TTA-1189型车轴精修中心孔工序检查记录
矿车关键工序检验记录
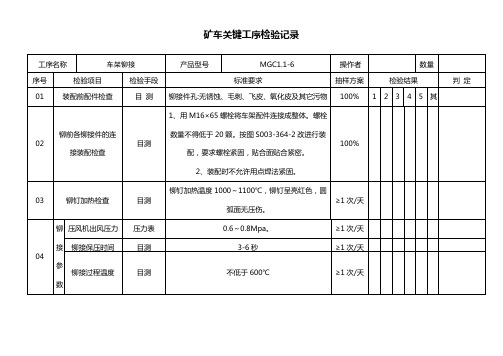
矿车关键工序检验记录
工序名称车架铆接产品型号MGC1.1-6操作者数量
序号检验项目检验手段标准要求抽样方案检验结果判定
01 装配前配件检查目测铆接件孔:无锈蚀、毛刺、飞皮、氧化皮及其它污物
等
100% 1 2 3 4 5
其
余
02 铆前各铆接件的连
接装配检查
目测
1、用M16×65螺栓将车架配件连接成整体。
螺栓数
量不得低于20颗。
按图S003-364-2改进行装配,
要求螺栓紧固,贴合面贴合紧密。
2、装配时不允许用点焊法紧固。
100%
03 铆钉加热检查目测铆钉加热温度1000~1100℃,铆钉呈亮红色,圆弧
面无压伤。
≥1次/天
04 铆
接
参
数
压风机出风压力压力表0.6~0.8Mpa。
≥1次/天铆接保压时间目测3-6秒≥1次/天铆接过程温度目测不低于600℃≥1次/天
05 铆接过程检验目测1、铆钉装入铆钉孔前,必须将铆钉上的氧化皮除掉。
2、顺序:先铆接空孔,再拆掉螺栓,铆接其余的孔。
5架/批
06 铆接质量检查目测/塞尺
1、铆钉:形状正确,圆弧面无压伤,无裂纹等。
2、用0.1㎜的塞尺检查不能插进为合格。
3、不合格的铆钉应铲除掉重铆,但更换有缺陷的铆
钉数量不应超过部件上的铆钉总数的7%。
5件/批
检验检验结论: 本工序合格□不合格□。
(工艺技术)工艺检查记录

(工艺技术)工艺检查记录注:该记录此版本(A/1)从2013年8月1日起执行,之前的版本同时作废。
工艺点检记录表DY-JL-ZK-06A/1注:该记录此版本(A/1)从2013年8月1日起执行,之前的版本同时作废。
工艺点检记录表DY-JL-ZK-06A/1注:该记录此版本(A/1)从2013年8月1日起执行,之前的版本同时作废。
工艺点检记录表DY-JL-ZK-06A/1注:该记录此版本(A/1)从2013年8月1日起执行,之前的版本同时作废。
工艺点检记录表DY-JL-ZK-06A/1注:该记录此版本(A/1)从2013年8月1日起执行,之前的版本同时作废。
工艺点检记录表DY-JL-ZK-06A/1注:该记录此版本(A/1)从2013年8月1日起执行,之前的版本同时作废。
工艺点检记录表DY-JL-ZK-06A/1注:该记录此版本(A/1)从2013年8月1日起执行,之前的版本同时作废。
工艺点检记录表DY-JL-ZK-06A/1注:该记录此版本(A/1)从2013年8月1日起执行,之前的版本同时作废。
工艺点检记录表DY-JL-ZK-06A/1注:该记录此版本(A/1)从2013年8月1日起执行,之前的版本同时作废。
工艺点检记录表DY-JL-ZK-06A/1注:该记录此版本(A/1)从2013年8月1日起执行,之前的版本同时作废。
工艺点检记录表DY-JL-ZK-06A/1注:该记录此版本(A/1)从2013年8月1日起执行,之前的版本同时作废。
工艺点检记录表DY-JL-ZK-06A/1注:该记录此版本(A/1)从2013年8月1日起执行,之前的版本同时作废。
工艺点检记录表DY-JL-ZK-06A/1注:该记录此版本(A/1)从2013年8月1日起执行,之前的版本同时作废。
工艺点检记录表DY-JL-ZK-06A/1注:该记录此版本(A/1)从2013年8月1日起执行,之前的版本同时作废。
工艺点检记录表DY-JL-ZK-06A/1注:该记录此版本(A/1)从2013年8月1日起执行,之前的版本同时作废。
标准工艺专项检查记录

标准工艺专项检查记录
编辑整理:
尊敬的读者朋友们:
这里是精品文档编辑中心,本文档内容是由我和我的同事精心编辑整理后发布的,发布之前我们对文中内容进行仔细校对,但是难免会有疏漏的地方,但是任然希望(标准工艺专项检查记录)的内容能够给您的工作和学习带来便利。
同时也真诚的希望收到您的建议和反馈,这将是我们进步的源泉,前进的动力。
本文可编辑可修改,如果觉得对您有帮助请收藏以便随时查阅,最后祝您生活愉快业绩进步,以下为标准工艺专项检查记录的全部内容。
监理“标准工艺”检查记录表
监理“标准工艺”检查记录表
监理“标准工艺”检查记录表
浙江电力建设监理公司
浙江电力建设监理限公司
浙江电力建设监理有限公司
浙江电力建设监理有限公司
浙江电力建设监理有限公司
编号:。
数控车床总装机整机检查记录

包装后应有明显标识:厂名、产品名称、型号规格、出厂编号、出厂年月、净重、毛重、箱体外形尺寸、起吊出处、发货地点、小心轻放、请勿倒置等字样。
