动平衡机技术要求
螺旋桨动平衡 标准
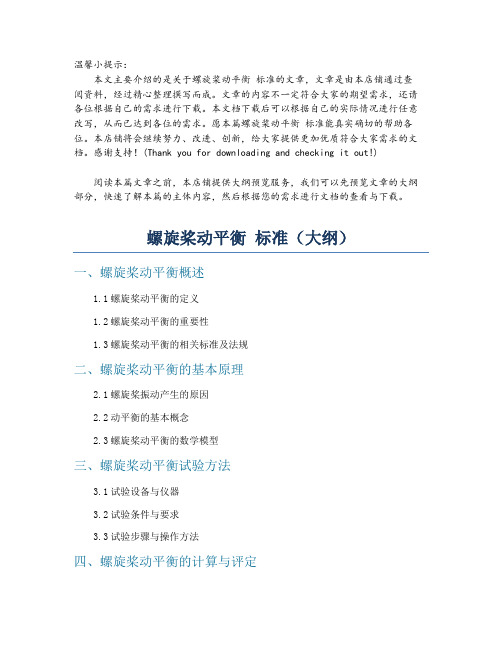
温馨小提示:本文主要介绍的是关于螺旋桨动平衡标准的文章,文章是由本店铺通过查阅资料,经过精心整理撰写而成。
文章的内容不一定符合大家的期望需求,还请各位根据自己的需求进行下载。
本文档下载后可以根据自己的实际情况进行任意改写,从而已达到各位的需求。
愿本篇螺旋桨动平衡标准能真实确切的帮助各位。
本店铺将会继续努力、改进、创新,给大家提供更加优质符合大家需求的文档。
感谢支持!(Thank you for downloading and checking it out!)阅读本篇文章之前,本店铺提供大纲预览服务,我们可以先预览文章的大纲部分,快速了解本篇的主体内容,然后根据您的需求进行文档的查看与下载。
螺旋桨动平衡标准(大纲)一、螺旋桨动平衡概述1.1螺旋桨动平衡的定义1.2螺旋桨动平衡的重要性1.3螺旋桨动平衡的相关标准及法规二、螺旋桨动平衡的基本原理2.1螺旋桨振动产生的原因2.2动平衡的基本概念2.3螺旋桨动平衡的数学模型三、螺旋桨动平衡试验方法3.1试验设备与仪器3.2试验条件与要求3.3试验步骤与操作方法四、螺旋桨动平衡的计算与评定4.1动平衡计算方法4.2动平衡评定标准4.3动平衡结果的处理与优化五、螺旋桨动平衡的修正措施5.1修正原理与方法5.2修正材料与工艺5.3修正效果的评价与验证六、螺旋桨动平衡的维护与管理6.1螺旋桨动平衡的日常检查与维护6.2螺旋桨动平衡的定期检测与评估6.3螺旋桨动平衡管理制度的建立与实施七、螺旋桨动平衡技术的发展与展望7.1螺旋桨动平衡技术的现状7.2螺旋桨动平衡技术的发展趋势7.3螺旋桨动平衡技术在未来的应用前景一、螺旋桨动平衡概述1.1 螺旋桨动平衡的定义螺旋桨动平衡是指在旋转过程中,螺旋桨各个部分的质量中心轴线与旋转轴线保持一致的状态。
动平衡的好坏直接影响到螺旋桨的使用寿命、工作效率以及整个系统的稳定运行。
动平衡包括静平衡和动平衡两个方面,静平衡是指在静止状态下,螺旋桨各个部分的质量中心轴线与旋转轴线重合;动平衡是指在旋转状态下,螺旋桨各个部分的质量中心轴线与旋转轴线无偏移。
动平衡机自校规程

煤炭科学研究总院重庆分院安全仪器装备实验室仪器设备自校准规范CYZ5×××—2006YYW-160型动平衡机自校准规范2006年5月30日批准 2006年6月5日实施煤炭科学研究总院重庆分院安全仪器装备实验室颁布YYW-160型动平衡机自校准规范CYZ5-XX—2006本自校准规范经煤炭科学研究总院重庆分院安全仪器装备实验室于2006年5月30日批准,自2006年6月5日起实施。
归口单位:煤炭科学研究总院重庆分院学术委员会起草单位:煤炭科学研究总院重庆分院安全仪器装备实验室本规范主要起草人:巨广刚、邓鹏目录1 范围 (1)2 引用文献 (1)3 术语和计量单位 (1)4 概述 (1)5技术要求 (1)6 校准条件 (1)7 校准项目和校准方法 (1)8 校准结果表达 (4)9 复校时间间隔 (4)10 附录 (4)YYW-160型动平衡机自校准规范1 范围本校验方法适用于不作外伸转子平衡校验的YYW-160A型动平衡机的校验。
2 引用文献按照GB4201-84《通用卧式平衡校验法》,并参照出厂检验,对YYW-160A型动平衡机进行性能测定。
3 术语和计量单位动平衡表征的是平面的轴向不平衡度。
4 概述动平衡机由控制箱、平横支架部分及平衡轴等部件组成。
5 技术要求≤0.5g.mm/kg。
5.1 每校正平面最小可达剩余不平衡量Umar≥85%。
5.2 不平衡量减少率URR6 校验条件6.1 室温:10~40℃;6.2 相对湿度:≤85%;6.3 电源电压:380±19V。
6.4 平衡转速:U校验:1300r/min;mar低阶校验:1300r/min;URR高阶校验:l300r/min;和650r/min。
URR7 校验项目和校对方法7.1 校验量具7.1.1 校验转子符合GB4201标准第2条规定的50Kg校验转子一只。
7.1.2 试重符合GB4201标准第3条规定的试重4组,每组2个。
1机床动平衡测试技术要求规范

机床动平衡测试技术规范沈阳机床(集团)有限责任公司“高速/复合数控机床及关键技术创新能力平台”课题组2012年5月1 简介动平衡技术是在转子校正面上进行校正平衡,校正后的剩余不平衡量,以保证转子在动态时是在许用不平衡量的规定范围内,在理想的情况下回转体旋转时与不旋转时,对轴承产生的压力是一样的,这样的回转体是平衡的回转体。
提高精度或精密化,减小振动噪音是制造技术的一个主要发展方向、是各种各类数控机床与基础制造装备在应用中所追求的目标。
动平衡技术不但可以用于各类数控机床,而且可用于各类设备包括大型和重型设备,还可用于高档数控装置等等。
因此,完成本课题的目标和任务对于国家“高档数控机床与基础制造装备”科技重大专项及其项目目标和任务来说,具有着重大作用和显著意义。
由于动平衡技术可用于各类数控机床、设备和高档数控装置。
