湿式石灰石_石膏法脱硫技术及分析 (1)
火电厂烟气脱硫工程技术规范石灰石-石灰-石膏法
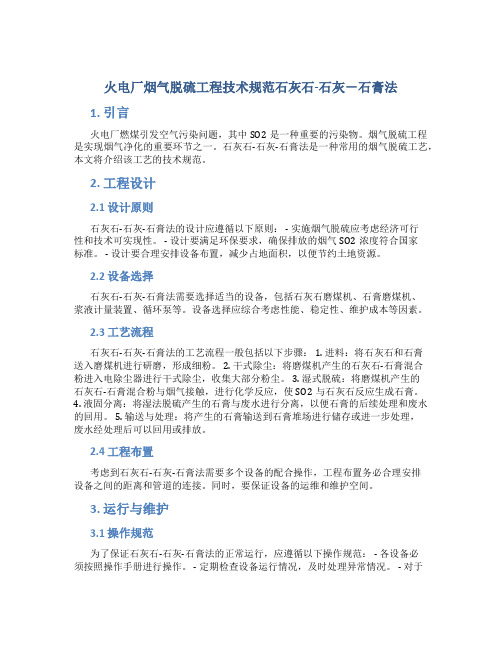
火电厂烟气脱硫工程技术规范石灰石-石灰-石膏法1. 引言火电厂燃煤引发空气污染问题,其中SO2是一种重要的污染物。
烟气脱硫工程是实现烟气净化的重要环节之一。
石灰石-石灰-石膏法是一种常用的烟气脱硫工艺,本文将介绍该工艺的技术规范。
2. 工程设计2.1 设计原则石灰石-石灰-石膏法的设计应遵循以下原则: - 实施烟气脱硫应考虑经济可行性和技术可实现性。
- 设计要满足环保要求,确保排放的烟气SO2浓度符合国家标准。
- 设计要合理安排设备布置,减少占地面积,以便节约土地资源。
2.2 设备选择石灰石-石灰-石膏法需要选择适当的设备,包括石灰石磨煤机、石膏磨煤机、浆液计量装置、循环泵等。
设备选择应综合考虑性能、稳定性、维护成本等因素。
2.3 工艺流程石灰石-石灰-石膏法的工艺流程一般包括以下步骤: 1. 进料:将石灰石和石膏送入磨煤机进行研磨,形成细粉。
2. 干式除尘:将磨煤机产生的石灰石-石膏混合粉进入电除尘器进行干式除尘,收集大部分粉尘。
3. 湿式脱硫:将磨煤机产生的石灰石-石膏混合粉与烟气接触,进行化学反应,使SO2与石灰石反应生成石膏。
4. 液固分离:将湿法脱硫产生的石膏与废水进行分离,以便石膏的后续处理和废水的回用。
5. 输送与处理:将产生的石膏输送到石膏堆场进行储存或进一步处理,废水经处理后可以回用或排放。
2.4 工程布置考虑到石灰石-石灰-石膏法需要多个设备的配合操作,工程布置务必合理安排设备之间的距离和管道的连接。
同时,要保证设备的运维和维护空间。
3. 运行与维护3.1 操作规范为了保证石灰石-石灰-石膏法的正常运行,应遵循以下操作规范: - 各设备必须按照操作手册进行操作。
- 定期检查设备运行情况,及时处理异常情况。
- 对于生产过程中的重要指标,如石膏产量、废水浓度等,应进行监测记录,以便进行评估与分析。
3.2 维护保养定期维护保养是确保石灰石-石灰-石膏法持续高效运行的关键。
石灰石-石膏湿法脱硫技术原理简介(一)
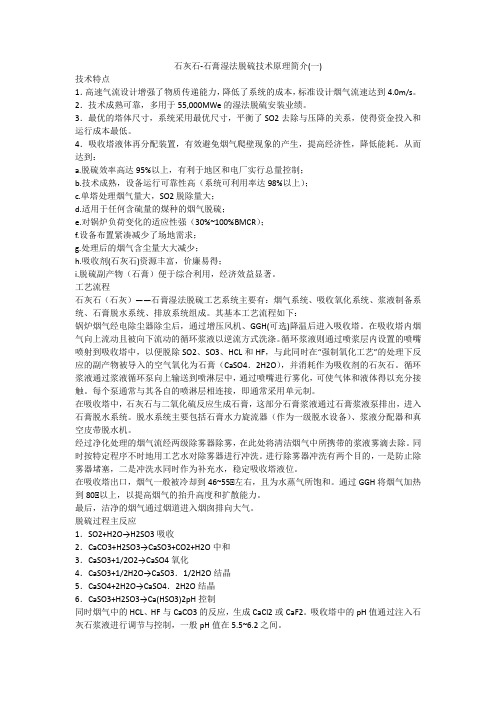
石灰石-石膏湿法脱硫技术原理简介(一)技术特点1.高速气流设计增强了物质传递能力,降低了系统的成本,标准设计烟气流速达到4.0m/s。
2.技术成熟可靠,多用于55,000MWe的湿法脱硫安装业绩。
3.最优的塔体尺寸,系统采用最优尺寸,平衡了SO2去除与压降的关系,使得资金投入和运行成本最低。
4.吸收塔液体再分配装置,有效避免烟气爬壁现象的产生,提高经济性,降低能耗。
从而达到:a.脱硫效率高达95%以上,有利于地区和电厂实行总量控制;b.技术成熟,设备运行可靠性高(系统可利用率达98%以上);c.单塔处理烟气量大,SO2脱除量大;d.适用于任何含硫量的煤种的烟气脱硫;e.对锅炉负荷变化的适应性强(30%~100%BMCR);f.设备布置紧凑减少了场地需求;g.处理后的烟气含尘量大大减少;h.吸收剂(石灰石)资源丰富,价廉易得;i.脱硫副产物(石膏)便于综合利用,经济效益显著。
工艺流程石灰石(石灰)——石膏湿法脱硫工艺系统主要有:烟气系统、吸收氧化系统、浆液制备系统、石膏脱水系统、排放系统组成。
其基本工艺流程如下:锅炉烟气经电除尘器除尘后,通过增压风机、GGH(可选)降温后进入吸收塔。
在吸收塔内烟气向上流动且被向下流动的循环浆液以逆流方式洗涤。
循环浆液则通过喷浆层内设置的喷嘴喷射到吸收塔中,以便脱除SO2、SO3、HCL和HF,与此同时在“强制氧化工艺”的处理下反应的副产物被导入的空气氧化为石膏(CaSO4.2H2O),并消耗作为吸收剂的石灰石。
循环浆液通过浆液循环泵向上输送到喷淋层中,通过喷嘴进行雾化,可使气体和液体得以充分接触。
每个泵通常与其各自的喷淋层相连接,即通常采用单元制。
在吸收塔中,石灰石与二氧化硫反应生成石膏,这部分石膏浆液通过石膏浆液泵排出,进入石膏脱水系统。
脱水系统主要包括石膏水力旋流器(作为一级脱水设备)、浆液分配器和真空皮带脱水机。
经过净化处理的烟气流经两级除雾器除雾,在此处将清洁烟气中所携带的浆液雾滴去除。
石灰石石膏湿法烟气脱硫工艺简介
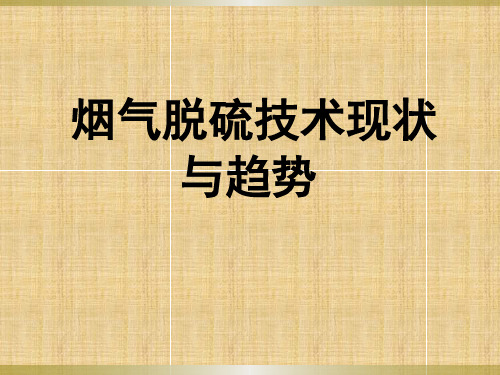
海水脱硫-技术情况
吸收剂:海水 脱硫率:70-90% 脱硫产物:SO42 优点:技术成熟、系统简单、投资低、运行
费低、脱硫效率高 特点:适用于沿海地区电厂,适用于低含硫
量烟气(S<1%) 技术拥有:挪威ABB公司、鲁奇·比晓夫
16
湿式氨法-工艺流程
17
湿式氨法-工艺原理
脱硫过程在溶液中进行,脱硫剂和脱硫产物均为湿态 世界范围 85%,其中石灰石法 36.7% 日本:98% 美国:92% 德国:90% 此工艺是世界范围内广泛应用、成熟的烟气脱硫技术
石灰石-石膏湿法烟气脱硫工艺简介
MET IFO Flue Gas Desulfurization Process MET IFO烟气脱硫流程
钙法 湿式钙法、半干式钙法
海水烟气脱硫 氨法
GE氨法(maruslex)、NKK氨法、Bischoff氨 法、电子束氨法、NADS氨-肥法 钠法 镁法 活性炭吸附法
5
烟气脱硫工艺的分类 -按脱硫率的分类
低脱硫率工艺 (<70%):炉内喷钙、管道 喷射
中脱硫率工艺(70%-90%):喷雾干燥、 CFB、LIFAC等
氨脱硫塔可生产出高价值的副产物,而不是低价值的硫 酸钙和亚硫酸盐污泥
与石灰石相比,氨脱硫塔运行具有较高的灵活性,特别 在高硫含量的情况与石灰石相比,氨脱硫塔的操作具有 较高的可靠性和有效性
19
MgO-工艺流程
20
氧化镁法-工艺原理
吸收 MgO + H2O → Mg(OH)2 Mg(OH)2 + SO2 → MgSO3 + H2O
皮带过滤器
Conveyor
输送机
回收水罐
石灰石(石灰)湿法脱硫技术分析
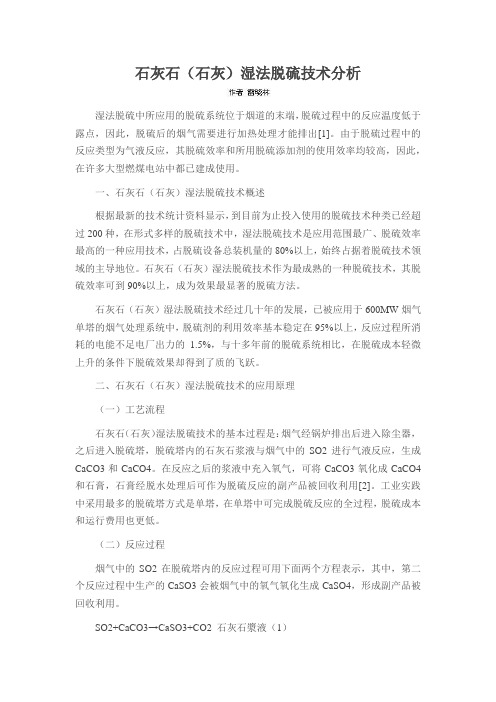
石灰石(石灰)湿法脱硫技术分析湿法脱硫中所应用的脱硫系统位于烟道的末端,脱硫过程中的反应温度低于露点,因此,脱硫后的烟气需要进行加热处理才能排出[1]。
