新能源大巴BMS结构与乘用车的区别
动力电池模组的结构认知

动力电池模组的结构认知引言概述:动力电池模组是电动汽车中的重要组成部分,它的结构对电池的性能和寿命有着重要影响。
本文将从五个大点出发,详细阐述动力电池模组的结构认知。
正文内容:1. 动力电池模组的基本构成1.1 电池单体:动力电池模组由多个电池单体组成,电池单体是电池模组的基本单元,其电压和容量决定了整个模组的性能。
1.2 电池管理系统(BMS):BMS是动力电池模组的核心部件,负责监控和管理电池的电压、温度、电流等参数,以确保电池的安全和性能稳定。
1.3 散热系统:动力电池模组需要通过散热系统来控制电池的温度,以保持电池在适宜的工作温度范围内,提高电池的寿命和性能。
1.4 连接件和电缆:动力电池模组内的电池单体需要通过连接件和电缆进行连接,确保电池单体之间的电流和信号传输畅通。
2. 动力电池模组的结构类型2.1 平板式结构:平板式结构是最常见的动力电池模组结构,电池单体按照水平或垂直方向排列,通过连接件和电缆连接。
2.2 立柱式结构:立柱式结构中,电池单体以垂直方向排列,通过连接件和电缆连接,可以提高模组的能量密度。
2.3 转子式结构:转子式结构中,电池单体以环形或螺旋状排列,通过连接件和电缆连接,可以提高模组的能量密度和散热效果。
3. 动力电池模组的保护措施3.1 短路保护:动力电池模组中的BMS系统可以通过监测电池的电流来及时判断是否存在短路情况,并采取相应的保护措施,以防止电池损坏。
3.2 过充保护:BMS系统可以根据电池的电压情况,及时控制充电过程,以避免电池过充,提高电池的使用寿命。
3.3 过温保护:BMS系统可以监测电池的温度,并在温度过高时采取相应的措施,如降低充电速度或断开电池连接,以保护电池不受过热损坏。
4. 动力电池模组的标准化与规范4.1 安全标准:动力电池模组需要符合一系列的安全标准,如电池安全性能测试、防护等级要求等,以确保电池的使用安全。
4.2 性能标准:动力电池模组需要符合一系列的性能标准,如能量密度、循环寿命、放电性能等,以保证电池的性能优良。
汽车设计-新能源汽车动力电池(PACK)的设计
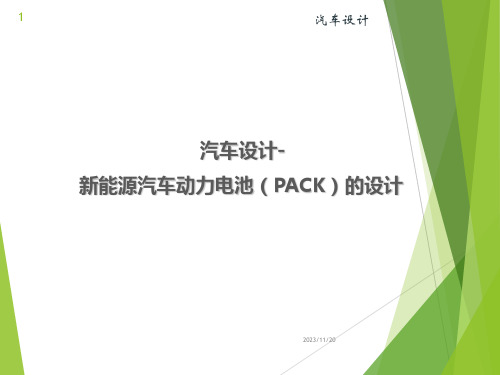
2023/11/20
3
动力电池的组成:
汽车设计
单体动力电池:构成动力电池模块的最小单元。一般由正极、负极、电解质、隔膜、外壳及端子(极 端)等组合而成,可实现电能与化学能之间的直接转换。
电池模组/电池模块:单体电池通过串联和并联在物理结构和电路上连接起来构成动力电池包或最小分 组,可作为一个单元替换。
a)人体触电防护 b)静电防护 c)电磁干扰防护
2023/11/20
20
电气安全设计:
4.电气隔离 (1)电气间隙
定义:在两个导电零部件之间或导电零部件与 设备防护界面之间测得的最短空间距离。即在保 证电气性能稳定和安全的情况下,通过空气能实 现绝缘的最短距离。
汽车设计
(2)爬电距离 定义:在两个导电部分之间沿绝缘材料表面的
(E1、E2、E3、En为各个电池的电动势)
E=nE1(各个电池电势差相同)
汽车设计
4、串联电池组的内阻
R0 R1 R2 R3 Rn
●如果每个电池的内阻相同则
R 0 nR 1
5、串联电池组所供给的电流
串联电池组与负载电阻R构成闭合回路时
I
E1 E2 E3 En R R 1 R 2 R 3 R n
2023/11/20
4
从单体到系统——单体电池:
铝壳包装而成的电 池,采用激光封口 工艺,全密封,铝 壳技术已非常成熟, 且对材料技术,如 气胀率、膨胀率等 指标,要求不高。
汽车设计
软包即软包锂电池,是在液 态锂离子电池套上一层聚合 物外壳的电池,采用铝塑复 合膜包装,软包锂电池的机 械强度不高,在出现安全事 故如内短路等情况下,电池 容易鼓起排气,降低了爆炸 风险。
1
汽车设计
解读电池管理系统BMS的作用及特点

解读电池管理系统BMS的作用及特点随着新能源概念的普及推广,新能源汽车也逐步走入了千家万户,新能源汽车作为寻常百姓的新购车选择已经开始侵占着原本属于传统燃油汽车的市场,作为目前新能源汽车最大的市场,中国的企业依靠着新能源汽车首次与国外企业站在同一起跑线,不断涌现的新技术新工艺,让中国的新能源汽车行业有了更充足的底气去放眼世界,心系未来。
提到传统燃油汽车的核心关键自然离不开俗称的三大件:发动机、底盘以及变速箱,在这三大件上,中国技术落后以德日美为首的国外汽车厂商已是共识。
而在新能源电动汽车上也有俗称的三大件:电池、电机和电控,由于新能源电动汽车在全球范围内仍是较新的行业,各国企业的起步相差并不大,这也让我国企业在汽车这个1886年发明至今的多用途动力驱动工具上拥有了与国外企业一较高下的条件。
本文重点给大家介绍新能源电动汽车三大件里的电控(业内普遍称之为电池管理系统BMS)。
新能源电动汽车与传统燃油汽车最大的区别是用动力电池作为动力驱动,而作为衔接电池组、整车系统和电机的重要纽带,电池管理系统BMS的重要性不言而喻,国内外许多新能源车企都将电池管理系统作为企业最核心的技术来看待,最著名的例子就是大家耳熟能详的特斯拉,特斯拉的电动汽车三大件中,电池来自于松下,电机来自于台湾供应商,而只有电池管理系统是特斯拉自主研发的核心技术,2008年-2015年期间特斯拉所申请的核心知识产权大都与电池管理系统相关,由此可见电池管理系统对于新能源汽车的重要性。
