离子束沉积
离子束辅助沉积二氧化硅
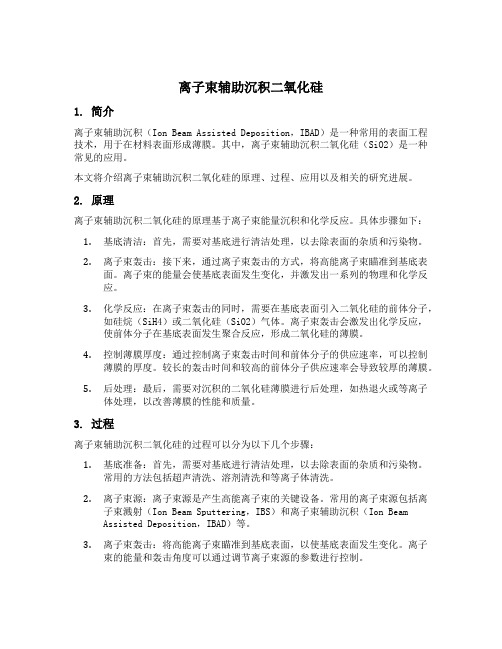
离子束辅助沉积二氧化硅1. 简介离子束辅助沉积(Ion Beam Assisted Deposition,IBAD)是一种常用的表面工程技术,用于在材料表面形成薄膜。
其中,离子束辅助沉积二氧化硅(SiO2)是一种常见的应用。
本文将介绍离子束辅助沉积二氧化硅的原理、过程、应用以及相关的研究进展。
2. 原理离子束辅助沉积二氧化硅的原理基于离子束能量沉积和化学反应。
具体步骤如下:1.基底清洁:首先,需要对基底进行清洁处理,以去除表面的杂质和污染物。
2.离子束轰击:接下来,通过离子束轰击的方式,将高能离子束瞄准到基底表面。
离子束的能量会使基底表面发生变化,并激发出一系列的物理和化学反应。
3.化学反应:在离子束轰击的同时,需要在基底表面引入二氧化硅的前体分子,如硅烷(SiH4)或二氧化硅(SiO2)气体。
离子束轰击会激发出化学反应,使前体分子在基底表面发生聚合反应,形成二氧化硅的薄膜。
4.控制薄膜厚度:通过控制离子束轰击时间和前体分子的供应速率,可以控制薄膜的厚度。
较长的轰击时间和较高的前体分子供应速率会导致较厚的薄膜。
5.后处理:最后,需要对沉积的二氧化硅薄膜进行后处理,如热退火或等离子体处理,以改善薄膜的性能和质量。
3. 过程离子束辅助沉积二氧化硅的过程可以分为以下几个步骤:1.基底准备:首先,需要对基底进行清洁处理,以去除表面的杂质和污染物。
常用的方法包括超声清洗、溶剂清洗和等离子体清洗。
2.离子束源:离子束源是产生高能离子束的关键设备。
常用的离子束源包括离子束溅射(Ion Beam Sputtering,IBS)和离子束辅助沉积(Ion BeamAssisted Deposition,IBAD)等。
3.离子束轰击:将高能离子束瞄准到基底表面,以使基底表面发生变化。
离子束的能量和轰击角度可以通过调节离子束源的参数进行控制。
4.前体分子供应:在离子束轰击的同时,需要在基底表面引入二氧化硅的前体分子,如硅烷(SiH4)或二氧化硅(SiO2)气体。
fib离子束沉积的原理
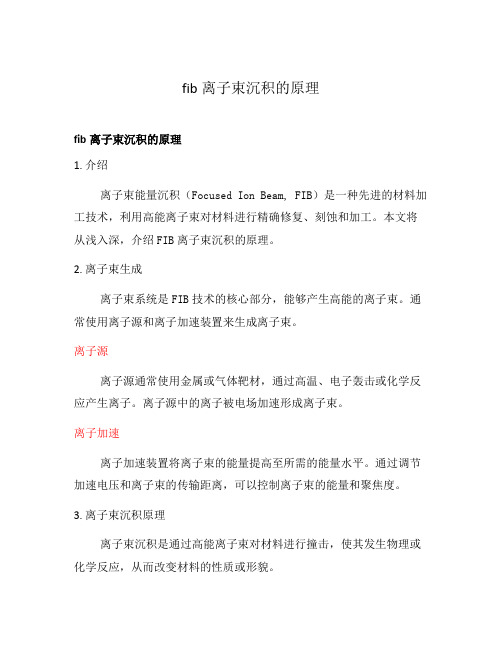
fib离子束沉积的原理fib离子束沉积的原理1. 介绍离子束能量沉积(Focused Ion Beam, FIB)是一种先进的材料加工技术,利用高能离子束对材料进行精确修复、刻蚀和加工。
本文将从浅入深,介绍FIB离子束沉积的原理。
2. 离子束生成离子束系统是FIB技术的核心部分,能够产生高能的离子束。
通常使用离子源和离子加速装置来生成离子束。
离子源离子源通常使用金属或气体靶材,通过高温、电子轰击或化学反应产生离子。
离子源中的离子被电场加速形成离子束。
离子加速离子加速装置将离子束的能量提高至所需的能量水平。
通过调节加速电压和离子束的传输距离,可以控制离子束的能量和聚焦度。
3. 离子束沉积原理离子束沉积是通过高能离子束对材料进行撞击,使其发生物理或化学反应,从而改变材料的性质或形貌。
物理效应离子束撞击材料表面时,会发生以下物理效应: - 离子的动能转化为材料内能,使材料加热,产生热应变和相变现象。
- 离子与材料原子发生碰撞,引起原子的位移、排列和表面重组。
- 离子束的能量沉积在材料中形成能量密集区,导致局部熔化、烧蚀或溶解。
化学效应离子束还可以引起材料的化学反应,例如: - 离子与材料原子发生化学反应,生成新的化合物。
- 离子束激发材料内部原子或分子,使其发生电子激发、离解和电离。
4. 应用领域FIB离子束沉积技术在以下领域有广泛的应用: - 微电子学:用于IC芯片的修复和改造。
- 材料科学:用于微纳加工、表面改性和纳米结构的制备。
- 生命科学:用于细胞操作、组织切片和生物样品制备。
5. 结论FIB离子束沉积技术利用高能离子束的物理和化学效应,对材料进行精确的修复、刻蚀和加工。
它在微电子学、材料科学和生命科学等领域具有广泛的应用前景。
作为资深的创作者,了解和掌握FIB离子束沉积的原理,将能够更好地应用和推动该技术的发展。
6. FIB离子束沉积的优势和挑战优势•高精度:FIB离子束沉积可以实现亚微米级别的加工精度,适用于高精度微纳加工需求。
