螺旋缝埋弧焊管内外自动焊焊枪结构设计
螺旋埋弧接钢管焊接和成型特点
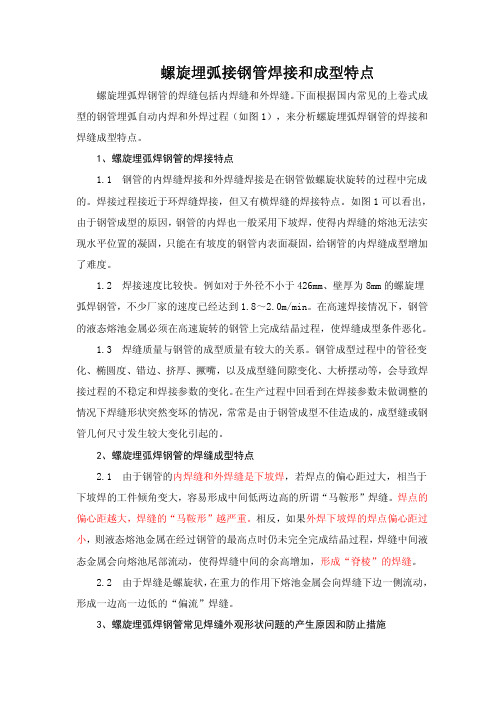
螺旋埋弧接钢管焊接和成型特点螺旋埋弧焊钢管的焊缝包括内焊缝和外焊缝。
下面根据国内常见的上卷式成型的钢管埋弧自动内焊和外焊过程(如图1),来分析螺旋埋弧焊钢管的焊接和焊缝成型特点。
1、螺旋埋弧焊钢管的焊接特点1.1 钢管的内焊缝焊接和外焊缝焊接是在钢管做螺旋状旋转的过程中完成的。
焊接过程接近于环焊缝焊接,但又有横焊缝的焊接特点。
如图1可以看出,由于钢管成型的原因,钢管的内焊也一般采用下坡焊,使得内焊缝的熔池无法实现水平位置的凝固,只能在有坡度的钢管内表面凝固,给钢管的内焊缝成型增加了难度。
1.2 焊接速度比较快。
例如对于外径不小于426mm、壁厚为8mm的螺旋埋弧焊钢管,不少厂家的速度已经达到1.8~2.0m/min。
在高速焊接情况下,钢管的液态熔池金属必须在高速旋转的钢管上完成结晶过程,使焊缝成型条件恶化。
1.3 焊缝质量与钢管的成型质量有较大的关系。
钢管成型过程中的管径变化、椭圆度、错边、挤厚、撅嘴,以及成型缝间隙变化、大桥摆动等,会导致焊接过程的不稳定和焊接参数的变化。
在生产过程中回看到在焊接参数未做调整的情况下焊缝形状突然变坏的情况,常常是由于钢管成型不佳造成的,成型缝或钢管几何尺寸发生较大变化引起的。
2、螺旋埋弧焊钢管的焊缝成型特点2.1 由于钢管的内焊缝和外焊缝是下坡焊,若焊点的偏心距过大,相当于下坡焊的工件倾角变大,容易形成中间低两边高的所谓“马鞍形”焊缝。
焊点的偏心距越大,焊缝的“马鞍形”越严重。
相反,如果外焊下坡焊的焊点偏心距过小,则液态熔池金属在经过钢管的最高点时仍未完全完成结晶过程,焊缝中间液态金属会向熔池尾部流动,使得焊缝中间的余高增加,形成“脊棱”的焊缝。
2.2 由于焊缝是螺旋状,在重力的作用下熔池金属会向焊缝下边一侧流动,形成一边高一边低的“偏流”焊缝。
3、螺旋埋弧焊钢管常见焊缝外观形状问题的产生原因和防止措施3.1 焊缝的余高过大和“脊棱”焊缝的余高过大的根本原因单位长度、单位宽度焊缝上堆积了过多的溶化金属所至。
螺旋缝双面埋弧焊钢管的生产工艺及质量控制

螺旋缝双面埋弧焊钢管的生产工艺及质量控制一、螺旋缝双面埋弧焊钢管的生产工艺及质量控制我公司螺旋缝双面埋弧焊钢管机组是采用现阶段较先进的工艺装备,在钢管外观、标称几何尺寸及椭圆度、直度控制上,优势明显。
螺旋缝双面埋弧焊钢管比其它焊管具有很多的优点: (一)、该焊管有相重叠的内外两条螺旋焊缝,起到增加刚性的作用,承压力也相应提高。
(二)、采用埋弧焊工艺,熔渣保护效果好。
因此,具有良好的冲击韧性和低温使用性能。
(三)、利用同等宽度的钢带可生产不同直径和长度的钢管,而且直度好。
易调整,尺寸精确,焊后不需定径和矫直。
该焊管还可以根据不同的材质,选用与之相匹配的焊接材料和焊接工艺,可适用于各种规格的焊管生产。
二、我公司生产机组结合国内许多厂家机组的特点,借鉴德国进口机组的设计,机组的适用范围、产品质量、都具有八、九十年代国际先进水平,也完全代表了国内先进水平,该机组前摆式主机,内承式成型机与外抱式成型机组,具有成型机理更合理,降低了管壁的残余应力,提高了钢管的承压能力,调整简便的优点。
机组采用上卷辊式成型、双面焊接的先进工艺,焊接设备采用美国林肯焊机,配备有管端自动平头倒棱机、X射线探伤机、自动超声波探伤机、500吨水压机,生产检测手段齐全,年生产能力可达20万吨,通过ISO9001国际质量体系认证,建立了持续有效的质量保证体系,产品质量达到现阶段国内比较先进的水平。
1、采用标准我国国家和行业标准:GB/T9711.1-97 SY/T5037-20002、质量体系(1)质量方针以加强管理为基础,以满足客户需要为目的,确保产品质量,追求企业的持续改进。
(2)人员资格制定了中期、长期、年度职工培训、教育计划,有完整的组织领导机构,有考核、奖罚管理制度,建有职工培训教育档案,对每个岗位人员的职责、资格和操作水平有严格要求,并经考核进行了上岗资格认证。
对焊接及检测岗位工作人员有特殊要求,需持考核证才能上岗。
(3)工序控制a.特殊工序:生产工序规定焊接、成型为特殊工序,每个特殊工序都相应建立质量控制点,进行重点控制管理。
最新螺旋埋弧焊钢管技术要求

双面螺旋缝埋弧焊钢管及3PE加强级外防腐技术要求钢管的技术要求1、产品名称:双面螺旋缝埋弧焊钢管。
2、燃气管道设计压力为0.4MPa。
3、材质:Q235B卷板。
4、卷板宽度:D219×7≥500mm(纵剪); D273×7≥500mm(纵剪);D325×7≥750mm(纵剪);D426×8≥750mm(纵剪)。
5、执行标准:GB/T9711.1-1997《石油天然气工业输送钢管交货技术条件第1部分:A级钢管》。
6、钢管外径:管径小于457的钢管,管体外径允许公差±0.75%。
D325×7和D426×8钢管在距管端101.6mm范围内,钢管外径允许下偏差为0.79mm且在距管端101.6mm范围内,应能允许内径比钢管规定外径大2.38mm的环规通过。
7、钢管壁厚:D219×7、D325×7、D426×8钢管壁厚公差下偏差允许范围为6%δ。
8、单根钢管的长度为12m(误差不大于0.02m)。
9、直度偏差不得超过钢管长度的0.2%。
10、钢管材料的化学成分其化学成分应符合下表:执行标准:GB/T700-200611、钢管的力学性能钢管的力学性能应符合下表12、钢管的试验和检验:应符合GB/T9711.1-1997的相关规定。
双面螺旋缝埋弧焊钢管的三层PE加强级外防腐的技术要求1、执行标准:GB/T23257-20092、防腐层应按GB/T23257-2009标准加工检验,并应有满足GB/T23257-2009标准要求的合格证书。
3、每批防腐管均应按GB/T23257-2009标准附录B的方法进行阴极剥离性能检验,结果应符合GB/T23257-2009的规定。
若不合格可再截取一次样品,若仍不合格不得降级使用,检验查处的不合格品,应重新进行防腐涂敷。
4、防腐管的吊装,应采用尼龙吊带或其他部损坏防腐层的吊具,防腐管堆放时,其底部应采用3道(或以上)支垫垫起,支垫最小宽度为100MM,运输时应采用尼龙带等捆绑固定,每根防腐管的捆绑带应大于正常出厂捆绑带的直径,防腐管的堆放层数不得大于5层。
螺旋埋弧焊接钢管工艺

螺旋埋弧焊接钢管工艺
螺旋埋弧焊接钢管工艺是一种常用的钢管连接方式,适用于大直径钢管的生产。
其具体工艺流程如下:
1. 钢管开割:根据钢管设计要求,对待焊接的钢管进行开割,并对板材进行打磨、清理。
2. 钢管预定位:将待埋弧焊接的钢管放入自动定位设备中,定位宽度和位置。
3. 管端面加工:将开割后的钢管端面进行加工,以保证钢管端面的平整度和垂直度。
4. 焊缝内部清理:清理管内/外的无效物质(如锈、油漆等)。
5. 埋弧焊接:在自动定位设备的控制下,用刚性接头将两根相邻的钢管固定起来,然后开始埋弧焊接。
