渗铝钢换热管与管板焊接工艺规程( 机 密 )
管子焊接工艺规范(包括合金管)

管子焊接工艺规范1 范围本规范规定了CO2气体保护焊和钨极氩弧焊用于管子焊接的焊接前准备、人员、工艺要求、工艺过程和检验。
本规范适用于管子与管子、管子与附件之间的对接和角接接头,焊接时,可采用纯CO2气体或CO2+Ar混合气体的CO2半自动或自动焊接,也可采用钨极氩弧焊。
焊接位置为管子水平转动位置和管子水平固定位置。
2规范性引用文件Q/SWS 42-010-2003焊缝返修通用工艺规范3 焊接前准备3.1 CO2半自动或自动焊焊丝选用,见表1。
表1 CO2半自动或自动焊焊丝选用3.2 钨极氩弧焊焊丝的选用,见表2。
表2 钨极氩弧焊焊丝的选用3.3 保护气体无论是CO 2半自动或自动焊所用的CO 2气体、CO 2+Ar 混合气体,还是钨极氩弧焊所用的纯Ar 气体,均应符合气体质量使用标准,其纯度达99.9 %。
3.4 焊接设备两侧各宽20mm 范围内)作清理,并去除油、锈等污物。
3.6.2 对于碳钢管的锈蚀,应用钢刷打磨除锈。
不锈钢管应用丙酮进行清理。
3.6.3 坡口加工残留毛刺应除去,并应重新清理。
4 人员凡从事该工艺焊接的焊工,必须经过船级社资格认可考试,考试合格并经船级社认可后,方能参与相应等级项目的焊接。
5 工艺要求5.1 装配要求5.1.1 装配工在安装管子对接时,首先要检查管子接口同心度,防止安装错边。
5.1.2 管子对接定位可选用定位“马”固定,或在焊缝内作定位焊固定。
5.1.3 装配间隙,见表3。
表3 装配间隙5.2 对于要求单面焊双面成型的管子拼缝,焊前,有色金属管内应充氩气保护,并采用钨极氩弧焊(TIG焊)打底。
5.3 船上安装要求单面焊双面成型的管子拼缝,因无法进行充气保护,焊接中应仔细观察熔池,以确保背面焊缝质量。
对于不锈钢管,焊后,管内要作钝化处理。
5.4 焊接参数为确保管子的焊接质量,焊接时应参照表4的焊接参数进行。
表4 焊接参数6 工艺过程6.1 焊前充气焊前先用铝铂胶带对所焊管子接缝两端面及坡口面封住(对于较长管子可采用海绵、泡沫、可溶纸等工具做成堵板,设置于距焊缝150mm~200mm的两侧,造成一个气室),管子一端充氩气,管子另一端开一个约5mm的小孔排气,等管子内空气排尽并被氩气充满后,方可开始焊接。
换热管与管板手工焊接通用工艺

换热管与管板手工焊接通用工艺
1 准备工作
1.1 检查管板孔表面粗糙度、管孔尺寸及换热管的尺寸和表面质量。
1.2 管板、折流板组装前应用丙酮清洗(不锈钢酸洗后仍需丙酮清洗);换热管(黑管或光亮管)均需用百叶轮打磨抛光处理两端部至少50mm,且不能减薄管壁厚度。
1.3 组装管束,并用保鲜膜对管头焊接部位进行保护
1.4 焊接设备应采用脉冲氩弧焊机及配套的焊枪组件;焊枪配用带滤网的导流器和至少12mm的喷嘴
2 焊前清洁与防护
2.1 焊前应用丙酮和绸布再次清洗管板孔、换热管端部及待焊表面(建议采用清洁50个接头焊接50个接头的形式进行)
2.2 焊前也应用丙酮和绸布对焊丝表面进行清洗
注:用绸布试擦显示无污才能焊接
3 焊接要求
3.1 每个接头应采用手工GTAW进行点焊(填丝要求按打底焊),点焊位置如图3.2 打底焊道起弧和收弧必须偏离点焊区域
3.3每个接头均采用手工钨极氩弧焊分三道焊,每道焊接方向均向上,焊道的起弧点和收弧点如图
3.3.1碳钢接头三道均采用填丝焊
3.3.2不锈钢接头第一道采用自熔焊,第二、三道均采用填丝焊
3.4 焊接时喷嘴应保持固定角度随电弧移动,送丝应保持连续;收弧时应采用脉冲衰减;灭弧后不应立即移开喷嘴,应继续通气进行保护
3.5 层间清理采用钢丝抛盘对焊缝及管口进行处理,必要时用丙酮清洗
3.6 焊道收弧应完全覆盖焊道起弧点(覆盖长度>2倍焊缝宽度);在多道焊中,前一焊道必须被下一焊道完全覆盖,焊接层的焊道头和焊道尾需相互错开(偏移)。
换热器中渗铝钢管的应用及焊接

选用T427焊条。但设备使用单位要求我们用El一
23—12Mo一16型焊条,此种焊条焊芯为不锈钢焊 丝,价格较贵,每吨价格20 000元左右。另外,在烘 焊条时发现,当温度为150℃时,焊缝有气孔,将温 度提高到250 oC以上后,才没有气孔。所以正式焊 接时,对El一23—12Mo—16型焊条作250 oC的烘 干处理。鉴此,在焊接时,两种焊条均使用了。为了 保证焊缝质量,选用了AX一300—1型焊机,施焊 时,尽量采取窄焊道,焊条不作横向摆动。 3.4管与管板的焊接工艺及焊接顺序 由于换热器列管贯穿上、下管板,且焊缝密,数 量多,稍不注意就易发生变形,影响设备的使用寿
3改造实践
3.1改造方案
会脱开。为了保证设备的正常运行,对新换热器列 管与管板连接采用焊接。但保证渗铝管与管板不同
・收稿日期:2009—04—10 作者简介:孙德义(1970一)男,辽宁葫芦岛,机械工程师,昆明理工大学毕业,现从事机械工程设计施工管理工作。
万方数据
有色矿冶
第25卷
材质焊接质量是关键。为此,我们曾向渗铝单位要 求保留管头部分不渗铝,但在渗铝工艺上对方无法 满足。而对管子上需焊的部位进行加工,将渗铝层 清除干净的方法,既浪费人力,又增加加工费用,而
文章编号:1007—967X(2009)05—0047—02
换热器中渗铝钢管的应用及焊接’
孙德义
(中冶葫芦岛有色金属集团有限公司,辽宁葫芦岛125003)
摘要:介绍了某硫酸厂转化系统的鳓000 mm换热器的结构和工况,给出了改造方案,通过选择
合适的焊接方法,采用手工电弧焊,表面渗铝处理换热器列管,抗氧化、耐腐蚀、耐高温,使 用效果好。
4结语
换热器焊接过程中,由于使用单位要求,主要采 用E一23—12Mo一16型焊条进行焊接,但我们曾用 T427焊条进行过试验,其焊缝质量能满足设计要 求,所以我们在新换热器制作中仍然使用T427焊条 焊了50个焊口。后来停产检修时进行了检查,发现 不管是用T427焊条还是用E1—23—12Mo一16焊 条,它们的焊缝表面情况均良好,仅四周漆膜有些脱
换热器组装焊接通用工艺要求及质量保证措施
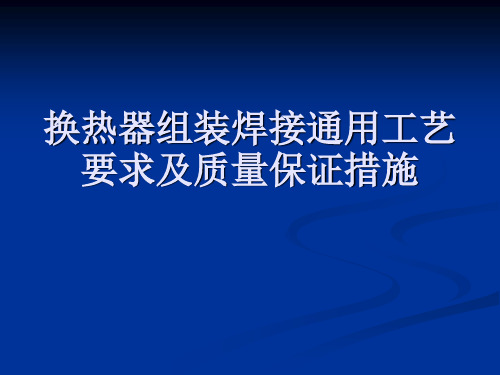
4.2.2 胀管平头 4.2..2.1 换热管头连接要求一般采用先胀后焊,具体根据工艺 要求确定。胀接应严格按胀接工艺进行。 4.2.2.2 胀接连接时,其胀接长度,不应伸出管板背面(壳程 侧),胀接部分与非胀接部分应圆滑过渡,胀接操作时要 特别注意管头焊接区域的防污染; 4.2.2.3 对于换热管壁厚≤1.5mm的薄壁钛换热器要求必须进行 贴胀。(可选用机械胀以保证管头焊接端全贴合,以减少 焊接收弧时的气孔。) 4.2.2.4 平头应保证管头平齐,及必要的管头伸出长度。 4.2.2.5 为防止管板孔内多潮生锈及清理后的有色金属表面再 次氧化,换热管组装完后应尽快安排焊工检查清理后施焊。 4.3 焊接 4.3.1 焊接前管头焊接区应用丙酮擦洗,热吹风机或火焰枪吹 扫烘干,必要时可用高压氩吹除管头杂物,严禁用压缩空 气对管头进行吹扫。 4.3.2 锆、钛等特材换热管头严禁使用钢丝刷抛光轮清理。
管板与换热管接头泄露返修工艺
