ch4 铁水预处理
常用铁水预处理技术

常用铁水预处理技术常用铁水预处理技术铁水预处理基础知识1、什么是铁水预处理?★铁水预处理指铁水兑人炼钢炉之前,为除去某些有害成份或回收某些有益成分的处理过程。
针对炼钢而言,主要是使铁水中硅、磷、硫含量降低到所要求的范围,以简化炼钢过程,提高钢的质量。
铁水预处理具体分为铁水炉外脱硅、脱磷和脱硫,有时脱磷和脱硫同时进行。
对于铁水含有特殊元素提纯精炼或资源综合利用而进行的提钒、提铌、提钨等预处理技术则称为特殊预处理。
2、什么是铁水“三脱”技术?★指铁水兑人炼钢炉之前,进行脱硫、脱硅、脱磷的预处理工艺过程。
3、铁水脱硫的目的是什么?★提高钢质、扩大品种和改善炼钢操作,提高钢的机械、工艺性能。
4、铁水脱硅的目的是什么?⑴减少转炉炼钢渣量、改善操作和提高炼钢经济指标。
硅是氧气转炉炼钢发热的元素,所以为了提高炼钢熔池温度和早化渣,往往希望铁水含硅高一些,但实践证明铁水含硅高时,为了保证转炉渣有较高的碱度,势必增加石灰消耗量,使渣量增多,冶炼时间延长,耗氧量增加,喷溅加剧,铁损增加,并给操作带来困难,从而降低炼钢生产率和增加生产成本。
铁水含硅量一般应控制在0.4%以下的水平。
(2)铁水预脱磷的需要脱硅是铁水预脱磷的先决条件。
铁水预脱磷要求脱磷反应区的氧位高,当加入氧化剂提高氧位时,硅首先就与氧作用而降低铁水中的氧位。
为此,脱磷首先要脱硅,脱磷前控制硅含量一般要求在0.15%以下。
5.铁水脱磷的目的是什么?(1)生产低磷钢、超低磷钢和不锈钢等工艺需要。
磷在钢中对性能的影响,除少数钢种为提高强度或耐大气腐蚀性,要求有一定含磷外,对大多数钢种是有害的,它降低钢的冲击韧性,尤其是低温冲击韧性;磷的枝晶偏析使板材产生带状组织,造成钢板各向异性。
随着新技术材料的发展,对某些品种钢要求磷含量≤0.01%(低磷钢) 或≤0.005%(超低磷钢) 。
用转炉工艺脱磷,虽然有较好的脱磷效果,但达到这种低磷的水平是难以完成的,如采取多次造渣操作,有可能达到,但都存在渣料消耗大,冶炼时间长,热损失大,金属收得率低等问题。
铁水预处理工艺技术操作规程范本
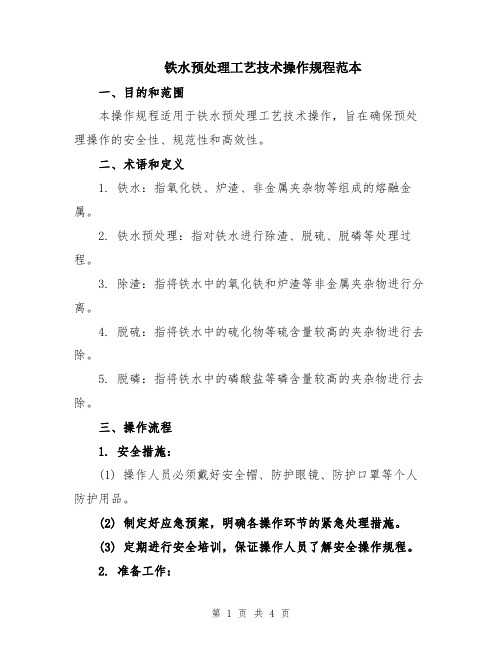
铁水预处理工艺技术操作规程范本一、目的和范围本操作规程适用于铁水预处理工艺技术操作,旨在确保预处理操作的安全性、规范性和高效性。
二、术语和定义1. 铁水:指氧化铁、炉渣、非金属夹杂物等组成的熔融金属。
2. 铁水预处理:指对铁水进行除渣、脱硫、脱磷等处理过程。
3. 除渣:指将铁水中的氧化铁和炉渣等非金属夹杂物进行分离。
4. 脱硫:指将铁水中的硫化物等硫含量较高的夹杂物进行去除。
5. 脱磷:指将铁水中的磷酸盐等磷含量较高的夹杂物进行去除。
三、操作流程1. 安全措施:(1) 操作人员必须戴好安全帽、防护眼镜、防护口罩等个人防护用品。
(2) 制定好应急预案,明确各操作环节的紧急处理措施。
(3) 定期进行安全培训,保证操作人员了解安全操作规程。
2. 准备工作:(1) 检查设备,确保设备正常工作。
(2) 铁水预处理所需材料和试剂应按规定配制并储存好。
(3) 根据预处理任务,准备好所需工具和器材。
3. 操作步骤:(1) 确保铁水温度符合处理要求,一般要求在1300℃以上。
(2) 打开铁水除渣设备的冷却水,确保冷却水通畅。
(3) 打开铁水预处理设备的进水阀门,将铁水缓慢地注入预处理设备中。
(4) 调整预处理设备的操作参数,如搅拌速度、气体流量等。
(5) 根据预处理任务需要,加入相应的脱硫剂、脱磷剂等试剂。
(6) 在预处理过程中,定期对设备进行检查和维护,保证设备正常工作。
(7) 根据预处理任务确定的处理时间,将预处理设备中的铁水分离出除渣、脱硫、脱磷后的铁水。
四、操作注意事项1. 操作人员必须熟悉设备的结构和工作原理,严格按照操作规程进行操作。
2. 操作过程中要注意设备的温度和压力变化情况,及时调整操作参数。
3. 在加入试剂时,要注意试剂的安全使用和防护措施,避免对人体和设备产生危害。
4. 注意设备的清洁和维护,定期进行设备的检查和保养,确保设备的正常运行。
五、操作记录每次进行铁水预处理操作时,必须详细记录以下内容:1. 操作人员、日期和班次。
铁水预处理安全操作规程
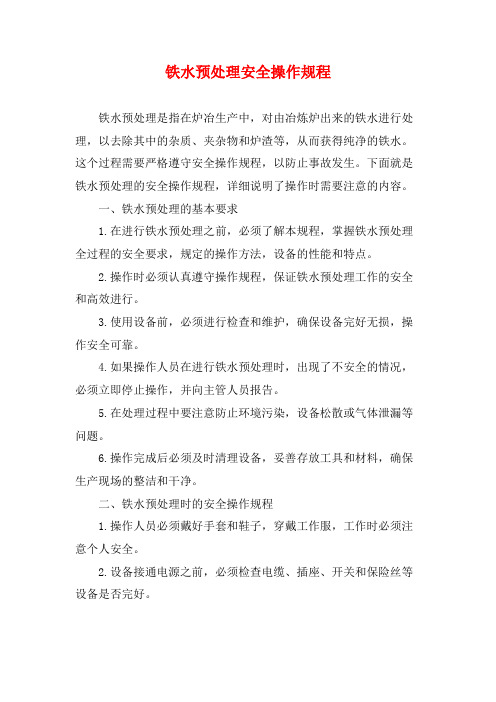
铁水预处理安全操作规程铁水预处理是指在炉冶生产中,对由冶炼炉出来的铁水进行处理,以去除其中的杂质、夹杂物和炉渣等,从而获得纯净的铁水。
这个过程需要严格遵守安全操作规程,以防止事故发生。
下面就是铁水预处理的安全操作规程,详细说明了操作时需要注意的内容。
一、铁水预处理的基本要求1.在进行铁水预处理之前,必须了解本规程,掌握铁水预处理全过程的安全要求,规定的操作方法,设备的性能和特点。
2.操作时必须认真遵守操作规程,保证铁水预处理工作的安全和高效进行。
3.使用设备前,必须进行检查和维护,确保设备完好无损,操作安全可靠。
4.如果操作人员在进行铁水预处理时,出现了不安全的情况,必须立即停止操作,并向主管人员报告。
5.在处理过程中要注意防止环境污染,设备松散或气体泄漏等问题。
6.操作完成后必须及时清理设备,妥善存放工具和材料,确保生产现场的整洁和干净。
二、铁水预处理时的安全操作规程1.操作人员必须戴好手套和鞋子,穿戴工作服,工作时必须注意个人安全。
2.设备接通电源之前,必须检查电缆、插座、开关和保险丝等设备是否完好。
3.进入操作场地之前,必须了解设备运行的方向和操作步骤,确保安全并确保自己的行动不会对他人造成危害。
