MIT6_042JS10_lec37_sol
LT8637 42V, 5A Synchronous Step-Down Silent Switch
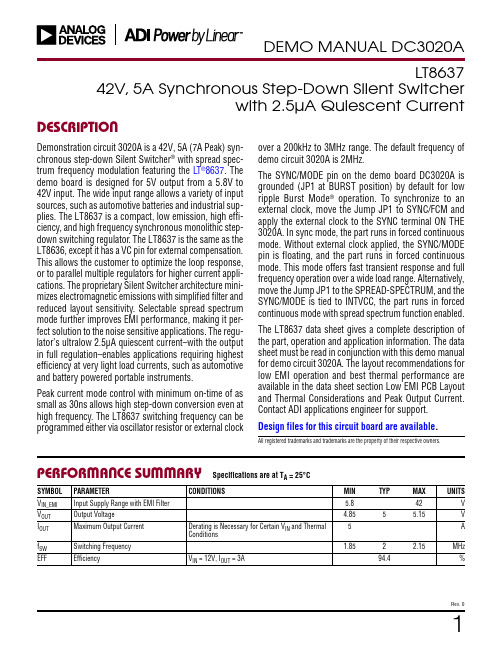
1Rev. 0DESCRIPTIONLT863742V, 5A Synchronous Step-Down Silent Switcherwith 2.5μA Quiescent CurrentDemonstration circuit 3020A is a 42V, 5A (7A Peak) syn-chronous step-down Silent Switcher ® with spread spec-trum frequency modulation featuring the L T ®8637. The demo board is designed for 5V output from a 5.8V to 42V input. The wide input range allows a variety of input sources, such as automotive batteries and industrial sup-plies. The LT8637 is a compact, low emission, high effi-ciency, and high frequency synchronous monolithic step-down switching regulator . The LT8637 is the same as the LT8636, except it has a VC pin for external compensation. This allows the customer to optimize the loop response, or to parallel multiple regulators for higher current appli-cations. The proprietary Silent Switcher architecture mini-mizes electromagnetic emissions with simplified filter and reduced layout sensitivity. Selectable spread spectrum mode further improves EMI performance, making it per-fect solution to the noise sensitive applications. The regu-lator’s ultralow 2.5μA quiescent current–with the output in full regulation–enables applications requiring highest efficiency at very light load currents, such as automotive and battery powered portable instruments.Peak current mode control with minimum on-time of as small as 30ns allows high step-down conversion even at high frequency. The LT8637 switching frequency can be programmed either via oscillator resistor or external clockAll registered trademarks and trademarks are the property of their respective owners.PERFORMANCE SUMMARYover a 200kHz to 3MHz range. The default frequency of demo circuit 3020A is 2MHz.The SYNC/MODE pin on the demo board DC3020A is grounded (JP1 at BURST position) by default for low ripple Burst Mode ® operation. To synchronize to an external clock, move the Jump JP1 to SYNC/FCM and apply the external clock to the SYNC terminal ON THE 3020A. In sync mode, the part runs in forced continuous mode. Without external clock applied, the SYNC/MODE pin is floating, and the part runs in forced continuous mode. This mode offers fast transient response and full frequency operation over a wide load range. Alternatively, move the Jump JP1 to the SPREAD-SPECTRUM, and the SYNC/MODE is tied to INTVCC, the part runs in forced continuous mode with spread spectrum function enabled. The LT8637 data sheet gives a complete description of the part, operation and application information. The data sheet must be read in conjunction with this demo manual for demo circuit 3020A. The layout recommendations for low EMI operation and best thermal performance are available in the data sheet section Low EMI PCB Layout and Thermal Considerations and Peak Output Current. Contact ADI applications engineer for support.Design files for this circuit board are available .Specifications are at T A = 25°CSYMBOL PARAMETERCONDITIONSMIN TYPMAX UNITSV IN_EMI Input Supply Range with EMI Filter 5.842V V OUT Output Voltage4.855 5.15V I OUT Maximum Output Current Derating is Necessary for Certain V IN and Thermal Conditions 5Af SW Switching Frequency 1.852 2.15MHz EFFEfficiencyV IN = 12V, I OUT = 3A94.4%QUICK START PROCEDUREDemonstration circuit 3020A is easy to set up to evalu-ate the performance of the LT8637. Refer to Figure 1 for proper measurement equipment setup and follow the procedure below:NOTE: When measuring the input or output voltage ripple, care must be taken to avoid a long ground lead on the oscilloscope probe. Measure the output voltage ripple by touching the probe tip directly across the output capacitor.1. Make sure the Jump JP1 is on the BURST position. Refer to the schematic.2. With power off, connect the DC power supply to VEMI and GND. Connect the load from VOUT to GND.3. Connect the voltage meter across the VIN_SENSE and GND for V IN measurement, and VOUT_SENSE and GND for V OUT measurement.4. Turn on the power at the input.NOTE: Make sure that the input voltage does not exceed 42V.5. Check for the proper output voltage (V OUT = 5V). NOTE: If there is no output, temporarily disconnect theload to make sure that the load is not set too high or is shorted.6. Once the proper output voltage is established, adjust the load within the operating ranges and observe the output voltage regulation, ripple voltage, efficiency and other parameters. For efficiency measurement, use the VIN_SENSE, GND, and VOUT_SENSE, GND accordingly.7. An external clock can be added to the SYNC terminal when SYNC function is used (JP1 on the SYNC position). When JP1 is in SYNC, and no external clock is connected to the SYNC terminal of the board, the SYNC/FCM pin is floating, and the LT8637 runs in forced continuous mode. JP1 can also set LT8637 in spread spectrum mode (JP1 on the SPREAD-SPECTRUM position).Figure 1. Proper Measurement Equipment Setup2Rev. 0QUICK START PROCEDUREEfficiency, 12V IN, FCMFigure 2. Efficiency vs Load Current, 12V IN, V OUT = 5VCISPR25 Radiated Emission Test with Class 5 Average LimitsFigure 3. Radiated Emission Test with CISPR 25, Average Limit, SS Mode. V IN = 14V, I OUT = 5A, V OUT = 5V3Rev. 0PARTS LISTITEM QTY REFERENCE PART DESCRIPTION MANUFACTURER/PART NUMBERRequired Circuit Components11C1CAP., 22µF, ALUM. ELECT., 63V, 20%, 6.3mm × 7.7mm, CE-BS SUN ELECTRONIC INDUSTRIES CORP, 63CE22BS 23C2, C10, C11CAP., 10µF, X7R, 50V, 10%, 1210, NO SUBS. ALLOWED MURATA, GRM32ER71H106KA12L32C3, C4CAP., 1µF, X5R, 50V, 10%, 0603AVX, 06035D105KAT2A41C5CAP., 0.1µF, X7R, 16V, 10%, 0603WURTH ELEKTRONIK, 885012206046 51C6CAP., 10pF, X7R, 50V, 10%, 0603AVX, 06035C100KAT2A61C7CAP., 100µF, X5R, 6.3V, 10%, 1206MURATA, GRM31CR60J107KE39L72C8, C16CAP., 1µF, X7R, 10V, 10%, 0603AVX, 0603ZC105KAT2A83C12, C13, C15CAP., 0.1µF, X7R, 50V, 10%, 0402AVX, 04025C104KAT2A91C17CAP., 560pF, C0G, 50V, 5%, 0603AVX, 06035A561JAT2A101C18CAP., 68pF, C0G, 50V, 5%, 0603AVX, 06035A680JAT2A111FB1IND., 30Ω AT 100MHz, FERRITE BEAD, 25%, 5A, 10mΩ, 0603TDK, MPZ1608S300ATAH0121L1IND., 2.2µH, 20%, 18.1A, 6.70mΩ, 6.56mm × 6.36mm,COILCRAFT, XEL6060-222MEBXEL6060, AEC-Q200131L2IND., 0.33µH, 20%, 19.2A, 3.52mΩCOILCRAFT, XAL5030-331MEB142R1, R4RES., 100k, 1%, 1/10W, 0603, AEC-Q200VISHAY, CRCW0603100KFKEA151R2RES., 17.8k, 1%, 1/10W, 0603, AEC-Q200NIC, NRC06F1782TRF161R3RES., 243k, 1%, 1/10W, 0603VISHAY, CRCW0603243KFKEA171R6RES., 1M, 1%, 1/10W, 0603, AEC-Q200VISHAY, CRCW06031M00FKEA181R7RES., 0Ω, 1/10W, 0603, AEC-Q200VISHAY, CRCW06030000Z0EA191R9RES., 8.06k, 1%, 1/10W, 0603YAGEO, RC0603FR-078K06L201U1IC, SYN. STEP-DOWN Silent Switcher, LQFN-20, 42V, 5A/7A ANALOG DEVICES, LT8637EV#PBF Additional Demo Board Circuit Components10R8RES., OPTION, 0603Hardware: For Demo Board Only14E2, E9, E11, E12TEST POINT, TURRET, 0.064" MTG. HOLE, PCB 0.062" THK MILL-MAX, 2308-2-00-80-00-00-07-0 26E4-E8, E10TEST POINT, TURRET, 0.094" MTG. HOLE, PCB 0.062" THK MILL-MAX, 2501-2-00-80-00-00-07-0KEYSTONE, 575-4 34J1-J4CONN., BANANA JACK, FEMALE, THT, NON-INSULATED,SWAGE, 0.218"41JP1CONN., HDR., MALE, 2 × 3, 2mm, VERT, STR, THT WURTH ELEKTRONIK, 6200062112154MH1-MH4STANDOFF, NYLON, SNAP-ON, 0.50"WURTH ELEKTRONIK, 70293500061XJP1CONN., SHUNT, FEMALE, 2-POS, 2mm SAMTEC, 2SN-BK-G4Rev. 05Rev. 0Information furnished by Analog Devices is believed to be accurate and reliable. However , no responsibility is assumed by Analog Devices for its use, nor for any infringements of patents or other rights of third parties that may result from its use. Specifications subject to change without notice. No license is granted by implication or otherwise under any patent or patent rights of Analog Devices.SCHEMATIC DIAGRAMP h o n e : (4086Rev. 0ANALOG DEVICES, INC. 202103/21ESD CautionESD (electrostatic discharge) sensitive device. Charged devices and circuit boards can discharge without detection. Although this product features patented or proprietary protection circuitry, damage may occur on devices subjected to high energy ESD. Therefore, proper ESD precautions should be taken to avoid performance degradation or loss of functionality.Legal Terms and ConditionsBy using the evaluation board discussed herein (together with any tools, components documentation or support materials, the “Evaluation Board”), you are agreeing to be bound by the terms and conditions set forth below (“Agreement”) unless you have purchased the Evaluation Board, in which case the Analog Devices Standard Terms and Conditions of Sale shall govern. Do not use the Evaluation Board until you have read and agreed to the Agreement. Your use of the Evaluation Board shall signify your acceptance of the Agreement. This Agreement is made by and between you (“Customer”) and Analog Devices, Inc. (“ADI”), with its principal place of business at One Technology Way, Norwood, MA 02062, USA. Subject to the terms and conditions of the Agreement, ADI hereby grants to Customer a free, limited, personal, temporary, non-exclusive, non-sublicensable, non-transferable license to use the Evaluation Board FOR EVALUATION PURPOSES ONL Y. Customer understands and agrees that the Evaluation Board is provided for the sole and exclusive purpose referenced above, and agrees not to use the Evaluation Board for any other purpose. Furthermore, the license granted is expressly made subject to the following additional limitations: Customer shall not (i) rent, lease, display, sell, transfer , assign, sublicense, or distribute the Evaluation Board; and (ii) permit any Third Party to access the Evaluation Board. As used herein, the term “Third Party” includes any entity other than ADI, Customer , their employees, affiliates and in-house consultants. The Evaluation Board is NOT sold to Customer; all rights not expressly granted herein, including ownership of the Evaluation Board, are reserved by ADI. CONFIDENTIALITY. This Agreement and the Evaluation Board shall all be considered the confidential and proprietary information of ADI. Customer may not disclose or transfer any portion of the Evaluation Board to any other party for any reason. Upon discontinuation of use of the Evaluation Board or termination of this Agreement, Customer agrees to promptly return the Evaluation Board to ADI. ADDITIONAL RESTRICTIONS. Customer may not disassemble, decompile or reverse engineer chips on the Evaluation Board. Customer shall inform ADI of any occurred damages or any modifications or alterations it makes to the Evaluation Board, including but not limited to soldering or any other activity that affects the material content of the Evaluation Board. Modifications to the Evaluation Board must comply with applicable law, including but not limited to the RoHS Directive. TERMINATION. ADI may terminate this Agreement at any time upon giving written notice to Customer . Customer agrees to return to ADI the Evaluation Board at that time. LIMITATION OF LIABILITY. THE EVALUATION BOARD PROVIDED HEREUNDER IS PROVIDED “AS IS” AND ADI MAKES NO WARRANTIES OR REPRESENTATIONS OF ANY KIND WITH RESPECT TO IT . ADI SPECIFICALL Y DISCLAIMS ANY REPRESENTATIONS, ENDORSEMENTS, GUARANTEES, OR WARRANTIES, EXPRESS OR IMPLIED, RELATED TO THE EVALUATION BOARD INCLUDING, BUT NOT LIMITED TO, THE IMPLIED WARRANTY OF MERCHANTABILITY, TITLE, FITNESS FOR A PARTICULAR PURPOSE OR NONINFRINGEMENT OF INTELLECTUAL PROPERTY RIGHTS. IN NO EVENT WILL ADI AND ITS LICENSORS BE LIABLE FOR ANY INCIDENTAL, SPECIAL, INDIRECT , OR CONSEQUENTIAL DAMAGES RESUL TING FROM CUSTOMER’S POSSESSION OR USE OF THE EVALUATION BOARD, INCLUDING BUT NOT LIMITED TO LOST PROFITS, DELAY COSTS, LABOR COSTS OR LOSS OF GOODWILL. ADI’S TOTAL LIABILITY FROM ANY AND ALL CAUSES SHALL BE LIMITED TO THE AMOUNT OF ONE HUNDRED US DOLLARS ($100.00). EXPORT . Customer agrees that it will not directly or indirectly export the Evaluation Board to another country, and that it will comply with all applicable United States federal laws and regulations relating to exports. GOVERNING LAW . This Agreement shall be governed by and construed in accordance with the substantive laws of the Commonwealth of Massachusetts (excluding conflict of law rules). Any legal action regarding this Agreement will be heard in the state or federal courts having jurisdiction in Suffolk County, Massachusetts, and Customer hereby submits to the personal jurisdiction and venue of such courts. The United Nations Convention on Contracts for the International Sale of Goods shall not apply to this Agreement and is expressly disclaimed.。
SCALANCE XB004-2LD 产品说明书

3-pole terminal block
● product component / 1 / fusing at power supply input
Yes
● fuse protection type / 1 / at input for supply voltage
0.6 A / 60 V
type of voltage / 2 / of the supply voltage
design
Box
width
45 mm
6GK50042BF001AB2 Page 1/2
7/4/2023
Subject to change without notice © Copyright Siemens
height depth net weight fastening method