由于脱硫过程中的反应类型为气液反应,其脱硫效率和所用脱硫添加剂的使用效率均较高,因此,在许多大型燃煤电站中都已建成使用。
一、石灰石(石灰)湿法脱硫技术概述根据最新的技术统计资料显示,到目前为止投入使用的脱硫技术种类已经超过200种,在形式多样的脱硫技术中,湿法脱硫技术是应用范围最广、脱硫效率最高的一种应用技术,占脱硫设备总装机量的80%以上,始终占据着脱硫技术领域的主导地位。
石灰石(石灰)湿法脱硫技术作为最成熟的一种脱硫技术,其脱硫效率可到90%以上,成为效果最显著的脱硫方法。
石灰石(石灰)湿法脱硫技术经过几十年的发展,已被应用于600MW烟气单塔的烟气处理系统中,脱硫剂的利用效率基本稳定在95%以上,反应过程所消耗的电能不足电厂出力的 1.5%,与十多年前的脱硫系统相比,在脱硫成本轻微上升的条件下脱硫效果却得到了质的飞跃。
二、石灰石(石灰)湿法脱硫技术的应用原理(一)工艺流程石灰石(石灰)湿法脱硫技术的基本过程是:烟气经锅炉排出后进入除尘器,之后进入脱硫塔,脱硫塔内的石灰石浆液与烟气中的SO2进行气液反应,生成CaCO3和CaCO4。
在反应之后的浆液中充入氧气,可将CaCO3氧化成CaCO4和石膏,石膏经脱水处理后可作为脱硫反应的副产品被回收利用[2]。
工业实践中采用最多的脱硫塔方式是单塔,在单塔中可完成脱硫反应的全过程,脱硫成本和运行费用也更低。
(二)反应过程烟气中的SO2在脱硫塔内的反应过程可用下面两个方程表示,其中,第二个反应过程中生产的CaSO3会被烟气中的氧气氧化生成CaSO4,形成副产品被回收利用。
SO2+CaCO3→CaSO3+CO2 石灰石漿液(1)SO2+Ca(OH)2→CaSO3+H2O 石灰浆液(2)(三)脱硫效率脱硫效率受到诸多因素的影响,其中,脱硫塔中的pH值对脱硫效率会产生较大的影响。
燃煤电厂石灰石_石膏法脱硫系统结垢分析与建议_邹鹏
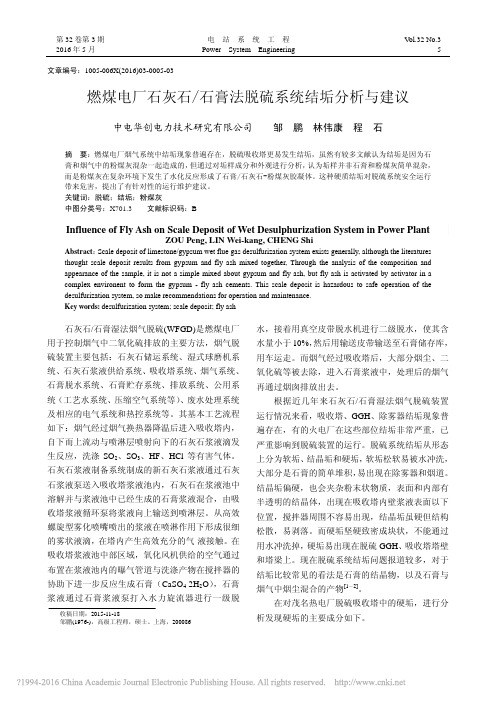
第32卷第3期电站系统工程V ol.32 No.3 2016年5月Power System Engineering 5 文章编号:1005-006X(2016)03-0005-03燃煤电厂石灰石/石膏法脱硫系统结垢分析与建议中电华创电力技术研究有限公司邹 鹏 林伟康 程 石摘要:燃煤电厂烟气系统中结垢现象普遍存在,脱硫吸收塔更易发生结垢,虽然有较多文献认为结垢是因为石膏和烟气中的粉煤灰混杂一起造成的,但通过对垢样成分和外观进行分析,认为垢样并非石膏和粉煤灰简单混杂,而是粉煤灰在复杂环境下发生了水化反应形成了石膏/石灰石-粉煤灰胶凝体。
这种硬质结垢对脱硫系统安全运行带来危害,提出了有针对性的运行维护建议。
关键词:脱硫;结垢;粉煤灰中图分类号:X701.3文献标识码:BInfluence of Fly Ash on Scale Deposit of Wet Desulphurization System in Power PlantZOU Peng, LIN Wei-kang, CHENG ShiAbstract:Scale deposit of limestone/gypsum wet flue gas desulfurization system exists generally, although the literatures thought scale deposit results from gypsum and fly ash mixed together, Through the analysis of the composition and appearance of the sample, it is not a simple mixed about gypsum and fly ash, but fly ash is activated by activator in a complex environent to form the gypsum - fly ash cements. This scale deposit is hazardous to safe operation of the desulfurization system, so make recommendations for operation and maintenance.Key words: desulfurization system; scale deposit; fly ash石灰石/石膏湿法烟气脱硫(WFGD)是燃煤电厂用于控制烟气中二氧化硫排放的主要方法,烟气脱硫装置主要包括:石灰石储运系统、湿式球磨机系统、石灰石浆液供给系统、吸收塔系统、烟气系统、石膏脱水系统、石膏贮存系统、排放系统、公用系统(工艺水系统、压缩空气系统等)、废水处理系统及相应的电气系统和热控系统等。
1湿式石灰石石膏法脱硫基本原理与影响因素

1湿式石灰石石膏法脱硫基本原理与影响因素湿式石灰石石膏法脱硫原理以及影响因素马双忱 1 2 / MET IFO Flue Gas Desulfurization ProcessGas Handling Sulfur DioxideAbsorptionGypsum DewateringReagent PreparationFuelAirDustCollectorAsh RemovalID FanAirLimeorLimestoneSiloWet Ball Millor SlakerSlurryStorage TankAbsorberWash WaterBeltFilterWaste WaterHydrocloneReclaimWater TankGypsumConveyorStackSO2 AbsorberBleedWaterReheater Optional- Steam- Gas-Liquid-Gas- Cycic Gas-GasBoilerMET IFO烟气脱硫流程烟气处理和 SO2吸收锅炉燃料空气除尘除尘器引风机空气水再热器可选蒸汽气-液-气循环烟气-烟气烟囱吸收器 SO2吸收器排放石灰或石灰石粉仓湿球磨机或消化器浆贮藏罐反应物制备石膏脱水石膏输送机回收水罐废水 1.2.3 湿式石灰石石膏法脱硫石皮带过滤器洗涤水水力旋流器灰石石膏法烟气脱硫Flue Gas DesulphurizationFGD 是用含石灰石的浆液洗涤烟气以中和脱除烟气中的SO2故又称之为湿式石灰石/石膏法烟气脱硫简称WFGD。