6. 定径修圆:焊接完成后,进行钢管的相应的修圆和定径的工作,以保证钢管的圆度和精度。
7. 焊接外覆盖层:将需要加外覆盖层的钢管放入自动外覆盖层装置,进行外覆盖层的焊接。
8. 尾部平整:将焊接钢管的尾部进行砂轮加工,使之平整。
通过以上的工艺流程,可以使焊接过程中的钢管质量得到有效的保证,从而满足相关工程的使用要求。
隔水管套内焊缝自动焊接机设计
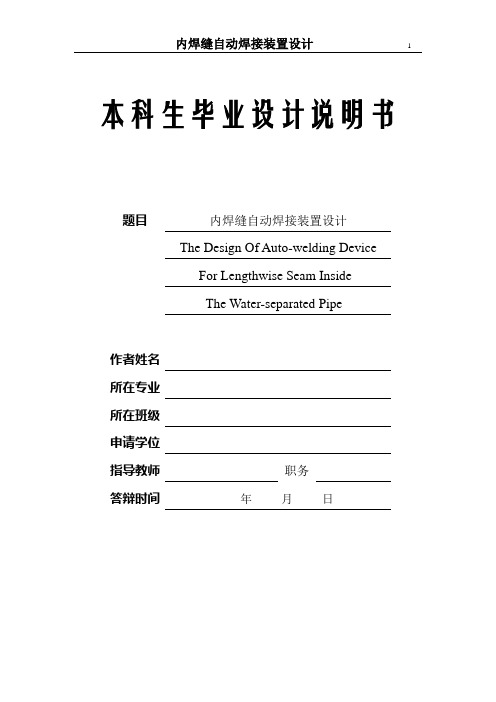
本科生毕业设计说明书题目内焊缝自动焊接装置设计The Design Of Auto-welding DeviceFor Lengthwise Seam InsideThe Water-separated Pipe作者姓名所在专业所在班级申请学位指导教师职务答辩时间年月日隔水管套内焊缝自动焊接装置设计摘要:快速接头隔水管系列产品,南油合众特有的为海洋石油配套的专用产品。
本设计是针对*SR-30、SR-24、SR-20、*SR-16、SR-13系列产品制造中,对卷制成管状板材的内纵焊缝能进行自动焊接的装置,包括机械系统设计和电气设计。
此设计采用自动焊接小车形式,能实现焊接位置的自动找正、焊接时的自动行走、自动导向。
关键词:隔水管内纵焊缝焊接焊接小车Abstract:Speedy junction of water-separated pipe , the series of which is specially produced for ocean rock oil in United Offshore construction hw. A auto-welding cart will be designed for lengthwise seam inside the water-separated pipe in this graduation project, which is divided into two portions---mechanic system design and electric system design. The cart can perform some functions such as searching the seam itself, walking along the seam automaticly and so on.Keywords: water-separated pipe auto-welding cart lengthwise seam第一章 概述第一节CO2气体保护焊简介CO2气体保护电弧焊是 利用CO2作为保护气体的气体保护电弧焊。
螺旋埋弧焊管内壁焊渣自动清理和防护装置设计

螺旋埋弧焊管内壁焊渣自动清理和防护装置设计摘要:螺旋埋弧焊管是一种以钢卷为原料,采用双线双面埋弧焊工艺焊接的螺旋焊管。
在常用于订购钢管的技术标准中,除了要求产品符合化学成分、机械性能、尺寸等要求外,钢管的表面质量也有一些要求。
管材表面质量可能影响管材的服务性能,严重缺陷可能影响管材的生产效率和质量率,增加公司成本。
针对冷弯弧焊管残馀焊缝和在线切割钢管过程中产生的金属爆裂引起的钢管表面质量问题,开发了钢管内壁自动清洗防护设备。
关键词:螺旋埋弧焊;管内壁焊渣自动清理;防护装置设计引言管道结构焊接时,由于速度快和焊接面不平坦,埋弧焊可能会在焊接液熔池结晶过程中进入空气和水中,从而形成焊接渣和空穴,影响焊接质量。
同时,在螺旋埋弧焊时,不正确的边、板边累积和成型间隙过大可能会影响螺旋埋弧焊的质量。
特别是,在使用较厚的壁焊管道时,焊接中的混合和空气孔可能会减少焊缝的强度和应力,从而降低焊缝的耐久性和机械性能,并由于池的深度而影响焊缝的寿命和使用效率因此,在进行螺旋铣削电弧管的焊接时,应注意焊接材料、焊接工艺、板边形状等。
避免混合气和空穴等问题,提高弧焊管的焊接质量。
1板材性能化学成分,超厚壁X80管线钢具有高强度、高韧性、良好的焊接性能和一定的抗腐蚀能力,随着厚度增加,DWTT控制难度急剧加大[6]。
为保证管体强度,同时提高低温冲击性能,在成分设计上采用低碳高Nb+Mo/Ni合金设计,开发出了1550mm×25.4mm厚壁X80热轧卷板。
成分设计时,采用LF+RH双联工艺,降低S、P含量,提高钢水洁净度,降低偏析,采用粗轧低温快轧技术,使精轧前再结晶奥氏体晶粒尺寸降低,提高断裂韧性;采用0.07%~0.09%的Nb微合金化提高晶粒细化效果;加入适量Cr、Mo等提高钢的淬透性,确保厚壁热轧卷板在层流冷却过程中,能有效缩小表面和心部的冷却速率差,从而确保板材厚度方向组织和力学性能的均匀稳定,并促进针状铁素体(AF)生成,提高低温韧性;考虑产品的经济性和综合性能,添加Ni和Cu元素,利用固溶强化效果提高超厚壁板材的强度和断裂韧性,利用Ni进一步提高钢的低温韧性。
φ406.4mm×8.8mm螺旋埋弧焊管生产工艺
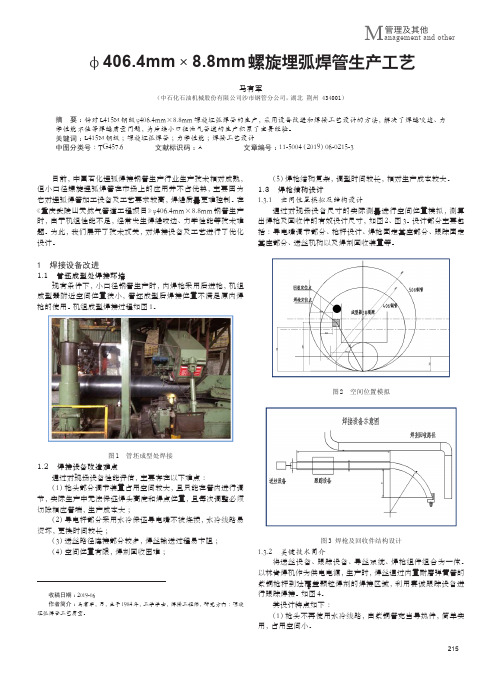
215管理及其他M anagement and otherφ406.4mm ×8.8mm 螺旋埋弧焊管生产工艺马有军(中石化石油机械股份有限公司沙市钢管分公司,湖北 荆州 434001)摘 要:针对L415M 钢级φ406.4mm×8.8mm 螺旋埋弧焊管的生产,采用设备改进和焊接工艺设计的方法,解决了焊缝咬边、力学性能不佳等焊缝质量问题,为后续小口径油气管道的生产积累了宝贵经验。
关键词:L415M 钢级;螺旋埋弧焊管;力学性能;焊接工艺设计中图分类号:TG457.6 文献标识码:A 文章编号:11-5004(2019)06-0215-3收稿日期:2019-06作者简介:马有军,男,生于1984年,工学学士,焊接工程师,研究方向:螺旋埋弧焊管工艺质量。
目前,中国石化埋弧焊接钢管生产行业生产技术相对成熟,但小口径螺旋埋弧焊管在市场上的应用并不占优势,主要因为它对埋弧焊管加工设备及工艺要求较高,焊缝质量更难控制。
在《重庆武陵山天然气管道工程项目》φ406.4mm×8.8mm 钢管生产时,由于机组性能不足,经常发生焊缝咬边、力学性能等技术难题。
为此,我们展开了技术攻关,对焊接设备及工艺进行了优化设计。
1 焊接设备改进1.1 管坯成型处焊接环境现有条件下,小口径钢管生产时,内焊枪采用后进枪,机组成型器附近空间位置狭小,管坯成型后焊接位置不满足原内焊枪的使用。
机组成型焊接过程如图1。
图1 管坯成型处焊接1.2 焊接设备改造难点通过对现场设备性能评估,主要存在以下难点:(1)枪头部分调节装置占用空间较大,且只能在管内进行调节,实际生产中无法保证焊头高度和焊点位置,且每次调整必须切除相应管端,生产成本大;(2)导电杆部分采用水冷保证导电嘴不被烧损,水冷线路易烫坏,更换时间较长;(3)送丝路径连接部分较多,焊丝输送过程易卡阻;(4)空间位置有限,焊剂回收困难;(5)焊枪结构复杂,调型时间较长,相对生产成本较大。
