EE141_s09_hw6_solution
VMware虚拟SAN(vSAN)技术白皮书说明书

Ready NodesVMWare Virtual SANVMware's Virtual SAN (vSAN) brings performance, low cost and scalability to virtual cloud deployments running on HPE hardware. An issue the cloud deployment model raises is the problem of adequate storage performance to virtual instances. Spinning disks and limited bandwidth networks lower IO rates over local drives. VMware’s solution to this is vSAN, which adds a temporary local storage “instance” in the form of a solid-state drive to each server. vSAN extends the concept of local instance storage to a shareable storage unit in each HPE server, where additionally, the data can be accessed by other servers over a LAN. The benefits of VSAN include:• Increased performance due to local server access to Flash storage• Lower infrastructure cost by removing the need for networked storage appliances • Highly scalable --simply add more servers to increase storage • Eliminate boot storms since data is stored locally• Unified management --no storage silo versus server silo separation problemsMellanox 10/25G Ethernet interconnect solutions enable unmatched competitive advantages in VMware environments by increase efficiency of overall server utilization and eliminating I/O bottleneck to enable more virtual machines per server, faster migrations and speed access to storage. Explore this reference guide to learn more about how Mellanox key technologies can help improve efficiencies in your vSAN environment. Higher Efficiency RoCE CertifiedWithout Offloads With Mellanox Offloads Efficient Hardware OffloadsA variety of new workloads and technologies areincreasing the load on CPU utilization. Overlay networks protocols, OVS processing, access to storage and others are placing a strain on VMware environments. High performance workloads require intensiveprocessing which can waste CPU cycles, and choke networks. The end result is that application efficiency is limited and virtual environments as a whole become inefficient. Because of these challenges, data center administrators now look to alleviate CPU loads by implementing intelligent network components that can ease CPU strain, increase network bandwidth and enable scale and efficiency in virtual environments.Mellanox interconnects can reduce the burden byoffloading many networking tasks, thereby freeing CPU resources to serve more VMs and process more data. Side-by-side comparison shows over a 70% reduction in CPU resources and a 40% improvement in bandwidth.Reduce CPU OverheadvSphere 6.5, introduced Remote Direct Memory Access over Converged Ethernet (RoCE). RoCE allows direct memory access from one computer to another without involving the operating system or CPU. The transfer of data is offloaded to a RoCE-capable adapter, freeing the CPU from the data transfer process and reducing latencies. For virtual machines a PVRDMA (para-virtualized RDMA) network adapter is used tocommunicate with other virtual machines. Mellanox adapters are certified for both in vSphere.Without Offloads With OffloadsRoCE dramatically accelerates communication between two network endpoints but also requires a switch that is configured for lossless traffic. RoCE v1 operates overlossless layer 2 and RoCE v2 supports layer 2 and layer 3. To ensure a lossless environment, you must be able to control the traffic flows. Mellanox Spectrum switchessupport Priority Flow Control (PFC) and Explicit Congestion Notification (ECN) which enables a global pause across the network to support RDMA. Once RoCE is setup onvSphere close-to-local, predictable latency can be gained from networked storage along with line-rate throughput and linear scalability. This helps to accommodate dynamic, agile data movement between nodes.HPE StoreFabric M-series and Mellanox ConnectX adapter solutions for VMWareProven PerformanceRDMA for vSAN and Ne x t-Gen StorageRDMA (Remote Direct Memory Access) allows two system to connect sub-OS directly to memory without requiring CPU cycles. This enables high bandwidth, increased IOPS, and low latencyconnectivity, which accelerates workloads running on parallel systems better than traditional TCP/IP connectivity.RDMA benefits to vSAN clusters include:•Improved app performance•Improved resync/rebuild/rebalance time •NVMe-oF technology enablement •Better VM consolidation•Improves cloning and vMotion operations times •Faster metadata updates across vSAN hostsMellanox End-to-End vSAN SolutionHyperconvergedReduce CapExHypeconverged deployments, like HPE SimpliVity and HPESynergy, are a demandingenvironment for networkinginterconnects. These consist ofthree software components: compute virtualization, storage virtualization and management, in which all three require an agile and responsive network.Deploying on 25G networks, like offered with Mellanox ConnectX adapters, assists with offload capabilities to optimizeperformance and availability of synchronization and replication ofvirtualized workloads .CapEx Analysis: 10G vs 25G Mellanox adapters and switchesaccelerate VM resources to improveperformance, enhance efficiency and provide high-availability and are a must-have feature for any VMware and hyperconverged environment. Deployment ConfigsEthernet AdaptersNetwork ManagementHPE vSAN Ready node AF-86x HPE 640FLR-SFP2810/25 2p ConnectX-4Lx(included in ReadyNode bundle)Just Add HPE StoreFabric M-series ToR 2x HPE StoreFabric SN2010M18 x 10/25G SFP + 4 x 40/100G QSFP up ½ width ToR switch means Full HA in 1UvSAN vSphere VMVMVMVMVMVM VM3x HPE DL380 Gen10 with SAS Exp.36x 32GB DDR415x HPE 1.6TB SAS WI SFF SSD 75x HPE 3.2TB SAS MU SFF SSD3x HPE Smart Array P816-a Gen10 12G 3c Dual 8GB microSD USB kitSKU: DL380Gen10_Expander_SAS_AF8-1HPE vSAN ReadyNode RAUp to 80TB in 7U including ToR▪Enable near-native performance for VMs thru stateless offloads▪Extend hardware resources w/ ROCE (RDMA over converged Ethernet)▪Accelerate virtualized networks with VXLAN, GENEVE & NVGRE▪Align network services with compute services for multitenant network supportHPE 640SFP282p 10/25G Ethernet HPE 842QSFP281p 100G EthernetHPE Smart Fabric Orchestrator ▪Visibility –topology view + in-band activity monitoring▪Automation –template based deployment and self healing▪Compliance –Interop validation with HPE SPOCK▪Reports –Fabric Reports + Ad-hoc reportingMonitoring▪Performance monitoring ▪Health monitoring ▪Detailed telemetry ▪Alerts and notificationsThere are over 20 HPE vSAN ReadyNodes with Mellanox Adapters, including:RDMARDMAVMWare vSAN works BEST on Mellanox RDMA enabled adapters and switches•DL380Gen10_All_NVMe_AF4 –1•DL380Gen10_All_NVMe_AF4 –2•DL360Gen10_SAS_AF4 –1•DL380Gen10_SAS_AF4 –1•DL380Gen10_All_NVMe_AF6 –1•DL380Gen10_All_NVMe_AF6 -2•DL360Gen10_SAS_AF6 -1•DL380Gen10_SAS_AF6 –1•DL360Gen10_SAS_AF8 –1•DL380Gen10_All_NVMe_AF8 –1•DL380Gen10_All_NVMe_AF8 –2•DL380Gen10_Expander_SAS_AF8 -1•DL360Gen10_SAS_HY2-1•DL380Gen10_SAS_HY2 -1。
Agile e6 Upgrade Tool 3.0 用户指南说明书

1
Agile e6.0
Chapter 2 Architecture and Basic Concepts
Architecture
The upgrade tool is implemented in Java. The tool accesses the databases directly using a JDBC connection. The configuration of all upgrade steps is stored in a set of xml control files. In addition SQL scripts are used for special steps. The log and error files are mainly in XML format. The user can execute the migration steps easily from the user interface of the Upgrade Tool.
贝利莫电子无压依赖特性控制阀说明书
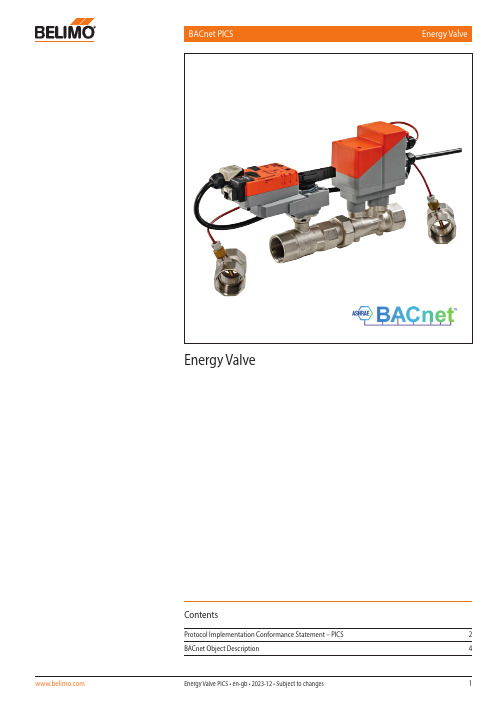
BACnet PICS Energy ValveEnergy ValveContentsProtocol Implementation Conformance Statement – PICS 2 BACnet Object Description 4General information Date26.01.2018Vendor Name BELIMO Automation AGVendor ID423Product Name Energy ValveProduct Model Number EV..R+(K)BAC, EV..R3+BAC, EV..F+(K)BACApplikations Software Version03.02-0000Firmware Revision12.25BACnet Protocol Revision 1.12Product Description Electronic pressure-independent characterisedcontrol valve with energy monitoringBACnet Standard Device Profile BACnet Application Specific Controller (B-ASC)Segmentation capability NoData Link Layer Options MS/TP masterBACnet IP, (Annex J)BACnet IP, (Annex J), Foreign DeviceDevice Address Binding No static device binding supportedNetworking Options NoneCharacter Sets Supported ISO 10646 (UTF-8)Gateway Options NoneNetwork Security Options Non-secure deviceConformance Listed by BTLBACnet Interoperability Building Blockssupported BIBBs Data sharing – ReadProperty-B (DS-RP-B)Data sharing – ReadPropertyMultiple-B (DS-RPM-B)Data sharing – WriteProperty-B (DS-WP-B)Data sharing – COV-B (DS-COV-B)Device management – DynamicDeviceBinding-B (DM-DDB-B) Device management – DynamicObjectBinding-B (DM-DOB-B) Device management – DeviceCommunicationControl-B (DM-DCC-B)BACnet MS/TP Baud rates9’600, 19’200, 38’400, 76’800 (Default: 38’400) Address0...127 (Default: 1)Number of nodes Max 32 (without repeater), 1 full busloadTerminating resistor120 ΩBACnet IP Port open (Default: 47’808)Parameterisation Tool through the integrated webserver !All writeable objects with instance number ≥ 90 are persistent and are not supposed to be written on a regular base.Standard Object Types Supported Objekt type Optional properties Writeable propertiesDevice DescriptionLocationActive COV SubscriptionsMax MasterMax Info FramesProfile Name Object IdentifierObject NameLocationDescriptionAPDU Timeout (1’000…60’000) Number of APDU Retries (0...10) Max Master (1...127)Max Info Frames (1...255)Analog Input [AI]DescriptionCOV IncrementAnalog Output [AO]DescriptionCOV IncrementPresent ValueAnalog Value [AV]Description Present ValueBinary Input [BI]DescriptionActive textInactive TextBinary Valve [BV]DescriptionActive textInactive TextPrresent ValueMulti-state Input [MI]DescriptionState TextMulti-state Output [MO]DescriptionState TextPresent ValueMulti-state Value [MV]DescriptionState TextPresent ValueThe device does not support the services CreateObject and DeleteObject.The specified maximum length of writable strings is based on single-byte characters andsupport up to 252 characters.Service processing The device supports the DeviceCommunicationControl and ReinitializeDevice services. No password is required.A maximum of 5 active COV subscriptions with a lifetime of 1…43‘200 sec. (12 hours) aresupported.Object Name Object Type[Instance]DescriptionCommentStatus_FlagsValues COV Increment AccessDevice Device[Inst.Nr]0…4’194’302Default: 1–WRelPos AI[1]Relative Position in %0...1005R AbsPos AI[2]Absolute Position in degree0...905R SpAnalog_V AI[5]Analog Setpoint in Volt0...10.001R RelFlow AI[10]Relative Flow in %0...1005R AbsFlow_lmin AI[11]Absolute Flow in l/min0...100’0001R AbsFlow_m3h AI[12]Absolute Flow in m3/h0...6000.1R AbsFlow_gpm AI[13]Absolute Flow in gpm0...100’0001R AbsFlow_ls AI[14]Absolute Flow in l/s0...100’0000.1R AbsFlow_lh AI[15]Absolute Flow in l/h0...100’000100R T1_C AI[20]Temperature 1 (remote) in C-10 (1201)T2_C AI[21]Temperature 2 (embedded) in C-10 (1201)DeltaT_K AI[22]Delta Temperature in K0...1301R T1_F AI[25]Temperature 1 (remote) in F14...2481R T2_F AI[26]Temperature 2 (embedded) in F14...2481R DeltaT_F AI[27]Delta Temperature in F0...2661R AbsPower_kW AI[30]Power in kW0...2.147e+610R E_Cooling_kWh AI[31]Cooling Energy in kWh0...2.147e+910R E_Heating_kWh AI[32]Heating Energy in kWh0...2.147e+910R E_Cooling_MJ AI[33]Cooling Energy in MJ0...2.147e+910R E_Heating_MJ AI[34]Heating Energy in MJ0...2.147e+910R AbsPower_kBTUh AI[35]Power in kBTU/h0...2.147e+610R E_Cooling_kBTU AI[36]Cooling Energy in kBTU0...2.147e+910R E_Heating_kBTU AI[37]Heating Energy in kBTU0...2.147e+910R RelPower AI[40]Relative Power in %0...3005R AbsPower_ton AI[45]Power in ton refrigeration0...2.147e+61R E_Cooling_tonh AI[46]Cooling Energy in ton*h0...2.147e+91R E_Heating_tonh AI[47]Heating Energy in ton*h0...2.147e+91R E_CoolReset_kWh AI[50]Cooling Energy in kWh, resettable with BV[31]0...2.147e+91R E_HeatReset_kWh AI[51]Heating Energy in kWh, resettable with BV[32]0...2.147e+91R E_CoolReset_kBTU AI[52]Cooling Energy in kBTU, resettable with BV[31]0...2.147e+91R E_HeatReset_kBTU AI[53]Heating Energy in kBTU, resettable with BV[32]0...2.147e+91RGlycolConcentration AI[60]Glycol concentration in %Measured value or override value from webserver Measured value: 0 (40)Override value: 0 (80)1RErrorState 