迈向Just-In-Time管理的道路1
管理 专用名词

管理专用名词来源:鐘鳴的日志MBOS——就是用Olympic的系统作管理手段,通过持续的活动使企业的体制越来越好,最终实现工厂的营运绩效达到理想的境界。
目的是要提升工作效率,降低各项成本,提高公司效益,更多内容可见内控部“MBOS”专栏。
2.SDA——Skill Development Activities的缩写,即跨部门技能开发活动,一般有高阶主管的直接参与,目的是要在短期内提升绩效的同时,希望同仁们能培养出持续追求进步的组织文化,以具备不断提升营运绩效的精神与能力,详细解释可见内控部“MBOS”专栏。
3.SGA——Small Group Activities的缩写,即小组活动,一般不跨部门,目的是改善日常工作,提高小组成员运用工具解决问题的能力,提升工作绩效。
4.JDI——Just Do It的缩写,即已有较为明确的改善方法,可以立即去做的活动,目的是要立即解决工作中遇到的问题,提升工作绩效。
5.6sigma——6Sigma是一种以数据为基础,追求近乎完美的质量管理方法,即被广泛接受的DMAIC,目的是达到更高的绩效和顾客满意度,详细解释可见内控部“SIX SIGMA”专栏。
6.学习型组织——所谓学习型组织,是指通过培养弥漫于整个组织的学习气氛、充分发挥员工的创造性思维能力而建立起来的一种有机的、高度柔性的、扁平的,符合人性的、能持续发展的组织。
创建学习型组织的目的是通过迈向学习型组织的种种努力,引导出一种不断创新、不断进步的新观念,从而使组织日新月异,不断创造未来。
更多内容可见内控部“学习型组织”专栏。
7.CTR——Cycle Time Reduction的缩写,即循环时间缩短。
它是一种针对作业流程的改善方法,通过脑力激荡画出现有流程和应有流程,寻找其间的差距,发现存在的问题点,然后成立小组进行改善的作业方法。
更多内容可见内控部“CTR”专栏。
8.6S——6S是企业管理的基础,是提升现场管理水平的重要手段,就是由日文字母6个S组成,具体为整理SEIRI、整顿SEITON、清洁SEIKETSU、清扫SEISO、素养SHITSUKE、安全SAFELY。
适时生产系统与全面质量管理 Just-in-time System
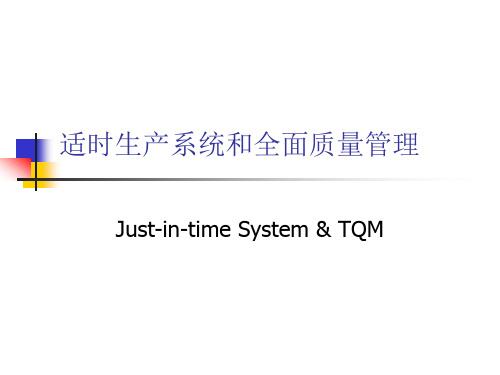
三、JIT为企业带来的好处
1、通过提高效率来降低成本并减少或消 除非增值作业。 2、不断提升产品质量。 3、对生产工人具有更大的挑战、变化和 责任。 4、降低部分产品不能被销售的风险。
案例
戴尔(Dell)电脑公司,每天通过因特网实现 100美元的电脑销售,长期以来一直是适时制 造制度的一个典范。戴尔公司通常是在收到订 单后,才开始调配元部件并装配电脑。戴尔公 司的大多数供应商储存元部件离戴尔公司的工 厂仅有几分钟的时间。但值得一提的是,JIT所 蕴含的哲学思想同样也适用于供应商、装配商 和分销商。例如,一份星期一早上9点发出的 客户订单,在星期二晚上9点就能够将货品装 上送货卡车。然而JIT原则不仅仅是运用在生产
适时生产系统的产品生产周期=增值时间+非 增值时间 增值时间为生产过程中对产品直接加工的必 要操作时间,非增值时间为储存、等待、运送 和检验时间。 消除非增值时间,使产品的生产周期等于生产 过程对产品实际加工的增值时间,从而使整个 生产过程得以不间断地进行。 这是适时生产系统的主要目的。
二、适时生产系统的特点
2、成本计算控制于材料购入和产品销售之时 1)购入材料或零部件,在材料或零部件到达 投入使用时,计入“在产品存货”帐户,生产 过程中发生的人工成本和其它制造成本计入 “制造费用”帐户 2)产品完工不计算成本,待产品销售时,直 接由“在产品存货”帐户和“制造费用分配” 帐户 转入“产品销售成本”帐户
在适时制下,产品成本毋需进行多环节的计算, 间接费用可直接追踪至产品。 1、成本计算控制于材料采购和产品完工之时 1)购买材料或零部件在到达投入使用时,借 记“原材料和在制品”,生产过程中发生的人 工成本和其他制造成本计入“制造费用”帐户 2)产品完工时,结转完工产品成本,贷记 “原材料和在制品”和“制造费用分配”帐户, 借记“产成品”帐户。
jit准时化管理思想与精益生产体系
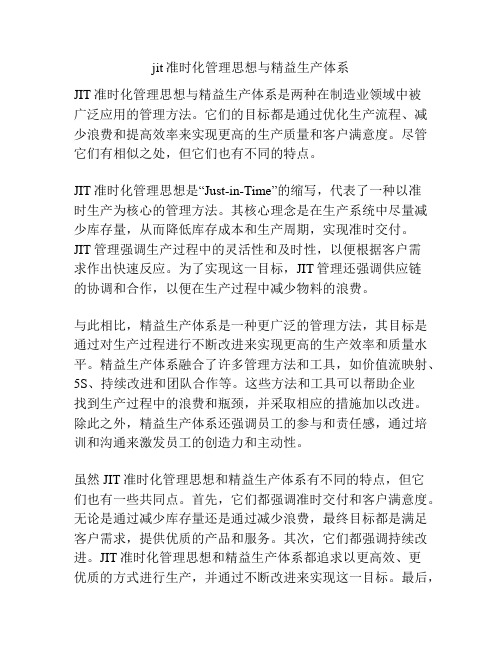
jit准时化管理思想与精益生产体系JIT准时化管理思想与精益生产体系是两种在制造业领域中被广泛应用的管理方法。
它们的目标都是通过优化生产流程、减少浪费和提高效率来实现更高的生产质量和客户满意度。
尽管它们有相似之处,但它们也有不同的特点。
JIT准时化管理思想是“Just-in-Time”的缩写,代表了一种以准时生产为核心的管理方法。
其核心理念是在生产系统中尽量减少库存量,从而降低库存成本和生产周期,实现准时交付。
JIT管理强调生产过程中的灵活性和及时性,以便根据客户需求作出快速反应。
为了实现这一目标,JIT管理还强调供应链的协调和合作,以便在生产过程中减少物料的浪费。
与此相比,精益生产体系是一种更广泛的管理方法,其目标是通过对生产过程进行不断改进来实现更高的生产效率和质量水平。
精益生产体系融合了许多管理方法和工具,如价值流映射、5S、持续改进和团队合作等。
这些方法和工具可以帮助企业找到生产过程中的浪费和瓶颈,并采取相应的措施加以改进。
除此之外,精益生产体系还强调员工的参与和责任感,通过培训和沟通来激发员工的创造力和主动性。
虽然JIT准时化管理思想和精益生产体系有不同的特点,但它们也有一些共同点。
首先,它们都强调准时交付和客户满意度。
无论是通过减少库存量还是通过减少浪费,最终目标都是满足客户需求,提供优质的产品和服务。
其次,它们都强调持续改进。
