催化裂化反再区空气环组装工艺改进
催化裂化装置反应再生系统优化改造

/
干气 液化石油气 3 # !4 3 # 3$ !4 # 4$
・ 0" 1 *! ) )2& 0" 7" 8" 97 97" 90% 9" 0$ 9" 0% 9! 04 9! 0$ ! :9% 0&3 " :9% 0&3 ! :9% 04 " :9% 04 # :9% 04 $ :9% 04 96 合计 &’ # &’ 3 # 6" &% # &! 3 # 6’ " # !" 4 # "" % # ’$#$ % # "4 &- # -’ $ # ’& # !$ ! # 4$ " # 4! & # !" & # 6$ ! # ’& &33 &" # 6 3 # 64 &" # "$ 3 " # 3" 4 # 6! ! # ’’ 6 # &! % # "&- # 66 4 # -% & # 4% $ # 6% # && & # ’4#& &33
计
!&&! 年第 "! 卷
达到多产液化石油气的目的。 (!) 提升管设两层原料喷嘴, 以适应不同原料 加工量, 并根据市场需要调整产品分布, 增加了装 置操作的灵活性。 (") 提升管出口粗旋风分离器改为挡板汽提 式粗旋风分离器, 将反应油气和催化剂快速分离, 同时尽可能地汽提掉催化剂上携带的油气, 减少 了二次反应, 增加了轻质油收率。 (#) 粗旋风分离器与顶旋风分离器采取软直 联形式, 缩短了反应油气和催化剂在沉降器中的 停留时间, 减少了二次反应, 同时减少了沉降器内 部的焦块形成, 保证了装置长周期运行。 ($) 汽提段的环形挡板改为新型高效汽提挡 板, 增加了汽提效果, 降低了焦炭中氢含量, 提高 了目的产品的收率。 (%) 沉降器中部增设格栅, 防止沉降器顶部的 焦块脱落后顺着待生立管掉到塞阀阀头, 影响催 化剂的循环量, 甚至堵塞待生立管。
催化裂化装置MGD工艺技术改造总结

催化裂化装置MGD工艺技术改造总结X武利春,夏建平,沈 兴,石占君,刘 建,孙 剑(中国石油呼和浩特石化公司,内蒙古呼和浩特 010070) 摘 要:为了适应环保要求,满足国家车用汽油质量标准,达到汽油质量升级的目的,催化裂化装置既要做到降低汽油烯烃含量,也要保证汽油辛烷值不降低。
研究决定,在停工检修期间对装置提升管反应器喷嘴部分进行技术改造,采用MGD工艺技术,结果表明,投用该工艺后,催化剂线路流化正常,操作运行平稳,能明显降低汽油的烯烃含量,汽油烯烃体积分数可降低6.5%。
关键词:催化裂化;MGD工艺;烯烃 中图分类号:T E968 文献标识码:A 文章编号:1006—7981(2012)05—0108—01 呼和浩特石化公司催化裂化装置改造设计加工能力为90万t/年,原料以常压渣油为主,另掺杂罐区蜡油和部分减压渣油。
反再部分采用两器为同轴式设计,再生器形式为单段逆流高效CO助燃剂完全再生。
根据公司500万t/年炼油扩能改造项目建设的需要,溶剂脱沥青装置拆除后,催化裂化原料性质将明显变重,催化汽油烯烃含量上升,出厂汽油烯烃无法长期稳定达到国Ⅲ质量指标要求。
为了能更好地降低汽油烯烃含量,最大限度地提高装置经济效益,研究决定,在停工检修期间对装置提升管反应器喷嘴部分进行改造,采用MGD工艺技术。
1 改造内容在原有设备的基础上对提升管反应器原料喷嘴部分进行了改造,将上喷嘴拆除,保留原料油下喷嘴,并将原料油下喷嘴上移,增加了预提升段长度,另外,在原料油喷嘴下方新增加2个改质汽油喷嘴,以满足降低汽油烯烃的目的。
2 投用后运行情况MGD改质汽油投用,喷嘴流量为20t/h,保护蒸汽流量为0.2t/h。
投用条件达到了MGD工艺的要求。
投用后催化剂流化正常,操作平稳,汽油烯烃含量明显下降,体积分数可控制在34.0%以下,辛烷值略有上升,产品分布较好。