1)AI[100]Error StateError Sensor T1: Error with remote temperature sensorError Sensor T2: Error with embedded temperature sensorError Flow Sensor: Error with the flow sensorActuator can‘t move: Mechanical overload due to blocked valve, etc.Flow with closed valve: Flow is measured but position of valve is closedAirbubbles: Air bubbles in the hydronic systemFlow not reached: Setpoint cannot be reached within 3min during flow controlPower not realized: Setpoint cannot be reached within 3min during power controlGear disengagement active: Gear disengaged button is pressedReverse flow detected: Reverse flow is detectedMP communication faulty: Internal communication between sensor and actuatorfaultyFreeze warning: Measured temperature & glycol concentration indicate thatgrease ice can build upBit 0: Error Sensor T1Bit 1: Error Sensor T2Bit 2: Error Flow SensorBit 3: Actuator cannot moveBit 4: Flow with closed valveBit 5: Air bubblesBit 6: Flow not reachedBit 7: Power not realizedBit 8: Gear disengagedBit 9: Reverse flow detectedBit 10: MP communicationfaultyBit 11: Freeze warning1RSpAbsFlow_lmin AI[111]Setpoint Absolute Flow in l/min0...100’0001R SpAbsFlow_m3h AI[112]Setpoint Absolute Flow in m3/h0...6000.1R SpAbsFlow_gpm AI[113]Setpoint Absolute Flow in gpm0...100’0001R SpAbsFlow_ls AI[114]Setpoint Absolute Flow in l/s0...100’0000.1R SpAbsFlow_lh AI[115]Setpoint Absolute Flow in l/h0...600100RSpRel AO[1]Setpoint Relative in %The set point is related either to the position, the flow (of Vmax) or the power(of Pmax).See ControlMode for more information → MV[100]0 (100)Default: 01CVmax_lmin AV[90]Maximum Flow Limit in l/min30%Vnom…VnomDefault: Vnom-WVmax_gpm AV [91]Maximum Flow Limit in gpm30%Vnom…VnomDefault: Vnom-WPmax_kW AV [95]Maximum Power Limit in kW0.5%Pnom…PnomDefault: Pnom-WObject Name Object Type[Instance]DescriptionCommentStatus_FlagsValues AccessSpPosReached BI [1]Setpoint Position reached0: No1: YesRSummaryStatus BI [101]Summary StatusSummarizes all status from MI 103 - 1070: OK1: Not OKRRstCoolEnergy BV [31]Reset Cooling EnergySets the Cooling Energy (AI[50] / AI[52]) to zero 0: None1: ResetWRstHeatEnergy BV [32]Reset Heating EnergySets the Heating Energy (AI[51] / AI[53]) to zero 0: None1: ResetWRstErrCount BV [100]Reset Error Counters0: None1: ResetWDeltaT_ MgrStatus MI [102]DeltaT Manager StatusNot selected: dT-Manager deactivatedStandby: dT-Manager activated but not activeActive: dT-Manager activeScaling standby: dT-Manager active with no limitation to the flowScaling active: dT-Manager active with limitation to the flow → AV[108]1: Not selected2: Standby3: Active4: Scaling standby5: Scaling activeRStatusSensor MI [103]Status SensorIndicates informations within the flow sensor and both temperature sensors 1: OK2: Flow sensor not OK3: T1 not OK4: T2 not OKRStatusFlow MI [104]Status FlowReverse flow detected: Energy Valves detected a reverse flowFlow not reached: Setpoint cannot be reached within 3min during flow controlFlow in closed position: Flow is measured but position of valve is closed 1: OK2: Reverse flow detected3: Flow not reached4: Flow in closed positionRStatusMedia MI [105]Status MediaAirbubbles: Airbubbles in the hydronic system. As long as there are airbubblesin the system, position control mode is active, regardless off control modesetting (ControlMode MV[100]).Freeze warning: Measured temperature & glycol concentration indicate thatgrease ice can build up 1: OK2: Airbubbles3: Freeze warningRStatusActuator MI [106]Status ActuatorActuator cannot move: Mechanical overload due to blocked valve, etc.Gear disengaged: Gear disengaged button is pressed 1: OK2: Actuator cannot move3: Gear disengagedRStatusPower MI [107]Status PowerPower not reached: Setpoint cannot be reached within 3min during powercontrol 1: OK2: Power not reachedRObject Name Object Type[Instance]DescriptionCommentStatus_FlagsValues COV Increment AccessPmax_kBTUh AV [96]Maximum Power Limit in kBTU/h0.5%Pnom…PnomDefault: Pnom-WVmax AV [100]Maximum Flow Limit in %30 (100)Default: 100-W Vnom_lmin AV [101]Nominal Volume Flow in l/min Vnom-W Vnom_gpm AV [102]Nominal Volume Flow in gpm Vnom-W SpDeltaT_K AV [103]Setpoint DeltaT in K1 (55)Default: 10-WSpDeltaT_F AV [104]Setpoint DeltaT inF2 (100)Default: 18-WPmax AV [105]Maximum Power Limit in %0.5 (100)Default: 100-W Pnom_kW AV [106]Nominal Power in kW Pnom-R Pnom_kBTUh AV [107]Nominal Power in kBTU/h Pnom-R SpFlow_DeltaT lmin AV [108]Setpoint Flow at DeltaT in l/min0...VnomDefault:Vnom-WSpFlow_DeltaT gpm AV [109]Setpoint Flow at DeltaT in gpm0...VnomDefault:Vnom-WElectronic pressure-independent characterised control valvewith energy monitoringOverride MO [1]Override ControlOverrides setpoint with defined valves. It will change back to None (1) after2 hours.1: None2: Close3: Open4: Vnom5: Vmax6: MotStop7: Pnom8: PmaxDefault: None(1)CControlMode MV [100]Control ModeThis value defines the interpretation of the setpoint 1: Position Control2: Flow Control3: Power ControlDefault: Flow control(2)WDeltaT_Limitation MV [101]DeltaT LimitationDisabled: dT-Manager not activedT-Manager: dT-Manager active with no restriction to flowdT-Manager scaling: dT-Manager active with restriction of flow → AV 108]1: Disabled2: dT-Manager3: dT-Manager scalingDefault: Disabled(1)WSpSource MV [122]Setpoint SourceIf Analog(1) then actuator is controlled by analog signal 0...10 V on wire 3.If Bus(2) then setpoint via bus SpRel AO[1]1: Analog2: BusDefault: Analog(1)W。
Leviton ATLAS-X1 Cat 6A Component-Rated UTP QUICKP

Page 1 of 2APPLICATIONThe ATLAS-X1 Cat 6A Component-Rated UTP QUICKPORT Jack supports 10GBASE-T networks. The jack is part of a complete ATLAS-X1 Cat 6A UTP system, ideal for the most demanding mission-critical network applications. The connector supports emerging technologies and will easily adapt to network trends.SPECIFICATIONThe jack shall meet or exceed the requirements for channel and component-level electrical transmission performance as described in ANSI/TIA-568.2-D (Cat 6A), ISO/IEC11801-1 (Class E A ), and EN 50173-1 (Class E A ). The jack shall be compliant with ANSI/TIA-1096-A, c(UL)us Listed, and be independently verified for electrical transmission performance and power delivery. The jack body shall be made of die-cast zinc and all plastic components shall be made of high-impact, fire-retardant plastic rated UL 94V-0. The jack shall support tool-free termination and re-termination and shall not require a specialized termination tool. The jack wiring shall be universal to accommodate T568A and T568B wiring schemes. The jack shall be available in 13 colors; more than established by the ANSI/TIA-606-C standard. The jack shall be offered in standard and shuttered styles and select jacks shall be supplied with interchangeable icons. The jack shall be compliant with IEEE 802.3 PoE Type 1, 2, 3, 4 (100 watts max).DESIGN CONSIDERATIONS• Use in any QUICKPORT™ housing to support Cat 6A UTP connectivity in surface-mount, flush-mount, or modular furniture outlets and field-configurable panels• Can be used in conjunction with other QUICKPORT snap-in modules for voice/data/video applications over UTP , coax, and fiber• To identify ports, use different colored modules andicons for each application (full selection of ANSI/TIA-606 compatible colors, 13 available)• Robust housing and shutter protects the jack in harsh environmentsATLAS-X1™ Cat 6A Component-Rated UTP QUICKPORT™ Jack6AUJK-xx6, ICONS-ICxFEATURES• Independently tested and guaranteed to exceed all component, permanent link, and channel margins• Patented Retention Force Technology™ (RFT) protects against tine damage and increases system longevity • For Power over Ethernet, RFT maintains contact force between plug and jack, preventing arcing from intermittent disconnects• Unique design supports tool-free termination andre-termination and requires no specialized termination tool • Short jack design supports a wider range of applications (e.g. shallow boxes, enclosures, bend radius, etc.)• Terminates from 26 to 22 AWG solid or stranded conductors for use on various cable types• Robust IDCs can withstand 20 re-termination cycles and jack contacts are tested for 750 plug-mating cycles to ensure system longevity• Available in 13 ANSI/TIA-606-C compatible colors • Tested and approved for use in air-handling spaces (plenum rating) in accordance with UL Standard 2043• Select jacks available with interchangeable icons (voice, data, A/V, blank) for easy ID• Jack with internal shutter protects against dust and debris • Solid metal body dissipates 53% more heat than plastic, minimizing damage from excess heat in PoE applications • Tine geometry prevents arcing damage where plug and jack make contactSTANDARDS & REGULATIONS• ANSI/TIA-568.2-D (Cat 6A)• ISO/IEC 11801-1 (Cat 6A)• EN 50173-1 (Cat 6A)• ANSI/TIA-1096-A (formerly FCC Part 68)• IEC 60603-7 (includes IEC 60512-5-2)• IEC 60512-99-002• IEEE 802.3 PoE Type 1, 2, 3, 4 (100 watts max)• Cisco UPOE, UPOE+ (90 watts max)• Power over HDBaseT™ PoH (95 watts max)• c(UL)us Listed (UL 1863)• UL 2043 Plenum Certified • RoHS 3• ETL verified to meet the IEC 60512-99-002 standard for support of IEEE 802.3 Type 4 PoE (100 watt) applicationsCOUNTRY OF ORIGINUSA and Mexico (Contact Customer Service for details)6AUJK-xx6, ICONS-ICxUSANetwork Solutions Headquarters +1 (800) 722 2082 *******************Leviton Berk-Tek Cable : +1 (800) 237 5835 ************************Asia Pacific+852 3620 2602********************Canada+1 (800) 461 2002**********************Europe+44 (0) 1592 772124 **********************Latin AmericaMX: +52 (55) 2128 6286 LATAM: +52 (55) 2333 5963 *********************Middle East & Africa +971 (4) 247 9800 *******************NETWORK SOLUTIONS PRODUCTS ARE AVAILABLE WORLDWIDE IN OVER 100 COUNTRIES. VISIT US ONLINE AT /NS TO LEARN MORE.Page 2 of 2For further support information, visit /ns/support6AUJK-xx6, ICONS-ICx6AUJK-xx6, ICONS-ICxMECHANICAL SPECIFICATIONSDimensions:See belowMaterials: Jack Body: Die-cast zincSpring-Wire Contacts: High quality, copper-based alloy, plated with 50 microinches of gold for lowest contact resistance andmaximum life Temp. (Storage):Temp. (Installation): Temp. (Operating):Humidity (Max.):WARRANTY INFORMATIONFor Leviton product warranties, go to /ns/warrantyPART NUMBERDescriptionStandard Jack Jack with Shutter GREENPACK™12-Pack Standard Jack ATLAS-X1™ Cat 6A Component-Rated UTP QUICKPORT™ Jack, white 6AUJK-RW66AUJK-SW66AUJK-CW6ATLAS-X1 Cat 6A Component-Rated UTP QUICKPORT Jack, light almond 6AUJK-RT66AUJK-ST6—ATLAS-X1 Cat 6A Component-Rated UTP QUICKPORT Jack, ivory 6AUJK-RI66AUJK-SI6—ATLAS-X1 Cat 6A Component-Rated UTP QUICKPORT Jack, yellow 6AUJK-RY66AUJK-SY6—ATLAS-X1 Cat 6A Component-Rated UTP QUICKPORT Jack, orange 6AUJK-RO66AUJK-SO6—ATLAS-X1 Cat 6A Component-Rated UTP QUICKPORT Jack, crimson 6AUJK-RC66AUJK-SC6—ATLAS-X1 Cat 6A Component-Rated UTP QUICKPORT Jack, dark red 6AUJK-RR66AUJK-SR6—ATLAS-X1 Cat 6A Component-Rated UTP QUICKPORT Jack, purple 6AUJK-RP66AUJK-SP6—ATLAS-X1 Cat 6A Component-Rated UTP QUICKPORT Jack, blue 6AUJK-RL66AUJK-SL66AUJK-CL6ATLAS-X1 Cat 6A Component-Rated UTP QUICKPORT Jack, green 6AUJK-RV66AUJK-SV6—ATLAS-X1 Cat 6A Component-Rated UTP QUICKPORT Jack, gray 6AUJK-RG66AUJK-SG6—ATLAS-X1 Cat 6A Component-Rated UTP QUICKPORT Jack, black6AUJK-RE66AUJK-SE66AUJK-CE6ATLAS-X1 Cat 6A Component-Rated UTP QUICKPORT Jack, brown6AUJK-RB66AUJK-SB6—Green (V)Blue (L)Purple (P)Crimson (C)Dark Red (R)Orange (O)Yellow (Y)Black (E)Gray (G)Ivory (I)Light Almond (T)Brown (B)Color-matched icons (ICONS-ICx) can be ordered separately in 72-quantity packs.x = icon color。
E+H溶解氧分析仪 中文
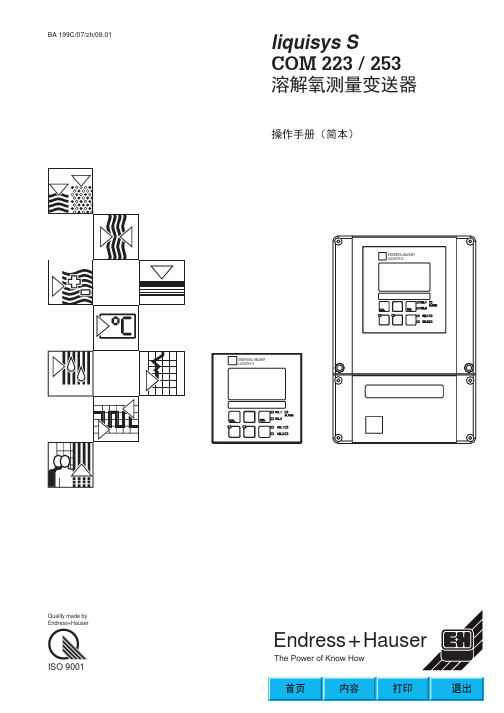
0 min
0...2000(min)S
ห้องสมุดไป่ตู้
0 min P2
Err.Delay
备注 对于传感器及过程监测 的设置
根据F2中的单位选择 以S或 min来输入报警延时 如P5=AC 或AC+CC,报警延时为有效
6
P3
低 报 的 阈 值 0.00mg/l
0.00...20.00mg/l
0.00% SAT 0.0...200.0% SAT
Altitude
A4
输入测量值的
阻尼系数
1 1...60
1 A4
Damping
测量值阻尼是取一定数 量的测量值作平均值 它被用于稳定波动非常 厉害的测量值 如果输 入1 则没有阻尼
2
5.2.2.SETUP 2
代码
含义
B
功能组
SETUP 2
B1
盐度
选择或范围 的出厂设定
0.0% 0.0...4.0%
lin O2
Sel.Type
该特性的斜体可以是正 或负 模拟或表格特性参阅 02(2) 02(3)
0211
选择电流范围
4-20 0-20
0212
0/4mA对 应 的 值 输入相应的氧
量值或温度值
0.00 mg/l 0.00...20.00 mg/l 0.0%SAT 0.0...200.0% SAT 0.0 -10.0...60.0
数值可以增加或改变 输入的数值会自动地 以电充上升顺序排列.
read O231
Sel.Table
1 O232
No.Elem.