JIT准时化管理思想和精益生产体系都追求以更高效、更优质的方式进行生产,并通过不断改进来实现这一目标。
最后,它们都需要全员参与。
无论是JIT管理还是精益生产体系,都需要员工的积极参与和团队合作,以便实现管理目标。
综上所述,JIT准时化管理思想和精益生产体系在制造业领域中都有广泛的应用。
尽管它们有不同的特点,但它们都以准时交付和持续改进为核心,通过优化生产流程和减少浪费来实现更高的生产效率和质量水平。
无论是选择采用JIT管理还是精益生产体系,企业都可以从中获得显著的竞争优势。
jit理念 -回复

jit理念-回复jit理念,即精益生产理念(Just-in-Time),是一种供应链管理和生产管理的方法。
它旨在通过减少浪费和提高效率,实现生产和供应的精确协调。
本文将分步介绍jit理念的起源、目标、原则和实施过程,以及它对企业产生的积极影响。
第一步:jit理念的起源jit理念最早起源于日本的汽车制造行业。
20世纪70年代,日本汽车制造商开始采用这一管理方法,以应对当时竞争激烈的市场。
日本汽车制造商通过jit理念的应用,成功地提高了生产效率和质量,降低了库存和生产成本,从而成为全球汽车行业的领导者。
第二步:jit理念的目标jit理念的目标是实现“所需即提供”,即在无浪费的前提下,实现零库存和零延迟的生产和供应。
通过实时调整生产和供应的速度,以最小化各种类型的浪费以及不必要的库存和延迟,jit理念可以提高生产和供应链的效率和质量。
第三步:jit理念的原则jit理念的实现依赖于一系列原则,包括:1. 一次正确:追求零缺陷和零错误。
通过提高生产线的质量和准确性,可以减少重工和返工的需要,从而提高生产效率。
2. 批量缩减:减少批量生产的大小。
通过降低批量生产的规模,可以降低库存水平和产生的过剩产品。
3. 小循环时间:减少生产和供应的周期时间。
通过提高生产和供应链的效率,可以减少产品的等待时间,从而提高客户满意度。
4. 快速产品交付:及时交付客户需求的产品。
通过减少延迟和响应时间,可以提高产品的交付速度和灵活性。
5. 稳定生产:确保生产过程的稳定性和可重复性。
通过减少生产中的波动和变异,可以提高生产线的稳定性和可靠性。
第四步:jit理念的实施过程jit理念的实施过程包括以下几个步骤:1. 价值流图:绘制产品的价值流图,以分析整个供应链的价值流程,并找出其中的浪费和瓶颈。
2. 浪费识别:识别并消除生产过程中的浪费,如超产、等待、运输、库存、动作、修理和过加工等。
3. 单一物流:优化物流流程,减少库存和运输时间。
现代管理理论的发展历程及发展趋势

现代管理理论的发展历程及发展趋势一、前言现代管理理论是在工业革命和科学技术进步的推动下逐步形成和发展起来的。
本文将从管理理论的发展历程和发展趋势两个方面进行探讨,以便更好地了解现代管理理论的演变和未来发展方向。
二、管理理论的发展历程1. 科学管理理论(1900年-1920年)科学管理理论的代表人物为弗雷德里克·泰勒。
他提出了科学管理的基本原则,包括工作分析、工作标准化、工作效率和工资激励等。
这一时期的管理理论主要关注工作过程的科学化和效率提升。
2. 行为管理理论(1920年-1950年)行为管理理论的代表人物为埃尔顿·梅奥。
他关注组织内部的人际关系和心理因素对工作绩效的影响,提出了人际关系理论和激励理论。
这一时期的管理理论主要关注员工的行为和动机,强调人性化管理。
3. 管理科学理论(1950年-1970年)管理科学理论的代表人物为赫伯特·西蒙和彼得·德鲁克。
他们运用数学和统计学方法研究管理问题,提出了决策理论和系统理论。
这一时期的管理理论主要关注决策和系统化思维。
4. 组织行为学理论(1970年-1990年)组织行为学理论的代表人物为道格拉斯·麦格雷戈尔。
他提出了X理论和Y理论,强调管理者对员工的不同假设会对员工产生不同的影响。
这一时期的管理理论主要关注组织文化和领导风格。
5. 现代管理理论(1990年至今)现代管理理论主要关注创新和变革。
代表人物包括彼得·圣吉和杰克·韦尔奇。
他们提出了敏捷管理和变革管理的理念,强调组织的灵便性和快速响应能力。
现代管理理论还关注可持续发展和社会责任等问题。
三、管理理论的发展趋势1. 灵便性和适应性现代管理理论越来越关注组织的灵便性和适应性。
随着市场环境的快速变化和技术的迅猛发展,组织需要具备快速调整和适应变化的能力,以保持竞争优势。
2. 创新和创业精神创新和创业精神在现代管理理论中占领重要地位。
准时制(Just-in-time)生产系统

2
基本目的
准时制生产(Just-in-time production)
准时制意味着要在所需要的时间、按所需要的量、生产 所需要的产品。
5
准时制生产
基本目的
每一道工序的人员在需要的时间按所需要的量到上一道 工序领取所需要的物料(零部件)。
这样上一道工序所要做的就是生产相等数量的零部件, 来补充所减少的物料数量。
通过降低成本来获得利润! • 减少各种浪费,比如:多余的库存、多余的劳动力等。 • 这里所涉及的成本概念是非常广泛的。
3
基本目的
消除过剩的生产
在生产过程中存在着四种浪费: • 过剩的生产资源(excessive production resources) • 过量的生产(overproduction) • 冗余的库存量(excessive inventory) • 不必要的投资(unnecessary capital investment)
• 为了使各个生产环节掌握生产时间和所需要的零件数 量,丰田公司使用了看板。
15
看板系统和准时制生产
什么是看板?
看板通常是一张放在矩形塑料封套中的卡片。 主要使用两种类型的看板:取货看板和生产指示看板
16
8
看板系统和准时制生产
什么是看板?
