液压系统的设计步骤与设计要求
液压系统设计小结
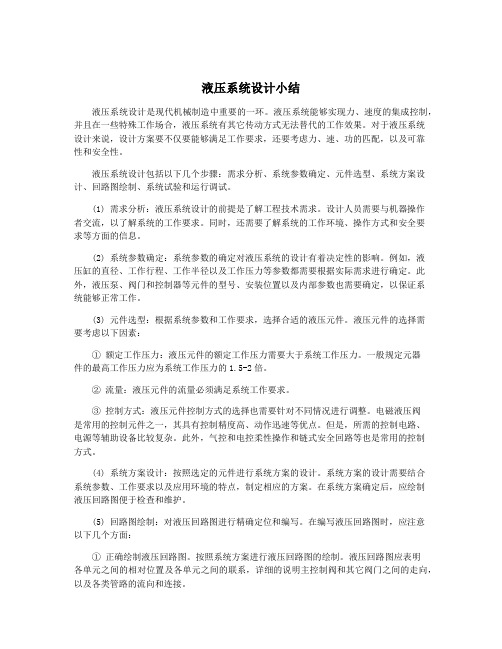
液压系统设计小结液压系统设计是现代机械制造中重要的一环。
液压系统能够实现力、速度的集成控制,并且在一些特殊工作场合,液压系统有其它传动方式无法替代的工作效果。
对于液压系统设计来说,设计方案要不仅要能够满足工作要求,还要考虑力、速、功的匹配,以及可靠性和安全性。
液压系统设计包括以下几个步骤:需求分析、系统参数确定、元件选型、系统方案设计、回路图绘制、系统试验和运行调试。
(1) 需求分析:液压系统设计的前提是了解工程技术需求。
设计人员需要与机器操作者交流,以了解系统的工作要求。
同时,还需要了解系统的工作环境、操作方式和安全要求等方面的信息。
(2) 系统参数确定:系统参数的确定对液压系统的设计有着决定性的影响。
例如,液压缸的直径、工作行程、工作半径以及工作压力等参数都需要根据实际需求进行确定。
此外,液压泵、阀门和控制器等元件的型号、安装位置以及内部参数也需要确定,以保证系统能够正常工作。
(3) 元件选型:根据系统参数和工作要求,选择合适的液压元件。
液压元件的选择需要考虑以下因素:① 额定工作压力:液压元件的额定工作压力需要大于系统工作压力。
一般规定元器件的最高工作压力应为系统工作压力的1.5-2倍。
② 流量:液压元件的流量必须满足系统工作要求。
③ 控制方式:液压元件控制方式的选择也需要针对不同情况进行调整。
电磁液压阀是常用的控制元件之一,其具有控制精度高、动作迅速等优点。
但是,所需的控制电路、电源等辅助设备比较复杂。
此外,气控和电控柔性操作和链式安全回路等也是常用的控制方式。
(4) 系统方案设计:按照选定的元件进行系统方案的设计。
系统方案的设计需要结合系统参数、工作要求以及应用环境的特点,制定相应的方案。
在系统方案确定后,应绘制液压回路图便于检查和维护。
(5) 回路图绘制:对液压回路图进行精确定位和编写。
在编写液压回路图时,应注意以下几个方面:① 正确绘制液压回路图。
按照系统方案进行液压回路图的绘制。
机械工程中的液压系统设计规范要求
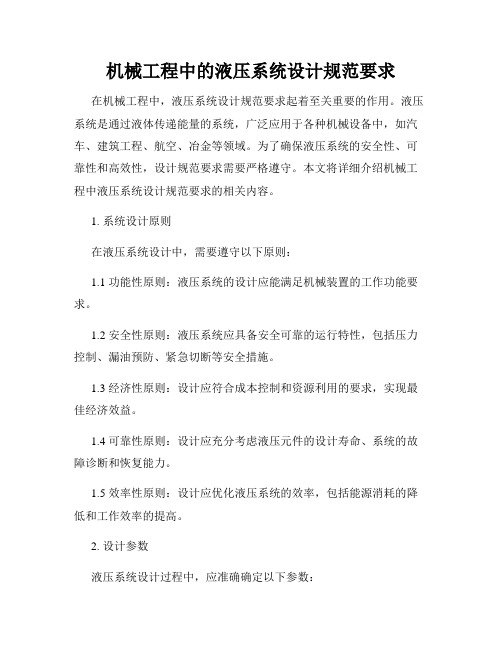
机械工程中的液压系统设计规范要求在机械工程中,液压系统设计规范要求起着至关重要的作用。
液压系统是通过液体传递能量的系统,广泛应用于各种机械设备中,如汽车、建筑工程、航空、冶金等领域。
为了确保液压系统的安全性、可靠性和高效性,设计规范要求需要严格遵守。
本文将详细介绍机械工程中液压系统设计规范要求的相关内容。
1. 系统设计原则在液压系统设计中,需要遵守以下原则:1.1 功能性原则:液压系统的设计应能满足机械装置的工作功能要求。
1.2 安全性原则:液压系统应具备安全可靠的运行特性,包括压力控制、漏油预防、紧急切断等安全措施。
1.3 经济性原则:设计应符合成本控制和资源利用的要求,实现最佳经济效益。
1.4 可靠性原则:设计应充分考虑液压元件的设计寿命、系统的故障诊断和恢复能力。
1.5 效率性原则:设计应优化液压系统的效率,包括能源消耗的降低和工作效率的提高。
2. 设计参数液压系统设计过程中,应准确确定以下参数:2.1 流量参数:根据工作条件和预测的流量需求,确定设计流量。
2.2 压力参数:根据工作条件和对系统安全和效率的要求,确定设计压力。
2.3 温度参数:根据操作环境和液压元件的温度特性,确定设计温度范围。
2.4 运动速度参数:根据运动要求和机械装置的特性,确定设计速度范围。
2.5 液体特性参数:根据工作介质的黏度、温度和污染程度等,确定液体特性参数。
3. 设备选择和安装3.1 正确的元件选择:根据设计参数和系统要求,选择适合的液压元件,如泵、阀和执行元件等。
3.2 安装要求:液压元件的安装应符合相关标准和规范,保证密封性和稳定性。
3.3 布局设计:液压系统的元件应合理布局,保证流动性和安全性。
4. 系统控制和调试4.1 控制方式:根据工作要求,选择合适的液压控制方式,如手动控制、自动控制和比例控制等。
4.2 液压回路设计:根据工作功能,确定液压回路的组成和连接方式。
4.3 控制单元设计:合理选择和安装控制单元,如液压泵和阀等,确保系统的稳定性和可靠性。
液压系统的设计

液压系统的设计液压系统设计是液压主机设计的重要组成部分,也是对前面各章内容的概括总结和综合应用。
本章主要阐述液压系统设计的一般步骤,设计内容和设计计算方法,并通过实例来说明液压系统的设计过程。
9.1 液压系统的设计步骤液压系统设计与主机的设计是紧密联系的,两者往往同时进行,互相协调。
设计液压系统时应首先明确主机对液压系统在动作、性能、工作环境等方面的要求,如执行元件的运动方式、行程、调速范围、负载条件、运行平稳性和精度、工作循环及周期、工作环境、安装空间大小、结构简单、工作安全可靠、效率高、使命寿命长、经济性好、使用维修方便等设计原则。
液压系统设计步骤大体上可按图9-1所示的内容和流程进行。
这里除了最后一项(8)外,均属性能设计范围。
这些步骤是相互关联,相互影响的,必须经反复修改才能完成。
设计步骤及方法介绍如下。
9.1.1 明确系统的设计要求设计液压系统时,首先要对液压主机的工况进行分析,明确主机对液压系统的要求,具体包括:1)主机的用途、主体布局、对液压装置的位置和空间尺寸的限制。
2)主机的工作循环,液压系统应完成的动作、动作顺序或互锁要求,以及自动化程度的要求。
3)液压执行元件的负载和运动速速的大小及其变化范围,运动平稳性、定位精度及转化精度等的要求。
4)液压系统的工作环境和工作条件。
5)工作效率、安全性、可靠性及经济性等要求。
9.1.2 分析系统工况,确定主要参数1.工况分析工况分析,就是分析主机在工作过程中各执行元件的运动速度和负载的变化规律。
它是拟定液压系统方案,选择或设计液压元件的依据。
工况分析包括动力参数分析和运动参数分析两个部分,即:1)动力参数分析就是通过计算液压执行元件的载荷大小和方向,并分析各执行元件在工作过程中可能产生的冲击、振动及过载等。
对于动作较复杂的机械设备,根据工艺要求,将各执行元件在各阶段所需克服的负载用图9-2a所示的负载-位移(F-L)曲线表示,称为负载图。
液压课程设计设计要求
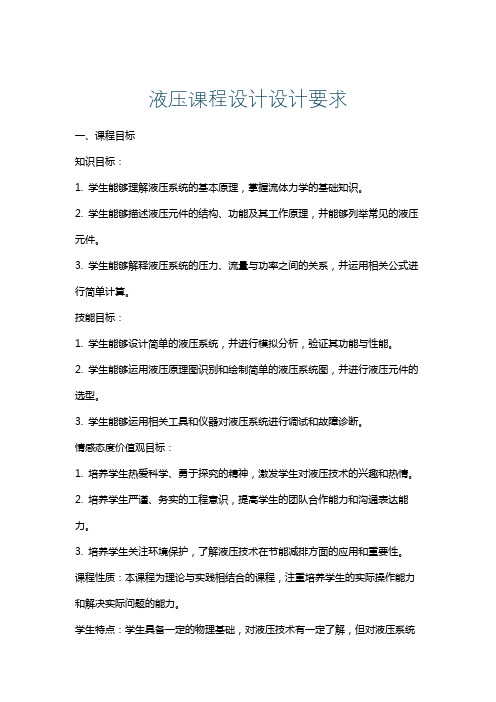