着色 光 清根 着色 清洗 清洗 烘干 水压 焊接 抛
1、用着色渗透探伤的方法,检查管板与换热管的焊缝泄漏点。 2、清根去除缺陷区域 3、清洗去除表面的着色剂 4、烘干去除内部的渗透剂、水渍等物 5、焊接 6、抛光 7、着色 8、清洗 9、水压
4.3.3 清理完后2小时内必须施焊,否则应重新进行清理。施焊前各个气 体管路和保护罩应预通气一段时间,保证无残留杂质和水气。 注:在焊接换热管之前必须完成壳体与管板的焊接。 4.3.4 焊丝必须在焊前清理干净,焊丝头的氧化段必须去除; 4.3.5 管头焊接必须严格按焊接工艺卡执行,在焊接过程中,应加强管头 高温区的保护,应提前送气,滞后停气,管头内放置铜芯。 4.3.6 焊接电流的选择应在保证工件焊透和熔合良好的情况下尽量采用小 规范; 4.3.7 整个管板接头的焊接顺序应在0°、90°、180°、270°和中间部位 对称错开施焊(如下图)
渗金属

渗金属是指以金属原子渗入钢的表面层的过程。
它是使钢的表面层合金化,以使工件表面具有某些合金钢、特殊钢的特性,如耐热、耐磨、抗氧化、耐腐蚀等。
生产中常用的有渗铝、渗铬、渗硼、渗硅等。
diffusion metallizing使一种或多种金属原子渗入金属工件表层内的化学热处理工艺。
将金属工件放在含有渗入金属元素的渗剂中,加热到一定温度,保持适当时间后,渗剂热分解所产生的渗入金属元素的活性原子便被吸附到工件表面,并扩散进入工件表层,从而改变工件表层的化学成分、组织和性能。
与渗非金属相比,金属元素的原子半径大,不易渗入,渗层浅,一般须在较高温度下进行扩散。
金属元素渗入以后形成的化合物或钝化膜,具有较高的抗高温氧化能力和抗腐蚀能力,能分别适应不同的环境介质。
渗金属的方法主要有固体法(如粉末包装法、膏剂涂渗法等)、液体法(如熔盐浸渍法、熔盐电解法、热浸法等)和气体法。
金属元素可单独渗入,也可几种共渗,还可与其他工艺(如电镀、喷涂等)配合进行复合渗。
生产上应用较多的渗金属工艺有:渗铝、渗铬、渗锌、铬铝共渗、铬铝硅共渗、钴(镍、铁)铬铝钒共渗、镀钽后的铬铝共渗、镀铂(钴)渗铝、渗层夹嵌陶瓷、铝-稀土共渗等。
渗铝钢铁和镍基、钴基等合金渗铝后,能提高抗高温氧化能力,提高在硫化氢、含硫和氧化钒的高温燃气介质中的抗腐蚀能力。
为了改善铜合金和钛合金的表面性能,有时也采用渗铝工艺。
渗铝的方法很多。
冶金工业中主要采用热浸、静电喷涂或电泳沉积后再进行热扩散的方法,大量生产渗铝钢板、钢管、钢丝等。
静电喷涂或电泳沉积后,必须经过压延或小变形量轧制,使附着的铝层密实后再进行扩散退火。
热浸铝可用纯铝浴,但更普遍的是在铝浴中加入少量锌、钼、锰、硅,温度一般维持在670℃左右,时间是10~25分。
机械工业中应用最广的是粉末装箱法,渗剂主要由铝铁合金(或纯铝、氧化铝)填料和氯化铵催化剂组成。
渗铝主要用于化工、冶金、建筑部门使用的管道、容器,能节约大量不锈钢和耐热钢。
316L不锈钢管与管板的焊接工艺
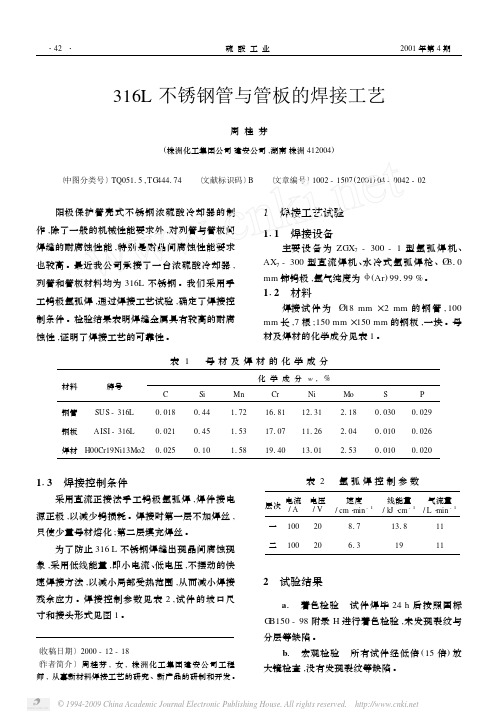
4 结论
a1 316 L 不锈钢管与管板焊接的控制参数 宜为 :
电流 100 A ,电压 20 V ,线能量 1318~19 kJ / cm 。
b1 正确选择焊材是减小焊缝晶腐蚀倾向的 条件之一 。可先根据舍弗勒焊缝组织图初步选 材 ,判断其能否使焊缝产生 A + F 双相组织且 F 含量约小于 5 % ,S、P 、C 杂质含量要尽量低 。
由于本焊接工艺采取了低线能量的快速焊接方法焊缝金属受热时间短温升不高缩短了冷却时在危险温度区12的停留时间使铬来不及析出与碳结合形成碳化铬所以减小了焊缝的晶间腐蚀倾向
· 4 2 · 硫 酸 工 业 2001 年第 4 期
316L 不锈钢管与管板的焊接工艺
图 1 焊接试件的坡口尺寸和接头形式 c1 晶间腐蚀检验 按照国标 GB433415 90 不锈钢耐酸钢晶间腐蚀倾向试验方法 ,将试件 打磨抛光 、清洗 、干燥后放在硫酸 + 硫酸铜 + 铜屑 的溶液中煮 16 h ,清洗干燥后在 240 倍金相显微 镜下检查 ,试件均无晶间腐蚀 。
3 结果分析
周桂芬
(株洲化工集团公司 建安公司 ,湖南 株洲 412004)
〔中图分类号〕TQ05115 , T G444174 〔文献标识码〕B 〔文章编号〕1002 - 1507 (2001) 04 - 0042 - 02
阳极保护管壳式不锈钢浓硫酸冷却器的制 作 ,除了一般的机械性能要求外 ,对列管与管板间 焊缝的耐腐蚀性能 ,特别是耐晶间腐蚀性能要求 也较高 。最近我公司承接了一台浓硫酸冷却器 , 列管和管板材料均为 316L 不锈钢 。我们采用手 工钨极氩弧焊 ,通过焊接工艺试验 ,确定了焊接控 制条件 。检验结果表明焊缝金属具有较高的耐腐 蚀性 ,证明了焊接工艺的可靠性 。
管道焊接工艺全套

管道焊接工艺全套一.钢材及焊接材料1 .焊接前必须查明所焊材料的钢号,以便正确地选用相应的焊接材料和确定合适的焊接工艺和热处理工艺。
2 .钢材必须符合国家标准(或部颁标准、专业技术标准)、进口钢材符合该国国家标准或合同规定的技术标准。
3 .焊接材[焊条、焊丝、铝棒、氮气、氧气、乙焕气(电石)和焊剂]的质量符合国家标准(或相关标准)。
4 .钢材、焊条、焊丝等均应有制造厂的质量合格证。
凡无质量合格证或对其质量有怀疑时,应按批号抽查试验。
合格后方可使用。
5 .焊条、焊丝的选用,应根据母材的化学成分、机械性能和焊接接头的抗裂性、碳扩散、焊前预热、焊后热处理以及使用条件综合考虑。
5.1 同种钢材焊接时,焊条(焊丝)的选用,一般符合下列要求:5.1. 焊缝金属性能和化学成分与母材相当。
5.2. 工艺性能良好。
5.2 异种钢材焊接时,焊条(焊丝)的选用,一般符合下列要求:(1)两侧之一为奥氏体不锈钢时,可选用含银量较高的不锈钢焊条(焊丝)。
(2)两侧钢材均为非奥氏体不锈钢时,可选用成分介于二者之间或合金含量低的一侧相配的焊条(焊丝)。
6 .铝极氮弧焊用的电极、宜采用铀铝棒,所用的氮气纯度不低于99.95%o7 .氧-乙焕焊所用的氧气纯度应在98.5%以上。
乙焕气纯度应符合GB6819-86《溶解乙焕》的规定。
如以电厂制备乙块气,电石应有出厂证明书,其质量可采用检查焊缝金属中的硫、磷含量(按被焊金属标准)的方法来确定;用于焊接的乙块气,应进行过滤,未经检查或杂质含量超过标准的电石,不得用于受监部件的焊接。
8 .埋弧自动焊用的焊剂应符合有关标准技术要求。
二.焊前准备1焊口的位置应避开应力集中区且便于施焊及热处理,一般应符合下列要求:1.1 锅炉受热面管子焊口,其中心线距离管子弯曲起点或汽包、联箱外壁以及支吊架边缘至少70mm,两个对接焊口间距离不得小于150mm。
1.2 管道对接焊口、其中心线距离管子弯曲起点不得小于管子的外径,且不小于IOOmm(焊接、锻制、铸造成型管件外),距支吊架边缘至少50mm,两个对接焊口间距离不得小于管子的直径,且不得小于150mm o1.3 管接头和仪表插座一般不可设置在焊缝或热影响区内。
钢制管件工艺规程

紧两端螺丝,用校针对三通支管外圆进行相应的校正。