取货看板上的内容指明零部件的种类和数量,这是下一 道工序向前一道工序所要求获得的。
合格的。同时这种流动必须不被打断。 • 因此,其中的质量控制非常重要,它配合准时制运作通
过看板系统共同实现。
11
基本目的
人旁自动化:
• 人旁自动化意味着要建立一个机制,来防止机器或者生 产线上产生不合格的产品。
• 名词“ Autonomation” (日文是, “Ninben-no-aru Jidoka,” 其 缩写是 “Jidoka”) 并不是指自动化, 而是对工艺过程中的 异常情况进行自主检查。
汽车配件仓库库存计划管理ppt课件
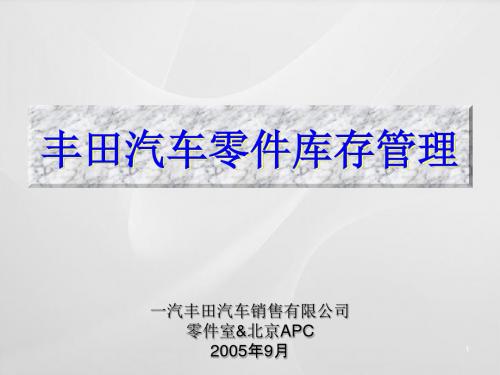
35
第五章 仓库保管七原则 2.1.按周转速度存放
* 常流动件远离作业区,效率低下。
* 常流动件存放于作业区附近,作业方便。
作业区
作业区
为常流动件; 为慢流动件; 为出入库行走路线。
现有库存量 在途库存量 追加订货量 客观的反映了库存的不足
23
当MAD增加时:
SSQ = MAD × ( O/C + L/T + S/S ) SOQ = SSQ - O/H - O/O + B/O
当MAD减小时:
SSQ = MAD × ( O/C + L/T + S/S ) SOQ = SSQ - O/H - O/O + B=</O0
① 重零件有落下伤人及损坏的危险; ② 上架、提取不便。
危险!
不便!
38
第五章 仓库保管七原则 2.3.竖置存放
有些象车门、排气管、挡风玻璃等扁平或细长形状的零件如平放会产生如下问题: ① 上面零件的重量会损坏下面的零件; ② 此类零件平放会浪费很大空间; ③ 由于排气管一类的零件过长,如平放会从货架伸出至通道,从而影响通行且不安全; ④ 难以提取。
增长期
月均需求 少
较多
较多
需求频度 低
低
较高
库存状态 不库存 不一定 建立库存
平稳期
衰退期
多
少(短期)
少(长期)
高
低(短期)
低(长期)
库存管理 “停止库存试验” 报废
11
第三章 Just In Time的库存管理方式
JIT——Just In Time准时生产方式,是由日本丰田汽车公司 …
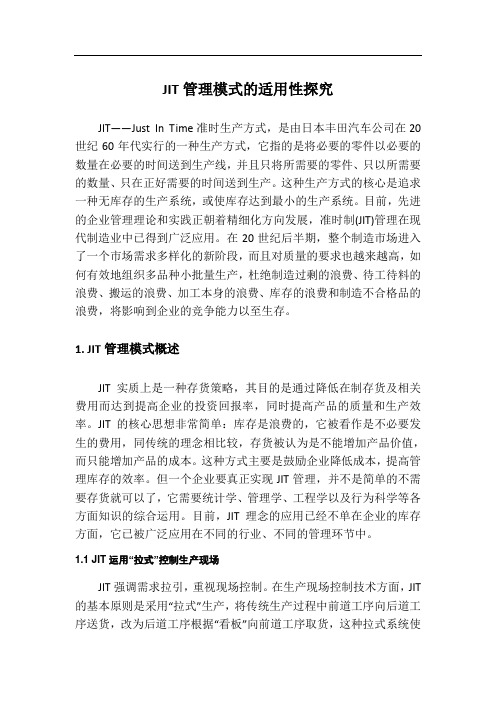
JIT管理模式的适用性探究JIT——Just In Time准时生产方式,是由日本丰田汽车公司在20世纪60年代实行的一种生产方式,它指的是将必要的零件以必要的数量在必要的时间送到生产线,并且只将所需要的零件、只以所需要的数量、只在正好需要的时间送到生产。
这种生产方式的核心是追求一种无库存的生产系统,或使库存达到最小的生产系统。
目前,先进的企业管理理论和实践正朝着精细化方向发展,准时制(JIT)管理在现代制造业中已得到广泛应用。
在20世纪后半期,整个制造市场进入了一个市场需求多样化的新阶段,而且对质量的要求也越来越高,如何有效地组织多品种小批量生产,杜绝制造过剩的浪费、待工待料的浪费、搬运的浪费、加工本身的浪费、库存的浪费和制造不合格品的浪费,将影响到企业的竞争能力以至生存。
1. JIT管理模式概述JIT实质上是一种存货策略,其目的是通过降低在制存货及相关费用而达到提高企业的投资回报率,同时提高产品的质量和生产效率。
JIT的核心思想非常简单:库存是浪费的,它被看作是不必要发生的费用,同传统的理念相比较,存货被认为是不能增加产品价值,而只能增加产品的成本。
这种方式主要是鼓励企业降低成本,提高管理库存的效率。
但一个企业要真正实现JIT管理,并不是简单的不需要存货就可以了,它需要统计学、管理学、工程学以及行为科学等各方面知识的综合运用。
目前,JIT理念的应用已经不单在企业的库存方面,它已被广泛应用在不同的行业、不同的管理环节中。
1.1 JIT运用“拉式”控制生产现场JIT强调需求拉引,重视现场控制。
在生产现场控制技术方面,JIT 的基本原则是采用“拉式”生产,将传统生产过程中前道工序向后道工序送货,改为后道工序根据“看板”向前道工序取货,这种拉式系统使得库存降低到最小限度,进而降低制造成本。
1.2 实现JIT的前提——物流设计合理化物流设计合理化是实现降低成本目标的最终途径,具体指在生产线内外,所有的设备、人员和零部件都得到最合理的调配和分派,在最需要的时候以最及时的方式到位。
justintime补库策略
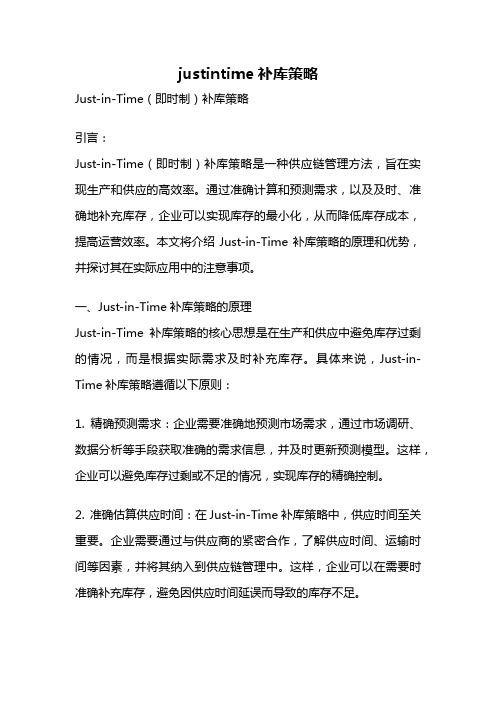
justintime补库策略Just-in-Time(即时制)补库策略引言:Just-in-Time(即时制)补库策略是一种供应链管理方法,旨在实现生产和供应的高效率。
通过准确计算和预测需求,以及及时、准确地补充库存,企业可以实现库存的最小化,从而降低库存成本,提高运营效率。
本文将介绍Just-in-Time补库策略的原理和优势,并探讨其在实际应用中的注意事项。
一、Just-in-Time补库策略的原理Just-in-Time补库策略的核心思想是在生产和供应中避免库存过剩的情况,而是根据实际需求及时补充库存。
具体来说,Just-in-Time补库策略遵循以下原则:1. 精确预测需求:企业需要准确地预测市场需求,通过市场调研、数据分析等手段获取准确的需求信息,并及时更新预测模型。
这样,企业可以避免库存过剩或不足的情况,实现库存的精确控制。
2. 准确估算供应时间:在Just-in-Time补库策略中,供应时间至关重要。
企业需要通过与供应商的紧密合作,了解供应时间、运输时间等因素,并将其纳入到供应链管理中。
这样,企业可以在需要时准确补充库存,避免因供应时间延误而导致的库存不足。
3. 协调供应链各环节:Just-in-Time补库策略需要企业与供应链各环节进行紧密协调。
这包括与供应商的信息共享、订单的及时传递和生产计划的协调等。
只有通过有效的沟通和协作,才能确保库存的及时补充,从而实现Just-in-Time的供应链管理。
二、Just-in-Time补库策略的优势Just-in-Time补库策略在实践中具有以下几个优势:1. 降低库存成本:Just-in-Time补库策略避免了库存过剩的情况,减少了企业的库存成本。