开题报告-管道外圆自动焊接机的结构设计

开题报告课题题目及来源:题目:管道外圆自动焊接机的结构设计题目来源:自拟课题研究的意义和国内外研究现状:目前管道施工已逐渐从手工焊接向全自动焊接方向发展。
管道建设地区跨度大,沿线施工环境恶劣,加之管道输送逐步向高压、大口径方向发展,这对管道环焊缝的焊接提出了更高的要求,管道环焊缝的焊接成为制约整个工程质量和建设周期的关键因素。
野外焊接环境十分恶劣,焊工劳动强度大,技术难度高,因此,工程上迫切需要实现管道的自动焊接,用以提高生产率、保证焊接质量、降低劳动强度和施工成本,而且自动焊接还能大幅度降低操作技术难度,解决焊工培养困难,流失严重等问题。
本设计的目的是对管道建设野外作业的管道外圆自动焊接机进行结构设计以达到体积小、重量轻、加工成本低、运动精度高、操作简便并且满足各项性能指标的要求。
管道外圆自动焊接机的国内外研究现状如下:(1)国外研究现状管道焊接广泛应用于各个工程领域当中,比如:油气工业、核能与热能工厂和化工厂。
管道外圆自动焊接机采用熔化极外圆焊接技术,最早出现于20世纪60 年代末期。
MIG金属焊丝惰性气体保护焊是美国制造业四十多种焊接中的一种,它是一种连接两个相同材料尤其是碳钢材料经济的方法。
美国CRC公司率先研制成功了一种高效管道焊接系统,即CRC多头气保护管道自动焊系统,并于1972年将该项技术应用于管道施工获得成功。
起初只是焊接小车带动焊枪行走,焊接参数(焊接电流、电压、焊接速度等)均为手动控制。
目前,生产外圆自动焊接设备的除了美国CRC公司外,还有德国VIETZ公司、美国MAGNATECH公司、荷兰VERAWELD公司、英国Noreast公司、法国SERIMER DASA公司、意大利PWT 公司等。
CRC公司智能化的P-500、P-600型以及SERIMER DASA公司的双枪焊接系统在世界范围内具有很高的技术水平。
到目前为止,CRC公司生产了P300, P400, P500和P600 4个型号的管道外圆自动焊机。
管道外圆自动焊接机结构设计_毕业设计说明书

毕业设计说明书管道外圆自动焊接机结构设计摘要:管道运输是油气运输中最主要、最快捷、经济、可靠的方式,可用于输送水、原油、天然气、成品油等,具有输量大、距离长、安全性高、成本低等优点,在各国发展迅速。
管道运输业的主体是管道,管道工程的核心工作是管口的焊接。
因此研究高效率、性能可靠的管道全位置自动焊接机具有十分重要的意义。
为解决管道建设野外作业的自动化焊接的难题,研制了一种导轨式管道焊接机器人,其关键技术包括:研制新型的行走机构、焊枪摆动机构、及机器人轨道、焊枪机械手。
介绍了导轨式焊接机结构的设计和焊接机控制,着重对其结构特点、动作原理、设计要点进行设计分析和说明。
现场应用表明,该机器人能沿导轨平稳、可靠的行走,进行管道外圆全位置焊接,其操作简便,成本低,适合我国现场施工作业及工人的技术水平,既保证了焊接质量,又提高了劳动效率。
关键词:轨道式焊接机;结构设计;管道;机械手指导老师签名:Cylindrical pipe automatic welding machine design Abstract:Pipeline transportation is the most important, quickest, economical and reliable method in petroleum transportation. It can transport water, crude oil, natural gas, oil product etc. It has a number of advantages: high transmission volumes, long distance, safety and cost-effectiveness, which is rapid developed in all the world. The subject of pipeline transportation is pipeline; the core of pipeline project is nozzle welding. So, it has very important significance to develop high efficient and reliable performance pipeline all-position automatic welding machine.An orbit pipeline welding robot has been developed to solve the problem of automatic welding during pipeline construction in the fields. Its key techniques consist of developing a new type of travel unit, welding torch as cillating unit, robot orbit and intelligent control system etc. The development work of the orbit pipeline welding robot mechanic system is introduced in the paper.The main illustration is about the system's structure,action principle,key points of design and machining technies and verifying calculation for selecting reduction gearbox with the wire feeder motor and the diameter of the wire-feed wheel. The application in fieldwork shows that the robot can trave1 along the orbit stably and reliably and carry through all-position welding. The welding is easy with low cost that is fit for fieldwork and worker in our country,guarantees the welding quality and improve working efficiency.Keywords:Orbital welding machine ;construction design ;pipeline;ManipulatorSignature of supervisor:管道外圆自动焊接机结构设计摘要:管道运输是油气运输中最主要、最快捷、经济、可靠的方式,可用于输送水、原油、天然气、成品油等,具有输量大、距离长、安全性高、成本低等优点,在各国发展迅速。