50 对三通支管进行车削、倒角。
60 对倒角好的三通进行初检,确认合格后进入下一个工作循环。
材料名称 无缝钢管 材质
注意事项
1.选择合理转速及切削用量, 速度过快,切削量过大,容易 使三通管脱离卡盘; 2.车削薄壁三通管时,应选择 相应的塞铁以防三通管在夹紧 过程中变形。
以使吹掉溶化的金属形成初始的切口,然后再将割炬嘴垂直于钢管表面切割
60 切割停止时,应松开割炬开关,再将割炬离开钢管。
70 进入下一个工作循环。
材料名称 无缝钢管 材质
注意事项
1.松开陶瓷喷嘴前,必须先切 断电源开关 ,严禁开机状态更 换电极导电嘴; 2.切钢管内线时,应在起点钻 一小孔,以免损坏电嘴; 3.切割中若发现等离子弧有异 常现象,应停止切割,并进行 检查。
20 接通电源,指示灯亮,顺序按¡ 电机一起动¡ 、¡ 电动三起动¡ 按钮,检查
控制油压力表调定在1.6Mpa。
30 将工作横梁回程作空行程运转,检查各按钮开关、阀门、限位开关是否灵活
可靠,确定液压系统工作正常。
40 安装并调整好所要推制的弯头模具,拧紧各紧固件螺丝。
50 按¡ 合模¡ 和¡ 松模¡ 按钮,检查限位开关及慢行程开关是否灵活可靠,合
按钮顶出缸复位。
15 确认成型三通符合标准时,再进行下一个工作循环。
材料名称 无缝钢管 材质 注意事项
碳钢、合金钢、奥氏体不锈钢
设备
工艺装备
三通管挤压机
三通模具
二硫化钼 粉
游标卡尺
标记 处数 更改文件号 签字 日期 标记
处数
设计(日期) 审核(日期) 更改文件号 签字 日期
换热器管束渗铝技术在炼油厂的应用
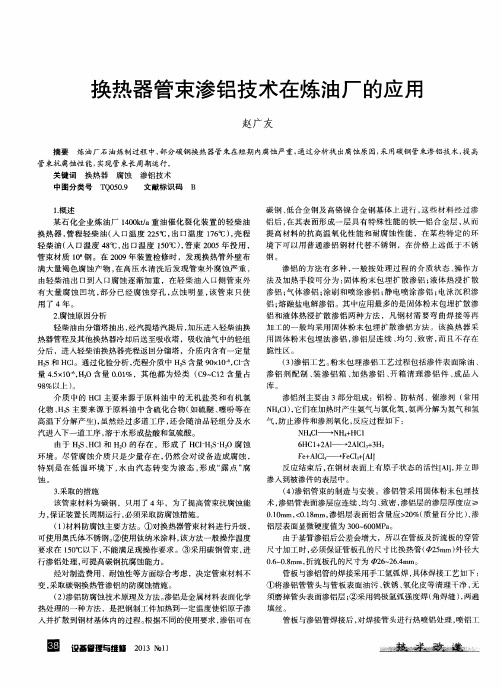
管板与渗铝管 的焊接采用手工氩弧焊 , 具体焊接工艺如下 :
变, 采取碳 钢换热管渗铝 的防腐蚀措施 。
( 2 ) 渗铝防腐蚀技术原理及方法 。 渗铝是金属材料表面化学 热处理的一种方法 ,是把钢制工件加热到一定温度使铝原子渗 入并扩散到钢材基体 内的过程。 根据不同的使用要求 , 渗铝可在
特 别是 在 低温 环境 下 , 水 由汽态 转变 为液 态 , 形成“ 露点 ” 腐
蚀 。
F e + A l C l 『 _ —+ F e C l [ A l 】
反应结束后 , 在 钢材表面上有原子状态 的活性[ a l 1 , 并立 即 渗入到被渗件 的表层中。
3 . 采 取 的 措 施
满 大量褐色腐蚀 产物 , 在高压水 清洗后发 现管束外腐 蚀严重 , 由轻柴油 出 口到入 口腐蚀 逐渐加重 ,在轻 柴油人 口侧 管柬外 有 大量腐 蚀 凹坑 , 部分 已经腐蚀 穿孔 , 点 蚀 明显 , 该 管束 只使
用 了 4年 。
渗铝 的方 法有多 种 , 一般按处理 过程 的介 质状态 、 操作方 法及加热手段可 分为 : 固体粉末包埋 扩散渗铝 ; 液体热浸 扩散 渗铝 ; 气体 渗铝 ; 涂刷和喷涂渗 铝 ; 静 电喷涂渗 铝 ; 电泳沉积 渗
经对制造费用 、耐蚀性等方面综合考 虑 ,决定管束材料 不
铝层表面显微硬度值为 3 0 0 ~ 6 0 0 MP a 。 由于基管渗铝后公差会增大 ,所以在 管板及折流板的穿管
尺寸加工时 , 必 须 保 证 管 板 孔 的 尺 寸 比换 热 管 (  ̄ b 2 5 m m) 外径大 0 . 6 ~ 0 . 8 m m, 折 流 板 孔 的 尺寸 为 2 6 ~ 2 6 . 4 mm。
薄壁不锈钢换热管与管板焊接工艺
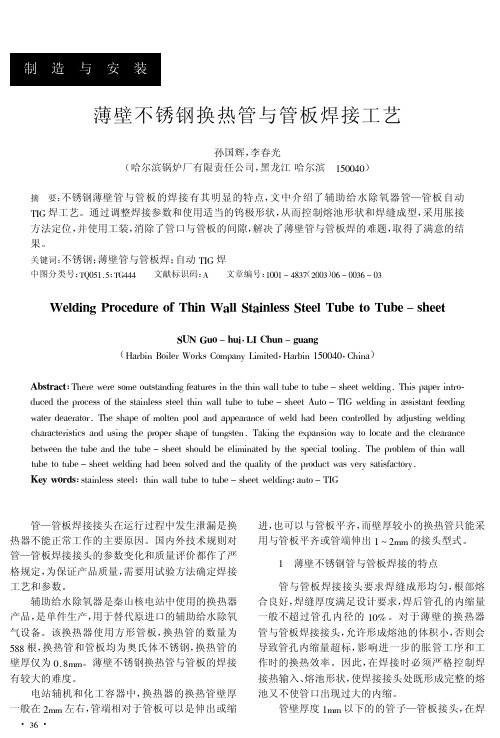
277。
=&! 材料 管和 管 板 材 料 和 规 格 分 别 为: 管 335>!;?9!3 管板 335>!B?9!! !C 2"77。 @!4 A 3&;77, =&" 接头形式 按设计要求的有效焊缝厚度应不小于 ! 倍的管 壁厚度即大于等于 3&;77。为此, 按上述要求, 管板 不需要倒角。因管壁较薄, 焊后无法保留管端, 管端 伸出管板的长度确定为 !&2 < "77。 =&= 焊接参数 焊接参数是否适当直接影响焊接质量, 焊接参 数的调整是制定焊接工艺的重要依据。对于管—管 板的焊接, 焊接参数对接头内在质量和外观成形均 有影响 (特别是钨极与管板的相对位置等) 。根据结 构特点, 通过试验采用了如表 " 所示的参数, 取得了 满意结果。
管与管板采用胀接的定位方式。
图!
钨极尖端形状
机械胀定位后, 管端与管板间仍然存在间隙, 为 防止管端向内翻边, 焊接前用工装将管端与管孔贴 合紧密, 使焊接过程中管端与管孔温度保持一致, 同 时熔化, 形成共同的焊接熔池而达到焊接的目的。
・ =E ・
>?/2
薄壁不锈钢换热管与管板焊接工艺
/@A!& B C@$ !&&"
摘
!"##$#)
不锈钢薄壁管与管板的焊接有其明显的特点, 文中介绍了辅助给水除氧器管—管板自动 要:
从而控制熔池形状和焊缝成型, 采用胀接 %&’ 焊工艺。通过调整焊接参数和使用适当的钨极形状, 方法定位, 并使用工装, 消除了管口与管板的间隙, 解决了薄壁管与管板焊的难题, 取得了满意的结 果。 不锈钢; 薄壁管与管板焊; 自动 %&’ 焊 关键词:
管壳式换热器换热管与管板焊接工艺

管壳式换热器换热管与管板焊接工艺摘 要:通过对换热管与管板焊接工艺的介绍,提出了一种行之有效的减少焊接变形的方法。
关键词:管板接头;氩弧焊;焊接单元;水压试验中图分类号:TE965:TG 441 文献标识码:B 文章编号:1002-3607(2002)04-0014-020 概述某工程建筑项目中,需制作沥青加热器、冷却器等设备,其壳体直径800mm ,长度6000mm ,主体材质Q235-B ,壳程设计压力0.6MPa ,管程设计压力0.5MPa ,属一类压力容器。
其中换热管469根,以8根拉杆固定在管板上,管板厚度δ=57mm ,管板孔径<25.4mm ,呈等边三角形均布,具体结构如图1所示。
图1 换热器管板孔具体结构换热管与管板的焊接接头质量好坏,直接影响换热器制造质量,一方面接头质量差容易发生泄漏,影响换热器的正常使用,另一方面,若是管板因焊接产生过大的变形,则会影响到管板与设备法蓝密封面的密封效果。
因此,管板焊接除应制定合理的焊接工艺外,还应采取措施,控制焊接变形。
1 焊接工艺评定根据G B151-1999《管壳式换热器》的要求,对于换热器的管束与管板焊接必须进行焊接工艺评定,制定合格的焊接工艺规程。
1.1 焊接方法的选择管板接头的形式如图2所示。
图2 管板接头形式因管子略高于管板且管子间距较小,采用钨极氩弧焊焊接工艺能保证成形美观,但对工件接头处的清洁度要求高(否则易产生气孔),因此焊前必须对接头处的油污、锈蚀作认真的清理。
1.2 焊接材料的选择根据管板材质Q235-B ,换热管材质20#,选择H08Mn2SiA 为焊接填充材料。
1.3 焊接工艺的确定按G B151制备试板和试管管束,试板厚度δ=60mm ,试管规格<25×2.5,组对前将试板与试管表面的油、污、锈等杂质清理干净,点焊采用钨极氩弧焊,焊材为H08Mn2SiA ,每个接头点两处,点焊位置在图3中的3点和9点位置。
