艾克特AT500中文说明书
Clinitek_500_操作手册

CLINITEK®500中文操作手册注意:此中文操作手册根据拜耳公司2002年的英文操作手册翻译,拜耳公司保留对原英文资料的更新权。
您在使用该手册时,有疑问,请查阅英文手册,目录1. 介绍使用目的 5 仪器组成和操作 5 光学系统7 定标7 规格8 结果报告2. 安装一般信息9 环境因素9 打开步骤9 仪器设定10 与打印机连接15 与计算机连接16 与条形码读取装置连接16 仪器的初始化检验16 3. 如何选择一般信息18 设定常规19A.设定菜单 #1 (日期;时间;计算机连接口;打印机) 20B.密码显示屏22C.设定菜单 #2 (语言;结果单位;附加分类系统;测试) 22D.设定菜单 #3 (日期,时间形式;日期,时间的分隔) 23E.设定菜单 #4 (测试的报告;阳性水平;正常水平) 24F.设定菜单 #5 (颜色;选择颜色,透明度;使用省略值) 25G.设定菜单 #6 (阳性水平颜色,透明度;报告的标志) 26H.设定菜单 #7 (被编辑的报告标志;输入样本ID;实验者ID) 27I. 设定菜单 #8 (计算机连接选择;条形码读取装置:密码) 28J. 设定菜单 #9 (省略的设定;硬件测试) 304.仪器操作一般信息32 使用准备33 参照试样测试34 常规试样测试34 A.基本操作35 B.如果使用试样ID代码37 C.使用ID代码而没有试样目录38 测试结束报告39 编辑确认报告39 寻找结果39 操作注意事项40 5.仪器维护一般清洗41 日常清洗41 消毒43 换纸44 6.附件7.简单维修一般要求46 更换打印头46 校正可触式显示器48 8.故障排除和服务一般要求49 何时寻求帮助49 何处寻求帮助49 故障排除表50 服务记录表54 9.附件和维修备件56 附件维修备件56 附录CPL:计算机和打印机的连接口57 一般信息串行口线缆针并行口线缆针介绍使用目的泰利特500尿液化学分析仪是一种半自动化桌面测试仪,能够读取“Bayer”反应试剂条,进行尿液分析。
Thermostat TC500A商品说明书
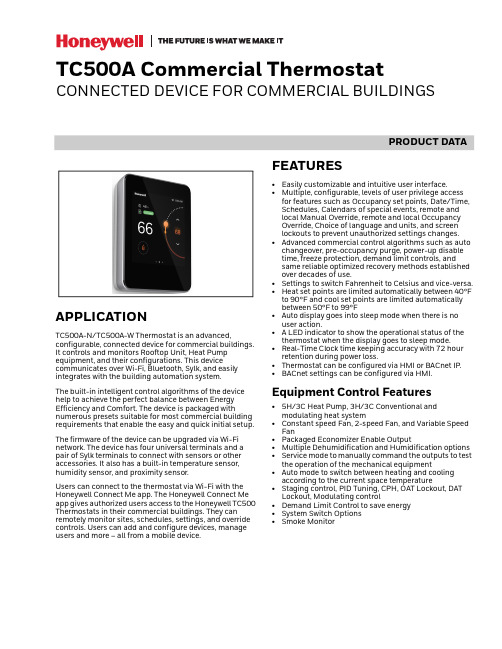
PRODUCT DATATC500A Commercial ThermostatCONNECTED DEVICE FOR COMMERCIAL BUILDINGSAPPLICATIONTC500A-N/TC500A-W Thermostat is an advanced,configurable, connected device for commercial buildings. It controls and monitors Rooftop Unit, Heat Pump equipment, and their configurations. This devicecommunicates over Wi-Fi, Bluetooth, Sylk, and easily integrates with the building automation system.The built-in intelligent control algorithms of the device help to achieve the perfect balance between Energy Efficiency and Comfort. The device is packaged withnumerous presets suitable for most commercial building requirements that enable the easy and quick initial setup.The firmware of the device can be upgraded via Wi-Fi network. The device has four universal terminals and a pair of Sylk terminals to connect with sensors or other accessories. It also has a built-in temperature sensor, humidity sensor, and proximity sensor.Users can connect to the thermostat via Wi-Fi with the Honeywell Connect Me app. The Honeywell Connect Me app gives authorized users access to the Honeywell TC500 Thermostats in their commercial buildings. They can remotely monitor sites, schedules, settings, and override controls. Users can add and configure devices, manage users and more – all from a mobile device.FEATURES•Easily customizable and intuitive user interface.•Multiple, configurable, levels of user privilege access for features such as Occupancy set points, Date/Time, Schedules, Calendars of special events, remote and local Manual Override, remote and local Occupancy Override, Choice of language and units, and screen lockouts to prevent unauthorized settings changes.•Advanced commercial control algorithms such as auto changeover, pre-occupancy purge, power-up disable time, freeze protection, demand limit controls, and same reliable optimized recovery methods established over decades of use.•Settings to switch Fahrenheit to Celsius and vice-versa.•Heat set points are limited automatically between 40°F to 90°F and cool set points are limited automatically between 50°F to 99°F•Auto display goes into sleep mode when there is no user action.• A LED indicator to show the operational status of the thermostat when the display goes to sleep mode.•Real-Time Clock time keeping accuracy with 72 hour retention during power loss.•Thermostat can be configured via HMI or BACnet IP.•BACnet settings can be configured via HMI.Equipment Control Features•5H/3C Heat Pump, 3H/3C Conventional and modulating heat system•Constant speed Fan, 2-speed Fan, and Variable Speed Fan•Packaged Economizer Enable Output•Multiple Dehumidification and Humidification options •Service mode to manually command the outputs to test the operation of the mechanical equipment•Auto mode to switch between heating and cooling according to the current space temperature•Staging control, PID Tuning, CPH, OAT Lockout, DAT Lockout, Modulating control•Demand Limit Control to save energy •System Switch Options •Smoke MonitorTC500A COMMERCIAL THERMOSTAT31-00398M-02 | Rev. 04-212TECHNICAL SPECIFICATIONSPower CharacteristicsDisplayIO CharacteristicsOperating EnvironmentTable 1. Power CharacteristicsPower SupplyRated voltage: 24VAC 50/60Hz,Working voltage range: 20-30VAC, UL listedclass-2 transformer or IEC 61558 listed transformer.Power Consumption (Display ON)Max. 8.5VA @ 24VAC (355mA @ 24VAC)Min. Load 4VA (all DOs OFF, No Sylk sensor)Max. Load96VA (all DOs ON)Table 2. DisplayDisplay Type 24 BPP TFT display with CTPResolutions 480x480 pixel Active Display Area 4” diagonally BacklightLCD (Dimmable)Table 3. IO CharacteristicsUIO x 2•Resistive Temperature Sensor Input—10K NTC type II, C7021 series —10K NTC type III,C7023 series —20K NTC, TR21 and C7041series.•Temperature Accuracy—±0.5°C (±1°F) at 10 – 32°C (50– 90°F)—±1.1°C (±2°F) at -1.1 – 50°C(30 – 122°F)•Voltage Input, SELV—0-10V, ±5% of full scale •Digital Input—Dry contact closure—Open circuit (≥ 100Kohms)—Closed circuit (≤100ohms)•Voltage Output—0-10V, ±3% of full scale @2KohmsUI x 2•Resistive Temperature Sensor Input—10K NTC type II, C7021 series —10K NTC type III,C7023 series —20K NTC, TR21 and C7041series•Temperature Accuracy—±0.5°C (±1°F) at 10 – 32°C (50– 90°F)—±1.1°C (±2°F) at -1.1 – 50°C(30 – 122°F)•Voltage Input, SELV—0-10V, ±5% of full scale •Digital Input—Dry contact closure—Open circuit (≥ 100Kohms)—Closed circuit (≤100ohms)DO (G,Y1,Y2,Y3,W1,W2,W3)•Relay Output— 1 Amps Max. at 24VAC DO (AUX)•Relay Dry Contact— 1 Amps Max. at 24VAC/DCTable 4. Operating EnvironmentAmbient Operating Temperature 32 to 122 °F (0 to +50°C)Ambient Operating Humidity 10 to 90% relative humidity (non-condensing)StorageTemperature -40 to 150 °F(-40 to 65.5°C)Protection ClassIP20Table 3. IO Characteristics (Continued)TC500A COMMERCIAL THERMOSTAT331-00398M-02 | Rev. 04-21CompliancesCommunication TechnologiesElectrical CharacteristicsSupported Sensors and FunctionsTable 5. CompliancesCertificates CE, FCC, ICES, UL/cUL, RoHs, REACH, California, Title 24, and Prop65.StandardsEN 60730-1, EN 60730-2-9, EN 301489-1, EN 301489-17, EN 300328, EN 301893, EN 62479, UL60730-1, UL60730-2-9, Title 47 part 15 subpart B, Title 47 part 15 subpart C, RSS 210, ICES-003Table 6. Communication TechnologiesBACnet IP Over Wi-FiWi-Fi802.11 b/g/nSupported security levels WPA,WPA3_WAP2_AES, WAP2_FBT_ENT, WPA2, WPA_ENT,WPA2_FBT, and WPA2_ENTBluetoothBLE 4.2 with 1 Mbps Classic Bluetooth with max. 3 Mbps Sylk TMHoneywell Sylk TMTable 7. Electrical CharacteristicsRated Impulse Voltage 500 VConstruction of Control Independently Mounted Control Operation Method Type 1 Action Pollution Degree 2Purpose of ControlOperating ControlTable 8. Supported Sensors and Functions Sensors Options Part Numbers Occupancy SensorDirect(Normally Open)Reverse (Normally Closed)Dry contactoccupancy sensorDirty Filter SensorDirect(Normally Open)Reverse (Normally Closed)DPS200, DPS400, DPS1000(Dry contact differentialpressure switch)Proof Of Air Flow SensorDirect(Normally Open)Reverse (Normally Closed)DPS200, DPS400, DPS1000(Dry contact airflow switch)Shutdown SensorDirect(Normally Open)Reverse (Normally Closed)Dry contactshutdown switchMixed Air Temperature Sensor NTC 20K, Type II NTC 10K, Type II SylkC7250C7021C7400S Outdoor Air Temperature Sensor NTC 20K, Type II NTC 10K, Type II Sylk C7250A C7021C7400S Return Air Temperature Sensor SylkC7400SDischarge Air Temperature Sensor NTC 20K, Type II NTC 10K, Type II SylkC7041C7021C7400SSpaceTemperature Sensors NTC 20K, Type II SylkTR21TR40/TR75 (max 4), TR120 (max 1)Fan Current Sensor Max Amps 0~<+Inf AmpsComing soonCO2 sensor (analog)0-10 VDC or Sylk Sylk C7232TR40-CO2, TR42-CO2Proof of waterflowDigital InputDry contactwaterflow switchTC500A COMMERCIAL THERMOSTAT31-00398M-02 | Rev. 04-214Terminal IdentificationFig. 1. TerminalsThermostat VariantsAccessoriesTable 9. Terminal IdentificationTerminalLabelConnection24VACR24VAC power from heating transformerC24VAC common (Neutral). For 2 transformer systems, use common wire from cooling transformerUIO11Universal input/output COM CommonUIO22Universal input/output COM Common UI11Universal input COM Common UI22Universal input COMCommonSylk (S-BUS)Sylk bus, master, power output Sylk bus, master, power outputRS485+BACnet Communications (coming soon)_BACnet Communications (coming soon)R-RCJumper between R and RC for single transformer system24VACRC 24VAC power from cooling transformer G FanY1Relay output, Compressor contactor (stage1)Y2Relay output, Compressor contactor (stage2)Y3Relay output, Compressorcontactor (stage3)/Configurable OutputW1Relay output, Heat (stage1)W2Relay output, Heat (stage2)W3Relay output, heat(stage3)/Configurable Output AuxRelay dry contact, Aux-1Relay dry contact, Aux-2Table 10. Thermostat Part NumbersTC500A-NThermostat with North American Wi-Fi conformanceTC500A-W (coming soon)Thermostat with outside of North American Wi-Fi conformanceTable 11. Accessories Part NumbersDecoplate-N TC500 deco plate for NA junction boxes Decoplate-WTC500 deco plate for Globe junction boxesTable 9. Terminal Identification TerminalLabel ConnectionTC500A COMMERCIAL THERMOSTAT531-00398M-02 | Rev. 04-21Terminal AssignmentsNOTE:*Marked sensors are supported in the future.Table 12. Terminal AssignmentsType Terminal LabelTerminal Assignments(Default & Optional Assignments)DEFAULTINPUTSOUTPUTSDigital OutputsDO1G Supply Fan High Speed FanDO2W1Heat Stage 1DO3W2Heat Stage 2DO4W3 / AuxHeat Stage 3Reversing Valve OB, Low Speed Fan,Occupancy, Simple Dehum, and Humidification.DO5Y1Cool Stage 1DO6Y2Cool Stage 2DO7Y3 / AuxCool Stage 3Economizer (Enable), Low Speed Fan,Occupancy, Simple Dehum, and Humidification.DO8(Dry Contact, 2 terminals)AuxEconomizer (Enable), Occupancy,Simple Dehum, Low Speed Fan, and Humidification.Universal InputsUI1(2 terminals)UI1NA Occupancy Sensor,Dirty Filter,Proof of Airflow,Shutdown Sensor,Mixed Air Sensor,Outdoor Air Sensor,Discharge Air Sensor,CO2 Sensor,Proof of Waterflow,Space Temp Sensor,*Filter Pressure sensor,*Compressor Current Sensor,*Fan Current Sensor,*Compressor Discharge, *Temperature sensor UI2(2 terminals)UI2NA Universal Inputs/ OutputsUIO1(2 terminals)UIO1NA Multi-Speed Fan (UIO1) Outdoor Air Damper UIO2(2 terminals)UIO2NAModulating Heat (UIO2) Outdoor Air DamperPowerRR 24v Power C C CommonRCRC 24v Power / Cooling Sylk Bus1S-BusSylk connection2TC500A COMMERCIAL THERMOSTAT31-00398M-02 | Rev. 04-216DIMENSIONS3 - 1/4” (82.75mm)TC500A COMMERCIAL THERMOSTAT731-00398M-02 | Rev. 04-21GENERAL SAFETY INFORMATION•When performing any work (installation, mounting, start-up), all manufacturer instructions and in particular the mounting Instructions guide (31-00399M) and the user guide (31-00400M) are to be observed.•TC500A-N/TC500A-W Thermostat may be installed and mounted only by authorized and trained personnel.•Rules regarding electrostatic discharge should be followed.•If TC500A-N/TC500A-W Thermostat is modified in any way, except by the manufacturer, all warranties concerning operation and safety are invalidated.•Make sure that the local standards and regulations are observed at all times.•Use only accessory equipment which comes from or has been approved by Honeywell.•It is recommended that devices be kept at roomtemperature for at least 24 hours before applying power. This is to allow any condensation resulting from low shipping/storage temperatures to evaporate.•Investigated according to United States Standard UL-60730-1, and UL60730-2-9.•Investigated according to Canadian National Standard(s) C22.2, No. 205-M1983 (CNL-listed).•Do not open TC500A-N/TC500A-W Thermostat, as it contains no user-serviceable parts inside!•CE declarations according to LVD Directive 2014/35/EU and EMC Directive 2014/30/EU.•Product standards are EN 60730-1 and EN 60730-2-9.•TC500A-N/TC500A-W Thermostat is Class B digital apparatus and complies with Canadian ICES-003.•This device complies with part 15 of the FCC Rules. Operation is subject to the following two conditions: (1) This device may not cause harmful interference, and (2) this device must accept any interference received, including interference that may cause undesired operation.•Caution: Changes or modifications to this unit not expressly approved by the party responsible forcompliance could void the user's authority to operate the equipment.•This device contains licence-exempttransmitter(s)/receiver(s) that comply with Innovation, Science and Economic Development Canada’s licence-exempt RSS(s). Operation is subject to the following two conditions:1.This device may not cause interference.2.This device must accept any interference, includinginterference that may cause undesired operation of the device.•L’émetteur/récepteur exempt de licence contenu dans le présent appareil est conforme aux CNR d’Innovation, Sciences et Développement économique Canada applicables aux appareils radio exempts de licence. L’exploitation est autorisée aux deux conditions suivantes:1.L’appareil ne doit pas produire de brouillage;2.L’appareil doit accepter tout brouillage radioélec -trique subi, même si le brouillage est susceptible d’en compromettre le fonctionnement.•This equipment has been tested and found to comply with the limits for a Class B digital device, pursuant to part 15 of the FCC Rules. These limits are designed to provide reasonable protection against harmfulinterference in a residential installation. This equipment generates uses and can radiate radio frequency energy and, if not installed and used in accordance with the instructions, may cause harmful interference to radio communications. However, there is no guarantee that interference will not occur in a particular installation. If this equipment does cause harmful interference to radio or television reception, which can be determined by turning the equipment off and on, the user isencouraged to try to correct the interference by one or more of the following measures:—Reorient or relocate the receiving antenna.—Increase the separation between the equipmentand receiver.—Connect the equipment into an outlet on a circuitdifferent from that to which the receiver is con -nected.—Consult the dealer or an experienced radio/TV tech -nician for help.•To satisfy FCC&IC RF exposure requirements, a separation distance of 20 cm or more should be maintained between the antenna of this device andpersons during device operation. To ensure compliance, operations at closer than this distance is not recommended.•Les antennes installées doivent être situées de facon à ce que la population ne puisse y être exposée à une distance de moin de 20 cm. Installer les antennes de facon à ce que le personnel ne puisse approcher à 20 cm ou moins de la position centrale de l’ antenne. Region Selection (for Wi-Fi 2.4G device)•Limited by local law regulations, version for North America does not have region selection option.Safety Information as per EN60730-1TC500A-N/TC500A-W Thermostat is intended for residential, commercial environments.TC500A-N/TC500A-W Thermostat is an independently mounted electronic control system with fixed wiring.TC500A-N/TC500A-W Thermostat is used for the purpose of building HVAC control and is suitable for use only in non-safety controls for installation on or in appliances.NoteAll images used in this document are for illustrative purposes only and may not match the actual product.TC500A COMMERCIAL THERMOSTAT® U.S. Registered Trademark© 2021 Honeywell International Inc.31-00398M-02 | Rev. 04-21Honeywell Building TechnologiesHoneywell715 Peachtree Street NE Atlanta, GA 。
AT5005_5006中英文说明书

Thanks for using our products, please read this manual thoroughly before operation
19 19 20 20
AT5005
Operating Instructions Control Elements Vertical Calibration Horizont of Spectrum Analyzers Spectrum Analyzer Requirements Frequency Measurements Resolution Sensitivity Video Filtering Spectrum Analyzer Sensitivity Frequency Response Tracking Generators
AT5005
Specifications
Frequency range: 0.1MHz to 1000MHz (lower frequency limit depends on probe type) Output impedance: 50 Output connector: BNC Input capacitance: 2pF (high imped Probe) Max. lnput Level: +10dBm (without destruction) 1dB-compression point: -2dBm (frequency range dependent) DC-input voltage: 20V max Supply Voltage: 6V DC, 4AA size batteries, Supply-power of Analyzer Supply Current: 8mA (H-Field Probe), 5mA (E-Fieldprobe), 24mA (High imp probe) Probe Dimensions: 195 40 19 (L*W*H)mm Housing: Plastic (electrically shielded internally)
Extech TM500 说明书.pdf_1697592638.6102712

User Manual12-Channel Thermocouple Datalogger Model TM500Additional User Manual Translations available at IntroductionCongratulations on your purchase of the Extech TM500 Thermometer, an SD Logger Series meter. This meter displays and stores temperature readings from up to twelve (12) Type K, J, T, R, E, or S thermocouple temperature probes. Logged data readings are stored on an SD card for transfer to a PC. This meter is shipped fully tested and calibrated and, with proper use, will provide years of reliable service. Please visit the Extech Instruments website () to check for the latest version of this User Guide.Meter Description1.Thermocouple inputs2.DC power adapter, SD memory slot, and PC interface jack3.Power ON‐OFF and Backlight key4.HOLD and NEXT key5.Power ON‐OFF and ESC key6.REC and ENTER7.TYPE ▲ key (K, J, T, R, E, or S)8.LOGGER (Offset) key9.SET (Time Check) key10.PAGE ▼ key (Display T1‐8 or T9‐12)26 810Display Description1.Temperature Channel number (1 – 8 or 9 – 12) 2.Thermocouple Type indicator (K, J, T, E, R, or S) 3.Temperature reading 4. Units of measure (C/F)Getting StartedPower ON ‐OFF∙ Power the meter by pressing the power button .∙ Press and hold the power button for at least 3 seconds to power OFF the meter.∙ This meter is powered by eight (8) 1.5VDC ‘AA’ batteries or by optional AC adaptor. If the meter will not switch ON please check that fresh batteries are installed in the rear battery compartment (refer to the battery replacement section later in this guide) or, in the case of the AC adaptor, check that the adaptor is connected correctly to the meter and to an AC source (refer to the AC Power Adaptor section later in this guide).Connecting Thermocouple SensorsThis meter can accept Thermocouple temperature probe Types K, J, T, E, R, or S.∙ Connect up to twelve (12) thermocouples to the sub ‐miniature jacks at the top of the meter labeled T1 through T12.