由于减少了仓储和管理费用,企业可以更加高效地运营。
2. 提高运营效率:Just-in-Time补库策略使得企业能够更加精确地预测需求,并及时补充库存。
这样,企业可以更好地满足客户需求,提高运营效率。
彼得德鲁克的管理理念

彼得德鲁克的管理理念
彼得德鲁克是管理学的先驱,被誉为现代管理学之父,他提出了许多重要的管理
理念,彼得德鲁克的管理理念强调目标导向、市场导向、知识管理和学习,他的
理念对于现代管理者和组织仍然具有重要的指导意义。
其中包括以下几点:
1. 管理目标理论(Management by Objectives,MBO):彼得德鲁克强调制定明确、可衡量的目标,通过目标的设定和达成来推动组织的发展,并鼓励员工参与目标
的制定和衡量过程。
2. 市场导向(Market-Oriented):彼得德鲁克认为,组织的成功取决于对市场的
了解和迎合,组织应该把顾客需求放在首位,紧密关注市场动态,及时调整产品
和服务以适应市场的变化。
3. 知识工作者(Knowledge Workers):彼得德鲁克强调知识工作者对于组织的重要性,他认为知识经济时代,知识工作者是组织的核心竞争力,组织应该重视他
们的创造力和发展,并提供必要的支持和激励。
4. 经验学习(Experiential Learning):彼得德鲁克认为,管理不仅仅是一种学问,更是一种实践,通过不断地实践和经验的积累,管理者可以逐渐提高自己的管理
水平,发展自己的管理技能。
5. 时间管理(Time Management):彼得德鲁克提出了重要而实用的时间管理理念,包括“时间日志”和“战略思维”的应用,帮助管理者有效地利用时间,提高工
作效率和生产力。
jit哲学生产与运营管理
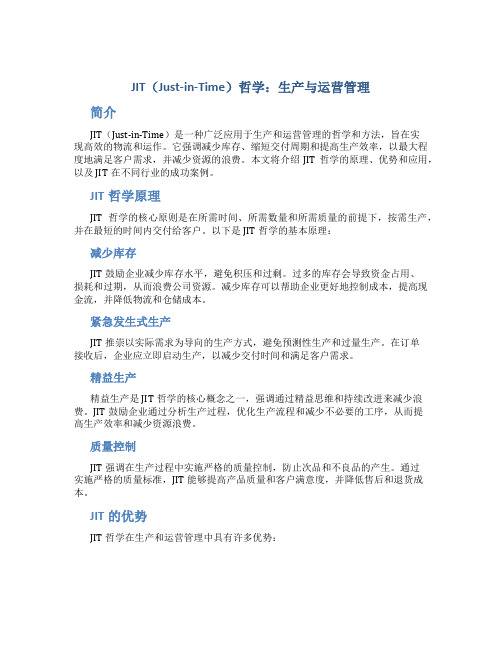
JIT(Just-in-Time)哲学:生产与运营管理简介JIT(Just-in-Time)是一种广泛应用于生产和运营管理的哲学和方法,旨在实现高效的物流和运作。
它强调减少库存、缩短交付周期和提高生产效率,以最大程度地满足客户需求,并减少资源的浪费。
本文将介绍JIT哲学的原理、优势和应用,以及JIT在不同行业的成功案例。
JIT哲学原理JIT哲学的核心原则是在所需时间、所需数量和所需质量的前提下,按需生产,并在最短的时间内交付给客户。
以下是JIT哲学的基本原理:减少库存JIT鼓励企业减少库存水平,避免积压和过剩。
过多的库存会导致资金占用、损耗和过期,从而浪费公司资源。
减少库存可以帮助企业更好地控制成本,提高现金流,并降低物流和仓储成本。
紧急发生式生产JIT推崇以实际需求为导向的生产方式,避免预测性生产和过量生产。
在订单接收后,企业应立即启动生产,以减少交付时间和满足客户需求。
精益生产精益生产是JIT哲学的核心概念之一,强调通过精益思维和持续改进来减少浪费。
JIT鼓励企业通过分析生产过程,优化生产流程和减少不必要的工序,从而提高生产效率和减少资源浪费。
质量控制JIT强调在生产过程中实施严格的质量控制,防止次品和不良品的产生。
通过实施严格的质量标准,JIT能够提高产品质量和客户满意度,并降低售后和退货成本。
JIT的优势JIT哲学在生产和运营管理中具有许多优势:资金节约通过减少库存水平和缩短生产周期,JIT能够减少企业的资金占用和运营成本。
企业可以将资金用于其他重要的投资和项目,提高资金利用效率。
提高生产效率JIT强调通过优化生产流程、减少不必要的工序和浪费,提高生产效率。
这可以帮助企业更好地利用资源,提高生产效率,并降低生产成本。
降低交付周期JIT推崇按需生产和紧急发生式生产的原则,能够缩短交付周期。
这样可以更快地响应客户需求,提高客户满意度,并在竞争激烈的市场中保持竞争优势。
质量控制JIT强调质量控制的重要性,通过严格的质量标准来防止次品和不良品的产生。
现代管理理论的发展历程及发展趋势

现代管理理论的发展历程及发展趋势一、发展历程1. 科学管理理论的兴起(19世纪末-20世纪初)科学管理理论的兴起可以追溯到19世纪末和20世纪初的美国。
弗雷德里克·泰勒是科学管理理论的奠基人,他提出了科学管理的基本原则,包括工作分析、工作标准化、工作优化等。
泰勒的理论主张通过科学的方法来管理组织,提高工作效率和生产力。
2. 行政管理理论的发展(20世纪20年代-40年代)行政管理理论在20世纪20年代至40年代得到了进一步发展。
亨利·福尔特提出了行政管理的原则,强调管理者应该具备良好的组织能力和领导能力。
马克斯·韦伯提出了官僚理论,认为官僚制度是一种高效的组织形式。
3. 行为科学理论的兴起(20世纪40年代-50年代)行为科学理论的兴起在20世纪40年代至50年代。
此时,管理学家开始关注人的行为和心理对组织的影响。
埃尔顿·梅约提出了人际关系学派的观点,强调组织中人与人之间的关系对组织的效果有重要影响。
4. 管理科学理论的发展(20世纪50年代-60年代)管理科学理论在20世纪50年代至60年代得到了发展。
这一时期,管理学家开始运用数学和统计方法来解决管理问题。
线性规划、决策树、排队论等方法被广泛应用于组织管理中。
5. 系统管理理论的兴起(20世纪60年代-70年代)系统管理理论的兴起在20世纪60年代至70年代。
系统管理理论认为组织是一个复杂的系统,各个部分相互关联,相互影响。
彼得·德鲁克提出了管理者应该采取系统思维的观点,将组织视为一个整体来进行管理。
6. 战略管理理论的发展(20世纪70年代至今)战略管理理论的发展在20世纪70年代至今。
战略管理理论强调组织应该具备长远的发展目标,并制定相应的战略来实现这些目标。
迈克尔·波特提出了五力模型和价值链模型等工具,帮助组织进行战略分析和制定。
二、发展趋势1. 知识管理的重要性不断提升随着信息技术的发展,知识管理在现代管理中的重要性不断提升。
生产管理NPS及IE七大手法
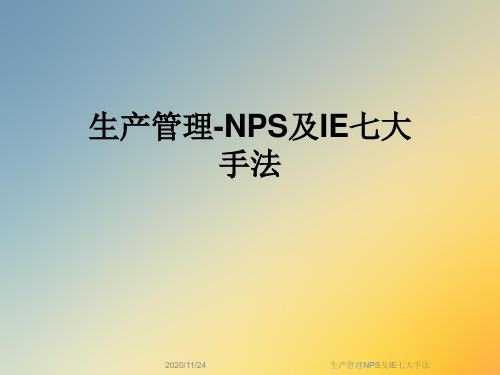
n 多能工:一个作业员可操作两种或两种以上的技能 n 水蜘蛛:从事非标准作业的人员(水面上的小虫,动作敏
捷、快速).
