How to Design Light Pipes(导光柱设计实例精讲-外文资料)
毕业设计论文:高架灯提升装置设计

本科生毕业论文(设计)题目高架灯提升装置设计学院制造与工程学院专业机械设计及其自动化教务处制表二Ο一二年五月二十八日目录摘要............................................................................................................................ 错误!未定义书签。
第1章绪论 (1)1.1背景 (1)1.2国内外现状 (2)1.2.1国内高架灯现状 (2)1.2.2真国外高架灯现状 (3)1.3优缺点 (4)第2章总体方案 (5)2.1设计要求 (5)2.2 设计参数 (5)2.3 具体方案 (6)2.3.1 机械传动方案 (6)2.3.2 灯盘到顶后自锁方案 (7)2.3.3 灯架组装方案 (8)2.3.4 升降装置总方案 (8)2.4本章小结 (9)第3章机械结构设计计算 (10)3.1 计算灯盘重量 (10)3.2 挂钩上轴的计算 (12)3.3选择电动机 (14)3.4运动学及动力学计算 (16)3.4.1总传动比计算 (16)3.4.3.各轴功率计算 (17)3.5.1.初取值 (18)3.5.2.中心距计算 (18)3.5.3.传动基本尺寸 (18)3.5.4.齿面接触疲劳强度验算 (19)3.5.5.齿面弯曲疲劳强度验算 (20)3.5.6.蜗杆轴扰度验算 (20)3.5.7.温度校核计算计算 (20)3.5.8.确定涡轮蜗杆基本尺寸 (20)3.6 圆柱齿轮传动的设计计算 (22)3.6.1. 选择齿轮材料 (22)3.6.2. 初步计算 (22)3.6.3,齿面接触疲劳强度计算 (22)3.6.4,确定传动主要尺寸 (24)3.7轴的初步设计计算 (26)3.7联轴器的选择和轴承 (27)3.7.1.联轴器选择 (27)3.8涡轮蜗杆及齿轮结构尺寸 (27)3.8轴按许用弯曲应力计算 (29)3.8.1.结构设计 (30)3.8轴承寿命计算 (37)3.7选用键并校核 (38)3.8 本章小结 (38)第4章附件设计 (39)4.1挂钩装置几何形状设计 (39)4.3 本章小结 (41)第5章结论与展望 (42)5.1 论文总结 (42)5.1 论文展望 (43)致谢 (44)参考文献 (45)第1章绪论1.1背景随着国家现代化建设的陆续推进,城市生活不断改善。
导光管采光施工工法
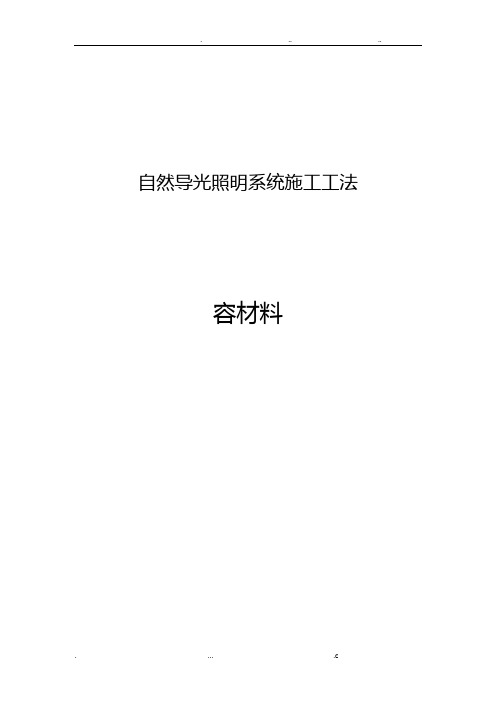
自然导光照明系统施工工法容材料二O一七年三月目录1.前言 (4)2.工法特点 (4)3.适用围 (5)4.工艺原理 (5)5.施工工艺流程及操作要点 (7)6.材料与设备 (19)7.质量控制 (20)8.安全措施 (22)9.环保措施 (23)10.效益分析 (23)11.应用实例 (25)自然导光照明系统施工工法1.前言当前,能源问题已经升级为全球性的重大问题,世界各国都在开发新能源,同时在利用新技术方面也不惜余力。
人工照明在现代照明中仍然占据着举足轻重的分量,全世界的平均照明用电已占总发电量的10%~20%。
经济的快速发展使得我国能源消耗速度日益增长,用电紧问题凸显,而照明用电又占有很大比重,根据统计表明我国照明用电约占全国总用电量的10%~12%。
充分利用天然光资源,采用被动式采光技术无疑是降低照明能耗的重要途径之一。
近年来,导光管作为一种新型高效的自然采光装置正在全国围迅速普及应用。
自然采光就是引用户外的天然光进入室进行照明的过程。
太是取之不尽,用之不竭的天然能源。
但是通过门窗等进入室的仅仅是很小一部分。
为了更好地利用太阳能。
人们研究出许多新技术,光导管系统便是其中之一。
光导管系统引入的是自然光,不需要消耗非可再生资源,而且不会对环境造成污染,能够节约20%~30%的建筑用电,对节能有着重要意义。
地区多云天气较多,尤其是冬季。
通过合理设计,积极采用导光管技术为各类难以直接使用自然光的建筑空间提供照明,对于节约能源、保护环境具有重要意义。
该工法经多个工程应用,大大提高了施工质量和节能效果,取得了显著的经济和社会效益。
2.工法特点2.1、导光管结构简单、重量轻、耐腐蚀、反射率高,材料可回收利用,安装拆卸简便灵活,无需后期维护,降低了人工维护和设备更新成本。
使用寿命长,一般在25年以上。
2.2、采用三点控位技术,运用两点定线、三点控位的原理,解决导光筒垂直度的问题;使用准直仪、全站仪并结合计算机设计、建模,对导光管的安装进行准确定位,充分保证导光管的位置精确,加快了施工进度,提高了施工质量。
光导管照明技术在建筑照明设计中的应用

光导管照明技术在建筑照明设计中的应用摘要:本文首先介绍了光导管照明技术的国内外发展历程及现状,阐述了光导管照明系统的基本结构和类型,结合实际工程案例,重点分析了光导管照明系统的优越性和目前存在的问题,并提出了光导管照明技术在建筑照明设计中的适用范围及其发展趋势。
关键词:自然采光建筑照明光导管节能减排Abstract: this paper first introduced the optical tube lighting technology at home and abroad and the development course and the present situation, this paper expounds the optical tube lighting system the basic structure and types, and combining with actual engineering example, analyzed the optical tube lighting system superiority and the existing problems, and puts forward the optical tube lighting technology in building lighting design of the applicable scope and development trend.Keywords: natural lighting building lighting optical tube energy conservation and emission reduction引言当今节能和保护环境已成为世界各地普遍关注的社会问题,并直接关系到社会的持续发展。
人工照明在现代照明中仍然占据着举足轻重的分量,全世界的平均照明用电已占总发电量的10%~20%,而我国照明用电已占总发电量的10%~12%。
导光柱设计指引之室内照明
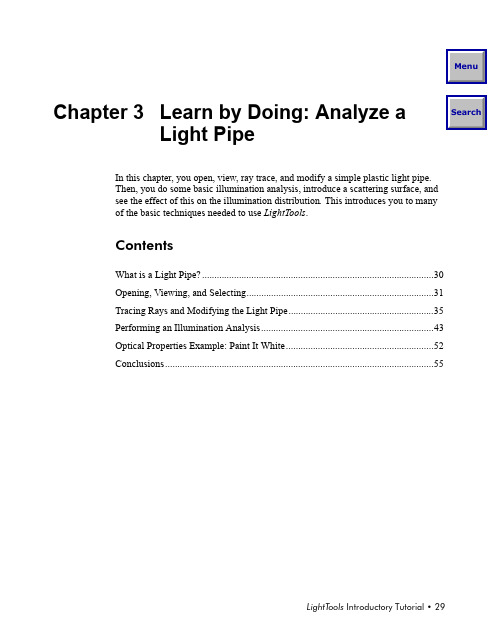
Light PipeIn this chapter, you open, view, ray trace, and modify a simple plastic light pipe.Then, you do some basic illumination analysis, introduce a scattering surface, andsee the effect of this on the illumination distribution. This introduces you to manyof the basic techniques needed to use LightTools.ContentsWhat is a Light Pipe? (30)Opening, Viewing, and Selecting (31)Tracing Rays and Modifying the Light Pipe (35)Performing an Illumination Analysis (43)Optical Properties Example: Paint It White (52)Conclusions (55)C HAPTER3Learn by Doing: Analyze a Light Pipe What is a Light Pipe?to one or more illuminated areas.complex, and LightTools is a great tool for designing and analyzing such systems.You will start with a simple L-shaped plastic light pipe with a single flat surface to illuminate. This is similar to light pipes used to illuminate buttons or indicator lights in various devices.When you are finished, the light pipe will look something like this:In this chapter, you learn how to:•Open an existing LightTools model.•Use 3D viewing selection tools.•Trace a fan of rays and modify the light pipe to redirect the rays to illuminate the target surface.•Use a pre-defined light source (simulating an LED) and a receiver (collection surface) to run a simple Monte Carlo illumination simulation.•Apply an optical property (Lambertian scattering) to a surface and rerun the illumination simulation.Some of these features are briefly explained as they are introduced here, and additional explanation is included in subsequent chapters. The main purpose of this chapter is to get familiar with the interface and with typical tasks and procedures. This is a very simple system, but it allows you to explore some of LightTools basic features.C HAPTER 3Learn by Doing: Analyze a Light Pipe Opening, Viewing, and SelectingThe starting point for this light pipe model is supplied with the sample models in the LightTools installation directory . It is made of plastic (polycarbonate) andconsists of two blocks joined using Boolean operations, with a simple light source, and a rectangular dummy element (that is, an element that has no optical effect) with a receiver for illumination analysis. The source and receiver are on a hidden layer, so you won't see them at first .Opening the Model1.Select File > Open on the menu bar.If you didn’t close your model after you finished setting preferences, aLightTools message is displayed warning that your model hasn’t been saved. Click Yes to close it now and continue.2.On the Open dialog box, browse to the \Tutorial folder of the LightToolsinstallation directory, shown in the following figure.3.Click the file name TD_Lpipe_start.1.lts and click the Open button.Note: Be sure that you have set your preferences as described in Chapter2.C HAPTER 3Learn by Doing: Analyze a Light Pipe LightTools models are saved in files with the file extension .lts (for LightTools System).Viewing the ModelThe model opens, and the 3D Design view is displayed, showing four panes(nominally, top, right, front, and isometric views, but you can change each pane as desired). Note that one of the panes has a red border around it, indicating that this is the active pane for any operations that depend on view-based coordinates. (In LightTools , you can use several different coordinate systems in various types of tasks.)Now that a model is open, the navigation windows contain structured lists, which you will soon use to keep track of the parts of the system you are modeling and the various windows you will open. If you would like to explore the lists, click on plus signs (+) to expand hidden levels, and click on minus signs (-) to collapse a list.1.Make sure the lower right pane is active (has a red border), then click the 1Pane button on the toolbar.The right side view now fills the entire display area, and the 4 Panetoolbar button is available to return to the 4-pane view when desired . Although younow see only a single view of the model, the right mouse button and the toolbar let you quickly change that view as needed.C HAPTER 3Learn by Doing: Analyze a Light Pipe e these view operations to set up a view similar to the following picture. Todo this, you can:–Rotate the View . Place the cursor over the model, hold down the right mouse button, and slowly move the mouse around to spin the 3D Design view.