3 混合原料性质表1混合原料性质对比项目改造前改造后密度(kg/m3)891.2894.5残炭(%) 4.47 5.67由表1可知,投用MGD工艺前后,原料性质变化很大,混合原料密度上升333,残炭上升了%,说明在投用MGD工艺后原料性质变重、变差。
改进催化裂化二反器气固输送状态

1 .前 言
实, 而予 提升蒸汽压力降至 0 5 a 提升力 . Mp , 3 不足 ,冲不破密 相床层 ,下 部蒸汽 压力憋到 05 a , . Mp 后 冲破密相床层 , 成” 3 形 打炮” 现象 , 催 化剂 冲起 后 ,后 续 蒸 汽压 力 迅 速下 降至 01 a . Mp ,流化终 止 ,催化剂 又 回落 到二反器
行两器 流化 ,催 化剂流化 经第一反应 器至二
流 ,而在 二反器内形成反混 ,回落至隔栅上 , 反器后 , 密度 和藏量 剧增 , 上限达 8 吨 ,而 造成 密度 、藏量上升 ,最终流化不起来。 . 5
用新 型提升管 反应器促使 不 同的反应器实 现 汽提段 无藏量显 示 ,说 明催化剂流 化动力不 裂化 、氢转移 和异构化反 应 ,以达到降低稀 足 ,停 留在二反器 中。
隔栅上 , 复冲击 , 往 形成这种振 动和响声 。具
由于对 大气污染 的 日益 重视 ,我 国 国家 环保局于 1 9 年 6 1日 99 月 发布 了 《 车用汽油 有 毒物质控制标准》 ,标准规定 了车用汽油的
规 格指标。该 标准于 2 0 0 0年 7月 1目起在北
京 、上海和广州执行 ,2 0 年 1 1日 03 月 在全 国执行 。该汽油质量 指标 中规定汽油烯 烃含 量 不大于 3 v 芳 烃含量不大 于 4 v 5 %, 0 %,苯 含量不 大于 2 v 硫 含量不大于 O 8 %。 . %, 5 .m 0 而我国成 品汽油 中催 化裂化 汽油 占 8 m 0 %以
烃含量 ,提高异 构烷烃含 量 的 目的。其第一
( )2 0 2 0 4年 5月 1 0日,装置切料后 ,提
不完全再生催化裂化装置再生器稀相超温的改进措施

不完全再生催化裂化装置再生器稀相超温的改进措施潘罗其;杨锦明;杜建文;陈正朝【摘要】分析了中国石油化工股份有限公司巴陵分公司催化裂化装置稀相超温的原因并提出了解决措施.通过更换合适孔径的汽提段锥段松动蒸汽孔板、改进待生套筒与待生立管间的密封结构、取消立管下段部分松动管线及实施松动管线的防断裂技术等一系列改造措施,消除了待生催化剂在密相床层中上部的不规则泄漏而造成的烧焦不均匀和松动风线断裂漏风引发CO二次燃烧的超温现象.优化改造后,再生烟气中CO的体积分数由改造前的6.5%~7.0%降为改造后的4.7%左右,CO在床层中分布均匀;稀相最高温度由708℃降为690℃,下降18℃,稀相温差仅17℃,消除了CO在稀相床层中二次燃烧引发的超温现象;进入再生器的风量平均增加了248m3/min,装置月平均处理量增加约4 950 t.【期刊名称】《炼油技术与工程》【年(卷),期】2018(048)007【总页数】5页(P29-33)【关键词】催化裂化;不完全再生;稀相超温;松动风线;二次燃烧;待生立管【作者】潘罗其;杨锦明;杜建文;陈正朝【作者单位】中国石油化工股份有限公司巴陵分公司,湖南省岳阳市414014;中国石油化工股份有限公司巴陵分公司,湖南省岳阳市414014;中国石油化工股份有限公司巴陵分公司,湖南省岳阳市414014;中国石油化工股份有限公司巴陵分公司,湖南省岳阳市414014【正文语种】中文1 装置存在问题中国石油化工股份有限公司巴陵分公司催化裂化装置采用MIP-CGP(增产丙烯、多产异构化烷烃的清洁汽油生产)工艺,以常压渣油为原料,年加工量1.05 Mt,同轴式反-再系统加外挂提升管反应器,再生烟气先通过烟机驱动主风机后进入CO焚烧炉和余热锅炉回收烟气中的化学能和余热。