而国内,电池管理系统BMS的研发生产主要集中在这三类企业:1、新能源汽车厂商,代表企业:比亚迪2、电池PACK厂商,代表企业:沃特玛、普莱德3、专业BMS厂商,代表企业:惠州亿能、深圳国新动力电池管理系统BMS到底有什么作用?电池管理系统BMS是一个本世纪才诞生的新产品,因为电化学反应的难以控制和材料在。
新能源汽车零部件分类
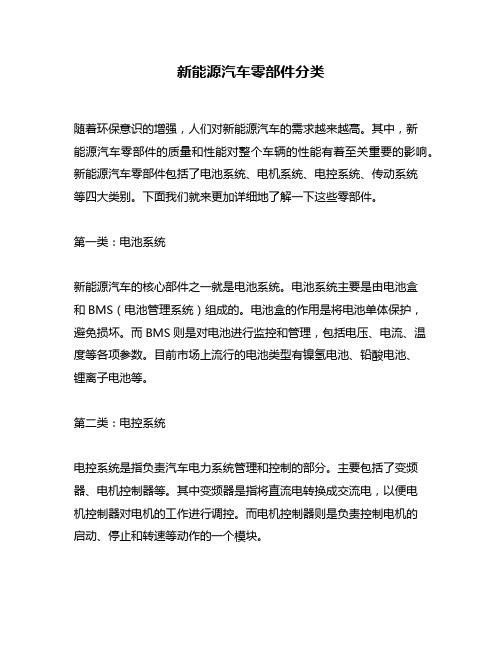
新能源汽车零部件分类随着环保意识的增强,人们对新能源汽车的需求越来越高。
其中,新能源汽车零部件的质量和性能对整个车辆的性能有着至关重要的影响。
新能源汽车零部件包括了电池系统、电机系统、电控系统、传动系统等四大类别。
下面我们就来更加详细地了解一下这些零部件。
第一类:电池系统新能源汽车的核心部件之一就是电池系统。
电池系统主要是由电池盒和BMS(电池管理系统)组成的。
电池盒的作用是将电池单体保护,避免损坏。
而BMS则是对电池进行监控和管理,包括电压、电流、温度等各项参数。
目前市场上流行的电池类型有镍氢电池、铅酸电池、锂离子电池等。
第二类:电控系统电控系统是指负责汽车电力系统管理和控制的部分。
主要包括了变频器、电机控制器等。
其中变频器是指将直流电转换成交流电,以便电机控制器对电机的工作进行调控。
而电机控制器则是负责控制电机的启动、停止和转速等动作的一个模块。
第三类:电机系统电机是新能源汽车的核心部件之一。
电机系统包括了电机、变速箱、减速器和传动轴等。
目前市场上的电机类型有同步电机、异步电机等种类。
电机有良好的低噪声、低震动、高效率等特点,可以使汽车更加省油、节能。
第四类:传动系统传动系统是将电机的动力传送至车轮,驱动汽车前进的部件。
传动系统包括了传动轴、万向节、差速器等,它们能有效地将电机的动力输送至车轮,从而形成汽车的动力系统。
除了以上四类电子部件外,新能源汽车还有其他零部件,比如充电系统、底盘部件等。
不过,以上四类部件是新能源汽车最关键的部分,对整个汽车的性能起着至关重要的作用。
总之,新能源汽车的发展必须依赖于零部件的不断创新和升级。
随着汽车制造技术的不断发展和革新,相信新能源汽车的性能和质量也会越来越好。
电池管理系统BMS架构及功能知识介绍

电池管理系统BMS架构及功能知识介绍新能源车与传统汽车最⼤的区别是⽤电池作为动⼒驱动,所以动⼒电池是新能源车的核⼼。
电动汽车的动⼒输出依靠电池,⽽电池管理系统BMS(BatteryManagementSystem)则是其中的核⼼,是对电池进⾏监控和管理的系统,通过对电压、电流、温度以及SOC等参数采集、计算,进⽽控制电池的充放电过程,实现对电池的保护,提升电池综合性能的管理系统,是连接车载动⼒电池和电动汽车的重要纽带。
国外公司BMS做的⽐较好的有联电、⼤陆、德尔福、AVL和FEV等等,现在基本上都是按照AUTOSAR架构以及ISO26262功能安全的要求来做,软件功能更多,可靠性和精度也较⾼。
国内很多主机⼚也都有⾃主开发的BMS产品并应⽤,前期在功能和性能上与国外⼀流公司相差甚远,但随着国内电池和BMS技术的快速发展差距正在逐步缩⼩,希望不久的将来能够实现成功追赶甚⾄超越。
BMS主要包括硬件、底层软件和应⽤层软件三部分。
硬件1、架构BMS 硬件的拓扑结构分为集中式和分布式两种类型:(1)集中式是将所有的电⽓部件集中到⼀块⼤的板⼦中,采样芯⽚通道利⽤最⾼且采样芯⽚与主芯⽚之间可以采⽤菊花链通讯,电路设计相对简单,产品成本⼤为降低,只是所有的采集线束都会连接到主板上,对BMS的安全性提出更⼤挑战,并且菊花链通讯稳定性⽅⾯也可能存在问题。
⽐较合适电池包容量⽐较⼩、模组及电池包型式⽐较固定的场合。
(2)分布式包括主板和从板,可能⼀个电池模组配备⼀个从板,这样的设计缺点是如果电池模组的单体数量少于12个会造成采样通道浪费(⼀般采样芯⽚有12个通道),或者2-3个从板采集所有电池模组,这种结构⼀块从板中具有多个采样芯⽚,优点是通道利⽤率较⾼,节省成本,系统配置的灵活性,适应不同容量、不同规格型式的模组和电池包。
2、功能硬件的设计和具体选型要结合整车及电池系统的功能需求,通⽤的功能主要包括采集功能(如电压、电流、温度采集)、充电⼝检测(CC和CC2)和充电唤醒(CP和A+)、继电器控制及状态诊断、绝缘检测、⾼压互锁、碰撞检测、CAN通讯及数据存储等要求。
汽车设计-新能源汽车动力电池(PACK)的设计

模组盖板
此处焊接(4处)
铝侧板1.5mm 或1.2mm
侧板绝缘 片
端板绝缘 片
铝端板 131*20*186.
5
汽车设计
线束隔离板 铝片1.5mm
厚
分解图
2020/10/15
12 电池模组典型设计案例-软包模组
汽车设计
2020/10/15
13
电池模组典型设计案例-圆柱模组
塑料柱 电池支架 镍片 PC片
32 防水设计:
汽车设计
O型密封圈
密封垫片
涂胶密封
2020/10/15
33
谢谢!