–Zoom . Hold down the Control key and the right mouse button and move the mouse up or down. Move the mouse up to zoom in, or move the mouse down to zoom out.–Pan . Hold down the Shift key and the right mouse button and move the mouse to move the view around (pan up, down, left, right). Note: These view operations do not change any aspect of the model itself; you are simply “walking around” the model to view it from different virtual positions in space. Note that the coordinate axis rotates when you rotate the view. The objects in the model are fixed with respect to this global coordinate system. LightTools provides commands (such as Move ) to change the positionof selected object(s) within the model.C HAPTER3Learn by Doing: Analyze a Light PipeSelecting Objects and SurfacesAs explained in Chapter1, there are two aspects to selection: the object itself, and(in most cases) the surface of the object. Some operations affect the object as asurface(s).There are several tools that you can use to select objects, but because selection is needed so frequently, it is also the default operation, DefaultSelect. You will see this command in the 3D Design view command line whenever no other tool is selected.1.Click with the left mouse button on any visible surface of the light pipe.The wireframe outline of the model is highlighted to show that it is selected.The surface you click on changes color and a tag point (an “X”) is displayed on that surface. The name of the selected surface is also highlighted in the System Navigator.2.Click on the name of a different surface in the System Navigator.The corresponding surface is highlighted in the 3D Design view. If you click a surface that is not directly visible (for example, the back surface or bottom surface), you won't see the highlighting when the model is displayed intranslucent mode. If you use the right mouse button to rotate the view, you will see the highlighting.Tag pointC HAPTER 3Learn by Doing: Analyze a Light Pipe To get ready for ray tracing, the next step restores the original side view and changes the rendering mode from translucent to wireframe.3.To restore the YZ plane view and set the scale to fit all objects in the visibleplane, click these toolbar buttons:Y-Z Plane and then Fit .4.Select View > Render Mode > Wireframe to display only the edges of theobjects.Wireframe render mode makes it easier to see and work with rays, but in thismode, you can select objects only by clicking on an edge. With translucent and solid rendering, you can click anywhere on a rendered surface to select it.Tracing Rays and Modifying the Light PipeThe basic operation of LightToolsis ray tracing. Everything else is based to some extent on tracing one or many rays and doing some calculations with them . LightTools’ Monte Carlo simulation traces many rays (thousands, sometimes millions, from defined sources) to predict illumination distributions.“Point-and-Shoot” Ray TracingPoint-and-shoot rays are defined graphically, interactively, by clicking a starting point and then making additional clicks to define the direction and, in the case of fans and grids, the extent of the ray bundle . These rays are called non-sequentialC HAPTER3Learn by Doing: Analyze a Light Pipehit. You typically trace a relatively small number of point-and-shoot rays to view and understand the behavior of light in the system and to instantly see the optical effect when you make changes to the model. Going beyond the requirements of a simulation tool, this capability helps to make LightTools an excellent design tool.Once you begin running illumination simulations, you must explicitly re-run thesimulation when you make changes to the model.Using the Command PaletteAs described in The Command Palette on page15, clicking one of the six category buttons displays a set of sub-category buttons.Clicking a sub-category button then displays a set of command buttons.The category, sub-category, and commandbutton sequence is represented as follows:Some command buttons, such as the Ray Fan button shown here, require one ormore clicks in a specific sequence to execute. A diagram is provided on the button itself with the click sequence indicated in the diagram.The Command line shows the command name (NSFanFromPoint, in this case),and above the command line you will see prompts for the input. As you clickthrough the sequence using the mouse (or enter data directly in the Command line), the command sequence is built and, upon completion, is executed.Trace a Ray FanYou can trace single rays, a fan of rays, or a grid of rays. There are several types of fans and grids: parallel, diverging, and converging. In this example, you will have a light source located 0.5 mm to the left of the entering face of the light pipe. Use the cursor coordinates displayed at the lower right of the 3D Design view for thefollowing steps.Note: If you followed the setup instructions in Chapter2, there is a 0.1 mm snap grid active, which restricts the mouse motion to 0.1 mm increments, making it easier to hit specific points.C HAPTER 3Learn by Doing: Analyze a Light Pipe 1.Click the Ray Fan button (NSFanFromPoint ). The command panel buttonsequence is shown below.2.Click at the point (X = 0, Y = 0, Z = -0.5) to start the ray fan. Be sure to releasethe mouse button after clicking. Each point is discrete.3.Click at (0, 1, 1) to define the top of the fan, then click at (0, -1, 1) to define thebottom of the fan .Follow the