DACS造船精度控制解决方案
船体结构装配中精度控制的几个措施

此 区域 的 曲 面 线 型 大 ,后 期 矫 正 调 整 难 度 大 。如 果 这 些 误 差 不 在 分 段 制 作 时 加 以控 制 ,到 船 台 大 合 拢 时 ,出现 分 段 错 位 超 出 了规 范 要 求 ,就 需要 通 过 复 杂 的工 艺 进 行
图2 B 0 G1 分段装 配示 意 图
13 在 船 体 中重 要 的结 构对 中部分 .
船 舶 结 构 中 重 要 的 结 构 对 中 部 分 ,通 常 都 位 于 应 力 高 度 集 中的 区域 ,不 仅 规 范 对 这 部 分 区域 的结 构 的 安 装 有 很 严 格 的 要 求 ,而 且 也 是 船 东船 检 检 查 的重 点 部 分 , 例 如 内 底 板 与 内壳 斜 板 、 内壳 斜 板 与 内壳 板 、槽 型 舱 壁 与 壁 墩 斜 板 等 部 分 。但 是 装 配 间 隙 的 存 在 ,以及 焊 接 时 的 焊 脚 、结 构 与 结 构 之 间 有 角 度 安 装 等 因 素 ,使 装 配 时 的精 度 控 制 更 加 困难 。 如果 在 小 合 拢 、 中 合 拢 装 配 时 没 有 控 制 好 精 度 ,到 大 合 拢 阶 段 ,累 积 的误 差 超 过 规 范 允 许 范 围 ,就 需 要 通 过 或 火 工 或 开 刀 进 行 调 整 ,甚 至 需 要 换 板 处 理 , 给 现 场 修 改 带 来 巨 大 的 工 作
3 00m m 。
当 G2m时, >5m 换 板 , 小 板 宽 30 m 最 0m
1 船 体 结构 装 配过 程 中的 特点
1 1 在 平直 的舯 体 部分 .
平 直 舯 体 一 般 位 于 全 船结 构 的 中 间 , 且 该 部 分 的结 构 线 形 变 化 相 对 小 ,平 直 部 分 较 多 且 结 构 形 式 类 似 , 占全 船 结 构 的很 大 部 分 。 因为 建 造 难 度 相 对 较 小 ,为 了 降 低 生 产 成 本 、提 高 生 产 效 率 ,船 厂 一 般 会 将 平 直 舯 体 部 分 分 段 设 计 为 无 余 量 建 造 分 段 ,但 这样 就 对 我 们 的 建 造 装 配3 0 D A)为例 , 直 在平 舯 体处 的D 段 ( 4 D1 D 一 0), 段 (4 s 0, S s 一 1) u ( 一 1) 除 了纵 向每 档 肋 位 放05 段 U1 U1 处 . mm 尺 外 ,在 大 接 缝 处 还 会 施 放 5 0 延 ~1 mm的 补 偿 量 ,来 补 偿 建 造 过 程 的 装 配 间
对于造船精度标准及尺寸精度 全 过程控制
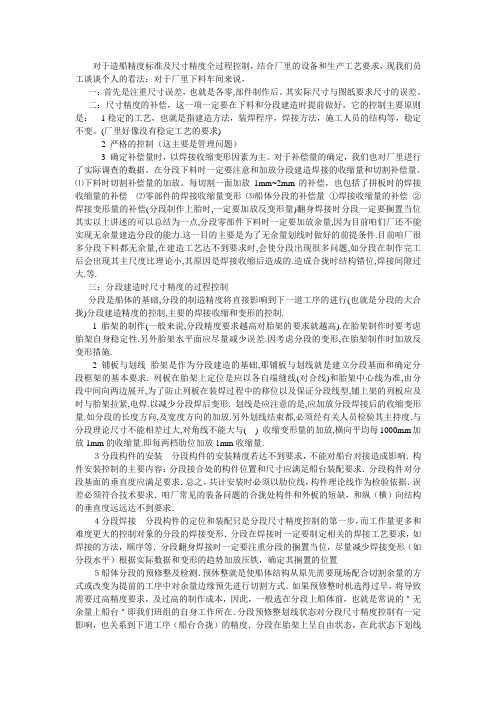
对于造船精度标准及尺寸精度全过程控制,结合厂里的设备和生产工艺要求,现我们员工谈谈个人的看法:对于厂里下料车间来说,一:首先是注重尺寸误差,也就是各零,部件制作后。
其实际尺寸与图纸要求尺寸的误差。
二:尺寸精度的补偿,这一项一定要在下料和分段建造时提前做好,它的控制主要原则是:1稳定的工艺,也就是指建造方法,装焊程序,焊接方法,施工人员的结构等,稳定不变。
(厂里好像没有稳定工艺的要求)2 严格的控制(这主要是管理问题)3 确定补偿量时,以焊接收缩变形因素为主。
对于补偿量的确定,我们也对厂里进行了实际调查的数据。
在分段下料时一定要注意和加放分段建造焊接的收缩量和切割补偿量。
⑴下料时切割补偿量的加放。
每切割一面加放1mm~2mm的补偿,也包括了拼板时的焊接收缩量的补偿⑵零部件的焊接收缩量变形⑶船体分段的补偿量①焊接收缩量的补偿②焊接变形量的补偿(分段制作上胎时,一定要加放反变形量)翻身焊接时分段一定要搁置当位其实以上讲述的可以总结为一点,分段零部件下料时一定要加放余量,因为目前咱们厂还不能实现无余量建造分段的能力.这一目的主要是为了无余量划线时做好的前提条件.目前咱厂很多分段下料都无余量,在建造工艺达不到要求时,会使分段出现很多问题,如分段在制作完工后会出现其主尺度比理论小,其原因是焊接收缩后造成的.造成合拢时结构错位,焊接间隙过大.等.三:分段建造时尺寸精度的过程控制分段是船体的基础,分段的制造精度将直接影响到下一道工序的进行(也就是分段的大合拢)分段建造精度的控制,主要的焊接收缩和变形的控制.1 胎架的制作(一般来说,分段精度要求越高对胎架的要求就越高).在胎架制作时要考虑胎架自身稳定性.另外胎架水平面应尽量减少误差.因考虑分段的变形,在胎架制作时加放反变形措施.2 铺板与划线胎架是作为分段建造的基础,那铺板与划线就是建立分段基面和确定分段框架的基本要求. 列板在胎架上定位是应以各自端缝线(对合线)和胎架中心线为准,由分段中间向两边展开,为了防止列板在装焊过程中的移位以及保证分段线型,铺上架的列板应及时与胎架拉紧,电焊.以减少分段焊后变形. 划线是应注意的是,应加放分段焊接后的收缩变形量.如分段的长度方向,及宽度方向的加放.另外划线结束都,必须经有关人员检验其主持度.与分段理论尺寸不能相差过大,对角线不能大与( ) 收缩变形量的加放,横向平均每1000mm加放1mm的收缩量.即每两档肋位加放1mm收缩量.3分段构件的安装分段构件的安装精度若达不到要求,不能对船台对接造成影响.构件安装控制的主要内容:分段接合处的构件位置和尺寸应满足船台装配要求.分段构件对分段基面的垂直度应满足要求.总之,共计安装时必须以肋位线,构件理论线作为检验依据.误差必须符合技术要求.咱厂常见的装备问题的合拢处构件和外板的短缺,和纵(横)向结构的垂直度远远达不到要求.4分段焊接分段构件的定位和装配只是分段尺寸精度控制的第一步,而工作量更多和难度更大的控制对象的分段的焊接变形.分段在焊接时一定要制定相关的焊接工艺要求,如焊接的方法,顺序等.分段翻身焊接时一定要注重分段的搁置当位,尽量减少焊接变形(如分段水平)根据实际数据和变形的趋势加放压铁,确定其搁置的位置5船体分段的预修整及检测.预休整就是使船体结构从原先需要现场配合切割余量的方式或改变为提前的工序中对余量边缘预先进行切割方式.如果预修整时机选得过早,将导致需要过高精度要求,及过高的制作成本,因此,一般选在分段上船体前,也就是常说的"无余量上船台"即我们班组的自身工作所在.分段预修整划线状态对分段尺寸精度控制有一定影响,也关系到下道工序(船台合拢)的精度.分段在胎架上呈自由状态,在此状态下划线要考虑到脱胎后焊接的收缩变形.分段脱胎后划线要考虑到分段离胎后发生较大的倾斜,则需要使其恢复水平状态,然后划线.划线前还应掌握分段变形情况.作一些必要的记录.对于平直分段,也就是双层底,炫侧分段的划线,一定要在分段应完成包括翻身后封底焊的全部焊接.及水火矫正工作后,才能进行划线.这种状态划线才能保证分段预修整的划线精度,也就是最理想的状态.另外划线时应同时划出与合拢口平行且距离为100mm的检查线和中心线或对合线做好记录.以备切割余量后上船台合拢检验.划线是主尺度应比理论小4mm~6mm也就是加放焊缝间隙,以确定合拢时不出现涨缝现象(只现于横向和纵向的大口处接缝,水平口处接缝除外,因它与分段合拢时水平数据误差有关)。