7
标识字体规范,行里整齐,表面字体颜色均匀
质量问题反馈单
质量问题反馈单
a在垂直主平面内
0.02/100
b在主平面内
0.015/100
G10
尾座套筒锥孔轴线对溜板移动的平行度(只许向上、向前偏)
a在垂直主平面内
0.024/300
b在主平面内
0.02(只许尾端高)
0.03~0.05
0.002~0.038
G12
刀架横向移动时对主轴轴线的垂直度
2.优等品有16个项目达到30%储备量要求
结构性能
空转实验:
1)主轴进行正转、反转、停止及变化转速实验。
2)进给机构做低、中、高进给速度(或进给量)及快速进给变化实验。
3)主轴轴承达稳定温度时测量前后轴承:温度70°C,温升40°C。
4)主轴正转、反转、停止(包括制动)的连续实验,连续实验不得少于7次。
10.纵横溜板移动时内防护无异常。
11.内防护的刮削板牢固,可靠。
附件、工具及技术文件
1.按装箱单清点附件及工具、规格、数量要相符,标记要清晰。
2.特殊附件按协议供应。
3.包括使用说明书、合格证、装箱单,技术文件要齐全、正确、清晰
数控车床厂内检查标准
机床型号
机床编号
日期
装配人员
检查人员
包装检查
检查内容
5
丝杠两端轴承座等高度0.01
6
丝杠与导轨等距度(冷检)
上母:0.03
侧母:0.03
7
轴承压盖的预压量0.02~0.05
钻孔桩成孔质量检查记录【范本模板】

施记表9温州市市政公用工程质量监督站监制施记表9温州市市政公用工程质量监督站监制施记表9温州市市政公用工程质量监督站监制施记表9温州市市政公用工程质量监督站监制施记表9温州市市政公用工程质量监督站监制施记表9温州市市政公用工程质量监督站监制施记表9温州市市政公用工程质量监督站监制施记表9温州市市政公用工程质量监督站监制施记表9温州市市政公用工程质量监督站监制施记表9温州市市政公用工程质量监督站监制施记表9温州市市政公用工程质量监督站监制施记表9温州市市政公用工程质量监督站监制施记表9温州市市政公用工程质量监督站监制施记表9温州市市政公用工程质量监督站监制施记表9温州市市政公用工程质量监督站监制施记表9温州市市政公用工程质量监督站监制施记表9温州市市政公用工程质量监督站监制施记表9温州市市政公用工程质量监督站监制施记表9温州市市政公用工程质量监督站监制施记表9温州市市政公用工程质量监督站监制施记表9温州市市政公用工程质量监督站监制施记表9温州市市政公用工程质量监督站监制施记表9温州市市政公用工程质量监督站监制施记表9温州市市政公用工程质量监督站监制施记表9温州市市政公用工程质量监督站监制施记表9温州市市政公用工程质量监督站监制施记表9温州市市政公用工程质量监督站监制施记表9温州市市政公用工程质量监督站监制施记表9温州市市政公用工程质量监督站监制施记表9温州市市政公用工程质量监督站监制施记表9温州市市政公用工程质量监督站监制施记表9温州市市政公用工程质量监督站监制施记表9温州市市政公用工程质量监督站监制施记表9温州市市政公用工程质量监督站监制施记表9温州市市政公用工程质量监督站监制施记表9温州市市政公用工程质量监督站监制施记表9温州市市政公用工程质量监督站监制施记表9温州市市政公用工程质量监督站监制施记表9温州市市政公用工程质量监督站监制施记表9温州市市政公用工程质量监督站监制施记表9温州市市政公用工程质量监督站监制施记表9温州市市政公用工程质量监督站监制施记表9温州市市政公用工程质量监督站监制施记表9温州市市政公用工程质量监督站监制施记表9温州市市政公用工程质量监督站监制施记表9温州市市政公用工程质量监督站监制施记表9温州市市政公用工程质量监督站监制施记表9温州市市政公用工程质量监督站监制施记表9温州市市政公用工程质量监督站监制施记表9温州市市政公用工程质量监督站监制。
焊钉焊接质量检查记录

GB50205-20001(5.3.2,5.3.3条)
工程名 称:
部位或楼 层:
施焊构件
检查批次:共 同类构件数量:
检查内容
钢结构B-1410
批 ,
批。
检查 区域 列轴
焊钉 名数
焊钉根部焊脚、焊脚 立面未熔和检查 (5.3.3条)
焊后弯曲试验检查 (5.3.2条)
பைடு நூலகம்
对检查中发现
数量
班
组
长
质检员
件;每件抽查焊钉数量1%,不应少于 每批 1个。 同类 (2)焊钉根部等内容检查,按总焊 构件 钉数抽查1%,不应少于10个; 抽查 (3)5.3.2条为主控项目 10%
或专业工长 年月日
施工单位:
或项目技术负责 人