∙ Select the desired mode of operation, and other setup features, in the Setup Mode. Refer to the Setup Mode section below.IMPORTANT NOTE : The supplied thermocouple probes are useable in the range of ‐20 to +250°C (‐4 to +482°F) only; even though the meter can display temperature values outside of this range. For measuring outside of the range specified here, please obtain thermocouples rated accordingly.14Setup ModeBasic settings at a glanceTo view the current configuration of the meter with regard to time, date, and datalogging sampling rate press the SET button for > 4 seconds. The meter will now display the configuration menu. The Setup page reverts to the temperature window in approximately 8 seconds if there are no button presses.Accessing the Setup mode1.Press and hold the SET button for at least 4 seconds to access the Setup menu.2.Press the NEXT button momentarily to step through the available parameters.3.When a parameter that is to be changed is flashing click ENTER to enter the change mode.Use the arrow keys to choose the setting and press the ENTER button to make the change.4.Note that the meter automatically switches out of the Setup mode if no key is pressedwithin 8 seconds.5.The available Setup parameters are listed below. Additional detailed information isprovided below this list:dAtE Set the clock (Year/Month/Date; Hours/Minutes/Seconds)LooP Start and End a loop measurement cycledEC Set the numerical format; USA (decimal: 20.00) or European (comma: 20,00)PoFF Automatic power‐off (Enable or disable the auto‐power off function)bEEP Set the beeper sound ON/OFFt‐CF Select the temperature unit of measure (C or F)SP‐t Set the datalogger sampling rate (1 to 3600 seconds)Sd F Format the SD memory cardSetting the Clock Time1.Access the dAtE parameter.2.Press the ENTER button.e the arrow buttons to change the YEAR value. Press ENTER to confirm setting.4.Repeat for MONTH, DAY, HOUR, MINUTE and SECONDS.5.Press the ENTER button to exit to the Setup mode. Press ESC to exit setup mode.Note: The clock will keep accurate time even when the meter is switched off. However, if the batteries expire the clock will have to be reset after fresh batteries are installed.Setting datalogging Loop modeThis meter can be set to record temperatures for the same time every day.Example – record temperatures every day from 9:00 to 13:001.Access the LooP parameter.2.Press the ENTER button.3.Set the Start Hour (0‐23) and press ENTER.4.Set the Start Minute and press ENTER.5.Set the Stop Hour and press ENTER.6.Set the Stop Minute and press ENTER.7.Press the up or down arrow to indicate YES and press ENTER.8.Press the REC button so the REC icon is visible on the display. The meter is now set up torecord temperature every day for the set time window.Setting dEC mode ‐ Numerical Format (comma or decimal)European and USA numerical formats differ. The meter defaults to USA mode where a decimal point is used to separate units from tenths, i.e. 20.00; The European format uses a comma, i.e. 20,00 to separate units from tenths. To change this setting:1.Access the dEC parameter.e the arrow buttons to select USA or EUro. Press ENTER to confirm setting.3.Press the ENTER button to exit to the Setup mode. Press ESC to exit setup mode. Setting Poff ‐ Enabling/Disabling the Auto Power OFF Feature1.Access the PoFF parameter.e the arrow buttons to select ON (enable) or OFF (disable). With the Auto Power OFFfeature enabled, the meter will automatically switch OFF after 10 minutes of inactivity.3.Press ENTER to confirm setting.4.Press the ENTER button to exit to the Setup mode. Press ESC to exit setup mode.Set the Beeper Sound ON or OFF1.Access the bEEP parameter.e the arrow buttons to select ON or OFF. Press ENTER to confirm setting.3.Press the ENTER button to exit to the Setup mode. Press ESC to exit setup mode.Set the Temperature Units of Measure (°C or °F)1.Access the t‐CF parameter.e the arrow buttons to select °C or °F. Press ENTER to confirm setting.3.Press the ENTER button to exit to the Setup mode. Press ESC to exit setup mode. Setting the Datalogger Sampling Time (Rate)1.Access the SP‐t parameter.e the arrow buttons to select the desired sampling rate. The available settings are: 0, 1, 2,5, 10, 30, 60, 120, 300, 600, 1800, and 3600 seconds. Use ‘0’ for manual logging mode.3.Press the ENTER button to confirm the entry.4.Press the ENTER button to exit to the Setup mode. Press ESC to exit setup mode.SD Card FORMATTING1.Access the Sd F parameter.e the arrow buttons to select YES to format the card (select NO to abort). Note that alldata on the card will be lost if formatting is attempted.3.Press ENTER to confirm selection.4.Press ENTER again to re‐confirm.5.Press the ENTER button to exit to the Setup mode. Press ESC to exit setup mode.Note: always format a new SD memory card before use.Measurements and related featuresBasic Thermocouple ModeThermocouples are connected at the top of the meter to the jacks labeled T1 through T12. Select the thermocouple type (J, K, etc.) to match the thermocouple type used. In normal thermocouple mode the meter will simultaneously display the temperature for thermocouples T1 through T12. Dashes are displayed if a thermocouple is not connected or if the measurement is out of range.Data HoldTo freeze a measurement on the display, press the HOLD button momentarily. The meter will emit a beep, the reading will hold, and the HOLD icon will switch on. Press the HOLD button again to release the display and exit the Data Hold mode returning the meter to the normal operating mode.Temperature Display OFFSETThe TM500 allows the user to set a display offset that applies to all of the thermocouple displays equally. To set the display offset follow the steps below:1.Press and hold the OFFSET button for 3 seconds to reach the offset screen. Thetemperature on the left is the currently displayed temperature for Channel 1 and thetemperature on the right is the offset temperaturee the up and down arrow keys to adjust the display on the right to offset the display asdesired.3.When finished, press the ENTER button to store the offset and return to normal operation.4.All of the thermocouple readings will now reflect the offset value programmed by theuser.To clear the OFFSET, follow the steps below:1.Switch the meter power OFF2.Press and hold the HOLD and REC buttons while switching the meter power ON3.Release the two buttons when the meter switches ON4.Press and hold the OFFSET button for 5 seconds and the display will show CODE 100e the up arrow button to change from CODE 100 to CODE 125 and then press ENTERe the arrow buttons to select YES or NO and then press ENTER7.If YES is selected, the meter will clear the previously programmed offset. If NO is selected,the meter will retain the offset programmed by the user.MAX‐MIN ReadingsFor a given measurement session, this meter can record the highest (MAX) and the lowest (MIN) readings for later recall.1.Press the REC button momentarily to access this mode of operation (REC icon appears)2.The meter is now recording the MAX and MIN readings.3.Press the REC button again to view the current MAX readings (MAX icon appears). Thereadings on the display are now the highest readings encountered since the REC icon was switched on (when the MAX‐MIN button was first pressed). To delete the MAX value, press the HOLD button. The display will show just the REC icon.4.Press the REC button again to view the current MIN readings (MIN icon appears). Thereadings on the display are now the lowest readings encountered since the REC icon wasswitched on (when the MAX‐MIN button was first pressed). To delete the MIN value, press the HOLD button. The display will show just the REC icon.5.To exit the MAX‐MIN mode, press and hold the REC button for at least 1.5 seconds. Themeter will beep, the REC‐MAX‐MIN icons will switch off, the MAX‐MIN memory will clear, and the meter will return to the normal operating mode.Display BacklightTo turn the display backlight ON or OFF, press the backlight button momentarily. The meter will beep when switching the backlight ON or OFF unless the beeper is disabled as described in the Setup Mode section of this user guide.Time CheckMomentarily press the SET button and the meters current Date and Time will appear in the lower left corner of the display.Sampling Time CheckWhen in normal mode, press the LOGGER button momentarily. The Sample rate setting will appear in the lower left corner of the display.AC Power AdaptorThis meter is normally powered by eight (8) 1.5V ‘AA’ batteries. An optional 9V power adaptor is available. When the adaptor is used, the meter is permanently powered and the power button will be disabled.DataloggingTypes of Data Recording∙Manual Datalogging: Manually log up to 99 readings onto an SD card via push‐button press.The sample rate must be set to 0 to implement this mode.∙Automatic Datalogging: Automatically log data onto an SD memory card where the number of data points is virtually limited only by the card size. Readings are logged at a rate specified by the user from 1 to 3600 seconds.SD Card Information∙Insert an SD card (from 1G size up to 16G) into the SD card slot at the bottom of the meter.The card must be inserted with the front of the card (label side) facing toward the rear of the meter.∙If the SD card is being used for the first time it is recommended that the card be formatted and the logger’s clock set to allow for accurate date/time stamping during dataloggingsessions. Refer to the Setup Mode section for SD card formatting and time/date settinginstructions.∙European and USA numerical formats differ. The data on the SD card can be formatted for either format. The meter defaults to USA mode where a decimal point is used to separate units from tenths, i.e. 20.00. The European format uses a comma, i.e. 20,00. To change this setting, refer to the Setup Mode section.Manual DataloggingIn the manual mode the user presses the LOG button to manually log a reading onto the SD card.1.Set the sampling rate to ‘0’ seconds as described in the Setup Mode section.2.Press REC button to turn on manual record mode. The REC icon will appear in the upperleft corner of the display. The lower portion of the display will show p‐n (n = memoryposition number 1‐99).3.Press the ENTER button momentarily to log a reading into memory. The LOGGER icon willflash each time a data point is stored (the SCAN SD icon will appear when the meteraccesses the card).4.Advance to the next memory location using the up arrow ▲ button.5.To exit the manual datalogging mode, press and hold the REC button for at least 1.5seconds.Automatic DataloggingIn automatic datalogging mode the meter takes and stores a reading at a user‐specified sampling rate onto a SD memory card. The meter defaults to a sampling rate of two seconds. To change the sampling rate, refer to the Setup Mode section (the sampling rate cannot be ‘0’ for automatic datalogging):1.Press REC button to turn on record mode. The REC icon will appear in the upper left cornerof the display.2.Start an automatic Datalogging session by pressing the LOGGER button.3.The meter will scan for an SD card and verify that it can be used to store data. If a card isnot inserted or if the card is defective, the meter will display SCAN SD indefinitely. In thiscase, switch the meter OFF and try again with a valid SD card.4.If the SD card is valid, the display will show the DATALOGGER icon and then theDATALOGGER and the REC icons will flash each time that a reading is stored.5.To pause the datalogger press the LOGGER button momentarily. The DATALOGGER and RECicons will stop flashing. To resume logging simply press the LOGGER button againmomentarily.6.To terminate the datalogging session press the LOGGER button to stop the logging and thenpress the REC button for at least 1.5 seconds.7.When an SD card is used for the first time a folder is created on the card and namedTMD01. Up to 99 spreadsheet documents (each with 30,000 readings) can be stored in this folder.8.When datalogging begins a new spreadsheet document named TMD01001.xls is created onthe SD card in the TMD01 folder. The data recorded will be placed in the TMD01001.xlsdocument until 30,000 readings are reached.9.If the measurement session exceeds 30,000 readings, a new document will be created(TMD01002.xls) where another 30,000 readings can be stored. This method continues forup to 99 documents, after which another folder is created (TMD02) where another 99spreadsheet documents can be stored. This process continues in this same fashion withfolders TMD03 through TMD10 (last allowable folder).SD Data Card to PC Data Transferplete a datalogging session as detailed in above in the previous sections. Hint: For thefirst test, simply record a small amount of test data. This is to ensure that the datalogging process is well understood before committing to critical datalogging.2.With the meter switched OFF, remove the SD Card.3.Plug the SD Card directly into a PC SD card reader. If the PC does not have an SD card slot,use an SD card adaptor (available at a store where computer accessories are sold).4.Power the PC and run a spreadsheet software program (Microsoft Excel). Open the saveddocuments in the spreadsheet software program (see example spreadsheet data screens below).Spreadsheet data exampleSpreadsheet example (Plotting the data)Battery Replacement and DisposalWhen the low battery icon appears on the LCD, the batteries must be replaced. Several hours of accurate readings are still possible in this condition; however, batteries should be replaced as soon as possible:∙Remove the two (2) Phillips screws from the rear of the meter.∙Remove and safely place the battery compartment and screws where they will not be lost. ∙Replace the eight (8) 1.5V ‘AA’ batteries observing polarity.∙Replace the battery compartment cover with the two (2) Phillips screws.Battery Safety Reminders∙ Never dispose of batteries in a fire. Batteries may explode or leak.∙Never mix battery types. Always install new batteries of the same type.Never dispose of used batteries or rechargeable batteries in household waste.As consumers, users are legally required to take used batteries to appropriatecollection sites, the retail store where the batteries were purchased, or whereverbatteries are sold.Disposal: Do not dispose of this instrument in household waste. The user is obligatedto take end‐of‐life devices to a designated collection point for the disposal ofelectrical and electronic equipment.SpecificationsGeneral SpecificationsDisplay Backlit LCD; LCD size: 82×61mm (3.23×2.40")Status indicators Over‐range (‐‐‐‐) and low batteryMeasurement Channels T1 to T12Sensor types Thermocouple types: K, J, T, E, R, and SMeasurement Units °C / °FOffset Adjustment To adjust the zero temperature deviation valueLinearity Compensation Linear compensation for the full rangeSampling Rate AUTO LOGGING: 1, 2, 5, 10, 30, 60, 120, 300, 600, 1800,3600 seconds.Memory Card SD memory card; 1G to 16GB sizeTemperature Compensation Automatic compensation for all thermocouple types Display update rate Approx. 1 second.Thermocouple inputs Single ended type (negative input grounded)Max. common mode voltage: 30VDCData Output RS‐232 serial protocolOperating Temperature 0 to 50°C (32 to 122°F)Operating Humidity 85% R.H. maximumAuto Power OFF A fter 10 minutes of inactivity (can be disabled)Power Supply Eight (8) 1.5 VDC batteries (optional 9V AC adaptor) Power Consumption With backlight & datalogger OFF: approx. 7.5mA dc With backlight OFF and datalogger ON: approx. 25mA dc With backlight ON and datalogger ON: approx. 36mA dc Weight 827g (1.84 lbs.) meter onlyDimensions Main instrument: 225 x 125 x 64mm (8.86 x 4.92 x 2.52”)Thermocouple Input (types K, J, T, E, R, and S)▪ The supplied thermocouple probes are useable in the range of ‐20 to +250°C (‐4 to +482°F) only. For measuring outside of this range, please obtain thermocouples rated accordingly. ▪ Accuracy specified for meter only. Input probes add additional measurement error.▪ The above specifications are tested under an environmental RF Field Strength lower than 3 V/M and a frequency lower than 30 MHzCopyright © 2013‐2016 FLIR Systems, Inc.All rights reserved including the right of reproduction in whole or in part in any formISO ‐9001 CertifiedSensor TypeResolution RangeAccuracyType K0.1°C‐100.0 to ‐50.1°C ±(0.4 % + 1°C) ‐50.0 to 999.9°C ±(0.4 % + 0.5°C) 1°C 1000 to 1300°C ±(0.4 % + 1°C) 0.1°F ‐148.0 to ‐58.1°F ±(0.4 % + 1.8°F) ‐58.0 to 999.9°F ±(0.4 % + 1°F) 1°F 1000 to 2372°F ±(0.4 % + 2°F) Type J0.1°C‐100.0 to ‐50.1°C ±(0.4 % + 1°C ) ‐50.0 to 999.9°C ±(0.4 % + 0.5°C) 1°C 1000 to 1150°C ±(0.4 % + 1°C) 0.1°F ‐148.0 to ‐58.1°F ±(0.4 % + 1.8°F) ‐58.0 to 999.9°F ±(0.4 % + 1°F ) 1°F 1000 to 2102°F ±(0.4 % + 2°F) Type T0.1°C‐100.0 to ‐50.1°C ±(0.4 % + 1°C) ‐50.0 to 400.0°C ±(0.4 % + 0.5°C) 0.1°F ‐148.0 to ‐58.1°F ±(0.4 % + 1.8°F) ‐58.0 to 752.0°F ±(0.4 % + 1°F ) Type E0.1°C‐100.0 to ‐50.1°C ±(0.4 % + 1°C) ‐50.0 to 900.0°C ±(0.4 % + 0.5°C) 0.1°F ‐148.0 to ‐58.1°F ±(0.4 % + 1.8°F) ‐58.0 to 999.9°F ±(0.4 % + 1°F ) 1°F 1000 to 1652°F ±(0.4 % + 2°F) Type R1°C0 to 600°C ±(0.5 % + 3°C) 601 to 1700°C 1°F 32 to 1112°F ±(0.5 % + 5°F) 1113 to 3092°F Type S1°C0 to 600°C ±(0.5 % + 3°C) 601 to 1500°C 1°F32 to 1112°F ±(0.5 % + 5°F)1113 t o 2732°F。
MEC ATLAS_500 Instruction-Manual
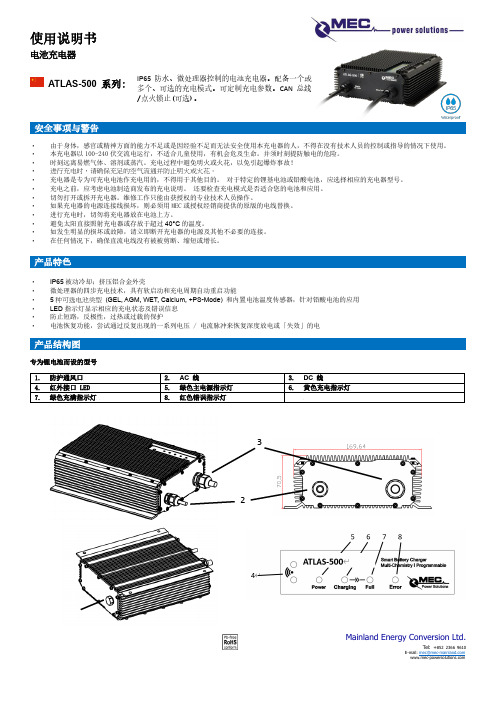
使用说明书电池充电器ATLAS-500 系列:安全事项与警告•由于身体,感官或精神方面的能力不足或是因经验不足而无法安全使用本充电器的人,不得在没有技术人员的控制或指导的情况下使用。
•本充电器以100-240伏交流电运行,不适合儿童使用,有机会危及生命。
并须时刻提防触电的危险。
•时刻远离易燃气体、溶剂或蒸汽。
充电过程中避免明火或火花,以免引起爆炸事故!•进行充电时,请确保充足的空气流通并防止明火或火花。
•充电器是专为可充电电池作充电用的,不得用于其他目的。
对于特定的锂基电池或铅酸电池,应选择相应的充电器型号。
•充电之前,应考虑电池制造商发布的充电说明。
还要检查充电模式是否适合您的电池和应用。
•切勿打开或拆开充电器。
维修工作只能由获授权的专业技术人员操作。
•如果充电器的电源连接线损坏,则必须用MEC或授权经销商提供的原版的电线替换。
•进行充电时,切勿将充电器放在电池上方。
•避免太阳直接照射充电器或存放于超过40°C的温度。
•如发生明显的损坏或故障,请立即断开充电器的电源及其他不必要的连接。
•在任何情况下,确保直流电线没有被被剪断、缩短或增长。
产品特色•IP65被动冷却;挤压铝合金外壳•微处理器的四步充电技术,具有软启动和充电周期自动重启功能•5种可选电池类型(GEL, AGM, WET, Calcium, +PS-Mode) 和内置电池温度传感器,针对铅酸电池的应用•LED指示灯显示相应的充电状态及错误信息•防止短路,反极性,过热或过载的保护•电池恢复功能,尝试通过反复出现的一系列电压 / 电流脉冲来恢复深度放电或「失效」的电产品结构图专为锂电池而设的型号1.防护通风口2.AC线3.DC线4.红外接口 LED5.绿色主电源指示灯6.黄色充电指示灯7.绿色充满指示灯8.红色错误指示灯IP65 防水、微处理器控制的电池充电器。
配备一个或多个、可选的充电模式。
可定制充电参数。
CAN 总线/点火锁止(可选)。
PlatinumTools TP500商品说明书

FEATURES•Tests for shorts, opens, miswires, reversals and split pairs•Auto-on and auto-off when testing cables, just plug both ends into tester!•Automatically tests for shorts with one end plugged into the tester•Cable test results displayed on main unitand remote unit, in less than 2 seconds afterplugging in the cable•Snap-together case for easy storage andconvenient patch cable testing•Tone generator mode for use with tone tracers, auto-off•Debug mode with from/to and failures for each pair•Battery low indicatorMain Unit Results – The main unit indicates thebeginning of a test by flashing the pair lights in sequencetop to bottom. The cable is then tested and the resultsdisplayed as follows:Pair light off – Pair is open. Depending on the wiringstandard, this may be correct.Pair light on – Pair is wired correctly.Pair light is flashing – One or more errors weredetected for this pair, as indicated by flashing errorlights.If there are no flashing lights, the results are displayedfor 2 seconds.If there was an error, the results are displayed for twiceas long.If the lights for the pairs expected are on, the cable isgood.Remote Unit Results – The remote unit indicates thebeginning of a test by flashing the pair lights quickly, theorder or number of lights flashed depends on the cablebeing tested.Debug Mode – (See “Ethernet Up-Link Cable Example”)Pair connected from1-2 to 3-6 (miswire)Pair connected from3-6 to 1-2 (miswire)Pair connected from4-5 to 4-5 (good)Pair connected from7-8 to 7-8 (good)。
Atlona AT-HD-SC-500 产品说明书
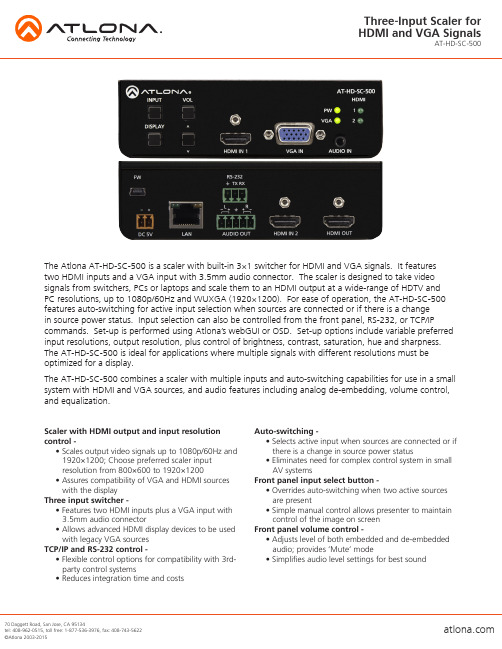