论船舶制造精度管理及过程控制技术

论船舶制造精度管理及过程控制技术船舶制造是一项复杂的工程,它需要精密的制造技术和严格的质量管理,以确保船舶的性能和安全。
在船舶制造过程中,精度管理和过程控制技术起着至关重要的作用。
本文将探讨船舶制造精度管理及过程控制技术的相关内容。
一、船舶制造精度管理1. 精度管理的重要性船舶制造是一项需要高精度的工程,船舶的性能和安全性直接取决于其制造质量。
精度管理在船舶制造中显得尤为重要。
在船舶制造过程中,对各个零部件的尺寸、形状、位置、表面质量等参数都需要进行严格的控制和管理,以确保最终组装的船舶能够满足设计要求。
2. 精度管理的方法精度管理的方法主要包括以下几个方面:(1)设立合理的精度标准。
在船舶制造中,需要根据设计要求和工艺要求,制定合理的精度标准。
这些标准需要考虑到船舶的使用环境、结构特点、材料特性等因素,以确保最终制造出的船舶能够符合使用要求。
(2)采用先进的测量技术。
在船舶制造过程中,需要采用先进的测量技术对各个零部件进行精密测量,以及时发现和纠正制造过程中的偏差和误差,确保零部件的精度。
(3)严格的质量控制。
对于船舶制造中的各个工序和环节,都需要进行严格的质量控制,以确保在每个制造环节都能够满足精度要求。
3. 精度管理的挑战在船舶制造中,精度管理面临着诸多挑战。
一方面,船舶的尺寸巨大,制造过程中需要考虑到许多特殊因素,比如船体的变形、焊接产生的应力、材料的热变形等。
船舶的制造周期长,制造过程中需要保证各个零部件之间的精度匹配,这对工艺和技术水平提出了更高要求。
二、船舶制造过程控制技术2. 过程控制技术的内容过程控制技术主要包括以下几个方面:(1)数据采集和监控。
通过在制造过程中设置传感器和监测设备,实时采集和监控各个零部件的制造数据,及时掌握制造过程中的各种信息。
(2)数据分析和处理。
通过对采集的数据进行分析和处理,找出制造过程中存在的问题和隐患,及时制定调整措施,确保制造过程的稳定性和可靠性。
船舶建造过程中的精度管理

船舶建造过程中的精度管理摘要:船舶建造过程中的精度管理是确保船舶结构和性能达到设计要求的关键因素之一。
本论文旨在研究船舶建造中精度管理的方法和策略。
首先,介绍了船舶建造中的精度要求,包括尺寸、形状、位置和性能等方面。
然后,讨论了精度管理的关键问题,如测量技术、材料控制、工艺控制和质量保证。
接着,提出了一些常用的精度管理工具和技术,如三维扫描、数字化建模和自动化控制系统。
最后,总结了船舶建造中精度管理的挑战和未来发展方向。
通过有效的精度管理,可以提高船舶的质量和性能,降低建造成本,提高竞争力。
关键词:船舶建造、精度管理、测量技术、材料控制、质量保证。
引言:船舶建造一直以来都是一项高度复杂的工程,而精度管理在此过程中占据着至关重要的地位。
船舶的尺寸、形状和性能直接影响其安全性、经济性以及环境友好性。
因此,确保船舶达到设计要求的精度水平至关重要。
本文将探讨船舶建造中的精度管理,包括其重要性、方法和工具。
精度管理不仅关乎船舶制造商的竞争力,还直接影响着全球海运行业的可持续性发展。
通过深入研究精度管理的各个方面,我们能够更好地理解和应对这一挑战,为船舶建造领域的未来提供更坚实的基础。
一、船舶建造中的精度要求与挑战船舶建造一直以来都是一项高度复杂的工程,要求船体的尺寸、形状、位置和性能达到预定的设计要求。
这些精度要求不仅影响船舶的性能,还关系到船舶的安全性、经济性和环保性。
因此,精度管理在船舶建造过程中占据着至关重要的地位。
本节将深入探讨船舶建造中的精度要求以及相关挑战。
1、船舶建造中的精度要求是多方面的,包括尺寸精度、形状精度、位置精度和性能精度。
在尺寸精度方面,船体的长度、宽度、高度等尺寸必须与设计图纸完全一致,以确保船舶的结构稳定性和航行性能。
形状精度要求关系到船舶的流体动力学特性,如船体的几何形状对水流的影响。
位置精度涉及到各种船舶组件的安装位置,如引擎、船桥等,以确保它们的功能正常运行。
最后,性能精度包括船舶的速度、燃油效率、载重能力等方面,这些性能指标直接影响着船舶的商业竞争力。
船舶制造精度管理及过程控制技术分析

船舶制造精度管理及过程控制技术分析摘要:在船舶制造精度方面,所提出的要求以及标准逐渐提高,对于船舶制造企业带来极大的挑战。
为适应当前的需求,需要改善传统的制造理念,使用现代化的管理方式,提升对于精度管理以及过程控制的专业性。
本文主要通过分析船舶制造精度管理的作用,说明在精度管理以及过程控制技术的应用措施,以供参考。
关键词:船舶制造;精度管理;过程控制技术引言:在国际贸易运输工作中,由于船舶运输的成本相对较低,在贸易运输中占据重要地位,且具有广阔的发展前景。
对此,在船舶制造工作中,需要适应时代发展的需求,顺应时代发展的趋势,加强对精度的管理以及过程的控制。
船体的精度控制作为船舶制造的重要工业,对于建造的质量具有直接影响,在日后工作中,需要加强对该环节的重视。
一、船舶制造精度管理的作用船舶制造领域相对于其它领域具有一定特殊性,该项工作中涉及多个部分的专业知识。
船舶作为海上运输的关键工具,建造体积巨大,且容易受到天气因素的影响。
对此,在船舶建造过程中对于安全性的要求极高。
精度管理主要在整体建造期间,将制造的余量用补偿量进行替代,利用补偿扩张的方式,提升对船舶精度的控制。
通常来说,数据是进行各类机械建造的核心内容,如果无法保证数据的准确性和真实性,对于机械制造的安全性和可靠性也会造成严重影响,在正式投入使用后极易出现安全事故,对于人员的生命和财产安全造成威胁。
数据是最基础的工作内容,通过对模型的应用,对于获取的数据信息进行分析,以此进一步提升数据的精准性,提高工作开展的安全性。
