低温冷风MQL切削镍基高温合金的仿真与实验研究
镍基高温合金的切削加工

镍基高温合金的切削加工CuttingofNickel-BasedHighTemperatureAlloy沈阳黎明航空发动机(集团)有限责任公司山东大学机械工程学院赵秀芬高级工程师.现主要从事航空发动机难加材料的匹配刀具选择.高效加工.切削参数优化.刀具国产化等方面的研究。
现在的涡扇发动机的材料中难加工材料占绝大部分,其中高温合金有65%,其相对加工性很低。
同时,航空航天发动机中叶片、机匣件等形状复杂,表面完整性要求又高,使镍基高温合金零件的切削加工更为困难。
航空发动机零件结构复杂,而高温合金等难加工材料加工难度更大。
对工件来说,复杂型面数控程序优化难,高温合金材料容易造成加工变形和让刀,使加工精度不符合要求;对46航空制造技术・2010年第11期赵秀芬王玉华刘阳王兴林万熠航空发动机零件结构复杂。
而高温合金等难加工材料加工难度更大。
对工件来说。
复杂型面数控程序优化难,高温合金材料容易造成加工变形和让刀,使iju-r精度不符合要求;对刀具来说,JjⅡ"r镍基高温合金零件,容易造成刀具快速磨损。
刀具消耗大。
刀具来说,加工镍基高温合金零件,容易造成刀具快速磨损,刀具消耗大。
镍基高温合金材料的主要成分为镍,以GH4169为例,其镍的含量为50%.55%,其余主要元素有Fe、Cr、Nb等。
它是以体心立方Ni3Nb(1,,)和面心立方Ni3(A1,Ti,Nb)(^y’)强化的镍铁基合怠通常称为镍基合金),从低温到700oc以下具有高的屈服强度、拉伸强度和持久强度。
在650。
C~7600C具有良好的塑性,一般认为GH4169的组织是由1基体和NbC、1’、1,,、8相组成。
NbC(Ti、Nb)(CN)等碳化物数量很少,比较稳定。
^y”相数量最多,是合金的主要强化相。
晶格常数为a0=3.642A,c0=7.406A,呈圆盘状在基体中弥散析出,强化作用是通过1,,的共格畸变而实现。
7’相数量次之,呈球状弥散析出,对合金起一部分强化作用,此外还有一些碳化物起强化相作用。
镍基高温合金的研究与工程应用
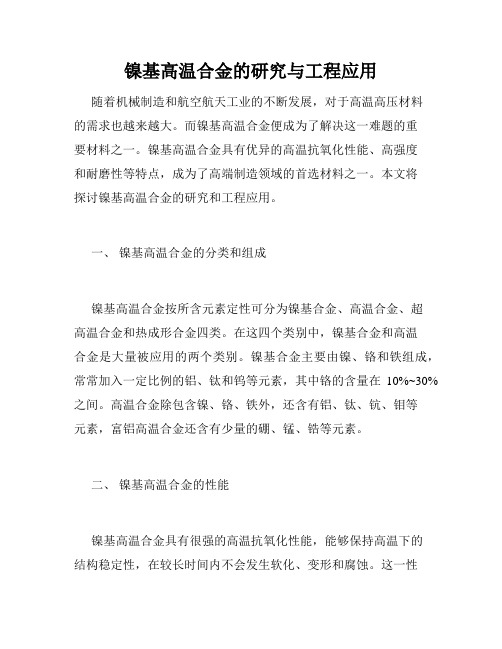
镍基高温合金的研究与工程应用随着机械制造和航空航天工业的不断发展,对于高温高压材料的需求也越来越大。
而镍基高温合金便成为了解决这一难题的重要材料之一。
镍基高温合金具有优异的高温抗氧化性能、高强度和耐磨性等特点,成为了高端制造领域的首选材料之一。
本文将探讨镍基高温合金的研究和工程应用。
一、镍基高温合金的分类和组成镍基高温合金按所含元素定性可分为镍基合金、高温合金、超高温合金和热成形合金四类。
在这四个类别中,镍基合金和高温合金是大量被应用的两个类别。
镍基合金主要由镍、铬和铁组成,常常加入一定比例的铝、钛和钨等元素,其中铬的含量在10%~30%之间。
高温合金除包含镍、铬、铁外,还含有铝、钛、钪、钼等元素,富铝高温合金还含有少量的硼、锰、锆等元素。
二、镍基高温合金的性能镍基高温合金具有很强的高温抗氧化性能,能够保持高温下的结构稳定性,在较长时间内不会发生软化、变形和腐蚀。
这一性能通过合金中添加铝、硅、钆等元素进行增强。
同时,镍基高温合金还具有高强度和耐磨性,能够在高速摩擦和高压环境下保持稳定性能,避免失效和生产事故的发生。
三、镍基高温合金的研究目前,针对镍基高温合金的研究主要集中在材料的制备、加工、表面处理和性能优化等方面。
对于材料制备方面,热状态下的粉末冶金、熔炼和快速凝固技术是当前的研究热点。
通过这些制备方法,能够获得颗粒更细、晶粒更细的材料。
对于材料加工方面,高温合金在制造过程中需进行多次热加工和热处理,以获得其高强度、高稳定性的特点。
表面处理方面,通常蒸镀、喷涂等方法常常用于增强镍基高温合金的抗腐蚀性能。
性能优化方面,深入研究各类添加元素对于合金力学性能的影响,以及不同工艺对于合金微观结构的影响均是当前研究的方向之一。
四、镍基高温合金的应用随着工业技术的不断提高,镍基高温合金的应用领域越来越广泛。
在航空航天、军事、电力、船舶制造等领域,镍基高温合金都有广泛的应用。
一方面,镍基高温合金能够长时间保持在高温高压环境下的稳定性能,在火箭发动机、航空发动机和汽车发动机等高温机件中得到应用。
镍基高温合金材料的研究进展

镍基高温合金材料的研究进展一、本文概述镍基高温合金材料作为一种重要的金属材料,以其出色的高温性能、良好的抗氧化性和优异的力学性能,在航空航天、能源、化工等领域具有广泛的应用。
随着科技的快速发展,对镍基高温合金材料的性能要求日益提高,其研究进展也备受关注。
本文旨在全面综述镍基高温合金材料的最新研究进展,包括其成分设计、制备工艺、组织结构、性能优化以及应用领域等方面,以期为未来镍基高温合金材料的进一步发展提供理论支持和指导。
本文首先介绍了镍基高温合金材料的基本概念和特性,概述了其在不同领域的应用现状。
随后,重点分析了镍基高温合金材料的成分设计原理,包括合金元素的选取与配比,以及如何通过成分调控优化材料的性能。
在制备工艺方面,本文介绍了近年来出现的新型制备技术,如粉末冶金、定向凝固、热等静压等,并探讨了这些技术对材料性能的影响。
本文还深入探讨了镍基高温合金材料的组织结构特点,包括相组成、晶粒大小、位错结构等,并分析了这些结构因素对材料性能的影响机制。
在性能优化方面,本文总结了通过热处理、表面处理、复合强化等手段提高镍基高温合金材料性能的研究进展。
本文展望了镍基高温合金材料在未来的发展趋势和应用前景,特别是在新一代航空航天发动机、核能发电、高温传感器等领域的应用潜力。
通过本文的综述,旨在为相关领域的研究人员和企业提供有益的参考和借鉴,推动镍基高温合金材料的进一步发展和应用。
二、镍基高温合金的基础知识镍基高温合金,也称为镍基超合金,是一种在高温环境下具有优异性能的特殊金属材料。
它们主要由镍元素组成,并添加了各种合金元素,如铬、铝、钛、钽、钨、钼等,以优化其热稳定性、强度、抗氧化性、抗蠕变性和耐腐蚀性。
镍基高温合金的这些特性使其在航空航天、能源、石油化工等领域具有广泛的应用。
镍基高温合金之所以能够在高温环境下保持优异的性能,主要得益于其微观结构的特殊性质。
这些合金在固溶处理和时效处理后,会形成一系列复杂的金属间化合物,如γ'、γ''和γ'″等,这些化合物在基体中弥散分布,起到了强化基体的作用。
基于Deform-3D的镍基高温合金残余应力仿真分析

基于Deform-3D的镍基高温合金残余应力仿真分析史若彤;邓子龙;高兴军;张绍禹;罗琳【摘要】GH4169 Nickel-based superalloys widely used, but it was difficult to cut.The residual stress of the machined surface could easily lead to the deformation of the workpiece, thereby the machining quality of the workpiece was affected.The variation of residual stress under different cutting parameters was studied by the simulation software Deform-3D.Simulation results showed that the change of cutting speed had little influence on the surface residual stress, the surface residual stress was increased with the increase of the cutting depth and the feed rate.The residual stress in workpiece was increased with the increased cutting parameters.%GH4169镍基高温合金应用广泛,但是属于难以加工的材料,而且已加工表面的残余应力很容易导致工件变形,从而影响工件的加工质量.应用Deform-3D软件,研究了不同切削用量下残余应力的变化规律.研究结果表明,切削速度的变化对表面残余应力的影响甚小;背吃刀量和进给量增大,表面残余应力随之增大;随着切削用量的增加,工件内部残余应力亦随之增加.【期刊名称】《辽宁石油化工大学学报》【年(卷),期】2017(037)004【总页数】4页(P49-52)【关键词】镍基高温合金;残余应力;Deform-3D;仿真分析;切削用量【作者】史若彤;邓子龙;高兴军;张绍禹;罗琳【作者单位】辽宁石油化工大学机械工程学院,辽宁抚顺 113001;辽宁石油化工大学机械工程学院,辽宁抚顺 113001;辽宁石油化工大学机械工程学院,辽宁抚顺113001;抚顺石化公司合成洗涤厂,辽宁抚顺 113004;中国石油审计服务中心,北京100028【正文语种】中文【中图分类】TB42GH4169是一种镍基高温合金,一般在大于600 ℃的温度及承受一定的载荷条件下工作。
镍基高温合金的研究和应用
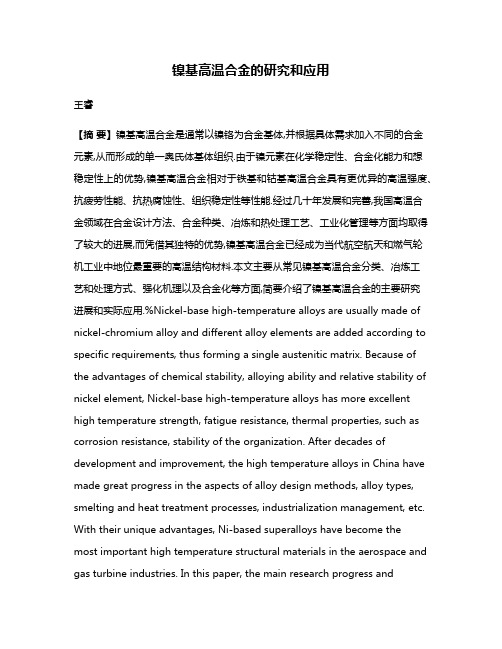
镍基高温合金的研究和应用王睿【摘要】镍基高温合金是通常以镍铬为合金基体,并根据具体需求加入不同的合金元素,从而形成的单一奥氏体基体组织.由于镍元素在化学稳定性、合金化能力和想稳定性上的优势,镍基高温合金相对于铁基和钴基高温合金具有更优异的高温强度、抗疲劳性能、抗热腐蚀性、组织稳定性等性能.经过几十年发展和完善,我国高温合金领域在合金设计方法、合金种类、冶炼和热处理工艺、工业化管理等方面均取得了较大的进展,而凭借其独特的优势,镍基高温合金已经成为当代航空航天和燃气轮机工业中地位最重要的高温结构材料.本文主要从常见镍基高温合金分类、冶炼工艺和处理方式、强化机理以及合金化等方面,简要介绍了镍基高温合金的主要研究进展和实际应用.%Nickel-base high-temperature alloys are usually made of nickel-chromium alloy and different alloy elements are added according to specific requirements, thus forming a single austenitic matrix. Because of the advantages of chemical stability, alloying ability and relative stability of nickel element, Nickel-base high-temperature alloys has more excellent high temperature strength, fatigue resistance, thermal properties, such as corrosion resistance, stability of the organization. After decades of development and improvement, the high temperature alloys in China have made great progress in the aspects of alloy design methods, alloy types, smelting and heat treatment processes, industrialization management, etc. With their unique advantages, Ni-based superalloys have become themost important high temperature structural materials in the aerospace and gas turbine industries. In this paper, the main research progress andpractical application of nickel-based superalloy are briefly introduced from the aspects of classification, smelting process and treatment, strengthening mechanism and alloying of common Ni-based superalloys.