prompts and watch the cursor coordinates to track the cursorlocation.PromptsCursor coordinatesC HAPTER 3Learn by Doing: Analyze a Light Pipe The fan is displayed. As you might expect, no light makes it to the desired output surface on top of the larger cube . You will have to modify the light pipe to get the light there. Note that the command button is no longer highlighted; to trace another ray fan, you would have to click the command button again .Make a CutTo reflect light to the top of the light pipe, you must introduce an angled surface. If the trim angle is correct, total internal reflection (TIR) will direct most of the light to the top surface without requiring any sort of coating. (TIR is the default surface property, but there are many others, as you will see.)1.Select the light pipe by clicking on any edge.2.Select the Trim button (TrimSolid ), shown below.To find out what the Trim button is used for, you can use What’s This? help.3.Select Help > What's This? on the main menu.The cursor changes to a question mark.Tip:The snap grid is not your only guide for precisely entering points . During anyoperation, you can right-click to display a shortcut menu with a Snapmenu item.You can snap points to objects, surfaces, coordinate axes, and even lines or rays.4.5.Click the X in the top right corner of the Help window to close it.6.Click the point (0, 0, 6.5) to define the section point, as prompted.The exact coordinate is not critical, because you will change it later to try to get more rays on the target surface. A “rubber band” line is displayed, along with text showing you the length and angle of the vector leading to the second point.7.Aim the normal vector at the lower right corner, making an angle of about -34º(the length is not critical), and then click to create the trim surface.If you make a mistake and trim away too much, select Edit > Undo and try again . It should look something like this:Name the ObjectIn the System Navigator, the Trim operation has created the new objectPlanePrimitive_n (where n is an integer). This is essentially an infinite “block” that has been Boolean-subtracted from the light pipe to form the trim plane surface, which is labeled HalfPlane (this is where the surface properties reside). You can keep the default name, but it is a good idea to give important objects a descriptive name, so they are easy to recognize later . In this case, you should rename the PlanePrimitive, because you will later modify the trim angle of this 3D object .Renaming is easy.1.In the System Navigator, right-click on PlanePrimitive_n and select Rename onthe shortcut menu.2.Type a new name, such as TIR_fold, and press Enter.3.Save the modified system:a.Select File > Save As .b.Navigate to the \LTUser (or other) directory.c.Key in a new name, such as Tut_Lpipe_trimmed.1.lts, and click Save.Note that the file name displays in the title bar (top edge) of the 3D Design view window.Changing PropertiesNow the light is getting to the collection surface, but it doesn't fill the surface and it isn’t very uniform. This is just a rough judgment based on a small number of rays, but it's often part of the iterative design process to use a few rays to make decisions about parameters, then do a Monte Carlo simulation to predict the illumination more precisely. It may not be possible to get a great distribution with a simple TIR surface, but it's easy to experiment with the angle and position of the trim surface.1.In the System Navigator, right-click on TIR_fold (the recently renamedPlanePrimitive_n ) and select Properties on the shortcut menu.The Properties dialog box gives you access to every detail of a model, and it changes, depending on the type of object selected . Right now, it displays the Coordinates tab, which applies to the entire selected object .(There is also ayou don’t need to use it at this time.)2.Move the Properties dialog box so that you can see the 3D Design view.3.Change the Absolute values of Z and Alpha to several different values, clickingApply each time.Can you get the ray fan to cover most of the top surface? The values shown (Z=6 and Alpha = 139º) are not necessarily optimum.4.Close the Properties dialog box. To do this, you can click the Cancel button orthe X in the top right corner.5.Click on the design view to make sure it is active.6.Save your modified file. This time, you can use File > Save, because you gave ita name when you saved it earlier.Tip: You can also click on the name of a window in the Window Manager to bring it forward and make it active.Tip: If the File menu is not displayed, the Properties dialog box may still be the active window. To re-display the menu bar, make the 3D Design view active.Performing an Illumination AnalysisPoint-and-shoot ray fans are great for simple analysis and design, because theyillumination performance, which requires several additions to the model: •One or more sources •One or more receivers •A few decisions, such as how many rays to trace, and whether or not to display them •Various charting features, which enable you to look at analysis resultsThe light pipe model already has a source and receiver, but they are on a hidden layer. Next, you will display them and do some quick illumination simulations . Later examples will explain the illumination results more extensively.LayersLightTools models can become very complex, with optical elements, mechanical parts, rays, sources, receivers, etc . The layer feature provides a way of managing this complexity, allowing you to separate objects on as many as 32 layers, any of which can be visible or hidden . A layer number is one of the properties assigned to a LightTools object. To see or set the layer number, right-click the object’s name in the System Navigation window, select the Properties shortcut menu and click on the Display tab.In this model, a light source and receiver for illumination analysis have already been defined and hidden on layer 2. Follow these steps to make them visible .1.Click on the design view.2.Select Edit > Preferences to display the Preferences dialog box.This dialog box controls many program parameters, with sections for General preferences, various defaults, and view-specific parameters for any views that are currently open (only the 3D Design view, in this case).Note: Making a layer visible or hidden affects only the display