制造工程基础课件
制造工程基础-第4章互换性原理

第四章公差及互换性4.1互换性原理1)互换性的概念实例(1)互换性的含义互换性是指按照同一规格制造的零件或部件,不经选择或辅助加工,任取其一,装配后就能满足预定的使用性能的性质。
(2)互换性的种类根据互换程度的不同,互换性可以分为以下两类。
完全互换又称绝对互换,即完全达到了上述互换性的要求。
即当零、部件在装配或更换时,事先不必挑选,装配时也无须进行修配就能装配在机器上,并能完全满足预定的使用性要求。
不完全互换又称有限互换,即装配时需要选择、分组或调整。
如,当对零件的精度要求很高时,为了便于制造,常在制造时把零件的公差适当放大,在装配前先根据零件的实际尺寸分组,然后按组进行装配,以保证预先规定的使用性能要求。
零件只能在本组内进行互换,这就属于不完全互换。
不完全互换也是保证产品使用性能的重要手段,是完全互换的必要补充。
对标准的部件,互换性还可分为内互换与外互换:组成标准部件的零件的互换称内互换,标准部件与其他部件的互换称外互换。
2)互换性的作用互换原则是现代化生产所必须遵循的基本原则之一。
应用互换性原则已成为提高生产水平和促进技术进步的强有力的手段。
(1) 简化设计工作:在设计上,采用具有互换性的标准零件和标准部件,将简化设计工作量,缩短设计周期,且便于应用计算机进行辅助设计。
(2) 缩短装配周期:在生产上,按互换性原则进行加工,各个零件可以同时分别加工,便于实现专业化、自动化生产。
由于工件单一,易于保证加工质量。
装配时,由于零、部件具有互换性,使装配过程能够连续而顺利地进行,从而大大缩短了装配周期。
(3) 缩短修理时间:在使用和修理上,具有互换性的备用零件和部件可以简单而迅速地替换磨损的或损坏的零、部件,这将缩短修理时间,节约修理费用,保证机器工作的连续性。
这一点尤其对重要设备和军用品的修复更具有重大意义。
(4) 简化管理:在管理上,使管理更简化、更科学,产品质量也更容易保证。
(5) 降低生产成本:在经济上,它缩小了生产规模,减少了不必要的厂房、设备、设施和相应的管理、技术、操作人员,这些都将大大降低生产的成本。
制造业基础知识 (1)
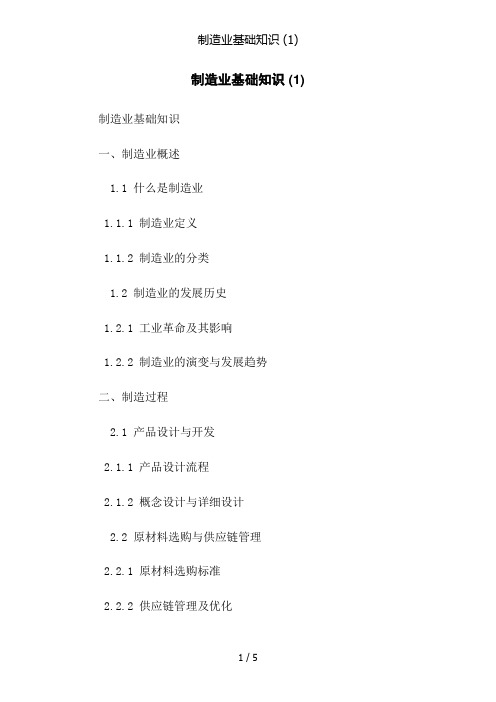
制造业基础知识 (1) 制造业基础知识一、制造业概述1.1 什么是制造业1.1.1 制造业定义1.1.2 制造业的分类1.2 制造业的发展历史1.2.1 工业革命及其影响1.2.2 制造业的演变与发展趋势二、制造过程2.1 产品设计与开发2.1.1 产品设计流程2.1.2 概念设计与详细设计2.2 原材料选购与供应链管理2.2.1 原材料选购标准2.2.2 供应链管理及优化2.3 生产计划与调度2.3.1 生产计划编制2.3.2 生产调度与控制2.4 制造过程与质量控制 2.4.1 制造流程管理2.4.2 质量控制方法及工具 2.5 产品组装与包装2.5.1 产品组装流程2.5.2 包装与运输要求三、制造工艺与设备3.1 传统制造工艺3.1.1 铸造工艺3.1.2 锻造工艺3.1.3 机械加工工艺3.2 先进制造工艺3.2.1 数控加工工艺3.2.2 激光切割工艺3.2.3 3d打印工艺3.3 