L-LUCL8560FAU-D中文资料
AD8568中文资料
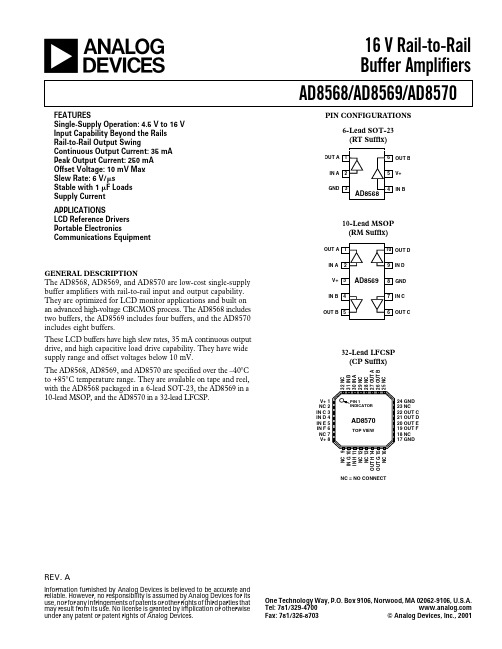
26
nV/√Hz
25
nV/√Hz
0.8
pA/√Hz
–2–
REV. A
元器件交易网
AD8568/AD8569/AD8570
ABSOLUTE MAXIMUM RATINGS* Supply Voltage (VS) . . . . . . . . . . . . . . . . . . . . . . . . . . . . . 18 V Input Voltage . . . . . . . . . . . . . . . . . . . . . . –0.5 V to VS +0.5 V Differential Input Voltage . . . . . . . . . . . . . . . . . . . . . . . . . . VS Storage Temperature Range . . . . . . . . . . . . –65°C to +150°C Operating Temperature Range . . . . . . . . . . . –40°C to +85°C Junction Temperature Range . . . . . . . . . . . . –65°C to +150°C Lead Temperature Range (Soldering, 60 sec) . . . . . . . . 300°C
Min Typ
Max
Unit
INPUT CHARACTERISTICS Offset Voltage Offset Voltage Drift Input Bias Current
Input Voltage Range Input Impedance Input Capacitance OUTPUT CHARACTERISTICS Output Voltage High
slp85xd称重传感器安装手册说明书
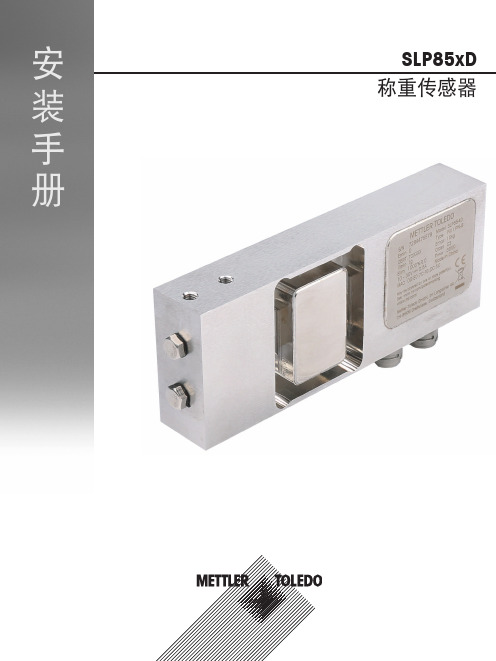
4 技术参数
20
4.1 通用数据 ................................................................................................................... 20
4.2 类型标号代码............................................................................................................ 22
4.3 尺寸 .......................................................................................................................... 22
4.4 接口规格 ................................................................................................................... 23
1.2.6 LED 状态灯 ................................................................................................. 9
1.2.7 通信电缆端头 ............................................................................................. 12
3 操作
19
BL8560-VPRD中文资料

7) Load transient response
-8Total 10 Pages
8/8/2006
元器件交易网
BL8560
Package Information:
3) Dropout Voltage vs. Output Current
4) Supply Current vs. Input Voltage
-7Total 10 Pages
8/8/2006
元器件交易网
BL8560
5) Ripple rejection vs. Frequency 6) Line transient response
-4Total 10 Pages
8/8/2006
元器件交易网
BL8560
Electrical Characteristics
BL8560, for arbitrary output voltage
Symbol
Parameter
Conditions
Min
Typ
Max
Units
-1Total 10 Pages
8/8/2006
元器件交易网
BL8560
Selection Guide BL8560 X X XX Pin Assignment
Pin Description
Pin Number
SOT-23-6C SOT-23-6D
SOT-23-6D
BL8560-WPRD
8/8/2006
元器件交易网
BL8560
Product Marking information:
SOT-23-6C SOT-23-6D
TDA8560中文资料
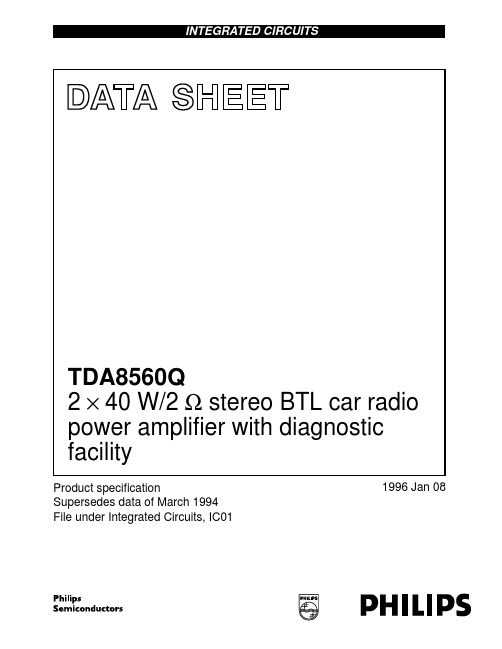
1996 Jan 08
2
元器件交易网
Philips Semiconductors Product specification
2 × 40 W/2 Ω stereo BTL car radio power amplifier with diagnostic facility
BLOCK DIAGRAM
V P1 3 input 1 1 mute switch Cm VP2 10
TDA8560Q
TDA8560Q
VA 365 Ω 18 kΩ power stage mute switch 4 output 1A
Cm
PROTECTIONS Load dump Soar Thermal Short - circuit Reverse polarity
Байду номын сангаас
元器件交易网
Philips Semiconductors Product specification
2 × 40 W/2 Ω stereo BTL car radio power amplifier with diagnostic facility
SHORT-CIRCUIT PROTECTION When a short-circuit occurs at one or more outputs to ground or to the supply voltage, the output stages are switched off until the short-circuit is removed and the device is switched on again, with a delay of approximately 20 ms, after removal of the short-circuit. During this short-circuit condition, pin 12 is continuously low. When a short-circuit across the load of one or both channels occurs the output stages are switched off during approximately 20 ms. After that time it is checked during approximately 50 µs to see whether the short-circuit is still present. Due to this duty cycle of 50 µs/20 ms the average current consumption during this short-circuit condition is very low (approximately 40 mA).
浪潮-服务器NF8560
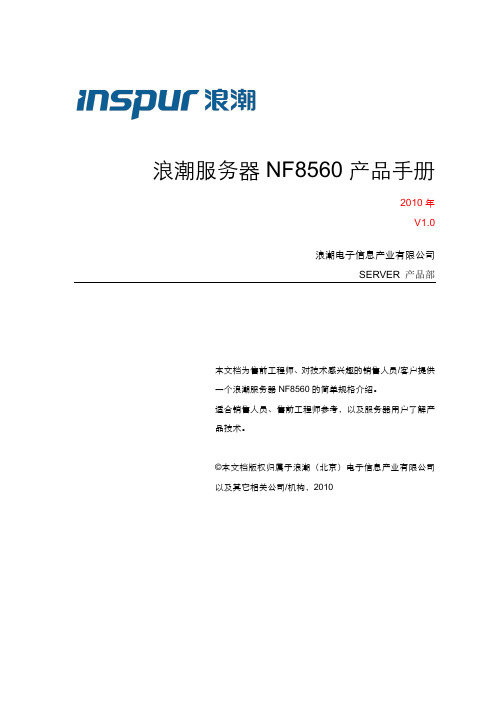
浪潮服务器NF8560产品手册2010年V1.0浪潮电子信息产业有限公司SERVER 产品部本文档为售前工程师、对技术感兴趣的销售人员/客户提供一个浪潮服务器NF8560的简单规格介绍。
适合销售人员、售前工程师参考,以及服务器用户了解产品技术。
©本文档版权归属于浪潮(北京)电子信息产业有限公司以及其它相关公司/机构,2010更新历史浪潮英信服务器NF8560产品手册产品定位在服务器系列中多路服务器以其高性能、高功能、高安全、高可靠的特征,适用于所有用户的应用环境,如关系型数据库、强调单机计算能力的科学计算、企业ERP及电子商务服务等应用方向,在该几大类应用中,主要的衡量标准为应用系统需求处理速度的大小,系统应用的重要程度等方面;对于政府、教育、大中型企业、特殊的行业等关键应用领域,虽在某些方面对计算需求要求较低,但对于系统及数据的安全性以及扩展能力要求较高,这类领域中主要的衡量标准为高可靠性与高功能,所以在四路产品的定位中更侧重应用方向和应用领域。
浪潮英信NF8560服务器为业界最先进的,具备优异计算性能、卓越可靠性及易用性的四插槽设计多路服务器系统,基于intel QPI技术NEHALEM-EX微架构多路多核处理器设计,强调灵活扩展、适用功能、高性能、高安全,定位于核心业务;在完善对传统应用的良好支持前提下,优化更高的内存、灵活I/O扩展,使之成为更加适用于基础架构优化的虚拟化整合、IT应用模式变革的云计算等前沿技术的最佳硬件平台。
产品特性:更高的计算能力:采用最新基于QPI高速互联技术,最高达8计算核心16计算线程24MB高速缓存的INTEL NEHALEM-EX XEON多路多核处理器,四插槽直连设计,提供高达32计算核心64处理线程,搭配TURBO智能加速技术,与前代基于FSB前端总线技术设计的服务器,系统联机事务综合处理性能提升2.5倍以上,高性能浮点计算能力提升3.8倍以上。
2008年Ford自动变速箱组件目录说明书

1622008 AUTOMATIC TRANSMISSION KIT & COMPONENTS CATALOG ©2008 PARKER HANNIFIN CORP. ALL RIGHTS RESERVED3790103008397797405R55N / 5R55S / 5R55WRWD 5 SpeedA544510034070670Input ShaftO.Dr. Ring GearO.Dr. CenterShaft783Center SupportInterm. BandDirect DrumForward ClutchForward PlanetReverse BandReverse DrumLow Sprag310037179520036178530311914363912911913910896904896437490996V.B.Parts741E414494765-6370Case313321320Valve Body917747765746322420002OHK Kit004Master L/Steels Kit 006Master 030External Seal Kit1632008 AUTOMATIC TRANSMISSION KIT & COMPONENTS CATALOG ©2008 PARKER HANNIFIN CORP . ALL RIGHTS RESERVEDRWD 5 Speed5R55N / 5R55S / 5R55W862981971961560961971985879565126106146861*229964974877564285872962972104124552894Intermediate Sprag690074266Park Gear264847Park Pawl Assy995-1995-2995-3995916-2916-3919922915916-2916-3919922916263EDA181554770Ext. Hsg.781493305678Output ShaftO.Dr. Band StrutInterm. Band Strut268841Internal Linkage991-2991-3994799991-4761P-4991072410992Yoke1642008 AUTOMATIC TRANSMISSION KIT & COMPONENTS CATALOG©2008 PARKER HANNIFIN CORP. ALL RIGHTS RESERVED*Prefix Letter ‘T’ denotes Toledo-Trans Kit (TTK) Brand Transmission Kits *Prefix Letter ‘B’ denotes Bryco Brand Transmission Kits002.............T16002AP......Overhaul Kit, 5R55N (With Bonded Pistons) 1999-Up ..............................................................1..........002.............T16002GP......Overhaul Kit, 5R55S/5R55W (With Bonded Pistons) 2002-Up..................................................1..........004.............T16004AP......Master L/Steels Kit, 5R55N (With Bonded Pistons) 1999-Up ....................................................1..........004.............T16004GP......Master L/Steels Kit, 5R55S/5R55W (With Bonded Pistons) 2002-Up .......................................1..........006.............T16006AP......Master W/Steels Kit, 5R55N (With Bonded Pistons) 1999-Up...................................................1..........006.............T16006GP......Master W/Steels Kit, 5R55S/5R55W (With Bonded Pistons) 2002-Up ......................................1..........E300...........45019............Gasket, 5R55N Bottom Pan (Plastic With Silicon Bead) OE Style (With Large Holes) 1999-Up 1..........XW4Z-7A191CA D305...........45097668......Gasket, 5R55N/5R55S/5R55W Extension Housing To Case 1999-Up......................................1..........XW4Z-7086-AA A309..........41217............Gasket, 5R55N/5R55S/5R55W Pump Bolt Washer...................................................................AR ........A310..........45097667......Gasket, 5R55N/5R55S/5R55W Pump 1999-Up..........................................................................1..........XW4Z-7A136AB A311...........1988096........O-Ring, 5R55N/5R55S/5R55W Pump Cover 1999-Up ...............................................................1..........XW4Z-7A248AA A313..........1994747........O-Ring, 5R55N Inner Pump Gear 1999-Up.................................................................................1..........F77Z-7L323AA E320...........45097692......Gasket, 5R55N Valve Body Separator Plate To Case 1999-Up ................................................1..........XW4Z-7D100-BF E320...........45097738......Gasket, 5R55S/5R55W Valve Body Separator Plate To Case (Upper) 2002-Up......................1..........1L2Z-7Z490AB-1A070..........70243V..........Seal, 5R55N/5R55S/5R55W Front (No Flange) (Rubber Coated) 1999-Up ..............................1..........F77Z-7A248AA D072...........70083............Seal, 5R55N Linkage 1999-Up ..................................................................................................1..........D5AZ-7B498A D074...........70283............Seal, 5R55N Rear 2WD 2000-Up ...............................................................................................1..........XW4Z-7052AA D074...........70205............Seal, 5R55S/5R55W Rear (W/Long Boot) 2WD 2002-Up .........................................................1..........F6UZ-7052A D074...........70282............Seal, 5R55S/5R55W Extension Housing 4X4 2002-Up .............................................................1..........1L2Z-7052BA175.............6358..............Ring Kit, 5R55N/5R55S/5R55W (2 Metal 4PTFE 2 Torlon Rings) 1999-Up ...............................1..........A178..........45060279......Ring, 5R55N, 5R55W, 5R55S Pump Support (Lock-Up) 1999-Up .............................................1..........B181...........TAW- 2212....Ring, 5R55N, 5R55W, 5R55S Forward Clutch Cylinder 1999-Up .............................................2..........D184...........45060265......Ring, 5R55N, 5R55W, 5R55S Output Shaft 1999-Up.................................................................1..........A179..........30308............Ring, 5R55N, 5R55W, 5R55S Overdrive Brake Drum 1999-Up.................................................2..........B179...........30308P ..........Ring, 5R55N, 5R55W, 5R55S Direct Clutch (Center Support) 1999-Up Torlon .........................2..........119.............45082NR........Friction Module, 5R55N 1999-Up................................................................................................1..........119.............45082LR........Friction Module, 5R55S/5R55W 2002-Up...................................................................................1..........E010...........45040N ..........Filter, 5R55N (3/8” Tall Pick-up Tube) 1999-Up ..........................................................................1..........XW4Z-7A098BB E010...........F-340.............Filter, 5R55S/5R55W (2 1/4” Tall Pick-Up Tube) 2002-Up..........................................................1..........1L2Z-7A098AC5R55N / 5R55S / 5R55WRWD 5 Speed1652008 AUTOMATIC TRANSMISSION KIT & COMPONENTS CATALOG ©2008 PARKER HANNIFIN CORP. ALL RIGHTS RESERVEDB022...........45090............Band, 5R55N Overdrive/Intermediate (Hi-Energy) 1999-Up......................................................2..........XW4Z-7D034BA 030.............45030G..........Bushing Kit, 5R55N/5R55S/5R55W 1999-Up.............................................................................1..........A034..........31530............Bushing, 5R55N/5R55S/5R55W Pump Cover 1999-Up .............................................................1..........A036..........31531............Bushing, 5R55N/5R55S/5R55W Overdrive Sun Gear 1999-Up................................................1..........A036..........45039............Bushing, 5R55N/5R55S/5R55W Stator (Front) 1999-Up ...........................................................1..........A037..........31532............Bushing, 5R55N/5R55S/5R55W