1Cr5Mo换热管与12Cr2Mo1管板焊缝焊后热处理工艺_丁颖

硬度分别 为 186H B 、 197H B、 182H B 和 189H B, 完 全满足产品硬度不大于 225H B 的技术要求 , 证明笔 者采用的焊后最终热处理工艺是正确的。
4
结语
对 不 同 热 处 理 工 艺 对 1Cr5Mo 换 热 管 与 12Cr 2Mo 1 管板焊缝硬度的影响进行了工 艺试验, 发现随着加热温度的增高, 焊缝硬度逐渐降低, 电加 热带热处理后 焊缝硬度比炉内热处理 后焊缝硬度 高。换热管与管板的焊后热处理优先选用炉内热处 理 , 如果确实无法实现可采用电加热带加热。采用 文中方案进行焊后最终热处理后, 管头硬度完全达 标 , 证明了热处理工艺的正确性 , 可为同类设备的处 理提供借鉴。
JB/ T 4709 2000 钢制压力容器焊接规程 中 规定 , 1Cr 5Mo 的焊 后热 处理 温度 不 小于 660 , 12Cr2M o1R 焊后热处理温度也为不小于660
[ 13]
。
现场检测管头焊缝处硬度较高 , 说明焊后最终热处 理加热温度 ( 700 10) 较低, 需要提高加热温度 , 通过焊后热处理来消除焊接应力并使焊缝硬度降低 到 225H B 以下。
参考文献 : [ 1] [ 2] [ 3] 丁 祁 丁 颖 , 刘大 博 . 00Cr22N i5M o3N 双 相不 锈钢 封头 固 飞 , 刘国振 , 贾晓 艳 . 固定管 板式换 热器热 处理 有 颖, 马 卓 . 螺 纹锁紧环换热器管箱筒体锻件的 热 溶热处理 [ J] . 石油化工设备 , 2010, 39( 2) : 66 - 68. 关问题的探讨 [ J] . 河南化工 , 2010, ( 8) : 31 - 32. 处理[ J] . 石油化工设备 , 2010, 39( 1) : 64 - 67. [ 4] [ 5] 曲桂英 , 刘长林 . 换 热器管板的手工电弧堆焊及热处 理 [ J] . 机械设计与制造工程 , 2001, ( 3) : 80 - 81, 84. 党兆凯 , 周 ( 4) : 63 - 66. [ 6] 康继东 , 谭 ( 8) : 10 - 12. [ 7] 张 海 龙, 朱 瑞 龙, 贾 ( 增 ) : 40 - 43. [ 8] 石晓霞 , 郭 兆成 , 乔 爱云 . 1Cr5M o 合金 钢管 热处 理 工 艺研究[ J] . 包钢科技 , 2010, ( 5) : 17 - 19. [ 9] 曲桂英 , 刘长林 . 换 热器管板的手工电弧堆焊及热处 理 [ J] . 机械设计与制造工程 , 2001, ( 3) : 80 - 81, 84. [ 10] [ 日 ] 铃 木春 羲 . 钢 材 的焊 接裂 纹 [ M ] . 梁 桂芳 , 译 . 北 京 : 机械工业出版社 , 1981. [ 11] 张康达 , 洪起超 . 压力容器手 册 [ M ] . 北京 : 劳动人事 出 版社 , 1987. [ 12] 大连工学 院 金 属学及 热处理 编写 小组 . 金属 学及 热 处理 [ M ] . 北京 : 科学出版社 , 1975. [ 13] JB/ T 4709 2000, 钢制压力容器焊接规程 [ S] . [ 14] 周 岐 , 王亚君 . 电焊工操作 技能问答 [ M ] . 北京 : 中 国 ( 张编 ) 电力出版 社 , 2008. 艳 , 等 . 12Cr2M oG 换 热 管 与 12Cr 2M o 1 管板焊 接工 艺 [ J] . 石油 化工设 备 , 2010, 39 华, 王 蕾 , 等 . 1Cr5M o 钢管道 焊后热 处 理质量评定指标研究 [ J] . 理化检验 ( 物理 分册 ) , 1999, 琦 , 徐继承 , 等 . 在用加氢反应器现场焊 接 修理后的 消除应力热处理 [ J] . 石油 化工设备 , 2010, 39
BFe30/16MnⅢ管壳式换热器换热管与管板接头的焊接工艺
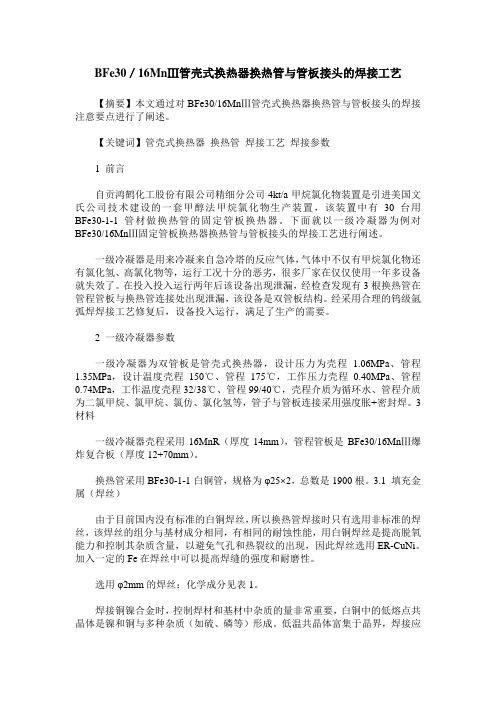
BFe30/16MnⅢ管壳式换热器换热管与管板接头的焊接工艺【摘要】本文通过对BFe30/16MnⅢ管壳式换热器换热管与管板接头的焊接注意要点进行了阐述。
【关键词】管壳式换热器换热管焊接工艺焊接参数1 前言自贡鸿鹤化工股份有限公司精细分公司4kt/a甲烷氯化物装置是引进美国文氏公司技术建设的一套甲醇法甲烷氯化物生产装置,该装置中有30台用BFe30-1-1管材做换热管的固定管板换热器。
下面就以一级冷凝器为例对BFe30/16MnⅢ固定管板换热器换热管与管板接头的焊接工艺进行阐述。
一级冷凝器是用来冷凝来自急冷塔的反应气体,气体中不仅有甲烷氯化物还有氯化氢、高氯化物等,运行工况十分的恶劣,很多厂家在仅仅使用一年多设备就失效了。
在投入投入运行两年后该设备出现泄漏,经检查发现有3根换热管在管程管板与换热管连接处出现泄漏,该设备是双管板结构。
经采用合理的钨级氩弧焊焊接工艺修复后,设备投入运行,满足了生产的需要。
2 一级冷凝器参数一级冷凝器为双管板是管壳式换热器,设计压力为壳程 1.06MPa、管程1.35MPa,设计温度壳程150℃、管程175℃,工作压力壳程0.40MPa、管程0.74MPa,工作温度壳程32/38℃、管程99/40℃,壳程介质为循环水、管程介质为二氯甲烷、氯甲烷、氯仿、氯化氢等,管子与管板连接采用强度胀+密封焊。
3 材料一级冷凝器壳程采用16MnR(厚度14mm),管程管板是BFe30/16MnⅢ爆炸复合板(厚度12+70mm)。
换热管采用BFe30-1-1白铜管,规格为φ25×2,总数是1900根。
3.1 填充金属(焊丝)由于目前国内没有标准的白铜焊丝,所以换热管焊接时只有选用非标准的焊丝,该焊丝的组分与基材成分相同,有相同的耐蚀性能,用白铜焊丝是提高脱氧能力和控制其杂质含量,以避免气孔和热裂纹的出现,因此焊丝选用ER-CuNi。
加入一定的Fe在焊丝中可以提高焊缝的强度和耐磨性。
换热管与管板连接通用工艺规程

换热管与管板连接通用工艺规程1 主题内容与适应范围1.1本规程规定了钢制管壳式换热器换热管与管板连接的方法和要求。
1.2本规程适用于本公司制造的碳素钢、低合金钢、不锈钢等材料制管壳式换热器的换热管与管板的连接。
其它材料制造的换热器的换热管与管板的连接亦可参照执行。
2总则2.1换热管与管板连接接头的制造除符合本规程的规定外,还应遵守国家颁布的有关法令、法规、标准、本公司其它相应规程和图样及专用工艺文件的要求。
2.2换热管与管板连接的连接方式有胀接、焊接、胀焊并用等型式。
具体连接方式在图样或公司技术部门在制造专用工艺中规定。
3一般要求3.1当换热管与管板采用胀接连接时,换热管材料的硬度值一般须低于管板材料的硬度值10~20HB,除换热管材料为不锈钢或有应力腐蚀场合外,可采用管端局部退火的方式来降低换热管材料的硬度。
3.2管孔表面粗糙度a)当换热管与管板焊接连接时,管孔表面粗糙度Ra值不大于25μm,且符合图样要求;b)当换热管与管板胀接连接时,管孔表面粗糙度Ra值不大于12.5μm,且符合图样要求,同时管孔表面不得有影响胀接紧密性的缺陷,如贯通的纵向或螺旋状刻痕等。