本课题成果将可以为各类数控机床、设备和高档数控装置的开发提供技术支持,同时为这些数控机床、设备及高档数控装置的设计、制造及安装提供理论依据与保证。
动平衡技术已越来越多地应用于航天航空、国防、飞机制造、汽车制造等行业,其工程意义是非常显著的,这项技术可用于各种各类的机床及装备,而且不但可应用于新机床以提高其技术含量和精度,还可应用于老机床以焕发其新春和加入现代制造行列,提高机床及装备的加工精度是此项技术的目的。
2 试验的目的(1)对于回转零部件,由于零件结构不对称、材质不均匀、加工或装配误差等因素,不可避免地存在质量不均衡。
根据平衡理论,我们把具有一定转速的回转件称为转子。
如果转子的质量分布对其轴线而言不均匀、不对称,即其中心主惯性轴不能与旋转轴线重合,那么旋转时就会产生不平衡离心力,它会对支承架和基础产生作用力,而且还会引起机器振动,振动的大小主要取决于不平衡量大小及支承架和基础的刚度。
如果振动严重,则会影响机器的性能和寿命。
因此,在几乎所有的回转体零件中,平衡工艺是必不可少的工艺过程,它是减小转子振动的极为重要的手段,它能解决由于自由离心力造成的振动。
车轮平衡检测、校正
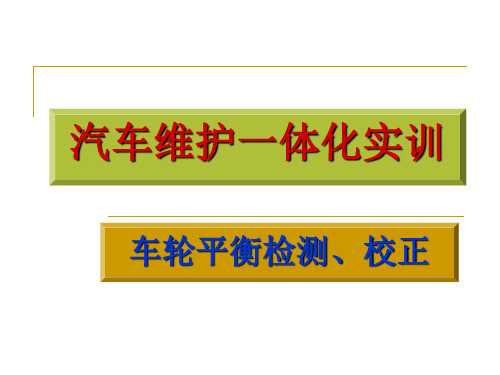
轮胎鼓包
磨损极限标志
2、清洁轮胎并拆除旧平衡块; 技术要求及注意事项:
(1) 对被测轮胎进行清洗,去掉泥沙,沙石等; (2) 拆掉车轮旧平衡块,拆完后不可随便丢弃。
3、检测轮胎压力并调整;
车轮动平衡机
主轴
测量卡钳
车轮锁紧扳手
显示仪
2、轮胎平衡块种类:
轮胎平衡块有两种,一种用于铝质辐板式车轮,一种 用于钢质辐板式车轮。铝制车轮所用平衡块直接粘贴到轮 辋内侧。钢质车轮所用平衡块卡在轮辋内、外边缘处。
钢质车轮用平衡块
铝质车轮用平衡块
轮胎动平衡的注意事项
1、首先要检查轮胎,然后清除石头和旧平衡块, 这一步不能省略,它是我们做轮胎动平衡的前提。
号
分分
扣分标准
1 安全问题 否决
造成人身、设备重大事故,或恶意顶撞考官,严重扰乱考场秩序,立即终 止考试,此题计0分。
2 安全文明 20分
1、不穿工作服、不穿工作鞋、不戴工作帽,各扣1分; 2、油、水洒落在地面或零部件表面未及时清理,每次扣1分; 3、垃圾没处理,每次扣1分; 4、竣工后未清理工具,每件扣1分; 5、不服从考官,出言不逊,每次扣3分;
□ 1:清理、检测被测轮胎。
检查轮胎花纹深度为:
mm,轮胎标准气压为:
(kpa)
□ 2:轮胎安装。
□ 3:选择正确测试方法。
□ 4:采集、输入数据,并将数据填写在下面:
轮辋边缘到测试机边缘的距离:
mm,轮辋的高度为:
mm,
轮胎断面宽度为:
mm。
□ 5:不平衡质量读取,并将测得值填写到表1中。
动平衡技术要求规范及操作指南设计

实用标准文档YYW-20T技术规范一、可平衡零件规格1.工件质量(包括平衡夹具)a.最小 500Kgb.最大 20000Kg2.每个支承座最大载荷 10500Kg3.工件最大直径Φ2500mm4.工件轴径范围a.小滚轮组Φ50~Φ190mmb.中滚轮组Φ190~Φ300mmc.大滚轮组Φ300~Φ400mmd.大滚轮组Φ190~Φ300mm5.工件两支承间距离 400~4400mm二、驱动主轴a.主轴电机:YVF2250M-4/B3 55KWb.平衡转速范围:100~1250r/min三、使用条件1.环境温度:-10~50℃2相对环境温度不超过85%3.电源:交流380V、50Hz,允许±10%的波动4.周围无强磁场及大的振动设备。
5.变速器型号:QJ五档系列变速器QJ805。
四、平衡精度1.最小可达剩余不平衡量:e mar≤0.4gmm/Kg2.不平衡量减少率:URR≥95%。
YYH-2000技术规范一、可平衡零件规格1.工件质量(包括平衡夹具)a.最小 500Kgb.最大 2000Kg2.每个支承座最大载荷 1050Kg3.工件最大直径Φ1600mm4.工件轴径范围a.小滚轮组Φ15~Φ190mmb.中滚轮组Φ190~Φ290mm5.工件两支承间距离 280~3100mm(圈带驱动)140~2250 mm(联轴节驱动)二、驱动a.联轴节驱动电机:YVF2180L-4/B3 22KWb.圈带驱动电机:YVF2180L-4/B5 22KWc.平衡转速范围:100~1200r/min三、使用条件1.环境温度:-10~50℃2相对环境温度不超过85%3.电源:交流380V、50Hz,允许±10%的波动4.周围无强磁场及大的振动设备。
四、平衡精度1.最小可达剩余不平衡量:e mar≤0.2gmm/Kg2.不平衡量减少率:URR≥95%。
操作指南1 安装参照系统接线图(图2),将彩色显视器插头、左右振动传感器插头、光电传感器插头和电源插头插好,一般情况下不需要变动。
汽车轮毂、制动鼓、制动盘动平衡技术要求
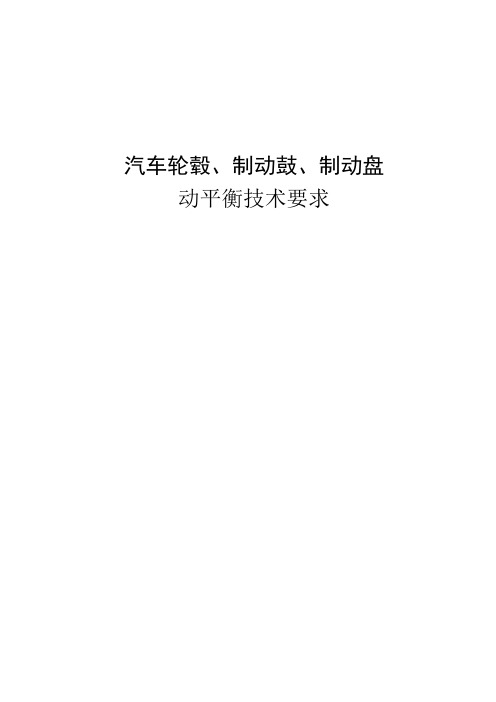
汽车轮毂、制动鼓、制动盘动平衡技术要求汽车轮毂、制动鼓、制动盘动平衡技术要求1 范围本标准规定了汽车用轮毂、制动鼓、制动盘动平衡的技术要求、试验方法、检验规则。