浅谈螺旋埋弧焊钢管的焊缝外观形状控制

浅谈螺旋埋弧焊钢管的焊缝外观形状控制浅谈螺旋埋弧焊钢管的焊缝外观形状控制?52?焊管?第29卷第2期?2006年3月浅谈螺旋埋弧焊钢管的焊缝外观形状控制罗天宝,乔晓堂(胜利钢管有限公司,山东淄博255082)摘要:分析了焊缝余高,焊缝宽度,焊缝过渡角,焊缝均匀性等焊缝外观形状的主要几何参数及其控制要求,并通过对钢管螺旋缝焊接和焊缝成型特点的分析,阐明了焊缝外观形状控制的难点.指出了焊缝外观形状常见问题的产生原因和防止措施,对生产实践有一定的指导意义.关键词:螺旋埋弧焊钢管;埋弧自动焊;焊缝外观形状中图分类号:TG44文献标识码:B文章编号:1001-3938(2006)02—0o52—040前言螺旋缝埋弧焊钢管焊缝的内在质量随着焊接材料的发展和焊接工艺的进步已得到了较好的保证,完全可以满足产品标准的要求,但焊缝的外观质量与客户对钢管质量日益严格的要求相比还有一定的差距.特别是随着3PE防腐技术在螺旋缝埋弧焊钢管上的应用,客户对焊缝的外观形状提出了更高的要求,因为不良的焊缝外观形状将对钢管的防腐质量和成本产生严重影响.此外,不良的焊缝外观形状对焊缝的超声波无损检测也有不良影响.因此,提高螺旋埋弧焊钢管的焊缝外观质量非常必要.1焊缝外观形状及其控制要求焊缝外观形状的主要几何参数有:焊缝余高,焊缝宽度,焊缝过渡角等(见图1),此外还包括焊缝的均匀性.B一焊缝宽度^一焊缝余高矗-_焊缝熔深a一焊缝过渡角图1焊缝形状示意图1.1焊缝余高焊缝余高是焊缝外观形状控制的最主要几何参数,大多数焊接产品标准对焊缝余高均有明确要求.在现行的APISPEC5L,GB/T9711.1—1997,GB/T9711.2—1999等螺旋埋弧焊钢管标准中,对焊缝余高要求最严格的是GB/I9711.2—1999标准,该标准对焊缝余高的规定是:当钢管壁厚r,≤15mm时,内,外焊缝余高均≤3mm;当钢管壁厚T>15mm时,内焊缝余高≤3mm,外焊缝余高≤4mm.而且除修磨咬边外,焊缝余高不得低于钢管轮廓.但是,许多用户都对焊缝余高提出了更严格的附加要求.例如在《西气东输工程用螺旋缝埋弧焊钢管技术条件》中,对西1016mm×14.6mm和1016mm×17+5mm两种钢管都规定了内焊缝余高≤3mm,外焊缝余高≤2.5mm的严格要求.对螺旋埋弧焊钢管焊缝余高的控制,主要应防止焊缝余高超高,同时也应防止因焊缝"马鞍形"过大,焊缝凹陷引起的焊缝高度低于钢管表面轮廓的现象.尤其需要引起重视的是,在焊缝余高符合产品验收标准要求情况下的焊缝中间"脊棱"问题.因为这种焊缝会在防腐时严重降低钢管焊缝处的防腐层厚度.1.2焊缝宽度焊缝宽度是决定焊缝外观形状的另一个主要第29卷第2期罗天宝等:浅谈螺旋埋弧焊钢管的焊缝外观形状控制参数,它和焊缝余高决定了焊缝的基本形状.现行的螺旋埋弧焊钢管标准都未对焊缝宽度做出明确要求.可以参考JB/T7949~1999(钢结构焊缝外形尺寸》标准的规定,对于I形焊缝,将钢管的焊缝宽度限制在6+8mm到6+28mm之间(6为对缝间隙);对于开坡口的焊缝,焊缝宽度限制在g十4mm到g十14mm之间(g为坡口最大宽度).在确定焊缝宽度时主要应考虑以下几个因素:首先应保证焊缝的充分熔合,特别是保证在焊缝有少量焊偏情况下的充分熔合,为此要求焊缝有一定的宽度;其次是应该保证焊缝与母材的平缓过渡,避免出现窄而高的焊缝,为此需要焊缝宽度和焊缝高度保持一个适当的比例,将焊缝的高度系数(焊缝宽度和焊缝高度之比)控制在一定的范围内.一般焊缝的高度系数应不小于4—8;第三,保持一定的焊缝成型系数(焊缝宽度和熔深之比),避免出现窄而深的焊缝,防止焊缝产生裂纹,气孔和夹渣等内部缺陷;第四,在满足以上要求的情况下,也不应一味加大焊缝宽度,因为这样一方面会增加焊丝,焊剂等焊接材料的消耗,此外也容易导致焊缝产生气孔,咬边等缺陷.因此,在确定焊缝宽度时需要和焊缝余高,焊缝熔深等一起综合考虑,以使焊缝获得良好的外观和横截面形状为基本原则.1.3焊缝过渡角焊缝过渡角即焊缝与母材之间的夹角,是表示焊缝与母材过渡情况的参数,过渡角越大,焊缝与母材过渡越平缓.反之亦反.对于焊缝与母材的过渡情况,现行的螺旋埋弧焊钢管产品标准都只定性要求"钢管焊缝与母材过渡平缓",而没有对焊缝的过渡角大小提出定量要求.在顾客对钢管的附加技术要求中,也未见有对焊缝过渡角提出明确规定的.但是,焊缝与母材过渡的不好是螺旋埋弧焊钢管的主要薄弱环节之一,因此,保证焊缝与母材尽可能平缓过渡对提高钢管质量有重要意义,应引起足够重视. 以笔者的生产经验,要充分保证焊缝与母材的平缓过渡,应将焊缝的过渡角控制在不小于135.,最好不小于150..1.4焊缝的均匀性焊缝的均匀性是指焊缝外观形状的连续一致性,包括焊缝宽度的一致性和焊缝高度的一致性. 对于焊缝的均匀性,现行的螺旋埋弧焊钢管产品标准都没有明确要求.虽然JB/1_7949—1999(钢结构焊缝外形尺寸》标准对埋弧焊缝外形的均匀性有规定,但对于螺旋埋弧焊钢管来说该标准的要求偏松,如果只满足于符合该标准,难以保证焊缝的均匀美观.根据螺旋埋弧焊钢管生产经验,应将同一根钢管的焊缝高度差控制在不超过1mm;将同一根钢管上焊缝的宽度差控制在不超过2mm,同时将任意50mm长度范围内的焊缝宽度差控制在不超过1mm.这样才能保证焊缝基本美观.2螺旋埋弧焊钢管焊接和焊缝成型特点螺旋埋弧焊钢管的焊缝包括内焊缝和外焊缝.下面根据国内常见的上卷式成型的钢管埋弧自动内焊和外焊过程(图2),来分析螺旋埋弧焊钢管的焊接和焊缝成型特点.图2焊接位置示意图2.1螺旋埋弧焊钢管的焊接特点(1)钢管的内焊缝焊接和外焊缝焊接是在钢管做螺旋状旋转的过程中同时完成的.焊接过程接近于环焊缝焊接,但又有横焊缝的焊接特点. 由图2可以看出,由于钢管成型的原因,钢管的内焊也一般采用下坡焊,使得内焊缝的熔池无法实现在水平位置的凝固,只能在有坡度的钢管内表面凝固,给钢管的内焊缝成型增加了难度. (2)焊接速度比较快.例如对于外径不小于426mm,壁厚为8mm的螺旋埋弧焊钢管,不少工厂的焊接速度已经达到了1.8—2.0m/min.在高速焊接的情况下,钢管的液态熔池金属必须在高速旋转的钢管上完成结晶过程,使焊缝成型条?54?焊管2006年3月件恶化.(3)焊缝质量与钢管的成型质量有较大的关系.钢管成型过程中的管径变化,椭圆度,错边,挤厚,噘嘴,以及成型缝间隙变化,大桥摆动等,会导致焊接过程的不稳定和焊接参数的变化,引起焊缝形状变化.在生产中经常会看到在焊接参数未做调整的情况下焊缝形状突然变坏的情况,这常常是由于钢管的成型不佳,成型缝或钢管几何形状发生较大变化而引起的.2.2螺旋埋弧焊钢管的焊缝成型特点(1)由于钢管内焊缝和外焊缝是下坡焊,若焊点偏心距过大,相当于下坡焊的工件倾角变大, 容易形成中间低两边高的所谓"马鞍形"焊缝.