输出X和Y数据组的数量 (X指测量值和Y指相应的 电流值)
1 O233
JST 电子连接器产品参考手册说明书
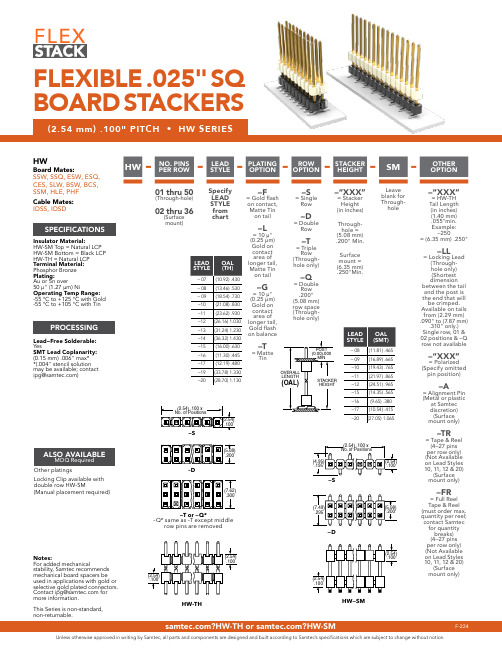
---PLATING OPTION-ROW OPTION-STACKER HEIGHT-SM-OTHER OPTION01 thru 50(Through-hole)02 thru 36(Surface mount)Specify LEAD STYLE from chart–F= Gold flash on contact,Matte Tin on tail –L= 10 µ" (0.25 µm) Gold on contact area of longer tail, Matte Tin on tail –G= 10 µ" (0.25 µm) Gold on contact area of longer tail, Gold flash on balance –T= Matte Tin–S = Single Row –D = Double Row –T= Triple Row (Through-hole only)–Q= Double Row .200" (5.08 mm) row space (Through-hole only)–“XXX”= Stacker Height (in inches)Through-hole =(5.08 mm) .200" Min.Surface mount =(6.35 mm) .250"Min.Leave blank for Through-hole–“XXX”= HW-TH Tail Length (in inches) (1.40 mm) .055"min.Example: –250= (6.35 mm) .250"–LL= Locking Lead (Through-hole only) (Shortest dimension between the tail and the post is the end that will be crimped. Available on tails from (2.29 mm) .090" to (7.87 mm).310" only.)Single row, 01 & 02 positions & –Q row not available –“XXX”= Polarized (Specify omitted pin position)–A= Alignment Pin (Metal or plastic at Samtec discretion)(Surface mount only)–TR= Tape & Reel (4–27 pins per row only)(Not Available on Lead Styles 10, 11, 12 & 20)(Surface mount only)–FR= Full Reel Tape & Reel (must order max. quantity per reel; contact Samtec for quantity breaks) (4–27 pins per row only)(Not Available on Lead Styles 10, 11, 12 & 20)(Surface mount only)Insulator Material:HW-SM Top = Natural LCP HW-SM Bottom = Black LCP HW-TH = Natural LCP Terminal Material: Phosphor Bronze Plating:Au or Sn over50 µ" (1.27 µm) NiOperating Temp Range:-55 °C to +125 °C with Gold -55 °C to +105 °C with TinLead–Free Solderable: YesSMT Lead Coplanarity:(0.15 mm) .006" max**(.004" stencil solution may be available; contact **************)Notes:For added mechanicalstability, Samtec recommends mechanical board spacers be used in applications with gold or selective gold plated connectors. ************************more information.This Series is non-standard,non-returnable.HWBoard Mates:SSW, SSQ, ESW, ESQ, CES, SLW, BSW, BCS, SSM, HLE, PHF Cable Mates:IDSS, IDSDHW-THHW—SM–Q* same as –T except middlerow pins are removedOther platingsLocking Clip available with double row HW-SM(Manual placement required)FLEXIBLE .025" SQ BOARD STACKERSUnless otherwise approved in writing by Samtec, all parts and components are designed and built according to Samtec’s specifications which are subject to change without notice.F-224。
TI产品中文版说明书

Load (A)E f f i c i e n c y (%)0.00.51.0 1.52.06065707580859095100D008V INV OUTL1TLV62569AProduct Folder Order Now Technical Documents Tools &SoftwareSupport &CommunityTLV62568A ,TLV62569AZHCSI23B –APRIL 2018–REVISED MARCH 2020采用SOT563封装并具有强制PWM 的TLV6256xA 1A 、2A 降压转换器1特性•强制PWM 模式可减少输出电压纹波•效率高达95%•低R DS(ON)开关:100m Ω/60m Ω•输入电压范围为2.5V 至5.5V •可调输出电压范围为0.6V 至V IN •100%占空比,可实现超低压降• 1.5MHz 典型开关频率•电源正常输出•过流保护•内部软启动•热关断保护•采用SOT563封装•与TLV62568、TLV62569引脚对引脚兼容•借助WEBENCH ®电源设计器创建定制设计方案2应用•通用负载点(POL)电源•STB 和DVR •IP 网络摄像头•无线路由器•固态硬盘(SSD)–企业级3说明TLV62568A 、TLV62569A 器件是经过优化而具有高效率和紧凑型解决方案尺寸的同步降压型直流/直流转换器。
该器件集成了输出电流高达2A 的开关。
在整个负载范围内,该器件将以1.5MHz 开关频率在脉宽调制(PWM)模式下运行。
关断时,流耗减少至2μA 以下。
内部软启动电路可限制启动期间的浪涌电流。
此外,还内置了诸如输出过流保护、热关断保护和电源正常输出等其他特性。
该器件采用SOT563封装。
器件信息(1)器件型号封装封装尺寸(标称值)TLV62568ADRL SOT563(6)1.60mm x 1.60mmTLV62568APDRL TLV62569ADRL TLV62569APDRL(1)如需了解所有可用封装,请参阅产品说明书末尾的可订购产品附录。
Cisco Secure ACS 购买指南说明书

Ordering GuideCisco Secure ACSThis document provides guidance on how to order Cisco Secure Access Control System (ACS) family products. It includes information on upgrade scenarios as well as information on software and hardware service offerings.OverviewCisco® ACS is designed to address both current and future corporate network access policy challenges. The world’s most trusted enterprise access and policy platform, it is used by more than 40,000 enterprises worldwide.The Cisco Secure ACS family includes:●Cisco Secure ACS: The Cisco flagship access and policy system, Cisco Secure ACSsupports up to hundreds of thousands of users and tens of thousands of network devices and is ideal for medium or large enterprises.●Cisco Secure ACS View: A dedicated reporting and monitoring device designed tocomplement Cisco Secure ACS, View helps ensure the highest level of network accesscontrol and compliance.●Cisco Secure ACS Express: Ideal for small and medium-sized businesses (SMBs) ormedium/small enterprises, ACS Express is an easy-to-deploy device with built-in reporting and monitoring. It supports up to 50 devices and 350 users.Cisco Secure ACSCisco Secure ACS is available as software for Windows servers (ACS for Windows) and as a dedicated appliance (ACS Solution Engine). Product part numbers are shown in Table 1. For guidelines on Cisco Secure ACS deployment, see the deployment guide at/en/US/products/sw/secursw/ps2086/prod_white_papers_list.html.Table 1. Cisco Secure ACS New Order Part NumbersPart Number DescriptionCSACS-4.2-WIN-K9 Cisco Secure ACS 4.2 for WindowsCSACSE-1113-K9 Cisco ACS Solution Engine – Cisco 1113 hardware with ACS version 4.2 preinstalledFor ACS for Windows, Software Application Support (SAS) is available. SAS entitles customers to maintenance and minor updates, plus access to online resources and support services.For ACS Solution Engine, SAS is required for software coverage and SMARTnet® is required for hardware coverage. SMARTnet has various service options to provide the hardware replacement coverage desired. For more information on SAS and SMARTnet, please visit/en/US/products/svcs/ps3034/ps2827/serv_category_home.html.Software upgrades are available for current ACS for Windows and ACS Solution Engine customers. Customers that have SAS contracts are entitled to minor upgrades. For example, a customer with SAS running ACS version 4.0 software would be entitled to ACS 4.1 and 4.2 upgrades. Customers that do not have SAS contracts can purchase minor upgrades. Part numbers for minor upgrades are identified by the “MR” designation.Customers that have SAS contracts can obtain upgrade kits using the Product Upgrade Tool (requires login) at /upgrade.SAS contracts do not cover major upgrades and these upgrades must always be purchased. For example, customers running ACS for Windows version 3.3 software that want to upgrade to ACS version 4.2 must purchase the upgrade part number CSACS-4.2-WINUP-K9.Upgrade part numbers are shown in Table 2. Note that there are different part numbers for ACS for Windows and ACS Solution Engine software upgrades.Table 2. Cisco Secure ACS Upgrade Part NumbersPart Number DescriptionCSACS4.2-WIN-MR-K9 ACS for Windows minor upgrade for customers with ACS for Windows versions 4.0 or 4.1 CSACS-4.2-WINUP-K9 ACS for Windows major upgrade for customers with ACS for Windows versions earlier than 4.0 CSACSE4.2-SW-MR-K9 ACS Solution Engine minor upgrade for customers with versions 4.0 or 4.1 (1112 or 1113hardware required)CSACSE-4.2-SWUP-K9 ACS Solution major upgrade for customers with versions earlier than 4.0 (1112 or 1113hardware required)CSACSE-1113-UP-K9 ACS Solution Engine hardware and software upgrade – for customers with 1111 or 1112hardware; includes Cisco 1113 hardware with ACS version 4.2 installedImportant: ACS Solution Engine version 4.2 is only supported on Cisco 1112 and 1113 hardware. Customers with Cisco 1111 hardware should consider upgrading to 1113 by purchasing CSACSE-1113-UP-K9. Trade-in credit may also be available through the Cisco Technology Migration Program (TMP).Cisco Secure ACS ViewCisco Secure ACS View collects and correlates data from multiple Cisco Secure ACS servers and logs to provide aggregate views of system activity as well as detailed information at the transaction level for both network access and device administration. Cisco Secure ACS View provides essential information for network monitoring and planning, access problem detection and troubleshooting, and entitlement and compliance reporting.Cisco Secure ACS View is recommended for all ACS 4.2 deployments. For guidelines on Cisco Secure ACS View deployment, see the deployment guide at/en/US/products/ps9302/prod_white_papers_list.html.Cisco Secure ACS View part numbers are shown in Table 3.Table 3. Cisco Secure ACS View Part NumbersPart Number DescriptionCSACS4.0-VIEW-K9 Cisco Secure ACS View appliance with ACS View 4.0 software and license for managing twoACS servers (version 4.1.4 or 4.2 required). ACS View does not support ACS Express.CSACS4.0-VIEWLIC License for managing an additional ACS server with Cisco Secure ACS View 4.0.For the ACS View appliance, an SAS contract is required for software coverage and SMARTnet isrequired for hardware coverage. SAS entitles customers to maintenance and minor updates, plusaccess to online resources and support services.Cisco Secure ACS ExpressCisco Secure ACS Express offers a comprehensive yet simplified feature set, a user-friendlygraphical user interface, and an attractive price point that allows placement of this product insituations where Cisco Secure ACS for Windows or Cisco Secure ACS Solution Engine may notbe suitable.Cisco Secure ACS Express part numbers are shown in Table 4.Table 4. Cisco Secure ACS Express Part NumbersPart Number DescriptionCSACS-5.0-EXP-K9 Cisco Secure ACS Express 5.0 applianceFor ACS Express, an SAS contract is required for software coverage and SMARTnet is requiredfor hardware coverage. SAS entitles customers to maintenance and minor updates, plus access toonline resources and support services.For More InformationPlease check the Cisco Secure ACS homepage at /go/acs for the latestinformation about Cisco Secure ACS.For more information contact the ACS marketing team at *****************, or contact youraccount representative.Printed in USA C07-500695-00 10/08。
ROHM Solution Simulator 用户指南.pdf_1705892277.949866
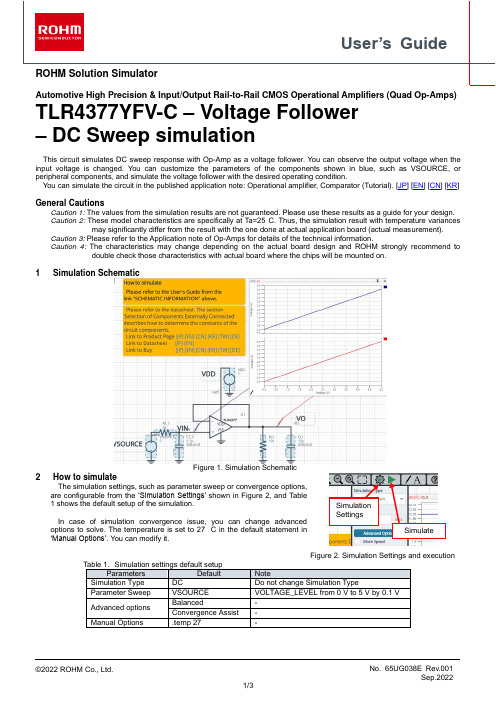
User’s Guide ROHM Solution SimulatorAutomotive High Precision & Input/Output Rail-to-Rail CMOS Operational Amplifiers (Quad Op-Amps) TLR4377YFV-C – Voltage Follower– DC Sweep simulationThis circuit simulates DC sweep response with Op-Amp as a voltage follower. You can observe the output voltage when the input voltage is changed. You can customize the parameters of the components shown in blue, such as VSOURCE, or peripheral components, and simulate the voltage follower with the desired operating condition.You can simulate the circuit in the published application note: Operational amplifier, Comparator (Tutorial). [JP] [EN] [CN] [KR] General CautionsCaution 1: The values from the simulation results are not guaranteed. Please use these results as a guide for your design.Caution 2: These model characteristics are specifically at Ta=25°C. Thus, the simulation result with temperature variances may significantly differ from the result with the one done at actual application board (actual measurement).Caution 3: Please refer to the Application note of Op-Amps for details of the technical information.Caution 4: The characteristics may change depending on the actual board design and ROHM strongly recommend to double check those characteristics with actual board where the chips will be mounted on.1 Simulation SchematicFigure 1. Simulation Schematic2 How to simulateThe simulation settings, such as parameter sweep or convergence options,are configurable from the ‘Simulation Settings’ shown in Figure 2, and Table1 shows the default setup of the simulation.In case of simulation convergence issue, you can change advancedoptions to solve. The temperature is set to 27 °C in the default statement in‘Manual Options’. You can modify it.Figure 2. Simulation Settings and execution Table 1.Simulation settings default setupParameters Default NoteSimulation Type DC Do not change Simulation TypeParameter Sweep VSOURCE VOLTAGE_LEVEL from 0 V to 5 V by 0.1 VAdvanced options Balanced - Convergence Assist -Manual Options .temp 27 - SimulationSettingsSimulate3 Simulation Conditions4 Op-Amp modelTable 3 shows the model pin function implemented. Note that the Op-Amp model is the behavior model for its input/output characteristics, and no protection circuits or the functions not related to the purpose are not implemented.5 Peripheral Components5.1 Bill of MaterialTable 4 shows the list of components used in the simulation schematic. Each of the capacitors has the parameters of equivalent circuit shown below. The default values of equivalent components are set to zero except for the ESR ofC. You can modify the values of each component.Table 4. List of capacitors used in the simulation circuitType Instance Name Default Value Variable RangeUnits Min MaxResistor R1_1 0 0 10 kΩRL1 10k 1k 1M, NC ΩCapacitor C1_1 0.1 0.1 22 pF CL1 10 free, NC pF5.2 Capacitor Equivalent Circuits(a) Property editor (b) Equivalent circuitFigure 3. Capacitor property editor and equivalent circuitThe default value of ESR is 0.01 Ω.