液晶电视外壳快速热循环注塑成型翘曲变形优化
电视机外壳热流道讲解不同型号的热流道变色
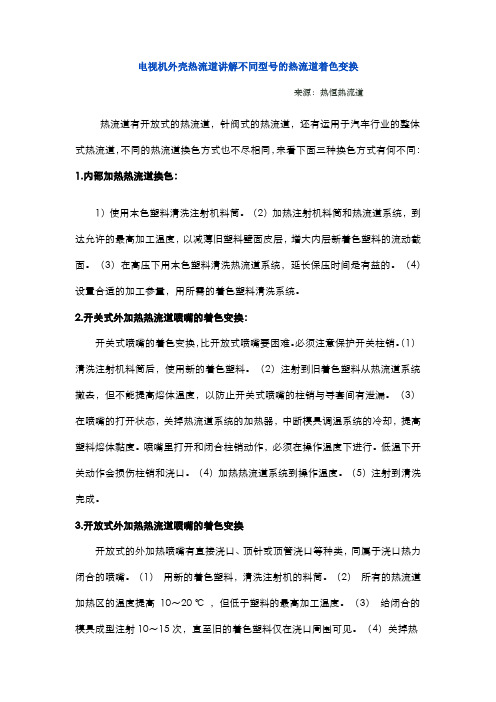
电视机外壳热流道讲解不同型号的热流道着色变换来源:热恒热流道热流道有开放式的热流道,针阀式的热流道,还有运用于汽车行业的整体式热流道,不同的热流道换色方式也不尽相同,来看下面三种换色方式有何不同:1.内部加热热流道换色:1)使用本色塑料清洗注射机料筒。
(2)加热注射机料筒和热流道系统,到达允许的最高加工温度,以减薄旧塑料壁面皮层,增大内层新着色塑料的流动截面。
(3)在高压下用本色塑料清洗热流道系统,延长保压时间是有益的。
(4)设置合适的加工参量,用所需的着色塑料清洗系统。
2.开关式外加热热流道喷嘴的着色变换:开关式喷嘴的着色变换,比开放式喷嘴要困难。
必须注意保护开关柱销。
(1)清洗注射机料筒后,使用新的着色塑料。
(2)注射到旧着色塑料从热流道系统撤去,但不能提高熔体温度,以防止开关式喷嘴的柱销与导套间有泄漏。
(3)在喷嘴的打开状态,关掉热流道系统的加热器,中断模具调温系统的冷却,提高塑料熔体黏度。
喷嘴里打开和闭合柱销动作,必须在操作温度下进行。
低温下开关动作会损伤柱销和浇口。
(4)加热热流道系统到操作温度。
(5)注射到清洗完成。
3.开放式外加热热流道喷嘴的着色变换开放式的外加热喷嘴有直接浇口、顶针或顶管浇口等种类,同属于浇口热力闭合的喷嘴。
(1)用新的着色塑料,清洗注射机的料筒。
(2)所有的热流道加热区的温度提高10~20 ℃ ,但低于塑料的最高加工温度。
(3)给闭合的模具成型注射10~15次,直至旧的着色塑料仅在浇口周围可见。
(4)关掉热流道系统的加热器,并中断模具调温系统的冷却。
让塑料熔体在流道壁上冷凝成高黏度的半固化物。
在重新注射时,新与旧的熔体容易混合。
(5)加热热流道系统到操作温度。
(6)以高的注射速率注射,直到获得均匀的着色。
壳盖注塑件模具结构优化设计及翘曲优化

时间、熔体温度和冷却时间。
关键词:优化设计;翘曲值;正交试验;工艺参数
中图分类号:TQ320.66
文献标识码:A
文章编号:1009-0134(2019)06-0110-04
0 引言
当塑料件与其他零件有配合关系时,为了保证配合 的精度,对产品的翘曲有很高的要求。塑料制品成型过 程是一个动态的多因素非线性耦合的过程,该过程中各 个因素的变动都对产品的质量产生一定的影响。在生产 塑料件的模具结构中,浇注系统和冷却系统直接影响着 产品的质量,因此能够设计出合理的浇注和冷却系统成 为产品质量的基础保证[1]。在确定模具结构后,设计合 理的工艺参数是进一步提高产品质量的方法。传统的设 计方法很难解决这些问题,CAE技术则可在模具制造前 对模具设计方案和注塑成型工艺参数进行模拟分析,从 而预测出产品可能存在的缺陷,避免了传统的模具制造 完后在注塑机上反复试模和修模的困境[2]。
2.2 冷却系统优化设计
冷却系统设计直接影响着塑料产品的生产效率和产 品质量,因此,设计合理的冷却系统具有极其重要的意 义。在冷却系统中,管道数量、管道直径、管道与制品 的距离、管道中心距以及排列方式等直接影响着冷却系 统的冷却效果。为了得到相对合理的冷却系统,通过采 用控制变量法,把多因素问题转变成单因素问题。每次 改变其中一个因素,而控制其余几个因素不变,以此研 究被改变因素对研究对象的影响大小。本项目共设计了 九种不同的冷却方案,具体方案如下:管道数从两条、 四条、六条和八条进行布置;管道直径设计了10mm和 12mm;管道与制品距离设计了25mm和20mm;管道中 心距从50mm、30mm到15mm进行布置,排列方式设计 了Y向和X向。具体参数如表2所示。
方案1 方案2 方案3 方案4 方案5
塑料制品的翘曲变形的原因分析和解决方法图文稿
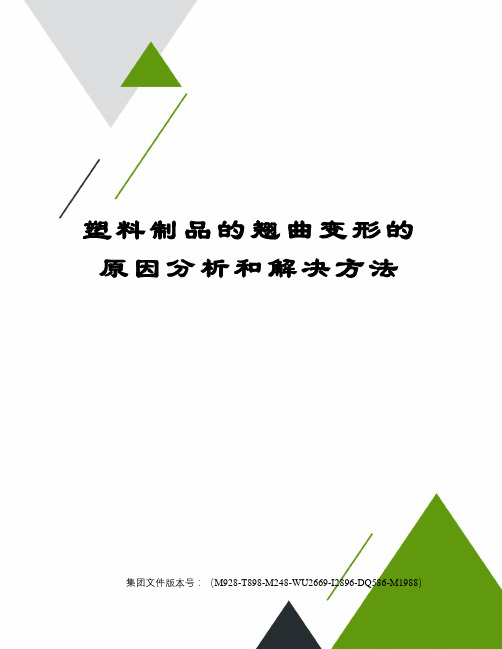
塑料制品的翘曲变形的原因分析和解决方法集团文件版本号:(M928-T898-M248-WU2669-I2896-DQ586-M1988)塑料制品的翘曲变形的原因分析和解决方法一、前言翘曲变形是指注塑制品的形状偏离了模具型腔的形状,它是塑料制品常见的缺陷之一。
出现翘曲变形的原因很多,单靠工艺参数解决往往力不从心。
结合相关资料和实际工作经验,下面对影响注塑制品翘曲变形的因素作简要分析。
二、模具的结构对注塑制品翘曲变形的影响。
在模具方面,影响塑件变形的因素主要有浇注系统、冷却系统与顶出系统等。
1.浇注系统注塑模具浇口的位置、形式和浇口的数量将影响塑料在模具型腔内的填充状态,从而导致塑件产生变形。
流动距离越长,由冻结层与中心流动层之间流动和补缩引起的内应力越大;反之,流动距离越短,从浇口到制件流动末端的流动时间越短,充模时冻结层厚度减薄,内应力降低,翘曲变形也会因此大为减少。