年月日
,且
(焊钉根部焊脚均匀,焊脚 立面的局部未熔和不足360
(30°弯曲时焊缝和热影 响区不应有肉眼可见的裂
存有缺陷焊钉 的处理结果
称 量 (只) °焊脚应进行修补平整)
纹)
检查数量 质量情况 检查数量 质量情况
主控项目:检查
项,符合要求
项。
检查结果 一般项目:检查
点,其中合格
点 合格 ,率
%
注: (1)检查数量:焊后弯曲试验检查每 批同类构件抽查10%,且不应少于10
6210曲轴自检记录表

240
所有孔口倒角,所有飞边、棱边
毛刺、棱边清理符合作业
要求
φ191g7(-0.015 -0.061)X14.50 -0.1
170
118±0.20
190
24-M30X2-6H,沉孔φ31X5
12-φ30H7(+0.021 0)
25N9(0 -0.052)深2140 -0.029
200
4-φ28,背刮10-φ56
2-φ13.9通孔,攻2-M16-6H
6210曲轴质量自检记录单
图号:曲轴编号:
工序
自检内容(单位:mm)
自检结果(单位:mm)
有无缺陷
操作者
日期
200
12-φ16.7,背刮φ32
230
φ2100 -0.031
φ1310 -0.031
250
φ170h6(0 -0.025)
第一档
第二档
第三档
第四档
第五档
第六档
270
φ200h6(0 -0.029)
第一档
第二档
第三档
自检结果(单位:mm)
有无缺陷
操作者
日期
140
精车
主轴
颈
R3Xφ266X1+0.25 +0.15XR12
0-Ⅲ主轴颈φ202±0.05
φ222±0.05
173-0.25 -0.40
60+0.60 +0.30
3580-0.10、R30
φ210±0.05(Ⅳ——Ⅸ)
φ1220 -0.04X6
150
φ3820 -0.197X51
M10底孔φ8.5
7xφ26
带式输送机机头(机尾)中间架检查记录

验
收
意
见
建设(监理)单位:
专业负责人:
年月日
施工(测量)单位:安徽建华机械有限公司
项目技术负责人:
年月日
5
4
机架两对角线之差
两对角线平均值的3/1000
5
中间架的距离
±1.5
6
中间架的高低差
间距的2/1000
7
机架接头在左右偏差与高低差
±1.0
8
滚筒横向中心线与胶带机纵向中心线应重合
<2
9
滚筒轴线与胶带机纵向中心线的垂直偏差
<2/1000
10
滚筒的轴线水平度
<1/1000
11
托辊横向中心线与胶带机纵向中心线重合偏差
带式输送机机头(机尾)中间架检查记录
工程名称
泰钢炼铁升级改造工程
建设单位
泰山钢铁集团
有限公司
构件名称
规格尺寸
执行标准
GB50205-2001
检查日期
序号
检查项目
允许偏差(mm)
实测偏差(mm)
1
胶带机纵向中心线与基础实际轴线距离
±20
2
机架中心线与胶带机纵向中心线的重合
<3
3
机架中心线的垂线度在25m长度内
钻孔桩检表及记录表
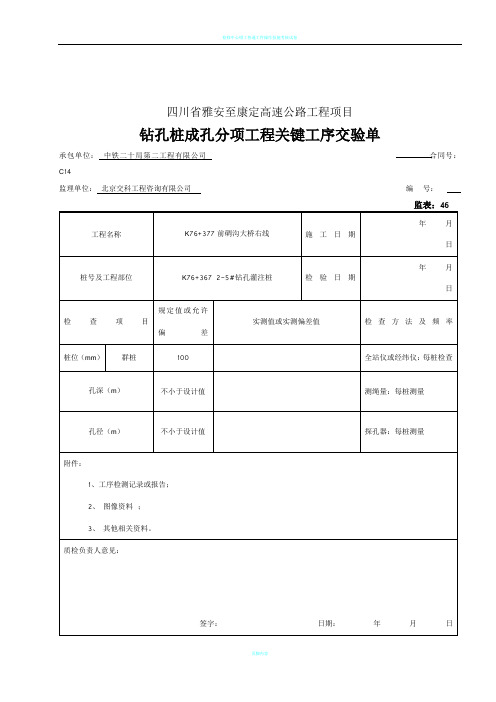
四川省雅安至康定高速公路工程项目钻孔桩成孔分项工程关键工序交验单承包单位:中铁二十局第二工程有限公司合同号:C14监理单位:北京交科工程咨询有限公司编号:监表:46四川省雅安至康定高速公路工程项目钻孔记录表承包单位:中铁二十局第二工程有限公司合同号:C14监理单位:北京交科工程咨询有限公司编号:记录表2页脚内容检查人:质检负责人:页脚内容四川省雅安至康定高速公路工程项目钻(挖)孔桩桩位检查记录表承包单位:中铁二十局第二工程有限公司合同号:C14监理单位:北京交科工程咨询有限公司编号:记录表4检查人: 质检负责人:四川省雅安至康定高速公路工程项目钢筋安装现场质量检验表承包单位: 中铁二十局第二工程有限公司 合同号: C14监理单位: 北京交科工程咨询有限公司 编 号:检表8.3.1-1四川省雅安至康定高速公路工程项目钢筋安装分项工程关键工序交验单承包单位:中铁二十局第二工程有限公司合同号:C14监理单位:北京交科工程咨询有限公司编号:监表:46四川省雅安至康定高速公路工程项目承包单位:中铁二十局第二工程有限公司合同号:C14监理单位:北京交科工程咨询有限公司编号:记录表7检查人: 质检负责人:四川省雅安至康定高速公路工程项目钻孔灌注桩现场质量检验表承包单位: 中铁二十局第二工程有限公司 合同号: C14监理单位: 北京交科工程咨询有限公司 编 