内齿齿环的传统加工工艺与电铸的比较
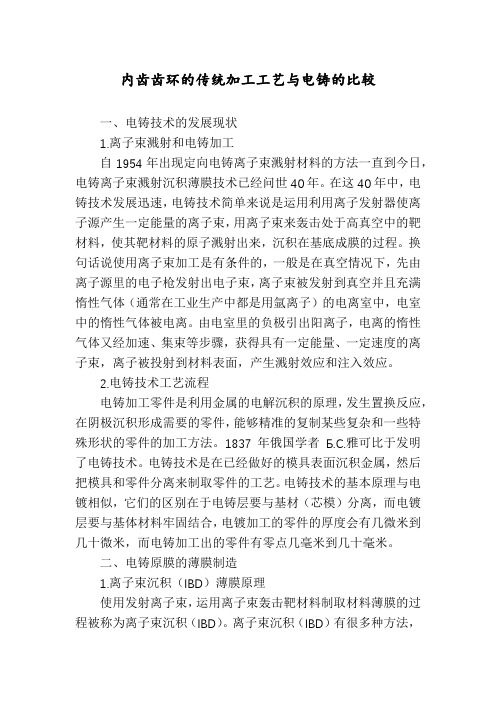
内齿齿环的传统加工工艺与电铸的比较一、电铸技术的发展现状1.离子束溅射和电铸加工自1954年出现定向电铸离子束溅射材料的方法一直到今日,电铸离子束溅射沉积薄膜技术已经问世40年。
在这40年中,电铸技术发展迅速,电铸技术简单来说是运用利用离子发射器使离子源产生一定能量的离子束,用离子束来轰击处于高真空中的靶材料,使其靶材料的原子溅射出来,沉积在基底成膜的过程。
换句话说使用离子束加工是有条件的,一般是在真空情况下,先由离子源里的电子枪发射出电子束,离子束被发射到真空并且充满惰性气体(通常在工业生产中都是用氩离子)的电离室中,电室中的惰性气体被电离。
由电室里的负极引出阳离子,电离的惰性气体又经加速、集束等步骤,获得具有一定能量、一定速度的离子束,离子被投射到材料表面,产生溅射效应和注入效应。
2.电铸技术工艺流程电铸加工零件是利用金属的电解沉积的原理,发生置换反应,在阴极沉积形成需要的零件,能够精准的复制某些复杂和一些特殊形状的零件的加工方法。
1837年俄国学者Б.С.雅可比于发明了电铸技术。
电铸技术是在已经做好的模具表面沉积金属,然后把模具和零件分离来制取零件的工艺。
电铸技术的基本原理与电镀相似,它们的区别在于电铸层要与基材(芯模)分离,而电镀层要与基体材料牢固结合,电镀加工的零件的厚度会有几微米到几十微米,而电铸加工出的零件有零点几毫米到几十毫米。
二、电铸原膜的薄膜制造1.离子束沉积(IBD)薄膜原理使用发射离子束,运用离子束轰击靶材料制取材料薄膜的过程被称为离子束沉积(IBD)。
离子束沉积(IBD)有很多种方法,其基本方法是离子束溅射沉积(IBSD),其他方法皆由此演变而来。
离子束沉积薄膜可用多种气体离子,使氩(Ar)氪(Kr)氦(He)氙(Xe)氖(Ne)等惰性气体离子用作轰击离子。
因为其稳定的化学性质而被使用,惰性气体的离子束发生的溅射现象为物理现象,不会改变沉积材料的化学性质,同过这一性质可以分析溅射离子、原子的化学性质及其物理性质是否被改变,生长薄膜的性质与结构正是这些粒子互相作用的产物。
电化学沉积薄制备技术
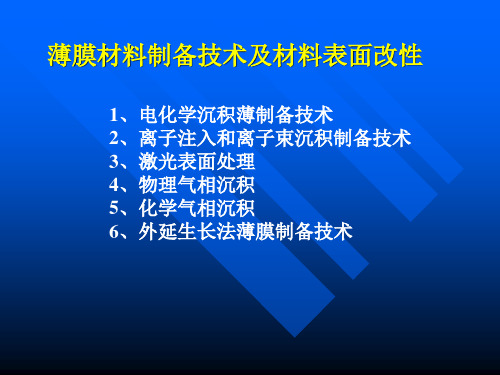
2、离子注入和离子束沉积制备技术
离 子 注 入 ( Ion Implantation ) 和 离 子 束 沉 积 ( Ion Beam Deposition)是表面改性和膜制备的重要手段。
离子注入:在真空中离化气体或固体蒸气源,引出离子束,将其加速到数 Kev或数百Kev后,直接注入到靶室内的基材表面,形成一定 浓度的离子注入层,改变表层的结构和组分,达到改善材料表 面结构和性能的目的。
其主要特点有: • 沉积过程温度低,镀层与基体间不存在残余热 应力,界面结合好 • 可以在各种形状复杂的表面和多孔表面制备均 匀的薄膜 • 镀层的厚度、化学组成、结构及孔隙率能够精 确控制 • 设备简单,投资少
电化学沉积技术可以分为: 阴极电化学沉积 阳极电化学沉积
阴极电化学沉积:薄膜材料在阴极得到。
离子注入技术的 主要应用包括: • 改善金属材料表
面特性 • 制备新的合金膜
材料 • 改善工具的表面
性能
离子束沉积:
离子束沉积有两种工艺方式: 一次离子束沉积和二次离子束沉积
一次离子束沉积:离子束由需要沉积膜的元素组成,并以低的 能量(约100ev)直接沉积到基体上。
二次离子束沉积(或称为离子束溅射沉积):离子束一般为 惰性气体,或反应性气体,以较高的能量(数百至数千ev) 打到靶板上,靶板由要求沉积的材料组成,离子使靶材料溅 射后沉积到基体上形成
至蒸发; • 材料在激光作用后冷却,
应用范围:半导体功能材料、各种金属材料、陶瓷材料和聚合物材料
离子注入的主要物理参数包括: 能量:决定了注入离子在基体中能够达到的深度。 剂量:决定注入层的浓度。 剂量率:单位时间内样品接受的注入剂量。
光学薄膜离子束辅助蒸发沉积技术新进展
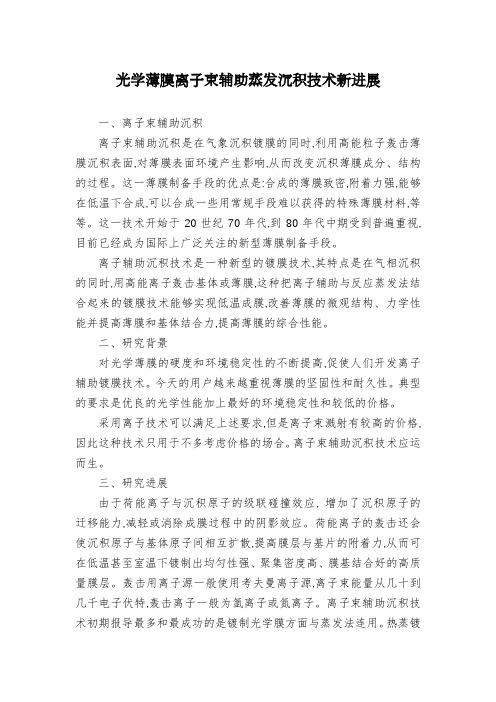
光学薄膜离子束辅助蒸发沉积技术新进展一、离子束辅助沉积离子束辅助沉积是在气象沉积镀膜的同时,利用高能粒子轰击薄膜沉积表面,对薄膜表面环境产生影响,从而改变沉积薄膜成分、结构的过程。