在精细化管理工作中,需要确保数据操作步骤的准确性,减少数据误差的几率,以此提高船舶制造工作的整体质量[1]。
二、船舶制造精度管理及过程控制技术应用措施(一)加强监测技术,强化过程控制检测工具的质量以及使用情况极易影响到船舶制造的精度,而科学合理的测量方式是获得补偿计算数据的主要方式。
检测技术直接影响了船舶制造的整体质量。
对此,为满足对精度的控制,需要改善传统接触式的测量方式,使用新型非接触式的测量方式。
论船舶制造精度管理及过程控制技术
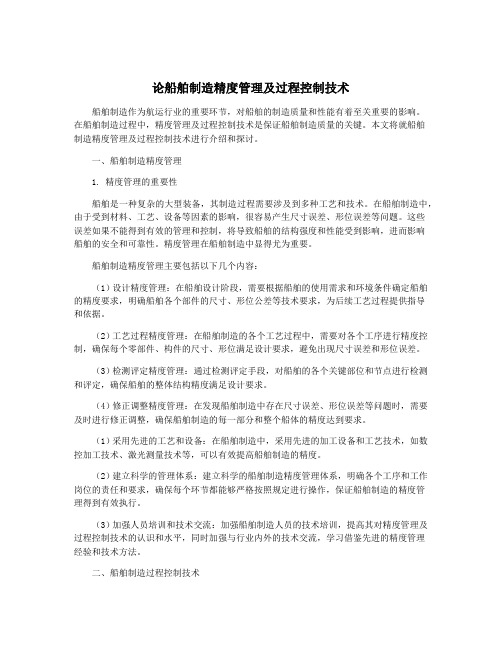
论船舶制造精度管理及过程控制技术船舶制造作为航运行业的重要环节,对船舶的制造质量和性能有着至关重要的影响。
在船舶制造过程中,精度管理及过程控制技术是保证船舶制造质量的关键。
本文将就船舶制造精度管理及过程控制技术进行介绍和探讨。
一、船舶制造精度管理1. 精度管理的重要性船舶是一种复杂的大型装备,其制造过程需要涉及到多种工艺和技术。
在船舶制造中,由于受到材料、工艺、设备等因素的影响,很容易产生尺寸误差、形位误差等问题。
这些误差如果不能得到有效的管理和控制,将导致船舶的结构强度和性能受到影响,进而影响船舶的安全和可靠性。
精度管理在船舶制造中显得尤为重要。
船舶制造精度管理主要包括以下几个内容:(1)设计精度管理:在船舶设计阶段,需要根据船舶的使用需求和环境条件确定船舶的精度要求,明确船舶各个部件的尺寸、形位公差等技术要求,为后续工艺过程提供指导和依据。
(2)工艺过程精度管理:在船舶制造的各个工艺过程中,需要对各个工序进行精度控制,确保每个零部件、构件的尺寸、形位满足设计要求,避免出现尺寸误差和形位误差。
(3)检测评定精度管理:通过检测评定手段,对船舶的各个关键部位和节点进行检测和评定,确保船舶的整体结构精度满足设计要求。
(4)修正调整精度管理:在发现船舶制造中存在尺寸误差、形位误差等问题时,需要及时进行修正调整,确保船舶制造的每一部分和整个船体的精度达到要求。
(1)采用先进的工艺和设备:在船舶制造中,采用先进的加工设备和工艺技术,如数控加工技术、激光测量技术等,可以有效提高船舶制造的精度。
(2)建立科学的管理体系:建立科学的船舶制造精度管理体系,明确各个工序和工作岗位的责任和要求,确保每个环节都能够严格按照规定进行操作,保证船舶制造的精度管理得到有效执行。
(3)加强人员培训和技术交流:加强船舶制造人员的技术培训,提高其对精度管理及过程控制技术的认识和水平,同时加强与行业内外的技术交流,学习借鉴先进的精度管理经验和技术方法。
精度控制对于船舶建造质量优化的措施

2))建立自检、互检和复验的制度,防止个人思想不集中和疲劳等人为因素而发生差错;
3)针对船舶特点和难点,对放样工进行预先培训,使其适应该船的放样工作,保证放样方法的正确性;
1)精确的统计气割、线状加热和设备偏差等加工过程中产生的材料收缩量和油压机、滚弯机的闷头余量,确定合理的加工补偿余量;
2))制定零件号料、切割、刨边和弯曲成形(包括热弯和冷弯)精度标准和允许公差范围.作为加工精度控制的标准(理论值+部装余量补偿值十分段余量补偿值+船台余量补偿值);
3))有针对性地对加工人员进行培训。一是教育他们怎样识图;二是教育他们认识精度控制的重要性;三是教育他们按照图纸的要求检验零件的加工精度是否达标;
4)建立反馈信息系统,分析分段合扰不上的原因,确定改进措施,提高精度控制水平,从而使船体建造质量得到进一步的提高。
结论
精度控制是一项复杂的系统工程,它贯穿于船舶制造的整个过程中,而且每个阶段相互牵连,相互影响。同时它涉及的面非常广,既包括科学分析和总结补偿量的分布,合理制订反变形控制量,又要有系统的精变控制体制和合理的控制方法来检测产品是否符台要求,其目的是保证不让次品流人下一道程序。精度控制的含义是控制过程中的控制。精度控制的最主要目的是持续的提高生产效率、降低成本、提高建造质量。精度控制反馈信息的分析结果可指导设计和工艺方法的调整,从而协调各分道生产线的工艺流程。
关键词:无余量;尺寸精度控制;焊接变形;误差;补偿量;建造质量
1引言
在船舶建造早期阶段,为了确保船舶整体尺寸,船舶分段建造师一般采用留余量建造方式。在合拢阶段时,根据船体尺寸变换情况,把合拢后多余的部分进行割除,即为留余量建造法。一般来说采用留余量建造法时,其调整工作占据船体建造工作总工时的很大比例。特别是在船台合拢阶段,仅调整工作工作量即占总船体工作量的40%~50%。并且留余量建造法不仅浪费材料,而且增加了施工人员的工作强度。因此,在保证船体整体尺寸的同时,留余量建造阻碍了船台乃至船舶建造效率继续提高,成为船舶建造效率的瓶颈。
船舶建造精度控制
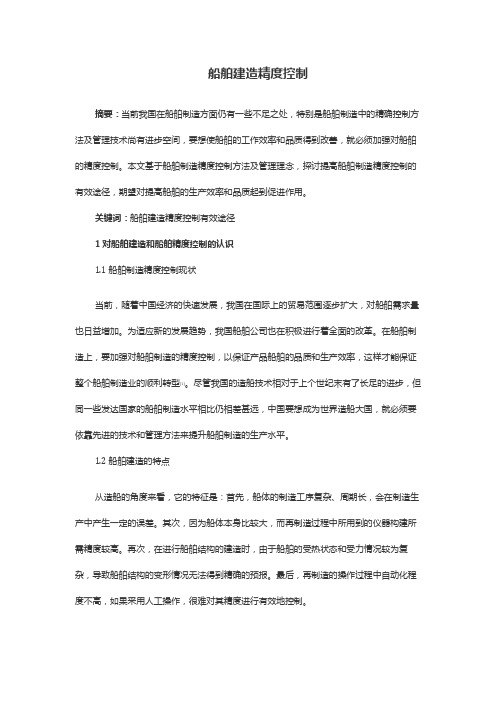
船舶建造精度控制摘要:当前我国在船舶制造方面仍有一些不足之处,特别是船舶制造中的精确控制方法及管理技术尚有进步空间,要想使船舶的工作效率和品质得到改善,就必须加强对船舶的精度控制。
本文基于船舶制造精度控制方法及管理理念,探讨提高船舶制造精度控制的有效途径,期望对提高船舶的生产效率和品质起到促进作用。
关键词:船舶建造精度控制有效途径1对船舶建造和船舶精度控制的认识1.1船舶制造精度控制现状当前,随着中国经济的快速发展,我国在国际上的贸易范围逐步扩大,对船舶需求量也日益增加。
为适应新的发展趋势,我国船舶公司也在积极进行着全面的改革。
在船舶制造上,要加强对船舶制造的精度控制,以保证产品船舶的品质和生产效率,这样才能保证整个船舶制造业的顺利转型[1]。
尽管我国的造船技术相对于上个世纪末有了长足的进步,但同一些发达国家的船舶制造水平相比仍相差甚远,中国要想成为世界造船大国,就必须要依靠先进的技术和管理方法来提升船舶制造的生产水平。
1.2船舶建造的特点从造船的角度来看,它的特征是:首先,船体的制造工序复杂、周期长,会在制造生产中产生一定的误差。
其次,因为船体本身比较大,而再制造过程中所用到的仪器构建所需精度较高。
再次,在进行船舶结构的建造时,由于船舶的受热状态和受力情况较为复杂,导致船舶结构的变形情况无法得到精确的预报。
最后,再制造的操作过程中自动化程度不高,如果采用人工操作,很难对其精度进行有效地控制。
1.3船舶制造精度控制的实质内容我国有关部门制定了船舶制造精度控制的具体内容和标准,以保证产品。