● 35 mm top hat DIN rail mounting ● wall mounting ● S7-1500 rail mounting product functions / management, configuration, engineering product function ● multiport mirroring ● CoS PROFINET conformity class product function / switch-managed product functions / redundancy product function ● Parallel Redundancy Protocol (PRP)/operation in the PRP-network ● Parallel Redundancy Protocol (PRP)/Redundant Network Access (RNA) standards, specifications, approvals reference code ● according to IEC 81346-2 ● according to IEC 81346-2:2019 standards, specifications, approvals / CE certificate of suitability / CE marking further information / internet links internet link ● to web page: selection aid TIA Selection Tool ● to website: Industrial communication ● to website: Industry Mall ● to website: Information and Download Center ● to website: Image database ● to website: CAx-Download-Manager ● to website: Industry Online Support security information security information
柔性检查作用域套件-USB 产品说明书
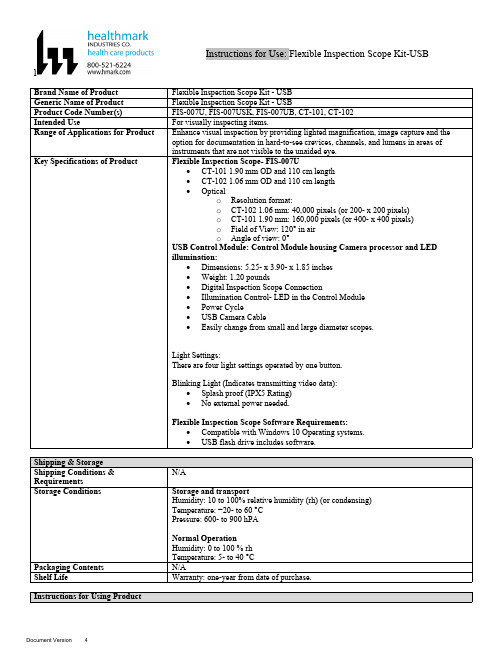
lInstructions for Use: Flexible Inspection Scope Kit-USB Brand Name of ProductFlexible Inspection Scope Kit - USB Generic Name of ProductFlexible Inspection Scope Kit - USB Product Code Number(s)FIS-007U, FIS-007USK, FIS-007UB, CT-101, CT-102Intended UseFor visually inspecting items.Range of Applications for ProductEnhance visual inspection by providing lighted magnification, image capture and the option for documentation in hard-to-see crevices, channels, and lumens in areas of instruments that are not visible to the unaided eye.Key Specifications of Product Flexible Inspection Scope- FIS-007U∙CT-101 1.90 mm OD and 110 cm length∙CT-102 1.06 mm OD and 110 cm length∙Opticalo Resolution format:o CT-102 1.06 mm: 40,000 pixels (or 200- x 200 pixels)o CT-101 1.90 mm: 160,000 pixels (or 400- x 400 pixels)o Field of View: 120° in airo Angle of view: 0°USB Control Module: Control Module housing Camera processor and LEDillumination:∙Dimensions: 5.25- x 3.90- x 1.85 inches∙Weight: 1.20 pounds ∙Digital Inspection Scope Connection∙Illumination Control- LED in the Control Module∙Power Cycle∙USB Camera Cable∙Easily change from small and large diameter scopes.Light Settings:There are four light settings operated by one button.Blinking Light (Indicates transmitting video data):∙Splash proof (IPX5 Rating)∙No external power needed.Flexible Inspection Scope Software Requirements:∙Compatible with Windows 10 Operating systems.∙USB flash drive includes software.Unpacking Flexible Inspection Scope:Carefully inspect for shipping damage. If there is any damage contact the shipping carrier and Heatlhmarkcustomer service 800-521-6224 immediately.USB Control Module: (Fig. 1).1.Digital Inspection Scope Connection 2.Illumination Control 3.Power Cycle B (Type C) on the right side of the boxFigure 1Flexible Inspection Scope™: (Fig. 2).∙CT-101 1.90 mm O.D. and 110 cm length ∙CT-102 1.06 mm O.D. and 110 cm lengthLarge1.90 mmSmall 1.06 mmFigure 2Flexible Inspection Scope™ Features3214Light/Illumination Settings: (Fig. 3).∙Five (5) light settingso Light on control indicats setting levelo Fifth setting is OFF∙Press light button to advance to next setting.∙Fifth setting turns the light OFF.Figure 3Power Cycle ButtonPress button to RESET camera (Fig. 4).Figure 41.Flexible Inspection Scope™ Plug (Fig. 5).Contains camera video connection as well as LED Light for illumination.1Figure 52.Flexible Working Length (Fig. 6).The portion of the Flexible Inspection Scope™ that is inserted into an item during visual inspection.The measuring scale markings on the Flexible Working Length are in centimeters (accuracy = ± 0.5 cm)2Figure 63.Distal Camera (Fig. 7).Distal portion of Flexible Inspection Scope™ that contains the camera lens3Figure 7SOFTWARE INSTALLATION:Note: This section is done only once when connecting the scope to the computer for the first time.∙System Requirements: MS Windows 10∙Install the Flexible Inspection Scope™ Software from the USB flash drive on a computer.Note: If you have any IT policies that may block this installation, please contact your IT team to give access to Healthmark scope viewer to install.1. Insert the USB Flash drive into your computer, and double click on the Healthmark Scope Viewer installer package to begin installation.2. The “Welcome to the Healthmark Scope Viewer Setup Wizard” screen pops up. Click on Next.3. Select the first tab Typical or setup type of your choice, click Next.4. Click Install and wait for installation to complete.5. Click Finish.STARTING SOFTWARE & CONNECTING SCOPE TO PC:(Fig 8).1.Open the Windows PC viewer software.2.Connect the Control Module to PC using USB Cable.3.Plug the Flexible Inspection Scope into the Control Module.4.In the viewer software, click Settings and Select USB Video Device, click on the desiredresolution, select the preferred Video Output Format, and then Click OK.5.Press the Power Cycle Button.Figure 86.Now you can start using the scope.Verifing OperationFollowing the steps listed below will ensure the proper use and performance of the Flexible Inspection Scope™. The Flexile Inspection Scope™ can be checked for normal operation by connecting it as described in the Startup section of this IFU.Normal operation includes:∙An image appearing on your computer monitor or HDMI Monitor.∙ A blinking light on Control Module near the Power Cycle button that indicates the image feed is transmitting.∙White light emitting from the distal end of the Digital Inspection Scope.∙An LED light on the control module top panel that indicates the light intensity of the device. Using SoftwareHealthmark Scope Viewer Software (Fig. 9).1.Capture button: Captures a Reference Image and saves it to the Reference Image folder.2.Main Image Window: Displays the image from the camera.3.Reference Image Window: Displays a reference image.4.Clear Button: Removes the image from the Reference image window.5.Open Reference Image button: Allows selection of a reference image from the Reference Imagefolder.6.Settings Button: Click to select the video camera and resolution settings.7.File Location Button: Click to change location where captured images are being saved.8.File Location Window: Shows the file path where captured images are being saved currently.9.Capture Image Button: Captures images and adds them to the File Location selected by the user(as shown in the File Location Window).10.Capture Video button: Click to record video. Click again to stop recording video.11.File Prefix: Type in text that you would like included in the file name of Captured Images.Figure 9Selecting Video Device or CameraFollow the directions below to select the video device or camera used to capture images using the Flexible Inspection Scope™ Viewer Software. (Fig. 10).1.Click Settings button in the lower left of the Scope Viewer software to display a list of videodevices or cameras being detected by your computer2.Select a device for capturing images using the Scope Viewera.The example below shows a webcam and USB Video Device in the Settings box. Select theUSB Video Device for the Flexible Inspection Scope™.b.You can also select your preferred Video Output Format from the dropdown box3.Click OK to view the selected Video Device.231Figure 10Capturing Still PicturesFollow the instructions for capturing still pictures from the Main Image Window.Select the Capture Image button. (Fig. 11).Figure 11Note: When an image is captured, “Image Captured” in red text will flash on the lower portion of the screen and a new file will appear in the Files Location.Capturing Video ImagesFollow the instructions below for capturing video from the Main Image Window.1.Select the Capture Video Button (Fig. 12).Figure 122.When the video is recording “Recording…” in red text will appear toward the bottom of thesoftware window.3.To stop recording, click Stop Capture. (Fig. 13).Figure 13Setting File PrefixFollowing the steps below allows you to create a file prefix that will appear after the underscore of image file names save to the File Location specified by the user.1.Click in the field next to File Prefix.2.Enter the characters that you would like to be included in the file name. (Fig 14).Figure 14Setting Location for Saved FilesFollowing the steps below allows you to set the file location of saved images using the Scope Viewer software.1.Click the File Location button.2.Select the file location you want to save captured images. (Fig 15).Figure 15Displaying Reference ImageThere are two ways to display a still image in the Reference Image Window on the Scope Viewer software.1.To display an image currently being displayed in the Main Image Window, click the Capture button. Note: The images will be saved in a file folder titled Reference Images in the designated File Location that the user specified in the File Location field. (Fig. 16).Figure 162.To display a saved image in the Reference Image Window from your File Location:a.Click the Open Reference Image button (Fig. 16 above).b.Select the file you want to display (Fig. 17 below).c.Click the OK Button, to display the image in the Reference Image Window. (Fig. 17).Figure 17Switching to a Different Flexible Inspection Scope™ on the Control Module:1.Press the Power button on the Control Module once.2.Disconnect the current Flexible Inspection Scope from the Control Module.3.Repeat the steps in the “STARTING SOFTWARE & CONNECTING SCOPE TO PC” procedure.Inserting Scope in ItemFigure 1Rotating Device to Avoid ObstacleFigure 2 Performing InspectionWipe down the Flexible Inspection Scope™ with a compatible wipe. Follow the manufacturer’s (Mfr.’s)Instructions for Use (IFU) for appropriate wipe usage. Click here to see the Chemical Compatibility Chart(PDF) for approved cleaning.The Flexible Inspection Scope™ is made of the same material as other common endoscopes. Any wipe,solution, or low temperature (≤ 60 °C [140 °F]) method intended for the reprocessing of endoscopes is likelycompatible with the Generation II Flexible Inspection Scope™ Catheters if used according to the productlabeling.Solutions Containing (Flexible Inspection Scope Only)Alcohol Ethoxylates Neutral or Near-Neutral pH DetergentsEnzymatic Cleaning Solutions Enzymatic DetergentsSodium Borated, Decahydrate Tetrapotassium PyrophosphateFlexible Inspection Scope™ has a fluid ingress protection rating of IPX7 (Waterproof) and can withstandimmersion in fluid up to one (1)-meter in depth for up to 30 minutes.Control Module USB has a fluid ingress protection rating of IPX5 (Water resistant) and can withstand asustained, low pressure water jet spray for up to three minutes.For Thorough Cleaning: CablesFollow the cleaning agent Mfr.’s IFU.1.Unplug and disconnect all components from the Control box prior to cleaning.2.Do not submerge or soak the cable for disinfection (cable is not waterproof).3.Wipe thoroughly with non-linting wipe moistened with facility approved neutral detergent. Use theappropriate brushes with detergent solution to remove any residues from areas that cannot bereached with the wipes.For Thorough Cleaning: Control Module1.Unplug and disconnect all components from the Control box prior to cleaning.2.Do not submerge or soak the cable for disinfection (Control Box is not waterproof).3.Wipe thoroughly with non-linting wipe moistened with facility approved neutral detergent. Use theappropriate brushes with detergent solution to remove any residues from areas that cannot bereached with the wipes.Note: Do NOT soak. Control Module and cables are not waterproof and should not be immersed.N/ACleaning –AutomatedDisinfection Control Module and CablesThese may be cleaned with alcohol based disinfectant wipes.Compatible agents (wipes and solutions) for disinfecting Flexible Inspection Scope™ and ControlModule:∙Hydrogen peroxide∙Isopropyl alcohol (IPA)∙Sodium hypochlorite (Bleach)∙Ortho-phenylphenol∙Quaternary ammonium.High-Level Disinfection (Flexible Inspection Scope™ Only)∙Select only disinfecting solutions listed in the compatible disinfecting methods.∙Follow all recommendations regarding health-hazards, dispensing, measuring, and storage from the Mfr. of cleaning and disinfecting agents.∙Soak the Flexible Inspection Scope™ in selected disinfecting solution per Mfr.’s IFU.∙Rinse the Flexible Inspection Scope™ with critical (sterile) water, again, following the disinfecting solutions Mfr.’s instructions.Reprocessing Chemical Compatibility Chart (PDF): Click here.。
1734-ob8(模块)

3
2 8
5 6 7
10 1
Description
Description
1
Mounting Base1
6
RTB Removal Handle
2 Mechanical Keying (oranal Block (RTB)1
3 Module Wiring Diagram
This equipment is considered Group 1, Class A industrial equipment according to IEC/CISPR Publication 11. Without appropriate precautions, there may be potential difficulties ensuring electromagnetic compatibility in other environments due to conducted as well as radiated disturbance. This equipment is supplied as "open type" equipment. It must be mounted within an enclosure that is suitably designed for those specific environmental conditions that will be present and appropriately designed to prevent personal injury resulting from accessibility to live parts. The interior of the enclosure must be accessible only by the use of a tool. Subsequent sections of this publication may contain additional information regarding specific enclosure type ratings that are required to comply with certain product safety certifications.