The Atlona AT-HD-SC-500 is a scaler with built-in 3×1 switcher for HDMI and VGA signals. It featurestwo HDMI inputs and a VGA input with 3.5mm audio connector. The scaler is designed to take video signals from switchers, PCs or laptops and scale them to an HDMI output at a wide-range of HDTV and PC resolutions, up to 1080p/60Hz and WUXGA (1920×1200). For ease of operation, the AT-HD-SC-500 features auto-switching for active input selection when sources are connected or if there is a changein source power status. Input selection can also be controlled from the front panel, RS-232, or TCP/IP commands. Set-up is performed using Atlona’s webGUI or OSD. Set-up options include variable preferred input resolutions, output resolution, plus control of brightness, contrast, saturation, hue and sharpness. The AT-HD-SC-500 is ideal for applications where multiple signals with different resolutions must be optimized for a display.The AT-HD-SC-500 combines a scaler with multiple inputs and auto-switching capabilities for use in a small system with HDMI and VGA sources, and audio features including analog de-embedding, volume control, and equalization.Scaler with HDMI output and input resolution control -• Scales output video signals up to 1080p/60Hz and 1920×1200; Choose preferred scaler inputresolution from 800×600 to 1920×1200• Assures compatibility of VGA and HDMI sources with the displayThree input switcher -• Features two HDMI inputs plus a VGA input with 3.5mm audio connector• Allows advanced HDMI display devices to be used with legacy VGA sourcesTCP/IP and RS-232 control -• Flexible control options for compatibility with 3rd- party control systems• Reduces integration time and costs Auto-switching -• Selects active input when sources are connected or if there is a change in source power status• Eliminates need for complex control system in small AV systemsFront panel input select button -• Overrides auto-switching when two active sources are present• Simple manual control allows presenter to maintain control of the image on screenFront panel volume control -• Adjusts level of both embedded and de-embedded audio; provides ‘Mute’ mode• Simplifies audio level settings for best soundSpecificationsSpecifications and availability subject to change without notice. Actual products, product images, and online product images may vary from images shown Video ResolutionsIN ***********/24/25/29.97/30/50/59.94/60Hz,1080i@50/59.94/60Hz,720p@50/59.94/60Hz,576p, 576i, 480p, 480i 1920x1200, 1680x1050, 1600x1200, 1600x900, 1440x900, 1400x1050, 1366x768, 1360x768, 1280x1024, 1280x800, 1280x768, 1152x864, 1024x768, 800x600, 640x480Preferred input resolution800x600, 1024x768, 1280x720, 1280x800, 1366x768, 1920x1080, 1920x1200OUT ***********/24/25/29.97/30/50/59.94/60Hz,1080i@50/59.94/60,720p@25/29.97/30/50/59.94/60 800x600, 1024x768, 1280x800, 1280x1024, 1366x768, 1400x1050, 1600x900, 1600x1200, 1680x1050, 1920x1200 Color Space YUV, RGB Chroma Subsampling 4:4:4, 4:2:2Color Depth 8-bit, 10-bit, 12-bitAudioAnalog IN 3.5mm stereo jack, -10 dBu nominal inputAnalog OUT Balanced, +4 dBu nominal analog output. Max output +18 dBu (only from 2Ch PCM sources) HDMI PCM 2Ch, LPCM 5.1, LPCM 7.1, Dolby Digital, DTS 5.1, Dolby Digital Plus, Dolby TrueHD, DTS-HD Master Audio, Dolby AtmosSample Rate 32kHz, 44.1kHz, 48kHz, 88.2kHz, 96kHz, 176.4kHz, 192kHz Bit rate up to 24-bit DistanceHDMI @ 1080pup to 10 metersup to 30 feetSignalBandwidth 6.75 Gbps CEC HDCP Switchable - Compliant/Non-compliantTemperatureOperating 0°C to 50°C 32°F to 122°F Storage -20°C to 60°C -4°F to 140°F Humidity 20 to 90% non-condensingPowerConsumption 10.4W Supply Input: AC100-240V ~ 50/60Hz 0.5A Output: DC 5V/3.6ADimensionH x W x D 38 x 127 x 102 (mm) 1.5 x 5 x 4.02 (inch)WeightDevice 0.27 kg 0.60 lbs。
AT500 600安装调试操作手册

AT500/600磁致伸缩液位/界位变送器安装调试操作手册目录一、存放 (3)二、安装和启动 (3)2.1 接线 (3)2.2 确定4Ma和20Ma设定点 (4)2.3 倒置安装 (4)2.4 高/低报警点设定 (4)2.5 4MA/20MA交直流微调 (5)三、故障处理信息 (7)3.1 正确上电 (7)3.2 输出稳定性 (7)一.存放如果需要,应该存放在优于安装条件的环境温度下并置于室内,不能超出以下范围:温度范围:-40-65℃湿度范围:0--100% R.H. 无冷凝二.安装和启动注意:在安装AT500/600浓缩(简易)型磁致伸缩变送器时,探管是与一套特氟隆套圈一体运送的,另有一套不锈钢套圈单独装在一个袋子里。
特氟隆套圈只应用于低压场合,最于高压场合只能用不锈钢套圈。
2.1接线连接导线到1/2"电器接口,然后用18线规的双绞线连接变送器外壳,用适当的导线密封装置以排除可能渗透的潮气。
变送器按以下方式回路供电:# Terminal Block+:24 VDC(+14VDC最小到+36VDC最大)# Terminal Block-:共同端/电流表# Terminal Block :电流表# Terminal Block:接地(确认接地正确,以排除可能存在的干扰)2.2确定4MA和20MA设定点本产品是无须日常标定的电子变送器。
如果需要重新标定,可以使用右图标出的开关点按照以下步骤标定:设定4MA/0%点-使罐内物位为0%-把磁棒放置于X处两秒钟进入标定模式-把磁棒从X处移动到Z处设置0点(4MA),这一步是通过检查输出是4.00MA来确定的。
设定20MA/100%点-使罐内物位为100%-把磁棒放置于X处两秒钟进入标定模式-把磁棒从X处移动到S处设置满量程点(20MA),这一步是通过检查输出是20.00MA来确定的。
注:以上步骤可以根据需要任意重复。
2.3倒置安装如果需要,变送器输出可以通过以下步骤倒转(注:使4-20Ma输出倒转)使物位在50%处(+or-10%)-把磁棒放置于X处两秒钟进入标定模式-把磁棒从X处移动到Z处设置0点(4MA)这一步是通过检查输出是4.00MA来确定的。
Catphan500-600manual
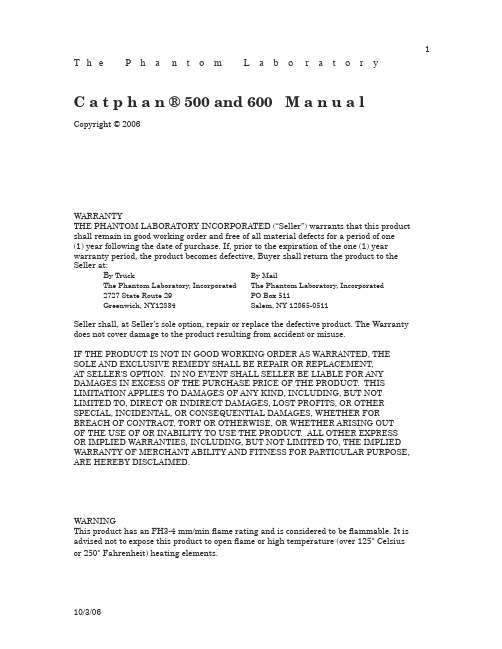
1 T h e P h a n t o m L a b o r a t o r yC a t p h a n ® 500 and 600 M a n u a lCopyright © 2006WARRANTYTHE PHANTOM LABORATORY INCORPORATED (“Seller”) warrants that this product shall remain in good working order and free of all material defects for a period of one(1) year following the date of purchase. If, prior to the expiration of the one (1) year warranty period, the product becomes defective, Buyer shall return the product to theSeller at:B y Truck By MailThe Phantom Laboratory, Incorporated The Phantom Laboratory, Incorporated2727 State Route 29 PO Box 511Greenwich, NY12834 Salem, NY 12865-0511Seller shall, at Seller’s sole option, repair or replace the defective product. The Warranty does not cover damage to the product resulting from accident or misuse.IF THE PRODUCT IS NOT IN GOOD WORKING ORDER AS WARRANTED, THESOLE AND EXCLUSIVE REMEDY SHALL BE REPAIR OR REPLACEMENT,AT SELLER’S OPTION. IN NO EVENT SHALL SELLER BE LIABLE FOR ANY DAMAGES IN EXCESS OF THE PURCHASE PRICE OF THE PRODUCT. THIS LIMITATION APPLIES TO DAMAGES OF ANY KIND, INCLUDING, BUT NOTLIMITED TO, DIRECT OR INDIRECT DAMAGES, LOST PROFITS, OR OTHER SPECIAL, INCIDENTAL, OR CONSEQUENTIAL DAMAGES, WHETHER FORBREACH OF CONTRACT, TORT OR OTHERWISE, OR WHETHER ARISING OUTOF THE USE OF OR INABILITY TO USE THE PRODUCT. ALL OTHER EXPRESSOR IMPLIED WARRANTIES, INCLUDING, BUT NOT LIMITED TO, THE IMPLIED WARRANTY OF MERCHANT ABILITY AND FITNESS FOR PARTICULAR PURPOSE, ARE HEREBY DISCLAIMED.WARNINGThis product has an FH3-4 mm/min flame rating and is considered to be flammable. It is advised not to expose this product to open flame or high temperature (over 125° Celsiusor 250° Fahrenheit) heating elements.10/3/0623 T h e P h a n t o m L a b o r a t o r yCatphan® ManualContentsWarranty 1Introduction 5Multi-Slice CT by David Goodenough, Ph.D. 6Initial phantom positioning 8Illustration of Catphan® models 9Incremental phantom modules positioning 10Phantom position verification 11CTP401 and CTP404 modules 12Patient alignment system check 13Scan slice geometry (slice width) 14Scan incrementation 15Circular symmetry 16Spatial linearity of pixel size verification 16Spherical acrylic contrast targets 16Sensitometry (CT number linearity) 17CTP591 Bead Geometry Module 18CTP528 High resolution module with 21 line pair per cm gauge and point source 19 Bead point source for point spread function and MTF 19Use of automated scanner MTF programs 20Bead point source (slice sensitivity profile) 2121 Line pair per centimeter high resolution gauge 22CTP515 Low contrast module with supra-slice and subslice contrast targets 23CTP486 Image uniformity module 25Installation and removal of test modules 27Optional phantom annuli 28Optional phantom housings 29Dose Phantoms 30Sample quality assurance program 31Automated computer analysis program 31Bibliography 3245 IntroductionThe Phantom Laboratory and physicist, David J. Goodenough, Ph.D., are continually developing and researching new tests and modifications for the Catphan® phantoms.The test objects that make up the current Catphan® models embody more than aquarter century of scientific evaluation and field experience. This manual outlines the applications of each module contained in the Catphan® 500 and 600 phantoms.We do not make specific recommendations on the content of your quality assurance program, because each medical imaging facility has its own unique set of requirements.A sample program is provided to give you ideas for possible program content. We suggesta review of local governing regulations, manufacturers’ specifications and the needs ofyour radiologists and physicists before developing your CT quality assurance program.The Catphan® instructional video, which illustrates the phantom setup and scanning ofthe different Catphan® sections, is also available.If you have any additional questions please contact The Phantom Laboratory at:Phone: 800-525-1190 or 518-692-1190Fax: 518-692-3329email: sales@Additional product information is available at: 6Multi-Slice CTby David J. Goodenough, Ph.D.At the request of The Phantom Laboratory I have put together this summary forphysicists who are familiar with CT image performance measurements and have not had experience with multi-slice CT scanners.Multi-slice uses the same basic approach to image reconstruction as axial single slice CT. Both modalities use the data from the detectors (positioned 360° around the patient) to reconstruct the axial patient images. The key difference between axial single slice CT and multi-slice is the axial image produced by single slice CT is developed from a single row of detectors, and the axial image made from a multi-slice scanner uses segments from several rows of detectors. With a multi-slice scan, as the patient moves through the gantry and the tube rotates around the patient, the detector rows utilized change as the patient and gantry move (see sketch on the next page).Additional variables in reconstruction result as the patient slice moves from one row of detectors to the next and the scanner reconstructs the images based on weightedaverages between the relevant rows. In this way, multi-slice CT is analogous to spiral or helical single slice CT, but where the reconstruction is obtained from the combined slices rather than the interpolation between the readings of a single moving slice. Now add in focal spot variables and a little scatter to define in more detail the challenges and variables included in the reconstruction of a multi-slice image.Because in spiral mode each multi-slice image is reconstructed from an ensemble of data taken in different positions across the beam and from different detector rows, the overall image quality differences between images are minimal. In the spiral mode each slice represents data as seen from all detector rows in a sense a kind of averaging of detector row positions. However, if you use a multi-slice “step and shoot” mode, where each of the slices may be created from a single detector row (or rows depending on the selected slice thickness) with a consistent collimation, the differences between the slices will be evident. Step and shoot mode in a multi-slice CT scanner is operated like a conventional axial scanner by imaging with a fixed table position and then moving the table to the next position before imaging the next section of the phantom with a fixed table position.For example, with a step and shoot 8 slice scan it is expected that the middle slicenumbers 4 and 5 will have better uniformity than outer slice numbers 1 and 8 because of the scanner x-ray beam geometry. However, if 1 and 8 or 4 and 5 are not similar, this may indicate a problem with the scanner.When assessing a scanner with a step and shoot mode, it is important to cover the full detector width with the selected test objects. If the test object is narrower than the slice, the table will need to be incremented between scanning sequences so the object can be scanned by all active rows of the detector.I recommend scanning through the entire phantom using different multi-slice spiralprotocols for performance evaluations, as well as using the step and shoot approach for the bead ramps where slice geometry and the MTF can be measured for each slice and uniformity section where the signal to noise and uniformity of each slice (detector row) can be evaluated.7This simplified illustration of a multi-slice sequence shows how the slices are reconstructed with information for different detector rows. The imaging sequence of thefirst selected slice (slice 1) of the patient begins when slice 1 moves over detector row A.As the tube continues to rotate and the patient continues to move through the gantry,slice 1 is picked up by the detectors in row B. At the same time slice 2, which was outside the detector view, is picked up by the detectors in row A. This sequence continues untilthe last selected region of the patient has passed through all the active detector rows.8Initial phantom positioningThe Catphan® phantom is positioned in the CT scanner by mounting it on the case.Place the phantom case on the gantry end of the table with the box hinges away from the gantry. It is best to place the box directly on the table and not on the table pads.Open the box, rotating the lid back 180°. If you are using an annulus, additional weight will need to be placed in the box to counterweigh the phantom. The patient straps can be used for additional stability.Remove the phantom from the box and hang the Catphan® from the gantry end of the box. Make sure the box is stable with the weight of the phantom and is adequatelycounterweighed to prevent tipping.Use the level and adjusting thumb screws to level the Catphan®. Once the phantom is level, slide the phantom along the end of the box to align the section center dots on the top of the phantom with the x axis alignment light.Use the table height and indexing drives to center the first section’s (CTP401 or CTP404, Slice Geometry) alignment dots on the side and top of the phantom with the scanner alignment lights.The z axis scan alignment position can be selected from the localizer scan, by centering the slice at the intersection of the crossed wire image created by the slice width ramps.Scan the first section (CTP401 or CTP404) and check the image for proper alignment as illustrated in the Phantom position verification section.9 Illustration of Catphan® 500 and 600 modelsCatphan® 500Catphan® 60010Incremental phantom module positioningThe Catphan® phantoms are designed so all test sections can be located by precisely indexing the table from the center of section 1 (CTP401 or CTP404) to the center of each subsequent test module. This design eliminates the need to remount the phantom once the position of section 1 (CTP401 or CTP404) has been verified. The indexing distances from section 1 are listed below. Additional illustrations on the preceeding page show the test modules and their index spacing. Phantom position and alignment verification is described on the next page.Catphan® 500 test module locations:Module Distance from section 1 centerCTP401CTP528, 21 line pair high resolution 30mmCTP528. Point source 40mmCTP515, Subslice and supra-slice low contrast 70mmCTP486, Solid image uniformity module 110mm Catphan® 600 test module locations:Module Distance from section 1 centerCTP404CTP591 Bead geometry 32.5mmCTP528, 21 line pair high resolution 70mmCTP528. Point source 80mmCTP515, Subslice and supra-slice low contrast 110mmCTP486, Solid image uniformity module 150mmPhantom position verificationBy evaluating the scan image of section 1 (CTP401 or CTP404) the phantom’s position and alignment can be verified. The section contains 4 wire ramps which rise at 23° angles from the base to the top of the module. The schematic sketches below indicate how the ramp images change if the scan center is above or below the z axis center of the test module. The use of the scanner’s grid image function may assist in evaluation ofphantom position.In this image the x, y symmetry of the centered ramp images indicates proper phantom alignment.When the ramps are evenly rotated clockwise from center, the phantom is too far into the gantry.When the ramps are evenly rotated counter-clockwise from center, the phantom needs to be moved toward the gantry. Poor alignment with the z axis is indicated when the ramps are not symmetrical in lenghts and rotation. If misalignment is indicated by the scan image, the phantom should be repositioned to obtain proper alignment and then rescanned. If the images of the repositioned phantom duplicate the original misalignment indications, the scanner’s alignment lights may require adjustment (contact your local service engineer).Once correct alignment has been established, you can proceed with the tests.CTP401 Module with slice width, sensitometry and pixel sizeCTP404 Module with slice width, sensitometry and pixel sizePatient alignment system checkThe laser, optical, and mechanical patient alignment system can be checked for accuracy. Align the white dots on the phantom housing with the alignment lights as discussedin Initial phantom positioning. The scanned image should show good alignment as discussed in Phantom position verification.For measuring the z axis alignment accuracy, measure from the center of the ramp image to the part of the ramp which aligns with the center of the phantom and sensitometry samples. Multiply the distance A by 0.42 to determine the z axis alignment light accuracy. To evaluate x and y accuracy, measure from the center of the phantom to the center of the scan field by use of the grid function or knowledge of the central pixel location.The accuracy of the localizer, pilot or scout view can be checked. To check this function perform a localization scan of the phantom. Align an axial scan at the crossing point of the wire ramps. Scan this axial cut and check the misalignment as discussed above.Scan slice geometry (slice width)Section 1 has two pairs of 23° wire ramps: one pair is oriented parallel to the x axis; the other pair to the y axis. These wire ramps are used to estimate slice width measurements and misalignment errors as previously discussed.Measuring slice width with the 23° wire ramps. The ramp angle is chosen tooffer trigonometric enlargement of 2.38 in the x-y image plane.To evaluate the slice width (Zmm), measure the Full Width at Half Maximum (FWHM) length of any of the four wire ramps and multiply the length by 0.42:(Zmm) = FWHM * 0.42To find the FWHM of the wire from the scan image, you need to determine the CT number values for the peak of the wire and for the background.To calculate the CT number value for the maximum of the wire, close down the CT “window” opening to 1 or the minimum setting. Move the CT scanner “level” to the point where the ramp image just totally disappears. The CT number of the level at this position is your peak or maximum value.To calculate the value for the background, use the region of interest function to identify the “mean” CT number value of the area adjacent to the ramp.Using the above CTvalues, determine the half maximum:First calculate the net peak... (CT # peak - background = net peak CT #) Calculate the 50% net peak... (net peak CT # ÷ 2 = 50% net peak CT #) Calculate the half maximum CT number...