船舶制造精度管理控制的本质是:既要进行补偿数量的计算与分析,又要监督船舶制造的全过程,还要保证船体制造的精确性。
通过严格、精细的计量方法,保证船舶的品质达到要求,从而提高船舶的生产效率[2]。
船舶制造精度控制的本质就是收集船舶生产过程中的损失和分配数据,由相关的技术人员根据这些信息进行生产调整,从而合理地分配船体制造的损失,收集造船环境的数据,对每一道工序的数据进行汇总进行科学而合理的对比,发现其中的缺陷,并进行纠正。
造船精度管理关键问题及对策

造船精度管理关键问题及对策摘要:精度管理与控制对船舶制造的重要性不言而喻,借助于有效的精度控制技术,能够有效寻找出船舶精度管理的重难点以及纰漏点,这对于及时发现并解决相关问题,提升船舶制造质量具有极为重要的意义。
本文简单探讨了提升船舶制造精度控制的有效途径,希望能为造船精度管理带来一定的参考价值。
关键词:造船工艺;精度控制;问题;对策引言在造船的过程中严格的控制船舶的精度,可以有效的提高船舶的质量,当船舶的精度得到控制,后期现场修整的工作量也会随之降低,从而提高了生产船舶的效率,同时也达到了为船舶企业实现收益最大化的目的,随着中国经济的发展,市场对船舶的需求量也越来越高,但是我国生产出来的船舶相对于其他发达国家所造的船舶,在质量还存在很大的缺陷,这往往都是由于船舶在制造过程中,精度管理控制的不够到位而导致的。
1精度管理的内涵造船精度管理就是以造船精度标准为基本准则,通过科学的管理方法及先进的工艺技术手段,对造船的全过程进行尺寸精度控制,达到提高工作效率、降低船舶建造成本,保证船舶产品质量的目的。
解决造船企业船舶建造中的精度问题主要有两大努力方向,第一是精度管理方法论研究,主要研究如何有进行效精度管理,既研究精度管理理论又研究管理方法,以及管理效果评价手段;第二是船舶高精度测量技术、船舶建造中对各类变形的预测预防技术,需要数学、测量学、力学和热学等多学科提供理论上支撑,将学科研究成果与船舶建造工艺的融合。
2我国制船业的现状因为起步较晚,中国造船业的理论和技术显得很是薄弱,缺乏专业性强的船舶制造设计人才,这使得我国的造船工作进展缓慢。
由于造船业需要投入很多的资金、人力和资源,中国造船业正在以缺乏先进技术为支撑和支持的条件下挣扎。
所以,近些年来,中国加强了与国际先进国家的合作,投入了大量财力和精力,加强了造船精度控制和管理,创造了具有高科技、高性价的船舶。
我国正在向造船强国转变,造船规模也在朝着巨大的总体建设方式发展。
基于DACS平台中小船厂船体分段建造精度管理研究

Байду номын сангаас
职教 与成 教
基于 D S平台巾小船厂船傩分段建造精度管理研究 AC
南通航 运 职业技 术 学院 傅 晓斌
[ 摘 要] 本文通过对船舶建造精度控 制工艺的概念和 内容 的阐述 , 分析 国内精度 管理 和研 究水平的进展和现状 , 讨 了制约 中小 探 型船厂发展精度控制技术的因素, 介绍 了 D S精度控制 系统, AC 并提 出了一些相应的对策。 [ 键 词 ] 体建 造 精 度控 制 关 船
一
、
3 船体合拢精度检查控制存在问题 、 传统测量方法效率低下 , 占用 吊机时间较长 ; 需要在现场对余量进 行切割 , 需要 对分段进行复位作业 ; 多分段需 要进行二次定位 , 响 很 影 船 台周期 ;传统 的测量手段很难对船体分段在船体成型过程中的变化 进行有效统计 , 为反变形的施放及无余量生产提供数据支持。 四 、 AC D S精 度 控 制 系 统 特点 1 可以同时测量角度和距离, 、 且精度较高 造船 用的全 站仪 测角精度 最 高能到 05秒 ,测距 精度 最高达 到 . 1 m 1p , 目前世界上精度最高的全站仪 , m +p m 是 并全部 自动显示和记录 , 无需人工读数 和记 录。 2 非接触式测量 , 、 想测哪里就测哪里 , 令测量人员更轻松 、 更安全 全站仪的激 光测距技术 , 以测量 2 0 5 0 可 0 — 0 米的物体表面 , 且专利 的 pn o t ipi 技术可 以精确测量船体的边缘 , n 角落以及一些难 以触及的地
方。
精度 控 制 研 究 是 改进 造 船 工 艺 水 平 的基 础 ,深 入 研 究 船 舶 制 造 中 的 精
度问题 , 分析造船工艺 的科学性和合理性 , 发现问题 , 找出改进措施 , 进 而为施工工艺改进提供理论基础和技术支持 。 推广先进的精度造船技术就是应用技术创新战略 ,是我国造船缩 短造船周期 、 降低成本 和提高竞争力的主要方法之一。 船舶建造精度控 制技术在我 国的船舶建造技 术中具有重要 的意 义,该项技术是适应我 国船舶工业跨越式发展急需解决 的重要课题之一 ,也是一项需要长期 持续 研 究 的 课 题 。 二 、 内 目前 研 究状 况 国 国内开展船舶建造精度控制技术研究 的起步较晚 。上世纪六十年 代中期 , 国开始从国外 引入船体建造精度管理的概念 , 我 但是 由于对这 概念缺乏足够的认识 , 忽视 了这项技术有其极其丰富的技术内容 , 而 片面的强调有关工艺部分 。 17 在 9 8年初开始 国内兴起 了一股研究和推 行精度造船的热潮 , 大连 、 沪东 、 江南和上海船厂成立课题 组研 究精度 造船 , 18 到 9 2年取 得了一定 的成就 , 实现 了货舱区分段精度造船 , 艏艉 分段预修整后上船台。但我 国在精度造船方面还没有形成一个完善的 数据库 和一整套系统支持且大多局 限于尺寸精度的研究 , 日、 与 韩先进 造船强 国还有一定差距 。 分段精度控制是船体精度控制的基础 , 国内的 分段精度控制技术 目前仅 限在船体 中部平直货舱 区域 以补偿量代替余 量, 而分段精 度控制包括 “ 主尺寸 、 线形 和结构位 置” 三方 面的控 制内 容。[ 2 1 国内研究也限于主尺寸控制 的理论方面 , 对分段的线形和结构位 置研究较少 。 国内的精度造船研究仅限于工具和技术方面, 个别造船公 司在船体建造精度控制 中的对合基准线控制技术 、全船余量和补偿量 加放技术 、 变形和反变形技术 以及在精度控制上的统计技术等。[ 3 1 由于 精度造船技术作为 日韩造船业 的核心技术 ,对 中国造船业进行技术封 锁, 中国造船业无法学 习其先进的精度控制方法和技术。国内各家船舶 企业之 间技术设施 的差异性 , 也基本上处于各 自发展的状态 。 