盛密科技7 SMART Sensor Module 传感器模块说明书
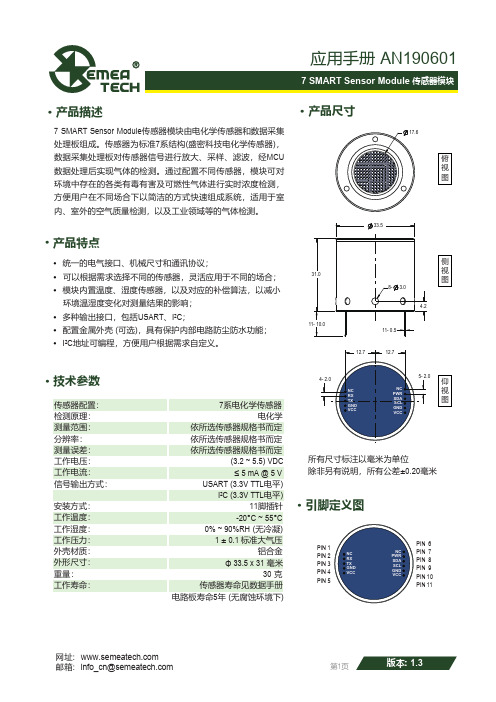
· 产品描述· 产品特点7 SMART Sensor Module 传感器模块由电化学传感器和数据采集处理板组成。
传感器为标准7系结构(盛密科技电化学传感器),数据采集处理板对传感器信号进行放大、采样、滤波,经MCU数据处理后实现气体的检测。
通过配置不同传感器,模块可对环境中存在的各类有毒有害及可燃性气体进行实时浓度检测,方便用户在不同场合下以简洁的方式快速组成系统,适用于室内、室外的空气质量检测,以及工业领域等的气体检测。
· 统一的电气接口、机械尺寸和通讯协议;· 可以根据需求选择不同的传感器,灵活应用于不同的场合;· 模块内置温度、湿度传感器,以及对应的补偿算法,以减小 环境温湿度变化对测量结果的影响;· 多种输出接口,包括USART 、I²C ;· 配置金属外壳 (可选),具有保护内部电路防尘防水功能;· I²C 地址可编程,方便用户根据需求自定义。
· 技术参数传感器配置:检测原理:测量范围:分辨率:电化学7系电化学传感器测量误差:依所选传感器规格书而定依所选传感器规格书而定依所选传感器规格书而定工作电压:工作电流:信号输出方式:USART (3.3V TTL 电平)(3.2 ~ 5.5) VDC≤ 5 mA @ 5 VI²C (3.3V TTL 电平)安装方式:工作温度:工作湿度:0% ~ 90%RH (无冷凝)11脚插针工作压力:-20°C ~ 55°C1 ± 0.1 标准大气压外壳材质:外形尺寸:重量:30 克铝合金工作寿命:Φ 33.5 x 31 毫米传感器寿命见数据手册电路板寿命5年 (无腐蚀环境下)产品尺寸·引脚定义图·PIN 1PIN 2PIN 3PIN 4PIN 5PIN PIN PIN PIN 6789PIN 10PIN 11所有尺寸标注以毫米为单位除非另有说明,所有公差±0.20毫米俯视图侧视图仰视图·USART 通信协议· 引脚定义5746321NC RX TX GND VCC NC PWR 预留针脚 (悬空)串口输入RX 串口输出TX 电源地电源 (3.2 ~ 5.5 V )预留针脚 (悬空)模块电源使能 (低电平关闭,高电平开启,内置上拉电阻) 默认上拉高电平911810SDA SCL GND VCCI²C 信号SDA (内置10kΩ上拉电阻) 默认上拉高电平I²C 信号SCL (内置10kΩ上拉电阻) 默认上拉高电平电源地电源 (3.2 ~ 5.5 V )注: 两个VCC 信号内部连通1. 串行通信参数起始位:1; 数据位:8; 停止位:1; 校验位:无; 波特率:115200 bps无特殊说明时,应答回复时间小于100ms (特殊情况请参考具体指令说明),当前命令回复前无法响应其他指令2. 帧格式 (每一通信帧的格式如下)首字节设备码功能码起始地址数据长度数据校验位(高位在前)H ID F A N D CRC16H :数据头,1Byte 固定为0x3AID :设备码,1Byte 默认为0x10,可由用户自定义F :功能码,1Byte ,例如(0x03)A :起始地址,2Bytes ,例如0x0001N :数据长度,1Byte ,以2个字节为单位,例如(0x02: 4字节)D :数据,N*2Bytes ,高位在前,例如(MSB LSB )定义为有符号短整型(signed short )CRC16:数据校验,2Bytes ,使用MODBUS_CRC16校验算法(算法详见附录1)3. 指令说明3.1 读取传感器类型上位机发送请求0x3A 0x100x010x00000x010x00000x82B0首字节设备码功能码起始地址数据长度数据校验位例:3A 10 01 00 00 01 00 00 82 B0模块接收正确数据应答首字节设备码功能码数据校验位0x3A0x100x01D(1byte数据)CRC16传感器类型代码 (十进制):0,1:无定义 2:CO 3:O2 4:H2 5:CH4 6:无 7:CO2 8:O3 9:H2S 10:SO2 11:NH3 12:CL2 13:ETO 14:HCL 15:PH3 16:无 17:HCN 18:无 19:HF 20:无21:NO 22:NO2 23:NOX 24:CLO2 25:无 26:无 27:无 28:无 29: 无 30:无31:THT 32:C2H2 33:C2H4 34:CH2O 35:无 36:无 37:无 38:无 39: CH3SH 40:C2H3CL 例:3A 10 01 0F 4C AD(十六进制0F=十进制15,即得到该传感器为PH3传感器)3.2 读取传感器数据 (单位为μg/m³)上位机发送请求首字节设备码功能码起始地址数据长度数据校验位0x3A0x100x030x00000x020x00000x7352例:3A 10 03 00 00 02 00 00 73 52模块接收正确数据应答首字节设备码功能码起始地址数据长度数据校验位0x3A0x100x030x00000x02D CRC16 D:接收到的数据,4Bytes 高位在前例:3A 10 03 00 00 02 00 00 00 5E 25 35 (D=0x0000005E=94, 得到传感器值为94μg/m³)3.3 读取传感器数据 (单位为ppb)上位机发送请求首字节设备码功能码起始地址数据长度数据校验位0x3A0x100x030x00020x020x00000x72EA 例:3A 10 03 00 02 02 00 00 72 EA模块接收正确数据应答首字节设备码功能码起始地址数据长度数据校验位0x3A0x100x030x00020x02D CRC16 D:接收到的数据,4Bytes 高位在前例:3A 10 03 00 02 02 00 00 00 4C A4 DA (D=0x0000004C=76, 得到传感器值为76ppb)备注:读取数据显示精度为1ppb,具体测试精度根据传感器不同而不同3.4 读取温度传感器数据 (单位为°C)上位机发送请求首字节设备码功能码起始地址数据长度数据校验位0x3A0x100x030x00040x010x00000x8262例:3A 10 03 00 04 01 00 00 82 62模块接收正确数据应答首字节设备码功能码起始地址数据长度数据校验位0x3A0x100x030x00040x01D CRC16 D:接收到的数据,2 Bytes 高位在前,除以100后得到温度值。
SIMATIC S7-1500F CPU 1516F-3 PN DP 产品数据手册说明书
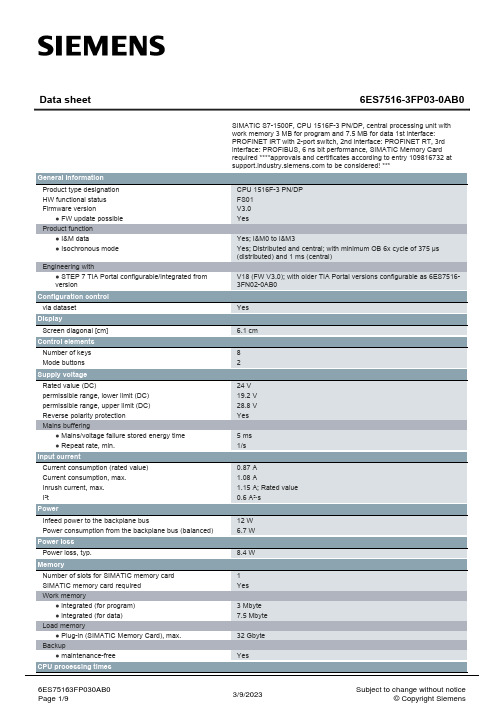
6.1 cm
8 2
24 V 19.2 V 28.8 V Yes
5 ms 1/s
0.87 A 1.08 A 1.15 A; Rated value 0.6 A²·s
12 W 6.7 W
8.4 W
1 Yes
3 Mbyte 7.5 Mbyte
32 Gbyte
Yes
6ES75163FP030AB0 Page 1/9
0 ... 65 535 1 Mbyte
0 ... 65 535 1 Mbyte
1 Mbyte 100 20 20 20; With minimum OB 3x cycle of 250 µs 50 3 3 2 100 4 2 1
24; Up to 8 possible for F-blocks
2 048
CPU 1516F-3 PN/DP FS01 V3.0 Yes
Yes; I&M0 to I&M3 Yes; Distributed and central; with minimum OB 6x cycle of 375 µs (distributed) and 1 ms (central)
V18 (FW V3.0); with older TIA Portal versions configurable as 6ES75163FN02-0AB0
3/9/2023
Subject to change without notice © Copyright Siemens
for bit operations, typ. for word operations, typ. for fixed point arithmetic, typ. for floating point arithmetic, typ. CPU-blocks Number of elements (total) DB
诺基亚 SCALANCE X204-2 Managed IE 交换机数据手册说明书
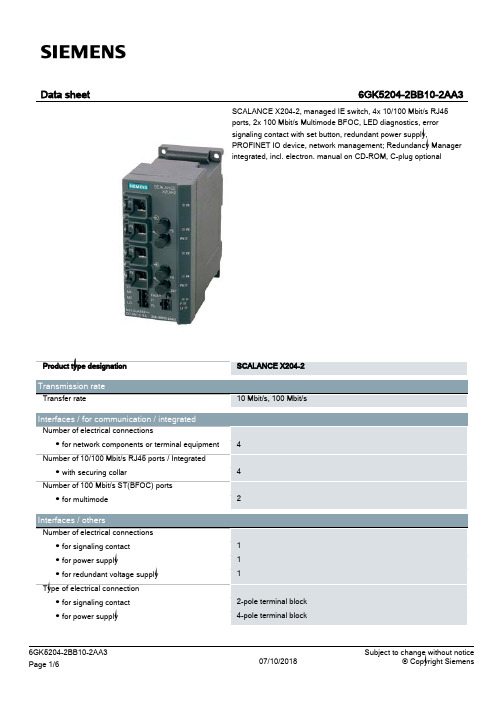
Product type designation
Transmission rate Transfer rate
Interfaces / for communication / integrated Number of electrical connections ● for network components or terminal equipment Number of 10/100 Mbit/s RJ45 ports / Integrated ● with securing collar Number of 100 Mbit/s ST(BFOC) ports ● for multimode
Interfaces / others Number of electrical connections ● for signaling contact ● for power supply ● for redundant voltage supply Type of electrical connection ● for signaling contact ● for power supply
SCALANCE X204-2 10 Mbit/s, 100 Mbit/s
4 4 2
1 1 1 2-pole terminal block 4-pole terminal block
6GK5204-2BB10-2AA3 Page 1/6
07/10/2018
Subject to change without notice © Copyright Siemens
● SICLOCK support
Yes
Protocol / is supported
● NTP
NXP SCM-i.MX 6 Series Yocto Linux 用户指南说明书
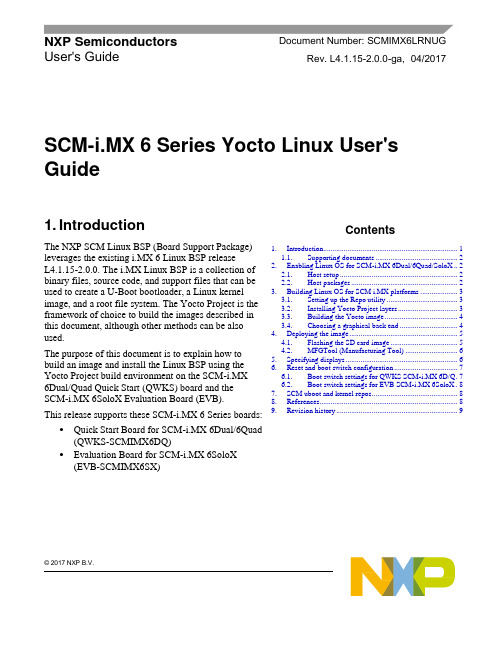
© 2017 NXP B.V.SCM-i.MX 6 Series Yocto Linux User'sGuide1. IntroductionThe NXP SCM Linux BSP (Board Support Package) leverages the existing i.MX 6 Linux BSP release L4.1.15-2.0.0. The i.MX Linux BSP is a collection of binary files, source code, and support files that can be used to create a U-Boot bootloader, a Linux kernel image, and a root file system. The Yocto Project is the framework of choice to build the images described in this document, although other methods can be also used.The purpose of this document is to explain how to build an image and install the Linux BSP using the Yocto Project build environment on the SCM-i.MX 6Dual/Quad Quick Start (QWKS) board and the SCM-i.MX 6SoloX Evaluation Board (EVB). This release supports these SCM-i.MX 6 Series boards:• Quick Start Board for SCM-i.MX 6Dual/6Quad (QWKS-SCMIMX6DQ)• Evaluation Board for SCM-i.MX 6SoloX (EVB-SCMIMX6SX)NXP Semiconductors Document Number: SCMIMX6LRNUGUser's GuideRev. L4.1.15-2.0.0-ga , 04/2017Contents1. Introduction........................................................................ 1 1.1. Supporting documents ............................................ 22. Enabling Linux OS for SCM-i.MX 6Dual/6Quad/SoloX .. 2 2.1. Host setup ............................................................... 2 2.2. Host packages ......................................................... 23.Building Linux OS for SCM i.MX platforms .................... 3 3.1. Setting up the Repo utility ...................................... 3 3.2. Installing Yocto Project layers ................................ 3 3.3. Building the Yocto image ....................................... 4 3.4. Choosing a graphical back end ............................... 4 4. Deploying the image .......................................................... 5 4.1. Flashing the SD card image .................................... 5 4.2. MFGTool (Manufacturing Tool) ............................ 6 5. Specifying displays ............................................................ 6 6. Reset and boot switch configuration .................................. 7 6.1. Boot switch settings for QWKS SCM-i.MX 6D/Q . 7 6.2. Boot switch settings for EVB SCM-i.MX 6SoloX . 8 7. SCM uboot and kernel repos .............................................. 8 8. References.......................................................................... 8 9.Revision history (9)Enabling Linux OS for SCM-i.MX 6Dual/6Quad/SoloX1.1. Supporting documentsThese documents provide additional information and can be found at the NXP webpage (L4.1.15-2.0.0_LINUX_DOCS):•i.MX Linux® Release Notes—Provides the release information.•i.MX Linux® User's Guide—Contains the information on installing the U-Boot and Linux OS and using the i.MX-specific features.•i.MX Yocto Project User's Guide—Contains the instructions for setting up and building the Linux OS in the Yocto Project.•i.MX Linux®Reference Manual—Contains the information about the Linux drivers for i.MX.•i.MX BSP Porting Guide—Contains the instructions to port the BSP to a new board.These quick start guides contain basic information about the board and its setup:•QWKS board for SCM-i.MX 6D/Q Quick Start Guide•Evaluation board for SCM-i.MX 6SoloX Quick Start Guide2. Enabling Linux OS for SCM-i.MX 6Dual/6Quad/SoloXThis section describes how to obtain the SCM-related build environment for Yocto. This assumes that you are familiar with the standard i.MX Yocto Linux OS BSP environment and build process. If you are not familiar with this process, see the NXP Yocto Project User’s Guide (available at L4.1.15-2.0.0_LINUX_DOCS).2.1. Host setupTo get the Yocto Project expected behavior on a Linux OS host machine, install the packages and utilities described below. The hard disk space required on the host machine is an important consideration. For example, when building on a machine running Ubuntu, the minimum hard disk space required is about 50 GB for the X11 backend. It is recommended that at least 120 GB is provided, which is enough to compile any backend.The minimum recommended Ubuntu version is 14.04, but the builds for dizzy work on 12.04 (or later). Earlier versions may cause the Yocto Project build setup to fail, because it requires python versions only available on Ubuntu 12.04 (or later). See the Yocto Project reference manual for more information.2.2. Host packagesThe Yocto Project build requires that the packages documented under the Yocto Project are installed for the build. Visit the Yocto Project Quick Start at /docs/current/yocto-project-qs/yocto-project-qs.html and check for the packages that must be installed on your build machine.The essential Yocto Project host packages are:$ sudo apt-get install gawk wget git-core diffstat unzip texinfo gcc-multilib build-essential chrpath socat libsdl1.2-devThe i.MX layers’ host packages for the Ubuntu 12.04 (or 14.04) host setup are:$ sudo apt-get install libsdl1.2-dev xterm sed cvs subversion coreutils texi2html docbook-utils python-pysqlite2 help2man make gcc g++ desktop-file-utils libgl1-mesa-dev libglu1-mesa-dev mercurial autoconf automake groff curl lzop asciidocThe i.MX layers’ host packages for the Ubuntu 12.04 host setup are:$ sudo apt-get install uboot-mkimageThe i.MX layers’ host packages for the Ubuntu 14.04 host s etup are:$ sudo apt-get install u-boot-toolsThe configuration tool uses the default version of grep that is on your build machine. If there is a different version of grep in your path, it may cause the builds to fail. One workaround is to rename the special versi on to something not containing “grep”.3. Building Linux OS for SCM i.MX platforms3.1. Setting up the Repo utilityRepo is a tool built on top of GIT, which makes it easier to manage projects that contain multiple repositories that do not have to be on the same server. Repo complements the layered nature of the Yocto Project very well, making it easier for customers to add their own layers to the BSP.To install the Repo utility, perform these steps:1.Create a bin folder in the home directory.$ mkdir ~/bin (this step may not be needed if the bin folder already exists)$ curl /git-repo-downloads/repo > ~/bin/repo$ chmod a+x ~/bin/repo2.Add this line to the .bashrc file to ensure that the ~/bin folder is in your PATH variable:$ export PATH=~/bin:$PATH3.2. Installing Yocto Project layersAll the SCM-related changes are collected in the new meta-nxp-imx-scm layer, which is obtained through the Repo sync pointing to the corresponding scm-imx branch.Make sure that GIT is set up properly with these commands:$ git config --global "Your Name"$ git config --global user.email "Your Email"$ git config --listThe NXP Yocto Project BSP Release directory contains the sources directory, which contains the recipes used to build, one (or more) build directories, and a set of scripts used to set up the environment. The recipes used to build the project come from both the community and NXP. The Yocto Project layers are downloaded to the sources directory. This sets up the recipes that are used to build the project. The following code snippets show how to set up the SCM L4.1.15-2.0.0_ga Yocto environment for the SCM-i.MX 6 QWKS board and the evaluation board. In this example, a directory called fsl-arm-yocto-bsp is created for the project. Any name can be used instead of this.Building Linux OS for SCM i.MX platforms3.2.1. SCM-i.MX 6D/Q quick start board$ mkdir fsl-arm-yocto-bsp$ cd fsl-arm-yocto-bsp$ repo init -u git:///imx/fsl-arm-yocto-bsp.git -b imx-4.1-krogoth -m scm-imx-4.1.15-2.0.0.xml$ repo sync3.2.2. SCM-i.MX 6SoloX evaluation board$ mkdir my-evb_6sxscm-yocto-bsp$ cd my-evb_6sxscm-yocto-bsp$ repo init -u git:///imx/fsl-arm-yocto-bsp.git -b imx-4.1-krogoth -m scm-imx-4.1.15-2.0.0.xml$ repo sync3.3. Building the Yocto imageNote that the quick start board for SCM-i.MX 6D/Q and the evaluation board for SCM-i.MX 6SoloX are commercially available with a 1 GB LPDDR2 PoP memory configuration.This release supports the imx6dqscm-1gb-qwks, imx6dqscm-1gb-qwks-rev3, and imx6sxscm-1gb-evb. Set the machine configuration in MACHINE= in the following section.3.3.1. Choosing a machineChoose the machine configuration that matches your reference board.