10、铸态高强度高韧性球墨铸铁生产技术
铸态QT600_10球墨铸铁的研制[1]
![铸态QT600_10球墨铸铁的研制[1]](https://img.taocdn.com/s3/m/2af5af1f10a6f524ccbf8522.png)
率有所下降; ( 3) 锰: 一部分锰溶入铁素体中提高球墨铸
铁强度, 但降低它的韧性; 同时形成少量碳化物 偏析在晶界上。因此在试验过程中, 采用低锰生 铁[ w( Mn) 0.12%] 和废钢适 当 配 比 熔 炼 , 严 格 控 制原铁液 w(Mn)≤0.30%;
( 4) 硫: 硫与球化元素有很强的化合能力, 生 成硫化物或硫氧化物, 不仅消耗球化剂, 造成球 化不稳定, 而且还使夹杂物数量增多, 导致铸件 产生缺陷, 此外, 还会使球化衰退速度加快; 因此 我们采用炉外吹氮气搅拌脱硫, 使原铁液 w( S) ≤0.020%, 以保证球化质量;
编
主要元素的 w(B %)
号
Si
Mn
S
Cu
RE
Mg
#1 2.66 0.24 0.012 0.51 0.038 0.039
#2 2.71 0.23 0.016 0.54 0.037 0.038
#3 2.61 0.23 0.011 0.57 0.041 0.042
#4 2.60 1.23 0.008 0.58 0.041 0.043
#5 2.55 0.26 0.010 0.57 0.041 0.042
#6 2.73 0.20 0.014 0.60 0.035 0.040
表 2 金相组织和力学性能 Tab.2 Microstructrue and mechanical properties
编
金相组织
力学性能
号 球化级别 珠光体数量(%) 抗拉强度/MPa 硬度(HB)
1 试验要求及方法
1.1 试验要求 ( 1) 力学性能及金相要求: 抗拉强度 σb≥600
MPa, 伸长率≥10%; 球化级别不低于 3 级( 参照 GB/T9441- 1988 球墨铸铁金相检验标准) ;
球墨铸铁700-10生产技术工艺

球墨铸铁700-10生产技术工艺关注我们请点这里铸造工业网7月10日近年有关高强度、高伸长率球墨铸铁的研究与生产技术开发受到相关研究机构的关注。
通过采用合理的成分设计、铁液净化、多元素合金固溶强化、晶粒细化等一系列生产工艺措施,探讨了铸态QT700-10工艺开发的可行性。
随着汽车工业的进步,商用车、重卡朝着重载、高速、低耗、低成本及良好的舒适性等方向发展,汽车底盘支架、托臂梁等零部件对高强度、高伸长率材料的综合性能要求也越来越高。
就材料的综合性能和成本而言,高强度、高伸长率球墨铸铁备受青睐,目前国家标准中关于球墨铸铁的要求,一般是低强度高伸长率或是高强度低伸长率,对于那些不仅要求高强度、还要求高韧性、高疲劳性能等的铸件,传统国标的球墨铸铁材料不能满足性能要求。
因此我公司与湖北汽车工业学院联合开展了高强度、高伸长率球墨铸铁研究工作,以满足汽车零部件轻量化需求。
1国内外球墨铸铁发展现状目前球墨铸铁的生产,都是根据GB/T 1348-2009《球墨铸铁件》标准,球墨铸铁的力学性能从QT350-22L到QT900-2共14个牌号,生产工艺己非常成熟,随着铸造企业质量控制水平的提高,绝大多数企业都能大批量稳定地生产。
然而,国内对高强度、高伸长率球墨铸铁技术研究与应用的报道并不多。
通过对国外球墨铸铁技术检索发现,SiboDur球墨铸铁是GF公司最新研发的铸态高强度高韧性球墨铸铁,对其化学成分及性能进行解读,SiboDur球墨铸铁形成了SiboDur450-17、SiboDur550-12、SiboDur700-10、SiboDur800-5系列,力学性能指标在传统球墨铸铁力学性指标中分布见图1 。