本标准适用于本公司生产的各类汽车。
2 规范性引用文件下列文件中的条款通过本标准的引用而成为本标准的条款。
凡是注日期的引用文件,其随后所有的修改单(不包括勘误的内容)或修订版均不适用于本标准,然而,鼓励根据本标准达成协议的各方研究是否可使用这些文件的最新版本。
凡是不注日期的引用文件,其最新版本适用于本标准。
GB/T 4201 平衡机的描述检验与评定GB/T 9239.1 机械振动恒态(刚性)转子平衡品质要求第1部分:规范与平衡允差的检验GB/T 9239.2 机械振动恒态(刚性)转子平衡品质要求第2部分:平衡误差JJG 011 就车式车轮动平衡仪检定规定3 术语和定义3.1 平衡:检查并在必要时调整转子质量分布,以保证在对应的工作转速频率下,剩余不平衡或者轴颈振动和(或)作用于轴承的力在规定限值内的工艺过程。
3.2 不平衡:转子旋转产生离心力所引起的振动力或运动作用于轴承时,该转子所处的状态。
3.3 剩余不平衡量:平衡后转子上剩余的不平衡量。
4 技术要求4.1 轮毂、制动鼓、制动盘应按照经规定程序批准的产品图样及技术文件制造,并应符合本标准要求。
4.2 轮毂、制动鼓、制动盘毛坏应进行抛丸处理,以消除残余应力,以防止变形。
4.3 轮毂、制动鼓、制动盘表面不得有毛刺、碰伤、划伤、裂纹等缺陷。
4.4 轮毂、制动鼓、制动盘必须全部经检验合格并清洗干净后才能装配。
4.5 轮毂、制动鼓、制动盘必须做动平衡试验,动不平衡要求应符合表1的规定。
产品的动不平衡量选用参考附录A(资料性附录)的规定。
表1 动不平衡要求表1(续)动不平衡要求4.6 剩余不平衡量的标识轮毂、制动鼓、制动盘(或轮毂制动鼓合件、轮毂制动盘合件)在动平衡机上测量动不平衡量,对剩余不平衡量做相应的标识。
动平衡机技术要求
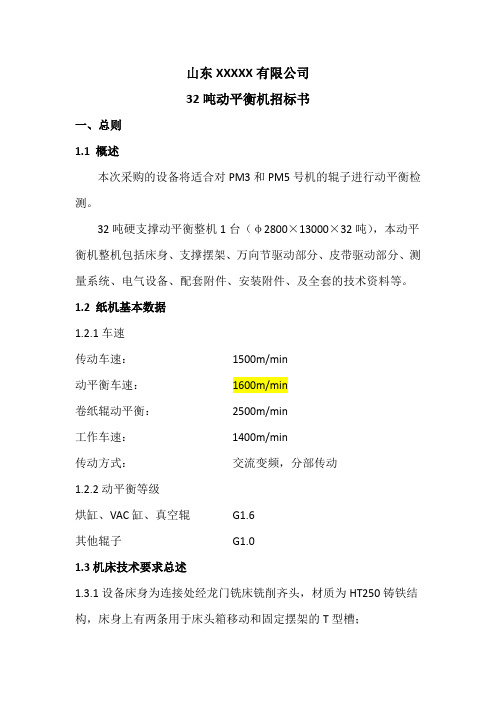
山东XXXXX有限公司32吨动平衡机招标书一、总则1.1 概述本次采购的设备将适合对PM3和PM5号机的辊子进行动平衡检测。
32吨硬支撑动平衡整机1台(φ2800×13000×32吨),本动平衡机整机包括床身、支撑摆架、万向节驱动部分、皮带驱动部分、测量系统、电气设备、配套附件、安装附件、及全套的技术资料等。
1.2 纸机基本数据1.2.1车速传动车速:1500m/min动平衡车速:1600m/min卷纸辊动平衡:2500m/min工作车速:1400m/min传动方式:交流变频,分部传动1.2.2动平衡等级烘缸、VAC缸、真空辊G1.6其他辊子G1.01.3机床技术要求总述1.3.1设备床身为连接处经龙门铣床铣削齐头,材质为HT250铸铁结构,床身上有两条用于床头箱移动和固定摆架的T型槽;*1.3.2在床身上安装一套支承摆架:标准支承摆架1组,所有摆架均采用锻钢线切割工艺,采用模块式结构;滚轮支承,带可锁定和可调节装置的压板安全架,刚度架上装有高精度磁力线圈测力传感器(采用进口件,不带机械放大器),用于检测摆架的振动;摆架的移动齿轮齿条的结构,并装有减速电机,电力驱动。
*1.3.3万向节驱动部分床头箱底座1件;六档机械齿轮变速箱1台;DC90KW电机1台;带刻度盘的万向联轴节1套。
(可轴向移动50mm 用于安装工件时的微调);2250Nm和50000Nm的专用万向节2套,带万向节保护罩;基准信号传感器1套(进口)。
皮带驱动采用气动张紧装置,确保每次工件受力均匀一致;基准信号传感器1套(进口);DC75KW电机1台。
1.3.4所有平衡机设备配套的电器设备、继电器、接触器、空气开关等电器元件须均采用国际知名品牌。
*1.3.5测量系统包括:德国进口产品,触摸屏设计,强大的向导提示,操作非常容易模块化设计,友好的服务系统,并可远程诊断嵌入式工业计算机,鼠标及外置键盘,强大的扩展功能,实现各种复杂的平衡任务,用Windows标准程序操作,USB接口,网络接口;双开门高档电控柜。
车轮动平衡机一些必须澄清的概念

10 、2 0、20 、20 、30 、30 的位 置 上 ,每 准 ( 8。 1。 4。 7。 0 。 3。 测量 )原 理 可 知 ,在 校 验转 子 上 加 已知标 准 试 进 行 一 次操 作 变 换 一个 位 置 ,每次 试 验 只 允许 一 次 重砝 码 m后 产 生 离 心力 F,通 过动 平 衡 机 中两 个 传 读 数 ,1 个 位 置 的检 测 数 据 应 记 人 表 2规 定 的 感 器 的反力 、 2 反 映。
件 :”
08 一 < <11 U .8 U . 2一 ( 3)
N = ± ± A Fx ±
( 式 × 4) L一 ( 6)式 得 :
% :,×
L
“. 将 l 点 的读 数 值 分 别 除 以相 应 平 面 的 6 7 2个 平 均 值 并 将 其 结 果 计 人 表 2相 应 平 面 平 均 值 倍 数
量 小于 1U …, 笔者 注 :U …, m ( m 是标 称 的最小 可达 剩 向 ”和 “ 对应 ” 了 。所 以 ,在有 的不 确 定度评 定 中 ,
余不平衡量 ,也 即车轮平衡机制造者宣称 自己的平 车轮动平 衡 机 的扩 展不 确定 度为 不平衡 量 5g 或平 衡