号:检表8.5.2四川省雅安至康定高速公路工程项目钻孔桩浇筑砼分项工程关键工序交验单承包单位:中铁二十局第二工程有限公司合同号:C14监理单位:北京交科工程咨询有限公司编号:监表:46四川省雅安至康定高速公路工程项目钻孔桩终孔后灌注混凝土前现场检查记录表承包单位:中铁二十局第二工程有限公司合同号:C14监理单位:北京交科工程咨询有限公司编号:记录表8检查人:质检负责人:四川省雅安至康定高速公路工程项目混凝土浇筑申请报告单承包单位:中铁二十局第二工程有限公司合同号:C14监理单位:北京交科工程咨询有限公司监表13四川省雅安至康定高速公路工程项目灌注桩水下混凝土灌注现场记录表承包单位:中铁二十局第二工程有限公司合同号:C14监理单位:北京交科工程咨询有限公司编号:记录表16检查人: 质检负责人:四川省雅安至康定高速公路工程项目 混凝土施工检查记录表承包单位:中铁二十局第二工程有限公司 合同号: C14监理单位:北京交科工程咨询有限公司 编 号:记录表13检查人:质检负责人:四川省雅安至康定高速公路工程项目钻孔灌注桩外观鉴定检查记录表承包单位:中铁二十局第二工程有限公司合同号: C14 监理单位:北京交科工程咨询有限公司编号:外观记录表8.5.2页脚内容检查人:质检负责人:现场监理:专业监理:页脚内容水准测量记录表承包单位:中铁二十局第二工程有限公司合同号:C14监理单位:北京交科工程咨询有限公司编号:工程名称: K76+377前碉沟大桥右线工程部位: K76+367 2-5#钻孔灌注桩检测日期:测量:计算:复核:四川省雅安至康定高速公路工程项目全站仪平面位置检测表承包单位:中铁二十局第二工程有限公司合同号: C14监理单位:北京交科工程咨询有限公司编号:工程名称: K76+377前碉沟大桥右线桩号及工程部位:K76+367 2-5#钻孔灌注桩日期:测表11页脚内容测量:计算:复核:页脚内容。
钻孔质量检查验收记录表
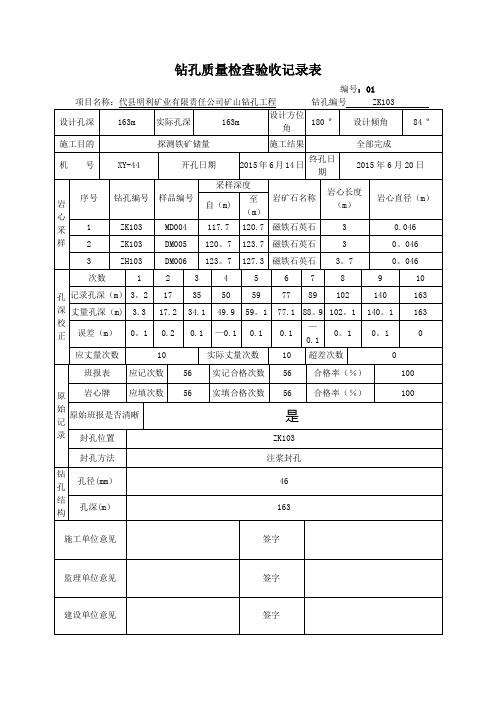
225.3
磁铁石英石
4。1
0.046
孔深校正
次数
1
2
3
4
5
6
7
8
9
10
记录孔深(m)
6
27。7
61。8
91
121。7
147
171.9
200.6
225
238。6
丈量孔深(m)
6。1
27。9
61.9
90。9
121.8
146。9
171。8
200.7
225.1。
238。6
误差(m)
0。1
0。2
0。1
46
孔深(m)
190。7
施工单位意见
签字
监理单位意见
签字
建设单位意见
签字
90.0
110.0
128
147
161
194
丈量孔深(m)
10。1
19。2
40。1
61.9
90.1
110。1
127。9
147。1
161.1
194
误差(m)
0.1
0.2
0.1
—0。1
0.1
0.1
—0.1
0.1
0。1
0
应丈量次数
10
实际丈量次数
10
超差次数
0
原始记录
班报表
应记次数
72
实记合格次数
72
合格率(%)
190。7
误差(m)
0.1
0。1
0。1
-0.1
0。1
0.1
-0。1
0.1
零部件检验记录10

样本
判定
数组
检验结果
1
2
3
4
5
6
7
8
9
1
核对型号、规格、合格证明。
6.5
2
材料:ABS。
6.5
3
外观:漆膜表面光亮、色泽均匀、无碰伤无明显缩痕、无飞边、配合面配合良好。
6.5
4
称重:与样品对比,无明显差别。
6.5
批量(N)
检验结论
检验员
检验记录
JL-5.1-06-15
零件名称
转刹把
检查水平
4.0
4
安全线高度:从底部量起,不低于其直径的二倍高度,不损伤鞍管强度。
4.0
批量(N)
检验结论
检验员
检验记录
JL-5.1-06-17
零件名称
链轮曲柄
检查水平
一般检查水平(Ⅰ)
供货单位
检验日期
序号
检验项目名称及要求
接收质量限
样本
判定
数组
检验结果
1
2
3
4
5
6
7
8
9
1
核对型号、规格、合格证明。
6.5
2
螺纹精度(左、右)M14×1.25-6H。
接收质量限
样本
判定
数组
检验结果
1
2
3
4
5
6
7
8
9
1
电镀件外观质量:色泽均匀、光亮,不得有起泡、剥离、烧黑、露底、露黄及明显的毛刺、花斑、针孔、麻点等缺陷。
6.5
2
表面氧化处理的零部件的表面氧化膜的色泽应均匀,不得有明显的花斑、锈斑或附着沉淀物。
回转窑安装检查记录
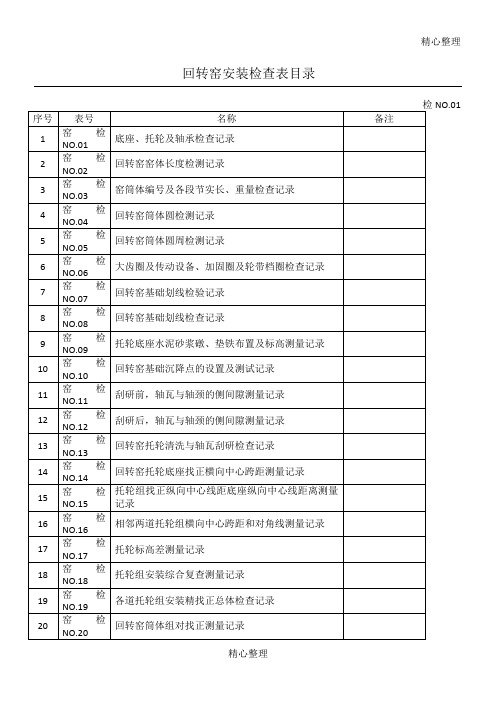
精心整理回转窑安装检查表目录
NO.01
NO.01
设备安装检测记录
窑检NO.02建设单位:
NO.03
设备安装检测记录