2020/10/15
2020/10/15
16
汽车设计
电池PACK常用结构件:
1.塑料件 常用材料有PP、PC、ABS、PC+ABS、PET、PBT、PA66、PA6、PVC等 用途:电气绝缘、结构强度件
案例:tesla
2020/10/15
17
汽车设计
电池PACK常用结构件:
2.钣金件 常用钢板或者铝板,钢板如DC01(SPCC),DC04,B340/590DP等 铝板1060-O,5083等
维护开关:电池包内部断 开,方便维修人员操作时 断电
2020/10/15
22
汽车设计
电气安全设计:
6.柔性母排
柔性母排又称叠片式绝缘软母排,俗称软铜片或者软铝排 柔性母排,是由多层防电晕的扁平薄铜片导体叠加,外层采用挤塑方式包覆绝缘层制作而成。
铜箔软连接的制造工艺为压焊或者钎焊。 压焊:
压焊是将铜箔叠片部分压在一起,采用分子扩散焊,通过大电流加热压焊成型。 铜箔厚度:0.05mm至0.3mm。 接触面可按用户要求镀锡或镀银。 钎焊: 钎焊是将铜箔叠片部分压在一起,采用银基钎焊料,与扁铜块对焊成型。 铜箔厚度:0.05mm至0.3mm。 接触面可按用户要求镀锡或镀银
新能源汽车电池管理系统(BMS)简介
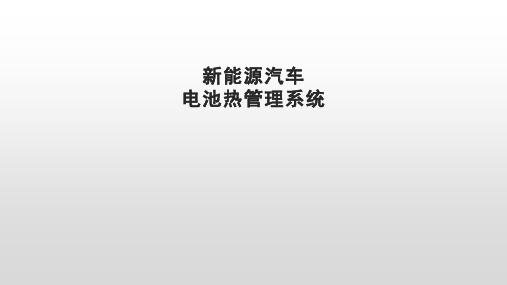
2.
重
大
前
期
电
池原始热方案管CFD仿理真分研析究
工
作
基
础
优化方案一
长安杰勋
优化方案二 优化方案三
长安志翔
恒通客车
2.
重
大
前
期
电
池原始热方案管CFD仿理真分研析究
工
作
基
础
长安杰勋
长安志翔
恒通客车
取进口流量1400m3/h, I=150A, 则发热功率为16.28KW。由仿真结 果可以看出,此结构的最高温度达 115℃,最大温差达30℃,电池组 温度分布严重不均匀。
2.
重
大
前
期
电
池优化热方案管一
理
研
究
工
作
基
础
长安杰勋
长安志翔
恒通客车
取进口流量1200m3/h, I=150A,则发热功率为16.28KW。由仿真 结果可以看出,最高温度已降到105℃,最大温差为15℃。
2.
重
大
前
期
电
池优化热方案管二
理
研
究
工
作
基
础
长安杰勋
进风
出风
长安志翔
恒通客车
取总进口流量3200m3/h, I=100A,则时发热功率为7.255KW。进 风口处电池温度高达65℃ ,出风口处温度为39℃ ,前后温差较大。
长安杰勋 长安志翔 恒通客车
350
24个 电 池 模 块 的 温 度 ( K)
345
第 13组 电 池
340 335
新能源汽车核心技术详解:电池包和BMS、VCU、-MCU

新能源汽车核心技术详解:电池包和BMS、VCU、MCU导读:为了使新能源爱好者和初级研发人员更好地了解新能源汽车的核心技术,北汽福田新能源系统开发部部长杨伟斌结合研发过程中的经验总结,从新能源汽车分类、模块规划、电控技术和充电设施等方面进行了分析。
2014年国内新能源汽车产销突破8万辆,发展态势喜人。
为了使新能源爱好者和初级研发人员更好地了解新能源汽车的核心技术,笔者结合研发过程中的经验总结,从新能源汽车分类、模块规划、电控技术和充电设施等方面进行了分析.1 新能源汽车分类在新能源汽车分类中,“弱混、强混”与“串联、并联”不同分类方法令非业内人士感到困惑,其实这些名称是从不同角度给出的解释、并不矛盾。
1.1消费者角度消费者角度通常按照混合度进行划分,可分为起停、弱混、中混、强混、插电和纯电动,节油效果和成本增等指标加如表1所示。
表中“-”表示无此功能或较弱、“+"个数越多表示效果越好,从表中可以看出随着节油效果改善、成本增加也较多.表1 消费者角度分类1.2技术角度图1 技术角度分类技术角度由简到繁分为纯电动、串联混合动力、并联混合动力及混联混合动力,具体如图1所示。
其中P0表示BSG(Belt starter generator,带传动启停装置)系统,P1代表ISG(Integrated starter generator,启动机和发电机一体化装置)系统、电机处于发动机和离合器之间,P2中电机处于离合器和变速器输入端之间,P3表示电机处于变速器输出端或布置于后轴,P03表示P0和P3的组合。
从统计表中可以看出,各种结构在国内外乘用或商用车中均得到广泛应用,相对来说P2在欧洲比较流行,行星排结构在日系和美系车辆中占主导地位,P03等组合结构在四驱车辆中应用较为普遍、欧蓝德和标致3008均已实现量产。
新能源车型选择应综合考虑结构复杂性、节油效果和成本增加,例如由通用、克莱斯勒和宝马联合开发的三行星排双模系统,尽管节油效果较好,但由于结构复杂且成本较高,近十年间的市场表现不尽如人意。
客车、乘用车、电池齐上阵哪个是南京金龙的重点

04□邮箱:************************■ 本报记者 余梦洁客车、乘用车、电池齐上阵 哪个是南京金龙的重点除了常见的大中型客车和轻客外,在南京市公交电动化战略研讨会期间,南京金龙还带来了纯电动MPV 和电芯、模组、pack,在纯电动领域的产品线更加丰富。
南京金龙客车制造有限公司副总裁、大客事业部总经理樊文堂介绍说,在未来,除了大中型、轻型客车等南京金龙的优势领域外,还会在SUV、MPV 领域发力。
“目前公司已经投资15亿元,并经过了工信部的两次审核,不出意外的话,这几个月就会有生产资质。