这一薄膜制备手段的优点是:合成的薄膜致密,附着力强,能够在低温下合成,可以合成一些用常规手段难以获得的特殊薄膜材料,等等。
这一技术开始于20世纪70年代,到80年代中期受到普遍重视,目前已经成为国际上广泛关注的新型薄膜制备手段。
离子辅助沉积技术是一种新型的镀膜技术,其特点是在气相沉积的同时,用高能离子轰击基体或薄膜,这种把离子辅助与反应蒸发法结合起来的镀膜技术能够实现低温成膜,改善薄膜的微观结构、力学性能并提高薄膜和基体结合力,提高薄膜的综合性能。
二、研究背景对光学薄膜的硬度和环境稳定性的不断提高,促使人们开发离子辅助镀膜技术。
今天的用户越来越重视薄膜的坚固性和耐久性。
典型的要求是优良的光学性能加上最好的环境稳定性和较低的价格。
采用离子技术可以满足上述要求,但是离子束溅射有较高的价格,因此这种技术只用于不多考虑价格的场合。
离子束辅助沉积技术应运而生。
三、研究进展由于荷能离子与沉积原子的级联碰撞效应, 增加了沉积原子的迁移能力,减轻或消除成膜过程中的阴影效应。
荷能离子的轰击还会使沉积原子与基体原子间相互扩散,提高膜层与基片的附着力,从而可在低温甚至室温下镀制出均匀性强、聚集密度高、膜基结合好的高质量膜层。
轰击用离子源一般使用考夫曼离子源,离子束能量从几十到几千电子伏特,轰击离子一般为氩离子或氮离子。
离子束辅助沉积技术初期报导最多和最成功的是镀制光学膜方面与蒸发法连用。
热蒸镀技术的优点是设备简单,并可容易地镀制多种物质,但利用蒸镀法沉积出的光学膜层常是疏松的柱状结构、抗湿性、耐磨性不能满足许多领域对膜层高可靠和长寿命的要求。
而简单的在热蒸镀中加入离子枪,进行离子束辅助沉积,则可镀制出高质量的光学膜。
在高功率激光薄膜材料中,氧化铅是一种常见的薄膜材料,它具有从紫外到红外较宽的透明区域,同时川花入还具有高的折射率和较高的抗激光损伤阑值。
电化学沉积薄制备技术--11
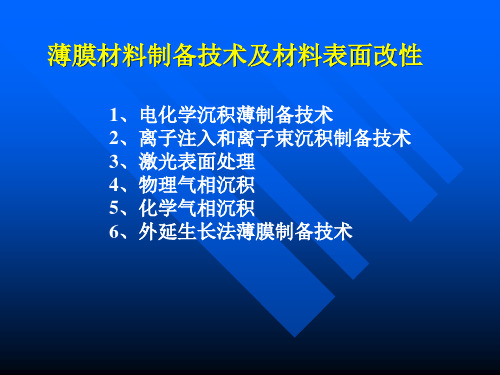
激光表面熔融
利用比相变硬化更高的激光能量密度, 辐照铸铁和高碳钢的表面,使表面层 熔融,通过自身冷却,在表面形成硬 的渗碳体组织。如图示出了以 3KW 的 CO2 激光用集成反射法辐照 FC25 铸铁 的断面硬度分布。表面 0.7mm 是熔融 凝固层,表面硬度 HV1000 以上,约到
2mm 深度是马氏体相变硬化层。再提
其主要工艺过程包括:
(1) 溶液中的还原剂(如H2O,NO3- )及一些有机分子在阴 极被还原为碱基(OH-) (2) 溶液中的金属离子或络合物与阴极上的碱基(OH-)发 生反应生成薄膜材料或薄膜材料的前驱体。 (3) 后续热处理。
阳极电化学沉积:薄膜材料在阳极得到。
其主要工艺过程包括: (1) 溶液中的低价阳离子在阴极表面被氧化为高价阳离子 (2) 高价阳离子与溶液中的碱基(OH-)反应生成各种功能 膜材料或其前驱体。 (3) 后续热处理。
再采用提高吸收率的涂层。这种方式的主要问题是:基体熔化层深,涂
层的稀释度大。 另一类是粉末注入法,即将涂层材料的粉末直接向激光辐照形
成的熔池中喂送,以实现扩散结合的涂覆。
表面合金化
激光表面合金化是用高能激光束作为热源,加热熔化已涂覆合
金元素的基体材料的表面,对其进行合金元素渗入的表面处理方法。
玻璃镀膜工艺

玻璃镀膜工艺
玻璃镀膜工艺是一种将薄膜涂覆在玻璃表面的技术。
这种工艺可以用于改善玻璃的光学性能、机械性能、耐化学性能和电学性能等方面。
目前,玻璃镀膜工艺已广泛应用于太阳能电池板、高精度光学仪器、汽车前挡风玻璃、建筑玻璃、电子显示器等领域。
玻璃镀膜工艺的主要方法包括物理气相沉积、化学气相沉积、离子束沉积和溅射沉积等。
这些方法各有特点,可以根据不同的应用情况选择合适的镀膜工艺。
一般来说,物理气相沉积适用于制备多层膜;化学气相沉积适用于制备单层膜;离子束沉积适用于制备高精度膜;溅射沉积适用于制备大面积膜。
在玻璃镀膜工艺中,薄膜的制备和表征是关键环节。
制备时需要控制沉积速率、沉积温度、沉积时间等参数,以获得所需的薄膜性能。
表征时需要使用各种分析手段,如X射线衍射、扫描电镜、透射电镜、拉曼光谱等,对薄膜的结构、成分、形貌等进行分析和评价。