•imx6dqscm-1gb-qwks (QWKS board for SCM-i.MX 6DQ with 1 GB LPDDR2 PoP)•imx6dqscm-1gb-qwks-rev3 (QWKS board Rev C for SCM-i.MX 6DQ with 1GB LPDDR2 PoP) •imx6sxscm-1gb-evb (EVB for SCM-i.MX 6SX with 1 GB LPDDR2 PoP)3.4. Choosing a graphical back endBefore the setup, choose a graphical back end. The default is X11.Choose one of these graphical back ends:•X11•Wayland: using the Weston compositor•XWayland•FrameBufferSpecify the machine configuration for each graphical back end.The following are examples of building the Yocto image for each back end using the QWKS board for SCM-i.MX 6D/Q and the evaluation board for SCM-i.MX 6SoloX. Do not forget to replace the machine configuration with what matches your reference board.3.4.1. X11 image on QWKS board Rev C for SCM-i.MX 6D/Q$ DISTRO=fsl-imx-x11 imx6dqscm-1gb-qwks-rev3 source fsl-setup-release.sh -b build-x11$ bitbake fsl-image-gui3.4.2. FrameBuffer image on evaluation board for SCM-i.MX 6SX$ DISTRO=fsl-imx-fb MACHINE=imx6sxscm-1gb-evb source fsl-setup-release.sh –b build-fb-evb_6sxscm$ bitbake fsl-image-qt53.4.3. XWayland image on QWKS board for SCM-i.MX 6D/Q$ DISTRO=fsl-imx-xwayland MACHINE=imx6dqscm-1gb-qwks source fsl-setup-release.sh –b build-xwayland$ bitbake fsl-image-gui3.4.4. Wayland image on QWKS board for SCM-i.MX 6D/Q$ DISTRO=fsl-imx-wayland MACHINE=imx6dqscm-1gb-qwks source fsl-setup-release.sh -b build-wayland$ bitbake fsl-image-qt5The fsl-setup-release script installs the meta-fsl-bsp-release layer and configures theDISTRO_FEATURES required to choose the graphical back end. The –b parameter specifies the build directory target. In this build directory, the conf directory that contains the local.conf file is created from the setup where the MACHINE and DISTRO_FEATURES are set. The meta-fslbsp-release layer is added into the bblayer.conf file in the conf directory under the build directory specified by the –e parameter.4. Deploying the imageAfter the build is complete, the created image resides in the <build directory>/tmp/deploy/images directory. The image is (for the most part) specific to the machine set in the environment setup. Each image build creates the U-Boot, kernel, and image type based on the IMAGE_FSTYPES defined in the machine configuration file. Most machine configurations provide the SD card image (.sdcard), ext4, and tar.bz2. The ext4 is the root file system only. The .sdcard image contains the U-Boot, kernel, and rootfs, completely set up for use on an SD card.4.1. Flashing the SD card imageThe SD card image provides the full system to boot with the U-Boot and kernel. To flash the SD card image, run this command:$ sudo dd if=<image name>.sdcard of=/dev/sd<partition> bs=1M && syncFor more information about flashing, see “P reparing an SD/MMC Card to Boot” in the i.MX Linux User's Guide (document IMXLUG).Specifying displays4.2. MFGTool (Manufacturing Tool)MFGTool is one of the ways to place the image on a device. To download the manufacturing tool for the SCM-i.MX 6D/Q and for details on how to use it, download the SCM-i.MX 6 Manufacturing Toolkit for Linux 4.1.15-2.0.0 under the "Downloads" tab from /qwks-scm-imx6dq. Similarly, download the manufacturing tool for the SCM-i.MX 6SoloX evaluation board under the "Downloads" tab from /evb-scm-imx6sx.5. Specifying displaysSpecify the display information on the Linux OS boot command line. It is not dependent on the source of the Linux OS image. If nothing is specified for the display, the settings in the device tree are used. Find the specific parameters in the i.MX 6 Release Notes L4.1.15-2.0.0 (available at L4.1.15-2.0.0_LINUX_DOCS). The examples are shown in the following subsections. Interrupt the auto-boot and enter the following commands.5.1.1. Display options for QWKS board for SCM-i.MX 6D/QHDMI displayU-Boot > setenv mmcargs 'setenv bootargs console=${console},${baudrate} ${smp}root=${mmcroot} video=mxcfb0:dev=hdmi,1920x1080M@60,if=RGB24'U-Boot > run bootcmd5.1.2. Display options for EVB for SCM-i.MX 6SXNote that the SCM-i.MX 6SX EVB supports HDMI with a HDMI accessory card (MCIMXHDMICARD) that plugs into the LCD connector on the EVB.Accessory boards:•The LVDS connector pairs with the NXP MCIMX-LVDS1 LCD display board.•The LCD expansion connector (parallel, 24-bit) pairs with the NXP MCIMXHDMICARD adapter board.LVDS displayU-Boot > setenv mmcargs 'setenv bootargs console=${console},${baudrate} ${smp}root=${mmcroot} ${dmfc} video=mxcfb0:dev=ldb,1024x768M@60,if=RGB666 ldb=sep0'U-Boot > run bootcmdHDMI display (dual display for the HDMI as primary and the LVDS as secondary)U-Boot > setenv mmcargs 'setenv bootargs console=${console},${baudrate} ${smp}root=${mmcroot} video=mxcfb0:dev=hdmi,1920x1080M@60,if=RGB24video=mxcfb1:dev=ldb,LDBXGA,if=RGB666'U-Boot > run bootcmdLCD displayu-boot > setenv mmcargs 'setenv bootargs ${bootargs}root=${mmcroot} rootwait rw video=mxcfb0:dev=lcd,if=RGB565'u-boot> run bootcmd6. Reset and boot switch configuration6.1. Boot switch settings for QWKS SCM-i.MX 6D/QThere are two push-button switches on the QWKS-SCMIMX6DQ board. SW1 (SW3 for QWKS board Rev B) is the system reset that resets the PMIC. SW2 is the i.MX 6Dual/6Quad on/off button that is needed for Android.There are three boot options. The board can boot either from the internal SPI-NOR flash inside the SCM-i.MX6Dual/6Quad or from either of the two SD card slots. The following table shows the switch settings for the boot options.Table 1.Boot configuration switch settingsBoot from top SD slot (SD3)Boot from bottom SD slot (SD2)Boot from internal SPI NORDefault1.References6.2. Boot switch settings for EVB SCM-i.MX 6SoloXThis table shows the jumper configuration to boot the evaluation board from the SD card slot SD3.7. SCM uboot and kernel repositoriesThe kernel and uboot patches for both SCM-i.MX 6 QWKS board and evaluation board are integrated in specific git repositories. Below are the git repos for SCM-i.MX 6 uboot and kernel:uBoot repo: /git/cgit.cgi/imx/uboot-imx.gitSCM Branch: scm-imx_v2016.03_4.1.15_2.0.0_gakernel repo: /git/cgit.cgi/imx/linux-imx.gitSCM branch: scm-imx_4.1.15_2.0.0_ga8. References1.For details about setting up the Host and Yocto Project, see the NXP Yocto Project User’s Guide(document IMXLXYOCTOUG).2.For information about downloading images using U-Boot, see “Downloading images usingU-Boot” in the i.MX Linux User's Guide (document IMXLUG).3.For information about setting up the SD/MMC card, see “P reparing an SD/MMC card to boot” inthe i.MX Linux User's Guide (document IMXLUG).9. Revision historyDocument Number: SCMIMX6LRNUGRev. L4.1.15-2.0.0-ga04/2017How to Reach Us: Home Page: Web Support: /supportInformation in this document is provided solely to enable system and softwareimplementers to use NXP products. There are no express or implied copyright licenses granted hereunder to design or fabricate any integrated circuits based on the information in this document. NXP reserves the right to make changes without further notice to any products herein.NXP makes no warranty, representation, or guarantee regarding the suitability of its products for any particular purpose, nor does NXP assume any liability arising out of the application or use of any product or circuit, and specifically disclaims any and all liability, including without limitation consequentia l or incidental damages. “Typical”parameters that may be provided in NXP data sheets and/or specifications can and do vary in different applications, and actual performance may vary over time. All operating parameters, including “typicals,” must be valida ted for each customer application by customer’s technical experts. NXP does not convey any license under its patent rights nor the rights of others. NXP sells products pursuant to standard terms and conditions of sale, which can be found at the following address: /SalesTermsandConditions .NXP, the NXP logo, NXP SECURE CONNECTIONS FOR A SMARTER WORLD, Freescale, and the Freescale logo are trademarks of NXP B.V. All other product or service names are the property of their respective owners.ARM, the ARM Powered logo, and Cortex are registered trademarks of ARM Limited (or its subsidiaries) in the EU and/or elsewhere. All rights reserved. © 2017 NXP B.V.。
诺帝菲尔 FSB-200产品说明书
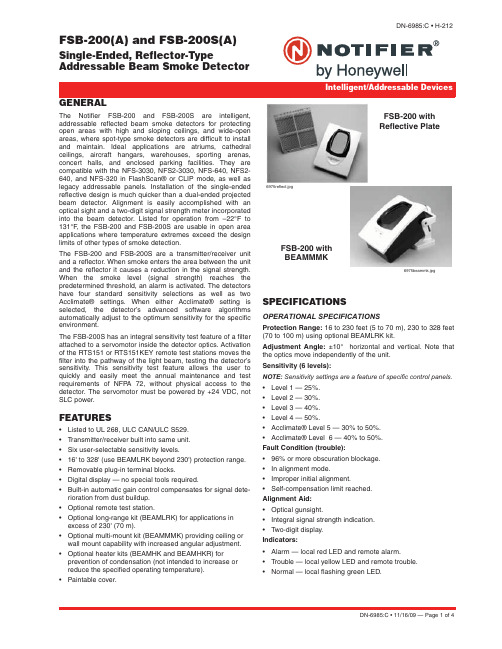
FSB-200(A) and FSB-200S(A)Single-Ended, Reflector-TypeAddressable Beam Smoke DetectorDN-6985:C • H-212GENERALThe Notifier FSB-200 and FSB-200S are intelligent,addressable reflected beam smoke detectors for protectingopen areas with high and sloping ceilings, and wide-openareas, where spot-type smoke detectors are difficult to installand maintain. Ideal applications are atriums, cathedralceilings, aircraft hangars, warehouses, sporting arenas,concert halls, and enclosed parking facilities. They arecompatible with the NFS-3030, NFS2-3030, NFS-640, NFS2-640, and NFS-320 in FlashScan® or CLIP mode, as well aslegacy addressable panels. Installation of the single-endedreflective design is much quicker than a dual-ended projectedbeam detector. Alignment is easily accomplished with anoptical sight and a two-digit signal strength meter incorporatedinto the beam detector. Listed for operation from –22°F to131°F, the FSB-200 and FSB-200S are usable in open areaapplications where temperature extremes exceed the designlimits of other types of smoke detection.The FSB-200 and FSB-200S are a transmitter/receiver unitand a reflector. When smoke enters the area between the unitand the reflector it causes a reduction in the signal strength.When the smoke level (signal strength) reaches thepredetermined threshold, an alarm is activated. The detectorshave four standard sensitivity selections as well as twoAcclimate® settings. When either Acclimate® setting is selected, the detector’s advanced software algorithms automatically adjust to the optimum sensitivity for the specific environment.The FSB-200S has an integral sensitivity test feature of a filter attached to a servomotor inside the detector optics. Activation of the RTS151 or RTS151KEY remote test stations moves the filter into the pathway of the light beam, testing the detector’s sensitivity. This sensitivity test feature allows the user to quickly and easily meet the annual maintenance and test requirements of NFP A 72, without physical access to the detector. The servomotor must be powered by +24 VDC, not SLC power.FEATURES•Listed to UL 268, ULC CAN/ULC S529.•T ransmitter/receiver built into same unit.•Six user-selectable sensitivity levels.•16' to 328' (use BEAMLRK beyond 230') protection range.•Removable plug-in terminal blocks.•Digital display — no special tools required.•Built-in automatic gain control compensates for signal dete-rioration from dust buildup.•Optional remote test station.•Optional long-range kit (BEAMLRK) for applications in excess of 230' (70 m).•Optional multi-mount kit (BEAMMMK) providing ceiling or wall mount capability with increased angular adjustment.•Optional heater kits (BEAMHK and BEAMHKR) for prevention of condensation (not intended to increase orreduce the specified operating temperature).•Paintable cover.SPECIFICATIONSOPERATIONAL SPECIFICATIONSProtection Range: 16 to 230 feet (5 to 70 m), 230 to 328 feet (70 to 100 m) using optional BEAMLRK kit.Adjustment Angle: ±10° horizontal and vertical. Note that the optics move independently of the unit.Sensitivity (6 levels):NOTE: Sensitivity settings are a feature of specific control panels.•Level 1 — 25%.•Level 2 — 30%.•Level 3 — 40%.•Level 4 — 50%.•Acclimate® Level 5 — 30% to 50%.•Acclimate® Level 6 — 40% to 50%.Fault Condition (trouble):•96% or more obscuration blockage.•In alignment mode.•Improper initial alignment.•Self-compensation limit reached.Alignment Aid:•Optical gunsight.•Integral signal strength indication.•Two-digit display.Indicators:•Alarm — local red LED and remote alarm.•Trouble — local yellow LED and remote trouble.•Normal — local flashing green LED.FSB-200 withReflective PlateFSB-200 withBEAMMMK6975reflect.jpg6975beammk.jpgTest/reset features:•Integral sensitivity test filter (FSB-200S only, requires external power supply).•Sensitivity filter (incremental scale on reflector).•Local alarm test switch.•Local alarm reset switch.•Remote test and reset switch (compatible with RTS151 and RTS151KEY test stations).Smoke Detector Spacing: On smooth ceilings, 30 – 60 feet (9.1 to 18.3 m) between projected beams and not more than one-half that spacing between a projected beam and a sidewall. Other spacing may be used depending on ceiling height, airflow characteristics, and response requirements. See NFPA 72.ENVIRONMENTAL SPECIFICATIONS Temperature: –22°F to 131°F (–30°C to 55°C).Humidity: 10 – 93% RH noncondensing.ELECTRICAL SPECIFICATIONS •Voltage: 15 to 32 VDC.•Average Standby Current (24 VDC): 2 mA maximum (LED flashing, SLC @ 24 V).•Alarm Current (LED on): 8.5 mA maximum.•Trouble Current (LED on): 4.5 mA maximum.•Alignment Current: 20 mA maximum.•External Supply (FSB-200S only):Voltage — 15 to 32 VDCCurrent — 0.5 A maximum.•Remote Output (Alarm):Voltage - 15 to 32 VDC (Output voltage same as deviceinput voltage)Current - 15 mA maximum, 6 mA minimum (Output current is limited by 2.2K ohm resistor)•Heater Kit BEAMHK:Voltage - 15 to 32 V; Current - 92 mA maximum @ 32 V (heater only); Power Consumption -nominal 1.6 W @ 24 V, maximum 3.0 W @ 32 V.•Reflector Heater Kit BEAMHKR:Voltage - 15 to 32 V;Current - 450 mA maximum @ 32 V (per reflector); Power Consumption (per reflector) - nominal 7.7 W @ 24 V,maximum 15.0 W @ 32 V.MECHANICAL SPECIFICATIONSShipping Weight: 3.7 lbs (1.68 kg)Detector Dimensions: 10.0" H x 7.5" W x 3.3" D (254 mm H x 191 mm W x 84 mm D).Reflector Dimensions for 16' to 230' (5 to 70m) Applications: 7.9" x 9.1" (200 x 230 mm).Reflector Dimensions for Applications Beyond 230'/70m: 15.7" x 18.1" (400 x 460 mm).SENSITIVITY SELECTIONThe detector has six sensitivity selections (sensitivity settings are a feature of specific control panels). Each of these selections is only acceptable over a specific distance separation between the detector and the reflector per UL 268. The chart below determines which selections are acceptable for your installed distance. The sensitivity of the detector can be set only when the housing is removed and the detector is not in the fine adjustment step of the alignment mode, indicated by the illumination of the dual digital display. T o set the sensitivity, depress the sensitivity button one time. See Switch Locations diagram. Once the switch is pressed, the digital display will illuminate and read the current sensitivity setting in percent obscuration. To change the sensitivity, continue to depress the sensitivity switch until the desired setting is achieved. The digital display will turn off automatically if no further switch presses occur.In addition to the four standard sensitivity selections, the detector has two Acclimate® settings. When either Acclimate®setting is chosen the detector will automatically adjust its sensitivity using advanced software algorithms to select the optimum sensitivity for the environment. The sensitivity will be continuously adjusted within the ranges specified in the chart above.Total obscuration can be converted to percent per foot, assuming uniform smoke density for the entire length of the beam. The chart below converts total obscuration percent per foot for all acceptable sensitivity settings.SensitivitySettingPercentObscurationDisplayReadingAcceptableDISTANCEbetweenDetectorandReflector(ft)AcceptableDISTANCEbetweenDetectorandReflector(m) Level 125%2516.4 to 120 5.0 to 36.6 Level 230%3025 to 1507.6 to 45.7 Level 340%4060 to 22018.3 to 67 Level 450%5080 to 32824.4 to 100 Acclimate ®Level 130% to 50%A180 to 15024.4 to 45.7 Acclimate ®Level 240% to 50%A280 to 20024.4 to 67Table 1: Total ObscurationWiring Diagram with RTS151/KEYWiring Diagram6985graph.tif6985wirerts151.tif Alignment and Adjustment Locations6985adjloc.tif Housing Screw Locations6985screwlocs.tifPARTS LISTItem QuantityT ransmitter/Receiver Unit 1Paintable Trim Ring 1Reflector 1Plug-In Terminal Blocks 3Isolator Shunts 2Instruction Manual 1Orange Sticky Paper 1FSB-200/FSB-200SSee RTS151/KEY Installation Instructionsfor electrical ratings of the RTS151/KEYRTS151/KEYPin 1Pin 2Pin 4Pin 3Pin 5Remote Alarm OutAUX (-)Reset InputTest InputSee electricalratings.or Previousdevice.32 VDC MaximumTwisted pair isrecommendedDeviceAcclimate® Plus™ is a trademark of Honeywell International Inc.