(50% net peak CT # + background CT # = half maximum CT #)Now that you have determined the half maximum CTnumber, you can measure the full width at half maximum of the ramp. Set the CT scanner level at the half maximumCT value and set your window width at 1. Measure the length of the wire image to determine the FWHM. Multiply the FWHM by 0.42 to determine the slice width.Schematic illustration of two sequential 5mm scans superimposed. L1 isthe center point on the 23° ramp in the first scan image and L2 is thecenter point on the 23° ramp on the second image.Scan incrementationUse the wire ramps to test for proper scanner incrementation between slices, and for table movement.Scan section 1 using a given slice width, (e.g. 5mm). Increment the table one slice width (e.g. 5mm) and make a second scan. Establish the x and y coordinates for the center of each ramp image. Calculate the distance between these points and multiply by the 23° ramp angle correction factor of 0.42.0.42(L1 - L2) = scan incrementationThis test can also be used to test table increment accuracy. Scan the section and increment the table 30mm in and out of the gantry and scan again. The ramp centers should be the same on both images.0.42(L1 - L2) = 0Circular symmetry of display systemThe circular phantom sections are used to test for circular symmetry of the CT image, including calibration of the CT display system. If an elliptical image is produced, the x-y balance of the image display system should be adjusted.Measuring spatial linearity in x and y axes.Spatial linearity of pixel size verificationThis section has four holes (one with a Teflon pin). These 3mm diameter holes are positioned 50mm on center apart. By measuring from center to center the spatial linearity of the CT scanner can be verified. Another use is to count the number of pixels between the hole centers, and by knowing the distance (50mm) and number of pixels, the pixel size can be verified.The Teflon pin is used for identification and orientation only. The ability to change the Teflon pin position enables organizations with more than one Catphan® phantom to identify their phantoms by images of the first section.Spherical acrylic contrast targetsThe section has five acrylic spheres located in a 30mm diameter circular pattern. These spheres are used to evaluate the scanner’s ability to image volume averaged spheres. The sphere diameters are 2, 4, 6, 8, and 10mm.Sensitometry (CT number linearity)Four or seven high contrast sensitometric targets surround the wire slice thickness ramps. Three are made from the commercial plastics: Teflon, acrylic and low density polyethylene (LDPE). The fourth is air. These targets range from approximately+1000 H to -1000 H.The monitoring of sensitometry target values over time and can provide valuable information, indicating changes in scanner performance.Linear attenuation coefficient µ [units cm-1]KEV Teflon Delrin Acrylic Polystryrene Water LDPE PMP Air40 0.556 0.327 0.277 0.229 0.240 0.209 0.189 050 0.447 0.283 0.244 0.209 0.208 0.191 0.173 060 0.395 0.260 0.227 0.196 0.192 0.181 0.164 062 0.386 0.256 0.224 0.194 0.190 0.179 0.162 064 0.380 0.253 0.221 0.192 0.188 0.178 0.160 066 0.374 0.251 0.219 0.191 0.186 0.177 0.160 068 0.370 0.248 0.217 0.189 0.184 0.175 0.158 070 0.363 0.245 0.215 0.188 0.182 0.174 0.157 072 0.359 0.243 0.214 0.186 0.181 0.172 0.155 074 0.355 0.240 0.211 0.185 0.179 0.171 0.155 076 0.351 0.238 0.210 0.184 0.178 0.170 0.154 078 0.346 0.236 0.208 0.183 0.177 0.168 0.152 080 0.342 0.234 0.207 0.180 0.175 0.167 0.151 090 0.328 0.225 0.199 0.175 0.170 0.163 0.147 0100 0.315 0.218 0.194 0.170 0.165 0.158 0.143 0Nominal material formulation and specific gravityMaterial Formula Specific Gravity* Electron Density (1023e/g) CT # est. Air 75%N, 23.2%O, 1.3%A 0.00 3.007 -1000 PMP [C6H12(CH2)] 0.83 3.435 -200 LDPE [C2H4] 0.92 3.429 -100 Water [H2O] 1.00 3.343 0 Polystryrene [C8H8] 1.05 3.238 -35 Acrylic [C5H8O2] 1.18 3.248 120 Delrin™ Proprietary 1.41 3.209 340 Teflon [CF2] 2.16 2.889 990 Contrast Scale (CS) is formally defined asCS = µm (E) - µw (E)CT m (E) – CT w (E)where m is reference medium, and w is water, and E is the effective energy of the CT beam.Alternatively, CS = µ1 (E) - µ2 (E)CT1 (E) – CT2 (E)where 1,2 are two materials with low z effective, similar to water (eg. acrylic & air).*For sensitometry inserts The Phantom Laboratory purchases a multiple year supply of material from a single batch. Samples of the purchased material are then measured to determine the actual specific gravity.CTP591 Bead Geometry ModuleThe Bead Geometry Module contains 3 pairs of opposed ramps and 2 individual beads. Two of the ramp pairs have 0.28mm diameter beads, spaced 1mm on center in the z direction. The other ramp pair has 0.18mm diameter beads, spaced 0.25mm on centerin the z direction. The 2 individual beads are 0.28mm and 0.18mm in diameter. A 50µ diameter tungsten wire is located 6cm from the center of the module. The wire and beads create point spreads that can be used to calculate the MTF (see the CTP528 section of this manual).The bead ramps can be used to measure the slice width of single or multiple slices following several different methods.•count the beads and multiply by the z axis increment•plot the ssp of the beads (see CTP528 section for additional information)•compare the bead maximum net CT # in thick and thin slices. Thin slice thickness = (( thick slice max net CT#) ÷ (thin slice max net CT#)) *(thick slice width)•z axis length at the full width at half maximum of a bead in a sagital or coronal image •full width at half max for a best-fit curve of the max points of the bead net values in a slice image.Note: Net value = (CT# of the bead) - (CT# of the background)CTP528 High resolution module with 21 line pair per cm gauge and point sourceThis section has a 1 through 21 line pair per centimeter high resolution test gaugeand two impulse sources (beads) which are cast into a uniform material. The beads are positioned along the y axis 20mm above or below the phantom’s center and 2.5 and 10mm past the center of the gauge in the z direction. On older CTP528 modules the bead is aligned in the z axis with the gauge.Bead Point Source for point spread function and MTFUse the impulse source to estimate the point source response function of the CT system. Print out a digitized image of the area surrounding the impulse source. Use the numerical data to determine the two-dimensional array of the CT values arising from the impulse source.The FWHM of the point spread function is determined from the best-fit curve of the point spread function numerical data.The average of several different arrays of impulse response functions is calculated to obtain the average point spread function of the system. These numerical values are used in conjunction with the Fourier Transform Program to provide an estimate of the two-dimensional spatial frequency response characteristics of the CT system (MTF). Illustration is on the next page.The tungsten carbide bead has a diameter of 0.011” or 0.28mm. Because the bead is subpixel sized it is not usually necessary to compensate for its size. However, some MTF programs are designed to compensate for it.PSFCTnumbersLine spread functionRelative position, x axisThe above illustration shows how by summing the columns (y axis) of numbers in the point spread function (PSF) the line spread function (LSF) for the x axis is obtained.0.00.51.00.80.60.40.30.20.10.90.73.0 6.09.012.00.0MTFSpatial Frequency (1/cm)The MTF curve results from the Fourier transform of the LSF data. Generallyit is easiest to use automated software for this operation. Some CT scanners are supplied with software which can calculate the MTF from the Catphan® bead images. Independent software is listed in the Current automated programs available section of the manual.Use of automated scanner MTF programsMany manufacturers include automated MTF software in the standard scanner software packages. Because the bead is cast into an epoxy background which has a different density than water, the software must accept an input for the background. The point size of .28mm must also be selected. While a sphere does produce a different density profile than a cross section of a wire or cylinder, the actual difference is not usually significant in current CT scanners.Bead point source for slice sensitivity profileThe bead in this module can be used to calculate the slice sensitivity profile (SSP).reconstruction. The length of the object at the Full Width at Half Maximum signal indicates the SSP. This measurement can be easily obtained on some systems, by making a sagittal or coronal reconstruction through the bead. The bead image in these reconstructions will appear as a small line. By setting the FWHM (use the same technique described in the Scan slice geometry section) measuring the z axis length of the bead image to obtain the SSP.If the scanner does not have the ability to measure z axis lengths in the sagittal or coronal planes, a SSP can be made by incrementing or spiraling the slice through the bead and reconstructing images in positive and negative table directions from the bead (using the smallest available increments) and plotting the peak CT number of the bead image in each slice. The FWHM measurement can then be made from the plotted CTvalues of the bead as a function of z axis table position.21 Line pair per centimeter high resolution gauge The 21 line pair/cm gauge has resolution tests for visual evaluation of high resolution ranging from 1 through 21 line pair/cm. The gauge accuracy is ± 0.5 line pair at the 21 line pair test and even better at lower line pair tests.The gauge is cut from 2mm thick aluminum sheets and cast into epoxy. Depending on the choice of slice thickness, the contrast levels will vary due to volume averaging. Line Pair/cm Gap SizeLine Pair/cm Gap Size 10.500 cm110.045 cm20.250 cm120.042 cm 30.167 cm130.038 cm40.125 cm140.036 cm 50.100 cm150.033 cm 60.083 cm160.031 cm 70.071 cm170.029 cm 80.063 cm180.028 cm 90.056 cm190.026 cm 100.050 cm200.025 cm 210.024 cmCTP515 low contrast module with supra-slice and subslice contrast targetsThe low contrast targets have the following diameters and contrasts:Supra-slice target diameters Subslice target diameters2.0mm3.0mm3.0mm 5.0mm4.0mm 7.0mm5.0mm 9.0mm6.0mm7.0mm8.0mm9.0mm15.0mmNominal target contrast levels.3%.5%1.0%Since the target contrasts are nominal, the actual target contrasts need to be determined before testing specific contrast performance specifications. The actual contrast levels are measured by making region of interest measurements over the larger target, and in the local background area. To determine actual contrast levels, average the measurements made from several scans. It is important to measure the background area adjacent to the measured target because “cupping” and “capping” effects cause variation of CT numbers from one scan region to another. Position the region of interest to avoid the target edges. The region of interest should be at least 4 x 4 pixels in diameter. Because low contrast measurements are “noisy” it is advisable to calculate the average of the multiple measurements made from several scans. Carefully monitor the mAs setting becausethe photon flux will improve with increased x-ray exposure. Use the size of the targets visualized under various noise levels to estimate information on contrast detail curves.All of the targets in each contrast group are cast from a single mix to assure that the contrast levels will be the same for all targets.The equation below can be used to convert the measured contrasts and diameters to other specified contrasts and diameters.(Measured Contrast) * (smallest diameter discernible) ≅ Constantexample: 5mm diameter @ 0.3% ≅ 3mm diameter @ 0.5%Along with the supra-slice (targets with z axis dimension longer than most maximum slice width) the CTP515 low contrast module includes subslice targets (targets withz axis length smaller than some of the usual slice width). The subslice targets are arranged in the inner circle of tests in the module.Subslice Supra-sliceThe subslice targets are cast from the same mix as the 1.0% supra-slice targets. Because they are from the same mix in the evaluation of the actual subslice target contrast the supra-slice targets can be used to establish contrast values. The subslice targets have z axis lengths of 3, 5, and 7mm and diameters of 3, 5, 7, and 9mm.The evaluation of subslice target readability is helpful in understanding the scanner’s different spiral imaging settings and how the settings will affect the ability to visualize small objects with low contrasts from their background.。
06-附录A OptiX Metro 500 技术规范

OptiX Metro 500 紧凑型STM-1多业务传输平台 技术手册目录目录附录A OptiX Metro 500 技术规范.........................................................................................A-1A.1 OptiX Metro 500设备特性.................................................................................................A-1A.1.1 接口类型.................................................................................................................A-1A.1.2 电接口....................................................................................................................A-2A.1.3 光接口....................................................................................................................A-2A.1.4 辅助接口.................................................................................................................A-2A.1.5 应用类型.................................................................................................................A-2A.1.6 电源和功耗.............................................................................................................A-2A.1.7 机械结构.................................................................................................................A-3A.1.8 电磁兼容性.............................................................................................................A-3A.1.9 环境条件.................................................................................................................A-4A.2 OptiX Metro 500主要指标.................................................................................................A-5A.2.1 光接口性能规范......................................................................................................A-5A.2.2 电接口规范.............................................................................................................A-8A.2.3 时钟定时和同步指标...............................................................................................A-9A.2.4 抖动性能指标........................................................................................................A-10A.3 电磁兼容(EMC)测试指标............................................................................................A-13附录A OptiX Metro 500 技术规范A.1 OptiX Metro 500设备特性本节列出了OptiX Metro 500在接口、电源、结构等方面的特性,帮助用户了解OptiX Metro 500。
艾 significance 198552 商品说明书

Eaton 198552Eaton Moeller® series Rapid Link - Speed controller, 2.4 A, 0.75 kW, Sensor input 4, 230/277 V AC, AS-Interface®, S-7.4 for 31 modules, HAN Q5, with manual override switch, with braking resistanceEaton Moeller® series Rapid Link Speed controller198552RASP5-2402A31-512R100S14015081964277157 mm 270 mm 220 mm 3.59 kgUL approval CEUL 61800-5-1 IEC/EN 61800-5-1 RoHSProduct NameCatalog NumberModel CodeEANProduct Length/Depth Product Height Product Width Product Weight Certifications Catalog Notes 3 fixed speeds and 1 potentiometer speedcan be switched over from U/f to (vector) speedParameterization: drivesConnect mobile (App)Diagnostics and reset on device and via AS-Interface Parameterization: FieldbusParameterization: drivesConnectParameterization: KeypadBreaking resistanceKey switch position AUTOKey switch position HANDTwo sensor inputs through M12 sockets (max. 150 mA) for quick stop and interlocked manual operationBraking resistanceInternal DC linkSelector switch (Positions: REV - OFF - FWD)IGBT inverterKey switch position OFF/RESETControl unitPC connectionManual override switchPTC thermistor monitoringThermo-click with safe isolation4-quadrant operation possible3 fixed speedsFor actuation of motors with mechanical brake1 potentiometer speedBrake chopper with braking resistance for dynamic brakingIP65NEMA 121st and 2nd environments (according to EN 61800-3) IIISpeed controllerVertical15 g, Mechanical, According to IEC/EN 60068-2-27, 11 ms, Half-sinusoidal shock 11 ms, 1000 shocks per shaftResistance: According to IEC/EN 60068-2-6Resistance: 57 Hz, Amplitude transition frequency onaccelerationResistance: 10 - 150 Hz, Oscillation frequencyFeaturesFitted with:FunctionsDegree of protection Electromagnetic compatibility Overvoltage category Product categoryMounting positionShock resistanceVibrationcontrolConnection ofsupply voltagevia adaptercable on roundor flexiblebusbar junctionDiagnostics andreset on deviceand via AS-Interfaceintegrated PTCthermistormonitoring andThermoclick withsafe isolationoptional: 4sensor inputswith M12-Yadapter forswitchover tocreep speedoptional: Fasterstop if external24 V failsTwo sensorinputs throughM12 sockets(max. 150 mA)for quick stopand interlockedmanualoperationwith AUTO -OFF/RESET -HAND keyswitcheswith selectorswitch REV -OFF - FWDASIAS-Interface profile cable: S-7.4 for 31 modulesC2, C3: depending on the motor cable length, the connected load, and ambient conditions. External radio interference suppression filters (optional) may be necessary.C1: for conducted emissions only2000 VAC voltageCenter-point earthed star network (TN-S network)Phase-earthed AC supply systems are not permitted.Resistance: 6 Hz, Amplitude 0.15 mmMax. 