总的来说,玻璃镀膜工艺是一项技术含量较高的工艺,可以为各种领域的应用提供高品质的玻璃产品。
- 1 -。
离子镀和离子束沉积课件

离子镀和离子束沉积在沉积速率、涂 层质量和应用范围等方面存在差异。 离子镀的沉积速率较高,但涂层质量 相对较差;离子束沉积的涂层质量较 好,但沉积速率较慢。此外,两种技 术在应用范围上也有所不同,离子镀 在工业生产中广泛应用,而离子束沉 积则更多应用于科学研究和高技术领 域。
技术发展趋势
随着科技的不断进步和应用需求的不断提高 ,离子镀和离子束沉积技术也在不断发展。
02
离子镀技术
真空镀膜技术
01
02
03
真空技术原理
真空技术是离子镀和离子 束沉积的基础,涉及抽真 空、气体控制和测量等环 节。
真空获得技术
包括机械泵、扩散泵、油 扩散泵和涡轮分子泵等, 用于获得高真空环境。
真空测量技术
通过测量各种气体压力参 数,如真空度、漏率等, 确保镀膜过程的稳定性和 可控性。
目前,技术发展的趋势主要包括提高涂层质 量、降低成本、开发新材料和拓展应用领域 等方面。例如,采用新型的电源技术和控制 系统可以提高涂层质量和沉积速率,同时降 低能耗和生产成本;开发新型的靶材和气体 源可以扩展技术的应用范围;探索与其他表 面处理技术的结合可以创造出更优异的表面
性能。
未来展望
离子镀和离子束沉积技术作为先进的表面处理技术,在未来仍具有广阔的发展前景和应用潜力。
离子束沉积工作原理
通过高能离子束轰击固体靶材,使靶材表面的原子或分子获得足够的能量而脱 离靶材表面,并沉积在基材表面形成涂层。
应用领域
离子镀应用领域
广泛应用于航空航天、汽车、电子、 光学等领域,用于提高材料表面的硬 度、耐磨性、耐腐蚀性以及附着性等 。
离子束沉积应用领域
主要用于制备高品质的薄膜材料,如 硬质涂层、光学薄膜、磁性薄膜等。 在微电子、光电子、生物医学等领域 有广泛应用。
离子束溅射沉积薄膜技术概述
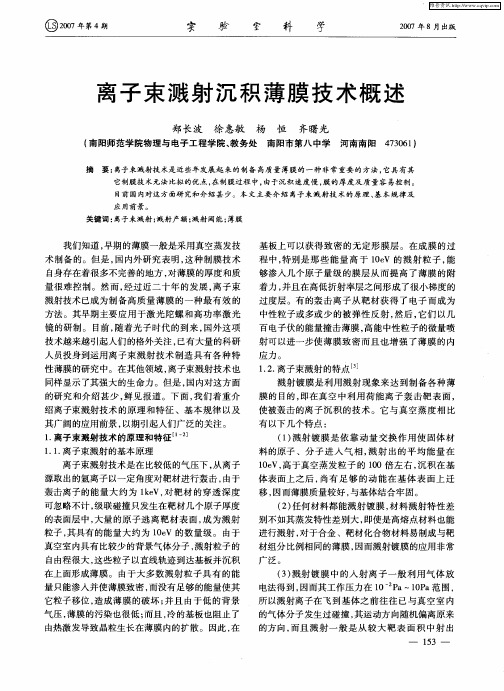
关键词 : 离子束溅射 ; 溅射产额 ; 溅射 阈能 ; 薄膜
我 们知道 , 早期 的薄膜 一般 是采 用真 空蒸 发技 术制 备 的 。但 是 , 内外 研 究 表 明 , 种 制膜 技 术 国 这 自身存 在着很 多不 完善 的地方 , 薄膜 的厚度 和质 对 量 很难 控 制 。然 而 , 经过 近 二 十年 的发展 , 离子 束 溅 射技术 已成 为制 备 高 质 量 薄膜 的一 种最 有 效 的
基 板上 可 以获得 致 密 的无 定形 膜 层 。 在成 膜 的过
程 中, 特别 是 那 些 能量 高 于 le 的 溅 射 粒 子 , OV 能 够 渗入 几个原 子 量 级 的膜 层 从 而提 高 了薄 膜 的 附 着 力 , 且在 高低 折射 率层之 间形 成 了很 小 梯度 的 并 过 度层 。有 的轰 击 离子 从 靶 材 获得 了 电子 而 成 为 中性粒 子或 多或 少 的被 弹性 反 射 , 后 , 然 它们 以几 百 电子伏 的能量撞 击薄 膜 , 能 中性粒 子 的微 量喷 高
摘
要: 离子束溅射技 术是 近些年发 展起 来的制备 高质量 薄膜 的一种非 常重要 的方法 , 它具有 其 它制膜技 术无法比拟的优 点 , 在制膜过程 中, 由于沉积速度慢 , 的厚 度及质量容 易控制 。 膜
目前 国 内对 这 方 面研 究 和介 绍 甚 少 。 本 文 主 要 介 绍 离 子 束 溅 射 技 术 的 原 理 、 本 规 律 及 基 应用前景。
维普资讯
( 0 年 4 @27 第 期 0
实 验 室 科 学
27 8 出 0年 月 版 0
离 子束 溅 射 沉 积 薄 膜 技 术 概 述
郑长波 徐 惠敏 杨 恒 齐曙 光
离子束辅助沉积原理

离子束辅助沉积原理宝子们!今天咱们来唠唠一个超酷的技术——离子束辅助沉积。
这玩意儿听起来是不是就很有科技感呢?咱先说说啥是沉积哈。
想象一下,你在一个超级微观的世界里,有一些小颗粒,它们就像一个个小小的建筑材料,慢慢地堆积在一个表面上,就像盖房子一样,一块砖一块砖地垒起来,这就是沉积啦。
那普通的沉积就有点像慢悠悠地手工堆东西,效率有时候不太高,而且堆出来的东西可能不是那么完美。
这时候,离子束辅助沉积就闪亮登场啦!离子束啊,就像是一群超级有活力的小助手。