生产管理NPS及IE七大手法
制造业的四大生产型态
n 一:流线化生产(根据产品的制作流程来布置设备的生
产方式)
n 二:安定化生产(人,机,料,质量,管理的安定) n 三:平准化生产(平坦、准时的生产---Just In Time) n 四:超市化生产(也叫后补充生产)
定动作 n 人的动作三不政策 1. 不摇头 2. 不转身3.不插秧
生产管理NPS及IE七大手法
良好的NPS线应具备的条件
n 能做出标准作业的生产线 n 没有浪费的物流 n 情报的流动 (目视化&广告牌管理) n 少人化的生产线 n 做全数检查的质量保证(避免制造与检验分开) n 保全性 (便于操作保养) n 安全性(劳动安全的考虑,机械安全,误动作的避免,
生产管理NPS及IE七大手法
工厂布置
n 水平布置改成垂直布置(依制程顺序布置) n U字型生产线(IO一致即出入口一致) n 长屋型变成大通铺(去除隔间) n 一笔划的布置(理想化)
生产管理NPS及IE七大手法
NPS对设备的新观念
n 设备设计考虑原则(小柔快流) 1. 小型化 2. 流动化 3. 柔软化 4. 快变化 n 设备布置三不政策: 1. 不落地生根 2. 不寄人篱下 3. 不离群索居 n 设备动作三不政策 1.不做切削空气的动作 2. 不做木偶动作3.不做立
排放物的收集,舒适作业环境照明排气等的提供) n 工厂全体性(A/C及物料、成品的搬运,配水电气,制
程搭配,预备扩充空间)
生产管理NPS及IE七大手法
现代管理理论的发展历程及发展趋势

现代管理理论的发展历程及发展趋势一、发展历程现代管理理论的发展可以追溯到20世纪初的科学管理运动。
以下是现代管理理论的主要发展阶段:1. 科学管理阶段(20世纪初)科学管理运动由弗雷德里克·泰勒(Frederick Taylor)和亨利·福特(Henry Ford)等人引领。
他们通过研究工作方法和生产流程,提出了科学管理的基本原则和方法,如分工、标准化、时间和运动研究等。
2. 行为科学阶段(20世纪30年代-50年代)行为科学阶段强调员工行为和组织行为对管理的影响。
埃尔顿·梅奥(Elton Mayo)等人进行了著名的霍桑实验,揭示了员工的社会和心理需求对工作绩效的影响,为人性化管理奠定了基础。
3. 管理科学阶段(20世纪40年代-60年代)管理科学阶段以数学模型和决策科学为基础,通过运筹学、线性规划和统计分析等方法,解决了管理中的决策问题。
此时,管理被视为一门科学,强调定量分析和理性决策。
4. 系统理论阶段(20世纪50年代-70年代)系统理论阶段将组织视为一个复杂的系统,强调组织内外各要素之间的相互作用和影响。
这一阶段的代表人物包括路德维希·冯·贝特兰费(Ludwig von Bertalanffy)和彼得·德鲁克(Peter Drucker)等。
5. 战略管理阶段(20世纪70年代至今)战略管理阶段强调组织与环境的关系,注重组织的长期发展和竞争优势。
迈克尔·波特(Michael Porter)提出了五力模型,匡助企业分析竞争力和制定战略。
此外,质量管理、变革管理和知识管理等概念也逐渐兴起。
二、发展趋势现代管理理论的发展仍在不断演进,以下是当前的发展趋势:1. 变革管理与创新随着市场环境和技术的不断变化,组织需要灵便应对变化并实现创新。
变革管理强调组织变革的规划、实施和评估,以确保变革的成功。
创新管理则关注创新的激励、流程和组织文化等方面。
【管理课件】案例20-丰田公司迈向Just-In-Time管理的道路

丰田公司迈向Just-In-Time管理的道路丰田的生产和管理系统长期以来一直是丰田公司的核心竞争力和高效率的源泉,同时也成为国际上企业经营管理效仿的榜样,例如,作为丰田生产管理一大特点的看板管理已被世界各地的企业所采用。
如今,世界很多大型企业都在学习丰田管理模式的基础上,建立了各自的管理系统,以试图实现标杆超越,像通用电气公司、福特公司、克莱斯勒公司等世界著名企业都加入了这一行列。
但是,令人惊异的是,尽管丰田管理模式已为全球所认同和接受,真正成功的企业却并不多,如今位于日本的丰田公司每天都要接受数以万计的企业高级管理者参观,这些参观者将他们看到的管理方式带到本国后,并没有得到意想的效果,为此,很多人认为丰田管理模式的成功根源于其独特的文化因素。
但事实并非如此,例如同是日本公司的尼桑和本田却并没有达到丰田的标准,而丰田本身却将其独特的管理模式带到了全世界,这其中的代表就是位于美国肯塔基州的丰田乔治城汽车生产厂,该厂自1988年7月开始在1300英亩的厂址上进行批量生产,年生产能力为200000辆Camry轿车,相当于以往美国从日本进口同类型轿车的总量,1991年秋天丰田美国公司引入了全新的Camry轿车,1992年该类型车的供应量为40000辆,销售额将增加20%。
新的Camry轿车属于中等家庭车系列,占有美国所有轿车市场l/3的市场份额,价格平均为$18500,税前平均利润为17%,显然,其经营绩效是十分瞩目的。
由此看来,丰田管理模式并不是因为其独特的日本文化而难以为其他国家的企业所学习,之所以存在管理方法难以移植的情况,主要原因在于参观者所看到的丰田管理模式只是其外在的东西,诸如它的活动、连接和生产流等都是较为固定、甚至死板的东西,但是,在这些看似简单的活动和流程后面,却蕴含着丰田公司巨大的柔性和适应性,正是这些看似简单、却颇具柔性的管理特点,造就了丰田公。
司举世瞩目的经营业绩,也使得他的柔性化生产管理方式--TPS (Toyota Production System)成为管理中的精髓,并使大规模定制模式下的敏捷产品开发和生产成为现实。
just-in-time供应链管理理念整理

just-in-time供应链管理理念整理Supply Chain Management : Just In TimeIntroductionIn the realm of supply chain management, “Just in time” refers to an inventory strategy that it used to improve a business’s return on investment through a reduction of in process inventory and all related costs. Just in time is driven by a series of signals, referred to as Kanban, which tell production processes when it is necessary to make the next part. Kanban can be visual signals, bu t are generally “tickets.” When implemented in a correct fashion, “Just in time” can help a producer improve in such areas as quality, efficiency, as well as the return on investment.When stock drops to a certain level, new stocks have to be ordered. This helps maintain space in the warehouse and keeps costs down to a reasonable amount. One drawback of “Just in time” however is that the re-order level is determined by the previous demand. If the demand rises above that amount, then inventory will be depleted a lot faster than usual and might cause customer service problems. In order to maintain a ninety five percent service rate, the company should always carry two standard deviations of safety stock. Around the Kanban, shifts in demand should be forecast until trends are established to reset the correct Kanban