Stator (Rear) 1999-Up............................................................1..........A046..........31533............Bushing, 5R55N/5R55S/5R55W Coast Clutch Drum e 56036A................................................................................................................................1..........B211...........45176A..........Washer, 5R55N/5R55S/5R55W Pump To Coast Clutch Drum .063" (Plastic) 1999-Up.............1..........F7TZ-7D014TA B211...........45176B ..........Washer, 5R55N/5R55S/5R55W Pump To Coast Clutch Drum .071" (Plastic) 1999-Up.............1..........F7TZ-7D014MA B211...........45176C ..........Washer, 5R55N/5R55S/5R55W Pump To Coast Clutch Drum .075" (Plastic) 1999-Up.............1..........F7TZ-7D014NA B211...........45176D ..........Washer, 5R55N/5R55S/5R55W Pump To Coast Clutch Drum .079" (Plastic) 1999-Up.............1..........F7TZ-7D014PA B211...........45176E ..........Washer, 5R55N/5R55S/5R55W Pump To Coast Clutch Drum .083" (Plastic) 1999-Up.............1..........F7TZ-7D014RA B211...........45176F ..........Washer, 5R55N/5R55S/5R55W Pump To Coast Clutch Drum .087" (Plastic) 1999-Up.............1..........F7TZ-7D014SA C232...........45145............Washer, 5R55N/5R55S/5R55W Bearing to Forward Hub (Solid Bronze) 1999-Up .................1..........FOTZ-7D090A D263...........45077............Washer, 5R55N/5R55S/5R55W Parking Gear To Case 1999-Up ..............................................1..........D4ZZ-7B368-AD410...........D56955J ........Switch, 5R55N Neutral Safety (12 Prong Connector) 1999-Up ...............................................1..........XW4Z-7F293AA E922...........33991............Nut, 5R55N/S/W Band 1999-Up .................................................................................................2..........380850-SRWD 5 Speed5R55N / 5R55S / 5R55W。
巴鲁夫 工业 RFID系统 产品手册说明书

Industrial RFID systems MANAGING ALL YOUR DATABalluff offers you a wide selection of data carriers and read/write heads for LF, HF and UHF applications. With the BIS V multi-frequency processor unit, all systems can be combined with each other. This adds flexibility and saves costs through lower inventory levels.Industrial RFID systems – managing all your dataAutomatic identification and tracking in productionTHE PERFORMANCE RANGEYour Balluff solutionsn HF RFID system (13.56 MHz) BIS M n LF RFID system (70/455 kHz) BIS C n LF RFID system (125 kHz) BIS L n UHF RFID system (860/960 MHz) BIS UGo online to individually configure your own system www.balluff.de/go/rfid-configuratorIO-LINK ALL-IN-ONE BIS V PROCESSOR UNIT1 Network block2 Read/write heads with IO-Link3 Data carriers4 Read/write heads with integrated processor unit5 Universal processor unit6 Read/write heads2266433315UHF by country-specific frequencies1 South Korea LF: 125 kHz HF: 13.56 MHzUHF: 917...920.8 MHz 2 JapanLF: 125 kHz HF: 13.56 MHzUHF: 916.7...920.8 MHz 3 ChinaLF: 125 kHz HF: 13.56 MHzUHF: 840.5...844.5 MHz 4 AustraliaLF: 125 kHz HF: 13.56 MHz UHF: 920...926 MHz5 South Africa LF: 125 kHz HF: 13.56 MHzUHF: 865.6...867.6 MHz 6 EuropeLF: 125 kHz HF: 13.56 MHzUHF: 865.6...867.6 MHz 7 USA/Canada/Mexico LF: 125 kHz HF: 13.56 MHz UHF: 902...928 MHz 8 BrazilLF: 125 kHz HF: 13.56 MHzUHF: 902...907.5 MHzWHAT ARE THECONSEQUENCES OF THE DIFFERENT FREQUENCIES?Briefly stated, different frequencies mean different working ranges, since the frequency determines the range. The frequency also affects the coupling behavior (see: How the system components communicate).LF is best suited for close range and for difficult conditions such as metallic surroundings. LF is therefore often used in tool identification.HF is ideal for parts tracking at close range up to 400 mm. With HF you can process and store larger quantities of data at high transmission speeds.UHF typically communicates at a range of 6 m distance. UHF allows simultaneous reading of multiple data carriers (multi-tagging).System frequenciesWorking range of the Balluff BIS RFID systemsSYSTEM STRUCTURERFID requires three main components. These form an RFID system:–■Data carrier (data storage)–■Read/write head (data transmission)–■Processor unit (data processing and communication)The system components in detail–■Data carrier (Tag/Data Carrier)Stores all kinds of data which is read or written by computers or automation equipment. The data carrier antenna sends and receives the signals. Read/write versions are available in various memory capacities and with various storage mechanisms.– Passive data carriers: without power supply – Active data carriers: with power supply–■Read/write headProvides power to the data carrier, reads its data and writes new data to it. It sends this data to the processor unit where the data is further processed. –■AntennaTransmits the power.– HF-/LF systems: Antenna is integrated in the read/write head– UHF systems: Usually passive antennas without read/write head electronics (integrated into the processor unit).–■Processor unitUsed for signal processing and preparation. It typically includes an integrated interface for connecting to the controller/PC system.UHF system: The read/write function can be integrated into the processor unit, so that only a passive antenna and the data carrier are required.How the system components communicateThe data carrier and read/write head connect via the frequency-dependent coupling.With UHF the coupling is via electromagnetic waves, and for LF and HF the coupling is inductive.Components of a HF/LF systemData carrier Read/write head Processor unitUsed at close range, the data carrier must be placed exactly within the read range of the read/write head.Components of a UHF systemData carrier Antenna withProcessor unitread/write head electronicsData carrier Passive antennaProcessor unit withread/write head electronicsIn UHF systems close placement of the data carrier in front of the antenna is not necessary because of the large working range. Still, there are a few rules (see: What to know about UHF systems).Various industry standards are in place both for theLF/HF range and for UHF for communication between the system components. These specify how the information is transmitted. There are also proprietary manufacturer-specific solutions available (see: What you need to know about LF/HF systems/UHF systems).SYSTEM CHARACTERISTICSWhy data storage is importantSelection of the data storage determines where data can be processed and with which components. You can use either of two storage concepts: the central database and decentralized data retention.Central data storage–■All data records are stored in a central database –■Data carrier is simply an identifier –■Mainly for reading informationCan be LF, HF or UHF systems, but mainly used with UHF systemsDecentralized data retention–■All data records are stored on data carriers –■The data carrier stores the identifier and all data records (no central database)–■For both reading and writing informationMainly used with HF/LF systemsWHAT YOU NEED TO KNOW ABOUT LF/HF SYSTEMSIn brief, the read/write distance in LF/HF systems is affected by the antenna shape and the traverse speed.When installing the data carriers the installation conditions and close proximity of metal play a role.Antenna shapeData carriers and read/write heads are constructedwith a rod or round antenna. To achieve the best results the antenna shape must be identical to that of the read/write head. This means: Use rod antenna with rod antenna or round antenna with round antenna.The antenna shape determines different field distributions and read distances. It also determines the active communication field.Ideal working rangeRound antenna–■The lobe of the antenna field is distributed evenly and symmetrically–■No polarization or directionality, even offset.This means the data carrier and read/write head Rod antenna–■The lobe of the antenna field is distributed unevenly and has additional sidelobes–■The is polarization and directionality, which allows greater read distances than with a round antenna–■Identical orientation of the data carrier and read/write head is important in order to achieve greater read distancesInstalling data carriersAccount for distance to metalTo reach the specified read/write distance, a data carrier in a metallic environment must be mounted at a certain distance from metal and within a certain metal-free clear zone. The exact specifications can be found in the data sheets. The following distinctions are made:–■Flush in metalThe sensing surface can be mounted flush on the surface of steel so that it is even with adjacent areas. The range here is less than for differently constructed/installed data carriers of the same size.–■On metalThe sensing surface must not be in contact or surrounded by steel.–■Metal-free (clear zone)The entire area of the data carrier must be kept clear of any type of metal.12365874Data carriers with various memory types are available Traditional memory chips are EEPROM and FRAM.Both types use inductive coupling for power supply and data transmission. They differ in the maximum number of write cycles.–■EEPROM (Electrical erasable programmableread only memory): 100,000 to 1,000,000 write cycles –■FRAM (Ferro-electrical random access memory): 1010 write cyclesHow traverse speed, read/write distance and data transmission time relate to each otherFor reliable data transfer between read/write head andDynamic read/write modeThe data carrier passes by the read/write head without stopping. This should be as close as possible to achieve a long read/write path.How to calculate the traverse speed for dynamic applications Traverse speed (v)Offset (s)=At least 315 mm of offset is required to read the data within a dwell time of 45 ms. Assuming the maximum offset is 340 mm, the read distance must be configured to be very short. The greater the offset of the read/write head, the greater the distance between data carrier and read/write head can be.Important industry standards–■ISO 15693International series of standards for non-contacting chip cards, identification systems and access controls. Operates at a frequency of 13.56 MHz and is the prevailing standard in automation.ISO 15693 defines the protocols for communication between data carrier and read/write head. The datacarriers and read/write heads from different suppliers are generally compatible if they adhere to the same standard. –■ISO 14443International series of standards for non-contact chipcards. These are used in identification systems and access controlling, but also for payment applications such as credit cards, public transportation tickets, etc. Operates at a frequency of 13.56 MHz.In contrast to the ISO 15693 standard, ISO 14443specifies that the data carrier and read/write head carry a manufacturer-specific identifier. Only if the identifiers agree can they communicate with each other.Balluff uses the most commonly accepted contactless chip technology NXP Mifare. This complies with ISO-Standards ISO 7816 and ISO 14443A.High performance solutions from BalluffIn addition to the industry standards there are proprietary systems that are not described by any standard. For example, high-performance solutions from Balluff that are faster and process more data than these industry standards allow. Here the following components are used:–■High-memory data carriers: Data carriers with a memory capacity > 8 kilobytes.