钻头参考分析
普通螺纹钻孔选用底孔钻头参考表

粗牙 5 47 47.2
正常情况应尽量选用钻底孔尺寸中的钻头,在出现烂牙,丝攻容易断时才选用最大底孔尺寸的钻头。
粗牙普通螺纹规格用字母“M”及“公称直径”表示,例如:M24表示公称直径为24mm的粗牙普通螺纹。
22 细牙 1 21 21.2 细牙 4 43.8 44
细牙 1.5 20.5 20.7 粗牙 5 42.7 42.9
细牙 2 19.9 20.1 52 细牙 1.5 50.5 50.7
粗牙 2.5 19.5 19.7 细牙 2 49.9 50.1
细牙 3 48.9 49.1
细牙 1.5 14.5 14.7 细牙 4 37.8 38
粗牙 2 14 14.2 粗牙 4.5 37.3 37.5
18 细牙 1 17 17.2 45 细牙 1.5 43 细牙 2 42.9 43.1
细牙 2 15.9 16.1 细牙 3 41.9 42.1
细牙普通螺纹用“M”及“直径X螺距”表示,M24X1.5表示公称直径为24mm,螺距为1.5mm的细牙普通螺纹。
左旋螺纹在规格后加“LH”表示,例如:M24-LH表示公称直径为24mm的左旋粗牙普通螺纹。
细牙 1 7 7.2 33 细牙 1.5 31.5 31.7
粗牙 1.25 6.7 6.9 细牙 2 30.9 31.1
10 细牙 0.75 9.2 9.4 细牙 3 29.9 30.1
细牙 1 9 9.2 粗牙 3.5 29.2 29.4
细牙 1.25 8.7 8.9 36 细牙 1.5 34.5 34.7
粗牙 0.7 3.3 粗牙 3 24 24.2
5 细牙 0.5 4.5 30 细牙 1 29 29.2
PCD及PDC钻头在石油钻井中的应用
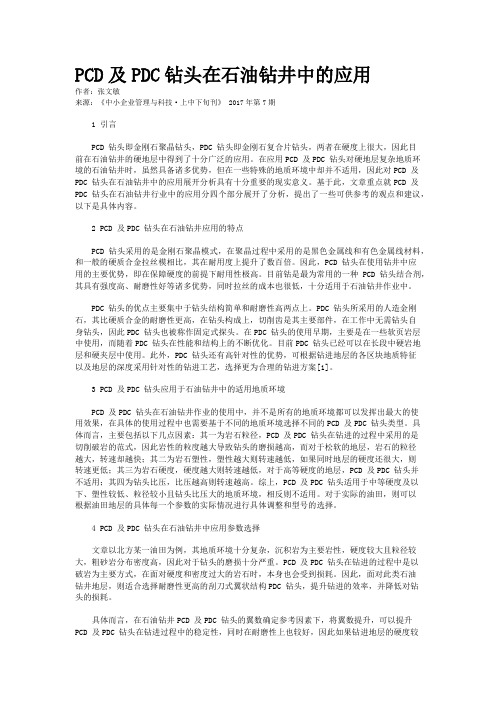
PCD及PDC钻头在石油钻井中的应用作者:张文敏来源:《中小企业管理与科技·上中下旬刊》 2017年第7期1 引言PCD 钻头即金刚石聚晶钻头,PDC 钻头即金刚石复合片钻头,两者在硬度上很大,因此目前在石油钻井的硬地层中得到了十分广泛的应用。
在应用PCD 及PDC 钻头对硬地层复杂地质环境的石油钻井时,虽然具备诸多优势,但在一些特殊的地质环境中却并不适用,因此对PCD 及PDC 钻头在石油钻井中的应用展开分析具有十分重要的现实意义。
基于此,文章重点就PCD 及PDC 钻头在石油钻井行业中的应用分四个部分展开了分析,提出了一些可供参考的观点和建议,以下是具体内容。
2 PCD 及PDC 钻头在石油钻井应用的特点PCD 钻头采用的是金刚石聚晶模式,在聚晶过程中采用的是黑色金属线和有色金属线材料,和一般的硬质合金拉丝模相比,其在耐用度上提升了数百倍。
因此,PCD 钻头在使用钻井中应用的主要优势,即在保障硬度的前提下耐用性极高。
目前钴是最为常用的一种PCD 钻头结合剂,其具有强度高、耐磨性好等诸多优势,同时拉丝的成本也很低,十分适用于石油钻井作业中。
PDC 钻头的优点主要集中于钻头结构简单和耐磨性高两点上。
PDC 钻头所采用的人造金刚石,其比硬质合金的耐磨性更高,在钻头构成上,切削齿是其主要部件,在工作中无需钻头自身钻头,因此PDC 钻头也被称作固定式探头。
在PDC 钻头的使用早期,主要是在一些软页岩层中使用,而随着PDC 钻头在性能和结构上的不断优化。
目前PDC 钻头已经可以在长段中硬岩地层和硬夹层中使用。
此外,PDC 钻头还有高针对性的优势,可根据钻进地层的各区块地质特征以及地层的深度采用针对性的钻进工艺,选择更为合理的钻进方案[1]。
3 PCD 及PDC 钻头应用于石油钻井中的适用地质环境PCD 及PDC 钻头在石油钻井作业的使用中,并不是所有的地质环境都可以发挥出最大的使用效果,在具体的使用过程中也需要基于不同的地质环境选择不同的PCD 及PDC 钻头类型。
PDC钻头钻井泥包原因及控制对策

PDC钻头钻井泥包原因及控制对策摘要:为了解决PDC钻肉钻井过程中产生泥包的问题,保障钻井作业的顺利进行,本文首先对PDC钻头钻井泥包产生的原因进行了分析,从作业流程到钻头材料,逐一进行了探讨,并提出了相应的控制措施。
关键词:PDC钻头;钻井泥包;控制措施引言:近年来,我国对能源的需求越来越高,页岩油气等非常规油气资源的开发陆续被提上日程,PDC钻头经过长时间的发展,现在已经成为钻井行业提速增效的重要工具,而因为开采环境的原因,经常会出现钻头泥包,大大降低了开采效率,所以对PDC钻头钻井泥包的产生原因及控制处理显得十分重要。
一、PDC钻头钻井泥包原因分析(一)钻井液性能原因在开展钻井作业过程中,钻头是其中的重要组成部分,还有一种物质也是十分重要的,那就是钻井液,它可以在岩层和钻头之间起到润滑的作用,还可以将多余的废屑带出地面,因为钻井液的类型不同,其中含有的成分也不同,润滑性及密度差异较大,密度较大的钻井液失水性很严重,各种杂质会很容易粘附在钻井壁上,形成泥包,随着钻井作业进行,就会依附到钻头上形成钻头泥包,润滑性过低也会导致大量泥岩颗粒吸附到钻头上,这是引发钻头钻井泥包的主要原因。
