冲压件工艺性分析与计算
冲压模具课程设计说明书 2
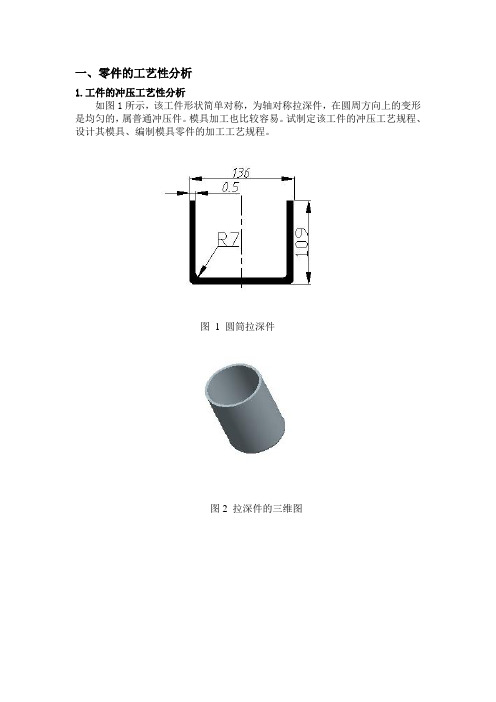
一、零件的工艺性分析1.工件的冲压工艺性分析如图1所示,该工件形状简单对称,为轴对称拉深件,在圆周方向上的变形是均匀的,属普通冲压件。
模具加工也比较容易。
试制定该工件的冲压工艺规程、设计其模具、编制模具零件的加工工艺规程。
图1 圆筒拉深件图2 拉深件的三维图2.工件材料化学成分和机械性能分析(1)材料分析工件的材料为08钢,属于优质碳素结构钢,优质沸腾钢,强度、硬度低,冷变形塑性很好,可深冲压加工,焊接性好。
成分偏析倾向大,时效敏感性大,故冷加工时应采用消除应力热处理或水韧处理,防止冷加工断裂。
08钢的主要机械性能如下:σ(兆帕) 280-390抗拉强度bσ(兆帕) 180屈服强度s抗剪强度(兆帕) 220-310延伸率δ 32%(2)结构分析工件为一窄凸缘筒形件,结构简单,圆角半径为r=7,厚度为t=0.5mm,满足筒形拉深件底部圆角半径大于一倍料厚的要求,因此,零件具有良好的结构工艺性。
(3)精度分析工件上尺寸均为未注公差尺寸,普通拉深即可达到零件的精度要求。
经上述分析,产品的材料性能符合冷冲压加工要求。
在零件工艺性分析的基础上制定其工艺路线如下:零件的生产包括落料、拉深(需计算确定拉深次数)、修边(采用机械加工)等工序,为了提高生产效率,可以考虑工序的复合,经比较决定采用落料与第一次拉深复合。
二、工件的拉深工艺分析及计算1.毛坯尺寸计算(1)计算原则相似原则:拉深前坯料的形状与拉深件断面形状相似;等面积原则:拉深前坯料面积与拉深件面积相等。
(2)计算方法由以上原则可知,旋转体拉深件采用圆形毛坯,其直径按面积相等的原则计算。
计算坯料尺寸时,先将拉深件划分为若干便于计算的简单几何体,分别求出其面积后相加,得拉深件总面积A。
图3 拉深件的坯料计算如图3所示,筒形件坯料尺寸,将圆筒件分成三个部分,每个部分面积分别为:(3)确定零件修边余量由于板料的各向异性和模具间隙不均等因素的影响,拉深后零件的边缘不整齐,甚至出现耳子,需在拉伸后进行修边。
冲压工艺过程设计-实验
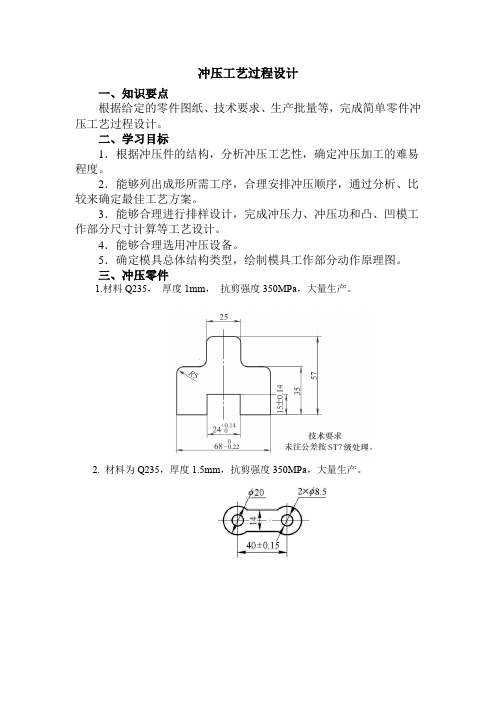
冲压工艺过程设计
一、知识要点
根据给定的零件图纸、技术要求、生产批量等,完成简单零件冲压工艺过程设计。
二、学习目标
1.根据冲压件的结构,分析冲压工艺性,确定冲压加工的难易程度。
2.能够列出成形所需工序,合理安排冲压顺序,通过分析、比较来确定最佳工艺方案。
3.能够合理进行排样设计,完成冲压力、冲压功和凸、凹模工作部分尺寸计算等工艺设计。
4.能够合理选用冲压设备。
5.确定模具总体结构类型,绘制模具工作部分动作原理图。
三、冲压零件
1.材料Q235,厚度1mm,抗剪强度350MPa,大量生产。
2. 材料为Q235,厚度1.5mm,抗剪强度350MPa,大量生产。
3.
4.
5.
6.中批量生产
7.
8.中批量生产
9.材料Q235,料厚2mm
10.材料为Q235钢,料厚t=1.5mm,中批量生产。
11.材料为Q235钢,料厚t=2mm,中批量生产。
13.材料为Q235钢,料厚t=2mm
14.材料为Q235钢,料厚t=2mm
15.材料为Q235钢,料厚t=1.2mm,所有尺寸公差取ST7级,大批量生产。
16.材料为Q235钢,料厚t=1.5mm,中批量生产。
18.材料为10钢,料厚t=0.5mm,中批量生产。
19.材料为08钢
20.