4.处理铁水时,必须保证操作范围、进料口及排渣口的清洁以及周围环境的整洁。
5.在未打开铁水处理设备前,必须先检查铁水是否注满设备,避免空气进入设备。
6.处理过程中要注意排放的尾气是否超标,以及设备是否连续运行。
7.当发生故障或事故时,必须立即停机,按照相关程序进行处理,确保安全生产。
8.清理过程中,必须避免清理剂或泥浆流入生产设备或配电室中,避免污染环境和设备。
9.操作人员必须严格按照操作流程进行操作,以避免不必要的风险。
三、铁水预处理时注意的事项1.铁水预处理时,必须保证处理设备干燥,并保持设备及操作区域的清洁。
2.处理设备的操作功率必须符合规定的范围内,严禁自行修改设备的操作参数。
3.预处理过程中要注意铁水温度,保持温度控制在规定范围内,避免因温度过高而导致的事故。
铁水预处理技术操作规程√

铁水预处理技术操作规程1、原料要求1.1 铁水条件铁水温度:T≥1250℃铁水硫含量:[S]≤0.140%处理铁水量:与转炉铁水装入量相符1.2 脱硫剂采用CaO系脱硫剂1.3 脱硫剂加入量范围处理前铁水s含量目标S 脱硫剂加入量(Kg/t铁)≤40 ≤20 4~4.5 ≤10 6.5-7.041~50 ≤40 3.0-3.5 ≤20 4.0~5.0 ≤10 6.0~6.551~60 ≤40 3.5-4.0 ≤20 6.0~6.5 ≤10 6.0~8.561~70 ≤40 3.5-4.5 ≤20 6.0~8.0 ≤10 7.5~9.071~80 ≤40 4.5-7.5≤20 7.5~9.0 ≤10 9.0~10.581~90 ≤40 5.5-7.0≤20 9.0~10.5 ≤10 10.0~12.591~100 ≤40 6.5-8.0≤20 10.5~11.5 ≤10 12.0~13.5101~110 ≤40 8.0-9.5≤20 11.5~12.5 ≤10 12.5~14.5>110 ≤40 ≥9.5≤20 13.0~14.5 ≤10 14.5~16.5注:(1)视脱硫剂理化指标上升、下降,可将前[S]减少或提高0.020%。
(2)前[S]≤0.045%时,可将前[S]提高0.005~0.010%。
(3)根据搅拌头状况、铁水带渣量的多少,脱硫剂加入量可适当调整。
(4)特殊情况(如:设备故障、生产节奏紧、前硫未及时分析出来等)脱硫剂加入量可按照上限硫含量进行处理。
2、扒渣作业2.1 启动液压电机,将罐倾翻至扒渣角度(以铁水不能溢出为准)。
2.2 接通扒渣扒电源选择手动或自动操作方法,确认各信号是否正常及各分功能紧停开关位置。
2.3 确认压缩空气入口压力≥0.4Mpa,小车前进端极限在零位,后退端极限在十位上。
2.4 调整大臂高度,试扒后再调整适宜高度。
2.5 当罐内渣块≥600kg(目测)时,原则上不能强行扒渣,应将铁水返回混铁炉。
铁水预处理工艺技术操作规程

铁水预处理工艺技术操作规程铁水预处理是指在铁水离合器和连铸机结合的连续铸造系统中,对铁水进行处理和净化的工艺过程。
铁水预处理的目的是提高铁水的质量和连铸机的稳定性,同时减少钢坯的次级缺陷和浪费。
铁水预处理工艺技术的操作规程分为以下几个主要步骤:1. 接收铁水:接收到来自高炉的铁水后,首先要进行样品的采集和检测,以确认铁水的成分和温度是否符合要求。
然后,根据铁水的质量情况和连铸机的工艺要求,决定是否需要进行预处理。
2. 铁水过量处理:如果铁水的成分不合格或者超过了连铸机的要求,需要进行过量处理。
通常使用的方法有加入石灰、石油焦等添加剂来减少硫、磷等有害元素的含量。
3. 温度控制:连铸机对铁水的温度要求比较严格,因此需要对铁水进行冷却或加热处理,以使温度控制在合适的范围内。
一般使用的方法有喷淋冷却、电磁感应加热等。
4. 净化处理:铁水中含有固体杂质、气体和液体杂质,对质量和连铸过程稳定性均有不良影响。
因此,需要进行净化处理,常见的方法有脱硫、脱氧、脱气等。
5. 过滤处理:通过过滤处理可以进一步减少铁水中的固体杂质,避免它们对连铸机的阻塞和钢坯质量的影响。
过滤器的选择和使用需要根据铁水的成分和允许的杂质含量来确定。
6. 加样控制:加样是指向铁水中添加其它合金元素或化学剂的过程。
加样的目的是调整铁水的成分和温度,以满足连铸机的工艺要求。
加样的方法有固态加样和液态加样两种。
需要注意的是加样的量要准确、均匀,并且加样前要进行预热处理。
7. 铁水储存和运输:铁水预处理后,需要储存和运输到连铸机的喷包中。
为了保证铁水的质量不受污染和温度不受影响,储存和运输过程中需要采取相应的保护措施,如密封储存、隔热保温等。
8. 预处理设备的维护:铁水预处理设备是保证预处理工艺顺利进行的关键。
因此,需要定期对设备进行检查、维护和保养,保证设备的正常运转和使用寿命。
以上是铁水预处理工艺技术操作规程的主要内容。
在实际操作中,还需要根据具体的工艺要求和设备情况进行适当的调整和改进。
铁水预处理技术

不同脱硅方法对铁水温度的影响
1 2 3 氧化铁随氧气一起喷入TPC 氧化铁随氧气一起喷入 氧化铁随氧气一起由顶部加入 顶部加入氧化铁
10
Northeastern University
铁水预脱硅方法及其选择
铁水预脱硅主要有三种方法: 铁水预脱硅主要有三种方法: 1)在高炉出铁沟脱硅 2)鱼雷罐车或铁水罐中喷射脱硅剂脱硅 3)“两段式”脱硅,即为前两种方法的结合, 两段式”脱硅,即为前两种方法的结合, 先在铁水沟内加脱氧剂脱硅, 先在铁水沟内加脱氧剂脱硅,然后在鱼雷罐车中喷 吹脱硅
Northeastern University
第二讲
铁水炉外处理技术
战东平
1
Northeastern University
2.1 铁水预处理简介