(二)钻井工程技术问题钻井作业过程的技术问题也不容小觑,为了提高工作效率,钻头的转速会越来越快,过快的钻头转速虽然加快了作业进程,但是大量碎屑无法及时排出,排出量跟不上作业量,钻头压力是影响钻头速度的重要因素,最佳条件下,钻速和钻压是成正比的,但是由于地质因素,有的岩层过软,而钻压过大、没有匀速送钻等操作会造成钻速过快或过慢,都会使钻头与地层接触过多而产生钻头泥包。
操作不当也会导致钻井液吸附废料能力下降,大量的碎屑会滞留在井壁处,形成泥堆,久而久之就会形成泥包,当钻头触及比较松软的土层时,泥包受到挤压,就会沾到井壁上去。
还有在下钻作业时,没有下入套管,钻头刮蹭到井壁上的泥包,也会形成钻头泥包。
(三)钻头类型及尺寸不合理在开展钻井作业时,也需要慎重选择钻头类型及尺寸,不同钻头的种类其结构是不同的,首先PDC钻头的结构会影响水力对其清洗的效果,比如散步式布齿和浅锥轮廓的钻头,水力冲洗的效果不明显,切削齿侧倾角较小的钻头,不易于碎屑的排出,钻头水眼的位置如果与喷射角度对不上,会在井底处形成钻井液涡流,使得钻头的刀片和切削齿得不到清洗,碎屑堆积就会产生泥包现象,钻头喷嘴太小,排量不够,废屑没有及时排出也会造成堆积。
钻具扭矩、重量计算参考标准

95.2-107.9 120.6
142.9-171.4 190.5-222.2 241.3-342.9 374.6-444.5 508-660.4
上扣扭矩
KN.m 2.4-3.7 4.2-6.9 7.1-11.5 17-26.4 50.3-57.5 65.5-86.1
空气中重 量kn 0 0 0 0 0 0 0
长度m
空气中重 加重钻杆 量kn 外/内径
长度m
1746.3 506.427 127/76 208.49
0
89/52.4
0
0
0
0
0
0
0
40 14 18 29.6
空气中重 量kn
145.943 0 0 0 0 0 0 0 0
228/72 203/72 178/72 178/57.2 165/72 165/57.2 159/72 159/57 127/57.2 120/51 89/38.1
牙轮钻头 上扣扭矩
外径
KN.m
95.2-107.9 120.6
142.9-171.4 190.5-222.2 241.3-342.9 374.6-444.5 508-660.4
4.1-4.7 6.1-7.5 9.5-12.2 16.3-21.7 38-43.4 46.1-54.2 54.2-81.3
0
197
0
172
16.2384 165
0
120
0
95
0
89
0
长度m 0
0 8.97
空气中重 量kn 0 0 0
10.4949 0 0 0 0
0 0
224
65
210
常用的锥柄麻花钻规格型号参考
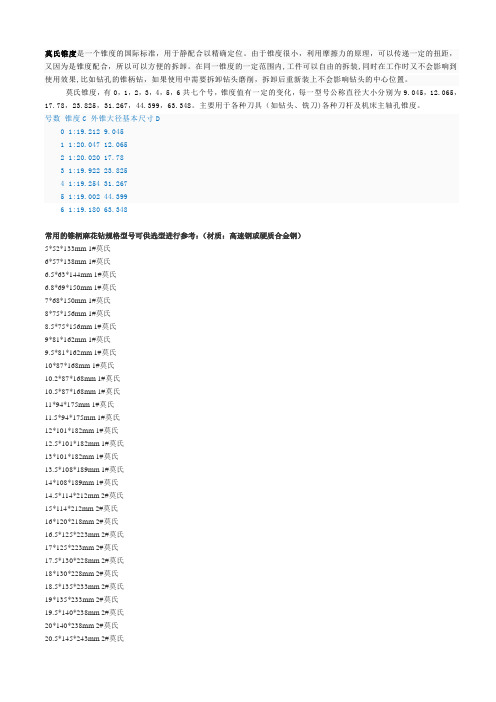
莫氏锥度是一个锥度的国际标准,用于静配合以精确定位。
由于锥度很小,利用摩擦力的原理,可以传递一定的扭距,又因为是锥度配合,所以可以方便的拆卸。
在同一锥度的一定范围内,工件可以自由的拆装,同时在工作时又不会影响到使用效果,比如钻孔的锥柄钻,如果使用中需要拆卸钻头磨削,拆卸后重新装上不会影响钻头的中心位置。
莫氏锥度,有0,1,2,3,4,5,6共七个号,锥度值有一定的变化,每一型号公称直径大小分别为9.045,12.065,17.78,23.825,31.267,44.399,63.348。
主要用于各种刀具(如钻头、铣刀)各种刀杆及机床主轴孔锥度。
号数锥度C 外锥大径基本尺寸D0 1:19.212 9.0451 1:20.047 12.0652 1:20.020 17.783 1:19.922 23.8254 1:19.254 31.2675 1:19.002 44.3996 1:19.180 63.348常用的锥柄麻花钻规格型号可供选型进行参考:(材质:高速钢或硬质合金钢)5*52*133mm 1#莫氏6*57*138mm 1#莫氏6.5*63*144mm 1#莫氏6.8*69*150mm 1#莫氏7*68*150mm 1#莫氏8*75*156mm 1#莫氏8.5*75*156mm 1#莫氏9*81*162mm 1#莫氏9.5*81*162mm 1#莫氏10*87*168mm 1#莫氏10.2*87*168mm 1#莫氏10.5*87*168mm 1#莫氏11*94*175mm 1#莫氏11.5*94*175mm 1#莫氏12*101*182mm 1#莫氏12.5*101*182mm 1#莫氏13*101*182mm 1#莫氏13.5*108*189mm 1#莫氏14*108*189mm 1#莫氏14.5*114*212mm 2#莫氏15*114*212mm 2#莫氏16*120*218mm 2#莫氏16.5*125*223mm 2#莫氏17*125*223mm 2#莫氏17.5*130*228mm 2#莫氏18*130*228mm 2#莫氏18.5*135*233mm 2#莫氏19*135*233mm 2#莫氏19.5*140*238mm 2#莫氏20*140*238mm 2#莫氏20.5*145*243mm 2#莫氏21*145*243mm 