阳极氧化工艺原理与常见故障分析
阳极氧化原理全解
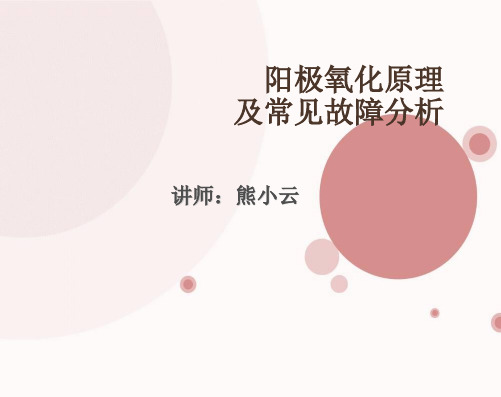
槽液温度是阳极氧化一个重要工艺参数,为确保氧化膜的质量和 性能要求恒定,一般需严格控制在选定温度±(1~2)℃范围内,控 制和冷却槽液温度有下列四种方法:
①冷冻机中的致冷剂与安装在氧化槽内的蛇形管连通直接冷却;
②用蛇形管间接冷却装置,即冷冻机冷却冷水池中的水,再用水泵 将冷水打入氧化槽中蛇形管内冷却槽液;
B、槽液液面上的漂浮物和油污应及时清除, 脱落在槽液中的铝工件和杂物应及时捞起。
C、氧化槽液沉淀物较少,一般只需一年倒 槽清底一 次,此时应刷洗或更换阴极板。
(三)氧化膜的影响因素:
• ①硫酸浓度: 当其他条件不变时,提高硫酸浓度,氧化膜的生长速度
减慢,这是由于生长中的氧化膜在较浓的硫酸溶液中溶
2、电化学氧化: A.定义: 将铝及其合金置于某种适当的电解液中 作为阳极,在外电流作用下,使其表面生 成氧化膜的过程称为阳极氧化,又称电化 学氧化。
B、阳极氧化膜的性质(与化学氧化膜相 比): ①氧化膜结构的多孔性; ②氧化膜的耐磨性; ③氧化膜的抗蚀性; ④氧化膜的电绝缘性; ⑤氧化膜的绝热性; ⑥氧化膜的结合力; ⑦氧化膜的硬度高; ⑧氧化膜的装饰性。
D.多孔膜形成过程: 1.阳极氧化初期,电流密度一般均超出临界电流密 度,形成均匀的壁垒型膜; 2.壁垒型膜逐渐成长。当电流密度低于临界值时, 铝离子不能再形成新膜物质,膜的表面暴露在电 解液中受到浸蚀; 3.进一步阳极氧化,溶液对膜的浸蚀变得不均匀; 4.形成的空洞之间存在发展竞争。这种发展有“自 催化”作用; 5.发展较快的空洞(主空洞)在向膜深处和横向发展 6.主空洞继续沿纵向和横向发展,相邻主空洞之间 互相靠近,主空洞之间的小空洞停止生长; 7.空洞停止横向发展,仅沿纵向深入,孔径固定。 此时,空洞的产生及发展阶段结束,阳极氧化进 入稳态阶段。
阳极氧化不良原因分析
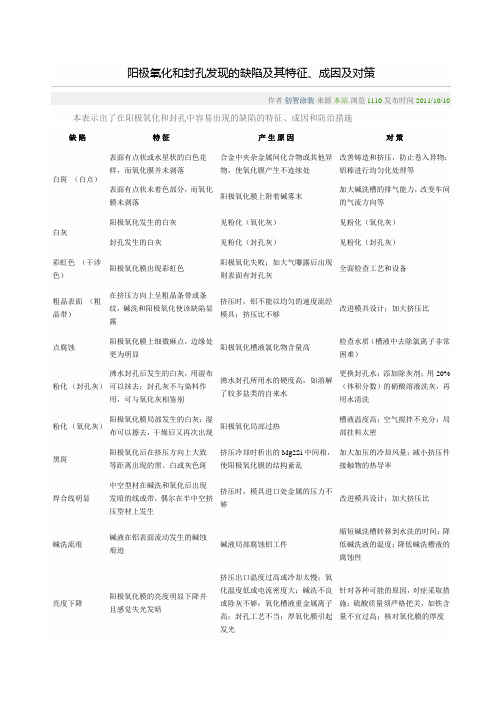
作者创智涂装来源本站浏览1110 发布时间2011/10/10本表示出了在阳极氧化和封孔中容易出现的缺陷的特征、成因和防治措施铝材阳极氧化封孔,不挂灰时间短.•信息名称:铝材阳极氧化封孔,不挂灰时间短.所在地:山东省威海市发布时间:2011-07-08加入收藏夹联系人:郭小姐威海云清化工开发院联系人:郭小姐女士电话:86-手机:传真:86-邮件:地址:山东省威海市文化中路89-2号查看全部产品进入展厅一、产品用途:本品为浅绿色粉末,适用于建筑铝型材和其他铝制品的封孔处理,本品封孔温度范围宽,它能够改善表面装饰的无色金属络合物, 在其它物质的支持下,依靠镍和氟化物离子的协同效应,发挥作用。
二、性能特点:1、同热水封孔的工艺相比, 冷封孔能缩短处理时间和节约加热所需的能源, 从能源成本和阳极氧化物生产线能力的角度来考虑这种优点就相当重要。
2、这种产品的结合能防止干净阳极氧化铝部件发绿的退色现象。
不产生白霜,其耐蚀性和耐磨性及硬度均高于沸水封孔处理.三、槽液组成及工艺条件:本品浓度 3.5-5.0克/升去离子水余量PH值5-5.6温度25-35℃时间8-15分钟(一分钟能封一个微米厚的氧化膜)Ni+ 0.9-1.2克/升F- 0.3-0.85克/升消耗量:0.8-1.5千克/吨材(约400m2)* 封孔后第一道用冷水洗,然后在进行温水洗.温水槽温度:60℃;时间:5分钟四、注意事项1、槽材料: 衬有塑料的钢或不锈钢。
特别须知要点:建议对溶液作过滤处理, (不可用筒式过滤器)。
为了保证溶液能长期使用, 避免溶液被全部排放, 每立方米中物料通过量达到1000m2,就应排放50 L/m3的槽液.2、用量: 产品用量和被处理氧化层的厚度和生产率有关。
3、阳极氧化层的质量:通过用封孔液的处理, 氧化层会产生一种反应, 这种反应约在24小时以后结束,然后才能用常规方法检查氧化层的质量。
4、用热水对上述处理层作5-10分钟的后冲洗, 就可以缩短这种反应时间, 经冲洗后处理层可以立即作质量的检验。
阳极氧化原理知识讲稿

3、电压: A、电压高,氧化膜生长速度提高,孔隙增 多,易染色,硬度和耐磨性提高。 B、电压低,生成氧化膜的速度慢,膜层 较致密。 4、氧化时间: 根据硫酸浓度,溶液温度、电压,膜厚而
定,其它条件不变,时间越长,膜厚越厚, 但达到一定厚度时,膜厚将不会增加(即 膜的溶解速度与生长速度相等)。
5、杂质离子影响: 可能存在的杂质离子:CLˉ、F ˉ、NO3
(二)工艺参数及操作条件:
HAL2S3O+:4:3-1105%g/-L20% 160-200g/L 温度:视具体情况而定 15℃-26℃ 电压:视具体情况而定
6V、8V、10V、13V、15V、17V 时间:视具体情况而定 10分-50分 搅拌:压缩空气搅拌
电源:直流电/交流电
注意事项: 1、硫酸电解液的配制; A.根据槽体的容积和硫酸浓度计算所需硫酸量 B.在槽内加3/4体积纯水,并打风搅拌; C.将硫酸缓缓加入槽内,并补充纯水至规定体
2.壁垒型膜逐渐成长。当电流密度低于临界值时,
铝离子不能再形成新膜物质,膜的表面暴露在电 解液中受到浸蚀;
3.进一步阳极氧化,溶液对膜的浸蚀变得不均匀; 4.形成的空洞之间存在发展竞争。这种发展有“自
催化”作用;
5.发展较快的空洞(主空洞)在向膜深处和横向发展 6.主空洞继续沿纵向和横向发展,相邻主空洞之间
①冷冻机中的致冷剂与安装在氧化槽内的蛇形管连通直接冷却;
②用蛇形管间接冷却装置,即冷冻机冷却冷水池中的水,再用水泵 将冷水打入氧化槽中蛇形管内冷却槽液;
③冷冻机中的致冷剂借助热交换器冷却槽液循环系统中的槽液;
④用槽液循环系统间接冷却装置,即冷冻机冷却冷水池中的水,再 用冷水借助热交换器冷却槽液循环系统中的槽液.