四、实验报告内容
1.冲压件的工艺性分析
2.分析工艺方案,选择最佳工艺方案
3.冲压工艺计算(排样及材料利用率,冲压力,工作零件尺寸计算)
4.模具结构类型(总体设计:送料方式,定位方式,卸料方式,出件方式,导向方式)
5.冲压设备的选择。
汽车车门制造冲压工艺分析

汽车车门制造冲压工艺分析摘要:在对汽车车门进行制造时,所使用的材料以及制造工艺都会影响车门的强度与钢度。
大部分汽车车门的制造过程是冲压,焊装,涂装最后与车身其他部件总装为一个白车身。
汽车车门的制造工艺是整车工艺的一个缩影,从小见大,了解它也就能帮助我们了解整车制造工艺。
笔者介绍了一种冲压工艺方法在汽车车门内板上的具体应用,降低了拉延模具制造难度,降低了制造成本。
关键词:车门材料;冲压工艺;分析一、制件冲压工艺概述冲压件一般需经过拉延/修边+冲孔/整形(或翻边)+冲孔等工序才能得到合格产品。
对于稍微复杂的钣金件,通过拉延仅能得到冲压件大概轮廓,经过后序的修边冲孔,再配合整形翻边等工序才能得到最终零件。
整形翻边等工艺可以降低拉延深度,简化拉延模面的形状,提高成形性,也就是提高了模具制造的可实现性及易操作性。
以常见的车门外板为例,展示普通冲压外覆盖件的工艺流程。
车门外板采用4步工序实现了零件的制造过程,因车门外板拉延深度较小,型面相对简单,因此采用的是一次拉延成形的方法,配合后面的修边、冲孔、翻边工序而成,这种一次拉延的冲压工艺方案是通过拉延得到基本的零件轮廓,后期的整形、翻边等都是对R角的微小型面进行小范围改变,这种工艺方法在实际生产中广泛应用,但同时也存在如下缺点和不足:(1)一次拉延工序得到几乎整个零件的全部形状特征,后工序主要是修边、冲孔、翻边,以及对局部的(小面积的)难以一次成形的型面做整形,得到零件。
此工艺比较死板,灵活变动的空间较小,限制了工艺设计的多样性。
(2)因为是一次拉延得到了零件的基本形状,所以拉延深度是固定的,零件的造型决定了拉延深度的大小,也就决定了成形的可实现性。
对于拉延深度较大的零件就存在拉延状态不稳定及拉延开裂的风险。
(3)拉延深度较大的零件拉延工序存在拉毛风险,为减少拉毛的概率,对于拉延模质量要求较高,比如硬度、光洁度都要提升一个等级,同时也要加强模具的日常保养维护,增加了制造成本。
冲压件工艺性分析

一、止动件冲压件工艺性分析1、零件材料:为Q235-A钢,具有良好的冲压性能,适合冲裁;2、零件结构:相对简单,有2个© 20mn t勺孔;孑L与孔、孔与边缘之间的距离也满足要求,最小壁厚为14mm(© 20mn的孔与边框之间的壁厚)3、零件精度:全部为自由公差,可看作IT14级,尺寸精度较低,普通冲裁完全能满足要求。
查表得各零件尺寸公差为:外形尺寸:130°1、48°).62、60_°.74、R403、R60』%内型尺寸:2000.052孔中心距:60± 0.37二、冲压工艺方案的确定完成该零件的冲压加工所需要的冲压基本性质的工序只有落料、冲孔两道工序。
从工序可能的集中与分散、工序间的组合可能来看,该零件的冲压可以有以下几种方案。
方案一:落料-冲孔复合冲压。
采用复合模生产。
方案二:冲孔-落料级进冲压。
采用级进模生产。
方案一只需一副模具,工件的精度及生产效率都较高,工件最小壁厚14mn 大于凸凹模许用最小壁厚3.6mm--4.0mm模具强度好,制造难度中等,并且冲压后成品件可通过卸料板卸下,清理方便,冲压模具设计0用川和屠”口匚JkTJIDliiftL 2闻1坤丘貝5「1「节操作简单。
方案二也只需一副模具,生产效率高,操作方便,工件精度也能满足要求,但是模具结构复杂,制造加工,模具成本较高。
结论:采用方案一为佳三、模具总体设计(1)模具类型的选择由冲压工艺分析可知,采用复合模冲压,所以模具类型为复合模。
(2)定位方式的选择因为该模具采用的是条料,控制条料的送进方向采用导料板,无侧压装置。
控制条料的送进步距采用挡料销定距。
而第一件的冲压位置因为条料长度有一定余量,可以靠操作工目测来定。
(3)卸料、出件方式的选择因为工件料厚为1.5mm相对较薄,卸料力也比较小,故可采用弹性卸料。
又因为是倒装式复合模生产,所以采用上出件比较便于操作与提高生产效率。
基于CAE技术的冲压件工艺性分析

结 果 必 须重 新 计 算 , 所 以 说 正 确 选 择 制 件 的
材料 至关 重要 。 6 些 零 件 受 搭 接 - 关 系及 零 件 特 征 限 制 ,
图 1 更 换 材 料 前后 变薄 量 对 比 无 法 对 产 品 进 行 更 改 ,
( ) C 4材 料 , 大 变 薄 量 4 % 而 其 材 质 又 无 法 满 足 aD 0 最 4
响 到 后 序 模 具 的 li . 现 场 调 试 时 间 以 及 最 终 模 具 J_ 和 tr -
的试模 次数 。冲压件 的工艺 性是 指 冲压件 生产 加工
的 难 易 程 度 。 压 4- 冲  ̄ 的加 工 工 序 很 多 , 个 _ 序 的工 每 - 1 2
艺 性又 各不 相 同 , 即使 是 同 一 个 零 件 , 同 的 生 产 厂 不 家 、 同 的设 计 人 员 , 工 艺 设 计 也 不 尽 相 同 。 不 其 因此 , 在 满 足 使 用 要 求 的前 提 下 , 件 设 计 应 力 求 简 单 、 零 规 则 、 称 , 便 节省 原 材料 , 少 冲压 工序 和模 具套 对 以 减 数 , 高 模 具 使 用 寿 命 , 终 使 零 件 成 本 降 到 最 低 _ 提 最 1 1 。
33 修 边 合 理 性 分 析 . 对 于 零 件 最 初 的边 界 确 定 ,设 计 者 更 多 考 虑 的 是 边 界 的 光 顺 性 ,但 在 某 些 情 况 下 这 样 的 边 界 反 而 导 致 修 边 时 模 具 的 刃 口太 弱 , 至 无 法 修 边 。 类 缺 甚 此
制造教 学科研
中 图 分 类 号 : G3 6 3 计 和 模 具 制 造 的 时 间 , 且 可 以保 证 零 件 而
冲压模具设计说明书
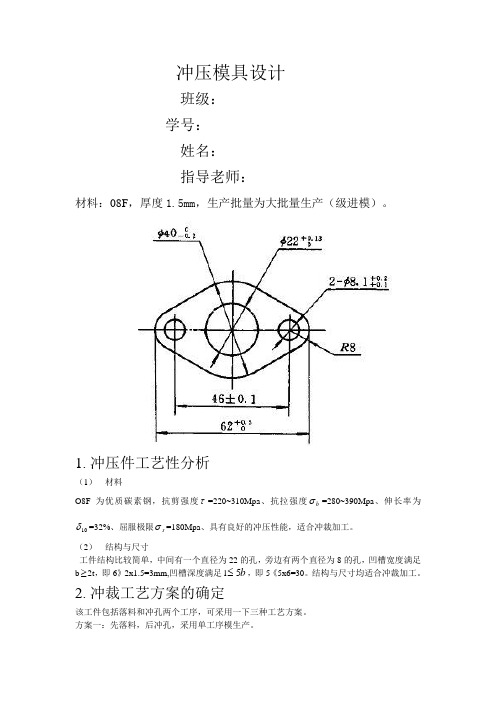
冲压模具设计班级: 学号: 姓名: 指导老师:材料:08F ,厚度1.5mm ,生产批量为大批量生产(级进模)。