–■High-speed data carriers: Combined with the associated read/write heads you can achieve up to eight times greater read speeds than applications that fall under DIN ISO 15693.WHAT YOU NEED TO KNOW ABOUT UHF SYSTEMSPower transmission between data carrier and read/write head is essential for optimal function of a UHF RFID system. Whether and how the antennas need to be aligned with each other depends on the type of polarization of the antennas.Relationship between antenna polarization and data carrier orientationThe polarization of a UHF antenna is determined by the direction of the electrical field of the wave.–■Linear polarized antennasThe electrical field runs either vertical or horizontal to be identically aligned in order to transmit power.–■Data carrier antennaIn UHF systems the coupling is electromagnetic. To transmit data the data carrier‘s antenna converts electromagnetic waves and high-frequency alternating current into each other. Here the polarization direction of the sending antenna and the orientation of the data carrier must be selected correctly. (See illustration for how to achieve optimal power transmission).Construction of a UHF data carrierUHF data carriers with a dipole antenna are often selected (see illustration above). Many other antenna shapes are available as well. These offer particular properties and determine the form factor of the data carrier.Other form factors for UHF data carriersTypical UHF industry standards–■ISO/IEC 18000-6:2013International series of standards that provide the general description of the air interface and signal transmission. The latest standard ISO 18000-63 was published in 2015.–■EPC Class1 Gen2Was published by the standardization organization EPC global, which develops voluntary standards. EPC Class 1 Gen2 Version 2.0.1 is fully compatible with ISO 18000-63.This compatibility mans you can use the same hardware infrastructure and the same data carriers both in an ISO standard environment and an EPC environment.Both standards are suitable for worldwide use. You must however take note of the various national RF regulations.UHF antenna field requires specific test scenariosIn brief: Since the surroundings affect the antenna field, you must perform the closest possible simulation of the ambient conditions.The UHF antenna beams its signal in a wide opening angle. Undesired reflections and absorption in a UHF RFID system Typical ideal antenna fieldin overlapping of wavetrains. Overall it can result in local fields with higher and lower field strengths, or even field collapses (read holes).If a data carrier finds itself in such a read hole, it can no longer communicate with the read/write head.Headquarters Balluff GmbHSchurwaldstrasse 973765 Neuhausen a. d. F.GermanyPhone +49 7158 173-0Fax +49 7158 5010******************D o c . n o . 949747E N · I 20 · S u b j e c t t o c h a n g e s .CONTACT OUR WORLDWIDE SUBSIDIARIES。
士兰微电子 SC8560带LED驱动的数字闹钟电路 说明书

数字位 4
分个位
分个位 分个位 秒个位
杭州士兰微电子股份有限公司
http:
版本号:1.1 2008.06.02 共10页 第4页
SC8560
表 2: 设置内容
显示模式 设置输入
功能说明
小时
按下后立即将小时位加 1,随后以 2Hz 的速率,在每个 1/4 秒和 3/4 秒时加 1。
备控制。
SC8560
版本号:1.1 2008.06.02 共10页 第6页
图 1、 12小时显示和60Hz输入线路
时钟应用电路(负电源使用)
杭州士兰微电子股份有限公司
http:
蜂鸣器
f=900Hz
12HR NC
60Hz NC
28 27 26 25 24 23 22 21 20 19 18 17 16 15
-0.4 ~ +0.4 700
-30 ~ +70 -55 ~ +125
单位 V V V V mA
mW °C °C
电气参数(除非特殊说明,Tamb=25°C,VSS=0V)
参数 工作电压 输入高电平 输入低电平 输入高电平 输入低电平 50/60Hz端输入电压 输入高电平电流1 输入低电平电流1 输入高电平电流2
10'S MIN c&d
10'S MIN e & MIN e
MIN b&g
MIN c&d
MIN a&f
Colon Out
1 2 3 4 5 6 7 8 9 10 11 12 13 14
正半周 负半周
管脚复用LED屏
注: 1、
共阴极
2、
a
8560MFP 彩色多功能一体机使用手册说明书

Paper input
3
1
100-sheet Tray wide range
of custom media and sizes
2 525-sheet main tray. Add one or two additional 525-sheet trays for a total capacity of 1,675 sheets
Go ahead, get creative. Print on business card stock, postcards, labels, transparencies and more. You can expect the same brilliant output no matter what the media.
Phaser® 8560MFP Letter-size Color Multifunction Printer
Xerox® Phaser® 8560MFP Multifunction Printer Affordable power for the busiest office
Phaser® 8560MFP Multifunction Printer
A color printer that meets the challenge
The Phaser 8560MFP multifunction printer delivers fast, attention-grabbing results.
• P ick up the pace with a first-page-out print time as fast as 6 seconds. Both black-andwhite and color print at up to 30 ppm.
8位微控编程学习

AT89S52
主要性能
l 与 MCS-51 单片机产品兼容
l 8K 字节在系统可编程 Flash 存储器
l 1000 次擦写周期
l 全静态操作:0Hz~33Hz
开始/停止控制定时器 2。TR2=1,定时器 2 开始工作
定时器 2 定时/计数选择标志位。 =0,定时; =1,外部事
件计数(下降沿触发)
co 捕捉/重载选择标志位。当 EXEN2=1 时,
=1,T2EX 出现负脉冲,
会引起捕捉操作;当定时器 2 溢出或 EXEN2=1 时 T2EX 出现负跳变,都
AT89S52
表 2 T2CON:定时器/计数器 2 控制寄存器
T2CON 地址为 0C8H 位可寻址
TF2 EXF2 RLCLK
TCLK
EXEN2
7
6
5
4
3
复位值:0000 0000B
TR2
2
1
0
符号
功能
TF2
wEXF2 wRCLK w. TCLK tai EXEN2 -yan. TR2
定时器 2 溢出标志位。必须软件清“0”。RCLK=1 或 TCLK=1 时,TF2 不用置位。 定时器 2 外部标志位。EXEN2=1 时,T2EX 上的负跳变而出现捕捉或重 载时,EXF2 会被硬件置位。定时器 2 打开,EXF2=1 时,将引导 CPU 执行定时器 2 中断程序。EXF2 必须如见清“0”。在向下/向上技术模式 (DCEN=1)下 EXF2 不能引起中断。 串行口接收数据时钟标志位。若 RCLK=1,串行口将使用定时器 2 溢出 脉冲作为串行口工作模式 1 和 3 的串口接收时钟;RCLK=0,将使用定 时器 1 计数溢出作为串口接收时钟。 串行口发送数据时钟标志位。若 TCLK=1,串行口将使用定时器 2 溢出 脉冲作为串行口工作模式 1 和 3 的串口发送时钟;TCLK=0,将使用定 时器 1 计数溢出作为串口发送时钟。 定时器 2 外部允许标志位。当 EXEN2=1 时,如果定时器 2 没有用作串行 时钟,T2EX(P1.1)的负跳变见引起定时器 2 捕捉和重载。若 EXEN2 =0,定时器 2 将视 T2EX 端的信号无效
CLG856工作液压系统维修手册
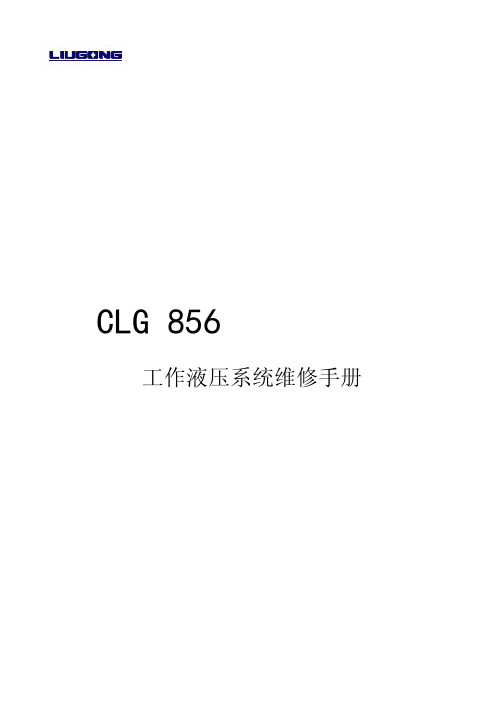
排量(转向):……………….………...63 ml/r 排量(先导):………………………....10 ml/r 转向液压系统调定压力:……………16 MPa 制动系统调定压力:………………..15 MPa 先导液压系统调定压力:………...…3.5 MPa 额定转速:……………………….2200 r/min 旋向:…………………………………...左旋 额定转速:……………………….2200 r/min 旋向:…………………………………...左旋 轴 伸 形 式 : EXT14Z×12/24D.P×30R×6f , SAE“C” 轴伸长度:…………………………….60 mm 有效花键长度:…..…………………...40 mm 进油口法兰连接尺寸:4-M12-7H,36±0.25 ×70±0.25 …..……………………………mm 出油口法兰连接尺寸(转向):4-M10-7H, 26±0.25×52±0.25 ……………………….mm 出油口法兰连接尺寸(先导):4-M10-7H, 22±0.25×48±0.25 ……………………….mm
液压油箱安装在车辆的右侧,用于向整
1.液压油箱 2.液压油加油口 3.液压系统回油 口 4.滤芯安装口 5.油位计 6.油箱清理口
个液压系统供油。在车辆采用湿式制动装置 时,也可为整车制动系统供油。油箱中设置 了回油过滤器,用于清除液压系统油路中的 杂质,以保证液压油液的清洁度。
液压系统中的工作齿轮泵、转向+先导 双联齿轮泵均安装在车辆的变速箱上。通过 变速箱内的分动齿轮,由发动机提供动力, 并向整个液压系统工作的提供压力油源。
组成及介绍
工作液压系统是用于控制装载机工作装置中动 臂和转斗以及其他附加工作装置动作。工作液压系 统油路主要分为两部分:先导控制油路和主工作油 路,主工作油路的动作是由先导控制油路进行控制, 以实现小流量、低压力控制大流量、高压力。整个 工作液压系统的元件组成主要有:液压油箱(带回 油过滤器)、工作泵、先导泵、组合阀、先导操纵阀、 分配阀、动臂油缸、转斗油缸、动臂及转斗自动复 位装置。
洛雷家庭中心L871T8系列快速入门指南说明书

Welcome!From all of us at Lorex, we welcome you to our community – thanks for your purchase of the Lorex Home Center. We designed this product with you in mind, to provide a new and seamless home monitoring solution. With its quality features that are easy to navigate, the Lorex Home Center will be more than a security system, but an extension of your home. Here’s how to get started.What you’ll find in the boxEthernet CableStorage (Pre-inserted)** See product packaging for details on storage configuration.Power Adapter Lorex Home CenterChoose a central location withwalls, ceilings, and other majorRecommendations for improving range:• Ensure the antennas arein the upright position.• If you need to extend the Lorex Home Center’s Wi-Fi signal, we recommend Extender (model #AX62TR). Place the extender halfway between the Lorex HomeConnect the Lorex Home Center1. Plug the power cable into the Lorex Home Center. Then plug the power adapter into a wall outlet.Follow the on-screen prompts to complete first-time setup.2. Create your passcode.Passcode – This is a 6-digit passcode used to unlock your device or disarm your sensors (in case you use sensors with the system). You do not have to enter the passcode manually if the Face Unlock feature has been activated. You also have the option to skip this step.3. Create your device password. Device Password – This password is used to add the Lorex Home Center to the Lorex Home app. It must consist of at least 8 characters and contain a combination of numbers, letters, and special characters. Note: If you forget both your passcode and device password, you must do a hardware reset. Press down on the reset button until a warning pop up appears. Select Yes .4. Set up Face Unlock.Face Unlock – This feature allows you to unlock the Lorex Home Center with thebuilt-in camera. Make sure that the camera lens is not covered, that nothing is covering your face, and that you position your face directly in front of the camera. A reasonable amount of light is required to have this function work properly. You also have the option to skip this step and cover the camera with the built-in lens cover for privacy.Important:Only one device owner’s face can be stored.5. Power on your new cameras and/or doorbell near the Lorex Home Center.Note: If you are adding existing cameras that were previously set up through the Lorex Home app, you will need to ensure that you are running the latest Lorex Homecompatible firmware and then reset the cameras. See page “Troubleshooting: Adding/ Updating Cameras” steps 7-10 for details. This will not erase any of the recordings stored on the cameras.6. Choose your preferred connection set up method from the following three options:Wired Wireless OfflineOption A - Wired Tap the wired icon and connect the Lorex Home Center to your home router using the provided Ethernet cable. The Lorex Home Center must be placed near your home router and positioned centrally relative to the different Lorex devices.Option B - Wireless Tap the wireless icon, select your Wi-Fi network from the list, then enter the Wi-Fi password to connect. The Lorex Home Center can be placed wherever there is a good connection to your home router and positioned centrally relative to the different Lorex devices.Note: Requires a dual-band router (2.4GHz/5GHz) with 5GHz Wi-Fi network enabled.Network SetupOption C - Offline Tap the offline icon to setup through a direct connection. The Lorex Home Center can work offline and no internet connection is required to operate it or connect it to different Lorex devices. Central placement is important for the Lorex devices to communicate directly with the Lorex Home Center. You will not be able to use the Lorex Home App to access the LorexHome Center remotely and will not receive automatic update notifications.Device Setup1. In the Device Setup screen, select the device that you want to add and tap Next .Note : Make sure your devices are compatible, powered on and nearby the Lorex Home Center for initial setup. Once set up, you can unplug them and move them to their final locations as long as they are within range of the Lorex Home Center.Important: If your camera has not been detected, you will need to update the camera’s firmware by connecting it directly to the router and update the firmware through the Lorex Home app. See page “Troubleshooting: Adding/Updating Cameras ” for more details.2. Pair the Lorex Home Center to the Lorex Home app for remote access and viewing.Notes : • Use the device password when asked (Step 3 in “Connect the Lorex Home Center ”). • This does not apply if you are using the offline connection method.Light Status IndicatorsAway*Home*Disarmed*System Error Voice AssistantActivated* This status only applies to the Lorex sensors.Home Screen Time and weather Network signal/ settings Live view all channels Turn notifications on/off Camera/device settingsPrivacy mode enabled Device viewSystem error Sensor status Privacy modePlayback recordingsDevice managerEventsPhotosDevice settings Saved recordings /snapshotsWeatherVoice prompts examplesLive View DevicesettingsEventtypePlay/ pauseTakesnapshotDevice name /channel selectionRecordvideo2-waytalkWarninglight*Siren*PrivacymodeHD video* Only compatible cameras support this function.Adjust speaker volume• Do Not Disturb mode: Tap to silence alerts, notifications, and light statuses that you get while your device is locked. Tap again to disable DND mode. • Privacy mode: Tap to turn off live feed from all cameras. Tap again to disable privacy mode.