阳极氧化表面处理工艺介绍
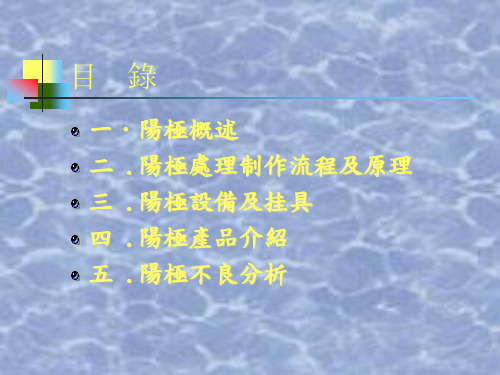
2>4 前處理
A.脫脂:除去沖壓/拋光等工段殘余的油脂
皂化:脫脂液中的鹼與工件表面的油脂反應,生成水溶性的肥皂與甘油
(C17H35COO)3C3H5+3NaOH 硬脂酸酯 鹼
3C17H15COONa+C3H5(OH)3
變形
內部髒污
造成單位 原材料 沖壓 焊接
拋光
拋光
不良原因
改善對策
來料不良 衝壓前模具上有小顆粒硬物, 衝 壓時壓在工件上
鐳射焊接能量過高
1.衝壓後打磨手法不正確, 壓力 過大 2.機 拋 時 手 法 不 正 確
1.提 高 機 拋 切 削 力 2.延 長 化 拋 時 間
衝壓前清除乾淨模具上小顆粒
1.鐳 射 焊 接 能 量 應 調 適 當 2.延 長 化 拋 時 間 3.提 高 鹼 咬 濃 度 ,延 長 鹼 咬 時 間 1.衝 壓 後 打 磨 手 法 正 確 ,壓 力 適 當 2.機 拋 用 手 壓 力 部 位 ,手 法 正 確
染色前處理原理圖 表面活性物質
氧化膜層
2>9 染 色
即將染料分子填充至Al2O3孔隙的過程,染料大致 上可分為有機與無機兩種,一般陽極用染料為有機性, 例煤碳綠所需的706,804兩種染料,結構如下:
染色原理圖
染料
氧化膜層
2>10 封 孔
Al2O3孔隙填充過染料后,如不加以處 理,放置一段時間后,孔隙中的染料會逐漸 析出或變色,為避免此現象發生, 染色后必 須將Al2O3孔隙加以封閉,即為[封孔](seal).
•氧化膜為雙層結構,內層為致密無孔的且少水的Al2O3 構成 ,稱為陰擋層,外層是由孔隙和孔壁組成的多孔 層,氧化膜壁與水反應,同時由于化學結合式吸附電解 陰离子,所以氧化膜的總組成為Al2O3 .Al(OH).(SO4)2.
阳极氧化常见问题分析

铝的阳极氧化是以铝或铝合金作阳极,以铅板作阴极在硫酸、草酸、铬酸等水溶液中电解,使其表面生成氧化膜层。
其中硫酸阳极氧化处理应用最为广泛。
铝和铝合金硫酸阳极氧化氧化膜层有较高的吸附能力,易进行封孔或着色处理,更加提高其抗蚀性和外观。
阳极氧化膜层厚一般3~15μm,铝合金硫酸阳极氧化工艺操作简单,电解液稳定,成本也不高,是成熟的工艺方法,但在硫酸阳极化过程中往往免不了发生各种故障,影响氧化膜层质量。
认真总结分析故障产生的原因并采取有效预防措施,对提高铝合金硫酸阳极氧化质量有重要的现实意义。
1常见故障及分析(1)铝合金制品经硫酸阳极氧化处理后,发生局部无氧化膜,呈现肉眼可见的黑斑或条纹,氧化膜有鼓瘤或孔穴现象。
此类故障虽不多见但也有发生。
上述故障原因,一般与铝和铝合金的成分、组织及相的均匀性等有关,或者与电解液中所溶解的某些金属离子或悬浮杂质等有关。
铝和铝合金的化学成分、组织和金属相的均匀性会影响氧化膜的生成和性能。
纯铝或铝镁合金的氧化膜容易生成,膜的质量也较佳。
而铝硅合金或含铜量较高的铝合金,氧化膜则较难生成,且生成的膜发暗、发灰,光泽性不好。
如果表面产生金属相的不均匀、组织偏析、微杂质偏析或者热处理不当所造成各部分组织不均匀等,则易产生选择性氧化或选择性溶解。
若铝合金中局部硅含量偏析,则往往造成局部无氧化膜或呈黑斑点条纹或局部选择性溶解产生空穴等。
另外,如果电解液中有悬浮杂质、尘埃或铜铁等金属杂质离子含量过高,往往会使氧化膜出现黑斑点或黑条纹,影响氧化膜的抗蚀防护性能。
ﻫ(2)同槽处理的阳极氧化零件,有的无氧化膜或膜层轻薄或不完整,有的在夹具和零件接触处有烧损熔蚀现象。
这类故障在流酸阳极氧化工艺实践中往往较多发生,严重影响铝合金阳极氧化质量。
由于铝氧化膜的绝缘性较好,所以铝合金制件在阳极氧化处理前必须牢固地装挂在通用或专用夹具上,以保证良好的导电性。
导电棒应选用铜或铜合金材料并要保证足够接触面积。
阳极氧化不良原因分析
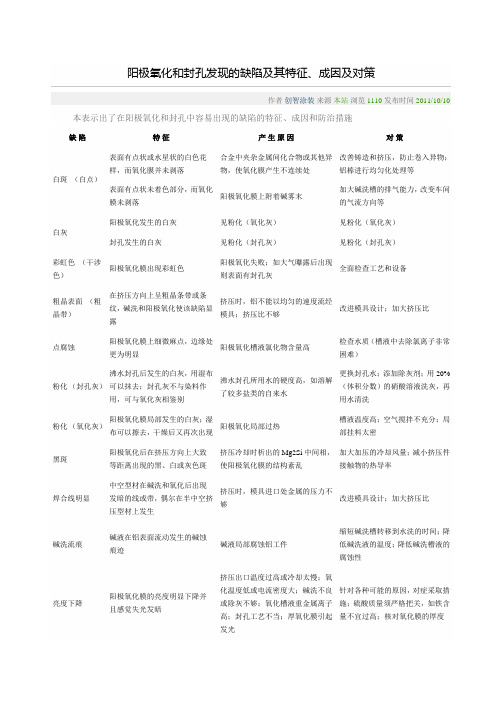
作者创智涂装来源本站浏览1110 发布时间2011/10/10本表示出了在阳极氧化和封孔中容易出现的缺陷的特征、成因和防治措施铝材阳极氧化封孔,不挂灰时间短.•信息名称:铝材阳极氧化封孔,不挂灰时间短.所在地:山东省威海市发布时间:2011-07-08加入收藏夹联系人:郭小姐0631-5755316威海云清化工开发院联系人:郭小姐女士电话:86-0631-5755316手机:137********传真:86-0631-5753425邮件:g xying123@地址:山东省威海市文化中路89-2号查看全部产品进入展厅一、产品用途:本品为浅绿色粉末,适用于建筑铝型材和其他铝制品的封孔处理,本品封孔温度范围宽,它能够改善表面装饰的无色金属络合物, 在其它物质的支持下,依靠镍和氟化物离子的协同效应,发挥作用。