一些平板形塑件,如果只使用一个中心浇口,因直径方向上的收缩率大于圆周方向上的收缩率,成型后的塑件会产生扭曲变形;若改用多个点浇口或薄膜型浇口,则可有效地防止翘曲变形。
当采用点浇口进行成型时,同样由于塑料收缩的异向性,浇口的位置、数量都对塑件的变形程度有很大的影响。
另外,多浇口的使用还能使塑料的流动比(L/t)缩短,从而使模腔内熔体密度更趋均匀,收缩更均匀。
同时,整个塑件能在较小的注塑压力下充满。
而较小的注射压力可减少塑料的分子取向倾向,降低其内应力,因而可减少塑件的变形。
2. 冷却系统在注射过程中,塑件冷却速度的不均匀也将形成塑件收缩的不均匀,这种收缩差别导致弯曲力矩的产生而使塑件发生翘曲。
如果在注射成型平板形塑件(如手机电池壳)时所用的模具型腔、型芯的温度相差过大,由于贴近冷模腔面的熔体很快冷却下来,而贴近热模腔面的料层则会继续收缩,收缩的不均匀将使塑件翘曲。
因此,注塑模的冷却应当注意型腔、型芯的温度趋于平衡,两者的温差不能太大(此时可考虑使用两个模温机)。
翘曲变形原因
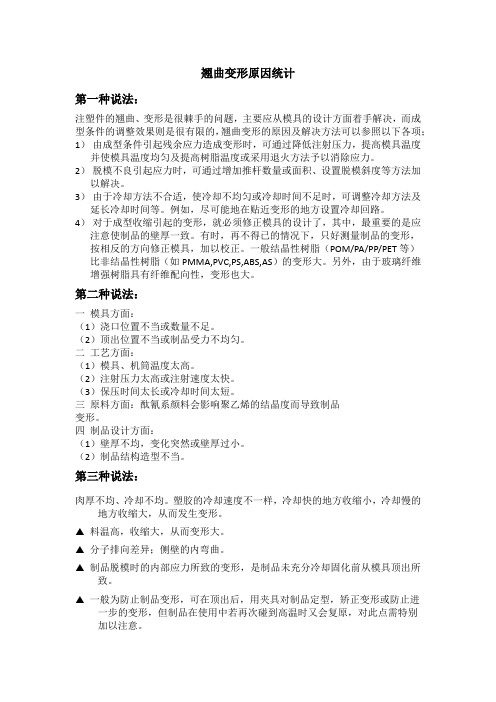
翘曲变形原因统计第一种说法:注塑件的翘曲、变形是很棘手的问题,主要应从模具的设计方面着手解决,而成型条件的调整效果则是很有限的,翘曲变形的原因及解决方法可以参照以下各项;1)由成型条件引起残余应力造成变形时,可通过降低注射压力,提高模具温度并使模具温度均匀及提高树脂温度或采用退火方法予以消除应力。
2)脱模不良引起应力时,可通过增加推杆数量或面积、设置脱模斜度等方法加以解决。
3)由于冷却方法不合适,使冷却不均匀或冷却时间不足时,可调整冷却方法及延长冷却时间等。
例如,尽可能地在贴近变形的地方设置冷却回路。
4)对于成型收缩引起的变形,就必须修正模具的设计了,其中,最重要的是应注意使制品的壁厚一致。
有时,再不得已的情况下,只好测量制品的变形,按相反的方向修正模具,加以校正。
一般结晶性树脂(POM/PA/PP/PET等)比非结晶性树脂(如PMMA,PVC,PS,ABS,AS)的变形大。
另外,由于玻璃纤维增强树脂具有纤维配向性,变形也大。
第二种说法:一模具方面:(1)浇口位置不当或数量不足。
(2)顶出位置不当或制品受力不均匀。
二工艺方面:(1)模具、机筒温度太高。
(2)注射压力太高或注射速度太快。
(3)保压时间太长或冷却时间太短。
三原料方面:酞氰系颜料会影响聚乙烯的结晶度而导致制品变形。
四制品设计方面:(1)壁厚不均,变化突然或壁厚过小。
(2)制品结构造型不当。
第三种说法:肉厚不均、冷却不均。
塑胶的冷却速度不一样,冷却快的地方收缩小,冷却慢的地方收缩大,从而发生变形。
☐料温高,收缩大,从而变形大。
☐分子排向差异;侧壁的内弯曲。
☐制品脱模时的内部应力所致的变形,是制品未充分冷却固化前从模具顶出所致。
☐一般为防止制品变形,可在顶出后,用夹具对制品定型,矫正变形或防止进一步的变形,但制品在使用中若再次碰到高温时又会复原,对此点需特别加以注意。
第四种说法:如果制件的收缩均匀,那么成型件不会发生变形或翘曲,只是单纯地变小了。
注塑件翘曲变形分析与成型工艺参数优化

Ab s t r a c t : B a s e d o n o r t h o g o n a l e x p e r i me n t d e s i g n , n u me r i c a l s i mu l a i t o n o f i n j e c t i o n mo l d i n g f o r p l a s i t c p a r t s u s i n g Mo l d l f o w
r e s e a r c h e d . T h e mu l t i p l e l i n e a r r e g r e s s i o n a n a l y s i s wa s d o n e , i t wa s f o u n d ha t t he t r e i s a v e r y g o o d c o .e l ti a o n b e t we e n p o we r f u n c t i o n r e g r e s s i o n mo d e l f o r t h e wa r p a g e o f p l a s t i c p a r t a n d e x p e r i me n t a l d a t a . T h e n he t o p t i mi z a t i o n r e g r e s s i o n mo d e l o f t h e
LCD后背板的注射成型参数正交优化设计