of objects, not their optical behavior. For example, a mirror on a hidden layer still reflects rays . To make 3D objects “invisible” to rays, you must use another option: the Ray Traceable check box on the Ray Trace tab of the Properties dialog box.3.In the navigation tree of the dialog box, click the plus sign (+) next to the ViewPreferences heading, and then click on the name of the 3D Design view below it.4.Click on the Layers tab to bring it to the front.5.Click the check box for layer 2 (Lum_Objects) to make it visible.6.Click OK.Clicking OK applies changes and closes the dialog box.The source and receiver symbols are now visible in the 3D Design view.Sources and Receivers Array This section briefly describes sources and receivers. Please see the LightToolsIllumination Module User’s Guide, Chapter2 and Chapter3 for detailedinformation about these types of objects.Sources.LightTools supports a variety of sources, from point sources to surface or volume emitters, in simple shapes to detailed lamp models made up of multiplesources and mechanical parts. You can also use simple sources with angular andspatial distributions (apodization files) applied to match measured or desireddistributions, as well as ray data sources created from measurements of realsources.Receivers. Receivers are special objects created to collect ray trace data forillumination calculations. LightTools supports spatial and angular receivers, andthey are usually attached to a surface of an object. (A far-field angular receiver is not attached to any object.)Receivers assign ray energy (weighted ray data) to bins (cells) in a collection mesh, and this allows the irradiance and other properties to be determined. There is a trade-off between radiometric accuracy (based on thenumber of rays per bin) and spatial accuracy (based on the number of bins across the receiver). LightTools allows you to re-bin the data without re-tracing the rays.In this sample model, a source and surface receiver are already defined. The source is a 1.0 watt point source with an apodization file attached to simulate the Gaussian intensity of an LED. The receiver is attached to the rectangular dummy element(named AirLens in this model, because that's its material) defined for this purpose.You can attach receivers to surfaces of real objects or to dummy elements,depending on your goals.Simulation Info and Ray PreviewA Monte Carlo simulation requires a large number of samples for accuratestatistical estimates of illumination. Samples in LightTools are traced rays, butunlike point-and-shoot rays, rays in an illumination simulation are traced in random directions from randomly selected points in or on the defined sources. Apodization and other factors affect the selection of random points so source behavior can beaccurately simulated.Before tracing large numbers of Monte Carlo rays, it’s a good idea to trace asmaller number with the Show Preview option turned on. When Show Preview is on, LightTools draws the rays in the design view, allowing you to see whether or notthings are working correctly. Drawing many rays may slow down the ray trace, so itmakes sense to keep the value for this option low or turn it off when you’re tracingthousands of rays (or more).1.Select Ray Trace > Simulation Input to display the Simulation Input dialogbox.2.Change the Total Rays to Trace to 200 and click Apply.3.Check the box next to the option Show Preview and enter 200 Rays.4.Click Apply, then OK.No rays are traced yet. You have just defined the parameters for the simulation.You can run the simulation from the Ray Trace menu or from the toolbar.5.Click the Begin All Simulations button or select Ray Trace > Begin All Simulations to trace and display the rays.Your 3D Design view should look something like the following figure. (The design view has been rotated in this example.)Understanding ChartsWhen you run a simulation, all of the output data is stored in memory; you see the results when you open an illumination chart . Because there are many ways to view and analyze illumination results, the best chart to display depends on your goals . In this example, you will look only at the illuminance (spatial) distribution on the predefined surface receiver . Other available analyses and charts (including the interactive LumViewer) will be discussed in later examples.Scatter charts are always a good starting point, because they are the closest thing to a view of the raw ray data. They don't tell you anything about the energy orstatistics, but they allow you to see how completely you have covered the receiver.1.With the 3D Design view active, select Analysis > Illuminance Display >Scatter Chart .With only 200 rays for preview, the scatter chart is not very dense, but it can help you understand the relationship between chart coordinates and system coordinates . In the figure below, the 3D Design view has been rotated so that the receiver surface has the same orientation as the chart . You can see that theNote: The menus always use the term illuminance , although, strictly speaking, this term applies only when photometric units are in use. In this example, the spatial distribution is in radiometric units of watts/mm 2.scatter chart is a kind of “ray diagram,” showing where the rays fall on the receiver surface.Tip:Chart coordinates are receiver coordinates. If you are not sure of the relationship between the chart coordinates and what you see in the design view, you can attach alocalcoordinate system to the surface holding the receiver. This was done in the figure above.To attach a local coordinate system, click the UCSOnSurface toolbarbutton, shown at left, and then click on the receiver surface . (UCS means user coordinate system. This is also the rotation point for right-mouseview operations.)A local coordinate system diagram is displayed on the surface. To return the UCS to the global origin, click the UCSToGLobalOrigin toolbarbutton, shown at left.Making the Big RunIf the simulation with a few rays doesn't show any major problems, you can try a bigger run.1.Click on the 3D Design view to make it active.2.Select Ray Trace > Simulation Input to display the Simulation Input dialogbox.3.Change the Total Rays to Trace to 10000.4.Clear the Show Preview check box and click OK.5.Click the Begin All Simulations buttonto trace the rays.This calculation will