二、性能特点:1、同热水封孔的工艺相比, 冷封孔能缩短处理时间和节约加热所需的能源, 从能源成本和阳极氧化物生产线能力的角度来考虑这种优点就相当重要。
2、这种产品的结合能防止干净阳极氧化铝部件发绿的退色现象。
不产生白霜,其耐蚀性和耐磨性及硬度均高于沸水封孔处理.三、槽液组成及工艺条件:本品浓度 3.5-5.0克/升去离子水余量PH值5-5.6温度25-35℃时间8-15分钟(一分钟能封一个微米厚的氧化膜)Ni+ 0.9-1.2克/升F- 0.3-0.85克/升消耗量:0.8-1.5千克/吨材(约400m2)* 封孔后第一道用冷水洗,然后在进行温水洗.温水槽温度:60℃;时间:5分钟四、注意事项1、槽材料: 衬有塑料的钢或不锈钢。
特别须知要点:建议对溶液作过滤处理, (不可用筒式过滤器)。
为了保证溶液能长期使用, 避免溶液被全部排放, 每立方米中物料通过量达到1000m2,就应排放50 L/m3的槽液.2、用量: 产品用量和被处理氧化层的厚度和生产率有关。
3、阳极氧化层的质量:通过用封孔液的处理, 氧化层会产生一种反应, 这种反应约在24小时以后结束,然后才能用常规方法检查氧化层的质量。
表面处理-阳极氧化处理分析

2>3鋁陽極氧化的機理(2)
•氧化膜的生長是增長和溶解這對矛盾動作中發生和 發展的,通電的瞬間,由于氧和鋁的有很強的絕緣電 阻由于氧化鋁體積比鋁離子體積大發生膨脹,陰擋 層變得凹凸不平,這就造成電流分佈不均勻,凹處電 陰較小而電流大,凸處相反,是電流密度高的凹處在 電場作用下發生氧化膜的電化學溶解,以及硫酸浸 蝕產生化學溶解,凹處加深漸變成孔穴,繼而形成多 孔的氧化膜. •具有很多高孔隙率和吸附的氧膜,可吸附染料,經過 封閉之后,便形成色彩較佳的裝飾性膜層.
機拋手法不正確 , 治具保護不全 , 機拋手法應正確 , 修復治具 , 自拋機調節位置 自拋機調節位置不當 適當 機拋手拿工件不正確 , 方向不正 確 人為產生 1. 化拋過腐蝕 2. 氧化槽導電不良 3. 氧化槽中有金屬離子 1. 脫脂不完全 2. 重工件退除不徹底 機拋手拿工件正確 , 方向正確 上下料人員手法伏化 1. 提高 CPBRI-20濃度 , 硝酸濃度適當 2. 工件與掛具應接觸良好 3. 定期清除陰極沉積物 , 一周兩次 1. 長脫脂時間 , 脫脂濃度 , 溫度采用上限增加 2. 重工件退除應徹底
多孔層
A
B C
阻擋層 鋁基件
2>7鋁陽極氧化膜生成曲線
24 22 20
8 4
A.膜層生長 B.陰擋層形成 C.膜層穩定生成, 直到溶解與生長速 率達到平衡
20 30 40 50 60
電壓/V
時間/s
2>8 染色前處理
Al2O3膜生成后,並不宜立刻染色,因為Al2O3
為無機物質,而染料為有機物質,兩者之間結合不
2>4 前處理
A.脫脂:除去沖壓/拋光等工段殘余的油脂 皂化:脫脂液中的鹼與工件表面的油脂反應,生成水溶性的肥皂與甘油 (C17H35COO)3C3H5+3NaOH 3C17H15COONa+C3H5(OH)3 硬脂酸酯 鹼 肥皂 甘油 乳化:除去工件表面無法皂化的油與腊 B.鹼咬: B-1.除去工件表面原有之Al2O3不導電層 先進行: Al2O3 +OH2Al3++含Al+其它 后進行: Al+NaOH NaAlO2+H2+其它 B-2. 調節工件表面的亮啞度(鹼咬=鹼腐蝕,破壞工件表面平整性, 造成光線散(漫)射,影響外觀 C.剝黑膜:去除工件表面黑色水膜,主要成份為HNO3.(室溫操作)
铝及铝合金硫酸阳极氧化常见故障的原因及排除措施

铝及铝合金硫酸阳极氧化常见故障的原因及排除措施铝及铝合金硫酸阳极氧化常见故障的原因及排除措施1. 引言铝及其合金广泛应用于各个领域,包括建筑、汽车、航空航天以及电子等行业。
为了增强其耐腐蚀性和提高外观,常常会对铝材进行硫酸阳极氧化处理。
然而,这种过程中可能会出现一些常见故障,影响其表面质量和性能。
本文将深入探讨铝及铝合金硫酸阳极氧化常见故障的原因及排除措施,以帮助读者更好地理解和解决这些问题。
2. 铝及铝合金硫酸阳极氧化常见故障2.1 腐蚀腐蚀是铝及铝合金硫酸阳极氧化常见的问题之一。
这可能是由于阳极氧化处理中的规范不当导致的,例如处理时间过长或温度过高。
可能存在原材料质量问题,如含有过多的杂质或不纯的硫酸,导致更易腐蚀的氧化层形成。
排除措施:正确控制氧化处理参数,如时间和温度,以确保处理的一致性。
应定期检查硫酸的质量,并确保其纯度。