近年来,为适应催化原料劣质化及油品质量升级的需要,需要将催化剂再生方式由原来的完全再生改为不完全再生,为此实施了MIP降烯烃工艺改造,并整体更换了汽提段、主风分布管和外取热器。
催化裂化工艺技术的改进

催化裂化工艺技术的改进催化裂化是一种重要的石油加工技术,主要用于将长链烷烃分子裂解为短链烯烃和芳烃。
以催化裂化技术为核心的石油炼制工艺已经发展了几十年,随着科学技术的不断进步,催化裂化技术也在不断改进和完善。
首先,研究人员通过改进催化剂的性能来提高催化裂化的效率。
催化剂是催化裂化技术的关键,可以促进原料油在裂化过程中的反应速率和选择性。
近年来,人们通过改变催化剂的组成、结构和物理化学性质,成功地实现了催化裂化反应的高效进行。
例如,研究人员发现,采用新型催化剂可以提高芳烃和短链烯烃的产率,同时降低副产物的生成率,从而提高产品的质量。
其次,研究人员改进了催化裂化反应器的结构和运行方式。
催化裂化反应器是催化裂化工艺的核心设备,直接影响到裂化产物的质量和产率。
为了提高催化裂化的效果,人们对反应器进行了各种改进。
例如,引入先进的内径梯度填料,可以增加反应器有效体积,提高催化剂与原料油的接触效率。
此外,还引入了多级反应器和中间分离回收装置,以优化反应条件,增加产品的收率,并减少催化剂的损失。
再次,研究人员改进了催化裂化过程中的催化剂再生技术。
催化剂的失活是催化裂化工艺中的一大难题,因为长期的高温、高压和有毒物质的作用会导致催化剂性能下降。
为了延长催化剂的使用寿命,人们引入了催化剂再生技术。
催化剂再生技术可以通过氧化、还原、酸洗和物理方法等手段,修复催化剂结构和活性,使其恢复到原来的状态,从而延长催化剂的使用寿命。
最后,研究人员还改进了催化裂化工艺中的产品分离和处理技术。
由于催化裂化反应产物的种类繁多、组成复杂,因此需要通过一系列的分离和处理工艺来得到目标产品。
为了提高产品的纯度和收率,人们引入了先进的分离技术,如闪蒸、吸附、蒸馏等。
此外,还研发了高效的处理技术,如催化裂化汽油加氢和重油深度加工等,以进一步提高产品的质量和降低环境污染。
综上所述,催化裂化工艺技术在不断改进和创新中不断提高着效率和产品质量。
通过改进催化剂的性能、反应器的结构、催化剂再生技术和产品分离处理技术,可以提高催化裂化的经济效益和社会效益,为石油加工行业的可持续发展做出贡献。
200万吨-年重油催化裂化反—再系统的设计

200万吨-年重油催化裂化反—再系统的设计200万吨/年重油催化裂化反—再系统的设计引言:随着工业化和城市化进程的加速发展,我们对石油产品的需求日益增长。
然而,石油资源的有限性使得石油加工工艺的研究显得尤为重要。
本文旨在探讨200万吨/年重油催化裂化反—再系统的设计。
一、催化裂化反—再系统的意义催化裂化是将较重、难以利用的石油馏分转化为高附加值的轻质石油产品的重要工艺之一。
200万吨/年的重油催化裂化反—再系统相当于每年从废旧物质中生产出200万吨的高附加值石油产品,对于节约资源、提高能源效率具有重要意义。
二、系统设计的基本原则1. 去除杂质:在重油催化裂化反应前,需要通过一系列处理步骤去除重油中的硫、氮等污染物,以保证反应的高效进行。
2. 催化剂选择:在催化裂化反应中,选择合适的催化剂对于提高反应效率非常关键。
我们可以选择活性高、稳定性好的催化剂,并结合新型载体材料、表面改性技术来改善催化剂性能,延长催化剂使用寿命。
3. 反应温度控制:催化裂化反应是一个高温反应,控制反应温度的适度升降,能够有效提高反应速率和产物分布,减少不良反应的发生,提高产品质量和数量。
4. 步骤合理性:合理地选择反应器结构和组件布置,能够有效地提高催化裂化反应的效果。
此外,选择合适的分离和再生工艺对产品质量的改善也至关重要。