level. Some feel that recycling Kanban at a quicker pace can help the system flex by up to thirty percent. Recently, producers have started touting a thirteen week average as a better predictor than previous forecasts would provide.Another term employed in “Just in time” is Kaizen. It means literally the continuous improvement of the process.History of Just in TimeThe Ford Motor Company first employed “Just in time”. It desc ribes the “dock to factory floor” concept, in which incoming materials were not even kept in storage, but went directly in to production. Of course, this concept relied upon a useful freight management system; the one employed is described in Ford’s Today and Tomorrow of the ye ar 1926. Later, this technique was taken up by Japan’s Toyota Motor Corporation in its Toyota Production System.Businesses in Japan are not able to afford large warehouse spaces. Prior to the 1950s, this was a major disadvantage because it forced the production lot size to be below that of the economic lot size. Thus, a poor return could be expected on a factory investment.Taiichi Ohno was Toyota’s main engineer in the 1950s. After examining several accounting assumptions, Ohno came to the realization that another method would be possible.It would be possible for the factory to implement “Just in time.” This would require the factory to increase in their flexibility, while simultaneously reducing their overhead costs related to retooling. Effectively, this would also reduce the economic lot size, which would be made to fit the current warehouse space. “Just in time” thus emerged as one of the main pillars of T oyota’s Production System.Over the next few years, Toyota re-designed car models to aid such production processes aswelding and paint spraying. Toyota was one of the first automobile manufacturers to use robots to perform such tasks. Some of the changes were rather minor; one of them was to simply standardize hole sizes that were used to hang parts onhooks. Fastener numbers and types were reduced so as to standardize the assembly tools and process. There were even instances when identical subassemblies were employed.It was then determined by leading engineers at Toyota that what needed to be mended in the retooling process was the amount of time that was required to change the stamping dies that body parts used. Using crowbars and wrenches, these parts had to be adjusted by hand. Sometimes it would take a period of several days to install large die sets and adjust it to fit Toyota’s high quality standards. Since they had to be installed one at a time by several experts, sometimes this would take up to several weeks all told.To remedy this situation, Toyota decided to implement a strategy invented by Shigeo Shingo called Single Minute Exchange of Die, or SMED. Using this strategy with simple fixtures, measurements could be substituted for adjustments. It would then take die changes only a few hours, rather than several days. This also reduced the skill level that was required, as the stampings’ quality was then controlled by a written formula. The remaining time was then typically utilized to search for hand tools and move dies. Die change times were reduced to about forty seconds thanks to the use of tool racks as well as major procedural alterations. These days, dies are changed through the factory in a ripple process as the new product begins to flow.Once Single Minute Exchange of Die was implemented in Toyota factories, economic lot sizes fell to as little as a single car. As little as one part could be stored in each assembly station, thanks to the fact that the process was carried over in to parts storage. Whenever a part was