机械设备与自动化3.3.1 传统机械设备3.3.2 自动化生产线3.3.3 应用与发展四、质量管理与标准化4.1 质量管理体系4.1.1 iSO9001质量管理体系 4.1.2 六西格玛质量管理方法 4.1.3 TPM全员生产管理4.2 质量控制与测试4.2.1 检测方法及工具4.2.2 非破坏性测试技术4.3 标准化与认证4.3.1 国内外质量标准4.3.2 产品认证与标志五、制造业发展趋势与挑战5.1 智能制造与工业互联网5.2 绿色制造与可持续发展5.3 与制造业应用5.4 制造业的国际竞争与合作附录:1.附件一:制造业相关数据统计报告2.附件二:制造业政策法规摘要法律名词及注释:1.法律名词1:解释12.法律名词2:解释23.法律名词3:解释3附件:附件一:制造业相关数据统计报告可参考相关统计机构发布的最新制造业统计数据,包括产值、销售额、利润等信息。
附件二:制造业政策法规摘要提供有关制造业的相关政策法规摘要,包括质量标准、工业安全等方面的规定。
《基础工业工程》课件

工业工程的应用领域
制造业
生产线的规划与设计、生产过程的优 化等。
物流业
服务业
服务流程的优化、服务系统的设计等。
物流系统的规划、配送路线的优化等。
工业工程的发展历程
01
02
03
起源
20世纪初,美国工程师泰 勒提出了“科学管理”理 论,为工业工程的发展奠 定了基础。
发展
20世纪中叶,随着制造业 的快速发展,工业工程得 到了广泛应用。
包括效率性、准确性和安全性等原 则。
质量控制与可靠性工
05
程
质量控制方法
统计过程控制
通过收集和分析生产过程中的数据,控制产品质量并 预防缺陷的产生。
抽样检验
从生产批次中抽取部分产品进行检验,以评估整批产 品的质量。
过程能力分析
评估生产过程的稳定性和一致性,确保产品质量满足 要求。
质量管理体系
ISO 9001
现状
现代工业工程融合了计算 机技术、人工智能等先进 技术,为生产制造系统的 优化提供了更多可能性。
生产运作管理
02
生产计划与控制
生产计划
制定生产计划,明确生产任务、 生产时间和生产数量,确保生产 活动的有序进行。
生产控制
对生产过程进行监控,及时调整 生产进度,确保生产计划的顺利 实施。
生产调度与排程
作业分析
作业流程分析
对生产过程中的作业流程进行详细分析,识别瓶颈环节和浪费现象。
作业单元划分
将复杂的作业过程划分为若干个相对独立的作业单元,便于进行有效的管理和优化。
动作研究
动作要素分析
对作业人员的操作动作进行分解和分析,找出最优的操作顺序和方法。
动作经济原则
制造业基础知识 (1)

制造业基础知识 (1)制造业基础知识 (1)制造业是指以物质为基础,通过一系列工艺流程将原材料或半成品转化为最终产品的过程。
它是现代工业生产的重要组成部分,为经济发展提供了关键支持。
制造业的历史制造业的历史可以追溯到远古时期,人类开始使用简单的工具以及手工艺技巧制造各种物品。
随着时间的推移,人类的制造技术不断进步,从而形成了现代制造业。
制造业的分类制造业可以根据产品的性质进行分类,常见的制造业包括机械制造、电子制造、化工制造、食品制造等。
不同的制造业具有不同的特点和工艺流程。
制造业的重要性制造业对于一个国家的经济发展具有重要的意义。