SiboDur球墨铸铁以Si和B作为合金化元素,其综合力学性能远远高于传统珠光体-铁素体球铁,适合制造承受冲击的铸件,广泛应用国外汽车行业。
2化学成分对球铁性能的影响2.1化学成分与金相组织SiboDur球墨铸铁是以Si和B作为合金化元素,实现铸态球铁高强度、高韧性综合力学性能,据此我们设计铸态QT700-10的主要化学成分见表1。
铸态高强度高塑性珠光体球墨铸铁的生产(1)

Nodular Iron铸态咼强度咼塑性珠光体球墨铸铁的生=(1)巩济民1,曾艺成2(1.中国一拖集团股份有限公司,河南洛阳4710002机械科学研究总院,北京100044)摘要:介绍了铸态高强度高塑性珠光体球墨铸铁的定义、特点、国内外研发情况及技术难点,详细阐述了生产此种球墨铸铁的要求以及应该采取的措施。
最后指出:要想生产出铸态高强度高塑性珠光体球墨铸铁,要生产球墨铸铁,要求和铸特点,体组织中的铁素体体积分数,再学成分铁铸型度采取有的强措施,最性能要求。
此夕卜,,生产出的铸,,铸的铸成,的。
关键词:球墨铸铁;铸态;高强度;高塑性中图分类号:TG255文献标志码:A文章编号:1003-(345(2021)02-0009-04DOI:10.3969/j.issn.1003-8345.2021.02.003Production of As-cast High Strength High-plastic Pearlite Nodular lron(I)GONG Ji-min1,ZENG Yi-cheng2(l.China Yituo Group Co.,LtM.,Luoyang471000,China;2.China Academy of Machinery Science and Technology,Beijing100044,China)Abstract:The definition,characteristics,domestic and foreign research-development situation and technical difficulties of theas-cast high strength high plasticity pearlite nodular iron were introduced,the requirements and measures for the productionof such nodular iron were described in detail.Finally pointed out:in order to produce as-cast high strength and high plastic pearlite nodular iron,it was necessary to determine the ferrite volume fraction in the matrix structure according to the grade requirements and casting characteristics on the basis of producing high quality nodular iron,and then took effective strengthening measures in aspects of chemical composition design,molten iron purification,alloying,casting