该方法是目前应用最广泛、技术最为成熟的烟气SO2排放控制技术。
其特点SO2脱除率高脱硫效率可达95以上能适应大容量机组、高浓度SO2含量的烟气脱硫吸收剂石灰石价廉易得而且可生产出副产品石膏高质量石膏具有综合利用的商业价值。
随着石灰石/石膏法FGD系统的不断简化和完善不仅运行、维修更加方便而且设备造价也有所降低。
石灰石石膏湿法烟气脱硫工艺
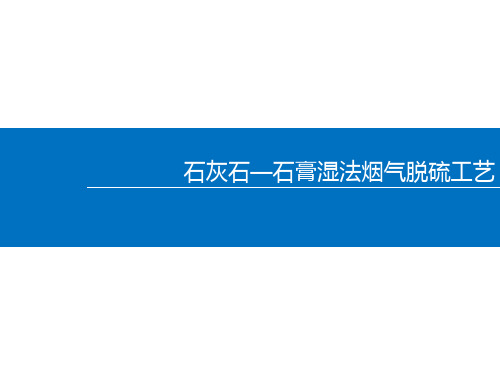
液柱与烟气进行两次接触 (上升 / 落下)
没有背压的直筒式喷嘴
自我冲洗(向上的喷嘴)
单层喷浆管/喷嘴 (结构简单1容8 易维修)
主要系统及设备介绍—浆液循环系统
循环浆泵用来将吸收塔浆池的浆液和加入的石灰石浆液循环不断的送到吸收塔喷淋
层,在一定压力下通过喷嘴充分雾化,与烟气反应。
根据防腐工艺不同,循环浆泵分为衬胶泵和防腐金属泵两种。
后橡Ba胶ck R衬ub套ber Liner B后ac盖k Split Casing
金属合金 叶MIemtaple轮Allellroy
Front Rubber
前Li橡ner胶衬套
F前ro盖nt Split
Casing
金M属et合al A金llo护y 套
Throatbush
((前fro磨nt w损ea盘r )
主要系统及设备介绍—吸收系统及设备
(一)吸收塔
吸收塔一般为钢制塔体,内衬玻璃鳞片,并具备烟气进出口烟道、人孔门、检查门、 钢制平台扶梯、法兰、液位控制、溢流管及所有需要的连接件等。 吸收塔除塔体外,还有搅拌器、喷淋层和两级除雾器(聚丙烯百叶窗式)。 此外,吸收塔还包括循环浆液泵和氧化空气风机。 脱硫塔从结构上来分主要有:填料塔、板式塔、液柱塔、喷淋塔(空塔)和鼓泡塔。
继续与回落的液滴进行同向传质。 烟气从逆流塔流出经过反应罐上部折转180°,自下而上通过顺流塔,与向上喷射的液
柱及向下回落的液滴再次进行气液接触。经除雾器除雾后排出。
净烟气 原(脏)烟气
主要系统及设备介绍—吸收系统及设备
液柱式喷淋塔的优势
净烟气
高密度的液滴层 (高密度的液滴层增大气液 接触面积)
原(脏)烟气
实际球)。
热电厂脱硫的工作原理
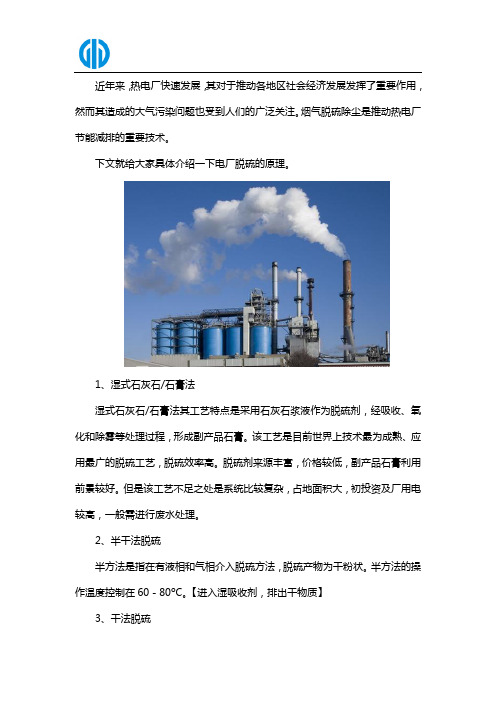
近年来,热电厂快速发展,其对于推动各地区社会经济发展发挥了重要作用,然而其造成的大气污染问题也受到人们的广泛关注。
烟气脱硫除尘是推动热电厂节能减排的重要技术。
下文就给大家具体介绍一下电厂脱硫的原理。
1、湿式石灰石/石膏法湿式石灰石/石膏法其工艺特点是采用石灰石浆液作为脱硫剂,经吸收、氧化和除雾等处理过程,形成副产品石膏。
该工艺是目前世界上技术最为成熟、应用最广的脱硫工艺,脱硫效率高。
脱硫剂来源丰富,价格较低,副产品石膏利用前景较好。
但是该工艺不足之处是系统比较复杂,占地面积大,初投资及厂用电较高,一般需进行废水处理。
2、半干法脱硫半方法是指在有液相和气相介入脱硫方法,脱硫产物为干粉状。
半方法的操作温度控制在60-80ºC。
【进入湿吸收剂,排出干物质】3、干法脱硫干法是指无液相介入完全在干燥状态下进行脱硫的方法。
如向炉内喷干燥的生石灰或石灰石粉末,即脱硫产物为粉状。
【进入干吸收剂,排出干物质】干法的操作温度在800-1300ºC。
4、炉内喷钙炉后活化脱硫工艺炉内喷钙和炉后增湿活化的干法脱硫工艺,具有占地较小、建设周期短、投资费用省, 适用于中低硫煤脱硫的特点, 一般Ca/ S < 2. 5 , 脱硫率60 %~80 %。
由芬兰FORTUM公司开发的炉内喷钙和炉后增湿活化脱硫系统, 即LIFAC工艺。
LIFAC 系统的主要优点是经济、所需设备占地少、不产生废水、最终产物是干灰, 在进一步提高脱硫率、完善设备运行状态、克服对锅炉的一些影响后, 不失为一经济实用的脱硫方法,但这种方法对技术的要求较高。
当然脱硫的方法还有很多,总得来说,热电厂烟气处理主要包括几个方面:直接处理、化石燃料应用和燃料处理,热电厂生产运营过程中往往在燃料燃烧之前对烟气进行脱硫处理,然而由于脱硫除尘技术应用存在很多问题,并且受到相关应用条件的限制,使得热电厂脱硫除尘效果较差。
同时,化石燃料燃烧过程中会产生大量的二氧化硫和粉尘,化石燃料燃烧脱硫是热电厂烟气脱硫除尘的关键,但是很多热电厂的除硫效率较低,往往无法达到除硫技术标准。
石灰石-石膏湿法脱硫技术的工艺流程、反应原理及主要系统
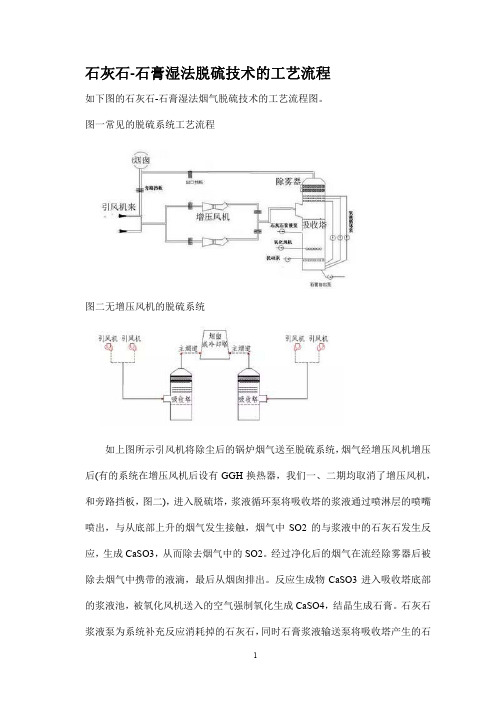
石灰石-石膏湿法脱硫技术的工艺流程如下图的石灰石-石膏湿法烟气脱硫技术的工艺流程图。
图一常见的脱硫系统工艺流程图二无增压风机的脱硫系统如上图所示引风机将除尘后的锅炉烟气送至脱硫系统,烟气经增压风机增压后(有的系统在增压风机后设有GGH换热器,我们一、二期均取消了增压风机,和旁路挡板,图二),进入脱硫塔,浆液循环泵将吸收塔的浆液通过喷淋层的喷嘴喷出,与从底部上升的烟气发生接触,烟气中SO2的与浆液中的石灰石发生反应,生成CaSO3,从而除去烟气中的SO2。
经过净化后的烟气在流经除雾器后被除去烟气中携带的液滴,最后从烟囱排出。
反应生成物CaSO3进入吸收塔底部的浆液池,被氧化风机送入的空气强制氧化生成CaSO4,结晶生成石膏。
石灰石浆液泵为系统补充反应消耗掉的石灰石,同时石膏浆液输送泵将吸收塔产生的石膏外排至石膏脱水系统将石膏脱水或直接抛弃。
同时为了防止吸收塔内浆液沉淀在底部设有浆液搅拌系统,一期采用扰动泵,二期采用搅拌器。
石灰石-石膏湿法脱硫反应原理在烟气脱硫过程中,物理反应和化学反应的过程相对复杂,吸收塔由吸收区、氧化区和结晶区三部分组成,在吸收塔浆池(氧化区和结晶区组成)和吸收区,不同的层存在不同的边界条件,现将最重要的物理和化学过程原理描述如下:(1)SO2溶于液体在吸收区,烟气和液体强烈接触,传质在接触面发生,烟气中的SO2溶解并转化成亚硫酸。