制造业可以创造就业机会,提供稳定的收入来源。
制造业的发展可以带动其他相关产业的发展,形成良性循环。
制造业的增长可以提高一个国家的国际竞争力。
制造业的挑战虽然制造业发展带来了众多的好处,但也面临一些挑战。
全球化竞争加剧,制造企业需要不断提高产品质量和技术水平,以满足市场需求。
和自动化技术的发展使得一些传统的制造岗位面临失业的风险。
环境保护的要求越来越严格,制造企业需要注重可持续发展,减少对环境的影响。
制造业的发展趋势随着技术的不断发展,制造业将面临一系列的变革。
智能制造将成为制造业的主要发展方向,通过融合物联网、大数据和等技术,提高生产效率和产品质量。
个性化定制将成为制造业的趋势,消费者对于个性化产品的需求不断增加,制造业需要快速调整生产模式。
可持续发展将成为制造业的重要目标,减少资源的消耗和环境的污染。
结论制造业作为现代工业发展的基础,具有重要的地位和作用。
随着技术的进步和市场的变化,制造业面临着许多挑战和机遇。
只有不断创新和适应变化,才能在竞争中立于不败之地。
工程材料及机械制造基础 PPT课件
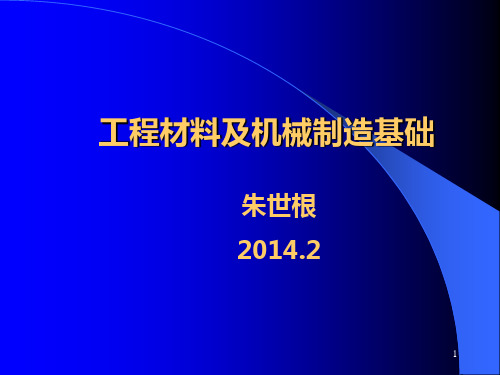
二、物理性能和化学性能
如:比重、熔点、耐腐蚀性等。
22
三、工艺性能
(材料适应成型加工工艺的能力, 反映对材料成型加工的难易程度) 铸造性能 压力加工性能 焊接性能 切削加工性能 热处理工艺性能
23
思考:
1、金属材料的机械性能中哪个性能最好? 2、已知某钢材的σS =240 MPa,σb =400
C: C↑——σ、HB↑,δ、ak↓。 当C>0.9%时,σ↓ Si: Si↑——σ、HB↑,δ、ak↓。 但∵Si含量少,故影响不大。 Mn: Mn↑——σ、HB↑,并减少S的危害。也
∵Mn含量少,故影响不大。 S: 生成FeS,FeS与Fe形成晶体(985℃熔点),
易热脆(高温加工时容易产生裂纹)。 P: P↑——σ、HB↑,δ、ak↓↓。易冷脆(钢在低
布氏硬度: 以压痕单位球面积上所承受载荷的大小, 作硬度值。(HB)
洛氏硬度: 以压痕的深度来确定其的硬度值。 (HRC)
19
HBS 压头为淬火钢球,用于测定较软金 属材料(<450HBS)如有色金属、灰 铸铁、退火、正火、调质钢。
HBW 压头为硬质合金球,用于测定较 硬金属材料(>450HBW)。
有色金属:铜、铝、镁、钛等及其合金 陶瓷
——无机非金属材料 玻璃 混凝土 塑料
——有机高分子(高分子聚合物)材料 橡胶 纤维
金属基 ——复合材料
纤维基
5
1、材 料
1.1 材料的分类——按性能分:
——结构材料:利用材料的力学性能,所制备的各 类器件或构件是为了承受各种形式 的载荷,主要起支撑作用。
——功能材料:具有特殊的电、磁、光、热、声、 力、化学性能和理化效应的各种新 材料。 用以对信息和能量的感受、计划、 输运、屏蔽、绝缘、吸收、控制、 记忆、存储、显示、发射、转化和 变换的目的。
机械制造基础课件

时间
§1钢的热处理原理 一.钢在加热时的组织转变 1.实际转变温度、过热度与过冷度:
2.钢在加热时的组织转变
钢在加热到AC1以上温度时的组织转变
P (F+Fe3C ) A
