第九章 烧结分析
材料科学基础第九章烧结

材料科学基础第九章烧结
二. 溶解-沉淀传质
1. 条件:
❖显著的液相量
❖固相在液相内有显著的可溶性
❖液相润湿固相
2. 原因(推动力):颗粒的表面能
3. 过程: 颗粒重排
溶解-沉淀传质
材料科学基础第九章烧结
❖颗粒重排:
颗粒在毛细管力作用下,通过粘性流动或在一些 颗粒间接触点上由于局部应力的作用而重新排列, 使堆积更致密。 致密化速率与粘性流动相应,线收缩与时间呈线 性关系:
材料科学基础第九章烧结
粘性蠕变通过粘度系数(η)把粘性蠕变速率(ε)与
应力(σ)联系起来 ,
又 KTd 2 8D* 8D* KTd 2
粘性蠕变产生区域:晶界区域、位错区域
材料科学基础第九章烧结
❖动力学关系:
烧结模型:双球模型(中心距缩短)
颈部增长公式:
x
( 3
1
)2
1
r 2
1
t 2
1、 推动力:粉末物料的表面能大于多晶烧结体的晶界 能 2、 衡量指标:通常用晶界能γGB和表面能γ SV之比值来衡 量烧结的难易。 GB S越V 小越易烧结。
❖对球形颗粒:弯曲表面由于表面张力而造成的压差 P 2
r
❖对非球形曲面: P ( 1 1 )
r1 r2
❖烧结的推动力: G VP
烧成后期空隙率:
6D*
Pt 2KT3L(tf t)
材料科学基础第九章烧结
材料科学基础第九章烧结
第三节 液相参与的烧结
液相烧结特点和类型:
凡有液相参加的烧结过程称为液相烧结。 液相烧结与固相烧结的异同点:
相同点:烧结的推动力都是表面能,烧结过程都是 由颗粒重排、气孔充填和晶粒生长等阶段组成 不同点:由于流动传质比扩散传质快,因而液相烧 结致密化速率高,可使坯体在比固态烧结温度低得 多的情况下获得致密的烧结体;影响液相烧结的因 素比固相烧结更为复杂,为定量研究带来困难。
《无机材料科学基础》第9章烧结

烧结和熔融 烧结是在远低于熔融温度下进行的,至少有一组元处于固 熔融则所有组元转变为液相 烧结和熔融的关系: 金属粉末:Ts≈(0.3---0.4)TM 盐 类:Ts≈0.57 TM 硅 酸 盐:Ts≈(0.8---0.9)TM
态
3、烧结与固相反应
固相反应:至少有两个组份参加,产物不同于任一反应物 烧结:可单或多组分,不发生化学反应,表面能推动下实现致密化的过程
3、烧结程度表征
(1)、气孔率 (2)烧结体密度 (4)强度 (5)晶粒尺寸 (7)坯体收缩率 (8)相对密度
(3)电阻 (6)吸水率
9.1.2与烧结有关的一些概念 1、烧结与烧成 烧结:仅指粉料经加热而致密化的物理过程 烧成:包括粉料在加热过程中发生的一切物理和化学变 化 例如:气体排除、相变、熔融;氧化、分解、固相 反应等
r r 将代入 Fx , , Fρ ,考虑 sin θ ≈ θ 2 2
,得
r F = γ ⋅θ 2 (ρ − x) A = AB∗ BC = ρ ∗ xθ
γ ∗θ (ρ − x) 1 1 =γ − σ = F A= 2 x ρ xρθ γ Qx >> ρ,∴σ ≈ − ρ
空位浓度差导致的晶格扩散是颗粒中心逼近的原因
3、扩散传质途径
4、扩散分期 、 (1)初期:表面扩散显著,空隙表面光滑和气孔球形化,坯 体收缩小(1%) 由9—16知颈部与晶体内浓度差 ∆ 2 C = [C 0 ]σΩ σ=γ
∆C = [C 0 ]γΩ
ρ
代入得
9—17 每秒从每厘米周长上扩散离开颈部的空位扩散流量 9—18 J = 4 DV ∆C DV:空位扩散系数,如D*自扩散系数, DV=
F x = γ AD = γ BC Fρ = γ AB = γ CD
第九章烧结复习习题及提纲

习题1.烧结推动力是什么? 它可凭哪些方式推动物质的迁移,各适用于何种烧结机理? 2.烧结过程是怎样产生的,各阶段的特征是什么?3.下列过程中哪一个能使烧结体强度增大,而不产生坯体宏观上的收缩? 试说明之。
(a)蒸发冷凝;(b)体积扩散;(c)粘性流动;(d)表面扩散;(e)溶解沉淀4.某氧化物粉末的表面能是1000erg/cm2,烧结后晶界能是550 erg/cm2,今用粒径为1μm的粉料(假定为立方体)压成1cm3的压块进行烧结,试计算烧结时的推动力。
5.试就(a)推动力来源;(b)推动力大小;(c)在陶瓷系统的重要性来区别初次再结晶,晶粒长大和二次再全结晶。
6.有人试图用延长烧结时间来提高产品致密度,你以为此法是否可行.为什么了?7.假如直径为5μm的气封闭在表而张力为280达因/厘米的玻璃内,气孔内氮气压力是0.8大气压,当气体压力与表面张力产生的负压平衡时,气孔尺寸是多少?8. 在1500℃,MgO正常的晶粒长大期间.观察到晶体在1小时内从直径从1μm 长大到10μm,在此条件下,要得到直径20μm的晶粒,需烧结多长时间?如已知晶界扩散活化能为60KCal/mol,试计算在1600℃下4小时后晶粒的大小,为抑制晶粒长大,加入少量杂质,在1600℃下保温4小时,晶粒大小又是多少?9.假定NiCr2O4的表面能为600erg/cm2,由半径0.5μm的NiO和Cr2O3粉末合成尖晶石。