2#莫氏21.5*150*248mm 2#莫氏22*150*248mm 2#莫氏22.5*150*248mm 2#莫氏23*150*248mm 2#莫氏23.5*150*248mm 3#莫氏24*160*281mm 3#莫氏24.5*160*281mm 3#莫氏25*160*281mm 3#莫氏25.5*165*286mm 3#莫氏26*165*286mm 3#莫氏26.5*165*286mm 3#莫氏27*170*291mm 3#莫氏27.5*170*291mm 3#莫氏28*170*291mm 3#莫氏28.5*175*296mm 3#莫氏29*175*296mm 3#莫氏29.5*175*296mm 3#莫氏30*175*296mm 3#莫氏31*180*301mm 3#莫氏32*185*334mm 4#莫氏33*185*334mm 4#莫氏34*190*339mm 4#莫氏35*190*339mm 4#莫氏36*195*344mm 4#莫氏38*200*349mm 4#莫氏39*200*349mm 4#莫氏40*200*349mm 4#莫氏42*205*354mm 4#莫氏45*210*359mm 4#莫氏50*220*369mm 4#莫氏。
金刚石钻头参考资料

由于热压烧结一般没有保护气氛,胎体 在烧结过程中容易氧化,影响胎体的致密化 及烧结强度。因此,在胎体材料中通常要加 入某些活泼金属元素,使其在烧结过程中起 到脱氧作用,例如锰和钛等。这样,在烧结 过程中,残存于胎体孔隙之中未及排除的氧 就会优先与这些活泼金属反应,生成氧化物, 从而促进其他粉末的烧结。大家知道,铜及 其合金容易浸润各种金属及其合金或化合物, 同样也容易浸润在烧结过程中所形成的活泼 金属的氧化物,活泼金属的氧化物对于胎体 的整体性能不仅无害,而且这些细小的氧化 物颗粒还可在胎体中起到弥散强化的作用。 其化学反应式为:
事实上胎体中的其他粉末由于已经存放了某些时间以及环境的影响其表面一点也不被氧化和在表面上一点吸附气体也没有是不可能的所添加的活泼金属除了有一部分与空隙中的氧发生反应外还有一部分将与粉末表面的这些氧化物或所吸附的气体发生反应其反应这些置换反应均为放热反应对于表面活化了的粘结金属以及中间相的烧结无疑是具有重要作用的
第三节 孕镶钻头
第三节 孕镶钻头
孕镶钻头是将金刚石与胎体粉末拌 合在一起所制成的钻头(图6-6),胎体将 金刚石全部包镶在里面,在钻头工作时, 金刚石随胎体的磨损以接力的形式不断 出露、工作、脱落、再出露。这种钻头 是为弥补大颗粒天然金刚石稀缺和昂贵 的不足而出现的。实践证明,孕镶金刚 石钻头具有优异的钻进性能和耐用性能。
.mm
• 石墨的线膨胀系数: 石 5.4 106 / C
• 钢体的线膨胀系数: 钢 15106 / C
中频炉
前已述及,对于孕镶钻头,其金刚石将随着
工作层胎体的磨损而逐渐出露,形成切削刃,胎 体工作面表层上切削刃的数量和出刃高度与金刚 石的浓度、粒度、品级以及胎体的耐磨性、对金 刚石的粘结性能密切相关。由于孕镶于胎体中的 金刚石是随机而又相对均匀地分布着,每粒金刚 石都经过初磨→初露→出刃工作→碎裂或脱落的 全过程。整个钻头胎体中的金刚石是以接力的形 式而进行工作的,如图6-7所示。与表镶钻头相比, 孕镶钻头对胎体性能有更复杂的要求。
电钻质量测评报告模板

电钻质量测评报告模板1. 引言本报告旨在对电钻的质量进行全面评估,以便消费者在购买时可以做出明智的选择。
我们通过对市面上多种电钻的实地测试和性能分析,对其质量进行了综合评估,并对每个要素进行了详细的说明。
2. 测评标准为了确保评估的准确性和可靠性,我们制定了以下测评标准:1. 功能性:包括功率、速度调节、转速控制、钻头更换方便程度等。
2. 质量感:包括外观设计、材质质量、使用过程中的手感等。
3. 安全性:包括启动开关的位置和设计、正反转开关的便捷性、防溅水功能等。
4. 耐用性:包括使用寿命、电钻头的质量等。
3. 测试过程在测试过程中,我们选取了市面上热销的5款电钻进行了实地测试和性能分析。
我们结合实际操作的需求和使用体验,测试了以下要素:1. 功率:通过切削钢材的速度和钻孔深度来评估电钻的功率。
2. 速度调节:通过不同速度下的切削效果和操控感受来评估电钻的速度调节功能。
3. 转速控制:通过调节不同转速下的切削效果和操作体验来评估电钻的转速控制功能。
4. 钻头更换方便程度:评估电钻更换钻头的便捷性和准确性。
5. 外观设计:评估电钻整体外观的美观程度和人机工程学设计的质量感受。
6. 材质质量:评估电钻外壳和内部构件的材质质量和制作工艺。
7. 使用过程中的手感:评估使用电钻时手感的舒适程度和操控性。
8. 启动开关的位置和设计:评估电钻启动开关的位置是否合理,设计是否符合使用者的习惯。
9. 正反转开关的便捷性:评估电钻正反转开关的设计和操控的便捷性。
10. 防溅水功能:评估电钻是否具备防溅水功能,以确保使用过程中的安全性。
11. 使用寿命:评估电钻的使用寿命和耐用性。
12. 电钻头的质量:评估电钻头的质量和切削效果。