三、系统设计的具体内容1. 前处理单元:主要包括在反应前对重油进行加热、脱水、除杂、除硫、除氮等步骤。
这些步骤旨在提高重油的质量,为后续的催化裂化反应做好准备。
2. 反应器单元:反应器单元是系统的核心部分,其中包括催化剂床、烟气分布器等。
在这个单元中,油与催化剂发生接触,经过裂化反应获得轻质石油产品。
合理地选择反应器结构和组件布置,能够提高催化裂化反应过程的效果。
3. 分离单元:分离单元是将裂解产物中的不同组分分离出来的过程。
通过减压蒸馏、消除剂分离等方法,可以将裂解产物中的轻质石油产品、液体石油气、重油等进行有效地分离。
催化裂化装置反_再系统的高温腐蚀与防护

专 论石油化工腐蚀与防护Corr osi on&Pr otecti on in Petr ochem ical I ndustry2009,26(4)・30・催化裂化装置反-再系统的高温腐蚀与防护苏志文(中国石油化工股份有限公司广州分公司,广州510726)摘要:催化裂化装置反-再系统的腐蚀主要表现为催化剂引起的磨蚀、冲蚀,高温气体腐蚀和应力腐蚀开裂等。
发生磨蚀和冲蚀的部位主要有:塞阀的阀头和滑阀的阀板、提升管预提升蒸汽喷嘴、原料油喷嘴、主风分布管、反应油气管线上弯头、提升管出口的快速分离设备、旋分的锥体顶端和翼阀阀板。
发生高温气体腐蚀的部位主要有:烟气线的热壁段以及与烟气接触的设备。
应力腐蚀开裂情况可分为热应力引起的焊缝开裂、氯化物应力腐蚀开裂及硝脆等。
目前,反-再系统的腐蚀主要还是以磨蚀、冲蚀以及高温气体腐蚀较为明显。
关键词:催化裂化 反-再系统 腐蚀类型 防护中图分类号:TE98519 文献标识码:A 文章编号:1007-015X(2009)04-0030-04 鉴于催化裂化原料重质化的发展趋势,催化裂化装置的腐蚀问题逐渐引起足够的重视。
催化裂化装置的腐蚀情况由于腐蚀部位、腐蚀介质、腐蚀的外界环境和腐蚀的诱因的不同而存在不同的腐蚀形态和不同的腐蚀类型。
对于不同的腐蚀部位,应根据其腐蚀介质和腐蚀环境的不同分别采取不同的防护措施。
一般说来,催化裂化装置按照工艺流程可分四个系统,即反-再系统、分馏系统、吸收稳定系统和能量回收系统还有脱硫-溶剂再生系统等。
文章根据催化裂化装置的工艺特点和腐蚀状况就高温部位反-再系统进行一些讨论。
1 催化剂引起的磨蚀和冲蚀由于催化剂具有一定的机械强度,同时随着反应油气和再生烟气高速流动,不断地冲刷构件的表面,使构件大面积减薄,甚至使构件局部穿孔;这种磨蚀和冲蚀现象对设备造成的影响非常严重,目前的解决措施除了提高设备材质的强度、构件的裕量外,还加耐磨衬里。
磨蚀和冲蚀的程度与催化剂的流速、流化状态下的密度、流动状态和高温机械强度有关。
石油催化裂化—反再系统工艺流程介绍

类型:单段再生
两段再生
快速流化床再生
2、再生器
催化剂堆积密度 较小 较大
稀相区气速 0.6 - 0.7 m/S 0.8 - 0.9 m/s
5-7m
稀相区 密相区
两级串联 旋风分离器
分离效率 99.99%
2、再生器
(分 碟布 形板 )式
目的:使烧焦空气进入床层时沿截面分布均匀
空气分布器
( 平 面 分树 布枝 管形 式和 环 形 )
3、取热器
3、取热器
内
外
取
取
热
热
4、主风机
作用:
➢ 提供烧焦所需的氧气; ➢ 保证再生器、烧焦罐内的
催化剂处于流化状态
课程小结
反
再
提升管反应器
系
统
再生器
典 型
取热器
设
主风机
备
提升管 快速分离器 旋风分离器
沉降器 汽提段
• 含催化剂颗粒的气体 • 由切线方向进入筒体 • 形成高速旋转的外涡流
• 颗粒被甩向器壁 • 落入灰斗 • 返回密相床层
• 气体受中心低压区吸引 • 形成向上内涡流 • 通过升气管排出
4.沉降器
沉降器:
利用重力的差别使流体(气体或液体)中的固体颗粒沉降的设备。