©2009 by Honeywell International Inc. All rights reserved. Unauthorized use of this document is strictly prohibited.This document is not intended to be used for installation purposes. We try to keep our product information up-to-date and accurate. We cannot cover all specific applications or anticipate all requirements.All specifications are subject to change without notice.For more information, contact Notifier. Phone: (203) 484-7161, FAX: (203) 484-7118.AGENCY LISTINGS AND APPROVALSThese listings and approvals apply to the devices specified in this document. In some cases, certain modules or applications may not be listed by certain approval agencies, or listing may be in process. Consult factory for latest listing status.•UL Listed: S2522 (FSB-200, FSB-200S)•ULC Listed: S2522 (FSB-200A, FSB-200SA)•CSFM: 7260-0028:228•MEA: 95-04-E•Maryland State Fire Marshal: Permit # 2167•FM ApprovedPRODUCT LINE INFORMATIONFSB-200: Intelligent beam smoke detector FSB-200A:Same as FSB-200 with ULC Listing.FSB-200S:Intelligent beam smoke detector with integral sen-sitivity test.FSB-200SA: Same as FSB-200S with ULC Listing.BEAMLRK: Long range accessory kit (required for applica-tions in excess of 230 ft/70 m).BEAMMMK:Multi-mount kit (provides ceiling or wall mount capability with increased angular adjustment).BEAMSMK: Surface-mount kit.RTS151: Remote test station.RTS151A: Same RTS151 with ULC listing.RTS151KEY: Remote test station with key lock.RTS151KEYA: Same as the RTS151KEY with ULC listing.BEAMHK: Heating kit for use with the transmitter/receiver unit of FSB-200S. For prevention of condensation.BEAMHKR: H eating kit for use with the reflector on FSB-200S. For prevention of condensation6500-MMK: Heavy-duty multi-mount kit for installations prone to vibration or where there is difficulty mounting the set angle.When installed with the transmitter/receiver unit, the 6500-SMK must be used as well.6500-SMK: Surface-mount kit (required when using 6500-MMK to mount transmitter/receiver).BEAMMMK(ceiling or wall mount kit sold sepa-rately)RTS151RTS151KEYBEAMHK6975b e a m m k .j p gr t s 151.w m frts151key.wmf6985hk.tif。
西门子 Sinteso 智能感知型 火灾探测系统 产品目录

Sinteso™ 产品目录1. 火灾报警控制器 (1)FS1120 CI1142/S/H47 智能感知型系统控制器 (1)FS1120 CC114x-CT/S/H67 智能感知型系统控制器 (2)FS1120 CI1142/S/Rack 智能感知型系统控制器(上柜式) (3)FS1120 CC114x-/S/Rack 智能感知型系统控制器(上柜式) (4)S11/EU消防辅助设备扩充机柜(上柜式) (5)2. Sinteso智能感知型探测设备 (6)FDO221-CN 光电感烟探测器 (6)FDT241-CN 感温探测器 (7)FDOOT241-CN 烟温复合型探测器 (8)FDB221 探测器底座 (9)FDB222 探测器底座(薄型) (9)FDSB291-CN 蜂鸣器底座 (10)FDM229-CN 手动报警按钮(碎玻式) (11)FDM228-CN 手动报警按钮(可复位式) (12)FDHM228-CN 消火栓报警按钮(可复位式) (13)FDCI225-CN 输入模块(4路) (13)FDCO224-CN 输出模块(4路) (14)FDCIO223-CN 输入输出模块(2路) (15)FDCL221-CN 线路隔离模块 (16)3. 通用产品 (17)OP520光电感烟探测器 (17)HI520电子感温探测器 (17)SO520非编址探测器底座 (17)DO1101A-Ex 集合型光电感烟探测器(防爆型) (18)DT1101A-Ex 集合型电子感温探测器(防爆型) (18)DB1101A 集合型探测器底座 (18)FDL241-9-CN 线型光束感烟探测器 (19)FDLB291 线型光束感烟探测器底座 (19)DLR1191 三棱反射镜 (20)DLR1192 反射板 (20)DLR1193 反射板 (20)DLH1191A 三棱反射镜加热元件 (20)FDF241-9 红外火焰探测器 (21)FDFB291底座 (22)DF119X防雨罩 (22)MV1 红外火焰探测器安装支架 (22)MWV1 红外火焰探测器球窝铰链 (22)SB3 防爆隔离栅 (23)EOL22(EX)非编址回路终端电阻(防爆型) (23)4. 控制器功能扩展部件 (25)E3M140 FDnet回路卡 (25)E3M080 非编址回路卡 (25)E3L020 输入输出联动卡(16路) (25)E3I040 层显转换卡(LON总线) (26)E3I020 RS232通讯卡 (26)K3I050显示驱动卡 (26)E3G070 通用控制卡 (27)E3G080灭火控制卡 (27)E3H020 网络通讯卡 (28)E3X102 主CPU卡 (28)E3X103 主CPU卡 (28)B3Q565 操作显示终端 (29)TPS11R 打印机(用于上柜式控制器) (29)TPS11W 打印机(用于壁挂式控制器) (29)FC9342 联动控制盘 (30)5. 辅助设备 (31)HY2114 警铃 (31)HSG1010 声光报警器 (31)BN3002C 吸顶式音箱 (32)ZA2725A 壁挂式音箱 (32)HGM2100-24 应急广播控制器 (33)HGM2425 广播功率放大器(250W) (34)HD210 火警电话分机 (35)HD220 手提火警电话 (36)HD230 电话插孔 (36)HDM2100-24 多线式火警通讯盘24路 (37)HY5711B 总线式火警通讯盘 (38)HY5714B总线式火警电话插孔 (39)HY5716B总线式火警电话分机 (39)BCH1936 立柜(带玻璃门) (40)BCH1950 双琴台 (40)BCB8005壁挂电源8A (41)BCB8002上柜电源20A (41)BCB8003上柜电源30A (42)ZA1952/15浮冲备用电池 (42)ZA1952/24浮冲备用电池 (42)ZA1952/38浮冲备用电池 (42)NP24-12 24AH/12V 电池 (42)NP38-12 38AH/12V 电池 (42)附件1 Sinteso智能感知型火灾自动报警及联动控制系统设计参考 (43)附件2 火灾报警系统的安装指南 (52)型号功能描述/技术参数部件号设备外观1. 火灾报警控制器FS1120CI1142/S/H47100720588FS1120 CC114x-CT/S/H67100720589FS1120CI1142/S/Rack100720590FS1120 CC114x-/S/Rack100720591S11/EUBCH1950或BCH1936 100673990型号功能描述/技术参数 部件号 设备外观FDO221-CN-10... +60 -30... +75 2. Sinteso 智能感知型探测设备100718388型号功能描述/技术参数部件号设备外观FDT241-CN100718389200+50-25...-25...+70-30...+75FDOOT241-CN100718390280+70-25...-30...+751...20FDB221 FDB222FDB221 探测器底座(瑞士生产)●可编址探测器底座,明装或暗装形式均适用。
MIT6_042JS10_lec06_sol

Another possibly bothersome point is that the proof assumes that if a set is infinite, it must have
more than n elements, for every nonnegative integer n. But really that’s the definition of infinity:
Solutions to In-Class Problems Week 3, Tue.
Problem 1. Lemma 4.9.4. Let A be a set and b ∈ / A. If A is infinite, then there is a bijection from A ∪ {b} to A. Proof. Here’s how to define the bijection: since A is infinite, it certainly has at least one element; call it a0 . But since A is infinite, it has at least two elements, and one of them must not be equal to a0 ; call this new element a1 . But since A is infinite, it has at least three elements, one of which must not equal a0 or a1 ; call this new element a2 . Continuing in the way, we conclude that there is an infinite sequence a0 , a1 , a2 , . . . , an , . . . of different elements of A. Now we can define a bijection f : A ∪ {b} → A: f (b) ::= a0 , f (an ) ::= an+1 f (a) ::= a for n ∈ N, for a ∈ A − {b, a0 , a1 , . . . } . � (a) Several students felt the proof of Lemma 4.9.4 was worrisome, if not circular. What do you think? Solution. There is no “solution” for this discussion problem, since it depends on what seems
SMC 开关设备操作指南说明书
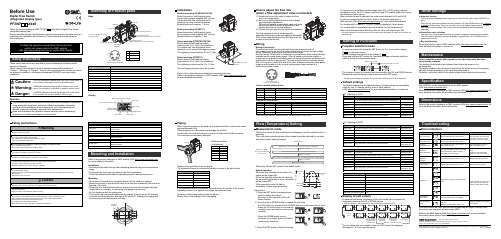
TroubleshootingSpecificationThe IODD file can be downloaded from the SMC website (URL ).Refer to the product catalogue or SMC website (URL ) for more detailed information about product specifications.DimensionsRefer to the product catalogue or SMC website (URL ) for more detailed information about dimensions.than above are displayed, please contact SMC.Error indicationSnap shot functionThe current flow rate/temperature value can be stored to the switch output ON/OFF set point.When the set value and hysteresis are set, press the UP and DOWN buttons for 1 second or longer simultaneously. Then, the set value of the sub display (right) shows [- - -], and then values corresponding to the current flow rate/temperature are automatically displayed.Peak/bottom value indicationThe max. (min.) rate/temperature when the power is supplied is detected and updated.The value can be displayed on the sub display by pressing the UP or DOWN button in measurement mode.Key-lock functionTo set this function, refer to SMC website (URL ) for more detailed information or contact us.MaintenanceHow to reset the product after a power cut or when the power has been unexpectedly removedThe settings of the product are retained from before the power cut or de-energizing.The output condition also recovers to that before the power cut or de-energizing,but may change depending on the operating environment.Therefore, check the safety of the whole system before operating the product.Function selection mode[F Select to display the function to be change [F mode to return to measurement mode.∗: The sub screen displays the content of function and the setting of the function alternately.The function number is increased and decreased by the UP and DOWN buttons.Display the required function number and press the SET button.Default settingsThe default settings are provided as follows. If these settings are acceptable,retain for use. To change setting, refer to SMC website(URL ) for more detailed information or contact us.Display of sub screenIn measurement mode, the display of the sub screen can be temporarily changed by pressing the UP or DOWN buttons.∗: After 30 seconds, it will automatically reset to the display selected in [F10].∗: Arbitrary displayThe set values and accumulated output of OUT2 cannot be displayed.(Example for 16 L/min type the above )The switch turns on within a set flow range (from P1L to P1H) during window comparator mode. Set P1L (switch lower limit) and P1H (switch upper limit) using the setting procedure above.When reversed output is selected, the main screen displays [n1L] and [n1H].To set accumulated output functions, refer to the product catalogue orSMC website (URL ) for more detailed information.For models with 2 outputs, [P_2] or [n_2] will be displayed. Set as above.For models with the temperature sensor attached, [ tn] will be displayed.When the fluid temperature falls below the set value, the output turns ON.∗: If a button operation is not performed for 30 seconds during the change of setting, the set value will start flashing.Refer to the SMC website (URL ) for more detailed information about product troubleshooting.Note: Specifications are subject to change without prior notice and any obligation on the part of the manufacturer.© 2018 SMC Corporation All Rights Reserved Akihabara UDX 15F, 4-14-1, Sotokanda, Chiyoda-ku, Tokyo 101-0021, JAPAN Phone: +81 3-5207-8249 Fax: +81 3-5298-5362URL PF ※※-OMV0007Safety InstructionsFlow (Temperature) SettingInstallationBracket mounting (PF3W704/720/740)Mount the product (with bracket) usingthe mounting screws supplied (M4 x 4 pcs.).For models with flow adjustment valve attached, fix using 8 mounting screws.Bracket thickness is approx. 1.5 mm.Measurement modeThe mode in which the flow is detected and displayed, and the switch function is operating.This is the basic operating mode; other modes should be selected for set-point and other function setting changes.Approx. 3 seconds for this period)Mounting and InstallationInstallation•Use the product within the specified operating pressure range and temperature range.•Proof pressure could vary according to the fluid temperature.Check the characteristics data for operating pressure and proof pressure.(4 pins) (Option)(Option)Direct mounting (PF3W704/720/740)Mount using the self tapping screws(nominal size: 3.0 x 4 pcs.) for installation.For models with flow adjustment valvePipingWhen connecting piping to the product, a spanner should be used on the metal piping attachment only.Using a spanner on other parts may damage the product.In particular, do not let the spanner come into contact with the M8 connector.The connector can be easily damaged.If the tightening torque is exceeded, the product can be broken. If the correct tightening torque is not applied, the fittings may become loose.Avoid any sealing tape getting inside the piping.Ensure there is no leakage from loose piping.3/824 mm 1/227 mm 3/432 mm Tighten to the specified torque for piping.The tightening torque for connection threads is shown in the table below.Direct mounting (PF3W711)Mount using the self tapping screws(nominal size: 4.0 x 4 pcs.) for installation.The tightening torque must be 1 to 1.2 Nm.The self tapping screws cannot be re-used.Refer to the outline dimension drawing for mounting hole size.Refer to the product catalogue or SMC website (URL )for more detailed information.WiringWiring of connectorConnections should only be made with the power supply turned off.Use separate routes for the Flow switch wiring and any power or high voltage wiring. Otherwise, malfunction may result due to noise.Ensure that the FG terminal is connected to ground when using a commercially available switch-mode power supply. When a switch-mode power supply isconnected to the product, switching noise will be superimposed and the product specification can no longer be met. This can be prevented by inserting a noise filter, such as a line noise filter and ferrite core, between the switch-mode power supply and the product, or by using a series power supply instead of a 141 mm How to adjust the flow rate(when a flow adjustment valve is mounted)(1) Rotate the knob of the valve to adjust the flowrate to the target value.(2) Be sure to confirm that there is no fluid leakagegenerated after adjustment.the valve several times for re-adjustment, and confirm that there is no fluid leakage.)(3) The flow adjustment valve is not designed forIf the valve is adjusted frequently, fluid may leak due to wear of the internal seal.BodyDisplayBracket mounting (PF3W711)Mount the product (with bracket) usingthe mounting screws supplied (M5 x 4 pcs.).Bracket thickness is approx. 2 mm.2. Press the UP or DOWN button to change the set value.The UP button is to increase and the DOWN button is to decrease the set value.•Press the UP button once to increase by one digit, press and hold to continuously increase.3. Press the SET button to finish the setting.•Press the DOWN button once todecrease by one digit, press and hold tocontinuously decrease.Mounting•Never mount the product in a location where it will be used as a support.•Mount the product so that the fluid flows in the direction indicated by the arrow on the side of the body.•Check the flow characteristics data for pressure loss and the straight inlet pipe length effect on accuracy, to determine inlet piping requirements.•Do not sharply reduce the piping size.•The monitor with integrated display can be rotated. It can be set at 90o intervals clockwise and anticlockwise, and also at 45o and 225o . Rotating the display with excessive force will damage the end stop.Refer to the product catalogue or SMC website (URL )for more detailed information.11/454 mm 11/254 mmBefore UseDigital Flow Switch(Integrated display type)(Integrated display type).Please read this manual carefully before operating the product and make sure you understand its capabilities and limitations. Please keep this manual handy for future reference.Safety InstructionsThese safety instructions are intended to prevent hazardous situations and/or equipment damage.These instructions indicate the level of potential hazard with the labels of"Caution", "Warning" or "Danger". They are all important notes for safety and must be followed in addition to International standards (ISO/IEC) and other safety regulations.OperatorWidth across flats of attachment<Operation>1. Press the SET button in measurement mode to display set values.Set value on the right side of the sub screen flashes.。