3.3连接前,连接部位的换热管与管板表面应采用机械或化学方法清理干净,不应留有影响胀接或焊接连接质量的毛刺、铁屑、锈斑、油污等。
a) 穿管前,应对换热管进行机加工平头,平管公差L+1㎜。
b) 穿管前,应采用钢丝刷、钢丝轮、砂纸将换热管管头(包括管口端部)毛刺、铁屑、锈斑、油污去除干净,至呈金属光泽。
用于焊接时,换热管刷管范围不小于换热管外径尺寸,且不小于25㎜;用于胀接时,换热管应呈现金属光泽,其长度应不小于二倍的管板厚度。
刷管后,换热管应放置在干燥通风处,已经刷管处理的换热管必须在7天内与管板进行胀接或焊接连接,否则应重新进行刷管处理。
c) 换热管的外伸长度,按产品焊接工艺规程执行。
对需打磨的管头要求打磨平整,不得有卷边现象,并用机械或化学方法清除管板、管端表面残留的砂轮灰等杂物。
铝热焊操作指导书

铝热焊接工艺介绍目录铝热焊接工艺介绍 (1)一、引言 (1)二、铝热焊接的技术原理 (2)2.1定义 (2)2.2原理 (2)三、铝热焊接的应用特点 (3)四、铝热焊接的操作方法: (3)4.1焊接操作 (4)4.2注意事项: (5)4.3常用模具型号 (6)一、引言铝热焊接技术可追溯到19世纪后期,当时德国就有人用铝作为氧化铁的还原剂来制作铸件和修补铸件。
20世纪初,德、英、美、法等国开始将铝热焊法付诸于钢轨的焊接,到50-60年代铝热焊接已是钢轨接头无缝焊接的普通技术。
该技术具有设备简单、投资少、焊接作业快,不需要大功率的电源,操作简便等特点,特别适用于野外施工和利用行车间隔的定点抢修,因而在各国发展很快。
我国在1958年开始试验研究并于1960年4月首次采用自制铝热焊剂进行了钢轨接头的焊接。
1966年开始批量生产钢轨铝热焊剂。
到1982年,我国已焊接了8000多公里无缝线路。
铝热焊接的商品名称为CADWELD,这是为了纪念查尔斯·卡特威尔博士(Dr. CharlesCaldwell) 1938年首次将这一技术应用到有色金属上。
目前铝热焊接应用领域有:钢轨焊接;铜芯电缆连接;接地极导线连接;铁路信号线的连接。
随着管道事业的发展、高压、薄壁高强度管道钢的应用,对焊接的热影响区有着更加苛刻的要求,NACE(美国腐蚀工程师协会)通过大量试验认定铝热焊可以应用在高强度的输油、气管道上,已列进了标准ANSI B31.4及31.8。
在接地连接技术中,IEEE(国际电工协会)第80号标准也推荐采用CADWELD技术。
在国内近几年颁布的防蚀标准中,电缆铝热焊接技术也是首选技术,如SYJ 36-89。
二、铝热焊接的技术原理2.1定义铝热焊接(也称热剂焊)就是利用金属氧化物和金属铝之间的放热反应所产生的过热熔融金属来加热金属而实现结合的方法。
铝热焊接是一种把两个或是多个导体或是多个导体焊接起来的焊接工艺,此工艺多用于阴极保护中管道与管道之间的连接;铝热焊接工艺通常是铝热焊剂和铝热焊模两者的组成品。
管道焊接工艺规程WPS

Ar
99. 99%
8~10L/min
Interpass temp max
最大层间温度
≤200℃
Trailing
尾部保护气
NO
NO
NO
Preheatmethod
预热方法
/
Backing
背部保护气
NO
NO
NO
ELECTRICAL CHARACTERISTICS电特性
Current电流AC或DC直流DCPolarity极性正接EN反接EP
Other其它:无
Weld Layer(s)
焊层
Process
焊接
方法
Filler Metal
填充金属
Current(A)电流
Volt.Range
(V)电压
范围
Travel Speed Range(cm/min)
焊接速度范围
Note
备注
Class
种类
Dia.(mm)
直径
Polarity
极性
Amp.Range
Thickness厚度范围:Base Metal母材:Groove坡口焊1.5~14mmFillet角焊不限制
Pipe Dia.管子直径范围:Groove坡口焊不限制Fillet角焊不限制
Other其他此工艺规程适用于壁厚≤3.91mm或管道直径≤2寸,且管道等级为以上所列的碳钢管道
FILLER METALS填充金属
注:立焊、仰焊电流小于上述15-20%。所有焊缝GTAW至少焊接2层,且不允许自熔。
Initiated by编制:
Date日期:
Reviewed by审核:
Date日期:
生产工艺钢管焊接工艺操作规程

生产工艺钢管焊接工艺操作规程1 编制依据1.1工业金属管道工程施工及验收规范GB50235-971.2生产运作控制程序HY-QP-082 范围和条件2.1适用于给水、煤气、热力钢管道接口焊接工序。
2.2该工序的前道工序必须经检验合格。
3 钢管接口焊接3.1管道焊接的焊工必须持有地、市以上劳动部门近期颁发的焊工合格证(有效期三年),凡中断焊接工作六个月以上的焊工在施工前均须参加考核,合格后方可施焊。
3.2每个焊工均应有各自的代号并注册备案,施焊后,在离焊缝100mm处打上焊工的代号。
3.3焊接钢管应根据母材型号选用相应的焊条。
焊接进口钢管,应预先进行焊接性能试验,以确定焊条型号。
3.4在使用焊条前,应检查焊条。
如有药皮不均匀,有气孔、裂纹、生锈、受潮的均不能使用。
外观合格的焊条,应参照说明书进行烘干。
随用的焊条应放在焊条桶内。
3.5钢管在焊接前,必须按下列要求进行选配:3.5.1相邻两管口其圆周长误差不得大于6mm,以保证接口错边符合要求。
3.5.2管口要圆,不圆度误差不超过±2mm。
3.5.3钢管切口与钢管的中心线不垂直度的偏差(切斜)不得大于1.5mm。
3.5.4钢管切口要求平齐,凹凸误差不超过±1mm,局部不平整长度不超过50mm,总长度不超过圆周的10%。
3.6钢管组装时应注意以下几点:3.6.1钢管组装前必须进行清扫,管内不得有泥土、石块、杂物、焊条等,且不应有积水。
钢管坡口应无毛刺及粘有汚物等。
3.6.2两环向焊缝间短管长度不应小于钢管直径,且不得小于100mm。
3.6.3直径大于DN100mm的有缝管组装时,两管管口处的纵向焊缝至少错开100mm,遇有特殊情况无法满足上述规定时,应采取加强焊接。
3.6.4组装管口的接口错边不超过较薄管壁厚的1/5。
3.6.5在干管上开孔连接支管时,开孔边缘距离管体焊缝不少于100mm。
3.6.6管端坡口附近10mm范围内,内外表面应清刷至露出金属本色,以保证坡口形式。
机组管路焊接规程
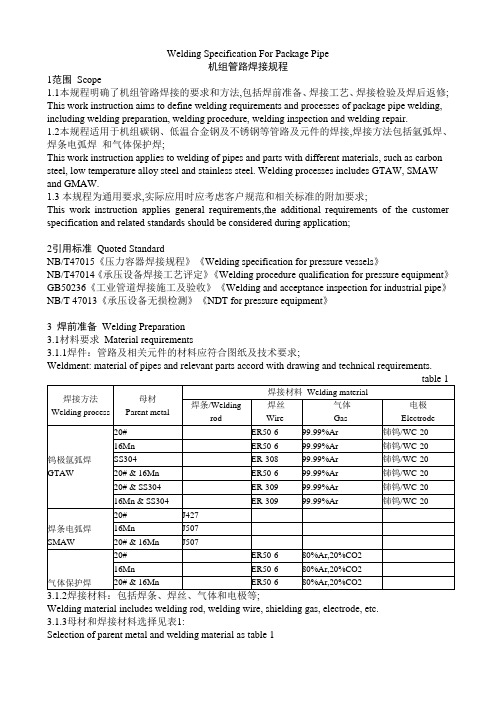