经验交流LCD后背板的注射成型参数正交优化设计南瑞亭1,2(1.广州市交通技师学院机电工程系 2.华南理工大学机械与汽车工程学院)摘要:针对注射成型过程中最常见的制件翘曲问题,尝试以LCD后背板为研究对象,对影响薄壳塑件翘曲变形的因素( 如模具温度、熔体温度、注射时间、保压压力、保压时间、冷却时间) 进行分析,以正交实验法找出最佳工艺参数组合,通过极差分析,确定实现低翘曲变形的最优方案为:模具温度85℃,注射时间0.6s,保压压力100%。
关键词:注射成型;工艺参数;翘曲变形;正交试验1 引言注射成型是塑料的主要加工方法之一,其生产效率高,能成型外形复杂、尺寸精确或带嵌件的注射制品;对各种塑料的加工适应性强,因此得到了广泛应用。
随着塑料注射工艺在汽车、摩托车、家用电器、仪器仪表等行业中的广泛运用,有关注射过程规律的把握、注射工艺参数优化的配置在国际上得到了广泛的重视。
而工业技术的不断发展,对注射成型塑料制品质量的要求越来越高,并且注射成型过程与一定工艺条件下高聚物的流变性能、热传导性能等密切相关,而且涉及复杂的物理动力学问题。
传统的作法是凭试模师傅,通过不断试错的方法实现参数的优化配置,这使得制件很难满足现代工业的要求。
所以,本文希望通过正交试验的极差分析得出较优的参数组合,以达到参数最优配置的目的[1~3]。
目前国际上还没有统一的对注塑件质量的评估标准,只能大致上将注射成型质量分为性能质量和表面质量。
性能质量包括制品内部组织结构形态、制品密度、制品物理力学性能、熔接痕强度以及与塑料收缩特性有关的制品尺寸和形状精度等;表面质量包括表面粗糙度及表观缺陷状况等[4,5]。
翘曲是与塑料收缩特性有关的制品变形,是当前注塑制品出现的主要缺陷之一。
翘曲主要由冷却不当、分子取向不平衡、模具浇注系统设计有缺陷、脱模系统不合理以及成型条件设置不当所引起[6]。
本文主要研究注射成型过程中常见的制品成型条件设置不当所引起的翘曲问题,以液晶显示器(Liquid Crystal Display,LCD) 后背板为实验对象,对影响薄壳塑件翘曲变形的因素( 如模具温度、熔体温度、注射时间、保压压力、保压时间、冷却时间等) 进行分析,并通过正交实验法找出最佳工艺参数组合。
注塑制品翘曲变形的优化

产生扭 曲变形 ; 若改用多个 点浇 1 3或薄膜 型浇 口, 则 可有 效地防止翘 曲变 形。当采用点浇进行成型时, 同样 由于塑料收缩的异 向性 , 浇 口的位置、 数 量都对塑件的变形程度有很大的影响。例如: 采用的是 3 0 %玻璃纤维增强 P A 6 , 而得到 的是重量为 4 . 9 5 k g的 大 型注 塑 件 , 因此 沿 四周 壁 流 动 方 向 上 设有许多加强肋 , 这样 , 对 各 个 浇 口都 能 获 得 充 分 的 平 衡 。 但 并 非 浇 口数 目
度随冷却水道长度的增加而上升, 使模 具的型腔 、 型芯沿水道产生温差。 因 此, 要求每个冷却回路的水道 长度小于 2米 。在 大型模具中应设置数条冷 却 回路 , 一条回路的进 口位于另一条 回路 的出 口附近 。 对 于长条形塑件 , 应 采用直通型水道。 我们的模具大多是采用 s型回路—— 既不利于循环 , 又延长周期 。顶 出系统 的设计也直接影响塑件的变形。如果顶出系统布置不平衡 , 将造成 顶出力的不平 : 而他塑 件变形。因此, 在设计顶出系统时应力求与脱模 阻 力相 平 衡 。 另 外 , 顶 出杆 的截 面 积 不 能 太 小 , 以防 塑 件 单 位 面 积 受 力 过 大 ( 尤 其在脱模温度太高时) 而使塑件产生变形 顶杆的布置应尽量 靠近脱模
发生翘 曲。 2 顶 出 系统 的设 计
塑化阶段即 由玻璃态料粒转化 为粘流态熔 体的过 程 ( 培训时讲过原料 塑化 的三态变化) 。 在这个过程 中, 聚合物的温度在轴 向、 径 向( 相对螺杆而 言) 温差会使 塑料产生应力 ; 另 外, 注 射 机 的注 射 压 力 、 速 率 等 参 数 会 极 大
阻 力 大 的部 位 。在 不 影 响 塑 件 质 量 ( 包括使用要求 、 尺寸精度与外观等) 的
注塑成型翘曲变形产生机理及解决办法PVC塑料网
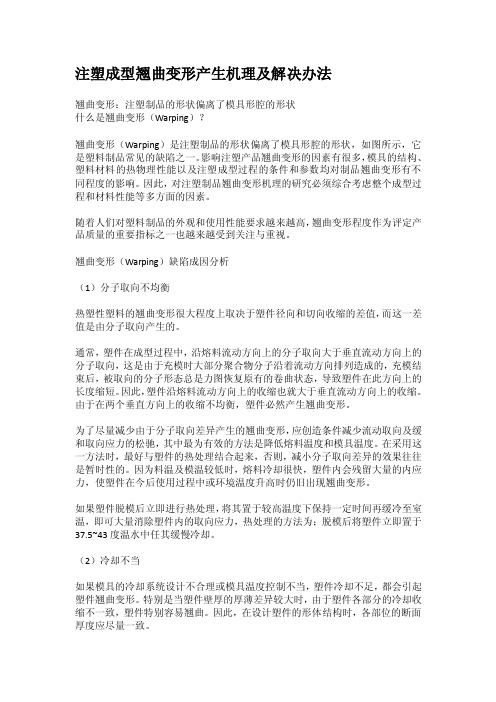
注塑成型翘曲变形产生机理及解决办法翘曲变形:注塑制品的形状偏离了模具形腔的形状什么是翘曲变形(Warping)?翘曲变形(Warping)是注塑制品的形状偏离了模具形腔的形状,如图所示,它是塑料制品常见的缺陷之一。
影响注塑产品翘曲变形的因素有很多,模具的结构、塑料材料的热物理性能以及注塑成型过程的条件和参数均对制品翘曲变形有不同程度的影响。
因此,对注塑制品翘曲变形机理的研究必须综合考虑整个成型过程和材料性能等多方面的因素。
随着人们对塑料制品的外观和使用性能要求越来越高,翘曲变形程度作为评定产品质量的重要指标之一也越来越受到关注与重视。
翘曲变形(Warping)缺陷成因分析(1)分子取向不均衡热塑性塑料的翘曲变形很大程度上取决于塑件径向和切向收缩的差值,而这一差值是由分子取向产生的。