4. 测评结果在我们的实地测试中,我们发现以下电钻具备较高的质量水平:1. 电钻A:具备强劲的功率,速度调节和转速控制功能良好,更换钻头方便,外观设计美观且质量感强,手感舒适,开关设计合理,具备防溅水功能,使用寿命长且电钻头质量优良。
钻头使用分析报告模板

钻头使用分析报告模板1. 简介钻头是一种用于钻孔的工具,广泛应用于建筑、矿产开采、石油钻探等领域。
本报告旨在对钻头的使用情况进行分析,以提供对钻头使用效果的评估和优化建议。
2. 数据收集为了进行钻头使用情况的分析,我们采集了以下数据:1. 钻孔直径:记录每个钻孔使用的钻头直径,单位为毫米。
2. 钻孔深度:记录每个钻孔的深度,单位为米。
3. 钻头类型:记录钻孔时使用的钻头类型,如钻石钻头、硬质合金钻头等。
4. 溢流情况:记录每个钻孔过程中的溢流情况,以描述钻孔是否顺利进行。
5. 换头次数:记录每个钻孔过程中需要更换钻头的次数。
以上数据是通过现场观察和工作日志记录获得的。
3. 数据分析3.1 钻头直径分析通过对钻孔直径数据的分析,我们可以了解钻头直径对钻孔效果的影响。
以下是我们的分析结果:钻头直径(mm)平均钻孔深度(m)100 5.2150 6.1200 7.3250 8.8300 9.6从上表可以看出,钻头直径与平均钻孔深度呈正相关关系,即钻头直径越大,平均钻孔深度越大。
这说明在需要较深钻孔的情况下,选择较大直径的钻头更为合适。
3.2 钻头类型分析通过对钻头类型数据的分析,我们可以了解不同类型钻头适用的钻孔情况。
以下是我们的分析结果:钻头类型平均钻孔深度(m)钻石钻头6.3硬质合金钻头7.9钢质钻头5.6水泥钻头4.2从上表可以看出,不同类型的钻头在钻孔深度上存在差异。
根据应用场景的不同,选择合适的钻头类型可以提高钻孔效果。
3.3 溢流情况分析通过对溢流情况数据的分析,我们可以了解溢流对钻孔效果的影响。
以下是我们的分析结果:溢流情况钻孔数量-无溢流68轻微溢流26中等溢流12严重溢流4从上表可以看出,大多数钻孔没有溢流情况,说明钻孔过程较为顺利。
溢流情况的出现可能意味着钻孔过程中出现了异常情况,需要进一步分析原因并采取措施进行改进。
3.4 换头次数分析通过对换头次数数据的分析,我们可以了解钻头的耐用性和替换频率情况。
BTA钻头受力分析

BTA钻头受力分析作者:师毓华来源:《科学与财富》2018年第30期摘要:BTA深孔钻削是金属切削中一种较为复杂的加工方式。
本文对首先对钻削过程中钻削力的来源进行了阐述,进而对BTA钻头的在加工过程中的受力进行了简化,从而获得了BTA深孔钻头的受力分析,为后续BTA钻头的设计与优化提供一定的参考。
关键词:BTA钻头;钻削力;深孔加工0.引言:BTA深孔钻削是深孔加工中常用的一种加工方法,由于其加工效率高产品质量好,目前广泛的应用于各种加工领域当中。
由于BTA深孔钻削属于内排屑自导向加工模式,所以钻头的受力对钻头在加工过程中的稳定性与自导性有着十分重要的影响。
1.钻削力的来源钻削过程是由刀具通过旋转加轴向进给,在待加工工件上加工出所需要的深孔,由于材料具有一定的韧性和硬度,材料在被加工过程中发生一系列的弹塑性变形,对钻头产生阻力,在切屑与工件分离的过程中切屑沿着前刀面流出,和前刀面接触并产生摩擦阻力。
随着刀具向前移动,工件已加工表面会有一定弹性恢复,继而与后刀面进行接触,然后产生摩擦力。
由此,钻削力的来源主要由以下三个方面组成[1]:(1)钻削过程中,被加工材料发生弹性变形所产生的阻力。
(2)钻削过程中,被加工材料发生塑性变形所产生的阻力。
(3)钻削过程中,切屑流出时对刀具前刀面产生的摩擦力和刀具向前移动时工件过渡表面和已加工表面对刀具后刀面挤压所产生摩擦力。
2.错齿BTA钻头钻削力分析BTA深孔钻削的过程中,除了刀具切削刃与工件接触以外,还有导向块与工件接触,致使加工过程中刀具的的受力分为三个部分,分别为切削刃所受的切削力、导向块所受的正压力和导向块与工件之间的摩擦力,这样一来使得刀具的受力相当复杂。
在一般的切削加工中,例如在车削加工中,只存在着工件、刀具、床身之间的正常力系,所以只需将车刀装在三向测力仪上,就可以测量出车刀所受的三向力。
而在深孔钻削的过程中,由于存在着导向块与工件之间的正压力和摩擦力,使工件与刀具切削刃和导向块之间构成封闭力系,所以就不能直接测量出切削刃所受的三向分力,只能测出刀具所受的轴向力与扭矩。
钻头和丝锥匹配标准

钻头和丝锥匹配标准钻头和丝锥是两种常用的切削工具,用于加工金属材料。
钻头主要用于钻孔,丝锥主要用于加工内螺纹。
钻头和丝锥的匹配标准涉及到钻头的选择、丝锥的选择以及加工参数等方面。
以下是钻头和丝锥匹配的相关参考内容。
一、钻头的选择1. 切削材料的选择:钻头的切削效果和寿命与切削材料的选择密切相关。
常见的钻头材料有高速钢、硬质合金、颗粒增强陶瓷等。
对于不同的材料,需要选择适合的钻头材料。
2. 钻头形状的选择:常见的钻头形状有直线钻头、锥形钻头、中心钻头、阴阳钻头等。
选择合适的钻头形状可以提高加工效率和质量。
3. 钻头直径的选择:钻头直径的选择应根据加工要求和工件材料来确定。
一般来说,选择稍大一点的钻头直径可以提高加工效率,选择稍小一点的钻头直径可以提高加工质量。