窑检NO.04建设单位:
NO.05
NO.06
设备安装检测记录
窑检NO.07建设单位:
设备安装检测记录
窑检NO.08建设单位:
隐蔽工程检测记录
窑检NO.09建设单位:
NO.10
设备安装检测记录
窑检NO.12
建设单位:
NO.13
NO.14
设备安装检测记录
窑检NO.15建设单位:
设备安装检测记录
窑检NO.16建设单位:
NO.17建设单位:
NO.18-1
窑检NO.18-2建设单位:
NO.19
NO.20
NO.21
设备安装检测记录
窑检NO.23-1建设单位:
施工单位:年月日
窑检NO.23-2建设单位:
建设单位:
NO.25
设备安装检测记录
窑检NO.26建设单位:
设备安装检测记录
窑检NO.27建设单位:
NO.28
NO.29
设备安装检测记录
窑检NO.30建设单位:
设备安装检测记录
窑检NO.31建设单位:
设备安装检测记录
窑检NO.32建设单位:
设备安装检测记录
窑检NO.33建设单位:
窑检NO.34建设单位:
设备安装检测记录
窑检NO.35建设单位:
回转窑安装分项工程质量检验评定表
窑检NO.35。
钢结构零件及部件加工(矫正和成型)质量检查记录

-12℃
检查日期
零部件
抽查件
检查情况(mm)
年
规
格
加工
数量
编号
数量
月
日
检查结果
主控项目:检查项,符合要求项。
一般项目:检查点,其中合格点,合格率%
注:1、冷矫正的加工温度全数检查制作工艺报告和施工记录;
2、钢材矫正后允许偏差,按矫正件抽查10%,不少于3件;班组长:质检员:
3、t—为加工件厚度,l—为构件长度,M—为1米长度范围,或专业工长:或项目技术负责人:
钢板的局部平面度(∆)
型钢弯
曲矢高
角钢的
垂直度
槽钢翼缘对腹板的垂直度
工字钢、H型钢翼缘对腹板的垂直度
不应有明显的凹面和损伤及划痕
碳素钢
低合金
结构钢
t≤14
t>14
允许偏差
不低于
不应超过
900℃
1.5
1.0
l/1000≯5.0
b/100,双肢栓接不得大于90°
b/80
b/100,
≯2.0
划痕深度≯0.5且≯负偏差的1/2
b—为型钢肢宽;年月日年月日
4、7.3.1条为主控项目。
12
GB50205-2001
钢结构零件及部件加工(矫正和成型)质量
检查记录(7.3.1,7.3.2,7.3.3,7.3.4,7.3.5,条)检查批次:共批,第批。
工程名称:构件名称:检查批次:施工单位:
检查内容
7.3.1条
钢材矫正后的允许偏差(mm)ቤተ መጻሕፍቲ ባይዱ
表面质量
冷矫正加工
环境温度
碳素钢和低合钢热矫正时加热温度
机械安装工程质量检查记录表格
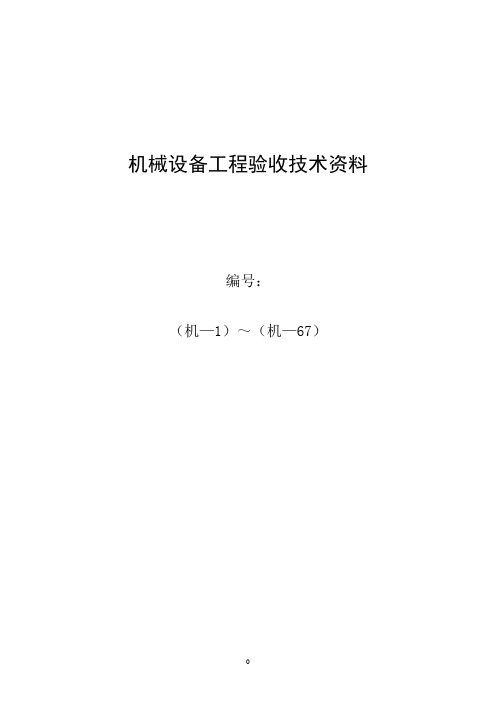
机械设备工程验收技术资料编号:(机—1)~(机—67)目录设备基础检查验收记录 (4)设备开箱检查验证记录 (5)垫板安装检记录 (6)设备安装、清洗、调整、检查记录 (7)班组自检记录 (8)滑动轴承装配检查记录(一) (9)滑动轴承装配检查记录(二) (10)滑动轴承装配检查记录(三) (11)滚动轴承装配检查记录(一) (12)滚动轴承装配检查记录(二) (13)联轴器装配检查记录 (14)CL型/CLZ型齿轮联轴器装配检查记录 (15)棒销联轴器装配检查记录 (16)弹性圈柱销联轴器装配检查记录 (17)十字轴式万向联轴器装配检查记录 (18)制动器装配检查记录 (19)皮带传动/链传动装配检查记录 (20)二级减速机装配检查记录 (21)三级减速机装配检查记录 (22)蜗轮蜗杆减速机装配检查记录 (23)园锥齿轮减速机装配检查记录 (24)空气压缩机安装检查记录(二) (26)往复活塞式压缩机安装检查记录(一) (27)往复活塞式压缩机安装检查记录(二) (28)往复活塞式压缩机安装检查记录(三) (29)往复活塞式压缩机安装检查记录(四) (30)往复活塞式压缩机安装检查记录(五) (31)螺杆压缩机、无润滑压缩机安装检查记录 (32)离心通风机安装检查记录(一) (33)离心通风机安装检查记录(二) (34)轴流通风机安装检查记录(一) (35)轴流通风机安装检查记录(二) (36)罗茨和叶氏鼓风机安装检查记录 (37)离心鼓风机安装检查记录(一) (38)离心鼓风机安装检查记录(二) (39)离心鼓风机安装检查记录(三) (40)离心鼓风机安装检查记录(四) (41)轴流鼓风机安装检查记录(一) (42)轴流鼓风机安装检查记录(二) (43)轴流鼓风机安装检查记录(三) (44)离心泵安装检查记录(一) (45)离心泵安装检查记录(二) (46)立式轴流泵安装检查记录(一) (47)机动往复泵安装检查记录(一) (49)机动往复泵安装检查记录(二) (50)蒸汽往复泵安装检查记录 (51)螺杆泵安装检查记录 (52)水环式真空泵安装检查记录 (53)单独传动辊道安装检查记录 (54)集中传动辊道安装检查记录 (55)链板输送机安装检查记录(一) (56)链板输送机安装检查记录(二) (57)皮带机安装检查记录(一) (59)皮带机安装检查记录(二) (60)布袋除尘器安装检查记录(一) (61)布袋除尘器安装检查记录(二) (62)电除尘器安装检查记录(一) (63)电除尘器安装检查记录(二) (64)刮板输送机安装检查记录 (65)螺施输送机安装检查记录(机-62) (66)斗式提升机安装检查记录(一) (67)斗式提升机安装检查记录(二) (68)机械设备试运转记录 (70)单位试车合格证 (71)无负荷联动试车合格证 (72)设备基础检查验收记录设备开箱检查验证记录垫板安装检记录设备安装、清洗、调整、检查记录班组自检记录滑动轴承装配检查记录(一)机—6工程编号分项工程施工单位单位工程设备名称分部工程安装图号施工日期年月日序号检查项目技术要求检查结果备注一厚壁轴瓦轴承的装配1 上、下轴瓦瓦背与轴承孔应接触良好(见图一)(1) 接触角a:稀油干油上轴瓦130°120°下轴瓦150°140°(2) 接触角内接角率:上轴瓦60%下轴瓦70%(3) 瓦侧间隙b:D≤200时,0.05塞尺不入D:轴公称直径D>200时,0.10塞尺不入简图及说明:上、下轴瓦内孔与相关轴颈的接触要求上下轴瓦瓦背与相关轴承孔的接触要求图一图二自检:班组长:施工负责人:技术负责人:质检员意见:质检员:滑动轴承装配检查记录(二)机—7工程编号分项工程施工单位单位工程设备名称分部工程安装图号施工日期年月日序号检查项目技术要求检查结果备注2上、下轴瓦接合面应接触良好0.05塞尺检查,塞入深度≤1/33 动压轴承的顶间隙:(见附表一)4 单侧间隙:顶间隙的1/2~1/35 上、下轴瓦内孔与轴颈接触良好(见图二)接触角度:稀油90°~120°干油90接触点数:≥每25×25范围内6 瓦口垫片与瓦口面形状相同宽度小于瓦口面1-2 长度小于瓦口面 1简图及说明:滑动轴承顶间隙(mm)表一基本尺寸d 最小间隙平均间隙最大间隙基本尺寸d最小间隙平均间隙最大间隙30<d≤50 0.025 0.050 0.075 160 0.13 0.16 0.20 50<d≤80 0.030 0.060 0.090 180 0.15 0.18 0.21 80<d≤120 0.027 0.117 0.161 200 0.17 0.20 0.23 130 0.085 0.137 0.188 220 0.19 0.22 0.25 140 0.085 0.137 0.188 240 0.21 0.24 0.27 150 0.12 0.15 0.19 250 0.22 0.25 0.28260 280 300 320 340 360 380 400 420 450 0.230.250.270.280.300.320.340.360.380.410.260.280.300.320.340.360.380.400.420.450.290.310.330.360.380.400.420.440.460.494805005305606006306707107508000.440.460.490.520.560.590.620.660.700.750.480.500.530.560.600.630.670.710.750.800.520.540.570.600.640.670.720.760.800.85自检:班组长:施工负责人:施工负责人:技术负责人:质检员意见:质检员:动压轴砂间隙与滑动速度的关系曲线10机—8工程编号分项工程施工单位单位工程设备名称分部工程安装图号施工日期年月日序号检查项目技术要求检查结果备注二薄壁轴瓦轴承装置1 轴瓦顶间隙(压铅法)(见附表二、图三)2 着色法检查瓦背与轴承座贴合情况轴瓦内径<180时,接触面积≥85% 轴瓦内径≥180时,接触面积≥70%3 装配后,在中分面处用0.02塞尺检查不入4 轴瓦侧间隙顶间隙的1/2~1/3 三静压轴承的装配1 油孔油腔应完好,油路畅通,轴承内外套应紧密无泄漏2 轴承外园与轴承孔间隙0.003-0.005 四含油轴套装配轴套与轴颈间隙为轴颈直径的1/1000~2/1000薄壁轴瓦顶间隙表二转速(r/min) <1500 