gone, a signal (Kanban) was emitted for a replacement part.Supply Chain Management : JIT PhilosophyIt should be kept in mind that “just in time” is not a simple step by step method, but an entire philosophy that must be observed in order to avoid the downfalls. The ideas comprising “just in time” philos ophy come from many different fields, such as industrial engineering, behavioral science, statistics, and production management. When it comes to how inventory is treated according to the “just in time” scheme, one must learn how inventory is to be viewed, the way i t expresses certain practices within the company’s management, as well as the philosophy’s main principles.As opposed to the traditional view of inventory, “just in time” views inventory as being wasteful, in that it incurs costs, rather than adding value to a company. This does not mean that inventory should be removed altogether at the expense of manufacturing. Rather, it expounds the idea that a company could save costs by eliminating inventory that does not compensate for issues related to manufacturing. Also, processes must be constantly upgraded so that the need for inventory is reduced.What is more, anytime that inventory is permitted to accumulate, a downward spiral begins。
日产Just-in-time 的例子
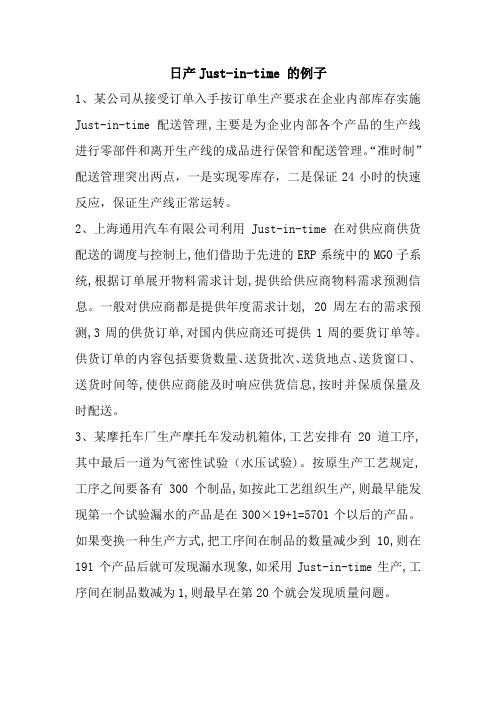
日产Just-in-time 的例子
1、某公司从接受订单入手按订单生产要求在企业内部库存实施Just-in-time 配送管理,主要是为企业内部各个产品的生产线进行零部件和离开生产线的成品进行保管和配送管理。
“准时制”配送管理突出两点,一是实现零库存,二是保证24小时的快速反应,保证生产线正常运转。
2、上海通用汽车有限公司利用Just-in-time在对供应商供货配送的调度与控制上,他们借助于先进的ERP系统中的MGO子系统,根据订单展开物料需求计划,提供给供应商物料需求预测信息。
一般对供应商都是提供年度需求计划, 20周左右的需求预测,3周的供货订单,对国内供应商还可提供1周的要货订单等。
供货订单的内容包括要货数量、送货批次、送货地点、送货窗口、送货时间等,使供应商能及时响应供货信息,按时并保质保量及时配送。
3、某摩托车厂生产摩托车发动机箱体,工艺安排有20道工序,其中最后一道为气密性试验(水压试验)。
按原生产工艺规定,工序之间要备有300个制品,如按此工艺组织生产,则最早能发现第一个试验漏水的产品是在300×19+1=5701个以后的产品。
如果变换一种生产方式,把工序间在制品的数量减少到10,则在191个产品后就可发现漏水现象,如采用Just-in-time生产,工序间在制品数减为1,则最早在第20个就会发现质量问题。
“精益生产与敏捷制造技术高级研修班”总结

“精益生产与敏捷制造技术高级研修班”总结“精益生产与敏捷制造技术高级研修班”总结2019年8月25日-9月7日,本人参加了中船集团赴日“精益生产与敏捷制造技术高级研修班”,培训主要包括丰田的GPS生产方式理论与实操培训、日本知名企业参观学习两大内容。
系统全面剖析了丰田精益生产理念,精益制造在汽车行业的应用,针对性的现场改善实战演练和精益制造标杆企业的参观交流。
现将学习情况总结如下:一、学习总结丰田的生产方式又称TPS,而GPS理念则是在TPS的基础上关注人财的育成而发展起来,GPS注重与企业经营管理系统地无缝链接,其核心是通过省人和彻底消除浪费,实现高效高质低成本的生产方式。
GPS生产方式的2大核心为准时化生产(Just in time)和自働化(Jidoka),准时化是指把必要的物品在必要的时候,只按要求的数量进行生产和搬运,最终实现成本的控制,避免浪费;自动化则是当设备发生异常问题时,不需要人工操作,让设备、生产线自动停止的生产机制,强调人与机械的完美结合。
GPS生产追求一人工的工作实质,提高赋予产品附加值的动作,减少其余的动作浪费,通过改善省人,来提高具有附加值工作的比率,实现更加有效地工作。
培训期间,系统深入了解了GPS生产方式在丰田汽车制造各环节的应用,丰田GPS通过后工序领取、后补充生产,把前后工序有效连接起来,着重针对看板在后工序领取的作用及功能,如何使用进行了讲解,开展了工厂看板管理模拟运行和标准作业改善实战演练,真实模拟了丰田公司任务计划的制定、原材料采购、生产加工、运输等关键过程运行,通过看板管理和标准作业改善模拟运行实战训练,强化了以后工序生产为导向的看板管理系统、GPS不浪费、防纠错等内容的理论学习,更深入理解了以最少浪费的作业顺序,确保安全和品质,通过有效率的作业组合,来实现高效率的生产的方法,导入GPS精益生产的精髓。
丰田公司及日本标杆企业实地参观与交流期间,在丰田及其子公司车间现场,机器人、机械手臂有条不紊运作;各种物料小车按指令和程序,穿梭在各工位流程,机器和人的有机完美合作,标准化作业让人震惊。
- 1、下载文档前请自行甄别文档内容的完整性,平台不提供额外的编辑、内容补充、找答案等附加服务。
- 2、"仅部分预览"的文档,不可在线预览部分如存在完整性等问题,可反馈申请退款(可完整预览的文档不适用该条件!)。
- 3、如文档侵犯您的权益,请联系客服反馈,我们会尽快为您处理(人工客服工作时间:9:00-18:30)。
迈向J u s t-I n-T i m e管理的道路--丰田公司的T P S管理模式丰田的生产和管理系统长期以来一直是丰田公司的核心竞争力和高效率的源泉,同时也成为国际上企业经营管理效仿的榜样,例如,作为丰田生产管理一大特点的广告牌管理已被世界各地的企业所采用。
如今,世界很多大型企业都在学习丰田管理模式的基础上,建立了各自的管理系统,以试图实现标杆超越,像通用电气公司、福特公司、克莱斯勒公司等世界着名企业都加入了这一行列。
但是,令人惊异的是,尽管丰田管理模式已为全球所认同和接受,真正成功的企业却并不多,如今位于日本的丰田公司每天都要接受数以万计的企业高级管理者参观,这些参观者将他们看到的管理方式带到本国后,并没有得到意想的效果,为此,很多人认为丰田管理模式的成功根源于其独特的文化因素。
但事实并非如此,例如同是日本公司的尼桑和本田却并没有达到丰田的标准,而丰田本身却将其独特的管理模式带到了全世界,这其中的代表就是位于美国肯塔基州的丰田乔治城汽车生产厂,该厂自1988年7月开始在1300英亩的厂址上进行批量生产,年生产能力为200000辆Camry轿车,相当于以往美国从日本进口同类型轿车的总量,1991年秋天丰田美国公司引入了全新的Camry轿车,1992年该类型车的供应量为40000辆,销售额将增加20%。
新的Camry轿车属于中等家庭车系列,占有美国所有轿车市场l/3的市场份额,价格平均为$18500,税前平均利润为17%,显然,其经营绩效是十分瞩目的。