1. 冲压件工艺性分析(1) 材料O8F 为优质碳素钢,抗剪强度τ=220~310Mpa 、抗拉强度b σ=280~390Mpa 、伸长率为10δ=32%、屈服极限s σ=180Mpa 、具有良好的冲压性能,适合冲裁加工。
(2) 结构与尺寸工件结构比较简单,中间有一个直径为22的孔,旁边有两个直径为8的孔,凹槽宽度满足b ≥2t ,即6》2x1.5=3mm,凹槽深度满足l b 5≤,即5《5x6=30。
结构与尺寸均适合冲裁加工。
2. 冲裁工艺方案的确定该工件包括落料和冲孔两个工序,可采用一下三种工艺方案。
方案一:先落料,后冲孔,采用单工序模生产。
方案二:落料——冲孔复合冲压,采用复合模生产。
方案三:冲孔——落料级进冲压,采用级进模生产。
综合考虑后,应该选择方案三。
因为方案三只需要一副模具,生产效率高,操作方便,工件精度也能满足要求,所以应该选用方案三比较合算。
3.选择模具总体结构形式由于冲压工艺分析可知,采用级进冲压,所以模具类型为级进模。
(1)确定模架及导向方式采用对角导柱模架,这种模架的导柱在模具对角位置,冲压时可防止由于偏心力矩而引起模具歪斜。
导柱导向可以提高模具寿命和工件质量,方便安装调整。
(2)定位方式的选择该冲件采用的柸料是条料,控制条料的送进方向采用导料板,无侧压装置;控制条料的送进步距采用侧刃粗定距;用导正销精定位保证内外形相对位置的精度。
(3)卸料、出件方式的选择因为该工件料厚1.5mm,尺寸较小,所以卸料力也较小,故选择弹性卸料,下出件方式。
4.必要的工艺计算(1)排样设计与计算该冲件外形大致为圆形,搭边值为a1=1.5mm,条料宽度为43.57mm,步距为A=88.4mm,一个步距的利用率为63.98%。
见下图S=1668.7-11x11x3.14-2x4x4x3.14=1188.28项目分类计算方法和结果排样冲裁件面积面积为1188.28mm条料宽度B=39.97+1.8+1.8=43.57mm 步距A=86.9+1.5=88.4mm材料利用率η冲压力的相关计算F 冲=KLt b τ=1.3*275*1.5*300=160875N F 卸=K 1F=0.04*160875=64350N F 推=nK 2F=4*0.055*160875=35392.5N F= F 冲+ F 卸+ F 推=260617.5N (3)计算模具压力中心代入公式X0=132.25115.69132.25396.14874.61132.2519.44115.6993.26132.250396.148++++++X X X X =19.73Y0=132.25115.69132.25396.14827.13132.250115.69)27.13(132.250396.148+++++-+X X X X =0(4) 计算凸、凹模工作部分尺寸并确定其制造公差 由于凸凹模的形状相对简单且材料较厚,冲裁间隙较大,可采用分开加工法确定凸凹模的刃口尺寸及公差。
冲压件工艺分析
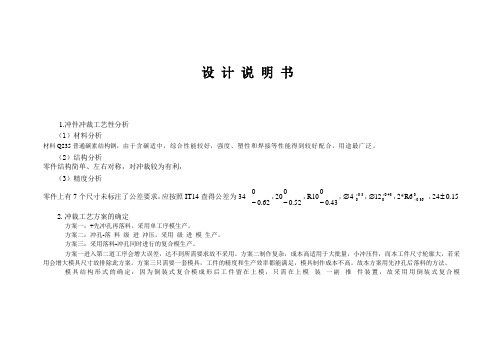
设 计 说 明 书1.冲件冲裁工艺性分析 (1)材料分析材料Q235普通碳素结构钢,由于含碳适中,综合性能较好,强度、塑性和焊接等性能得到较好配合,用途最广泛。
(2)结构分析零件结构简单、左右对称,对冲裁较为有利,(3)精度分析零件上有7个尺寸未标注了公差要求,应按照IT14查得公差为34.00-,2052.00-,R1043.00-,4∅3.00+,43.0012+∅,2*R6036.0- ,2415.0± 2.冲裁工艺方案的确定方案一:+先冲孔再落料。
采用单工序模生产。
方案二:冲孔-落 料 级 进 冲压。
采用 级 进 模 生产。
方案三:采用落料-冲孔同时进行的复合模生产。
方案一进入第二道工序会增大误差,达不到所需要求故不采用。
方案二制作复杂,成本高适用于大批量,小冲压件,而本工件尺寸轮廓大,若采用会增大模具尺寸故排除此方案。
方案三只需要一套模具,工件的精度和生产效率都能满足,模具制作成本不高。
故本方案用先冲孔后落料的方法。
模具结构形式的确定:因为倒装式复合模成形后工件留在上模,只需在上模 装 一副 推 件装置,故采用用倒装式复合模材料Q235 t=2一、 冲裁工艺计算 (一)凸、凹模刃口尺寸计算查表得Z min=0.246,Zmax=0.36, Z max-Z min=0.074.落料件 :3462.00-,2052.00-,R1043.00-. ,R6036.0- ,X=0.5 (3462.00-) : D A =(D max – x △)A0δ+=33.690.030+D T =( D A –Z min) 0T δ-= 33.44400.02- (2052.00-): D A =19.75025.00+ , D T =19.50402.00+(1043.00-):D A =9.68502.00+ , D T =9.439002.0-(R6036.0-) :D A =5.98202.00+ , D T =5.736002.0-冲孔件,4∅3.00+,43.0012+∅,3.0012+∅ : d T =(d min + x △) 0T δ-= 12.21500.02-dA = (d min + x△+ Z min) Aδ+=12.46102.0+4∅43 .0+: dT =4.1500.02-,dA=4.39602.0+孔中心距2415.0±LA=(Lmin+0.5△)±△/8= 25±0.0375排样分析零件形状,应采用单直排的排样方式,零件可能的排样方式有下图所示的两种。
阶梯型钢制零件的冲压工艺分析及模具设计
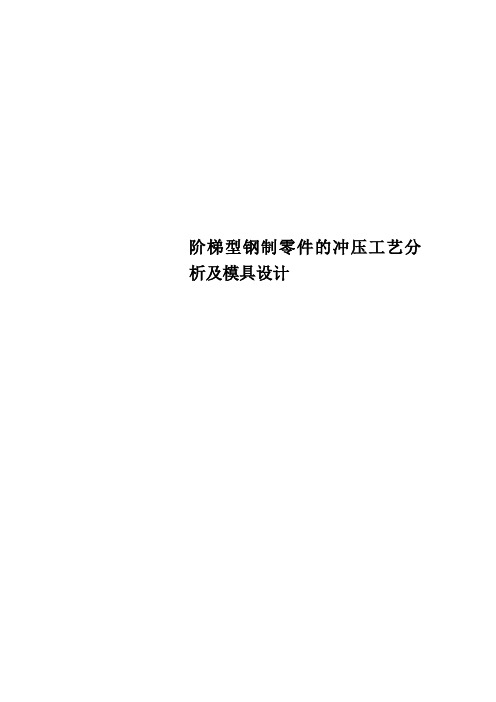
阶梯型钢制零件的冲压工艺分析及模具设计摘要拉深是利用模具使平板毛坯变成为开口的空心零件的冲压方法,用拉深工艺可以制成筒形、阶梯形、锥形、抛物面形、盒形和其他不规则形状的薄壁零件,其中又以筒形件简单和多见,而有凸缘筒形件又分为宽凸缘和窄凸缘件。
在拉深工艺设计时,必须知道冲压件能否一次拉出,这就引出了拉深系数的概念。
拉伸系数决定于每次拉深时允许的极限变形程度。
在多次拉深中,对于宽凸缘拉深件,则应在第一次拉深时,就拉成;零件所要求的凸缘直径,而在以后各次拉深中,凸缘直径保持不变。