焊点偏心距越大,焊缝的"马鞍形"越严重.相反,如外焊下坡焊的焊点偏心距过小,则液态熔池金属在经过钢管的最高点时仍未完全完成结晶过程,焊缝中间液态金属会向熔池尾部流动,使焊缝中间增高,形成余高过大或中间有"脊棱"的焊缝.(2)由于焊缝是螺旋状,在重力作用下熔池金属会向焊缝下边一侧流动,形成一边高一边低的"偏流"焊缝,这种焊缝下边一侧过渡较差.3螺旋埋弧焊钢管常见焊缝外观形状问题的产生原因和防止措施3.1焊缝余高过大和焊缝"脊棱"焊缝余高过大的根本原因是单位长度,单位宽度焊缝上堆积了过多的熔化金属所致.具体原因主要有:①焊接规范搭配不当,电流过大,电压过小以及焊速过慢;②焊点位置不当,焊点偏心距过小,液态熔池金属流向熔池尾部,导致焊缝高度增大,特别是焊缝中间的余高增大,形成焊缝"脊棱";③焊丝后倾角过大,使熔池金属剧烈后排;④双丝焊的前,后焊丝间距过小.防止措施:①通过工艺试验确定合理的焊接规范匹配;②合理调整焊点位置,焊丝倾角和焊丝间距等工艺参数;③厚壁钢管采用开坡口的焊接工艺,可有效降低焊缝余高.3.2焊缝"马鞍形"太大焊缝"马鞍形"长期以来一直是螺旋埋弧焊钢管一个比较典型的问题,在钢管的内焊缝上表现得尤为突出.其产生的最主要原因是下坡焊时的钢管焊点偏心距过大.对于开坡口的焊缝,坡El深度和角度过大也是焊缝产生"马鞍形"的主要原因.防止措施:①采用尽可能小的焊点偏心距.当下坡焊的焊件倾角大于4.时,焊缝就会出现马鞍形,由此可推导出,对于半径为R的钢管,要使焊缝不出现马鞍形,至少必须使焊点的偏心距~<Rsin4.,即.厂偏≤O.07R,考虑到钢管在生产过程中是不断旋转的,内焊的焊点偏心距比此计算值还应更小,而外焊的焊点偏心距比此计算值可更大一些;②采用较低的焊速和焊接电压,有利于防止和减小焊缝"马鞍形";③综合考虑,合理选择坡口形状.另外,在焊缝表面不低于母材的情况下,只要将焊缝"马鞍形"的深度控制在一定的范围内,例如深度不超过1mm,则钢管的内焊缝不一定要求消除马鞍形,而应将重点放在控制马鞍形焊缝与母材金属的过渡上.只要焊缝整体均匀,与母材过渡平缓,则允许内焊缝存在一定的马鞍形.3.3焊瘤焊瘤是指焊缝表面的局部凸起现象.其产生的主要原因有:①焊接过程中的焊接规范搭配不当;②焊剂性能不好,粘度过大的焊剂容易产生焊瘤现象;③焊接时使用的焊剂不干净,焊剂中含有氧化铁,焊丝头等杂物,使焊缝局部熔化金属增加,造成焊瘤.防止措施:①选择合适的焊接规范,焊接电流和电压应合理匹配,避免出现焊接电流过大而焊接电压过小的情况;②选用优质的焊剂,并保证焊剂使用过程的清洁.3.4焊缝表面压坑焊缝表面压坑是由于焊接时熔池和熔渣界面处的气泡对即将凝固的熔池金属的压力而产生的.具体原因有:①焊缝附近或焊丝上有较多的油,锈和水,导致焊接时产生大量气体;②焊剂在使用前未按规定烘干以及焊剂较脏,有较多的杂物;③焊剂比重大,熔渣粘度大以及焊剂的堆积高度大,使焊接时产生的气体难以及时排出.防止措施:①选用比重轻,粘度小的烧结焊剂,使用前保证焊剂的烘干和清洁,使用中在不明弧的前提下尽可能减少焊剂堆积高度;②彻底清第29卷第2期罗天宝等:浅谈螺旋埋弧焊钢管的焊缝外观形状控制除焊件和焊丝表面的油,锈和水.3.5焊缝"偏流"焊缝"偏流"产生的主要原因是:①焊点位置不当,焊点偏心距过大或过小;②焊接速度过快,导致液态熔池未结晶就处于较大的坡度位置;③焊剂送给位置不正确,焊剂对熔池的压力不对称.防止措施:①根据管径大小和焊接规范合理选择焊点位置,尽可能使熔池在接近水平的位置完成结晶过程;②以正确方式送给焊剂,减少焊剂送给过程中焊剂对熔池的冲击,焊剂碗最好做成上大下小的形状,以尽可能减少焊剂碗内熔池前部的焊剂流动.3.6焊缝与母材过渡不平缓焊缝与母材过渡不平缓分两种情况.一种是因焊缝余高过大引起的过渡不平缓,其产生的主要原因是焊接参数选择不当,如焊接电流过大,电压过低,焊接速度过快,焊丝后倾角度过大,焊点偏心距过小等,产生细而高的"麻杆"形焊缝;另一种是在焊缝余高不大的情况下,因焊缝过渡角过小而产生的焊缝与母材过渡不平缓,其产生的原因一是焊点偏心距不当而导致焊缝"偏流",二是由于液态金属和焊剂熔渣的表面张力较大,导致焊缝与母材过渡不平缓.此外,焊剂的质量密度,颗粒度及焊接时的堆积高度,焊剂的熔渣粘度等也对焊缝与母材的平缓过渡有重要影响.防止措施:①选择合适的焊剂,保证焊剂颗粒大小适度且均匀,焊接时在保证不出现明弧的情况下尽量降低焊剂的堆积高度,同时保证焊剂清洁;②寻找最佳的焊接规范匹配,采用较低的焊速,较小的焊接电流,配合适当的焊接电压,有利于得到高度低而过渡平缓的焊缝形状;③合理调整焊丝倾角和焊点位置,避免焊缝"偏流".④在厚板的焊接中,采取开坡口的方法,可以有效改善焊缝与母材的过渡.3.7?焊缝形状不均匀或"锯齿形"焊缝焊缝形状不均匀的主要原因有:①由于焊接送丝机构机械故障,送丝轮磨损,焊丝硬弯等引起送丝不均匀,焊接时出现"打点"或焊缝"夹腰"现象;②由于焊接机头刚性不足或连接松动,机头在焊接时发生颤动,引起焊缝形状变化;③由于导电嘴磨损,导致焊接时焊接电流变化,引起焊缝尺寸的变化;④由于钢管成型不良,如管径变化,钢管椭圆,成型缝错边或噘嘴,成型缝问隙变化,大桥摆动等,使得焊接过程不稳定而引起焊缝形状不均匀;⑤在其他条件相同的情况下,当焊接电压较大时,由于电弧的挺度变差,飘移增加,导致焊缝宽度不均匀;⑥电弧磁偏吹引起的电弧摆动.在焊接时,有时还会出现焊缝宽度在短时间内频繁变化的"锯齿形"焊缝,使焊缝形状严重恶化.其产生的原因有:①焊点偏心距过大或过小, 使焊缝产生单边"锯齿形";②如果焊接时焊剂的送给位置不当,焊剂堆积高度过大,会给液态熔池产生较大的冲击力和压力,造成"锯齿形"焊缝. 提高焊缝均匀性的措施有:①搞好设备维护,防止由于焊接送丝不稳,导电嘴磨损,焊接机头不稳等引起的焊缝不均;②提高钢管的成型质量,防止因钢管几何形状变化导致的焊缝形状变化;③使焊点位置和焊剂送给位置保持在最佳状态;④合理确定焊接规范,并保持焊接过程的稳定;⑤防止和减少磁偏吹.4结语从以上分析可以看出,虽然和一般的焊接结构相比,螺旋埋弧焊钢管的螺旋焊缝要获得优质的焊缝外观形状困难会更大一些,但通过合理选择和使用焊接材料,制定最佳的焊接工艺参数,保证钢管的成型稳定,螺旋埋弧焊钢管完全可以获得高度低,与母材过渡平缓,整齐美观的优良焊缝,充分满足客户对钢管的质量要求.参考文献:[1]陈祝年.焊接工程师手册[M].北京:机械工业出版社,2002.[2]中国机械工程协会焊接学会.焊接手册,焊接方法及设备,第卷[M].北京:机械工业出版社,2001.[3]JB/T7949--1999,钢结构焊缝外形尺寸[s].[4]Q/SYXQ14--2002,西气东输工程用螺旋缝埋弧焊钢管技术条件[s].『5]GB/T9711.2—1999,石油天然气工业输送钢管交货技术条件第2部分:B级钢管[s].作者简介:罗天宝(1966一),男,工程师,长期从事螺旋埋弧焊管生产的37_艺技术和管理工作.收稿Et期:2005—1O一12编辑:罗刚。