这些小助手可是带电的哦,就像一群充满能量的小精灵。
它们是怎么来的呢?其实是通过一些特殊的设备,把原子或者分子变成离子,然后加速,让它们形成一束离子流。
这些离子束冲向要沉积的表面的时候,那可就热闹啦。
就好比一群热情的小工冲向工地一样。
它们和那些要沉积的材料小颗粒会发生各种各样好玩的互动。
比如说,离子束的能量可以把要沉积的材料原子或者分子打得更“听话”。
原本那些原子可能是懒洋洋地,在那里晃悠着准备沉积,离子束一冲过来,就像给它们打了一针兴奋剂,让它们变得更活跃,排列得也更整齐有序了。
而且哦,离子束还像一个严格的监工。
在沉积的过程中,如果有一些原子或者分子没有按照理想的方式堆积,离子束就会把它们“推”到正确的位置。
这就好比盖房子的时候,工人要是把砖头放歪了,监工就会把砖头扶正一样。
这样沉积出来的薄膜或者涂层,质量就特别好。
再说说这个离子束辅助沉积在材料表面改性方面的厉害之处吧。
你想啊,材料的表面就像人的脸一样,要是能给它做个超级棒的“美容”,那这个材料就会变得更厉害。
离子束辅助沉积就可以在材料表面形成一层特殊的涂层。
这层涂层就像是给材料穿上了一件超级防护服。
比如说,这个涂层可以让材料变得更耐磨,就像给材料的表面穿上了一层厚厚的铠甲,怎么磨都不容易坏。
又或者可以让材料变得更耐腐蚀,就像给材料表面打了一把伞,酸雨啊、化学腐蚀啊,都不怕。
还有哦,离子束辅助沉积在光学材料上的应用也超有趣。
离子束沉积法制备金刚石薄膜

离子束沉积法制备金刚石薄膜要说起金刚石薄膜,很多人可能会觉得很遥远,甚至有点科幻。
但事实上,金刚石薄膜的应用早已悄悄进入了我们生活的各个角落,从高端电子器件到硬度超强的刀具,甚至在一些医疗器械上都有它的身影。
说到这,大家可能会想,这东西看起来那么高大上,它是怎么制作出来的呢?这就要提到一个名字:离子束沉积法。
听上去有点复杂,但其实它的原理并不难懂,接下来我们就带大家走进这个神奇的世界,看看金刚石薄膜是如何诞生的。
先说离子束沉积法,它其实就是通过一种特殊的方式,把离子加速到非常高的速度,然后用这些高速飞来的离子撞击到目标表面。
这些离子好像一群“飞奔的牛仔”,在这个过程中,它们不仅能够改变目标表面的原子结构,还能把这些原子“送”到目标材料上,形成新的薄膜。
是不是有点像是飞舞的刀锋,精准又有力?这个过程有点像是玩拼图,但拼的是原子。
嗯,就是这么酷。
不过,说到这里,可能有小伙伴要问了,离子束沉积法为什么这么受欢迎呢?那可是因为金刚石薄膜的特性实在是太强大了。
大家都知道,金刚石硬度超高,是自然界中最硬的物质之一,用来做刀具、切割工具,简直就是一把神器。
可是,金刚石本身不容易加工,体积大了就不好控制,所以这时候金刚石薄膜就派上用场了。
通过离子束沉积法制作的金刚石薄膜,薄薄的一层,却能拥有金刚石的硬度,既保留了它的强度,又能更灵活地应用。
离子束沉积法制备的金刚石薄膜非常均匀、致密,不容易出现裂缝。
就好像一块巧克力蛋糕,外面看着平滑无比,咬一口却发现里面的每一层都很有质感,吃一口就是满满的满足感。
这层金刚石薄膜在很多地方都能派上用场,比如电子器件、热管理系统、甚至航空航天领域。
是的,你没听错,这种薄膜可以在那么严苛的环境下生存,简直是“硬核”中的硬核。
说到这里,也许你会觉得这事儿听起来挺高科技的,实际上也没那么神秘。
金刚石薄膜本身并不是什么不可触及的东西,离子束沉积法也并不是说得高深莫测,它就像是打开了一个魔法盒子,让我们有了更多的可能性。
聚焦离子束诱导沉积_概述及解释说明

聚焦离子束诱导沉积概述及解释说明1. 引言1.1 概述离子束诱导沉积(Ion Beam Induced Deposition,简称IBID)是一种在材料表面上利用高能离子束进行沉积的先进技术。
通过控制离子束的能量、流强和轰击时间等参数,可以实现对材料表面进行局部改变并沉积出所需形状和结构的纳米材料。
该技术广泛应用于微电子器件制备、光学薄膜制备以及生物医学领域等多个领域。
1.2 文章结构本文将着重介绍离子束诱导沉积的原理、材料科学中的应用、技术发展现状与挑战以及未来的发展趋势。
下面将分别在各章节中详细阐述相关内容。
1.3 目的本文旨在全面概述离子束诱导沉积技术,并探讨其在材料科学领域中的应用前景和发展趋势。