SO2+H2O<===>H2SO3除了SO2外烟气中的其他酸性成份,如HCL和HF也被喷入烟气中的浆液脱除。
装置脱硫效率受如下因素影响,烟气与液体接触程度,液气比、雾滴大小、SO2含量、PH值、在吸收区的相对速度和接触时间。
(2)酸的离解当SO2溶解时,产生亚硫酸,同时根据PH值离解:H2SO3<===>H++HSO3-对低pH值HSO3-<===>H++SO32-对高pH值从烟气中洗涤下来的HCL和HF,也同时离解:HCl<===>H++Cl-F<===>H++F-根据上面反应,在离解过程中,H+离子成为游离态,导致PH值降低。
石灰石-石膏湿法脱硫工艺的基本原理
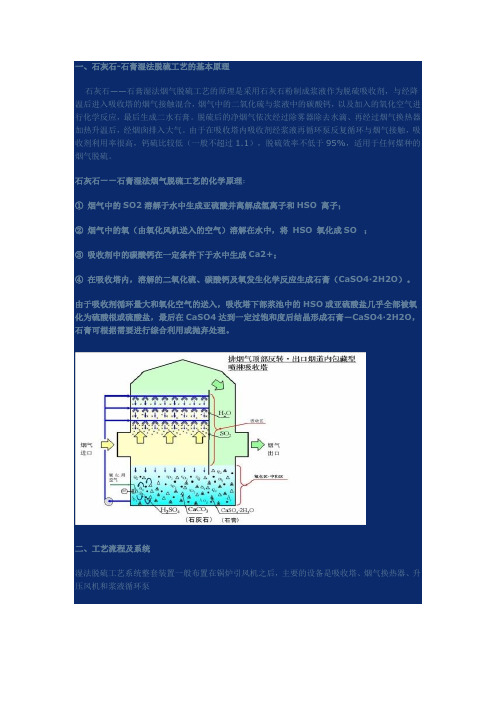
一、石灰石-石膏湿法脱硫工艺的基本原理石灰石——石膏湿法烟气脱硫工艺的原理是采用石灰石粉制成浆液作为脱硫吸收剂,与经降温后进入吸收塔的烟气接触混合,烟气中的二氧化硫与浆液中的碳酸钙,以及加入的氧化空气进行化学反应,最后生成二水石膏。
脱硫后的净烟气依次经过除雾器除去水滴、再经过烟气换热器加热升温后,经烟囱排入大气。
由于在吸收塔内吸收剂经浆液再循环泵反复循环与烟气接触,吸收剂利用率很高,钙硫比较低(一般不超过1.1),脱硫效率不低于95%,适用于任何煤种的烟气脱硫。
石灰石——石膏湿法烟气脱硫工艺的化学原理:①烟气中的SO2溶解于水中生成亚硫酸并离解成氢离子和HSO 离子;②烟气中的氧(由氧化风机送入的空气)溶解在水中,将HSO 氧化成SO ;③吸收剂中的碳酸钙在一定条件下于水中生成Ca2+;④在吸收塔内,溶解的二氧化硫、碳酸钙及氧发生化学反应生成石膏(CaSO4·2H2O)。
由于吸收剂循环量大和氧化空气的送入,吸收塔下部浆池中的HSO或亚硫酸盐几乎全部被氧化为硫酸根或硫酸盐,最后在CaSO4达到一定过饱和度后结晶形成石膏—CaSO4·2H2O,石膏可根据需要进行综合利用或抛弃处理。
二、工艺流程及系统湿法脱硫工艺系统整套装置一般布置在锅炉引风机之后,主要的设备是吸收塔、烟气换热器、升压风机和浆液循环泵我公司采用高效脱除SO2的川崎湿法石灰石-石膏工艺。
该套烟气脱硫系统(FGD)处理烟气量为定洲发电厂#1和#2机组(2×600MW)100%的烟气量,定洲电厂的FGD系统由以下子系统组成:(1)吸收塔系统(2)烟气系统(包括烟气再热系统和增压风机)(3)石膏脱水系统(包括真空皮带脱水系统和石膏储仓系统)(4)石灰石制备系统(包括石灰石接收和储存系统、石灰石磨制系统、石灰石供浆系统)(5)公用系统(6)排放系统(7)废水处理系统1、吸收塔系统吸收塔采用川崎公司先进的逆流喷雾塔,烟气由侧面进气口进入吸收塔,并在上升区与雾状浆液逆流接触,处理后的烟气在吸收塔顶部翻转向下,从与吸收塔烟气入口同一水平位置的烟气出口排至烟气再热系统。
关于石灰石-石膏湿法脱硫装置石膏脱水困难的分析及措施
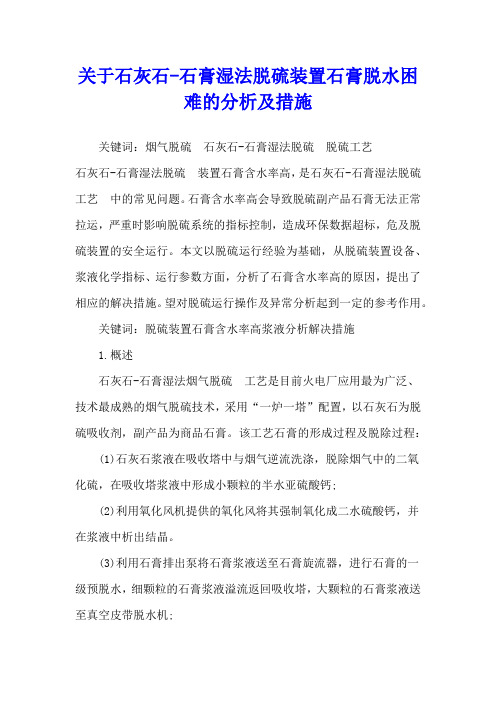
关于石灰石-石膏湿法脱硫装置石膏脱水困难的分析及措施关键词:烟气脱硫石灰石-石膏湿法脱硫脱硫工艺石灰石-石膏湿法脱硫装置石膏含水率高,是石灰石-石膏湿法脱硫工艺中的常见问题。
石膏含水率高会导致脱硫副产品石膏无法正常拉运,严重时影响脱硫系统的指标控制,造成环保数据超标,危及脱硫装置的安全运行。
本文以脱硫运行经验为基础,从脱硫装置设备、浆液化学指标、运行参数方面,分析了石膏含水率高的原因,提出了相应的解决措施。
望对脱硫运行操作及异常分析起到一定的参考作用。
关键词:脱硫装置石膏含水率高浆液分析解决措施1.概述石灰石-石膏湿法烟气脱硫工艺是目前火电厂应用最为广泛、技术最成熟的烟气脱硫技术,采用“一炉一塔”配置,以石灰石为脱硫吸收剂,副产品为商品石膏。
该工艺石膏的形成过程及脱除过程: (1)石灰石浆液在吸收塔中与烟气逆流洗涤,脱除烟气中的二氧化硫,在吸收塔浆液中形成小颗粒的半水亚硫酸钙;(2)利用氧化风机提供的氧化风将其强制氧化成二水硫酸钙,并在浆液中析出结晶。
(3)利用石膏排出泵将石膏浆液送至石膏旋流器,进行石膏的一级预脱水,细颗粒的石膏浆液溢流返回吸收塔,大颗粒的石膏浆液送至真空皮带脱水机;(4)浆液通过真空皮脱水机后,形成含水量小于10%的石膏,输送至石膏库外运。
在石灰石-石膏湿法烟气脱硫工艺中,石膏含水量高、石膏脱水困难是普遍存在的问题,石膏能否正常脱水,不但反应出吸收塔浆液品质活性,更是脱硫系统能否正常运行的关键。
在实际运行工作当中,多次遇到由于各种原因导致石膏脱水困难的情况,通过采取相应的调整措施,恢复了系统的正常运行。
2.石膏含水率高的表现(1)脱硫装置脱水系统无法形成含水率小于10%的商品石膏,只能形成含水率在15%-25%的稠糊状石膏,石膏库的石膏无法堆积、装车运输。
(2)吸收塔内浆液密度不断升高,脱硫效率明显下降,通过增加钙硫比、液气比后脱硫效果无明显提升,同等工况条件下供浆量大于正常运行值。
石灰石石膏湿法脱硫原理
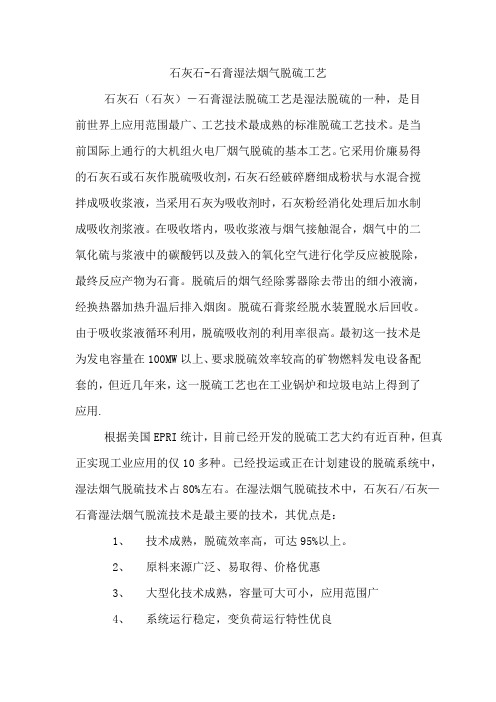
石灰石-石膏湿法烟气脱硫工艺石灰石(石灰)-石膏湿法脱硫工艺是湿法脱硫的一种,是目前世界上应用范围最广、工艺技术最成熟的标准脱硫工艺技术。
是当前国际上通行的大机组火电厂烟气脱硫的基本工艺。
它采用价廉易得的石灰石或石灰作脱硫吸收剂,石灰石经破碎磨细成粉状与水混合搅拌成吸收浆液,当采用石灰为吸收剂时,石灰粉经消化处理后加水制成吸收剂浆液。
在吸收塔内,吸收浆液与烟气接触混合,烟气中的二氧化硫与浆液中的碳酸钙以及鼓入的氧化空气进行化学反应被脱除,最终反应产物为石膏。
脱硫后的烟气经除雾器除去带出的细小液滴,经换热器加热升温后排入烟囱。
脱硫石膏浆经脱水装置脱水后回收。
由于吸收浆液循环利用,脱硫吸收剂的利用率很高。
最初这一技术是为发电容量在100MW以上、要求脱硫效率较高的矿物燃料发电设备配套的,但近几年来,这一脱硫工艺也在工业锅炉和垃圾电站上得到了应用.根据美国EPRI统计,目前已经开发的脱硫工艺大约有近百种,但真正实现工业应用的仅10多种。
已经投运或正在计划建设的脱硫系统中,湿法烟气脱硫技术占80%左右。