三、 中小 型 船 厂 目前 在 分 段 精 度控 制 方面 的 问题 由于 软 硬 件 的 差距 , 测 量 与 精 度 控 制 方 面 更 加 薄 弱 , 本 还 是 处 在 基 于事前加余量建造 , 事后测量切割的状态 , 并且缺乏对精度控制的分析 研究能力 。 对船体分段精度控制体系 的研究方面基本是空 白, 也没有 可操作 的控制方法 ,这样对 巾小型船厂船体分段精度控制体系和方法 的研究就很有意义和必要 了。 1分段建造精度控制 的问题 、 非数字化的测量 , 其结果要手工记录 , 不便于与现代的造船设计软 件及现代的数据处理 分析方法结合 , 不利于形成有效的数据库 ; 钢尺量 距的准确性不稳定 , 而且非 常不方 便 , 对于大型船只 的结构件 , 钢尺无 法完成准确的测量; 数据采集需要的人员较多 , 工作效率低 下。 2 分段及总段精度检查控制存在的问题 、 分段体必须按 照特定要求摆放 , 否则不好进行测量 ; 数据报表需要 人工计算 , 不方便与设计数据 进行 直接对 比; 效率 比较低 , 容易出现错 误, 造成工期延误 ; 由于测量手段及数据处理方式 的落后 目前还无法形 成有效 的精度管理机制及精度数据循环。
船舶建造精度控制技术质量的优化措施

船舶建造精度控制技术质量的优化措施摘要:现代船舶建造具有工序多、制造复杂、工件大的特点。
钢料经预处理、零件加工、部件组装、分段组装、船台合拢才能形成整艘船体。
其间要经过多工种的加工,包括切割、冷热加工、焊接、吊装等,期间还要经过数次车辆运输、吊车吊运。
由于船体或设备部件工件大,对船舶装配误差、加工误差、运输过程中的变形误差等的累积控制一直是船舶建造中的难题。
如何保证船体部件、船舶分段、整船的精度,一直是造船界所共同研究的课题。
近几十年,随着船舶建造新规范和标准要求的实施以及现代船舶测量技术的发展,在理论计算、数据积累、经验估算方面都已取得了一些进展并应用于船舶实践,对有效地开展船舶精度管理起到了十分积极的作用。
关键词:无余量;尺寸精度控制;焊接变形;误差;补偿量;建造质量一.引言在船舶建造技术早期阶段,为确保船舶整体尺寸,船舶分段建造师一般采用留余量建造方式,在合拢阶段根据实际情况,把合拢部位多余的部分进行割除,即采用留余量建造法。
一般来说采用留余量建造法,其调整工作占据船体建造工作工时的很大比例。
特别是在船台合拢阶段,仅调整工作即占船体工作量的40%-50%。
不仅如此,留余量建造法浪费材料,对分段建造质量影响很大,增加了施工人员的工作强度。
并且由于火焰加工,造成了结构的变形。
因此,留余量建造在保证船体尺寸的同时,在建造技术精益求精的今天,成为提高船台乃至船舶建造效率的瓶颈。
而企业是否采用无余量建造法,成为企业建造技术是否先进的重要标志之一。
而对于尺寸精度的控制则是这项技术的关键。
分段能够实现无余量上船台,一方面可以减少船台修正工作,如划线、余量切割临时搭载脚手架等,从而节省吊装时数,是分段快速精准、可靠定位,提高船体搭载速度和质量,降低安全事故系数,减少生产成本;另一方面为预舾装在分段上精确定位创造了条件,这样可使舾装件在船台合拢尺寸准确度大大提升,也减少了舾装件的修补工作,有次提高了舾装件的安装质量。
船舶制造精度管理及过程控制技术分析
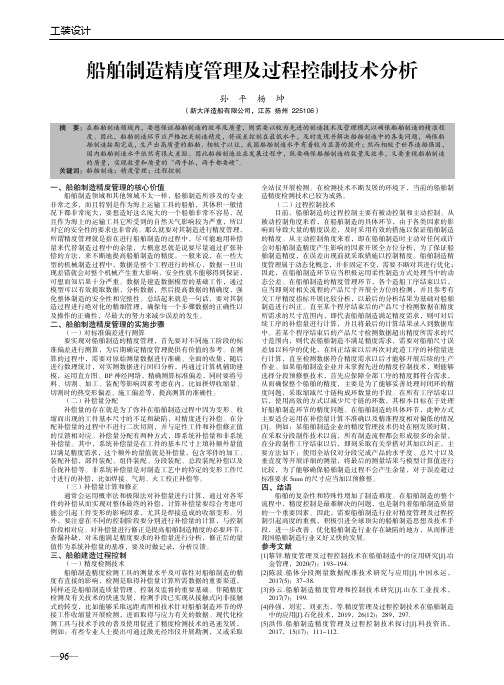
工装设计—96—船舶制造精度管理及过程控制技术分析孙 平 杨 坤(新大洋造船有限公司,江苏 扬州 225106)一、船舶制造精度管理的核心价值船舶制造领域和其他领域不太一样,船舶制造所涉及的专业非常之多,而且特别是作为海上运输工具的船舶,其体积一般情况下都非常庞大,要想造好这么庞大的一个船舶非常不容易,况且作为海上的运输工具它所受到的自然天气影响较为严重,所以对它的安全性的要求也非常高。
那么就要对其制造进行精度管理,所谓精度管理就是指在进行船舶制造的过程中,尽可能地用补偿量来代替制造过程中的余量,大概意思就是说要尽量通过扩张补偿的方法,来不断地提高船舶制造的精度。
一般来说,在一些大型的机械制造过程中,数据是整个工程进行的核心,数据一旦出现差错就会对整个机械产生重大影响,安全性就不能够得到保证,可想而知后果十分严重。
数据是建造数据模型的基础工作,通过模型可以有效提取数据,分析数据,然后提高数据的精确度,强化整体制造的安全性和完整性。
总结起来就是一句话,要对其制造过程进行绝对化的精细管理,确保每一个步骤数据的正确性以及操作的正确性,尽最大的努力来减少误差的发生。
二、船舶制造精度管理的实施步骤(一)对标准偏差进行测算 要实现对船舶制造的精度管理,首先要对不同施工阶段的标准偏差进行测算,为后期确定精度管理提供有价值的参考。
在测算的过程中,需要对原始测量数据进行准确、全面的收集,随后进行数理统计,对实测数据进行回归分析,再通过计算机辅助建模,运用直方图、BP 神经网络,精确测算标准偏差,同时要将号料、切割、加工、装配等影响因素考虑在内,比如拼焊收缩量、切割时的热变形偏差、施工偏差等,提高测算的准确性。
(二)补偿量分配 补偿量的存在就是为了弥补在船舶制造过程中因为变形、收缩而出现的工件基本尺寸的不足和缺陷,对精度进行补偿。
在分配补偿量的过程中不进行二次切割,并与定性工件和补偿修正值的反馈相对应。
补偿量分配有两种方式,即系统补偿量和非系统补偿量。
船舶建造精度控制方法

船舶建造精度控制方法前言:在船舶建造中,落实有效的精度控制是很重要的,实际精度除了会影响建造质量,还对造船业和世界航运业的发展具有重要影响。
提高造船精度可确保安全生产、提升建造质量、减少实际花费。
船舶建造过程中要做好每一个环节,减少累积误差,才能有效实现精度控制。
同时,每一道工序中,都要重视精度问题,落实好控制措施,避免误差的产生。
本文阐述精度控制的重要性,深入分析了各种控制方法和具体内容。
关键词:船舶建造;精度管理;控制方法摘要:我国造船业发展迅速,为促进航运业发展提供了有力支撑。
造船精度关系到船舶的整体建造质量,对造船业和航运业的发展也具有重要影响。
在现代交通运输业和造船业竞争日益激烈的背景下,提升造船精度变得尤为关键,只有这样,才可以保证船舶的质量能符合航运的需要。
对此,造船企业应当加大对精度问题的重视,使用先进的工艺和控制方法,提高精度控制效果。
提高建造工艺的精度是提高造船质量的重要保证。
1船舶建造的发展1.1船舶建造的特点船舶建造是一个复杂的系统工程。
船舶建造包括钢材预处理、数控切割、加工等多道工序。