衡 机所 能达 到的指 标 )” 。 “. 两个 1 6 4用 0 ( 者注 : 笔
衡来检验。而关 于最小可达剩余不平衡量 ,在 G / BT
检 测
JF 11— 20 J 15 0 6应该 说 已经叙 述 ,“ _ 最 小 可 27 120 54 0 3- 06中已经规定得很明确 ,1 个点 的读数值 2 满 足 了条 件 ( .8 < <11 ) 08 .2 ,则 达剩余不平衡量 e , 20 ・ mk ” ≤ 0 m / 。 g g 但 在 规 范 的校 准 部 分 提 到如 何 判 断 ,却 没 有 明 合 格 。
数控机床加工过程中的刀具动态平衡技巧

数控机床加工过程中的刀具动态平衡技巧数控机床加工是现代制造业中常见且重要的工艺技术,而刀具动态平衡则是数控机床加工过程中的关键要素之一。
本文将介绍数控机床加工过程中刀具动态平衡的技巧,以帮助读者更好地理解和应用于实际生产中。
刀具动态平衡是指在数控机床运转过程中,对刀具进行调整以消除刀具在高速旋转时产生的不平衡力。
刀具动态平衡技巧的应用,不仅可以提高加工精度和效率,还可以延长刀具的使用寿命,减少机床的磨损。
首先,刀具的动态平衡是通过在刀具上安装平衡块或进行刀具编组来实现的。
平衡块的选择应根据实际情况来确定,一般情况下,较小的不平衡可通过在刀具上进行加块的方法来解决,而较大的不平衡则需要使用动平衡机进行校正。
刀具编组是指将不平衡的刀具分成若干组,每组中的刀具相互平衡,从而达到整体平衡的目的。
其次,在进行刀具动态平衡时,需要注意刀具的刚度。
刀具的刚度与刀具材料、工件材料以及刀具几何形状等因素密切相关。
一般情况下,刚度较低的刀具容易产生不平衡,因此需要采取措施提高刀具的刚度。
例如,可以选择刚度较好的刀具材料,优化刀具的设计结构,以提高刀具的刚性。
另外,刀具动态平衡还需要注意刀具的安装与调整。
在安装刀具时,要确保刀具与主轴的配合间隙适当,以及刀片的固定稳固。
调整刀具时,应根据实际情况采取适当的方法。
一种常用的调整方法是采用不同厚度的平衡垫片来平衡刀具,将平衡垫片安装在刀具的两侧,以达到刀具的动态平衡。
此外,刀具的磨损状态也会影响刀具的平衡状态。
因此,在加工过程中需要定期检查和修整刀具,及时更换磨损严重的刀片。
同时,还需要合理选择刀具的切削条件,避免过度切削导致刀具的不平衡。
总结起来,数控机床加工过程中的刀具动态平衡技巧包括选择适当的平衡块或进行刀具编组、提高刀具的刚度、注意刀具的安装与调整、定期检查和修整刀具以及合理选择切削条件等。
这些技巧的应用可以有效地提高加工的质量和效率,降低成本,推动制造业的发展。
车轮动平衡机检定规程试行
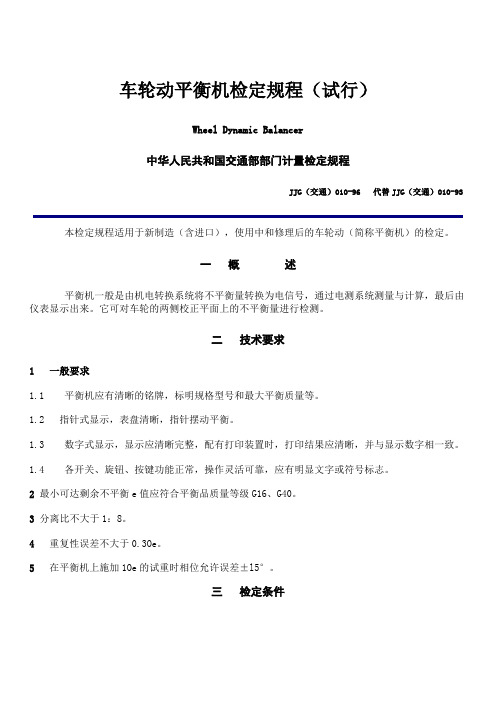
车轮动平衡机检定规程(试行)Wheel Dynamic Balancer中华人民共和国交通部部门计量检定规程JJG(交通)010-96 代替JJG(交通)010-93本检定规程适用于新制造(含进口),使用中和修理后的车轮动(简称平衡机)的检定。
一概述平衡机一般是由机电转换系统将不平衡量转换为电信号,通过电测系统测量与计算,最后由仪表显示出来。
它可对车轮的两侧校正平面上的不平衡量进行检测。
二技术要求1 一般要求1.1 平衡机应有清晰的铭牌,标明规格型号和最大平衡质量等。
1.2 指针式显示,表盘清晰,指针摆动平衡。
1.3 数字式显示,显示应清晰完整,配有打印装置时,打印结果应清晰,并与显示数字相一致。
1.4 各开关、旋钮、按键功能正常,操作灵活可靠,应有明显文字或符号标志。
2 最小可达剩余不平衡e值应符合平衡品质量等级G16、G40。
3 分离比不大于1:8。
4重复性误差不大于0.3Oe。
5在平衡机上施加1Oe的试重时相位允许误差±l5°。
三检定条件6 环境条件6.1 环境温度0-30°C6.2 相对湿度应小于85%6.3 电源电压波动量不应超过额定值的±10%6.4 检定现场周围应无强烈的振动源和高频信号干扰。
7 检定用器具7.1 架盘天平一架,称量范围0.2kg;7.2 砝码:克、毫克组各1套(M级);27.3 专用检定装置7.3.1 标准检定转子(见附表1);7.3.2 试重1组(见附录2)。
四检定项目与检定方法8 一般要求的检定通过目测,手感进行,其结果应符合第1条要求。
9 最小可达剩余不平衡量的检定9.1 准备9.1.1 选择一个质量约为平衡机允许平衡最大质量三分之一的标准转子。
9.1.2 选择平衡转速。
9.1.3 e值的确定(g·mm/kg),再由公式(1)计算e值:根据车轮最大工作转速,由附录3图2确定epere=me/2R (1)per式中:m--标准转子的质量(kg);R--标准转子的校验半径(mm);e--许用剩余比不平衡量(g·mm/kg)。
高速动平衡g1.0标准

高速动平衡g1.0标准全文共四篇示例,供读者参考第一篇示例:高速动平衡g1.0标准是一种用于评估高速旋转机械设备动态平衡性能的技术标准。