通过系统性地介绍离子束诱导沉积技术原理和工艺流程,读者将对该技术有一个清晰全面的了解。
同时,文章还将重点讨论离子束诱导沉积在光学薄膜制备、二维材料生长和生物医学领域中的应用研究进展。
最后,文章将分析离子束诱导沉积技术当前存在的问题与挑战,并展望其未来的发展前景。
以上是“1. 引言”部分内容的详细清晰撰写,希望能对你撰写长文有所帮助。
2. 离子束诱导沉积的原理2.1 离子束诱导沉积的基本概念离子束诱导沉积(Ion Beam Induced Deposition,IBID)是一种利用离子束能量和动量传递来控制材料表面微观结构形成的技术。
该技术通过将高速离子束定向轰击目标材料表面,并在被轰击区域引起化学反应或物理相变,从而在局部区域上产生所需形态和组分的材料。
2.2 离子泵浦技术的应用示例离子泵浦技术是一种常用于真空系统中的开关设备,可实现气体压力的控制和调节。
在离子束诱导沉积过程中,离子泵浦技术被广泛应用于提供必要的低压环境,以便减少气体分子对待生成物质质量、致密度和晶格结构等性能产生不利影响。
2.3 离子束诱导沉积的工艺流程离子束诱导沉积工艺流程主要包括以下步骤:步骤1:设定离子束参数。
对于离子束诱导沉积,需要设定合适的离子种类、能量和通量等参数。
离子注入和薄膜沉积

离子注入和薄膜沉积离子注入和薄膜沉积是两种重要的表面工程技术,它们都能够改变材料表面的物理和化学性质,从而提高材料的性能和功能。
离子注入是一种将离子束注入固体材料中的技术。
离子注入常常被用来提高材料的硬度、耐磨性、化学稳定性等性质。
离子注入的原理是将电荷载体称为离子的高能量束,投射到材料表面或者表面下一定深度的位置。
离子注入时,需要控制离子束的能量、束流密度和注入时间等参数,以达到最佳效果。
离子注入通常需要使用离子源、加速器、注入系统和检测系统等设备。
离子注入主要有两种类型:浅层离子注入和深层离子注入。
浅层离子注入是将离子注入到材料表面下使用小于几十纳米的深度中的表面层。
这种注入能够改善材料表面的性能,并产生新的材料特性和功能,例如渗碳和渗硼处理在表面制备具有高耐磨性和高耐蚀性的工具和零件。
深层离子注入是在材料表面以下的深度中形成未均匀分布的点缺陷,以改善材料的辐射、耐腐蚀性、氢脆裂性等性能。
深层注入会在深层产生有利的物理和化学特性,使材料能够更好地抵抗环境中的攻击。
薄膜沉积技术是在基板表面沉积非常薄的材料层,以改善材料表面的性能。
薄膜沉积技术是一种制备单晶薄膜、多晶薄膜和非晶薄膜的表面工程技术。
薄膜沉积技术通常使用化学气相沉积(CVD)、物理气相沉积(PVD)、离子束沉积(IBD)或电泳沉积等方法。
这些方法具有独特的优缺点,需要根据材料的性质和应用需求选择合适的方法。
例如,CVD可用于沉积非晶薄膜,PVD可用于沉积多晶薄膜,IBD可用于沉积单晶薄膜,而电泳法则可用于沉积均相或弥散的材料。
薄膜沉积能够改善材料的表面性能,例如增加硬度、降低摩擦系数、改善光学特性等。
这些应用非常广泛,如金属离子沉积可以形成具有高导电性能的导电膜,而非晶氮化硅沉积可以制备具有耐热、耐腐蚀性能的电气元件。
总之,离子注入和薄膜沉积是两种表面工程技术,是改善材料表面性能的重要手段。
这些技术为制造高品质的电子元件、导电器、半导体器件、光学器件和涂层等提供了支撑。
热处理中的物理气相沉积热处理技术
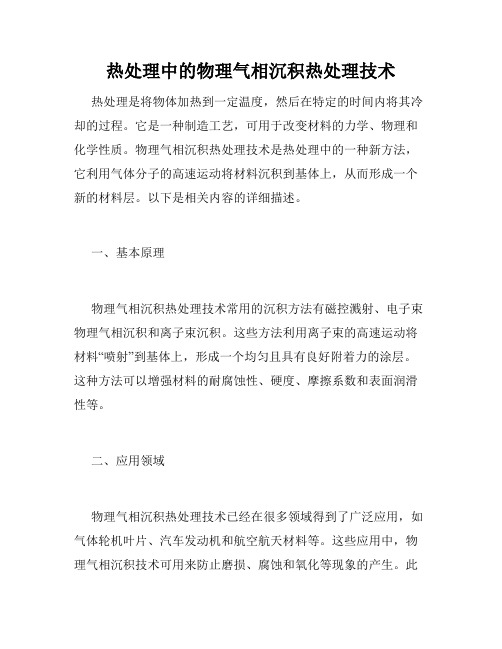
热处理中的物理气相沉积热处理技术热处理是将物体加热到一定温度,然后在特定的时间内将其冷却的过程。
它是一种制造工艺,可用于改变材料的力学、物理和化学性质。
物理气相沉积热处理技术是热处理中的一种新方法,它利用气体分子的高速运动将材料沉积到基体上,从而形成一个新的材料层。
以下是相关内容的详细描述。
一、基本原理物理气相沉积热处理技术常用的沉积方法有磁控溅射、电子束物理气相沉积和离子束沉积。
这些方法利用离子束的高速运动将材料“喷射”到基体上,形成一个均匀且具有良好附着力的涂层。
这种方法可以增强材料的耐腐蚀性、硬度、摩擦系数和表面润滑性等。
二、应用领域物理气相沉积热处理技术已经在很多领域得到了广泛应用,如气体轮机叶片、汽车发动机和航空航天材料等。
这些应用中,物理气相沉积技术可用来防止磨损、腐蚀和氧化等现象的产生。