待建造成型后,还需要进行最后的精度测量,这是验收的重要一步。
在进行船舶建造时,需根据吊车能力和船舶的结构特征,完成对船舶的设计工作,并形成完善的方案,确定制作流程。
由于船舶结构的复杂性,部分零件需进行热处理、冷加工和焊接,这会带来一定的尺寸误差、结构误差和形状误差等,导致船舶精度的控制难度增加。
根据船舶建造这一特点,需要落实好精度控制,减小建造的误差,避免存在质量问题。
1.2重要意义目前大多数中国造船企业非常重视建造的精度控制技术,这些企业以建造精度为控制目标,通过精度控制技术和适当的建造工艺实现对不同部件的控制。
此外,一部分中国造船企业还会学习国外先进造船技术和精度控制技术,在造船过程中进行更加全面的检查和验证,这样能够确保船舶的质量,以及在使用时的可靠性。
通过先进的精度控制方法,合理设计控制的流程,以此来分析建造时会出现的误差和热变形,然后在进行有效的控制,来降低误差的数值,确保建造的精度。
船舶制造精度管理及过程控制技术

船舶制造精度管理及过程控制技术摘要:随着社会经济和技术的快速发展,船舶制造业发展迅速。
船舶制造对精度的要求越来越高。
船舶制造企业应引进先进理念,提高科学管理水平,有效优化生产工艺。
只有管理理念和生产技术的有效结合,才能提高船舶制造的过程管理和控制质量。
确保制造质量完全符合船舶要求。
随着国家整体生产水平的提高,造船业取得了显著进步,但在过程控制的精度管理方面仍存在许多缺陷和不足,最终生产质量仍有显著提高。
因此,船舶制造企业不仅要加强新技术的开发和应用,还要分析过程管理中存在的问题,以完善我国的船舶制造体系。
关键词:船舶制造;精度管理;过程控制技术精度管理是在制造过程中运用科学的管理理念,控制生产过程,避免施工过程中出现问题,减少修整工作量,提高生产效率,保证质量。
精度管理的核心是精密控制技术,造船业的转型可以通过技术应用实现。
一、精度管理的内涵船舶本身的制造是一项复杂而专业的任务,精度是一项难以控制的指标。
操作的准确性和船舶的质量无法保证。
精度管理是指通过补偿而不是使用中的剩余量逐渐增加补偿范围,从而控制船体结构的位置精度。
精细化管理、加强补偿量分配和计算、关注关键数据和避免潜在错误,确保数据的准确性。
测量数据对补偿的量分配和计算有一定的影响。
只有保证数据的准确性,才能保证项目的整体质量。
数据收集只是主要任务。
必须根据数据建立适当的模型,并用于数据分析以完成计算。
然后将反推法补偿分配给每个阶段,并按特定顺序使用。
在精度管理领域,不仅要精细化管理,还要补偿分配关注,加强技术研究和创新,严格有效地管理误差,提高管理精度,提高船舶质量。
二、船舶制造精度管理要点分析在船舶制造的现阶段,为了提高制造精度,通过适当的补偿形式减少制造过程中存在的尺寸差异,以提高船舶质量,降低生产成本。
1.标准偏差预算。
在制造过程中,精度管理的第一步是规划生产和加工的每个阶段的标准偏差。
在标准偏差规划过程中,需要收集生产、加工和实际制造过程中获得的大量信息,然后使用相关软件进行统计分析,建立数据模型,并在计算机上实施准确的标准偏差规划。
造船精度软件系统介绍

造船精度控制系统介绍造船精度的控制,从测量学的角度来说属于精密工业测量的范畴,主要是要对船体的部件进行坐标,长度,垂直度等造船过程中所需要的尺寸数据进行测量和计算,并形成精度控制数据分析库,从而达到对船体尺寸进行有效的控制,使之符合设计的要求,并对数据进行一定的分析,为提高造船的速度和质量提供必要的数据支持。
从测量的内容来分,主要包含划线测量、分段测量、搭载定位等主要三大内容,划线测量主要是在分段制造时对原材料进行激光划线,确定部件的形状和大小,为切割划出轮廓线,目前一般采用激光经纬仪、手持测距仪、激光水准仪以及钢卷尺进行测量;分段测量主要是对船体分段的端口的关键点进行测量,以便确定建造分段与设计分段的差值,然后进行预修整,也就是我们通常所说的进行余量切割,之后才可以将分段进行吊装搭载;而搭载定位主要是在船台船坞进行分段搭载的时候,需要确定搭载分段的位置,以便和船体正确合拢而进行的测量工作,一般是在中合拢或大合拢时采用。
分段测量和搭载定位在传统的造船中,主要采用经纬仪和钢尺以及吊大锤进行测量,随着测量技术的发展,日韩等较先进造船厂已普遍采用全站仪配合计算机辅助系统(即测量软件)进行精度控制,日韩在精度造船方面已经积累了很丰富的经验,我们国家的造船业目前正在从余量造船向数字造船转变,最终发展为精度造船。
精度造船是造船业精度控制发展的重要方向,做好数字化精度控制,是发展精度造船的重要基础,就我国造船业精度控制现状而言,各大船厂都在进行精度控制的改革,力求先做到数字造船,积累一定的经验后,在逐步过渡到精度造船。
数字造船就离不开数字化的硬件设备和软件,全站仪和数字化造船软件是数字造船的数据采集基础。
全站仪是一种能够采集空间点三维坐标的光电设备,不需要对测量的物体进行接触,就能够获得2MM左右的测量精度,由于其操作简单,方便快捷,精度可靠,所以被广泛的应用于造船行业,日韩的大型船厂拥有全站仪的数量都是100多台,国内的上海外高桥,长青造船厂等也拥有数十台全站仪。
船舶建造精度控制技术

船舶建造精度控制技术(1)第一章现代船舶建造精度管理基础1、现代船舶生产中,船舶零件为了尽量减少修整工作量,各国在取得大量船舶生产实践测量数据的基础上,运用数理统计方法,逐步以不需修割的零件补偿量代替余量的方法来控制造船偏差,这样逐步发展形成了一门技术称为造船精度管理技术。
2、现代船舶建造精度管理技术是以船舶建造理论为基础的系统工程,是建立在管理学、测量学、金属材料学和可靠性理论基础之上的综合性学科。
3、造船精度管理是当代造船的重大新技术之一,它主要是在船舶建造过程中加放尺寸补偿量取代余量,通过合理的工艺技术和管理技术,对船体零件、部件和主尺度进行精度控制,以提高建造质量,最大限度地减少现场修整的工作量,缩短船舶建造周期,降低船体建造成本。
4、精度造船简单地说就是在船舶建造过程中用补偿量代替余量,逐步增加补偿量的使用范围,并控制船体结构位置精度。
以最少的成本将船舶建造的主尺寸偏差、线形偏差和结构错位控制在标准范围内,保证船舶质量。
精度管理是一项系统工程,对船舶制造企业而言,关键是全面、全过程推行精度控制,其核心是实施造船精度设计。
5、船舶建造精度管理的对象为船舶在建造过程中产生的收缩变形、扭曲变形和角变形。