• Panic mode: Press and hold panic mode for 5 seconds to turn on all lights and sirens from compatible active or smart deterrence cameras/doorbell. Tap again to turn off.• Bluetooth audio: Any bluetooth capable device can play audio through the Lorex Home Center’s speakers. Go to your bluetooth capable device’s Settings > Bluetooth, turn on Bluetooth, then select “Lorex Home Center”. Complete the pairing process to begin streaming music/audio.Adjust brightness Home Screensaver DefinitionsDevice settings Mute Do Not Disturb mode Privacy mode Panic modeBluetooth audio: play, pause, skip Auto adjust brightnessSwipe-down MenuLorex Voice AssistantThe Lorex Voice Assistant is a specially designed voice assistant for the Lorex Home Center. It was developed with your privacy in mind. All voice processing is done inside the Lorex Home Center. This means that no voice information leaves the device and makes response time quick. To enable this feature make sure that the microphone hardware kill switch is turned on and say the wake up word “Lorex”.A sample voice command: “Lorex, show me all cameras!”For a sampling of the different voice commands, tap on the Voice Prompts icon on the home screen. For a full list of supported voice commands, visit the product page at .Note: Voice control also works in offline mode.Troubleshooting: Adding/Updating Cameras1. Make sure the camera is powered on.2. Scan the QR code on the right side of the page to install the free Lorex Home app from the App Store or Google Play Store.3. Tap the Lorex Home icon to launch the app. If you don’t already have an account, tap Sign up , then follow the on screen prompts to create an account.4. Once the status LED on the camera is flashing green and the startup chime sounds, tap +.5. Scan the QR code on the camera using your mobile device’s camera (or tap Manually enter Device ID ).6. Follow the rest of the in-app instructions until your camera is set up.7. After setup, tap the camera’s settings icon and then tap Upgrade Firmware . Your camera will automatically reboot. If there is no “Upgrade Firmware” message, then you have the latest firmware installed.8. Tap the camera’s settings icon and tap Remove Device at the bottom.9. Press and hold the reset button on your camera and wait for the chime.10. Return to step 1 on the Device Setup page.For compatible cameras that have already been set up in the Lorex Home app, follow steps 7-10. For cameras that have not been detected during set up, follow theinstructions below to update them with the latest firmware.For up-to-date information and support,visit /series/LHC .To purchase the Lorex Home Center Extender (AX62TR),additional cameras and sensors, visit and/or authorized resellers.Do more with the Lorex Home CenterFCC NOTICE THIS DEVICE COMPLIES WITH PART 15 OF THE FCC RULES. OPERATION IS SUBJECT TO THE FOLLOWING TWO CONDITIONS:(1) THIS DEVICE MAY NOT CAUSE HARMFUL INTERFERENCE, AND (2) THIS DEVICE MUST ACCEPT ANY INTERFERENCE RECEIVED, INCLUDING INTERFERENCE THAT MAY CAUSE UNDESIRED OPERATION.Important:• The Lorex Home Center is rated for indoor use only. Do not use outdoors.• Only use with included power supply.• Only use with compatible memory. See product support page for details on compatible memory.L871T8_QSG_EN_R2。
SC8560中文资料
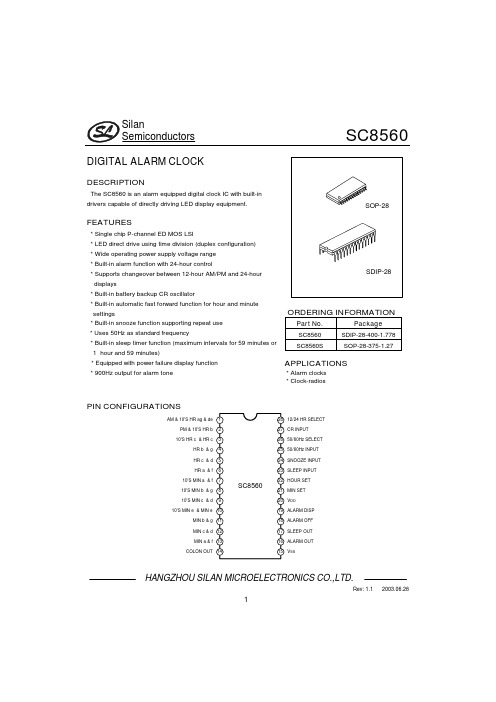
HANGZHOU SILAN MICROELECTRONICS CO.,LTD.Rev: 1.1 2003.06.261DIGITAL ALARM CLOCKDESCRIPTIONThe SC8560 is an alarm equipped digital clock IC with built-in drivers capable of directly driving LED display equipment.FEATURES* Single chip P-channel ED MOS LSI* LED direct drive using time division (duplex configuration) * Wide operating power supply voltage range * Built-in alarm function with 24-hour control* Supports changeover between 12-hour AM/PM and 24-hour displays* Built-in battery backup CR oscillator* Built-in automatic fast forward function for hour and minute settings* Built-in snooze function supporting repeat use * Uses 50Hz as standard frequency* Built-in sleep timer function (maximum intervals for 59 minutes or 1 hour and 59 minutes)* Equipped with power failure display function* 900Hz output for alarm toneORDERING INFORMATIONPart No.PackageSC8560 SDIP-28-400-1.778SC8560S SOP-28-375-1.27APPLICATIONS* Alarm clocks * Clock-radiosPIN CONFIGURATIONSAM & 10'S HR ag & de10'S HR c & HR cPM & 10'S HR b HR b & g HR c & d HR a & f 10'S MIN a & f 10'S MIN b & g 10'S MIN c & d10'S MIN e & MIN e MIN b & g MIN c & d MIN a & f COLON OUT 12/24 HR SELECT CR INPUT 50/60Hz SELECT 50/60Hz INPUT SNOOZE INPUT SLEEP INPUTHOUR SET MIN SET V DDALARM DISP ALARM OFF SLEEP OUT ALARM OUT V SSHANGZHOU SILAN MICROELECTRONICS CO.,LTD.Rev: 1.1 2003.06.262BLOCK DIAGRAM50/60H z 12/24H R C R I n p u t50/60H z I n p u tM i n u t e S e tH o u r S e tA l a r m D i s p l a yS l e e p D i s p l a yS n o o z e I n p u tO F F O u t p u t O u t p u tO u t p u t A M & 10'S H R a g & d eP M & 10'S H R b0'S H R c & H R cH R b &gH R c &dH R a &f0'S M I N a &f10'S M I N b &g10'S M I N c &d10'S M I N e & M i n ei n b &gM i n c &di n a &fHANGZHOU SILAN MICROELECTRONICS CO.,LTD.Rev: 1.1 2003.06.263ABSOLUTE MAXIMUM RATINGS (Ta =25°C, Vss =0V)CharacteristicSymbolConditionValueUnitMaximum Supply Voltage V DD max.-15.0 ~ + 0.3 V Input Voltage 1V IN(1) 50/60Hz input -15.0 ~ + 0.3 V Input Voltage 2 (except pin 26) V IN(2) Except 50/60Hz input -15.0 ~ + 0.3 V Output VoltageV OUT-15.0 ~ + 0.3 V Input Clamp current( pin 26) I IN 50/60Hz input -0.4 ~ +0.4 mA Allowable Power Dissipation P D Ta=70°C 700 mWOperating Temperature Topr -30 ~ +70 °C Storage TemperatureTstg-55+125°CELECTRICAL CHARACTERISTICS (Tamb=25°C, V DD =-12.0V, V SS =0V,Unless otherwise specified)ParameterSymbolTest conditions MinTypMaxUnitSupply Voltage V DD-14.0 -7.5 VInput “H” level Voltage V IH(1) 50/60Hz Input -1.0 V Input “L” level Voltage V IL(1) 50/60Hz Input V DD +2V Input “H” level Voltage V IH(2) Except 50/60Hz input -1.5 V Input “L” level VoltageV IL(2) Except 50/60Hz inputV DD +2V50/60 Hz input pin input voltage V AC-INV LEDVInput “H” level current(1) I IH1 50/60Hz Input, V IN =V SS 10 μA Input “L” level current(1) I IL1 50/60Hz Input, V IN =V DD 10 μA Input “H” level current(2) I IH2Input pins other than 50/60Hz Input,V IN =V SS20μA Input “L” level current(2) I IL2Input pins other than 50/60Hz Input,V IN =V DD10 μA Output “H” level current(1) I OH1Alarm output and sleep output, V OH =V SS -1V5 mA Output leakage current(1) I OF1Alarm output and sleep output, V OUT =V DD10 μA Output “H” level current(2) I OH2AM& 10’S HR ag&de (24H mode),V OUT =V DD -1V 36 mA Output leakage current(2) I OF2AM& 10’S HR ag&de (24H mode),V OUT =V DD20 μA Output “H” level current(3)I OH3Segment Output other than those listed above , V OUT =Vss-1V18 mA (To be continued)HANGZHOU SILAN MICROELECTRONICS CO.,LTD.Rev: 1.1 2003.06.264(Continued)ParameterSymbolTest conditionsMin Typ Max UnitOutput leakage current(3) I OF3Segment Output other than those listed above, V OUT =V DD20μA Power failure detection voltage V DF -7.5 -5.0VConsumption currentI CC Output set to off and pull-down attached input set to open 5 7 mABackup oscillator stability factor fs Standard value,900Hz, V DD = -9V 10%-10 10 % Backup oscillator accuracyfaStandard value,900Hz, V DD = -9V-10 10 % DESCRIPTION OF OPERATIONSTerminal DescriptionOperating Description50/60 Hz Input:Built-in Shumidt circuit enable noise elimination at 50/60Hz commercial frequencies with use of a simple CR filter. Built-in pull-up resistor.CR Input When the AC power supply is interrupted, the time counter switches to a holding state and a built-in oscillator promptly begins operation. If 50/60Hz input continuous for 3 clocks without arriving, this oscillator’s output is activated and functions as the time counter clock in place of 50/60Hz input. The frequency levelof this clock oscillator is determined according to the CK Value. While the above mentioned oscillator is operating using backup mode, all segment output is switched to OFF. (Note) When the backup oscillator is in use due to an AC power supply interruption, the 50/60Hz input pin must be maintained open or at a Vss level.50/60Hz Selective Input When 50/60 selective input is connected to Vss,50Hz use is enable. When 50/60selective input is left open, V DD is activated using an internal pull-down resistor and the setting is switched to enable use at 60Hz.Display Mode Selective Input (Alarm Select/Sleep Select )Since the pull-down resistor is built-in, selection from four display modes is possible using two SPST switches (single-pole and single-throw switches). Table l shows these display mode selections.Time Setting InputThere are two setting inputs for use with “hour” and “minute”. Time content settings shown in Table 2 are possible by activating Vss to these pins. A pull-down resister is built-in.12/24H Select Input Leaving this pin unconnected (V DD ) causes the 12-hour basis to be selected,connecting this pin to V SS cause the 24-hour basis to be selected .An internal pull-down resistor is provided.(To be continued)HANGZHOU SILAN MICROELECTRONICS CO.,LTD.Rev: 1.1 2003.06.265(Continued)Terminal DescriptionOperating DescriptionPower Failure Detection display If the power supply voltage drops and is applied again, all the on-segments flashand the power failure indication mode is entered. The power failure indicationmode is released by applying V SS to “hour set” or “ minutes set”.Alarm Operation and Alarm OutputThe alarm signal outputs when alarm content marches the time .When not resetby either snooze input or alarm off input, output continues after l hour and 59 minutes. This output signal consists of 900 Hz 2 Hz intermittent (50% duty) modulation signals. When the need arises, a filter can be applied to alter the alarm signal to a DC signal.Snooze InputWhen the alarm is sounding and instantly activating Vss to this pin, alarm output is set to OFF for a period between 8 and 9 minutes after which time the alarm signalis once again output .The snooze function can be used repeatedly in l hour and 59 minutes intervals. A pull-down resist is built-in. Activating Vss to the snooze pin when the alarm is OFF resets the sleep timer counter to [0:00].