在湿法烟气脱硫技术中,石灰石/石灰—石膏湿法烟气脱流技术是最主要的技术,其优点是:1、技术成熟,脱硫效率高,可达95%以上。
2、原料来源广泛、易取得、价格优惠3、大型化技术成熟,容量可大可小,应用范围广4、系统运行稳定,变负荷运行特性优良5、副产品可充分利用,是良好的建筑材料6、只有少量的废物排放,并且可实现无废物排放7、技术进步快。
石灰石/石灰—石膏湿法烟气脱硫工艺,一般布置在锅炉除尘器后尾部烟道,主要有:工艺系统、DCS控制系统、电气系统三个分统。
基本工艺过程在石灰石一石膏湿法烟气脱硫工艺中,俘获二氧化硫(SO2)的基本工艺过程:烟气进入吸收塔后,与吸收剂浆液接触、进行物理、化学反应,最后产生固化二氧化硫的石膏副产品。
基本工艺过程为:(1)气态SO2与吸收浆液混合、溶解(2) SO2进行反应生成亚硫根(3)亚硫根氧化生成硫酸根(4)硫酸根与吸收剂反应生成硫酸盐(5)硫酸盐从吸收剂中分离用石灰石作吸收剂时,SO2在吸收塔中转化,其反应简式式如下: CaCO3+2 SO2+H2O ←→Ca(HSO3)2+CO2在此,含CaCO3的浆液被称为洗涤悬浮液,它从吸收塔的上部喷入到烟气中。
脱硫工艺流程说明

脱硫工艺流程说明湿法脱硫工艺流程主要包括石灰石-石膏法和碱性洗涤液法两种方式。
1. 石灰石-石膏法:将石灰石(CaCO3)加入到反应塔中与燃烧产生的SO2发生反应,生成石膏(CaSO4)和二氧化碳(CO2)。
石膏随后被分离出来用于再利用或处理。
2. 碱性洗涤液法:用碱性洗涤液(如氢氧化钠、氨水等)与燃烧产生的SO2进行反应,生成相应的盐类,然后通过沉淀或其他方式分离出来。
干法脱硫工艺流程主要包括石灰石喷雾干法脱硫和双碱法两种方式。
1. 石灰石喷雾干法脱硫:将粉状石灰石喷射到燃烧产生的SO2气流中,通过干法吸收,然后分离出SO2和粉尘。
2. 双碱法:使用两种碱性吸收剂,通常是碳酸氢钠和氢氧化钙,通过干法反应吸收SO2,然后分离出生成的产物。
脱硫工艺流程中需要考虑的参数包括燃料类型、SO2排放浓度、处理效率、再生利用和处理废料等。
不同的工艺流程适用于不同的工业设备和排放标准,因此在选择和设计脱硫工艺时需要综合考虑各种因素。
对于脱硫工艺流程,还有一些其他重要的细节和注意事项需要考虑。
首先,脱硫工艺需要根据具体的工业设备和生产流程进行选择和设计。
比如在煤电厂中,石灰石-石膏法常被用于处理燃煤产生的二氧化硫。
而在工业炉窑中,干法脱硫工艺更为常见。
各种工艺都需要根据具体情况进行优化设计,以提高脱硫效率、减少能耗和减少对环境的影响。
其次,脱硫工艺需要考虑处理后的副产品处理问题。
例如,石膏、除尘灰等副产品需要经过处理后才能达到国家排放标准,或者进行再利用。
对副产品的有效利用不仅可以减少环境污染,还可以降低生产成本。
此外,脱硫工艺的运行参数也需要严格控制。
这包括脱硫剂的投加量、反应温度、气体流速以及脱硫设备的清洁维护等。
通过对这些参数的严格控制,能够确保脱硫工艺的高效运行,减少设备的停机维护,提高设备的使用寿命。
在脱硫工艺的选择中,也需要考虑对能源的消耗。
比如干法脱硫通常需要更多的能源用于干燥和加热过程,而湿法脱硫则需要更多的水资源。
石灰石石膏法脱硫原理
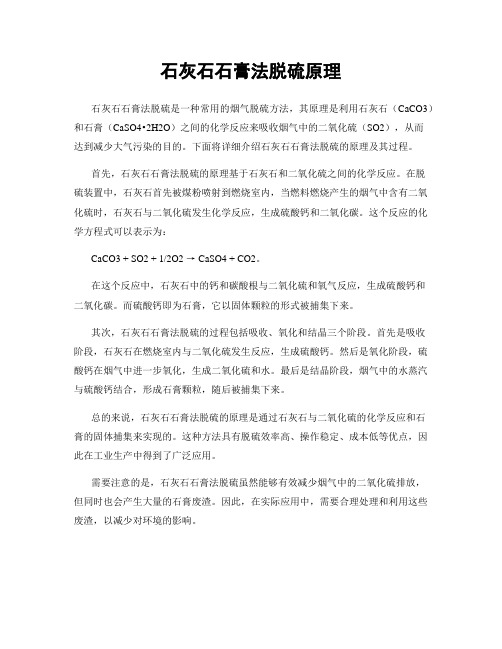
石灰石石膏法脱硫原理石灰石石膏法脱硫是一种常用的烟气脱硫方法,其原理是利用石灰石(CaCO3)和石膏(CaSO4•2H2O)之间的化学反应来吸收烟气中的二氧化硫(SO2),从而达到减少大气污染的目的。
下面将详细介绍石灰石石膏法脱硫的原理及其过程。
首先,石灰石石膏法脱硫的原理基于石灰石和二氧化硫之间的化学反应。
在脱硫装置中,石灰石首先被煤粉喷射到燃烧室内,当燃料燃烧产生的烟气中含有二氧化硫时,石灰石与二氧化硫发生化学反应,生成硫酸钙和二氧化碳。
这个反应的化学方程式可以表示为:CaCO3 + SO2 + 1/2O2 → CaSO4 + CO2。
在这个反应中,石灰石中的钙和碳酸根与二氧化硫和氧气反应,生成硫酸钙和二氧化碳。
而硫酸钙即为石膏,它以固体颗粒的形式被捕集下来。
其次,石灰石石膏法脱硫的过程包括吸收、氧化和结晶三个阶段。
首先是吸收阶段,石灰石在燃烧室内与二氧化硫发生反应,生成硫酸钙。
然后是氧化阶段,硫酸钙在烟气中进一步氧化,生成二氧化硫和水。
最后是结晶阶段,烟气中的水蒸汽与硫酸钙结合,形成石膏颗粒,随后被捕集下来。
总的来说,石灰石石膏法脱硫的原理是通过石灰石与二氧化硫的化学反应和石膏的固体捕集来实现的。
这种方法具有脱硫效率高、操作稳定、成本低等优点,因此在工业生产中得到了广泛应用。
需要注意的是,石灰石石膏法脱硫虽然能够有效减少烟气中的二氧化硫排放,但同时也会产生大量的石膏废渣。
因此,在实际应用中,需要合理处理和利用这些废渣,以减少对环境的影响。
综上所述,石灰石石膏法脱硫是一种重要的烟气脱硫方法,其原理是基于石灰石和石膏之间的化学反应来吸收二氧化硫。
通过合理的操作和管理,可以实现高效、稳定的脱硫效果,减少大气污染物排放,保护环境和人类健康。
几种脱硫工艺选择
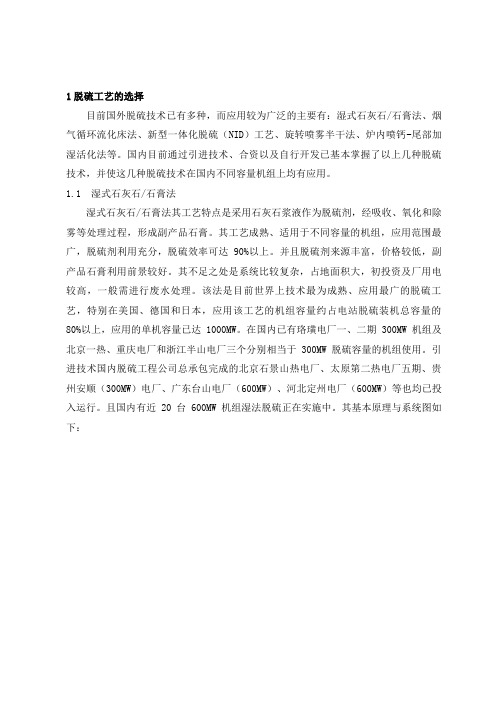
1脱硫工艺的选择目前国外脱硫技术已有多种,而应用较为广泛的主要有:湿式石灰石/石膏法、烟气循环流化床法、新型一体化脱硫(NID)工艺、旋转喷雾半干法、炉内喷钙-尾部加湿活化法等。
国内目前通过引进技术、合资以及自行开发已基本掌握了以上几种脱硫技术,并使这几种脱硫技术在国内不同容量机组上均有应用。
1.1 湿式石灰石/石膏法湿式石灰石/石膏法其工艺特点是采用石灰石浆液作为脱硫剂,经吸收、氧化和除雾等处理过程,形成副产品石膏。
其工艺成熟、适用于不同容量的机组,应用范围最广,脱硫剂利用充分,脱硫效率可达90%以上。
并且脱硫剂来源丰富,价格较低,副产品石膏利用前景较好。
其不足之处是系统比较复杂,占地面积大,初投资及厂用电较高,一般需进行废水处理。
该法是目前世界上技术最为成熟、应用最广的脱硫工艺,特别在美国、德国和日本,应用该工艺的机组容量约占电站脱硫装机总容量的80%以上,应用的单机容量已达1000MW。