【期刊名称】《化工中间体》【年(卷),期】2017(000)007【总页数】2页(P50-51)【关键词】镍基高温合金;航空航天【作者】王睿【作者单位】江苏省常州市武进区前黄高级中学国际分校江苏 213000【正文语种】中文【中图分类】T高温合金特指以镍、钴、铁或三者与铬的合金为基体,能够承受苛刻的机械应力和600℃以上高温环境的一类高温结构材料.它一般具有较高的室温和高温强度、良好的抗蠕变性能和疲劳性能、优良的抗氧化性和抗热腐蚀性能、优异的组织稳定性和使用可靠性.上个世纪50年代初,我国通过仿照前苏联,自主研制并生产了出第一款高温合金GH3030,从而拉开了我国对于高温合金研究和应用的序幕.20世纪60年代初,我国投入大量人力和物力研究高温合金等军工领域用材料,许多高温合金的研究和生产中心在此时得以建立,并且引进了大量的科研和检测设备.这一阶段,考虑到我国本身存在quot;缺钴少镍quot;的情况,因此我国在高温合金领域特别是铁基高温合金上取得了前所未有的突破,研究和生产均出具规模,生产了诸如GH4037、K417等多个牌号的高温合金.但是由于基体本身化学和物理性质的原因,铁基高温合金在多方面均远逊色与同成分的镍基高温合金,因此在改革开放后,镍基高温合金逐渐成为我国高温合金研究和生产的主体,通过全面紧扣镍原矿,引进欧美技术,我国在粉末镍基高温合金,单晶镍基高温合金和定向凝固柱晶高温合金等尖端领域均取得了重大突破,先后推出了FGH 系列粉末涡轮盘材料,第一、二代单晶镍基高温合金DD402、DD26等.本文主要从镍基高温合金常见分类、冶炼和制备工艺、强化机理和合金化、实际应用等几个方面来简要介绍了镍基高温合金的研究发展.镍基高温合金具有许多种类,通常按照成型工艺的不同,将其分为铸造高温合金和变形高温合金.铸造高温合金由铸造工艺制备,通常分为等轴晶、定向柱晶和单晶三种.而变形高温合金普遍由粉末工艺制备,分为粉末高温合金和弥散强化型高温合金,通常具有良好的冷热加工性能和力学性能.(1)粉末高温合金利用粉末冶金工艺制造而成的高温合金称为粉末高温合金.传统铸造-锻造工艺制成的高合金化高温合金,存在宏观偏析严重、难于成型、疲劳性低等缺点,因此在工艺生产中并未大规模使用.随着粉末工艺的推广,通过在真空或惰性气体气氛下,以制粉工艺将高合金化难变形高温合金制成细小粉末,再通过不同的成形法制成目标合金.由于晶粒细小、成分均匀、微观偏析轻微,故相对于传统铸造合金,粉末高温合金往往在热加工性能,屈服强度和疲劳强度等力学性能上均得到较大提升.目前我国常用的粉末高温合金主要有FGH系列等,其中80年代研制的FGH95是目前强度最高的粉末高温合金.(2)定向柱晶高温合金通过定向凝固技术,使得合金内的横向晶界被消除,制备出只保留了平行于主应力轴的单一晶界的合金称为定向柱晶高温合金.定向凝固柱晶工艺通过螺旋选晶器或籽晶法,只允许一个柱状晶生长,可制成消除一切晶界的单晶涡轮叶片或导向叶片.定向柱晶高温合金具有优异的高温强度和屈服强度,并且相较于单晶高温合金,工艺更为简单、制作成本和检验成本也更低,因此定向柱晶高温合金被广泛应用于涡轮叶片的制造.(3)单晶高温合金采用定向凝固工艺消除所有晶界的高温合金称为单晶高温合金.单晶高温合金同样采用定向凝固技术,但是在型壳设计上增加了单晶选择通道.由于合金内一切晶界被消除,合金化程度很高,其高温强度、疲劳性能等力学性能相对于等轴晶和定向柱晶高温合金有了大幅度的提高,因此在尖端航空领域,单晶高温合金得到广泛应用,比如美国F35战斗机涡轮叶片所采用的的即使第三代镍基单晶高温合金CMSX-10.但是单晶高温合计由于制造成本相对较高、工艺复杂,因此使用受到局限.不同种类的镍基高温合金采用的制备方式截然不同,定向柱晶高温合金和单晶高温合金均采用定向凝固技术,粉末高温合金采用粉末冶金工艺方法生产,而传统的铸造高温合金采用铸-锻工艺生产.粉末高温合金和单晶高温合金是时下应用最前沿的两类镍基高温合金,因此对于其制备方法的研究是具有直接代表意义的.(1)定向凝固技术制备单晶高温合金和定向柱晶高温合金通常采用定向凝固技术,二者差别在于单晶高温合金往往会增设单晶选择通道.现在常用的定向凝固技术有,高速凝固法(HRS)、液态金属冷却法(LMC)、发热剂法(EP)和功率降低法(PD)等,这其中高速凝固法和液态金属凝固冷却法是目前应用最广的制造工艺.高速凝固法(HRS)通过在加热区底部增设了隔热挡板,并且在水冷底盘添加水冷套,使浇注后型壳与加热器之间发生了相对移动,增大了挡板附近的温度梯度,从而实现细化组织,消除晶界各异性的目的.液态金属冷却法(LMC)则是通过加入一个冷却剂槽,通常以锡为冷却剂.当合金熔体浇注成型后,将其从加热器中移出并逐渐匀速浸入到液态锡冷却剂中,这样在合金凝固表面和内部形成了较大的温度梯度,促使晶粒以单一方向生长.通过控制诸如冷却剂温度、浸入速率等参数可以调整合金的晶粒尺寸.(2)粉末冶金工艺粉末冶金工艺通常分为粉末制备和粉末固结两个阶段.目前在实际生产中的粉末制备工艺主要采用气体雾化法和旋转电极法.气体雾化法又被称为AA法,首先将真空熔炼过的母合金加入到雾化设备中,在真空环境下进行重熔,熔解的合金经由漏嘴流出后,在高压气体流的冲击下被雾化成粉末,其中氩气是最常用的气体.旋转电极法则是将合金料在高速旋转,利用固定的钨电极产生等离子弧来连续熔化合金料,这样在离心力的作用下,形成的液滴飞出形成了细小的粉末.粉末制备成功后,需要进行固结以便成形.由于传统的高温合金粉末中往往含有难烧结且易氧化元素,因此在传统的直接烧结工艺下成形相当困难,必须引入高温高压气氛.目前常见的粉末固结方式有真空热压成形、热等静压成形、热挤压和锻造、电火花烧结等成型方法,其中热等静压和热挤压是国内常用的两个工艺.镍基高温合金的强化效应通常组织强化和工艺强化两种.第一种是因为高温合金中的合金元素和基体元素相互作用,引起组织的变化而产生的强化效应.工艺强化是通过改良生产工艺、处理方式、锻造工艺等来实现对高温合金性能的提升.众多强化方式中,合金化对于高温合金性能的改变尤为重要.镍可以通过固溶、形成第二相等方式与加入的合金元素相互作用,其中常见的合金元素有Cr,W,Mo,Re,Al,Ti,Ta,C,B,Zr和稀土元素等十余种合金元素,这些元素在合金中起着不同的作用.Cr是镍基高温合金中含量相对较高的一个元素,它以固溶态存在于基体中,从而改善镍基高温合金的抗氧化性和抗热腐蚀性.W和Mo通过提高扩散激活能,降低合金中的扩散,从而增强原子间结合力,提高合金的硬度和高温强度.Al 是最主要的γ'相形成元素,且在高温下能形成保护性的氧化膜,提高合金的抗氧化性能,因此Al也常被用于表面化处理.其他如C,B,Zr和稀土元素等微量元素,在镍基高温合金中的含量均在1%以下,但是也起着很强的作用.经过几十年的研究和发展,镍基高温合金虽已经在多个方面均取得较大的突破,但为了满足航空、航天领域对于高性能高温合金材料不断增加的需求,也为了应对相关领域的国际竞争,增加我国的制空竞争力,在以后得研究中仍得从以下几个方面加强:(1)建立和完善更有效的合金设计方法,通过调整合金元素的比例,改善制造工艺来得到强度更高,质量更轻,成本更低的镍基高温合金;(2)应该对尖端高温合金诸如第三代单晶高温合金、第五代粉末高温合金的研制,改善制备工艺,使得这类合金的性能和质量更加稳记录并完善合金的性能和数据;(3)要扩大应用范围,扩展对于民用燃气轮机中高温合金的研制和开发.总之,镍基高温合金是航空航天领域发展的核心关键,高温材料的强度决定了飞机发动机的推重比和性能,因此研究镍基高温合金是认识材料领域,了解我国乃至世界航空航天领域发展,探索我国国防事业的一块敲门砖.王睿,男,江苏省常州市武进区前黄高级中学国际分校;研究方向:材料类.【相关文献】[1]郭建亭.高温材料学[J].北京:科学出版社,2010.06.[2]张义文.粉末高温合金研究进展[J].中国材料进展,2013年第1期.[3]孙晓峰.镍基单晶高温合金研究进展[J].中国材料进展,2012年第12期.[4]王斌,Al对高温合金高温抗氧化性能的影响[J].材料热处理技术,2012年5月.。
GH4169镍基高温合金铣削过程数值模拟
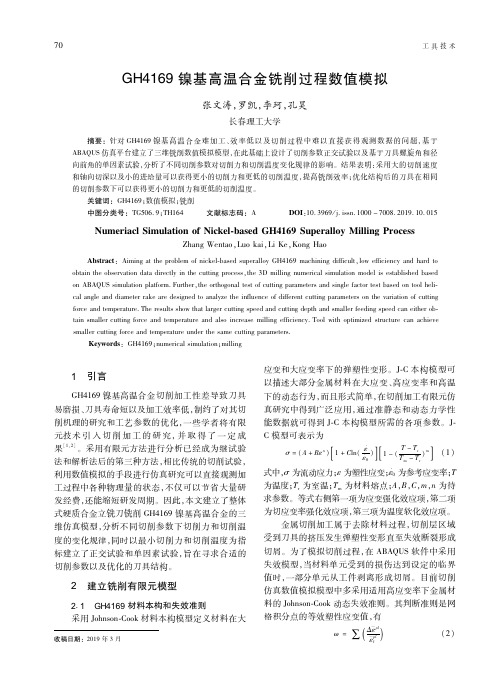
常量 值
常量 值
A(MPa) 450 d1
0.239
B(MPa) 1700 d2 0.456
n 0.65
d3 -0.3
c 0.017
d4 0.07
m 0.71
d5 2.5
有限元模型设计及边界条件定义 选用株洲钻石 PM4ED12.0G型整体式硬质 合金立铣刀,采用逆向建模方式。通过 OKIO三维 扫描仪生成铣刀点云,由 GeomagicDesign和 Solid Works软件生 成 铣 刀 切 削 刃 部 分 CAD模 型,导 入 ABAQUS分析 软 件 中。 刀 具 和 工 件 进 行 离 散 化 处 理,刀具采用 四 面 体 非 结 构 性 网 格 (适 用 于 结 构 复 杂且对 精 度 要 求 不 高 的 模 型),刀 具 网 格 类 型 为 C3D10MT,共 15168个单元;工件采用六面体结构 性网格,切削层区域网格进行密集划分,网格单元尺 寸选用径向切深的 1/3[4],远离切削区域的网格采 取稀疏处理,可在不影响精度的前提下提高计算速 度,工件网格类型为 C3D8RT,共 43736个单元。 刀具与工件之间的接触有相互间的热传导和摩 擦等。设刀具和工件之间的传热系数为 30W/(mm2· K),摩擦系数为 0.1。工件固定下端面,定义刀具沿 X轴的进给运动和 Z轴的旋转运动,初始温度设置 为 293.15K(见图 1)。
" 建立铣削有限元模型
"! >?$!8@ 材料本构和失效准则 采用 JohnsonCook材料本构模型定义材料在大
收稿日期:2019年 3月
应变和大应变率下的弹塑性变形。JC本构模型可
以描述大部分金属材料在大应变、高应变率和高温
镍基高温合金的切削性能及切削参数优化

镍基高温合金的切削性能及切削参数优化镍基高温合金是一种在高温环境下具有优异性能的材料,被广泛应用于航空、航天和能源等领域。
然而,由于其高硬度、高强度和高热稳定性,切削镍基高温合金是一项具有挑战性的任务。
因此,研究镍基高温合金的切削性能并优化切削参数对于提高切削效率和工件质量具有重要意义。
首先,镍基高温合金的切削性能受材料本身的特性影响。
镍基高温合金具有较高的硬度和强度,因此切削过程中会产生较大的切削力和切削温度。
同时,高温合金还具有一定的塑性变形能力,这会导致切削刃具的磨损加剧。
因此,切削镍基高温合金需要选择合适的切削刃具和切削液,并采取适当的切削策略,以减小切削力和切削温度,延长刀具寿命。
其次,切削参数的选择对镍基高温合金的切削性能具有重要影响。
切削速度、进给速度和切削深度是常用的切削参数。