液压课程设计设计要求一、课程目标知识目标:1. 学生能够理解液压系统的基本原理,掌握流体力学的基础知识。
2. 学生能够描述液压元件的结构、功能及其工作原理,并能够列举常见的液压元件。
3. 学生能够解释液压系统的压力、流量与功率之间的关系,并运用相关公式进行简单计算。
技能目标:1. 学生能够设计简单的液压系统,并进行模拟分析,验证其功能与性能。
2. 学生能够运用液压原理图识别和绘制简单的液压系统图,并进行液压元件的选型。
3. 学生能够运用相关工具和仪器对液压系统进行调试和故障诊断。
情感态度价值观目标:1. 培养学生热爱科学、勇于探究的精神,激发学生对液压技术的兴趣和热情。
2. 培养学生严谨、务实的工程意识,提高学生的团队合作能力和沟通表达能力。
3. 培养学生关注环境保护,了解液压技术在节能减排方面的应用和重要性。
课程性质:本课程为理论与实践相结合的课程,注重培养学生的实际操作能力和解决实际问题的能力。
学生特点:学生具备一定的物理基础,对液压技术有一定了解,但对液压系统的设计与应用尚处于起步阶段。
教学要求:教师应结合课本内容,注重理论与实践相结合,通过案例分析、实验操作等教学手段,帮助学生达到课程目标。
同时,关注学生的个体差异,鼓励学生积极参与,培养学生的自主学习能力。
在教学过程中,将课程目标分解为具体的学习成果,以便进行有效的教学设计和评估。
二、教学内容1. 液压系统原理:流体力学基础,液压系统工作原理,液压油性质与选用。
教材章节:第一章 液压系统概述2. 液压元件:液压泵、液压马达、液压缸、控制阀等元件的结构、功能及工作原理。
教材章节:第二章 液压元件3. 液压系统设计:液压系统设计步骤,系统压力、流量计算,液压元件选型。
教材章节:第三章 液压系统设计4. 液压系统模拟与仿真:运用专业软件进行液压系统模拟分析,验证系统性能。
教材章节:第四章 液压系统模拟与仿真5. 液压系统调试与故障诊断:液压系统调试方法,常见故障现象、原因及排除方法。
挖掘机液压系统设计

挖掘机液压系统设计挖掘机作为一种重型工程机械,广泛应用于土木工程、水利工程、矿山工程等领域。
其液压系统作为重要的动力传递和控制装置,对挖掘机的工作效率和性能起着至关重要的作用。
因此,挖掘机液压系统设计至关重要。
一、液压系统工作原理在挖掘机液压系统中,液压泵将机器的动力转换为液压能,通过管道输送至液压缸或液压马达,驱动斗杆、斗杆缸、斗杆滑板等机械部件运动。
同时,通过液压控制阀的调节,实现对液压系统的控制,如液压油的流量、压力等参数,从而控制挖掘机的动作。
二、液压系统设计要求1. 稳定性:挖掘机在工作时需要承受较大的载荷和冲击,因此液压系统设计要求稳定可靠,能够保证机器正常运行。
2. 效率:高效的液压系统设计可以提高挖掘机的工作效率,减少能源消耗,降低运行成本。
3. 灵活性:液压系统设计要求机器动作灵活,能够满足不同工况下的要求,提高挖掘机的适应性和操作性。
4. 安全性:液压系统设计应具备良好的安全性能,确保挖掘机在工作过程中不发生液压系统故障及相关事故。
三、液压系统设计步骤1. 确定液压系统工作压力:根据挖掘机的工作负荷和工作环境确定液压系统的工作压力,以保证系统正常工作。
2. 选择液压元件:根据液压系统的压力、流量等参数选择适合的液压泵、液压缸、液压马达等元件。
3. 设计液压管路:设计合理的液压管路,保证液压油的快速输送和减小压力损失,提高系统效率。
4. 配置液压控制阀:根据挖掘机的工作要求配置液压控制阀,实现对挖掘机动作的精确控制。
5. 系统集成测试:完成液压系统设计后进行系统集成测试,验证系统的稳定性、效率和安全性。
四、优化液压系统设计1. 采用先进的液压技术:挖掘机液压系统设计可以采用先进的液压技术,如负载敏感控制、节流阀控制等,提高系统的性能和效率。
2. 应用智能化控制:结合电子控制技术,实现液压系统的智能化控制,提高挖掘机的自动化程度和操作便利性。
3. 优化系统布局:合理布置液压元件和管路,减小系统的体积和重量,提高挖掘机的运行效率和操作舒适性。
液压系统研制实施方案
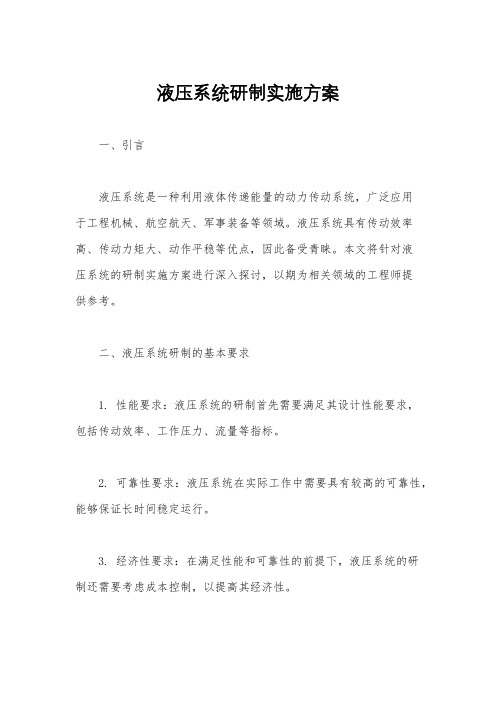
液压系统研制实施方案一、引言液压系统是一种利用液体传递能量的动力传动系统,广泛应用于工程机械、航空航天、军事装备等领域。
液压系统具有传动效率高、传动力矩大、动作平稳等优点,因此备受青睐。
本文将针对液压系统的研制实施方案进行深入探讨,以期为相关领域的工程师提供参考。
二、液压系统研制的基本要求1. 性能要求:液压系统的研制首先需要满足其设计性能要求,包括传动效率、工作压力、流量等指标。
2. 可靠性要求:液压系统在实际工作中需要具有较高的可靠性,能够保证长时间稳定运行。
3. 经济性要求:在满足性能和可靠性的前提下,液压系统的研制还需要考虑成本控制,以提高其经济性。
三、液压系统研制的技术方案1. 液压元件的选型:液压系统的研制首先需要根据设计要求选择合适的液压元件,包括液压泵、液压阀、液压缸等。
在选型时需要考虑元件的性能、品质、价格等因素。
2. 液压系统的布局设计:液压系统的布局设计需要考虑元件之间的连接方式、管路的布置方式、油箱的容积等因素,以保证系统的紧凑性和稳定性。
3. 液压系统的控制策略:液压系统的研制还需要考虑控制策略的制定,包括开环控制、闭环控制、比例控制等方式,以实现对系统的精准控制。
4. 液压系统的试制与调试:在研制过程中需要进行系统的试制与调试工作,以验证设计方案的可行性,并对系统进行性能优化。
四、液压系统研制的实施步骤1. 确定研制目标:明确液压系统的使用环境、工作条件、性能要求等,为研制工作奠定基础。
2. 设计方案制定:根据研制目标,制定液压系统的设计方案,包括选型、布局、控制策略等内容。
3. 元件采购与加工:根据设计方案,采购所需的液压元件,并进行加工制造。
4. 系统组装与调试:将液压元件进行组装,并进行系统的调试工作,验证系统的性能。
5. 系统性能测试:对研制的液压系统进行性能测试,以验证其满足设计要求。
6. 系统优化与改进:根据性能测试结果,对系统进行优化与改进,以提高其性能和可靠性。
液压系统设计规范要求
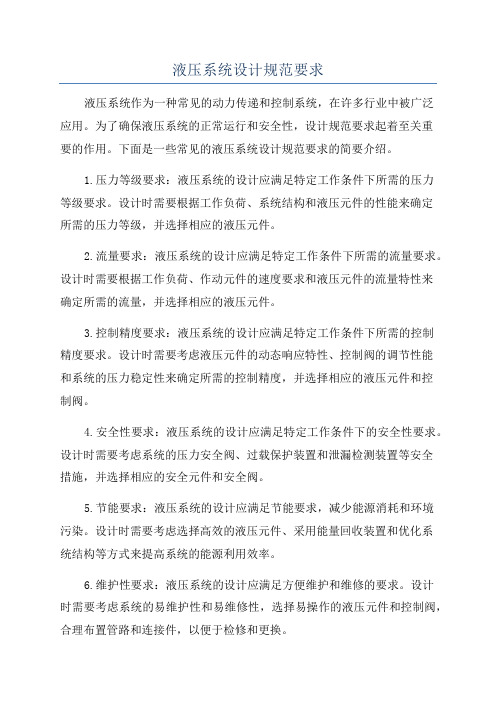
液压系统设计规范要求液压系统作为一种常见的动力传递和控制系统,在许多行业中被广泛应用。
