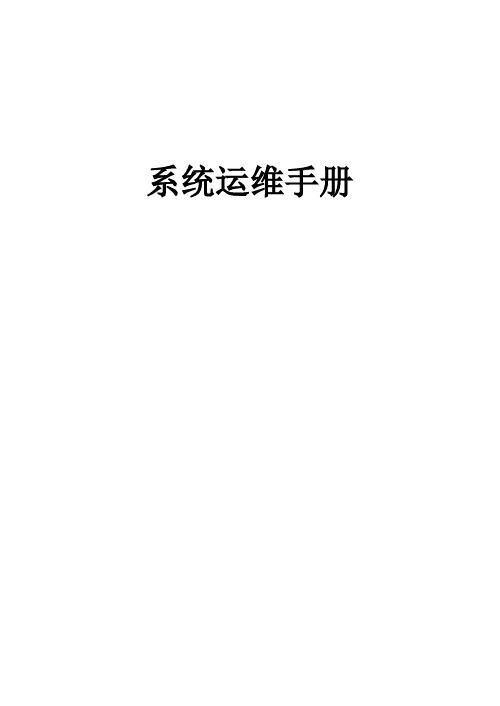
系统运维手册1、目的 (3)2、适用范围 (3)3、服务器及数据库概述 (3)3.1 服务器概述 (3)3.2 数据库概述 (3)4、系统服务程序的详细说明 (3)4.1系统服务程序的构成 (3)4.2 系统服务程序的启动、关闭及维护管理 (4)4.2.1 dhcp主服务 (4)4.2.2 dhcp从服务 (5)4.2.3 web管理模块 (5)5、服务器硬件维护(略) (6)6、windows 2003系统的日常维护 (6)6.1 定期检查磁盘空间 (6)6.2 维护系统注册表 (7)6.3 定期备份系统注册表 (7)6.4清理system路径下的无用的dll文件 (7)7、备份策略 (8)7.1 备份方式 (8)7.2 备份计划 (8)7.3 常见故障恢复 (8)9、数据库的日常维护 (11)9.1 检查数据库的基本状况 (11)9.2 检查数据库日志文件 (11)9.4监控数据库表空间的使用情况(字典管理表空间) (11)9.4.1 判断是否需要碎片整理 (11)10、命令解释 (12)1、目的楚天行消费卡管理系统运营支撑系统使用的服务器中,服务器均采用windows xp操作系统,数据库版本为:sql server 2000,随着业务的开展,sql server 数据库中存储的数据量也不断增大,这样操作系统和数据库的日常维护就显得十分重要。
本手册详细描述了程序模块,windows xp操作系统,负载平衡及sql server 数据库等日常检查的主要步骤,指导现场工程师对其进行监控和维护。
2、适用范围使用者为网e通宽带网络运营支撑系统维护工程师3、服务器及数据库概述3.1 服务器概述3.2 数据库概述数据库软件分别安装在主服务器上。
4、系统服务程序的详细说明4.1系统服务程序的构成4.2 系统服务程序的启动、关闭及维护管理4.2.1 dhcp主服务4.2.1.1 dhcp主服务说明4.2.1.2 dhcp启动、关闭及进程查看方法1、启动方法:输入:cd /opt/dpcp./dhcpd即可注意:请首先确认数据库服务正常,数据库监听正常。
- 1、下载文档前请自行甄别文档内容的完整性,平台不提供额外的编辑、内容补充、找答案等附加服务。
- 2、"仅部分预览"的文档,不可在线预览部分如存在完整性等问题,可反馈申请退款(可完整预览的文档不适用该条件!)。
- 3、如文档侵犯您的权益,请联系客服反馈,我们会尽快为您处理(人工客服工作时间:9:00-18:30)。
精密空调安装、维护手册NEXT系列RC GROUP S.p.A目录声明 (4)前言 (5)第一章概述 (6)1.1质量保证 (6)1.2 开机调试 (6)1.3 保修终止 (6)1.4 机组代码 (7)第二章技术信息 (8)2.1 机组概述 (8)2.2 工作原理 (8)2.4 选件 (17)2.5 安全装置 (17)2.6 技术数据 (17)第三章搬运和运输 (18)3.1 包装和拆箱 (18)3.2 搬运和吊装 (18)第四章安装和调试 (19)4.1 安全须知 (19)4.2 安装区域 (19)4.3 面板的开关 (19)4.4 管线连接 (20)4.5 机组安装 (21)4.6 空气过滤器拆卸NEXT UNDER H4 / H5 / H6 / H7 / H8 (21)4.7 制冷剂管道的连接(适用于DX 型和 DX.P型) (22)4.8 板式换热器的水管连接 ( DW / DW.P型) (24)4.9 附加盘管(制冷或制热)的水管连接 (25)4.10 冷凝水排水 (27)4.11 加湿器的供水管连接 (27)4.12 风管连接 (27)4.13 水管的清洗和排空 (28)4.14 电气连接 (28)4.15 开机前检查 (28)4.16 开机前的压缩机预热(DX/DW机组) (28)4.17 机组调试 (29)第五章部件和参数的调整 (30)第六章 使用 (31)6.1 使用建议 (31)6.2 设备操作件 (31)6.3 控制器显示和键盘 (32)6.4 微处理器的控制功能 (34)6.5 温湿度的设定 (34)6.6 报警记录 (35)6.7 计时器和维护报警 (35)6.8 时钟设定 (35)6.9 报警显示 (36)6.10 返回主菜单 (36)6.11 菜单显示内容的选择 (37)6.12 机组的长期停机 (37)6.13 长期停机后的开机 (37)6.14 热泵机组的融霜 (37)7.1 维护信息 (38)7.2 维护周期表 (38)7.3 压缩机维护周期表 (38)7.4 压力容器的检查 (39)7.5 冷凝器的清洁 (39)7.6 检查水流量和清洁换热器 (39)7.7 维修 (39)第八章故障分析 (40)8.1 故障代码 (40)8.2 故障分析 (41)第九章备件更换 (43)声明艾洛其空调(北京)有限公司版权所有。