通常,塑件在成型过程中,沿熔料流动方向上的分子取向大于垂直流动方向上的分子取向,这是由于充模时大部分聚合物分子沿着流动方向排列造成的,充模结束后,被取向的分子形态总是力图恢复原有的卷曲状态,导致塑件在此方向上的长度缩短。
因此,塑件沿熔料流动方向上的收缩也就大于垂直流动方向上的收缩。
由于在两个垂直方向上的收缩不均衡,塑件必然产生翘曲变形。
为了尽量减少由于分子取向差异产生的翘曲变形,应创造条件减少流动取向及缓和取向应力的松驰,其中最为有效的方法是降低熔料温度和模具温度。
在采用这一方法时,最好与塑件的热处理结合起来,否则,减小分子取向差异的效果往往是暂时性的。
因为料温及模温较低时,熔料冷却很快,塑件内会残留大量的内应力,使塑件在今后使用过程中或环境温度升高时仍旧出现翘曲变形。
如果塑件脱模后立即进行热处理,将其置于较高温度下保持一定时间再缓冷至室温,即可大量消除塑件内的取向应力,热处理的方法为;脱模后将塑件立即置于37.5~43度温水中任其缓慢冷却。
(2)冷却不当如果模具的冷却系统设计不合理或模具温度控制不当,塑件冷却不足,都会引起塑件翘曲变形。
注塑翘曲变形调机法

注塑翘曲变形调机法
1.调节模具温度:模具温度过高或过低会引起翘曲变形,因此需要根据材料的熔点和熔融温度进行模具温度的合理调节。
2.调节注塑压力:注塑压力过大或过小也会造成翘曲变形,需要根据料胆的大小和材料的流动性进行适当的调节。
3.调节注塑速度:注塑速度过快或过慢都会对成型品的质量产生影响,需要根据材料的流动性和注塑过程中的温度和压力进行适当的调节。
4.增加模具冷却时间:通过增加模具冷却时间来改善翘曲变形问题,这样可以使成型品更加均匀、稳定。
5.改变料胆厚度:可以通过改变料胆的厚度来减少翘曲变形问题,适当增加料胆的厚度可以有效地提高成型品的稳定性。
6.改变模具结构:改变模具结构,增加支撑结构,防止成型品出现翘曲变形。
注塑制品翘曲变形的原因分析

注塑制品变形、弯曲、扭曲现象的发生主要是由于塑料成型时流动方向的收缩率比垂直方向的大,使制件各向收缩率不同而翘曲,又由于注射充模时不可避免地在制件内部残留有较大的内应力而引起翘曲,这些都是高应力取向造成的变形的表现。所以从根本上说,模具设计决定了制件的翘曲倾向,要通过变更成型条件来抑制这种倾向是十分困难的,最终解决问题必须从模具设计和改良着手。 这种现象的主要有以下几个方面造成:
(2)模具温度过高,冷却时间过短,使脱模时的制件过热而出现顶出变形。
(3)在保持最低限度充
(4)必要时可对容易翘曲变形的制件进行模具软性定形或脱模后进行退米处理。
1.模具方面:
(1)制件的厚度、质量要均匀。
(2)冷却系统的设计要使模具型腔各部分温度均匀,浇注系统要使料流对称避免因流动方向、收缩率不同而造成翘曲,适当加粗较难成型部份的分流道、主流道,尽量消除型腔内的密度差、压力差、温度差。
(3)制件厚薄的过渡区及转角要足够圆滑,要有良好的脱模性,如增加脱模余度,改善模面的抛光,顶出系统要保持平衡。
(4)排气要良好。
(5)增加制件壁厚或增加抗翘曲方向,由加强筋来增强制件抗翘曲能力。
(6)模具所用的材料强度不足。
2.塑料方面:
结晶型比非结晶型塑料出现的翘曲变形机会多,加之结晶型塑料可利用结晶度随冷却速度增大而降低,收缩率变小的结晶过程来矫正翘曲变形。
3.加工方面:
(1)注射压力太高,保压时间太长,熔料温度太低速度太快会造成内应力增加而出现翘曲变形。
改善液晶电视机注塑模点浇口冲击磨损问题
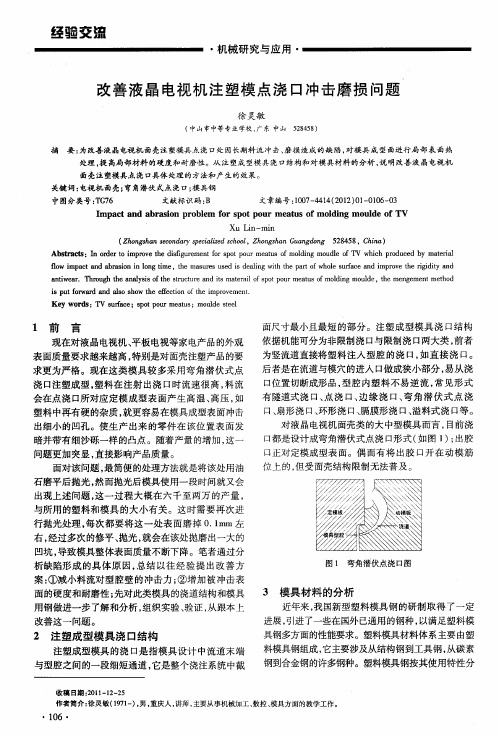
塑料中再有硬 的杂质 , 就更容易在模具成型表面冲击
出细小 的 凹孔 。使 生 产 出来 的零 件 在 该位 置 表 面发 暗 并带 有 细 沙砾一样 的凸点 。随着产 量 的增 加 , 一 这 问题更 加突 显 , 接影 响产 品质量 。 直 面对该 问题 , 最简便 的处 理方法 就是将该 处用 油 石 磨平 后抛 光 , 而抛 光后模 具使用 一段 时间就 又会 然 出现上 述 问题 , 一 过 程 大概 在六 千至 两万 的产 量 , 这 与所用 的塑 料 和模 具 的 大小 有关 。这 时需 要再 次 进 行 抛 光处理 , 次 都要 将 这 一处 表 面 磨 掉 0 1 m 左 每 . m
Ke r s V s ra e;s o o rme t s y wo d :T u fc p tp u au ;mo l e s e ud t l e
1 前
言 面尺寸ຫໍສະໝຸດ 小且最 短 的部 分 。注塑 成 型模 具 浇 口结 构