(This is known as the one-touch sleep timer reset function.)Alarm Off InputActivating this input pin to Vss instantly sets alarm output to OFF. A pull-down resistor is built-in.Sleep Timer and Sleep Output:Sleep output can turn on the radio and can be set for time intervals of 59 minutes or l hour and 59 minutes. Refer to Table 2 for the proper selection procedure (59minutes or l hour and 59 minute selection). This sleep timer is constructed using a down counter and when the counter content arrives at [00], output is set to off and the radio turns off .Adding Vss to snooze input turns sleep output off, when sleep output is on.TABLE 1:DISPLAY MODESSelective Input AlarmSleepDisplay Mode Digit No.1Digit No.2Digit No.3Digit No.4NC NC Time display 10’s place for hour ,AM/PM Hour 10’s place for minute Minute VssNC Alarm display10’s place for hour ,AM/PMHour10’s place for minuteMinute NC Vss Sleep display Clear Hour10’s place forminute Minute VssVss Second displayClearMinute10’s place for secondSecondNote: Activating Vss using two inputs simultaneously (alarm select and sleep select), the display mode is switchedto display seconds.HANGZHOU SILAN MICROELECTRONICS CO.,LTD.Rev: 1.1 2003.06.266TABLE 2:SETTING CONTENTSDisplay ModeSet lnputFunctionsHOURlmmediately adds 1 to hour digits and then assigns an additional 1. at a speed of 2 Hz , after each 1/4 to 3/4 second .MIN lmmediately adds 1 to minute digits and then assigns an additional 1. at a speed of 2 Hz, after each 1/4 to 3/4 second . Seconds are reset.TimeBOTH Operates both as outline above. HOUR(Note)Second digits are cleared to [00].MIN Time holds. Second (Alarm &Sleep)BOTH Resets hour and minute digits as [0:00] when operating in 24-Hmode or [12:00] when operating in 12-H mode.HOURlmmediately adds 1to hour digits and then assigns an additional 1, at a speed of 2 Hz, after each 1/4to 3/4 second.MIN lmmediately adds 1 to minute digits and then assigns an additional 1, at a speed of 2 Hz, after each 1/4to 3/4 second.Alarm BOTH Resets hour and minute digits to [0:00] when operating in 24-hour mode or [12:00] when operating in, 12-hour mode.-Sets sleep counter to [0:59] instantly when V DD is activated to sleep select. HOUR Sets sleep counter to [1:59] instantly when V DD is activated to sleep select and hour at the same time.MIN Sleep counter looses 1 at a speed of 2 Hz SleepBOTHSleep counter looses 1 at a speed of 2 HzOnce conditions have been switched to reset or hold, input of other functions is locked until HOUR and MIN input have separated. Note:When the digital reading for seconds is between 30 and 59 seconds, 1 is added to digits for minutes as the digital reading for seconds resets to [00]HANGZHOU SILAN MICROELECTRONICS CO.,LTD.Rev: 1.1 2003.06.267CLOCK-RADIO APPLICATION CIRCUIT (Positive Power Supply)12T h i s c i r c u i t i s u s e d a s n o i s e i n t e r f e r e n c e s t r i p p e r f o r t h e L W b a n d .( B a c k u p c o n t r o l i s e n a b l e d e x c e p t f o r b a t t e r y b a c k u p m o d eC y c l e 212 H o u r D i s p l a y a n d 60H z C i r c u i t D i a g r a mHANGZHOU SILAN MICROELECTRONICS CO.,LTD.Rev: 1.1 2003.06.268CLOCK APPLICATION CIRCUIT (Negative Power Supply)12u t p u t i s n o t u s e d , C R i n p u t i s c o n n e c t e d t o V s s .C y c l e 212 H o u r s D i s p l a y a n d 60H z C i r c u i t d i a g r a mSOP-28-375-1.27 UNIT:mmHANGZHOU SILAN MICROELECTRONICS CO.,LTD.Rev: 1.1 2003.06.269HANGZHOU SILAN MICROELECTRONICS CO.,LTD.Rev: 1.1 2003.06.2610Attachment Revision HistoryDataREVDescription Page2000.12.31 1.0 Original2003.06.26 1.1 Add ”SOP-28-375-1.27”Add” ORDERING INFORMATION”DEL”FUNCTIONS”1, 9 11。
IntelCPU机器指令中文版手册
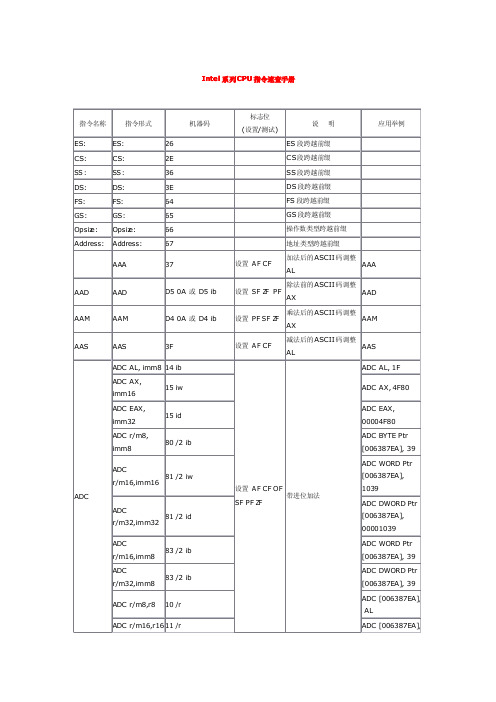
BOUND r32,m32&32
F80
A ND BYTE Ptr [006387EA], 39
A ND WORD Ptr [006387EA], 1039
A ND DWORD Ptr [006387EA], 00001039
A ND WORD Ptr [006387EA], 39
A ND DWORD Ptr [006387EA], 39
AAS ADC
AAS
3F
ADC AL, imm8 14 ib
ADC AX, imm16
15 iw
ADC EAX, imm32
15 id
ADC r/m8, imm8
80 /2 ib
ADC 81 /2 iw
r/m16,imm16
ADC 81 /2 id
r/m32,imm32
ADC 83 /2 ib
r/m16,imm8 ADC
ADD r8,r/m8 02 /r
ADD r16,r/m16
03 /r
ADD r32,r/m32
03 /r
A ND AL, imm8 24 ib
A ND A X, imm16
25 iw
A ND EAX, imm 25 id
设置 A F CF OF 加法
SF PF ZF
设置 CF OF PF 逻辑与
SF ZF
BT r/m32,r32 0F A3 BT
BT 0F BA /4
r/m16,imm8
BT 0F BA /4
r/m32,imm8
BTC
BTC r/m16,r16 0F BB
设置 ZF 设置 ZF 不影响标志位 设置 CF 设置 CF
NAU85L20评估板用户手册说明书

NAU85L20 Evaluation BoardUser ManualVersion 2.0 User ManualContents1INTRODUCTION (4)2SETUP (6)2.1Power Connectors (6)2.2Analog Input Connector (7)2.3I2S I/O Ports (9)2.4Jumper setting summary (10)2.5PCB Setting (11)2.6AP Connections and Readout Setting (12)3NAU85L20 EVALUATION BOARD GUI (15)3.1Device Control (16)3.2Quick Start (17)3.3FLL (19)3.4Digital Audio Interface (20)3.5Clock Div (21)3.6PowerUp and Gains (22)3.7ADC (23)3.8Filters (24)3.9Limiters (25)3.10Others (26)4NAU85L20 EVALUATION BOARD SCHEMATIC (28)Figure 1: NAU85L20 Evaluation Board with Analog Input Configuration (4)Figure 2 EVB Top view (5)Figure 3 EVB Bottom View (5)Figure 4: External Connectors on EVB for Power Supplies (6)Figure 5: Jumpers Locations on EVB for different Power Connections (7)Figure 6: Jumper Location on EVB for ADC Inputs (9)Figure 7: ADC connection with AP outputs (12)Figure 8: AP connection for NAU85L20 ADC (12)Figure 9: I2S Port connection forNAU85L20 (13)Figure 10: AP Measurement Readout (14)Figure 11: NAU85L20 GUI Front page—Device Control (15)Figure 12: Device Control Tab dictation (16)Figure 13: Quick Start Tab (18)Figure 14: NAU85L20 Demo GUI FLL Tab (20)Figure 15: NAU85L20 Demo GUI Digital Audio Interface Tab (21)Figure 16: NAU85L20 Demo GUI Digital Clock Div Tab (22)Figure 17: NAU85L20 Demo GUI Digital PowerUp& Gains Tab (23)Figure 18: NAU85L20 Demo GUI Digital ADC Tab (24)Figure 19: NAU85L20 Demo GUI Digital Filters Tab (25)Figure 20: NAU85L20 Demo GUI Digital Limiter Tab (26)Figure 21: NAU85L20 Demo GUI Digital Others Tab (27)Table 1: Power Supply Voltages (7)Table 2: MIC Jumper Configuration (8)Table 3: Analog Input Configuration (8)Table 4:Analog Input Test Pin Configuration (9)Table 5: I2S I/O Port2 Pin out (10)Table 6: Jumper Connections Summary (11)1IntroductionThis document describes the process to setup the NAU85L20Dual Audio ADC Evaluation Board and the included GUI Software.Figure 1: NAU85L20 Evaluation Board with Analog Input ConfigurationFigure 2 EVB Top view Figure 3 EVB Bottom View2 Setup2.1 Power ConnectorsThe NAU85L20 Evaluation Board can be powered on by one of the supply options as mentioned below.1. Power connector P1 ( DC adapter)2. Banana Plug (BP2-BP3 using 5Vdc and GND to use onboard LDO)3. Applying external power to BP4, BP6,BP1, BP54. USB 5V supply (CN4)5.Port2 connectorVDDMIC BP4USB CN45VDC P1BP2BP3PORT2Figure 4: External Connectors on EVB for Power SuppliesWhen applying 5V through P1 or the Banana plug, the power is routed through several LDOs that willsupply the correct voltages needed by the NAU85L20 for normal operation. To route these sources to the chip, JP12, 14, 15, 20, and 21 must be shorted between pins 1 and 2.USB port CN4 can also supply 5V to these LDOs through a diode by connecting pin 1 and 2 of JP13.2Table 1: Power Supply VoltagesIf you would like to run the board at voltages other than th at the LDO’s provide then you can put jumper sat JP12, 14, 15, and 20 between pins 2 and 3 and apply the desired voltage to the appropriate banana plugs. It should be noted that JP21 must be shorted to apply power to the chip.You can also transfer voltage from VDDA to VDDC by shorting JP18, voltage from VDDB to VDDMIC by shorting JP19, and voltage from MB_5PO to EXT 5V by shorting JP17. Please note that in all the cases the power should be supplied only through one port the other port should have no power supply.JP18JP13JP15JP12JP21JP20JP19JP14JP17Figure 5: Jumpers Locations on EVB for different Power Connections2.2 Analog Input ConnectorWhen testing the analog microphones, please refer to the table below for the configuration settings.Table 2: MIC Jumper ConfigurationWhen testing with analog inputs, please refer to the table below for the configuration settings.Table 3: Analog Input ConfigurationAlternatively, analog input can also be supplied through table shown below:Table 4:Analog Input Test Pin ConfigurationCH1JP1CH4JP1CH4JP4CH4JP2CH1JP4TP8TP6Figure 6: Jumper Location on EVB for ADC Inputs2.3 I 2S I/O PortsThe I2S clock I/Os are provided through Port1and Port2 as described in the tables belowTable 4: I2S I/O Port1 Pin OutTo select port1 connect pins 1-6, 2-7, 3-8, 4-9, and 5-10 of JP3.Else,to select port2 short pins 6-11, 7-12,8-13, 9-14, and 10-15 of JP3.Port1 can be used for measurement with analyzer.If AP is configured as master of I2S bus then JP1 1-2 jumper need to be used. In case AP is configured as slave use JP1 2-3.You can select two possible set of Digital Output through JP2. If pins 2 and 3 of JP2 are shorted the digital output of Channel 1 and 2(ADC DO12 pin 10 on DUT) is selected. And if pins 1 and 2 are shorted the digital output of Channel 3 and 4(ADC DO34 pin 9 on DUT) is selected.For I2C communication connect pins 1 and 2 of JP4 and JP5, please leave other pins of JP5 open for RevA board. Short pins 1 and 2 of JP6 if you are using USB supply. Else if you are using VDDB supply Verify that the VDDB voltage level is at 3.3V and connect pins 2 and 3 of JP6. You can connect pins 1 and 2 of JP9 to enable Mode pin for 2-wire Read/Write operation. The Device Address of the NAU85L04 is either 0x1C(CSB=0) or 0x1D (CSB=1).2.4Jumper setting summaryTable 6 below shows all the jumper connections and its corresponding functions:2.5PCB SettingFigure 7: ADC connection with AP outputsFigure 7 shows PCB connection from AP analog output ChA to NAU85L20 CH1 input. Differential inputs are connected from Audio Precision toTP1 and TP3. For single ended input close jumper CH1JP4 and supply positive signal to TP1. To supply analog differential or Single ended input to rest of the channels repeat the above process by following the setup mentioned in Table 4:Analog Input Test Pin Configuration.2.6AP Connections and Readout SettingFigure 8: AP connection for NAU85L20 ADCFigure 8 shows the connection at AP for NAU85L20 ADC test. The differential analog output A is connected to DUT with differential balanced outputs. The bottom right colors in Figure 9 shows the AP signals’ connection with demo board shown below.Figure 9: I2S Port connection forNAU85L20Figure 10: AP Measurement ReadoutFigure 10 shows AP setting and readout manual. Analog Generator configuration should choose bal-float with 40 ohm Zout. Digital Analyzer should set as the following;Analyzer: DSP audio analyzerInput: Digital @ ISR3NAU85L20 Evaluation Board GUIThe GUI will allow the user to write and read I2C commands through USB to the NAU85L20. The front page, Device Control, is shown as the following;Figure 11: NAU85L20 GUI Front page—Device ControlNAU85L20 GUI has the following 10 tabloids;a) Device control: resetting whole chip, loading and saving register file, writing and readingregister values, and read/write register historyb) Quick Start: providing quick set-up NAU88L20 with register setting freec) FLL: setting FLL(frequency