随着现代工业的发展,高速旋转机械设备在生产中的应用越来越广泛,而动平衡技术作为保证机械设备正常运行的重要手段,也变得尤为重要。
制定高速动平衡g1.0标准,对于提高机械设备的性能、减少故障和延长设备寿命都具有重要意义。
高速动平衡g1.0标准是由国内外专家多年实践经验总结和研究成果基础上制定的,它主要用于评估高速旋转机械设备的动平衡性能。
根据该标准,用户可以通过测量旋转机械设备的振动水平、分析振动数据以及进行动平衡调整,来确保设备在高速运转时的平衡性能达到要求。
只有通过动平衡g1.0标准评定后的机械设备,才能够保证在高速运转时具备良好的平衡性能,同时也可以减少机械设备在运行过程中出现不稳定、振动过大等问题,从而延长设备的使用寿命。
在高速动平衡g1.0标准中,首先需要对机械设备进行振动测试。
振动测试是通过专用的振动测量仪器对设备的振动水平进行监测和记录,可以有效发现设备在运行过程中存在的不平衡问题,并保证振动数据的准确性和可靠性。
根据振动数据,可以分析出机械设备在哪些位置存在不平衡问题,从而为后续的动平衡调整提供重要依据。
根据高速动平衡g1.0标准,机械设备存在不平衡问题时需要进行动平衡调整。
动平衡调整是通过在设备转子上添加特定重物或切削一部分材料的方式,使得设备在运行时不再发生不平衡现象,从而保证设备的平衡性能。
在进行动平衡调整时,需要根据设备的具体特点和振动数据分析结果来确定调整方案和调整方法,确保设备在高速运转时的平衡性能得以完全恢复。
除了对机械设备进行振动测试和动平衡调整外,高速动平衡g1.0标准还要求用户在设备运行过程中进行定期检查和维护。
通过定期检查和维护,可以有效预防设备在运行过程中出现不平衡问题,保证设备长时间稳定运行。
用户还应该对设备进行定期保养和清洁工作,确保设备在运行过程中不受到外界环境的影响,减少设备出现故障的可能性。
破碎机动平衡机 -回复
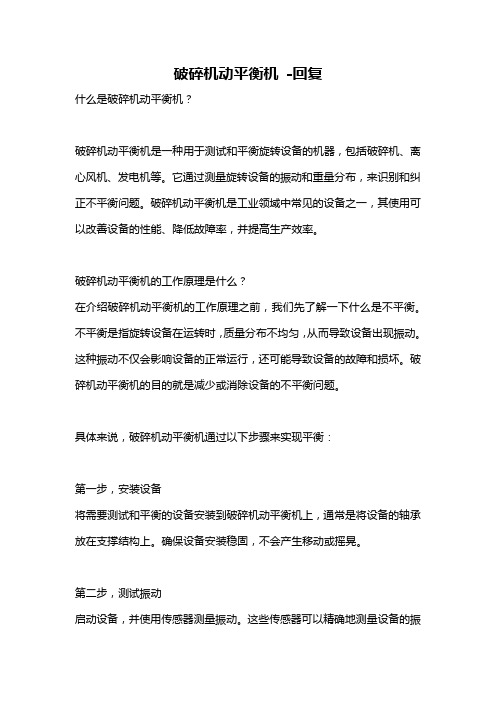
破碎机动平衡机-回复什么是破碎机动平衡机?破碎机动平衡机是一种用于测试和平衡旋转设备的机器,包括破碎机、离心风机、发电机等。
它通过测量旋转设备的振动和重量分布,来识别和纠正不平衡问题。
破碎机动平衡机是工业领域中常见的设备之一,其使用可以改善设备的性能、降低故障率,并提高生产效率。
破碎机动平衡机的工作原理是什么?在介绍破碎机动平衡机的工作原理之前,我们先了解一下什么是不平衡。
不平衡是指旋转设备在运转时,质量分布不均匀,从而导致设备出现振动。
这种振动不仅会影响设备的正常运行,还可能导致设备的故障和损坏。
破碎机动平衡机的目的就是减少或消除设备的不平衡问题。
具体来说,破碎机动平衡机通过以下步骤来实现平衡:第一步,安装设备将需要测试和平衡的设备安装到破碎机动平衡机上,通常是将设备的轴承放在支撑结构上。
确保设备安装稳固,不会产生移动或摇晃。
第二步,测试振动启动设备,并使用传感器测量振动。
这些传感器可以精确地测量设备的振动频率、幅值等参数,从而确定设备是否存在不平衡问题。
第三步,计算重量分布根据振动数据,破碎机动平衡机可以计算出设备的重量分布情况。
通过将设备分成若干部分,计算每个部分的质量,并标记其相对位置。
第四步,添加校正质量根据设备的重量分布情况,破碎机动平衡机会计算出需要添加的校正质量。
这些校正质量通常是一些特定的配重块,可以固定在设备上的某些位置。
第五步,安装配重块根据计算出的校正质量和位置,将配重块固定在设备上。
通常,破碎机动平衡机会提供相应的安装指导,以确保配重块的正确安装。
第六步,再次测试振动重新启动设备,并再次测量振动。
如果振动幅值得到显著降低,说明设备的不平衡问题得到了解决。
如果振动没有明显改善,可能需要进一步调整校正质量的位置和数量。
通过以上步骤,破碎机动平衡机可以帮助用户实现设备的动平衡,有效减少设备的振动,提高设备的性能和使用寿命。
破碎机动平衡机的应用范围有哪些?破碎机动平衡机广泛应用于各个工业领域,包括采矿、制造、能源等。
动平衡作业指导书

按设备保养相应规章制度进行保养;设 备需进行周期性检查;设备运行表及交 接班记录要做好
自检
防锈油、干净抹布等
设备保养不当,影 响设备性能及精度
检
安全事故
经多次重复验证,转子动平衡试验自检合格后报专
不及时送检、填写
检,J检,见证合格后,填写动平衡试验报告,并 动平衡试验报告内容要填写完整,数据 自检
报告不规范影响产
零件送检 交付检相关验员留存备查;卸下转子,转入指定区 真实可信,各相关人员签字清晰、齐 、专 润滑油、记号笔等 品(资料)成套,
确保转子水平。
工件的轴颈,并加上少量润滑油;
转子安装
根据转子外径选择合适皮带,松开安全架紧固螺 杆,掀起安全架,将转子轴承档放在支架滚轮上, 放置方式为转子上端在左侧,在滚轮外圆涂少量润 滑油,调整合上安全架,拧紧紧固螺杆,将皮带套 在转子外圆上,调整传动系统的手柄和手轮,使皮 带松紧适中。
转子应轻起、轻放,以防碰坏支架;移 动摇架时应同时将工件转动或两个支架 同时同速移动,以免轴颈和滚轮表面划 痕磨损,不允许在滚轮架上进行敲、撞 击;安全架滚轮与轴表面接触不能有间 隙;皮带松紧度以转动时皮带与转子不 发生相对滑动为准。