前者 现在对液晶电视机、 平板 电视等家电产品的外观 依 据机 能可分 为非 限制浇 口与 限制 浇 口两大 类 , 如直 接 浇 口。 表面质量要求越来越高 , 特别是对面壳注塑产品的要 为竖 流道直接 将塑 料 注入 型 腔 的浇 口, 易从浇 求更为严格 。现在这类模具较多采用弯角潜伏式点 后者是在流道与模穴的进人 口做成狭小部分 , 口位 置切断成 形 品 , 腔 内塑 料 不 易 逆 流 , 型 常见 形 式 浇 口注塑成型 , 塑料在注射出浇 口时流速很 高, 料流 会在 点浇 口所 对应 定 模 成型 表 面产 生 高 温 、 高压 , 如 有 隧道式浇 口、 浇 口、 缘 浇 口、 角潜 伏 式 点 浇 点 边 弯 口、 形浇 口、 扇 环形 浇 口、 膜形 浇 口、 膈 溢料 式浇 口等 。
家用电器外壳的注塑成型工艺分析与模具设计

家用电器外壳的注塑成型工艺分析与模具设计背景随着家电产品的不断更新换代,外壳设计越来越考究,所以家用电器外壳的制作工艺也在不断的优化。
注塑成型是目前家用电器外壳制作中应用最广泛的一种工艺,因此对注塑成型工艺的分析和模具设计显得尤为重要。
工艺分析注塑成型的原理是利用注塑机将加热熔融的塑料通过射嘴喷射到模具中,随后快速冷却成型。
家用电器外壳制作工艺要考虑参数调整和制造材料的选择。
参数调整1. 温度调整:温度会影响塑料的熔化、流动和固化速度等,工作温度要依据塑料种类进行调整。
2. 压力调整:注塑成型时需要对模具施加一定压力,压力过大或过小都会影响成型效果。
3. 注塑时间:注塑时间需要根据模具的制作要求来调整。
制造材料的选择1. 家电外壳通常采用ABS或PC等高性能塑料制作,这些材料的性能要与产品要求相匹配。
模具设计模具设计是注塑成型过程中非常重要的一环,一个好的模具设计直接影响着产品质量和效率。
模具结构1. 分模式:常见的分模式有单动、双动和侧向动等,选择不同的分模结构要根据产品形状和工艺要求进行。
2. 浇道设计:浇道的设计要符合塑料充模的要求,同时不影响产品的外观。
3. 冷却系统:要设计一套合理的冷却系统以保证产品能够迅速有效地冷却固化。
注意事项1. 模具尺寸要与注塑成型机相匹配。
2. 模具加工精度要高,确保产品尺寸稳定。
3. 模具表面硬度要高,并进行光洁度处理。
总结通过对家用电器外壳注塑成型工艺的分析和模具设计,我们可以制作出高质量、高精度的产品。
注塑成型技术仍在不断发展,我们有理由相信未来注塑成型技术会更加优化和完善。
投影仪后盖注塑翘曲变形的优化

0.2272mm
0.1753mm
Z 方向的翘曲量
1.177mm
1.309mm
1.019mm
三种不同进浇点产生的各方向的翘曲量如表 1 所示,
106
现代制造技术与装备
2017 第 10 期 总第 251 期
投影仪后盖最大产生翘曲量的方向为 Z 向,其他方向翘曲量 与 Z 向较小很多。因此,减小 Z 方向翘曲量就可以减小总的 翘曲量。从表 1 可以清楚获知,进浇点中,三点进浇的 Z 方 向的翘曲量 1.019mm 最小,总的翘曲量 1.081mm 也最小。因此, 三点进浇相对其他两种进浇方式对制品可以更小或更好。 3 注塑工艺参数优化
模具系统的浇口位置、形式和数量都会影响塑料熔体 的填充状态。流动距离越长,冻结层与中心流动层之间流 动和补缩引起的内应力越大;反之,内应力则降低,翘曲 变形也会减少。由于投影仪后盖大小、形状等因素,本文 决定采用三板式模具。要减小翘曲量,可以从模具结构浇 注系统进行优化。通过几种不同进浇方式进行 Moldflow 软件翘曲量分析,得到最小翘曲量的进浇方式来作为最终 选取的进浇方式。下面对三种不同进浇方式(图 2)进行
注射 时间 /s
模具 温度 /℃
熔体 温度 /℃
Z 向翘曲 量 /mm
均值 1
1.198
0.968
0.940
均值 2
1.046
0.979
0.983
均值 3
0.924
工艺与装备
105
投影仪后盖注塑翘曲变形的优化
陆春伟
(江苏省吴中中等专业学校,苏州 214187)
摘 要:投影仪后盖在模具制造方面属于典型的薄壁塑件,而薄壁塑件在制造过程中最难控制或解决的问题 就是翘曲变形。本文通过 Moldflow 软件,对投影仪后盖的三种不同进浇方式进行优化,然后结合正交设计对注 塑工艺参数进行优化,得到了最优工艺参数组合,有效控制了投影仪后盖的翘曲变形。
注塑模具制品的翘曲、变形原因及解决方法

注塑模具制品的翘曲、变形原因及解决方法
注塑成型是批量生产某些形状复杂部件时用到的一种加工方法。
具体指将受热融化的材料由高压射入模腔,经冷却固化后,得到成形品。
出现的翘曲、变形问题主要应从注塑模具设计方面解决,而成型条件的调整效果则是很有限的。
东莞恒圣塑胶实业有限公司专业为您介绍以下是翘曲、变形的原因及解决方法:
一、由成型条件引起残余应力造成变形时,可通过降低注射压力、提高注塑模具温度,并使注塑模具温度均匀,及提高树脂温度或采用退火方法予以消除应力。
二、脱模不良引起应力变形时,可通过增加推杆数量或面积、设置脱模斜度等方法加以解决。
三、由于冷却方法不合适,使冷却不均匀或冷却时间不足时,可调整冷却方法及延长冷却时间等。
四、对于成型收缩所引起的变形,就必须修正注塑模具的设计。