为了确保液压系统的正常运行和安全性,设计规范要求起着至关重要的作用。
下面是一些常见的液压系统设计规范要求的简要介绍。
1.压力等级要求:液压系统的设计应满足特定工作条件下所需的压力等级要求。
设计时需要根据工作负荷、系统结构和液压元件的性能来确定所需的压力等级,并选择相应的液压元件。
2.流量要求:液压系统的设计应满足特定工作条件下所需的流量要求。
设计时需要根据工作负荷、作动元件的速度要求和液压元件的流量特性来确定所需的流量,并选择相应的液压元件。
3.控制精度要求:液压系统的设计应满足特定工作条件下所需的控制精度要求。
设计时需要考虑液压元件的动态响应特性、控制阀的调节性能和系统的压力稳定性来确定所需的控制精度,并选择相应的液压元件和控制阀。
4.安全性要求:液压系统的设计应满足特定工作条件下的安全性要求。
设计时需要考虑系统的压力安全阀、过载保护装置和泄漏检测装置等安全措施,并选择相应的安全元件和安全阀。
5.节能要求:液压系统的设计应满足节能要求,减少能源消耗和环境污染。
设计时需要考虑选择高效的液压元件、采用能量回收装置和优化系统结构等方式来提高系统的能源利用效率。
6.维护性要求:液压系统的设计应满足方便维护和维修的要求。
设计时需要考虑系统的易维护性和易维修性,选择易操作的液压元件和控制阀,合理布置管路和连接件,以便于检修和更换。
7.可靠性要求:液压系统的设计应满足可靠性要求,确保系统能够长时间、稳定地运行。
设计时需要考虑液压元件的寿命和可靠性,选择可靠性较高的液压元件和材料,并采取相应的措施来提高系统的可靠性。
8.环境适应性要求:液压系统的设计应满足特定工作环境的要求,如高温、低温、潮湿、腐蚀等。
设计时需要选择适应工作环境的液压元件和密封件,选用符合环保要求的液压油和材料。
总之,液压系统设计规范要求涉及压力等级、流量要求、控制精度、安全性、节能性、维护性、可靠性和环境适应性等方面。
专用铣床液压系统设计课程设计
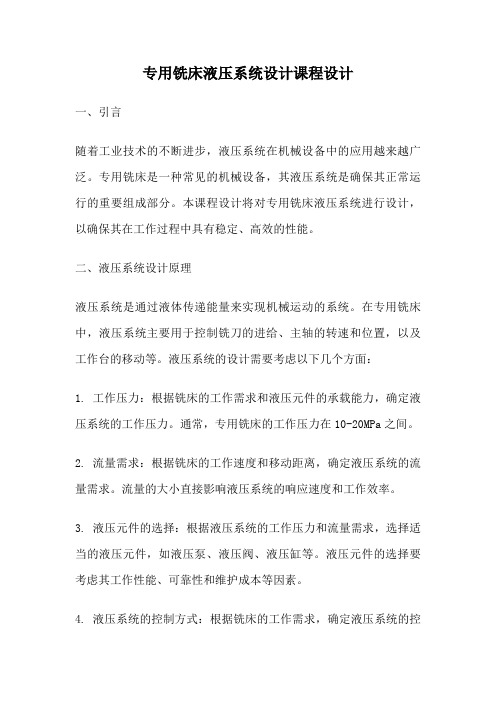
专用铣床液压系统设计课程设计一、引言随着工业技术的不断进步,液压系统在机械设备中的应用越来越广泛。
专用铣床是一种常见的机械设备,其液压系统是确保其正常运行的重要组成部分。
本课程设计将对专用铣床液压系统进行设计,以确保其在工作过程中具有稳定、高效的性能。
二、液压系统设计原理液压系统是通过液体传递能量来实现机械运动的系统。
在专用铣床中,液压系统主要用于控制铣刀的进给、主轴的转速和位置,以及工作台的移动等。
液压系统的设计需要考虑以下几个方面:1. 工作压力:根据铣床的工作需求和液压元件的承载能力,确定液压系统的工作压力。
通常,专用铣床的工作压力在10-20MPa之间。
2. 流量需求:根据铣床的工作速度和移动距离,确定液压系统的流量需求。
流量的大小直接影响液压系统的响应速度和工作效率。
3. 液压元件的选择:根据液压系统的工作压力和流量需求,选择适当的液压元件,如液压泵、液压阀、液压缸等。
液压元件的选择要考虑其工作性能、可靠性和维护成本等因素。
4. 液压系统的控制方式:根据铣床的工作需求,确定液压系统的控制方式。
常见的控制方式有手动控制、自动控制和数控控制等。
三、液压系统设计步骤1. 确定系统要求:根据专用铣床的工作特点和要求,明确液压系统的工作压力、流量需求和控制方式等。
2. 选择液压元件:根据系统要求,选择合适的液压元件。
液压泵的选择要考虑其流量和压力特性;液压阀的选择要考虑其控制特性和可靠性;液压缸的选择要考虑其负载能力和运动特性等。
3. 绘制液压系统图:根据系统要求和液压元件的选择,绘制液压系统图。
液压系统图应包括液压泵、液压阀、液压缸等液压元件的连接关系和管路布置。
4. 计算液压系统参数:根据系统要求和液压元件的特性,计算液压系统的参数,如泵的流量和压力、液压缸的负载和速度等。
5. 设计液压系统控制装置:根据系统要求和控制方式,设计液压系统的控制装置。
控制装置可以采用手动操作、电气控制或计算机控制等方式。
上料机液压系统设计

上料机液压系统设计液压系统在上料机中的设计是非常重要的,它是实现上料机正常工作的关键组成部分。
本文将从液压系统的组成、工作原理、设计要求及优化等方面进行详细介绍。
一、液压系统组成液压系统主要由液压源、执行元件、控制元件、辅助元件及液压工作介质等组成。
1.液压源:通常由液压泵提供动力,将机械能转化为液压能。
2.执行元件:主要有液压缸、液压马达等。
在上料机中,液压缸用于实现上料斗的升降和倾斜等动作。
3.控制元件:包括阀门、阀芯、阀座等。
通过对液压油流进行控制和调节,实现液压系统各个部件的协调工作。
4.辅助元件:主要有油箱、滤清器、冷却器等。
油箱提供液压油的贮存和冷却,滤清器用于过滤液压油中的杂质,冷却器用于降低液压油的温度。
5.液压工作介质:通常采用液压油作为液压系统的工作介质。
液压油具有一定的粘度和热稳定性,能够在高温和高压力下正常工作。
二、液压系统工作原理液压系统的工作原理是基于帕斯卡定律。
即压力在静态液体中传递时,作用在液体上的力是与所受面积成正比的。
根据这一原理,液压系统通过控制液压油的流量和压力,实现对液压缸的控制。
当液压系统启动时,液压泵将液压油从油箱中吸入,在压力作用下,向执行元件(液压缸)提供动力。
通过控制元件的控制,可以实现液压油的流向和压力调节,从而实现上料斗的升降和倾斜等动作。
三、液压系统设计要求1.性能要求:液压系统在上料机中的设计应保证系统的工作性能稳定可靠,具有较高的工作效率和运行平稳性。
2.安全要求:液压系统设计应考虑到系统的安全性,包括液压元件的强度和稳定性,系统的漏油及漏压检测与报警等。
3.节能要求:液压系统设计应尽可能降低能源损耗,提高系统的能源利用率。
4.维修保养要求:液压系统的设计应便于维修和保养,包括易于检修和更换液压元件,便捷的油液更换与滤清以及液压系统的保养周期等。
四、液压系统设计优化针对上述设计要求,可以通过以下方式对液压系统进行优化设计:1.选择合适的液压元件:根据上料机的工作条件和需求,选择适合的液压泵、液压缸和控制阀等元件,保证其质量和性能符合要求。
液压系统的设计计算步骤和内容

• 最大负载值是初步确定执行元件工作压力和结构尺寸的依据。 • 液压马达的负载力矩分析与液压缸的负载分析相同,只需将上述负载
设计计算
步骤和内容
4~5
>5~7