档,待运转后,即可转换到高速进行检测,等显示 正,有的转子虽然质量不大,但转子外 自检
2
工艺过程
动平衡检 测
数字平稳后,按停止键,停止电机,显示屏上显示 不平衡重量及位置角度(显示屏两侧的上下数为转
径较大,影响到拖动功率时,也只能先 用低速校正;当机器信噪比较差时,屏
、专
子相应的不平衡重量和位置角度,角度是以标记点 幕会不断闪烁“S”而没有不平衡量值 检
固定后,要确保旋转的平衡机部件不会 碰到光电头、连接电缆和支架;为了使 光点头正常工作,必须确保无外部光源
动平衡机工作原理
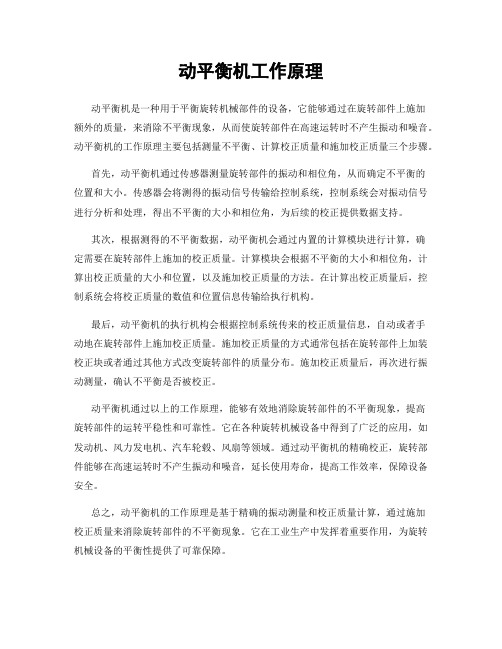
动平衡机工作原理动平衡机是一种用于平衡旋转机械部件的设备,它能够通过在旋转部件上施加额外的质量,来消除不平衡现象,从而使旋转部件在高速运转时不产生振动和噪音。
动平衡机的工作原理主要包括测量不平衡、计算校正质量和施加校正质量三个步骤。
首先,动平衡机通过传感器测量旋转部件的振动和相位角,从而确定不平衡的位置和大小。
传感器会将测得的振动信号传输给控制系统,控制系统会对振动信号进行分析和处理,得出不平衡的大小和相位角,为后续的校正提供数据支持。
其次,根据测得的不平衡数据,动平衡机会通过内置的计算模块进行计算,确定需要在旋转部件上施加的校正质量。
计算模块会根据不平衡的大小和相位角,计算出校正质量的大小和位置,以及施加校正质量的方法。
在计算出校正质量后,控制系统会将校正质量的数值和位置信息传输给执行机构。
最后,动平衡机的执行机构会根据控制系统传来的校正质量信息,自动或者手动地在旋转部件上施加校正质量。
施加校正质量的方式通常包括在旋转部件上加装校正块或者通过其他方式改变旋转部件的质量分布。
施加校正质量后,再次进行振动测量,确认不平衡是否被校正。
动平衡机通过以上的工作原理,能够有效地消除旋转部件的不平衡现象,提高旋转部件的运转平稳性和可靠性。
它在各种旋转机械设备中得到了广泛的应用,如发动机、风力发电机、汽车轮毂、风扇等领域。
通过动平衡机的精确校正,旋转部件能够在高速运转时不产生振动和噪音,延长使用寿命,提高工作效率,保障设备安全。
总之,动平衡机的工作原理是基于精确的振动测量和校正质量计算,通过施加校正质量来消除旋转部件的不平衡现象。
它在工业生产中发挥着重要作用,为旋转机械设备的平衡性提供了可靠保障。
转子平衡的选择与确定 转子动平衡技术的方法
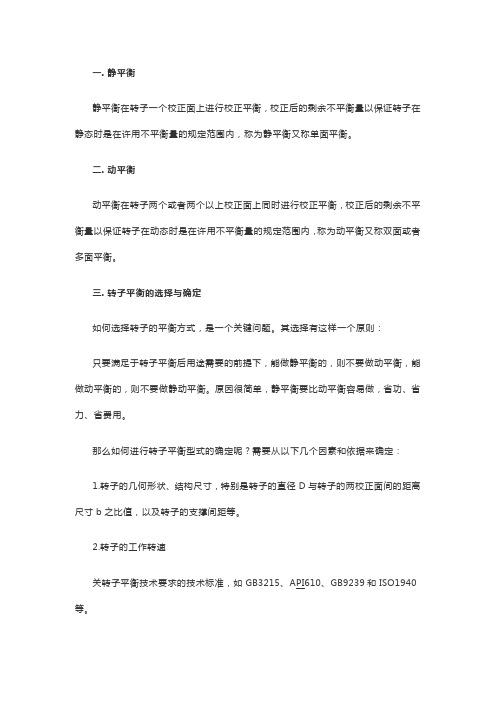
一. 静平衡静平衡在转子一个校正面上进行校正平衡,校正后的剩余不平衡量以保证转子在静态时是在许用不平衡量的规定范围内,称为静平衡又称单面平衡。
二. 动平衡动平衡在转子两个或者两个以上校正面上同时进行校正平衡,校正后的剩余不平衡量以保证转子在动态时是在许用不平衡量的规定范围内,称为动平衡又称双面或者多面平衡。
三. 转子平衡的选择与确定如何选择转子的平衡方式,是一个关键问题。
其选择有这样一个原则:只要满足于转子平衡后用途需要的前提下,能做静平衡的,则不要做动平衡,能做动平衡的,则不要做静动平衡。
原因很简单,静平衡要比动平衡容易做,省功、省力、省费用。
那么如何进行转子平衡型式的确定呢?需要从以下几个因素和依据来确定:1.转子的几何形状、结构尺寸,特别是转子的直径D与转子的两校正面间的距离尺寸b之比值,以及转子的支撑间距等。
2.转子的工作转速关转子平衡技术要求的技术标准,如GB3215、API610、GB9239和ISO1940等。
3.转子做静平衡的条件在GB9239平衡标准中,对刚性转子做静平衡的条件定义为:如果盘状转子的支撑间距足够大并且旋转时盘状部位的轴向跳动很小,从而可忽略偶不平衡(动平衡),这时可用一个校正面校正不平衡即单面(静)平衡,对具体转子必须验证这些条件是否满足。
在对大量的某种类型的转子在一个平面上平衡后,就可求得最大的剩余偶不平衡量,并除以支撑距离。
如果在最不利的情况下这个值不大于许用剩余不平衡量的一半,则采用单面(静)平衡就足够了。
从这个定义中不难看出转子只做单面(静)平衡的条件主要有三个方面:(1)一个是转子几何形状为盘状;(2)一个是转子在平衡机上做平衡时的支撑间距要大;(3)再一个是转子旋转时其校正面的端面跳动要很小。
对以上三个条件作如下说明:(1)何谓盘状转子主要用转子的直径D与转子的两校正面间的距离尺寸b之比值来确定。
在API610标准中规定D/b<6时,转子只做单面平衡就可以了;D/b≥6时可以作为转子是否为盘状转子的条件规定,但不能绝对化,因为转子做何种平衡还要考虑转子的工作转速。
- 1、下载文档前请自行甄别文档内容的完整性,平台不提供额外的编辑、内容补充、找答案等附加服务。
- 2、"仅部分预览"的文档,不可在线预览部分如存在完整性等问题,可反馈申请退款(可完整预览的文档不适用该条件!)。
- 3、如文档侵犯您的权益,请联系客服反馈,我们会尽快为您处理(人工客服工作时间:9:00-18:30)。