cooling rate and so on to finally guarantee the properties requirements.In addition,it was suggested that enterprises should work hard on quality managementto ensure the production of castings with stable quality and customer satisfaction,and cooperate with relevant design departmentsto optimize the structure of castings and integrate castings,so that the effect of lightweight will be more obvious.Key words:nodular iron;as-cast;high strength;high plasticity,国内铸态高强度高塑性球墨铸铁有两种:一种以铁素体体的高强度高塑性球墨铸铁,特点有的塑性;)指,高强度强度一高600MPa),虽然塑性有变收稿日期:2020-11-30修订日期:2021-03-27作者简介:巩济民(1941.3—),男,汉族,河南西平人,毕业于武汉工学院(现武汉理工大学)铸造专业,高级工程师,主要从事铸铁熔炼及材料研究工作。
铸态高韧性球铁冷却壁的生产工艺
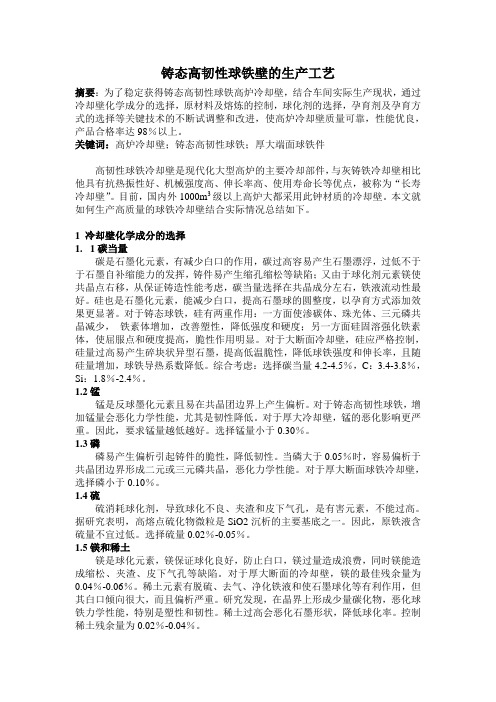
铸态高韧性球铁壁的生产工艺摘要:为了稳定获得铸态高韧性球铁高炉冷却壁,结合车间实际生产现状,通过冷却壁化学成分的选择,原材料及熔炼的控制,球化剂的选择,孕育剂及孕育方式的选择等关键技术的不断试调整和改进,使高炉冷却壁质量可靠,性能优良,产品合格率达98%以上。
关键词:高炉冷却壁;铸态高韧性球铁;厚大端面球铁件高韧性球铁冷却壁是现代化大型高炉的主要冷却部件,与灰铸铁冷却壁相比他具有抗热振性好、机械强度高、伸长率高、使用寿命长等优点,被称为“长寿冷却壁”。
目前,国内外1000m3级以上高炉大都采用此钟材质的冷却壁。
本文就如何生产高质量的球铁冷却壁结合实际情况总结如下。
1 冷却壁化学成分的选择1.1碳当量碳是石墨化元素,有减少白口的作用,碳过高容易产生石墨漂浮,过低不于于石墨自补缩能力的发挥,铸件易产生缩孔缩松等缺陷;又由于球化剂元素镁使共晶点右移,从保证铸造性能考虑,碳当量选择在共晶成分左右,铁液流动性最好。
硅也是石墨化元素,能减少白口,提高石墨球的圆整度,以孕育方式添加效果更显著。
对于铸态球铁,硅有两重作用:一方面使渗碳体、珠光体、三元磷共晶减少,铁素体增加,改善塑性,降低强度和硬度;另一方面硅固溶强化铁素体,使屈服点和硬度提高,脆性作用明显。
对于大断面冷却壁,硅应严格控制,硅量过高易产生碎块状异型石墨,提高低温脆性,降低球铁强度和伸长率,且随硅量增加,球铁导热系数降低。
综合考虑:选择碳当量4.2-4.5%,C:3.4-3.8%,Si:1.8%-2.4%。
1.2锰锰是反球墨化元素且易在共晶团边界上产生偏析。
对于铸态高韧性球铁,增加锰量会恶化力学性能,尤其是韧性降低。
对于厚大冷却壁,锰的恶化影响更严重。
因此,要求锰量越低越好。
选择锰量小于0.30%。
1.3磷磷易产生偏析引起铸件的脆性,降低韧性。
当磷大于0.05%时,容易偏析于共晶团边界形成二元或三元磷共晶,恶化力学性能。
对于厚大断面球铁冷却壁,选择磷小于0.10%。