Welding Specification For Package Pipe机组管路焊接规程1范围Scope1.1本规程明确了机组管路焊接的要求和方法,包括焊前准备、焊接工艺、焊接检验及焊后返修; This work instruction aims to define welding requirements and processes of package pipe welding, including welding preparation, welding procedure, welding inspection and welding repair.1.2本规程适用于机组碳钢、低温合金钢及不锈钢等管路及元件的焊接,焊接方法包括氩弧焊、焊条电弧焊和气体保护焊;This work instruction applies to welding of pipes and parts with different materials, such as carbon steel, low temperature alloy steel and stainless steel. Welding processes includes GTAW, SMAW and GMAW.1.3本规程为通用要求,实际应用时应考虑客户规范和相关标准的附加要求;This work instruction applies general requirements,the additional requirements of the customer specification and related standards should be considered during application;2引用标准Quoted StandardNB/T47015《压力容器焊接规程》《Welding specification for pressure vessels》NB/T47014《承压设备焊接工艺评定》《Welding procedure qualification for pressure equipment》GB50236《工业管道焊接施工及验收》《Welding and acceptance inspection for industrial pipe》NB/T 47013《承压设备无损检测》《NDT for pressure equipment》3焊前准备Welding Preparation3.1材料要求Material requirements3.1.1焊件:管路及相关元件的材料应符合图纸及技术要求;Weldment: material of pipes and relevant parts accord with drawing and technical requirements.Welding material includes welding rod, welding wire, shielding gas, electrode, etc.3.1.3母材和焊接材料选择见表1:Selection of parent metal and welding material as table 13.2坡口准备及焊件装配Groove preparation and weldment assembly3.2.1对接焊时,焊件厚度小于2mm 时可不开坡口,厚度大等于2mm 时应开单边30º~40 º,钝边0.5~ 1.0mm 的V 型坡口,坡口一般采用机械方法加工,端面应保持平整,不得有裂纹、分层、夹杂及毛刺等;When weldment thickness for butt welding is less than 2mm, groove isn’t needed, and when weldment thickness for butt welding is more than 2mm, V shape groove is needed, single-groove angle should be 30 to 40 degrees, blunt edge should be 0.5 to 1mm. usually, grooves are cut by mechanical method, the face keeps smooth, there is no crack, layering, inclusion, burr, etc.坡口形式及组对间隙等参数如下图:Groove shape and clearance norms as below:3.2.21/4(最大为3mm)时,两被焊件之间要有3:1 的斜坡过渡;此斜坡过渡一般采用机械方法在较厚件上加工,加工后的斜坡端部应与较薄件良好配合;When butt welding with different thickness weldments, if the thickness difference is more 1/4 time of the thinner weldment (Maximum 3mm), there is a slope of 3:1 for transition between the two welded parts. Usually, mechanical method is used for slope machining on the thicker weldment. The slope end should adapt to the thinner weldment.3.2.3对接焊时,组对后的管口错边量应小于焊件壁厚的10%且最大不超过1mm;承插焊时,径向组对间隙应小于 1.5mm;当机组的油路采用承插焊时,承口与插口的轴向不宜留间隙; When butt welding, the align deviation value is less than 10% of weldment thickness and the maximum value is 1mm.When socket welding, radial direction clearance is less than 1.5mm. When socket welding for oil pipes of package, there should be no axial clearance between sockets.3.2.4焊件装配前应将坡口及内外表面两侧各15~20mm 范围清理干净;不得有水、铁锈、油污和其它有害杂质;The outside and inside surfaces of weldments which are 15 to 20 mm distant from the groove end need to be cleaned. There should be no water, rust, oil and any other detrimental impurity.3.2.5焊件用氩弧焊定位点焊时,一般可沿管周均匀点焊四处,定位焊的厚度一般不超过焊缝正常厚度的一半,以熔化钝边为宜;定位焊应保证质量,不得有裂纹,否则应清除重焊,如存在未熔合、未焊透、气孔、夹渣等缺陷时亦应清除;When tack welding with GTAW, generally, 4 welding spots should be evenly distributed around the pipe, welding spot thickness is less than half of the normal seam thickness