probably take a little longer (a few seconds or more,depending on your CPU’s speed). You may see the Progress dialog box, shownbelow. Tip: If a calculation ever takes too long, you can interrupt the simulation by clicking the Pause button . You can then look at other windows, and even opennew analysis windows to see if you have enough data. Then, click Continue or Stop in the Progress dialog box, as needed .Analysis Results and Re-binningAt this point, your scatter chart should be quite dense with rays. With more rays,the illuminance (actually, irradiance, in this case, with units of W/mm2 and no photometric weighting. Please see Chapter2 of the LightTools Illumination Module User’s Guide for information on radiometric vs. photometric calculations). To display a raster chart, make the design view the active window, and select Analysis > Illuminance Display > Raster Chart on the main menu.The raster chart shows a pseudo-color coded, graphically smoothed map of irradiance (spatial) distribution on the receiver, along with a histogram showing the energy levels. You can see a fairly “hot” region in the center, with dark edges. How much data is here? How accurate is it? As with most objects in LightTools, receivers and charts have properties, and you can look to them to answer these questions. 1.Right-click near the center of the raster chart (on the shaded area).The Properties dialog box for the Illumination Mesh_shade is displayed. Like other property dialog boxes, it has a small navigation tree. (You can also access mesh and other properties from the Illumination Manager section of the System Navigator, even if no charts are open.)2.Click on the plus sign (+) to expand the tree chart, then click on the sub-itemilluminanceMesh_n, (where n is a number).In this dialog box, the Properties tab shows that the Mesh Dimensions have been set to 9 bins by 15 bins. (Auto Mesh Boundaries, turned off in this case, is the default. It normally sets the number of bins to try to get a required accuracy level.) The Results tab contains read-only (calculated) values, including a(radiometric) Error Estimate at Peak, which should be about 10% for the 9x15 mesh . What if you have fewer bins?3.In the Properties tab, change the bins to X = 5 and Y = 9 and click Apply.The Error Estimate on the Results tab changes to around 6%. (Due to the statistical nature of Monte Carlo simulation, your numbers will not exactly match these.) This is called re-binning and is very useful for understanding the statistics of your illumination data . Note that in this case (with a TIR angled surface, with no coating), the total power is about 0.63 watts. The total power of the source is 1 watt.Tip: If you would like to see the content of two or more tabs at once, you canopen them in separate windows. To do this, right-click on the tab title, and selectOpen Tab in New Window on the shortcut menu, as shown above.Optical Properties Example: Paint It WhiteTo improve the uniformity of illumination in this case , you could try a number of techniques: “stair-step” extrusions, a curved surface, patterns of paint dots, or 3D textures (bumps or grooves), for example .One quick option to try is to paint it white . LightTools provides a number of pre-defined optical properties, including one called White Paint, in an easy-to-use library of properties. These library properties are created by combining several basic properties; for example, the White Paint property creates a Lambertianscatterer with 92% reflectance . You can, of course, set basic properties directly, and you can save and name your own combinations in .opr (for o ptical pr operty) files .1.In the 3D Design view, rotate the view so that you can click on the TIR_foldsurface.2.Right-click, and select Optical Properties on the shortcut menu.The Properties dialog box is displayed, with the Optical Properties tab in the foreground.3.Click the radio button for Load From Library.4.Select Surface Finishes from the first drop-down list, shown in the followingfigure.5.In the second drop-down list, select WhitePaint.1.opr.6.Click OK.Scattered rays tend to bounce and re-scatter, as illustrated in the followingdiagram. As a result, you may see some warning messages about maximum hits for the NS rays in your model. The reason is that if the rays hit a surface more than the default “max hits” of 1000 times, a warning is displayed in the Console window.Now you can re-run the illumination simulation with a single click.7.Activate the design view and click the Begin All Simulations button to re-run the simulation.8.Check the charts again. To bring a chart to the foreground, you can click on the chart window or click on the name of the chart in the Window Navigator. Although still less than optimum, the Scatter and Raster Charts both do show greater uniformity over a larger area of the receiver, as shown in the following figure.。
Light-Guideing导光柱设计指南
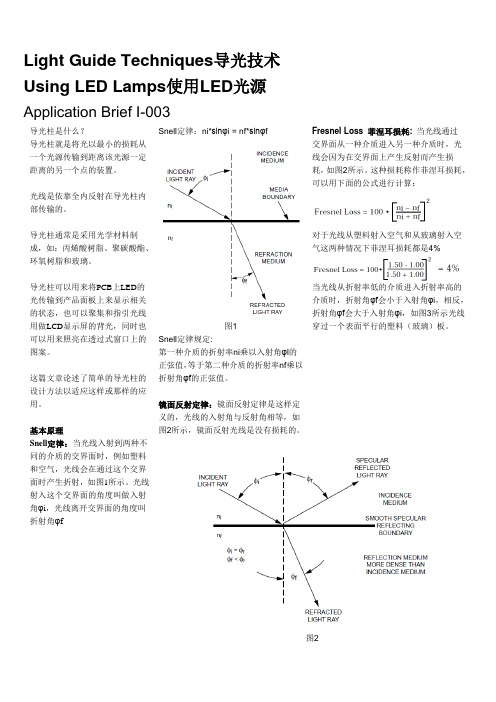
Light Guide Techniques导光技术Using LED Lamps使用LED光源Application Brief I-003导光柱是什么?导光柱就是将光以最小的损耗从一个光源传输到距离该光源一定距离的另一个点的装置。
光线是依靠全内反射在导光柱内部传输的。
导光柱通常是采用光学材料制成,如:丙烯酸树脂、聚碳酸酯、环氧树脂和玻璃。
导光柱可以用来将PCB上LED的光传输到产品面板上来显示相关的状态,也可以聚集和指引光线用做LCD显示屏的背光,同时也可以用来照亮在透过式窗口上的图案。
这篇文章论述了简单的导光柱的设计方法以适应这样或那样的应用。
基本原理Snell定律:当光线入射到两种不同的介质的交界面时,例如塑料和空气,光线会在通过这个交界面时产生折射,如图1所示。
光线射入这个交界面的角度叫做入射角φi,光线离开交界面的角度叫折射角φf Snell定律:ni*sinφi = nf*sinφf图1Snell定律规定:第一种介质的折射率ni乘以入射角φi的正弦值,等于第二种介质的折射率nf乘以折射角φf的正弦值。
镜面反射定律:镜面反射定律是这样定义的,光线的入射角与反射角相等,如图2所示,镜面反射光线是没有损耗的。
Fresnel Loss 菲涅耳损耗: 当光线通过交界面从一种介质进入另一种介质时,光线会因为在交界面上产生反射而产生损耗,如图2所示。
这种损耗称作菲涅耳损耗,可以用下面的公式进行计算:对于光线从塑料射入空气和从玻璃射入空气这两种情况下菲涅耳损耗都是4%当光线从折射率低的介质进入折射率高的介质时,折射角φf会小于入射角φi,相反,折射角φf会大于入射角φi,如图3所示光线穿过一个表面平行的塑料(玻璃)板。
图2图3 图4 完全内反射:当折射角等于90°时,入射光将会折射并沿着两种介质的交界面传播,如图4所示。
这时sin φf (90°) = 1.0,因此Snell定律就简化成ni*sin φi = nf. 这个公式可以用来计算产生完全内反射的临界入射角φc:空气的折射率为1.0,所以上式中的nf = 1.0,因此只要知道导光柱所采用的介质的折射率就能够迅速计算出这种介质内产生完全内反射的临界入射角.对于绝大多数的塑料和玻璃,它们的折射率约为1.50,因此,对于采用这两种材质制成的导光柱的完全内反射临界角约为42°导光柱内部与外界空气的交界面上产生的镜面反射可以用来帮助在导光柱内传输光线。
用LightTools设计导光管
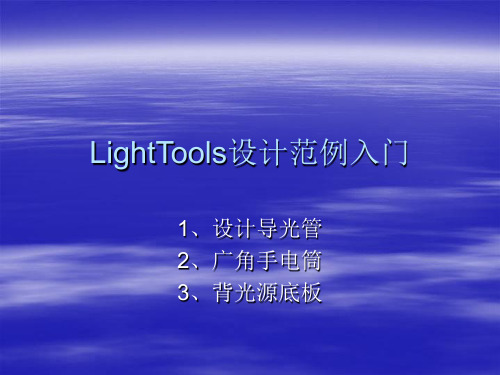
1、设计导光管型、改变视角、光线模拟
预览
导光管(Light Pipe):把光线透射到需要照 明的区域。 掌握:
1.3D模型的掌握和观察角度。 2.使用扇型光线追踪并调节反光镜角度。 3.使用光源和接收器进行简单的蒙特卡罗模拟。 4.使用光学性质修改表面参数并进行照明模拟。
Monte Carlo初步模拟
Illumination > Setup Simulation(Done) Monte Carlo不使用单个点作为光源,也没 有等角度分布的光线,方向完全随机; 使用少量光线进行模拟 Illumination > Simulation Info,将光线数 量设置为200,并将Preview Ray选中。 选择Start Simulation(!)