loop locked) registersd) Digital Audio Interface: controlling NAU85L20 difital audio interface, such as I2S, PCM,Justified, word length, etc.e) Clock Div: controlling NAU85L20 system clocks including MCLK, ADC, GPIO, etc.f) Power Up & Gains: controlling ADC analog amplifiers’ gain, power -up, MIC voltage, and bias. g) ADC: controlling four ADC channels digital gains, mux, and enable.h) Filters: controlling ADC digital high pass filter, Notch filter, filter sampling rate. i) Limiter: Controlling ALC (Automatic Level Control) register setting. j) Others: Miscellaneous registers.3.1 Device ControlDevice control is the first page of NAU85L20 GUI. It shows as below;CHIP Reset/I2CRegister Read/WriteHistoryFrom Register Read/Write EntryFigure 12: Device Control Tab dictationFor this front page, there are several features marked in Figure 12 for Device Control;a) RUN, Continuous Run, STOP: are buttons for run, continuous run, andstop command for Nau85L20 GUI. When click the white arrow, , GUI starts to run.will change to . During GUI running, , click to stop GUI.b) GUI Tabs; The summary of all NAU85L20 Tabs shows on top edge. Clicking specifictab, GUI will enter the tab for further application. As shown and marked in Figure 12,currently there are ten tabs available.c) CHIP Reset/I2C Address Chip reset: reset button will clean up all current registersettings saving in GUI, and I2C address selection is used to select a right I2C addressfor GUI.d) Register Read/Write Entry: register settings tab allows the user to write to and readfrom a single register. When writing a register, you can choose whether or not to havethe GUI automatically read the register after every write by using the “Read back?”,button. Using this button ensures that the register was written correctly.e) Save/Load Register file: button will save all registers to or load a set of registers to orfrom a text file of your choice. To load a file, click button, a directorypath window will show up for you to select register file. To save verified register settins,clicking and allocate the register settings to target directoryf) Register Read/Write History: the table will show the last 6 entry from read/write registersetting.g) QUIT: Selecti ng “Quit” button to quit NAU85L20 GUI.3.2Quick StartQuik Start tab has default register settings with selective buttons.a) For enable ADC, button sequencesb) Enable mic biasc) Enable FLLd) Disable FLLe) Writing Register light blinks to show activity of writing register. ExecutionIndicatorFigure 13: Quick Start Tab3.3FLLThe integrated FLL can be used to generate a master system clock, MCLK, from MCLKl, BCLK or FS as a reference. Because of the FLL’s tolerance of jitter, it may be used to generate a stable MCLK from less stable input clock sources or it can be used to generate a free-running clock in the absence of an external reference clock source.This Control Tab gives access to various controls and settings in the FLL block. Control of these bits is normally automatic when using the Device Control panel. These controls are provided in this panel for convenient manipulation and evaluation of the FLL section features.The description and function of each of these control bits is explained in detail in the Register Map and FLL found in Table of Contents of the NAU85L20 Datasheet. The name for each control in this panel matches the name given to specific control bits in NAU85L20 control registers as described in the detailed register map in NAU85L20 Datasheet.Figure 14: NAU85L20 Demo GUI FLL Tab3.4Digital Audio InterfaceThis Control Tab gives access to various controls and settings in the Digital Audio Interface. Control of these bits is normally automatic when using the Device Control panel. These controls are provided in this panel for convenient manipulation and evaluation of the Digital Audio Interface.The description and function of each of these control bits is explained in detail in the Register Map and Digital Audio Interface found in Table of Contents of the NAU85L20 Datasheet. The name for each control in this panel matches the name given to specific control bits in NAU85L20 control registers as described in the detailed register map in NAU85L20 Datasheet.Figure 15: NAU85L20 Demo GUI Digital Audio Interface Tab3.5Clock DivThis Control Tab consists of controls for Clock source, Clock Division, and GPIO Control. Control of these bits is normally automatic when using the Device Control panel. These controls are provided in this panel for convenient manipulation and evaluation of the Clock Division.The description and function of each of these control bits is explained in detail in the Register Map found in Table of Contents of the NAU85L20 Datasheet. The name for each control in this panel matches the name given to specific control bits in NAU85L20 control registers as described in the detailed register map in NAU85L20 Datasheet.Figure 16: NAU85L20 Demo GUI Digital Clock Div Tab3.6Power Up and GainsThis Control Tab gives access to various controls and settings to change PowerUp and gains of different channels. Control of these bits is normally automatic when using the Device Control panel. This panel also includes controls for MicBias, VMID, and ACDC.The description and function of each of these control bits is explained in detail in the Register Map found in Table of Contents of the NAU85L20 Datasheet. The name for each control in this panel matches the name given to specific control bits in NAU85L20 control registers as described in the detailed register map in NAU85L20 Datasheet.Figure 17: NAU85L20 Demo GUI Digital PowerUp& Gains Tab3.7ADCThis Control Tab gives access to various controls and settings in the ADC converter blocks. Controls are also included here for gain options associated with the ADC function. Control of these bits is normally automatic when using the Device Control panel. Some controls are arranged in columns to configure and change settings of individual channel. These controls are provided in this panel for convenient manipulation and evaluation of the ADC section features.The description and function of each of these control bits is explained in detail in the Register Map and ADC Digital block found in Table of Contents of the NAU85L20 Datasheet. The name for each control in this panel matches the name given to specific control bits in NAU85L20 control registers as described in the detailed register map in NAU85L20 Datasheet.Figure 18: NAU85L20 Demo GUI Digital ADC Tab3.8FiltersThis Control Tab gives access to various controls and settings in the filtering blocks. Controls are also included here for High Pass filter, Notch filter, and ADC sample rate.Control of these bits is normally automatic when using the Device Control panel. Some controls are arranged in columns to configure and change settings of individual channel. These controls are provided in this panel for convenient manipulation and evaluation of the signal processing settings.The description and function of each of these control bits is explained in detail in the Register Map and ADC/digital signal processing found in Table of Contents of the NAU85L20 Datasheet. The name for eachcontrol in this panel matches the name given to specific control bits in NAU85L20 control registers as described in the detailed register map in NAU85L20 Datasheet.Figure 19: NAU85L20 Demo GUI Digital Filters Tab3.9LimitersThis Control Tab gives access to various controls and settings for the Input Limiter and ALC signal control blocks. Control of these bits is normally automatic when using the Device Control panel. These controls are provided in this panel for convenient manipulation and evaluation of the Input Limiter and ALC signal control blocks.The description and function of each of these control bits is explained in detail in the Register Map and Input Limiter/ALC signal control blocks found in Table of Contents of the NAU85L20 Datasheet. Thename for each control in this panel matches the name given to specific control bits in NAU85L20 control registers as described in the detailed register map in NAU85L20 Datasheet.Figure 20: NAU85L20 Demo GUI Digital Limiter Tab3.10OthersThis Control Tab consists of controls which are occasionally used. It includes controls for Mic mute, and I2C control.The description and function of each of these control bits is explained in detail in the Register Map found in Table of Contents of the NAU85L20 Datasheet. The name for each control in this panel matches the name given to specific control bits in NAU85L20 control registers as described in the detailed register map in NAU85L20 Datasheet.Figure 21: NAU85L20 Demo GUI Digital Others Tab4NAU85L20 Evaluation Board Schematic5Revision History。
珍贵手册:盾浏锁定系列L TC8569、L TC8570系列、L TC8571、L TC8572系列
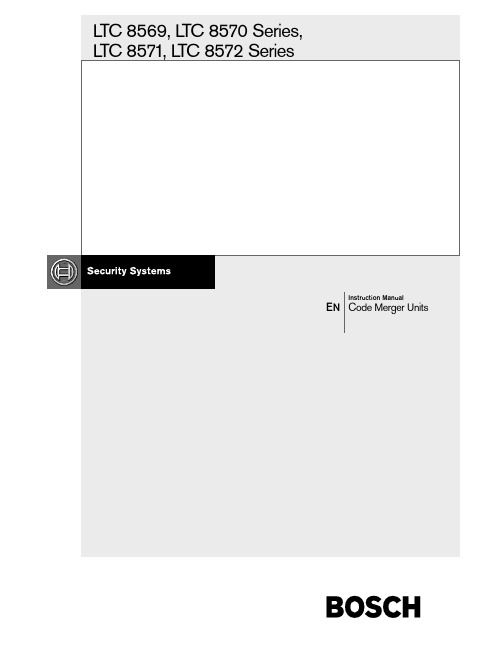
Important Safeguards1.Read, Follow, and Retain Instructions- All safetyand operating instructions should be read andfollowed before operating the unit. Retain instructions for future reference.2.Heed Warnings- Adhere to all warnings on the unitand in the operating instructions.3.Attachments- Attachments not recommended bythe product manufacturer should not be used, as they may cause hazards.4.Installation Cautions- Do not place this unit on anunstable stand, tripod, bracket, or mount. The unitmay fall, causing serious injury to a person andserious damage to the unit. Use only manufacturer-recommended accessories, or those sold with theproduct. Mount the unit per the manufacturer'sinstructions. Appliance and cart combination should be moved with care. Quick stops, excessive force, or uneven surfaces may cause the appliance and cartcombination to overturn.5.Cleaning- Unplug the unit from the outlet beforecleaning. Follow any instructions provided with theunit. Generally, using a damp cloth for cleaning issufficient. Do not use liquid cleaners or aerosolcleaners.6.Servicing- Do not attempt to service this unityourself. Opening or removing covers may exposeyou to dangerous voltage or other hazards. Refer all servicing to qualified service personnel.7.Damage Requiring Service- Unplug the unit fromthe main AC power source and refer servicing toqualified service personnel under the followingconditions:•When the power supply cord or plug is damaged.•If liquid has been spilled or an object has falleninto the unit.•If the unit has been exposed to water and/orinclement weather (rain, snow, etc.).•If the unit does not operate normally, whenfollowing the operating instructions. Adjust onlythose controls specified in the operatinginstructions. Improper adjustment of other controlsmay result in damage, and require extensive workby a qualified technician to restore the unit tonormal operation.•If the unit has been dropped or the cabinetdamaged.•If the unit exhibits a distinct change inperformance, this indicates that service is needed.8.Replacement Parts- When replacement parts arerequired, the service technician should usereplacement parts specified by the manufacturer orthat have the same characteristics as the original part.Unauthorized substitutions may result in fire,electrical shock or other hazards.9.Safety Check- Upon completion of servicing orrepairs to the unit, ask the service technician toperform safety checks to ensure proper operatingcondition.10.Power Sources- Operate the unit only from the typeof power source indicated on the label. If unsure ofthe type of power supply to use, contact your dealeror local power company.