铁水预处理:是指铁水兑入炼钢炉之前对其进行脱 铁水预处理: 除杂质元素或从铁水中回收有价值元素的一种铁水 处理工艺。 处理工艺。 铁水预处理: 铁水预处理: 普通铁水预处理 特殊铁水预处理 普通铁水预处理:铁水脱硫、脱硅和脱磷、 普通铁水预处理:铁水脱硫、脱硅和脱磷、铁水同 时脱硅、脱磷、脱硫( 三脱” 时脱硅、脱磷、脱硫(即“三脱”)。 特殊铁水预处理: 特殊铁水预处理:针对铁水中的特殊元素进行提纯 精炼或资源综合利用而进行的处理过程, 精炼或资源综合利用而进行的处理过程,如铁水提 提铌、提钨等。 钒、提铌、提钨等。
8
Northeastern University
[Si] + 2(FeO) = SiO2(s) + 2Fe ∆G1=-356020+130.47T J·mol-1 [Si] + Fe2O3(s) = SiO2(s) + Fe(l) ∆G2=-287800+60.38T J·mol-1 [Si] + Fe3O4(s) = SiO2(s) + Fe(l) ∆G3=-275860+156.49T J·mol-1
铁水预处理全解课件
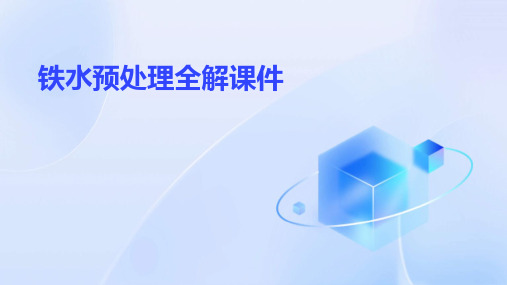
铁水预处理的流程
铁水预处理通常包括铁水脱硫、脱磷 、脱氧等步骤,这些步骤可以根据不 同的工艺要求进行组合。
铁水脱磷通常采用氧化法或偏心炉底 出钢法
铁水预处理对于现代钢铁生产具有重要意义,它不仅能够提高钢材的质量和性能 ,还能够降低生产成本、减少环境污染、提高企业的竞争力。因此,加强铁水预 处理技术的研究和应用,是钢铁企业可持续发展的重要保障。
02
铁水预处理技术
铁水脱硫技术
总结词
铁水脱硫技术是铁水预处理中的重要环节,可以有效降低铁水中的硫含量,提高钢材质量。
案例概述
钢铁企业C在铁水预处理方面注重 资源节约和环境保护,积极推广 低碳、绿色生产方式。
处理流程
钢铁企业C的铁水预处理流程主要 包括铁水脱硫、脱磷、脱硅等环节 ,以降低铁水中杂质含量。
技术特点
钢铁企业C的铁水预处理技术具有资 源节约、环保、高效等特点,为企 业的可持续发展奠定了基础。
05
铁水预处理未来发展
详细描述
铁水脱磷技术通常采用氧化脱磷法,通过向铁水中加入氧化剂,使铁水中的磷 氧化生成磷酸盐,从而达到脱磷的目的。常用的氧化剂包括空气、氧气、铁矿 粉等。
铁水脱硅技术
总结词
铁水脱硅技术是铁水预处理中的重要环节,可以有效降低铁 水中的硅含量,提高钢材的强度和韧性。
详细描述
铁水脱硅技术通常采用喷吹法或搅拌法,通过向铁水中喷吹 或加入脱硅剂,使脱硅剂与铁水中的硅反应,生成固态硅酸 盐,从而达到脱硅的目的。常用的脱硅剂包括CaO、 Ca(NO3)2等。
铁水脱硫通常采用喷吹法或搅拌法, 通过向铁水中喷吹或加入脱硫剂,使 铁水中的硫含量降低。
1-铁水预处理工艺

3.2 铁水脱磷装置示意图
四、转炉双联法脱磷工艺
日本和歌山制铁所炼钢厂工艺布置示意图
4.1 脱磷转炉
脱磷炉加15%废钢(尺寸稍小些) 脱碳炉加2%废钢(尺寸稍大些) 脱磷炉:废钢与脱碳炉渣一起从料槽加入。 BOFd[p]:[C]:4.7%~3.7% 吹氧时间9min [P]:从0.1%(1000ppm)→降到0.01% (100ppm)周期时间20min 炉龄: 25000炉,炉渣R:≤2,渣量 ~35kg/t,脱磷炉供氧强度是脱碳炉的1/4~1/2。 脱磷炉加入造渣料:BOFd[C]返渣(约占脱碳 炉渣总量的1/2)+石灰 脱磷炉渣:由于碱度≤2,可直接用于筑路 等 半钢温度1300℃左右, 回收煤气,流量为 35000~40000m3/h
五、铁水预处理对纯净钢的意义
铁水含磷、硫可降到低或超低含量水平。 提高转炉生产率、降低成本、节约能耗。 极低碳钢的清洁度。钢中T[O]、[N]、[H]含
量降低。 有利于复吹转炉冶炼高碳钢时的“保碳出钢 技术”。 有效地提高铁、钢、材系统的综合经济效益。
二、铁水脱Si(120t转炉)
铁水脱Si的重要意义: 铁水脱磷的必要条件 利于减少石灰加入量和渣量
铁水脱Si的工艺方法铁水罐脱硅 转炉脱硅
2.1 脱Si剂、脱Si原理
脱硅剂: 氧化剂:氧气,氧化铁皮,精矿粉,烧结矿粉,氧 化铁烟尘 溶剂:石灰,萤石 铁水脱Si化学反应: [Si]+O2(g)=SiO2 [Si]+(2/3)Fe2O3(s)=SiO2(s)+(4/3)Fe [Si]+(1/2)Fe3O4(s)=SiO2(s)+(3/2)Fe [Si]+2(FeO)=SiO2(s)+2Fe
转炉炼钢操作-铁水预处理

相关知识
四、常见脱硫剂及特点 1.苏打灰
其主要成分为Na2CO3,铁水中加入苏打灰后,与硫作用发生以下3个化学 反应:
用苏打灰脱硫,工艺和设备简单,其缺点是脱硫过程中产生的渣会腐蚀 处理罐的内衬,产生的烟尘污染环境,对人有害。目前很少使用。
相关知识
四、常见脱硫剂及特点 2.石灰粉
其主要成分为CaO,用石灰粉脱方法 2. KR搅拌法
KR法铁水预处理脱硫具体操作要求如下: (1)在处理之前,必须将铁水包内的渣子充分扒除,否则会严重影响 脱硫效果。 (2)处理过程中设置搅拌器的转数一般为90~120r/min,在搅动1~ 1.5min后开始加入脱硫剂,搅动时间约13min左右。 (3)处理完毕后,还需仔细地扒除脱硫渣。 ① KR搅拌法的优点:脱硫效率高、脱硫剂消耗少、金属损耗低。 ② KR搅拌法的缺点:温降大,处理10~15min过程温降约50 ℃,搅拌 过程为了铁水液面波动,液面至包口距离应不小于629mm。