螺旋埋弧焊管外焊缝形状控制技术探讨

中 图分类 号:G 4 T 45
文献 标志码 : B
文 章编 号:0 13 3 (0 20 —0 6 0 10 —9 82 1)2 0 5— 6
Dic s i n o Co r lOu sde W ed o l fS s u so n nt o t i l Pr f e o AW H p i Pi e
f r a d a k n f p c a t o f t i n g e i o to r li g a d t o se l i gt mp o ewed p o l , o w r i d o e ilmeh d o i z g ma n t c n rla cwed n n w — tp wed n i rv l rf e s u li c o i S st e e r q i me t u sd l r f ef m i ec ai g Oa me t h u r o t e e n st o t ewed p o l o p p o t . o i i r n Ke r s S W H i e wed fr n ; c e tii ; b i u t ; l i gf x b v l y wo d : A p p ; l mi g e c n r t o l i wed n u ; e e o cy q y l
疲 劳失 效 。另 外 ,随着 3 E和 F E防腐 技 术 的 P B
采 用 ,对 螺 旋 埋 弧 焊 管 焊 缝 形 状 同 样 提 出 了 更 高 的 要 求 。如 西 气 东 输 工 程 等 条 件 中要 求 外 焊 缝余 高 控
W ANG i1 Ha .i
(h n ogS egi S ad n h nl
z PC . Ld , io2 5 8 , hn og h a 砷 o, t. Zb 5 02 S ad n ,C i ) n
螺旋缝埋弧焊钢管焊接方法-概述说明以及解释

螺旋缝埋弧焊钢管焊接方法-概述说明以及解释1.引言1.1 概述概述部分是文章引言的一部分,该部分主要对螺旋缝埋弧焊钢管焊接方法进行简要介绍和概括。
以下是可能的内容:螺旋缝埋弧焊钢管焊接方法是一种广泛应用于钢管制造和施工领域的焊接技术。
它通过使用螺旋缝埋弧焊设备,将电极自动供给并在焊接过程中形成一个连续的螺旋缝,将钢管焊接在一起。
这种方法可以用于焊接各种类型的钢管,包括长焊缝和大直径钢管。
螺旋缝埋弧焊钢管焊接方法具有一些独特的特点和优势。
首先,它可以实现连续高效的焊接,提高生产效率。
其次,该方法可以在较大直径和较长长度的钢管上进行焊接,适用于各种工程项目。
此外,螺旋缝埋弧焊钢管焊接方法还具有较高的焊接质量和可靠性,焊接接头具有良好的力学性能和耐腐蚀性能。
然而,螺旋缝埋弧焊钢管焊接方法也存在一些局限性和挑战。
其中一个挑战是焊接设备和操作的复杂性,需要专业技术人员进行操作和维护。
此外,在焊接过程中还需要对工艺参数进行严格控制,以确保焊接质量。
因此,掌握螺旋缝埋弧焊钢管焊接方法的基本原理和工艺参数非常重要。
本文将详细介绍螺旋缝埋弧焊钢管焊接方法的基本原理、工艺参数以及优缺点。
通过对该方法的深入研究和了解,可以更好地应用和控制螺旋缝埋弧焊钢管焊接方法,提高焊接质量和效率,推动其进一步发展和应用。
1.2 文章结构本文将从以下几个方面来详细介绍螺旋缝埋弧焊钢管焊接方法:螺旋缝埋弧焊钢管焊接方法的基本原理、螺旋缝埋弧焊钢管焊接方法的工艺参数以及螺旋缝埋弧焊钢管焊接方法的优缺点。
首先,在第二章的正文部分,将详细介绍螺旋缝埋弧焊钢管焊接方法的基本原理。
这包括焊接过程中的电弧传递方式、熔池形成和冷却过程等关键步骤。
通过对基本原理的深入解析,读者可以对螺旋缝埋弧焊钢管焊接方法的工作原理有一个全面的认识。
其次,本文将探讨螺旋缝埋弧焊钢管焊接方法的工艺参数。
这部分内容将介绍焊接电流、焊接速度、电弧间隙等工艺参数的选择与调整原则。
螺旋焊管内焊双丝焊装置的设计与应用
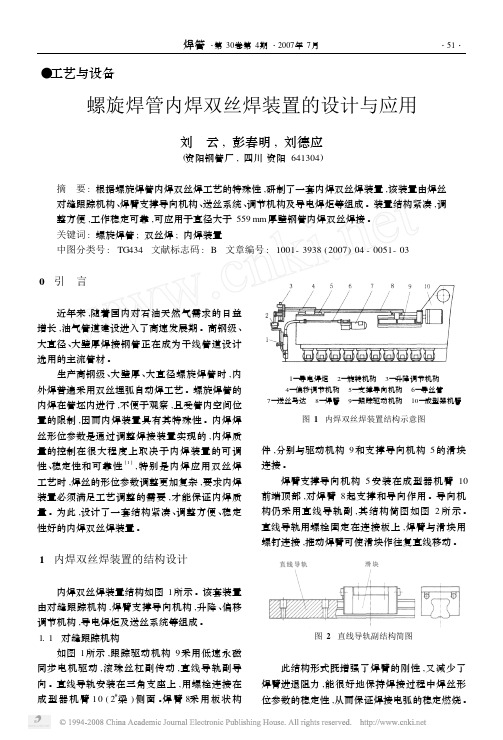
焊管 ·第 30卷第 4期 ·2007年 7月
·51·
螺旋焊管内焊双丝焊装置的设计与应用
刘 云 , 彭春明 , 刘德应
(资阳钢管厂 , 四川 资阳 641304)
摘 要 : 根据螺旋焊管内焊双丝焊工艺的特殊性 ,研制了一套内焊双丝焊装置 ,该装置由焊丝 对缝跟踪机构 、焊臂支撑导向机构 、送丝系统 、调节机构及导电焊炬等组成 。装置结构紧凑 ,调 整方便 ,工作稳定可靠 ,可应用于直径大于 559 mm 厚壁钢管内焊双丝焊接 。 关键词 : 螺旋焊管 ; 双丝焊 ; 内焊装置 中图分类号 : TG434 文献标志码 : B 文章编号 : 1001- 3938 (2007) 04 - 0051- 03
0 引 言
近年来 ,随着国内对石油天然气需求的日益 增长 ,油气管道建设进入了高速发展期 。高钢级 、 大直径 、大壁厚焊接钢管正在成为干线管道设计 选用的主流管材 。
生产高钢级 、大壁厚 、大直径螺旋焊管时 ,内 外焊普遍采用双丝埋弧自动焊工艺 。螺旋焊管的 内焊在管坯内进行 ,不便于观察 ,且受管内空间位 置的限制 ,因而内焊装置具有其特殊性 。内焊焊 丝形位参数是通过调整焊接装置实现的 ,内焊质 量的控制在很大程度上取决于内焊装置的可调 性 、稳定性和可靠性 [ 1 ] ,特别是内焊应用双丝焊 工艺时 ,焊丝的形位参数调整更加复杂 ,要求内焊 装置必须满足工艺调整的需要 ,才能保证内焊质 量 。为此 ,设计了一套结构紧凑 、调整方便 、稳定 性好的内焊双丝焊装置 。
1. 3 升降调节机构 图 1中升降调节机构 3设计成手动丝杠 、双
柱导向结构 ,通过旋转机构与导电焊炬连接 。通 过手动调节丝杠 ,可使导电焊炬沿垂直方向上下 移动 ,从而实现对焊丝伸出长度的调整 。该调节 机构只负责对焊丝伸长量一个形位参数的调整 。 1. 4 旋转机构
螺旋缝埋弧焊钢管工艺过程
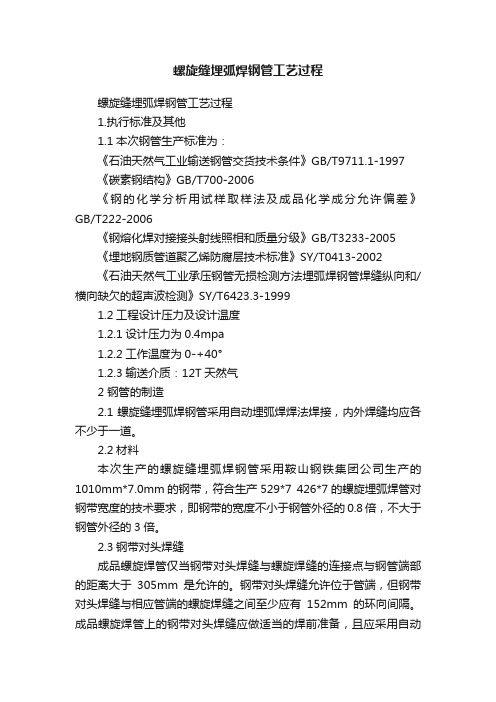
螺旋缝埋弧焊钢管工艺过程螺旋缝埋弧焊钢管工艺过程1.执行标准及其他1.1本次钢管生产标准为:《石油天然气工业输送钢管交货技术条件》GB/T9711.1-1997《碳素钢结构》GB/T700-2006《钢的化学分析用试样取样法及成品化学成分允许偏差》GB/T222-2006《钢熔化焊对接接头射线照相和质量分级》GB/T3233-2005《埋地钢质管道聚乙烯防腐层技术标准》SY/T0413-2002《石油天然气工业承压钢管无损检测方法埋弧焊钢管焊缝纵向和/横向缺欠的超声波检测》SY/T6423.3-19991.2工程设计压力及设计温度1.2.1设计压力为0.4mpa1.2.2工作温度为0-+40°1.2.3输送介质:12T天然气2 钢管的制造2.1螺旋缝埋弧焊钢管采用自动埋弧焊焊法焊接,内外焊缝均应各不少于一道。