二、设计广角手电筒
一、初步设计 二、添加具体光源和接收器
一、广角手电筒
广角手电筒发出的光线具有较强的会聚性。 可以用一个点光源和一个抛物面反射镜构成。 设计目标:手电筒在300mm处发出的光斑小 于100mm。
Raster Chart:表示了 不同能量密度的空间分 布区域。 右边表示不同颜色所表 示的能量密度。 中间比较“热”,能量 密度高。旁边温度 “低”,能量密度低。
进一步分析
右击Raster Chart。 接收器被划分为9×15个格子。
将X从9改为5,Y从15改为9。 减少格子数目可以减少误差。
接收器设置
接收器作用:计量光线数量用于分析计算。 一般是一个平面,附在某个模型的表面(远 场接收器除外)。 接收器一般把光线分配在网格结构中。这表 示辐射精度(Radiometric accuracy)和空间 精确度(Spartial accuracy)是互相矛盾的。 本例接收器是附着在“空气透镜”上,即允 许接收器附着在实体模型或者虚拟模型上。
光导管照明技术在建筑照明设计中的应用

光导管照明技术在建筑照明设计中的应用摘要:本文首先介绍了光导管照明技术的国内外发展历程及现状,阐述了光导管照明系统的基本结构和类型,结合实际工程案例,重点分析了光导管照明系统的优越性和目前存在的问题,并提出了光导管照明技术在建筑照明设计中的适用范围及其发展趋势。
关键词:自然采光建筑照明光导管节能减排abstract: this paper first introduced the optical tube lighting technology at home and abroad and the development course and the present situation, this paper expounds the optical tube lighting system the basic structure and types, and combining with actual engineering example, analyzed the optical tube lighting system superiority and the existing problems, and puts forward the optical tube lighting technology in building lighting design of the applicable scope and development trend.keywords: natural lighting building lighting optical tube energy conservation and emission reduction中图分类号:tu113.6+6 文献标识码:a 文章编号:引言当今节能和保护环境已成为世界各地普遍关注的社会问题,并直接关系到社会的持续发展。
人工照明在现代照明中仍然占据着举足轻重的分量,全世界的平均照明用电已占总发电量的10%~20%,而我国照明用电已占总发电量的10%~12%。
毕业论文:基于tracepro的led导光管设计
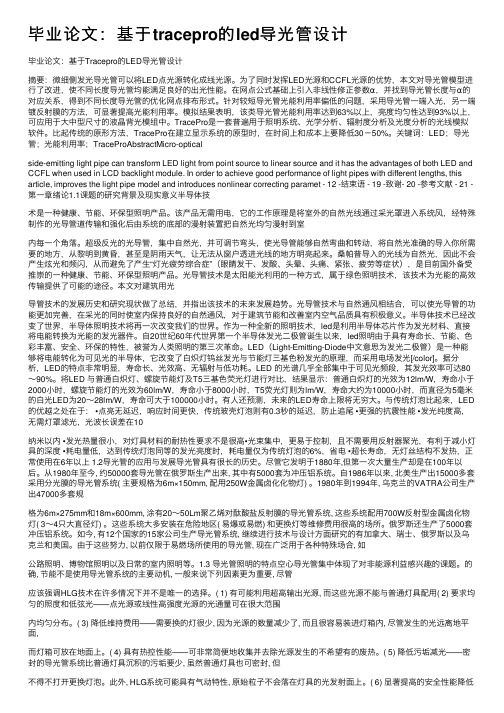
毕业论⽂:基于tracepro的led导光管设计毕业论⽂:基于Tracepro的LED导光管设计摘要:微细侧发光导光管可以将LED点光源转化成线光源。
为了同时发挥LED光源和CCFL光源的优势,本⽂对导光管模型进⾏了改进,使不同长度导光管均能满⾜良好的出光性能。
在⽹点公式基础上引⼊⾮线性修正参数α,并找到导光管长度与α的对应关系,得到不同长度导光管的优化⽹点排布形式。
针对较短导光管光能利⽤率偏低的问题,采⽤导光管⼀端⼊光,另⼀端镀反射膜的⽅法,可显著提⾼光能利⽤率。
模拟结果表明,该类导光管光能利⽤率达到63%以上,亮度均匀性达到93%以上,可应⽤于⼤中型尺⼨的液晶背光模组中。
TracePro是⼀套普遍⽤于照明系统、光学分析、辐射度分析及光度分析的光线模拟软件。
⽐起传统的原形⽅法,TracePro在建⽴显⽰系统的原型时,在时间上和成本上要降低30-50%。
关键词:LED;导光管;光能利⽤率;TraceProAbstractMicro-opticalside-emitting light pipe can transform LED light from point source to linear source and it has the advantages of both LED and CCFL when used in LCD backlight module. In order to achieve good performance of light pipes with different lengths, this article, improves the light pipe model and introduces nonlinear correcting paramet - 12 -结束语 - 19 -致谢- 20 -参考⽂献 - 21 -第⼀章绪论1.1课题的研究背景及现实意义半导体技术是⼀种健康、节能、环保型照明产品。
Light Guideing导光柱设计指南

Light Guide Techniques导光技术Using LED Lamps使用LED光源Application Brief I-003导光柱是什么导光柱就是将光以最小的损耗从一个光源传输到距离该光源一定距离的另一个点的装置。
光线是依靠全内反射在导光柱内部传输的。
导光柱通常是采用光学材料制成,如:丙烯酸树脂、聚碳酸酯、环氧树脂和玻璃。
导光柱可以用来将PCB上LED的光传输到产品面板上来显示相关的状态,也可以聚集和指引光线用做LCD显示屏的背光,同时也可以用来照亮在透过式窗口上的图案。
这篇文章论述了简单的导光柱的设计方法以适应这样或那样的应用。
基本原理Snell定律:当光线入射到两种不同的介质的交界面时,例如塑料和空气,光线会在通过这个交界面时产生折射,如图1所示。
光线射入这个交界面的角度叫做入射角φi,光线离开交界面的角度叫折射角φf Snell定律:ni*sinφi = nf*sinφf图1Snell定律规定:第一种介质的折射率ni乘以入射角φi的正弦值,等于第二种介质的折射率nf乘以折射角φf的正弦值。
镜面反射定律:镜面反射定律是这样定义的,光线的入射角与反射角相等,如图2所示,镜面反射光线是没有损耗的。
Fresnel Loss 菲涅耳损耗: 当光线通过交界面从一种介质进入另一种介质时,光线会因为在交界面上产生反射而产生损耗,如图2所示。
这种损耗称作菲涅耳损耗,可以用下面的公式进行计算:对于光线从塑料射入空气和从玻璃射入空气这两种情况下菲涅耳损耗都是4%当光线从折射率低的介质进入折射率高的介质时,折射角φf会小于入射角φi,相反,折射角φf会大于入射角φi,如图3所示光线穿过一个表面平行的塑料(玻璃)板。
图2图3图4完全内反射:当折射角等于90°时,入射光将会折射并沿着两种介质的交界面传播,如图4所示。
这时sin φf (90°) = ,因此Snell 定律就简化成ni*sin φi = nf. 这个公式可以用来计算产生完全内反射的临界入射角φc :空气的折射率为,所以上式中的nf = ,因此只要知道导光柱所采用的介质的折射率就能够迅速计算出这种介质内产生完全内反射的临界入射角.对于绝大多数的塑料和玻璃,它们的折射率约为,因此,对于采用这两种材质制成的导光柱的完全内反射临界角约为42°导光柱内部与外界空气的交界面上产生的镜面反射可以用来帮助在导光柱内传输光线。
lightguideing导光柱设计指南
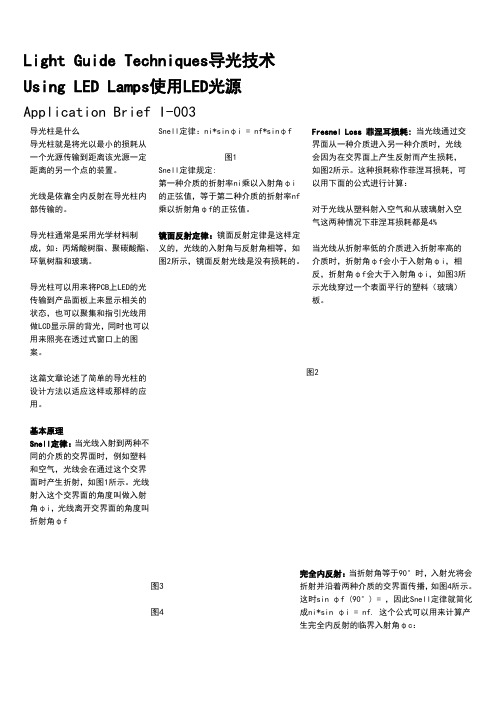
Light Guide Techniques导光技术Using LED Lamps使用LED光源Application Brief I-003导光柱是什么导光柱就是将光以最小的损耗从一个光源传输到距离该光源一定距离的另一个点的装置。
光线是依靠全内反射在导光柱内部传输的。
导光柱通常是采用光学材料制成,如:丙烯酸树脂、聚碳酸酯、环氧树脂和玻璃。
导光柱可以用来将PCB上LED的光传输到产品面板上来显示相关的状态,也可以聚集和指引光线用做LCD显示屏的背光,同时也可以用来照亮在透过式窗口上的图案。
这篇文章论述了简单的导光柱的设计方法以适应这样或那样的应用。
基本原理Snell定律:当光线入射到两种不同的介质的交界面时,例如塑料和空气,光线会在通过这个交界面时产生折射,如图1所示。
光线射入这个交界面的角度叫做入射角φi,光线离开交界面的角度叫折射角φf Snell定律:ni*sinφi = nf*sinφf图1Snell定律规定:第一种介质的折射率ni乘以入射角φi的正弦值,等于第二种介质的折射率nf乘以折射角φf的正弦值。
镜面反射定律:镜面反射定律是这样定义的,光线的入射角与反射角相等,如图2所示,镜面反射光线是没有损耗的。
Fresnel Loss 菲涅耳损耗: 当光线通过交界面从一种介质进入另一种介质时,光线会因为在交界面上产生反射而产生损耗,如图2所示。