最重要的是应注意使制品壁厚一致。
关键词:模具加工,大型模具加工,大型注塑产品,注塑机产品。
液晶电视的前壳注射模具设计方法分析 王洋

液晶电视的前壳注射模具设计方法分析王洋摘要:以液晶电视机的前壳为例,结合液晶电视机的前壳注射模具制作方法选择一个科学合理的模具设计方法至关重要。
通过选择合适的电视机前壳注射模具设计方法可以提高电视机显示屏的使用寿命,而且还可以强化其清晰度,从而从整体上提高液晶电视机的整体使用性能。
下面这篇文章主要就对液晶电视机的前壳注射模具设计方法进行研究和分析,对高光无痕注射成型工艺进行模拟分析,对设计方法进行阐述。
关键词:液晶电视机前壳;高光无痕;模具设计;流动分析随着社会经济的发展以及人们生活水平的提高,人们对液晶电视机的质量要求也越来越高。
一方面要求电视机整体使用性能要好,另一方面要求电视机的外观比较具备审美观,但是传统的显示器制作方法无法很好地满足用户的这些要求,电视机生产厂家就需要采用先进的技术对液晶电视的前壳进行优化设计,将前壳大造成高光无痕的造型;同时还要对电视显示屏的温度进行控制。
基于此,我国很多电视机生产厂家研究出了基于Moldflow的高光无痕的电视机前壳注射模具设计方法,下文对此进行详细的阐述和介绍。
一、液晶显示器的优势及结构1.1液晶显示器的优势液晶显示屏的材料组成部分主要是有机高分子合成材料,这些材料的纯度相对是比较高的,这就使得电视机液晶显示器的本身结构构造方面比较好。
液晶显示器内部能够流通的电压以及电流值相对也比较小,可以保证液晶显示屏不被受到高电压或者高电流的侵蚀和破坏;与此同时,液晶显示器的防辐射性也比较好,即使显示器在出现各种光线的时候也不会对人体产生任何的光线辐射。
另外,液晶显示器的外观结构比较优美,符合人的审美观的要求。
由此可见,液晶显示器的整体结构比较协调,优势比较多。
下面就以液晶显示器的前壳作为研究对象,对其内部结构进行阐述。
1.2液晶显示器的主要结构液晶显示器的大小尺寸是不一样的,但是其内部结构大径相同。
一般情况下,液晶显示器内部的主要组成部分就是前壳以及内部的液晶屏幕,还有一些散热孔等。
电视机外壳注塑模具设计-设计说明书

第一章绪论1.1注塑成型模具简介注塑成型也称为注射成型,它是目前塑料加工中最普遍采用的方法之一,可用来生产空间几何形状非常复杂的塑料制件。
由于它具有应用面广、成型周期短、花色品种多、制件尺寸稳定、产品易更新换代、生产效率高、模具服役条件好、塑件尺寸精度高、生产操作容易实现机械化和自动化等诸方面的优点,因此,在整个塑料制件生产行业中,注塑成型占有非常重要的地位。
目前,除了少数几种塑料品种外,几乎所有的塑料(即全部热塑性塑料和部分热固性塑料)都可以采用注塑成型。
据统计,注塑制件约占所有塑料制件总产量的30%,全世界每年生产的注塑模数量约占所有塑料成型模具数量的50%。
薄壁注塑成型(thin-wallen jectionm olding,TWIM)技术也称为薄壁塑件注塑成型技术。
目前关于薄壁注塑成型还没有统一的定义。
Mahishi和Maloney 把其定义为流长厚度比LIT,即从熔体进人模具到熔体必须充填的型腔最远点的流动长度L和相应平均壁厚T之比在100或者150以上的注塑为薄壁注塑;而Whetten和Fasset 定义为:所成型塑件的厚度小于1mm,同时塑件的投影面积在50以上的注塑成型;还有学者把所成型塑件的壁厚小于1mm (或1.5mm)或者是t/d(塑件厚度t,塑件直径d,针对圆盘型塑件)在0.05以下的注塑成型定义为薄壁注塑成型。
由此可看出,要给出一个适合所有塑料原料和塑件形状的薄壁注塑成型定义还是比较困难的;同时随着技术的发展,薄壁注塑成型定义的临界值也将发生变化,它应该是一个相对的概念。
常规注塑成型工艺已为人们所熟悉,但薄壁注塑成型则不然,因为随着壁厚的减薄,聚合物熔体在型腔中的冷却速度加剧,在很短时间内就会固化这使得成型的过程变的复杂,成型难度加大,常规的注塑成型工艺条件已不能满足需要。
常规注塑成型的一个不足就是填充过程和冷却过程往往交织在一起,但由于常规塑件的尺寸比较大,所以对成型的过程影响不大,但在薄壁注塑成型中这个不足就成为致命的问题。
毕业设计模版液晶电视快速热循环注塑成型工艺参数

Numericalsimulationof LCD panelsrapidheatingcyclemoldinghasbeencarried out, which is based on the mold created in moldflow software. By the analysis the range of process parameters have been confirmed,defects ofplasticcan been found out and the reasons have been studied.