此外,这种技术还可以用于制备高温橡胶、电子元件和可调谐微波滤波器等。
三、优势和不足物理气相沉积热处理技术具有以下优势:1. 涂层均匀:物理气相沉积技术可以在材料基体的表面形成薄而均匀的涂层。
2. 操作简单:这种技术不需要高温处理,所以需要的设备和成本较低。
3. 节省材料:物理气相沉积技术在制备涂层时只需要少量材料,因此可以节省材料成本。
此外,物理气相沉积热处理技术还有一些不足:1. 不适用于大规模生产:这种方法适用于制备小批量和特殊材料,不适用于大批量生产。
2. 需要严格的条件和控制:物理气相沉积热处理技术需要严格的设备条件和操作控制,否则容易出现涂层不均匀、附着力差和氧化等问题。
四、未来发展趋势物理气相沉积热处理技术的发展具有以下趋势:1. 新型涂层材料:科学家正在研究和开发新型涂层材料,以满足更广泛的应用需求。
2. 纳米技术:纳米材料的制备成为热处理技术的一个重要方向,物理气相沉积技术可以制备各种涂层材料和纳米材料。
3. 自动化技术:随着自动化技术的发展,医疗、汽车、电子和航空等行业的需求也逐渐增长,这将促进物理气相沉积热处理技术的发展。
沉积法制备薄膜
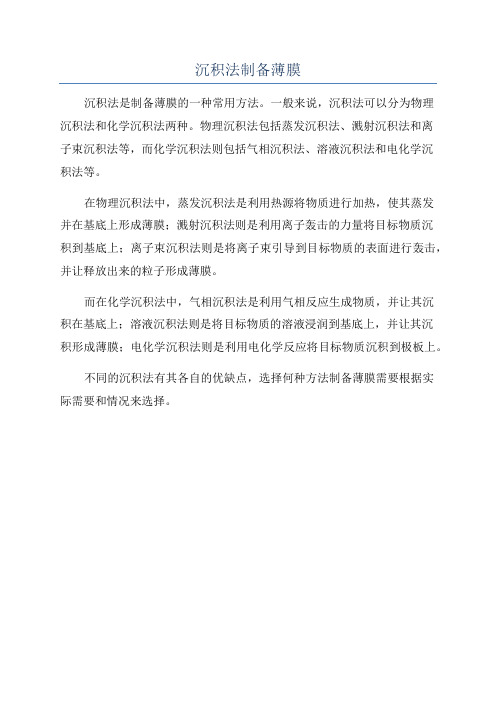
沉积法制备薄膜
沉积法是制备薄膜的一种常用方法。
一般来说,沉积法可以分为物理
沉积法和化学沉积法两种。
物理沉积法包括蒸发沉积法、溅射沉积法和离
子束沉积法等,而化学沉积法则包括气相沉积法、溶液沉积法和电化学沉
积法等。
在物理沉积法中,蒸发沉积法是利用热源将物质进行加热,使其蒸发
并在基底上形成薄膜;溅射沉积法则是利用离子轰击的力量将目标物质沉
积到基底上;离子束沉积法则是将离子束引导到目标物质的表面进行轰击,并让释放出来的粒子形成薄膜。
而在化学沉积法中,气相沉积法是利用气相反应生成物质,并让其沉
积在基底上;溶液沉积法则是将目标物质的溶液浸润到基底上,并让其沉
积形成薄膜;电化学沉积法则是利用电化学反应将目标物质沉积到极板上。
不同的沉积法有其各自的优缺点,选择何种方法制备薄膜需要根据实
际需要和情况来选择。
第7章 离子镀和离子束沉积
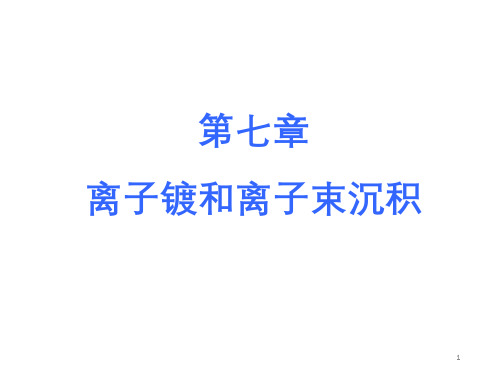
2
离子镀概述
过程:
• 真空度抽至10-4Pa的髙真空后,通入 惰性气体(如Ar),使真空度达到1~101Pa。 • 接通高压电源,在蒸发源与基片之间 建立了一个低压气体的等离子体区。
• 使镀材蒸发,蒸发粒子进入Plasma区, 与其中的正离子和被激活的惰性气体 原子及电子发生碰撞,其中一部分蒸 发粒子被电离成正离子,正离子在负 高压电场加速的作用下,到达并沉积 在基片表面成膜;其中一部分获得了 能量的原子,也沉积成膜。
17
离子束沉积
离化团束沉积
• 膜层致密,附着力 强,结晶性好 • 对基板及薄膜损伤 小,可用于制备半 导体膜和磁性膜等 功能薄膜
• 可大量输运蒸镀原 子,沉积速率高
• 可独立调节各个实 验参数,镀膜过程 及薄膜性能可控
18
离子束沉积
离子束辅助沉积
离子束辅助沉积是指在气相沉积镀膜的同时,用具有一定能量 的离子束进行轰击,以提高薄膜质量。
15
离子束沉积
离子束沉积方法分类: • • • • • 直接引出式 质量分离式 部分离化式(离子镀) 离化团束沉积 离子束辅助沉积 可调参数 • 离子种类 • 离子能量 • 离子电流大小 • 入射角 • 束斑大小 • 离子比例 • 基片温度 • 真空度
16
离子束沉积
直接引出式和质量分离式
从离子源引出离子束后,再进行质量 分离,选择其中的某种离子照射基片
离子轰击在离子镀中的作用
对基片表面的作用(膜层沉积之前)
1)溅射清洗。高能粒子轰击基片表面,引起表面原子射出,产生溅射。 清除吸附气体、溅射掉表面物质、发生化学反应。 2)产生缺陷和位错网。轰击粒子的能量传递给表面的晶格原子。 3)破坏表面结晶结构。稳定的缺陷造成表面晶体结构的破坏变成非晶态 结构。同时,气体的掺入也会破坏表面的结晶结构。 4)气体掺入。低能离子轰击会造成气体掺入表面和淀积膜之中,掺入气 体量可高达百分之几。 5)表面成分变化。由于系统内各成分的溅射率不同,会造成表面成分与 基体成分的不同。
为什么要使用IAD(离子辅助沉积)?