2000 mAbove 1000 m with 1 % performance reduction per 100 m -10 °C40 °C-40 °C70 °C< 95 %, no condensationIn accordance with IEC/EN 501780.2 - 2.4 A, motor, main circuit Adjustable, motor, main circuit< 10 ms, Off-delay< 10 ms, On-delay97 % (η)2.5 A3.5 mA120 %Maximum of one time every 60 seconds380 V 1 HP≤ 0.6 A (max. 6 A for 120 ms), Actuator for external motor brake≤ 30 % (I/Ie)Adjustable to 100 % (I/Ie), DC - Main circuit230/277 V AC -15 % / +10 %, Actuator for external motor brake 765 VDCProtocolRadio interference classRated impulse withstand voltage (Uimp) System configuration type AltitudeAmbient operating temperature - min Ambient operating temperature - max Ambient storage temperature - min Ambient storage temperature - max Climatic proofingCurrent limitationDelay timeEfficiencyInput current ILN at 150% overload Leakage current at ground IPE - max Mains current distortionMains switch-on frequencyMains voltage - min Assigned motor power at 460/480 V, 60 Hz, 3-phase Braking currentBraking torqueBraking voltageSwitch-on threshold for the braking transistor480 V380 - 480 V (-10 %/+10 %, at 50/60 Hz)Sensorless vector control (SLV)PM and LSPM motorsU/f controlSynchronous reluctance motorsBLDC motors0 Hz500 HzFor 60 s every 600 sAt 40 °C3.6 A45 Hz66 Hz2.4 A at 150% overload (at an operating frequency of 8 kHz and an ambient air temperature of +40 °C)0.75 kW400 V AC, 3-phase480 V AC, 3-phase0.1 Hz (Frequency resolution, setpoint value)200 %, IH, max. starting current (High Overload), For 2 seconds every 20 seconds, Power section50/60 Hz 10 kAType 1 coordination via the power bus' feeder unit, Main circuit230/277 V AC (external brake 50/60 Hz)24 V DC (-15 %/+20 %, external via AS-Interface® plug)AS-InterfacePlug type: HAN Q5Specification: S-7.4 (AS-Interface®)Number of slave addresses: 31 (AS-Interface®)Max. total power consumption from AS-Interface® power supply unit (30 V): 190 mAC3 ≤ 25 m, maximum motor cable lengthC1 ≤ 1 m, maximum motor cable lengthC2 ≤ 5 m, maximum motor cable lengthMeets the product standard's requirements.Meets the product standard's requirements.Meets the product standard's requirements.Mains voltage - maxMains voltage toleranceOperating modeOutput frequency - minOutput frequency - maxOverload currentOverload current IL at 150% overloadRated frequency - minRated frequency - maxRated operational current (Ie)Rated operational power at 380/400 V, 50 Hz, 3-phase Rated operational voltageResolutionStarting current - maxSupply frequencySwitching frequency Rated conditional short-circuit current (Iq)Short-circuit protection (external output circuits)Rated control voltage (Uc)Communication interfaceConnectionInterfacesCable length10.2.2 Corrosion resistance10.2.3.1 Verification of thermal stability of enclosures10.2.3.2 Verification of resistance of insulating materials to normal heat10.2.3.3 Resist. of insul. mat. to abnormal heat/fire by internal elect. effects8 kHz, 4 - 32 kHz adjustable, fPWM, Power section, Main circuitAC voltageCenter-point earthed star network (TN-S network)Phase-earthed AC supply systems are not permitted.Meets the product standard's requirements.Meets the product standard's requirements.Does not apply, since the entire switchgear needs to be evaluated.Does not apply, since the entire switchgear needs to be evaluated.Meets the product standard's requirements.Does not apply, since the entire switchgear needs to be evaluated.Meets the product standard's requirements.Does not apply, since the entire switchgear needs to be evaluated.Does not apply, since the entire switchgear needs to be evaluated.Is the panel builder's responsibility.Is the panel builder's responsibility.Is the panel builder's responsibility.Is the panel builder's responsibility.Is the panel builder's responsibility.The panel builder is responsible for the temperature rise calculation. Eaton will provide heat dissipation data for the devices.Is the panel builder's responsibility. The specifications for the switchgear must be observed.System configuration type10.2.4 Resistance to ultra-violet (UV) radiation10.2.5 Lifting10.2.6 Mechanical impact10.2.7 Inscriptions10.3 Degree of protection of assemblies10.4 Clearances and creepage distances10.5 Protection against electric shock10.6 Incorporation of switching devices and components10.7 Internal electrical circuits and connections10.8 Connections for external conductors10.9.2 Power-frequency electric strength10.9.3 Impulse withstand voltage10.9.4 Testing of enclosures made of insulating material10.10 Temperature rise10.11 Short-circuit ratingIs the panel builder's responsibility. The specifications for the switchgear must be observed.The device meets the requirements, provided the information in the instruction leaflet (IL) is observed.ETN.RASP5-2402A31-512R100S1.edzramo5_v20.dwgrasp5_v20.stpeaton-bus-adapter-rapidlink-speed-controller-dimensions-004.eps eaton-bus-adapter-rapidlink-speed-controller-dimensions-003.eps eaton-bus-adapter-rapidlink-speed-controller-dimensions-002.eps eaton-bus-adapter-rapidlink-speed-controller-dimensions-005.epsRapid Link 5 - brochureDA-SW-drivesConnect - InstallationshilfeDA-SW-USB Driver PC Cable DX-CBL-PC-1M5DA-SW-Driver DX-CBL-PC-3M0DA-SW-USB Driver DX-COM-STICK3-KITDA-SW-drivesConnect - installation helpDA-SW-drivesConnectMaterial handling applications - airports, warehouses and intra-logisticsIL034085ZUGeneration change from RA-SP to RASP 4.0Generation change RAMO4 to RAMO5Generation change from RA-MO to RAMO 4.0Configuration to Rockwell PLC for Rapid LinkGeneration Change RA-SP to RASP5Generation Change RASP4 to RASP5DA-DC-00004184.pdfDA-DC-00004508.pdfDA-DC-00004514.pdfDA-DC-00003964.pdf10.12 Electromagnetic compatibility10.13 Mechanical functioneCAD modelmCAD model,Eaton Corporation plc Eaton House30 Pembroke Road Dublin 4, Ireland © 2023 Eaton. All Rights Reserved. Eaton is a registered trademark.All other trademarks areproperty of their respectiveowners./socialmedia。
AT500变频器说明书V2.0

AT500变频器说明书V2:0AT500变频器说明书V2:01:引言1.1 目的本文档旨在提供AT500变频器的使用说明和操作指南,以帮助用户正确地安装、调试和维护该变频器。
1.2 范围本文档适用于AT500系列变频器的所有型号和规格。
它包含了变频器的基本介绍、技术规格、操作指南、故障排除等内容。
2:变频器概述2.1 产品介绍本章介绍AT500变频器的主要特点和应用领域。
2.2 技术规格本章详细列出AT500变频器的技术规格,包括输入电压、输出功率、额定电流等参数。
3:安装与接线3.1 安装前准备本章介绍AT500变频器安装前需要做的准备工作,包括工具和材料的准备、安全事项等。
3.2 变频器安装本章详细讲解AT500变频器的安装步骤,包括机械安装、电气连线等。
4:参数设置与调试4.1 参数设置概述本章介绍AT500变频器的参数设置功能和操作界面。
4.2 基本参数设置本章详细说明AT500变频器的基本参数设置方法,包括电机参数、频率范围、过载保护等。
4.3 高级参数设置本章讲解AT500变频器的高级参数设置,如速度控制、运行模式、编码器设置等。
5:运行与控制5.1 开机与停机本章介绍AT500变频器的开机和停机方法。
5.2 运行模式切换本章讲解AT500变频器的运行模式切换,如速度控制、定位控制等。
6:故障排除6.1 常见故障与处理方法本章了AT500变频器常见故障及其处理方法。
6.2 故障代码对照表本章提供了AT500变频器故障代码的解释和对照表。
7:维护与保养7.1 维护周期本章介绍AT500变频器的维护周期和保养注意事项。
7.2 保养方法本章详细说明AT500变频器的保养方法和步骤,包括清洁、润滑等。
附件:本文档涉及附件,请参考附件部分获取更多相关信息。
法律名词及注释:1:法律名词1:注释说明。
2:法律名词2:注释说明。
林肯电子 Vantage 500 商品说明书
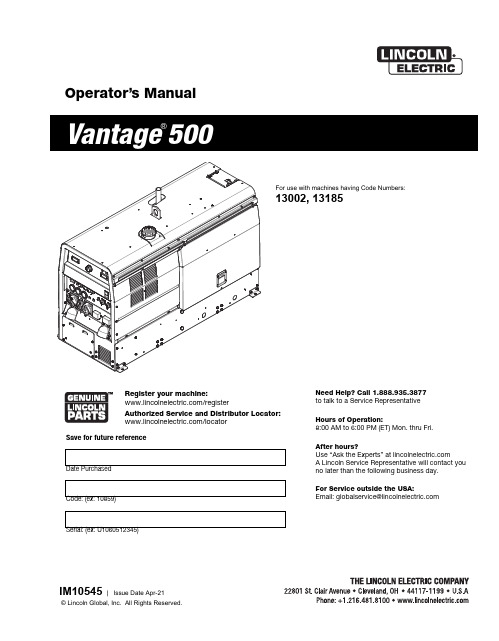
Operator’s Manual500Register your machine:/registerAuthorized Service and Distributor Locator: /locatorFor use with machines having Code Numbers:13002, 13185Need Help? Call 1.888.935.3877 to talk to a Service Representative Hours of Operation:8:00 AM to 6:00 PM (ET) Mon. thru Fri.After hours?Use “Ask the Experts” at A Lincoln Service Representative will contact you no later than the following business day.For Service outside the USA:Email:*********************************Save for future referenceDate PurchasedCode: (ex: 10859)Serial: (ex: U1060512345)SECTION A:WARNINGSC ALIFORNIA PROPOSITION 65 WARNINGSWARNING: This product, when used for welding or cutting, produces fumes or gases which contain chemicals known to the State of California to cause birth defects and, in some cases, cancer. (California Health & Safety Code § 25249.5 et seq.)ARC WELDING CAN BE HAZARDOUS. PROTECTYOURSELF AND OTHERS FROM POSSIBLE SERIOUS INJURY OR DEATH. KEEP CHILDREN AWAY.PACEMAKER WEARERS SHOULD CONSULT WITH THEIR DOCTOR BEFORE OPERATING.Read and understand the following safety highlights. For additional safety information, it is strongly recommended that you purchase a copy of “Safety in Welding & Cutting - ANSI Standard Z49.1” from the American Welding Society, P.O. Box 351040, Miami, Florida 33135 or CSA Standard W117.2-1974. A Free copy of “Arc Welding Safety” booklet E205 is available from the Lincoln Electric Company, 22801 St. Clair Avenue, Cleveland, Ohio 44117-1199.BE SURE THAT ALL INSTALLATION, OPERATION,MAINTENANCE AND REPAIR PROCEDURES ARE PERFORMED ONLY BY QUALIFIED INDIVIDUALS.FOR ENGINE POWERED EQUIPMENT.1.a.Turn the engine off before troubleshootingand maintenance work unless themaintenance work requires it to be running.1.b.Operate engines in open, well-ventilated areas or vent the engineexhaust fumes outdoors. 1.c.Do not add the fuel near an open flame weldingarc or when the engine is running. Stop the with hot engine parts and igniting. Do not spill fuel when filling tank. If fuel is spilled, wipe it up and do not start engine until fumes have been eliminated.1.d. Keep all equipment safety guards, coversand devices in position and in good repair.Keep hands, hair, clothing and tools away from V-belts, gears, fans and all other moving parts when starting, operating or repairing equipment.1.e.In some cases it may be necessary to remove safety guards toperform required maintenance. Remove guards only when necessary and replace them when the maintenance requiring their removal is complete. Always use the greatest care when working near moving parts. 1.f. Do not put your hands near the engine fan. Do not attempt tooverride the governor or idler by pushing on the throttle control rods while the engine is running. 1.g.To prevent accidentally starting gasoline engines while turningthe engine or welding generator during maintenance work,disconnect the spark plug wires, distributor cap or magneto wire as appropriate. 1.h.To avoid scalding, do not remove the radiatorpressure cap when the engine is hot.ELECTRIC ANDMAGNETIC FIELDS MAY BE DANGEROUS2.a.Electric current flowing through any conductorcauses localized Electric and Magnetic Fields (EMF).Welding current creates EMF fields around welding cables and welding machines 2.b.EMF fields may interfere with some pacemakers, andwelders having a pacemaker should consult their physician before welding. 2.c.Exposure to EMF fields in welding may have other health effectswhich are now not known. 2.d.All welders should use the following procedures in order tominimize exposure to EMF fields from the welding circuit:2.d.1.Route the electrode and work cables together - Securethem with tape when possible.2.d.2.Never coil the electrode lead around your body.2.d.3.Do not place your body between the electrode and workcables. If the electrode cable is on your right side, the work cable should also be on your right side.2.d.4.Connect the work cable to the workpiece as close as pos-sible to the area being welded.2.d.5.Do not work next to welding power source.SAFETYPage Installation.......................................................................................................................Section A Technical Specifications.......................................................................................................A-1 Machine Specification...................................................................................................A-2 Safety Precautions........................................................................................................A-3 VRD (Voltage Reduction Device)..................................................................................A-3 Location and Ventilation................................................................................................A-3 Stacking........................................................................................................................A-3 Angle of Operation........................................................................................................A-3 Lifting.............................................................................................................................A-3 High Altitude Operation.................................................................................................A-4 High Temperature Operation........................................................................................A-4 Cold Weather Operation......................................................................................................A-4 Towing..................................................................................................................................A-4 Vehicle Mounting..................................................................................................................A-4 Pre-Operation Engine Service..............................................................................................A-4 Oil..................................................................................................................................A-5 Fuel...............................................................................................................................A-5 Engine Coolant..............................................................................................................A-5 Battery Connections......................................................................................................A-5 Muffler Outlet Pipe........................................................................................................A-5 Spark Arrester...............................................................................................................A-5 Remote Control.............................................................................................................A-5 Electrical Connections..........................................................................................................A-6 Machine Grounding..............................................................................................................A-6 Welding Terminals................................................................................................................A-6 Welding Output Cables........................................................................................................A-6 Cable Installation..................................................................................................................A-6 Auxiliary Power Receptacles and Plugs...............................................................................A-7 Standby Power Connections................................................................................................A-7 Connection of Lincoln Electric Wire Feeders.................................................................A-7,A-8 ________________________________________________________________________________ Operation.........................................................................................................................Section B Safety Precautions ..............................................................................................................B-1 General Description..............................................................................................................B-1 For Auxiliary Power..............................................................................................................B-1 Engine Operation..................................................................................................................B-1 Add Fuel...............................................................................................................................B-1 Break in Period.....................................................................................................................B-1 Welder Controls.............................................................................................................B-2,B-3 Engine Controls....................................................................................................................B-4 Fuel Consumption.........................................................................................................B-4 Starting and Stopping the Engine...........................................................................B-4,B-5 Welding Operation................................................................................................................B-5 Duty Cycle and Electrode Information...........................................................................B-5 Constant Current (Stick) Welding.........................................................................................B-5 Downhill Pipe (Stick) Welding.......................................................................................B-5 Tig Welding...................................................................................................................B-6 Typical Current Ranges for Tungsten Electrodes.........................................................B-6 Wire Welding-CV...........................................................................................................B-7 Arc Gouging..................................................................................................................B-7 Auxiliary Power.....................................................................................................................B-7 Simultaneous Welding and Power Loads.....................................................................B-7 Extension Cord Recommendations...............................................................................B-7 ________________________________________________________________________________ Accessories.....................................................................................................Section C Field Installed Options / Accessories ...............................................................................C-1 ________________________________________________________________________________(5) Center-Tapped to ground.NOTE: This data is for reference only. Fuel consumption is approximate and can be influenced by many factors, including engine maintenance, environmental conditions and fuel quality.VANTAGE® 500 Extension Cord Length Recommendations (Use the shortest length extension cord possible sized per the following table.)Current (Amps)1520152044Voltage Volts120120240240240Load(Watts)180024003600480095003060(9)(18)40307560(12)(9)(23)(18)755015010050(23)(15)(46)(30)(15)1258822517590(38)(27)(69)(53)(27)175138350275150(53)(42)(107)(84)(46)300225600450225(91)(69)(183)(137)(69)Maximum Allowable Cord Length in ft. (m) for Conductor SizeConductor size is based on maximum 2.0% voltage drop.14 AWG12 AWG10 AWG8 AWG 6 AWG 4 AWGTABLE B.6SAFETY PRECAUTIONSRead the Safety Precautions in the front of this manual and in the Engine Owner’s Manual before working on this machine.Keep all equipment safety guards, covers, and devices in position and in good repair. Keep hands, hair, clothing, and tools away from the gears, fans, and all other moving parts when starting, operating, or repairing the equipment.------------------------------------------------------------------------Routine MaintenanceAt the end of each day’s use, refill the fuel tank to minimize moisture condensation in the tank. Running out of fuel tends to draw dirt into the fuel system.Also, check the crankcase oil level and add oil if indicated.outlet tube to create the critical seal, there will be some initial resistance, similar to breaking the seal on a jar. Gently move the end of the filter back and forth to break the seal then rotate while pulling straight out. Avoid knocking the filter Rotate the filter while pullingstraight out.If your air cleaner has a safety filter, replace it every third primary filter change. Remove the safety filter as you would the primary filter. Make sure you cover the air cleaner outlet tube to avoid any If your air cleaner is equipped with a Vacuator Valve Visually check and physically squeeze to make sure the valve is flexible and not inverted, damaged or plugged.Inspect the new filter carefully, paying attention to If the service cover hits the filter before it is fully in place, remove the cover and push the filter (by hand) further into the air cleaner and try again. The cover should go on with no extra force.slightly, adjust itself and distribute the sealing pressure evenly. To complete a tight seal, apply pressure by hand at the outer rim of the filter, not the flexible center. (Avoid pushing on the center of the urethane end cap.) No cover pressure is required to hold the seal.NEVER use the service cover to push the filter into place! Using the cover to push the filter in could cause damage to the housing, cover Visually inspect the old filter for any signs of leaks. A streak of dust on the clean side Inspect the OldFilter for Leak CluesInspect the New Filter for DamageOuter edge of the outlet tubeInner edge of the outlet tubeThis Troubleshooting Guide is provided to help you locate and repair possible machine malfunctions.Simply follow the three-step procedure listed below.Step 1.LOCATE PROBLEM (SYMPTOM).Look under the column labeled “PROBLEM (SYMP-TOMS)”. This column describes possible symptoms that the machine may exhibit. Find the listing that best describes the symptom that the machine is exhibiting.Step 2.POSSIBLE CAUSE.The second column labeled “POSSIBLE CAUSE” lists the obvious external possibilities that may contributeto the machine symptom.Step 3.RECOMMENDED COURSE OF ACTIONThis column provides a course of action for the Possible Cause, generally it states to contact your local Lincoln Authorized Field Service Facility.If you do not understand or are unable to perform the Recommended Course of Action safely, contact your local Lincoln Authorized Field Service Facility.HOW TO USE TROUBLESHOOTING GUIDEService and Repair should only be performed by Lincoln Electric Factory Trained Personnel.Unauthorized repairs performed on this equipment may result in danger to the technician and machine operator and will invalidate your factory warranty. For your safety and to avoid Electrical Shock, please observe all safety notes and precautions detailed throughout this manual.__________________________________________________________________________VANTAGE®500VANTAGE®500ATENÇÃOJapaneseChineseKoreanArabicREAD AND UNDERSTAND THE MANUFACTURER’S INSTRUCTION FOR THIS EQUIPMENT AND THE CONSUMABLES TO BE USED AND FOLLOW YOUR EMPLOYER’S SAFETY PRACTICES.SE RECOMIENDA LEER Y ENTENDER LAS INSTRUCCIONES DEL FABRICANTE PARA EL USO DE ESTE EQUIPO Y LOS CONSUMIBLES QUE VA A UTILIZAR, SIGA LAS MEDIDAS DE SEGURIDAD DE SU SUPERVISOR.LISEZ ET COMPRENEZ LES INSTRUCTIONS DU FABRICANT EN CE QUI REGARDE CET EQUIPMENT ET LES PRODUITS A ETRE EMPLOYES ET SUIVEZ LES PROCEDURES DE SECURITE DE VOTRE EMPLOYEUR.LESEN SIE UND BEFOLGEN SIE DIE BETRIEBSANLEITUNG DER ANLAGE UND DEN ELEKTRODENEINSATZ DES HER-STELLERS. DIE UNFALLVERHÜTUNGSVORSCHRIFTEN DES ARBEITGEBERS SIND EBENFALLS ZU BEACHTEN.ATENÇÃOJapaneseChineseKoreanArabicLEIA E COMPREENDA AS INSTRUÇÕES DO FABRICANTE PARA ESTE EQUIPAMENTO E AS PARTES DE USO, E SIGA AS PRÁTICAS DE SEGURANÇA DO EMPREGADOR.CUSTOMER ASSISTANCE POLICYThe business of The Lincoln Electric Company is manufacturing and selling high quality welding equipment, consumables, and cutting equipment. Our challenge is to meet the needs of our customers and to exceed their expectations. On occasion, purchasers may ask Lincoln Electric for advice or information about their use of our products. We respond to our customers based on the best information in our possession at that time. Lincoln Electric is not in a position to warrant or guarantee such advice, and assumes no liability, with respect to such information or advice. We expressly disclaim any warranty of any kind, including any warranty of fitness for any customer’s particular purpose, with respect to such information or advice. As a matter of practical consideration, we also cannot assume any responsibility for updating or correcting any such information or advice once it has been given, nor does the provision of information or advice create, expand or alter any warranty with respect to the sale of our products.Lincoln Electric is a responsive manufacturer, but the selection and use of specific products sold by Lincoln Electric is solely within the control of, and remains the sole responsibility of the customer. Many variables beyond the control of Lincoln Electric affect the results obtained in applying these types of fabrication methods and service requirements.Subject to Change – This information is accurate to the best of our knowledge at the time of printing. Please refer to for any updated information.。