为了保证以后拉深时凸缘不变形,宽凸缘拉深件首次拉入凹模的材料应比零件最后拉深部分实际所需材料多3%~5%,这些多余材料在以后各次拉深中,逐渐将减少部分材料挤回到凸缘部分,使凸缘增厚,从而避免拉裂。
关键词:拉深;成型工艺;拉裂AbstractThe deep drawing is a pressing process. It can make a sheet blank into a uncork piece with die. A process with deep drawing can manufacture workpiece in many shapes. And the tappered workpiece which includes broad protruding edge workpieces and narrow protruding edge workpieces is the most usual.The coefficient of the deep drawing is important when you have to be sure whether it can make it in one time. The coefficient lies on the limit of the deformation degree every deep drawing process allows.Key words: deep drawing; forming process; restriction crack目录摘要 (I)Abstract (II)1 绪论 (1)2 拉深件的工艺性分析 (3)2.1 分析工件的冲压工艺性 (3)工件形状 (3)2.2 08F材料的化学成分和机械性能 (4)3 拉深工序计算 (5)3.1 阶梯形筒形件的拉深工序计算原则 (5)阶梯形件拉深工序计算程序 (5)3.2 必要的工序计算 (5)修边余量δ的确定 (5)毛坯尺寸计算 (5)判断阶梯筒形部分的拉深次数 (7)确定工件的制造工序步骤 (8)画出拉深工序图 (9)4 工序压力计算和压力机的选择 (11)4.1 压力机的选择原则 (11)4.2 落料拉深工序压力计算 (11)排样图的设计 (11)计算落料拉深复合工序压力 (15)初选压力机 (17)校核压力机的电动机功率 (18)4.3 二次拉深工序压力计算 (19)计算二次拉深工序压力 (19)初选压力机 (20)校核压力机的电动机功率 (21)4.4 扩口力计算 (22)计算扩口工序压力 (22)初选压力机 (23)校核压力机的电动机功率 (23)5 模具结构设计 (25)5.1 落料拉深工序模具设计 (25)落料拉伸复合模选用原则 (25)模具工作部分尺寸和公差计算 (25)模具其他零件的结构尺寸计算 (27)5.2 二次拉深工序模具设计......................... 错误!未定义书签。
冲压件工艺性分析与计算
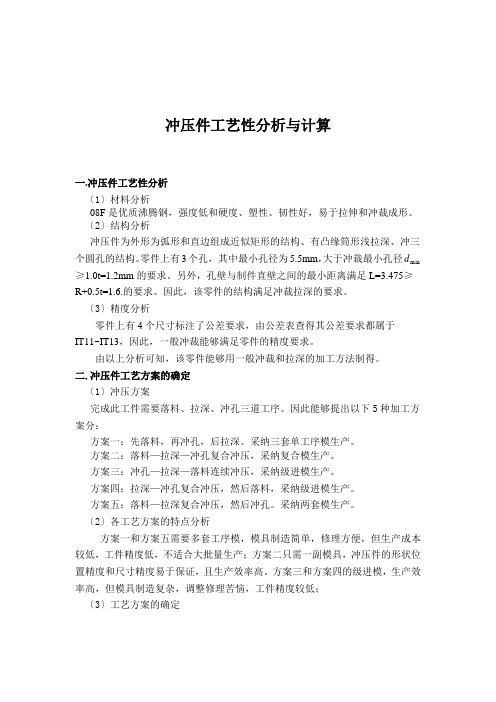
冲压件工艺性分析与计算一.冲压件工艺性分析〔1〕材料分析08F是优质沸腾钢,强度低和硬度、塑性、韧性好,易于拉伸和冲裁成形。
〔2〕结构分析冲压件为外形为弧形和直边组成近似矩形的结构、有凸缘筒形浅拉深、冲三个圆孔的结构。
零件上有3个孔,其中最小孔径为5.5mm,大于冲裁最小孔径dmin ≥1.0t=1.2mm的要求。
另外,孔壁与制件直壁之间的最小距离满足L=3.475≥R+0.5t=1.6.的要求。
因此,该零件的结构满足冲裁拉深的要求。
〔3〕精度分析零件上有4个尺寸标注了公差要求,由公差表查得其公差要求都属于IT11~IT13,因此,一般冲裁能够满足零件的精度要求。
由以上分析可知,该零件能够用一般冲裁和拉深的加工方法制得。
二.冲压件工艺方案的确定〔1〕冲压方案完成此工件需要落料、拉深、冲孔三道工序。
因此能够提出以下5种加工方案分:方案一:先落料,再冲孔,后拉深。
采纳三套单工序模生产。
方案二:落料—拉深—冲孔复合冲压,采纳复合模生产。
方案三:冲孔—拉深—落料连续冲压,采纳级进模生产。
方案四:拉深—冲孔复合冲压,然后落料,采纳级进模生产。
方案五:落料—拉深复合冲压,然后冲孔。
采纳两套模生产。
〔2〕各工艺方案的特点分析方案一和方案五需要多套工序模,模具制造简单,修理方便,但生产成本较低,工件精度低,不适合大批量生产;方案二只需一副模具,冲压件的形状位置精度和尺寸精度易于保证,且生产效率高。
方案三和方案四的级进模,生产效率高,但模具制造复杂,调整修理苦恼,工件精度较低;〔3〕工艺方案的确定比较三个方案,采纳方案五生产更为合理。
尽管模具结构较其他方案复杂,但 由于零件的几何形状简单对称,模具制造并不困难。
因此,在本设计中,将采纳落料、拉深复合模的设计方案。
三.冲压工艺运算〔1〕凸、凹模刃口尺寸的运算依照零件形状特点,刃口尺寸运算采纳分开制造法。
落料件尺寸的运算,落料差不多运算公式为A 0max A )(δ+-=X ΔD D0min max 0min A T T T )()(δδ----=-=Z X ΔD Z D D尺寸44mm ,经查得该零件凸、凹模最小间隙Z min =0.126mm ,最大间隙Z max =0.180mm ;凸模制造公差m m 02.0T =δ,凹模制造公差m m 03.0A =δ。
冲压件工艺性分析讲解
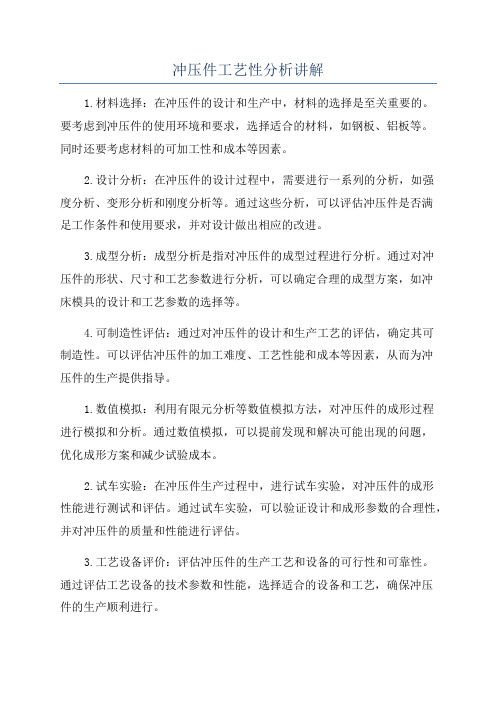
冲压件工艺性分析讲解1.材料选择:在冲压件的设计和生产中,材料的选择是至关重要的。
要考虑到冲压件的使用环境和要求,选择适合的材料,如钢板、铝板等。
同时还要考虑材料的可加工性和成本等因素。
2.设计分析:在冲压件的设计过程中,需要进行一系列的分析,如强度分析、变形分析和刚度分析等。
通过这些分析,可以评估冲压件是否满足工作条件和使用要求,并对设计做出相应的改进。
3.成型分析:成型分析是指对冲压件的成型过程进行分析。
通过对冲压件的形状、尺寸和工艺参数进行分析,可以确定合理的成型方案,如冲床模具的设计和工艺参数的选择等。
4.可制造性评估:通过对冲压件的设计和生产工艺的评估,确定其可制造性。
可以评估冲压件的加工难度、工艺性能和成本等因素,从而为冲压件的生产提供指导。
1.数值模拟:利用有限元分析等数值模拟方法,对冲压件的成形过程进行模拟和分析。