在1200℃和1400℃时Ni2+和Cr3+离子的扩散系数分别为:Ni2+在NiO中D1473=1×10-11;D1673=3×10-10cm2/s;Cr3+在Cr2O3中D1473=7×10-11;D1673=10-9cm2/s,求在1200℃和1400℃烧结时,开始1秒的线收缩率是多少?(假定扩散粒子的半径为0.59Å) 10.材料的许多性能如强度、光学性能等要求其晶粒尺寸微小且分布均匀,工艺上应如何控制烧结过程以达到此目的?11.试分析二次再结晶过程对材料性能有何种效应?12.特种烧结和常规烧结有什么区别?试举例说明。
第九章复习题答案
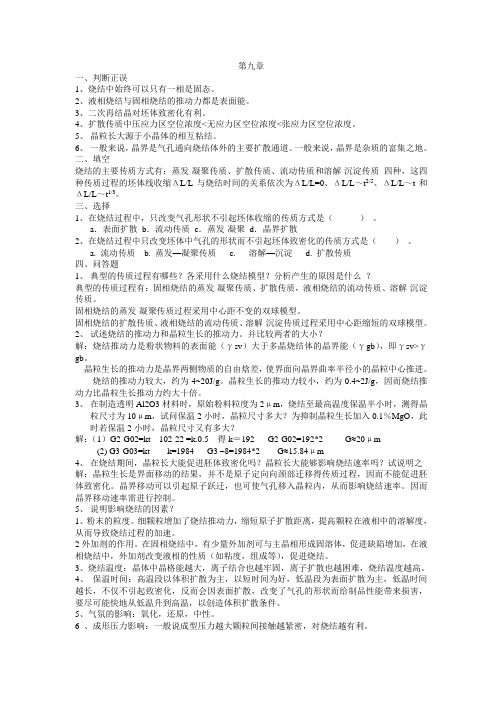
第九章一、判断正误1、烧结中始终可以只有一相是固态。
2、液相烧结与固相烧结的推动力都是表面能。
3、二次再结晶对坯体致密化有利。
4、扩散传质中压应力区空位浓度<无应力区空位浓度<张应力区空位浓度。
5、晶粒长大源于小晶体的相互粘结。
6、一般来说,晶界是气孔通向烧结体外的主要扩散通道。
一般来说,晶界是杂质的富集之地。
二、填空烧结的主要传质方式有:蒸发-凝聚传质、扩散传质、流动传质和溶解-沉淀传质_四种,这四种传质过程的坯体线收缩ΔL/L与烧结时间的关系依次为ΔL/L=0、ΔL/L~t2/5、ΔL/L~t和ΔL/L~t1/3。
三、选择1、在烧结过程中,只改变气孔形状不引起坯体收缩的传质方式是()。
a.表面扩散b.流动传质c.蒸发-凝聚d.晶界扩散2、在烧结过程中只改变坯体中气孔的形状而不引起坯体致密化的传质方式是()。
a. 流动传质b. 蒸发—凝聚传质c. 溶解—沉淀d. 扩散传质四、问答题1、典型的传质过程有哪些?各采用什么烧结模型?分析产生的原因是什么?典型的传质过程有:固相烧结的蒸发-凝聚传质、扩散传质,液相烧结的流动传质、溶解-沉淀传质。
固相烧结的蒸发-凝聚传质过程采用中心距不变的双球模型。
固相烧结的扩散传质、液相烧结的流动传质、溶解-沉淀传质过程采用中心距缩短的双球模型。
2、试述烧结的推动力和晶粒生长的推动力。
并比较两者的大小?解:烧结推动力是粉状物料的表面能(γsv)大于多晶烧结体的晶界能(γgb),即γsv>γgb。
晶粒生长的推动力是晶界两侧物质的自由焓差,使界面向晶界曲率半径小的晶粒中心推进。
烧结的推动力较大,约为4~20J/g。
晶粒生长的推动力较小,约为0.4~2J/g,因而烧结推动力比晶粒生长推动力约大十倍。
3、在制造透明Al2O3材料时,原始粉料粒度为2μm,烧结至最高温度保温半小时,测得晶粒尺寸为10μm,试问保温2小时,晶粒尺寸多大?为抑制晶粒生长加入0.1%MgO,此时若保温2小时,晶粒尺寸又有多大?解:(1)G2-G02=kt 102-22 =k.0.5 得k=192 G2-G02=192*2 G≈20μm(2) G3-G03=kt k=1984 G3 –8=1984*2 G≈15.84μm4、在烧结期间,晶粒长大能促进胚体致密化吗?晶粒长大能够影响烧结速率吗?试说明之解:晶粒生长是界面移动的结果,并不是原子定向向颈部迁移得传质过程,因而不能促进胚体致密化。
9-1烧结
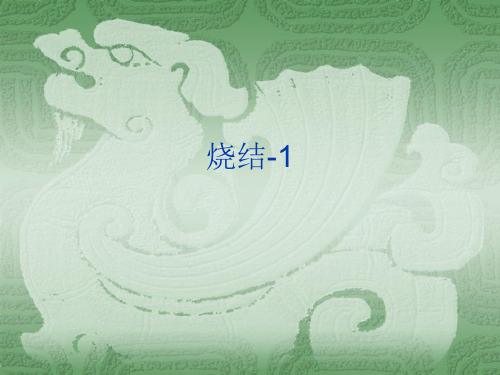
lμm的材料烧结时所发生的自由焓降低 粒度为 lμm的材料烧结时所发生的自由焓降低 8.3J/g. 石英转变为β 石英时, 约8.3J/g.而 α-石英转变为β-石英时,能量变 化为1.7kJ mol,一般化学反应前后能量变化> 1.7kJ/ 化为1.7kJ/mol,一般化学反应前后能量变化> 200kJ/mol.因此, 200kJ/mol.因此,烧结推动力与相变和化学反应 的能量相比还是极小的.常温下需很长的时间进行, 的能量相比还是极小的.常温下需很长的时间进行, 才能达到致密化,因此,需对粉体加以高温, 才能达到致密化,因此,需对粉体加以高温,才能 促使粉末体在短时转变为烧结体. 促使粉末体在短时转变为烧结体.
烧结过程中性质的变化: 烧结过程中性质的变化:
2.烧结的宏观定义: 烧结的宏观定义: 烧结的宏观定义 根据烧结粉末体所出现的宏观变化可以认为, 根据烧结粉末体所出现的宏观变化可以认为, 烧结是把一种或多种固体粉末经过成型 是把一种或多种固体粉末经过成型, 烧结是把一种或多种固体粉末经过成型,在低于熔 点的高温作用下, 点的高温作用下,通过坯体间颗粒相互粘结和物质 传递,气孔排除,体积收缩,强度提高, 传递,气孔排除,体积收缩,强度提高,逐渐变成 具有一定的几何形状和坚固整体的过程. 具有一定的几何形状和坚固整体的过程. 应该注意, 应该注意,烧结过程是一个复杂的物理化学过 除物理变化外,有的还伴随有化学反应, 程.除物理变化外,有的还伴随有化学反应,如固 相反应等.但烧结过程并不依赖予化学反应的作用; 相反应等.但烧结过程并不依赖予化学反应的作用; 这是烧结区别于固相反应的一个重要方面. 这是烧结区别于固相反应的一个重要方面.纯氧化 物的烧结过程, 物的烧结过程,粉末冶金制品的烧结过程等都不依 赖于化学反应的作用. 赖于化学反应的作用.