二、丝锥的选择1. 材料的选择:丝锥的材料要具有足够的硬度和耐磨性,以确保加工质量和寿命。
常见的丝锥材料有高速钢、硬质合金等。
2. 规格的选择:丝锥的规格包括螺纹标准、螺纹尺寸等。
选择合适的规格可以确保加工的内螺纹质量和尺寸精度。
3. 使用方式的选择:不同的丝锥有不同的使用方式,包括手动丝锥、机械丝锥等。
选择合适的使用方式可以提高加工效率和准确性。
三、加工参数的选择1. 切削速度:切削速度对于钻头和丝锥的切削效果和寿命有重要影响。
通常,在加工过程中,应根据材料的硬度和加工要求选择适当的切削速度。
一般来说,切削速度过大可能导致钻头或丝锥过早磨损,切削速度过小可能导致加工效率低下。
2. 进给量:进给量对于加工质量和效率有重要影响。
选择适当的进给量可以确保刀具正常切削,提高加工效率。
3. 冷却润滑:在钻孔和切削内螺纹的过程中,冷却润滑是非常重要的。
通过适当的冷却润滑可以降低工具的温度,减少切削力,延长钻头和丝锥的使用寿命。
以上是钻头和丝锥匹配的相关参考内容。
在实际应用中,钻头和丝锥的选择和匹配应根据具体的加工要求、工件材料和加工设备等因素综合考虑,以提高加工效率和质量。
钻头径参考表

公制粗螺纹公制细螺纹
螺纹下孔钻头径参考表
之材质、硬度、形状、尺寸等之影响,多少会有所变动,因此于
参考上表之同时,变请增减若干
美制粗螺纹英制螺纹
注:本表建议的钻头径,以市面上出售的标准钻头选择之使用钻头钻孔用,由于使用时加工条件及被削材质配合度而影响孔的尺寸和精密度,有很大差别,请检查孔径是否在规格内,不适当时依实际情况,请适当变更钻头径。
注:单位:M/M表示
螺纹咬合率计算公式
牙纹公制外径=
2.5钻咀外径= 2.35 标准牙山高度:公制牙.英美联合牙:0.541266P
牙距(公制牙)=0.45
惠氏牙(旧英制牙) :0.5565P P=牙距饱牙率(公制牙)=30.79200738
管牙 :0.6403P
底径=牙型外径-0.2*牙距-0.00403*牙距*饱牙率+0.0127*RH精度
牙纹公制外径
2.5
牙孔底径 2.4牙距0.45
RH精度7
饱牙率54.5354
螺纹下孔钻头径参考表
钻头径。
牙轮钻机破岩作用机理及受力分析

牙轮钻机破岩作用机理及受力分析内蒙古包头市014080摘要:牙轮钻机合理的工作制度取决于被射孔岩石的物理力学特性和射孔参数的选择。
大量实际统计数据表明,钻具的损坏、磨损和过早报废与钻具质量和操作人员有关。
各矿山都将钻具列为“大宗消耗件”,除了价格昂贵外,还会造成废孔,效率低下,成本上升。
钻具主要由钻杆、扶正器和牙轮钻头组成。
每一次过早损坏都会改变其他物品的载荷和作用,增加钻井设备的振动和载荷,导致过早损坏。
因此,研究矿用牙轮钻头的力学性能非常重要。
与传统的弹塑性强度理论和解析方法相比,基于有限元方法的仿真分析和研究是矿用牙轮钻头研究领域的重要发展趋势之一。
关键词:牙轮钻机;破岩机理;有限元;受力;牙轮钻头是牙轮钻机工作时进行破碎岩石的工具,它的性能优劣将直接影响钻孔质量、钻孔速度和钻孔成本。
牙轮钻头在孔底的运动是非常复杂的,特别是牙轮钻头与岩石的相互作用机理尚。
矿用牙轮钻机是露天矿山开采的主要穿孔设备之一。
广泛用于冶金、煤炭、化工、建材等工业部门的大中型露天矿山钻凿炮孔。
牙轮钻机穿孔原理,主要是通过其回转、加压机构使钻具回转,并给钻头施加轴向压力,由这种动压和静压产生的应力,使岩石破碎(剪碎和压碎),同时用压缩空气将岩渣排出,形成炮孔。
通过对矿用牙轮钻头牙爪进行瞬态动力学研究,以新的钻头运动学和动力学模型为基础对矿用牙轮钻头牙爪进行有限元力学数值模拟。
一、矿用牙轮钻头结构由于牙轮钻头结构的特殊性及在孔底运动的复杂性,使得人们对它的研究还不是很深入,尤其对移轴牙轮钻头的研究时间比较短,在移轴牙轮啮合图的绘制、运动学的研究方面的文献还很少,而在动力学方面的研究大都基于钻头为刚性体、岩石为弹性体的假设,这并不能够真实合理的反映牙轮钻头与岩石之间的相互作用。
1.牙掌。
牙掌是一个形状复杂的锻造零件。
其主要部位是各部轴承的轴颈、掌背、以及牙掌体上部与钻杆相联接的螺纹部分。
通常爪尖是整个牙掌的薄弱部分,为了减小掌背的磨损,在掌背与孔壁之间有一30~5的夹角,并在爪尖外表面处堆焊一层硬质合金粉,且镶嵌一些平头的硬质合金柱。
钻头资料参考
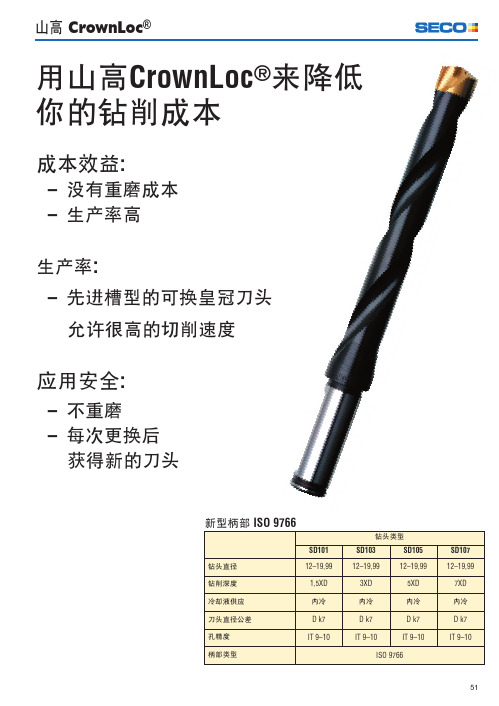
H00-1.5 H00-2.0 H00-2.5
0.9 Nm 2.0 Nm 3.0 Nm
54
山高皇冠钻头
钻深 ~ 3 x D
SD103
ISO 9766 适用柄:Weldon 1835B、ISO 5414、 DIN 60880。 内冷却。
2005 年 3 月供货。
钻头 直径 (mm)
最大钻削 深度 l4
R7: ISO 9766柄
钻头直径
SD100 - 14.00 - P
备件套装
钻头直径 12 – 13.99 14 – 16.99 17 – 19.99
槽型种类
P = 钢件 M = 不锈钢 K = 铸铁
SD101
SD101–SP–5.0 SD101–SP–6.0 SD101–SP–7.0