通过数值模拟,可以提前发现和解决可能出现的问题,优化成形方案和减少试验成本。
2.试车实验:在冲压件生产过程中,进行试车实验,对冲压件的成形性能进行测试和评估。
通过试车实验,可以验证设计和成形参数的合理性,并对冲压件的质量和性能进行评估。
3.工艺设备评价:评估冲压件的生产工艺和设备的可行性和可靠性。
通过评估工艺设备的技术参数和性能,选择适合的设备和工艺,确保冲压件的生产顺利进行。
4.成本分析:对冲压件的生产成本进行分析和评估。
通过对材料、设备、工艺和劳动力等成本的计算和比较,确定生产成本的构成和控制方案,提高生产效率和降低成本。
冲压件工艺性分析的目的是为了确保产品的质量和生产效率。
通过对冲压件的设计和生产过程进行分析和评估,可以发现和解决潜在的问题,优化冲压板的工艺设计和生产流程,提高产品的质量和生产效率。
同时,工艺性分析还可以为产品的质量控制和工艺改进提供参考和依据。
综上所述,冲压件工艺性分析是冲压件生产过程中不可或缺的环节。
通过对材料、设计、成型和成本等多个方面的分析和评估,可以确保冲压件的质量和生产效率。
冲压件工艺可行性分析
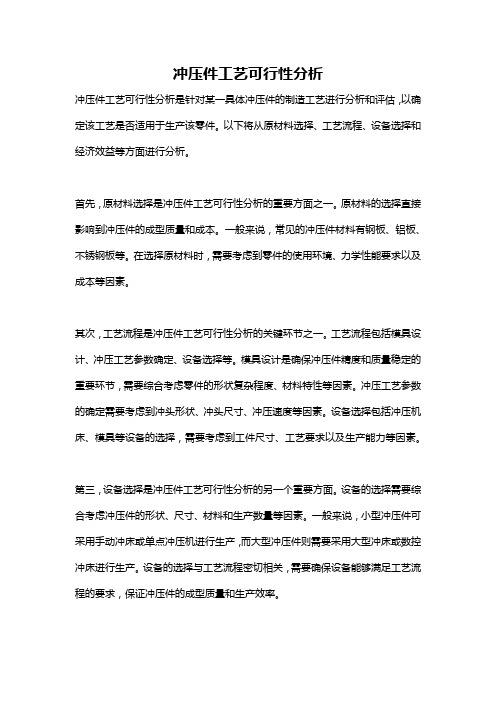
冲压件工艺可行性分析冲压件工艺可行性分析是针对某一具体冲压件的制造工艺进行分析和评估,以确定该工艺是否适用于生产该零件。
以下将从原材料选择、工艺流程、设备选择和经济效益等方面进行分析。
首先,原材料选择是冲压件工艺可行性分析的重要方面之一。
原材料的选择直接影响到冲压件的成型质量和成本。
一般来说,常见的冲压件材料有钢板、铝板、不锈钢板等。
在选择原材料时,需要考虑到零件的使用环境、力学性能要求以及成本等因素。
其次,工艺流程是冲压件工艺可行性分析的关键环节之一。
工艺流程包括模具设计、冲压工艺参数确定、设备选择等。
模具设计是确保冲压件精度和质量稳定的重要环节,需要综合考虑零件的形状复杂程度、材料特性等因素。
冲压工艺参数的确定需要考虑到冲头形状、冲头尺寸、冲压速度等因素。
设备选择包括冲压机床、模具等设备的选择,需要考虑到工件尺寸、工艺要求以及生产能力等因素。
第三,设备选择是冲压件工艺可行性分析的另一个重要方面。
设备的选择需要综合考虑冲压件的形状、尺寸、材料和生产数量等因素。
一般来说,小型冲压件可采用手动冲床或单点冲压机进行生产,而大型冲压件则需要采用大型冲床或数控冲床进行生产。
设备的选择与工艺流程密切相关,需要确保设备能够满足工艺流程的要求,保证冲压件的成型质量和生产效率。
最后,经济效益是冲压件工艺可行性分析的评估指标之一。
经济效益包括原材料成本、设备投资、生产效率等因素。
通过分析成本和效益之间的关系,可以评估冲压件工艺的可行性。
同时,还需要考虑市场需求和竞争情况,确保冲压件工艺在市场上有一定的竞争优势。
综上所述,冲压件工艺可行性分析需要考虑原材料选择、工艺流程、设备选择和经济效益等多个方面。
只有在综合考虑了这些因素后,才能确定冲压件工艺的可行性,并为冲压件的生产提供有效的参考和指导。
冲压件制程质量分析报告

冲压件制程质量分析报告冲压件制程质量分析报告1. 引言冲压件是制造业中常见的一种加工工艺,广泛应用于汽车、电子等行业。
冲压件的质量直接关系到产品的性能和使用寿命,因此对冲压件制程的质量进行分析十分必要。
2. 分析目标本次分析旨在对某公司生产的冲压件制程的质量进行评估,发现存在的问题并提出改进措施,以提高产品的质量。
3. 数据收集通过对该公司生产的一批冲压件的制程数据进行收集和整理,包括材料、工艺参数、设备情况等。
同时,还进行了对冲压件产品进行外观质量检测和尺寸精度测量。
4. 分析方法针对数据收集到的冲压件制程数据,采用统计学的方法进行分析。
主要包括以下几个方面的分析内容:4.1 材料分析通过对材料的化学成分、物理性能等进行测试,检查材料的质量是否符合要求,包括强度、硬度、韧性等指标。
4.2 工艺参数分析分析冲压件的工艺参数设置,包括模具的设计和制作、压力大小、速度等。
通过对工艺参数进行分析,找出可能存在的问题,如模具磨损、压力不均匀等。
4.3 设备分析对冲压机设备进行检查和分析,包括设备的稳定性、精度等。
通过检查设备是否存在异常状况或者故障,进一步确定影响冲压件质量的因素。
4.4 外观质量检测通过对冲压件外观质量的检测,包括表面光洁度、涂层质量等,找出存在的问题,如划痕、表面缺陷等。
4.5 尺寸精度测量对冲压件的尺寸进行测量,与设计图纸进行对比,以确定尺寸精度是否符合要求。
如存在尺寸偏差过大的问题,则需要对制程进行调整。
5. 结果分析通过上述的分析方法,得到了以下几个结果:5.1 材料质量良好,符合要求。
通过对材料的化学成分和物理性能进行测试,发现材料质量良好,各项指标均符合要求。
5.2 部分工艺参数需要进行调整。
通过分析工艺参数,发现一些模具的磨损程度较高,需要进行更换。
同时,还发现部分冲压机的压力不均匀,导致冲压件的质量不稳定。
因此,需要对模具和冲压机进行调整和维护。
5.3 设备存在一些问题。
冲压产能分析计算公式

冲压产能分析计算公式
在进行冲压产能分析时,需要考虑以下几个因素:
1.冲床的理论生产能力:冲床的生产能力是指冲床在理想状态下的最大冲压速度和冲程,以每分钟冲击次数(SPM)来衡量。
冲床的生产能力与冲床的型号、性能以及压力传递机构有关。
2.工艺参数的选择:冲压的工艺参数包括冲件的厚度、材料性质、冲孔直径、冲裁长度、冲击次数等。
这些参数的选择将直接影响到冲压件的产能和质量,需要根据产品的要求和设备的能力进行合理的选择。
3.产品的设计优化:在进行冲压产能分析时,需要对产品的结构进行优化设计,以最大限度地提高冲压的效率和质量。
例如,通过减小冲件的厚度、优化冲孔的位置和数量、合理设计冲裁的长度等,可以达到提高产能的效果。
在进行冲压产能分析时,可以采用以下公式进行计算:
1.冲床的理论生产能力计算公式:
产能(件/分)=[(冲床的冲击次数SPM)×(每次冲击的冲程)]/1000其中,冲床的冲击次数SPM可以通过冲床的技术手册或者设备厂家提供的数据得到,每次冲击的冲程可以通过观察冲床的冲程显示板得到。
2.工艺参数的选择公式:
例如,对于冲孔的直径和冲裁的长度可以通过以下公式计算:
冲孔直径(mm)= 冲件的厚度(mm)+ 余量(mm)
冲裁长度(mm)= 冲孔直径(mm)+ 余量(mm)