材料科学基础 第九章 烧结

3、影响因素 1)烧结时间t
1 x t 3 r
如:氯化钠球的烧结实验。 对蒸发-凝聚传质,延长时间 对烧结影响不大
2)压力影响 Po
对于硅铝酸盐材料蒸气压低,影响较小。 如:Al2O3,在1200℃时,P = 10-41Pa
图9-5 氯化钠在750º C时球形颗粒之 间颈部生长
3)颗粒半径 r 的影响
被水膜包裹的两 固体球的粘附
粘附作用是烧结初始阶段,导致粉体颗粒间产生键合、靠拢 和重排.并开始形成接触区的一个原因。 粘附力的大小直接取决于物质的表面能和接触面积,故粉状 物料间的粘附作用特别显著。
二、物质的传递—传质过程
P
气相传质 — 蒸发-凝聚传质 扩散传质 流动传质
C
塑性流动 粘性流动
f
dv dx
固 相 烧 结
F dv S dx
溶解-沉淀传质 C f
液相 烧结
(一)蒸发-凝聚传质
1、概念 固体颗粒表面的曲率不同,高温时在系统的不同部位有不同的蒸 气压,质点通过蒸发,再凝聚实现质点的迁移,促进烧结。 这种传质过程一般在高温下蒸气压较大的系统内发生,如PbO、 BeO、FeO、ZnO、TiO2的烧结。 模型:在球形颗粒表面有正曲率半 径,在两个颗粒联接处有一个小的 负曲率半径的颈部。 物质将从蒸气压高的凸形颗粒表面 蒸发,通过气相传递而凝聚到蒸气 压低的凹形颈部,从而使颈部逐渐 被填充。
当 r↓ ,x/r↑ 。 一般烧结 r =10m。
x 3 M P 0 r 2 R 3 2T 3 2 d 2
23
r 2 3 t 1 3
13
4)温度 T 的影响
T↑,P0↑↑, x/r↑↑。
材料科学基础相图习题

1.下图为一匀晶相图,试根据相图确定:(1) w B =0.40的合金开始凝固出来的固相成分为多少?(2)若开始凝固出来的固体成分为w B =0.60,合金的成分为多少?(3)成分为w B =0.70的合金最后凝固时的液体成分为多少?(4)若合金成分为w B =0.50,凝固到某温度时液相成分w B =0.40,固相成分为w B =0.80,此时液相和固相的相对量各为多少?2.Mg —Ni 系的一个共晶反应为:0.23520.546g g i M L M N 纯+(570℃)设w Ni 1=C 1为亚共晶合金,w Ni 2=C 2为过共晶合金,这两种合金中的先共晶相的质量分数相等,但C 1合金中的α总量为C 2台金中α总量的2.5倍,试计算C 1和C 2的成分。
3.根据A-B 二元相图(1) 写出图中的液相线、固相线、α和β相的溶解度曲线、所有的两相区及三相恒温转变线;(2) 平衡凝固时,计算A-25B(weight%)合金(y ’y 线)凝固后粗晶β相在铸锭中的相对含量;(3) 画出上述合金的冷却曲线及室温组织示意图。
4.根据如图所示的二元共晶相图(1)分析合金I,II的结晶过程,并画出冷却曲线;(2)说明室温下合金I,II的相和组织是什么,并计算出相和组织组成物的相对含量?(3)如果希望得到共晶组织加上5%的 初的合金,求该合金的成分。
(4)合金I,II在快冷不平衡状态下结晶,组织有何不同?5.指出下列相图中的错误:6.试述二组元固溶体相的吉布斯(Gibbs)自由能-成分曲线的特点?(a) (b)(c) (d)1.下图为一匀晶相图,试根据相图确定:(1) w B =0.40的合金开始凝固出来的固相成分为多少?(2)若开始凝固出来的固体成分为w B =0.60,合金的成分约为多少?(3)成分为w B =0.70的合金最后凝固时的液体成分约为多少?(4)若合金成分为w B =0.50,凝固到某温度时液相成分w B =0.40,固相成分为w B =0.80,此时液相和固相的相对量各为多少?第1题答案2.Mg —Ni 系的一个共晶反应为:0.23520.546g g i M L M N 纯+(570℃)设w Ni 1=C 1为亚共晶合金,w Ni 2=C 2为过共晶合金,这两种合金中的先共晶相的质量分数相等,但C 1合金中的α总量为C 2台金中α总量的2.5倍,试计算C 1和C 2的成分。
烧结指标报告分析

烧结指标报告分析1. 引言烧结是一种重要的冶金过程,用于将粉末颗粒熔结在一起形成固体块状材料。
烧结指标报告分析是对烧结过程中的关键指标进行系统评估和分析,以便为优化烧结工艺和提高产品质量提供指导。
本文将对烧结指标报告进行详细分析,包括烧结温度、烧结时间、烧结效率等关键指标的测量结果和评估。
通过这些指标的分析,我们可以了解烧结过程中的问题和潜在风险,从而采取相应的措施来改善烧结工艺和提高产品质量。
2. 烧结温度分析烧结温度是影响烧结质量的重要因素之一。
在烧结过程中,温度的高低直接影响到烧结颗粒的熔结程度和结晶度。
通过对烧结温度的测量和分析,我们可以评估烧结过程中的温度控制是否稳定以及是否存在温度异常。
根据烧结指标报告,我们可以获得不同时间段内的烧结温度数据。
通过对这些数据的分析,我们可以发现温度的波动情况、峰值温度以及温度变化趋势。
同时,我们还可以与烧结工艺参数进行对比,以确定温度异常的原因,并采取相应的措施进行调整。
3. 烧结时间分析烧结时间是指将颗粒物料放置在高温环境中进行加热和熔结的时间。
烧结时间的长短直接影响到烧结颗粒的熔结程度和结晶度。
通过对烧结时间的测量和分析,我们可以评估烧结过程中的时间控制是否合理以及是否存在时间不足或过长的情况。
烧结指标报告中提供了不同烧结时间下的烧结效果数据。