艾顿 Moeller 系列快速链接速度调控器 198834说明书

Eaton 198834Eaton Moeller® series Rapid Link - Speed controllers, 8.5 A, 4 kW, Sensor input 4, 180/207 V DC, AS-Interface®, S-7.4 for 31 modules, HAN Q5, with manual override switch, with fanAllgemeine spezifikationEaton Moeller® series Rapid Link Speed controller198834195 mm270 mm 220 mm 3.77 kgUL 61800-5-1 UL approval CEIEC/EN 61800-5-1 RoHS4015081968923RASP5-8401A31-512R001S1Product NameCatalog NumberProduct Length/Depth Product Height Product Width Product Weight Certifications Catalog Notes EANModel Code3 fixed speeds and 1 potentiometer speedcan be switched over from U/f to (vector) speed control Connection of supply voltage via adapter cable on round or flexible busbar junctionDiagnostics and reset on device and via AS-InterfaceInternal and on heat sink, temperature-controlled Fan Parameterization: drivesConnectParameterization: drivesConnect mobile (App) Parameterization: KeypadParameterization: FieldbusKey switch position HANDManual override switchSelector switch (Positions: REV - OFF - FWD)PC connectionKey switch position AUTOPTC thermistor monitoringControl unitInternal DC linkIGBT inverterThermo-click with safe isolationKey switch position OFF/RESETTwo sensor inputs through M12 sockets (max. 150 mA) for quick stop and interlocked manual operationFanFor actuation of motors with mechanical brake1 potentiometer speed3 fixed speeds IP65NEMA 121st and 2nd environments (according to EN 61800-3)IIISpeed controllerAS-Interface profile cable: S-7.4 for 31 modulesASIC2, C3: depending on the motor cable length, the connected load, and ambient conditions. External radio interference suppression filters (optional) may be necessary.C1: for conducted emissions only2000 VAC voltageCenter-point earthed star network (TN-S network)Phase-earthed AC supply systems are not permitted.Vertical15 g, Mechanical, According to IEC/EN 60068-2-27, 11 ms, Half-sinusoidal shock 11 ms, 1000 shocks per shaftResistance: According to IEC/EN 60068-2-6Resistance: 57 Hz, Amplitude transition frequency on accelerationResistance: 10 - 150 Hz, Oscillation frequencyResistance: 6 Hz, Amplitude 0.15 mm Above 1000 m with 1 % performance reduction per 100 m Max. 2000 m-10 °C40 °C-40 °C70 °CFeatures Fitted with:Functions Degree of protectionElectromagnetic compatibility Overvoltage categoryProduct categoryProtocolRadio interference classRated impulse withstand voltage (Uimp) System configuration typeMounting position Shock resistance Vibration AltitudeAmbient operating temperature - min Ambient operating temperature - max Ambient storage temperature - min Ambient storage temperature - max< 95 %, no condensation In accordance with IEC/EN 50178Adjustable, motor, main circuit 0.8 - 8.5 A, motor, main circuit < 10 ms, Off-delay < 10 ms, On-delay 98 % (η)7.8 A3.5 mA120 %Maximum of one time every 60 seconds 380 V480 V380 - 480 V (-10 %/+10 %, at 50/60 Hz)U/f controlPM and LSPM motorsSensorless vector control (SLV) BLDC motorsSynchronous reluctance motors 0 Hz500 HzFor 60 s every 600 s At 40 °C12.7 AClimatic proofingCurrent limitationDelay timeEfficiency Input current ILN at 150% overload Leakage current at ground IPE - max Mains current distortion Mains switch-on frequencyMains voltage - min Mains voltage - max Mains voltage toleranceOperating mode Output frequency - min Output frequency - max Overload current Overload current IL at 150% overload45 Hz66 Hz4 kW400 V AC, 3-phase480 V AC, 3-phase0.1 Hz (Frequency resolution, setpoint value)200 %, IH, max. starting current (High Overload), For 2 seconds every 20 seconds, Power section50/60 Hz8 kHz, 4 - 32 kHz adjustable, fPWM, Power section, Main circuitAC voltageCenter-point earthed star network (TN-S network)Phase-earthed AC supply systems are not permitted.5 HP≤ 0.6 A (max. 6 A for 120 ms), Actuator for external motor brakeAdjustable to 100 % (I/Ie), DC - Main circuit≤ 30 % (I/Ie)280/207 V DC -15 % / +10 %, Actuator for external motor brake10 kAType 1 coordination via the power bus' feeder unit, Main circuit180/207 V DC (external brake 50/60 Hz)24 V DC (-15 %/+20 %, external via AS-Interface® plug)AS-InterfacePlug type: HAN Q5Number of slave addresses: 31 (AS-Interface®) Specification: S-7.4 (AS-Interface®)Max. total power consumption from AS-Interface® power supply unit (30 V): 190 mA C3 ≤ 25 m, maximum motor cable length C2 ≤ 5 m, maximum motor cable length C1 ≤ 1 m, maximum motor cable lengthMeets the product standard's requirements.Rated frequency - minRated frequency - maxRated operational power at 380/400 V, 50 Hz, 3-phase Rated operational voltageResolutionStarting current - maxSupply frequencySwitching frequencySystem configuration type Assigned motor power at 460/480 V, 60 Hz, 3-phase Braking currentBraking torqueBraking voltageRated conditional short-circuit current (Iq)Short-circuit protection (external output circuits) Rated control voltage (Uc)Communication interfaceConnectionInterfacesCable length10.2.2 Corrosion resistanceMeets the product standard's requirements.Meets the product standard's requirements.Meets the product standard's requirements.Meets the product standard's requirements.Does not apply, since the entire switchgear needs to be evaluated.Does not apply, since the entire switchgear needs to be evaluated.Meets the product standard's requirements.Does not apply, since the entire switchgear needs to be evaluated.Meets the product standard's requirements.Does not apply, since the entire switchgear needs to be evaluated.Does not apply, since the entire switchgear needs to be evaluated.Is the panel builder's responsibility.Is the panel builder's responsibility.Is the panel builder's responsibility.Is the panel builder's responsibility.Is the panel builder's responsibility.Generation change from RA-MO to RAMO 4.0Generation Change RASP4 to RASP5Generation change from RA-SP to RASP 4.0 Elektromagnetische Verträglichkeit (EMV)Generation change RAMO4 to RAMO5Firmware Update RASP 4.0Generation Change RA-SP to RASP5Configuration to Rockwell PLC for Rapid LinkConfiguration to Rockwell PLC Rapid Link 5 Generationentausch RAMO4 zu RAMO5 Generationenwechsel RA-SP zu RASP5Generationentausch RA-SP zu RASP4.0Anschluss von Frequenzumrichtern an Generatornetze Generationentausch RA-MO zu RAMO4.0 Generationswechsel RASP4 zu RASP5MN040003_DEMN034004_DERapid Link 5 - brochureDA-SW-Driver DX-CBL-PC-3M0DA-SW-drivesConnect - installation helpDA-SW-USB Driver PC Cable DX-CBL-PC-1M5DA-SW-drivesConnectDA-SW-USB Driver DX-COM-STICK3-KITDA-SW-drivesConnect - InstallationshilfeMaterial handling applications - airports, warehouses and intra-logisticsETN.RASP5-8401A31-512R001S1.edzIL034085ZUDE | Rapid Link 5Sortimentskatalog Antriebstechnik-DE10.2.3.1 Verification of thermal stability of enclosures10.2.3.2 Verification of resistance of insulating materials to normal heat10.2.3.3 Resist. of insul. mat. to abnormal heat/fire by internal elect. effects10.2.4 Resistance to ultra-violet (UV) radiation10.2.5 Lifting10.2.6 Mechanical impact10.2.7 Inscriptions10.3 Degree of protection of assemblies10.4 Clearances and creepage distances10.5 Protection against electric shock10.6 Incorporation of switching devices and components10.7 Internal electrical circuits and connections10.8 Connections for external conductors10.9.2 Power-frequency electric strength10.9.3 Impulse withstand voltage10.9.4 Testing of enclosures made of insulating material Anmerkungen zur AnwendungBenutzerhandbücherBroschüreneCAD model Installationsanleitung InstallationsvideosKatalogeEaton Konzern plc Eaton-Haus30 Pembroke-Straße Dublin 4, Irland © 2023 Eaton. Alle Rechte vorbehalten. Eaton ist eine eingetrageneMarke.Alle anderen Warenzeichen sindEigentum ihrer jeweiligenBesitzer./socialmediaThe panel builder is responsible for the temperature rise calculation. Eaton will provide heat dissipation data for the devices.Is the panel builder's responsibility. The specifications for the switchgear must be observed.Is the panel builder's responsibility. The specifications for the switchgear must be observed.The device meets the requirements, provided the information in the instruction leaflet (IL) is observed.ramo5_v22.dwgrasp5_v22.stpeaton-bus-adapter-rapidlink-speed-controller-dimensions-002.eps eaton-bus-adapter-rapidlink-speed-controller-dimensions-004.eps eaton-bus-adapter-rapidlink-speed-controller-dimensions-003.eps eaton-bus-adapter-rapidlink-speed-controller-dimensions-005.eps10.10 Temperature rise10.11 Short-circuit rating10.12 Electromagnetic compatibility 10.13 Mechanical function mCAD model Zeichnungen。
MIT6_042JS10_lec27_sol
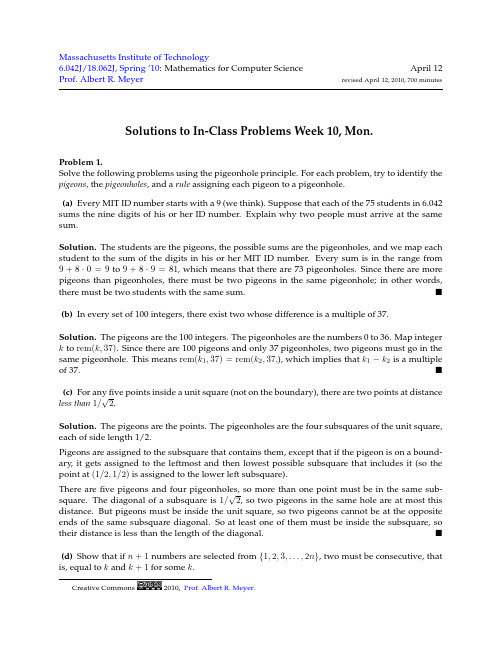
3
Problem 3. Your 6.006 tutorial has 12 students, who are supposed to break up into 4 groups of 3 students each. Your TA has observed that the students waste too much time trying to form balanced groups, so he decided to pre-assign students to groups and email the group assignments to his students. (a) Your TA has a list of the 12 students in front of him, so he divides the list into consecutive groups of 3. For example, if the list is ABCDEFGHIJKL, the TA would define a sequence of four groups to be ({A, B, C } , {D, E, F } , {G, H, I } , {J, K, L}). This way of forming groups defines a mapping from a list of twelve students to a sequence of four groups. This is a k -to-1 mapping for what k ? Solution. Two lists map to the same sequence of groups iff the first 3 students are the same on both lists, and likewise for the second, third, and fourth consecutive sublists of 3 students. So for a given sequence of 4 groups, the number of lists which map to it is (3!)4 because there are 3! ways to order the students in each of the 4 consecutive sublists. �
SiAECOSYS V2 IV代 EM系列控制器程序手册说明书
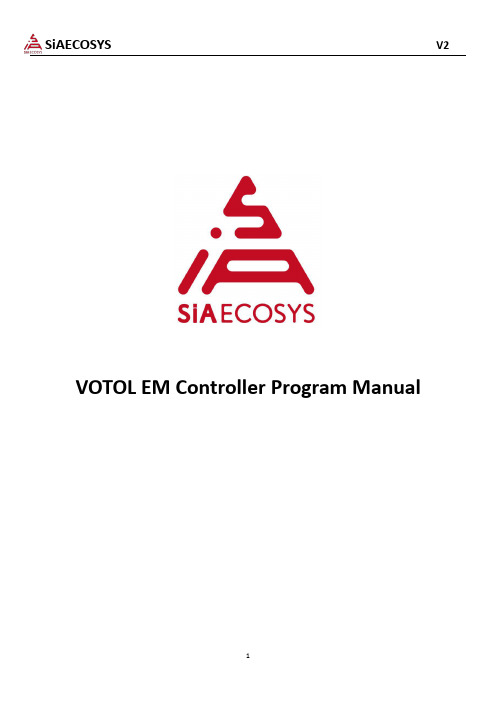
VOTOL EM Controller Program ManualIt is forbidden to non-specialists use!This manual was explained in detail for the IV generation EM series controller,which update download illustrates and parameter adjustment.Before using the software,please read this manual.In order to facilitate the operation,please keep this manual.In order to make the software of maximum utility,please make sure the end user to use this manual.Please be sure to read the manual carefully before starting the operation.Disclaimer:For theⅣgeneration of EM series controller program updates and parameter adjustment can only bedone by professional and technical personnel.If without the written permission of our company for theⅣVOTOL generation EM series,theapplication update to download and parameter of the controller adjustment is not allowed.It is forbidden to non-professional personnel operate this software.In the above event,our company will no longer be responsible for accident happens by controller.1.Software installation(only support win7/10)1.1USB Driver Installation(1)Download the“USB-to-serial-win10-20150814”file,decompressing file.(2)choose the suitable driver with your computer for installation.win7,win8,win10are available.1.11.Decompress the operation first2.Unzip the YH-340USB package and select CH341SER.EXE to install it.Follow the steps above to install(3)After installation,pls.connect the USB cable with controller and computer.If it’s unable to connect,pls.Check below steps.Right click“my computer”in the desktopthen click“device manager”choose“port(COM&LPT)”choose the COM with“!”,click“serach automatically for updated driver software”Close the software when you finishAfter running,please run the software directly:EM_V3series debugging program;If the port has”自2012已停产,请联系供货商处理方法(Pls contact supplier if it is stop production since2012)”First step:Install driver PL2303_Prolific_DriverInstaller_v110Second:Right click to update the driver and select Browse Computer to find the driver software.Thrid:Click to select from the list of drivers for your computer;Select version3.3.10.140(2009-11-19),click Next,close the window when finished;2.Controller connection2.1Connect controllerController host computer simple wiring diagramDescription:controller B+connects battery B+controller B-connects battery B-,controller electric door locks connect battery or controller B+;The USB debug line is connected to the controller debug port;2.1.1According to the controller with CAN or without CAN to select the appropriate USB debug line;with CAN controller need to check the CAN enable,without CAN does not need to check;EM200controller needs to exchange the debug line CAN-H and CAN-L ,otherwise can’t connect the controller;2.1.2Host computer selectionEM50EM100EM150without CAN chooseEM50EM100EM150with CAN chooseEM200chooseSpecific host model needs to inquire the related sales;3Open the computer device manager before connecting to the computer to check whether the USB port is successfullyinstalled.Select the appropriate host computer to connect the host computer to the serial port when the controller is not powered.After selecting the corresponding serial port on the device port,click CreatFile.2.2Then power on(connect with e-lock),click connect(in setting1page),the nominal voltage should not be0.If it’s0,click connect again.3.The settingSetting page11.1:Voltage equipment1.1.1、Battery voltage setting:Corresponding to the ECU voltage,absolutely not allowe overpressure.1.1.2、Lead-acid battery overvoltage,undervoltage,soft undervoltage basic value default:due to software settings defects,the original voltage compensation+1V.1.1.3、The lithium battery is set according to the actual lithium battery parameter value.Due to software setting defects,the original voltage compensation+1V.The original lithium battery parameters are compensated for+1V,and the total compensation is+2V.1.1.4、Attention1.1.4.1、Overvoltage fault:After open the electric door lock,the vehicle doesn’t move.The Controller overvoltage protection function starts.1.1.4.2、ECU undervoltage fault:due to the lithium battery protection board overvoltage device is too high or the undervoltage setting is too low,resulting in lithium battery protection,burning MOS.Please adjust suitable battery voltage before running the motor and controller(for lithium battery).Overvoltage:real overvoltage+3VUndervoltage:real undervoltage+1VSoft undervoltage:undervoltage +3Vg.real overvoltage 84V,set 87V.real undervotlage 60V,set 61V.Soft undervotlage:64V.1.2:Current device1.2.2、Phase current setting:can only be adjusted downwards.1.2.3、Attention1.2.3.1、Setting the busbar current too high,causing the ECU burn MOS.1.2.3.2、As the phase current value decreases,the corresponding motor stall protection time is shortened.Setting page 21throttle voltage adjust(1)low protection value:The throttle error is shown(2)Starting voltage:when the value is reached,the motor starts running(3)End voltage:when the value is reached,the controller thinks the full voltage is reached (it is recommended to set the voltage lower 0.2v compared with thactual torque voltage).