在切削速度方面,较高的切削速度有助于提高切削效率,但过高的切削速度会导致刀具磨损加剧和切削表面质量下降。
进给速度的选择应考虑到切削力和切削温度的控制,较低的进给速度可以减小切削力和切削温度,但会降低切削效率。
切削深度的选择应根据工件的要求和刀具的承载能力进行合理确定。
为了优化切削参数,可以采用试验和数值模拟相结合的方法。
通过切削试验,可以获得切削力、切削温度和切削表面质量等关键参数,并评估切削性能。
同时,利用数值模拟方法,可以对切削过程进行仿真,预测切削力和切削温度的变化规律,为切削参数的优化提供依据。
综上所述,镍基高温合金的切削性能及切削参数优化对于提高切削效率和工件质量具有重要意义。
通过选择合适的切削刃具和切削液,以及合理调整切削参数,可以降低切削力和切削温度,延长刀具寿命,同时提高切削效率和工件表面质量。
未来的研究还应进一步探索切削机理和切削参数的优化方法,以满足高温合金在不同应用领域的需求。
镍基高温合金材料研究进展汇总
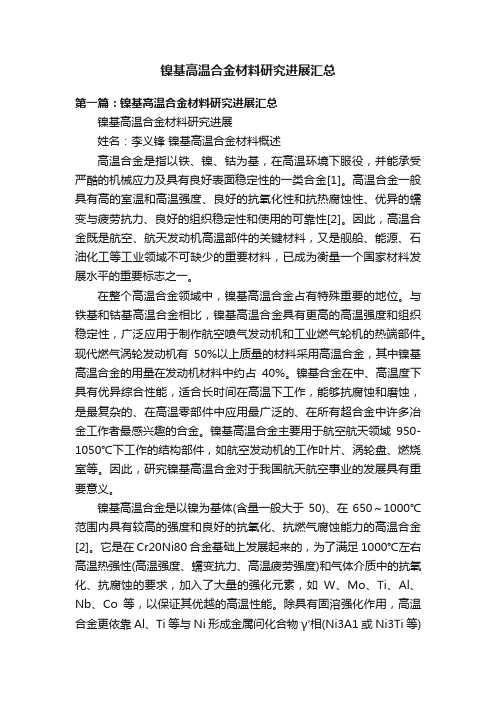
镍基高温合金材料研究进展汇总第一篇:镍基高温合金材料研究进展汇总镍基高温合金材料研究进展姓名:李义锋镍基高温合金材料概述高温合金是指以铁、镍、钴为基,在高温环境下服役,并能承受严酷的机械应力及具有良好表面稳定性的一类合金[1]。
高温合金一般具有高的室温和高温强度、良好的抗氧化性和抗热腐蚀性、优异的蠕变与疲劳抗力、良好的组织稳定性和使用的可靠性[2]。
因此,高温合金既是航空、航天发动机高温部件的关键材料,又是舰船、能源、石油化工等工业领域不可缺少的重要材料,已成为衡量一个国家材料发展水平的重要标志之一。
在整个高温合金领域中,镍基高温合金占有特殊重要的地位。
与铁基和钴基高温合金相比,镍基高温合金具有更高的高温强度和组织稳定性,广泛应用于制作航空喷气发动机和工业燃气轮机的热端部件。
现代燃气涡轮发动机有50%以上质量的材料采用高温合金,其中镍基高温合金的用量在发动机材料中约占40%。
镍基合金在中、高温度下具有优异综合性能,适合长时间在高温下工作,能够抗腐蚀和磨蚀,是最复杂的、在高温零部件中应用最广泛的、在所有超合金中许多冶金工作者最感兴趣的合金。
镍基高温合金主要用于航空航天领域950-1050℃下工作的结构部件,如航空发动机的工作叶片、涡轮盘、燃烧室等。
因此,研究镍基高温合金对于我国航天航空事业的发展具有重要意义。
镍基高温合金是以镍为基体(含量一般大于50)、在650~1000℃范围内具有较高的强度和良好的抗氧化、抗燃气腐蚀能力的高温合金[2]。
它是在Cr20Ni80合金基础上发展起来的,为了满足1000℃左右高温热强性(高温强度、蠕变抗力、高温疲劳强度)和气体介质中的抗氧化、抗腐蚀的要求,加入了大量的强化元素,如W、Mo、Ti、Al、Nb、Co等,以保证其优越的高温性能。
除具有固溶强化作用,高温合金更依靠Al、Ti等与Ni形成金属问化合物γ′相(Ni3A1或Ni3Ti等)的析出强化和部分细小稳定MC、M23C6碳化物的晶内弥散强化以及B、Zr、Re等对晶界起净化、强化作用。
镍基高温合金热处理实验
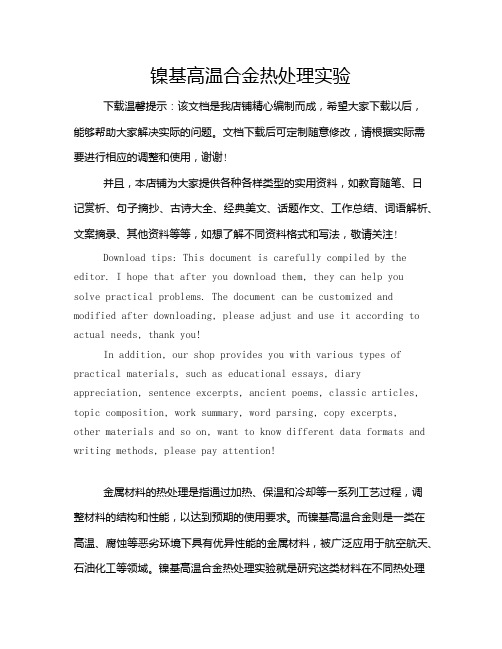
镍基高温合金热处理实验下载温馨提示:该文档是我店铺精心编制而成,希望大家下载以后,能够帮助大家解决实际的问题。
文档下载后可定制随意修改,请根据实际需要进行相应的调整和使用,谢谢!并且,本店铺为大家提供各种各样类型的实用资料,如教育随笔、日记赏析、句子摘抄、古诗大全、经典美文、话题作文、工作总结、词语解析、文案摘录、其他资料等等,如想了解不同资料格式和写法,敬请关注!Download tips: This document is carefully compiled by the editor. I hope that after you download them, they can help yousolve practical problems. The document can be customized and modified after downloading, please adjust and use it according to actual needs, thank you!In addition, our shop provides you with various types of practical materials, such as educational essays, diary appreciation, sentence excerpts, ancient poems, classic articles, topic composition, work summary, word parsing, copy excerpts,other materials and so on, want to know different data formats and writing methods, please pay attention!金属材料的热处理是指通过加热、保温和冷却等一系列工艺过程,调整材料的结构和性能,以达到预期的使用要求。
镍基高温合金激光焊接工艺研究

镍基高温合金激光焊接工艺研究1 绪论1.1 选题的依据及意义高温合金是航空发动机的关键材料,而镍基及镍铁基高温合金是目前高温合金结构材料的重要组成部分,镍基高温合金由于具有优异的耐热性及耐腐蚀性,被称之为“航空发动机的心脏”,具有组织稳定、工作温度高、合金化能力强等特点,目前已成为航空航天、军工、舰艇燃气机、火箭发动机所必须的重要金属材料,同时在高温化学、原子能工业及地面涡轮等领域得到了广泛的应用。
据统计,在国外一些先进的飞机发动机中,高温合金的用量已达发动机重量的55%~60%。
用于制造涡轮叶片的材料主要是镍基高温合金,同时镍基高温合金还是目前航空发动机和工业燃汽轮机等热端部件的主要用材,在先进发动机中这种合金的重量占50%以上。
在镍基高温合金的焊接上,目前主要采用氩弧焊、电子束焊、钎焊与扩散焊等。
激光焊具有高能量密度、深穿透、高精度、适应性强、不需要真空装置,热输入小,热影响区小且焊缝深宽比大,焊后变形小,表面光洁,可自冷淬火,焊接工艺参数调节比较容易等特性,因此非常适用于镍基高温合金的焊接。
1.2 国内外的研究概况及发展趋势1.2.1镍基高温合金的发展及现状高温合金的发展与航空发动机的进步密切相关。
1929年,英美Merica、Bedford和Pilling等人将少量的Ti和Al加入到soNi一ZoCr电工合金,使该合金具有显著的蠕变强化作用,但这并未引起人们的注意。
1937年,德国HanS von ohain涡轮喷气发动机Heinkel问世,1939年英国也研制出whittle涡轮喷气发动机。
然而,喷气发动机热端部件特别是涡轮叶片对材料的耐高温性和应力承受能力具有很高要求。
1939年英国Mond镍公司(后称国际镍公司)首先研制成一种低C且含Ti的镍基合金Nimonic75,准备用作whittle发动机涡轮叶片,但不久,性能更优越的Nimonic80合金问世,该合金含铝和钛,蠕变性能至少比Nimonic75高50℃。
基于镍基高温合金加工工艺的研究与应用

机 电 产 品 开 崖 与钏 新
VO . , . I 23 NO 5
Sep. 01 , 0 2
基 于镍基 高温合 金加工工艺 的研 究与应用
刘 逢 博
( 捷伦科技 ( 安 上海 )有 限公 司 ,上 海 2 0 3 ) 0 1 1
摘
要 :通 过 对 气 相 质 谱 分 析 仪 中镍 基 高 温 合 金 Ic n 12 n o e 5零 件 ( 6 离子 源腔 体 ) 的 切 削加 工 工 艺 的 分 析 研
究 .以及 通过 对 不 同切 削 刀具 ( 层 刀具 C 涂 VD&P VD)的 性 能研 究和 参 数 的组 合 试 验 ,验 证 并 总 结 出了合 理 有 效 的 工 艺方 案 ,攻 克 了加 工 难 点 并卓 有 成 效 地 达 到 延 长 刀 具 寿命 和 设 计 目标 ,
又 降低 了制 造 成 本
Re e c & App i a i n g Te pe a ur l y Par a hi ng Pr c s s ar h lc to on Hi h m r t e Alo tM c ni n e h oo is (h n h i Agl tT c n lge S a g a)Co,t, h n h i 0 1 1 e . d S ag a L 2 0 3 ,Chn ) ia Ab ta t Ha es de n eerh dc  ̄n p r ah sa dpo eso ce— ae ih tmp rtr l y ( cn 12 ), ihi ue sr c: v u id adrsace u igapo c e n rc s n Nik l bsdhg e eaueao I o e6 5 whc s sd t l n
高温合金的研究现状

航空航天镍基高温合金的研究现状1万艳松2鞠祖强南昌航空大学航空制造工程学院10032129 万艳松南昌航空大学航空制造工程学院10032121 鞠祖强摘要简单介绍了镍基高温合金的发展历程,综述了近年来镍基高温合金的研究进展,并探讨了镍基高温合金的应用和发展趋势。
关键字:镍基高温合金性能发展现状1.引言高温合金是一种能够在600℃以上及一定应力条件下长期工作的金属材料,而镍基高温合金是以镍为基体(含量一般大于50%) 在650~1000℃范围内具有较高的强度和良好的抗氧化、抗燃气腐蚀能力的高温合金。
2.镍基高温合金发展过程镍基高温合金(以下简称镍基合金)是30年代后期开始研制的。
英国于1941年首先生产出镍基合金Nimonic 75(Ni-20Cr-0.4Ti);为了提高蠕变强度又添加铝,研制出Nimonic 80(Ni-20Cr-2.5Ti-1.3Al)。
美国于40年代中期,苏联于40年代后期,中国于50年代中期也研制出镍基合金。
镍基合金的发展包括两个方面:合金成分的改进和生产工艺的革新。
50年代初,真空熔炼技术的发展,为炼制含高铝和钛的镍基合金创造了条件。
初期的镍基合金大都是变形合金。
50年代后期,由于涡轮叶片工作温度的提高,要求合金有更高的高温强度,但是合金的强度高了,就难以变形,甚至不能变形,于是采用熔模精密铸造工艺,发展出一系列具有良好高温强度的铸造合金。
60年代中期发展出性能更好的定向结晶和单晶高温合金以及粉末冶金高温合金。
为了满足舰船和工业燃气轮机的需要,60年代以来还发展出一批抗热腐蚀性能较好、组织稳定的高铬镍基合金。
在从40年代初到70年代末大约40年的时间内,镍基合金的工作温度从700℃提高到1100℃,平均每年提高10℃左右。
3.镍基高温合金成分和性能镍基合金是高温合金中应用最广、高温强度最高的一类合金。
其主要原因,一是镍基合金中可以溶解较多合金元素,且能保持较好的组织稳定性;二是可以形成共格有序的A3B型金属间化合物γ'[Ni3(Al,Ti)]相作为强化相,使合金得到有效的强化,获得比铁基高温合金和钴基高温合金更高的高温强度;三是含铬的镍基合金具有比铁基高温合金更好的抗氧化和抗燃气腐蚀能力。
激光增材制造镍基高温合金研究进展

激光增材制造镍基高温合金研究进展一、本文概述随着科技的快速发展,激光增材制造(LAM)作为一种先进的制造技术,已经在航空、能源、医疗等领域展现出广阔的应用前景。
镍基高温合金作为一种重要的高温结构材料,其优良的力学性能、高温抗氧化性和抗腐蚀性使其成为航空航天、能源发电等领域的关键材料。
激光增材制造镍基高温合金的研究对于提升我国高端制造业的竞争力具有重要意义。