(Note 2) These parameters can take any positive value or zero in simulation but it does not guarantee the operation of the IC in any condition. Refer to the datasheet to determine adequate value of parameters.6 Recommended Products6.1 Op-AmpTLR4377YFV-C : Automotive High Precision & Input/Output Rail-to-Rail CMOS Operational Amplifier (QuadOp-Amp). [JP] [EN] [CN] [KR] [TW] [DE]TLR2377YFVM-C : Automotive High Precision & Input/Output Rail-to-Rail CMOS Operational Amplifier (DualOp-Amp). [JP] [EN] [CN] [KR] [TW] [DE]TLR377YG-C : Automotive High Precision & Input/Output Rail-to-Rail CMOS Operational Amplifier. [JP] [EN] [CN] [KR] [TW] [DE]LMR1802G-LB : Low Noise, Low Input Offset Voltage CMOS Operational Amplifier. [JP] [EN] [CN] [KR] [TW] [DE] Technical Articles and Tools can be found in the Design Resources on the product web page.NoticeROHM Customer Support System/contact/Thank you for your accessing to ROHM product informations.More detail product informations and catalogs are available, please contact us.N o t e sThe information contained herein is subject to change without notice.Before you use our Products, please contact our sales representative and verify the latest specifica-tions :Although ROHM is continuously working to improve product reliability and quality, semicon-ductors can break down and malfunction due to various factors.Therefore, in order to prevent personal injury or fire arising from failure, please take safety measures such as complying with the derating characteristics, implementing redundant and fire prevention designs, and utilizing backups and fail-safe procedures. ROHM shall have no responsibility for any damages arising out of the use of our Poducts beyond the rating specified by ROHM.Examples of application circuits, circuit constants and any other information contained herein areprovided only to illustrate the standard usage and operations of the Products. The peripheral conditions must be taken into account when designing circuits for mass production.The technical information specified herein is intended only to show the typical functions of andexamples of application circuits for the Products. ROHM does not grant you, explicitly or implicitly, any license to use or exercise intellectual property or other rights held by ROHM or any other parties. ROHM shall have no responsibility whatsoever for any dispute arising out of the use of such technical information.The Products specified in this document are not designed to be radiation tolerant.For use of our Products in applications requiring a high degree of reliability (as exemplifiedbelow), please contact and consult with a ROHM representative : transportation equipment (i.e. cars, ships, trains), primary communication equipment, traffic lights, fire/crime prevention, safety equipment, medical systems, servers, solar cells, and power transmission systems.Do not use our Products in applications requiring extremely high reliability, such as aerospaceequipment, nuclear power control systems, and submarine repeaters.ROHM shall have no responsibility for any damages or injury arising from non-compliance withthe recommended usage conditions and specifications contained herein.ROHM has used reasonable care to ensur e the accuracy of the information contained in thisdocument. However, ROHM does not warrants that such information is error-free, and ROHM shall have no responsibility for any damages arising from any inaccuracy or misprint of such information.Please use the Products in accordance with any applicable environmental laws and regulations,such as the RoHS Directive. For more details, including RoHS compatibility, please contact a ROHM sales office. ROHM shall have no responsibility for any damages or losses resulting non-compliance with any applicable laws or regulations.W hen providing our Products and technologies contained in this document to other countries,you must abide by the procedures and provisions stipulated in all applicable export laws and regulations, including without limitation the US Export Administration Regulations and the Foreign Exchange and Foreign Trade Act.This document, in part or in whole, may not be reprinted or reproduced without prior consent ofROHM.1) 2)3)4)5)6)7)8)9)10)11)12)13)。
EFLOW用户指南 Release 12.3说明书

Path
:
Online
: True
RestartNeeded : False
2. Set execution policy and verify.
Set-ExecutionPolicy -ExecutionPolicy AllSigned -Force
Get-ExecutionPolicy AllSigned
5
EFLOW User's Guide, Release 12.3
3. Download and install EFLOW.
$msiPath = $([io.Path]::Combine($env:TEMP, 'AzureIoTEdge.msi')) $ProgressPreference = 'SilentlyContinue' Invoke-WebRequest "https:∕∕aka.ms∕AzEFLOWMSI_1_4_LTS_X64" -OutFile $msiPath
▶ The Windows host OS with virtualization enabled ▶ A Linux virtual machine ▶ IoT Edge Runtime ▶ IoT Edge Modules, or otherwise any docker-compatible containerized application (runs on
AES 1235 品牌 BNS 产品名称 磁性安全传感器 型号 101170049说明书

DATASHEETDataOrdering dataNote (Delivery capacity)Phased-out product Product type description AES 1235101170049Article number (ordernumber)EAN (European Article4030661297118 Number)27-37-18-19eCl@ss number, version12.027-37-18-19eCl@ss number, version11.027-37-18-19eCl@ss number, version9.0EC001449ETIM number, version7.0EC001449ETIM number, version6.0Available until31.12.2023Approvals - StandardsCertificates BGcULusGeneral dataStandards BG-GS-ET-14BG-GS-ET-20EN IEC 62061EN ISO 13849-1EN IEC 60947-5-1EN IEC 60947-5-3EN IEC 60947-5-5EN IEC 60204-1EN IEC 60947-1Climatic stress EN 60068-2-3BG-GS-ET-14Enclosure material Glass-fibre reinforced thermoplastic, ventilated Gross weight240 gGeneral data - FeaturesStop-Category0Wire breakageYesdetectionCross-circuit detection YesFeedback circuit YesYesAutomatic resetfunctionReset afterYesdisconnection of supplyvoltageEarth connectionYesdetectionYesIntegral systemdiagnostics, statusNumber of LEDs12Number of normallyclosed (NC)1Number of normallyopen (NO)Number of undelayed2semi-conductor outputswith signaling functionNumber of safety2contactsNumber of signalling2outputsSafety classificationStandards EN ISO 13849-1EN IEC 61508Safety classification - Relay outputsdPerformance Level, uptoCategory3PFH value 1.00 x 10⁻⁷ /hNotice for max. 50,000 switching cycles/year and max. 80% contact load2Safety Integrity Level(SIL), suitable forapplications inMission time20 Year(s)Mechanical data20,000,000 OperationsMechanical life,minimumMounting Snaps onto standard DIN rail to EN 60715Mechanical data - Connection techniqueTerminal designations IEC/EN 60947-1Termination rigid or flexibleScrew terminals M20 x 1.5Cable section, minimum0.25 mm²2.5 mm²Cable section,maximumTightening torque of0.6 NmClipsMechanical data - DimensionsWidth22.5 mmHeight100 mmDepth121 mmAmbient conditionsDegree of protection ofIP40the enclosureDegree of protection ofIP54the mounting spaceDegree of protection ofIP20clips or terminalsAmbient temperature+0 ... +55 °CStorage and transport-25 °Ctemperature, minimumStorage and transport+70 °Ctemperature, maximumResistance to vibrations10...55 Hz, Amplitude 0.35 mm, ± 15 % Restistance to shock30 g / 11 msAmbient conditions - Insulation valuesRated impulse4 kVwithstand voltage UimpOvervoltage category IIIDegree of pollution2Electrical dataFrequency range50 Hz60 HzOperating voltage24 VAC -15 % / +10 %24 VDC -10 % / +20 %Ripple voltage10 %Thermal test current 6 ARated operating voltage24 VACRated operating voltage24 VDC20.4 VACRated AC voltage forcontrols, 50 Hz,minimum26.4 VACRated control voltage atAC 50 Hz, maximum20.4 VACRated AC voltage forcontrols, 60 Hz,minimum26.4 VACRated control voltage atAC 60 Hz, maximum20.4 VDCRated AC voltage forcontrols at DC minimumRated control voltage at28.8 VDCDC, maximum5 WElectrical powerconsumption0.1 ΩContact resistance,maximumin new stateNote (Contactresistance)Drop-out delay in case80 msof power failure,typically20 msDrop-out delay in caseof emergency, typically100 msPull-in delay atautomatic start,maximum, typically20 msPull-in delay at RESET,typicallyMaterial of the contacts,Ag-Ni 10 and 0.2 µm gold-plated electricalElectrical data - Safe relay outputsVoltage, Utilisation230 VACcategory AC-156 ACurrent, Utilisationcategory AC-15Voltage, Utilisation24 VDCcategory DC-136 ACurrent, Utilisationcategory DC-13Switching capacity,10 VDCminimum10 mASwitching capacity,minimum250 VACSwitching capacity,maximum8 ASwitching capacity,maximumElectrical data - Digital inputs10 … 30 VDCInput signal, HIGHSignal "1"0 … 2 VDCInput signal, LOW Signal"0"40 ΩConduction resistance,maximumElectrical data - Digital OutputVoltage, Utilisation24 VDCcategory DC-120.1 ACurrent, Utilisationcategory DC-12Electrical data - Relay outputs (auxiliary contacts) Switching capacity,24 VDCmaximumSwitching capacity,2 AmaximumElectrical data - Electromagnetic compatibility (EMC)EMC rating EMC-DirectiveIntegral system diagnosis (ISD)Note (ISD -Faults)The following faults are registered by the safety monitoring modules and indicated by ISD.Faults Failure of the safety relay to pull-in or drop-outFailure of door contacts to open or closeCross-wire or short-circuit monitoring of the switch connectionsInterruption of the switch connectionsFault on the input circuits or the relay control circuits of the safety monitoring moduleOther dataNote (applications)Safety sensorGuard systemNoteNote (General)Inductive loads (e.g. contactors, relays, etc.) are to be suppressed by means of asuitable circuit.Wiring exampleNote (Wiring diagram)The wiring diagram is shown with guard doors closed and in de-energised condition.To secure a guard door up to PL d and Category 3Monitoring 1 guard door(s), each with a magnetic safety sensor of the BNS rangeThe ISD tables (Intergral System Diagnostics) for analysis of the fault indications andtheir causes are shown in the appendix.Expansion of enable delay time: The enable delay time can be increased from 0.1 s to1 s by changing the position of a jumper link connection under the cover of the unit.The feedback circuit monitors the position of the contactors K3 and K4.Start push button: A start push button (NO) can optionally be connected into thefeedback circuit. With the guard door closed, the enabling paths are then not closeduntil the start push button has been operated.If only one external relay or contactor is used to switch the load, the system can beclassified in Control Category 3 to ISO 13849-1, if exclusion of the fault “Failure of theexternal contactor” can be substantiated and is documented, e.g. by using a reliabledown-rated contactor. A second contactor leads to an increase in the level of securityby redundant switching to switch the load off.If neither start button nor feedback circuit are connected, a jumper connection must bemounted between X1 and A1.Modification for 2 NC contacts: The safety monitoring module can be modified tomonitor two NC contacts by bridging the terminals A1 and X2. In this configuration, theshort-circuit detection becomes inoperative.Ordering codeProduct type description:AES 123(1)(1)56without start-up test6with start-up testDocumentsOperating instructions and Declaration of conformityAES 1235 / AES 1236(245.3 kB, 10.05.2019, Revision D)BG-test certificateAES and BNS - BG-GS-ET-14 - AES 1135 / AES 1136 / AES 1145 / AES 1146 / AES 1155 / AES 1156 / AES 1165 / AES 1166 / AES 1175 / AES 1176 / AES 1235 / AES 1236 / AES 1265 / AES 1266 / AES 1185(1.4 MB, 10.05.2019, Revision F)BG-test certificateAES - BG-GS-ET-20 - AES 1135 / AES 1136 / AES 1145 / AES 1146 / AES 1155 / AES 1156 / AES 1165 / AES 1166 / AES 1175 / AES 1176 / AES 1235 / AES 1236 / AES 1265 / AES 1266(738.9 kB, 10.05.2019, Revision D)UL CertificateAES / FWS / BNS / BN(415.3 kB, 01.08.2019)Wiring example (electr. wiring)AES 123x(19.6 kB, 10.05.2019)Wiring example (electr. wiring)AES 123x(19.7 kB, 10.05.2019)InfoAES 1135 / AES 1136 / AES 1165 / AES 1166 / AES 1185 / AES 1235 / AES 1236(34.3 kB, 30.06.2021)SISTEMA-VDMA library(659.5 kB, 23.03.2023)PicturesProduct picture (catalogue individual photo)ID: kaes1f09| 711.0 kB | .jpg | 265.642 x 529.167 mm - 753 x 1500 px - 72 dpi| 84.7 kB | .png | 74.083 x 147.461 mm - 210 x 418 px - 72 dpiWiring exampleID: maes1l11| 34.0 kB | .cdr || 143.8 kB | .jpg | 352.778 x 408.517 mm - 1000 x 1158 px - 72 dpiWiring exampleID: kaes1l41| 34.1 kB | .cdr || 139.5 kB | .jpg | 352.425 x 396.875 mm - 999 x 1125 px - 72 dpiK.A. Schmersal GmbH & Co. KG, Möddinghofe 30, 42279 WuppertalThe details and data referred to have been carefully checked. Images may diverge from original. Further technical data can be found in the manual. Technical amendments and errors possible.Generated on: 27/07/2023, 01:44。
SiAECOSYS V2 IV代 EM系列控制器程序手册说明书
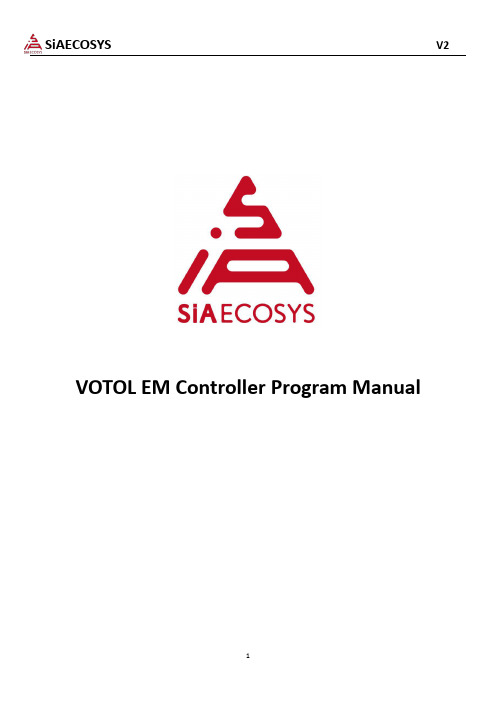