在国内已有珞璜电厂一、二期300MW机组及北京一热、重庆电厂和浙江半山电厂三个分别相当于300MW脱硫容量的机组使用。
引进技术国内脱硫工程公司总承包完成的北京石景山热电厂、太原第二热电厂五期、贵州安顺(300MW)电厂、广东台山电厂(600MW)、河北定州电厂(600MW)等也均已投入运行。
且国内有近20台600MW机组湿法脱硫正在实施中。
其基本原理与系统图如下:1.2 烟气循环流化床干法烟气循环流化床干法脱硫(CFB-FGD)技术是世界著名环保公司德国鲁奇·能捷斯·比肖夫(LLB)公司开发的世界先进水平的循环流化床干法烟气脱硫技术。
CFB-FGD是目前干法脱硫技术商业应用中单塔处理能力较大、脱硫综合效益较为优越的一种方法。
该工艺已经先后在德国、奥地利、波兰、捷克、美国、爱尔兰等国家得到广泛应用,最大已运行单机、单塔机组容量为300MW,采用该技术设计的单塔处理烟气量可达到2800000Nm3/h。
湿式石灰石—石膏法脱硫常用实验方法
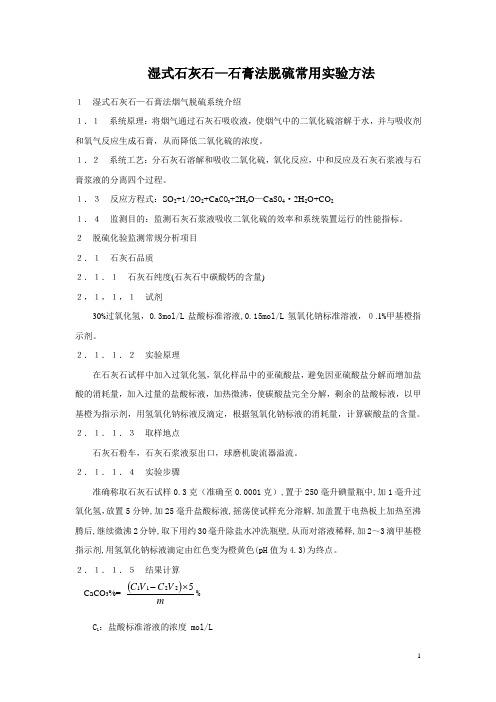
湿式石灰石—石膏法脱硫常用实验方法1湿式石灰石—石膏法烟气脱硫系统介绍1.1系统原理:将烟气通过石灰石吸收液,使烟气中的二氧化硫溶解于水,并与吸收剂和氧气反应生成石膏,从而降低二氧化硫的浓度。
1.2系统工艺:分石灰石溶解和吸收二氧化硫,氧化反应,中和反应及石灰石浆液与石膏浆液的分离四个过程。
1.3反应方程式:SO2+1/2O2+C aCO3+2H2O—C aSO4·2H2O+CO21.4监测目的:监测石灰石浆液吸收二氧化硫的效率和系统装置运行的性能指标。
2脱硫化验监测常规分析项目2.1石灰石品质2.1.1石灰石纯度(石灰石中碳酸钙的含量)2,1,1,1试剂30%过氧化氢,0.3mol/L盐酸标准溶液,0.15mol/L氢氧化钠标准溶液,0.1%甲基橙指示剂。
2.1.1.2实验原理在石灰石试样中加入过氧化氢,氧化样品中的亚硫酸盐,避免因亚硫酸盐分解而增加盐酸的消耗量,加入过量的盐酸标液,加热微沸,使碳酸盐完全分解,剩余的盐酸标液,以甲基橙为指示剂,用氢氧化钠标液反滴定,根据氢氧化钠标液的消耗量,计算碳酸盐的含量。
2.1.1.3取样地点石灰石粉车,石灰石浆液泵出口,球磨机旋流器溢流。
2.1.1.4实验步骤准确称取石灰石试样0.3克(准确至0.0001克),置于250毫升碘量瓶中,加1毫升过氧化氢,放置5分钟,加25毫升盐酸标液,摇荡使试样充分溶解,加盖置于电热板上加热至沸腾后,继续微沸2分钟,取下用约30毫升除盐水冲洗瓶壁,从而对溶液稀释,加2~3滴甲基橙指示剂,用氢氧化钠标液滴定由红色变为橙黄色(pH值为4.3)为终点。
2.1.1.5结果计算CaCO3%=()mVCVC52211⨯-%C1:盐酸标准溶液的浓度 mol/LV 1:加入盐酸标准溶液的体积 mlC 2;氢氧化钠标准溶液的浓度 mol/LV 2;滴定时消耗氢氧化钠标准溶液的体积 mlm :试样的质量g备注:此方法现在不适用于石灰石中碳酸钙的测定,只适用于石膏中碳酸钙的测定,在石膏中碳酸钙的测定实验中,加15毫升盐酸标液。
- 1、下载文档前请自行甄别文档内容的完整性,平台不提供额外的编辑、内容补充、找答案等附加服务。
- 2、"仅部分预览"的文档,不可在线预览部分如存在完整性等问题,可反馈申请退款(可完整预览的文档不适用该条件!)。
- 3、如文档侵犯您的权益,请联系客服反馈,我们会尽快为您处理(人工客服工作时间:9:00-18:30)。
第21卷第2期上海电力学院学报Vo.l21,No.2 2005年6月J ournal of Shanghai Univers it y of E l ectric Po w er J une 2005 文章编号:1006-4729(2005)02-0132-05湿式石灰石-石膏法脱硫技术及分析 收稿日期:2005-03-08王富勇(福建电力职业技术学院,福建泉州 362000)摘 要:火力发电厂烟气脱硫方法之一的湿式石灰石-石膏法脱硫法,其主要优点是:原料价廉易得;投资及运行费用较低;技术应用广且成熟.并提出了进一步完善湿式石灰石-石膏法脱硫技术的建议.关键词:湿式;脱硫技术;石灰石-石膏法;结垢;生成物中图分类号:X701.3 文献标识码:ATechni que and Anal ysis ofDesulfurization ofW etL m i estone-gyps u mW ANG Fu-yong(Fuji an E l ectric Voca tio nal and Technica l College,Quanzhou 362000,China)Abst ract: There ar e m any w ays o f flue gas desulfuriza tion i n po w er p lants.A t p r esent we t li m estone-gypsum i n the w e t desu lfurization is one of t h e m ost popu larm ethods in t h e w orl d because of its lo w cost in m aterials,easy access,less invest m ent,lo w operation cost and w ide application. This paper offers suggestions on ho w to consumm ate the techn i q ue of we t li m estone-gypsu m furt h e r. K ey w ords: w e t;desulfurizing techn i q ue;li m est o ne-gypsum m e thod;fouling;resu ltant 长期以来,我国的能源以煤炭为主,因而电力工业也是以消耗煤炭的火力发电为主.伴随着经济的快速发展和能源需求的不断增长,煤炭的利用在给我们带来巨大物质财富和生活水平提高的同时,也带来了越来越大的负面影响.目前我国SO2的排放量已成为世界第一,酸雨区面积占国土总面积的30%,青藏高原以东、长江干流以南已成为世界第3大酸雨区.