通过对这些数据的分析,我们可以比较不同烧结时间下的烧结结果,找出最佳的烧结时间范围。
同时,我们还可以结合其他指标数据,如烧结温度和烧结压力,综合评估烧结时间对产品质量的影响。
4. 烧结效率分析烧结效率是指烧结过程中原料的转化率和产品的质量利用率。
烧结效率直接影响到产品的成品率和质量稳定性。
通过对烧结效率的测量和分析,我们可以评估烧结过程中的能源利用效率和原料利用效率。
烧结指标报告中包含了不同烧结工艺条件下的烧结效果数据。
通过对这些数据的分析,我们可以比较不同工艺条件下的烧结效率,找出最佳的工艺参数组合。
同时,我们还可以结合其他指标数据,如烧结温度和烧结时间,综合评估烧结效率对产品质量的影响。
烧结组织特征分析讲解
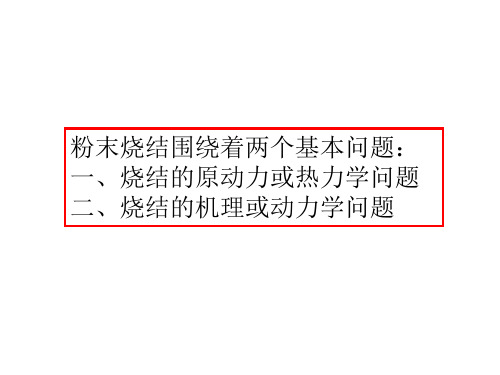
合肥微尺度物质科学国家实验室(中国科技大学2003年) 以多学科综合为特点、以国家重大战略需求和交叉前沿领域 为导向的新型实验室,其学科领域涉及物理、化学、材料、生 物和信息,实现了五大一级学科之间大跨度的整合。
粉末烧结围绕着两个基本问题: 一、烧结的原动力或热力学问题 二、烧结的机理或动力学问题
烧结(sintering)定义 宏观定义
在高温下(低于熔点),陶瓷生坯固体颗粒的相互键联,晶粒长大,空隙 (气孔)和晶界渐趋减 少,通过物质的传递,其总体积收缩,密度增加,最后 成为具有某种显微结构的致密多晶烧结体,这种现象称为烧结
热处理(heat treatment) 1、热处理是将材料放在一定的介质内加热、保温、冷却,通过改变材料表 面或内部的组织结构,来控制其性能的一种综合工艺过程。 2、热处理工艺一般包括加热、保温、冷却三个过程,有时只有加热和冷却 两个过程。这些过程互相衔接,不可间断。 3、热处理的目的是改变材料的内部组织(金相组织)和结构,以获得我们 所需适当方式加热、保温和冷却,以获得所需要的组 织结构与性能的加工方法。
课程安排 固体物理学(solid-state physics)是研究固体的性质、它的微观结构及 其各种内部运动,以及这种微观结构和内部运动同固体的宏观性质的关系 的学科。 固体化学(solid chemistry)研究固体物质的制备、组成、结构和性质 的化学分支学科。固体化学的研究始于20世纪20年代,到了60年代,由于 科学技术的发展,对固体材料的需求更加迫切,同时也为固体材料的研究 提供了必要的实验手段,固体化学进入蓬勃发展的新阶段。固体化学着重 研究实际固体物质的化学反应、合成方法、晶体生长、化学组成和结构, 特别是固体中的缺陷及其对物质的物理及化学性质的影响,探索固体物质 作为材料实际应用的可能性。 材料过程工程学(Process Engineering of Materials)基于材料学、 系统工程学和生态学有关理论,对材料由原生到被废弃的生命全过程进行 集成优化,以期对自然环境低能耗、少污染和充分利用可再生资源的工艺 和各种工程问题进行研究的科学。
第九章-烧结分析

烧
再
概
结
结
过
晶
程
和
及
晶
述
机
粒
理
长
大
影 响 烧 结 的 因 素
§9.1 概述
烧结过程是一门古老的工艺,早在公元前3000 年,人类就掌握了这门工艺,但对烧结理论的研 究和发展仅开始于20世纪中期。现在,烧结过程 在许多工业部门得到广泛应用,如陶瓷、耐火材 料、粉末冶金、超高温材料等生产过程中都含有 烧结过程。
F v
S
x
式中,τ是极限剪切力。
烧结时的粘性流动和塑性流动都会出现 在含有固、液两相的系统。当液相量较大并 且液相粘度较低时,是以黏性流动为主;而 当固相量较多或粘度高时则以塑性流动为主。
⑵ 扩散传质(固相烧结传质方式)
扩散传质是指质点(或空位)借助于浓度梯度推动而迁 移的传质过程。烧结初期由于粘附作用使粒子间的接触 界面逐渐扩大并形成具有负曲率的接触区(颈部)。在 表面张力的作用下,所产生的附加压力使颈部的空位浓 度比离子其他部位的浓度大,存在一个过剩空位浓度。
度提高。
二、烧结推动力
粉体颗料尺寸很小,比表面积大,具有 较高的表面能,即使在加压成型体中,颗料 间接面积也很小,总表面积很大而处于较高 能量状态。根据最低能量原理,它将自发地 向最低能量状态变化,使系统的表面能减少。
烧结是一个自发的不可逆过程,系统表面 能降低是推动烧结进行的基本动力。
表面张力能使凹、凸表面处的蒸气压P分别低 于和高于平面表面处的蒸气压Po,并可以用开尔 文本公式表达:
粘性流动传质 : 若存在着某种外力场,如表面张力作用时,
则质点(或空位)就会优先沿此表面张力作用的
方向移动,并呈现相应的定向物质流,其迁移
烧结

第九章烧结§9-1 概述本节主要内容有:1)烧结定义;2)与烧结有关的一些概念;3)烧结过程推动力;4)烧结模型一、烧结定义如下图9.1所示,为烧结过程中坯体所发生的变化。
由图可见,在烧结过程中,体系发生如下物理化学过程:颗粒间由点接触开始(图9.1a)→接触面积扩大→颗粒聚集→颗粒中心距逼近(图9.1b)→逐渐形成晶界→气孔形状发生变化→体积缩小,连通的气孔变成各自孤立的气孔→大部分气孔从晶体中排除。
这些物理过程随烧结温度的升高而逐渐推进。
图9-1烧结过程中坯体所发生的变化1.定义:根据烧结过程中所出现的宏观变化可以认为:一种或多种固体(金属、氧化物、氮化物、粘土…)粉末经过成型,在加热到一定温度后气孔排除、体积收缩,在低于熔点温度下变成致密、坚硬的烧结体,这种过程称为烧结。