Action 500系列商品用户手册说明书
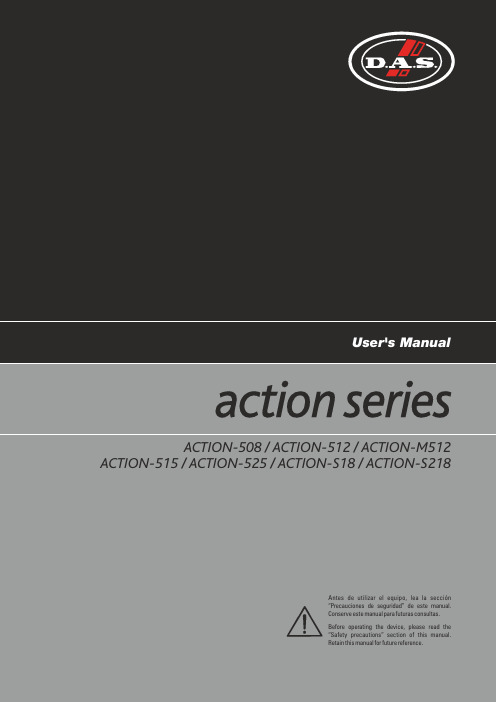
User's Manual ACTION-508 / ACTION-512 / ACTION-M512 ACTION-515 / ACTION-525 / ACTION-S18 / ACTION-S218Antes de utilizar el equipo, lea la sección“Precauciones de seguridad” de este manual.Conserve este manual para futuras consultas.Before operating the device, please read the“Safety precautions” section of this manual.Retain this manual for future reference.INTRODUCTION RIGGING SYSTEM 6 - 78 - 1334514 - 1617 - 1818LINE DRAWINGS SPECIFICATIONSCONFIGURATIONSSAFETY PRECAUTIONS WARRANTYDECLARATION OF CONFORMITY Manual del Usuario / action 500 series / User’s Manual2x ACTION-5082x ACTION-508 + 1x ACTION-S182x ACTION-512 + 2x ACTION-S182x ACTION-515) + 2x ACTION-S182x ACTION-525 + 2x ACTION-S2182x ACTION-M512action-500 passive series Precauciones de SeguridadSafety PrecautionsCajas acústicas pasivas / Passive loudspeaker enclosuresManual del Usuario / action 500 series / User’s Manual3Todos nuestros productos están garantizados por un periodo de 24 meses desde la fecha de compra.Las garantías sólo serán válidas si son por un defecto de fabricación y en ningún caso por un uso incorrecto del producto.Las reparaciones en garantía pueden ser realizadas, exclusivamente, por el fabricante o el servicio de asistencia técnica autorizado.Otros cargos como portes y seguros, son a cargo del comprador en todos los casos.Para solicitar reparación en garantía es imprescindible que el producto no haya sido previamente manipulado e incluir una fotocopia de la factura de compra.All our products are warrantied against any manufacturing defect for a period of 2 years from date of purchase.The warranty excludes damage from incorrect use of the product.All warranty repairs must be exclusively undertaken by the factory or any of its authorised service centers.To claim a warranty repair, do not open or intend to repair the product.Return the damaged unit, at shippers risk and freight prepaid, to the nearest service center with a copy of the purchase invoice.4Manual del Usuario / action 500 series / User’s Manual5Y es conforme a las siguientes Normas Armonizadas Europeas:In accordance with Harmonized European Norms:lEN 60065:2014.- Audio, video and similar electronic apparatus. Safety requirements.lEN 50581:2012.- Technical documentation for the assessment of electrical and electronic products with respect to the restriction ofhazardous substances.DECLARACIÓN DE CONFORMIDAD DECLARATION OF CONFORMITYDAS Audio Group, S.L.C/ Islas Baleares, 24 - 46988 - Pol. Fuente del Jarro - Valencia. España (Spain).Declara que :Declares that :ACTION-508 / ACTION-512 / ACTION-M512ACTION-515 / ACTION-525 / ACTION-S18 / ACTION-S218Cumple con los objetivos esenciales de las Directivas:Abide by essential objectives relating Directives:l De Baja Tensión / Low Voltage 2014/35/UE l RoHS2011/65/UE lRAEE (WEEE)2012/19/UEManual del Usuario / action 500 series / User’s ManualACTION-512- Two-way full-range system- 12" bass loudspeaker, 12MI (2,5" VCD)- Compression driver , M-34 (1,4" VCD) with titanium diaphragm - Asymmetric enclosure design for stage monitor use - Built-in rigging points (eyebolt based)- Stand mountableThe ACTION-512 is a 2-way passive full-range loudspeaker that utilizes a 12” low frequency transducer and a 1” exit compression driver. The multi-angle cabinet is constructed of Birch plywood protected by an environmentally friendly black paint finish. Two bar handles and a steel grille are provided. A 35mm tripod socket with angle double (0º and -10º) allows for stand mounting.ACTION-508- 2-way, full-range system - 8″ bass loudspeaker, 8GV (1,5" VCD) - Compression driver , M-34 (1,4" VCD) with titanium diaphragm - Asymmetric enclosure design for stage monitor use - Built-in rigging points- Stand mountableThe ACTION-508 is a compact 2-way passive full-range loudspeaker that utilizes a 8” low frequency transducer and a full compression driver. The multi-angle cabinet is constructed of Birch plywood protected by an enviormentally friendly ISO-flex black paint finish. A rear located handle and a robust steel grille are provided. A 35 mm tripod socket allows for stand mounting.ACTION-M512- Dedicated stage monitor- 12" bass loudspeaker, 12MI (2,5" VCD)- Compression driver , M-34 (1,4" VCD) with titanium diaphragm - Low profile enclosure design for minimum visual impact - Black paint finish- Stand mountableThe ACTION-M512 is a dedicated stage monitor designed for use with external amplification. The enclosure is constructed from Birch plywood and is protected with a black paint finish. Two side located handles facilitate handling and a steel grille protects the components. A pole mount socket adds versatility to the ACTION-M512.6INTRODUCTIONFeaturesThe action 500 series inherits the exceptional sound quality and rugged build that have made DAS professional systems an internacional sound reinforcement standard. Designed from “real-world” experience, they offer users outstanding performance, absolute reliability, and unparalleled convenience. Whether it is in a high-profile venue or on the stage of a major event, the action series will provide the power and definition needed to make your performance a success.Manual del Usuario / action 500 series /User’s Manual7ACTION-525- 2-way, full-range system- 2 x 15" bass loudspeaker, 15MI (2,5" VCD)- Compression driver with titanium diaphragm, M-44 (1,75" VCD)- Two steel-reinforced handlesThe ACTION-525 is a 2-way passive full range loudspeaker utilizes two 15” bass loudspeakers for extra low frequency punch and higher SPL. High frequencies are handled by a 1” compression driver with titanium diaphragm. The trapezoidal cabinet is constructed using Birch plywood and protected with a hard-wearing black paint finish. Two bar handles and a steel grille sealed against corrosion using a polyamide powder coat finish are provided. Rigging points provide a safe and simple way to fly the ACTION-525 cabinets.ACTION-S18- Bass-reflex subwoofer system- 18" low frequency transducer, 18FW (3" VCD) - Precise and powerful bass reproduction- Top located pole mount socketThe ACTION-S18 bass system incorporates a 18” low frequency transducer with a 3 " voice coil mounted as a direct radiator into a bass-reflex cabinet. The loudspeaker is protected by a perforated steel grille, sealed against corrosion using a powder coat finish. The ACTION-S18 is designed for use in biamped systems. A top located pole-mount socket permits mounting full-range systems above the ACTION-S18 and two bar handles makes moving easy.ACTION-S218- High output bass-reflex subwoofer system - Twin 18" loudspeakers, 18FW (3" VCD) - Durable black paint finish- Side located bar handlesThis high power bass-reflex subwoofer system uses dual 18" bass loudspeakers equipped with 3" voice coils. The exceptional power handling capacity and efficiency provide high sound pressure levels of powerful bass. Two hand locations facilitate handling. The cabinet is designed to be stacked in the vertical position in order to reduce the units "on-stage" footprint.ACTION-515- Two-way, full-range system- 15" bass loudspeaker, 15MI (2,5" VCD)- Compression driver with titanium diaphragm, M-34 (1,4" VCD - Asymmetric enclosure design for stage monitor use - Built-in rigging points (eyebolt based)- Stand mountable with angle double (0º and -10º)This 2-way passive full-range loudspeaker utilizes a 15” low frequency transducer and a 1” exit compression driver with titanium diaphragm. The cabinet is constructed of Birch plywood and finished with an environmentally friendly black paint finish. Two bar handles are provided and a steel grille protects components. A 35mm tripod socket with angle double (0º and -10º) allows for stand mounting. Rigging points provide a safe and simple solution for suspending the ACTION-515.Manual del Usuario / action 500 series /User’s ManualSE:INPUCONFIGURATIONS8Manual del Usuario / action 500 series / User’s Manual9Manual del Usuario / action 500 series / User’s ManualA C T I O N -508A C T I O N -508000S E : I N P U10Manual del Usuario / action 500 series / User’s Manual0S E : I N P U11Manual del Usuario / action 500 series / User’s Manual0000S E : I N P U12Manual del Usuario / action 500 series / User’s Manual A C T I O N -S 218A C T I O N -S 2180000S E : I N P U13Manual del Usuario / action 500 series / User’s Manual A CTI ON-M 512A CTI O N-M5120SE:INPURIGGINGThis manual contains needed information forflying DAS Audio line array systems, description ofthe elements and safety precautions. To performany operations related to flying the system, readthe present document first, and act on thewarnings and advice given. The goal is to allow theuser to become familiar with the mechanicalelements required to fly the acoustic system, aswell as the safety measures to be taken duringset-up and teardown.Only experienced installers with adequateknowledge of the equipment and local safetyregulations should fly speaker boxes. It is theuser's responsibility to ensure that the systems tobe flown (including flying accessories) comply withstate and local regulations.The working load limits in this manual are theresults of tests by independent laboratories. It isthe user's responsibility to stay within safe limits. Itis the user's responsibility to follow and complywith safety factors, resistance values, periodicalsupervisions and warnings given in this manual.Product improvement by means of research anddevelopment is on going at D.A.S. Specificationsare subject to change without notice.It is common practice to apply 5:1 safetyfactors for enclosures and static elements. Forslings and elements exposed to material fatiguedue to friction and load variation the followingratios must be met; 5:1 for steel cable slings, 4:1for steel chain slings and 7:1 polyester slings.Thus, an element with a breaking load limit of1000 kg may be statically loaded with 200 kg (5:1safety factor) and dynamically loaded with 142 kg(7:1 safety factor).When flying a system, the working load mustbe lower than the resistance of each individualflying point in the enclosure, as well as each box.Hanging hardware should be regularly inspectedand suspect units replaced if in doubt. This isimportant to avoid injury and absolutely no risksshould be taken in this respect. It is highlyrecommended that you implement an inspectionand maintenance program on flying elements,including reports to be filled out by the personnelthat will carry out the inspections. Localregulations may exist that, in case of accident,may require you to present evidence of inspectionreports and corrective actions after defects werefound.WarningsAbsolutely no risks should be taken with regards to public safety. When flying enclosures from ceiling support structures, extreme care should be taken to assure the load bearing capabilities of the structures so that the installation is absolutely safe. Do not fly enclosures from unsafe structures. Consult a certified professional if needed. All flying accessories that are not supplied by DAS Audio are the user's responsibility. Use at your own risk.Introduction Flyable action 500 series models feature 6 internal steel angles, with 2 mounting threads each, so that 12 flying points are available (2 on each side, 3 on the top panel and 3 on the bottom panel and 2 on the rear panel). Eyebolt flying points are factory sealed with M10 screws, which are replaced with eyebolts on the flying points as required. Flying with eyebolts is very economical and safe, and is specially recommended for fixed installations where the boxes are permanently fixed. The illustration shows the internal metal hardware of an enclosure with eyebolt flying.14Manual del Usuario / action 500 series / User’s ManualThe Allen-head screws must be removed andreplaced by M10 eyebolts on one side of theenclosure. Each rigging point has 200 kg (440 lb)working load limit. Then choose the slings orchains of required load resistance and length,bearing in mind that the length difference betweenthe front and back slings or chains will determinethe vertical orientation. Alternatively, the backbottom eyebolt points can be used to providevertical orientation.The ANL-2 set is an optional set of threeeyebolts and three carabiners. (Dimensions are inmilimetres).Flying with eyeboltsEach ANL-2 eyebolt has a rated working loadof 200 kg. (440 lb). Each ANL-2 carabiner has aworking load of 330 kg (726 lb). If using otherhardware, make sure it is rated to handle therequired load.When using eyebolts it is important to bear inmind that the rated working load is only true for aload applied in the plane of the eye, and issignificantly reduced for other angles. The drawingillustrates the concept. The table shows thevariation of the working load as a function of theload angle. In the case of the ANL-2 eyebolt, thismeans that the 200 kg working load becomes 60kg at 45 degrees. Do not use eyebolt flying if theload angle is higher than 45 degrees.The following illustrations show different viewson eyebolt flying for a single box. The length of theback cables or chains determines the verticalangle of thebox.ANL-215Manual del Usuario / action 500 series /User’s ManualInstructions for AXU (only ACTION-508 and ACTION-512 enclosures)16IntroductionThe AXU-ACT8are designed for ACTION-508and ACTION-508A enclosures.The AXU-ACT12are designed for ACTION-512and ACTION-512A enclosures.Safety PrecautionsWall plugs provided are to be used in brick walls only.For other wall materials, source the suitable wall plugbefore use.DAS Audio is not responsible for use other than therecommended or whether it be the result of insufficientstrength of the support structure. Use only the screwsand wall plugs supplied on surfaces that will providesufficient support. Do not use on surfaces such as plaster,and gypsum. It is highly recommended and in most partsof the world mandatory, that a safety cable be used tosecure the enclosure to the structure.To ensure optimum safety, the installation should bechecked thoroughly at regular intervals replacing alldeteriorated elements.Loosen the screws before reorienting the speaker.Never force the rigging elements.Contact a licensed rigger if there is any doubt.Mounting instructionsYou can consult the AXU-ACT8mounting instructions for ACTION-508enclosures on the web: You can consult the AXU-ACT12mounting instructions for ACTION-512enclosures on the web:Manual del Usuario / action 500 series / User’s ManualTRD-6 / TRD-7 accessories-10º0ºThe models ACTION-512 and ACTION-515 dispose the 35mm tripod socket with angle double (0º and -10º) for stand mounting.LINE DRAWINGSALL DIMENSIONS IN MILLIMETERS17Manual del Usuario / action 500 series / User’s ManualU M _A C T 5_01_E NDAS Audio Group, S.L. C/. Islas Baleares, 24. 46988 Fuente del Jarro. Paterna. Valencia. España. Tel.: +34 96 134 0860。
Alcatel-Lucent VitalQIP 500Appliance快速启动指南说明书