本文将对激光增材制造镍基高温合金的研究进展进行全面的概述,分析当前激光增材制造技术在镍基高温合金制备中的应用现状,探讨其存在的挑战与问题,并展望未来的发展趋势。
文章首先将对激光增材制造技术的原理、特点及其在镍基高温合金制备中的优势进行简要介绍随后,重点综述近年来国内外在激光增材制造镍基高温合金方面的研究成果,包括材料设计、工艺优化、性能表征等方面结合当前研究的不足,对激光增材制造镍基高温合金的未来研究方向进行展望,以期为相关领域的科研人员提供有益的参考和启示。
二、激光增材制造镍基高温合金的基本原理能量输入与粉末熔化:激光增材制造过程中,高能激光束被聚焦在金属粉末床上,粉末吸收激光能量并迅速加热至熔点以上。
熔化的粉末在激光束移开后迅速凝固,形成一层薄薄的金属层。
这个过程反复进行,层层叠加,最终形成所需的复杂结构。
熔池动力学:熔池的形成和动力学对最终构件的质量至关重要。
熔池的大小、形状和稳定性受到激光功率、扫描速度、粉末层厚度等因素的影响。
理解熔池动力学对于优化工艺参数、控制晶粒生长和提高力学性能具有重要意义。
微观结构控制:激光增材制造过程中的快速加热和冷却导致了复杂的微观结构形成。
镍基高温合金中常见的微观结构包括柱状晶等轴晶和树枝晶等。
这些微观结构对合金的力学性能、耐热性和耐腐蚀性有着显著影响。
通过控制工艺参数,可以在一定程度上调控这些微观结构。
固态相变与热处理:在激光增材制造过程中,镍基高温合金可能经历多种固态相变,这些相变会影响合金的性能。
后续的热处理工艺如固溶处理和时效处理,可以进一步优化合金的微观结构和性能。
镍基高温合金Waspaloy铣削仿真研究
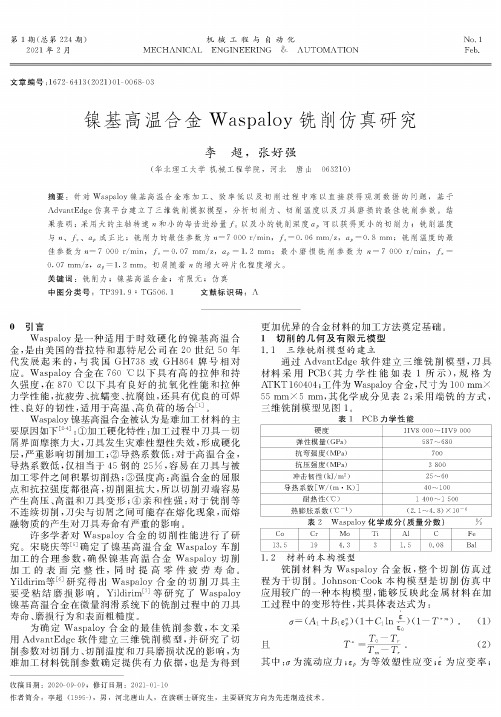
且
f 厂
(2)
其中:为流动应力;p为等效塑性应变;为应变率;
收稿日期:2020-09-09;修订日期:2021-01-10 作者简介:李超(1995-),男,河北唐山人,在读硕士研究生,主要研究方向为先进制造技术。
2021年第1期
李超,等:镍基高温合金Waspaloy铳削仿真研究
-69 -
€0为参考应变率;犃1为初始屈服应力;犅1为材料应变
各因素影响依次为进给量>铳削深度>主轴转速;后
刀面最小磨损水平为B2C3A3 ,即狀=7 000 r/min, f狕=0. 07 mm/z,ap = 1. 2 mm°
表8 VBmax的极差分析结果
狋C )
,Emax (gm/min)
1 5 000 0 06 0. 8 6. 25 268.44 1 281.94 28
2 5 000 0 07
1 6. 25 386. 7 1 278.57
25
3 5 000 0 08 1. 2 6. 25 520.34 1 318.65
34
4 6 000 0 06
文献标识码:A
0引言 Waspaloy是一种适用于时效硬化的镍基高温合
金,是由美国的普拉特和惠特尼公司在 20世纪50年 代发展起来的,与我国GH738或GH864牌号相对 应。Waspaloy合金在760 C以下具有高的拉伸和持 久强度,在870 C以下具有良好的抗氧化性能和拉伸 力学性能,抗疲劳、抗蠕变、抗腐蚀,还具有优良的可焊
变化趋势(犳=0. 08 mm/z,p = 1 mm)
变化趋势(n=7 000 r/min,p = 1 mm) 化趋势(n=7
= 0.06 mm/z)
3. 2 正交试验结果
镍基单晶高温合金微尺度磨削温度仿真

镍基单晶高温合金微尺度磨削温度仿真巩亚东;周俊;周云光;黄雄俊【摘要】针对镍基单晶高温合金具有较强各向异性以及镍基单晶高温合金微尺度磨削温度场研究较少的情况,建立了基于Hill模型的三维磨削温度仿真模型,并采用任意拉格朗日-欧拉法(ALE),实现单晶材料微磨削过程有限元温度仿真,分析微磨削过程中的温度场分布及其变化情况,研究了不同磨削深度、磨削速度以及不同晶面{(100),(110)和(111)}对微磨削温度的影响规律.结果显示:微磨削高温区发生在磨粒前表面与工件接触的半椭圆形区域,即第Ⅱ温度区;磨削区域温度随着磨削深度增加而增加,随着主轴转速增加而增加;在镍基单晶高温合金不同晶面内微磨削时,(111)晶面温度最高,(110)晶面次之,(100)面微磨削温度最小.%According to the condition that rare studies are working on micro-grinding temperature field for the nickel-based single crystal superalloy which has strong anisotropy ,three dimensional simulation model based on the Hill model was established by ALE method for temperature simulation in micro-grinding process for nickel-based single crystal superalloy. The distribution and variation of temperature fields in the micro-grinding process were discussed, and the influences of grinding depth, grain velocity and different crystal face{(100),(110) and (111)}on the micro-grinding temperature were analyzed. The simulation results showed that the high temperature zone happens in the semi ellipse region between the front surface of abrasive and the workpiece. The grinding temperature increases with the grinding depth and grinding speed. During the micro-grinding ofsingle crystal materials, the temperature of ( 111 ) crystal plane is the highest, and the (110) is the second, and the (100) is the least.【期刊名称】《东北大学学报(自然科学版)》【年(卷),期】2018(039)001【总页数】5页(P82-86)【关键词】镍基单晶高温合金;磨削;微磨削;磨削仿真;磨削温度场【作者】巩亚东;周俊;周云光;黄雄俊【作者单位】东北大学机械工程与自动化学院,辽宁沈阳 110819;东北大学机械工程与自动化学院,辽宁沈阳 110819;东北大学机械工程与自动化学院,辽宁沈阳110819;东北大学机械工程与自动化学院,辽宁沈阳 110819【正文语种】中文【中图分类】TH161镍基单晶高温合金是一种性能良好的材料,因其具有优越的抗热疲劳性能、抗蠕变性能、组织稳定性好,广泛应用于航空涡轮发动机转子叶片上,而涡轮发动机中最易破坏的部分(榫头和榫槽)是采用磨削工艺制造而成的,因此研究磨削中单晶材料温度场很有意义.随着镍基单晶高温合金微型零件的需求越来越多,这对微尺度磨削技术提出了更高的要求.而磨削过程中过高的温度对加工表面质量有不利影响,它会造成加工表面烧伤,导致工件表面层机械性能下降.同时磨削镍基单晶高温合金产生的塑性变形层在高温作用下可能发生相变,导致再结晶发生.另外,过高的磨削温度还会导致残余应力的产生以及热变质层等问题,进而影响到零件的疲劳强度和使用性能.国内外许多学者对磨削温度进行了研究,如:Outwater等通过剪切面上的移动热源理论建立了热量传入工件的热源模型[1];Hahn经过研究得出磨削热主要在磨粒磨削面上生成[2];Malkin采用热电偶测量温度的方法,发现磨削热源的长度是几何长度的2~3倍[3];Rowe等建立了把砂轮以及工件的热特性考虑进去的较简化的传热模型[4];Guo等在Rowe模型的基础上建立了可以把磨削液的影响考虑进去的新模型[5].虽然国内外对磨削温度作了大量的研究,但关于镍基单晶高温合金的微尺度磨削温度仿真还没有人研究.而微尺度磨削工艺作为镍基单晶高温合金微型零件加工的重要方法,实现其温度场的仿真研究对了解镍基单晶高温合金的微磨削温度场分布、控制磨削温度和提高镍基单晶高温合金的加工质量具有重要的意义[6-7]. 由于微磨削中磨棒以及加工零件尺寸较小,实验中不易测量或无法通过实验测得较准确的磨削温度[8],因此对镍基单晶高温合金微磨削加工进行仿真是很有必要的.通过大型有限元分析软件ABAQUS实现的微磨削温度仿真[9],可以不受实际环境限制.本文通过单晶材料的微磨削温度仿真模型,分析了微尺度磨削中温度场变化情况,以及磨削深度、主轴转速和不同晶面对磨削温度的影响及其变化规律.1 单颗磨粒仿真模型的建立磨削过程的实质是大量无规则的离散分布的磨粒进行的滑擦、耕犁、切削等的综合作用.磨削中每一颗磨粒都是一个发出热量的点热源,正是由于这一个个的点热源综合作用引起磨削温度的产生.因此可以把微磨削过程简化为单颗粒模型从而实现单晶材料微磨削温度的仿真研究.1.1 几何模型为比较真实地模拟磨削过程,建立模型前,利用超景深显微镜观察了磨头直径0.9 mm、表层电镀500#CBN磨粒的微磨棒,其放大500倍照片如图1所示;并测得磨粒尺寸约为20 μm.由图1可以看出,实际中磨粒的形状多为四棱锥形状,为较真实模拟真实磨削环境,将仿真磨粒形状确立为四棱锥,尺寸设定为20 μm.为提高计算效率,将磨粒简化为3维离散刚体,同时,考虑到磨粒的温度计算和接触稳定性,适当增加了磨粒的网格剖分密度.图2为最终确立的仿真磨粒形状.图1 微磨棒与磨粒照片Fig.1 Micro grinding rod and abrasive grain图2 磨粒建模Fig.2 Modeling of abrasive grain根据仿真需要,设定仿真模型的尺寸为60 μm×60 μm×20 μm,考虑工件为三维可变形体,并进行热-力双向耦合计算;工件材料考虑成正交各项异性材料,通过改变材料坐标系实现单晶材料的不同晶面和晶向的模拟计算;材料失效通过ABAQUS的累积损伤机理实现,其中,损伤初始化准则采用剪切损伤,损伤演化形式采用线性位移模式;另外定义仿真模型初始温度为20 ℃;为了减少计算量将工件上磨粒磨削区域特别细化,最终建立完成的单颗粒仿真模型装配图如图3所示.图3 单颗磨粒仿真模型Fig.3 Simulation model of single abrasive1.2 材料模型只有正确的材料模型才能保证仿真结果的正确性.本文仿真模型采用的是针对正交各向异性单晶材料的Hill材料模型.Hill材料模型目前广泛应用于拉伸和压缩屈服应力相等或相差不大的正交各向异性材料[10],而对于镍基单晶高温合金,DD3是一种典型正交各向异性镍基单晶高温材料,其结构是FCC,它的拉伸和压缩屈服应力几乎相等,特别适用于Hill模型.Hill材料模型表示方法:(1)式中:σs为参考屈服应力,一般取某一主轴方向的屈服应力;A,B,C,D,E和F是6个独立的各向异性参数,它们和材料主方向相关,可以通过沿三个材料主方向的单向拉伸试验和剪切屈服试验确定.对于FCC结构的单晶材料,沿材料主轴[001],[011]和[111] 三个方向的屈服特性相等,因此可以得到如下关系:A=B=C=1,D=E=F.于是可以把式(1)变化成式(2),得到Hill材料模型的简化表达式,式中D为材料常数,可以通过其他方向屈服应力来确定.