2、烧结程度衡量指标:在烧结过程中,宏观上出现体积收缩、致密度提高和强度增加。
通常采用坯体收缩率、气孔率、吸水率、烧结体密度与理论密度之比(相对密度)等指标来衡量。
如下图9-2所示。
二、与烧结有关的一些概念1、烧结与烧成:烧成包括多种物理或化学变化,如脱水、坯体内气体分解、多相反应和熔融、溶解、烧结等。
而烧成仅仅指粉料经加热而致密化的简单物理过程。
因此,烧结仅仅是烧成过程的一个重要部分。
2、烧结与熔融:烧结是在远低于固态物质的熔融温度下进行的。
烧结与熔融这两个过程都是由原子热振动而引起的,但熔融时全部组元均转变为液相,而烧结时至少有一组元是固态。
3、烧结与固态反应:这两个过程均在低于材料熔点或熔融温度之下进行,并且在过程的自始至终至少有一相是固态。
在固相反应的过程中,组分间在高温下发生化学反应,但在烧结过程中,组分间并不发生化学反应。
三、烧结过程推动力:1、推动力:近代烧结理论认为,粉状物料的表面能大于多晶烧结体的晶界能,这就是烧结的推动力。
粉体经烧结后,晶界能取代了表面能,这就是多晶材料稳定存在的原因。
2、表面能来源:粉料在粉碎与研磨的过程中消耗的机械能,以表面能形式贮存在粉体中;粉碎引起晶格缺陷,使内能增加。
无机材料科学基础 第9章 烧结

二、与烧结有关的一些概念
1、
烧结(sintering)与烧成(firing)
烧成包括多种物理和化学变化。而
烧结仅仅指粉料经加热而致密化的 简单物理过程,显然烧成的含义及 包括的范围更宽,一般都发生在多 相系统内。而烧结仅仅是烧成过程
的一个重要部分。
二、与烧结有关的一些概念
2、
烧结和熔融(melting)
固体颗粒表面曲率不同,在高温时必然在 再凝聚实现质点的迁移,促进烧结。 这种传质过程仅仅在高温下蒸气压较大的
系统的不同部位有不同的蒸气压。质点通过蒸发,
系统内进行,如氧化铅、氧化铍和氧化铁的烧结。
蒸发—凝聚传质采用中心距不变的双球模型, 如图9—4示。 在球形颗粒表 面有正曲率半 径,而在两个 颗粒联接处有 一个小的负曲 率半径的颈部
3/ 2
1/ 3
r
2 / 3
t
1/ 3
此方程得出了颈部半径(x)和影响生长速
率的其它变量(r,P0,t之间的相互关系。
如图9-5(A)和9-5(B)。
影响蒸发—凝聚传质的因素:
1、不能用延长烧结时间促进烧结。
2、粉末的起始粒度愈小,烧结速率愈大。 3、提高烧结温度,可以提高烧结速率。
第九章 烧 结
Chapter 9 Sintering
§9—1
概
述
§9—1 Introduction
烧结目的:把粉状物料转变为致密体
当原料配方、粉体粒度、成型等工序完成以后,烧结 是使材料获得预期的显微结构以使材料性能充分发挥 的关键工序 一般说来,粉体经过成型后,通过烧结得到的致密体 是一种多晶材料。其显微结构由晶体、玻璃体和气孔 组成。烧结过程直接影响显微结构中晶粒尺寸、气孔 尺寸及晶界形状和分布。
烧结过程概述
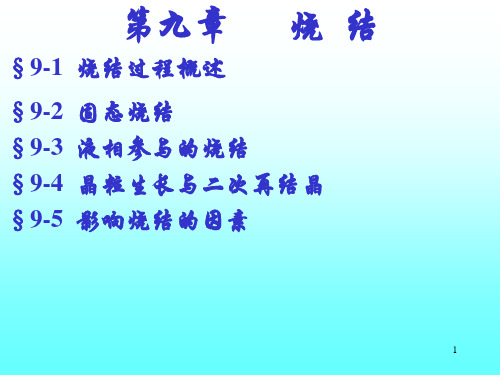
§9-1 烧结过程概述 §9-2 §9-3 §9-4 §9-5
烧 结
固态烧结 液相参与的烧结 晶粒生长与二次再结晶 影响烧结的因素
1
§9-1 烧结过程概述
烧结是粉末冶金、陶瓷、耐火材料、超高温材料等学 科的一个重要工序。烧结的目的是把粉状物料转变为致密 体。
一.烧结的定义
1.烧结——一种或多种固体粉末经过成型,在一定温度下 开始收缩,排除气孔致密化,在低于熔点温度下变成致密 、坚硬的烧结体的过程称为烧结。
作用在ABCD面积元上的应力ζ为:
F 1 1 2 ( x) ( ) 2 S x x
ζ≈-/ρ
13
2.晶粒中心靠近机理
颗粒接触点处的应力使扩散传质中的物质定向迁移。物质向气 孔迁移,而空位(气孔作为空位源)作反向迁移。
如图,颈部中心受到压应力ζ2, 在压应力区,空位浓度低; 颈部表面受到张应力ζρ, 在张应力区,空位浓度高。
2
空位由浓度高的区域向浓度低的区域迁移,即由颈部表面→颈 部中心(颗粒内部)迁移; 质点作反方向迁移,即由颈部中心(颗粒内部)→颈部表面迁 移。结果使颗粒中心距离缩短。
14
设:颗粒内部空位浓度[C0],空位形成能ΔGf; 颈部中心空位浓度[Cn],空位形成能ΔGf+ζΩ; 颈部表面空位浓度[Ct],空位形成能ΔGf-ζΩ; ζΩ——形成体积为Ω空位所做的附加功。 不同部位的空位形成能不同,其次序为: 压应力区空位形成能>无应力区>张应力区; 空位浓度计算表达式:
2.烧结与熔融
相同点:都是由高温下质点迁移的结果。 不同点:熔融通过质点迁移其间距增大,并且全部组元都 处于液态; Tamman提出烧结温度TS与熔融温度TM间的规律:硅酸盐 TS=0.8-0.9TM
第九章烧结
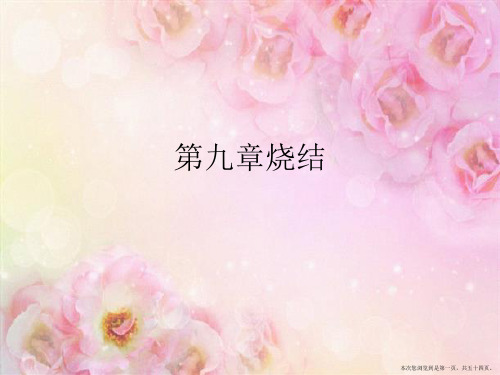
由颗粒中心距逼近而引起的收缩:
V V3LL49rt
本次您浏览到是第三十二页,共五十四页。
(5)影响粘性烧结的因素
1)粒径:10μm减少至1μm,烧结速率增大10倍。
2)粘度:粘度和粘度随温度的迅速变化是需要控制的最重要因素。 一个典型钠钙硅玻璃,若温度变化100℃,粘度约变化1000倍。 如果某坯体烧结速率太低,可以采用加入液相粘度较低的 组分来提高烧结速率。
3、传质过程 第一阶段:颗粒重排
T ,出现足够量液相,固相颗粒在P 作下 重
新排列,收缩率60%以上;
第三阶段:溶解-沉析
小颗粒接触点处被溶 解
液相传质