石灰价格便宜、使用安全,但在石灰粉颗粒表面易形成2CaO·SiO2致密层, 限制了脱硫反应进行,因此,石灰耗用量大,致使生成的渣量大和铁损大, 铁水温降也较多。另外,石灰还有易吸潮变质的缺点。
相关知识
四、常见脱硫剂及特点 3.电石粉
用电石粉脱硫,铁水温度高时脱硫效率高,铁水温度低于1300℃时脱硫 效率很低。另外,处理后的渣量大,且渣中含有未反应尽的电石颗粒,遇水 易产生乙炔(C2H2)气体,故对脱硫渣的处理要求严格。在脱硫过程中也容 易析出石墨碳污染环境。电石粉易吸潮生成乙炔(乙炔是可燃气体且易发生 爆炸),故电石粉需要以惰性气体密封保存和运输。
相关知识
三、铁水预脱硫的方法 2. KR搅拌法
这种脱硫方法是以一种外衬耐火材料的搅拌器浸入铁水罐内,利用搅拌 器在铁水中旋转搅动铁水,使铁水产生漩涡,在铁液面中央部分产生一个漩 涡下流坑,同时加入脱硫剂使其在下陷坑中被卷入铁水内部进行脱硫反应 (如图所示),从而得到脱硫的目的。
铁水预处理
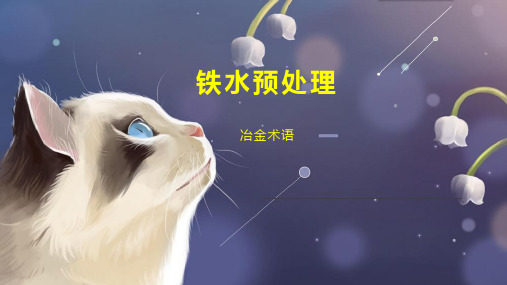
冶金术语
01 工艺简介
03 目的 05 剂
目录
02 分类 04 工艺方法
铁水预处理是指将铁水兑人炼钢炉之前脱除杂质元素或回收有价值元素的一种铁水处理工艺,包括铁水脱硅、 脱硫、脱磷(俗称“三脱”),以及铁水提钒、提铌、提钨等。
我国很多钢厂都采用了铁水预脱硫处理,甚至铁水三脱处理、提钒、提铌、提钨等,尤其是对于生产超低硫、 超低磷钢种的转炉炼钢车间。
工艺简介
铁水预处理是指铁水进入炼钢炉之前采取的冶炼工艺。铁水预处理工艺始于铁水炉外脱硫,1877年,伊顿() 等人用以处理不合格的生铁。铁水预脱硅、预脱磷始于1897年,英国人赛尔(Thiel)等人用一座平炉进行预处理 铁水,脱硅、脱磷后在另一座平炉中炼钢,比两座平炉同时炼钢效率成倍提高。到20世纪初,由于人们致力于炼 钢工艺的改进,所以铁水预处理技术发展曾一度迟缓。直至20世纪60年代,随着炼钢工艺的不断完善和材料工业 对钢材产品质量的要求开趋严格,铁水预处理得到了迅速的发展,并逐步成为钢铁冶金的必要环节。
分类
铁水预脱硅
研究表明,铁水中硅含量为0.3%即可保证化渣和足够高的出钢温度,硅过多反而会恶化技术经济指标。因此, 有必要开展铁水预脱硅处理。
脱硅剂以能够提供氧源的氧化剂材料为主,以调整炉渣碱度和改善流动性的熔剂为辅。如日本福山厂脱硅剂 组成为铁皮0~100%、石灰0~20%、萤石0~10%;日本川崎水岛的脱硅剂为烧结矿粉75%、石灰25%。脱硅生成的 渣必须扒除,否则影响下一步脱磷反应的进行。
(4)抗蚀、焊接和切削性能:钢中硫化物夹杂还会引起坑蚀现象。在钢的焊接过程中,钢中的硫化锰夹杂能 引起热撕裂。硫对钢还有一种很好的影响,即它能改善钢的切削性能。
工艺方法
铁水预处理技术01-02

¾ 历史背景: 60年代,氧枪转炉炼钢的崛起工业的发展给钢铁材料质量和焊接性能
好;抗腐蚀和高温性能好 用户需求:降低钢中杂质:硫、磷含量越低越好! 发展现状:30年代开始,60年代蓬勃发展!
第一章 铁水预处理概述
序,有的厂铁水实现了100%的预处理。平均约80%的铁 水经过脱硫;日本50%左右的铁水经过脱硅,40%以上的 铁水经过脱磷处理。
第一章 铁水预处理概述
• 2. 国外三脱技术的发展
¾ 六类十六种脱硫方法: 摇动法:瑞典的单向偏心摇动铁水罐法,日本神户尼崎铁
厂可逆旋转式DM摇包法。 机 械 搅 拌 法 : 原 西 德 DO(Damage Ostberg) 法 、
受研究者关注。
第一章 铁水预处理概述
• 4. 铁水预处理发展趋势 预脱硫→预脱硅→预脱磷(同时脱磷脱硫);
未来以喷吹法为主; 脱硫剂受原料经济和钢材产品要求而波动; 发展方向:高效、廉价、易得的复合脱硫剂;CaO系、
外预处理技术已在世界各国广泛应用。
第一章 铁水预处理概述
¾ 铁水预处理的必要性和迫切性:
是脱硫反应化学冶金学合理性的必要;
☺高炉: 动力学条件差,脱硫要付出代价;
☺
高炉脱硫:高炉温、焦比高、产量低。
☺转炉: 热力学条件不好,几乎无脱硫能力。
☺炉外: 可创造良好的热力学和动力学条件。
是钢材市场竞争力紧迫性的必要;
RS(Rheinstahl) 法 和 赫 歇 法 、 日 本 新 日 铁 KR(Kambara Reactor)法、千叶NP法。 吹气搅拌法: 新日铁PDS(底喷)法和CLDS(顶喷)法。 钟罩压入法:美国Janes Laughlin公司的镁焦法。 喷 吹 法 : 西 德 Thyssen 的 ATH(斜 插喷 枪 )法; 新日铁的 TDS(顶喷)法。 炉前铁水沟连续脱硫法。
铁水预处理工艺技术操作规程
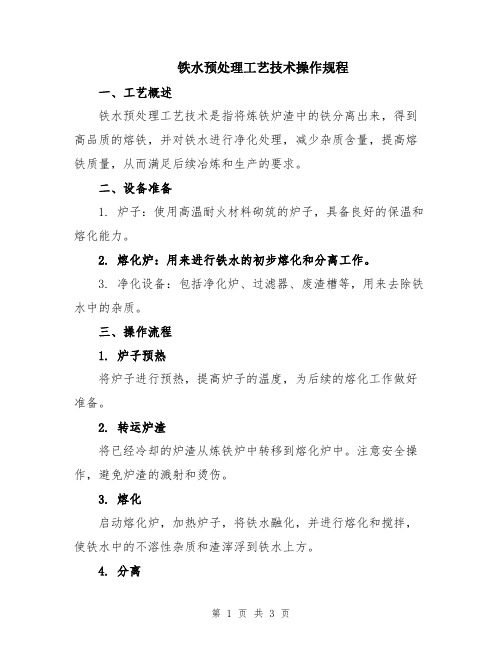
铁水预处理工艺技术操作规程一、工艺概述铁水预处理工艺技术是指将炼铁炉渣中的铁分离出来,得到高品质的熔铁,并对铁水进行净化处理,减少杂质含量,提高熔铁质量,从而满足后续冶炼和生产的要求。
二、设备准备1. 炉子:使用高温耐火材料砌筑的炉子,具备良好的保温和熔化能力。
2. 熔化炉:用来进行铁水的初步熔化和分离工作。
3. 净化设备:包括净化炉、过滤器、废渣槽等,用来去除铁水中的杂质。
三、操作流程1. 炉子预热将炉子进行预热,提高炉子的温度,为后续的熔化工作做好准备。
2. 转运炉渣将已经冷却的炉渣从炼铁炉中转移到熔化炉中。
注意安全操作,避免炉渣的溅射和烫伤。
3. 熔化启动熔化炉,加热炉子,将铁水融化,并进行熔化和搅拌,使铁水中的不溶性杂质和渣滓浮到铁水上方。
4. 分离利用铁水和炉渣的不同密度,通过熔化炉的倾斜或倒转,使炉渣从铁水中分离出来,进入废渣槽。
及时停止动作,避免废渣槽溢出和烫伤。