”他进一步表示,此外,今年南京金龙还会在三方面开展工作:“第一是零部件,围绕核心三电系统深挖深做,电机、电池、整车控制都是重点。
作为新能源车企业,不能只做‘组装厂’。
第二是开拓海外市场。
第三是发展燃料电池。
”所以,现场展示了这么多产品也就不足为奇。
轻客:已开始执行3000辆物流车意向现场展示的轻客为“同一个车型的两个版本”,即D11纯电动公路动车和D11纯电动物流车。
“受制于市场环境,此前纯电动物流车一直处在‘雷声大,雨点小’的尴尬处境。
今年新能源车市场的变化点之一,就会是物流车。
”据公司相关人士介绍,目前已经获得3000辆物流车意向订单,而总意向达到几万辆,“今年物流市场有机会,各厂家也都比较看重这个市场。
”大客:从6~18米全覆盖NJL6769BEV:这是为深圳公交定制开发的7.6米公交。
深圳公交有一个特点,即要求续驶里程较长,达到200~250公里,这可能与其运营模式有关。
深圳公交一直以来对电量要求都比较高,因为其场站补电不太方便,白天没有太多时间充电,所以要求尽量做到晚上充满电后能跑一天,因此其从七八米到12米的车电量都相对较高。
南京金龙为其提供的车辆在去年年底投运,其中8.5米车投运967辆,7.6米和6.8米一共投运832辆。
NJL6806BEVG10:8米车型可以兼做商用,当天展示的是公交版,由于其造型与普通公交有一些差异,对外观要求高的客户会选择这种产品。
新能源汽车动力电池包的组成

新能源汽车动力电池包的组成
新能源汽车动力电池包一般由以下几个主要组成部分构成:
1. 电池单体:电池单体是动力电池包的基本组成单元,是多个电池模块串联组成电池包的基础。
电池单体一般由正负极材料、电解质和隔膜等组成。
2. 电池管理系统(BMS):电池管理系统是电池包的主控制
系统,负责监控电池单体的电压、温度、电流等状态,并进行数据采集、处理和控制。
BMS还能对电池包进行故障检测和
故障管理,从而确保电池包的安全性和性能。
3. 散热系统:新能源汽车动力电池包工作过程中会产生大量的热量,如果不能及时散热,会影响电池的寿命和性能。
因此,电池包通常还配备有散热系统,包括散热片、散热管路、冷却液等,以保持电池温度的稳定。
4. 结构支持和保护:电池包需要具备一定的结构强度和稳定性,以保护电池单体免受外界环境的影响和机械振动的冲击。
常见的结构支持和保护装置包括外壳、挡板、防护板等。
5. 充电和放电接口:电池包需要通过充电接口与外部电源相连接,以进行电池充电。
同时,电池包内部还需要提供放电接口,连接到动力系统,以将电能输出给电动机供动力使用。
总而言之,新能源汽车动力电池包的组成包括电池单体、电池管理系统、散热系统、结构支持和保护以及充放电接口等多个
组成部分。
这些部分相互配合,形成一个功能完整的电池系统,为电动汽车提供动力供应。
新能源汽车高压电气系统的组成

新能源汽车高压电气系统的组成随着人们对环保和能源问题的日益关注,新能源汽车作为一种清洁能源车型,正逐渐受到用户的青睐。
在新能源汽车中,高压电气系统是其重要组成部分之一,起着至关重要的作用。
本文将从以下几个方面对新能源汽车高压电气系统的组成进行详细介绍。
一、动力电池组动力电池组是新能源汽车高压电气系统的核心部分,它提供了整车的动力来源。
动力电池组一般由若干个电池单体组成,这些电池单体经过合理的组合和连接,形成了一个能够提供电能的整体组件。
动力电池组的性能和稳定性直接影响着新能源汽车的续航里程和动力输出。
二、高压电池管理系统(BMS)高压电池管理系统是对动力电池组进行监控和管理的关键部件。
其主要功能包括对电池的充放电管理、温度控制、电池状态估计、安全保护等。
通过高压电池管理系统,可以对动力电池组的工作状态进行实时监测和调节,保证动力电池组的安全可靠运行。
三、高压直流-直流变换器(DC-DC)高压直流-直流变换器用于将动力电池组输出的高压直流电转换为低压直流电,以供给车载12V电网和低压电子设备使用。
在新能源汽车中,12V电网主要用于驱动车辆的辅助系统,如灯光、空调等,高压直流-直流变换器的性能直接影响着这些设备的正常工作。
四、电动汽车控制器(EVCU)电动汽车控制器是新能源汽车中用于控制电动驱动系统的关键部件。
它可以根据驾驶员的操作和车辆状态实时调节电动机的输出功率和扭矩,从而实现车辆的动力控制和能量回收。
电动汽车控制器在保证车辆动力性能的也需要对高压电气系统进行监控和保护。
五、高压关断器和保险在新能源汽车高压电气系统中,为了保证车辆的安全可靠运行,通常会设置高压关断器和保险装置。
高压关断器可以在车辆发生故障或事故时切断动力电池组与电动机之间的连接,起到保护车辆和乘客的作用。
而保险装置则可以在高压电气系统发生短路或过载时,及时切断电路,防止事故的发生。
六、高压电气系统的散热和隔离由于新能源汽车高压电气系统在运行过程中会产生较多的热量,并且有着较高的安全风险,因此在系统设计中需设计有效的散热系统和隔离措施。
汽车bms的名词解释
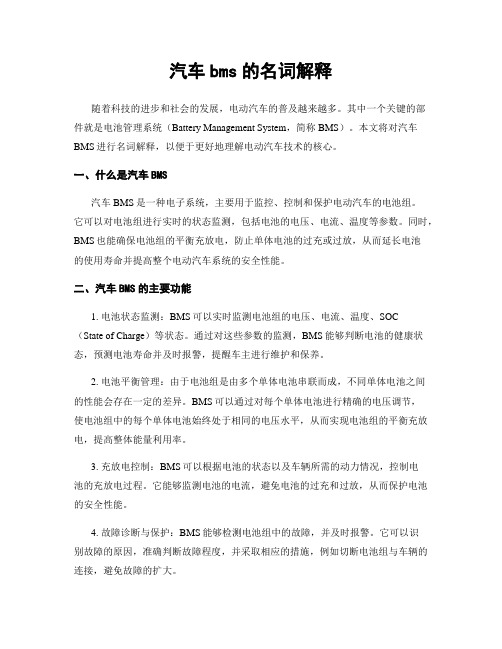
汽车bms的名词解释随着科技的进步和社会的发展,电动汽车的普及越来越多。
其中一个关键的部件就是电池管理系统(Battery Management System,简称BMS)。