VOTOL EM Controller Program ManualIt is forbidden to non-specialists use!This manual was explained in detail for the IV generation EM series controller,which update download illustrates and parameter adjustment.Before using the software,please read this manual.In order to facilitate the operation,please keep this manual.In order to make the software of maximum utility,please make sure the end user to use this manual.Please be sure to read the manual carefully before starting the operation.Disclaimer:For theⅣgeneration of EM series controller program updates and parameter adjustment can only bedone by professional and technical personnel.If without the written permission of our company for theⅣVOTOL generation EM series,theapplication update to download and parameter of the controller adjustment is not allowed.It is forbidden to non-professional personnel operate this software.In the above event,our company will no longer be responsible for accident happens by controller.1.Software installation(only support win7/10)1.1USB Driver Installation(1)Download the“USB-to-serial-win10-20150814”file,decompressing file.(2)choose the suitable driver with your computer for installation.win7,win8,win10are available.1.11.Decompress the operation first2.Unzip the YH-340USB package and select CH341SER.EXE to install it.Follow the steps above to install(3)After installation,pls.connect the USB cable with controller and computer.If it’s unable to connect,pls.Check below steps.Right click“my computer”in the desktopthen click“device manager”choose“port(COM&LPT)”choose the COM with“!”,click“serach automatically for updated driver software”Close the software when you finishAfter running,please run the software directly:EM_V3series debugging program;If the port has”自2012已停产,请联系供货商处理方法(Pls contact supplier if it is stop production since2012)”First step:Install driver PL2303_Prolific_DriverInstaller_v110Second:Right click to update the driver and select Browse Computer to find the driver software.Thrid:Click to select from the list of drivers for your computer;Select version3.3.10.140(2009-11-19),click Next,close the window when finished;2.Controller connection2.1Connect controllerController host computer simple wiring diagramDescription:controller B+connects battery B+controller B-connects battery B-,controller electric door locks connect battery or controller B+;The USB debug line is connected to the controller debug port;2.1.1According to the controller with CAN or without CAN to select the appropriate USB debug line;with CAN controller need to check the CAN enable,without CAN does not need to check;EM200controller needs to exchange the debug line CAN-H and CAN-L ,otherwise can’t connect the controller;2.1.2Host computer selectionEM50EM100EM150without CAN chooseEM50EM100EM150with CAN chooseEM200chooseSpecific host model needs to inquire the related sales;3Open the computer device manager before connecting to the computer to check whether the USB port is successfullyinstalled.Select the appropriate host computer to connect the host computer to the serial port when the controller is not powered.After selecting the corresponding serial port on the device port,click CreatFile.2.2Then power on(connect with e-lock),click connect(in setting1page),the nominal voltage should not be0.If it’s0,click connect again.3.The settingSetting page11.1:Voltage equipment1.1.1、Battery voltage setting:Corresponding to the ECU voltage,absolutely not allowe overpressure.1.1.2、Lead-acid battery overvoltage,undervoltage,soft undervoltage basic value default:due to software settings defects,the original voltage compensation+1V.1.1.3、The lithium battery is set according to the actual lithium battery parameter value.Due to software setting defects,the original voltage compensation+1V.The original lithium battery parameters are compensated for+1V,and the total compensation is+2V.1.1.4、Attention1.1.4.1、Overvoltage fault:After open the electric door lock,the vehicle doesn’t move.The Controller overvoltage protection function starts.1.1.4.2、ECU undervoltage fault:due to the lithium battery protection board overvoltage device is too high or the undervoltage setting is too low,resulting in lithium battery protection,burning MOS.Please adjust suitable battery voltage before running the motor and controller(for lithium battery).Overvoltage:real overvoltage+3VUndervoltage:real undervoltage+1VSoft undervoltage:undervoltage +3Vg.real overvoltage 84V,set 87V.real undervotlage 60V,set 61V.Soft undervotlage:64V.1.2:Current device1.2.2、Phase current setting:can only be adjusted downwards.1.2.3、Attention1.2.3.1、Setting the busbar current too high,causing the ECU burn MOS.1.2.3.2、As the phase current value decreases,the corresponding motor stall protection time is shortened.Setting page 21throttle voltage adjust(1)low protection value:The throttle error is shown(2)Starting voltage:when the value is reached,the motor starts running(3)End voltage:when the value is reached,the controller thinks the full voltage is reached (it is recommended to set the voltage lower 0.2v compared with thactual torque voltage).(4)High protection value:when the value is higher than that,the torque fault will be displayed2Start setting adjustment (for tricycle gear box only)(1)Starting torque:used for gear combination(2)Combined torque:a force of lifting after gear clearance is combined(3)Upward slope:upward slope of motor torque(4)Downward slope:downward slope of motor torque3Controller and motor temperature protection function adjustment(1)Start:Enter into the function of temperature protection,limit the motor torque.(2)Over temperature:Cut off the output of motor torque(3)Recover:When the motor temperature lower than the temperature protection value,you can re-twist the throttle, then the motor will restore motivation(4)Maximum:The motor maximum temperature is150Setting for page23.1:Parameters setting for sports mode(S gear)3.2.1、Busbar current setting:According to the controller type current corresponding to the selection,the vehicle speed is adjusted according to the motor parameters.BOOST weak magnetic value>high speed weak magnetic value3.2.3、Automatic logout enablers,confirm by select:Check the jog button /uncheck the long press button,choose one3.2.3.1、Check to make the jog effective.The weak magnetic time enters the exit and can be adjusted. 3.2:Downhill electric brake assist:start by select“HDC Enable”,downhill electric brake assist(slow down in steep slopes)function.Enable electric brake by enter minimum speed,if less than the speed,the function will be invalid.3.2.1Value400corresponding to speed around15kmh(it depends on motor feature,sometimes with a3.2.2、Note:The drum motor is not suitable for use,resulting in loose motor shaft.3.3、Flux weakening compensation:only valid when the inner rotor motor type is selected as V-shaped magnetic steelNote:The maximum value of255is generally filled in953.4、Three gear setting:Confirm the motor base speed value adjustment setting parameter value.The basic speed is filled in according to the<Appendix EM_V3Parameter Adjustment Calculation Formula>.3.4.1、The low,medium,high,and third speed values are valid within100%of the parameter value,and the medium,high,and high speed values are exceeded and the100%parameter value is filled.Exceeded by weak magnetic file(medium,high,BOST)3.4.2、In the flux weakening area,the actual parameters of the motor are adjusted,and the vehicle speed is based on the road test.3.4.3、Single voltage mode:The high voltage value is invalid.3.4.4、Attention3.4.4.1、Drum motor:60KM/H motor weak magnetic speed is less than<120%,80KM/H motor weak magnetic speed is less than<125%,110KM/H motor weak magnetic speed is less than<135%.2.4.4.3Inner rotor motor Hall:The built-in Hall weak magnetic speed is less than<135%,and the external Hall weak magnetic speed is less than170%.3.4.4.3、Internal rotor motor magnetic knitting:Built-in flux weakening speed<230%.3.4.4.4The motor base speed exceeds100%of the motor speed value and enters the weak value zone adjustment parameter.BOOST>High speed weak magnetic file.3.4.4.5Weak magnetic failure:The flux weakening value exceeds the motor and controller parameter values,causing the motor to demagnetize and the controller to burn MOS.3.5、Jog/push selection:choose one3.6、The three-speed default gear:the electric door lock opens the default several options.3.7、Soft start setting:The smaller the value,the softer the start.3.8、Speed limit setting:3.8.1、Function selection:speed limit,unlimited speed,two choices,default speed limit3.8.2、The speed limit speed is calculated based on vehicle parameter requirements.<Appendix EM_V3 parameter adjustment calculation formula>3.8.3、The upper limit speed and the solution speed limit are determined according to customer requirements.Setting page33.1、Motor Setting:3.1.1、Motor pole pairs:Fill in according to the motor manufacturer parameters.3.1.2、Hall phase shift angle:Fill in according to the motor manufacturer parameters.3.1.3、Motor type:Fill in according to the motor manufacturer parameters.Note:Wheel Hub motor is surface mount3.1.4、Hall,phase line exchange:exchange the motor forward and reverse.3.2、The controller to speedometer date output has2types:Single-line speedometer and hall speedometer, it needs to be decided by the vehicle’s speedometer.3.3、Moving assist and cruising function:Used in two-wheelersNote:Speed"3KM/H,torque9~19N.M3.4Cruise function:function selection,the default does not open.3.5Dual voltage setting:default single voltage。
IBM Spectrum Control V5.2.12 快速入门指南说明书
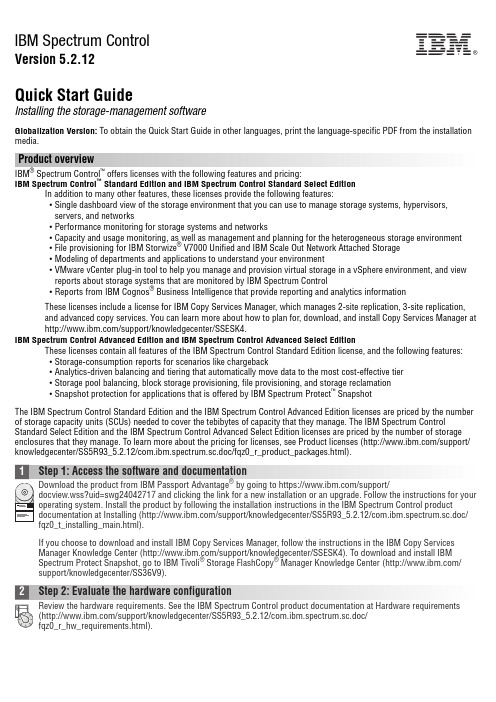
IBM Spectrum ControlVersion 5.2.12Quick Start GuideInstalling the storage-management softwareGlobalization Version:To obtain the Quick Start Guide in other languages, print the language-specific PDF from the installation media.Product overviewIBM®Spectrum Control™offers licenses with the following features and pricing:IBM Spectrum Control™Standard Edition and IBM Spectrum Control Standard Select EditionIn addition to many other features, these licenses provide the following features:v Single dashboard view of the storage environment that you can use to manage storage systems, hypervisors,servers, and networksv Performance monitoring for storage systems and networksv Capacity and usage monitoring, as well as management and planning for the heterogeneous storage environmentv File provisioning for IBM Storwize®V7000 Unified and IBM Scale Out Network Attached Storagev Modeling of departments and applications to understand your environmentv VMware vCenter plug-in tool to help you manage and provision virtual storage in a vSphere environment, and viewreports about storage systems that are monitored by IBM Spectrum Controlv Reports from IBM Cognos®Business Intelligence that provide reporting and analytics informationThese licenses include a license for IBM Copy Services Manager, which manages 2-site replication, 3-site replication, and advanced copy services. You can learn more about how to plan for, download, and install Copy Services Manager at /support/knowledgecenter/SSESK4.IBM Spectrum Control Advanced Edition and IBM Spectrum Control Advanced Select EditionThese licenses contain all features of the IBM Spectrum Control Standard Edition license, and the following features:v Storage-consumption reports for scenarios like chargebackv Analytics-driven balancing and tiering that automatically move data to the most cost-effective tierv Storage pool balancing, block storage provisioning, file provisioning, and storage reclamationv Snapshot protection for applications that is offered by IBM Spectrum Protect™SnapshotThe IBM Spectrum Control Standard Edition and the IBM Spectrum Control Advanced Edition licenses are priced by the number of storage capacity units (SCUs) needed to cover the tebibytes of capacity that they manage. The IBM Spectrum Control Standard Select Edition and the IBM Spectrum Control Advanced Select Edition licenses are priced by the number of storage enclosures that they manage. To learn more about the pricing for licenses, see Product licenses (/support/ knowledgecenter/SS5R93_5.2.12/com.ibm.spectrum.sc.doc/fqz0_r_product_packages.html).If you choose to download and install IBM Copy Services Manager, follow the instructions in the IBM Copy Services Manager Knowledge Center (/support/knowledgecenter/SSESK4). To download and install IBMSpectrum Protect Snapshot, go to IBM Tivoli®Storage FlashCopy®Manager Knowledge Center (/ support/knowledgecenter/SS36V9).2Step 2: Evaluate the hardware configurationReview the hardware requirements. See the IBM Spectrum Control product documentation at Hardware requirements (/support/knowledgecenter/SS5R93_5.2.12/com.ibm.spectrum.sc.doc/fqz0_r_hw_requirements.html).IBM®3Step 3: Evaluate the system configuration and install the prerequisite software Review the software requirements:v Learn about the software requirements for the product at Software requirements (/support/knowledgecenter/SS5R93_5.2.12/com.ibm.spectrum.sc.doc/fqz0_r_sw_requirements.html).v Learn about the hardware, products, and operating systems that you can use with IBM Spectrum Control at/support/docview.wss?uid=swg21386446.4Step 4: Install DB2Before you install IBM Spectrum Control, you must install the version of IBM DB2®Enterprise Server Edition that isincluded with IBM Spectrum Control. IBM Spectrum Control stores the information that it collects about storageresources in a DB2 database.Follow the instructions in DB2 (/support/knowledgecenter/SS5R93_5.2.12/com.ibm.spectrum.sc.doc/ fqz0_t_installing_db2.html).5Step 5: Install IBM Spectrum ControlYou can use an installation program or a command line in silent mode to install IBM Spectrum Control. Follow theinstructions in Installing IBM Spectrum Control (/support/knowledgecenter/SS5R93_5.2.12/com.ibm.spectrum.sc.doc/fqz0_t_installing_tpc.html).6Step 6: (Optional) Install Cognos Business Intelligence reportsThe IBM Spectrum Control installation process includes the option to install IBM Cognos Business Intelligence (BI)reports and the product that is required to produce these reports: Jazz™for Service Management and its reportingservices (IBM Tivoli Common Reporting). Cognos BI produces scheduled reports from the data that is gathered by IBM Spectrum Control.Learn about Cognos BI reports at Reporting (/support/knowledgecenter/SS5R93_5.2.12/com.ibm.spectrum.sc.doc/fqz0_c_webbasedgui_rpting_ic_ov.html). Also learn about the components that you must install to use Cognos BI reports at Install Jazz for Service Management and Tivoli Common Reporting(/support/knowledgecenter/SS5R93_5.2.12/com.ibm.spectrum.sc.doc/fqz0_c_jazzsm_tcr.html).If you choose not to install Cognos BI, you can use the reporting features of the IBM Spectrum Control user interface to produce reports about the status, capacity, and performance of the storage resources that you want to monitor. If you have the Advanced Edition or Advanced Select Edition license, chargeback and consumer reports are available.7Step 7: Get startedFollow the tasks in Getting started with IBM Spectrum Control (/support/knowledgecenter/SS5R93_5.2.12/com.ibm.spectrum.sc.doc/fqz0_r_getting_started.html).More informationFor more information, see the following resources:v PDF product documentation: Printable documentation (/support/knowledgecenter/SS5R93_5.2.12/ com.ibm.spectrum.sc.doc/fqz0_r_printable_pdf_files.html)v Product support: https:///support/entry/myportal/product/tivoli/ibm_spectrum_control/ibm_spectrum_control_standard_edition?productContext=365750483IBM Spectrum Control Version 5.2.12 Licensed Materials - Property of IBM. © Copyright IBM Corp. 2014, 2016. US Government Users Restricted Rights - Use, duplication or disclosure restricted by GSA ADP Schedule Contract with IBM Corp.IBM, the IBM logo, and ®are trademarks or registered trademarks of International Business Machines Corp., registered in many jurisdictions worldwide. Other product and service names might be trademarks of IBM or other companies. A current list of IBM trademarks is available on the web at “Copyright and trademark information” (/legal/copytrade.shtml).Printed in Ireland。