孕育期:从保温到奥氏体形成,这段时间叫孕育 期 晶粒度分8级,晶粒度级别越小,晶粒越粗。 加热温度越高、保温时间越长、加热速度越慢, 则奥氏体晶粒越粗。
(三) 含碳量与组织、性能的关系
(四) 相图的应用: 铁碳合金相图主要用于铸造、锻造、焊接、 热处理等热加工工艺的制定
第四章 钢的热处理
§1钢的热处理原理
§2钢的热处理工艺
钢的热处理的定义
将钢在固态下加热到一定温度,并保持一 段时间,以适当的冷却速度进行冷却,以改变 钢的组织,从而获得预期性能的工艺方法。
2.冷却曲线及过冷度
实际结晶温度低于熔点,称为过冷,其差值为 过冷度。
冷却速度越大,过冷度也越大。
3.结晶过程 结晶过程=晶核形成+晶核成长
晶核来源:自发形核、外来形核
树枝晶的成长
尖端处散热快,温度低,过冷度大,成长动力大, 长得快,形成一次晶轴、二次晶轴等,直到晶间 填满。形成大小不一、方向不同的多晶体。
2.奥氏体A:
由C固溶于γ铁中形成的间隙固溶体,对碳的溶解度 1148℃时为 2.11% , 727℃ 时为0.77% 。A是高温组 织,在727℃以上存在,其强度、硬度较低,塑性好。
3.渗碳体Fe3C:
由铁和碳形成的化合物,含碳量6.69%。硬度高,强 度低,塑性、韧性极差。是钢的主要强化相,其形状、 数量、大小及分布对性能有很大影响。
3.淬火方法
4.钢的淬透性 由表面至50%马氏体的距离为淬硬性深度 影响因素: 化学成分 加热温度和保温时间
机械制造工程技术基础:特种加工技术

激光器
机械系统
12.5 激光加工
❖12.5.3 激光对焦
演示
12.5 激光加工
❖12.5.4 激光器加工的范围(皮革纺织)
12.5 激光加工
❖12.5.4 激光器加工的范围(广告工艺)
12.5 激光加工
❖12.5.4 激光器加工的范围(建筑模型)
12.5 激光加工
❖12.5.4 激光器加工的范围(工业加工)
机械制造工程技术基础
特种加工技术
学习内容
1 掌握特种加工的概念 2 了解特种加工典型加工原理方法 3 分析特种加工与传统加工技术的区别
引言 零件的生产制造过程是怎样的?
机械加工
机械加工
传统加工(车、铣、刨、磨、钳)
现代加工
普通数控加工
(数控车、数控铣)
特种加工
(激光演示)
12.1 特种加工
❖12.1 特种加工概念
海宝笔筒图纸
海宝笔筒产品
12.4 熔融成形制作
❖ 使用快速成形制作海宝笔筒的过程
三维模型
海宝切笔片筒处图理纸
海宝笔筒产品
后处理 工件
·
设备加工
12.4 快速成形技术
❖12.4.2 快速成形技术特点
1、高度柔性:无需任何专用夹具或工具。 2、设计制造一体化:(CAD/CAM一体化)。 3、快速性 :几个小时到几十个小时就可制造出零件。 4、自由形状制造:可以制造任意复杂的三维几何实体。 5、材料的广泛性:如纤维、塑料、纸、陶瓷、金属等。
石等硬脆材料,比用金刚石刀具切割具有切片薄、切
口窄、精度高、生产率高、经济性好的优点。
12.6 超声波加工
❖12.6.3 超声波加工应用范围
工程材料与机械制造基础-3-金属的晶体结构与结晶

17:05
金属的结晶
• 纯金属的结晶过程 • 液态金属的结晶过程分为两个阶段:① 形成晶核,② 晶核长大。