➢ 将气溶胶或悬浮液导入器内,经一定时间的静置或极慢的 流动,然后将沉降物导出器外。
课程:石油炼制运行与操控
知识点:反再系ห้องสมุดไป่ตู้典型设备
催化裂化
反应-再生系统 分馏系统 吸收-稳定系统
反再系统典型设备
1、提升管反应器
提升管反应器
提
快 速
旋 风
沉
汽
升
催化裂化装置(FCC)能量优化途径和方法
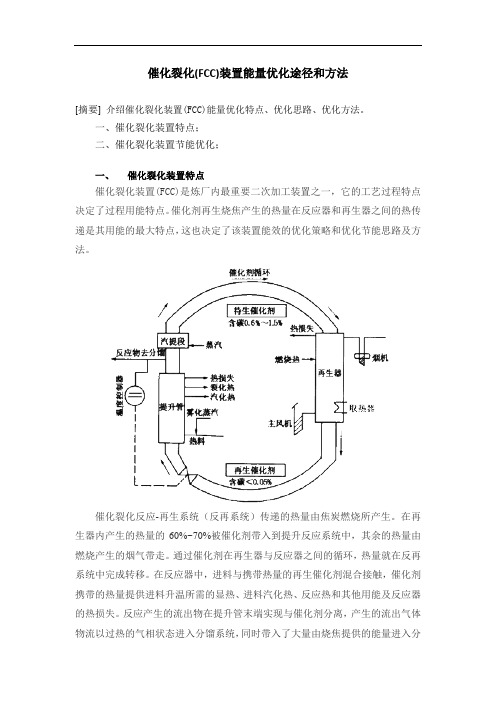
催化裂化(FCC)装置能量优化途径和方法
[摘要] 介绍催化裂化装置(FCC)能量优化特点、优化思路、优化方法。
一、催化裂化装置特点;
二、催化裂化装置节能优化;
一、 催化裂化装置特点
催化裂化装置(FCC)是炼厂内最重要二次加工装置之一,它的工艺过程特点决定了过程用能特点。
催化剂再生烧焦产生的热量在反应器和再生器之间的热传递是其用能的最大特点,这也决定了该装置能效的优化策略和优化节能思路及方法。
催化裂化反应-再生系统(反再系统)传递的热量由焦炭燃烧所产生。
在再生器内产生的热量的60%~70%被催化剂带入到提升反应系统中,其余的热量由燃烧产生的烟气带走。
通过催化剂在再生器与反应器之间的循环,热量就在反再系统中完成转移。
在反应器中,进料与携带热量的再生催化剂混合接触,催化剂携带的热量提供进料升温所需的显热、进料汽化热、反应热和其他用能及反应器的热损失。
反应产生的流出物在提升管末端实现与催化剂分离,产生的流出气体物流以过热的气相状态进入分馏系统,同时带入了大量由烧焦提供的能量进入分。
催化裂化装置反再系统施工技术方法

催化裂化装置反再系统施工技术方法摘要:反再系统(反应器和再生器)是催化裂化装置的核心设备,是影响催化裂化装置安全和经济效益的关键因素,两器的施工工艺复杂,壳体厚度相差较大,焊接工作量和施工难度比较大,焊接变形较难控制、吊装难度大、内件安装精度要求高.本文我们主要以青海大美项目60万吨/年DMTO装置反再系统为例来探讨“两器”的组对安装工艺流程。
关键词:反应器、再生器、壳体组装、焊接、压力试验。
一、施工概述1、施工方法反应器、再生器采用“立式组装法”施工。
分段组对时按排版图的顺序和位置,采用立装法,由下至上依次组装各筒节,形成分段筒体。
分段安装时采用正装法将各分段筒体按顺序进行吊装。
封头、椎体需在组装平台上单独进行组装。
顶部封头预制成型组焊合格后,需翻转进行衬里施工。
顶部封头吊装前需将旋风、料腿等内部构件临时放置在筒体内。
2、反应器、再生器主要设备参数设备名称反应器(R1101)再生器(R1102)容器类别III类(A2级)II类(D2级)设计压力 MPa 0.25 0.25工作压力 MPa 0.2―0.3 0.2―0.3设计温度℃介质550,壳体350 介质720,壳体350工作温度℃450―550 600―720介质甲醇,油气,催化剂烟气,催化剂容器规格ϕ15600/ϕ11800×45090×36ϕ7000/ϕ5500×25300×22/24金属净重(不含衬里)600t 160t热处理局部热处理不做热处理液压试验 MPa3、反应器、再生器主要吊装分段参数筒节预制组对时可采用75t汽车吊两台,280t履带吊一台,400t履带吊一台进行现场分片分段组装。
其中反应器分四段、再生器分二段进行吊装,反应器、再生器分段吊装时第一段均采用400t履带吊吊装,其余各段吊装以及封头翻转均采用600t履带吊主吊,采用400t履带吊溜尾配合。
二、主要施工程序筒体、封头成品半成品及旋风分离器等内件检验验收→封头、椎体等组装成型→筒节、裙座组装成型→分段组装焊接→焊缝无损检测→接管安装→各段部分内件安装→劳动保护安装→基础验收→分段吊装(除封头外)→段之间环焊缝热处理、无损检测→上封头衬里→上封头翻转、吊装→旋风系统及内件安装→拆除临时加固件→交工验收。
万吨年新疆渣油催化裂化反再系统工艺设计