奥斯卡作用域OX 9000系列4合1仪器作用域多功能仪表分析仪记录器安全说明书
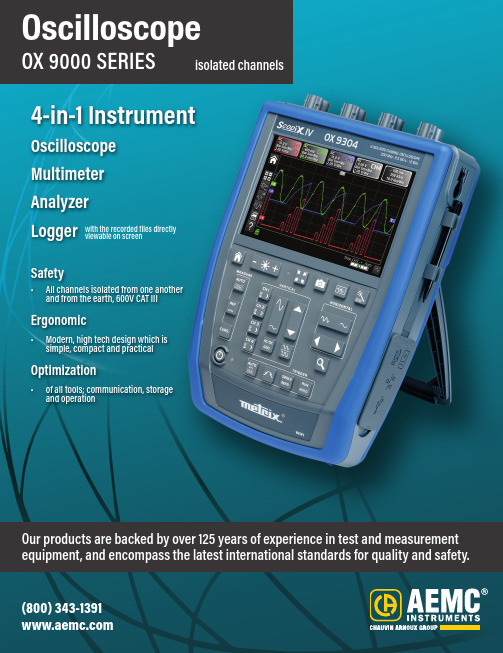
Our products are backed by over 125 years of experience in test and measurement equipment, and encompass the latest international standards for quality and safety.OscilloscopeOX 9000 SERIES4-in-1 InstrumentOscilloscope Multimeter AnalyzerLogger Safety•All channels isolated from one another and from the earth, 600V CAT IIIErgonomic•Modern, high tech design which is simple, compact and practicalOptimization•of all tools; communication, storage and operationisolated channelswith the recorded files directly viewable on screen2 Technical Assistance (800) 343-1391ERGONOMICSOriginalIn a housing tailor-made to be as compact as possible, the mechanical design makes it possible to integrate the hardware components in a small size with the keypad benefits from new technology developed inthe automotive industry.Scope in carrying case with shoulder strap, set of two 5 ft color-coded leads, alligator clips and test probes, 10 ft USB cable, µSD memory card, 1-PROBIX Banana Plug Adapter, 1 stylipen, LI-ION 5.8 Ah battery pack, PA40W-2 power adapter with 110V power cord. Additionalaccessories may be model dependent.Designed to simplify use with one button access to most functionsCHANNEL AND PARAMETER IDENTIFICATIONEach channel and related parameters are identified with identical color against a black background for simpler, quicker viewing.EASY ACCESS VIA TOUCH SCREENIntuitive icons are provided to facilitate their use, even with gloves on.ADJUSTABLE STRAPThis helps to optimize operation of the oscilloscope in your hand or on your shoulder when working in the field.A stand is also available to vary the orientation of the oscilloscope when it is placed on a bench. The oscilloscope can be safely left unattended using the Kensington locking system.NEW KEYPAD DESIGN FOR OPTIMUM USER COMFORTConfiguration and measurement displays are simple to access from the front panel in one of these 5 specific areas: Utilities (brightness, full screen, screenshot), Measurements, Vertical, Horizontal, Trigger.LINE POWER OR LI-ION BATTERYPort on left side.Technical Assistance (800) 343-1391 3APPLICATIONSElectronic maintenanceThe OX 9304 model is ideal for electronics with its300 MHz bandwidth, 4 x 600V CAT III isolated channels, advanced trigger functions, integrated FFT function,complex mathematical calculations on the curves, automatic measurements on 4 channels and the built-in WEB server.Industrial maintenanceThe OX 9304’s large 7-inch screen, 300 MHz bandwidth, 4 x 600V CAT III isolated channels and Harmonic Analyzer and Multimeter modes make it ideal for industrial maintenance applications.Ideal for electronic and industrial maintenanceIP54Housing protected against dust and water spray.DIRECT ACCESS ZOOM BUTTON7" WVGA WIDE COLOR TFT TOUCH SCREENMakes it easy to view and read the measurements clearly.It also provides a screen resolution of 800 x 480 dpi with manual or automatic brightness.TOUCH-SCREEN STYLUS STORAGEAmong the essential tools available, the sylus is equipped with a hook for the addition of a cord to make it captive, as required. One end is slightly flattened to prevent rolling when placed on a table or bench.COMMUNICATION INTERFACESThese are isolated from one another and from the measurement channels. A dedicated compartment on the right side protected by a flexible cover contains all the different communication interface ports:• USB host for communication with a PC• wired RJ45 or WiFi for communication with a PC or printing via a network printer• µSD card for data storage with quick transfer and forupgrading of the instrument's firmware AUTOSET BUTTONDIRECT SETTING AND SET-UP BUTTONS Quickly and effortlessly adjusts the horizontal and vertical; sensitivity and scales to provide the best resolution.Channels are isolated.4 Technical Assistance (800) 343-1391ACCESSORIESOSCILLOSCOPE OX 9000 SERIESThe plug and play accessories included areautomatically recognized when connected to the oscilloscope. They provide quick and easyimplementation with total user safety. Additionally, accessories equipped with BNC connectors orstandard banana plugs can also be connected when using the supplied adapter.Interchangeable ID Markers can be used on theaccessories plugged into a given channel to identify them with the trace color displayed on the screen.Additionally the 10:1 probe accessory is equipped with3 adjustable buttons to optimize its measurement capabilities.voltage measurements• by probe with different bandwidths and attenuation• by BNC or banana jack connection current measurements• by AC or AC/DC current clamp • directly through banana jack connections temperature measurements• using a K thermocouple sensor • using a PT100 RTD sensorAccessories & ReplacementsCat #2124.73 - PROBIX PRHX1 10:1 Probe, 250MHz 600V CAT III Cat #2124.77 - PROBIX Current Probe, 20mA-20A 1MHz-3dB Cat #5000.17 - Set of 5 styli pensOnce one of the provided standard accessories has been plugged in, it is automatically identified and itscharacteristics and calibration references are retrieved by the OX9000 Series Oscilloscope. All accessories are directly powered by the oscilloscope.Sensor coefficients scales and units of measure are managed automatically, as is channel configuration. Control buttons on the probes can be used to modify the settings of the channels to which they are connected. They also offer functions accessible on the oscilloscope's front panel.Accessories automatically recognized when connected to the oscilloscopeIdentification and Safety ManagementChannel Configuration and Sensor ManagementPROBE FUNCTIONSTechnical Assistance (800) 343-1391 5COMMUNICATIONChoice of communication interfaces―you can choose the type of communicaton to fit your requirements.Several communication choices are built into the OX9000 Series oscilloscope.• Wired Ethernet LAN network with integrated DHCP server for easy connection to your network• WiFi ® radio link to communicate with a PC, tablet or smartphone using the dedicated interfaces• USB for interfacing with the PC; record, recall or load configurations• µSD with >8 GB, default storage giving priority over the 1 GB internal memoryFile ManagementAny of the signal traces can be displayed instantaneously as the reference by pressing a single button which will obtain a comparison an immediate measurements of the deviation of ongoing measurements.Backups are available in various formats for direct export into a standard application such as Windows base spreadsheets or word processors.It is easy to take screenshots directly from the front panel and save them in a .PNG format, print documents on a network printer and transfer or delete files in the file manager.Data Processing• Use the oscilloscope screen to recall screenshots and stored traces for direct review on screen• On your PC, use the ScopeNet application in your web browser with either the USB or Ethernet connection for remote control and programming with SCPI commandsElectrical TroubleshootingEducationIn the laboratoryFor added equipment and operator safety all communication from theinstrument is totally isolated from the measurement process6 Technical Assistance (800) 343-1391Improved functions and performance levels of the OX9000 Series4 MODES: Oscilloscope, Multimeter, Analyzer, RecorderTrigger FunctionsAn oscilloscope with complex trigger functionsrecords what is necessary, while capturing all the faults The OX9000 models offer advanced triggers whichcomplement the main edge trigger options: pulse width, counting and delay.• The Delay mode enables you to observe any event with maximum resolution, even if it occurs a long time after effective triggering, or on two different channels.• The Counting mode enables you to count theevents before triggering, so that you can check the content of digital frames. For example, the trigger can be linked to a second “auxiliary” signal which is different from the “main” signal.Automatic MeasurementsComprehensive automatic measurements are displayed with cursors for precise analysis. The automaticmeasurements window displays all 20 parameters at the touch of a button for 4 channels. Two horizontal and vertical cursors can be used to view the section of the signal where the first automatic measurement was performed.A specific measurement area can then be selected by framing it with manual cursors for more accurate, reliable results.Direct comparison of two traces can be performed by checking the “reference memory deviation” box, so that these 20 signal parameters are displayed in terms of deviations.• wider bandwidth up to 300 MHz• new triggering and recording options • increased storage capacity, and more!• 12 bit resolution • 2.5 GS/secOSCILLOSCOPE:VIEW ALL 4 CHANNELS SIMULTANEOUSLY waveform + FFTwaveform + XY waveform + zoomThe Math FunctionsIn oscilloscope mode, the MATH functions (1, 2, 3 and 4) allow you to define a mathematical function for each of the traces, along with vertical scaling and labeling of the actual physical unit.The mathematical editor is capable of displaying 4 calculated traces on which all the automatic or cursor measurements remain available. This means it ispossible to examine the waveforms, such as the power (V x I), and perform all the associated measurements.A large number of operators are available, including +, -, x and / , as well as more complex operators such as sine, cosine, exponential, logarithm, square root, etc.opening the way for specific applications.Real-time Fast Fourier Transform (FFT) for frequency decomposition of your signals on 4 channelsThe FFT is used to calculate, from 2500 pointsupwards, the discrete representation of a signal in the frequency domain from its representation in the time domain. It is often particularly useful for arriving at an effective diagnosis during qualitative analysis of the signals:• measurement of the individual harmonics or distortion of a signal• analysis of a pulse response• search for the source of noise in the logic circuits Several weighting windows are available, as well as 2 representation modes: linear or logarithmic (scale in dB). The 2 cursors can then be used for precise measurements of the frequency lines, the levels and the attenuations, taking advantage of the 80 dB dynamic range allowed by the 12-bit / 2.5 GS/s conversion.The autoset button makes it easier to obtain anoptimum spectral representation to which a graphical zoom can be applied to analyze all the details of the spectrum.Technical Assistance (800) 343-1391 74 MODES: Oscilloscope, Multimeter, Analyzer, RecorderHarmonics4 Simultaneous ChannelsHarmonic AnalysisHarmonic analysis is performed on all 4 channels up to the 63rd order to comply with the requirements of the EN 50160 standard (THD on harmonics up to the 50th), with a fundamental frequency between 40 and 450 Hz.It is possible to preselect the frequency of the fundamental for the standards (50 Hz, 60 Hz and 400 Hz).This function helps to improve analytical performance and, above all, measurement when the level of a harmonic order is greater than the fundamental.It is possible to view the harmonic analyses of two or four channels simultaneously: RMS level, harmonic distortion, harmonic frequency, phase of the harmonic in relation to the fundamental.MultimeterBy simply selecting the dedicated icons, you can gain access to the multimeter mode without changing the measurement input channels. The OX9000 models offer an 8,000-count TRMS digital multimeter with two or four channels which can perform the following measurements:• amplitude (DC or AC voltage and current, power, temperature, etc.)• resistance, continuity, capacitance • component diode testsTemperature is measured using the Pt 100 and Pt 1000 sensors or K thermocouples via the dedicated PROBIXsensors. The power measurements are proposed as follows with choice of the configuration:• single-phase power• three-phase power on balanced network without neutral Measurement between H and V cursors:T1, T2, Dt, 1/Dt, V1, V2, dV, Ph• three-phase power on balanced network with neutral • 3-wire three-phase power (2-wattmeters method)Recorder/loggerThis is the mode for recording the trends in Multimeter mode. A genuine fast digital logger is provided inside the instrument to monitor the variations of physical or mechanical phenomena over time. It offers acquisition intervals as short as 40µs between 2 measurements and recording can cover any period from 2 seconds to one month.The four modes are directly accessed at the press of a button or touchscreen icon providing instant access the mode you needChauvin Arnoux ®, Inc. d.b.a AEMC ® Instruments • 15 Faraday Dr. • Dover, NH 03820 USA • (800) 343-1391 • (508) 698-2115 • Fax (508) 698-2118E-mail:**************| Export Department: +1 (603) 749-6434 x520 • Fax +1 (603) 740-7550 •E-mail:***************950.BR-OX9000Series_1021 • Printed in the USA© 2021 Chauvin Arnoux ®, Inc. d.b.a. AEMC® Instruments Call the AEMC ® Instruments Technical Assistance Hotline for immediate consultation with an applications engineer: (800) 343-1391 (Ext. 351)。