•For units intended to operate from battery power,refer to the operating instructions.•For units intended to operate with External PowerSupplies, use only the recommended approvedpower supplies.•For units intended to operate with a limited powersource, this power source must comply withEN60950. Substitutions may damage the unit orcause fire or shock.•For units intended to operate at 24V AC, normalinput voltage is 24 V AC. V oltage applied to theunit's power input should not exceed 30V AC. User-supplied wiring, from the 24V AC supply to unit,must be in compliance with electrical codes (Class2 power levels). Do not ground the 24V AC supplyat the terminals or at the unit's power supplyterminals.11.Coax Grounding- If an outside cable system isconnected to the unit, ensure that the cable system is grounded. U.S.A. models only - Section 810 of theNational Electrical Code, ANSI/NFPA No.70,provides information regarding proper grounding ofthe mount and supporting structure, grounding of the coax to a discharge unit, size of groundingconductors, location of discharge unit, connection togrounding electrodes, and requirements for thegrounding electrode.12.Grounding or Polarization- This unit may beequipped with a polarized alternating current lineplug (a plug with one blade wider than the other).This safety feature allows the plug to fit into thepower outlet in only one way. If unable to insert theplug fully into the outlet, try reversing the plug. If the plug still fails to fit, contact an electrician to arrangereplacement of the obsolete outlet. Do not defeat the safety purpose of the polarized plug.Alternately, this unit may be equipped with a3-wire grounding plug (a plug with a third pin, forgrounding). This safety feature allows the plug to fitinto a grounding power outlet only. If unable to insert the plug into the outlet, contact an electrician toarrange replacement of the obsolete outlet. Do notdefeat the safety purpose of the grounding plug.13.Lightning- For added protection during a lightningstorm, or when this unit is left unattended andunused for long periods of time, unplug the unit from the wall outlet and disconnect the cable system. This will prevent damage to the unit due to lightning andpower line surges.Table of ContentsImportant Safeguards . . . . . . . . . . . . . . . . . . . . . . . . . . . . . . . . . . . . . . . . . . . . . . . . . . . . . . . . . . . . . . . . . .2 Safety Precautions . . . . . . . . . . . . . . . . . . . . . . . . . . . . . . . . . . . . . . . . . . . . . . . . . . . . . . . . . . . . . . . . . . . .3 FCC Information . . . . . . . . . . . . . . . . . . . . . . . . . . . . . . . . . . . . . . . . . . . . . . . . . . . . . . . . . . . . . . . . . . . . .4 1UNPACKING . . . . . . . . . . . . . . . . . . . . . . . . . . . . . . . . . . . . . . . . . . . . . . . . . . . . . . . . . . . . . . . . . .7 2SERVICE . . . . . . . . . . . . . . . . . . . . . . . . . . . . . . . . . . . . . . . . . . . . . . . . . . . . . . . . . . . . . . . . . . . . .7 3DESCRIPTION . . . . . . . . . . . . . . . . . . . . . . . . . . . . . . . . . . . . . . . . . . . . . . . . . . . . . . . . . . . . . . . .7 4POWER SPECIFICATIONS . . . . . . . . . . . . . . . . . . . . . . . . . . . . . . . . . . . . . . . . . . . . . . . . . . . . . .8 5INSTALLATION . . . . . . . . . . . . . . . . . . . . . . . . . . . . . . . . . . . . . . . . . . . . . . . . . . . . . . . . . . . . . . .9 5.1General . . . . . . . . . . . . . . . . . . . . . . . . . . . . . . . . . . . . . . . . . . . . . . . . . . . . . . . . . . . . . . . . . . . . . . .9 5.2Camera Address Offset Feature . . . . . . . . . . . . . . . . . . . . . . . . . . . . . . . . . . . . . . . . . . . . . . . . . . . . .9 6OPERATION . . . . . . . . . . . . . . . . . . . . . . . . . . . . . . . . . . . . . . . . . . . . . . . . . . . . . . . . . . . . . . . . .10 7CONFIGURTATION EXAMPLE . . . . . . . . . . . . . . . . . . . . . . . . . . . . . . . . . . . . . . . . . . . . . . . . .11 8PINOUTS . . . . . . . . . . . . . . . . . . . . . . . . . . . . . . . . . . . . . . . . . . . . . . . . . . . . . . . . . . . . . . . . . . . .13 9TROUBLESHOOTING . . . . . . . . . . . . . . . . . . . . . . . . . . . . . . . . . . . . . . . . . . . . . . . . . . . . . . . . .13T wo 2-meter (6 ft) data cables, for interface to Allegiant main CPU bays, are supplied with the 2-channel versions; four cables are supplied with the 4-channel versions. These units can provide data to any device capable of accepting biphase control code, including the following:•Allegiant Satellite systems•AutoDome Series cameras•Conventional Allegiant Receiver/Driver Series •Allegiant LTC 8770 Relay Follower SeriesControl code wiring to the remote devices can be connected to the outputs of the code mergers using either star or daisy chain wiring configurations. Each output is capable of driving up to eight (8) remote devices using a daisy chain wiring configuration. Multiple units may be cascaded to obtain additional biphase code outputs.The Code Merger units also provide an address offset functionality. This feature is convenient when it is necessary to convert camera address numbers, encoded within the biphase data, to a higher value. Offset increments of 16, 32, or 48 can be enabled via an internal dip switch selection.4POWER SPECIFICATIONS Model No.Rated Voltage Power1Voltage RangeL TC 8569/60120 VAC, 50/60 Hz108 to 13212 W L TC 8570/60120 VAC, 50/60 Hz108 to 13212 W L TC 8569/50220-240 VAC, 198 to 26412 W50/60 HzL TC 8570/50220-240 VAC, 198 to 26412 W50/60 HzL TC 8571/60120 VAC, 50/60 Hz108 to 13212 W L TC 8572/60120 VAC, 50/60 Hz108 to 13212 W L TC 8571/50220-240 VAC, 198 to 26412 W50/60 HzL TC 8572/50220-240 VAC, 198 to 26412 W50/60 Hz1Nominal power at rated voltage.5INSTALLATION5.1GeneralCode Merger units are supplied in an indoor rated enclosure designed to fit a standard EIA 19" rack. Install the unit in the rack using appropriate mounting hardware (not supplied).Input connections to a Code Merger are made to any of its 9-pin D-type connectors. The pinouts of the supplied 2-meter (6 feet) data cables can be connected directly to the control code output connector of an Allegiant Series Matrix Switcher system. Remember to tighten all connector attachment screws at each connection point.If the control code sources are beyond the length of the cable, or are not Allegiant systems, the data cables must be adapted as necessary, for connection to the control device. If desired, a user-supplied 9-pin D-type connector may be used for interfacing to the Code Mergers. Pinouts for the 9-pin connectors are described within this manual.Connect shielded twisted pair cable (Belden 8760 or equivalent) between the camera site receiver/driver locations, and any of the 32/64 outputs provided on the rear panel of the Code Merger unit. The same data is generated from all outputs, thus it is irrelevant which one is used.Eight (8) pairs of removable screw terminal blocks are provided, each having four (4) connection groups per block. T ypically, a single camera site receiver/driver or AutoDome is connected to each output, but the biphase output of these units is rated to handle up to eight (8) devices, when connected in a daisy chain configuration, to a maximum of 1.5 km (5000 ft).In a daisy chain connection, the cable is looped through each AutoDome camera or receiver/driver along the way. Only the last unit in the daisy chain connection must be terminated. The remaining receiver/drivers must have the terminating resistor removed when the looping cable is connected.Select and maintain a wire color convention to avoid confusion at the various camera sites.Example: White to "+", Black to "-", and Shield to "S".Follow the standard installation instructions, provided with the AutoDome Camera or Allegiant Series Receiver/Driver unit, for setting device address and connecting the data cable to the unit.Connect the AC power cord to an appropriate power source. The green Power LED on the code merger unit front panel should illuminate when power is applied.5.2 Camera Address Offset Feature (effective May 2003, Date Code 0314)Code Merger units contain an optional feature that can be used to offset the camera addresses for data being received by code merger inputs 2, 3, and 4. Input 2 can be set to offset addresses by 16, input 3 by an offset of 32, and/or input 4 by an offset of 48. This feature allows code mergers to be used in multi-device systems where some of the control devices do not support offset camera addresses of the data being generated. Refer to sample configuration diagrams for additional details.The cover of the Code Merger must be removed to access the dip switch used for configuration of options. Follow the instructions below to set the camera address offset.Figure 1 - Cover and Rack Brackets Removal•Locate dip switch # S101, as shown in Figure 2.Divar Series© 2004 Bosch Security Systems GmbH3935 890 04213 04-12 | Updated March 15, 2004 | Data subject to change without notice.Bosch Security Systems, Inc.850 Greenfield RoadLancaster, PA 17601 USA T el: 800-326-3270Fax: 1-717-735-6560Bosch Security Systems B.V.P.O. Box 800025600 JB Eindhoven The NetherlandsT ele +31 4027 80000Bosch Security Systems Pte Ltd.38C Jalan Pemimpin Singapore 577180Republic of Singapore T el: 65 (6) 319 3486。
莫卡 UC-8540 系列火车到地面计算机说明书
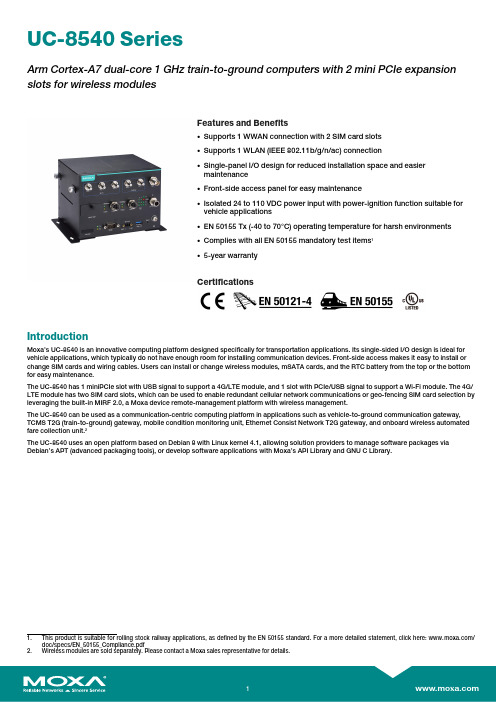