备件套装标识
SD103
SD105-14.00/14.99-80-16R7
157.4 109.4
48
89.4 13.5
16
20
80
SD105-15.00/15.99-80-16R7
158.3 110.3
48
90.3 14.5
16
20
80
SD105-16.00/16.99-80-16R7
159
111
48
91
15.5
16
20
95
最大钻削 深度 l4
(mm)
型号
20
SD101-12.00/12.49-20-20R5
20
SD101-12.50/12.99-20-20R5
20
SD101-13.00/13.99-20-20R5
25
SD101-14.00/14.99-25-20R5
钻削与钻头8学习.pptx

• 群钻的优点: • 横刃缩短,圆弧刃、内刃上前角平均增大了
15度,使进给力下降了35%-50%,转矩 下降了10%-30%,进给两毕普通麻花钻提 高了约3倍,钻孔效率大大提高。 • 钻头的寿命可以提高2-3倍; • 钻头的定心作用提高,钻孔精度提高,形位 误差与加工表面粗糙度减小; • 选用不同的钻型加工不同的材料均可改善钻 孔的质量,取得满意的效果。 • 圆弧刃切出的过渡表面有凸起的圆环筋,可 以防止钻孔偏斜,减少了孔径的扩大,加强 了定心导向作用,
件,提高钻头寿命,这种适合脆性材料。 三、磨处分屑槽,便于排屑
第17页/共36页
三 修磨前面
目的是为了改变前角的分布,增大或减小前角 或改变刃倾角,用来满足不同的加工要求,
第18页/共36页
常见的修磨方式
一将外缘处磨出倒棱面前面,减小前角,增大 进给力,避免钻孔时引起扎刀;
二是沿切削刃磨出倒棱,增加刃口强度,使用 较硬的才,或是钻削韧性较好的材料以增加 变形,有利于断屑。
第34页/共36页
第35页/共36页
感谢您的观看!
第36页/共36页
• 进给量:一般按下列公式进行估算:
f=(0.01-0.02)d ,合理修磨的钻头可以选
用f=0.03d
第14页/共36页
钻的修磨
缺点:前角从+30°到-30°,横刃长前角-55°, 定心差,轴向力大,刚性差,排屑困难 目的:磨短横刃增大前角,修磨主刃顶角分屑槽
一、修磨横刃
十字形修磨
第15页/共36页
• 枪钻切削部分的一个重要特点是只有单刃切削,钻尖与轴线不在一直线上, 而是偏离了一定距离e,外刃余偏角一般大于内刃余偏角,能够使作用在钻 头上的合力的径向分力始终指向切削部分的导向面,这样就能够保证深孔钻 得到很好的导向作用。
钨钢钻头加工参数

钨钢钻头加工参数钨钢钻头是一种重要的切削工具,它的加工参数直接影响到加工效率和产品质量。
本文将系统地介绍钨钢钻头的加工参数,包括刀具材料、刀具几何参数、刀具工艺参数及工艺优化等方面,旨在为钨钢钻头的加工提供参考和指导。
一、钨钢钻头的刀具材料1.1 钨钢材料介绍钨钢是一种高速钢,具有优良的硬度、热稳定性和切削性能,适合加工高硬度、高强度的工件。
常见的钨钢有W18Cr4V、W6Mo5Cr4V2和W2Mo9Cr4V等系列,它们的成分、热处理工艺和性能略有不同。
1.2 刀具材料选择钨钢钻头的加工参数首先要根据工件材料选择合适的刀具材料。
对于普通碳素钢、合金钢和铸铁等工件,可选择W18Cr4V或W6Mo5Cr4V2。
而对于高硬度材料如不锈钢、钛合金和高温合金等,宜选用W2Mo9Cr4V。
二、钨钢钻头的刀具几何参数2.1 刀具形状钨钢钻头的刀具形状有直柄钻头、锥柄钻头、螺旋钻头等多种类型,根据具体工件形状和加工要求选择合适的刀具形状。
2.2 刀具几何角度包括主切削刃角、前角、侧角、后角等,这些角度的选择要考虑到工件材料、切削条件和加工方式等因素。
三、钨钢钻头的刀具工艺参数3.1 切削速度切削速度是指刀具在单位时间内切削过程中所通过的切削长度。
钨钢钻头的切削速度与刀具材料、工件材料及切削深度密切相关,一般应根据实际情况进行调整。
3.2 进给量进给量是刀具每转动一周时,切削点相对于工件的移动距禀。
进给量的大小会直接影响到加工表面的质量和加工效率,应根据加工情况和工件要求进行合理的确定。
3.3 主轴转速主轴转速是刀具旋转的速度,也称转速。
合理的主轴转速可以保证切削表面的质量,避免刀具损坏和加工效率低下,因此需要根据刀具直径、切削深度和材料硬度等因素进行调整。
四、钨钢钻头的工艺优化4.1 刃磨处理钨钢钻头的刃磨处理对于保证刀具的切削性能和寿命至关重要。
刃磨处理应根据刀具材料和加工要求选择合适的砂轮,确保刀具刃口的光洁度和几何形状的精确度。
- 1、下载文档前请自行甄别文档内容的完整性,平台不提供额外的编辑、内容补充、找答案等附加服务。
- 2、"仅部分预览"的文档,不可在线预览部分如存在完整性等问题,可反馈申请退款(可完整预览的文档不适用该条件!)。
- 3、如文档侵犯您的权益,请联系客服反馈,我们会尽快为您处理(人工客服工作时间:9:00-18:30)。
10
整体硬质合金钻头
新型高性能 整体硬质合金钻头
生产率高
– 最新的镀层与硬质合金棒料技术
每孔成本低
– 每转进给量高 – 切削速度高 – 刀具寿命长
范围
– 7xD – Ø 5.5 – Ø 20