5. 净化将分离出来的铁水再次进行净化处理。
将铁水通过过滤器,去除其中的杂质,提高铁水的纯度。
6. 收集和贮存将净化处理后的铁水收集起来,并进行贮存和封存,以备后续冶炼和生产使用。
四、操作注意事项1. 安全操作人员必须佩戴符合规定的防护装备,确保自身的安全。
在操作过程中,严禁单人操作,必须有两人或以上协同作业。
同时,要遵守火源禁区规定,确保操作环境的安全。
2. 温度控制在炉子预热和熔化过程中,要严格控制温度,根据具体工艺要求进行调整,避免温度过高或过低对设备和产品品质的影响。
3. 火源控制在炉子预热和熔化过程中,要合理控制火源的大小和位置,确保炉子达到所需的温度和熔化效果。
4. 废渣处理废渣槽中的废渣要定期清理,以免影响铁水的分离和净化效果。
同时,废渣要根据相关规定进行分类处理,避免对环境造成污染。
5. 设备维护定期对设备进行检查和维护,确保设备的正常运行。
对于故障设备要及时停止使用,并进行维修或更换。
6. 监控和记录在操作过程中,要进行现场监控,记录相关数据和指标,以备后续的分析和改进工作。
铁水预处理工艺技术操作规程
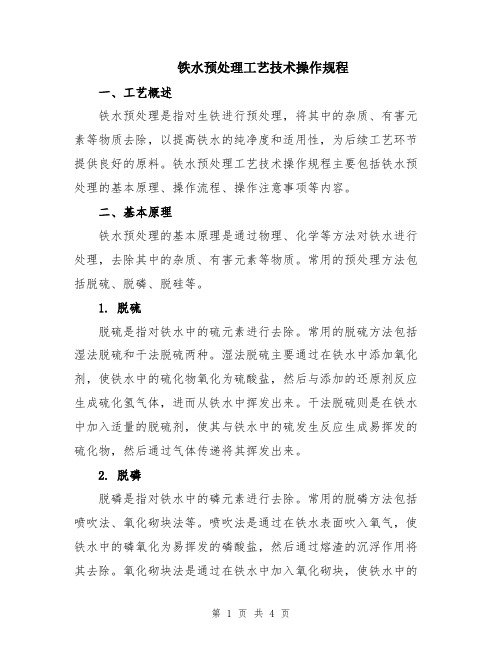
铁水预处理工艺技术操作规程一、工艺概述铁水预处理是指对生铁进行预处理,将其中的杂质、有害元素等物质去除,以提高铁水的纯净度和适用性,为后续工艺环节提供良好的原料。
铁水预处理工艺技术操作规程主要包括铁水预处理的基本原理、操作流程、操作注意事项等内容。
二、基本原理铁水预处理的基本原理是通过物理、化学等方法对铁水进行处理,去除其中的杂质、有害元素等物质。
常用的预处理方法包括脱硫、脱磷、脱硅等。
1. 脱硫脱硫是指对铁水中的硫元素进行去除。
常用的脱硫方法包括湿法脱硫和干法脱硫两种。
湿法脱硫主要通过在铁水中添加氧化剂,使铁水中的硫化物氧化为硫酸盐,然后与添加的还原剂反应生成硫化氢气体,进而从铁水中挥发出来。
干法脱硫则是在铁水中加入适量的脱硫剂,使其与铁水中的硫发生反应生成易挥发的硫化物,然后通过气体传递将其挥发出来。
2. 脱磷脱磷是指对铁水中的磷元素进行去除。
常用的脱磷方法包括喷吹法、氧化砌块法等。
喷吹法是通过在铁水表面吹入氧气,使铁水中的磷氧化为易挥发的磷酸盐,然后通过熔渣的沉浮作用将其去除。
氧化砌块法是通过在铁水中加入氧化砌块,使铁水中的磷与氧化砌块发生反应生成磷酸盐,然后通过熔渣的沉浮作用将其去除。
3. 脱硅脱硅是指对铁水中的硅元素进行去除。
常用的脱硅方法包括湿法脱硅和干法脱硅两种。
湿法脱硅主要是通过在铁水中加入足够量的碱性矿物,使硅与碱性矿物发生反应生成易挥发的硅酸盐,然后通过熔渣的沉浮作用将其去除。
干法脱硅则是在铁水中加入适量的脱硅剂,使其与铁水中的硅发生反应生成易挥发的硅化物,然后通过气体传递将其挥发出来。
三、操作流程铁水预处理的操作流程按照脱硫、脱磷、脱硅的顺序进行,具体步骤如下:1. 脱硫操作流程(1) 检查脱硫设备及周围环境的安全情况。
(2) 开始对铁水进行脱硫前,要先对铁水进行预热,使其温度达到预定的要求。
(3) 进行湿法脱硫时,在预热后的铁水中加入适当的氧化剂,并根据预定的脱硫时间进行搅拌。
炼钢第二讲铁水预处理
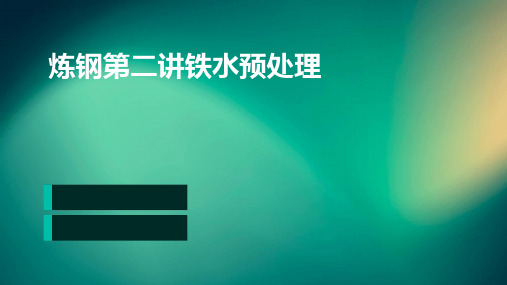
通过铁水预处理,可降低钢材中的夹杂物、气泡等缺陷,提高产品 合格率,减少废品率。
用户满意度
优质的钢材产品可满足用户更高的需求,提高用户满意度,增强企业 市场竞争力。
节能减排效果评估
能源消耗
铁水预处理可降低转炉冶炼的能耗,减少能源消 耗和生产成本。
环境保护
通过铁水预处理中的脱硫、脱磷等操作,可减少 废气、废渣的排放,降低环境污染。
搅拌装置
用于加强铁水与脱硫剂、脱磷剂等反应物 的混合,提高反应效率。
脱磷炉
通过向铁水中加入氧化剂或还原剂进行脱 磷反应,并配备有渣铁分离装置以去除生 成的磷酸盐或磷氧化物。
03 铁水预处理操作与优化
操作规程与注意事项
严格遵守安全操作规程
保持设备清洁
在进行铁水预处理时,必须佩戴防护 用品,确保人员安全。
无人化操作
无人化操作是钢铁行业实现智能化、自动化的重要方向之一。通过引入先进的自动化设备和控制系统,钢铁 企业可以实现铁水预处理的无人化操作,进一步提高生产效率和安全性。
06 总结与展望
本次课程重点内容回顾
铁水预处理的目的和意义
去除铁水中的有害元素,调整铁水成 分,提高钢铁质量。
铁水预处理的方法
脱硅、脱锰等其他元素去除
脱硅
硅在铁水中主要以硅酸盐形态存在,通过加入碱性氧化物 (如石灰)与硅酸盐反应生成硅酸钙等化合物,上浮至渣 层去除。
脱锰
锰在铁水中主要以锰的氧化物形态存在,通过还原反应将 锰的氧化物还原为金属锰,再利用其与硫的亲和力较强的 特性,将锰与硫结合生成硫化锰上浮去除。
其他元素去除
调整成分
根据后续炼钢工艺要求, 通过预处理调整铁水成分, 如增加废钢比、提高铁水 温度等。
铁水预处理工艺技术操作规程
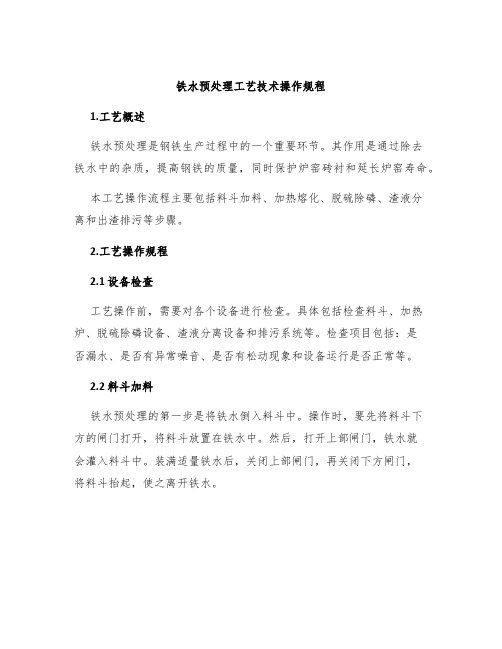
铁水预处理工艺技术操作规程1.工艺概述铁水预处理是钢铁生产过程中的一个重要环节。
其作用是通过除去铁水中的杂质,提高钢铁的质量,同时保护炉窑砖衬和延长炉窑寿命。
本工艺操作流程主要包括料斗加料、加热熔化、脱硫除磷、渣液分离和出渣排污等步骤。
2.工艺操作规程2.1 设备检查工艺操作前,需要对各个设备进行检查。
具体包括检查料斗、加热炉、脱硫除磷设备、渣液分离设备和排污系统等。
检查项目包括:是否漏水、是否有异常噪音、是否有松动现象和设备运行是否正常等。