17:05
纯金属的结晶过程
• 晶核的形成过程 • 液态金属中存在着原子排列规则的小原子团,它们时 聚时散,称为晶坯。 • 在T0以下, 经一段时间后(即孕育期), 一些大尺寸的 晶坯将会长大,称为晶核。
刃型位错
螺型位错
刃型位错和螺型位错
刃型位错的形成
实际金属的结构
• 刃型位错:当一个完整晶体某晶面以上的某处多出半 个原子面,该晶面象刀刃一样切入晶体,这个多余原 子面的边缘就是刃型位错。 • 半原子面在滑移面以上的称正位错,用“ ┴ ”表示。 • 半原子面在滑移面以下的称负位错,用“ ┬ ”表示。
17:05
{110}
Z (110) (011) (011) (101) (101) Y (110)
X
17:05
金属的晶体结构
立方晶系常见的晶向为:
100 : [100]、 [010]、 [001] 110 : [110]、 [101]、 [011]、 [1 10]、 [1 01]、 [0 1 1] 111 : [111]、 [1 11]、 [1 1 1]、 [111]
密排六方晶格的参数
常见的金属晶格
• 密排六方晶格
晶格常数:底面边长 a 和高 c,
c/a=1.633
1 原子半径 :r a 2 原子个数:6 配位数: 12 致密度:0.74 常见金属: Mg、Zn、 Be、Cd等
常见的金属晶格
三种常见晶格的密排面和密排方向
•单位面积晶面上的原子数称晶面原子密度。
17:05 三斜
金属的晶体结构
现代制造系统 教学课件 罗振璧 朱耀祥 等编著 第一章 制造系统工程基础
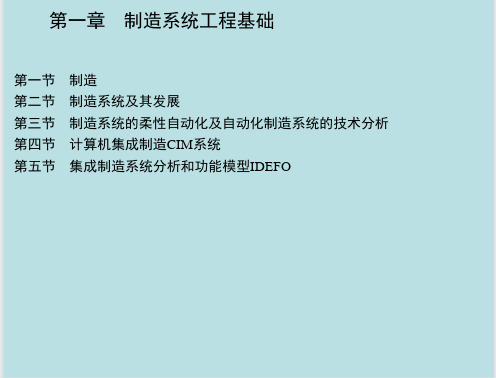
3.制造系统的发展
达到这些目标后可以满足以下制造业市场的要求: (1)可按顾客的订单与生产组织要求快速组成新产品或变换产品的批量生产能 力。 (2)能够实现无缝地“缩放”的制造系统生产规模和布局(组态)。 (3)允许方便快捷地组织多品种产品的混流生产或并流生产。 (4)能够达到低的系统重构与技术升级费用、高的生产效率,从根本上改变在 现代市场环境下传统制造系统高投资、高风险与低的投资回报率的现况。 (5)短的制造系统试生产周期和稳定可靠的加工质量与产量。
(一)企业成功的要素(一)企业成功的要素
(1)企业的市场定位、目标和实现目标的战略与商务实践。 (2)能否形成相对于其他竞争对手的竞争优势。 (3)建成企业竞争的核心能力。 (4)建立成功的制造战略。 (5)建立诚信、合作、实干与创新的企业文化。 (6)对企业或核心公司建立加盟企业群集(Enterprises Cluster)/联盟,形成 有核心能力与竞争优势的制造企业群集中心或地域制造中心,以适应经济 全球化与区域化和激烈的市场竞争。
3.制造系统的发展
图1-3 制造系统的市场环境与技术特点
图1-4
我国现代制造技术的发展现状
1. 超高速加工方面 仍处于低级阶段,还没有形成完整、系统的研究体系和方法。国内
磨削砂轮的线速度一般在45~60m/s,尚未超过80 m/s。 超高速切削/磨削技术和其机床装备,与国际先进水平相比,还有
较大差距。 2. 超精密加工方面
(二)制造企业面对的形势