山东XXXXX 有限公司 32吨动平衡机招标书一、总则 1.1概述本次采购的设备将适合对PM3和PM5号机的辘子进行动平衡检测。
32吨硬支撑动平衡整机1台(4)2800X13000X32吨),本动平 衡机整机包括床身、支撑摆架、万向节驱动部分、皮带驱动部分、测 量系统、电气设备、配套附件、安装附件、及全套的技术资料等。
其他辐子13机床技术要求总述1.3.1设备床身为连接处经龙门铳床铳削齐头,材质为HT250铸铁结构,床身上有两条用于床头箱移动和固定摆架的T 型槽;1.2纸机基本数据 1.2.1车速传动车速: 动平衡车速: 卷纸辘动平衡: 工作车速: 传动方式:1.2.2动平衡等级烘缸、VAC 缸、真空辘1500m/mi n 1600m/min 2500m/min 1400m/min交流变频,分部传动G1.6 G1.0*1.3.2在床身上安装一套支承摆架:标准支承摆架1组,所有摆架均釆用锻钢线切割工艺,采用模块式结构;滚轮支承,带可锁定和可调节装置的压板安全架,刚度架上装有高精度磁力线圈测力传感器(采用进口件,不带机械放大器),用于检测摆架的振动;摆架的移动齿轮齿条的结构,并装有减速电机,电力驱动。
*1.3.3万向节驱动部分床头箱底座1件;六档机械齿轮变速箱1台; DC90KW电机1台;带刻度盘的万向联轴节1套。
(可轴向移动50mm 用于安装工件时的微调);2250Nm和50000Nm的专用万向节2套, 带万向节保护罩;基准信号传感器1套(进口)。
皮带驱动采用气动张紧装置,确保每次工件受力均匀一致;基准信号传感器1套(进口);DC75KW电机1台。
134所有平衡机设备配套的电器设备、继电器、接触器、空气开关等电器元件须均采用际知名品牌。
*1.3.5测量系统包括:德国进口产品,触摸屏设计,强大的向导提示,操作非常容易模块化设计,友好的服务系统,并可远程诊断嵌入式工业计算机,鼠标及外置键盘,强大的扩展功能,实现各种复杂的平衡任务,用Windows标准程序操作,USB接口,网络接口;双开门高档电控柜。
*1.3.6传动处轴承SKP品牌。
*1.3.7电机采用:Z4系列直流电机;*1.3.8圈带传动所使用皮带使用进口品牌;*1.3.9在东北地区有售前售后服务机构,同类型的产品在造纸行业的业绩近5年在国内不少于10家;二、技术参数和供货范围2.1技术要求2・2供货范围2.2.1主机包括:15000mm的机器床身,完整的摆架,包括传感器,主轴驱动装置,带有齿轮箱,基准信号传感器。
2.2.2驱动方式:万向节驱动,DC 90 kw直流调速控制电机配动平衡机专用6档变速齿轮箱,可输出平衡转速约为:16-160/28-280/46-460/68-680/100-1000/150-1500/18-180(R) rpm o 两套万向节,最人扭矩5000/2250 Nm0人的万向节用于重型转子的低速平衡,小的万向节用于小型转子的相对高速平衡。
变速齿轮箱在沿床身方向还有约50 mm的微调,方便重型转子的安放和调整。
223附加皮带驱动装置BU6/7 (7/70) 1套1套下悬式皮带驱动方式,作为主轴驱动的附加驱动装置。
包括:1带有电机用安装法兰的皮带驱动支架,1皮带涨紧和引导装置,1套皮带轮,2条平驱动带(1备用),1附加皮带驱动电机DC75kW1皮带驱动沿床身方向的移动装置,1套轴向限位支架,1光电信号发生器,1主轴驱动和皮带驱动的切换开关。
相应皮带驱动的参数为:2.2.4电气控制:一个直流调速控制电机,主开关,四象限直流调速装置,重要操作情况控制,超级快速熔断器,励磁单元,交流接触器,操作装置,电流表, 转矩调节电位器30%-100%,速度调节电位器10%-100%o2.2.5支承方式:针对可能出现的各种类型的辘子形式支承方式4滚轮支撑方式用于带有轴头的转子1套标准滚轮架:60-2501套扩展滚轮架:250-500支承方式2: V型板支撑用于带有轴承的转子,支撑轴承外圈。
用户根据转了实际尺寸自行定制支承方式3:1套T型连接平台用于带轴承座的转子,通过平台上的T型连接槽直接安放在平衡机摆架上进行平衡。
最大承重50 000 kgo2.2.6摆架电动移动机构7/70 1套两个摆架的电动移动和控制,适合于大型的平衡机,替代手工棘轮扳手操作,移动速度约2米每分钟。
*2.2.7测量系统要求测量系统要求为德国原装进口,具有屮间挠度测量功能,并按照三点校正法进行平衡解算,准确给出不平衡量的角度和量值。
1套测量系统(100-5000RPM)徳国原装进口高精度的先进测量系统,触摸屏设计,强大的向导提示,操作非常容易模块化设计,友好的服务系统,并可远程诊断嵌入式工业计算机,鼠标及外置键盘,强人的扩展功能,实现各种复杂的平衡任务,用Windows标准程序操作,USB接口,网络接口,1套打印系统HP UP1106包括一个激光打印机,用于建立专业的平衡报告,包括硬件和软件驱动,安装在控制柜中,适合车间使用环境。
2套电子角度定位EAI在测量装置和驱动Z间建立连接,快速而准确地发现转了上不平衡量的位置,手动操作。
(分别用于圈带和万向节驱动)1套转子特性定标RPC改善在分离面困难的情况下的平衡,或用于在工作转速平衡弹性转了。