Lenovo ThinkAgile HX3321 Certified Node for SAP HA
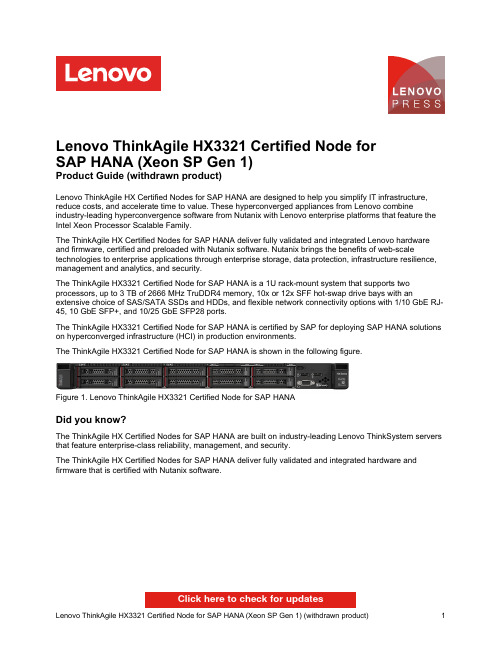
Lenovo ThinkAgile HX3321 Certified Node forSAP HANA (Xeon SP Gen 1)Product Guide (withdrawn product)Lenovo ThinkAgile HX Certified Nodes for SAP HANA are designed to help you simplify IT infrastructure, reduce costs, and accelerate time to value. These hyperconverged appliances from Lenovo combine industry-leading hyperconvergence software from Nutanix with Lenovo enterprise platforms that feature the Intel Xeon Processor Scalable Family.The ThinkAgile HX Certified Nodes for SAP HANA deliver fully validated and integrated Lenovo hardware and firmware, certified and preloaded with Nutanix software. Nutanix brings the benefits of web-scale technologies to enterprise applications through enterprise storage, data protection, infrastructure resilience, management and analytics, and security.The ThinkAgile HX3321 Certified Node for SAP HANA is a 1U rack-mount system that supports two processors, up to 3 TB of 2666 MHz TruDDR4 memory, 10x or 12x SFF hot-swap drive bays with an extensive choice of SAS/SATA SSDs and HDDs, and flexible network connectivity options with 1/10 GbE RJ-45, 10 GbE SFP+, and 10/25 GbE SFP28 ports.The ThinkAgile HX3321 Certified Node for SAP HANA is certified by SAP for deploying SAP HANA solutions on hyperconverged infrastructure (HCI) in production environments.The ThinkAgile HX3321 Certified Node for SAP HANA is shown in the following figure.Figure 1. Lenovo ThinkAgile HX3321 Certified Node for SAP HANADid you know?The ThinkAgile HX Certified Nodes for SAP HANA are built on industry-leading Lenovo ThinkSystem servers that feature enterprise-class reliability, management, and security.The ThinkAgile HX Certified Nodes for SAP HANA deliver fully validated and integrated hardware and firmware that is certified with Nutanix software.Click here to check for updatesFigure 2. ThinkAgile HX3321 Certified Node for SAP HANA front viewFigure 3. ThinkAgile HX3321 Certified Node for SAP HANA 10-drive bay rear viewThe following figure shows the rear view of the ThinkAgile HX3321 Certified Node for SAP HANA with 12 drive bays.Figure 4. ThinkAgile HX3321 Certified Node for SAP HANA 12-drive bay rear viewThe rear of the ThinkAgile HX3321 Certified Node for SAP HANA includes the following components: Three (models with 10 drive bays) or one (models with 12 drive bays) PCIe expansion slotsTwo SFF SAS/SATA hot-swap rear drive bays (models with 12 drive bays)One LOM card slotOne 1 GbE port for XClarity ControllerOne VGA portTwo USB 3.0 portsTwo hot-swap power suppliesTable 4. Memory selection optionsDescription Part number Featurecode Quantity2666 MHz RDIMMsThinkSystem 8GB TruDDR4 2666 MHz (1Rx8 1.2V) RDIMM 7X77A01301AUU1-12+12------ThinkSystem 16GB TruDDR4 2666 MHz (2Rx8 1.2V) RDIMM 7X77A01303AUNC 12-12+12----ThinkSystem 32GB TruDDR4 2666 MHz (2Rx4 1.2V) RDIMM 7X77A01304AUND --1224---2666 MHz LRDIMMsThinkSystem 64GB TruDDR4 2666 MHz (4Rx4 1.2V) LRDIMM 7X77A01305AUNE ----1224--2666 MHz 3DS RDIMMsThinkSystem 64GB TruDDR4 2666MHz (4Rx4, 1.2V) 3DS RDIMM4ZC7A08716AUW5------12+12-ThinkSystem 128GB TruDDR4 2666 MHz (8Rx4 1.2V) 3DS RDIMM 7X77A01307AUNF-----1224192 G B288 G B384 G B576 G B768 G B1.5 T B2.25 T B 3 T B3m Cat6 Green Cable 00WE139AVG010m Cat6 Green Cable 90Y3718A1MT 25m Cat6 Green Cable90Y3727A1MWDescriptionPart number Feature code The following table lists transceivers and cables for the 10 GbE SFP+ ports.Table 11. Transceivers and cables for 10 GbE SFP+ portsDescriptionPart numberFeature code10 GbE SFP+ SR transceivers for 10 GbE SFP+ ports Lenovo 10GBASE-SR SFP+ Transceiver 46C34475053Lenovo 10GBASE-LR SFP+ Transceiver 00FE331B0RJOptical cables for 10 GbE SFP+ SR transceivers Lenovo 0.5m LC-LC OM3 MMF Cable 00MN499ASR5Lenovo 1m LC-LC OM3 MMF Cable 00MN502ASR6Lenovo 3m LC-LC OM3 MMF Cable 00MN505ASR7Lenovo 5m LC-LC OM3 MMF Cable 00MN508ASR8Lenovo 10m LC-LC OM3 MMF Cable 00MN511ASR9Lenovo 15m LC-LC OM3 MMF Cable 00MN514ASRA Lenovo 25m LC-LC OM3 MMF Cable00MN517ASRB Passive SFP+ DAC cables for 10 GbE SFP+ ports Lenovo 0.5m Passive SFP+ DAC Cable 00D6288A3RG Lenovo 1m Passive SFP+ DAC Cable 90Y9427A1PH Lenovo 1.5m Passive SFP+ DAC Cable 00AY764A51N Lenovo 2m Passive SFP+ DAC Cable 00AY765A51P Lenovo 3m Passive SFP+ DAC Cable 90Y9430A1PJ Lenovo 5m Passive SFP+ DAC Cable 90Y9433A1PK Lenovo 7m Passive SFP+ DAC Cable00D6151A3RHActive SFP+ DAC cables for 10 GbE SFP+ ports Lenovo 1m Active DAC SFP+ Cable 00VX111AT2R Lenovo 3m Active DAC SFP+ Cable 00VX114AT2S Lenovo 5m Active DAC SFP+ Cable00VX117AT2TSFP+ active optical cables for 10 GbE SFP+ ports Lenovo 1m SFP+ to SFP+ Active Optical Cable 00YL634ATYX Lenovo 3m SFP+ to SFP+ Active Optical Cable 00YL637ATYY Lenovo 5m SFP+ to SFP+ Active Optical Cable 00YL640ATYZ Lenovo 7m SFP+ to SFP+ Active Optical Cable 00YL643ATZ0Lenovo 15m SFP+ to SFP+ Active Optical Cable 00YL646ATZ1Lenovo 20m SFP+ to SFP+ Active Optical Cable00YL649ATZ2The following table lists transceivers and cables for the 25 GbE SFP28 ports. Table 12. Transceivers and cables for 25 GbE SFP28 portsDescription Part number Feature code25 GbE SFP28 SR transceivers for 25 GbE SFP28 portsLenovo 25GBASE-SR SFP28 Transceiver7G17A03537AV1B Optical cables for 25 GbE SFP28 SR transceiversLenovo 0.5m LC-LC OM3 MMF Cable00MN499ASR5 Lenovo 1m LC-LC OM3 MMF Cable00MN502ASR6 Lenovo 3m LC-LC OM3 MMF Cable00MN505ASR7 Lenovo 5m LC-LC OM3 MMF Cable00MN508ASR8 Lenovo 10m LC-LC OM3 MMF Cable00MN511ASR9 Lenovo 15m LC-LC OM3 MMF Cable00MN514ASRA Lenovo 25m LC-LC OM3 MMF Cable00MN517ASRB Passive copper cables for 25 GbE SFP28 portsLenovo 1m Passive 25G SFP28 DAC Cable7Z57A03557AV1W Lenovo 3m Passive 25G SFP28 DAC Cable7Z57A03558AV1X Lenovo 5m Passive 25G SFP28 DAC Cable7Z57A03559AV1Y Active optical cables for 25 GbE SFP28 portsLenovo 3m 25G SFP28 Active Optical Cable7Z57A03541AV1F Lenovo 5m 25G SFP28 Active Optical Cable7Z57A03542AV1G Lenovo 10m 25G SFP28 Active Optical Cable7Z57A03543AV1H Lenovo 15m 25G SFP28 Active Optical Cable7Z57A03544AV1J Lenovo 20m 25G SFP28 Active Optical Cable7Z57A03545AV1KPower supplies and cablesThe ThinkAgile HX3321 Certified Nodes for SAP HANA ship with two power supplies. The following table lists the power supply options that are available for selection.Table 13. Power supply selection optionsDescription Featurecode QuantityThinkSystem 750W (230/115V) Platinum Hot-Swap Power Supply AVWA2 ThinkSystem 750W (230V) Titanium Hot-Swap Power Supply AVW92 ThinkSystem 1100W (230V/115V) Platinum Hot-Swap Power Supply AVWB2Israel 2.8m, 10A/250V, C13 to SI 32 Line Cord 39Y79206218Israel 4.3m, 10A/250V, C13 to SI 32 Line Cord 81Y23816579Italy 2.8m, 10A/250V, C13 to CEI 23-16 Line Cord 39Y79216217Italy 4.3m, 10A/250V, C13 to CEI 23-16 Line Cord 81Y23806493Japan 2.8m, 12A/125V, C13 to JIS C-8303 Line cord 46M2593A1RE Japan 2.8m, 12A/250V, C13 to JIS C-8303 Line Cord 4L67A083575472Japan 4.3m, 12A/125V, C13 to JIS C-8303 Line Cord 39Y79266335Japan 4.3m, 12A/250V, C13 to JIS C-8303 Line Cord 4L67A083626495Korea 2.8m, 12A/250V, C13 to KS C8305 Line Cord 39Y79256219Korea 4.3m, 12A/250V, C13 to KS C8305 Line Cord 81Y23856494South Africa 2.8m, 10A/250V, C13 to SABS 164 Line Cord 39Y79226214South Africa 4.3m, 10A/250V, C13 to SABS 164 Line Cord 81Y23796576Switzerland 2.8m, 10A/250V, C13 to SEV 1011-S24507 Line Cord 39Y79196216Switzerland 4.3m, 10A/250V, C13 to SEV 1011-S24507 Line Cord 81Y23906578Taiwan 2.8m, 10A/125V, C13 to CNS 10917-3 Line Cord 23R71586386Taiwan 2.8m, 10A/250V, C13 to CNS 10917-3 Line Cord 81Y23756317Taiwan 2.8m, 15A/125V, C13 to CNS 10917-3 Line Cord 81Y23746402Taiwan 4.3m, 10A/125V, C13 to CNS 10917-3 Line Cord 4L67A08363AX8BTaiwan 4.3m, 10A/250V, C13 to CNS 10917-3 Line Cord 81Y23896531Taiwan 4.3m, 15A/125V, C13 to CNS 10917-3 Line Cord 81Y23886530United Kingdom 2.8m, 10A/250V, C13 to BS 1363/A Line Cord 39Y79236215United Kingdom 4.3m, 10A/250V, C13 to BS 1363/A Line Cord 81Y23776577United States 2.8m, 10A/125V, C13 to NEMA 5-15P Line Cord 90Y30166313United States 2.8m, 10A/250V, C13 to NEMA 6-15P Line Cord 46M2592A1RF United States 2.8m, 13A/125V, C13 to NEMA 5-15P Line Cord 00WH5456401United States 4.3m, 10A/125V, C13 to NEMA 5-15P Line Cord 4L67A083596370United States 4.3m, 10A/250V, C13 to NEMA 6-15P Line Cord 4L67A083616373United States 4.3m, 13A/125V, C13 to NEMA 5-15P Line Cord4L67A08360AX8ADescriptionPart number Feature code Configuration note: If the 1100 W AC power supplies in the certified node are connected to a low-voltage power source (100 - 125 V), the only supported power cables are those that are rated above 10 A; cables that are rated at 10 A are not supported.Rack installationRack installationThe ThinkAgile HX3321 Certified Nodes for SAP HANA ship with a rail kit. The following table lists the rail kit options that are available for selection.Table 15. Rack kit selection optionsDescription FeaturecodeQuantity(min / max)4-post rail kitsThinkSystem Tool-less Slide Rail AXCA0 / 1 ThinkSystem Tool-less Slide Rail Kit with 1U CMA AXCB0 / 1 Lockable front bezelThinkSystem 1U Security Bezel AUWR0 / 1Configuration note: One of the rail kits is required for selection.The following table summarizes the rail kit features and specifications.Table 16. Rail kit features and specifications summaryFeature Tool-less Slide RailWithout CMA With 1U CMACMA Not included IncludedRail length730 mm (28.74 in.)807 mm (31.8 in.)Rail type Full-out slide (ball bearing)Tool-less installation YesIn-rack maintenance Yes1U PDU support Yes0U PDU support Limited*Rack type IBM and Lenovo 4-post, IEC standard-compliant Mounting holes Square or roundMounting flange thickness 2 mm (0.08 in.) – 3.3 mm (0.13 in.)Distance between front and rear mounting flanges^609.6 mm (24 in.) – 863.6 mm (34 in.)* If a 0U PDU is used, the rack cabinet must be at least 1100 mm (43.31 in.) deep if no CMA is used, or at least 1200 mm (47.24 in.) deep if a CMA is used.^ Measured when mounted on the rack, from the front surface of the front mounting flange to the rear most point of the rail.TrademarksLenovo and the Lenovo logo are trademarks or registered trademarks of Lenovo in the United States, other countries, or both. A current list of Lenovo trademarks is available on the Web athttps:///us/en/legal/copytrade/.The following terms are trademarks of Lenovo in the United States, other countries, or both:Lenovo®AnyBay®Lenovo ServicesThinkAgile®ThinkSystem®TruDDR4XClarity®The following terms are trademarks of other companies:Intel® and Xeon® are trademarks of Intel Corporation or its subsidiaries.Linux® is the trademark of Linus Torvalds in the U.S. and other countries.Microsoft®, PowerShell, Windows PowerShell®, and Windows® are trademarks of Microsoft Corporation in the United States, other countries, or both.Other company, product, or service names may be trademarks or service marks of others.。
西门子 KTP600 基本面板操作指南说明书
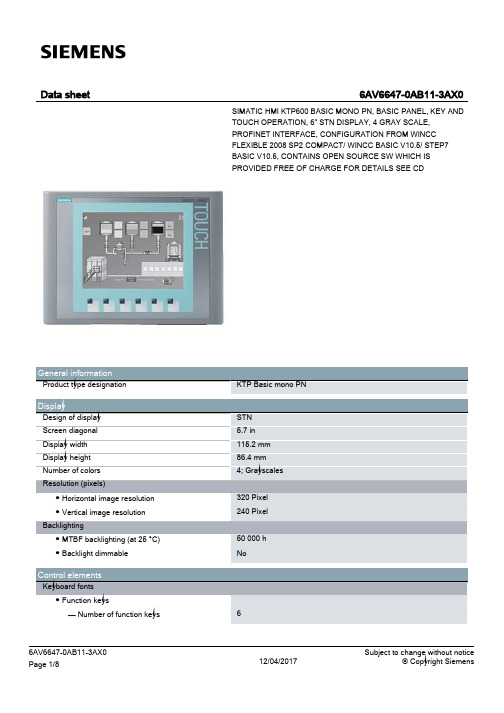
6AV6647-0AB11-3AX0 Page 2/8
12/04/2017
Subject to change without notice © Copyright Siemens
Number of industrial Ethernet interfaces Number of RS 485 interfaces Number of RS 422 interfaces Number of RS 232 interfaces Number of USB interfaces Number of 20 mA interfaces (TTY) Number of parallel interfaces Number of other interfaces Number of SD card slots With software interfaces Industrial Ethernet
● Industrial Ethernet status LED
Protocols PROFINET Supports protocol for PROFINET IO IRT PROFIBUS MPI Protocols (Ethernet) ● TCP/IP ● DHCP ● SNMP ● DCP ● LLDP WEB characteristics ● HTTP ● HTML Further protocols ● CAN ● EtherNet/IP ● MODBUS
Operating systems proprietary pre-installed operating system ● Windows CE
Yes Yes Yes
Yes Yes Yes Yes Yes Yes Yes
Moxa产品说明书