18
系统工作压力的确定
表9-3 按主机类型选择系统工作压力
设备 类型
磨床
机床
组合机床 牛头刨床
插床 齿轮加工
机床
车床 铣床 镗床
珩磨 拉床 机 龙门 床 刨床
农业机械 汽车工业 小型工程 机械及辅 助机械
工程机械 重型机械 锻压设备 液压支架
船用 系统
压力 /MPa
摆动缸
单叶片缸转角小于300°,双叶片缸转角小于150°
往复摆动运动
齿轮、叶片马达 轴向柱塞马达 径向柱塞马达
结构简单、体积小、惯性小 运动平稳、转大、转速范围宽 结构复杂、转大、转速低
设计计算
步骤和内容
高速小转矩回转运动 大转矩回转运动 低速大转矩回转运动
7
负载分析
• 负载分析就是通过计算确定各液压执行元件的负载大小和方向,并分 析各执行元件运动过程中的振动、冲击及过载能力等情况。
设计计算
步骤和内容
2
1.1 液压系统的设计依据和工况分析
液压系统的设计依据
• 设计要求是进行工程设计的主要依据。设计前必须把主机对液压系统 的设计要求和与设计相关的情况了解清楚,一般要明确下列主要问题:
液压系统设计的规范要求

液压系统设计规范一、图样规定1、对日勺标注各视图日勺关系,正常日勺三视图不用标注视向,摆放要原则,其他视图均要有明显的箭头及字母指示标注。
假如正常视图中可以体现清晰,不要再单独画出局部视图,在不影响图面质量的前提下尽量在重要视图中标注尺寸(尤其是阀板图)。
2、规定视图要以主视图左上角为坐标原点。
3、图纸上的字体要采用仿宋体,字体大小按1:1图面选择4号。
二、多种部件的规定1、原理图:(1)主电机、泵的参数,循环冷却装置日勺参数,这些参数包括如下标识可直接写在有关元件图形的附近。
(2)压力表、压力阀、压力继电器、蓄能器多种压力的设定值。
(3)多种管路(如压力、回油、泄油等)和连接液压执行元件管路外径和壁厚。
(4)各液压执行机构要标注名称,对应的液压油缸或液压马达要标注规格参数及接油口尺寸。
(5)多种过滤器日勺过滤精度。
(6)多种不一样性能管子时代号(P、T、1、A、B、X等),详细编号规则按“液压系统常用编码规则”执行。
(7)温度、液位、油箱容积等日勺设定值。
(9)介质日勺型号及等级规定。
(10)电机、电气触点、电磁铁线圈编号。
(11)测压点代号:泵站部分压力口采用MPUMP2 ................ ;阀站部分执行机构A、B压力口MA1MB1,MA2、MB2 ..........(12)所有的压力、温度、液位、电磁铁代号都要设铭牌。
液压站要设置液压厂厂铭牌(大、小两种规格),在泵、阀站对应位置给出底板,明细中不用给出厂铭牌序号,把合不能采用钾钉,要用螺钉或再加螺母把紧。
(13)计量单位应符合国标规定(常用------ mm、MPa、kW、m/s、1∕min>m1/r、r/min、kg、V-Hz>℃等)。
2、总图(1)技术性能中要清晰写出系统流量、压力、电机、泵、加热器、油箱容积、液压介质型号与等级等参数,如下示例。
(2)技术规定示例技术要求(3)总图中要标注所有大部件日勺(安装图样中部件)定位尺寸及最大外型尺寸,多种部件之间互相连接日勺管道代号、管子外径和壁厚等规定。
液压系统的设计毕业设计

液压系统的设计毕业设计液压系统的设计毕业设计引言液压系统是一种利用液体传递能量的技术,广泛应用于各个领域,如工业、农业、航空航天等。
在液压系统的设计中,需要考虑多个因素,包括系统的结构、元件的选择、流体的性质等。
本文将探讨液压系统的设计过程,并介绍一些常见的设计原则和方法。
一、液压系统的基本原理液压系统的基本原理是利用液体在封闭的管路中传递力和能量。
液压系统由液压泵、执行元件、控制阀等组成。
液压泵通过机械能转化为液压能,将液体压入管路中。
控制阀通过控制液体的流动方向和流量来实现对执行元件的控制。
执行元件将液体的能量转化为机械能,完成所需的工作。
二、液压系统的设计步骤1. 确定系统的需求:在进行液压系统的设计之前,需要明确系统的工作要求和目标。
例如,需要确定系统的工作压力、流量需求、工作环境等。
2. 选择液压元件:根据系统的需求,选择合适的液压元件,包括液压泵、执行元件、控制阀等。
在选择液压元件时,需要考虑元件的性能参数、可靠性、成本等因素。
3. 设计管路布局:根据系统的工作需求和元件的选择,设计合理的管路布局。
管路布局应考虑液体的流动路径、压力损失、泄漏等因素,以确保系统的稳定性和效率。
4. 进行系统分析:通过数学模型和仿真软件对系统进行分析,评估系统的性能和可靠性。
分析过程中需要考虑液体的性质、流动特性、压力变化等因素。
5. 进行系统优化:根据系统分析的结果,对系统进行优化。
优化的目标可以包括提高系统的效率、减少能量损失、降低成本等。
6. 进行系统测试:设计完成后,进行系统的实际测试。
测试过程中需要检查系统的各个部件是否正常工作,是否满足设计要求。
三、液压系统设计的原则和方法1. 简化系统结构:在液压系统的设计中,应尽量简化系统的结构,减少元件的数量和复杂性。
简化系统结构可以提高系统的可靠性和维护性。
2. 选择合适的元件:在选择液压元件时,应考虑元件的性能参数、可靠性、成本等因素。
选择合适的元件可以提高系统的性能和效率。
叉车液压系统设计

叉车液压系统设计叉车液压系统设计是指在设计和制造叉车时,设计工程师需要考虑的叉车液压系统的设计要点和流程。
叉车液压系统是叉车的核心部件之一,它通过液压传动和控制来实现叉车的起重、升降、倾斜和推力等功能。
设计一个稳定可靠的叉车液压系统是叉车设计中非常重要的一环。
1.功能需求分析:首先需要明确叉车液压系统的功能需求,包括叉车的起重能力、升降高度、倾斜角度、推力要求等。
根据这些需求来确定液压系统的参数,如液压油泵的流量和压力、液压缸的直径和行程等。
2.组件选型:根据功能需求和设计要求,选择合适的液压组件,包括液压泵、液压缸、液压阀等。
需要考虑的因素包括工作压力、流量、尺寸、耐磨性、可靠性和价格等。
3.系统布局设计:根据叉车结构和安装空间的限制,设计液压系统的布局。
要考虑到液压元件的位置和连接方式,以及液压管路的布置和长度,以确保液压系统的紧凑和可靠。
4.液压回路设计:根据叉车功能需求和液压组件的选择,设计液压回路。
液压回路包括供油回路和控制回路。
供油回路保证液压油能够流动到液压缸,并提供足够的流量和压力;控制回路控制液压系统的动作和停止。