11
整件硬质合金钻头 SD10
钻深 ~ 3 x D 整体式钻头 DIN 6537A - 圆柱柄
外冷却。 镀层:TiAlN。 孔的精度: IT 8-9。 表面粗糙度:Ra 1-2 μ m。
SD103-16.00/16.99-50-20R5
131,5
81,5
50
62
13
15,6
20
60
SD103-17.00/17.99-60-25R5
147,2
91,2
56
71
14
16,6
25
60
SD103-18.00/18.99-60-25R5
148,1
92,1
56
72
15
17,6
25
60
SD103-19.00/19.99-60-25R5
钻削 – 钻头的选择
钻头与切削参数的选择
1 选择钻头的类型 • 钻头的选择由以下因素决定: – 孔径 – 孔深 – �精度与表面粗糙度要求 – 机床 • 根据孔径、孔深与钻削范围,使用下图来选择合适 ������ •如果应用场合的工况好而且主轴的跳动小,使用整 �������������� • 如果表面粗糙度的要求高,可使用整体式、皇冠式 或焊接式钻头。 • 使用前一页上的指导在不同的钻头(整体式、皇冠 式、焊接式与刀片式)中进行选择。 • 使用第79或115页来选择刀片式钻头合适的柄部型 式。皇冠钻与焊接钻只供应Whistle Notch型柄部。 对于整体式钻头,在圆柱柄与Whistle Notch柄之间 进行选择。 1a • 对于刀片式钻头,查阅样本里选择钻头的部分,并 根据刀具参数表获得合适的刀片类型推荐。 • 根据切削参数推荐表获得合适的刀片槽型与材质等 级。 1b • 对于皇冠钻,查阅样本里选择钻头的部分,并根据 刀具参数表获得合适的皇冠刀头类型推荐。 • 根据切削参数推荐表获得合适的皇冠刀头槽型。
山高整体硬质合金钻头
• 针对不同的工件材料优化槽型 – 标准,-M,-T • 倒角钻 M4-M16 • (Ti,Al)N 镀层 – Al的含量高,针对更好的红硬性与耐氧化及化学磨损的能力 • 高精度的孔 – IT8–IT9 • 圆柱柄 DIN6537A 与 Whistle Notch柄 DIN 6537B
40 40
40
SD103-13.00/13.99-40-20R5
119,1
69,1
50
49
11
12,6
20
50
SD103-14.00/14.99-50-20R5
129,9
79,9
50
60
12
13,6
20
50
SD103-15.00/15.99-50-20R5
130,7
80,7
50
61
12
14,6
20
50
尺寸 mm
l3s 48 49
a 10 10
Dcby 11,6 12,1
dm 20 20
SPGX 0502-C1 SPGX 0502-C1 SPGX 0502-C1 SPGX 0502-C1 SPGX 0502-C1 SPGX 0602-C1 SPGX 0602-C1 SPGX 0602-C1 SPGX 0602-C1 SPGX 0602-C1 SPGX 0602-C1 SPGX 0703-C1 SPGX 0703-C1 SPGX 0703-C1 SPGX 0703-C1 SPGX 0703-C1 SPGX 0903-C1 SPGX 0903-C1 SPGX 0903-C1 SPGX 0903-C1 SPGX 0903-C1 SPGX 0903-C1 SPGX 11T3-C1 SPGX 11T3-C1
注意: 不包括在标准范围里的钻头可按照非标或半非标产品生产。
外形尺寸 mm 钻头 直径 Dc (mm) 3,0 3,1 3,175 3,2 3,3 3,4 3,5 3,572 3,6 3,7 3,8 3,9 3,969 4,0 4,1 4,2 4,3 4,366 4,4 4,5 4,6 4,7 4,763 4,8 4,9 5,0 5,1 5,159 5,2 5,5 5,556 5,8 5,953 6,0 6,35 6,5 钻头 直径 Dc (英制) 1/8 9/64 5/32 11/64 3/16 13/64 7/32 15/64 1/4 最大钻削 深度 l4 (mm) 14 14 14 14 14 14 15 15 15 15 17 17 17 17 17 17 18 18 18 18 18 18 20 20 20 20 20 20 20 21 21 21 21 21 23 23
SCGX 050204.. SCGX 050204.. SCGX 050204.. SCGX 050204.. SCGX 050204.. SCGX 050204.. SCGX 050204.. SCGX 050204.. SCGX 060204.. SCGX 060204.. SCGX 060204.. SCGX 060204.. SCGX 070308.. SCGX 070308.. SCGX 070308.. SCGX 070308.. SCGX 070308.. SCGX 09T308.. SCGX 09T308.. SCGX 09T308.. SCGX 09T308.. SCGX 09T308.. SCGX 09T308.. SCGX 09T308..