在没有得到本公司书面许可时,任何单位和个人不得擅自摘抄、复制本资料(软件等)中的一部分或全 部,不得以任何形式(包括资料和出版物)进行传播。
本手册在中国大陆地区适用。
RC保留因技术改进修改参数而不预先通知的权利。
RC GROUP S.p.A前言感谢您选用RC机房空调。
用户如有任何问题,请与本公司当地的办事处及售后服务机构联系,也可直接与总部联系。
本手册作为机组的一部分满清妥善保存,以备将来使用。
为是机组得到最佳的使用,请在安装前仔细阅读本手册。
所有的安装工作和操作必须由熟练的专业人员完成。
如果对机组的安装要求和工作原理没有足够了解。
不了解足够的安全常识、没有采取足够的防护措施,请不要对机组进行任何操作,以免造成不必要的机组故障和人身财产的伤害。
建议对机组的安装、测试、整改必须由专业人员完成,在安装期间须遵照相关法律法规采取足够的防护措施。
安装人员和(或)设计人员对机组的机组的安装质量和正确使用负责。
RC对违反本手册或当地相关法律法规造成的任何财产或人身伤害不承担责任。
若安装、使用不符合要求或规范,将使用户丧失保修权利。
第一章概述1.1质量保证除风冷冷凝器只经过电气测试和制冷剂泄露测试外,其他机组在出厂前已进行严格的运行测试。
机组的保修期为自开机调试完成之日起12个月,但不超过自发货之日起18个月(如合同中另有规定,按照合同之规定执行)。
无RC书面授权,用户对机组任何的任何改动或违反RC的使用、维护手册之行为,将自动丧失保修权利。
1.2 开机调试机组的开机调试必须由艾洛其空调(北京)有限公司—意大利RC在中国大陆地区的子公司进行。
开机调试成功后,用户与RC调试工程师共同签署调试报告,调试报告与其他随机资料一起保存,作为机组质量保证有效性的依据。
1.3 保修终止用户出现下列行为,机组的保修自动终止:-违反本手册之规定-操作使用不当-违反安全操作规程-无RC书面授权,用户对机组做出任何改动1.4 机组代码1.4.1设备铭牌说明制机型统回路无 – 单系DC – 双系形尺寸规格缩机数量旋压缩机义制冷量 – KWKC –紧凑型,配皮带传动风机(仅适用于CW)P – 热泵机组第二章技术信息2.1 机组概述neXt机组针对高科技以及恒温恒湿等场所设计和制造。
设备必须安装在室内,或受保护的不被腐蚀的环境下。
设备配置了微处理器控制,可以监视全部部件的功能状态,并可外接监控系统进行通讯。
机组在工厂内全部组装完成,在通常情况下,现场安装只需要进行制冷管路,供排水管和电气的连接即可(DX 机组充注有制冷剂并安装维修截止阀),减少了安装时间和安装费,为了保持机组的高性能和对人员机器和环境的安全保护,在开始安装工作之前,由机组所有者在现场组织一个完整的项目管理,分析对从机组安装到机组报废期间内,所有可能会遇到的潜在问题。
2.2 工作原理根据换热器内的工作流体不同,分为直接蒸发式机组(风冷型和水冷型)和冷冻水机组。
2.2.1 风冷直接膨胀式机组机组主要由送风机、室内热交换盘管、节流装置、一台或两台压缩机、室外热交换器和室外风机组成。
室内热交换盘管有两种:室内空气被风机输送经过蒸发器,制冷效果由压缩机的热力循环实现。
蒸发器吸收空气的热能,并将热能传递到冷凝器,从而将室内的热量转移到外面的空气中。
制冷剂系统主要部件有压缩机、风冷冷凝器、膨胀阀、蒸发器,其流程图2-1、2-2图2-1 DX制冷系统图图2-2 DX.P热泵机组系统图2.2.2水冷直接膨胀式机组(配水冷冷凝器)NeXt DW.O / NeXt DW.U / NeXt DW.DL机组主要是由蒸发器、一个或多个压缩机和板式换热器组成。
室内空气被风机输送经过蒸发器,制冷效果由压缩机的热力循环实现。
通过蒸发器吸收来的热量被传递到板式换热器,然后传递到冷却水中。