其中,冲件的厚度和冲孔直径可以根据产品的设计要求和材料的性质
进行选择,余量是为了确保冲孔和冲裁的合理性和准确性而增加的一定值。
通过以上公式的计算和分析,可以得到冲压工艺和设备的生产能力,
从而确定工艺参数和设备投资,进一步提高生产效率和降低生产成本。
冲压件设计

冲压与模具设计说明书1.冲压件工艺性分析该冲压件材料为08钢,具有良好的冲压性能,适合冲裁。
该冲压件结构相对简单,孔径为10mm,孔与边缘之间的最小距离为7mm,所有尺寸均满足冲压工艺的要求,适合冲裁。
所有尺寸公差取IT13级,满足普通冲裁的经济精度要求。
综合上述,该冲压件的冲压工艺性良好,适合冲压加工。
图1-12.模具工艺方案的确定由图1-1可以看出,生产该冲压件的冲压工序为落料和冲孔。
根据上述工艺分析的结果,可以采用下述几种方案。
方案一:先落料,后冲孔,采用单工序模生产。
方案二:落料冲孔复合冲压,采用复合模生产。
方案三:冲压、落料级进行冲压,采用级进模生产。
方案一的模具结构简单,但生产效率低,不能满足大量生产对效率的要求。
方案二的冲压件精度及生产效率都高,但模具比较复杂,制造难度大,而且难以实现自动化。
方案三的生产效率高,操作方便,易于实现自动化,冲压精度也能满足要求。
因此,选择方案三。
3.模具结构形式确定(1)模具类型的选择根据上述方案,选用级进模。
(2)凹模结构形式采用整体凹模(3)定位方式的选择利用导料板倒料和侧刃定距。
(4)卸料、出件方式的选择采用弹性卸料和下出件方式。
(5)导向方式的选择选用对角导柱的滑动导向方式。
4. 主要设计计算(1)排样设计 由于该工件为冲裁件,且外形与孔型结构都比较简单,因此可以直接进行排样设计。
根据工件的结构,选用有废料的单直排,由表查的搭边值为2mm ,侧搭边值为2.5mm ,则条料宽度为B=26mm+12mm+1.5×2.5+1×1.5=43.25mm(侧刃定距时,条料宽度的计算公式为B=(L+1.5a+nb),a 市侧搭边值;n 是侧刃数量,这里取1)进距为L=12mm+12mm+2mm=26mm图1-2此工件只需落料和冲孔两道工序,因此在排样时,第一工位利用侧刃冲去等于进距的料边进行定距,第二工位冲孔,第三工位空位,第四工位落料,空位的目的是增大冲ф5mm 孔凹模和落外形凹模之间的壁厚,以保证凹模强度。
冲压件工艺性(3篇)

第1篇一、引言冲压件是机械制造领域中广泛使用的一种零件,其生产工艺性对产品的质量和成本有着重要的影响。
本文将围绕冲压件工艺性展开讨论,分析其特点、影响因素及优化措施。
二、冲压件工艺性特点1. 高精度:冲压件具有很高的尺寸精度和形状精度,可实现复杂形状的零件制造。
2. 高效率:冲压工艺自动化程度高,生产效率高,可实现大批量生产。
3. 低成本:冲压件生产过程中,材料利用率高,加工设备简单,降低了生产成本。
4. 易于实现多样化:冲压件可加工成各种形状和尺寸,适应性强。
5. 易于实现表面处理:冲压件表面光滑,易于进行表面处理,如镀锌、喷漆等。
三、冲压件工艺性影响因素1. 材料性能:材料的选择对冲压件的工艺性有很大影响。
常用的冲压材料有低碳钢、合金钢、不锈钢等。
不同材料具有不同的强度、塑性和硬度,需根据产品要求选择合适的材料。
2. 冲压模具:模具是冲压件生产的关键,其设计、制造和选用对冲压件的工艺性有直接影响。
模具的精度、刚度和磨损程度都会影响冲压件的尺寸精度和形状精度。
3. 冲压设备:冲压设备包括压力机、模具安装设备等。
设备的性能、精度和稳定性对冲压件的工艺性有重要影响。
4. 工艺参数:冲压工艺参数包括冲压速度、压力、温度等。
合理的工艺参数可以保证冲压件的尺寸精度、形状精度和表面质量。
5. 操作人员技能:操作人员的技能水平直接影响冲压件的生产质量和效率。
四、冲压件工艺性优化措施1. 优化材料选择:根据产品要求,选择合适的材料,提高材料的塑性和可冲压性。
2. 优化模具设计:采用先进的模具设计方法,提高模具的精度和寿命。
合理设计模具结构,降低生产成本。
3. 选用高性能冲压设备:提高设备的性能、精度和稳定性,确保冲压件的质量。
4. 优化工艺参数:根据产品要求,合理设置冲压速度、压力和温度等工艺参数,保证冲压件的尺寸精度、形状精度和表面质量。
5. 提高操作人员技能:加强操作人员培训,提高其技能水平,确保生产过程中的产品质量。
第七章 冲压技术工艺文件

八、绘制模具图 六、冲压文件的填写(冲压工艺过程卡和工序卡)
第二节 制订冲压工艺方案实例
一、工艺分析
冲压工序是落料、拉探和冲孔 1)外径φ100+1. 4,精度大致为ITl5级; 2)底部孔为φ40+
0.15,IT11级;
3)圆角半径r8满足拉深要求r≥(2-3)t 4 )底部孔 φ40 远远大于冲裁工艺对最小孔
第七章
冲压技术工艺文件
工艺规程是指导零件生产过程的技术文件,冲压工艺文件一 般指冲压工艺过程卡,是模具设计以及指导冲压生产工艺过程 的依据。
冲压件的生产过程包括:原材料的准备,各种冲压工序和必 要的辅助工序。有时还需配合一些非冲压工序,如切削加工、 焊接、铆接等,才能完成一个冲压零件的全部制作过程。 在编制冲压工艺规程时,通常是根据冲压件的特点、生产批 量、现有设备和生产能力等,拟订出数种可能的工艺方案,在 对各种工艺方案进行全面的综合分析和比较之后,选定一种较 先进、最经济、最合理的工艺方案。
零件拉深次数为2次。
三、工艺方案
方案一:落料——冲孔——一次拉深——二次拉深
方案二:落料——一次拉深——二次拉探——冲孔
方案三;落料与冲孔复合——一次拉深——二次拉深
方案四;落料与一次拉深复合——二次拉深——冲孔
方案五;落料与冲孔复合——一次拉深与二次拉深在 同套模具上完成 方案六:落料、冲孔与一次拉探三工序复合——二次 拉深
径的要求(d≥1.0t);
5)底部孔壁到筒形件壁部距离为27mm,远离圆角处。
二、工艺计算
工件直径:d=100-3=97mm;高度:H=120-1.5=118.5mm
冲压件的工艺参数优化

冲压件的工艺参数优化冲压件是一种常用的金属制造工艺,广泛应用于汽车、家电、航空航天和电子等领域。
工艺参数的优化对冲压件的质量、成本和生产效率具有重要影响。
本文将围绕冲压件的工艺参数进行优化展开,讨论其影响因素和优化方法。