如果发现腐蚀问题,可以考虑增加氧化电压和降低氟离子浓度,以增加氧化层的密度和耐蚀性。
2.2 颜色不均匀铝及铝合金硫酸阳极氧化处理过程中出现的颜色不均匀也是一个普遍存在的故障。
这可能由于电解液中存在浓度梯度或流速不均匀导致的。
铝材基体的合金成分也可能会影响颜色的均匀性。
排除措施:确保电解液的浓度均匀,可以通过搅拌电解液或增加搅拌装置来实现。
另外,调整电流密度和处理时间,以平衡铝材表面的氧化反应速率,从而避免颜色不均匀问题的发生。
2.3 孔洞和气泡在铝及铝合金硫酸阳极氧化过程中,孔洞和气泡也经常出现。
这可能是由于工艺参数设置错误,如电流密度或处理时间过高,导致氧化层无法均匀形成。
排除措施:调整工艺参数,以确保电流密度适中,并根据铝材的形状和尺寸合理设定处理时间。
使用合适的搅拌设备可以提高电解液的流动性,从而减少气泡和孔洞的产生。
3. 其他问题与个人观点除了上述常见故障,铝及铝合金硫酸阳极氧化过程中可能还会遇到其他问题。
电解槽污染、表面纹理不佳以及氧化层附着力不强等。
针对这些问题,应该结合具体情况进行分析和解决。
阳极氧化原理全解(课堂PPT)

2020/7/12
12
(二)工艺参数及操作条件:
AHL2S3O+:4:3-1105%g/-L20% 160-200g/L 温度:视具体情况而定 15℃-26℃ 电压:视具体情况而定
6V、8V、10V、13V、15V、17V 时间:视具体情况而定 10分-50分 搅拌:压缩空气搅拌
①氧化膜结构的多孔性; ②氧化膜的耐磨性; ③氧化膜的抗蚀性;
④氧化膜的电绝缘性;
⑤氧化膜的绝热性;
⑥氧化膜的结合力;
⑦氧化膜的硬度高;
⑧氧化膜的装饰性。
2020/7/12
5
C、阳极氧化分类: ①硫酸阳极氧化;
②草酸阳极氧化;
③铬酸阳极氧化;
④磷酸阳极氧化;
⑤瓷质阳极氧化;
⑥硬质阳极氧化; ⑦微弧阳极氧化。
利用10%-15%的H2SO4。
2020/7/12
17Leabharlann 2、温度:一般情况下,电解液温度控制比较严格, 有的需用保持在±1℃范围内,溶液温度高, 氧化膜溶解速度大,生成的速度减小,生
成的膜疏松。若温度过低,氧化膜发脆易 裂。当控制温度在18-22℃时,得到的氧化 膜多孔,吸附性强,富有弹性,抗蚀性好, 但耐磨性较差;
催化”作用;
5.发展较快的空洞(主空洞)在向膜深处和横向发展 6.主空洞继续沿纵向和横向发展,相邻主空洞之间
互相靠近,主空洞之间的小空洞停止生长;
7.空洞停止横向发展,仅沿纵向深入,孔径固定。
此时,空洞的产生及发展阶段结束,阳极氧化进
入稳态阶段。
2020/7/12
11
阳极氧化常见故障分析

证足够接触面积 .夹具与零件接触处 , 既要保证电流自由通过 , 又要尽可能减少夹
具和零件间的接触面积过小 ,电流密度太大 ,会产生过热易烧损零件和夹具 .无氧 化膜或膜层不完整等现象,主要是由于夹具和制件接触不好,导电不良或者是由于 夹具上氧化膜层未彻底清除所致.
(3)铝合金硫酸阳极氧化处理后 ,氧化膜呈疏松粉化甚至手一摸就掉 ,特别是
用耐酸泵抽入硫酸脱脂槽内二次利用。降低氧化槽内 的铝含量也可用硫酸回收设备。
B、槽液液面上的漂浮物和油 污应及时清除,脱落在槽 液中的铝工件和杂物应及 时捞起。
C、氧化槽液沉淀物较少,一般只需一年倒槽清底一 次,
此时应刷洗或更换阴极板。
(三)氧化膜的影响因素:
1.硫酸浓度 当其他条件不变时,提高硫酸浓度,氧化膜的生长速度减慢,这 是由于生长中的氧化膜在较浓的硫酸溶液中溶解速度加快的结果。 若硫酸浓度太低,导电性下降,其氧化时间就要延长;硫酸的浓 度升高,有利於多孔膜的生成,该膜的弹性好,吸附力强;易获 得防护装饰性氧化膜,硫酸浓度多利用上限,即20%的H2SO4,
量超出15g/L时,氧化膜会出现不规则现象,且皮膜色泽发黄,
膜层性能下降。因此,为了染色色泽均匀, Al3+含量必须控制 在5~12g/L之间。
7、电流密度: 电流密度越大,膜较硬,耐磨性好,但电流 密度过高,则会因焦耳热影响,使膜层溶解作用增 加,电流密度过高,膜层氧化时间过长,膜疏松, 硬度降低,对于需染色或电解着色的氧化膜,电流
注:铝的阳极氧化是以铝或铝合金作阳极,以铅板作阴极在硫酸、草 酸、铬酸等水溶液中电解,使其表面生成氧化膜层。其中硫酸阳 极氧化处理应用最为广泛。铝和铝合金硫酸阳极氧化氧化膜层有 较高的吸附能力,易进行封孔或着色处理,更加提高其抗蚀性和 外观。阳极氧化膜层一般3-15um,铝合金硫酸阳极氧化工艺操作
阳极氧化原理全解

(4)偶然发生铝合金硫酸阳极氧化后氧化膜暗淡无 光,有时产生点状腐蚀,严重时黑色点状腐蚀显著, 导致零件报废,引起较大损失.