2.2 料斗加料铁水预处理的第一步是将铁水倒入料斗中。
操作时,要先将料斗下方的闸门打开,将料斗放置在铁水中。
然后,打开上部闸门,铁水就会灌入料斗中。
装满适量铁水后,关闭上部闸门,再关闭下方闸门,将料斗抬起,使之离开铁水。
2.3 加热熔化装有铁水的料斗被送入加热炉中,加热至铁水完全熔化。
操作时,要按照设定的炉温和时间进行加热,在保证料斗不炸裂的前提下,确保铁水能够熔化。
2.4 脱硫除磷熔化后的铁水含有大量的硫和磷等杂质,需要进行脱除。
脱硫除磷设备是通过注入双氧水、氯化钙等化学试剂,将硫和磷等杂质转化为气体或沉淀,使其分离出铁水。
操作时,应按照设定的比例加入化学试剂,然后搅拌,进行反应,最后将杂质分离出来。
2.5 渣液分离经过脱硫除磷后的铁水含有较多的渣液,需要进行分离。
渣液分离设备通过旋转作用使铁水和渣分离,最终得到清洁的铁水,并将渣液排放到渣液仓中。
操作时,要按照设定的转速和时间进行分离。
分离后的渣液需要及时清理,以免影响下一次操作。
2.6 出渣排污渣液分离后,剩余的渣需要进行排出。
操作时,要先打开渣液仓下方的闸门,将渣排放到指定位置。
然后,关闭闸门,清理留在设备内的渣液和杂物。
排污作业应按照环保要求进行,不得将废渣氧化物和有害物质排到环境中。
3.注意事项1.操作人员应熟练掌握操作流程和设备使用知识,日常对设备进行检查和维护,确保设备运行正常;2.加热炉温度不要超过设定值,以免料斗炸裂;3.脱硫除磷过程中应严格按照试剂比例加入,并确保试剂质量合格;4.渣液分离设备应按照设定的转速和时间进行分离,不得过度或不足;5.排污作业应按照环保要求进行,废渣氧化物和有害物质不得排入环境中。
第4章铁水预处理介绍

5
4.2 铁水预处理脱硫
4.2.1 铁水预处理脱硫的意义
铁水炉外脱硫工艺之所以在经济上和技术上是合理可 行的,主要基于以下原因: 1)铁水中含有大量的硅、碳和锰等还原性好的元素,因 此在使用不同类型的脱硫剂,特别是强脱硫剂如钙、镁、 稀土等金属及其合金时,不会发生大量的烧损,以致影响 脱硫反应的进行; 2)铁水中碳和硅等能够大大提高硫在铁水中的活度系数, 使硫很容易就能脱到很低水平; 3)铁水中氧含量较低,硫的分配系数相应有所提高,有 利于脱硫;
6
4.2 铁水预处理脱硫
4)铁水炉外脱硫可以在鱼雷车、铁水罐中进行,也可以 在出铁槽中进行,这样可以减少处理投资; 5)铁水处理温度较低,对处理装臵的寿命有益; 6)在铁水炉外脱硫的过程中铁水成分的变化比炼钢或钢 水处理过程中钢水成分的变化对最终钢种的影响小。
脱硫费用($/kg)
项目 高炉脱硫 铁水预处理脱硫 转炉脱硫 最小值 25 6 43 最大值 30 13 311 条件 低硫焦(S:0.45%)增加焦比进行低S铁水操作 从0.04%脱至0.005%S,从0.02%脱至0.005% 0.047%S铁水和0.074%S废钢,0.005%S铁水和 0.015%S废钢
14
4.2 铁水预处理脱硫
莱茵法的搅拌器是采用铁芯加强的耐火材料制成的倒 T型 搅拌器,处理时转速为60~70转/分。 其特点是:莱茵搅拌器只是部分插入铁水内部,通过搅拌 使罐上部的铁水和熔剂形成涡流搅动,混合接触,并通过 循环流动使整个包内铁水都达到上层脱硫区来实现预处理 的目的。 采用 RS法脱硫时,用熔剂CaC2: 5~ 8 kg/t,处理时间: 10min,脱硫率:70~80%。
19
4.2 铁水预处理脱硫
铁水预处理(脱硫)
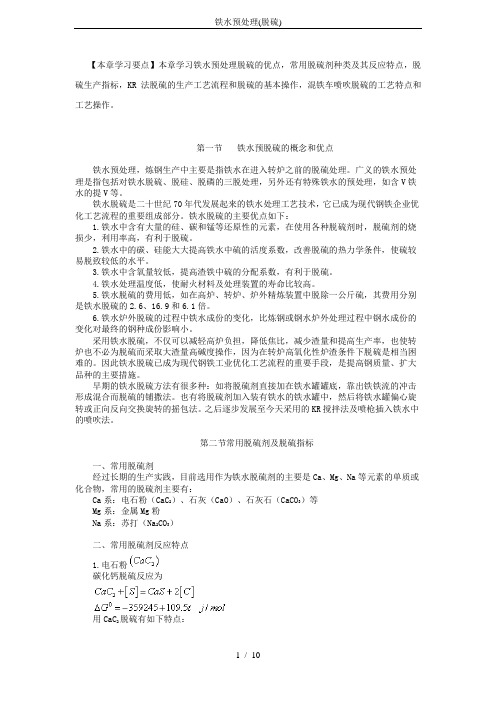
【本章学习要点】本章学习铁水预处理脱硫的优点,常用脱硫剂种类及其反应特点,脱硫生产指标,KR法脱硫的生产工艺流程和脱硫的基本操作,混铁车喷吹脱硫的工艺特点和工艺操作。
第一节铁水预脱硫的概念和优点铁水预处理,炼钢生产中主要是指铁水在进入转炉之前的脱硫处理。
广义的铁水预处理是指包括对铁水脱硫、脱硅、脱磷的三脱处理,另外还有特殊铁水的预处理,如含V铁水的提V等。
铁水脱硫是二十世纪70年代发展起来的铁水处理工艺技术,它已成为现代钢铁企业优化工艺流程的重要组成部分。
铁水脱硫的主要优点如下:1.铁水中含有大量的硅、碳和锰等还原性的元素,在使用各种脱硫剂时,脱硫剂的烧损少,利用率高,有利于脱硫。
2.铁水中的碳、硅能大大提高铁水中硫的活度系数,改善脱硫的热力学条件,使硫较易脱致较低的水平。
3.铁水中含氧量较低,提高渣铁中硫的分配系数,有利于脱硫。
4.铁水处理温度低,使耐火材料及处理装置的寿命比较高。
5.铁水脱硫的费用低,如在高炉、转炉、炉外精炼装置中脱除一公斤硫,其费用分别是铁水脱硫的2.6、16.9和6.1倍。
6.铁水炉外脱硫的过程中铁水成份的变化,比炼钢或钢水炉外处理过程中钢水成份的变化对最终的钢种成份影响小。
采用铁水脱硫,不仅可以减轻高炉负担,降低焦比,减少渣量和提高生产率,也使转炉也不必为脱硫而采取大渣量高碱度操作,因为在转炉高氧化性炉渣条件下脱硫是相当困难的。
因此铁水脱硫已成为现代钢铁工业优化工艺流程的重要手段,是提高钢质量、扩大品种的主要措施。
早期的铁水脱硫方法有很多种:如将脱硫剂直接加在铁水罐罐底,靠出铁铁流的冲击形成混合而脱硫的铺撒法。
也有将脱硫剂加入装有铁水的铁水罐中,然后将铁水罐偏心旋转或正向反向交换旋转的摇包法。
之后逐步发展至今天采用的KR搅拌法及喷枪插入铁水中的喷吹法。
第二节常用脱硫剂及脱硫指标一、常用脱硫剂经过长期的生产实践,目前选用作为铁水脱硫剂的主要是Ca、Mg、Na等元素的单质或化合物,常用的脱硫剂主要有:Ca系:电石粉(CaC2)、石灰(CaO)、石灰石(CaCO3)等Mg系:金属Mg粉Na系:苏打(Na2CO3)二、常用脱硫剂反应特点1.电石粉碳化钙脱硫反应为用CaC2脱硫有如下特点:1)在高碳系铁水中,CaC2分解出的Ca离子与铁水中的硫有极强的亲和力。