Quick Start Guide 9YZ045530500RJZZA, Issue 1VitalQIPQIP TM500Appliance®Thank you for selecting Alcatel-Lucent VitalQIP®Appliances. This guide is intended to help you to set up the QIP TM500 appliance and quickly connect it to the network. Refer to the table below to ensure that all items are included in the box.Prerequisites1.If this is your first appliance, become familiar with the QIP Appliance Overview (see Note belowfor how to access). The guide provides an overview of the VitalQIP appliances and describes how to configure the three types of appliances: AMS (Appliance Management Software), ESM (Enterprise Server Module) and AMM (Appliance Management Module).Note: A full set of VitalQIP Appliance documentation is available on the Alcatel-Lucentdownload site (). You can download the documents by logging in to the portal using your registered User Name and Password. The appliance-relateddocuments are contained in the VitalQIP Appliance Manager area. If you have any questions, please contact Technical Support (listed at the end of this guide).2.You need to have an appliance on your network configured as an AMS. The steps below describehow to configure this appliance as an AMS.3.If you want to make this appliance an AMM, your AMS administrator needs to create a record forthis appliance in the AMS and provide the appliance setup information in print or electronicformat. Setup of an appliance in the AMS is described in “View appliance setup information” in Chapter 2 of the AMS User’s Guide.Figure 1. QIP 500 front viewItem QuantityQIP 500 Appliance1Quick Start Guide1Stand, Rubber Mounts, cable1Power cable1DB9-to-RJ45 Serial Connector1Figure 2. QIP 500 rear viewAppliance setup instructionsThe following steps describe how to configure this appliance. If your AMS administrator has provided you with Appliance configuration data (config.txt file) on a USB memory stick, you will be performing "Auto Config" and can bypass many of the following steps. Otherwise, you will be performing "Manual Config." The steps required for Auto Config are prefixed with [A] and the steps required for Manual Config are prefixed with [M]. The steps required by both Auto and Manual are prefixed with [A/M]. If you are configuring the appliance as an AMS, follow the Manual Config steps and then proceed to the "Configuring Appliance as an AMS" section.1.[A/M] Attach the appliance to an appropriate rack using the supplied rack mount hardware.2.[A/M] Connect a network cable to the Ethernet port labelled NIC 1 on the back of the appliance.3.[A/M] If you are setting up a DNS High Availability pair, connect a crossover cable between the pair using NIC 2on the back of the appliances. Both appliances in the pair need to be on the same subnet.4.[A] Connect the USB memory stick to a USB port.5.[M] Connect a laptop to the serial port (see Figure 2) or a monitor and a keyboard to the appropriate ports on theappliance. You may also use the virtual console of the Lights Out capability (see below for configuration). If you are connecting to a serial port, make sure the serial port is set to 9600n81 and disable any software flow control. These devices can be removed after the initial setup.6.[A/M] Connect the supplied power supply cables to the back of the appliance and to a power source (110v or 240v).The appliance automatically powers up after the power source is connected. If the power does not come on, push the power-on button.7.[A/M] You should see a flickering green light indicating network connectivity. If you do not see the light, contactyour network support team to check on network connectivity. If the cable has network connectivity and the connectivity indicator is still not lit on the back of the appliance, contact Technical Support.8.[A] After a successful Auto Config, the appliance will appear online in the AMS. Contact the AMS administrator andconfirm the configuration was successful. If you do not see the appliance appear online in the AMS, you can manually correct the data. To do this, repeat the Appliance setup instructions following the Manual Config steps.9.[M] Once the boot is complete, the appliance console menu opens:Welcome to VitalQIP ApplianceCopyright [year(s)] Alcatel-Lucent. All rights reserved.>10.[M] To configure the appliance, enter enable. The prompt changes to # to indicate that you are now in privilegedmode.11.[M] Contact your AMS administrator to obtain the configuration information. If you are setting up the appliance asan AMS, you need to define: Hostname, IPv4 address, IPv6 address (optional), Netmask, Gateway. Otherwise, your AMS administrator should have set up the appliance in the AMS and needs to provide you the followinginformation: Hostname, IPv4 address, IPv6 address (optional), Netmask, Gateway, AMS URI, and Secret Key. 12.[M] Once you have the above information, enter the following at the appliance console:# configconfig# hostname<Hostname>config# address<IPv4 address>config# v6address<IPv6 address (optional)>config# netmask<Netmask>config# gateway<Gateway address>config# ams<AMS URI (not needed for AMS appliance)>config# key<Secret Key (not needed for AMS appliance)>The first time you configure, you are presented with licence information. Read the license information carefully, and enter Yes to accept or No to refuse.13.[M] To set up a password to restrict access to the appliance, enter password. A password must be alphanumericand at least 6 characters.Note: The appliance console password can also be set up and maintained in the AMS. Refer to Chapter 2 in the AMS User’s Guide for more information. For information on other configuration options, refer to Part II of the AMS Install Guide.14.[M] Use the show command to make sure there are no data entry problems during the configuration in step 12.15.[M] To save the configuration, enter the following,config# saveconfig# back# rebootand confirm the reboot. Once the reboot is complete, the appliance console menu is displayed.Note: If you are configuring the appliance as an AMS, continue on to the next section.16.[M] Enter verify to check connectivity to the AMS server. If successful, you see a verify successful response. Ifthe verify command fails, type enable to enter privileged mode, followed by config. If there was an error, go to Step 12 and repeat the process.If verify fails again, check to see if basic network connectivity exists between the appliance and your network. For example, double-check the input fields, check the cable(s), and ping the address of the appliance from another machine. If there is successful connectivity but you are still unable to verify successfully, contact Technical Support.17.[M] If the verify command is successful, use the enable command to enter privileged mode again.18.[M] Enter authenticate to connect to AMS. If successful, you see an authentication successful response.If the authenticate command fails, use the config and show commands to check if there was a mistake in data entry in Step 12, especially the system key. If there was an error, go to Step 12 and repeat the config process. If authenticate fails again, reboot the appliance and go back to Step 12. If authentication fails once again, ask the AMS administrator to resend the “system key”. Go back and reenter the system key. If there is still an issue, contact Technical Support.19.[M] If authentication is successful, enter disable to exit privileged mode. The appliance is ready to be configuredby the AMS. Provide the AMS administrator with the status of the appliance.Configuring appliance as an AMSTo configure the QIP 500 appliance as an AMS, you must first manually configure the appliance as described above. To complete the AMS configuration, continue with the following steps:1.On the appliance console, enter enable followed by amsserver.2.Enter activate to begin installing the AMS packages. This will take several minutes and you will see the progressas the packages are installed and the AMS database is initialized.3.To import Enterprise and Remote packages into the AMS, enter importpackages. This will populate the AMSdatabase with the packages necessary to configure Enterprise (ESM) and remote (AMM) appliances. You can also download the most recent packages from the Alcatel-Lucent download site ().4.Once you have the packages imported into the AMS, you can safely remove the package files from the applianceusing the clean command. This will free up several GB of disk space.5.Enter back and disable to exit privileged mode.6.You should now be able to access the AMS web-based interface by entering https://<appliance-ip>:9985/ams in abrowser. Login with Username "amsadmin" and Password "amsadmin".Configuring Lights Out ManagementThe QIP 500 appliance is equipped with Lights Out management capability that allows you to remotely manage the appliance using a web-based interface. To configure Lights Out, do the following:1.Connect a network cable from a laptop to the NIC 1 Ethernet port on the back of the appliance (Lights Out uses ashared NIC). The laptop needs to be able to access the 192.168.1.0/24 subnet.2.Access the web-based interface by entering http://192.168.1.8 in a browser. Login with Username "ADMIN" andPassword "changeit".3.Click on the Server Health tab and verify that the server health is reported as healthy. If not, contact TechnicalSupport.4.Select Configuration/Network to set the network settings. Select Configuration/Users to set the ADMINpassword. Save the settings.5.To remotely launch the system console, select Remote Control/Console Redirection and click LaunchConsole.6.Disconnect the network cable from the laptop and connect the appliance directly into the network.Contacting technical supportIf you need assistance with the QIP 500, contact technical support via phone or web.Region Address Contact informationNorth America Alcatel-Lucent400 Lapp Road, Suite 101East Whiteland, PA 19355 USA Phone: 1-866-LUCENT8 (582-3688) Option 1, Option 2 E-mail: **************************Web: /supportEurope, Middle East, and Africa Alcatel-LucentVoyager PlaceShoppenhangers RoadMaidenheadBerkshire SL6 2PJ, UKPhone: 00 800 00 LUCENT or +353 1 692 4579E-mail: **************************Web: /supportCentral and South America Alcatel-Lucent Brazil S/AAvenida Marginal Direita Anchieta, 400 -Km 11,5CEP: 04182-901 - Jardim Santa Cruz -Sao Paulo - SP, BrazilPhone: 0800 89 19325 or +55 11 3205 7626E-mail: **************************For other local CALA numbers, consult the web site http://www.alcatel-/support or contact your local sales representative.Asia Pacific Alcatel-Lucent Australia280 Botany RoadAlexandria NSW 2015Australia Phone: 1800-458-236 (toll free from within Australia)(IDD) 800-5823-6888 (toll free from Asia Pacific - China, Hong Kong, Indonesia, South Korea, Malaysia, New Zealand, Philippines, Singapore, Taiwan, and Thailand)(613) 9614-8530 (toll call from any country)E-mail: **************************Web: /support© 2012 Alcatel-Lucent。
IMT埃柯特说明书_最新版本)

状态显示屏
ACT
天津埃柯特 A.C.T Control
开阀电源
关阀
向开启阀门方向运行。顺时针旋转操作旋钮,电动装
置向关阀方向运行。选择就地保持时,旋动操作旋钮
后松开,电动装置将向该方向持续运动,直至全行程。
选择就地点动时,旋动操作旋钮时,电动装置将向该
方向持续运动,若中途放开旋钮,电动装置将停止运 操作:功能按钮
步骤三:再次使用遥控器按下“停止”键。
2. “确认”操作
参数设定中,“确认”操作用于在菜 单选择页面确认所选选项,进入下一级 菜单;或者在参数设定页面“确认”当 前参数,回到上一级菜单的作用。
做法一:
ACT
就地保持 20%
100%
开阀 电源
关阀
ACT
参数查询 参数设定 语言选择钮转至“现
电动装置对选择旋钮有定位锁起保护功能,避免意外操作。建议使用标准挂锁。(见
本章第一张图)
6
第3章 电动装置显示界面说明
3.1 显示界面概览
接通电源后,电动装置液晶显示屏背光将点亮,同时电源指示灯将点亮。显示界面 包括一块128×64的图形点阵式液晶显示屏和三个LED灯组成。
其中,显示屏用于显示阀门的工作方式、状态、开度位置(用0~100%值表示)、故 障报警以及参数设定时参数的显示等。
关阀
作用;在数字设定方式时,起到“增加”本设定数字位数值
的作用。 5
做法一:
步骤一:将操作旋钮转至“关阀”位置;
步骤二:松开操作旋钮,让其自动回到“初始”位置。
做法二:在功能按钮处于“现场”情况下,使用遥控器按下“关”键。
5. “上移”/“循环右移”操作 在选项选择设定方式时,起到“上移”到下一个选项 的作用;在数字设定方式时,起到“循环右移”到下一位 数字的作用。 做法一: 步骤一:将操作旋钮转至“开阀”位置;
AirTurn BT500 Bluetooth控制器说明书

BT500 ManualSupport for:AirTurn DIGIT 500AirTurn DUO 500C ONTENTSContents2 Before Turning on Your AirTurn4 BT500 Controls5 Power6 Connecting and Pairing6 Open and Closed Pairing6 Open Pairing6Closed Pairing7Reset Pairing7 Switching Between Pairing Methods8 Pairing in AirDIRECT MODE 18 Pairing in MODE 2-6 (Keyboard/Mouse)9 Pairing in MODE 7 (MIDI)9 MIDI Mode10 MODES for BT50011Changing the MODE12 Virtual Keyboard in iOS12 Power Consumption13 Recharging the Battery13 LED Indications13 AirTurn Manager14 Unit Identification14 Care of Your AirTurn15 Warranty15 Radio Information16 Recycling and Disposal18 Battery Information18 Battery Disposal19 Trademarks19Thank you for purchasing an AirTurn BT500 Bluetooth controller.We hope you enjoy many years of use from it.From page turning,to effects management and presentation control,the AirTurn provides a myriad of uses.B EFORE T URNING ON Y OUR AirTurnThe BT500works with most Bluetooth4and5devices.This includes iPad3and later,iPhone4S and later,and most devices running Android 4.3 or later with Bluetooth 4 or 5.Most PCs and Macs equipped with Bluetooth4.x or5and HID (keyboard)support are compatible.For older PCs you can use Bluetooth 4.1 or 5 USB dongles that can connect to the AirTurn.A compatible app is required.Apps are listed on the AirTurn website: https:///appsThere are three compatibility modes:AirTurn Direct,HID, (keyboard),and MIDI.Not all compatible apps will function in every mode. See the MODES section for additional information.BT500 C ONTROLSThe BT500 series uses the same transceiver for each model. The controls consist of a power button, a membrane pad with 5 buttons, a dedicated Mode button, two stereo ports for use with up to four pedals, two LED indicators, and a USB-C port for charging. The function of each button is explained on page 12.P OWERON-Press and hold the Power Button for one second and the LEDs flash.The blue LED will begin to blink2times per second until pairing is started.OFF-Press and hold the Power Button until the red and blue LEDs turn off.C ONNECTING AND P AIRINGOnce the AirTurn is selected for pairing,the blue LED will blink 5 times per second until pairing is completed.O PEN AND C LOSED P AIRINGAirTurn devices have the ability to pair to your tablet or computer two different ways.We call them Open and Closed pairing. Open pairing is the default method.O PEN P AIRINGAirTurn devices pair in the same way that almost all Bluetooth devices pair.In Open Pairing you do not need to delete the pairing to connect to another device so you can easily connect your AirTurn to your iPad,smartphone or computer.In fact,youcan connect up to8Bluetooth devices.(In MODE1(AirDirect) you can connect to an unlimited number of devices).Bear in mind you can only be connected to one device at a time.If two of your devices have Bluetooth turned on,you must turn off the Bluetooth of the one you do not wish to connect to while you connect to the other device.No reset is required with Open Pairing.If you connect to more than8devices,the next pairing will delete the pairing that you haven’t used recently.If you delete or “forget”the pairing of the AirTurn on a device,restart the Bluetooth and attempt to re-pair with the AirTurn–It may require two attempts to connect.C LOSED P AIRINGThis method locks one AirTurn to one tablet,phone or computer. Use this method if you only intend to be connected to one tablet,phone or computer.Also,use this method if you are in an ensemble with other players using AirTurn devices.It will ensure that you don’t inadvertently connect to each other’s devices. Pairing is required in all MODES.R ESET P AIRINGTo delete all pairings,or if you would like to connect to another device,or you are having connection problems,you can pair again by removing all the existing pairing connections.First,delete the pairing from the host device and turn off the Bluetooth.Then,hold the power button on the AirTurn for6 seconds.The LEDs will turn off,but don’t release until they blink 3 more times. You are now ready to pair again.S WITCHING B ETWEEN P AIRING M ETHODSYou can easily switch between Open and Closed pairing methods.With your AirTurn powered off,hold down the MODE button and hold the power button to turn on as usual.Both LEDs will flash to confirm–twice for open pairing,three times for closed pairing.You can also change the Pairing method using the AirTurn Manager App, in Advanced settings.P AIRING IN A IR DIRECT MODE 1Note:This MODE is for AirDirect specific apps only.AirDirect MODE was created to prevent conflicts with the virtual keyboard.1.Power on the AirTurn2.Be sure the AirTurn is in MODE1(Hold down the MODEbutton for 1 blink of the red light)3.Turn on your device’s Bluetooth thena.On iOS,go to the app you want to use and find theBluetooth setup screenb.On Android, go to the AirTurn manager App4.Find the AirTurn in the device list and tap on it5.If required, tap on the Pair button in the dialog boxP AIRING IN MODE 2-6 (K EYBOARD/M OUSE)iOS–Select Settings>Bluetooth and turn on Bluetooth if it is off.When the AirTurn is discovered,tap on the selection.A dialog box will then appear. Tap on Pair.Android–Select Settings>Bluetooth,and turn it on if it is off. Make sure your device is set to discoverable,tap the SCAN button.When the AirTurn appears,tap to pair.If asked to verify a passcode, click OK.PC–Select Control Panel>My Bluetooth Devices>Select “Add a device” > Click next and complete pairing.Mac–Select Apple>System Preferences>Bluetooth and turn on Bluetooth.P AIRING IN MODE 7 (MIDI)With all devices,ensure Bluetooth is turned on and switch your AirTurn to Mode 7.iOS–Go to the MIDI App you wish to use and find the Bluetooth MIDI connection settings.Select your AirTurn in the list. If requested, tap Pair.Android–Select Settings>Bluetooth.Tap the SCAN button. When the AirTurn appears,tap to pair.If you are asked to verify the passcode, click on OK.PC–Select Control Panel>My Bluetooth Devices>Select “Add a device”>Click next and complete pairing.(Middleware may be required)Mac–Select File>New Finder Window>Applications> Utilities>Audio MIDI Setup>Select“Bluetooth”>Next to the AirTurn click “Connect”MIDI M ODEMIDI Mode is for sending basic MIDI commands to your app. Support for Bluetooth MIDI is required,and special setup for your tablet or computer may be required.MIDI commands may be setup using the AirTurn Manager.More detailed instructions available online(/support/midi)or reach out to our support team at*******************for further assistance.MODES FOR BT500There are seven modes available on your AirTurn.Each mode sends a different signal for each pedal.The AirTurn is set to MODE2by default.You can also customize MODES2-6with the AirTurn Manager App.(See page12for instructions on mode changes)Switch 1Switch 2Switch 3Switch 4Switch 5 Mode 1AirDirectMode 2Up Arrow Left Arrow DownArrowRightArrowEnterMode 3Page Up Left Arrow Page Down RightArrowEnterMode 4V olume Up PreviousTrackV olumeDownNext Track Play/PauseMode 5Space Left Click Enter Right Click Home Mode 63p m Shift +R Space Mode 7Damper Portamento Sostenuto Soft Pedal LegatoC HANGING THE MODE1.Turn on the AirTurn.2.Press and hold the MODE button.The red LED willflash once per second from1to7flashes.Thenumber of flashes corresponds to the MODEnumber. Be sure to count the flashes.3.Release the MODE button following the number offlashes that reflects the desired MODE.The blue andred LED will flash together the number of timesindicating which MODE has been set.Example:To set MODE2,hold the MODE button for2 flashes of the red LED,release,and both LEDs will flash2 times to confirm the MODE 2 setting.Note:Once the MODE has been set,it will remain the same until it is changed following the above steps.V IRTUAL K EYBOARD IN iOSTo turn on the virtual keyboard in iOS,put the cursor into a text box and press the Power Button.Both LEDs will flash once to signify that the button was pressed.The button will only work in Modes2-6.Virtual keyboard support for MODE1is automatic. This is not available for Android except when using MODE 1.P OWER C ONSUMPTIONThe AirTurn uses an idle timeout function to conserve power. After two hours of inactivity when powered on and connected, the AirTurn will power down automatically.The timer is reset when any button is pressed.You can change this time out period or turn it off completely using the AirTurn Manager software. The AirTurn averages a usage of1160μA when powered on and 5 μA when off.R ECHARGING THE B ATTERY A ND B ATTERY S AFETYTo charge the battery,insert the charging cable into theport and plug the other end into any USB source.The RedLED will slowly blink to indicate charging,and turn solidwhen complete. A charge will last for about 250 hours. The BT500series includes several battery safety features to help maintain battery life and health.The battery will stop providing power if it is too low,and stop charging when full.Charging is disabled when the unit is above45°C,or below0°C(113°f and 32°f).Charging resumes when the unit is back within operating range.LED I NDICATIONSLED indication State3 red flashes when attempting to power on Battery is too low to operateRed flash every 3 seconds Battery is lowRed flash once a second ChargingSolid red Fully chargedBlue flashing rapidly (twice a second)Ready to connectBlue flashing very rapidly (5 times aConnectingsecond)Blue flash every 3 seconds ConnectedSolid blue Pedal pressedRapid red flash Temperature too high/lowA IR T URN M ANAGERTo change the configuration of your AirTurn and update its firmware to the latest available,download the AirTurn Manager App from the Apple App Store or Google Play Store.It is available for iPad,iPhone,most Android devices and Mac computers.The App allows you to configure the key repeat rate,power saving settings,select pairing method and configure the signals for each of the pedals in each mode.If any firmware updates are available,you will be notified after the App has connected.After performing the update,the AirTurn will install it and shut down.Remove the pairing from your iOS/Android/PC/Mac device,power on the AirTurn,and reconnect. It is recommended to check for updates quarterly.U NIT I DENTIFICATIONThe unit name in your Bluetooth host consists of several codes to help with support and identifying your specific device.For example:BT500v3.0.2 ABCDV2.1.0 refers to the firmware number.ABCD refers to the MAC address.This is helpful if there are many AirTurn units in the same location.Your MAC address will always be the same so you can easily identify your unit.You will find your specific MAC address labeled on the bottom of your AirTurn at the end of the serial number.R ESET TO F ACTORY D EFAULTSTo reset the AirTurn to factory defaults,hold the first two switches while powering on the device.Both LEDs will flash3 times and then the AirTurn will power off.There is also a reset option through the AirTurn Manager.C ARE OF Y OUR A IR T URNWipe down using a damp cloth with a mild detergent or soap-based cleaner to remove dirt and stains from your AirTurn.