对于本仿真模型,最终根据DD3的各方向材料特性以及式(2)确立D值为1.709.DD3在100 ℃环境下[100]晶向主要的材料参数:导热率为10.19 W·m-1·℃-1;比热容为481 J·kg-1·℃-1;热膨胀系数为12.38 ℃-1;弹性模量为130 GPa;泊松比为0.313;密度为8 200 kg·m-3;材料常数D为1.709.对于DD3其他主要晶向和不同温度下具体的材料参数,可以查阅《中国航空材料手册》获得.(2)将DD3特定的材料性能参数导入到ABAQUS的Hill模型中,就可以实现镍基单晶高温合金的微尺度磨削仿真.1.3 仿真模型的实验验证为说明仿真模型的正确性,对DD3设计了单因素实验,并采用热电偶测量法分别测量了不同晶面处的磨削温度,结果发现实验中不同晶面内磨削温度变化趋势与仿真结果变化趋势基本一致,从而验证了Hill材料模型模拟单晶材料各向异性的可行性,最终确定Hill材料模型是适用于DD3的,说明了仿真模型的可行性.实验中设定主轴转速为50 000 r/min,磨削深度为10 μm,进给速度为100 μm/s,分别测得(100),(110)和(111)晶面内平均磨削温度为145,161和181 ℃.观察数据可得出,相同磨削参数磨削单晶材料不同晶面时,在(100)晶面磨削时磨削温度最低,(111)晶面内最大,(110)的磨削温度介于之间,这趋势与仿真结果一致(不同晶面相关仿真结果与分析见2.5节).并且在实验中发现,实验测量的微磨削温度明显低于仿真出的磨削温度,仿真出的磨削温度一般达到300 ℃以上,而实验测量温度只有180 ℃左右,这是因为实验测量的磨削温度不是瞬时的.磨粒磨削工件时产生磨削热需要一定的时间传递到热电偶接头上,而且热电偶丝还需要特定的反应时间才能测量到温度信号,并且在热传递过程还会有大量的损失,导致热电偶接头处测量的磨削温度并不是瞬时最高温度;而仿真温度是通过电脑高速运算得出的,计算出的结果具有瞬时性,计算结果即为磨削过程中理论上最高温度,故导致仿真出的磨削温度明显高于实验测量的磨削温度.2 仿真结果与分析2.1 温度区定义磨削本质是单颗磨粒的切削过程,根据金属切削机理,可以将磨削中材料切屑形成过程划分为3 个变形区,热的产生主要发生在变形区内,依此可以将3个变形区划分为3个温度区.图4是单晶材料三维微磨削仿真的温度云图,为了便于观察和分析温度场的变化,将三维模型从磨粒中间切分得到图5所示的剖面图,从剖面图中可以清楚地看到温度场的3个温度区Ⅰ,Ⅱ和Ⅲ.图4 三维仿真温度云图Fig.4 Temperature field in micro-grinding simulation 图5 温度区Fig.5 Temperature zones第Ⅰ变形区为剪切温度区,热主要来自于材料切屑变形产生的剪切热;第Ⅱ变形区为磨屑-前刀面摩擦温度区,热主要来源于材料变形产生的剪切热和磨屑与刀面摩擦产生的摩擦热;第Ⅲ变形区为工件-后刀面摩擦温度区,热主要来源于磨粒底部与工件间的摩擦热.根据仿真结果可以发现,第Ⅱ变形区的温度明显高于Ⅰ,Ⅲ温度区,这是因为第Ⅱ变形区的温度相对于其他温度区既有材料变形的剪切热,又有摩擦产生的大量的摩擦热.高温中心发生在第Ⅱ变形区.2.2 微磨削中温度场变化图6为微磨削过程中磨粒速度1 m/s,磨削深度5 μm时不同时刻温度场的变化情况.由图6可以发现,当磨粒刚开始切入时材料变形主要发生在磨粒底部刃口处,变形产生的剪切热导致刃口处温度急剧上升,在t=3.2×10-6 s时高温达到178 ℃;随着磨粒的持续切入,磨粒前表面靠近底部一侧形成一半椭圆形磨削温度区,这是因为磨屑沿着磨粒前表面摩擦不断产生的摩擦热以及材料变形产生的剪切热综合作用的结果,在t=5.1×10-6 s时最高温度达到252 ℃;随着磨粒前表面堆积材料的增加,磨屑对磨粒压力增加,磨屑与磨粒前表面摩擦产生的热也增加,磨削高温中心开始沿磨屑移动方向扩大,到t=1.0×10-5 s时磨削温度基本稳定,温度持续在320 ℃上下波动,此时磨削过程进入稳定状态.图6 微磨削仿真过程中温度场变化Fig.6 Temperature field in micro-grinding simulation(a)—t=3.2×10-6 s,θmax=178 ℃;(b)—t=5.1×10-6 s,θmax=252 ℃;(c)—t=9.6×10-6 s,θmax= 321 ℃;(d)—t=1.3×10-5 s,θmax=335 ℃;(e)—t=2.0×10-5 s,θmax=318 ℃;(f)—t=2.5×10-5 s,θmax=329 ℃.2.3 磨削深度对微磨削温度的影响保持其他磨削参数不变,将磨削深度分别设定为2,4,6 μm,得到不同磨削深度下的温度仿真结果,如图7所示.根据仿真结果可以看出,随着磨削深度的增加,微磨削温度也随之升高.磨粒开始切入工件材料时温度开始提升并迅速增加到300 ℃左右,之后磨削温度基本稳定,随着磨削过程的进行上下波动.分析认为,温度随磨削深度的增加而增加是因为深度的增大:一方面使得磨粒切削厚度增加,单位时间内材料磨除量增加,磨削能也增加,导致剪切热增多,磨削温度相应增加;另一方面由于切深增加,磨粒与试件的接触面积增大,而镍基单晶高温合金本身导热性较差,使得磨削热的散热条件变差,热量不能及时传递出去导致磨削温度增加.图7 不同磨削深度下磨削温度随时间变化曲线Fig.7 Curves of grinding temperature change with time under different grinding depths2.4 微磨棒线速度对微磨削温度的影响利用DD3单晶材料进行微磨削温度仿真,保持磨削深度、晶向、晶面等参数不变,磨棒线速度vs分别设定为0.5,1.0,1.5,2.0和2.5 m/s.不同vs 条件下磨削区最高温度随时间变化曲线如图8所示.图8 磨削速度不同时磨削温度随时间变化曲线Fig.8 Curves of grinding temperature change with timeunder different grinding speed通过仿真结果发现在DD3微磨削加工中,磨棒线速度vs对磨削区最高温度影响的规律:随着磨棒线速度的提高,磨削温度是逐渐增加的,并且速度从0.5增加到1.5 m/s时,磨削温度增加较快;从1.5增加到2.5 m/s时,磨削温度增加较慢.经分析认为产生这种结果的原因是在磨棒线速度较低时,磨粒单位时间内需要去除材料较少,磨粒所承受的负荷较小,单位时间内经剪切变形和摩擦作用产生的热量较少,并且由于速度较慢热量可以更多地随着磨屑和空气传递出去,故磨棒线速度低时磨削温度也较低;随着磨棒线速度的增加,此时单位时间内需要去除的材料增加,单位时间内由于摩擦和材料剪切变形产生的热急剧增加,磨削速度的增加又导致产生的热量不能及时传递出去,使磨削温度区的温度急剧上升,最后在磨粒前表面与材料接触区形成微磨削温度区的高温中心.2.5 不同晶面对微磨削温度的影响在磨削深度为5 μm,微磨棒线速度为1 m/s,晶向为0°的微磨削条件下,分别在(100),(110)和(111)晶面内实现微磨削温度仿真,得到时间t=1.2×10-5 s时不同晶面仿真温度云图,如图9所示.图9 不同晶面磨削温度云图Fig.9 Temperature contour in different crystal face(a)—θ(100)=288.3 ℃; (b)—θ(110)=315.3 ℃; (c)—θ(111)=352.4 ℃.仿真结果显示不同晶面内磨削温度不同,磨削温度分别为352.4,315.3,288.3.大小为θ(111)>θ(110)>θ(100).这是因为单晶材料DD3在不同晶面内弹性模量是不一样的,查阅《中国航空材料手册》可知,DD3镍基单晶高温合金不同晶面内弹性模量大小为E(111)>E(110)>E(100),并且当温度为760 ℃时E(111)=217GPa,E(110)=162 GPa,E(100)=97.5 GPa.由于(111)晶面弹性模量较大,在该晶面内磨粒使材料产生单位变形需要的磨削力也较大,(111)晶面内材料产生单位变形时将会产生更多的剪切热,并且由于单位变形所需磨削力较大,单位变形量内磨粒与材料间由于摩擦生成的热也较多,最终导致沿(111)晶面内磨削时磨削温度最高.同理分析得到在(100)晶面磨削时产生的磨削热和剪切热相对较少,故磨削温度较低,(110)晶面内磨削时的磨削温度介于(111)和(100)晶面之间.3 结论1) 采用Hill材料模型实现了单晶材料微磨削温度仿真,并通过微磨削温度测量实验验证了模型的正确性.仿真结果发现,微尺度磨削加工中温度场有3个温度区,磨削高温区域分布在磨屑-磨粒前刀面接触区,即第Ⅱ温度区.2) 沿镍基单晶高温合金3个主要晶面磨削时,沿着(111)晶面磨削时产生的磨削温度最高,沿着(110)晶面磨削时磨削温度次之,沿着(100)晶面磨削时的磨削温度最低,沿着(100)晶面更有利于加工镍基单晶高温合金.3) 在镍基单晶高温合金的微尺度的磨削过程中,磨削温度随着磨削深度和磨削速度的增加而增大.参考文献:[1] Outwater J O,Shaw M C.Surface temperatures in grindings [J].Journal of Heat Transfer—Transactions of ASME,1952,74:73-78.[2] Hahn R S.On the nature of the grinding process[C]//Proceedings of the 3rd Machine Tool Design and Research Conference.Birmingham,1962:129-154.[3] Malkin S,Cook N H.The wear of grinding wheels.part 2:fracturewear[J].ASME Journal of Engineering for Industry,1971,11:1129-1133. [4] Rowe W B,Black S C,Mills B.Experimental investigation of heat transferin grinding[J].Annals of the CIRP,1995,44(5):329-332.[5] Guo C,Wu Y,Varghese V,et al.Temperatures and energy partition for grinding with vitrified CBN wheels [J].Annals of the CIRP,1999,48(1):29-34.[6] Zhou Y G,Gong Y D,Zhu Z X,et al.Modelling and optimisation of surface roughness from microgrinding of nickel-based single crystal superalloy using the response surface methodology and geneticalgorithm[J].International Journal of Advanced Manufacturing Technology,2015,34(2):62-74.[7] Aurich J C,Engmann J,Schueler G M,et al.Micro grinding tool for manufacture of complex structures in brittle materials[J].CIRP Annals—Manufacturing Technology,2009,58(1):311-314.[8] Qureshi A H,Koenigsberger F.An investigation into the problem of measuring the temperature distribution on the rake face of a cuttingtool[J].Annals of the CIRP,1966,14(2):189-199.[9] 赵腾伦.ABAQUS6.6在机械工程中的应用[M].北京:中国水利水电出版社,2007:55-65.(Zhao Teng-lun.The application of ABAQUS6.6 in mechanical engineering[M].Beijing:China Water Power Press,2007:55-65.)[10]Hill R.The mathematical theory of plasticity[M].London:Oxford University Press,1950:89-100.。