本文将对汽车BMS进行名词解释,以便于更好地理解电动汽车技术的核心。
一、什么是汽车BMS汽车BMS是一种电子系统,主要用于监控、控制和保护电动汽车的电池组。
它可以对电池组进行实时的状态监测,包括电池的电压、电流、温度等参数。
同时,BMS也能确保电池组的平衡充放电,防止单体电池的过充或过放,从而延长电池的使用寿命并提高整个电动汽车系统的安全性能。
二、汽车BMS的主要功能1. 电池状态监测:BMS可以实时监测电池组的电压、电流、温度、SOC(State of Charge)等状态。
通过对这些参数的监测,BMS能够判断电池的健康状态,预测电池寿命并及时报警,提醒车主进行维护和保养。
2. 电池平衡管理:由于电池组是由多个单体电池串联而成,不同单体电池之间的性能会存在一定的差异。
BMS可以通过对每个单体电池进行精确的电压调节,使电池组中的每个单体电池始终处于相同的电压水平,从而实现电池组的平衡充放电,提高整体能量利用率。
3. 充放电控制:BMS可以根据电池的状态以及车辆所需的动力情况,控制电池的充放电过程。
它能够监测电池的电流,避免电池的过充和过放,从而保护电池的安全性能。
4. 故障诊断与保护:BMS能够检测电池组中的故障,并及时报警。
它可以识别故障的原因,准确判断故障程度,并采取相应的措施,例如切断电池组与车辆的连接,避免故障的扩大。
5. 温度管理:电池的工作温度是影响电池性能和寿命的重要因素。
BMS可以监测电池的温度变化,并根据实时数据进行控制。
它可以通过将电池组与散热系统连接,实现散热和温度控制,保证电池组在合适的温度范围内运行。
三、汽车BMS的重要性汽车BMS在电动汽车中的作用不可忽视。
它承担着监测、控制和保护电池组的重要任务。
新能源汽车总体构造部件的名称及其作用安装位置

电池系统电池组:存储电能,并提供给电动机驱动汽车;根据不同车型,电池组可能由多个电池模块组成。
电池管理系统(BMS):监测和调节电池组的状态,以确保电池组的安全和优化效能。
电驱动系统电机:负责将电能转换为机械能,驱动车轮转动。
逆变器:将电池输出的直流电转换为交流电,以提供给电机使用。
电控器:调节电池输出电流和电压的控制器,确保电动机的安全和高效运行。
充电系统充电口:连接外部充电设施和电池组,用于将电池充满电。
充电器:将外部提供的交流或直流电源转换为适合电池组的电压和电流,进行充电。
充电线束:连接充电器、电池、电机以及控制系统,管理电能的流动。
底盘系统轮胎和悬挂系统:提供对路面的缓冲和稳定性。
刹车系统:由制动盘、刹车片、刹车钳组成,转换车辆内部能量为热能并停止车辆。
转向系统:由转向机构、传动轴、万向节等组成,实现车辆的转向操作。
车身结构框架/车身结构:整车的主体骨架,支撑车身其他部分。
门/窗:车身进出口,以及通风、观察等作用。
灯光系统:前/后灯、转向灯、雾灯、照明灯等,用于行车安全和人员及车辆能见度。
安全系统气囊系统:安装在散热器内部、车门、座位等位置,以防止碰撞时乘客受伤。
防抱死刹车系统(ABS):使用电控制,避免轮胎在紧急制动时阻塞,增加车辆行驶的稳定性。
车身稳定控制系统(ESP):在车辆行驶中,通过传感器读取车辆的转向状态,进行刹车或驱动控制,保证车辆行驶的稳定性。
以下是新能源汽车主要部件的安装位置:电池系统电池组:根据不同车型,主要安装的位置有:车身下方、后备箱、车门等。
电池管理系统(BMS):主要安装在电动车的电控箱中。
电驱动系统电机:一般安装在车轮轴或者变速器上的位置。
逆变器:一般安装在电动车的电控箱中。
电控器:一般安装在电动车的电控箱中。
充电系统充电口:一般安装在车辆侧面、前脸等位置。
充电器:一般安装在电动车的电控箱中。
充电线束:一般安装在车身底部或者车架内部。
底盘系统轮胎和悬挂系统:安装在车轮下方的部位。
bms汽车名词解释
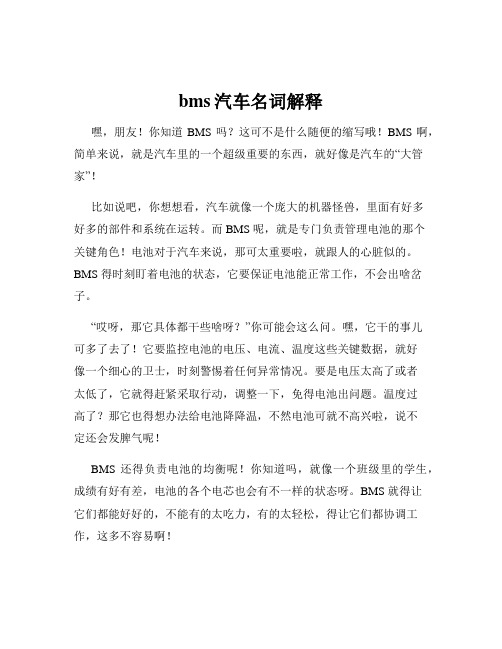
bms汽车名词解释
嘿,朋友!你知道 BMS 吗?这可不是什么随便的缩写哦!BMS 啊,简单来说,就是汽车里的一个超级重要的东西,就好像是汽车的“大管家”!
比如说吧,你想想看,汽车就像一个庞大的机器怪兽,里面有好多
好多的部件和系统在运转。
而 BMS 呢,就是专门负责管理电池的那个
关键角色!电池对于汽车来说,那可太重要啦,就跟人的心脏似的。
BMS 得时刻盯着电池的状态,它要保证电池能正常工作,不会出啥岔子。
“哎呀,那它具体都干些啥呀?”你可能会这么问。
嘿,它干的事儿
可多了去了!它要监控电池的电压、电流、温度这些关键数据,就好
像一个细心的卫士,时刻警惕着任何异常情况。
要是电压太高了或者
太低了,它就得赶紧采取行动,调整一下,免得电池出问题。
温度过
高了?那它也得想办法给电池降降温,不然电池可就不高兴啦,说不
定还会发脾气呢!
BMS 还得负责电池的均衡呢!你知道吗,就像一个班级里的学生,成绩有好有差,电池的各个电芯也会有不一样的状态呀。
BMS 就得让
它们都能好好的,不能有的太吃力,有的太轻松,得让它们都协调工作,这多不容易啊!
“哇,原来 BMS 这么厉害啊!”你肯定会这么感叹。
可不是嘛!没
有 BMS 的精心照料,汽车的电池可没法好好工作,那汽车还怎么跑起
来呀!所以说啊,BMS 真的是汽车里不可或缺的一部分,就像我们生
活中离不开那些默默付出的人一样!