●Do not get the AirTurn wet or place it in direct sunlight forextended periods of time.●Do not open the unit, as there are no user serviceable parts.●Do not put the AirTurn in the trash. Please recycle.W ARRANTYAirTurn,Inc.,(“AirTurn”),warrants to the first consumer purchaser that the AirTurn BT500, (the“Product”),when shipped in its original container,will be free from defective workmanship and materials,and agrees that it will,at its option,either repair the defect or replace the defective Product or part thereof with a new or remanufactured equivalent at no charge to the purchaser for parts or labor for one year from date of purchase.This warranty does not apply to any appearance items of the Product nor to any Product the exterior of which has been damaged or defaced,which has been subjected to misuse, abnormal service or handling,or which has been altered or modified in design or construction, nor does it apply to batteries that may be supplied.In order to enforce the rights under this limited warranty,the purchaser should request a RMA number via email or phone following the directions on the support page at /support.The purchaser shall return the product at their expense.The repaired or replaced product will be returned at the expense of AirTurn.The limited warranty described herein is in addition to whatever implied warranties may be granted to purchasers by law.ALL IMPLIED WARRANTIES INCLUDING THE WARRANTIES OF MERCHANTABILITY AND FITNESS FOR USE ARE LIMITED TO ONE YEAR FROM THE DATE OF THE PURCHASE.Some states do not allow limitations on how long an implied warranty lasts, so the above limitation may not apply to you.The warranties described herein shall be the sole and exclusive warranties granted by AirTurn and shall be the sole and exclusive remedy available to the purchaser.Correction ofdefects,in the manner and for the period of time described herein,shall constitute complete fulfillment of all liabilities and responsibilities of AirTurn to the purchaser with respect to the Product and shall constitute full satisfaction of all claims,whether based on contract, negligence,strict liability or otherwise.In no event shall AirTurn be liable,or in any way responsible,for any damages or defects in the Product which were caused by repairs or attempted repairs performed by anyone other than an authorized servicer,nor shall AirTurn be liable or in any way responsible for any incidental or consequential economic or property damage.Some states do not allow the exclusion of incidental or consequential damages,so the above exclusion may not apply to you.THIS WARRANTY GIVES YOU SPECIFIC LEGAL RIGHTS.YOU MAY ALSO HA VE OTHER RIGHTS, WHICH V ARY FROM STATE TO STATE.R ADIO I NFORMATION●Bluetooth 5.0 low energy radio●Transmit power: -1 dBm peak●TX peak current: 18.2 mA●Frequency 2.36GHz to 2.50GHzApproximate Range: 200 feet (61 Meters) subject to orientation and other factors.This device complies with Part 15 of the FCC Rules.Operation is subject to the following two conditions:(1) this device may not cause harmful interference, and(2)this device must accept any interference received,including interference that may cause undesired operation.CAUTION:Changes or modifications not expressly approved by the party responsible for compliance could void the user’s authority to operate the equipment.NOTE:This equipment has been tested and found to comply with the limits for a Class B digital device,pursuant to Part15of the FCC Rules.These limits are designed to provide reasonable protection against harmful interference in a residential installation.This equipment generates,uses,and can radiate radio frequency energy,and,if not installed and used in accordance with the instructions,may cause harmful interference to radio communications.However,there is no guarantee that interference will not occur in a particular installation.If this equipment does cause harmful interference to radio or televisionreception,which can be determined by turning the equipment off and on,the user is encouraged to try to correct the interference by one or more of the following measures:--Reorient or relocate the receiving antenna.--Increase the separation between the equipment and receiver.--Connect the equipment into an outlet on a circuit different from that to which the receiver is connected.--Consult the dealer or an experienced radio/TV technician for help.Contains FCC ID: 2AA9B04Contains transmitter module IC: 12208A-04This device complies with Industry Canada license-exempt RSS standard(s).Operation is subject to the following two conditions:(1)this device may not cause interference,and(2) this device must accept any interference,including interference that may cause undesired operation of the device.KCC(Korea)BMD-300has type certification in Korea with certification number R-CRM-Rgd-BMD-300Contains ANATEL approved module # 00820-21-05903Este equipo contiene el módulo con IFT #: NYCE/CT/0146/17/TSAirTurn also holds unintended emissions testing on file for FCC/CER ECYCLING AND D ISPOSALElectronic components and construction complywith RoHS and REACH standards.Packaging is recyclable. Please recycle.Contains Lithium Ion Battery.Battery should bedisposed of according to local law.AirTurn willrecycle returned batteries and electronics.Pleaserequest an RMA from the support desk:*******************B ATTERY I NFORMATIONContains Lithium-Polymer Battery.Charging with a standard5V USB charger with the provided adaptor cable is recommended. Charging from a laptop or a computer with a sleep setting is not recommended.A charge will last for about250hours,generally a battery should last 2-5 years.Operating temperature of your AirTurn device should be between -20C and+55C.Charging temperature should be between0C and +45C,The temperature sensor inside the case will stop the charging if temperatures go outside that range.B ATTERY D ISPOSAL— Do not put lithium ion batteries in the trash.— Recycling is always the best option.—The battery should be disposed of according to local law. AirTurn will recycle returned batteries and electronics.Please request an RMA from the support desk:******************* T RADEMARKSiPhone, iPod, iOS, iPad are trademarks of Apple, Inc.Android is a trademark of Google, Inc.Powerpoint, Word are trademarks of Microsoft AirTurn, BT500, and its respective logos are trademarks ofAirTurnCheck out other great products from AirTurn including tablet holders, portable tablet stands, and accessories******************* 888-247-1223。
艾克夫sl500中文说明书

图形显示采用10.5"液晶显示器、16种颜色、分辨率640 x 480 pixels像素形象显示。
基本菜单控制程序启动时,计算机显示一个主屏。
第一屏称为主菜单,它形象地显示采煤机及其主要参数。
用户操作功能键F1 – F8可以直接转换基本菜单。
.可使用以下基本菜单:F1: 主菜单形象化的采煤机、截割、牵引和泵电机的温度、电缆拖拉监测、位置和速度信息。
F2: "截割"菜单所有读数涉及截割电机:温度、电流、电压和所有数字监测传感器。
F3: "牵引"菜单所有读数涉及牵引驱动: 温度、电流、电压和所有数字监测传感器F4: "液压"菜单所有读数涉及液压系统: 温度、电流、电压和所有数字监测传感器F5: "水"菜单所有读数涉及滚筒喷雾和冷却水F6: "温度"菜单所有读数涉及的传感器温度,这些传感器不属于上述菜单或者由于空间限制未能出现在上述菜单中F7: "电流 /电压"菜单所有读数涉及的电流电压不属于上述菜单或者由于空间限制未能出现在上述菜单中F8: "自动化" 菜单 (可选项)所有读数涉及与功能和自动化系统的状态相关的重要信息。
可以使用基本菜单中的下列其它键:F9作为基本菜单的功能显示图形菜单??显示故障信息、其它帮助文字或者储存的故障信息ENTER进入已选择的显示各种参数的菜单图形显示说明标题栏标题栏由3部分组成。
中间部分显示标题和当前时间。
条的颜色显示控制程序的状态。
如果没有出现故障,条的颜色为灰色。
如果出现引起单元出错的多个故障,颜色变为红色。
如果只出现警告、不太重要的或者过时信息,则条的颜色为黄色。
标题栏的两端反应的是指令发生器的状态(手动/遥控)。
其中的文字指的是当前运行的指令发生器。
条的颜色表明:来自该指令发生器的驱动是否能够接通?灰色- 采用该指令发生器不能接通驱动绿色- 采用该指令发生器能接通驱动红色- 指令发生器预先接通,但是没有运行带限制的垂直图形条这些垂直图形条主要用于显示温度、电流和电压读数。
- 1、下载文档前请自行甄别文档内容的完整性,平台不提供额外的编辑、内容补充、找答案等附加服务。
- 2、"仅部分预览"的文档,不可在线预览部分如存在完整性等问题,可反馈申请退款(可完整预览的文档不适用该条件!)。
- 3、如文档侵犯您的权益,请联系客服反馈,我们会尽快为您处理(人工客服工作时间:9:00-18:30)。
前言AT500系列变频器是高性能矢量型和转矩控制型变频器。
产品采用了与目前国际领先技术同步的无速度传感器矢量控制技术和转矩控制技术,不仅具有与国际高端变频器同样优异的控制性能,同时还结合中国的应用特点,进一步强化了产品的可靠性和环境的适应性以及客户化和行业化的设计,能够更好地满足各种传动应用的需求。
注意事项●为说明产品的细节部分,本手册中的图例有时为拆下外罩或安全遮盖物的状态。
使用本产品时,请务必按规定装好外壳或遮盖物,并按照手册的内容进行操作。
●本手册中的图例仅为了说明,可能会与您订购的产品有所不同。
●本公司致力于产品的不断改善,产品功能会不断升级,所提供的资料如有变更,恕不另行通知。
●如您使用中有问题,请与本公司各区域代理商联系,或直接与本公司客户服务中心联系。
客服电话:0510-******** 传真:0510-********24小时技术服务电话:133******** 133********安全注意事项安全标记说明:危险:错误使用,可能会导致火灾、人身严重伤害,甚至死亡。
注意:错误使用,可能导致人身中等程度的伤害或者轻伤,以及发生设备损坏。
█用途危险●本系列变频器用于控制异步电动机的变速运行,不能用于其他用途,否则可引起变频器故障或火灾。
●本系列变频器不能简单的应用于医疗装置等直接与人身安全有关的场合。
●本系列变频器是在严格的质量管理体系下生产的,如果变频器的故障可能会导致重大事故或损失,则需要设置冗余或旁路等安全措施,以防万一。
█到货检验注意●若发现变频器受损或缺少零部件则不可安装,否则可能发生事故。
█安装注意●搬运、安装时,请托住产品底部,不能只拿住外壳,以防砸伤脚或损坏变频器。
●变频器要安装于金属等阻燃物上,远离易燃物体,远离热源。
●安装作业切勿将钻孔残余物落入变频器内部,否则可能引起变频器故障。
●变频器安装于柜内,电控柜应配置风扇、通风口,柜内应构建有利于散热的风道。
█接线危险●必须由合格的电气工程人员进行接线工作,否则有触电或损坏变频器的危险。
●接线前请确认电源处于断开状态,否则可能有触电或火灾的危险。
●接地端子PE要可靠接地,否则变频器外壳有带电的危险。
●请勿触摸主回路端子,变频器主回路端子接线不要与外壳接触,否则有触电的危险。
●变频器整机的漏电流大于5mA,漏电流的具体数值由使用条件决定,为保证安全,变频器和电机必须接地。
█接线注意●三相电源不能接到输出端子U、V、W,否则将造成变频器损坏。
●绝对禁止在变频器的输出端连接电容或相位超前的LC/LR噪声滤波器,否则将导致变频器内部器件损坏。
●请确认电源相数、额定电压是否与产品的铭牌相符,否则可能造成变频器损坏。
●不能对变频器进行耐压测试,否则可能造成变频器损坏。
●变频器的主回路端子配线和控制回路端子配线应分开布线或垂直交叉,否则将造成控制器信号受干扰。
●主回路端子的配线电缆请使用带有绝缘套管的线鼻子。
●变频器输入及输出电缆长度超过100米时,建议使用输出电抗器,以避免过大的分布电容产生的过电流导致变频器故障。
█运行危险●变频器配线完成并装上盖板后,方可通电,带电状态下严禁拆下盖板,否则有触电的危险。
●当设置了故障自动复位或停电后再启动功能时,应对机械设备采取安全隔离措施,否则可能造成人员伤害。
●变频器接通电源后,即使处于停机状态,变频器的端子上仍带电,不能触摸,否则可能造成触电。
●在确认运行命令被切断后,才可以复位故障和告警信号,否则可能造成人员伤害。
█运行注意●不要采用接通或断开供电电源的方式来启停变频器,否则可能引起变频器损坏。
●运行前,请确认电机及机械是否在允许的使用范围内,否则可能会损坏设备。
●散热器和制动电阻温度很高,请勿触摸,否则有烫伤的危险。
●在提升设备上使用时,请同时配置机械抱闸装置。
●请勿随意更改变频器参数,变频器的绝大多数出厂设定参数已能满足运行要求,只要设定一些必要的参数即可,随意修改参数可能导致机械设备的损坏。
●在有些工频和变频切换的场合,应使控制工频和变频切换的两个接触器互锁。
█维护、检查危险●在通电状态,请勿触摸变频器的端子,否则有触电的危险。
●如果要拆卸盖板,请务必断电。
●断电后等待至少10分钟或确认充电CHARGE指示灯已熄灭,才能进行保养和检查,以防止主回路电解电容的残余电压造成人员伤害。
●请指定合格的电气工程人员进行保养、检查或更换部件。
注意●线路板上有CMOS大规模集成电路,请勿用手触摸,以防静电损坏线路板。
█其它注意●禁止自行改造变频器,否则会导致人员伤害。
目录前言......................................................................................................................................................................... - 1 - 目录......................................................................................................................................................................... - 4 - 第一章产品信息 .................................................................................................................................................... - 5 -1.1产品型号说明......................................................................................................................................... - 5 -1.2产品铭牌说明......................................................................................................................................... - 5 -1.3 AT500变频器系列 ................................................................................................................................. - 5 -1.4产品各部分说明 ..................................................................................................................................... - 6 -1.5产品技术规格说明.................................................................................................................................. - 7 -1.6产品外观及安装尺寸.............................................................................................................................. - 9 -1.7键盘外观及安装尺寸............................................................................................................................ - 12 -1.8键盘托盘外观及开孔尺寸..................................................................................................................... - 12 - 第二章产品机械安装 ........................................................................................................................................... - 14 -2.1安装环境 .............................................................................................................................................. - 14 -2.2 产品盖板的拆卸 .................................................................................................................................. - 15 - 第三章产品电气安装 ........................................................................................................................................... - 15 -3.1与外围器件的连接................................................................................................................................ - 15 -3.2外围电气元件使用说明 ........................................................................................................................ - 15 -3.3外围器件的选型指导............................................................................................................................ - 15 -3.4制动电阻的选型指导............................................................................................................................ - 15 -3.5接线方式 .............................................................................................................................................. - 19 - 第四章键盘与显示............................................................................................................................................... - 25 -4.1操作与显示界面 ................................................................................................................................... - 25 -4.2键盘指示灯说明 ................................................................................................................................... - 26 -4.3键盘按键说明....................................................................................................................................... - 26 -4.4功能码查看和修改方法 ........................................................................................................................ - 26 -4.5菜单模式选择....................................................................................................................................... - 27 - 第五章参数一览表............................................................................................................................................... - 28 - 第六章参数说明 .................................................................................................................................................. - 49 - F0组基本功能参数组............................................................................................................................... - 50 - F1组电机参数组...................................................................................................................................... - 55 - F2组输入端子.......................................................................................................................................... - 56 - F3组输出端子.......................................................................................................................................... - 62 - F4组辅助参数组...................................................................................................................................... - 64 - F5组矢量控制参数组............................................................................................................................... - 71 - F6组V/F控制参数组 ................................................................................................................................ - 72 - F7组启停控制参数组............................................................................................................................... - 74 - F8组键盘及显示参数组........................................................................................................................... - 77 - F9组故障及保护参数组........................................................................................................................... - 78 - FA组PID参数组 ...................................................................................................................................... - 83 - FB组摆频、定长、计数及转矩控制参数组.............................................................................................. - 85 - FC组多段速与简易PLC参数组.............................................................................................................. - 88 - FD组通讯功能参数组 .............................................................................................................................. - 90 - FE组快速菜单参数组 .............................................................................................................................. - 90 - P0组模拟量四点偏置参数组.................................................................................................................... - 91 - P1组模拟量校正参数组........................................................................................................................... - 92 - H0组基本监视参数组 .............................................................................................................................. - 93 - 第七章维护保养与故障诊断 ................................................................................................................................ - 96 -7.1变频器的日常保养与维护..................................................................................................................... - 96 -7.2 变频器的保修说明............................................................................................................................... - 96 -7.3 故障报警及对策 .................................................................................................................................. - 97 - 附录一:Modbus 通讯协议.............................................................................................................................. - 100 -1.1 协议内容 ........................................................................................................................................... - 100 -1.2 通讯帧说明........................................................................................................................................ - 100 -1.3 通讯数据地址定义............................................................................................................................. - 103 -1.4 FD组通讯参数说明............................................................................................................................ - 105 -第一章产品信息1.1产品型号说明铭牌上变频器型号一栏用数字和字母表示了产品系列、电源等级、功率等级、制动单元等信息。