这种损耗称作菲涅耳损耗,可以用下面的公式进行计算:对于光线从塑料射入空气和从玻璃射入空气这两种情况下菲涅耳损耗都是4%当光线从折射率低的介质进入折射率高的介质时,折射角φf会小于入射角φi,相反,折射角φf会大于入射角φi,如图3所示光线穿过一个表面平行的塑料(玻璃)板。
图2图3图4完全内反射:当折射角等于90°时,入射光将会折射并沿着两种介质的交界面传播,如图4所示。
这时sin φf (90°) = ,因此Snell定律就简化成ni*sin φi = nf. 这个公式可以用来计算产生完全内反射的临界入射角φc:空气的折射率为,所以上式中的nf = ,因此只要知道导光柱所采用的介质的折射率就能够迅速计算出这种介质内产生完全内反射的临界入射角.对于绝大多数的塑料和玻璃,它们的折射率约为,因此,对于采用这两种材质制成的导光柱的完全内反射临界角约为42°导光柱内部与外界空气的交界面上产生的镜面反射可以用来帮助在导光柱内传输光线。
34导光管采光系统PPT课件

系统内部还可以安装不锈钢网,防止他人从管道进入室内。 多用于别墅建筑。
防盗螺丝 26
系统性能 4— 隔热性好
27
系统性能 5— 低碳、环保
● 导光管采光系统100%利用自然光照明,可完全取代白天的电力照明,每天可提供8-10个小时 的自然光照明,无能耗,一次性投资,无需维护,节约能源,创造效益,同时也减少了大量 二氧化碳和其他污染物的排放。
尚拓导光管采光系统
Suntube Tubular Skylight
1
标题添加
点击此处输入相 关文本内容
标题添加
点击此处输入相 关文本内容
总体概述
点击此处输入 相关文本内容
点击此处输入 相关文本内容
2
公司总部外貌
深圳生产基地3外貌
公司简介
北京东方风光新能源技术有限公司成立于二零零五年,是国内首家从事导光管采 光系统(也叫光导照明系统)的研发、生产和销售的高新技术企业。
采用与特警盾牌相拟的材料达到硬度高,抗冲击性强、耐摩擦等效 果;
能过滤90%以上的有害紫外线,有利于人的健康;对室内物品不会产 生影响。
海拉之光范例设计过程

范例一1.创建一个空白几何文件选择"File / New" 然后选择"geometry",左键单击。
2.插入一个圆柱光源A.选择"Lightsources / Cylinder Light Source"。
B.设置长度length为5,半径radius为0.5。
C.演示颜色设置255,255,0或者点击“…”选择色板D.选择"create ray bundle for interactive raytrace"选择"with grid on touch surface"可创建一个UV坐标表示光线接触面E.光源类型我们选择lambert emitter并设置一个光通量1000流明。
F.输入一个源名称,点击<Apply>。
演示如图。
3定义一个反射面我们定义一个抛物面反射面A.选择"Geometry / Standard Geometry / Rectangular Paraboloid"出现右图编辑框B.顶部设置定义当前轴系。
我们保留默认设置。
、C.下一个设置定义几何。
设置min x,max x和min y,max y为-50和50即默认值。
设置焦点长度的x,y坐标为x,y=25。
选择一种颜色和一个名称。
D.现在我想指定两种属性给这个面。
第一,我们想它反射光线。
in LucidShape's terminologywe want to attach amaterial to it。
第二,我们想知道在这面上的照度。
所以我们要安装一个传感器在面上。
因此我们选择带反射性的the actor tab "Specularreflective" material 并命名,例如"reflector"。
E.点击<Apply>创建反射器。
- 1、下载文档前请自行甄别文档内容的完整性,平台不提供额外的编辑、内容补充、找答案等附加服务。
- 2、"仅部分预览"的文档,不可在线预览部分如存在完整性等问题,可反馈申请退款(可完整预览的文档不适用该条件!)。
- 3、如文档侵犯您的权益,请联系客服反馈,我们会尽快为您处理(人工客服工作时间:9:00-18:30)。
Learn by Example: How to Design Light PipesLight plays an important role in the design of many hardware products. Often, they are both decorative and functional. Indicator lights are the most minimal user interface: They tell you whether the device is turned on, low on battery, or “thinking” really hard.On modern electronics, the light’s source is almost always an LED. However, you rarely see exposed LED components on the exterior of a device. What you do see is the exit surface of a light pipe (also known as a light guide).Light pipes can focus, diffuse, or redirect light; most light pipes do some combination of these.Design considerations include:•Minimizing loss during transmission•Minimizing the number of LEDs needed (they are power-hungry components that destroy battery life)•Maximizing color mixing for RGB LEDsIn our teardowns, we’ve seen many light pipes—they’re one of our favorite types of components because each one is so unique. Today, we want to dig deeper into some unique light pipe applications and explain the principles behind each design.Application 1: Extending Light’s ReachAs I mentioned, LEDs are power-hungry components. So for portable electronics, you should only use the light when the user is actively interacting with the device, and you’ll want to minimize the number of LEDs needed. Light pipes can be used to extend the reach of LEDs so you can use fewer to achieve the same illumination effect. Here are two examples of how light pipes illuminate logos and thumb pads.Example 1: Illuminated Logo of Under Armour Heart Rate MonitorThe UA heart rate monitor’s front cover features a sizeable logo. The engineers behind this product managed to light up this logo evenly, with just one tiny top-firing LED at the center of the main PCBA. This LED doesn’t have much reach by itself.Under Armour LEDEnter the light pipe: It’s made of a milky plast ic that could be polycarbonate resin (normally transparent) with added titanium dioxide. The more titanium dioxide that’s added, the more milky the plastic, which improves diffusion.The cone-shaped cavity feature at the center of the light pipe is designed to match the LED; the angular wall of the