1.传统制造面对的困境 2.新兴工业化国家必须走可持续发展的道路 3.传统制造业的投资效益下滑 4.产品的寿命周期迅速缩短
1.传统制造面对的困境
(1)现有产品饱和,现存的制造生产能力大量闲置。 (2)产业与研究开发R&D的转移迫使发达国家的低中技术产品、基础产业与 部分研究开发向发展中国家与地区转移。 (3)制造企业的职业吸引力迅速下滑,一流的工程技术、管理人才和技术工 人后继乏人。 (4)由于过去工业化过程中资源的滥用,已经引发了人类的生存危机。
制造业基础知识 (1)
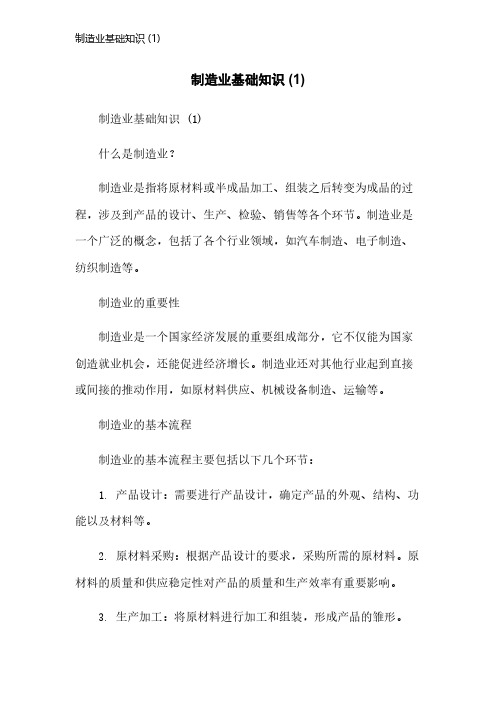
制造业基础知识 (1)制造业基础知识 (1)什么是制造业?制造业是指将原材料或半成品加工、组装之后转变为成品的过程,涉及到产品的设计、生产、检验、销售等各个环节。
制造业是一个广泛的概念,包括了各个行业领域,如汽车制造、电子制造、纺织制造等。
制造业的重要性制造业是一个国家经济发展的重要组成部分,它不仅能为国家创造就业机会,还能促进经济增长。
制造业还对其他行业起到直接或间接的推动作用,如原材料供应、机械设备制造、运输等。
制造业的基本流程制造业的基本流程主要包括以下几个环节:1. 产品设计:需要进行产品设计,确定产品的外观、结构、功能以及材料等。
2. 原材料采购:根据产品设计的要求,采购所需的原材料。
原材料的质量和供应稳定性对产品的质量和生产效率有重要影响。
3. 生产加工:将原材料进行加工和组装,形成产品的雏形。
4. 质量检验:对成品进行质量检测,确保产品符合标准和要求。
5. 包装和装运:对产品进行包装,准备出货。
6. 销售和售后服务:将产品销售给客户,并提供售后服务,解决客户的问题和需求。
制造业的技术变革随着科技的发展和创新,制造业也经历了多次技术变革。
以下是一些重要的技术变革:1. 工业革命:18世纪的工业革命是制造业史上重要的里程碑之一,它引入了机械化生产,提高了生产效率。
2. 自动化生产:20世纪的自动化生产技术使得制造业可以实现流水线生产和大规模生产,进一步提高了生产效率。
3. 信息技术的应用:随着计算机和网络技术的发展,制造业可以实现数字化管理、智能化生产等,提高了生产力和产品质量。
4. 和机器学习:和机器学习技术的应用,使得制造业可以实现智能化、自适应的生产方式,提高了生产效率和产品质量。
制造业的挑战,制造业也面临着一些挑战:1. 市场竞争:全球范围内的市场竞争加剧,需要制造业不断提高产品质量和降低成本。
2. 环境问题:制造业的发展也带来了环境问题,如污染和资源浪费等,需要采取可持续发展的方式进行生产。
智能制造工程---案例演示版ppt课件

翼监测
智
件
功能的 发动机
信
慧系
ERP
息
工
统 运
PLM
安
厂行
全
服层
MES
MES
保
务
CAPP
障
规
QMS
标
范
准
智慧工厂服务总线
数
据
归
集
基础信息
层
数据库
定位信息 数据库
生产数据 库
实时监测 数据库
视频监控 数据库
三维模型 数据库
…
设
物联网
备
采 集
智能传
层
感器
智能执 行单元
智能仪 表
智能电 源
智能显 示器
智能环 境控制
MES
PLM
其他管控 系统
引变压器、工业用特种变压器 产品制造能力:1100kV超高压
直流换流变
.