5.液压管路设计:设计液压管路时需要考虑流量、压力损失和泄漏的问题。
应尽量缩短液压管路的长度,减小管路的阻力和压力损失。
在连接液压元件时,要确保管路和接头的密封性,以防止液压油泄漏。
6.液压控制阀设计:根据叉车的功能需求,选择合适的液压控制阀。
液压控制阀控制液压油的流动和压力,使液压系统能够实现叉车的各种动作。
7.安全保护设计:叉车液压系统设计时需要考虑安全保护措施。
例如,应设置液压缸的限位阀,以防止液压缸的过载和损坏;可设置液压安全阀,以防止液压系统的压力过高。
8.效率和节能设计:在设计叉车液压系统时,应考虑提高系统的效率和节能性。
例如,可以采用变容泵和柔性输送阀等节能措施,以减小能源消耗和环境污染。
总之,叉车液压系统设计需要综合考虑功能需求、组件选型、系统布局、液压回路、管路设计、控制阀设计、安全保护和节能等方面的要求,以设计一个稳定可靠、高效节能的叉车液压系统。
简述液压系统设计的工作步骤

简述液压系统设计的工作步骤液压系统设计是指根据工作需求和系统性能要求,综合考虑液压元件的选型、液压元件的布置和连接、液压系统的控制与保护等因素,设计出一个满足设备工作需求的液压系统。
液压系统设计的工作步骤主要包括以下几个方面:1.需求分析与规定:这一步骤主要是对液压系统工作的需求进行分析和规定。
需求分析包括工作压力、流量要求、工作温度范围、工作环境要求等方面的考虑,规定则是在需求分析的基础上对液压系统的工作参数进行具体规定。
2.液压元件的选型:根据工作压力、流量要求以及规定的工作参数,从液压元件产品手册、厂家技术资料和液压元件选型手册中选取合适的液压元件。
液压元件的选型包括选取合适的液压泵、阀门、执行元件等。
3.系统图的绘制:根据工作需求和选定的液压元件,绘制出液压系统的结构图和工作原理图。
结构图主要是表现液压系统各个部件之间的布置关系和连接方式,工作原理图则是表现液压系统各个部件之间的工作原理和控制关系。
4.系统参数计算:根据液压元件的选型和系统图,对液压系统各个部分的参数进行计算。
主要包括液压泵的排量和功率计算、液压缸的有效面积计算、阀门的流量和压力损失计算等。
这些参数计算的正确与否直接影响到液压系统的性能指标是否得以实现。
5.系统接口设计:液压系统在工作过程中需要与其他机械系统或电气系统进行配合,因此需要进行系统接口设计。
主要包括液压系统与机械系统的连接方式、液压系统与电气系统的控制信号传递方式等。
6.控制与保护系统设计:液压系统控制与保护是液压系统工作的关键环节,所以需要进行相应的控制与保护系统设计。
包括设计液压系统的控制方式(手动控制、自动控制等)、液压系统的安全保护装置(压力开关、过载保护等)等。
7.系统布置与装配:设计完液压系统后,需要进行系统布置与装配。
主要包括选择系统的布置位置、液压元件的安装位置和固定方式、管路的布置与连接等。
合理的系统布置与装配能够减小液压系统的压力损失和泄漏,提高系统的工作效率和可靠性。
液压系统设计方法

液压系统设计方法液压系统是一种通过液体传递能量的系统,广泛应用于各种工业和机械设备中。
液压系统设计的目标是实现高效、可靠的能量传递和控制,同时满足系统的性能要求。
下面是液压系统设计的一般方法和步骤。
第一步:明确系统的工作要求在液压系统设计之前,首先需要明确系统的工作要求,包括工作条件、所需输出力或动力、速度和精度要求等。
这些要求将直接影响到系统的设计和选型。
第二步:选择液压元件在液压系统中,液压元件起到能量传递和控制的作用。
选择适合系统要求的液压元件是液压系统设计的核心步骤之一、常见的液压元件包括液压泵、阀门、缸体、马达等。
在选择液压元件时,需要考虑其技术参数、工作压力范围、流量要求、密封性能和可靠性等。
第三步:设计液压系统布局液压系统布局是指液压元件在系统中的位置和连接方式。
液压系统布局的设计直接影响液压系统的性能和工作效率。
在设计液压系统布局时,需要考虑以下几个因素:1.系统的可维修性和易操作性,便于维护和检修。
2.尽量减少管路的长度和对流动的阻力,提高系统的工作效率。
3.避免液压元件之间的相互干扰和干涉,确保系统的正常工作。
第四步:计算和选择液压元件参数在设计液压系统时,需要计算和选择液压元件的参数。
例如,液压泵的流量和压力选择要根据系统的工作需求来确定,阀门的开口面积需要根据所需流量来计算,缸体的尺寸和活塞面积需要根据所需输出力来选择等。
第五步:进行系统的动态和静态模拟在液压系统设计的过程中,进行系统的动态和静态模拟可以帮助工程师预测系统的性能和响应。
动态模拟可以用于分析系统的运动特性和响应时间,判断系统是否满足要求;静态模拟可以用于分析系统的压力分布和流动性能,优化设计。
第六步:进行系统的试验验证总结:。
液压系统设计步骤

液压系统设计的步骤大致如下:1.明确设计要求,进行工况分析。
2.初定液压系统的主要参数。
3.拟定液压系统原理图。
4.计算和选择液压元件。
5.估算液压系统性能。
6.绘制工作图和编写技术文件。
一、工况分析本机主要用于剪切工件装配时可通过夹紧机构来剪切不同宽度的钢板。
剪切机在剪切钢板时液压缸通过做弧形摆动提供推力。
主机运动对液压系统运动的要求:剪切机在剪切钢板时要求液压装置能够实现无级调速,而且能够保证剪切运动的平稳性,并且效率要高,能够实现一定的自动化。
该机构主要有两部分组成:机械系统和液压系统。
机械机构主要起传递和支撑作用,液压系统主要提供动力,它们两者共同作用实现剪切机的功能。
本次主要做液压系统的设计。
在上述工作的基础上,应对主机进行工况分析,工况分析包括运动分析和动力分析,对复杂的系统还需编制负载和动作循环图,由此了解液压缸或液压马达的负载和速度随时间变化的规律,以下对工况分析的内容作具体介绍。
该系统的剪切力为400T剪切负载F=400×10000=4×106N一、运动分析主机的执行元件按工艺要求的运动情况,可以用位移循环图(L—t),速度循环图(v—t),或速度与位移循环图表示,由此对运动规律进行分析。
1.位移循环图L—t图(1)为液压机的液压缸位移循环图,纵坐标L表示活塞位移,横坐标t表示从活塞启动到返回原位的时间,曲线斜率表示活塞移动速度。
该图清楚地表明液压机的工作循环分别由快速下行、运行压制、保压、泄压和快速回程五个阶段组成。
图(1)位移循环图2.速度循环图v—t(或v—L)工程中液压缸的运动特点可归纳为三种类型。