- 1、下载文档前请自行甄别文档内容的完整性,平台不提供额外的编辑、内容补充、找答案等附加服务。
- 2、"仅部分预览"的文档,不可在线预览部分如存在完整性等问题,可反馈申请退款(可完整预览的文档不适用该条件!)。
- 3、如文档侵犯您的权益,请联系客服反馈,我们会尽快为您处理(人工客服工作时间:9:00-18:30)。
铸态高强度高韧性球墨铸铁生产技术李永红刘思明(安徽神剑科技股份有限公司安徽合肥 230022)摘要本文以铸态QT600-10材质生产技术为例,简要介绍了铸态高强度高韧性球墨铸铁件控制要点:在铸态通过控制影响力学性能的微观组织因素,满足球墨铸铁件高强度和高韧性的要求。
关键词铸态高强度高韧性;铸态QT600-10;合金化;铸态高强度高韧性球墨铸铁件,在满足特殊性能要求的基础上,减少了热处理环节,节约了中间运输成本,缩短了供货周期,是企业在制造过程中,努力追求的方向,特别是当前市场竞争激烈日趋白热化的环境下,可以有效减低企业生产成本,提高产品竞争力。
现结合本企业,在多年生产铸态高强度高韧性球墨铸铁件方面积累的经验,以QT600-10材质为例介绍其控制方法。
1 引言包括球墨铸铁在内的铸造合金的性能是由其含有一定成分的显微组织所决定的,要获得所需的性能,可以通过控制其显微组织,并使该组织中含有一定数量的合金强化元素。
通常强度与塑性之间始终存在矛盾,而随着对合金强化基体组织认识的加深,对于金属材料性能特殊要求的不断提高,要求球墨铸铁强度达到600MP以上,同时要求其具有很好的强韧性延伸率10%以上,通过热处理很难同时保证强度与韧性要求,通过控制影响显微组织的因素(化学成分,合金化,熔炼质量,球化孕育处理、壁厚条件、冷却速度等),可以满足铸态高强度,高韧性要求,现简单介绍其控制方法:2 化学成分的选择2.1 碳碳促进镁的吸收,改善球化、提高石墨球的圆整度;提高铁液的流动性,减少铸件的疏松缺陷和缩凹倾向;能够促进石墨化,减小白口倾向。
但是,过高的碳又容易产生石墨漂浮,使铸件综合性能降低。
因此将碳控制为3.5%~3.7%。
2.2硅促进石墨化元素,在球墨铸铁生产中由于硅的孕育作用,使珠光体和铁素体的比例改变:Si控制在2.0%~2.5%有利于珠光体组织的生成,而为了在保证强度达到600MP的基础上,延伸率达到10%,必须适当提高孕育效果,保证一定比例的铁素体组织,将硅控制在2.5%~2.8%。
2.3 锰锰使稳定珠光体元素,可以提高强度和硬度,降低塑性和韧性;但锰易产生偏析,锰量过多,易在共晶团边界形成化合物,降低铸件的力学性能,对厚大铸件更为严重。
一般不采用锰作为铸态形成珠光体的元素,将锰控制为<0.5%。
2.4 硫硫与镁、稀土亲和力很强,消耗铁液中的球化元素,形成MgS、RES渣,降低球化率;硫越高、消耗球化剂越多、因此铁液含硫量高是造成球化元素残留量少而导致球化不良的主要原因;另外,含硫量高还容易产生夹渣、皮下气孔等缺陷。
故S<0.03 %。
2.5 磷磷在球铁中溶解度很低,当磷超过某一含量时,易偏析于共晶团边界形成磷共晶,降低铸件的塑性、韧性和强度,并且使铸件产生冷裂。
因此P <0.05 %。
2.6 镁和稀土铁液中有一定的镁和稀土元素的残留量才能保证石墨成球。
在稀土镁球铁中,镁起主要球化作用,稀土起辅助球化作用,并起到净化铁液、抗球化干扰元素的作用。
将它们控制在如下范围:Mg残0.030%~0.05%、RE残0.030%~0.05%。
2.7铜+锡铜在共晶转变时,促进石墨化,减少或消除游离渗碳体的形成;在共析转变时,促进珠光体的形成,可减少或完全抑制铁素体的形成;对基体固溶强化。
是铸态高强度高韧性球墨铸铁生产中,理想的合金元素。