制冷系统主要部件有压缩机、板式换热器、膨胀阀、蒸发器,其流程图2-3、2-4图2-3 DW制冷系统图图2-4 DW.P热泵机组系统图2.2.3 冷冻水型机组NeXt CW / NeXt CW.K / NeXt CW.KC / NeXt CW.DL机组主要由表冷器构成。
室内空气被风机输送经过蒸发器,制冷效果由从冷水机的冷冻水实现的 表冷器吸收室内空气的热量传给冷冻水,冷冻水被外界冷水机组冷却。
电动阀控制表冷器内的冷冻水流量。
图2-5 CW机组系统图2.3 主要部件2.3.1部件一、室内机组DX机组室内机包括制冷部分(压缩机、蒸发器、膨胀阀、视液镜、电磁阀、干燥过滤器、储液罐、安全阀等)、电加热、加湿器、送风机等部件。
DW机组包括DX室内机组的部件之外,还有板式换热器、水流量调节阀。
CW机组包括制冷部分(表冷器、水流量调节阀、除湿阀)电加热、加湿器、送风机等部件。
压缩机:采用高效涡旋压缩机,具有震动小、噪音低、高效节能、可靠性高的特点。
蒸发器:采用高散热效率的翅片管换热器。
针对具体机型对分配器进行设计和验证,保证冷媒在每个回路分配的均匀性,极大地提高了换热器的利用率。
热力膨胀阀采用外平衡式热力膨胀阀,运行稳定,同时取温度和压力信号,对冷媒的流量调节更精准。
加湿器电极加湿器模拟量加湿,结构形式简洁,可靠性高、使用简单、加湿洁净度高。
风机采用高效率、高可靠性的直连后倾离心风机,维护方便。
电加热管采用冲压铝翅片加热管,发热速度快,热量均匀、安全可靠。
视液镜制冷剂系统循环的窗口,可观察冷媒的状态,主要检测系统的水份含量情况。
当系统含水量超标时,其底色由绿色变为黄色。
液路电磁阀液路电磁阀最主要的功能压缩机停机时防止液态制冷剂的迁移,保护压缩机。
干燥过滤器干燥过滤器在一段时间内能有效除去系统中存在的水分,同时过滤系统中长期运行产生的杂质,保证了系统的正常运行。
储液罐储存一定量的液态制冷剂,保证制冷剂系统的稳定性。
板式换热器(用于水冷系列)采用AISI316不锈钢钎焊式板式换热器,具有结构紧凑、换热效率高的特点。
冷却水调节阀(用于水冷系列)水流量调节阀采集制冷系统的高压信号来调节阀的开度,控制流过板式换热器的水流量,保证系统的稳定。
冷冻水调节阀(适用于冷冻水系列)标配三通阀,选配两通阀,通过采集房间温度信号来调节阀门的开度,控制通过表冷器的水流量,保证房间温度的恒定。
除湿阀(适用于冷冻水系列)通过采集房间湿度信号来调节阀门的开度,控制通过表冷器的水流量,保证房间湿度的恒定。
二室外机组(制冷系统,用于风冷系列)室外机采用高散热效率的翅片换热器,不易积尘,清洗、维护方便。
风机采用轴流式低噪音风机或离心式低噪音风风机。
室外机由风机、冷凝器、调速控制器等主要器件组成。
风机适用电压范围广,通过采集高压信号来调整风机的转速,可靠性高,保证了制冷剂系统的稳定性。
T_TEAMMATE_DXA系列配置轴流风机,适用于散热环境较好的场所,有水平气流和垂直气流两种。
T_TEAMMATE_DXC系列配置离心风机,适用于散热环境不良的场所,可接送风管道将热量排放到较远的场所。
2.3.2机组图片下面给出了不同机组的图片图2-6 neXt.DX.O(上送风)系列图2-7 neXt.DX.U(下送风)系列图2-8 neXt.CW.O(上送风)系列图2-9 neXt.CW.U(下送风)系列图2-10 neXt.CW.KC.O(上送风)系列图2-11 neXt.CW.KC.U(下送风)系列图2-12 neXt.DL(弥漫时送风)系列图2-13 TEAM MATE(左边为轴流风机,右边为离心风机)2.4 选件用户如有特殊的需求可以在生产前提出,RC可以满足如下选择:–热气加热系统 (neXt DX / DW)–热水加热系统–附加回路系统–自然冷却系统 (neXt DW)–室内机支架–底部挡板–静压箱–止回风阀–制冷量控制系统(neXt DX / DW)–冷却水调节阀 (neXt DW)–冷凝排水泵–电极加湿器–电加热器如需选件,请与RC办事处或代理商索取安装使用手册。
2.5 安全装置在设计和生产阶段,RC已经安装安全装置(主动的或被动的)符合设备安装地的强制法规和规范。
各种类型的装置可如下所示安装–门锁开关: 打开或关闭电路–安全阀: 安装于制冷剂系统的储液罐。
图2-26 门锁式主开关与安全阀2.6 技术数据2.6.1 设备技术参数在随机文件中有描述 (数据文件和外型尺寸)。