万吨年新疆渣油催化裂化反再系统工艺设计引言本文将介绍万吨年新疆渣油催化裂化反再系统的工艺设计。
催化裂化是一种常用的炼油技术,可将重质原油转化为高附加值的轻质产品。
本设计旨在提高反应转化率、优化产品分布并减少能耗。
首先,将会介绍系统的基本原理和工艺流程,然后深入讨论关键设备的选择和设计参数的优化。
最后,对设计方案进行总结和展望。
基本原理和工艺流程催化裂化反再系统是一种将重质原油转化为轻质产品的工艺,通过使用催化剂在高温下进行催化裂化反应。
基本原理是将原油在催化剂的作用下进行热解,产生大量的气体和液体产品。
该工艺流程通常包括以下步骤:1.反应器:原油和催化剂在高温下反应,产生裂解产物。
反应器通常采用流化催化床或移动床反应器。
2.分离器:将反应产物进行分离,得到轻质产品(如汽油、柴油)和重质产物(如渣油)。
3.催化再生:将用于反应的催化剂中吸附的杂质和积碳进行燃烧,恢复催化剂活性。
4.裂解气体处理:对裂解气体进行处理,如脱硫、脱氮、脱氢等。
设备选择和设计参数的优化反应器选择在选择反应器时,应综合考虑以下因素:•反应器类型:流化催化床反应器和移动床反应器是常用的选择。
流化催化床反应器具有较高的传热和传质效率,适合处理高含硫原料油;移动床反应器则适用于处理低含硫原料油。
•反应器尺寸:需要根据预计的产量和催化剂的重量来确定反应器的尺寸。
较大的反应器容器可以提高生产效率和运行稳定性。
•反应器温度和压力:反应器的温度和压力会影响反应的转化率和选择性。
应根据催化剂的性质和裂化产物的需求来确定最佳的反应条件。
分离器设计分离器的设计应考虑以下因素:•分离器类型:常见的分离器类型包括闪蒸塔、吸附分离塔和精馏塔。
根据不同的产品需求和分离要求,选择合适的分离器类型。
•收率和选择性:通过调整分离器的操作条件,如温度、压力和塔板,来达到所需的产品收率和选择性。
•分离器尺寸:分离器的尺寸应根据预计的产量和产品质量要求来确定。
较大的分离器可以提高分离效率和产品质量。
浅谈催化裂化装置大气环境污染和治理

能源环保与安全一、概述催化裂化装置的大气污染源主要来自再生烟气,再生烟气中含有S0、NO等有害组分和催化剂粉尘,会对周围环境造成污染。
有加热炉的装置,燃料在燃烧时也会产生一定的S0、NO等污染物质。
二、大气环境污染源和危害1.S0污染原料中的硫一般有5% ̄15%的沉积到焦炭上,在催化剂再生时,硫被氧化成S0,一般含有90%以上的S0,10%以下的SO3。
S0是具有剧烈辛辣窒息性气味的气体,在适宜的条件下会生成硫酸酸雾,它还可以与NOx发生光化学反应形成新的有毒物质,产生更严重的毒害。
S0主要会造成呼吸道的病变。
并且由于植物比人对S0更敏感,当其浓度超过0.01mg/kg时,即可对植物能造成损害。
2.NOx污染催化原料中的氮化物经过高温反应后,部分沉积在催化剂上,在高温条件下,与再生氧反应生成NO,并经再生烟气排至大气。
再生烟气中NO的含量与原料中的总氮量及过剩含量及催化剂上的铂浓度有关,总氮量、过剩氧含量、铂浓度越大,烟气中NO含量越高。
NO不仅直接对人体有害,而且NO与烃类气体共存时会产生光化学烟雾,对环境危害更大。
3.催化剂粉尘污染重油催化裂化装置每加工1吨原料油约损失催化剂0.8kg左右。
一套年处理量为150万吨的重油催化裂化装置每年向大气中排放的粉尘量近1000吨,这些粉尘中绝大部分小于10um。
大气中的颗粒物,一般大于10um的粉尘由于本身的重力作用能迅速落到地面,称为落尘。
如果小于10m就称为漂尘,空气中浮游粒子和漂尘一般具有很强的吸附能力,可把很多有害气体带入人体肺的深部,带入肺的深部会促成许多急性或慢性呼吸道病症的发生。
三、大气环境污染的治理1.S0的治理催化装置降低S0排放量的主要手段有原料加氢脱硫、烟气脱硫和使用硫转移催化剂及选择低硫含量的原料。