这类故障往往是偶然发生并有特殊原因造成的.在 铝合金阳极氧化过程中,中途断电又重新给电,往 往会使氧化膜暗淡无光,而中途停电零件在清洗 槽停留过久,清洗水槽酸度过高,水质不净,含悬浮 物、泥砂等较多,往往会使铝合金制件发生电化 学腐蚀,发生点状腐蚀黑斑等。有时向电解液中 添加自来水,水经漂白粉处理且Cl-含量超标或有 时盛装过HCl的容器未经彻底清洗又盛装硫酸, 都会使阳极氧化电解液中混入超量的Cl-,从而导 致铝合金零件阳极氧化产生点状腐蚀使产品报废 等。
B、槽液液面上的漂浮物和油污应及时清除, 脱落在槽液中的铝工件和杂物应及时捞起。
C、氧化槽液沉淀物较少,一般只需一年倒 槽清底一 次,此时应刷洗或更换阴极板。
(三)氧化膜的影响因素:
• ①硫酸浓度: 当其他条件不变时,提高硫酸浓度,氧化膜的生长速度 减慢,这是由于生长中的氧化膜在较浓的硫酸溶液中溶 解速度加快的结果。若硫酸浓度太低,导电性下降,其 氧化时间就要延长;硫酸的浓度升高,有利於多孔膜的 生成,该膜的弹性好,吸附力强;易获得防护装饰性氧 化膜,硫酸浓度多利用上限,即20%的H2SO4,为了获 得硬而厚的耐磨氧化膜,应选用较稀的硫酸溶液,通常
(五)预防故障的措施
铝合金硫酸阳极氧化膜质量好坏,抗蚀防护性能的优劣主要取 决于铝合金的成分,膜层厚度以及阳极氧化处理工艺条件,如温 度、电流密度、使用水质及阳极氧化后的填充封闭工艺等。 要减少或避免阳极氧化故障提高产品质量要从微细处着手, 采取有效措施。
7、电流密度: 电流密度越大,膜较硬,耐磨性好,但电
流密度过高,则会因焦耳热影响,使膜层溶
阳极氧化工艺原理

2、温度: 一般情况下,电解液温度控制比较严格, 有的需用保持在±1℃范围内,溶液温 度高,氧化膜溶解速度大,生成的速度 减小,生成的膜疏松。若温度过低,氧 化膜发脆易裂。当控制温度 在18-22℃时,得到的氧化膜多孔,吸 附性强,富有弹性,抗蚀性好,但耐磨 性较差;
槽液温度是阳极氧化一个重要工艺参数,为确保 氧化膜的质量和性能要求恒定,一般需严格控制 在选定温度±(1~2)℃范围内,控制和冷却槽液 温度有下列四种方法: ①冷冻机中的致冷剂与安装在氧化槽内的蛇形管 连通直接冷却; ②用蛇形管间接冷却装置,即冷冻机冷却冷水池中 的水,再用水泵将冷水打入氧化槽中蛇形管内冷 却槽液; ③冷冻机中的致冷剂借助热交换器冷却槽液循环 系统中的槽液; ④用槽液循环系统间接冷却装置,即冷冻机冷却冷 水池中的水,再用冷水借助热交换器冷却槽液循 环系统中的槽液.
B、槽液液面上的漂浮物和油 污应及时清除,脱落在槽 液中的铝工件和杂物应及 时捞起。 C、氧化槽液沉淀物较少,一 般只需一年倒槽清底一 次, 此时应刷洗或更换阴极板。
(三)氧化膜的影响因素:
①硫酸浓度:
当其他条件不变时,提高硫酸浓度,氧化膜的 生长速度减慢,这是由于生长中的氧化膜在较 浓的硫酸溶液中溶解速度加快的结果。若硫酸 浓度太低,导电性下降,其氧化时间就要延长; 硫酸的浓度升高,有利於多孔膜的生成,该膜 的弹性好,吸附力强;易获得防护装饰性氧化 膜,硫酸浓度多利用上限,即20%的H2SO4, 为了获得硬而厚的耐磨氧化膜,应选用较稀的 硫酸溶液,通常利用10%-15%的H2SO4。
2
同上
稀释或更换 槽液
合金铝 Si 悬 中的Si溶 浮于电 解进入电 解液中 解液
2+
使电解变得浑 浊,并常常以粉状 吸附在工件上
阳极氧化缺陷及处理方式

阳极氧化缺陷及处理方式(实用版)编制人:__________________审核人:__________________审批人:__________________编制单位:__________________编制时间:____年____月____日序言下载提示:该文档是本店铺精心编制而成的,希望大家下载后,能够帮助大家解决实际问题。
文档下载后可定制修改,请根据实际需要进行调整和使用,谢谢!并且,本店铺为大家提供各种类型的实用资料,如教育随笔、日记赏析、句子摘抄、古诗大全、经典美文、话题作文、工作总结、词语解析、文案摘录、其他资料等等,想了解不同资料格式和写法,敬请关注!Download tips: This document is carefully compiled by this editor. I hope that after you download it, it can help yousolve practical problems. The document can be customized and modified after downloading, please adjust and use it according to actual needs, thank you!In addition, this shop provides you with various types of practical materials, such as educational essays, diary appreciation, sentence excerpts, ancient poems, classicarticles, topic composition, work summary, word parsing, copy excerpts, other materials and so on, want to know different data formats and writing methods, please pay attention!阳极氧化是一种常用的表面处理技术,可以提高金属表面的耐蚀性、耐磨性和美观性。
阳极氧化工艺原理与常见故障分析

C、阳极氧化分类: ①硫酸阳极氧化; ②草酸阳极氧化; ③铬酸阳极氧化; ④磷酸阳极氧化; ⑤瓷质阳极氧化; ⑥硬质阳极氧化; ⑦微弧阳极氧化。
D、阳极氧化机理
1、电极反应:
阳极:H2O—2E→2H++[O] 2AL+3[3O] →AL2O3+1670.5J 阴极: 2H++2E →H2↑
膜的溶解:
酸阳极氧化槽,往往处理1-2槽零件后,疏松粉化现 象就会出现,明显地影响氧化膜的质量. 由于铝合金阳极氧化膜电阻很大,在阳极氧化工艺 过程中会产生大量焦耳热,槽电压越高产生热量越 大,从而导致电解液温度不断上升.所以在阳极氧化 过程中,必须采用搅拌或冷却装置使电解液温度保 持在一定范围.一般情况下,温度应控制在1524℃,氧化膜质量较佳.若电解液温度超过30 ℃, 氧化膜会产生疏松粉化,膜层质量低劣,严重时发生 “烧焦”现象。另外,当电解液温度恒定时,阳 极电流密度也必须予以限制,因为阳极电流密度 过高,温升剧烈,氧化膜也易疏松呈粉状或砂粒 状,对氧化膜质量十分不利。
2
同上
稀释或更换 槽液
合金铝 Si 悬 中的Si溶 浮于电 解进入电 解液中 解液
2+
使电解变得浑 浊,并常常以粉状 吸附在工件上
过滤排除
3+含量: 6、Al
电解液中Al3+含量控制在0.5~5g/L时, 有助于氧化膜的抗蚀性和耐磨性, Al3+ 含量在5g/L以下时,膜层对染色吸附 3+含量在5~15g/L时,氧 能力下降, Al 3+含量 化膜吸附能力基本保持稳定,Al 超出15g/L时,氧化膜会出现不规则现 象,且皮膜色泽发黄,膜层性能下降。 因此,为了染色色泽均匀, Al3+含量 必须控制在5~12g/L之间。
阳极氧化故障与分析
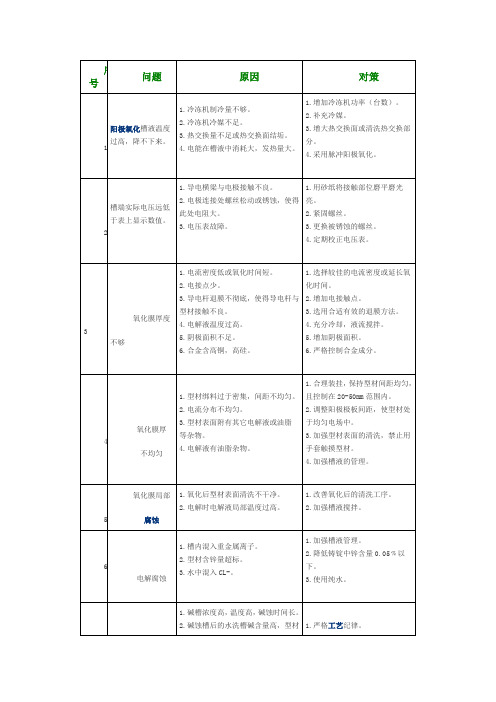
问题
原因
对策
1
阳极氧化槽液温度过高,降不下来。
1.冷冻机制冷量不够。
2.冷冻机冷媒不足。
3.热交换量不足或热交换面结垢。
4.电能在槽液中消耗大,发热量大。
1.增加冷冻机功率(台数)。
2.补充冷媒。
3.增大热交换面或清洗热交换部分。
4.采用脉冲阳极氧化。
2
槽端实际电压远低于表上显示数值。
1.导电横梁与电极接触不良。
1.选择较佳的电流密度或延长氧化时间。
2.增加电接触点。
3.选用合适有效的退膜方法。
4.充分冷却,液流搅拌。
5.增加阴极面积。
6.严格控制合金成分。
4
氧化膜厚
不均匀
1.型材绑料过于密集,间距不均匀。
2.电流分布不均匀。
3.型材表面附有其它电解液或油脂等杂物。
4.电解液有油脂杂物。
1.合理装挂,保持型材间距均匀,且控制在20-50mm范围内。
氧化膜
耐蚀性不够
1.合金成分影响(如Si,Fe高)。
2.电解液浓度高。
3.电解时间长。
1.改善合金成份。
2.控制浓度在规定值。
3.提高电流密度,缩短时间。
13
型材表面
起灰、粉化
1.封孔液被污染,PH过高。
2.电解液温度高,浓度高,溶AL3+量高,电流密度高,处理时间长。
1.更改封孔液。
2.遵守工艺规程。
14
黑斑点
1.硝酸中和不足。
2.挤压型材冷却不均不充分,导致粗大的Mg2Si析出沉淀。
1.提高硝酸浓度或延长中和时间。
2.提高挤压淬水,冷却风扇的能力。
15
电击烧伤
阳极氧化退膜 -回复
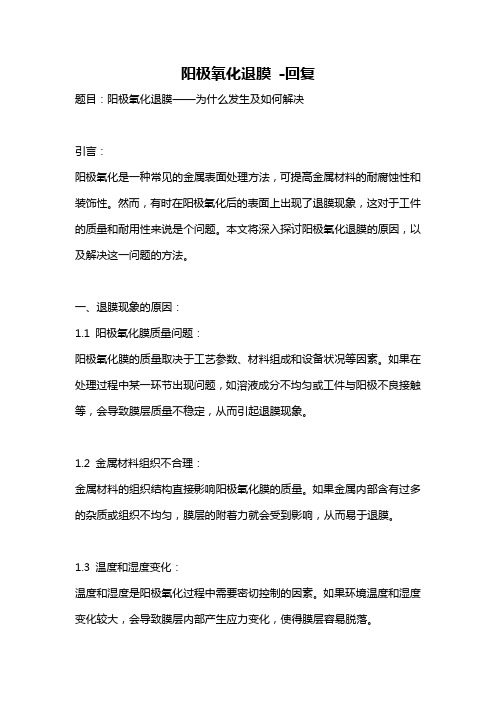
阳极氧化退膜-回复题目:阳极氧化退膜——为什么发生及如何解决引言:阳极氧化是一种常见的金属表面处理方法,可提高金属材料的耐腐蚀性和装饰性。
然而,有时在阳极氧化后的表面上出现了退膜现象,这对于工件的质量和耐用性来说是个问题。
本文将深入探讨阳极氧化退膜的原因,以及解决这一问题的方法。
一、退膜现象的原因:1.1 阳极氧化膜质量问题:阳极氧化膜的质量取决于工艺参数、材料组成和设备状况等因素。
如果在处理过程中某一环节出现问题,如溶液成分不均匀或工件与阳极不良接触等,会导致膜层质量不稳定,从而引起退膜现象。
1.2 金属材料组织不合理:金属材料的组织结构直接影响阳极氧化膜的质量。
如果金属内部含有过多的杂质或组织不均匀,膜层的附着力就会受到影响,从而易于退膜。
1.3 温度和湿度变化:温度和湿度是阳极氧化过程中需要密切控制的因素。
如果环境温度和湿度变化较大,会导致膜层内部产生应力变化,使得膜层容易脱落。
二、解决退膜现象的方法:2.1 优化工艺参数:通过调整阳极氧化过程中的工艺参数,如电压、电流密度、溶液浓度和处理时间等,可以改善膜层的质量。
严格控制每个步骤的操作要求,确保全过程的稳定性和一致性。
2.2 提升金属材料的纯度:通过优化金属材料的生产工艺,减少杂质的含量,并控制金属的组织结构,可以提高阳极氧化膜的附着力和稳定性。
合理选择原材料,并对金属材料进行预处理,以确保其质量达到要求。
2.3 控制处理环境的温湿度:在阳极氧化过程中,严格控制处理环境的温度和湿度变化,避免因环境变化而导致膜层受力变化进而退膜。
可以通过使用恒温恒湿的设备,或者采取湿度和温度自动调节系统进行控制。
2.4 加强膜层之间的亲和力:在阳极氧化处理后,可以通过进行化学处理或热处理等方法,增强膜层与基材之间的结合力。
这些处理方法能够促使膜层与基材之间形成更牢固的化学键,增加膜层的附着力。
2.5 检测和质量控制:建立一套完善的质量检测体系,对阳极氧化处理后的产品进行检测,及时发现退膜等质量问题。
阳极氧化法原理

阳极氧化法原理
阳极氧化法是一种常用的材料表面处理方法,它通过在电解液中通电,使金属材料在阳极处生成氧化物层来改变材料的表面性质。
在阳极氧化过程中,在阳极处通电,电流导致金属材料电子流动,从而在表面形成氧化层。
这个过程可以用如下的反应方程来表示:
M + O2 + 2H2O + 2e--> MO + 2OH-
其中,M表示金属材料,O2表示氧气,H2O表示水,e-表示电子。
MO表示金属氧化物,OH-表示氢氧化离子。
阳极氧化法可以改变金属材料表面的性质,如提高抗腐蚀性、改变表面颜色、改变表面硬度和摩擦系数等。
但是,阳极氧化法也有一些局限,如对于一些轻质金属材料,氧化层较薄,不够稳定,可能会在使用过程中脱落。
另外,阳极氧化法的加工效率较低,不适用于大批量生产。
铝单板表面处理工艺

铝单板表面处理工艺铝单板是一种广泛应用于建筑外墙装饰的材料,其表面处理工艺是非常重要的环节。
表面处理不仅能够美化铝单板的外观,还能提高其耐腐蚀性和耐磨性,延长材料的使用寿命。
本文将介绍铝单板表面处理的几种常见工艺。
一、阳极氧化工艺阳极氧化是一种常见的铝单板表面处理工艺,其原理是在铝单板表面形成一层厚度约10微米的氧化铝膜。