一、冲压件的工艺参数及其影响因素冲压件的工艺参数包括材料选择、模具设计、冲压力、冲压速度、冲压温度和润滑剂等。
这些参数的选择直接影响着冲压件的尺寸精度、表面质量、力学性能和工艺可行性。
1. 材料选择材料的选择是冲压件工艺参数优化的关键因素之一。
不同材料具有不同的机械性能和可加工性。
合适的材料能够提高冲压件的强度、硬度和耐磨性,同时还能减少变形和裂纹的产生。
2. 模具设计模具设计直接关系到冲压件的尺寸精度和形状复杂度。
合理的模具设计应考虑到冲击力的分布、模具的刚性和稳定性。
优化模具结构和加工工艺能够降低瑕疵、提高生产效率。
3. 冲压力和冲压速度冲压力和冲压速度是冲压件工艺参数中最基本的两个参数。
冲压力直接影响冲压件的塑性形变和材料强度的改变,而冲压速度则影响冲击力的大小和分布。
合理的压力和速度选择能够提高冲压件的尺寸精度、表面质量和工艺稳定性。
4. 冲压温度冲压温度是指材料在冲压过程中的温度变化。
冲压温度对冲压件的塑性变形、力学性能和表面质量有重要影响。
过高或过低的温度都可能导致冲压件变形或质量不合格。
要根据材料的热变形特性和工艺要求选择适当的冲压温度。
5. 润滑剂润滑剂在冲压过程中起到润滑、降低摩擦和冷却的作用。
适当的润滑剂能够减少摩擦力和热量,降低冲压件的变形和瑕疵率。
选择合适的润滑剂类型、浓度和方式对冲压件的质量和生产效率具有重要意义。
二、冲压件工艺参数优化方法为了提高冲压件的质量、成本和生产效率,需要通过优化工艺参数来达到最佳的制造效果。
以下是几种常见的优化方法:1. 实验设计法实验设计法是通过设计合理的实验方案来优化冲压件的工艺参数。
通过改变多个工艺参数的组合,以响应曲面法或遗传算法等方法建立数学模型,将冲压件的质量指标作为目标函数,通过实验和分析来确定最佳工艺参数组合。
- 1、下载文档前请自行甄别文档内容的完整性,平台不提供额外的编辑、内容补充、找答案等附加服务。
- 2、"仅部分预览"的文档,不可在线预览部分如存在完整性等问题,可反馈申请退款(可完整预览的文档不适用该条件!)。
- 3、如文档侵犯您的权益,请联系客服反馈,我们会尽快为您处理(人工客服工作时间:9:00-18:30)。
冲压件工艺性分析与计算一.冲压件工艺性分析(1)材料分析08F是优质沸腾钢,强度低与硬度、塑性、韧性好,易于拉伸与冲裁成形。
(2)结构分析冲压件为外形为弧形与直边构成近似矩形的结构、有凸缘筒形浅拉深、冲三个圆孔的结构。
零件上有3个孔,其中最小孔径为5.5mm,大于冲裁最小孔径dmin ≥1.0t=1.2mm的要求。
另外,孔壁与制件直壁之间的最小距离满足L=3.475≥R+0.5t=1.6.的要求。
因此,该零件的结构满足冲裁拉深的要求。
(3)精度分析零件上有4个尺寸标注了公差要求,由公差表查得其公差要求都属于IT11~IT13,因此,普通冲裁能够满足零件的精度要求。
由以上分析可知,该零件能够用普通冲裁与拉深的加工方法制得。
二.冲压件工艺方案的确定(1)冲压方案完成此工件需要落料、拉深、冲孔三道工序。
因此能够提出下列5种加工方案分:方案一:先落料,再冲孔,后拉深。
使用三套单工序模生产。
方案二:落料—拉深—冲孔复合冲压,使用复合模生产。
方案三:冲孔—拉深—落料连续冲压,使用级进模生产。
方案四:拉深—冲孔复合冲压,然后落料,使用级进模生产。
方案五:落料—拉深复合冲压,然后冲孔。
使用两套模生产。
(2)各工艺方案的特点分析方案一与方案五需要多套工序模,模具制造简单,维修方便,但生产成本较低,工件精度低,不适合大批量生产;方案二只需一副模具,冲压件的形状位置精度与尺寸精度易于保证,且生产效率高。
方案三与方案四的级进模,生产效率高,但模具制造复杂,调整维修烦恼,工件精度较低;(3)工艺方案的确定比较三个方案,使用方案五生产更为合理。
尽管模具结构较其他方案复杂,但 由于零件的几何形状简单对称,模具制造并不困难。
因此,在本设计中,将使用落料、拉深复合模的设计方案。
三.冲压工艺计算(1)凸、凹模刃口尺寸的计算根据零件形状特点,刃口尺寸计算使用分开制造法。
落料件尺寸的计算,落料基本计算公式为A0max A )(δ+-=X ΔD Dmin max 0min A T T T )()(δδ----=-=Z X ΔD Z D D尺寸44mm ,经查得该零件凸、凹模最小间隙Z min =0.126mm ,最大间隙Z max =0.180mm ;凸模制造公差m m 02.0T =δ,凹模制造公差m m 03.0A =δ。
将以上各值代入A T δδ+≤min max Z Z -校验是否成立。
经校验,不等式成立,因此,可代入上式计算工作零件刃口尺寸。
m m 44m m 05.044A1=⨯-=)(D m m 874.43m m 126.044T1=-=)(D尺寸mm 2.36,查得其min Z 、m ax Z 、T δ、A δ数值同上一尺寸,因此同样满足A T δδ+≤min max Z Z -的要求,则m m 2.36m m 05.02.36A2=⨯-=)(Dm m 874.31m m 126.02.36T2=-=)(D尺寸mm 50R ,查得其min Z 、m ax Z 、T δ、A δ数值同上一尺寸,因此同样满足A T δδ+≤min max Z Z -的要求,则m m 50m m 05.050A3=⨯-=)(D m m 937.49m m 2/126.050T3=-=)(D 冲孔尺寸计算,冲孔基本公式为0min T T )(δ-+=X Δd dA0min min A )(δ+++=Z X Δd d尺寸φmm 018.05.13-,查得凸模制造公差mm 02.0=T δ,凹模制造公差m m 02.0=A δ。