and it should melt the rootface.Tack weld quality must be guaranteed and there should be no incomplete fusion, incomplete penetration, pore, slag, etc. , otherwise re-weld is needed.3.2.6焊接带有塑料、橡胶、钎焊接头等不耐高温的焊件时(如阀门、板换等),应先将不耐热部位拆下后焊接,或者采取适当的降温措施(如用湿布包裹、浸入水中等)后采用小电流多层焊的方式进行焊接;When joining weldments with plastic, rubber, brazed join ts, etc., which don’t resist heat ( such as valves and plate heat exchanger ), the parts don’t resist heat which should be removed, andappropriate cooling actions should be taken, such as wrapping stupe or dipping in water, then low current and multilayers welding method is used to join.4焊工和焊接防护Welder And Welding Protection4.1焊接工作应由有相应资格的焊工担任,焊工焊前应熟悉图样、技术条件、工艺文件和本标准的要求,对装配不合格的焊件,焊工应不予焊接; Welders must be qualified and they need to be familiar with drawings, technical specification, process documents and this work instruction. Welders can reject welding if the weldment assembly is poor.4.2焊工在进行焊接作业前必须穿戴好相应的劳保护具,检查焊接电源、气源有无漏电、泄漏等危险隐患,如果存在隐患,必须先消除后才能开始焊接;Welders should wear protection articles, check welding power source and gas source before welding operation. If there is any hidden danger, it must be eliminated.4.3当焊接场所环境温度低于0℃时,应在坡口两侧100mm范围内预热到手感温度(15℃左右)为宜(黑色金属可不预热),焊接场所环境温度低于-11℃,16Mn等低合金钢要预热到100~150℃左右才能进行焊接,当环境温度低于-18℃时不应进行焊接操作;When environment temperature is lower than 0 Celsius degree, pre-heat is needed and it should be up to hand temperature (about 15 Celsius degrees) on both of the groove sides which is 100mm distance to th e groove end. (Black metal don’t need to be pre-heated). When environment temperature is lower than subzero 11 Celsius degrees, low alloy steel such as 16Mn need to bepre-heated to 100 to 150 Celsius degrees. When environment temperature is lower than subzero 18 Celsius degrees, welding must be stopped.4.4焊条电弧焊工作场地风速小于10m/s,氩弧焊工作场地风速应小于2m/s,否则应有适当的防风措施; Wind speed should be less than 10m per second on SMAW worksite and wind speed should be less than 2m per second on GTAW worksite, otherwise wind prevention action is needed.5焊接工艺规范Welding Procedure Specification5.1各种不同材质及规格的管路焊接方法选择表2:Welding process selection of different materials and different sizes as table 2:5.2管路焊接时打底焊用钨极氩弧焊,工艺参数如表3:Welding procedure parameters of GTAW for root passes as table 3:Welding procedure parameters of GTAW for intermediate passes and cover passes as table 4:5.4 管路焊接时填充或盖面焊用焊条电弧焊,工艺参数如表5:Welding procedure parameters of SMAW for intermediate passes and cover passes as table 5:5.5 管路焊接时填充或盖面焊用气体保护焊,工艺参数如表6:Welding procedure parameters of GMAW for intermediate passes and cover passes as table 6:6焊后检查与返修Post Weld Inspection And Repair6.1焊后外观检查Post weld visual inspection6.1.1焊后由焊工对焊缝外观进行检查,主要检查焊缝成型,有无表面缺陷(气孔、咬边等),目视检测焊缝尺寸(焊脚高度、焊缝余高、宽度等);Welders do post weld visual inspection, including weld appearance, surface defects (pore, undercut, etc.), weld dimension (weld leg, reinforcement, width)6.1.2外观检查前焊工应去除飞溅、焊渣等异物,并将焊缝及热影响区表面用钢丝轮抛光(焊件油漆等因受热碳化、起泡的部位也要清理干净);Welders should clean surface dirt including welding spatter, slag, etc., clean the surface of