这种氧化铝膜不仅能够增强铝单板表面的硬度和耐腐蚀性,还能够增加其表面的附着力,使得后续的喷涂、印刷等工艺更加稳定。
阳极氧化工艺的优点是处理后的铝单板表面均匀光滑,色泽鲜艳,具有很好的装饰效果。
二、电泳涂装工艺电泳涂装是一种以电解液为介质,在铝单板表面形成一层均匀涂层的工艺。
其原理是利用电解作用将涂料引入铝单板表面的微小孔洞中,形成一层均匀、致密的涂层。
电泳涂装工艺的优点是处理后的铝单板表面涂层均匀、厚度可控,附着力强,耐腐蚀性好,具有很好的装饰效果。
此外,电泳涂装工艺还具有环保、节能等优点,因此在现代建筑装修中得到了广泛应用。
三、喷涂工艺喷涂工艺是一种常见的铝单板表面处理工艺,其原理是在铝单板表面喷涂一层涂料。
喷涂工艺的优点是处理速度较快、成本较低,且可以根据需要调整涂层的厚度和颜色。
但是,喷涂工艺的缺点是涂层厚度不易控制,附着力较弱,耐腐蚀性较差,且需要使用有机溶剂等化学物质,对环境造成一定的污染。
四、粉末喷涂工艺粉末喷涂是一种新型的铝单板表面处理工艺,其原理是将粉末涂料喷洒在铝单板表面,然后在高温环境下进行固化。
粉末喷涂工艺的优点是涂层厚度均匀、附着力强、耐腐蚀性好,且可以根据需要调整涂层的厚度和颜色,具有很好的装饰效果。
此外,粉末喷涂工艺还具有环保、节能等优点,因此在现代建筑装修中得到了越来越广泛的应用。
铝单板表面处理工艺是影响铝单板质量和使用寿命的重要环节。
不同的表面处理工艺有着各自的优缺点,建筑装修设计者可以根据项目需求和预算等因素进行选择。
在实际应用中,还应注意表面处理工艺的操作规范、材料质量等问题,以确保处理后的铝单板具有优良的性能和装饰效果。
- 1、下载文档前请自行甄别文档内容的完整性,平台不提供额外的编辑、内容补充、找答案等附加服务。
- 2、"仅部分预览"的文档,不可在线预览部分如存在完整性等问题,可反馈申请退款(可完整预览的文档不适用该条件!)。
- 3、如文档侵犯您的权益,请联系客服反馈,我们会尽快为您处理(人工客服工作时间:9:00-18:30)。
如果表面产生金属相的不均匀、组织偏析、微杂 质偏析或者热处理不当所造成各部分组织不均 匀等,则易产生选择性氧化或选择性溶解。若 铝合金中局部硅含量偏析,则往往造成局部无 氧化膜或呈黑斑点条纹或局部选择性溶解产生 空穴等。另外,如果电解液中有悬浮杂质、尘 埃或铜铁等金属杂质离子含量过高,往往会使 氧化膜出现黑斑点或黑条纹,影响氧化膜的抗 蚀防护性能。
2、电化学氧化: A.定义: 将铝及其合金置于某种适当 的电解液中作为阳极,在外电 流作用下,使其表面生成氧化 膜的过程称为阳极氧化,又称 电化学氧化。
B、阳极氧化膜的性质(与化学氧化膜 相比): ①氧化膜结构的多孔性; ②氧化膜的耐磨性; ③氧化膜的抗蚀性; ④氧化膜的电绝缘性; ⑤氧化膜的绝热性; ⑥氧化膜的结合力; ⑦氧化膜的硬度高; ⑧氧化膜的装饰性。
AL2O3+3H2SO4=AL2(SO4)3+3H2O
E、H2SO4物理性质: ①98.3%的浓H2SO4,是无色粘稠状 液体,沸点338度,是一种难挥发性的酸 ②化学性质: a.强酸性; b.易与活泼金属反应; c.浓H2SO4具有吸水性,结合水后放 出大量的热,常温下, 浓H2SO4遇铁、 铝合金发生钝化。
2、温度: 一般情况下,电解液温度控制比较严格, 有的需用保持在±1℃范围内,溶液温 度高,氧化膜溶解速度大,生成的速度 减小,生成的膜疏松。若温度过低,氧 化膜发脆易裂。当控制温度 在18-22℃时,得到的氧化膜多孔,吸 附性强,富有弹性,抗蚀性好,但耐磨 性较差;
槽液温度是阳极氧化一个重要工艺参数,为确保 氧化膜的质量和性能要求恒定,一般需严格控制 在选定温度±(1~2)℃范围内,控制和冷却槽液 温度有下列四种方法: ①冷冻机中的致冷剂与安装在氧化槽内的蛇形管 连通直接冷却; ②用蛇形管间接冷却装置,即冷冻机冷却冷水池中 的水,再用水泵将冷水打入氧化槽中蛇形管内冷 却槽液; ③冷冻机中的致冷剂借助热交换器冷却槽液循环 系统中的槽液; ④用槽液循环系统间接冷却装置,即冷冻机冷却冷 水池中的水,再用冷水借助热交换器冷却槽液循 环系统中的槽液.
酸阳极氧化槽,往往处理1-2槽零件后,疏松粉化现 象就会出现,明显地影响氧化膜的质量. 由于铝合金阳极氧化膜电阻很大,在阳极氧化工艺 过程中会产生大量焦耳热,槽电压越高产生热量越 大,从而导致电解液温度不断上升.所以在阳极氧化 过程中,必须采用搅拌或冷却装置使电解液温度保 持在一定范围.一般情况下,温度应控制在1524℃,氧化膜质量较佳.若电解液温度超过30 ℃, 氧化膜会产生疏松粉化,膜层质量低劣,严重时发生 “烧焦”现象。另外,当电解液温度恒定时,阳 极电流密度也必须予以限制,因为阳极电流密度 过高,温升剧烈,氧化膜也易疏松呈粉状或砂粒 状,对氧化膜质量十分不利。
H2SO4:10%-20% 160-200g/L
时间:视具体情况而定 10分-50分 搅拌:压缩空气搅拌 电源:直流电/交流电
注意事项:
1、硫酸电解液的配制; A.根据槽体的容积和硫酸浓度计算所需硫酸量 B.在槽内加3/4体积纯水,并打风搅拌; C.将硫酸缓缓加入槽内,并补充纯水至规定体 积(注意切勿将水加入硫酸中) D.冷却至工艺条件温度; E.化验室取样分析,OK后即可投入生产 2、硫酸的纯度要求: 最好用试剂,我们通常用CP(化学纯) 硫酸。
B、槽液液面上的漂浮物和油 污应及时清除,脱落在槽 液中的铝工件和杂物应及 时捞起。 C、氧化槽液沉淀物较少,一 般只需一年倒槽清底一 次, 此时应刷洗或更换阴极板。
(三)氧化膜的影响因素:
①硫酸浓度:
当其他条件不变时,提高硫酸浓度,氧化膜的 生长速度减慢,这是由于生长中的氧化膜在较 浓的硫酸溶液中溶解速度加快的结果。若硫酸 浓度太低,导电性下降,其氧化时间就要延长; 硫酸的浓度升高,有利於多孔膜的生成,该膜 的弹性好,吸附力强;易获得防护装饰性氧化 膜,硫酸浓度多利用上限,即20%的H2SO4, 为了获得硬而厚的耐磨氧化膜,应选用较稀的 硫酸溶液,通常利用10%-15%的H2SO4。
2、氧化膜的生长过程: 总体上说包含两个方面: 一是膜的生成过程; 二是膜的电化学溶解过程.