其内容包括健全精度管理体系、建立精度管理制度、完善精度检测手段与方法、提出精度控制目标、确定精度计划、制订精度标准、制订预防尺寸偏差的工艺技术措施和精度超差后的处理措施等。
6、通过船厂实践表明,开展船体建造精度管理可以使装焊工效提高1~2倍,使船体建造总劳动量减少10%左右。
7、精密工程测量是采用非常规的测量仪器和方法,使其测量的绝对精度达到毫米级以上要求的测量工作。
8、PDCA质量循环理论。
PLAN代表计划、DO代表执行、CHECK代表检测、ACTION代表改进,表示质量管理持续改进的一个循环。
9、装配间隙尺寸(封闭环)=理论尺寸(组成环)-实际尺寸(组成环)+焊接补偿值(组成环)10、船舶建造精度管理是一门交叉学科,涉及很多新工艺、新技术。
船舶制造精度管理及过程控制技术

船舶制造精度管理及过程控制技术发布时间:2021-12-29T07:29:16.864Z 来源:《防护工程》2021年23期作者:江彭[导读] 在船舶制造的整个流程中,精度控制是最难解决的问题,也是制约着船舶制造质量的一个重要因素。
因此,在船舶制造环节当中,相关人员应严格把关制造精度,将误差控制在最低水平,及时发现并解决船舶制造中的各类问题,确保船舶制造按期完成,生产出高质量的船舶。
基于此,下文将对船舶制造精度管理及过程控制技术展开一系列的分析。
江彭扬州中远海运重工有限公司江苏省扬州市225200摘要:在船舶制造的整个流程中,精度控制是最难解决的问题,也是制约着船舶制造质量的一个重要因素。
因此,在船舶制造环节当中,相关人员应严格把关制造精度,将误差控制在最低水平,及时发现并解决船舶制造中的各类问题,确保船舶制造按期完成,生产出高质量的船舶。
基于此,下文将对船舶制造精度管理及过程控制技术展开一系列的分析。
关键词:船舶制造;精度管理;过程控制技术随着现代科技的不断发展,船舶行业的制造进步十分显著,船舶的制造不断地进行改进和创新,但也正是因为船舶制造各个方面的变化过于频繁,所以在这个领域的专业人员必须充分了解每一次变化,紧跟船舶制造创新的步伐,根据改变不断地进行调整适应,优化原有的管理方式,优化原有的技术发展,不断地推动船舶制造业的持续性发展。
1 船舶制造精度管理的核心价值船舶制造行业中精度管理指在进行船舶制造的过程中,尽可能地用补偿量来代替制造过程中的余量,大概意思就是说要尽量通过扩张补偿的方法,来不断地提高船舶制造的精度。
一般来说,在一些大型的机械制造过程中,数据是整个工程进行的核心,数据一旦出现差错就会对整个机械产生重大影响,安全性就不能够得到保证,可想而知后果十分严重。
数据是建造数据模型的基础工作,通过模型可以有效提取数据,分析数据,然后提高数据的精确度,强化整体制造的安全性和完整性。
总结起来就是一句话,要对其制造过程进行绝对化的精细管理,确保每一个步骤数据的正确性以及操作的正确性,尽最大的努力来减少误差的发生。
- 1、下载文档前请自行甄别文档内容的完整性,平台不提供额外的编辑、内容补充、找答案等附加服务。
- 2、"仅部分预览"的文档,不可在线预览部分如存在完整性等问题,可反馈申请退款(可完整预览的文档不适用该条件!)。
- 3、如文档侵犯您的权益,请联系客服反馈,我们会尽快为您处理(人工客服工作时间:9:00-18:30)。
DACS——数字化三维精度控制系统
13
DACS造船精度控制系统软件介绍
(1)分段测量及现场分析软件:DACS-PDA
运行于掌上电脑,用于连接全站仪现场测量分段、现场进行误差分析 特点
1. 架设仪器方便,只需整平仪器,所有操作在手薄上 完成,即使非专业人员也能轻松操作 2. 可根据现场需要自由设置基准轴、基准面 3. 分段或总段可自由摆放、脱胎测量,不需要在胎架 上调平摆放 4. 根据气象条件自动进行误差修正,大大提高数据测 量精度,数据自动记录,无须手工记录 5. 现场可检测、计算多种几何量(长度、直角度、平 面度、准直度等),画余量线 6. 现场可进行分段分析、模拟搭载测量,实时确定各 精度管理点的误差值 7. 软件界面可选择显示中,英,韩三种语言
DACS精度控制系统的作用(一、二)
1.为大合拢搭载提供指导 通常情况下,在分段搭载时,定位人员总是默认该分段是没有问题的;也就是说,控 制点是按理论数据来进行定位的。然而,在实际搭载中由于分段制造精度的问题,现场 不可避免的会出现错位、离空等现象。这是就需要对定位数据进行修正,以期达到数据 与对合状态的一个最佳平衡点。如果分段质量较差,那么现场的调整工作就会很复杂; 并且,如果定位人员的经验不够老道的话很容易出现问题。如果一个分段在搭载前就已 经了解它的整体状况,那么我们就可以在搭载前对分段的定位数据进行修正。在办公室 中找到定位数据与分段对合的平衡点,就可以减轻外场工作量,提高定位效率及精度。 2.分析分段偏差 做过大合拢的人可能都有这样的感觉:都说分段质量差,其实一种类型的分段无非就 是那几种问题,这就是我们所说的相似分段的相同偏差类型问题。着眼于点解决的就是 那个点,而着眼于面解决的是无数个点。分段类型偏差就是面,因为解决了这种类型偏 差问题,就解决了N个可能存在这种问题的分段的精度问题。这又引出了另一个矛盾,过 程控制与精度分析的主次问题。事实上并不存在矛盾,这只是精度管理发展的不同阶段 的不同侧重点。就目前情况来说,从整个过程去实现精度管理很难切实实现。那么精度 管理是不是就不用做了?当然不是。我们可以先抓主要矛盾,再抓次要矛盾,逐步去实 现整个过程的控制。
标准分段
全站仪
DACS-SIMULATION
全站仪
搭载分段
DACS——数字化三维精度控制系统
分段建造精度控制的问题 非数字化的测量,其结果要手工记录,不便于与现代的造船设计软件及现代的数据 处理分析方法结合,不利于形成有效的数据库 钢尺量距的准确性不稳定,而且非常不方便,对于大型船只的结构件,钢尺无法完 成准确的测量 数据采集需要的人员较多,工作效率低下 分段及总段精度检查控制存在的问题 分段体必须按照特定要求摆放,否则不好进行测量 数据报表需要人工计算,不方便与设计数据进行直接对比 效率比较低,容易出现错误,造成工期延误 由于测量手段及数据处理方式的落后目前还无法形成有效的精度管理机制及精度数 据循环 船体合拢精度检查控制存在问题 传统测量方法效率低下,占用吊机时间较长 需要在现场对余量进行切割,需要对分段进行复位作业 很多分段需要进行二次定位,影响船台周期 传统的测量手段很难对船体分段在船体成型过程中的变化进行有效统计,为反变形 的施放及无余量生产提供数据支持。 DACS——数字化三维精度控制系统 4