1500-3000 >3000顶间隙(mm) (0.8-1.2)d/1000 (1.2-1.5)d/1000 (1.5-2)d/1000 注:d为轴颈的公称直径(mm)图三压铅法测量轴承间隙自检:班组长:施工负责人:技术负责人:质检员意见:质检员:顶间隙:S1=b1-(a1+a2) /2S2=b2-(a3+a4)/2式中:S1—一端顶间隙S2—另一端顶间隙b1b2—轴颈上铝丝压扁后厚度a1a2a3a4—轴瓦合缝处接合面上各垫片厚度或铝丝压扁后厚度11机—9工程编号分项工程施工单位单位工程设备名称环境温度℃分部工程安装图号施工日期年月日序号检查项目技术要求检查结果备注1热装温度≤100℃冷装温度≥-80°2 轴承外圈与轴承座在对称中心线的120°范围内接触良好0.03塞尺塞入长度≤1/33 轴承外圈与轴承座(或箱体半园孔)不得有夹帮现象:b max h max 各瓦口尺寸:①各瓦口尺寸:②各瓦口尺寸:③各瓦口尺寸:④各瓦口尺寸:⑤各瓦口尺寸:⑥简图及说明:滚动轴承装配修帮尺寸自检:班组长:施工负责人:技术负责人:质检员意见:质检员:12滚动轴承装配检查记录(二)机—10工程编号分项工程施工单位单位工程设备名称分部工程安装图号施工日期年月日序号检查项目技术要求检查结果轴承型号4 轴承与轴肩间隙:(1) 园锥滚子轴承,推力球轴承≤0.05(2) 其他()≤0.105 向心球轴承装配间隙C 0.2~0.4 当温差较大或中心距大于500时C=6 推力球轴承,园锥滚于轴承轴向游隙Δ= 简图及说明:图一轴承装配间隙cC=L·a·Δt+0.15注:c—轴承外圈与端兽盖间的间隙(mm)L—两轴承中心距(mm);a—轴材料的线膨胀系数,宜取a为12×10-6Δt—轴工作时温度与环境温度差(℃)自检:班组:施工负责人:技术负责人:质检员意见:质检员:13联轴器装配检查记录机—11工程编号分项工程施工单位单位工程设备名称分部工程安装图号施工日期年月日序号检查项目技术要求检查结果备注1 两轴心径向位移2 两轴线轴向倾斜3 端面间隙简图及说明:方法一自检:班组长:施工负责人:技术负责人:质检员意见:质检员:14CL型/CLZ型齿轮联轴器装配检查记录机—12工程编号分项工程施工单位单位工程设备名称分部工程安装图号施工日期年月日序号检查项目技术要求检查结果备注1 两轴心径向位移2 两轴线倾斜3 端面间隙C简图及说明:联轴器外形最大直径D 两轴心径向位移不是大于两轴线倾斜不得大于端面间隙C不得小于170-185 0.30 0.5/1000 2.5220-150 0.45 0.5/1000 2.5290-430 0.65 1.0/1000 5.0490-590 0.90 1.5/1000 5.0680-780 1.20 1.5/1000 7.5900-1100 1.50 2.0/1000 10.01250 1.50 2.0/1000 15.0端面间隙应使外齿轴套与端盖在两轴窜动到端面,间隙为最大尺寸位置地不接触自检:班组长:施工负责人:技术负责人:质检员意见:质检员:CL型齿轮联轴节1—内齿外套;2—外齿轴套;3—端盖CLZ型中间轴的齿轮联轴节1—中间轴;2—主轴15棒销联轴器装配检查记录机—13工程编号分项工程施工单位单位工程设备名称分部工程安装图号施工日期年月日序号检查项目技术要求检查结果备注1 两轴心径向位移2 两轴线倾斜3 端面间隙C简图及说明:棒销联轴器装配要求联轴器外形最大直径D 两轴心径向位移不是大于两轴线倾斜不得大于端面间隙C不得小于145-270 0.1 0.2/1000 5290-470 0.2 0.2/1000 10520-750 0.3 0.2/1000 10850-1110 0.5 0.2/1000 15 棒销联轴器1-半联轴器端面;2-档板;3-外套;4-棒销端面间隙应使半联轴器端面与档板在两轴窜动到端面间隙为最大尺寸时不接触。
立车装配质量检验记录