2.2材料本次生产的螺旋缝埋弧焊钢管采用鞍山钢铁集团公司生产的1010mm*7.0mm的钢带,符合生产529*7 426*7的螺旋埋弧焊管对钢带宽度的技术要求,即钢带的宽度不小于钢管外径的0.8倍,不大于钢管外径的3倍。
2.3钢带对头焊缝成品螺旋焊管仅当钢带对头焊缝与螺旋焊缝的连接点与钢管端部的距离大于305mm是允许的。
钢带对头焊缝允许位于管端,但钢带对头焊缝与相应管端的螺旋焊缝之间至少应有152mm的环向间隔。
成品螺旋焊管上的钢带对头焊缝应做适当的焊前准备,且应采用自动埋弧焊、自动熔化极气体保护电弧焊或这些焊接工艺的复合焊焊接。
允许将钢带对头焊缝的余高铣去,但铣削处焊缝原始表面不得低于母材表面。
2.4不允许对焊接长钢管2.5钢的种类钢管应采用GB/T700中的Q235B钢焊制。
2.6可追溯性制造厂应制定并遵循保持熔炼批和/或批标识的控制程序,直至表明所有要求的熔炼批和/或批实验已进行且复合标准要求为止。
第二节 埋弧焊设备的结构和工作原理

第二节埋弧焊设备的结构和工作原理一、埋弧焊电源一般埋弧焊多采用粗焊丝,电弧具有水平的静特性曲线。
按照前述电弧稳定燃烧的要求,电源应具有下降的外特性。
在用细焊丝焊薄板时,电弧具有上升的静特性曲线,宜采用平特性电源。
埋弧焊电源可以用交流(弧焊变压器)、直流(弧焊发电机或弧焊整流器)或交直流并用。
要根据具体的应用条件,如焊接电流范围、单丝焊或多丝焊、焊接速度、焊剂类型等选用。
一般直流电源用于小电流范围、快速引弧、短焊缝、高速焊接,所采用焊剂的稳弧性较差及对焊接工艺参数稳定性有较高要求的场合。
采用直流电源时,不同的极性将产生不同的工艺效果。
当采用直流正接(焊丝接负极)时,焊丝的熔敷率最高;采用直流反接(焊丝接正极)时,焊缝熔深最大。
采用交流电源时,焊丝熔敷率及焊缝熔深介于直流正接和反接之间,而且电弧的磁偏吹最小。
因而交流电源多用于大电流埋弧焊和采用直流时磁偏吹严重的场合。
一般要求交流电源的空载电压在65V以上。
为了加大熔深并提高生产率,多丝埋弧自动焊得到越来越多的工业应用。
目前应用较多的是双丝焊和三丝焊。
多丝焊的电源可用直流或交流,也可以交、直流联用。
双丝埋弧焊和三丝埋弧焊时焊接电源的选用及联接有多种组合。
二、埋弧焊机埋弧焊机分为自动焊机和半自动焊机两大类。
(一)半自动埋弧焊机半自动埋弧焊机的主要功能是:(1)将焊丝通过软管连续不断地送入电弧区;(2)传输焊接电流;(3)控制焊接起动和停止;(4)向焊接区铺施焊剂。
因此它主要由送丝机构、控制箱、带软管的焊接手把及焊接电源组成。
软管式半自动埋弧焊机兼有自动埋弧焊的优点及手工电弧焊的机动性。
在难以实现自动焊的工件上(例如中心线不规则的焊缝、短焊缝、施焊空间狭小的工件等),可用这种焊机进行焊接。
(二)自动埋弧焊机自动埋弧焊机的主要功能是;(1)连续不断地向焊接区送进焊丝;(2)传输焊接电流;(3)使电弧沿接缝移动;(4)控制电弧的主要参数;(5)控制焊接的起动与停止;(6)向焊接区铺施焊剂;(7)焊接前调节焊丝端位置。
- 1、下载文档前请自行甄别文档内容的完整性,平台不提供额外的编辑、内容补充、找答案等附加服务。
- 2、"仅部分预览"的文档,不可在线预览部分如存在完整性等问题,可反馈申请退款(可完整预览的文档不适用该条件!)。
- 3、如文档侵犯您的权益,请联系客服反馈,我们会尽快为您处理(人工客服工作时间:9:00-18:30)。
设计2开发43螺旋缝埋弧焊管内外自动焊焊枪结构设计王爱玲',方天一2(1.辽阳石油钢管制造有限公司,辽宁辽阳111003; 2.吉林华信新型结构科技有限公司,吉林磐石132301)摘要:介绍传统焊枪和新设计埋弧焊管内外自动焊焊枪的结构.分析新型埋弧焊枪的工作原理,对比两种焊枪在生产中的应用情况。
分析认为:与传统焊枪相比,新设计的埋弧焊枪能始终保证焊丝与导电嘴一侧接触,保证焊接时焊丝的位置稳定,通过风冷可以有效降低焊丝温度,同样工况下提高了焊缝形貌及理化性能结果。
新设计的焊枪结构仍存在短板,无法针对多丝焊进行调节;焊接内径较大的焊管时,利用传导机构调节内焊丝位置较容易,管径小时则不易操作。
建议与自动化测量技术相结合,根据导电嘴损耗自动调节焊丝位置,避免因忘记手动操作或位置局限难操作等引起的焊丝位置偏离而造成的产品质量问题。
关键词:焊接钢管;焊枪;自动焊;结构;设计中图分类号:TG434文献标志码:B文章编号:1001-2311(2019)01-0043-05Design of Structure of Welding Torchfor Automatic Internal/External Welding of HSAW PipeWANG Ailing1,FANG Tianyi2(1.Liaoyang Petroleum Steel Pipe Manufacturing Co.,Ltd.,Liaoyang111003,China;2.Jilin Huaxin New Structure Technology Co.,Ltd.,Panshi132301,China)Abstract:Described are the structures of the conventional welding torch and the newly-designed welding torch for automatic intemal/extemal welding of the HSAW pipe.Analyzed is the operational principle of the pared are the industrial application statuses of the said two torches.The analysis reveals that compared with the conventional welding torch,the newly-designed welding torch for the HSAW pipe is capable of ensuring that the welding wire keeps in any case contacting the tip side,and the welding wire is stably positioned during the operation process.It is also revealed that the welding wire temperature can be obviously lowered down via air-cooling so as to enhance the morphology and physiochemical properties given that the working conditions remain the same.Nevertheless the new welding