→晶粒长大,坯体致密
较大颗粒沉 积
本次您浏览到是第三十六页,共五十四页。
4、影响因素: 时间 颗粒的起始粒度 溶解度、润湿性 液相数量 烧结温度。
t
2、温度 T 增加,有利于烧结。 3、颗粒粒度 ,愈小烧结速率愈大。 4、特点:烧结时颈部扩大,气孔形状改变,但双球 之间中
心距不变,因此坯体不发生收缩,密度不变。
本次您浏览到是第十七页,共五十四页。
二、扩散传质
对象:多数固体材料,由于其蒸汽压低。 1、扩散传质机理
应力分析:
颈部表面→张应力 颗粒接触点→压应力 颗粒中心→无应力
扩散途径 空位扩散:优先由颈表面接触点; 其次由颈表面内部扩散 原子扩散:与空位扩散方向相反, 扩散终点:颈部。 扩散途径:(参见图9-8)
本次您浏览到是第二十页,共五十四页。
2、扩散传质的三个阶段
1)初期(x/r﹤0.3):表面扩散为主
(因为表面扩散温度<<体积扩散温度)
例 Al2O3 T表面=330℃ T体积=900℃; 特点:气孔率大,收缩约1%。 原因:表面扩散对空隙的消失和烧结体收缩
烧结原理(详细资料)
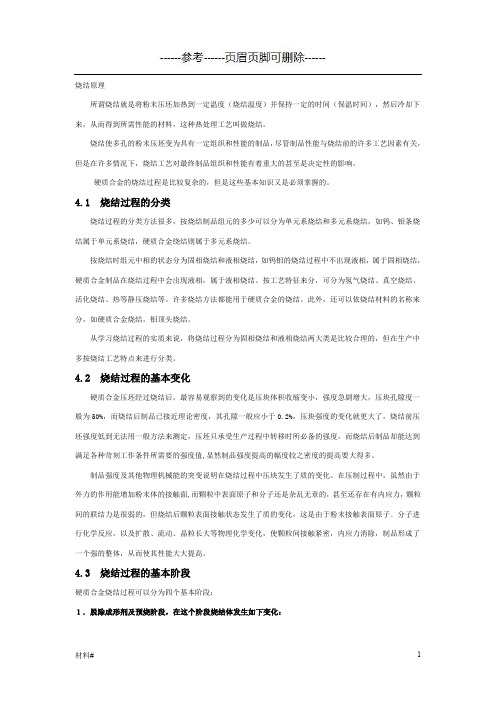
烧结原理所谓烧结就是将粉末压坯加热到一定温度(烧结温度)并保持一定的时间(保温时间),然后冷却下来,从而得到所需性能的材料,这种热处理工艺叫做烧结。
烧结使多孔的粉末压坯变为具有一定组织和性能的制品,尽管制品性能与烧结前的许多工艺因素有关,但是在许多情况下,烧结工艺对最终制品组织和性能有着重大的甚至是决定性的影响。
硬质合金的烧结过程是比较复杂的,但是这些基本知识又是必须掌握的。
4.1 烧结过程的分类烧结过程的分类方法很多,按烧结制品组元的多少可以分为单元系烧结和多元系烧结,如钨、钼条烧结属于单元系烧结,硬质合金绕结则属于多元系烧结。
按烧结时组元中相的状态分为固相烧结和液相烧结,如钨钼的烧结过程中不出现液相,属于固相烧结,硬质合金制品在烧结过程中会出现液相,属于液相烧结。
按工艺特征来分,可分为氢气烧结、真空烧结、活化烧结、热等静压烧结等。
许多烧结方法都能用于硬质合金的烧结。
此外,还可以依烧结材料的名称来分,如硬质合金烧结,钼顶头烧结。
从学习烧结过程的实质来说,将烧结过程分为固相烧结和液相烧结两大类是比较合理的,但在生产中多按烧结工艺特点来进行分类。
4.2 烧结过程的基本变化硬质合金压坯经过烧结后,最容易观察到的变化是压块体积收缩变小,强度急剧增大,压块孔隙度一般为50%,而烧结后制品已接近理论密度,其孔隙一般应小于0.2%,压块强度的变化就更大了,烧结前压坯强度低到无法用一般方法来测定,压坯只承受生产过程中转移时所必备的强度,而烧结后制品却能达到满足各种苛刻工作条件所需要的强度值,显然制品强度提高的幅度较之密度的提高要大得多。
制品强度及其他物理机械能的突变说明在烧结过程中压块发生了质的变化。
在压制过程中,虽然由于外力的作用能增加粉末体的接触面,而颗粒中表面原子和分子还是杂乱无章的,甚至还存在有内应力,颗粒间的联结力是很弱的,但烧结后颗粒表面接触状态发生了质的变化,这是由于粉末接触表面原子﹑分子进行化学反应,以及扩散、流动、晶粒长大等物理化学变化,使颗粒间接触紧密,内应力消除,制品形成了一个强的整体,从而使其性能大大提高。
烧结内容提要本章叙述了烧结定义推动力和基本模型分析
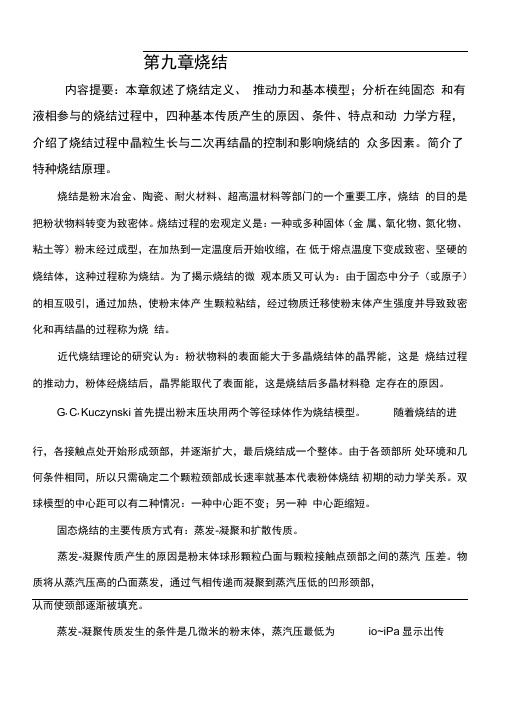
第九章烧结内容提要:本章叙述了烧结定义、推动力和基本模型;分析在纯固态和有液相参与的烧结过程中,四种基本传质产生的原因、条件、特点和动力学方程,介绍了烧结过程中晶粒生长与二次再结晶的控制和影响烧结的众多因素。
简介了特种烧结原理。
烧结是粉末冶金、陶瓷、耐火材料、超高温材料等部门的一个重要工序,烧结的目的是把粉状物料转变为致密体。
烧结过程的宏观定义是:一种或多种固体(金属、氧化物、氮化物、粘土等)粉末经过成型,在加热到一定温度后开始收缩,在低于熔点温度下变成致密、坚硬的烧结体,这种过程称为烧结。
为了揭示烧结的微观本质又可认为:由于固态中分子(或原子)的相互吸引,通过加热,使粉末体产生颗粒粘结,经过物质迁移使粉末体产生强度并导致致密化和再结晶的过程称为烧结。
近代烧结理论的研究认为:粉状物料的表面能大于多晶烧结体的晶界能,这是烧结过程的推动力,粉体经烧结后,晶界能取代了表面能,这是烧结后多晶材料稳定存在的原因。
G• C• Kuczynski首先提出粉末压块用两个等径球体作为烧结模型。
随着烧结的进行,各接触点处开始形成颈部,并逐渐扩大,最后烧结成一个整体。
由于各颈部所处环境和几何条件相同,所以只需确定二个颗粒颈部成长速率就基本代表粉体烧结初期的动力学关系。
双球模型的中心距可以有二种情况:一种中心距不变;另一种中心距缩短。
固态烧结的主要传质方式有:蒸发-凝聚和扩散传质。
蒸发-凝聚传质产生的原因是粉末体球形颗粒凸面与颗粒接触点颈部之间的蒸汽压差。
物质将从蒸汽压高的凸面蒸发,通过气相传递而凝聚到蒸汽压低的凹形颈部,从而使颈部逐渐被填充。
蒸发-凝聚传质发生的条件是几微米的粉末体,蒸汽压最低为io~iPa显示出传质效果。
这种传质的特点是烧结时颈部扩大,气孔形状改变,但双球之间中心距不变,因此由蒸发-凝聚单一传质发生烧结,坯体不发生收缩,即「丄L = 0。
扩散传质是大多数固体材料烧结传质的主要形式。
产生扩散传质的原因是颗粒不同部位空位浓度差。
烧结动力学模型及其机理..