DACS——数字化三维精度控制系统
12
DACS精度控制系统的作用(四)
4.模拟搭载,提高搭载效率 对于船体建造来说那就是:下水才是硬道理。要提高搭载效率无非是要使总段大型化 、搭载无余量化。对于平直分段时,工艺简单,只要严格按照工艺执行,要做到分段的 无余量搭载问题并不太大。而事实上对搭载效率影响最大的并不是平直分段,而是线型 分段。 对于复杂线型分段,特别是采用双斜切胎架进行组装的分段,其精度控制角度很难从 整个过程去实现严格的尺寸链控制。要实现无余量只能寄希望于最后一刀,也就是预修 割。事实上,曲面分段的划线精度受约束的条件太多。比如,板幅的划线精度、胎架的 制造精度,甚至划线工的素质,任何一方面出现问题都可能导致超过10mm的偏差, 10mm偏差导致的结果要么就是换板、偷堆焊;要么就是搭载时再割一刀。要解决这个 问题无非是两条路,①提高整个过程的控制力度,以尺寸链角度去控制分段的建造精度 ;②提高最后一刀的精度。哪个实现起来容易些? 计算机模拟搭载就是以精确测量的分段为操作对象,按搭载要求在计算机中进行的分 段对合的模拟操作。实现模拟搭载的条件:①分段测量精度足够;②进行模拟搭载的人 员具备足够的搭载常识;③软件的处理速度及精度能达到要求;④切割工不要瞎搞,做 到无余量搭载是顺理成章的事情。 举个例子:GB51双曲球形总段,与之对接的分段是三个独立吊装的分段。无余量前要 调5-6小时,余量100mm多;无余量后2小时。
三维设计系统 DACS-OFFICE
组成
Production Information Model
DACS——数字化三维精度控制系统
15
DACS造船精度控制系统软件介绍
(3)三维搭载模拟软件:DACS-SIMULATION
运行于室内PC机,用于对多个相邻分段之间的搭载模拟 特点 1. 参考三维设计模型,以实测数据为基准进行 模拟 2. 通过旋转、移动等功能,精确分析搭载状态 3. 自动分析搭载条件(高度、垂直度、平面度) 4. 快速分析分段间的重叠、段差 5. 自动计算分段搭载时的切割量 6. 自动生成模拟搭载预测结果报告书 组成 模拟搭载界面
DACS——数字化三维精度控制系统
11
DACS精度控制系统的作用(三)
3.为精度控制提供数据、技术和积累 我们都很羡慕日韩船厂的精度控制的很好,补偿量套个公式一算又准又快。显然这些 公式不是他们凭空捏造出来的,而是他们根据分段建造工艺、流程总结归纳出来的。总 结的基础是什么?就是数据!所以说精度管理就是要用数据说话。只有建立在大量有效 的数据基础之上的精度管理才是真正意义上的精度管理。
DACS-PDA 蓝牙或数据线 全站仪
界面
组成
室内电脑 有线连接或 无线网络
DACS——数字化三维精度控制系统
14
DACS造船精度控制系统软件介绍
(2)三维分段精度管理软件:DACS-OFFICE
运行于室内PC机,主要用于对单个分段的精度管理 界面 特点
1. 读取大型设计软件Tribon、CADDS5等设计模型 2. 计算各种几何量,同DACS-PDA版 3. 设计图上标注设计点号,自动提取设计点坐标, 实测数据可自动匹配计算三维误差 4. 可分析计算合拢口切割量、加强筋错位、对接面 错位 5. 自动生成报表,并可以Excel、PDF、Html等格式 存档 6. 打印精度检查控制报表,便于事前测量安排、事 后核对检查
数据线
PDA支架
全站仪
三脚架
附件箱
隐蔽杆
回转标靶
拐角反射靶
平面反射靶
反射靶固定器 9
DACS——数字化三维精度控制系统
DACS精度控制系统特点
可以同时测量角度和距离,且精度较高 造船用的全站仪测角精度最高能到0.5秒,测距精度最高达到 1mm+1ppm,是 目前世界上精度最高的全站仪 ,并全部自动显示和记录,无需人工读数和记录 非接触式测量,想测哪里就测哪里,令测量人员更轻松、更安全 全站仪的激光测距技术,可以测量200-500米的物体表面,且专利的pinpoint技术 可以精确测量船体的边缘,角落以及一些难以触及的地方 造船用的专业测量软件,数据测量非常简单快捷 专业测量软件配合全站仪,在现场只需将仪器整平、瞄准等简单操作,其余操作都 在软件上完成,软件操作符合造船业操作习惯,非常简单 三维分段精度管理软件可以自动化进行分段的精度控制和分析 数据采集回来后,可以将数据导入计算机进行分段模拟搭载、检查分段CUT/WELD值 、形成精度检查表等 ,严格控制各分段的精度,与设计数据进行准确直观的对比,并按 要求输出报表 船体三维模拟搭载软件可以将各分段在电脑里进行模拟合拢和搭载 在船体上坞台之前,可以先在计算机里进行模拟合拢和搭载,确保船体能够一次合拢 ,避免在坞期时间过长以及返工 整套系统全中文化操作,只要会简单电脑的人都可以操作 现场测量的仪器设备、测量软件以及室内的后处理软件,全部采用中文操作,使用简 单,自动化程度高,非常容易上手 DACS——数字化三维精度控制系统 10
DACS数字化三维造船精度控制解决方案
DACS(Dimensional & Accuracy Control System)
目录
1
问题
2
解决方案
3
实际应用
4
目标与服务
5
用户
DACS——数字化三维精度控制系统
2
1
传统造船业精度控制存在问题
问题
DACS——数字化三维精度控制系统
3
1、传统造船业精度控制存在问题
精度不良造成的问题
1、搭载工作重复进行 2、修整工作量增加、吊机时间增长 3、坞期增加、工期延迟
DACS——数字化三维精度控制系统
5
传统精度控制工作总结
传统造船业采用的技术手段比较落后,明显不适应现代造船对时间、 精度的要求。 目前造船业比较发达的日本和韩国,已经进入了精度造船的时代,我 们国家的造船业正从余量造船向无余量造船的时代过渡,要全面进入精 度造船,还需要一个相当长的时间。 采用现代数字化的造船精度控制设备和软件,是造船业从余量造船到 无余量造船过渡的一个重要手段。 青岛海徕天创科技有限公司是在国内首家涉足研究造船精度控制系统 的专业高科技公司,在研究国外先进精度控制系统的基础上,开发出了 国内第一套造船精度控制系统,旨在推动造船行业的数字化进程,努力 使我国造船业在精度控制方面达到韩日造船的水平,是造船行业最佳的 精度控制解决方案。
DACS——数字化三维精度控制系统
6
2
DACS造船精度控制系统产品介绍
解决 方案
DACS——数字化三维精度控制系统