硬质合金刀具铣削镍基单晶高温合金DD5磨损试验

硬质合金刀具铣削镍基单晶高温合金DD5磨损试验巩亚东;梁彩霞;李强;刘洺君【摘要】为探究在干切削和水基微量润滑(WMQL)条件下刀具磨损对DD5铣削表面质量的影响规律,采用四刃PVD-TiAlN涂层硬质合金刀具以及超景深显微镜和扫描电镜等设备,以刀具副后刀面磨损宽度为主要评价指标,对硬质合金刀具副后刀面磨损形态、磨损机理进行分析和研究,并采用三维轮廓仪对零件表面粗糙度进行测量.研究结果表明,与干切削相比,采用水基微量润滑冷却技术,能够延长刀具寿命并改善材料的铣削加工性;硬质合金刀具的主要磨损机理为粘结磨损、磨粒磨损、氧化磨损和扩散磨损.【期刊名称】《东北大学学报(自然科学版)》【年(卷),期】2018(039)009【总页数】6页(P1283-1287,1326)【关键词】单晶高温合金DD5;铣削;刀具磨损;磨损机理;水基微量润滑【作者】巩亚东;梁彩霞;李强;刘洺君【作者单位】东北大学机械工程与自动化学院, 辽宁沈阳 110819;东北大学机械工程与自动化学院, 辽宁沈阳 110819;东北大学机械工程与自动化学院, 辽宁沈阳 110819;东北大学机械工程与自动化学院, 辽宁沈阳 110819【正文语种】中文【中图分类】TH161镍基单晶高温合金是以镍为主要元素的无晶界高温合金,具有良好的抗氧化性、组织稳定性和使用可靠性[1-2],比多晶高温合金具有更优异的高温强度和良好的蠕变抗力,在瞬时高温环境下,不存在高温进阶弱化、纵向晶界裂纹等问题,因此,近年来成为航空发动机以及燃气涡轮叶片的关键材料[3-4].然而镍基高温合金属于难加工材料,合适的刀具和冷却技术可以改善铣削过程中存在的加工效率低、成本高等问题,因此,不同冷却条件下铣削刀具磨损试验研究具有重要理论意义和实用价值.目前,涂层硬质合金刀具已获得广泛应用[5],对于不同涂层材料硬质合金刀具磨损破损形态及磨损机理已有深入研究[6].Najiha等[7]研究表明水基MQL条件下磨损后刀具呈现出完整几何形状,切削刃出现边界磨损和微小崩刃现象;Zhuang等[8]在不同冷却条件下研究镍基高温合金加工性能,结果发现MQL技术能够减轻刀具磨损,改善表面质量,减小表面粗糙度,并提高加工效率.就目前文献来看,很少有铣削DD5刀具磨损机理的试验研究,因此,有必要对刀具磨损过程进行深入探究.试验采用TiAlN硬质合金刀具对单晶镍基高温合金DD5进行不同冷却条件下铣削试验,针对刀具副后刀面磨损宽度及刀尖形貌,采用超景深显微镜和扫描电镜进行观察检测并对失效刀具表面元素进行能谱分析,研究干切削和水基MQL技术下TiAlN 涂层刀具铣削DD5的刀具寿命和磨损机理,期望能够为高效、绿色环保的铣削镍基合金提供试验依据.1 试验条件和方法1.1 试验材料试验材料为镍基单晶高温合金DD5,除有质量分数56.7%的基体元素Ni外,还添加了一些其他的合金元素(质量分数),如3%Re,7.5%Co,7%Cr,6.2%Al及6.5%Ta,在各种合金元素的综合作用下,DD5表现出了优异的物理性能.另外,单晶高温合金消除了多晶高温合金的晶界,存在各向异性,金相组织如图1所示.本次试验在(001)晶面上沿[110]方向进行槽铣加工,材料形状和几何尺寸如图1所示.图1 工件尺寸与材料金相图Fig.1 Workpiece size and material metallography 1.2 试验方案相关文献[9]将后刀面磨损量作为刀具失效评价指标,而试验中槽底面与刀具副后刀面直接接触,对材料表面质量有直接影响,因此,试验将副后刀面作为检测对象.随着加工过程进行,副后刀面与槽底面不断摩擦,产生明显磨损,且磨损宽度容易测量,因此试验中采用的评价标准如下:1) 副后刀面最大磨损宽度(VBmax)达到0.3 mm,将达到标准前的累积切削距离作为刀具寿命;2) 刀尖或切削刃出现崩刃.为测量刀具副后刀面磨损宽度并研究刀具磨损机理,在切削加工过程中对铣刀进行监测.试验将探究冷却条件对切削距离和磨损机理的影响,每种冷却条件进行3次试验.根据厂家推荐标准,刀具优选试验切削参数分别设置为:线速度(vs)=37.7 m/min,每齿进给量(fz)=13 μm,切削深度(ap)=0.18 mm,切削宽度为6 mm.1.3 试验条件试验刀具选用GM-4E PVD-TiAlN涂层硬质合金刀具,直径为6 mm,如图2所示.该刀具采用超细微粒(0.6 μm)钨钢基体,具有极高的耐磨性和强度,可加工高硬度材料,能实现高温下的稳定加工.而通过前期的工作发现,适用于切削多晶镍基高温合金Inconel 718的PVD-AlTiN涂层硬质合金刀具并不适用于该材料的铣削加工,其原因可能是由于涂层中较高Al元素含量导致的过强亲和性而引起的粘结造成的[10-11].图2 试验刀具Fig.2 Experimental tool试验采用KS-2107油气水三相复合润滑冷却系统,其结构原理如图3所示,将双喷头对称固定在铣刀两侧,水和油在压缩空气和雾化喷嘴的作用下,会以高速喷射到切削区,实现润滑和冷却作用.微量润滑系统根据油脂化学、界面化学反应原理制造,可自然降解的油分子能够在水分子的界面上形成一层薄油膜.图3 微量润滑系统原理图Fig.3 Schematic of minimum quantity lubricationsystem试验选用TH5650立式加工中心,最大转速6 000 r/min;采用三维轮廓测量仪测量零件表面粗糙度(Ra),Ra是基于区域形貌的评定参数,以随机5个点的平均值作为材料的Ra;采用KEYENCE VHX-1000E数字光学显微镜实现副后刀面磨损宽度的测量和工件表面形貌的检测,并采用扫描电镜和能谱分析(EDX)检测磨损后刀具及其表面元素成分.2 试验结果分析2.1 刀具寿命比较加工过程中刀面和材料被加工表面不断挤压摩擦,使得刀具涂层开裂剥落,服役寿命缩短.冷却条件对刀具寿命具有重要影响,干切削能够节约成本,但会加剧刀具磨损[12];浇注式冷却能够延长刀具寿命,但会对环境和工作人员身体健康产生危害.水基MQL技术在高压空气流作用下能够将可降解的植物油和水雾化成微米级小液滴[13],可实现有效润滑和减少刀具磨损,且绿色环保.图4分别为干切削和水基MQL条件下刀具达到VBmax前的累积切削距离,在试验条件范围内,基于水基MQL技术的累积切削距离比干切削约增加30%.试验结果表明,基于干切削的刀具磨损曲线具有三个磨损阶段,切削距离在0~0.8 m和1.4~1.9 m磨损较快,呈线性上升趋势,分别为初期磨损和剧烈磨损阶段;在0.8~1.4 m 副后刀面磨损宽度变化缓慢,为正常磨损阶段.由于刀具涂层不均匀,初期磨损较快;随着切削过程的进行,刀具表层接触面积较小的凸起部分已经磨掉,受到比较均匀的摩擦作用,副后刀面与已加工表面的接触面积逐渐增大,刀具进入正常磨损阶段;当刀具进一步磨损,副后刀面磨损宽度累积到170 μm时,刀具开始加剧磨损.加工过程中应当避免进入剧烈磨损阶段,磨损后的刀具会影响工件表面质量,从而影响零件服役稳定性.水基微量润滑技术下,磨损曲线呈持续上升趋势,在达到失效标准前能够切削更长的距离,说明水基微量润滑能够改善刀具的磨损速率.在1.3~1.5 m磨损曲线出现陡然上升现象,主要原因可能是前1.3 m累积切削过程对刀具涂层产生严重机械冲击,最终在这一阶段出现涂层大面积脱落的情况,导致刀具副后刀面磨损宽度剧增.图5是刀具副后刀面磨损区域的大小随切削距离的变化.干切削条件下,刀具副后刀面出现明显粘结,磨损区域逐渐增大;水基MQL技术条件下,刀尖表面无明显粘结,但三角形磨损区域同样逐渐向内侧扩大.图4 累积切削距离与刀具前刀面磨损曲线Fig.4 Curves of the tool flank wear with theaccumulated milling distance图5 不同冷却条件下刀具副后刀面随切削距离变化显微照片Fig.5 Micrograph of tool flank wear developmentwith cutting distance under different cooling conditions(a),(b),(c)—干切削; (d),(e),(f)—水基MQL.2.2 刀具磨损机理试验中为探究刀具磨损机理,采用超景深显微镜和扫描电镜检测铣刀副后刀面的磨损形貌,主要观察副后刀面是否存在粘结、涂层脱落、切削刃崩刃、微崩刃等现象;采用能谱仪对磨损后刀具副后刀面元素进行检测,分析刀具表面和工件材料元素之间的相互作用.2.2.1 磨粒磨损磨粒磨损是工件材料中的硬质点连续滑擦刀具表面所形成的条纹状磨损带(如图6a 所示).主要由于切削时,刀具表面和工件不断循环接触中摩擦产生热量,导致表面硬度降低.干切削条件下也存在磨粒磨损,如图7所示,但其程度明显低于水基MQL条件.2.2.2 粘结磨损通过比较图5两把铣刀的副后刀面发现,干切削条件下的切屑粘结现象比较严重,主要原因是切屑得不到及时清理,在工件表面不断堆积并与刀具摩擦,由热、力、化学等综合作用形成粘结.图7和图8分别对两种切削条件下副后刀面元素含量进行定性分析,结果表明刀具表面均存在镍基高温合金中的主要元素Ni,因此可以判断刀具表面产生粘结,存在粘结磨损,且干切削的粘结磨损更为严重.试验中刀具涂层和工件材料均含有Al元素,由于元素本身的亲和性,极易在刀具表面形成粘结,粘结层在机械冲击作用下易从刀面脱落,脱落过程将会撕裂刀具涂层,造成刀具粘结磨损.断续切削过程不断重复,粘结层又重新形成并脱落,会加剧粘结磨损的进行,最终涂层会大面积撕裂并露出基体材料(如图6c所示).图6 水基MQL条件下刀具失效形貌显微图Fig.6 Micrograph of failure tool under water-MQLcutting(a)—刀具磨损形貌; (b)—刀尖磨损二维图; (c)—刀具磨损放大图; (d)—刀尖磨损三维形貌光学放大图.2.2.3 氧化磨损图7和图8表明,两种冷却条件下,刀具磨损后表面均存在氧元素,说明铣削加工时,刀具材料中的一些元素可以与空气中的氧发生化学反应,生成氧化产物[6],例如Al2O3,WO3,Co2O3.Al和O具有较高的亲和性[14],极易形成Al2O3附着在刀具表面,随着铣削加工的进行,氧化层易于被切屑带走或被工件摩擦破坏,造成刀具的氧化磨损.图9中的EDS分析表明直线上氧元素含量每点各不相同,说明氧化程度不统一.较靠近磨损区域的氧含量较多,证明切削区有利于氧结合其他元素形成化合物,而距离磨损区域较远的位置氧含量相对较少.图7 干切削条件下刀具SEM和EDS分析Fig.7 SEM micrograph and EDS analysis of tooladhesion under dry cutting图8 水基MQL条件下刀具SEM和EDS分析Fig.8 SEM micrograph and EDSanalysis of tooladhesion under water-MQL cutting2.2.4 扩散磨损通过刀尖线扫描分析可以探究刀具磨损过程中是否存在扩散磨损.