我觉得 BMS 就是汽车的无名英雄,虽然我们平时可能不太会注意
到它,但它却一直在背后默默地为我们的出行保驾护航!这就是BMS,汽车的重要伙伴!。
新能源汽车BMS系统结构及关键技术解析
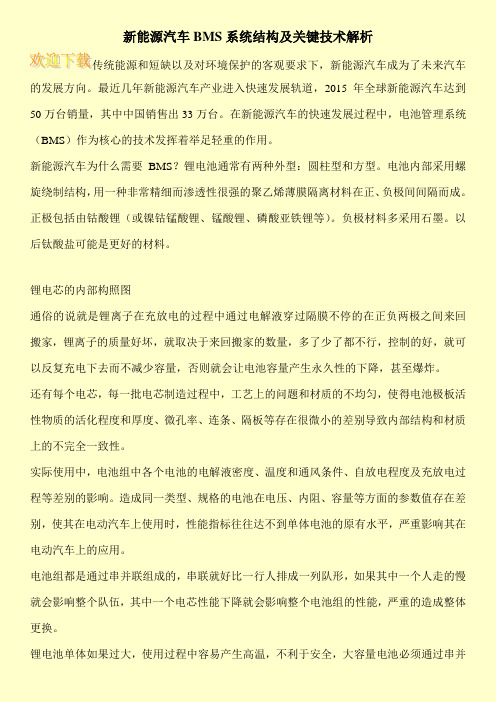
新能源汽车BMS系统结构及关键技术解析传统能源和短缺以及对环境保护的客观要求下,新能源汽车成为了未来汽车的发展方向。
最近几年新能源汽车产业进入快速发展轨道,2015年全球新能源汽车达到50万台销量,其中中国销售出33万台。
在新能源汽车的快速发展过程中,电池管理系统(BMS)作为核心的技术发挥着举足轻重的作用。
新能源汽车为什么需要BMS?锂电池通常有两种外型:圆柱型和方型。
电池内部采用螺旋绕制结构,用一种非常精细而渗透性很强的聚乙烯薄膜隔离材料在正、负极间间隔而成。
正极包括由钴酸锂(或镍钴锰酸锂、锰酸锂、磷酸亚铁锂等)。
负极材料多采用石墨。
以后钛酸盐可能是更好的材料。
锂电芯的内部构照图通俗的说就是锂离子在充放电的过程中通过电解液穿过隔膜不停的在正负两极之间来回搬家,锂离子的质量好坏,就取决于来回搬家的数量,多了少了都不行,控制的好,就可以反复充电下去而不减少容量,否则就会让电池容量产生永久性的下降,甚至爆炸。
还有每个电芯,每一批电芯制造过程中,工艺上的问题和材质的不均匀,使得电池极板活性物质的活化程度和厚度、微孔率、连条、隔板等存在很微小的差别导致内部结构和材质上的不完全一致性。
实际使用中,电池组中各个电池的电解液密度、温度和通风条件、自放电程度及充放电过程等差别的影响。
造成同一类型、规格的电池在电压、内阻、容量等方面的参数值存在差别,使其在电动汽车上使用时,性能指标往往达不到单体电池的原有水平,严重影响其在电动汽车上的应用。
电池组都是通过串并联组成的,串联就好比一行人排成一列队形,如果其中一个人走的慢就会影响整个队伍,其中一个电芯性能下降就会影响整个电池组的性能,严重的造成整体更换。
锂电池单体如果过大,使用过程中容易产生高温,不利于安全,大容量电池必须通过串并。
电动汽车bms工作原理
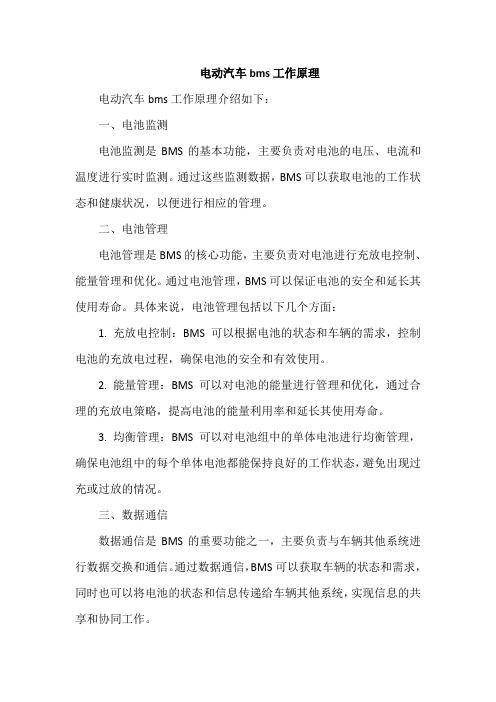
电动汽车bms工作原理
电动汽车bms工作原理介绍如下:
一、电池监测
电池监测是BMS的基本功能,主要负责对电池的电压、电流和温度进行实时监测。
通过这些监测数据,BMS可以获取电池的工作状态和健康状况,以便进行相应的管理。
二、电池管理
电池管理是BMS的核心功能,主要负责对电池进行充放电控制、能量管理和优化。
通过电池管理,BMS可以保证电池的安全和延长其使用寿命。
具体来说,电池管理包括以下几个方面:
1. 充放电控制:BMS可以根据电池的状态和车辆的需求,控制电池的充放电过程,确保电池的安全和有效使用。
2. 能量管理:BMS可以对电池的能量进行管理和优化,通过合理的充放电策略,提高电池的能量利用率和延长其使用寿命。
3. 均衡管理:BMS可以对电池组中的单体电池进行均衡管理,确保电池组中的每个单体电池都能保持良好的工作状态,避免出现过充或过放的情况。
三、数据通信
数据通信是BMS的重要功能之一,主要负责与车辆其他系统进行数据交换和通信。
通过数据通信,BMS可以获取车辆的状态和需求,同时也可以将电池的状态和信息传递给车辆其他系统,实现信息的共享和协同工作。
四、安全保护
安全保护是BMS的最基本要求,主要负责对电池进行过流、过压、欠压、过温等保护。
通过这些保护措施,BMS可以确保电池的安全和可靠性,防止因电池故障而导致的事故发生。
五、故障诊断
故障诊断是BMS的重要功能之一,主要负责对电池的故障进行诊断和定位。
通过故障诊断,BMS可以及时发现电池的异常和故障,并采取相应的处理措施,确保电池的安全和可靠性。
同时,故障诊断也可以为后续的维护和保养提供参考和依据。
新能源汽车动力蓄电池系统构造与检修主要内容与要求(一)

新能源汽车动力蓄电池系统构造与检修主要内容与要求(一)新能源汽车动力蓄电池系统构造与检修主要内容与要求构造要求•高能量密度:新能源汽车动力蓄电池系统应具备高能量密度,以提供足够的电能续航里程。
•高功率密度:系统需要具备高功率密度,以满足车辆瞬时高功率输出的需求。
•优化的体积与重量:蓄电池系统应在保证功率与能量密度的前提下,尽可能减小体积和重量,以提高整车的运行效率。
•高安全性:系统必须具备良好的安全性能,包括防火防爆、高温切断、过充过放保护等功能。
•长寿命:系统应具备长寿命特性,以提高整体经济性。
主要内容1.电芯:动力蓄电池系统的基本组成单元,通常由多个电芯组合而成。
电芯应具备高能量密度和高功率密度,并具备长寿命特性。
例如,锂离子电池是目前主流的电芯类型,其高能量密度和长寿命性能适用于新能源汽车动力蓄电池系统。
2.电池管理系统(BMS):BMS是对电池系统进行管理和控制的核心部件。
其主要功能包括电芯均衡、温度控制、充放电控制、故障诊断等。
例如,BMS可监测电池组中每个电芯的电压和温度,对其进行均衡,以确保各个电芯之间的状态一致性。
3.冷却系统:动力蓄电池系统在工作过程中会产生大量的热量,冷却系统用于散热,以保持电池组的温度在安全范围内。
例如,冷却系统可以采用液冷或气冷方式,通过循环流体或风扇将热量带走。
4.电池箱和绝缘材料:电池箱是安装电芯的外部结构,应具备较高的强度和耐腐蚀性。
绝缘材料用于隔离电池箱和电芯,以防止电池短路和其他安全问题的发生。
示例解释以一款新能源汽车的电池系统为例,该车采用锂离子电池作为动力蓄电池系统,满足高能量密度和长寿命的要求。
电芯由多个锂离子电池组成,通过BMS进行管理和控制,实现电芯均衡、温度控制等功能。