12,00 12,30 12,50 12,70 12,80 13,00 13,10 13,30 13,50 13,70 13,80 14,00 14,20 14,29 14,50 14,70 14,80 15,00 15,25 15,50 15,70 15,80 15,88 16,00 16,50 16,67 16,70 16,80 17,00 17,46 17,50 17,70 17,80 18,00 18,50 18,70 18,80 19,00 19,05 19,50 19,70 19,80
148,9
92,9
56
73
16
18,6
25
2 选择切削参数 2a • 根据样本中选择钻头的刀具参数表确定最大钻削深 度。 2b • 对于刀片式钻头,还要根据样本里的刀具参数表确 定径向调节极限。 • 使用第175页开始的表格把工件材料按山高材料组别 进行分类。 • 根据所选钻头,查阅切削参数推荐表。 • 根据切须参数推荐表,查询切削速度与进给量的推 荐值。 • 切削参数计算公式参见第174页。
• 钻型选择: P = 钢件,M = 不锈钢,K = 铸铁。 • �体式钻头 DIN 6537B – Whistle Notch柄部。 • 内冷却。 • 皇冠刀头信息见第 49 页。
2a
适用钻 头直径 (mm)
最大 钻深 (mm) l4
1b
皇冠刀头型号 型号 SD103-12.00/12.49-40-20R5 SD103-12.50/12.99-40-20R5 SD100-12.00-X SD100-12.30-X SD100-12.50-X SD100-12.70-X SD100-12.80-X SD100-13.00-X SD100-13.10-X SD100-13.30-X SD100-13.50-X SD100-13.70-X SD100-13.80-X SD100-14.00-X SD100-14.20-X SD100-14.29-X SD100-14.50-X SD100-14.70-X SD100-14.80-X SD100-15.00-X SD100-15.25-X SD100-15.50-X SD100-15.70-X SD100-15.80-X SD100-15.88-X SD100-16.00-X SD100-16.50-X SD100-16.67-X SD100-16.70-X SD100-16.80-X SD100-17.00-X SD100-17.46-X SD100-17.50-X SD100-17.70-X SD100-17.80-X SD100-18.00-X SD100-18.50-X SD100-18.70-X SD100-18.80-X SD100-19.00-X SD100-19.05-X SD100-19.50-X SD100-19.70-X SD100-19.80-X l2 118,3 118,7 l1s 68,3 68,7 lc 50 50
1a
���� 中心刀片 外缘刀片 径向调节 0,3 0,3 0,3 0,2 0,15 0,5 0,35 0,35 0,3 0,3 0,1 0,5 0,5 0,5 0,3 0,2 0,5 0,5 0,5 0,35 0,2 0,1 0,5 0,5
2b
+ 0,15 0,15 0,3 0,3 0,35 0,1 0,15 0,15 0,2 0,35 0,5 0,25 0,4 0,45 0,5 0,5 0,2 0,35 0,45 0,5 0,5 0,5 0,4 0,3
钻头直径, mm
7
钻削 – 钻头的选择
可转位刀片钻头 SD55
钻深 3 x D ISO 9766 柄部
山高 CrownLoc®
钻深 ~ 3 x D SD 103
• 刀片信息见第 116–117页。
2a
尺寸 mm 最大 钻深 钻头直 径 Dc (mm) l4 (mm) 15 15,5 16 16,5 17 17,5 18 18,5 19 20 21 22 23 24 25 26 27 28 29 30 31 32 33 34 45 47 48 50 51 53 54 56 57 60 63 66 69 72 75 78 81 84 87 90 93 96 99 102 型号 SD55-15-45-25R7 SD55-15.5-47-25R7 SD55-16-48-25R7 SD55-16.5-50-25R7 SD55-17-51-25R7 SD55-17.5-53-25R7 SD55-18-54-25R7 SD55-18.5-56-25R7 SD55-19-57-25R7 SD55-20-60-25R7 SD55-21-63-25R7 SD55-22-66-25R7 SD55-23-69-25R7 SD55-24-72-25R7 SD55-25-75-32R7 SD55-26-78-32R7 SD55-27-81-32R7 SD55-28-84-32R7 SD55-29-87-32R7 SD55-30-90-32R7 SD55-31-93-32R7 SD55-32-96-40R7 SD55-33-99-40R7 SD55-34-102-40R7 l2 136 137,5 139 140,5 142 143 145 146,5 148 151 154 157 160 163 170 173 176 179 182 185 188 199 202 205 l1s 80 81,5 83 84,5 86 87,5 89 90,5 92 95 98 101 104 107 110 113 116 119 122 125 128 131 134 137 lc 56 56 56 56 56 56 56 56 56 56 56 56 56 56 60 60 60 60 60 60 60 68 68 68 l3s 49,5 51,2 53 54,7 56,5 58,2 60 61,2 63,5 67 70,5 74 77,5 81 82 85,5 89 92,5 96 99,5 103 102 105,5 109 dm 25 25 25 25 25 25 25 25 25 25 25 25 25 25 32 32 32 32 32 32 32 40 40 40 D5m 45 45 45 45 45 45 45 45 45 45 45 45 45 45 50 50 50 50 50 50 50 59 59 59