- 1、下载文档前请自行甄别文档内容的完整性,平台不提供额外的编辑、内容补充、找答案等附加服务。
- 2、"仅部分预览"的文档,不可在线预览部分如存在完整性等问题,可反馈申请退款(可完整预览的文档不适用该条件!)。
- 3、如文档侵犯您的权益,请联系客服反馈,我们会尽快为您处理(人工客服工作时间:9:00-18:30)。
第四章铁水预处理武汉科技大学冶金工程系张保平4 .1 铁水预处理的基本概念4.1 铁水预处理的基本概念•铁水预处理是指铁水进入炼钢炉之前,为脱硫、脱硅、脱磷而进行的处理过程。
•除上述普通铁水预处理外,还有特殊铁水预处理,如脱铬、脱锰以及针对铁水含有特殊元素提纯精炼或资源综合利用而进行的提钒、提铌、提钨、提铬等预处理过程。
•实际生产过程中,铁水预处理分为深脱和浅脱。
4.2 铁水预处理的冶金原理4.2.1 铁水预脱硫的冶金原理4.2.1.1 铁水脱硫剂的种类•铁水脱硫剂的种类很多,在实际生产中,用作铁水脱硫剂的主要是Ca、Mg、Na 等元素的单质或化合物。
•常用的脱硫剂主要有:☐Ca系脱硫剂,包括电石粉 (CaC2)、石灰 (CaO)、石灰石 (CaCO3)等;☐Mg系脱硫剂,包括金属Mg粉、镁焦、镁合金等;☐Na系脱硫剂,主要是苏打粉(Na2CO3)。
•CaC2脱硫的反应式如下:CaC2(s) +[S] =CaS(s) +2[C]•石灰脱硫反应式:☐铁水硅含量高(>0.05%)时,反应式为:2CaO(s)+[S]+l/2[Si] = CaS (s)+1/2(Ca2SiO4)(s) ☐硅含量低时,反应式为:CaO(s)+[S]+[C] = (CaS)(s)+CO(g)•铁水中加入苏打灰后,与铁水中的硫发生以下3个化学反应:Na2CO3(l) +[S] + 2[C] = Na2S(l) + 3{CO}Na2CO3(l) +[S] + [Si] = Na2S(l) + SiO2(s) + 3{CO}Na2O + [S] = Na2S(l) + [O]•镁通过喷枪喷入铁水后,在高温下发生液化、气化并溶于铁水:Mg(S) →Mg(l) →{Mg} →[Mg]•在高温下,镁和硫有很强的亲和力,溶入铁水中的[Mg]和{Mg}都能与铁水中的[S]迅速反应生成固态的MgS,上浮进入渣中。
镁与硫的相互反应存在两种情况:•第一种情况:{Mg} + [S] = MgS(s)•第二种情况:{{Mg} →[Mg][Mg] + [S] =MgS(S)4.2.2 铁水脱磷的冶金原理4.2.2 铁水脱磷的冶金原理4.2.2.1 铁水脱磷的基本冶金条件•铁水在氧化性渣下的脱磷反应式表示如下:2[P]+5(FeO) +4(CaO) =(4CaO·P2O5) + 5Fe4.2.2.1 铁水脱磷的基本冶金条件•由此可得出脱磷反应的热力学基本条件:•(1)铁水中氧含量要高。
铁水脱磷需要提供氧,实际生产中经常采用加入铁氧化物或辅助吹氧的方式来提供氧。
铁氧化物是脱磷剂的主要组成,主要有铁矿、烧结矿、氧化铁皮,转炉烟尘以及转炉炉渣,一般(FeO)≮20%。
•(2)渣中起固定脱磷产物的碱性氧化物含量要高。
(碱度R=2~3),脱磷的初级产物(3FeO·P2O5)不稳定,通过加入碱性氧化物,让磷在高碱度炉渣中形成稳定的4CaO·P2O5或3Na2O·P2O5。
4.2.2.1 铁水脱磷的基本冶金条件•(3)铁水温度要低。
铁水氧化脱磷反应为放热反应,铁水温度低,Kp、Lp值就大,因此温度低有利于铁水脱磷。
温度为1250℃~1400℃对脱磷有利。
•(4)铁水初始硅含量要低。
在高炉铁水条件下,铁水中还含有0.4%~0.6%左右的[Si],[Si]与氧的亲和力远大于[P]。
硅酸钠与硅酸钙的稳定性比磷酸钠和磷酸钙好,因此必须对铁水预脱硅,才能用石灰或苏打渣系进行有效脱磷。
因此,为保证有效的脱磷必须先将[Si]降低到<0.1%~0.15%。
4.2.2.2 脱磷剂的组成4.2.2.2 脱磷剂的组成•氧化剂、固定剂和助熔剂是铁水脱磷的三大要素。
•实践证明Fe2(SO4)3、MnO2、CaSO4、Fe2O3、FeO、MnO等都是很好的脱磷氧化剂,CaCO3次之。
•固定剂:CaO等。
•助熔剂:CaCl2、CaF2等。
4.2.2.3 不同脱磷剂的脱磷反应4.2.2.3 不同脱磷剂的脱磷反应(1)石灰系脱磷剂•石灰系脱磷剂常用的组成范围为(%),固定剂:氧化剂:助熔剂=30~70:20~45:0~40。
(2)苏打系脱磷剂•固体Na2CO3在852℃熔化为液体,在铁水处理温度下是流动性很好的液体,可按下式分解为:Na2CO3(L) = Na2O(L) + CO2故脱磷反应为:4.2.3 脱硅反应的冶金原理4.2.3 脱硅反应的冶金原理•脱硅剂是以提供氧源的材料为主剂,氧化剂有固体氧化剂和气体氧化剂。
•固体氧化剂主要有:铁矿石、球团矿、烧结矿、轧钢铁皮、铁矿砂、锰矿粉等,其主要成分是氧化铁、氧化锰。
气体氧化剂主要是氧气。
•除主剂外还加入少量副剂。
常用的副剂主要是石灰、萤石、CaCl2、NaCl、CaO 十CaF2、CaO十CaF2十Na2CO3以及转炉钢渣等。
一般将炉渣碱度((CaO十CaF2)/SiO2)调整为0.9~1.2。
4.3 铁水预处理的方法及设备4.3 铁水预处理的方法及设备•随着铁水预处理技术的发展,铁水预处理方法很多。
•用于铁水预脱硫的方法有:铺撒法、摇包法、机械搅拌法、喷粉法、喂线法、气泡搅拌法、气泡泵法、钟罩加入法等。