原料加氢一般有专门的加氢精制及加氢裂化装置,同时受原料品种的限制,目前国内催化装置还很少有自主选择原料的可能,因此在此处重点介绍硫转移催化剂和烟气脱硫技术。
催化裂化技术介绍及改造指南

催化裂化技术介绍MIP-CGPMIP-CGP:即增产丙烯、多产异构化烷烃的清洁汽油生产技术,该技术是中国石化石油化工科学院(石科院)在多产异构烷烃的催化裂化技术基础上开发出来的一种生产汽油组成满足欧ⅲ排放标准并增产丙烯的催化裂化工艺。
该工艺技术以重质油为原料,采用由串联提升管反应器构成的新型反应系统,在不同的反应区内设计与烃类反应相适应的工艺条件并充分利用专用催化剂结构和活性组元。
烃类在新型反应区内可选择性地转化,生成富含异构烷烃的汽油和丙烯,在生产清洁汽油的同时为石油化工装置提供更多的丙烯原料。
该工艺具有以下特点:①采用串联提升管反应器形式的反应系统,优化催化裂化的一次反应和二次反应,从而减少干气和焦炭产率,有利于产物分布的改善;②设计两个反应区,第一反应区以裂化反应为主;第二反应区以氢转移反应和异构化反应为主,适度二次裂化;③第一反应区反应温度更高,反应时间更短;第二反应区反应温度略低,主要以延长反应时间来促进二次反应,在二次裂化反应和氢转移反应的双重作用下,汽油从烯烃转化为丙烯和异构烷烃,汽油中的烯烃含量大幅度下降,同时汽油的辛烷值保持不变或略有增加;④专用催化剂具有强化不同反应区反应的功能,更好地满足该工艺生产方案的要求;⑤调变催化剂的裂化反应活性和氢转移反应活性以增加液化气的产率和液化气中的丙烯含量,从而提高丙烯产率和降低汽油烯烃含量。
基于上述特点,原料油在第一反应区内一次裂化反应深度增加,从而生成更多的富含烯烃的汽油和富含丙烯的液化气;在第二反应区内,汽油中的烯烃发生氢转移、异构化反应和二次裂化反应,从而降低汽油中的烯烃含量和增加液化气产率和丙烯产率。
多产柴油和液化气的MGD技术MGD 技术是中国石油化工股份有限公司石油化工科学研究院(RIPP)开发的以重质油为原料,利用常规催化裂化装置同时多产液化气和柴油,并可显著降低汽油烯烃含量的工艺技术。
该技术与常规催化裂化技术相比,具有以下特点:(1)采用粗汽油控制裂化技术,增加液化气产率,降低汽油烯烃含量,调节裂化原料的反应环境以增加柴油馏份的生成和保留。
- 1、下载文档前请自行甄别文档内容的完整性,平台不提供额外的编辑、内容补充、找答案等附加服务。
- 2、"仅部分预览"的文档,不可在线预览部分如存在完整性等问题,可反馈申请退款(可完整预览的文档不适用该条件!)。
- 3、如文档侵犯您的权益,请联系客服反馈,我们会尽快为您处理(人工客服工作时间:9:00-18:30)。
现状调查
以往在进行再生器空气环组对安装时(如图一所 示) ,厂家将空气环上的连接板已经焊接完成,我们 采用的是先将滑动板销轴与空气换进行连接,安装完毕 后(如图二所示),进行空气环水平组对作业,最后对 空气环进行水平效验(如图三所示),这样以来,在组 对时容易造成环管组对间隙过大,如果保证组对间隙及 水平度组对,空气环与连接板,连接板与滑动板之间容 易产生变形,导致滑动板位移不顺畅,严重时会造成空 气环连接板焊缝撕裂,影响装置正常运行。此次大检修 施工工期紧、任务重,采用原有的方法既费时又费工, 不利于快速、高效、保质保量组对。
原因分析
人
人员技术水平不够 工机具不符合规格 工人操作不熟练 空气环连接板 与滑动板不匹配
机
工机具没有经过效验
料
安装方法不合理 组对空气环方法不合理
内部温度未达到设计要求
法
环
空 气 环 连 接 板 与 滑 动 板 不 能 平 稳 滑 动
要因确认一
要因一:人员技术水平不够 确认方法:通过调查与分析,我们对参加此次安装组 对人员中的8人进行了技能鉴定调查:
巩固措施