(4)High protection value:when the value is higher than that,the torque fault will be displayed2Start setting adjustment (for tricycle gear box only)(1)Starting torque:used for gear combination(2)Combined torque:a force of lifting after gear clearance is combined(3)Upward slope:upward slope of motor torque(4)Downward slope:downward slope of motor torque3Controller and motor temperature protection function adjustment(1)Start:Enter into the function of temperature protection,limit the motor torque.(2)Over temperature:Cut off the output of motor torque(3)Recover:When the motor temperature lower than the temperature protection value,you can re-twist the throttle, then the motor will restore motivation(4)Maximum:The motor maximum temperature is150Setting for page23.1:Parameters setting for sports mode(S gear)3.2.1、Busbar current setting:According to the controller type current corresponding to the selection,the vehicle speed is adjusted according to the motor parameters.BOOST weak magnetic value>high speed weak magnetic value3.2.3、Automatic logout enablers,confirm by select:Check the jog button /uncheck the long press button,choose one3.2.3.1、Check to make the jog effective.The weak magnetic time enters the exit and can be adjusted. 3.2:Downhill electric brake assist:start by select“HDC Enable”,downhill electric brake assist(slow down in steep slopes)function.Enable electric brake by enter minimum speed,if less than the speed,the function will be invalid.3.2.1Value400corresponding to speed around15kmh(it depends on motor feature,sometimes with a3.2.2、Note:The drum motor is not suitable for use,resulting in loose motor shaft.3.3、Flux weakening compensation:only valid when the inner rotor motor type is selected as V-shaped magnetic steelNote:The maximum value of255is generally filled in953.4、Three gear setting:Confirm the motor base speed value adjustment setting parameter value.The basic speed is filled in according to the<Appendix EM_V3Parameter Adjustment Calculation Formula>.3.4.1、The low,medium,high,and third speed values are valid within100%of the parameter value,and the medium,high,and high speed values are exceeded and the100%parameter value is filled.Exceeded by weak magnetic file(medium,high,BOST)3.4.2、In the flux weakening area,the actual parameters of the motor are adjusted,and the vehicle speed is based on the road test.3.4.3、Single voltage mode:The high voltage value is invalid.3.4.4、Attention3.4.4.1、Drum motor:60KM/H motor weak magnetic speed is less than<120%,80KM/H motor weak magnetic speed is less than<125%,110KM/H motor weak magnetic speed is less than<135%.2.4.4.3Inner rotor motor Hall:The built-in Hall weak magnetic speed is less than<135%,and the external Hall weak magnetic speed is less than170%.3.4.4.3、Internal rotor motor magnetic knitting:Built-in flux weakening speed<230%.3.4.4.4The motor base speed exceeds100%of the motor speed value and enters the weak value zone adjustment parameter.BOOST>High speed weak magnetic file.3.4.4.5Weak magnetic failure:The flux weakening value exceeds the motor and controller parameter values,causing the motor to demagnetize and the controller to burn MOS.3.5、Jog/push selection:choose one3.6、The three-speed default gear:the electric door lock opens the default several options.3.7、Soft start setting:The smaller the value,the softer the start.3.8、Speed limit setting:3.8.1、Function selection:speed limit,unlimited speed,two choices,default speed limit3.8.2、The speed limit speed is calculated based on vehicle parameter requirements.<Appendix EM_V3 parameter adjustment calculation formula>3.8.3、The upper limit speed and the solution speed limit are determined according to customer requirements.Setting page33.1、Motor Setting:3.1.1、Motor pole pairs:Fill in according to the motor manufacturer parameters.3.1.2、Hall phase shift angle:Fill in according to the motor manufacturer parameters.3.1.3、Motor type:Fill in according to the motor manufacturer parameters.Note:Wheel Hub motor is surface mount3.1.4、Hall,phase line exchange:exchange the motor forward and reverse.3.2、The controller to speedometer date output has2types:Single-line speedometer and hall speedometer, it needs to be decided by the vehicle’s speedometer.3.3、Moving assist and cruising function:Used in two-wheelersNote:Speed"3KM/H,torque9~19N.M3.4Cruise function:function selection,the default does not open.3.5Dual voltage setting:default single voltage。
恩智浦 MIMXRT1020 EVK 开发板硬件用户指南说明书
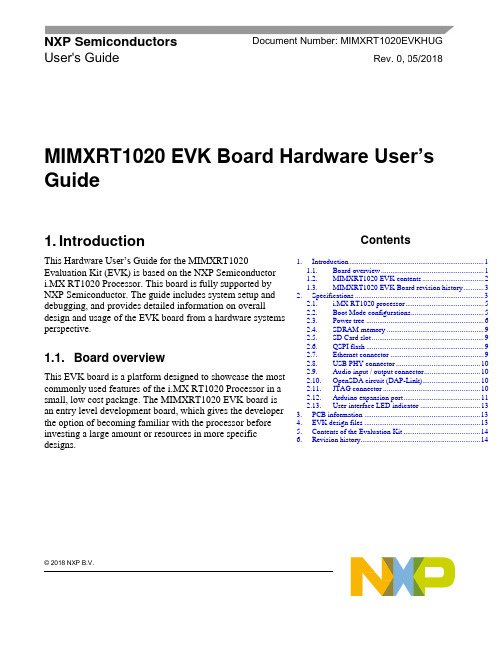
© 2018 NXP B.V.MIMXRT1020 EVK Board Hardware User’sGuide1.IntroductionThis Hardware User’s Guide for the MIMXRT 1020Evaluation Kit (EVK) is based on the NXP Semiconductor i.MX RT1020 Processor. This board is fully supported by NXP Semiconductor. The guide includes system setup and debugging, and provides detailed information on overall design and usage of the EVK board from a hardware systems perspective.1.1. Board overviewThis EVK board is a platform designed to showcase the most commonly used features of the i.MX RT1020 Processor in a small, low cost package. The MIMXRT1020 EVK board is an entry level development board, which gives the developer the option of becoming familiar with the processor before investing a large amount or resources in more specific designs.NXP Semiconductors Document Number: MIMXRT1020EVKHUGUser's GuideRev. 0 , 05/2018Contents1.Introduction ........................................................................ 11.1.Board overview ....................................................... 11.2.MIMXRT1020 EVK contents ................................. 21.3.MIMXRT1020 EVK Board revision history ........... 32.Specifications ..................................................................... 32.1.i.MX RT1020 processor .......................................... 52.2.Boot Mode configurations ....................................... 52.3.Power tree ............................................................... 62.4.SDRAM memory .................................................... 92.5.SD Card slot ............................................................ 92.6.QSPI flash ............................................................... 92.7.Ethernet connector .................................................. B PHY connector ............................................. 102.9.Audio input / output connector .............................. 102.10.OpenSDA circuit (DAP-Link) ............................... 102.11.JTAG connector .................................................... 102.12.Arduino expansion port ......................................... er interface LED indicator ................................ 133.PCB information .............................................................. 134.EVK design files .............................................................. 135.Contents of the Evaluation Kit ......................................... 146.Revision history (14)IntroductionFeatures of the MIMXRT1020 EVK board are shown in Table 11.2. MIMXRT1020 EVK contentsThe MIMXRT1020 EVK contains the following items: •MIMXRT1020 EVK Board•USB Cable (Micro B)Specifications 1.3. MIMXRT1020 EVK Board revision history•Rev A: Prototype.2. SpecificationsThis chapter provides detailed information about the electrical design and practical considerations of the EVK Board, and is organized to discuss each block in the following block diagram of the EVK board.( Figure 1)Figure 1. Block diagramThe overview of the MIMXRT1020 EVK Board is shown in Figure 1 & Figure 2.SpecificationsFigure 2. Overview of the MIMXRT1020 EVK Board (Front side)Figure 3. Overview of the MIMXRT1020 EVK Board (Back side)Specifications 2.1. i.MX RT1020 processorThe i.MX RT1020 is a new processor family featuring NXP's advanced implementation of the Arm® Cortex®-M7 Core. It provides high CPU performance and best real-time response. The i.MX RT1020 provides various memory interfaces, including SDRAM, Raw NAND FLASH, NOR FLASH,SD/eMMC, Quad SPI, HyperBus and a wide range of other interfaces for connecting peripherals, such as WLAN, Bluetooth™, GPS. Same as other i.MX processors, i.MX RT1020 also has rich audio features, including SPDIF and I2S audio interface.The i.MX RT1020 applications processor can be used in areas such as industrial HMI, IoT, motor control and home appliances. The architecture's flexibility enables it to be used in a wide variety of other general embedded applications too. The i.MX processor provides all interfaces necessary to connectp eripherals such as WLAN, Bluetooth™, GPS.The more detail information about i.MX RT1020 can be found in the Datasheet and Reference Manual2.2. Boot Mode configurationsThe device has four boot modes (one is reserved for NXP’s use). The boot mode is selected based on the binary value stored in the internal BOOT_MODE register. Switch (SW8-3 & SW8-4) is used to select the boot mode on the MIMXRT1020 EVK Board.Typically, the internal boot is selected for normal boot, which is configured by external BOOT_CFG GPIOs. The following Table 3 shows the typical Boot Mode and Boot Device settings.NOTEFor more information about boot mode configuration, see the System Boot chapter of theMIMXRT1020 Reference Manual. (waiting for update)For more information about MIMXRT1020 EVK boot device selection and configuration, see the main board schematic. (waiting for update)Specifications2.3. Power treeA DC 5 V external power supply is used to supply the MIMXRT1020 EVK Board at J2, and a slide switch SW1 is used to turn the Power ON/OFF. J23 and J9 also can be used to supply the EVK Board. Different power supply need to configure different Jumper setting of J1. Table 4 shows the details:NOTEFor some computers’ USB, it cannot support 500ma before establishingcommunication. In this case, it is recommended to replace the computer oruse the power adapter(J2) to power the EVK Board.The power tree is shown in Figure 4SpecificationsFigure 4. Power TreeThe power control logic of the MIMXRT1020 EVK board is shown in the Figure 5: •It will power up SNVS, and then PMIC_REQ_ON will be switched on to enable external DC/DC to power up other power domains.•ON/OFF button is used to switch ON/OFF PMIC_REQ_ON to control power modes.•RESET button and WDOG output are used to reset the system power.SpecificationsFigure 5. Power Control Diagram The power rails on the board are shown in Table 5.Specifications2.4. SDRAM memoryOne 256 Mb, 166MHz SDRAM (MT48LC16M16A2P) is used on the EVK Board.2.5. SD Card slotThere is a SD card slot(J15) on the MIMXRT1020 EVK Board. J15 is the Micro SD slot for USDHC1 interface. If the developer wants to boot from the SD Card, the boot device switch (SW8) settings should be: OFF, ON, ON, OFF, as shown in Table 3.2.6. QSPI flashA 64 Mbit QSPI Flash is used on the MIMXRT1020 EVK Board. If the developer wants to boot from the QSPI Flash, the boot device switch(SW8) settings should be: OFF, OFF, ON, OFF, as shown in Table 3.2.7. Ethernet connectorThere is one Ethernet Mac controller in the MIMXRT1020 processor. The Ethernet subsystem of the MIMXRT1020 EVK Board is provided by the KSZ8081RNB 10/100M Ethernet Transceiver (U11) and a RJ45 (J14) with integrated Magnetic.Figure 6. Ethernet Connector RJ45Specifications2.8. USB PHY connectorThe MIMXRT1020 contains a integrated USB 2.0 PHYs capable of connecting to USB host/device systems at the USB low-speed (LS) rate of 1.5 Mbits/s, full-speed (FS) rate of 12 Mbits/s or at the USB 2.0 high-speed (HS) rate of 480 Mbits/s.2.9. Audio input / output connectorThe Audio CODEC used on the MIMXRT1020 EVK Board is Wolfson’s Low Power, high quality Stereo Codec, WM8960.The MIMXRT1020 EVK Board include one headphone interface (J11), one onboard MIC (P1), two speaker interfaces (J12, J13). J11 is a 3.5 mm audio stereo headphone jack, which supports jack detect.2.10. OpenSDA circuit (DAP-Link)The OpenSDA circuit (CMSIS–DAP) is an open-standard serial and debug adapter. It bridges serial and debug communications between a USB host and an embedded target processor.CMSIS-DAP features a mass storage device (MSD) bootloader, which provides a quick and easy mechanism for loading different CMSIS-DAP Applications such as flash programmers, run-control debug interfaces, serial-to-USB converters, and more. Two or more CMSIS-DAP applications can run simultaneously. For example, run-control debug application and serial-to-USB converter runs in parallel to provide a virtual COM communication interface while allowing code debugging via CMSIS-DAP with just single USB connection.For the MIMXRT1020 EVK Board, J23 is the connector between the USB host and the target processor. Jumper to serial downloader mode to use stable DAP-Link debugger function. If developer wants to make OpenSDA going to the bootloader mode, and press SW5 when power on. Meanwhile, the OpenSDA supports drag/drop feature for U-Disk. First, use the seral downloader mode and drag/drop the image file to U-Disk. Then select QSPI Flash as boot device and reset the Board, the image will run.2.11. JTAG connectorJ16 is a standard 20-pin/2.54 mm Box Header Connector for JTAG. The pin definitions are shown in Figure 7. Support SWD by default.SpecificationsFigure 7. JTAG pin definitions2.12. Arduino expansion portJ17 – J20 (unpopulated) is defined as Arduino Interface. The pin definitions of Arduino Interface are shown in Table 6.Specifications2.12.1. Power switchSW1 is a slide switch to control the power of the MIMXRT1020 EVK Board when the power supply is from J2. The function of this switch is listed below:•Sliding the switch to the ON position connects the 5 V power supply to the Evaluation board main power system.