图(2)为种液压缸的v—t图,液压缸开始作匀加速运动,然后匀速运动,速度循坏图液压缸在总行程的一大半以上以一定的加速度作匀加速运动,然后匀减速至行程终点。
v—t图速度曲线,不仅清楚地表明了液压缸的运动规律,也间接地表明了三种工况的动力特性。
二、动力分析液压缸运动循环各阶段的总负载力。
液压系统的设计步骤与设计要求
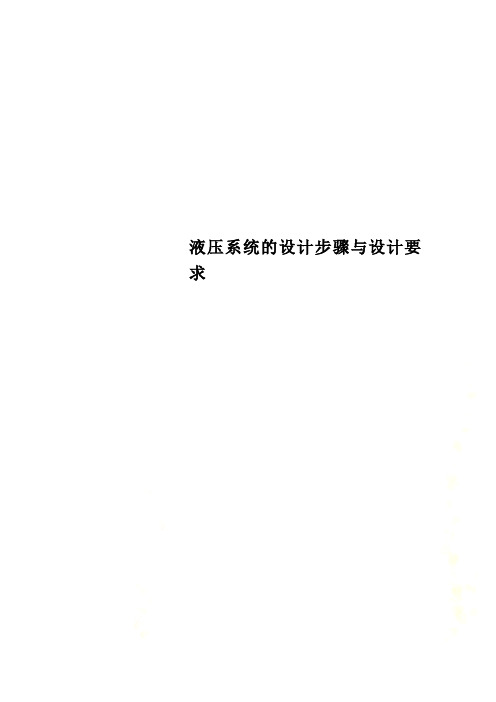
液压系统的设计步骤与设计要求液压系统的设计步骤与设计要求液压传动系统是液压机械的一个组成部分,液压传动系统的设计要同主机的总体设计同时进行。
着手设计时,必须从实际情况出发,有机地结合各种传动形式,充分发挥液压传动的优点,力求设计出结构简单、工作可靠、成本低、效率高、操作简单、维修方便的液压传动系统。
1.1 设计步骤液压系统的设计步骤并无严格的顺序,各步骤间往往要相互穿插进行。
一般来说,在明确设计要求之后,大致按如下步骤进行。
1)确定液压执行元件的形式;2)进行工况分析,确定系统的主要参数;3)制定基本方案,拟定液压系统原理图;4)选择液压元件;5)液压系统的性能验算;6)绘制工作图,编制技术文件。
1.2 明确设计要求设计要求是进行每项工程设计的依据。
在制定基本方案并进一步着手液压系统各部分设计之前,必须把设计要求以及与该设计内容有关的其他方面了解清楚。
1)主机的概况:用途、性能、工艺流程、作业环境、总体布局等;2)液压系统要完成哪些动作,动作顺序及彼此联锁关系如何;3)液压驱动机构的运动形式,运动速度;4)各动作机构的载荷大小及其性质;5)对调速范围、运动平稳性、转换精度等性能方面的要求;6)自动化程序、操作控制方式的要求;7)对防尘、防爆、防寒、噪声、安全可靠性的要求;8)对效率、成本等方面的要求。
制定基本方案和绘制液压系统图3.1制定基本方案(1)制定调速方案液压执行元件确定之后,其运动方向和运动速度的控制是拟定液压回路的核心问题。
方向控制用换向阀或逻辑控制单元来实现。
对于一般中小流量的液压系统,大多通过换向阀的有机组合实现所要求的动作。
对高压大流量的液压系统,现多采用插装阀与先导控制阀的逻辑组合来实现。
速度控制通过改变液压执行元件输入或输出的流量或者利用密封空间的容积变化来实现。
相应的调整方式有节流调速、容积调速以及二者的结合——容积节流调速。
节流调速一般采用定量泵供油,用流量控制阀改变输入或输出液压执行元件的流量来调节速度。
液压泵性能测试的液压系统设计

液压泵性能测试的液压系统设计本文档旨在介绍液压泵性能测试的液压系统设计的主要内容和步骤。
确定测试需求和目标:在设计液压系统之前,需要明确测试的目标和要求。
这包括测试的参数、范围以及所需的精度。
选择合适的液压泵:根据测试需求选择合适的液压泵。
考虑泵的工作压力、流量和功率等参数,以及泵的可靠性和耐用性。
确定液压油的特性:根据液压泵的工作要求选择合适的液压油。
考虑油的粘度、温度范围以及对系统的兼容性。
设计液压系统:根据测试需求和选择的液压泵,设计液压系统。
这包括确定系统的布局、选用适当的阀门和管道,以及计算系统所需的油箱容积和冷却器的功率。
考虑系统的安全性:在设计液压系统时,要考虑系统的安全性。
确保系统的压力和温度控制在安全范围内,并采取必要的安全措施,如安装压力开关和温度传感器。
进行系统测试和调试:在设计完成后,进行系统测试和调试。
确保系统的各个部件正常工作,并满足测试要求和目标。
液压泵性能测试的液压系统设计是一个复杂的过程,需要考虑多个因素。
通过明确测试需求和目标,选择合适的液压泵和液压油,并进行系统的安全考虑和测试调试,可以设计出满足要求的液压系统。
液压泵性能测试是评估液压泵工作性能的一种重要方法。
设计液压系统是为了在测试中提供适当的工作条件。
本文将介绍液压泵性能测试的背景和意义,并说明设计液压系统的目的。
性能测试是确定液压泵在不同工况下的工作特性的过程。
通过性能测试,可以评估液压泵的流量、压力、效率等参数,并分析泵的负载能力、稳定性和可靠性。
性能测试结果对于液压系统的设计、优化和故障诊断具有重要指导意义。
设计液压系统的目的是为液压泵性能测试提供准确、可靠的工作环境。
液压系统需要满足一定的工作压力和流量要求,并且能够稳定运行以提供稳定的工况条件。
同时,设计液压系统还需要考虑泵的进口和出口管道的布置、阀门的选择和控制以及传感器的安装等因素。
在液压泵性能测试的液压系统设计中,需要充分考虑液压系统的安全性、可靠性和易操作性。
第9章液压系统设计与计算-

• 快进时:
差动系统
p F A1 A2
qv快 (A1A2)
非差动系统
p1
F A1
A2 A1
p2
q v快A1
P pq
•工进时:
p1
A2 A1
F pb A1
q v工A1
P p工q工
• 快退
p1
A2 A1
pb
F A1
qv快退A2
P pq
图9-2 组合机床执行元件工况图
Ff f FN
(9-2)
式中 FN——运动部件及外负载对支撑面的正压力; f——摩擦系数,分 静摩擦系数( fS≤0.2~0.3)和动摩擦系数(fd ≤0.05~0.1)。
(3)惯性负载 Fa 惯性负载是运动部件的速度变化时,由其惯性而产生的负
载,可用牛顿第二定律计算:
Fa
ma Gv g t
液压缸推力F(N)
F =( Ffs + FL ± Fg) /ηm F =( Ffd + FL +Fa± Fg) /ηm F =( Ffd + FL± Fg) /ηm F =( Ffd + FL — Fa± Fg) /ηm F =( Ffd + FL ± Fg) /ηm F =( Ffd + FL — Fa± Fg) /ηm F =( Ffs + Fa ± Fg) /ηm
来验பைடு நூலகம்,即
A q min v min
(9-5)
qmin—流量阀最小稳定流量。
液压马达:排量的计算式为
2T
V
p Mm
(9-6)
式中 T—液压马达的总负载转矩,N.m; ηMm—液压马达的机械效率; p—液压马达的工作压力,pa; V—所求液压马达的排量,m3/r。
液压系统设计流程
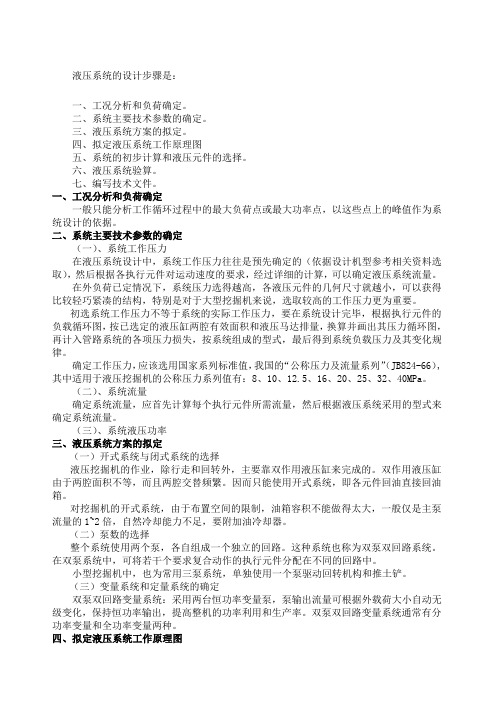
液压系统的设计步骤是:一、工况分析和负荷确定。
二、系统主要技术参数的确定。
三、液压系统方案的拟定。
四、拟定液压系统工作原理图五、系统的初步计算和液压元件的选择。