AL2O3.H2O
A B C 多孔层 阻挡层 铝基体
A.通电瞬间,氧和铝有很大亲和力,铝基 材迅速形成一层致密无孔的阻挡层,其 厚度取决于槽电压。 B.由于氧化铝原子体积大,故发生膨 胀,阻挡层变得凹凸不平,造成电流 分布不均匀,凹处电阻小,电流大, 凸处相反。 C.凹处在电场作用下发生电化学溶解 以及H2SO4的化学溶解,凹处逐渐变 成孔穴,凸处变成孔壁,阻挡层向多 孔层转移。
7、电流密度: 电流密度越大,膜较硬,耐磨性 好,但电流密度过高,则会因焦耳 热影响,使膜层溶解作用增加,电 流密度过高,膜层氧化时间过长, 膜疏松,硬度降低,对于需染色或 电解着色的氧化膜,电流密度宜取 2~2.0A/dm2,装饰性阳极氧 1.5A/dm 2; 化膜电流密度宜取0.5~0.8A/dm
杂 质
来源
最大允 含量 (g/L)
对阳极氧化膜质 量的影响
排除方法
Cl-
水
0.05
在氧化膜上形 用去离子水 成黑色腐蚀斑点, 或蒸馏水配制 严重时铝制品表 槽液,并严格 面会发生穿孔而 控制清槽水质。 报废。
F-
水
0.01
同上
同上
AL3+
铝基 体在阳 极氧化 过程中 溶解进 入电解 液
10
氧化膜透 明度变差,染 色性能下降, 耐蚀性、耐 磨性下降, 严重时会导 致工件烧蚀。
8、搅拌影响: 因氧化膜电阻较大,在电流作 用下产生很高的焦耳热,如不及时 扩散,工件易被烧损,即使不烧烂, 生成的膜多疏松,甚至粉化。一般 采用压缩空气搅拌,用于搅拌电解 液的压缩空气必须经过油水分离 器净化,以免污染槽液;
9、材质影响: 所谓材质不仅仅指合金成分, 还包括组织状态(热处理状态)和 表面加工状态。铝越纯,生成氧化 膜透明光亮,否则,氧化膜透明度和 光亮度越低,且抗蚀力越差,组织状 态或加工不同,形成氧化膜不均 匀。
2
同上
稀释或更换 槽液
合金铝 Si 悬 中的Si溶 浮于电 解进入电 解液中 解液
2+
使电解变得浑 浊,并常常以粉状 吸附在工件上
过滤排除
3+含量: 6、Al
电解液中Al3+含量控制在0.5~5g/L时, 有助于氧化膜的抗蚀性和耐磨性, Al3+ 含量在5g/L以下时,膜层对染色吸附 3+含量在5~15g/L时,氧 能力下降, Al 3+含量 化膜吸附能力基本保持稳定,Al 超出15g/L时,氧化膜会出现不规则现 象,且皮膜色泽发黄,膜层性能下降。 因此,为了染色色泽均匀, Al3+含量 必须控制在5~12g/L之间。
(四)常见故障及分析: (1)铝合金制品经硫酸阳极氧化处理后,发生局 部无氧化膜,呈现肉眼可见的黑斑或条纹,氧化 膜有鼓瘤或孔穴现象.此类故障虽不多见但也 有发生. 上述故障原因,一般与铝和铝合金的成分、组织 及相的均匀性等有关,或者与电解液中所溶解 的某些金属离子或悬浮杂质等有关。铝和铝合 金的化学成分、组织和金属相的均匀性会影响 氧化膜的生成和性能。纯铝或铝镁合金的氧化 膜容易生成,膜的质量也较佳。而铝硅合金或 含铜量较高的铝合金,氧化膜则较难生成,且 生成的膜发暗、发灰、光泽性不好。
(2)同槽处理的阳极氧化零件,有的无氧化膜或膜 层轻薄或不完整,有的在夹具和零件接触处有烧 损熔蚀现象.这类故障在硫酸阳极氧化工艺实践 中往往较多发生,严重影响铝合金阳极氧化质量.
由于铝氧化膜的绝缘性较好,所以铝合金制件在 阳极氧化处理前必须牢固地装挂在通用或专用 夹具上,以保证良好的导电性.导电棒应选用铜 或铜合金材料并要保证足够接触面积.夹具与零 件接触处,既要保证电流自由通过,又要尽可能 减少夹具和零件间的接触面积过小,电流密度太 大,会产生过热易烧损零件和夹具.无氧化膜或 膜层不完整等现象,主要是由于夹具和制件接触 不好,导电不良或者是由于夹具上氧化膜层未彻 底清除所致. (3)铝合金硫酸阳极氧化处理后,氧化膜呈疏松粉 化甚至手一摸就掉,特别是填充封闭后,制件表 面出现严重粉层,抗蚀性低劣.这一类故障多发 生在夏季,尤其是没有冷却装置的硫
D.多孔膜形成过程: 1.阳极氧化初期,电流密度一般均超出临界电流密 度,形成均匀的壁垒型膜; 2.壁垒型膜逐渐成长。当电流密度低于临界值时, 铝离子不能再形成新膜物质,膜的表面暴露在电解 液中受到浸蚀; 3.进一步阳极氧化,溶液对膜的浸蚀变得不均匀; 4.形成的空洞之间存在发展竞争。这种发展有“自 催化”作用; 5.发展较快的空洞(主空洞)在向膜深处和横向发展 6.主空洞继续沿纵向和横向发展,相邻主空洞之间 互相靠近,主空洞之间的小空洞停止生长; 7.空洞停止横向发展,仅沿纵向深入,孔径固定。 此时,空洞的产生及发展阶段结束,阳极氧化进入 稳态阶段。
3、电压: A、电压高,氧化膜生长速度提高,孔 隙增多,易染色,硬度和耐磨性提高。 B、电压低,生成氧化膜的速度慢,膜 层较致密。
4、氧化时间: 根据硫酸浓度,溶液温度、电压, 膜厚而定,其它条件不变,时间越 长,膜厚越厚,但达到一定厚度时, 膜厚将不会增加(即膜的溶解速度 与生长速度相等)。
5、杂质离子影响: 可能存在的杂质离子:CLˉ、F ˉ、 3 ˉ、AL3﹢、CN2 ﹢ 、 2﹢ 、 NO Fe Si 2 ﹢等 A、 CLˉ、F ˉ、NO3 ˉ等阴离子含量 高时,氧化膜孔隙增加表面粗糙、 疏松。CLˉ﹤0.05g/L F ˉ ﹤0.01g/L 3﹢、CN2 ﹢ 、Si 2 ﹢主要影 B、 AL 响氧化膜色泽,透明度和抗蚀性。
3、槽液维护
A、对槽液要定期进行分析,一般只分析游离 硫酸和铝含量。槽液在使用过程中,游离硫 酸浓度会逐渐下降,而铝含量上升,当游离 硫酸浓度降到规定浓度下限,铝含量尚未升 到上限时,只需计量添加硫酸,但当铝含量 超过规定上限时,应排放部分(1/4~1/3) 槽液,然后再计量添加硫酸和去离子水。排 放的硫酸溶液可用耐酸泵抽入硫酸脱脂槽内 二次利用。降低氧化槽内的铝含量也可用硫 酸回收设备。