酸雨污染每年给我国造成的损失超过1100亿元人民币,占国内生产总值的2%~3%.按照目前控制污染的方式和力度,预计到2020年,我国SO2排放量将达到2.8×107t左右,超过大气环境容量约1.6×107t,将对生态环境和人体健康造成严重影响.我国酸雨呈典型的硫酸型酸雨,有90%以上的SO2来自于能源利用,SO2排放的增加量与煤炭消耗量的相关系数高达0.98[1].因此,采用合理的烟气脱硫技术,控制燃煤产生的SO2,是减少SO2排放量的关键,也是抑制我国酸雨污染的关键.燃煤炉烟气脱硫方法主要有:湿式石灰石-石膏法、荷电干吸收剂喷射法、喷雾干燥法烟气脱硫、炉内喷钙加尾部增湿活化脱硫、循环流化床锅炉脱硫、有机胺循环法脱硫,以及磷铵合肥法烟气脱硫法、海水脱硫法、电子束照射法排烟脱硫等.其中湿式石灰石-石膏法脱硫技术在大型燃煤锅炉中应用最广,在我国高达85%.1 脱硫原理及工艺流程该法使用石灰石作为吸收剂,副产品是脱硫石膏,具有价廉、技术成熟、运行稳定可靠、脱硫效率高(大于等于95%)、Ca /S 比低(1.03~1.05)、适用于任何煤种、脱硫副产品可用率高等优点.目前200MW 及以上容量机组大多选择湿式石灰石-石膏法脱硫工艺,如重庆珞璜电厂的2×360MW 机组、重庆电厂的2×300MW 机组、扬州电厂1×200MW 机组、京能热电厂1×200MW 机组等.北京一热2×410t /h 炉采用湿式石灰石-石膏法脱硫工艺,其排放出的SO 2只有5~8m g /m 3,远低于国标400m g /m 3.1.1 脱硫原理石灰石-石膏法脱硫的基本原理是:进入吸收塔烟气中的SO 2被吸收而成为H 2SO 3.此时,H 2SO 3被离解为H +及H SO 3-离子.其中:一部分H SO 3-被烟气中的O 2氧化成H 2SO 4,再和浆液中的CaC O 3反应生成C aSO 4 2H 2O (即石膏);另一部分H SO 3-在吸收塔贮槽中被空气氧化成H 2SO 4,再和原料中的C a CO 3中和,形成CaSO 4 2H 2O.由此可见,湿式石灰石-石膏法脱除烟气中SO 2主要有两大过程:一是吸收,二是氧化[2].其主要反应为C a CO 3+2SO 2+H 2O →C a (HSO 3)2+C O 2↑C a (H SO 3)2+12O 2+H 2O →C aSO 4 2H 2O +SO 22CaSO 3 12H 2O +O 2+3H 2O →2CaSO 4 2H 2OCa 2++SO 42-+2H 2O →C aSO 4 2H 2O 1.2 工艺流程湿式石灰石-石膏法的脱硫工艺流程如图1所示.图1 湿式石灰石-石膏法的工艺流程 此工艺流程主要包括烟气系统、吸收系统、吸收剂制备系统、石膏脱水及储存系统等.基本工艺流程为:除尘后的烟气经热交换及喷淋冷却后进入吸收塔内,与吸收剂浆液逆流接触,脱除所含的SO 2,净化后的烟气从吸收塔排出,通过除雾和再热升压,最终从烟囱排入大气.吸收塔内生成的含亚硫酸钙的混合浆液用泵送入p H 调节槽,加酸将p H 值调至4.5左右,然后送入氧化塔,由加入的约5kg /c m 2的压缩空气进行强制氧化,生成的石膏浆液经增稠浓缩、离心分离和皮带脱水后形成石膏制品.吸收剂的制备是将石灰石磨制成石灰石粉,133 王富勇:湿式石灰石-石膏法脱硫技术及分析由石灰石筒仓输送至石灰浆调制槽,制成的石灰石浆液通过浆泵打入吸收塔.2 脱硫技术问题分析2.1 存在的主要问题2.1.1 结垢和沉积结垢主要有3种形式:一是灰垢,主要集中在吸收塔入口干/湿交界处,原因是高温烟气中的灰分在遇到喷淋液的阻力后,与喷淋的石膏浆液一起堆积在入口,且越积越多;二是石膏垢,当吸收塔的石膏浆液中的CaSO4过饱和度大于或等于1.4时,溶液中的CaSO4就会在吸收塔内各组件表面析出结晶形成石膏垢;三是当浆液中CaSO3浓度偏高时就会与CaSO4同时结晶析出,形成混合结晶C a(SO3)x(SO4)1/2H2O,即CCS 垢[3].结垢和沉积将使管道堵塞、磨损、腐蚀,以及系统阻力增加,从而使烟气的流通面积减小,流速增大,烟气与浆液的接触几率减小,导致脱硫效率降低.2.1.2 设备磨损由于流体(烟气和石灰石浆液)中含有固体颗粒,流速高,当流体流过脱硫设备及管道时对相关部位产生切向切削和法向冲击而造成磨损,特别是当流体中含有剥落的垢块时磨损更加严重.磨损使浆泵等脱硫设备及管道的运行不稳定,从而降低脱硫效率.2.1.3 设备腐蚀腐蚀主要发生在热交换器、烟道和吸收塔等处.为满足吸收塔的进口烟温要求,流经热交换器的烟气温度可能会降至酸露点,烟气中的硫酸蒸汽凝结并附着于受热面,从而产生低温腐蚀,并会引起受热面粘结烟尘,导致堵塞加重.腐蚀使换热设备的运行可靠性降低,可用率下降,直接影响脱硫系统的运行效果.2.2 改进措施2.2.1 防止结垢和堵塞在吸收塔的结构设计方面应尽量做到以下几点.(1)型式合适 目前用于湿法烟气脱硫系统的典型吸收塔有喷淋塔、填料塔、多孔板塔、液柱塔等,使用最为广泛的是喷淋洗涤塔(塔内无复杂的结构部件).(2)结构简单 内部结构不能复杂,一般采用无浆液停滞的塔结构.如重庆珞璜电厂就选用中空的液柱塔,塔内设置上百个陶瓷喷嘴.喷嘴喷出约6m高的液柱,烟气与脱硫浆液逆流接触,从而使塔内结垢大大减少[4].(3)液气比要适当 注意选用适当的液汽比,设计合适的循环液量、吸收塔液室容量,以控制石膏的饱和度,并确保石膏晶种的生成.(4)选择合理的工艺 如在吸收塔入口烟道增加冲洗水喷嘴,定期冲洗结尘,以减少结垢.在日本CT-121工艺中,气体分散方法使表观气流流速可达数千m3/(m2h),形成的汽泡层使气液界面加大;J BR内反应区由于空气鼓泡与机械搅拌,使空气与液体充分混合,再加上有悬浮的石膏晶种和足够的停留时间,可使石膏晶粒长至需要的大小[3],从而大大减轻了结垢和堵塞.在运行操作方面,要做到以下几点.(1)提高除尘器的效率和可靠性,强化除尘效果,严格控制烟气带入的尘量.(2)为加快亚硫酸钙的氧化速度,压缩空气最好以极细小的气泡送入,一般宜采用回转式雾化器将压缩空气送入氧化塔底.在保证强制氧化的空气量方面,应控制好氧化风机的台数,使CaSO3氧化成CaSO4的量增加.