六、液压系统验算。
七、编写技术文件。
一、工况分析和负荷确定一般只能分析工作循环过程中的最大负荷点或最大功率点,以这些点上的峰值作为系统设计的依据。
二、系统主要技术参数的确定(一)、系统工作压力在液压系统设计中,系统工作压力往往是预先确定的(依据设计机型参考相关资料选取),然后根据各执行元件对运动速度的要求,经过详细的计算,可以确定液压系统流量。
在外负荷已定情况下,系统压力选得越高,各液压元件的几何尺寸就越小,可以获得比较轻巧紧凑的结构,特别是对于大型挖掘机来说,选取较高的工作压力更为重要。
初选系统工作压力不等于系统的实际工作压力,要在系统设计完毕,根据执行元件的负载循环图,按已选定的液压缸两腔有效面积和液压马达排量,换算并画出其压力循环图,再计入管路系统的各项压力损失,按系统组成的型式,最后得到系统负载压力及其变化规律。
确定工作压力,应该选用国家系列标准值,我国的“公称压力及流量系列”(JB824-66),其中适用于液压挖掘机的公称压力系列值有:8、10、12.5、16、20、25、32、40MPa。
(二)、系统流量确定系统流量,应首先计算每个执行元件所需流量,然后根据液压系统采用的型式来确定系统流量。
(三)、系统液压功率三、液压系统方案的拟定(一)开式系统与闭式系统的选择液压挖掘机的作业,除行走和回转外,主要靠双作用液压缸来完成的。
双作用液压缸由于两腔面积不等,而且两腔交替频繁。
因而只能使用开式系统,即各元件回油直接回油箱。
对挖掘机的开式系统,由于布置空间的限制,油箱容积不能做得太大,一般仅是主泵流量的1~2倍,自然冷却能力不足,要附加油冷却器。
(二)泵数的选择整个系统使用两个泵,各自组成一个独立的回路。
这种系统也称为双泵双回路系统。
在双泵系统中,可将若干个要求复合动作的执行元件分配在不同的回路中。
- 1、下载文档前请自行甄别文档内容的完整性,平台不提供额外的编辑、内容补充、找答案等附加服务。
- 2、"仅部分预览"的文档,不可在线预览部分如存在完整性等问题,可反馈申请退款(可完整预览的文档不适用该条件!)。
- 3、如文档侵犯您的权益,请联系客服反馈,我们会尽快为您处理(人工客服工作时间:9:00-18:30)。
液压系统得设计步骤与设计要求液压传动系统就是液压机械得一个组成部分,液压传动系统得设计要同主机得总体设计同时进行。
着手设计时,必须从实际情况出发,有机地结合各种传动形式,充分发挥液压传动得优点,力求设计出结构简单、工作可靠、成本低、效率高、操作简单、维修方便得液压传动系统。
1、1 设计步骤液压系统得设计步骤并无严格得顺序,各步骤间往往要相互穿插进行。
一般来说,在明确设计要求之后,大致按如下步骤进行。
1)确定液压执行元件得形式;2)进行工况分析,确定系统得主要参数;3)制定基本方案,拟定液压系统原理图;4)计算与选择液压元件;5)液压系统得性能验算;6)绘制工作图,编制技术文件。
1、2 明确设计要求设计要求就是进行每项工程设计得依据。
在制定基本方案并进一步着手液压系统各部分设计之前,必须把设计要求以及与该设计内容有关得其她方面了解清楚。
1)主机得概况:用途、性能、工艺流程、作业环境(温度、湿度、振动冲击)、总体布局(及液压传动装置得位置与空间尺寸得要求)等;2)液压系统要完成哪些动作,动作顺序及彼此联锁关系如何;3)液压驱动机构得运动形式,运动速度;4)各动作机构得载荷大小及其性质;5)对调速范围、运动平稳性、换向定位精度等性能方面得要求;6)自动化程度、操作控制方式得要求;7)对防尘、防爆、防腐、防寒、噪声、安全可靠性得要求;8)对效率、成本等方面得要求。
主机得工况分析通过工况分析,可以瞧出液压执行元件在工作过程中速度与载荷变化情况,为确定系统及各执行元件得参数提供依据。
液压系统得主要参数就是压力与流量,它们就是设计液压系统,选择液压元件得主要依据。
压力决定于外载荷。
流量取决于液压执行元件得运动速度与结构尺寸。
主机工况分析包括运动分析与动力分析,对复杂得系统还需编制负载与动作循环图,由此了解液压缸或液压马达得负载与速度随时间变化得规律,以下对工况分析得内容作具体介绍。
2、1 运动分析主机得执行元件按工艺要求得运动情况,可以用位移循环图(L—t) ,速度循环图(v—t) ,或速度与位移循环图表示,由此对运动规律进行分析。
1、位移循环图L —t液压机得液压缸位移循环图纵坐标L 表示活塞位移,横坐标t 表示从活塞启动到返回原位得时间,曲线斜率表示活塞移动速度。
该图清楚地表明液压机得工作循环分别由快速下行、减速下行、压制、保压、泄压慢回与快速回程六个阶段组成。
2、速度循环图v —t(或v —L)工程中液压缸得运动特点可归纳为三种类型。
图为三种类型液压缸得v —t 图,第一种如图中实线所示,液压缸开始作匀加速运动,然后匀速运动,最后匀减速运动到终点;第二种,如图中虚线所示,液压缸在总行程得前一半作匀加速运动,在另一半作匀减速运动,且加速度得数值相等;第三种,液压缸在总行程得一大半以上以较小得加速度作匀加速运动,然后匀减速至行程终点。
v —t 图得三条速度曲线,不仅清楚地表明了三种类型液压缸得运动规律,也间接地表明了三种工况得动力特性。
位移循环图速度循环图2、2 动力分析动力分析,就是研究机器在工作过程中,其执行机构得受力情况,对液压系统而言,就就是研究液压缸或液压马达得负载情况。
1.液压缸得负载及负载循环图(1)液压缸得负载力计算。
工作机构作直线往复运动时,液压缸必须克服得负载由六部分组成:F=Fc+Ff+Fi+FG+Fm+Fb (1)式中:Fc 为工作阻力;Ff 为摩擦阻力;Fi 为惯性阻力;FG 为重力;Fm 为密封阻力;Fb 为排油阻力。
①工作阻力Fc :为液压缸运动方向得工作阻力,对于机床来说就就是沿工作部件运动方向得切削力,此作用力得方向如果与执行元件运动方向相反为正值,两者同向为负值。
该作用力可能就是恒定得,也可能就是变化得,其值要根据具体情况计算或由实验测定。
②摩擦阻力Ff : 为液压缸带动得运动部件所受得导轨摩擦阻力,它与导轨得形状、放置情况与运动状态有关,其计算方法可查有关得设计手册。
图为最常见得两种导轨形式,其摩擦阻力得值为:平导轨: Ff=f∑Fn (2)V 形导轨: Ff=f∑Fn/[sin(α/2)] (3)式中:f 为摩擦因数;∑Fn 为作用在导轨上总得正压力或沿V 形导轨横截面中心线方向得总作用力;α为V 形角,一般为90°。