车辆配备冷却系统,通过液冷方式散热,保持电池组的温度在安全范围内。
电池箱采用高强度材料制造,配备绝缘材料进行隔离,以提高安全性能。
以上是新能源汽车动力蓄电池系统构造与检修的主要内容与要求。
新能源电动汽车的内部结构功能分析
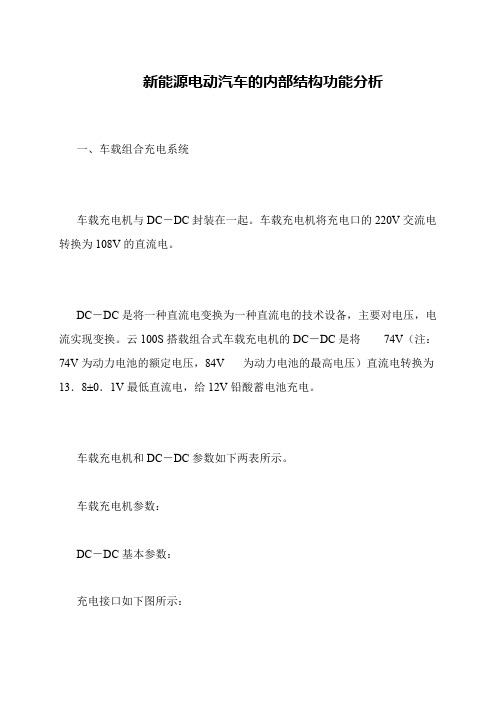
到 ON 档,分电盒总正接触器吸合,动力电池 74V 两相直流电进入驱动电机 控制器。驱动电机控制器先将两相直流电转换三相直流电,再结合档位、油 门模拟量等控制信号控制输出到驱动电机的电流,从而实现对车辆驱动系统 的管理。
机的转速及转向,从而驱动电动汽车的行驶。 3.减速器 减速器是将电机的高速运转通过齿轮传动变成低速大扭矩的装置。他不同 于传统汽油车的变速箱,减速器只有固定减速比,没有调速功能,速度以及 方向的变化是通过电机控制器来实现。减速器的固定减速比为:7.3。 4.驱动电机参数 5.驱动电机控制器与参数 MC3336 系列低压交流控制器是一款应用于低压交流电动车辆的驱动器, 采用了国内外一流的交流电机控制器算法,实现了对交流电机宽调速范围内 转矩的精准控制。相比于直流电机驱动系统,交流驱动系统可以实现更宽的 电机调速范围,从而提高了车辆的行驶速度;交流电机无碳刷、全密闭、免 维护,系统可靠性大大提高:交流系统能达到更高的效率,实现灵活的能量 回馈控制,从而有效地提升续航里程。 驱动电机控制器通过 35 芯插接件,将驱动电机、启动开关、仪表、档位 开关、油门信号、刹车信号等联系起来,从而使车辆有序的进行。 启动钥匙
新能源电动汽车的内部结构功能分析
一、车载组合充电系统 车载充电机与 DC-DC 封装在一起。车载充电机将充电口的 220V 交流电 转换为 108V 的直流电。 DC-DC 是将一种直流电变换为一种直流电的技术设备,主要对电压,电 流实现变换。云 100S 搭载组合式车载充电机的 DC-DC 是将 74V(注: 74V 为动力电池的额定电压,84V 为动力电池的最高电压)直流电转换为 13.8±0.1V 最低直流电,给 12V 铅酸蓄电池充电。 车载充电机和 DC-DC 参数如下两表所示。 车载充电机参数: DC-DC 基本参数: 充电接口如下图所示:
- 1、下载文档前请自行甄别文档内容的完整性,平台不提供额外的编辑、内容补充、找答案等附加服务。
- 2、"仅部分预览"的文档,不可在线预览部分如存在完整性等问题,可反馈申请退款(可完整预览的文档不适用该条件!)。
- 3、如文档侵犯您的权益,请联系客服反馈,我们会尽快为您处理(人工客服工作时间:9:00-18:30)。
工程师:新能源大巴BMS结构与乘用车的区别
这篇文章主要介绍新能源大巴的电池和BMS的结构与乘用车的区别,这里是从一个乘用车工程师的角度来看的。
本文主要分三个部分,新能源大巴行业、新能源电池系统结构和新能源大巴的BMS系统,抛砖引玉欢迎各位拍砖。
第一部分新能源大巴行业
其实数数全球的商用车(大巴+卡车),大致的方向还是沿着就有的习惯做HEV,国内总体而言,是以纯电动+PHEV为主的。
这里的主要原因,还是欧美日在发动机和变速箱方面的积累,如果按照国内的纯电动大巴模式,配置300kwh以上的,很大的价值都给电池给占去了。
·商用巴士:New Flyer、Thomas、Navistar/IC、Volvo、Hino、Smith、GM、Daimler、TOYOTA和MitsubishiFuso。
·卡车 Smith、Volvo、Navistar、Daimler、TOYOTA、Hino、ISUZU、Iveco、PACCAR、Azure Dynamics、Daihatsu、Nissan和Mitsubishi Fuso。
图1和图2的数据制图,是参考了《Key Factors of the Power Battery Development in 2013:E-Motorcycle & EV》一文里面的数据。
图1 美国和日本新能源大巴的情况
图2 除中国外新能源商用车电池供给情况
与之相比,国内的情况是根据补贴来的,有了较大的单位的每度电补贴以后,做纯电动这种形式就变得更有利了。
所以总体来说,对于商用车的以每度电补贴,完全扭转了整个技术路线,直接把国内所有做大巴的企业将HEV砍掉(这事就是发生在2013和2014的时候,现在已经回不过去了),转到BEV和配置较高的电池的PHEV的形式上来了。
图 3 2014年中国商用车销售情况
更有趣的是,通过配置电池,将电动里程零耗油的部分换算进去,就可以把整个驱动系统的效率的差异打掉,所以对比国外的技术水平,我们的PHEV一下子把老师傅给超过去了。
这个有点类似文字游戏,是通过加多了钱(国家补贴和地方补贴)配置多的电池的代价换来的。
从运营公司的角度来看,用电还是省钱,所以出现某地一天充五次插电式大巴的故事发生了。
图4 商用车的油耗水平
第二部分新能源大巴电池系统架构
我们这里使用A123&万向的例子来看这个系统架构,我们来对比两个案子美国的Navistar和上汽万向的纯电动大巴,他们都是拿着A123的模组来,按照A123的基本成组模式。
1) 上汽和万向合资纯电动大巴
图5包括模组成组,电池包布置还有系统框图,其中模组(含BMU)这一级,基本是电池厂出来各个产品(大车、小车)都能用了。
整个从单体=》模组=》电池包,然后在车顶和车位来配置两大块。
图5 上汽万向纯电动大巴
2) Navistar的HEV电池包
欧洲和美国也用了不少A123的电池系统(基础是20Ah的电芯),整个结构是非常类似的。
如图6所示,采取单体串联=》模组并联=》再串联的电池构成的模式来获取大的容量。