(2)LCDPanelsAnalysisMolding
A LCD Panelis considered as an example, which has been molded in UG software.The 3D mold has been imported into CAD Doctor software to be simplified.The simplified moldhas been meshed, the runner system, the heating system and cooling system have been created in moldflow 2021.
图1-3常见注塑缺点
随着塑料制品应用的日趋普遍,人们对塑料制品的精度,形状,功能,本钱等提出了更高的要求,CIM成型工艺已难以适应这种要求。为知足上述要求,目前生产中要紧通过打磨,喷涂和抛光等二次加工技术来提高塑件的表面质量。可是,后续的抛光和喷涂等工艺会造成生产原料和能源的浪费,增加塑料制品的生产成
注塑成型中,电视机前壳变形缺陷的解决思路(超实用)

注塑成型中,电视机前壳变形缺陷的解决思路(超实用)有网上好友问我关于注塑成型中电视机前壳变形的解决方法,现说下这个问题。
电视机壳是我们注塑成型生产中常见的一种产品,结构也较简单,就是一个四边的框,面带垂直边的结构,部分有侧抽芯但没有螺纹一般也不用气辅技术。
材料有ABS,HIPS,PC/ABS,PC等。
这几种材料的电视机框我都做过,还算有点发言权。
早期的电视机前壳多用ABS,主要是早期的产品都是CRT的,前壳要装显像管,需要承受很高的力,特别是BOSS柱强度要足够,能耐各个方面包括对角线方向的跌落试验的。
所以原先都用强度高又便宜的ABS,但后来为了节省成本,很多小电视比如24吋以下的都慢慢改成了HIPS,强度也可以。
再后来,CRT电视不流行了,改成了液晶电视或等离子电视,后二者结构都差不多,只是更薄了垂直边更短了,改成了PC/ABS的多。
某些个别的品牌也有用PC的,但属于非主流。
所以电视机框的结构就两大类:一类是正面与垂直边都很宽很长的CRT壳,另一类是正面宽但垂直边很短的液晶壳结构,我们分别说。
这两类的模具浇口形式多为潜伏式浇口,只是有的4个有的6个,道理相同。
另外还有少数有膜片浇口的属于非主流不予以讨论。
关于变形要求,因为前壳要与后壳装配,所以要求一般是不能前凸,如果前凸那么与后壳装配会有缝隙,一般要求平或者稍微前凹,因为前凹的前壳与后壳装配就不留缝隙。
不管是液晶壳还是CRT壳,调整变形的道理都一样- - -第一是用模温调整,第二是用产品正面边与垂直边的收缩差异来调整。
液晶壳薄,垂直边短,对熔接线等表面缺陷要求高,生产时要用高模温。
这种结构调整时产品正面边与垂直边的收缩差为次要,因为垂直边短,收缩效应差。
主要考虑的是模温调整。
后模温度稍微高点,就会朝后拱形变形,但出模后放置的细节要特别注意。
CRT壳比较厚,对熔接线要求级别低,且一般都需要喷涂,所以表面要求低,所以生产一般用低模温,这情况下的变形调节以正面边与垂直边的收缩差为主。
- 1、下载文档前请自行甄别文档内容的完整性,平台不提供额外的编辑、内容补充、找答案等附加服务。
- 2、"仅部分预览"的文档,不可在线预览部分如存在完整性等问题,可反馈申请退款(可完整预览的文档不适用该条件!)。
- 3、如文档侵犯您的权益,请联系客服反馈,我们会尽快为您处理(人工客服工作时间:9:00-18:30)。
Vol.19,No.3 Sep . 2 0 1 9
液晶电视外壳快速热循环注塑成型翘曲变形优化
褚 晶 ,徐 勇
(南通航运职业技术学院,南通 226010)
摘 要 :快 速 热 循 环 注 塑 成 型 可 使 塑 件 获 得 较 高 的 外 观 表 面 质 量 ,但 成 型 过 程 中 塑 件 产 生 的 翘 曲 变 形 较大,针对该问题,以液晶电视外壳为对象,通过 Molflow 软件进行快速热循环建模,分析成型过程中翘曲 产 生 的 机 理 ,设 计 正 交 试 验 ,获 得 影 响 翘 曲 的 主 要 工 艺 参 数 ,通 过 响 应 面 模 型 对 关 键 参 数 进 行 优 化 ,获 得 最 优 工 艺 参 数 组 合 ,试 验 验 证 该 方 法 可 以 有 效 控 制 翘 曲 变 形 。
2.3 试验结果分析 对 正 交 试 验 结 果 进 行 分 析 ,计 算 出 各 水 平 最 大 收 缩 率 的 均 值 K ,K1A=(y1+y2+y3+y4)/4 ,求 得 极 差 R ,
充填/保压
保压中期/冷却前期
缩 ,塑 件 表 面 凝 结 。 当 进 入 保 压 中 期 和 冷 却 前 期 时 ,型 腔 内 的 熔 体 开 始 冷 却 ,发 生 约 束 收缩,见图 1b。 进入保压后期和冷却后期, 塑件进一步冷却并在塑件截面上形成不对 称的残余应力,见图 1c。不对称的拉伸应力 和压缩应力在塑件中心层上产生一个弯矩 作用,使塑件翘曲变形,见图 1d。