立车装配质量检验记录编号:J8.2-02 普通型双立柱立式车床数控总装装配质量检验记录产品型号:产品名称:用户名称:出厂编号:______________ 公司总则一、此卡片为检验普通、数控型双柱立式车床;二、机床的几何精度、数控精度、工作精度按所检验产品型号的合格证及补充验收报告验收技术要求执行;三、参照标准及文件:GB/T9061-20__6 金属切削机床通用技术条件;JB/T9874-1999 金属切削机床装配通用技术条件;JB/T4116-96 单、双柱立式车床精度检验;JB/T10051-1999 金属切削机床液压系统通用技术条件;JB/T9877-1999 金属切削机床清洁度的测定;GB/T6576-20__2 润滑系统技术条件;GB15760-20__4 安全防护通用技术条件;Q/Q2J06.06-2021 铸铁件和铸钢件清理检验及涂底漆工艺规程;GB5226.1-20__2 机械安全、机械电气设备;Q/Q2JO1.271-20__5 机床电气检验要求;JB/T 8356.1-1996 机床包装技术条件;JB/T 8356.2-1996 机床包装箱;GB/T 4879-1999 防锈包装。
四、机床验收检验报告顺序:1、总装;2、空运转试验(试车)与电气检验交叉进行;3、负荷试验;4、几何精度检验;5、数控精度检验;6、工作精度检验;7、油漆检验;8、包装检验。
五、机床验收检验要求:验收检验前,应将机床安装和调整好,一般应自然调平,使机床处于水平位置。
主要零件登记表零件名称图号编号备注一、试车工序序号检验内容及要求检验结论备注 1 各部零件装配齐全,加工表面无磕碰、划伤、锈蚀等现象。
2 沉头螺钉不应凸出零件表面,螺栓尾端应略凸出螺母倒角值,固定销钉应略凸出零件表面。
3 夹紧机构可靠稳定,各油缸无渗油现象,操纵机构灵活可靠。
4 工作台液压浮起(),当低于 0.04 时电位传感器报警,浮起一致性0.01。
车轴检测工艺

尺框带着踏面磨耗尺,在导板上左右移动到擦伤或凹陷最深处,来测量磨耗性踏面局部擦伤或凹陷深度尺寸。如在擦伤或凹陷处测量为3.5mm,在同一直径线上未擦伤或凹陷处测量为2mm,则擦伤或凹陷深度为1.5mm。
(3)车轮踏面剥离长度测量(0—75mm)
车轮踏面剥离长度尺寸,用轮辋厚度测尺(15)在踏面剥离处进行测量。
(4)轮对内侧距离三处差最大值1。
6.测量记录填写及保管
6.1凡经检测后的部件,都必须填写检测记录。
6.2检测记录应严格按规定格式填写,相关人员签字必须齐全。
6.3检测记录作为检修工作的原始凭据,内容填写要清晰、真实、及时、准确、完整,不得涂改。
6.4检测记录与报告应归类放置,并妥善保管,以便查阅。
1.3确认量具状态良好,检定不过期。
2.工艺装备及要求
2.1注意事项
(1)使用过程中,应防止对各部件的剧烈摔碰,以免损坏和变形。
(2)测量块是测量仪的关键部位,不得拆动,以免影响测量准确度。
(3)仪器使用后要涂机油,以防生锈。较长时间不用时,测头、测量块应擦上机油。
(4)相对运动部位应经常滴少量洁净润滑油。
4.测量作业
4.1测量车轮,如图1
(1)车轮踏面圆周磨耗深度测量(-2—9mm)
磨耗性车轮踏面70mm处圆周磨耗的测量,推动螺钉(2)沿水平方向,将尺框(4)推至定位快(8)左侧然后由下向上带动轮缘厚度测尺推至导板(5)根部,再向右推动尺框至定位块挡住为止。然后将检查器置于检查车轮上,并将检查器同轮缘顶部和轮辋内侧面靠紧,再推下螺钉,使踏面磨耗尺(10)抵住踏面,即可在游标(16)读出分度值0.1mm的踏面磨耗值。
成都工务机械段
轴承业质量标准检查表061123

过程中失效潜在风险的评估(PFMEA)
先期产品质量策划(APQP)
输出值应把风险评估量值化,以便优先处理足够的改进行动和完成工序路线和供方控制计划。
过程中失效潜在风险的评估(PFMEA)
轴承业建议AIAQ发表的过程FMEA来实施该项活动。
9
收到反映
对此合同进行审核并做记录
本合同签署
10
正式同意标准内容,
用第21页上格式确认
11
轴承业采购质量方针
确保产品与服务的供应不会成为向轴承业的最终客户提供服务的瓶颈
公司质量方针
12
基于他们质量体系,过程能力和工作业绩,使用过审批的供应商
与轴承业的供货协议
13
鼓励供应商推行不断地持续改进
持续改进实例
对用于新建和生产阶段的测定技术,必要的测量和试验设备必须进行评估。
供方控制计划”
样品大小和抽样频率需规定,包括新建和生产阶段
供方控制计划”
控制方法,例如统计过程控制,检查记录防错技术的处理,自动装置等
供方控制计划”
不符合的产品或运行失控的应对方案。
供方控制计划”
轴承业建议AIAG 出版的先期质量策划和控制计划的方式
·除非轴承业另有规定,否则IS/ISIR 的零件应该从一批不低于300件的有效生产中获取
PPAP报告
·这一批产品应该在产品生产地点根据用于批量生产的条件和环境来生产。
PPAP报告
·递交的按照规定质量的轴承业、样品和报告包括:
PPAP报告
—生产流程图
PPAP报告
—显示完全符合轴承业规格的实测尺寸/检查结果,