导轨形式③惯性阻力Fi 。
惯性阻力Fi 为运动部件在启动与制动过程中得惯性力,可按下式计算:(4)式中:m 为运动部件得质量(kg);a 为运动部件得加速度(m/s2) ;G 为运动部件得重量(N);g 为重力加速度,g=9、81 (m/s2) ;Δv 为速度变化值(m/s);Δt 为启动或制动时间(s),一般机床Δt =0、1~0、5s ,对轻载低速运动部件取小值,对重载高速部件取大值。
④重力F G :垂直放置与倾斜放置得移动部件,其本身得重量也成为一种负载,当上移时,负载为正值,下移时为负值。
⑤密封阻力F m :密封阻力指装有密封装置得零件在相对移动时得摩擦力,其值与密封装置得类型、液压缸得制造质量与油液得工作压力有关。
在初算时,可按缸得机械效率(ηm=0、9)考虑;验算时,按密封装置摩擦力得计算公式计算。
⑥排油阻力F b :排油阻力为液压缸回油路上得阻力,该值与调速方案、系统所要求得稳定性、执行元件等因素有关,在系统方案未确定时无法计算,可放在液压缸得设计计算中考虑。
(2)液压缸运动循环各阶段得总负载力。
液压缸运动循环各阶段得总负载力计算,一般包括启动加速、快进、工进、快退、减速制动等几个阶段,每个阶段得总负载力就是有区别得。
①启动加速阶段:这时液压缸或活塞处于由静止到启动并加速到一定速度,其总负载力包括导轨得摩擦力、密封装置得摩擦力(按缸得机械效率ηm =0、9计算) 、重力与惯性力等项,即:F=Ff+Fi±FG+Fm+Fb (5)②快速阶段: F=Ff±FG+Fm+Fb (6)③工进阶段: F=Ff+Fc±FG+Fm+Fb (7)④减速: F=Ff±FG-Fi+Fm+Fb (8)对简单液压系统,上述计算过程可简化。
例如采用单定量泵供油,只需计算工进阶段得总负载力,若简单系统采用限压式变量泵或双联泵供油,则只需计算快速阶段与工进阶段得总负载力。
(3)液压缸得负载循环图。
对较为复杂得液压系统,为了更清楚得了解该系统内各液压缸(或液压马达) 得速度与负载得变化规律,应根据各阶段得总负载力与它所经历得工作时间t 或位移L 按相同得坐标绘制液压缸得负载时间(F—t) 或负载位移(F—L) 图,然后将各液压缸在同一时间t(或位移) 得负载力叠加。
负载循环图图中所示为一部机器得F —t 图,其中:0~t1为启动过程;t1~t2为加速过程;t2~t3为恒速过程; t3~t4为制动过程。
它清楚地表明了液压缸在动作循环内负载得规律。
图中最大负载就是初选液压缸工作压力与确定液压缸结构尺寸得依据。
2、液压马达得负载工作机构作旋转运动时,液压马达必须克服得外负载为:M=Me+Mf+Mi (9)(1)工作负载力矩Me 。
工作负载力矩可能就是定值,也可能随时间变化,应根据机器工作条件进行具体分析。
常见得载荷力矩有被驱动轮得阻力矩、液压卷筒得阻力矩等。
(2)摩擦力矩Mf 。
为旋转部件轴颈处得摩擦力矩,其计算公式为:Mf=fGR (N²m) (10)式中:G 为旋转部件得重量(施加于轴颈上得径向力)(N);f 为摩擦因数,启动时为静摩擦因数,启动后为动摩擦因数;R 为轴颈半径(m)。
(3)惯性力矩Mi 。
为旋转部件加速或减速时产生得惯性力矩,其计算公式为:(11)式中:ε为角加速度(rad/s2) ;Δω为角速度得变化(rad/s);Δt 为加速或减速时间(s);J 为旋转部件得转动惯量(kg、m2) ,J=1GD2/4g。
式中:GD 2为回转部件得飞轮效应(Nm2) 。
各种回转体得GD 2可查《机械设计手》。
根据式(9),分别算出液压马达在一个工作循环内各阶段得负载大小,便可绘制液压马达得负载循环图。
2、2 初选系统工作压力压力得选择要根据载荷大小与设备类型而定。
还要考虑执行元件得装配空间、经济条件及元件供应情况等得限制。
在载荷一定得情况下,工作压力低,势必要加大执行元件得结构尺寸,对某些设备来说,尺寸要受到限制,从材料消耗角度瞧出不经济;反之,压力选得太高,对泵、缸、阀等元件得材质、密封、制造精度也要求很高,必然要提高设备成本。
一般来说,对于固定得尺寸不太受限得设备,压力可以选低一些,行走机械重载设备压力要选得高一些。
制定基本方案与绘制液压系统图3、1制定基本方案(1)制定调速方案液压执行元件确定之后,其运动方向与运动速度得控制就是拟定液压回路得核心问题。
方向控制用换向阀或逻辑控制单元来实现。
对于一般中小流量得液压系统,大多通过换向阀得有机组合实现所要求得动作。
对高压大流量得液压系统,现多采用插装阀与先导控制阀得逻辑组合来实现。
速度控制通过改变液压执行元件输入或输出得流量或者利用密封空间得容积变化来实现。
相应得调整方式有节流调速、容积调速以及二者得结合——容积节流调速。
节流调速一般采用定量泵供油,用流量控制阀改变输入或输出液压执行元件得流量来调节速度。
此种调速方式结构简单,由于这种系统必须用闪流阀,故效率低,发热量大,多用于功率不大得场合。
容积调速就是靠改变液压泵或液压马达得排量来达到调速得目得。
其优点就是没有溢流损失与节流损失,效率较高。
但为了散热与补充泄漏,需要有辅助泵。
此种调速方式适用于功率大、运动速度高得液压系统。
容积节流调速一般就是用变量泵供油,用流量控制阀调节输入或输出液压执行元件得流量,并使其供油量与需油量相适应。
此种调速回路效率也较高,速度稳定性较好,但其结构比较复杂。
节流调速又分别有进油节流、回油节流与旁路节流三种形式。
进油节流起动冲击较小,回油节流常用于有负载荷得场合,旁路节流多用于高速。
调速回路一经确定,回路得循环形式也就随之确定了。
节流调速一般采用开式循环形式。
在开式系统中,液压泵从油箱吸油,压力油流经系统释放能量后,再排回油箱。
开式回路结构简单,散热性好,但油箱体积大,容易混入空气。
容积调速大多采用闭式循环形式。
闭式系统中,液压泵得吸油口直接与执行元件得排油口相通,形成一个封闭得循环回路。
其结构紧凑,但散热条件差。
(2)制定压力控制方案液压执行元件工作时,要求系统保持一定得工作压力或在一定压力范围内工作,也有得需要多级或无级连续地调节压力。
一般在节流调速系统中,通常由定量泵供油,用溢流阀调节所需压力,并保持恒定。
在容积调速系统中,用变量泵供油,用安全阀起安全保护作用。
在有些液压系统中,有时需要流量不大得高压油,这时可考虑用增压回路得到高压,而不用单设高压泵。