有重要作用。这里将保压和冷却各分为两个阶段,
充填
见图 3。熔体充满型腔后至开始冷却阶段为保压前
温度/℃
期 ,此 时 模 具 温 度 保 持 高 温 恒 定 ;当 冷 却 开 始 后 ,进
入 保 压 后 期 ,此 时 模 具 温 度 快 速 下 降 至 低 温 。 在 此
过 程 中 ,冷 却 前 的 保 压 压 力 和 保 压 时 间 ,冷 却 后 的 保
第3期
褚 晶 ,等 :液 晶 电 视 外 壳 快 速 热 循 环 注 塑 成 型 翘 曲 变 形 优 化
5
尺 寸 为 472 mm × 318 mm × 15 mm。 将 产 品 的 数 字 模 型 导 入 Moldflow 2013 软件进行分析前处理,分析模型见图 2。同时,在软 件中创建浇注系统,该产品采用 4 个牛角浇口,流道直径为 6 mm。 这里采用蒸汽加热快速热循环注塑技术,冷却水管布置在型腔侧, 而型芯侧采用传统冷却方式。
冷凝层 熔融层 冷凝层
高温
自由收缩
低温
a
保压后期/冷却后期
低温
自由收缩
中间截面 残余应力
弯矩
高温
约束收缩
低温
b
约束收缩
翘曲变形
弯矩
2 液晶电视外壳快速热循环成型分析
2.1 分析模型 本 研 究 以 液 晶 电 视 外 壳 为 对 象 ,外 形
低温
c
d
图 1 翘曲变形形成机理示意图
收 稿 日 期 :20 19 - 05- 23 作者简介:褚晶(1981- ),女,江苏沛县人,南通航运职业技术学院汽港教研室助理工来自师,研究方向为汽车、港口机械等。
关键词:液晶电视; 快速热循环成型; 响应面模型; 翘曲变形 中图分类号:TQ320.662 文献标志码:A 文章编号:2096-0425(2019)03 - 0004 - 04
塑 料 注 塑 成 型 技 术 经 过 几 十 年 的 发 展 ,被 广 泛 应 用 于 电 器 、汽 车 、通 信 工 程 、医 疗 卫 生 、航 空 航 天 等 领 域 。 近 年 来 ,快 速 热 循 环 注 塑 成 型(Rapid Heat Cycle Molding,简 称“RHCM”)[1-3]获 得 越 来 越 广 泛 的 关 注 。 相比传统成型工艺,RHCM 可以彻底消除塑件表面的熔接痕、喷射痕、流痕、浮纤等,有效提高塑件的外观 质 量 ,使 塑 件 在 后 续 的 装 配 中 无 须 打 磨 、喷 涂 、罩 光 等 二 次 加 工 就 可 以 直 接 满 足 使 用 要 求 ,缩 短 生 产 流 程 , 降 低 生 产 成 本 ,但 [4-6] RHCM 塑 件 的 翘 曲 变 形 较 大 。 本 文 分 析 RHCM 塑 件 产 生 翘 曲 变 形 的 原 因 ,找 出 相 关 重要参数并通过响应面模型进行工艺的优化。
压压力和保压时间是控制翘曲变形的重要参数。因
此 ,本 研 究 以 这 4 个 参 数 为 主 要 因 素 ,在 4 个 水 平 上
进行正交试验,具体方案见表 1、表 2。
出水口
快速加热冷却进水口 型芯侧冷却进水口 图 2 分析模型
保压 保压后期 前期 冷却前期 冷却后期
玻璃转化温度
时间/s 图 3 模具温度变化曲线图
第 19 卷 第 3 期 2 019 年 9月
江 苏 工 程 职 业 技 术 学 院 学 报(综 合 版)
Journal of Jiangsu College of Engineering and Technology
DOI:10.19315/j.issn.2096-0425.2019.03.002
1 快速热循环成型翘曲变形的机理
RHCM 塑 件 虽 然 可 获 得 高 质 量 外 观 ,但 其 翘 曲 变 形 明 显 大 于 CIM(陶 瓷 注 射 成 型 ,Ceramic Injection
Molding,简称“CIM”)塑件,这主要由于 RHCM 的注塑过程仅对模具型腔进行快速加热和冷却控制,而对模
具 型 芯 仍 采 用 恒 温 控 制 ,使 得 塑 件 型 腔 侧 表 面 温 度 远 高 于 型 芯 侧 温 度 ,塑 件 因 冷 却 不 均 产 生 较 大 翘 曲 变
形[7- 。 8] 在塑料充满型腔时,型腔内的塑料上下两层为冷凝层,中间为熔融层[9-11],见图 1a。型腔和型芯的温
度 差 导 致 两 个 冷 凝 层 厚 度 不 均 ,发 生 自 由 收
2.2 数值模拟试验
RHCM 工艺是在合模之前将模具温度提升到玻璃转化温度
以 上 ,避 免 熔 体 在 填 充 过 程 中 过 早 发 生 冷 凝 。 根 据 翘 曲 变 形 产
生 的 机 理 ,熔 体 的 不 均 匀 收 缩 是 产 生 翘 曲 的 主 要 原
因 ,因 此 ,保 压 和 冷 却 过 程 的 工 艺 参 数 对 控 制 翘 曲 具