UC-8540SeriesArm Cortex-A7dual-core1GHz train-to-ground computers with2mini PCIe expansion slots for wireless modulesFeatures and Benefits•Supports1WWAN connection with2SIM card slots•Supports1WLAN(IEEE802.11b/g/n/ac)connection•Single-panel I/O design for reduced installation space and easiermaintenance•Front-side access panel for easy maintenance•Isolated24to110VDC power input with power-ignition function suitable forvehicle applications•EN50155Tx(-40to70°C)operating temperature for harsh environments•Complies with all EN50155mandatory test items1•5-year warrantyCertificationsIntroductionMoxa’s UC-8540is an innovative computing platform designed specifically for transportation applications.Its single-sided I/O design is ideal for vehicle applications,which typically do not have enough room for installing communication devices.Front-side access makes it easy to install or change SIM cards and wiring ers can install or change wireless modules,mSATA cards,and the RTC battery from the top or the bottom for easy maintenance.The UC-8540has1miniPCIe slot with USB signal to support a4G/LTE module,and1slot with PCIe/USB signal to support a Wi-Fi module.The4G/ LTE module has two SIM card slots,which can be used to enable redundant cellular network communications or geo-fencing SIM card selection by leveraging the built-in MIRF2.0,a Moxa device remote-management platform with wireless management.The UC-8540can be used as a communication-centric computing platform in applications such as vehicle-to-ground communication gateway, TCMS T2G(train-to-ground)gateway,mobile condition monitoring unit,Ethernet Consist Network T2G gateway,and onboard wireless automated fare collection unit.2The UC-8540uses an open platform based on Debian8with Linux kernel4.1,allowing solution providers to manage software packages via Debian’s APT(advanced packaging tools),or develop software applications with Moxa’s API Library and GNU C Library.1.This product is suitable for rolling stock railway applications,as defined by the EN50155standard.For a more detailed statement,click here:/doc/specs/EN_50155_Compliance.pdf2.Wireless modules are sold separately.Please contact a Moxa sales representative for details.AppearanceSpecificationsComputerCPU Armv7Cortex-A7dual-core1GHzStorage Pre-installed8GB eMMCSupported OS Linux Debian8(Linux kernel v4.1)System Memory Pre-installed1GB DDR3LStorage Slot mSATA slots x1,internal mini-PCIe socketComputer InterfaceExpansion Slots mPCIe slot x2Ethernet Ports Auto-sensing10/100/1000Mbps ports(M12X-coded)x2 Cellular Antenna Connector QMA x2USB3.0USB3.0hosts x1,type-A connectorsWi-Fi Antenna Connector QMA x3Serial Ports RS-232/422/485ports x1,software selectable(DB9male) Number of SIMs2Console Port RS-232(TxD,RxD,GND),4-pin header output(115200,n,8,1) GPS Antenna Connector TNC x1SIM Format MicroInput/Output InterfaceButtons Reset buttonLED IndicatorsSystem Power x1System Ready x1Programmable x1LAN2per port(10/100/1000Mbps)Serial2per port(Tx,Rx)Wireless Signal Strength Cellular/Wi-Fi x6Serial SignalsRS-232TxD,RxD,RTS,CTS,DTR,DSR,DCD,GNDRS-422Tx+,Tx-,Rx+,Rx-,GNDRS-485-2w Data+,Data-,GNDRS-485-4w Tx+,Tx-,Rx+,Rx-,GNDGPS InterfaceHeading Accuracy0.3degreesIndustrial Protocols NMEA0183,version4.0(V2.3or V4.1configurable),UBX,RTCM Receiver Types72-channel u-blox M8engineTime Pulse0.25Hz to10MHzVelocity Accuracy0.05msPower ParametersInput Current 1.66A@24VDC,0.36A@110VDCInput Voltage24to110VDCPower Connector M12A-coded4-pin male connectorPower Consumption40W(max.)Physical CharacteristicsProtection UC-8540-T-CT-LX:PCB conformal coatingDimensions(with ears)190x120x125mm(7.46x4.72x4.92in)Dimensions(without ears)160x120x120mm(6.30x4.72x4.72in)Housing MetalInstallation Wall mountingIP Rating IP40Weight Product only:1,600g(3.53lb) Environmental LimitsAmbient Relative Humidity5to95%(non-condensing)Operating Temperature Standard Models:-25to55°C(-13to131°F)Wide Temp.Models:-40to70°C(-40to158°F) Storage Temperature(package included)-40to85°C(-40to185°F)Standards and CertificationsEMC EN55032/35EMI CISPR32,FCC Part15B Class AEMS IEC61000-4-2ESD:Contact:6kV;Air:8kVIEC61000-4-3RS:80MHz to1GHz:20V/mIEC61000-4-4EFT:Power:2kV;Signal:2kVIEC61000-4-5Surge:Power:2kV;Signal:2kVIEC61000-4-6CS:10VIEC61000-4-8PFMFRailway EN50121-4,EN50155Railway Fire Protection EN45545-2Safety EN62368-1,IEC62368-1Shock IEC60068-2-27,IEC61373,EN50155 Vibration IEC60068-2-64,IEC61373,EN50155 DeclarationGreen Product RoHS,CRoHS,WEEEWarrantyWarranty Period5yearsDetails See /warrantyPackage ContentsDevice1x UC-8540Series computer Documentation1x quick installation guide1x warranty cardCable1x4-pin header to DB9console cableDimensionsOrdering InformationModel Name CPU Antenna Connector Type Operating Temp.Conformal Coating UC-8540-LX Armv7Cortex-A7dual-core1GHz QMA-25to55°C–UC-8540-T-LX Armv7Cortex-A7dual-core1GHz QMA-40to70°C–UC-8540-T-CT-LX Armv7Cortex-A7dual-core1GHz QMA-40to70°C✓Accessories(sold separately)Wi-Fi Wireless ModulesUC-8500-WLAN33-Q-AC3transmitter3receiver Wi-Fi card module,3QMA connectors with cablesUC-8500-WLAN33-Q-AC-TELEC2transmitter2receiver Wi-Fi card module with TELEC certification,2QMA connectors with cables Cellular Wireless ModulesUC-8500-4GCat6-Q-NAMEU LTE Cat.6module for North America and Europe,2QMA connectors with cables,-40to60°Coperating temperatureUC-8500-4GCat6-Q-APAC LTE Cat.6module for North America and Europe,2QMA connectors with cables,-40to60°Coperating temperatureCablesCBL-F9DPF1x4-BK-100Console cable with4-pin connector,1mPower AdaptersPWR-24250-DT-S1Power adapter,90to264VAC,24VDC,2.5A DC loadPower CordsPWC-C13AU-3B-183Power cord with Australian(AU)plug,1.83mPWC-C13CN-3B-183Power cord with three-prong China(CN)plug,1.83mPWC-C13EU-3B-183Power cord with Continental Europe(EU)plug,1.83mPWC-C13UK-3B-183Power cord with United Kingdom(UK)plug,1.83mPWC-C13JP-3B-183Power cord with Japan(JP)plug,7A/125V,1.83mPWC-C13US-3B-183Power cord with United States(US)plug,1.83m©Moxa Inc.All rights reserved.Updated Jul27,2021.This document and any portion thereof may not be reproduced or used in any manner whatsoever without the express written permission of Moxa Inc.Product specifications subject to change without notice.Visit our website for the most up-to-date product information.。
LX8580-00CDD资料
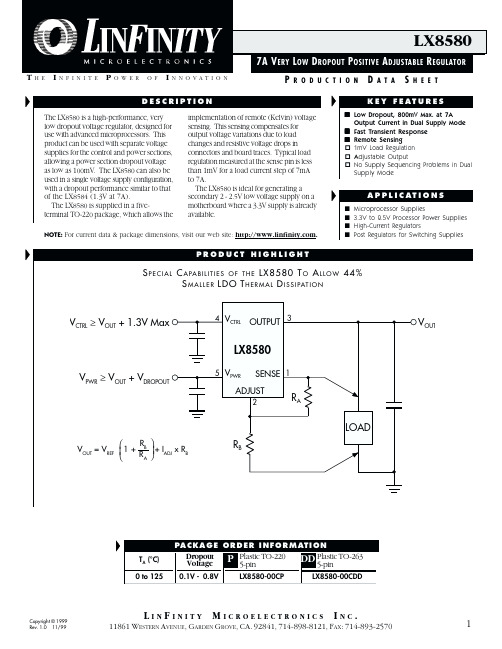
K E Y F E AT U R E S
I Low Dropout, 800mV Max. at 7A Output Current in Dual Supply Mode I Fast Transient Response I Remote Sensing ! 1mV Load Regulation ! Adjustable Output ! No Supply Sequencing Problems in Dual Suppl ERY LOW D ROPOUT P OSITIVE A DJUSTABLE R EGULATOR
T
H E
I
N F I N I T E
P
O W E R
O F
I
N N O VA T I O N
P
R O D U C T I O N
D
A T A
TAB IS OUTPUT
5 4 3 2 1
V PWR VCTRL OUTPUT ADJUST SENSE
DD PACKAGE (Top View)
Junction Temperature Calculation: TJ = TA + (PD x θJA). The θJA numbers are guidelines for the thermal performance of the device/pc-board system. All of the above assume no ambient airflow.
NOTE: For current data & package dimensions, visit our web site: .
PRODUCT HIGHLIGHT
S P E C I A L C A PA B I L I T I E S O F T H E LX8580 T O A L L O W 44% S M A L L E R LDO T H E R M A L D I S S I PAT I O N
- 1、下载文档前请自行甄别文档内容的完整性,平台不提供额外的编辑、内容补充、找答案等附加服务。
- 2、"仅部分预览"的文档,不可在线预览部分如存在完整性等问题,可反馈申请退款(可完整预览的文档不适用该条件!)。
- 3、如文档侵犯您的权益,请联系客服反馈,我们会尽快为您处理(人工客服工作时间:9:00-18:30)。
s
s
s
s
s s s
s s
s
s
s
s
L8560 Low-Power SLIC with Ringing
Data Sheet April 2000
Table of Contents
Contents Page Contents Page
Features .................................................................... 1 Description ................................................................. 1 Pin Information ........................................................... 6 Functional Description ................................................ 9 Absolute Maximum Ratings ..................................... 10 Recommended Operating Conditions ...................... 11 Electrical Characteristics .......................................... 11 Ring Trip Requirements ......................................... 16 Test Configurations .................................................. 17 Applications ............................................................. 19 Characteristic Curves............................................. 19 dc Applications ...................................................... 21 Battery Feed...................................................... 21 Overhead Voltage ............................................ 22 Adjusting Overhead Voltage ............................. 23 Adjusting dc Feed Resistance........................... 23 Adjusting Overhead Voltage and dc Feed Resistance Simultaneously.............................. 24 Loop Range....................................................... 24 Off-Hook Detection ........................................... 24 Ring Ground Detection...................................... 25 Longitudinal Balance.............................................. 25 Power Derating ..................................................... 25 Battery Switch ....................................................... 26 VCC/VEE Supplies ................................................... 27 Power Ringing ....................................................... 27 Ringing SLIC Balanced Ring Signal Generation ....................................................... 27 POTS for ISDN Terminal Adapters ................... 27
Data Sheet April 2000
L8560 Low-Power SLIC with Ringing
Features
s s
Description
The L8560 full-feature, low-power subscriber line interface circuit (SLIC) is optimized for low power consumption while providing an extensive set of features. This part is ideal for ISDN terminal adapter applications and short-loop, power-sensitive applications such as pair gain and cable telephony. This part is also designed for PBX, DLC, or CO applications. The SLIC includes an auxiliary battery input and a battery switch. In short-loop applications, SLICs can be used in high battery to present a high on-hook voltage, and then switched to low battery to reduce off-hook power. To help minimize the required auxiliary battery voltage, the dc feed resistance and overhead voltage are set at 55 Ω and 6.7 V, respectively. This allows an undistorted on-hook transmission of a 3.14 dBm signal into a 900 Ω loop impedance. The device offers the reverse battery function. Using the reverse battery, the device can provide a balanced power ring signal to tip and ring. In this mode of operation, the battery switch is used to apply a high-voltage battery during ringing and a lower-voltage battery during the talk and idle states. Also included in the L8560 is a dc current-limit switch, which increases the dc current limit during power ringing. In addition, dc overhead voltage is reduced during the ring state. With the battery and current-limit switches, and overhead reduction, the L8560 can provide sufficient power to ring a true North American 5 REN load of 1386 Ω + 40 µF. The device offers ring trip and loop closure supervision with 0.3 V and 2 mA hysteresis, respectively. It also includes the ground start state and ring ground detection. A summing node for meter pulse injection to 2.2 Vrms is also included. The 44-pin PLCC version also has a spare uncommitted op amp, which may be used for ac gain setting or meter pulse filtering.
Full-feature set for central office applications Also ideal for ISDN terminal adapters, pair gain, and cable telephony applications Auxiliary input for second battery, and internal switch to enable its use to save power in short telephone loops 5 V only operation or optional ±5 V operation for reduced power consumption Low active power (85 mW typical) and scan power (61 mW typical) with 5 V only operation Low active power (68 mW typical with auxiliary battery) and scan power (45 mW typical) with ±5 V operation Quiet tip/ring polarity reversal Per-line ringing available for short loops Reduced overhead and increased current limit during ring mode for lower-battery operation or increased ring loop length Supports meter pulse injection Distortion-free full duplex from 0 mA dc loop current on-hook transmission Convenient operating states: — Forward powerup — Polarity reversal powerup — Forward sleep — Ground start — Disconnect Adjustable supervision functions: — Off-hook detector with longitudinal rejection — Ground key detector with longitudinal rejection — Ring trip detector Independent, adjustable dc and ac parameters: — dc feed resistance (44-pin PLCC version) — Loop current limit — Termination impedance Thermal protection