图9为水基MQL 条件下的线扫描分析,由Ti元素含量可知刀尖涂层已经脱落而漏出基体材料,而基体材料中Co元素的分布波动说明Co元素在切削过程中向粘结层发生了扩散,造成刀尖处Co元素含量的降低,影响刀具切削性能,造成刀具的扩散磨损.图9 水基MQL条件下刀具SEM和EDS线扫描分析Fig.9 SEM micrograph and EDS analysis of tooladhesion under water-MQL cutting2.3 刀具磨损对表面质量的影响加工过程中其他参数保持不变,刀具副后刀面磨损宽度成为主要变量,因其直接与材料槽底面接触,其磨损宽度直接影响工件表面质量.工件表面质量一般包括表面形貌和表面粗糙度,试验对被加工零件槽底面形貌进行了观察,如图10所示.材料表面形貌是由刀具运动轨迹和表面缺陷共同构成,观察两种切削条件下被加工表面形貌发现,新刀加工时,加工表面的圆弧形纹理浅而密;随着磨损量的增加,刀具运动轨迹凹槽加深、凸起增高.干切削条件下,切削距离为1.74 m时,材料表面的凹凸痕迹已经非常明显,如图10c所示;而水基MQL条件下,切削距离达到2.51 m时,被加工表面出现明显滑擦痕迹,如图10f所示.通过比较两种冷却条件下刀具失效前槽底的最大Ra值可知,水基微量润滑比干切削约降低10%.干切削条件下,刀具失效前铣槽底Ra值已经达到初始值2倍,如图11所示.被加工表面质量的变化主要由以下两方面原因引起:副后刀面的磨损宽度逐渐增大引起刀具在已加工表面上残留面积增大,从而增加刀具副后刀面和槽底面的摩擦;涂层脱落减弱切削刃和刀尖切削能力,引起粗糙度值上升和表面滑擦.图10 不同切削距离表面形貌变化显微照片Fig.10 Micrograph of surface topography underdifferent cutting distances(a),(b),(c)—干切削; (d),(e),(f)—水基MQL.图11 不同切削条件下刀具表面形貌Fig.11 Surface topography under different cutting conditions比较可知,水基MQL条件下的刀具表面形貌要优于干切削,证明水基微量润滑技术有明显冷却润滑效果,不仅能够延长刀具寿命,还能够改善被加工表面质量.3 结论1) 刀具磨损试验表明,干切削条件下,GM铣刀加工DD5时具有标准的磨损曲线;刀具在水基MQL技术条件下的切削距离比干切削长约0.6 m,证明水基微量润滑技术能够延长刀具寿命,减缓刀具磨损.2) 采用扫描电镜和能谱分析对GM铣刀磨损机理的探究结果表明,铣削DD5硬质合金刀具失效是磨粒磨损、粘结磨损、扩散磨损和氧化磨损的共同作用.3) 比较发现,刀具在干切削条件下有更明显的粘结磨损,在水基MQL条件下有更明显的磨粒磨损.磨损后刀具表面出现涂层脱落、微崩刃等磨损形貌.4) 刀具磨损试验表明,副后刀面磨损宽度对材料被加工表面形貌有明显影响,新刀首次加工,加工表面刀痕浅而密,切削距离不断加长,副后刀面磨损宽度不断增加;刀具失效前,干切削条件下的材料表面凹凸痕迹逐渐明显,水基MQL条件下的材料表面出现清晰滑擦现象.参考文献:【相关文献】[1] Ezugwu E O,Bonney J,Yamane Y.An overview of the machinability of aeroengine alloys [J].Journal of Material Processing Technology,2003,134(2):233-253.[2] Thangavel P.An experimental investigation on the effect of turning parameters onsurface roughness [J].International Journal of Manufacturing Research,2008,3(3):285-300.[3] Zhou Y G,Gong Y D,Zhu Z X,et al.Modelling and optimization of surface roughness from micro grinding of nickel-based single crystal superalloy using the response surface methodology and genetic algorithm [J].The International Journal of Advanced Manufacturing Technology,2016,85(9):2607-2622.[4] Zhou Y G,Gong Y D,Cai M,et al.Study on surface quality and subsurface recrystallization of nickel-based single-crystal superalloy in micro-grinding [J].The International Journal of Advanced Manufacturing Technology,2017,90(5/6/7/8):1-20. [5] 李友生,邓建新,张辉.高速车削钛合金的硬质合金刀具磨损机理研究 [J].摩擦学学报,2008,28(5):443-447.(Li You-sheng,Deng Jian-xin,Zhang Hui.Wear mechanism of cemented carbide tool in high speed machining titanium alloy[J].Tribology,2008,28(5):443-447.)[6] Hao Z P,Fan Y H,Lin J Q,et al.Wear characteristics and wear control method of PVD-coated carbide tool in turning Inconel 718 [J].The International Journal of Advanced Manufacturing Technology,2015,78(5):1329-1336.[7] Najiha M S,Rahman M M.Experimental investigation of flank wear in end milling of aluminum alloy with water-based TiO2 nanofluid lubricant in minimum quantity lubrication technique[J].The International Journal of Advanced Manufacturing Technology,2016,86(9/10/11/12):2527-2537.[8] Zhuang K,Zhang X,Zhu D,et al.Employing preheating-and cooling-assisted technologies in machining of Inconel 718 with ceramic cutting tools:towards reducing tool wear and improving surface integrity [J].The International Journal of Advanced Manufacturing Technology,2015,80(9):1815-1822.[9] Bushlya V,Zhou J M,Avdovic P,et al.Wear mechanisms of silicon carbide-whisker-reinforced alumina(Al2O3-SiCw)cutting tools when high-speed machining aged alloy 718 [J].The International Journal of Advanced ManufacturingTechnology,2013,68(5/6/7/8):1083-1093.[10]Li Q,Gong Y D,Sun Y,et ling performance optimization of DD5 Ni-based single-crystal superalloy[J].The International Journal of Advanced Manufacturing Technology,2018,94(5/6/7/8):2875-2894.[11]Li Q,Gong Y D,Cai M,et al.Research on surface integrity in milling Inconel 718 superalloy[J].The International Journal of Advanced ManufacturingTechnology,2017,92(3):1-15.[12]Khan M M A,Mithu M A H,Dhar N R.Effects of minimum quantity lubrication on turning AISI 9310 alloy steel using vegetable oil-based cutting fluid [J].Journal of Materials Processing Technology,2009,209(15/16):5573-5583.[13]Tawakoli T,Hadad M J,Sadeghi M H.Influence of oil mist parameters on minimumquantity lubrication - MQL grinding process [J].International Journal of Machine Tools & Manufacture,2010,50(6):521-531.[14]Li H Y,He H B,Han W Q,et al.A study on cutting and tribology performances of TiN and TiAlN coated tools [J].International Journal of Precision Engineering and Manufacturing,2015,16(4):781-786.。
1预应力切削镍基高温合金的试验研究_彭锐涛

月 2012 年 10 月
彭锐涛等:预应力切削镍基高温合金的试验研究
187
和使用寿命,因此构件在实际使用前常常进行表面 [5] 残余应力的调控 。从调控工序时间上来看,目前 控制残余应力的方法主要分为两类:一类是切削加 工后通过表面压延或增加表面密度等方法来控制, [6] 如喷丸、滚压和渗碳渗氮以及表面涂层等 ,这些 方法成本昂贵、效率较低,还会引起额外的表面硬 化,降低了零件的冲击韧度;另一类是在切削加工 [7] 的过程中进行控制,包括采用强冷低温切削 、微 [8] 量润滑切削 等方法,以及优化切削参数和刀具形 [9] 状 ,然而前者同样需要专用设备,后者由于影响 加工表面残余应力的因素多而复杂,仅考虑调整加 工参数往往难以稳定控制加工表面的残余应力。因 此,探索在切削加工过程中主动控制加工表面残余 应力的有效方法,对实现高温合金等难加工材料的 高效高质加工具有重要意义。 本文提出采用预应力切削方法,研制轴类高温 合金零件的预拉伸车削装置,在三组不同预应力条 件下对镍铜高温合金轴件进行切削试验,探讨预应 力切削对加工表面残余应力的调整机理,研究预应 力对切削力和切屑形态以及表面硬度、表面粗糙度 和表面形貌等加工表面完整性指标的影响规律。