1套高速挠性转子测量BFR针对挠性转了的特殊软件,包括: 显示加速过程中的测量,振动速度和振动位移的测量,振动速度的双倍频(2f)测量。
储存加速过程中的测量值,并可以在波特图和尼奎斯特图屮显示,对转子的高速特性进行分析。
1套3和4通道测量3,4MC附加测量通道,测量附加支撑的传感器信号,也可以测量振动速度或跳动。
1套激光径向跳动测量装置LWA 14/20需要打开测量系统3和4通道测量(2.18),用来不接触测量的转了表面的同心度,包括传感器支架(需要提供用户转子直径数据)。
主要参数:测量范圉:+10 mm灵敏度:0.5 Vpp/mm基准距离: 4 0mm分辨率:10 ii m测量冃标最小直径:200 mm2.2.8其它未列出的所有配套项目(包括技术参数,供货明细和作用等)。
三.质量要求乙方提供的设备必须是成熟可靠的产品,设备在质量保证期内,因设备设计或制作不良及其他供货方的责任造成的质量问题事项故障,厂家马上进行无偿修理或更换并调试好;即使超过质量保证期(在设备使用寿命内),如果是设备本质上的质量问题也要求无偿修理或更换并调试好。
.工作环境及要求1.供电:三相电源:AC 10000V , AC380V±10% 50Hz±2%。
2.气源:气压0.4〜0.6 MPa。
3.温度:・5〜45 °C o4.相对湿度:通常55%〜80%,最大不超过95% o五、设备技术资料1.乙方提供三套中、英文的电气、机械、液压、冷却系统、详细技术说明书、设备使用维修说明书、相应控制系统技术资料和机床操作、编程手册。
另外,上述所有资料提供电子版一份(含中、英文)。
2.乙方提供机床备件清单:备件清单明细由:制造商、产地、规格及订货号项目标签构成。
3.乙方须在合同生效15天内提供设备基础图以及对场地和坏境的要求(如地面承重,室内建筑预设要求,机位基础要求,适应温度、湿度、电源标准等),甲方负责设备基础施工和二次灌浆并将设备电源引进到主令开关位置。
4.乙方提供出厂检验报告、原产地证明和甲方验收常规标准。
六、设备安装、调试、验收及技术培训1.设备制造完成后,乙方及时通知甲方派员到乙方工厂进行预验收, 并做好各项目验收记录。
验收标准包括上述国标和部标及双方签订的技术协议。
在预验收合格,双方在预验收报告上签字认可•手续齐全后,方可办理发货。
2•货物运抵甲方安装现场后,双方共同对货物进行开箱,清点验收。
3.设备安装调试所需的专用工具、仪器等均由乙方自行解决,甲方提供通用工具和设备吊装并提供必要的配合,机床调试用的液压油、润滑油由甲方解决。
4.机床在甲方工厂安装调试后进行最终验收,乙方按设备技术资料和图纸要求进行设备安装、调试,整机试车、试生产,连续运转72 小时无故障,并达到精度和效率等要求,由双方签字确认,调试验收合格。
5.设备在甲方工厂安装调试完毕后,对甲方操作人员、维修人员进行现场培训。
经培训合格后,操作者能熟练独立操作,如达不到甲方上岗要求,乙方重新培训,费用由乙方承担,直到达到上岗要求。
5.1数控系统方面的维修操作培训,包括:各种界面的进入方法及密码;数据恢复备份方法;PLC诊断操作;厂家自定义的维修个性化界面的操作。
5.2机械机构调整和拆卸方法,包括:机械整体结构及各部分元件位置;数控刀盘精度调整;各传动坏节中皮带调整和更换方法;主轴的拆卸和装配方法;设备各部分精度调整和补偿方法。
5.3设备维护保养方面培训,包括:重要数据保持电池位置、电池型号及更换时间;机床易损件更换操作;设备需定期维护保养部位的维护保养操作。
5.4设备油漆外观按照泉林统一要求制作。
5.5设备易损件、备件清单由乙方提供并负责供应,按出厂价80% 供给。
七、售后服务1.质保期:自甲方最终验收合格之日算起,保修期主机2年数控系统3年。
在质保期内正常操作情况下,乙方负责对设备免费维修,更换损坏零部件。
机床在质保期满一个月前,必须对机床静态精度和动态精度免费进行检测和调整,并达到出厂时合格证要求。
即使超过质量保证期,如果是设备本质上的质量问题也要求无偿修理或更换并试好。
免费保修期内出现设备故障(非不正当操作造成),一年免费质保期按故障处理完毕,签字验收当日起重新计算时间。
2.乙方在中国人陆境内必须设有具备较强能力的固定维修服务站及备品、配件库。
投标时必须出示相应的资信证明文件。
3.在设备使用寿命期内,乙方应保证对甲方所购设备终身维修,并保证设备零配件、易损件的供应。
4.乙方应保证甲方在设备的寿命期内,15天内买到所必需的备件。
5.设备维修反应时间在24小时Z内,48小时内到达现场,修理工期不超过5天。
八、投标要求1・应列岀机床的标准配置项,机床附件清单,并计入投标总价。
2•应列出机床的选项、备件、并计入投标总价。
3•应列出设备安装、调试费用,并计入投标总价。
4 •各分项均应单独列出价格。
九、本技术要求仅提供有限的技术要求,并未对一切技术细节做出规定,也未充分引述有关标准的详细条文,乙方产品应保证符合有关国家、行业技术规范和标准的要求,同时甲乙双方的招投标文件和投标澄清文件作为技术协议的一部分仍然有效。
十、交货期2个月。