通过改进后我们在保证了空气环对口错 变量以及空气环整体的水平度和椭圆度后, 经过装置一年的正常运行,空气环任然能够 滑动,事实证明采用新的工艺方法后能有效 解决空气环滑动问题,该施工方法已纳入施 工方案。
无形效益
通过对再生器空气 环组对安装技术的改进, 提高了施工效率,降低 成本,高效、快速、高 质量的完成了空气环的 安装组对工作。同时, 通过此次QC活动的开 展,增强了班组的凝聚 力及创新能力。
实施对策
我们采用新的安装方法,在进行再生器空气环组对时,人工利 用倒链先将空气环各段进行组对,组对完毕后(如图二所示),待 水平度达到指标后,在进行滑动板销轴与支座的连接(如图三所 示),以此类推,完成所有空气环的组对安装。
( 图 二 )
( 图 三 )
1、人工利用倒链先将空气环各段在空中进行整体组对 (如图四、图五所示)。
要因确认四
要因四:组对空气环方法不合理 确认方法:通过调查与分析,现有的安装方法在保证 空气环的对口错变量以及整体水平度和椭圆度后,连 接板与滑动板之间容易产生变形,连接板与滑动板不 能平稳滑动。 结论:要因
要因确认五
要因五:内部温度未达到设计要求 确认方法:通过调查与分析,在装置正常运行时反再 区内温度为400-500℃,符合标准。 结论:非要因
(图四)
(图五)
2、待水平度达到SH3514-2001 石油化工设备安装工 程质量标准后,在进行滑动板销轴与支座的连接(如图六、 图七所示)。
( 图 六 )
( 图 七 )
效果检查
通过采用新的空气环组对安装方法,在 保证空气环对口错变量以及空气环整体水平 度和椭圆度后,经过装置1年的平稳运行, 在今年大检修时我们对其进行了检查,空气 环仍然能够滑动,不像以往大检修时连接板 和滑动板已经严重变形,空气环不能滑动。
鉴定级别 初级工 中级工 高级工
人数
2人
3人
3人
结果达到了空气环组对安装所需要的技术水平。 结论:非要因
要因确认二
要因二:工机具没有经过效验 确认方法:通过调查与分析,在作业过程中所使用的 倒链、水平尺等工机具均经过计量鉴定。 结论:非要因
要因确认三
要因三:空气环连接板与滑动板不匹配 确认方法:通过调查与分析,空气环材质与连接板都 为不锈钢,滑动板与连接板之间是用销子连接,能够 使其之间滑动。 结论:非要因
水空气环安装能 力上新台阶 有效解决了空气 环不能滑动 解决了空气环连 接板、滑动板的 变形 采用新的空气环 组对方法
总结
此次技术改进活动的完成,从技术方面提高了我公 司在空气环组对安装的施工能力,解决了空气环滑动难的 问题,缩短了施工工期,不仅提高了企业经济效益,而且 提高了社会效益,为以后同类施工奠定了基础。
经济效益
改进前: 人工费用:42000元 铆工200元/天 : 20天×200元/天×6人=24000元 焊工260元/天:260元/天×10天×6人=15600元 架子工200元/天 :200元/天×2天×6人=2400元 再生器空气环安装工期 15天 改进后:人工费用:10100元 铆工200元/天 7天×200元/天×4人=5600元 焊工260元/天:5天×260元/天×3人=3900元 架子工200元/天 :200元/天×1天×3人=600元 再生器空气环安装工期 7天 合计节约: 人工费用: 42000元-10100元=31900元 节约工期: 15天-7天=8天
现状调查
(图一)
现状调查
(图二)
(图三)
选题理由
公司要求
提高再生器空气环组对质量 原有技术组对空气环容易造成 连接板或斜管接口处变形使得 空气换无法滑动
实际情况
选定课题
反再区空气环组装工艺改进
目标及目标值的确定
目标:提高再生器空气环组对质量,使空气 环能够平稳滑动。
目标值:装置运行一年后连接板与滑动板之 间不变形,空气环 Nhomakorabea够平稳滑动。