第九章烧结动力学模型及其机理烧结是粉末冶金、陶瓷、耐火材料、超高温材料和金属陶瓷等生产过程的一个重要工序。
任何粉体经成型后必须烧结才能赋予材料各种特殊的性能。
陶瓷烧结体是一种多晶材料。
材料性能不仅与材料组成有关,而且还与材料的显微结构有密切关系。
当配方、原料粒度、成型等工序完成以后,烧结是使材料获得预期的显微结构以使材料性能充分发挥的关键工序。
因此了解粉末烧结过程及机理,了解烧结过程动力学对控制和改进材料性能有着十分重要的意义。
9.1 烧结的定义烧结通常是指在高温作用下粉体颗粒集合体表面积减少、气孔率降低、颗粒间接触面加大以及机械强度提高的过程。
烧结是一复杂的物理化学过程,除物理变化外,有的还伴随有化学变化,如固相反应。
这种由固相反应促进的烧结,又称反应烧结。
高纯物质通常在烧结温度下基本上无液相出现;而多组分物系在烧结温度下常有液相存在。
有无液相参加其烧结机理有原则区别,所以将烧结分为无液相参加的烧结(或称纯固相烧结),及有液相参加的烧结(或称液相烧结)两类。
另外还有一些烧结过程,如热压烧结等,其烧结机理有其特殊性。
陶瓷粉料成型后变成具有一定外形的坯体,坯体内一般包含着百分之几十的气孔(约25-60%),而颗粒之间只有点接触,如图9.1(a)所示。
在高温下所发生的主要变化是:颗粒间接触界面扩大,逐渐形成晶界;气孔的形状变化,如图(b),体积缩小,从连通的气孔变成各自孤立的气孔并逐渐缩小,如图(c),以致最后大部分甚至全部气孔从坯体中排除。
这就是烧结所包含的主要物理过程。
图9.1 气孔形状及尺寸的变化示意图烧结必须在高温下进行,但烧结温度及烧结温度范围,因原料种类、制品要求及工艺条件不同而异。
纯物质的烧结温度与其熔点间有一近似关系,如金属的开始烧结温度约为0.3-0.4T M(熔点),无机盐类约为0.57T M,硅酸盐类约为0.8-0.9T M。
由此可见,开始烧结温度都低于其熔融温度。
实验证明,物料开始烧结温度,常与其质点开始迁移的温度一致。
第9章 材料的烧结02

热压烧结 热压烧结是一种单向 加压的压力烧结方式. 简单地说就是高温下的 干压成型.
优点: 缩短烧结所需时间,降低烧结温度; 烧结体致密度高; 坯体成型所需压力低. 缺点: 只能生产简单形状制品; 单件生产,效率低; 制品表面较粗糙,精度低,需要后期加工; 模具耗损大,寿命短.
气压烧结 在炉膛内充填 某种气氛的气 体,气压高于外 界气压. 主要用 于防止坯体成分 分解挥发.
如果坯体中原始晶粒尺寸是均匀的,在烧结过程中晶粒生长 按D2-D02=Kt 进行,直至达到极限尺寸D1为止. 此时烧结体中 每个晶粒的晶界数为3~8个,晶界曲率都不大,不能使晶界越 过夹杂物运动,晶粒生长停止. 如果烧结体的细晶粒基相中有少数晶界数大于10的晶粒,其 晶粒尺寸大于平均晶粒尺寸,这些大晶粒就成为二次再结晶的 晶核,其长大速率在开始阶段取决于晶粒的边数. 当长大到某一程度时,大晶粒直径Dg>>Dm,其生长驱动力随 之增大,晶界移动时快速扫过气孔,在短时间内将第一代小晶 粒吞并,生成含有封闭气孔的大晶粒,导致不连续的晶粒生长.
以硅碳棒为发热体,最高加热温度1450℃.
以硅钼棒为发热体,最高加热温度1700℃.