(3)控制溶液中易于结晶的物质不要过饱和(过饱和度小于等于140%),以保持一定的晶种,使石膏晶体的生长有较大优势.(4)控制吸收液中水分蒸发速度和蒸发量,防止过饱和.(5)控制溶液的p H值,防止发生剧变.如能将浆液的pH值控制在4.5左右,则亚硫酸钙氧化成硫酸钙的环境最佳,可保证亚硫酸钙的氧化率.(6)根据锅炉的负荷即烟气排放量的多少作跟踪调节控制.(7)依据运行经验控制启停循环泵的台数,并尽可能使脱硫系统连续稳定运行,以减少系统启停的次数.(8)通过加添加剂的方法,增加H SO3-的活度,降低C a2+的浓度,使系统在未饱和状态下运行,防止硫酸钙结垢,如添加氯化钙、氧化镁、有机134上 海 电 力 学 院 学 报 2005年酸(如己二酸)、表面活性剂等.另外,为防止喷雾嘴和除雾器结垢,在采用简单构件的同时,应加强过滤与清洗.2.2.2 防止磨损为了防止磨损,必须做到如下几点.(1)设计时设备采用耐磨材料,并加内衬(如泵采用衬胶技术)或涂敷耐磨损材料;磨损严重部位(如管道的弯头、三通以及变径管等),可采取特殊防护措施,其备件应采用防磨材料制造,以便维修和更换.(2)运行时采用合理的流速(金属磨损与流速的3~3.5次方成正比关系);并控制流体中的固体颗粒含量(撞击次数越多磨损越多),如对进入吸收塔前的烟气进行高效除尘(静电除尘);还要加强运行监控,以减少进入泵内的空气量,调整好吸入侧护板与叶轮之间的间隙,以减少气蚀磨损.(3)检修时应加强对磨损严重部位的检测和修复.2.2.3 防止腐蚀防止腐蚀的措施主要有以下几条.(1)优化设计 根据流体的组成、温度和浓度等使用耐腐材料,并考虑防腐内衬的施工.如重庆珞璜电厂二期脱硫系统热交换器采用ND钢,并设计成光管式,减小壁厚,加大肋片厚度,增加肋片间距;吸收塔采用内衬玻璃鳞片树脂技术,不但基本解决了低腐问题,减少了维护费用,而且提高了运行的可靠性[4].又如连州电厂采用不锈钢、氯丁基橡胶、玻璃鳞片涂层和玻璃钢等防腐材料,有效地解决了腐蚀问题[3].(2)加强运行监测和维护 如pH值范围的监测,因为控制pH值对脱硫效率和防止氧化皮有重大作用,但不适当地降低p H值也会导致加速腐蚀.因此,运行时要及时清理沉积物和氧化皮,否则会增加点蚀和缝隙腐蚀.2.2.4 生成物的利用和处理石灰石-石膏法脱硫的主要附产物是二水石膏(C aSO42H2O),其纯度一般在90%以上,日本、法国的利用率都在90%以上.通常可采用以下3种方法利用二水石膏.(1)将石膏仓中的粉状二水石膏直接卖给用户(主要是建材部门),加工成石膏制品;(2)将粉状二水石膏加工成半成品(如粒状),再卖给水泥厂,或将二水石膏加工成半水石膏(C aSO41/2H2O)出售;(3)电厂自己设置石膏制品生产线,如将粉状二水石膏制成石膏砌块和粉刷石膏等.目前,石膏不仅能得到综合利用,而且在不影响粉煤灰利用的情况下能保证有充足的处理堆放场地.残留SO2和CO2的处理可采用如下两种方法.(1)用一定的化学液对残留的少量SO2和CO2进行吸收处理.如亚太环保开发研究的以氨气、氨水或碳铵为原料,吸收SO2并同步催化氧化亚硫酸盐为硫酸铵,再与氯化钾反应生成硫酸钾及副产品氯化铵的技术;或用碱溶液(如造纸厂的碱性废液)吸收CO2,SO2后对生成物进行再处理.(2)用活性碳或在尾部烟道内涂石灰乳吸收残余的SO2.3 几点建议3.1 脱硫设备国产化以降低脱硫成本脱硫设备国产化是降低设备造价的根本出路.首先对国外转让技术进行消化吸收.如日本千代田公司CT-121工艺(即J BR鼓泡式反应器,将SO2的吸收、氧化、中和、结晶,以及除尘等合并到一个单独的气相-液相-固相反应器中)、德国斯坦米勒公司技术等,在消化吸收的基础上经过工程实践,进行标准转换和技术创新,创立了自己的品牌,特别是对目前主要依赖进口的专用设备,如大容量循环浆泵、大容量氧化风机、塔内喷淋系统等,均应加大研制开发的力度,并大力推广脱硫除尘一体化技术.3.2 提高脱硫工程的综合经济性工程经济性的综合评价,应综合考虑工程投资和安全运行及运行费用进行,包括一次投资、年运行费,以及整个系统的安全运行、设备寿命等.因此应结合脱硫示范工程选择一合适的价位.湿法脱硫技术,公用系统考虑统一采用气-气加热器(GGH),可接受的价位一般为:2×600MW机组不大于300~350元/K W;2×300MW机组不高于350~400元/k W;200MW及以下机组不高于135 王富勇:湿式石灰石-石膏法脱硫技术及分析400元/k W[1].3.3 避免二次污染虽然目前的技术水平已使脱硫石膏能得到综合利用,但由于其产品还相对较少,再加上投资资金、销路及价格低廉等问题,造成部分工厂对采用脱硫技术不积极.有的干脆弃用脱硫及其副产品加工技术,不进行任何处理就直接排放,从而引发二次污染.此外,湿式石灰石-石膏法在处理SO2的同时又增加了CO2的排放量,对大气造成了新的污染.因此,如何完善湿式石灰石-石膏法脱硫技术,减少投资及运行费用,大力开发副产品,提高副产品价格,拓宽销路,更合理、更环保地进行脱硫治污乃是当务之急.3.4 从政策上保证脱硫措施的落实(1)实行排污许可证制度;(2)新建机组必须上脱硫设备;(3)提高SO2排污收费标准;(4)实行优惠扶持政策,如脱硫机组可享受优先上网、环保折价、资金补贴等.我国在《对燃煤二氧化硫排放污染防治技术政策》中已明确规定:燃用含硫量2%煤的机组或大容量机组(200MW)的电厂锅炉,在建设烟气脱硫设施时,宜优先考虑采用湿式石灰石-石膏法工艺.4 结束语大型机组采用湿式石灰石-石膏法烟气脱硫技术,其高脱硫效率是目前解决环保压力的最佳出路.我们必须大力加强脱硫技术的国产化及创新,解决初投和运行费用偏高等问题,并辅以优惠政策,鼓励此种技术的推广.参考文献:[1] 舒惠芬.燃煤电厂的S02控制[J].电力设备,2003,(8):4~8.[2] 吴怀兆.火力发电厂环境保护[M].北京:中国电力出版社,1996.[3] 曾庭华,杨 华,马 斌,等.湿法烟气脱硫系统的安全性及优化[M].北京:中国电力出版社,2004.[4] 陈绍敏.珞璜电厂湿式石灰石-石膏法脱硫系统运行中存在的问题及其分析[J].热力发电,2004,(7):46~48.136上 海 电 力 学 院 学 报 2005年。