weld and heat affected zone with steel wire wheel before post weld visual inspection (The paint on weldments’ surface is heated to carbonization or blister which also should be cleane d).6.2无损检测(射线检测)NDT(RT)6.2.1射线检测评定方法和评定级别:无损检测的方法及质量评定应符合JB/T4730《承压设备无损检测》的规定,二级片及以上为合格;Radiographic test evaluation method and grade: method and quality grade of NDT accords toJB/4730《NDT for pressure equipment》, higher than Grade Ⅱof the radiographic test film is accepted.6.2.2拍片比例:按照项目抽检焊缝进行射线照相,抽检比例不少于5% ;如客户有特殊要求,则按照客户要求比例进行无损检测;RT Ratio: do random inspection with RT for every project, the inspection ratio is no less than 5% of welds. Do non-destructive test according to customer’s require d ratio if the customer has some special requirements.6.2.3一次通过率统计:按照射线照相底片数量进行统计,合格率为90% ,当合格率低于90%时,另增加该项目管路上10%的焊缝进行扩拍;FPY: statistic according to RT film quantity, higher than 90% of FPY is accepted. If FPY is less than 90%, another 10% of welds need to be tested with RT.6.3焊后返修Post weld repair6.3.1焊缝表面缺陷由焊工自检后自行修补,但表面裂纹不得擅自处理,应及时申报焊接工程师,确定返修方案后再行处理;Welders repair normal surface defects by themselves. If some surface cracks, welders need to report to welding engineer who makes out repair procedure.6.3.2焊缝余高过高、表面成型不良、表面气孔夹渣、小于壁厚5%且最深不超过0.5mm 的咬边、大管径对接焊的根部凸出等缺陷可以直接用砂轮进行打磨整修,打磨后的焊件外观要平滑过渡;Defects including higher reinforcement, poor forming, surface porosity and slag, undercut with less than 5% of thickness and no more than 0.5mm of depth, root bulging of large diameter pipes with butt welding, etc., can be repaired by grinding wheel, the weldment appearance need be smooth for transition after grinding.6.3.3未焊透、未熔合、较深的气孔夹渣等缺陷应将缺陷彻底清除后补焊;Defects including incomplete penetration, incomplete fusion, deeper pore, slag, etc., need to be eliminated and repaired.6.3.4焊缝缺陷可用碳弧气刨、砂轮或其它机械方法清除,不允许用电弧或气割火焰熔除,使用碳弧气刨时应磨去渗碳层;Weld defects can be removed by gouging, grinding or other mechanical methods, arc cutting and gas cutting are not allowed, and carburized layer must be removed.6.3.5焊缝同一位置修补次数不应超过两次,第三次修补必须经焊接工程师批准;It is not allowed to repair twice for one weld seam, the third time repair must be approved by welding engineer.6.3.6修补后,应按原焊缝的质量要求对修补处及其附近进行质量检查The repaired weld seams must be checked according to the former weld quality requirement.。
- 1、下载文档前请自行甄别文档内容的完整性,平台不提供额外的编辑、内容补充、找答案等附加服务。
- 2、"仅部分预览"的文档,不可在线预览部分如存在完整性等问题,可反馈申请退款(可完整预览的文档不适用该条件!)。
- 3、如文档侵犯您的权益,请联系客服反馈,我们会尽快为您处理(人工客服工作时间:9:00-18:30)。
渗铝钢换热管与管板焊接规程
1. 将渗铝钢管管头与冷换管板表面油污、铁锈、氧化皮等清理干净,无须磨掉管头表面渗铝层,但需磨掉管头端面渗铝层,或下料切掉管头端面渗铝层,以防止管头端面含铝量过高,影响焊接质量。
2. 采用钨极氩弧强度焊(角焊缝),二遍填丝。
3. 第一便填丝建议使用焊丝规格型号为φ1.4-φ1.6mm JG—50(H08Mn2SiA),第二便填丝建议使用焊丝规格型号为φ2.0mm JG—50(H08Mn2SiA)钨极选用φ2.5-φ3.0mm。
如管板堆焊不锈钢时,焊丝材质建议使用H1Cr 24Ni13。
4. 渗铝管头应露出焊接端面2.5-3 mm,焊接电流应控制在第一便填丝120— 140A,。
第二便填丝160— 180A,管头焊后不准有烧损击穿。
修补焊缝也应采用氩弧焊。
5. 冷换管束管头与管板焊后应进行贴账,不允许强度胀。
以上焊接规程不能代替焊接工艺,使用单位要根据以上规程进行焊接工艺评定,确定焊接工艺,以确保焊接质量。
非常重要∶1. 渗铝管供货长度不小于6030mm,因穿管前要进行二次定尺下料,在焊接前应将非下料一端磨掉管头端面渗铝层,以防止管头端面含铝量过高,产生裂纹。
2. 管板及折流板孔加工公差尺寸应增加0.2mm。
φ25的渗铝管,保证管板孔径不小于φ25.6,折流板不小于φ25.9;φ19的渗铝管,保证管板孔径不小于φ19.6,折流板不小于φ19.9。
抚顺市天隆石化设备防腐厂技术科。