而铜量小于0.4%时,对于大量增加珠光体数量没有明显影响,对于薄壁铸件采用铜作为合金元素保证强韧性要求是最为理想的选择,根据壁厚条件,控制Cu的范围为0.20~0.50%;而对于厚壁件,采用一定比例的微量合金元素锡(在0.04%可以消除铁素体获得铸态珠光体;加入0.06%~0.10%,可使64mm厚的断面在铸态完全珠光体,且不形成游离渗碳体)配合一定比例的铜来控制基体组织比例,并强化微观组织,根据铸件壁厚Cu+Sn%为0.2~0.5%+0.02~0.05%,可以有效保证铸态球墨铸铁件的强韧性要求。
3 铁液的熔炼铁液采用中频感应电炉熔炼工艺,使用尽可能纯净的生铁:P、S、干扰球化元素及各类合金元素要尽可能低;回炉铁一般为同材质的浇冒口、废品或加工的铁屑,便于合金回用降低成本,也有利于铁水成分控制;废钢应尽可能选用单一种类、干净,无砂、锈等杂物的废钢;合金铜、锡是产品性能是否能达到要求的关键,在不利用特殊专用球化剂、孕育剂的情况下,如何确保合金在铁水中均匀,是产品质量和性能稳定的基础,考虑到两种合金在熔炼过程中不烧损,在熔炼前期以合金形式加入到炉底熔炼,可以确保合金在整炉铁水中最大限度的浓度均匀;原铁水化学成分控制原则上CE适中,C 高,Si低,Mn,P,S低,干扰元素Ti低的前提下,炉料配比使C:3.6~3.8%,Si:1.1~1.5%。
4 球化及孕育处理4.1 球化剂的选用球化剂的选用与铁液质量有关:原铁液中含硫量不同,选用含稀土量不同的球化剂,即使利用电炉熔炼,如果使用的生铁中含硫及其它杂质元素多,原铁水含S>0.03%,则选用FeSiMg8RE7的球化剂;S<0.03%时,则选用低稀土的FeSiMg8RE5或FeSiMg8RE3球化剂。
球化剂质量不仅与化学成分有关,而且与粒度也有一定的关系,生产实践过程中,粒度过大,不易快速溶解,使反应熔化时间长,导致球化剂上浮至铁液表面烧损,镁的吸收率下降,影响球化效果;同时,球化剂粒度过小,特别是呈粉末状的比例要严格控制,因为铁水温度高,容易直接烧损,温度低则,直接氧化。
生产过程中球化剂粒度主要还是取决于球化包的大小和球化温度:生产过程中使用300Kg球化包,球化处理温度15100C~15400C,因此球化剂粒度选用5~30 mm,超标粒度的球化剂应小于5%。
4.2球化处理采用通用的堤坝式冲入法球化处理,堤坝高度为100~200mm,球化剂加入球化包堤坝靠炉体一侧后,加0.4%的粒度为3~8mm孕育剂覆盖在球化剂上,用铁叉捣平捣紧,再加放一块厚度8mm专用压板用铁叉捣平,由此可提高镁的回收率20%~30%,球化剂加入量约为铁水重量的1.0%~1.2%。
球化反应时间一般为100秒~120秒,球化时铁水应避免直接冲到球化剂上,球化方式应是铁水大约到1/3时开始球化反应。
由于电炉熔炼的铁水纯度高,表面活度大,铁水容易氧化,因此球化反应结束后,要立即加集渣剂覆盖,及时转包孕育,球化处理后的铁水应该尽可能快的浇注完毕,避免球化衰退和温度降低过多,影响产品质量,一般根据铸件大小,等待浇注的时间,不超过8分钟。
4.3 孕育处理孕育剂选用常用的75FeSi,为提高孕育效果,并合理控制终硅量根据生产条件,采用二次孕育处理方式:采用冲入法球化时在球化剂表面加入0.4%的孕育剂,孕育剂粒度3~8 mm,待冲入铁液进行球化处理时,同时发生孕育作用,在浇注前将铁水从球化包转入浇注包时在铁水表面加入0.2~0.3%的粒度为1~3mm的孕育剂作为二次孕育,可以有效防止孕育衰退提高孕育效果。