torch has its short comings,for instance,in case of multi-wire welding,no adjustment can be made,and when welding pipes with rather large ID,it is rather easy to adjust the welding wire position with the conduction mechanism,whereas in case of welding smallsized pipes,it is not so easy to manage the same thing.Therefore it is suggested to combine the automatic measurement technology to get the welding wire position adjusted automatically as per the current contact tip loss so as to prevent any product quality problem as caused by deviation of the welding wire position as resulting from forgetting manual operation or failing to operate due to location limitation.Key words:weld pipe;welding torch;automatic welding;structure;design埋弧焊是一种电弧在焊剂层下燃烧进行焊接的方法⑴,具有焊接质量稳定、焊接生产效率高、无弧光及烟尘少等优点。
在埋弧焊过程中,传统的焊王爱玲(1970-),女,工程师,主要从事石油钢管生产的焊接工艺及质量管理工作。
枪利用导电嘴把焊接电源的能量导入到焊丝上,并通过电弧,把焊接线能量输入到钢管焊缝的熔池之中⑵;但在实际生产中传统焊枪上的导电嘴容易磨损,从而导致焊丝卡壳或高温。
本文主要介绍一种新型埋弧焊枪,分析新型埋弧焊枪的工作原理,并对比其与传统埋弧焊枪在试验生产中的应用情况。
STEEL PIPE Feb.2019,Vol.48,No.1钢管2019年2月第48卷第1期44设计2开发1传统焊枪结构螺旋缝埋弧焊管要求焊接连续性高,且熔池形态稳定,否则容易引起焊接缺陷及影响焊缝性能,所以焊枪上的导电嘴负责把焊接线能量稳定输入到 熔池之中,焊枪的作用至关重要。
但传统焊枪上的导电嘴在实际生产中容易磨损,从而导致焊丝卡壳或高温⑷。
传统焊枪结构如图1所示。
1 — 1号焊头2—接头3 —导电杆4—连接螺栓5—螺母6 —导电嘴图1传统焊枪结构示意2新埋弧焊枪结构设计为解决螺旋缝埋弧焊管实际生产中传统焊枪焊 接过程中遇到的问题,设计焊枪结构,保证螺旋缝埋弧焊钢管过程中的焊缝质量。
新设计的新型埋弧焊枪结构如图2所示,其特 征是:芯杆的顶部固定在底座上,芯杆内设有供焊丝通过的轴向通道,底座顶部有供焊丝通过的孔, 底座顶部的孔与芯杆的轴向通道相连通,还包括导电连接板,调整连接板通过螺钉固定在导电连接板 上,导电连接板和调整连接板上都设有供芯杆通过的孔,调整连接板上固定有立板,带有台肩的调整 螺栓的前端固定在底座上,调整螺栓的后端从立板中伸出,伸岀部分上装有调整手柄,调整螺栓上套设有矩形圆弹簧,矩形圆弹簧的前端顶在调整螺栓的台肩上,矩形圆弹簧的后端顶在立板上,底座上设有销轴,调整连接板上设有与底座上销轴相配合的瓦座;导电连接板的底部固定有空心的导电连接杆,导电嘴安装在压帽上,压帽与导电连接杆的底 部螺纹连接,芯杆经调整连接板、导电连接板进入到导电连接杆内,芯杆左半部分的长度小于右半部 分的长度,芯杆左半部分的底端位于导电连接杆内,芯杆右半部分则伸入到导电嘴内。
同时在导电 连接杆上设与其中间空心部分相连通的冷却风道。
1—底座2—芯杆3—轴向通道4 —连接板5—导电连接板6—冷却风道7 —导电嘴8—压帽9—导电连接杆10 —螺钉11 —瓦座 12—销轴13—调整手柄14—立板15—矩形圆弹簧16—调整螺栓图2新型埋弧焊枪结构示意3新设计的埋弧焊枪工作原理当焊丝与导电嘴的通孔之间间隙大时,拧动调 整手柄,使调整连接板和导电连接板围绕底座上的销轴进行摆动,芯杆支撑焊丝固定不动,确保焊丝出离导电嘴后方向不变,焊丝输出中心始终不发生变化,不会出现焊偏现象及因焊丝偏差而产生的焊丝卡壳问题,并能保证导电嘴导电稳定,焊接熔深 稳定,焊接效果好。
由于在导电连接杆上设有冷却风道,所以可对导电连接杆和导电嘴降温,从而降低焊丝温度,达到同等焊接规范下熔深最大,且减少了电能消耗。
4两种焊枪在试验生产中的应用情况4.1钢管生产线简介加工产品规范水平PSL2、材质A25-X100,直径406-1 422 mm 、壁厚6.0-25.4 mm 的各种规格 螺旋缝埋弧焊管。
焊接设备主要由焊接电源(1INCOLN 焊机、US 控制系统)、控制箱、送丝装 置、焊头装置、跟踪装置和调整机构组成。
焊接电源采用数字电源,可采用内、外3丝及以上进行焊 接,该机组的焊接部分基本实现自动化,并使用激光焊缝自动跟踪系统,能实现内、外焊焊头的自动 定位、监视功能。
STEEL PIPE Feb. 2019, Vol. 48, No.1设计2开发454.2生产钢管基本信息对使用新设计的焊枪与传统焊枪生产钢管进行对比试验,生产钢管基本信息见表1。
表1生产钢管基本信息钢级规格/mm直径壁厚焊接方式焊丝数量执行标准L245M1 422 14内外埋弧焊接各1丝API Spec 5L —20124.3两种焊枪生产情况在使用内外焊缝自动跟踪系统情况下,两种焊 枪均重新更换同材质导电嘴,每种焊枪在同一钢管机组上分别连续生产50 h,按照表1基本信息生产钢管,每种焊枪生产钢管各60根,每根钢管长度大约12 m 。
4.3.1内外焊缝焊偏量对比第一组试验:选取新型焊枪与传统焊枪分别生产的前10根钢管,因前10根钢管导电嘴基本无磨损。
按照API Spec 5L —2012要求,在每根钢管上取3个内外焊缝焊偏试样,取测量结果平均值进行记录,每种焊枪分别记录10组焊偏试验数据。
传统焊枪与新设计焊枪内外焊缝焊偏量见表2,对比如图3所示。
表2传统焊枪与新型焊枪内外焊缝焊偏量 mm项目最小值最大值平均值标准差传统焊枪0.60 1.70 1.100.35新型焊枪0.201.200.810.36新型焊枪焊偏值Y1传统焊枪焊偏值图3新型焊枪与传统焊枪内外焊缝焊偏量对比第二组试验:每种焊枪生产的钢管按照导电嘴使用的焊接时间进行取样,按照API Spec 5L —2012 要求,每偶数小时分别在两种焊枪焊接的钢管上随机各抽取3个焊偏试样,取平均值进行记录,在两 个焊枪上的导电嘴使用时间达到20 h 后,焊偏量随导电嘴使用时间变化量如图4所示。