图6 Navistar的HEV大巴
总体来说,纯电大巴的电池系统结构,大体根据结构工程师来布置,分成4~8个包;HEV+PHEV的包呢,分的数量少一些都包在一起。
区别的地方在于,如比亚迪和CATL(这两家)采取的是较大的单体,先串联然后总的进行并联配置,如比亚迪的系统设计。
三组电池包并联,标准输出电压直流540V,组内电池模组串联,每组电池包21个模组,每个模组内含有8个单体电池(标准电压3.3V),模组的电压为26.67V。
在K9的布置中,采取前桥承载1个电池包,后桥左右各承载一个电池包,整车高压线束通过左风道、车内电子路牌和右侧尾部立柱的模式,由于采取这种模式,比亚迪需要在每个电池包内进行配电管理,考虑主正、主负和预充继电器,每个电池包内需要一个BMS主控进行独立核算。
图7 比亚迪系统的设计
CATL的纯电动巴士通用电池箱230/320KWH,电芯:200Ah LFP(多层卷绕方形铝壳),模组为2P3S 或 3P2S,电池箱(铝压铸)为2P18S 或 3P12S(6个模组),电箱参数:
57.6V/23kWh 或 38.4V/23kWh;其中230kWh电池系统由10个2P18S电池箱串联,320kWh 电池系统由14个3P12S电池箱串联。
图8 CATL的系统设计
图9,是以前在分析五洲龙和沃特玛电池时候画的,算是比较典型的系统架构图,这里拿来作为完全串联的一种架构模式。
图9 沃特玛五洲龙的系统设计
所有大的新能源大巴这里的几个问题其实是普遍存在的:
1)单体确实比较大,采用LFP还是必由之路,否则200Ah的电芯,内层发热散热问题较大
2)电池包分别布置在多个区域,导致区域内的各种环境条件(温度、振动),整个电池组内的温差,按照实际的情况在10度以上
3)单个包,配置BMU或者继电器之后,本身的安全性需要独立设计核算,内部加继电器的,BMU的控制权限需要提升,整个分布式控制系统的低压控制线和通信线所受的回路比较大
4)电池模组的堆叠,机械应力上差异也比较大,把模组堆在模组上,其实不是好好的主意。
第三部分新能源大巴的BMS
新能源大巴几乎都是采用,分布式管理系统(电池管理系统+多个温度电压测量单元方式)将电池模组的功能独立分离,整个系统形成了单体电压和温度测量均衡单元、电池管理控制器、继电器控制器和整车控制器,三层两个网络的形式。
这里主要考虑的问题还是基于模块化的考虑,生产和组装分离,在装车的时候进行网络配置。
如果单从BMS的角度来看,大巴车的BMS系统与乘用车的主要有以下的差异:
1) 由于大巴车辆的电源系统是基于24V系统,所以对于BMS来说里面需要考虑的供电问题。
a. 电源系统的特别是抑制这块需要单独设计,由于BMS的电源部分需要用个Buck电路来替代LDO,如图10所示,24V系统的考量还是需要在电源上做更多处理,否则脉冲抑制不住会烧毁器件。
b. 由于24V系统的原因,配置DC-DC是必须的,BMS的计算量偏大,总线频率和电流量就大一些,这里一般配置2路Buck拓扑的DC-DC给电源供电。
c.BMU的供电也是一个大问题了,所以BMU的内部架构,往往是只能将MCU、测量和备份芯片从模组取电,否则需要在BMS里面构建一个24V配电盒的功能,加些熔丝在里面了。
d. 由于大巴的24V电池容量高一些,对于漏电流方面的管理需要弱化一些。
图10 BMS电源系统架构
图11 12V和24V电源抑制
2) CAN通信的脉冲抑制,同上由于线束的布置问题,CAN上面的串扰不是一点点大,导致原有的设计需要更改。
a. BMS在这里一般有三路CAN电路,分诊断CAN、与整车控制器通信CAN和BMU的CAN,由于电池包的分散布置,使得整个BMS和BMU之间CAN的环路太长,耦合进来的东西会比较多
b. 由于某些部件,比如电动压缩机、电机控制器,本身控制板上的CAN线耦合了很多的东西,使得BMS外部收到的干扰也很多,所以实际沟通下来的情况,就是通信电路和错误帧非常多
图12 乘用车CAN通信电路
3) 单体均衡,由于电动大巴容量(1个就是200Ah,还有2P和3P的)很大,很多公司用了加大的被动均衡或者主动均衡电路,这块区别也比较大,所以看到有公司给大的均衡电阻配置独立的散热器的。
所以未来如果发展的方向是大容量的电池,像比亚迪这样提高母线的电压,将压力从单体容量上转移给逆变器和电机,就是IGBT上还是靠谱的
4) 由于大巴的电源波动,某些公司甚至独立配了个12V备份电源独立给电池包内配置一个供电系统,所以一般BMU和BMS之间只有CAN线和报警线之间的关系了,这里补一个安全气囊的PWM报警输出口的电路,我个人觉得其实BMU和BMS之间在未来需要有一个额外的通信备份接口,用PWM定义确实比较合适,在图里面把Collision改成单体过压和模组过压的报警就可以直接使用了
图13 PWM报警接口定义参考
这块内容,主要还是根据和汽车电子俱乐部的相关工程师一起交流和总结的内容,实际的情况比这个更复杂一些。
由于大巴企业的BMS供应商普遍仅仅参考《QCT 897-2011 电动汽车用电池管理系统技术条件》这份行业标准来做产品,整个BMS产品的水平就很值得商榷了。
如果仔细对比整个细节的参数和样品验证的数量,其实和GBT 28046-2011 道路车辆电气及电子设备的环境条件和试验(1~5)之间都有很大的差距。
图14 QCT897-2011内技术要求
本文小结
我个人是觉得,未来纯电大巴可能形成三个分布式BMS系统,独立算三个堆的参数模式,汇总到VCU这块可能更好一些。
不过更有可能的是(2020年以后),随着补贴的退坡,整个商用车的购置从补贴模式向市场化模式转变,大部分的系统还是回到插电式+超级电容,在沿线做快速补电的模式。