Copyright © 2017 Moxa Inc.Released on March 31, 2017About MoxaMoxa is a leading provider of edge connectivity, industrial computing, and network infrastructure solutions for enabling connectivity for the Industrial Internet of Things. With over 30 years of industry experience, Moxa has connected more than 50 million devices worldwide and has a distribution and service network that reaches customers in more than 70 countries. Moxa delivers lasting business value by empowering industry with reliable networks and sincere service for industrial communications infrastructures. Information about Moxa’s solutions is available at .How to Contact MoxaTel: 1-714-528-6777 How to Build an IoT Application with Moxa's ThingsPro and AWS IoT ServiceMoxa Technical Support Team****************Contents1Introduction .................................................................................... 2 2Application Scenario ....................................................................... 2 3Prerequisites ................................................................................... 3 4Solution .......................................................................................... 3 5Additional Reading (8)1IntroductionMoxa’s ThingsPro™ 2.0 Suite simplifies the development of IoT applications and facilitates data acquisition as well as remote device management. ThingsPro provides Modbus communications, data acquisition, wireless networking, and device management, in a few simple steps, allowing users to focus on developing applications instead of complex system integration.For users who develop data acquisition and asset management software programs on their own, ThingsPro provides the ability to transfer field data to the AWS IoT service without requiring any additional programming on the gateway. ThingsPro 2.0 includes generic Modbus protocol and AWS IoT support, which you can use to easily configure protocol data polling tables and AWS IoT connection settings. You can then upload the data collected to the AWS IoT service. In this article, we describe how to configure the MODBUS device template in ThingsPro, retrieve data from ThingsPro, and upload the data to a remote HTTP server.2Application ScenarioSet up an environment to send real-time device data updates to the AWS IoT service using ThingsPro 2.0. Here, ThingsPro is used as a Modbus data logger and the AWS function provided by ThingsPro isused to configure the connection to the AWS IoT service.3 Prerequisites1. Moxa UC-8112 gateway computer with Internet access, and ThingsPro2.0 Gateway and SDcard installed.For information about setting up a Moxa UC-8112, refer to the ThingsPro User’s Manual .2. PC/notebook with Chrome browser and Microsoft Device Explorer installed3. Modbus device (e.g., Moxa ioLogik-E2242)4. AWS IoT configuration: thing name, CA certificate, device certificate, device private key,mqtt topics, and mqtt endpoint4 SolutionComplete the following steps to create your IoT application using ThingsPro and AWS IoT service:1. Choose an equipment template.a. In the ThingsPro Gateway web page, click (Menu).b. In the ThingsPro Gateway menu, click on the Modbus & Logging link.c. Open the EQUIPMENT TEMPLATE tabd. Browse through the Template List to locate the template corresponding to the Modbusdevice or create a new template.For details on creating a new template, refer to the ThingsPro User’s Manual .In this article, we use the Modbus device E2242, which is already listed in the TemplateList .2. Create an instance of the Modbus device .a. Select the MODBUS DEVICE tab.b. Configure the Modbus device with a communication interface (serial or Ethernet).Because the connected device (E2242) uses Modbus TCP protocol, click on theMODBUS/TCP tab.i. Click (Add TCP interface).ii. Fill in the TCP interface settings and click SAVE .The Modbus/TCP interface for E2242 is added to the TCP List .iii. Click on the (Add connected device) button corresponding to E2242 to adda connected device.iv. Fill in the Device Name .v. Select a Template to combine MODBUS/TCP interface with the Modbus device.vi. Specify the Unit ID for the device and click SAVE .ThingsPro will now start continuously polling data from the device.To check the status, click(Show connected devices). If the Request Status is green, ThingsPro is able to send requests to the Modbus TCP deviceand receive data.e the AWS IoT service for real-time data update.a.In the ThingsPro Gateway menu, click on the AWS IoT link in the Applications section.b.Fill in the AWS IoT service details.c.Select the Enable optiond.Click SAVEThe AWS IoT interface will use the information provided to create a connection with the AWS IoT service. Once the connection is established, data can be uploaded to the AWS IoT service in real time.5Additional ReadingGetting Started with AWS IoT。
维亚维诺 SmartClass 4800 网络测试仪产品说明书

With the ability to test electrical and optical Ethernet links as well T1and E1 interfaces, the SmartClass 4800 allows technicians to test all common business class interfaces. T echnicians can test the quality of voice services regardless of whether they are delivered via VoIP or PRI. The industry’s smallest handheld instrument can test throughout the service life cycle, including service activation, troubleshooting, and maintenance. Advanced Ethernet test features such as TrueSpeed VNF per RFC 6349 and, J-Profiler help field technicians test their networks faster and more accurately than ever before.Key Benefitsy Optimized for field use witha multitouch screen, scripted workflows, and clear resultsy Supports efficient best practices with repeatable methods and proceduresKey Featuresy Electrical (10/100/1000) and optical (100M, 1GE, 10GE) Ethernet interfacesy Automated, enhanced RFC 2544 and SAMComplete testing per ITU-T Y.1564y Integrated burst testing approach per MEF 34 and RFC 6349 TrueSpeed VNF™ TCP throughput testingy Compatible with VIAVI fiber microscopes, and optical power metersy Supports the Datacom Expansion Module (DEM), which expands the testing of legacy technologies, specifically Datacom serial interfacesApplicationsy Business services installations, service activation and troubleshootingy Mobile and backhaul characterization, validation, and troubleshootingBrochureVIAVISmartClass 4800Tool of choice for all-in-one service testingOptimized for business services installation teams, the SmartClass 4800 is the modern tool for ensuring data and voice services achieve expected key performance indicators (KPI).Best Practice Workflow (Single and Multiple Services):1. J-QuickCheck: Basic Connectivity and Throughput Test2. Single-Service: Enhanced RFC 25443. Multi-Service: Y.1564 SAMComplete For Ethernet KPI Verification4. J-Proof Layer 2 Control Plane Transparency Test5. RFC 6349 TrueSpeed VNF:Layer 4 TCP ThroughputThis test workflow is applicable to Ethernet Business Services and Wireless Backhaul network topologies.TrueSAM Saves Valuable Service Activation TimeT est better and quicker with automated tests combined into one ultimate installation tool:y J-QuickCheck — a fast, automated test (RFC 2544, Y .1564) for validating end-to-end and auto-negotiation configurationy Enhanced RFC 2544 — an automated turn-up test for validating key performance indicators (KPIs)/concurrently measuring SLAs such as throughput, frame delay , delay variation, frame loss, and committed burst size (CBS) — optionaly Y .1564 SAMComplete — an automated service verification test that speeds the installation of multiple classes of services (COS)y TrueSpeed VNF per RFC 6349 — an automated, standards-based test that can save up to 25% of operating expenses (OpEx) and reveals the reason for slow file downloads, eliminating finger-pointingy Interoperable with VIAVI Fusion for throughput testing, including TrueSpeed VNF and Fusion QT-600Optimized for Field TechniciansThe SmartClass 4800 makes testing Ethernet and voice services easy: y All test interfaces are readily availabley Compact form factor for easy portability: 7 x 9.5 x 3 in (17.8 x 24.1 x 7.62 cm) y Large 7 in multi-touch displayy T ablet-like interface for easy navigation through test information and advanced workflows y Integrated WiFi and Bluetooth lets you easily connect test sets and offload resultsCompatible with VIAVI Solutions Fiber Test ToolsThe SmartClass 4800 is compatible with :y The P5000i and FiberChek fiber microscope for connector end-face inspection and analysis y MP-Series optical power meters for optical power and loss measurementsOptimized for Easy Field Usey Fixed test interfaces eliminate loose pluggable modules y LEDs indicate plug-ins for testsy A streamlined user interface provides simple pass/fail, green/red results y Extended battery life enables longer test times y Boots up rapidly from power-on to test startSmartClass 4800SmartClass 4800PEthernetEthernetEthernetEthernet LAN/WANPart of the Leading T-BERD/MTS Test PortfolioStrataSyncEmpower Y our AssetsStrataSync is a hosted, cloud-enabled solution for managing assets, configurations, and test data on VIAVI instruments. It ensures that all instrument software is current and the latest options are installed. StrataSync lets you manage inventory , test results, andperformance data anywhere with browser-based ease while it also improves technician and instrument efficiency. StrataSync manages and tracks test instruments, collects and analyzes results from the entire network, and it informs and trains the workforce.VIAVI StrataSync enabledCommon Application BaseSame user interface + same results + same methods and proceduresActivate services more quickly andaccuratelyReduce mean time to repair (MTTR) on network problemsT est the widest range of traditional and emerging telecom interfacesEnables Network Evolution — Today and TomorrowThe SmartClass 4800 meets leading-edge, carrier-grade Ethernet requirements: y Ensures reliability with link and service OAM (IEEE 802.3ah, 802.1ag, and ITU-T Y .1731)y Validates network scalability with VLAN, Q-in-Q, MAC-in-MAC, MPLS, and VPLS tunnelling technologiesy Full-featured VoIP and IP video turn-up and troubleshooting tests y Supports packet transport network (PTN) evolution with MPLS-TPtechnologyEnhanced RFC 2544 with J-QuickCheck SAMComplete per ITU-T Y .1564Fusion TrueSpeed VNF per RFC 6349© 2021 VIAVI Solutions Inc.Product specifications and descriptions in this document are subject to change without notice.Patented as described at /patentsSmartClass4800-br-tfs-tm-ae 30168388 911 0821C ontact Us+1 844 GO VIAVI(+1 844 468 4284)To reach the VIAVI office nearest you, visit /contact。
- 1、下载文档前请自行甄别文档内容的完整性,平台不提供额外的编辑、内容补充、找答案等附加服务。
- 2、"仅部分预览"的文档,不可在线预览部分如存在完整性等问题,可反馈申请退款(可完整预览的文档不适用该条件!)。
- 3、如文档侵犯您的权益,请联系客服反馈,我们会尽快为您处理(人工客服工作时间:9:00-18:30)。
€
€
6. You may have noticed that the simulated power is higher than the calculated in Part 5. To explore the reasons, simulate the power dissipation at different clock frequencies (100MHz, 200MHz, 300MHz, … 500MHz) and plot power versus frequency. Does power extrapolate to 0 at DC? Why doesn’t it? (10 pts)
Байду номын сангаас
EECS 141
In last homework we have learned how to calculate the equivalent capacitance and resistance of a logic gate from basic device parameters. In this homework we will learn an alternative approach to extracting capacitance and resistance. We will do so through simulation. 1. Use the unit size inverter from homework #1 and construct a simulation schematic as shown in Fig. 1 below. VDD is 1V. Specify the pulsating input source same as in homework #1 (500MHz, 10ps rise/fall time, V1=0V and V2=1V). Simulate the propagation delay in two loading cases: CL=2fF and CL=4fF. (8 pts)
Figure 1 Simulation Schematic to Extract Inverter Resistance and Output Capacitance.
CL tpHL tpLH
2fF 20.1ps 22.7ps
4fF 33.7ps 38.3ps
2. Next we will extract the equivalent capacitance and resistance of this inverter, assuming that propagation delay of an inverter can be approximated by
Explain why the discrepancy between calculation and simulation is within or beyond your expectation. (10 pts)
t pHL + t pLH 32.5 ps + 39.5 ps = = 36 ps 2 2
UNIVERSITY OF CALIFORNIA College of Engineering Department of Electrical Engineering and Computer Sciences
Jan M. Rabaey Homework #6
Due Monday, March 16, 5pm, box in 240 Cory
€
Figure 3 Simulation Schematic from Homework #1.
Hand calculation:
t p = 0.69 × Req × (Cd + 4 Cg ) = 0.69 × 10.6 kΩ × (0.93 fF + 4 × 0.57 fF )
t p = 23.5 ps
€
7. You have learned from recent lectures that the dynamic power of an inverter actually consists of two parts: power due to charging and discharging load capacitance, and power due to short circuit conduction. Can you design an experiment in simulation that can separate these two parts in the total power dissipation? (0 pts. This part of the homework is optional and will not be graded. It is here to entertain your curiosity and creativity!)
Therefore
20.1 ps + 22.7 ps = 0.69 × Req × (Cd + 2 fF ) 2 33.7 ps + 38.3 ps = 0.69 × R × (C + 4 fF ) eq d 2
Req = 10.6 kΩ Cd = 0.93 fF
€
3. To estimate input capacitance of the inverter, replace the load capacitor in Fig. 1 with another unit-size inverter. Remember € to load the additional inverter with a 2fF capacitor (Fig. 2). Simulate the propagation delay of the original inverter and estimate its input capacitance (Cg). (8 pts)
There is apparently large discrepancy between calculation and simulation, owing to several € (model approximation, un-equal pull-up and pull-down, etc.). But the biggest factor is factors the € finite rise and fall time at the inverter’s input. The 0.69×R×C equation assumes step input. Actual input to the inverter however has finite slope. The simulated result is hence the sum of its step response time and the ramp time of input. As a matter of fact propagation delay at the inverter’s input in Fig. 3 is
t pHL + t pLH 22.8 ps + 27.4 ps = = 25.1 ps 2 2
A more appropriate equation that calculates the delay with ramped input is
€
t p ,ramp = t p ,step +
VT* × t p ,in VDD
Linear fit to above curve yields:
P = 3.7 × 10−15 × f + 12.6 nW
Apparently when frequency (f) is 0, power is not. The extra 12.6nW can be considered the leakage power of this inverter.
Figure 4 Adding a Small Resistor to the Inverter’s Supply.
Hand calculation:
2 P = CV 2 f = (Cd + 4 Cg ) × VDD ×f
P = (0.93 f + 4 × 0.57 f ) × 12 × 500 M = 1.6µW
€
Or
36 ps = 23.5 ps +
VT* ≈ 0.5V
VT* × 25.1 ps 1V
€
5. Next € we will research on another important aspect of digital circuit design: energy. Use the capacitance estimated in Parts 2 and 3, calculate dynamic power dissipation of the inverter circled in Fig. 3, then compare it with simulated average power dissipation. To isolate the inverter from rest of the circuit, a simple method is to insert an arbitrarily small resistor in series with the inverter’s supply (Fig. 4). (6 pts)
Figure 2 Simulation Schematic to Extract Inverter Input Capacitance.