ZrO2发热体高温电炉
氮气炉
最高加热温度2000℃ 氧化气氛:ZrO2发热体 中性气氛:石墨发热体
2.压力烧结
压力烧结是在加热时对烧结体施加一定的压力促使其致 密化的烧结方法. 烧结体的致密化主要依靠外加压力作用下的物质迁移来 完成. 故压力烧结温度通常无压烧结低得多,可使烧结体 的晶粒几乎不生长或生长很少的情况下得到接近理论密度 的致密陶瓷材料. 施加机械压力:热压烧结 施加气压:气压烧结、高温等静压烧结
1650℃, 1h
1650℃, 4h
- 1、下载文档前请自行甄别文档内容的完整性,平台不提供额外的编辑、内容补充、找答案等附加服务。
- 2、"仅部分预览"的文档,不可在线预览部分如存在完整性等问题,可反馈申请退款(可完整预览的文档不适用该条件!)。
- 3、如文档侵犯您的权益,请联系客服反馈,我们会尽快为您处理(人工客服工作时间:9:00-18:30)。
可见,作为烧结动力的表面张力可以通 过流动、扩散和液相或气相传递等方式 推动物质的迁移。
三、 烧结机理
(一) 颗粒的粘附作用 (二) 物质的传递
1. 颗粒的粘附作用 例子: 把两根新拉制的玻璃纤维相互叠放在一起,
金属粉末Ts≈(0.3—0.4)Tm 无机盐类Ts≈0.57Tm 硅酸盐类Ts≈(0.8—0.9)Tm
实验表明,物料开始烧结温度常与其质点开始明 显迁移的温度一致。
§9.2 烧结过程及机理 一、烧结过程
首先从烧结体的宏观性质随温度的变化上
来认识烧结过程。
+ (一)烧结温度对烧结体性质的影响
+
图1是新鲜的电解铜粉(用氢还原的), 经高压成型后,在氢气气氛中于不同温度 下烧结2小时然后测其宏观性质:密度、比 电导、抗拉强度,并对温度作图,以考察 温度对烧结进程的影响。
烧结中期
烧结后期
二、烧结推动力
粉体颗料尺寸很小,比表面积大,具有
较高的表面能,即使在加压成型体中,颗料
间接面积也很小,总表面积很大而处于较高 能量状态。根据最低能量原理,它将自发地 向最低能量状态变化,使系统的表面能减少。
烧结是一个自发的不可逆过程,系统表面 能降低是推动烧结进行的基本动力。
表面张力能使凹、凸表面处的蒸气压P分别低 于和高于平面表面处的蒸气压Po,并可以用开尔 文本公式表达: 对于球形表面
二、烧结的定义
压制成型后的粉状物料在低于熔点的高温 作用下、通过坯体间颗粒相互粘结和物质传递, 气孔排除,体积收缩,强度提高、逐渐变成具 有一定的几何形状和坚固坯体的过程。 通常用烧结收缩、强度、容重、气孔率等物理 指标来衡量物料烧结质量的好坏。
三、烧结分类
按照烧结时是否出现液相,可将烧结分为两类: 固相烧结
一、烧结理论的研究与发展
烧结理论的研究对象是粉末和颗粒的烧结 过程。这些粉末和颗粒可以使晶体或非晶体、 工程陶瓷或耐火材料、金属或合金。
烧结理论的第一次飞跃:1945年,晶体中的粘性流 动、颗粒表面的原子迁移; 烧结理论的第二次飞跃:1971年,第二层面的烧结 理论研究 烧结理论的第三次飞跃:计算机模拟技术的运用和 发展。
从材料动力学角度看烧结过程的进行依赖于 基本动力学过程—扩散,因为所有传质过程都依 赖于质点的迁移。烧结中粉末物料的种种变化, 还会涉及到相变、固相反应等动力学过程,尽管 烧结的进行在某些情况下并不依赖于相变和固相 反应等的进行。烧结是材料高温动力学中最复杂 的动力学过程。 无机材料的性能不仅与材料组成有关,还与 材料的显微结构有关。配方相同而晶粒尺寸不同 的烧结体,由于晶粒在长度或宽度方向上某些参 数的叠加,晶界出现频率不同,从而引起材料性 能的差异。如细小晶粒有利于强度的提高;材料 的电学和磁学参数在很宽的范围内也收到晶粒尺 寸的影响;
第九章 烧 结
烧 结 过 程 及 机 理
概
述
再 结 晶 和 晶 粒 长 大
影 响 烧 结 的 因 素
§9.1 概述
烧结过程是一门古老的工艺,早在公元前3000 年,人类就掌握了这门工艺,但对烧结理论的研 究和发展仅开始于20世纪中期。现在,烧结过程 在许多工业部门得到广泛应用,如陶瓷、耐火材 料、粉末冶金、超高温材料等生产过程中都含有 烧结过程。 烧结的目的是把粉状材料转变为致密体,并 赋予材料特有的性能。烧结得到块体材料是一种 多晶材料,其显微结构由晶体、玻璃体和气孔组 成。烧结直接影响显微结构中晶粒尺寸和分布、 气孔大小形状和分布及晶界的体积分数等。
烧结温度下基本上无液相出 现的烧结,如高纯氧化物之 间的烧结过程。 有液相参与下的烧结,如多组 分物系在烧结温度下常有液相 出现。
液相烧结
近年来,在研制特种结构材料和功能材料的同时,产 生了一些新型烧结方法。如热压烧结,放电等离子体 烧结,微波烧结等。
三、烧结温度和熔点的关系
泰曼指出,纯物质的烧结温度Ts与其熔点Tm有如 下近似关系:
烧结过程的模型示意图
根据烧结性质随温度的变化,我们可以把烧结过程 用下图的模型来表示,以增强我们对烧结过程的感 性认识。
a)烧结前
b)烧结后
铁粉烧结的SEM照片
烧 结 过 程 的 三 个 阶 段
烧结初期
坯体中颗粒重排,接触处 产生键合,空隙变形、缩 小(即大气孔消失),固气总表面积没有变化。 传质开始,粒界增大,空 隙进一步变形、缩小,但 仍然连通,形如隧道。 传质继续进行,粒子长大, 气孔变成孤立闭气孔,密 度达到95%以上,制品强 度提高。
除晶粒尺寸外,微结构中的气孔常成为应力 的集中点而影响材料的强度;气孔又是光散射中 心而使材料不透明;烧结过程可以通过控制晶界 移动而抑制晶粒的异常生长,或通过控制表面扩 散、晶界扩散和晶格扩散而填充气孔,改善材料 性能。因此,当配方、原料粒度、成型等工序完 成后,烧结是使材料获得预期的显微结构以使材 料性能充分发挥的关键工序。 研究物质在烧结过程中的各种物理化学变化。 对指导生产、控制产品质量,研制新型材料显得 特别重要。
比电导(Ω-1· cm-3)
密度(影响 l一比电导 2一拉力 3一密度
+ 结果与讨论: 随烧结温度的升高,比电导和抗拉强度增加。 曲线表明,在颗粒空隙被填充之前 (即气孔率
显著下降以前),颗粒接触处就已产生某种键 合,使得电子可以沿着键合的地方传递,故 比电导和抗拉强度增大。 温度继续升高,物质开始向空隙传递,密度 增大。当密度达到理论密度的 90 ~ 95 %后, 其增加速度显著减小,且常规条件下很难达 到完全致密。说明坯体中的空隙(气孔)完全排 除是很难的。
P 2M ln P0 RTr
(1)
对于非球形表面
P M 1 1 ln ( ) P0 RT r1 r2
(2)
表面凹凸不平的固体颗粒,其凸处呈正压,凹处呈负 压,故存在着使物质自凸处向凹处迁移。
如果固体在高温下有较高蒸气压,则可以通 过气相导致物质从凸表面向凹表面处传递。 此外若以固体表面的空位浓度 C 或固体溶解 度 L 分别代替式 2 中的蒸气压 P ,则对于空位 浓度和溶解度也都有类似于式 2的关系,并 能推动物质的扩散传递。