由于铸态高强度高韧性球墨铸铁件的性能主要由合金化后的微观基体组织保证,而珠光体数量以及铁素体基体强度主要依靠合金铜、锡的作用体现,适当加强孕育效果,有利于铸件在保证抗拉强度达到600MP的前提下,有较强的韧性,延伸率>10%,并能有效消除碳化物,有利于铁水补缩,减小铁水收缩倾向,防止铸件产生疏松。
5 结果5.1在实际生产过程中,选用优质原材料(生铁、废钢);利用中频电炉进行熔炼,根据壁厚条件,合理设计化学成分,合金化,把球化前铁液成分控制到工艺要求范围内;选用合理的球化孕育处理工艺,实现了铸态高强度高韧性球墨铸铁件的稳定生产,薄壁件及厚壁件化学成分控制要求如下表所示:表1 薄壁件及厚壁件化学成分控制要求铁液C% Si% Mn% P% Cu% Sn% S%薄壁件 3.5~3.7 2.5~2.7 0.15~0.40 <0.05 0.2`0.5 ---- <0.03厚壁件 3.4~3.7 2.6~2.8 0.30~0.50 <0.05 0.2`0.4 0.02~0.05 <0.035.2 不同壁厚铸态高强度高韧性球墨铸铁件化学成分一览表表2不同壁厚铸态高强度高韧性球墨铸铁件化学成分一览表铁液C% Si% Mn% P% Cu% Sn% S%1#壁厚6mm 3.52 2.50 0.15 0.036 0.25 --- 0.0162#壁厚8mm 3.50 2.60 0.20 0.035 0.30 ---- 0.0153#壁厚10mm 3.48 2.62 0.30 0.036 0.40 --- 0.0164#壁厚12mm 3.55 2.60 0.35 0.035 0.50 ---- 0.0155#壁厚30mm 3.53 2.68 0.30 0.035 0.20 0.020 0.0166#壁厚40mm 3.55 2.65 0.35 0.035 0.25 0.027 0.0147#壁厚50mm 3.45 2.70 0.40 0.037 0.30 0.030 0.0158#壁厚60mm 3.60 2.80 0.50 0.037 0.40 0.049 0.013 5.3 不同壁厚铸态高强度高韧性铸件性能、石墨形态、组织一览表表3不同壁厚铸态高强度高韧性铸件性能、石墨形态、组织一览表试样序号性能石墨形态组织bσMPa δ(%) HB 球化率% 石墨大小级别珠光体比例%碳化物比例% 1# 610 17 210 92 7~8 30 ≤1% 2# 625 15 215 95 7 35 ≤1%3# 630 14 220 95 7 35 ≤1%4# 620 15 220 92 6~7 40 ≤1%5# 630 13 230 90 7 45 ≤1%6# 625 14 220 92 7 40 ≤1%7# 615 15 215 92 6~7 35 ≤1%8# 630 12 235 90 6 45 ≤2% 5.4 不同壁厚铸态高强度高韧性铸件本体基体组织金相对比图:图1不同壁厚铸态高强度高韧性铸件本体基体组织金相对比图6 结论6.1在实际生产中通过控制影响铸态微观组织的因素,控制铸态球墨铸铁件的铸态基体组织和力学性能;6.2铸态高强度高韧性球墨铸铁件的生产,要根据不同壁厚条件,合理设计化学成分,选用不同合金化工艺,在熔炼条件一定,保证球化孕育的基础上,通过控制基体组织比例,发挥合金强化作用,满足不同壁厚铸件的高强度高韧性要求。
参考文献[1]吴德海,钱力,胡家骢.灰铸铁、球墨铸铁及其熔炼[M].北京:中国水利水电出版社.2006:64-74[2]《铸造技术标准手册》编委会.铸造技术标准手册.北京.中国物质出版社.2004:90,165作者简介:李永红:男、1979年2月7日、2002年7月毕业于华北工学院、学士、工程师、主要从事铸造技术应用、管理和工艺设计工作。