- 1、下载文档前请自行甄别文档内容的完整性,平台不提供额外的编辑、内容补充、找答案等附加服务。
- 2、"仅部分预览"的文档,不可在线预览部分如存在完整性等问题,可反馈申请退款(可完整预览的文档不适用该条件!)。
- 3、如文档侵犯您的权益,请联系客服反馈,我们会尽快为您处理(人工客服工作时间:9:00-18:30)。
2018年7月第46卷第14期机床与液压MACHINETOOL&HYDRAULICSJul 2018Vol 46No 14DOI:10.3969/j issn 1001-3881 2018 14 007收稿日期:2017-01-17作者简介:朱林(1958 ),男,硕士,教授,专业方向为机械设计制造及其自动化㊂E-mail:775193964@qq com㊂低温冷风MQL切削镍基高温合金的仿真与实验研究朱林,路丹妮(西安石油大学机械工程学院,陕西西安710065)摘要:为探究低温冷风微润滑这种绿色加工技术应用于难加工材料时的效果,对难加工材料GH4269在干式㊁浇注式和低温冷风微量润滑条件下进行仿真模拟与切削试验㊂用ABAQUS对GH4169在3种方式下切削力和切削温度进行仿真;设计多因素正交实验对仿真结果进行验证㊂通过比较不同润滑方式对切削力及切削温度的影响,得出影响曲线图,从而揭示难加工材料GH4169在车削过程中切削力的变化情况,为实际的生产加工积累和提供基础数据㊂关键词:低温冷风;微润滑;镍基高温合金;ABAQUS仿真中图分类号:TH117 2㊀㊀文献标志码:A㊀㊀文章编号:1001-3881(2018)14-024-3SimulationandExperimentalResearchofNickel⁃baseHeat⁃resistingAlloyinLowTemperatureColdAirandMicroLubricationCuttingZHULin,LUDanni(SchoolofMechanicalEngineering,Xi anShiyouUniversity,Xi anShaanxi710065,China)Abstract:Thesimulationandcuttingexperimentsofdifficult⁃to⁃cutmaterialGH4169undertheconditionofdrycutting,conven⁃tionallubricantsandMQLweredescribed.ThecuttingforceandtemperatureofGH4169inthethreewaysweresimulatedbyusingABAQUS,themethodofmulti⁃factorswasusedtoconductthecuttingexperiments.Comparingthedifferentlubricationwaysinfluenceoncuttingforceandcuttingtemperature,thecurvesofthedifferentfactorswereillustratedandthechangeoftheforceduringthecut⁃tingprocesswasobtained.Thebasicdatafromthisresearchcanbeusedorasreferenceinthepracticalapplications.Keywords:Lowtemperaturecoldwind;Microlubrication;Nickel⁃baseheat⁃resistingalloy;ABAQUSsimulation㊀㊀随着人们生活水平的提高以及科学技术的发展,生活环境质量和人身心健康得到了更高的关注,人们对制造业的发展提出了更高的要求和更严格的制约㊂传统切削方法中干式切削技术虽然可以作为绿色切削加工技术[1],但对刀具材料要求过高;微量润滑技术应用在难加工材料上又很难达到加工要求,为此,各国科学家对低温冷风微润滑切削技术[2][也称低温冷风MQL(MinimumQuantityLubrication)切削技术]展开了研究㊂就目前国内外研究材料来看,研究这种新型技术所用的材料都是常用的普通材料[3]㊂此次研究选用GH4169镍基合金这种难加工材料作为研究材料,通过ABAQUS对干切削㊁浇注式切削和低温冷风微量润滑3种方式下切削力和切削温度进行仿真,再设计实验对仿真结果进行验证,以此探究低温冷风微润滑这种绿色加工技术应用于难加工材料时的效果,为实际的生产加工提供基础依据㊂1㊀切削力与切削温度的仿真与实验1 1㊀基于ABAQUS的温度场及力场的有限元仿真镍基高温合金中较多的合金元素以及强化相γᶄ[Ni3(Al,Ti)的存在]使得其成为应用最广㊁高温强度最高并且切削性能更差的一类㊂作者采用有限元软件ABAQUS/Explicit[3]对镍基高温合金GH4169在不同切削条件下的切削过程做数值分析,主要对切削温度场的变化规律进行了模拟,在设定3种不同润滑方式边界条件时,主要不同体现在工件表面换热系数不同㊁干切削时未使用切削液将其定义为空气自然对流换热冷却㊂在给定参数的条件下,从开始切削到稳态切削的温度分布情况如图1所示,切削力仿真结果云图如图2所示㊂由图1可得:干切削最高温度可达1092ħ,浇注润滑条件下最高756ħ,低温冷风微润滑条件下最高429ħ㊂由图2可得:干切削最大切削力可达1599N,浇注润滑条件下最大1108N,低温冷风微润滑条件下最大930N㊂经过数据分析,得出结论:低温冷风微润滑条件下切削,镍基高温合金的切削温度及切削力都能够有效地降低,最高切削温度比传统浇注降低35%,比干式降低44%;最高切削力比传统浇注降低8 7%,比干式降低25 7%㊂图1㊀切削温度仿真结果图2㊀切削力仿真结果云图1 2㊀GH4169不同条件下的切削实验及分析对不同润滑方式下切削力进行实验时采用对比方法,选用仪器有:CTL⁃40/1 5型冷风机㊁红外测温仪㊁CA⁃1A动态电阻应变仪㊁三向车削测力仪㊂仅研究润滑方式对切削力的影响时,根据实验数据做出多因素正交试验直观分析表(如表1所示)㊂表1㊀正交试验结果直观分析表F/N润滑方式微量润滑A微量润滑B湿式润滑干式润滑极差Fxmax333 73321 525307 91394 42286 5125Fymax307 5475298 285285 722366 90281 18Fzmax898 01894 38848 2151038 09189 875㊀㊀根据直观表做出分析图,如图3所示㊂由实验结果可见传统湿式润滑效果与低温冷风微润滑相差不大,但干切削却明显使切削力偏大,另外通过微量润滑A(即5mL/h出油量)与微量润滑B(即8mL/h出油量)结果可见出油量大时更有利于减小摩擦从而减小切削力㊂图3㊀润滑方式对切削力的影响在切削速度为89m/min㊁进给量2mm/r㊁背吃刀量0 8mm的条件下测试干切削㊁浇注式润滑和微量润滑条件下车削温度,测试结果分别如图4(a)㊁(b)㊁(c)所示㊂可看出:低温冷风微量润滑和干切削以及传统浇注式润滑比起来切削温度显著降低㊂温度柱形图如图5所示㊂图4㊀温度测试结果㊃52㊃第14期朱林等:低温冷风MQL切削镍基高温合金的仿真与实验研究㊀㊀㊀图5㊀3种润滑方式下的切削温度对比1 3㊀实验结果与仿真对比将切削速度为89m/min㊁进给量2mm/r㊁背吃刀量0 8mm试验条件下的数值进行比对,如图6所示,图(a)为切削温度对比折线图,图(b)为切削力对比折线图㊂可以看出:切削力㊁切削温度的仿真数据大于实验数据,这是因为在仿真时定义的边界条件都是最理想化的,但是实际加工中会有各种不定因素以及误差的影响㊂但是其变化规律是相同的,依然是低温冷风微润滑条件下的切削为最优㊂图6㊀切削温度㊁切削力仿真与实验对比图2㊀结束语通过低温冷风微润滑切削过程仿真与实验,分析得到如下结论:(1)在同样的条件下,低温冷风微润滑的切削力比传统浇注式及干切削的切削力都要小㊂这主要是由于低温冷风微润滑喷出混合雾化的润滑油具有较强的吸附和换热能力,可以在工件-刀具㊁切屑-刀具间形成坚实的润滑油膜,对切削区进行良好的润滑和强力的降温㊂(2)在低温冷风微润滑的作用下切削可以有效降低切削温度㊂浇注式润滑效果优于干式切削是由于大量切削液以流换热方式将切削热迅速带走,而低温冷风微润滑更优于浇注式是由于冷风射流机将空气冷却后与微量润滑切削液一起喷射入切削区,其喷嘴处最低温度可达到-40ħ,从而快速降低切削温度㊂(3)在低温介质的作用下切削,可以达到提高刀具的耐用度和加工表面质量的目的㊂参考文献:[1]汪通悦.干切削的关键技术[J].机械制造,2005,43(1):27.WANGTY.KeyTechniquesofDryCutting[J].Machinery,2005,43(1):27.[2]罗永顺,曾伟民.关于干切削技术推广问题的探讨[J].现代制造工程,2004(10):103-104.LUOYS,ZENGWM.TheDiscussionofDryCuttingTechnology sPopularization[J].ModernManufacturingEn⁃gineering,2004(10):103-104.[3]张昌义,顾祖慰.冷风切削技术的发展应用及课题[J].工具技术,2008,42(10):39-42.ZHANGCY,GUZW.Improvement,UsingandTasksofColdAirCuttingTechnology[J].ToolEngineering,2008,42(10):39-42.[4]李春胜,黄德彬.机械工程材料手册[M].北京:电子工业出版社,2007.[5]胡壮麒,彭平,刘轶,等.镍基合金中γᶄ相界面的强化设计[J].金属学报,2002,38(11):1121-1126.HUZL,PENGP,LIUY,etal.DesignofγᶄPhaseInter⁃faceStrengtheningofNickel⁃baseSuperalloy[J].ActaMe⁃tallurgicaSinica,2002,38(11):1121-1126.[6]康文利.高温合金的切削加工分析[J].装备制造技术,2010(9):124-125.KANGWL.AnalysisofMachinabilityforHighTemperatureAlloy[J].EquipmentManufacturingTechnology,2010(9):124-125.[7]石亦平,周玉蓉.ABAQUS有限元分析实例详解[M].北京:机械工业出版社,2006.[8]张铁,张军,孙宝元,等.三向压电式动态车削测力仪的性能研究[J].压电与声光,2008,30(6):705-707.ZHANGT,ZHANGJ,SUNBY,etal.StudyonThree⁃di⁃mentionalDynamometerofPiezoelectricityonTurning[J].Piezoelectrics&Acoustooptics,2008,30(6):705-707.[9]朱林,张晓琴.镍基高温合金在低温冷风微润滑条件下的切削研究[J].装备制造技术,2015(12):21-23.ZHUL,ZHANGXQ.NickelBaseHeat⁃resistingAlloyinLowTemperatureColdAirandMicrolubricationCuttingResearch[J].EquipmentManufacturingTechnology,2015(12):21-23.㊃62㊃机床与液压第46卷。