cone helps to direct the emitted light into the light pipe.The cone is the entry point of the light pipe, and the entry point should always be placed as close to the light source as possible, to minimize loss.Light pipe diffuserLet’s see the actual effect of the light pipe:1.Without the light pipe, there is a strong hot spot in the center of the logo and notmuch light elsewhere.2.With the light pipe, the light emitted by the LED is spread out more evenly andthe extreme hot spot is gone.Under Armour LED without lightpipe Under Armour LED with light pipeExample 2: Illuminated Thumb Pad of Logitech G600 MMO MouseThe Logitech G600 MMO mouse has a twelve-button thumb pad. Each key is backlit, and the user can customize the light’s color. How many LEDs do you think are used to light up all these keys?The answer is TWO! Isn’t tha t surprising? What wizardry!The secret is side-firing LEDs that emit light directly into a flat plate of a light pipe. Notice how close the entry point of the light pipe is to the LEDs. You can’t afford losses when the lights have a long way to go to their exit points.Notice how the opposing elastomer thumb pad part has black paint spots on some keys, but not others? These black spots are close to the LED, likely to mask hot spots.Also note that the light pipe plate is super glossy, and the surfaces encapsulating the light pipe’s top and bottom sides are both white. Both of these features help maximize the total internal reflection and improve color mixing.Application 2 - Bending LightLEDs cannot always be located right behind the intended exit point of the lights, so light pipes are often used to transport light emitted by a board-mounted LED to an exit window some distance away. They can even “bend” light, as long as it’s within the limitations of physics.Here are a few examples:Example 1: Neato Light “Arc”This light pipe cradles the Neato’s power button. It has two entry points for LEDs to illuminate the entire path evenly. The second LED is needed because light does not like to bend past 90 degrees. If only one LED were used, significant loss would happen where the second entry point is, and the end of the arc would be dark.The entry points of the light pipe match the shape of the LEDs well.Neato light pipeNote that the top surface of the light pipe is textured, whereas all the othersurfaces are glossy. Textured surfaces encourage light to exit, and glossy surfaces encourage internal reflection.Also note that aluminum foil covers the underside of the light pipe. This has two purposes:1.To maximize total internal reflection2.To prevent users from seeing internal components underneath the light pipeExample 2: TiVo Bolt Status LightsThe TiVo Bolt has five status indicator lights. For all of these, the light source had to be “bent” through light pipes to exit the enclosure.One of these is a very classic “light pipe,” a clear polycarbonate tube that’sslightly bent to transport light from the source to the exit point at the logo. The entry point is a flat surface—this is a light pipe that has not been matched to the LED, incurring brightness loss. However, this simplifies the injection moldtooling of the light pipe.TiVo light pipeThe other four indicator lights appear in a row.TiVo indicator lightsThis set-up uses a multi-unit light pipe—think of this as a multi-lane roadway! Each “roadway” has its own entry and exit points. The light sources are four surface-mounted LEDs in a row.The light pipe is covered by a two-piece black shroud, which eliminates light leakage. Since the TiVo Bolt enclosure is white (not light-proof), without the shroud, we wouldn’t be able to see each light distinctly.Light pipeshroudMain TakeawaysWe hope you enjoyed this “anthology” of light pipe examples. Put your own spin on these established designs, and add some shiny to your next project! Now that you have form factor inspiration, check out our guide to prototyping light pipes with 3D printing.。