经验算满足A T δδ+≤min max Z Z -,因此mm 41.13mm )18.05.032.13(002.0002.0T1--=⨯+=d m m 33134.13m m )126.018.05.032.13(02.0002.00A1++=+⨯+=d 尺寸φmm 5.518.00+,查得其min Z 、m ax Z 、T δ、A δ数值同上一尺寸,因此同样满足A T δδ+≤min max Z Z -的要求,则mm 59.5mm )18.05.05.5(002.0002.0T2--=⨯+=dmm 716.5mm )126.018.05.05.5(02.0002.00A2++=+⨯+=d拉深尺寸计算 ,拉深基本公式为d0d δD D =p )(p Z D D δ-=尺寸mm 033.030-φ,p δ=0.03 d δ=0.05,双边间隙Z=2.2t=2.64,则d 0d δD D ==05.00300p )(p Z D D δ-==003.0)64.230(-=05.0036.27中心距尺寸计算 :零件上两孔中心距为L=mm 5.1709.009.0+-mm(2)拉深凸、凹模圆角半径的计算凹模圆角半径的计算:拉深凹模圆角半径的计算为()t d D r d -80.01=此零件落料冲孔的周长L 为94mm ,材料厚度t 为1.2mm ,08F 钢的抗拉强度b σ取390MPa ,则零件所需拉深力为()()mm t d D r d 35.22.16.272.3680.080.01=⨯-=-= 凸模圆角半径的计算:拉深凸模圆角半径的计算为18.01d r r p =根据凹模圆角半径,计算凸模半径为88.135.28.08.011=⨯=d r r p =四.冲压力的计算及初选压力机 (1)落料工序冲压力的计算冲裁力基本计算公式为τKLT F =此零件落料的周长1L 为153mm ,材料厚度t 为1.2mm ,08F 钢的抗剪强度τ取310MPa ,则冲裁该零件所需冲裁力为kN 748.73990N 3102.11533.1≈=⨯⨯⨯=N F 落模具使用弹性卸料装置与推件结构,所需卸料力X1F 与推件力T1F 为kN 7.3N 7405.0X X1=⨯==F K FkN 07.4N 74055.01T T1≈⨯⨯==F NK F 因此落料工序冲总压力为:kN 77.81kN )07.47.374(T1X11=++=++=F F F F 落总 (2)拉深工序冲压力的计算拉深力基本计算公式为 1k Lt F b σ=拉深此零件落料冲孔的周长L 为94mm ,材料厚度t 为1.2mm ,08F 钢的抗拉强度b σ取390MPa ,则零件所需拉深力为1k Lt F b σ=拉深=94×1.2×390×1=43.99kN 压边力的基本计算公式Aq Q =此零件在压边圈下毛坯的投影面积A 为322,单位压边力q 取3,则该零件所需压边力为kN Aq Q 966.03322=⨯==模具使用弹性卸料装置与推件结构,所需卸料力X2F 与推件力T2F 为kN 25.2N 956.4405.0Q (X X2=⨯=+=)拉深F K FkN 45.2N 956.44055.0Q (T T2≈⨯=+=)拉深F NK F 因此拉深工序冲总压力为:kN F 66.492.452.250.96643.99F F Q F t2x22≈+++=+++=拉深总 冲孔工序冲压力的计算冲裁力基本计算公式为τKLT F =此零件冲孔的周长2L 为77mm ,材料厚度t 为1.2mm ,08F 钢的抗剪强度τ取310MPa ,则冲裁该零件所需冲裁力为kN3737237N 3102.1773.1≈=⨯⨯⨯=N F 冲模具使用弹性卸料装置与推件结构,所需卸料力3X F 与推件力3T F 为 kN85.1N 3705.0X X3=⨯==F K FkN11.6N 37055.03T T3≈⨯⨯==F NK F因此落料冲孔工序冲总压力为:kN96.44kN )11.685.137(T3X33=++=++=F F F F 落总(4)压力机的选择计算的落料、拉深工序压力压力:kN F 43.13166.4977.81F F 211=+=+=总总 计算的冲孔工序压力压力:kN F 96.44F 31==总因此,落料、拉深复合模初选设备为开式压力机J23—16;冲孔模初选设备为开式压力机J23—6.3 (4)压力中心的计算由于改冲裁件为对称图形,因此它的压力中心位于冲件轮廓图形的几何中心上。
即拉深圆的圆心位置。
五.排样(1)竖排(如图1)图1a.搭边查表3-7,选取mm a 11=,a =1.8 mm 。
b.送料步距与条料宽度平行于送料方向的冲件宽度D=36.2,因此,送料步距为: mm a D S 2.3712.361=+=+=模具无側压装置,导料板与最宽条料之间的间隙Z=0.5(表3-9),条料宽度单向公差20.0=∆(表3-11),冲裁件垂直于送料方向的最大尺寸44max =D ,条料宽度为:mm Z a D B 020.000max 01.48)5.08.1244()2(-∆-∆-∆-=+⨯+=++=导料板间的距离为:mm Z a D B 6.485.028.124422max 0=⨯+⨯+=++= c. 板料利用率选用1.2mm ×1500mm ×1000mm 的板料。
落料件面积为2232.1698mm 使用横裁可裁条料数为:311.481500=÷(条),余8.9mm ,每条板料可冲制件数262.37)11000(=÷-(件),因此每张板料可冲制件数8063126=⨯(件)。
材料的利用率为:%3.91%100)10001500(80622.1698≈⨯⨯÷⨯使用竖裁可裁条料数为:201.481000=÷(条),余38mm ,每条板料可冲制件数402.37)11500(=÷-(件),因此每张板料可冲制件数8004020=⨯(件)。
材料的利用率为:%6.90%100)10001500(80022.1698≈⨯⨯÷⨯(2)横排(如图2)a.搭边查表3-7,选取mm a 5.11=,a =1.2 mm 。
b.送料步距与条料宽度平行于送料方向的冲件宽度D=44,因此,送料步距为: mm a D S 5.455.1441=+=+=模具无側压装置,导料板与最宽条料之间的间隙Z=0.5(表3-9),条料宽度单向公差20.0=∆(表3-11),冲裁件垂直于送料方向的最大尺寸2.36max =D ,条料宽度为:mm Z a D B 020.000max 01.39)5.02.122.36()2(-∆-∆-∆-=+⨯+=++=导料板间的距离为:mm Z a D B 6.395.022.122.3622max 0=⨯+⨯+=++=c. 板料利用率选用1.2mm×1500mm×1000mm的板料。
落料件面积为21698mm.232使用横裁可裁条料数为:38÷(条),余14.2mm,每条板料可冲1500=1.39制件数21÷(=-(件),因此每张板料可冲制件数798 10005.45)5.138=⨯(件)。