为什么要使用IAD(离子辅助沉积)?发表于八月 23, 2017二月 5, 2020利用:•降低拥有成本•平均维护时间长(MTBM)•更高的投资回报率和吞吐量使用离子辅助沉积(IAD,有时也称为离子束辅助沉积),您可以实现与离子束溅射(IBS,也称为IBD,用于离子束沉积)相似的性能,但总拥有成本较低,回报率更高您的投资。
与仅使用蒸发沉积相比,IAD允许您创建更密集的薄膜,且散布更少,从而可以生产出高质量,无缺陷,应力低且对环境稳定的薄膜。
了解沉积的不同类型诸如电子束和热蒸发之类的蒸发沉积技术是简单且广泛使用的,它以合理的成本覆盖了广泛的波长范围,但薄膜质量较低。
IBS具有出色的薄膜稳定性,耐用性和精确性,但成本较高且产量较低。
IAD提供了坚实的中间基础,具有合理的机械耐用性和精度,与离子束溅射相比,其成本更低,产量更高。
与蒸发不同,IAD不需要加热基材,从而可以选择更多材料。
但是,与IBD相比,它确实会产生更高的散射和损耗。
1个IAD的工作方式IAD是标准电子束技术的一种变体,它添加了指向基板的高能离子束。
该束释放的离子使蒸发的薄膜更致密。
较高密度的涂层可提高抗湿性(更好的环境稳定性),更好的机械耐久性和更低的分散性。
另外,离子束也可以用于预清洁或蚀刻衬底。
使用IAD,您可以实现:•独立控制离子电流密度和离子能量以优化膜性能•使用100%O2或N2反应性气体可长期运行,可确保稳定运行,而不会因工艺漂移而延长运行时间它们是用途IAD非常适合要求高质量和控制的苛刻光学应用。
由于离子辅助沉积工艺不需要像其他薄膜沉积方法那样多的热量,因此可以涂覆塑料材料,例如聚碳酸酯透镜。
准备了解更多?下载我们的信息图,IAD的5大好处。
并且,请留意我们的下一篇文章,该文章将更深入地探讨IAD的优势,并探讨RF与DC源之间的关系-哪个更好?。
- 1、下载文档前请自行甄别文档内容的完整性,平台不提供额外的编辑、内容补充、找答案等附加服务。
- 2、"仅部分预览"的文档,不可在线预览部分如存在完整性等问题,可反馈申请退款(可完整预览的文档不适用该条件!)。
- 3、如文档侵犯您的权益,请联系客服反馈,我们会尽快为您处理(人工客服工作时间:9:00-18:30)。
离子束沉积
离子束沉积技术是一种利用高能量离子束对目标表面进行沉积技术。
这项技术可用于形成薄膜、涂层、晶体等多种形式的材料。
离子束沉积技术可以实现准确、快速和低成本的产品制造。
离子束沉积具有很高的精度和质量可靠性,因此在很多行业得到了广泛应用。
离子束沉积技术的基本原理是将高能量的离子束投射到目标表面上,离子束投射的过程中,离子束会带电离子,电离子带有一定量的能量,电离子中的能量会转化为目标表面的晶体结构,从而形成表面层。
离子束沉积技术可用于直接在目标表面上制造新的结构,可以实现精细的调节和细化知觉,有利于产品精度的提高。
离子束沉积技术有许多优点,其中首先要指出的是精度高、质量可靠、产品性能稳定可靠。
离子束沉积技术可用于微细加工、精细结构的制造、无损测试、复杂三维结构的制造等。
其次,离子束沉积技术所采用的离子投射方式,耗电量少,可以节约大量的能源,也有利于环境的保护。
最后,离子束沉积技术可以避免热情况下产品结构的变形,制造过程中没有大量的有害气体产生,安全性更高。
离子束沉积技术已经在航空航天、电子电器、光电、医疗器械等多个领域得到了广泛应用。
在航空航天领域,离子束沉积技术可用于制造航空航天器的结构件,如导弹外壳、卫星外壳、发动机叶片等,可以大大降低重量和减少摩擦,从而提升航空航天器的性
能。
在电子电器领域,离子束沉积技术可以快速地生产出特殊电子元件,具有高精度、高可靠性以及耐高温和耐冲击等特点,可用于制造汽车、工业控制器、太阳能电池等电子元件。
此外,离子束技术也可用于制造高质量的医疗器械,如胸管、肝管等,可有效改善人类的健康水平。
综上所述,离子束沉积技术在多个行业得到了广泛应用。
离子束沉积技术具有准确、快速和低成本的特性,可以有效改善产品的精度、质量和可靠性。