•Sliding the switch to OFF position immediately removes all power from the board.2.12.2. ON/OFF buttonSW2 is the ON/OFF button for MIMXRT1020 EVK Board. A short pressing in OFF mode causes the internal power management state machine to change state to ON. In ON mode, a short pressing generates an interrupt (intended to be a software-controllable(power-down). An approximate 5 seconds or more pressing causes a forced OFF. Both boot mode inputs can be disconnected.2.12.3. Reset buttonThere are two Reset Button on the EVK Board. SW5 is the Power Reset Button. Pressing the SW5 in the Power On state will force to reset the system power except SNVS domain. The Processor will be immediately turn off and reinitiate a boot cycle from the Processor Power Off state. SW3 is POR Reset Button.EVK design files 2.12.4. USER buttonSW4 is the USER Button(GPIO5-00) for developers using. Pressing can produce changes in high and low levels.2.13. User interface LED indicatorThere are four LED status indicators located on the EVK Board. The functions of these LEDs include: •Main Power Supply(D3)Green: DC 5V main supply is normal.Red: J2 input voltage is over 5.6V.Off: the board is not powered.•Reset RED LED(D15)•OpenSDA LED(D16)•USER LED(D5)3. PCB informationThe MIMXRT1020 EVK Board is made using standard 2-layer technology. The material used was FR-4. The PCB stack-up information is shown in Table 7.4. EVK design filesThe schematics, layout files, and gerber files (including Silkscreen) can be downloaded from/MIMXRT1020-EVK(waiting for update).Revision history5. Contents of the Evaluation KitNOTEPower adaptor, Micro SD Card are not standard parts of the Evaluation Kit.6. Revision historyTable 9 summarizes the changes made to this document since the initial release.Document Number: MIMXRT1020EVKHUGRev. 0 05/2018How to Reach Us: Home Page: Web Support: /supportInformation in this document is provided solely to enable system and softwareimplementers to use NXP products. There are no express or implied copyright licenses granted hereunder to design or fabricate any integrated circuits based on the information in this document. NXP reserves the right to make changes without further notice to any products herein.NXP makes no warranty, representation, or guarantee regarding the suitability of its products for any particular purpose, nor does NXP assume any liability arising out of the application or use of any product or circuit, and specifically disclaims any and all liability, including without limitation consequenti al or incidental damages. “Typical” parameters that may be provided in NXP data sheets and/or specifications can and do vary in different applications, and actual performance may vary over time. All operating parameters, including “typicals”, must be validated for each customer application by customer’s technical experts. NXP does not convey any license under its patent rights nor the rights of others. NXP sells products pursuant to standard terms and conditions of sale, which can be found at the following address: /SalesTermsandConditions . While NXP has implemented advanced security features, all products may be subject to unidentified vulnerabilities. Customers are responsible for the design and operation of their applications and products to reduce the effect of these vulnerabilities oncustomer’s applications and products, and NXP accepts no liability for any vulne rability that is discovered. Customers should implement appropriate design and operating safeguards to minimize the risks associated with their applications and products NXP, the NXP logo, NXP SECURE CONNECTIONS FOR A SMARTER WORLD, , Freescale, the Freescale logo, and Kinetis, are trademarks of NXP B.V. All other product or service names are the property of their respective owners. Arm and Cortex are registered trademarks of Arm Limited (or its subsidiaries) in the EU and/or elsewhere. All rights reserved. © 2018 NXP B.V.。
固纬电子实业MFG-2000系列多通道函数信号发生器使用手册说明书

多通道函数信号发生器MFG-2000系列使用手册固纬料号NO.82MF32K000EC1ISO-9001认证企业2015.07本手册所含资料受到版权保护,未经固纬电子实业股份有限公司预先授权,不得将手册内任何章节影印、复制或翻译成其它语言。
本手册所含资料在印制之前已经过校正,但因固纬电子实业股份有限公司不断改善产品,所以保留未来修改产品规格、特性以及保养维修程序的权利,不必事前通知。
固纬电子实业股份有限公司台湾台北县土城市中兴路7-1号目录安全说明 (6)产品介绍 (10)面板介绍 (12)显示 (21)设置信号发生器 (22)快速操作 (24)如何使用数字输入 (26)如何使用帮助菜单 (27)顯示區域的分配 (29)选择波形 (30)调制 (32)扫描 (41)脉冲串 (43)ARB (45)工具栏 (51)菜单树 (52)默认设置 (70)操作 (72)CH1/CH2通道 (74)RF通道 (87)Pulse 通道 (98)功率放大器 (109)调制 (112)3幅值调制 (AM) (115)幅移键控 (ASK) 调制 (122)频率调制 (FM) (128)频移键控 (FSK) 调制 (134)相位(PM)调制 (140)相移键控 (PSK) 调制 (146)脉冲宽度(PWM)调制 (151)总和(SUM)调制 (157)频率扫描 (163)脉冲串模式 (172)辅助系统功能设置 (182)存储和调取 (183)选择远程接 (187)系统和设置 (191)通道功能设置 (195)双通道操作 (199)任意波形 (204)插入内置波形 (205)显示任意波形 (207)编辑任意波形 (214)输出任意波形 (223)存储/调取任意波形 (225)远程接口 (234)确立远程连接 (239)网络浏览器控制界面 (244)指令列表 (252)4状态寄存器指令 (260)接口设置指令 (263)应用指令 (264)输出指令 (270)脉冲设置指令 (279)幅值调制(AM)指令 (283)振幅键控(ASK)指令 (288)频率调制(FM)指令 (292)频移键控(FSK)指令 (297)相位调制(PM)指令 (301)相位键控(PSK)指令 (305)总和调制(SUM)指令 (309)脉宽调制(PWM)指令 (314)频率扫描(Sweep)指令 (319)脉冲串模式(Burst)指令 (329)任意波形(ARB)指令 (340)计频器(Counter)指令 (348)相位 (Phase) 指令 (350)耦合(Couple)指令 (351)存储和调取指令 (354)错误信息 (356)SCPI状态寄存器 (369)附录 MFG-2000系列规格 (375)EC符合性声明书 (385)GLOBL HEADAQARTERS (386)任意波内建波形 (387)索引 (395)56安全说明本章节包含操作和存储信号发生器时必须遵照的重要安全说明。
MCS-2110 CS-2110系列芯片控制器产品说明书

U O n/Off orProportional Control UC onvenient Receptacles for Input andOutput Connections U C ompact Benchtop Design U 15 A Maximum Output UJ , K Thermocouple or RTD Input U O n/Off Power SwitchThe MCS-2110 and CS-2110 seriesbenchtop controllers are ideal for laboratory use and applications requiring portable temperature control. Pre-wired input andoutput receptacles at the back of the case enable quick and easyconnections to power, thermocouple or RTD input and power output.Thermocouple models use universal female connector to accept either a miniature or standard male connector. RTD models use a 3-prong female connector to accept an OTP-U-M type connector. A 120 Vac, 15 A maximum output receptacle can be used to control heaters or other devices up to 1800 watts. TheMCS-2110 and CS-2110controllers operate in either on/off or proportional control modes, selectable by a simple front panel adjustment.Control ModesThe CN2110 provides precise, solid state proportion control with automatic reset (PI) that will control most heating applications. On/off control may be selected forapplications where maximum output life (load switching) is needed.All models operate on 120 Vac, 15 A and include a 1.5 m (5') power cord.MCS-2110 SeriesBenchtop Temperature ControllersMCS-2110J-R shownsmaller than actual size.Ordering Examples: MCS-2110J-R , benchtop controller, single 15 A relay output, Type J thermocouple input, -73 to 760°C (-100 to 1400°F) range.OCW-3, OMEGACARE SM extends standard 1-year warranty to a total of 4 years.SpecificationsControl Modes: On/off, PI-proportional with integralControl AdjustmentsProportional Band: sensor range Automatic Reset:0.0 to 99.9 repeats/minuteCycle Time: 0.1 to 60.0 seconds On/Off Deadband: 1° to 100°F or °C Setpoint Upper Limit: Sensor range °F or °C Setpoint Lower Limit: Sensor range °F or °C Output Limit: 0 to 100%Alarm Adjustments:Type: Absolute high or lowSetpoint: Sensor range °F or °CAlarm Dead Band: 0° to 100°F or °C Control/Alarm Outputs Relay: Form “A”, 120 Vacresistive loads at 30 seconds, cycle time; 15 A, 500,000 operations; 15 A, 1 million operations; 5 A, 5 million operationsSolid State Relay: Up to 10 A at 40°C Sensor Input: Switch selectable, J, K thermocouple or RTDInput Update Rate: 4 samples/s Readout Stability:J and K Thermocouple: ±1°F/10°F change in ambient temperature RTD: ±0.5 per 10°F change in ambient temperatureOpen Sensor and Out-of-Range Conditions: Displays “SENS”; control output 0%Instrument Power: 120 Vac <10 Va Operating Environment: 0° to 65°C (32°to 150°F)Enclosure Material: High-temperature ABS plastic rated for 0° to 175°F Front Panel: NEMA 4X construction Influence of Line Voltage Variation: ±0.1% of sensor span per 10% change in nominal line voltage Noise Rejection:Common Mode Noise: <2°F with 230 Vac, 60 Hz applied from sensor input to groundSeries Mode Noise: <2°F with 100 mV, peak-to-peak series mode noiseRFI: Typically <0.5% of sensor span at distance of 1 m (3.1’) from a transmitter of 4 W at 464 MHz Sensor Leadwire Effect:RTD: ±0.1% of sensor span per 20Ω balanced leadwire resistanceThe UPJ-K-F universal connector accepts eitherRear ViewMC OutputAC powerOMEGACARE SM extended warranty program isavailable for models shown on this page. Ask your sales representative for full details when placing an order. OMEGACARE SM covers parts, labor and equivalent loaners.。
西门子 KTP600 基本面板操作指南说明书
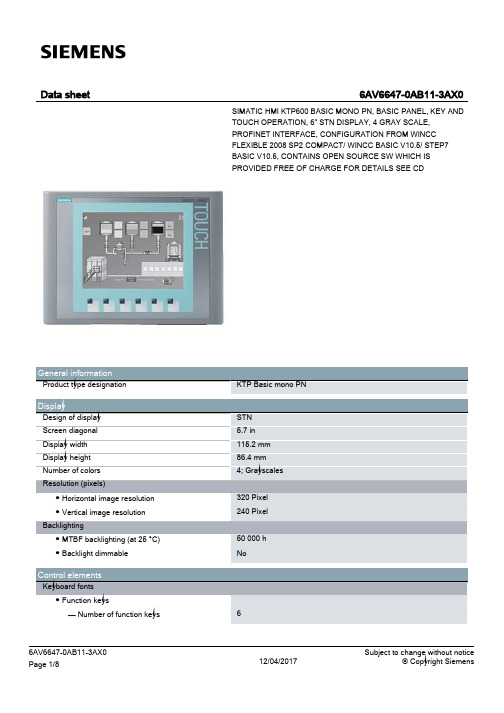
6AV6647-0AB11-3AX0 Page 2/8
12/04/2017
Subject to change without notice © Copyright Siemens
Number of industrial Ethernet interfaces Number of RS 485 interfaces Number of RS 422 interfaces Number of RS 232 interfaces Number of USB interfaces Number of 20 mA interfaces (TTY) Number of parallel interfaces Number of other interfaces Number of SD card slots With software interfaces Industrial Ethernet
● Industrial Ethernet status LED
Protocols PROFINET Supports protocol for PROFINET IO IRT PROFIBUS MPI Protocols (Ethernet) ● TCP/IP ● DHCP ● SNMP ● DCP ● LLDP WEB characteristics ● HTTP ● HTML Further protocols ● CAN ● EtherNet/IP ● MODBUS
Operating systems proprietary pre-installed operating system ● Windows CE
Yes Yes Yes
Yes Yes Yes Yes Yes Yes Yes
- 1、下载文档前请自行甄别文档内容的完整性,平台不提供额外的编辑、内容补充、找答案等附加服务。
- 2、"仅部分预览"的文档,不可在线预览部分如存在完整性等问题,可反馈申请退款(可完整预览的文档不适用该条件!)。
- 3、如文档侵犯您的权益,请联系客服反馈,我们会尽快为您处理(人工客服工作时间:9:00-18:30)。
Then for every � > 0, Pr {|An − µn | > �} ≤ (1)
(a) Prove the Generalized Pairwise Independent Sampling Theorem.
Solution. Essentially identical to the proof of Theorem 21.5.1 in the text, except that G gets re
(b) What would the Markov bound be on the probability that the gambler will win at least 108 hands on a given day? Solution. The expected n by Markov, Pr {R ≥ 108} ≤ 54/108 = 1/2. � (c) Assume the outcomes of the card games are pairwise independent. What is the variance in the number of hands won per day? Solution. The variance can also be calculated using linearity of variance. For an individual hand the variance is p(1 − p) where p is the probability of winning. Therefore the variance is 120(1/6)(5/6) + 60(1/2)(1/2) + 20(1/5)(4/5) = 523/15 = 34
placed by X and Var [Gi ] by b, with the equality where the b is first used becoming ≤. � (b) Conclude that the following holds: Corollary (Generalized Weak Law of Large Numbers). For every � > 0,
Solutions to In-Class Problems Week 13, Fri.
3
Theorem (Generalized Pairwise Independent Sampling). Let X1 , X2 , . . . be a sequence of pairwise independent random variables such that Var [Xi ] ≤ b for some b ≥ 0 and all i ≥ 1. Let An ::= X1 + X2 + · · · + Xn , n µn ::= E [An ] . b 1 · . �2 n
n→∞
lim Pr {|An − µn | ≤ �} = 1.
Solution. Pr {|An − µn | ≤ �} =1 − Pr {|An − µn | > �} ≥1 − b/(n�2 ) and for any fixed �, this last term approaches 1 as n approaches infinity. (by (1)), �
(A very slightly better bound of 0.01182 comes from using the one-sided Chebyshev bound from Problem ??.) �
Problem 3. The proof of the Pairwise Independent Sampling Theorem 21.5.1 was given for a sequence R1 , R2 , . . . of pairwise independent random variables with the same mean and variance. The theorem generalizes straighforwardly to sequences of pairwise independent random vari ables, possibly with different distributions, as long as all their variances are bounded by some constant.
13 15 .
� (d) What would the Chebyshev bound be on the probability that the gambler will win at least 108 hands on a given day? You may answer with a numerical expression that is not completely evaluated. Solution. Pr {R − 54 ≥ 54} ≤ Pr {|R − 54| ≥ 54} ≤ V ar[R] 523 = ≈ 0.01196. 2 15(54)2 54
Solutions to In-Class Problems Week 13, Fri.
Problem 1. A herd of cows is stricken by an outbreak of cold cow disease. The disease lowers the normal body temperature of a cow, and a cow will die if its temperature goes below 90 degrees F. The disease epidemic is so intense that it lowered the average temperature of the herd to 85 degrees. Body temperatures as low as 70 degrees, but no lower, were actually found in the herd. (a) Prove that at most 3/4 of the cows could have survived. Hint: Let T be the temperature of a random cow. Make use of Markov’s bound. Solution. Let T be the temperature of a random cow. Then the fraction of cows that survive is the probability that T ≥ 90, and E [T ] is the average temperature of the herd. Applying Markov’s Bound to T : Pr {T ≥ 90} =≤ E [T ] 85 17 = = . 90 90 18
MIT OpenCourseWare
6.042J / 18.062J Mathematics for Computer Science
Spring 2010
For information about citing these materials or our Terms of Use, visit: /terms.
Massachusetts Institute of Technology 6.042J/18.062J, Spring ’10: Mathematics for Computer Science Prof. Albert R. Meyer
May 7
revised May 5, 2010, 857 minutes
But 17/18 > 3/4, so this bound is not good enough. Instead, we apply Markov’s Bound to T − 70: Pr {T ≥ 90} = Pr {T − 70 ≥ 20} ≤ E [T − 70] = (85 − 70)/20 = 3/4. 20 � (b) Suppose there are 400 cows in the herd. Show that the bound of part (a) is best possible by giving an example set of temperatures for the cows so that the average herd temperature is 85, and with probability 3/4, a randomly chosen cow will have a high enough temperature to survive. Solution. Let 100 cows have temperature 70 degrees and 300 have 90 degrees. So the probability that a random cow has a high enough temperature to survive is exactly 3/4. Also, the mean temperature is (1/4)70 + (3/4)90 = 85. So this distribution of temperatures satisfies the conditions under which the Markov bound im plies that the probability of having a high enough temperature to survive cannot be larger than 3/4. �
Creative Commons