•用于铁水预脱磷的方法,按照处理设备可分为炉外法、炉内法;按照加料方式可分为喷吹法、搅拌法;按照工艺特点可分为:专用炉法、SARP法、ORP法、NPP法。
4.3 铁水预处理的方法及设备•用于铁水预脱硅的方法,按处理场所不同,可分为在高炉出铁过程中向炉前铁水沟加固体氧化剂连续脱硅法,向铁水罐或混铁车内喷射脱硅剂脱硅和吹氧法脱硅。
•按加入脱硅剂方法不同,有自然投入法、喷枪在铁水面上的液面喷吹法和喷枪插入铁水内的喷吹法等。
•按搅拌方法不同,有吹气搅拌、铁水落下流搅拌、喷吹的气粉流搅拌和叶轮搅拌方法等。
4.3.1 铺撒法(投入法)4.3.1 铺撒法(投入法)•铺撒法是一种简易的铁水预处理法,处理过程中只需将处理剂铺撒在铁水沟适当位置,预处理剂随铁流而下,或将处理剂撒在铁水罐底部,靠铁流的冲击使预处理剂和铁水发生反应而脱除有关杂质元素或提取有用元素。
•该工艺对生产条件有较强的适应性,无明显工艺缺陷。
进行脱硫预处理时,铁水温降7~8℃。
且脱硫渣没有回硫倾向。
无铁损及喷枪烧损。
•缺点也不少。
4.3.2 摇动法4.3.2 摇动法•摇动法,也称为铁水容器搅拌处理法。
可以分为:☐回转炉法。
即在回转炉的铁水面上加入熔剂,并进行搅拌;☐摇包法。
在偏心回转包的铁水中加入熔剂。
包的转速为40~50转/分;DM摇包法,摇包能正逆向进行,铁水和熔剂混合良好,转速为43转/分,正逆换向周期14秒,中间停止三秒。
•该法容器转动笨重,动力消耗高,包衬寿命低,使用较少。
4.3.3 机械搅拌法4.3.3 机械搅拌法•机械搅拌法是铁水预处理技术的重要进展, 它放弃了转动的容器运动方式, 通过机械搅动来使液体金属与熔剂混合接触达到脱硫、脱硅、脱磷的目的。
•机械搅拌法可以分为以下几种:DO法、莱茵法(RS法)、KR搅拌法、赫歇法、NP法。
几种方法中,KR法应用比较广泛。
4.3.3.1 莱茵法4.3.3.1 莱茵法•这种方法也称为RS法(Rhein Stahl),是德国莱茵河钢铁厂的克雷默(F.Kraemer)等人于1969年研制成功的,后来在曼内斯曼(Mannesmann)公司引进了200t的RS装置。
欧洲各国也采用此法,是一种用于铁水预脱硫的方法。
4.3.3.1 莱茵法•莱茵法的搅拌器是采用铁芯加强的耐火材料制成的倒T型搅拌器,处理时转速为60~70转/分。
•其特点是:莱茵搅拌器只是部分插入铁水内部,通过搅拌使罐上部的铁水和熔剂形成涡流搅动,混合接触,并通过循环流动使整个包内铁水都达到上层脱硫区来实现预处理的目的。
•采用RS法脱硫时,用熔剂CaC2 5~8 kg/t,处理时间10min,脱硫率70~80%。
4.3.3.2 KR搅拌法4.3.3.2 KR搅拌法•KR法(Kambara Reactor)是日本新日铁钢铁厂于1963年开始研制,1965年投入工业生产。
以后被日本钢管和住友金属公司等厂家采用,铁水罐容量可达200t以上,该法主要用于脱硫。
•我国最早的KR系统是武钢二炼钢1979年由新日铁引进的KR专利和设备。
•KR法的主体设备包括:升降装置、机械搅拌装置、搅拌桨更换车、熔剂输送装置、扒渣系统等。
4.3.3.2 KR搅拌法4.3.3.2 KR搅拌法•KR搅拌法就是将耐火材料制成的并经过烘烤的十字形搅拌头插入铁水罐液面下一定深处, 并使之旋转。
•当搅拌器旋转时, 铁水液面形成“V” 形旋涡( 中心低, 四周高), 此时加入脱硫剂、脱磷剂后, 熔剂微粒在浆叶端部区域内由于湍动而分散, 并沿着半径方向“吐出”, 然后悬浮, 绕轴心旋转和上浮于铁水中, 也就是说, 借这种机械搅拌作用使熔剂卷入铁水中并与接触, 混合、搅动, 从而进行脱硫脱磷反应。
•当搅拌器开动时, 在液面上看不到熔剂, 停止搅拌后, 所生成的干稠状渣浮到铁水面上, 扒渣后即达到脱硫、脱磷的目的。
4.3.3.2 KR搅拌法•对于KR搅拌法,由于熔剂在叶片上端打散,使这个部容易受到磨损,所以选择四个叶片的搅拌头最为合适。
搅拌头使用4个叶片,可以使其旋转时铁水面不易产生波浪, 铁水飞溅较少, 叶片的磨损情况也小, 可以减少搅拌的更换次数, 提高使用寿命, 降低耐火材料消耗等,处理效果明显好于两个叶片。
•十字型搅拌头的形状如图所示,搅动头为高铝质耐火材料,寿命为90~100次,每使用3~4次后需要用耐火材料进行修补。
4.3.3.2 KR搅拌法4.3.3.2 KR搅拌法•与莱茵法相比,两种方法的最大区别是:搅拌器插入铁水深度不同,KR 法是将搅拌器沉浸到铁水内部, 而不是在铁水和熔剂之间的界面上。
通过搅拌形成铁水运动旋涡使熔剂撒开并混入铁水内部, 加速预处理过程,其铁水流动情况如图所示。
4.3.4 吹气搅拌法•吹气搅拌法主要有顶吹法、底吹法(PDS或CLDS)和气泡泵法三种。
顶吹法和底吹法预先将熔剂加到铁水表面,然后通过顶枪或罐底的透气砖往铁水中喷吹气体进行搅拌。
这两种方法设备费用低,操作简便,但处理效果不如机械搅拌法好。
•CLDS法是改进了的PDS法,一般能连续处理4罐铁水,这样可以提高处理效率,省去了除渣何减少铁损失,但是需要倒包处理。
4.3.4 吹气搅拌法•气泡泵法也称气泡泵环流搅拌法,简称GMR法。
它是应用气泡泵的扬水原理研制成功的,如图所示。
•在新型装置上气泡泵本身旋转,可以进一步提高处理效率,缩短处理时间。
4.3.5 喷射法•喷射法也称喷粉法或喷吹法,主要有ATH法、TDS法、铁水罐喷射法。
•ATH法是1970年原西德蒂森公司研究成功并投入应用的一种方法,它将一支外衬耐火材料的喷枪与水平方向成一定角度(如600或700)斜插入鱼雷罐内,用载气向熔池内喷射固体粉末熔剂进行脱硫、脱磷处理。