由此看来,丰田管理模式并不是因为其独特的日本文化而难以为其他国家的企业所学习,之所以存在管理方法难以移植的情况,主要原因在于参观者所看到的丰田管理模式只是其外在的东西,诸如它的活动、连接和生产流等都是较为固定、甚至死板的东西,但是,在这些看似简单的活动和流程后面,却蕴含着丰田公司巨大的柔性和适应性,正是这些看似简单、却颇具柔性的管理特点,造就了丰田公司举世瞩目的经营业绩,也使得他的柔性化生产管理方式--TPS (ToyotaProductionSystem)成为管理中的精髓,并使大规模定制模式下的敏捷产品开发和生产成为现实。
以下从纵(历史发展)、横(管理特点)两个方面来揭示丰田公司JIT管理的奥秘。
的"JustinTime"这一理念的具体体现。
日本汽车工业从其起步到今天经历了一个"技术设备引进对国产化→建立规模生产体制→高度成长→工业巨大化→强化国际竞争力→出口增大对全球战略"这样一个过程。
但是,从一开始的技术设备引进阶段,日本汽车工业就没有全部照搬美国的汽车生产方式。
这其中除了当时的日本国内市场环境、劳动力以及二次世纪大战之后资金短缺等原因以外。
一个很重要的原因是,以丰田汽车公司副总裁大野耐一等人为代表,他们从一开始就意识到了,美国汽车工业的生产方式虽然已很先进,但需采取一种更灵活,更能适应市场需求的能够提高产品竞争力的生产方式。
在20世纪后半期,整个汽车市场进入了一个市场需求多样化的新阶段,而且对质量的要求也越来越高,随之给制造业提出的新课题即是,如何有效地组织多品种小批量生产,否则的话,生产过剩所引起的只是设备、人员、库存费用等一系列的浪费,从而影响到企业的竞争能力以至于生存。
在这种历史背景下,1953年,日本丰田公司的副总裁大野耐一综合了单件生产和批量生产的特点和优点,创造了一种在多品种小批量混合生产条件下高质量、低消耗的生产方式即准时生产(JustInTime,简称JIT)。
JIT生产方式的基本思想是"只在需要的时候,按需要的量,生产所需的产品",也就是追求一种无库存,或库存达到最小的生产系统。
JIT的基本思想是生产的计划和控制及库存的管理。
JIT生产方式以准时生产为出发点,首先暴露出生产过量和其他方面的浪费,然后对设备、人员等进行汰淘、调整,达到降低成本、简化计划和提高控制的目的。
在生产现场控制技术方面,JIT 的基本原则是在正确的时间,生产正确数量的零件或产品,即准时生产。
它将传统生产过程中前道工序向后道工序送货,改为后道工序根据"广告牌"向前道工序取货,广告牌系统是JIT生产现扬控制技术的核心,但JIT不仅仅是广告牌管理。
JIT的目标是彻底消除无效劳动和浪费,具体要达到以下目标:1.废品量最低(零废品)。
JIT要求消除各种引起不合理的原因,在加工过程中每一工序都要求达到最好水平。
2.库存量最低(零库存),JIT认为,库存是生产系统设计不合理、生产过程不协调、生产操作不良的证明。
3.准备时间最短(零准备时间)。
准备时间长短与批量选择相联系,如果准备时间趋于零,准备成本也趋于零,就有可能采用极小批量。
4.生产提前期最短。
短的生产提前期与小批量相结合的系统,应变能力强,柔性好。
5.减少零件搬运,搬运量低。
零件送进搬运是非增值操作,如果能使零件和装配件运送量减小,搬运次数减少,可以节约装配时间,减少装配中可能出现的问题。
6.机器损坏低。
7.批量小。
为了达到上述目标,JIT对产品和生产系统设计考虑的主要原则有以下三个方面:1.在当个产品寿命周期已大大缩短的年代,产品设计应与市场需求相一致,在产品设计方面,应考虑到产品设计完后要便于生产。
2.尽量采用成组技术与流程式生产。
3.与原材料或外购件的供应者建立联系,以达到JIT供应原材料及采购零部件的目的。
在JIT方式中,试图通过产品的合理设计,使产品易生产,易装配,当产品范围扩大时,即使不能减少工艺过程,也要力求不增加工艺过程,具体方法有:(1)模块化设计;(2)设计的产品尽量使用通用件,标准件;(3)设计时应考虑易实现生产自动化。
JIT的基础之一是均衡化生产,即平均制造产品,使物流在各作业之间、生产线之间、工序之间、工厂之间平衡、均衡地流动。
为达到均衡化,在JIT中采用月计划、日计划,并根据需求变化及时对计划进行调整。
JIT提倡采用对象专业化布局,用以减少排队时间、运输时间和准备时间,在工厂一级采用基于对象专业化布局,以使各批工件能在各操作间和工作间顺利流动,减少通过时间;在流水线和工作中心一级采用微观对象专业化布局和工作中心形布局,可以减少通过时间。
JIT可以使生产资源合理利用,包括劳动力柔性和设备柔性。
当市场需求波动时,要求劳动力资源也作相应调整。
如需求量增加不大时,可通过适当调整具有多种技能操作者的操作来完成;当需求量降低时,可采用减少生产班次、解雇临时工、分配多余的操作工去参加维护和维修设备。
这就是劳动力柔性的含义;而设备柔性是指在产品设计时就考虑加工问题,发展多功能设备。
JIT强调全面质量管理,目标是消除不合格品,消除可能引起不合格品的根源,并设法解决问题,JIT中还包含许多有利于提高质量的因素,如批量小、零件很快移到下工序、质量问题可以及早发现等。
JIT生产管理方式在70年代末期从日本引入我国,长春第一汽车制造厂最先开始应用广告牌系统控制生产现场作业。
到了1982年,第一汽车制造厂采用广告牌取货的零件数,已达其生产零件总数的43%。
8O年代初,中国企业管理协会组织推广现代管理方法,广告牌管理被视为现代管理方法之一,在全国范围内宣传推广,并为许多企业采用。
近年来,在我国的汽车工业;电子工业、制造业等实行流水线生产的企业中应用JIT,获得了明显效果,例如第一汽车制造厂、第二汽车制造厂、上海大众汽车有限公司等企业,结合厂情创造性地应用JIT,取得了丰富的经验,创造了良好的经济效益。
JIT以订单驱动,通过广告牌,采用拉动方式把供、产、销紧密地衔接起来,使物资储备,成本库存和在制品大为减少,提高了生产效率,这一生产方式在推广应用过程中,经过不断发展完善,为日本汽车工业的腾飞插上了翅膀,提高了生产效率。
这一生产方式亦为世界工业界所注目,被视为当今制造业中最理想且最具有生命力的新型生产系统之一。
二、"广告牌"方式管理方法以往日本汽车生产商从各自独立的公司那里获得零部件,而单个企业内部的纵向联系又显得不够紧密,因此为了彻底解决这个问题民主高度相互信任和尊重的基础上,丰田公司同它们的零部件供应商建立了牢固的协作关系,这种作关系主要依靠交叉管理、相互融资、技术转移和规定作业区来维系,所以,"广告牌"和"及时供应"等管理方法能在供应商中到采用。
其结果合理的生产流水线的安排减少了运输费用,使运输中造成的损失减少到最低程度,并大幅度降低了必要的库存作备。
在"广告牌"制度下,很多部件一直要等到下一道工序需要前几个小时才生产出来,免去这些库存也就暴露了人员过多、人员不足及机器效率低等早就存在的问题,并加以纠正。
以上这些管理上的变革产生的效果是惊人的,丰田汽车每售100辆因质量问题受到申诉的数量从1969年的4.5次下降到1973年的l.3次,生产效率也大为很高。
三、TPS的管理方法与精髓丰田管理的一个主要思想就是在保持稳定质量的同时,能够使生产能及时反映市场的变化,并在逐步改善提高的基础上,最大限度地降低成本。
而这种指导思想反映在丰田的发展战略上,就表现为不盲目地进行扩张,或步其他企业的后尘,匆匆进入某一市场,而是稳扎稳打,在充分了解市场和建立起自己完整的供应体系或竞争力后,再当机立断地进入海外市场,无论是他进入美国市场,还是后来进入亚洲,包括中国市场,都表现为这一特点。
当然,丰田公司独特的经营管理意识不仅反映在它的发展战略上,更反映在它的日常管理上,为了全面揭示丰田的管理艺术,特别是以JIT为重要内容的TSP,下面将从4个方面来介绍他的现场作业管理,从中可以使我们对它的JIT有着更深入的了解。
1.员工该如何工作丰田公司的管理思想中认为,要想实现及时化、质量稳定的生产,就必须从作业活动的细微之处抓起,把所有的工作分化为一个一个相互衔接的流程,并规定好各流程的作业内容、所处的位置、作业时间和作业绩效。
例如,在汽车座椅的安装活动上,螺丝的安装都是以同样的顺序进行,安装的时间也是规定好的,甚至连上螺丝的扭矩也被规定得清清楚楚。
这种精确的管理方法不仅仅运用在重复性的生产活动中,同时也被运用在企业的所有活动中,无论是职能型的活动,还是管理活动也都如此。
这一管理方法表面上看起来非常简单,但事实上并不是所有的企业都能做到。
以TMM(ToyotaMotorManufacturing,,Inc,简称美国丰田汽车工厂)厂中安装前座椅为例,操作人员被要求从纸板箱中取出4颗螺丝,然后安装在汽车上,扭紧,然后在计算机中输入一个代码,以表明整个作业已经无暇疵地完成,再等待下一辆汽车的安装。
新手往往由经验丰富的老工人手把手地教,当新手遇到任何困难和问题时,如没有扭紧螺丝或忘记输入代码时,老工人就会立刻帮助他们。