5
.
5
.
5
商发智慧工厂整体架构图
决
策
智慧工厂驾驶舱
层
数据分析
知识管理
信
息
智慧工厂门户
展
示
生产进度
安全监控
能耗管理
专家系统 环境监测 生产资源
…
层
ID号的
智能制
带ID号
智能装
具有在
原材料
造
的零部
配
智慧 维护
智能制造-智能工厂构建
.
智慧决策
5
.
5
华西能源
.
5
华西能源
.
5
华西能源
.
5
.
5
高压开关数字化工厂总体需求
机械制造工程基础

机械制造工程基础
机械制造工程基础包括机械工艺、机械加工、机械设计等方面的知识。
1. 机械工艺:机械工艺是机械制造过程中的一系列工艺操作和方法的总称,包括铸造、锻造、冷热加工、焊接、表面处理等工艺过程。
机械工艺的选择和优化可以影响到制造成本、质量和生产效率。
2. 机械加工:机械加工是将原材料或半成品经过一系列的切削、磨削、钻孔、铣削、车削等加工方式,将其加工成所需形状和尺寸的工艺过程。
常见的机械加工方法有车削、铣削、钻削等。
3. 机械设计:机械设计是指根据产品的使用要求和工艺要求,设计出满足功能和性能要求的机械产品。
机械设计涉及到材料选择、结构设计、运动学、动力学等方面的知识。
4. 机械制造自动化:机械制造自动化是利用计算机、传感器、执行器等技术手段实现机械制造过程的自动化,增加生产效率和产品质量的一种方法。
其中涉及到自动化设备的选型、控制系统的设计和集成等技术。
5. 机械工程材料:机械制造中使用的材料有金属材料和非金属材料两大类。
金属材料包括钢、铝、铜等,非金属材料包括塑料、复合材料等。
了解不同材料的物理、化学性质以及适用范围对机械制造很重要。
6. 机械安全:机械制造过程中需要考虑机械设备的安全性。
保证机械设备的安全操作和使用,可以减少事故的发生,提高工作效率。
机械安全包括机械结构的安全设计、安全控制系统的设计以及劳动者的安全操作等方面知识的学习和应用。
以上是机械制造工程基础的相关内容,通过学习和实践,可以提高机械制造的技能和能力。
【制造工程基础-清华课件】chapter4-1

• 砂型铸造工艺流程、特点 • 造型材料的制备及要求(型砂、芯砂) • 模样制作的缩尺要求 • 液体金属流动性定义、要求、影响因素 • 浇注过程分析(直浇道形状、浇注时间) • 纯金属、共晶合金、非共晶合金金属的凝固机制 • 铸件结构设计基本原则 • 浇注位置的选Байду номын сангаас原则 • 浇注系统的组成、各部分作用,封闭式浇注系统和开放式
浇注系统的主要区别在哪里 • 冒口、冷铁补缩原理 • 铸造工艺共性缺陷、主要形成原因分析、防止措施 • 砂型铸造工艺缺陷、主要形成原因分析、防止措施
《机械制造工程基础》第3.3章外圆内圆和平面的加工

平面加工质量控制是机械制造过程中的基本要求,主要 涉及平面度和表面粗糙度的控制。
详细描述
平面加工质量控制主要包括以下几个方面
1. 刀具的选择与修磨
根据平面加工的要求,合理选择刀具材料、切削刃和切 削角度,定期修磨刀具,确保切削刃锋利。
2. 切削参数的调整
切削速度、进给量和切削深度等参数的合理调整,对平 面加工的精度和表面质量有较大影响。
平面加工刀具
铣刀
用于铣削加工,根据不同的铣削需求选择不同类型和规格的铣刀。
刨刀
用于刨削加工,根据不同的刨削需求选择不同类型和规格的刨刀。
砂轮
用于磨削加工,根据不同的磨削需求选择不同粒度和硬度的砂轮。
研磨剂和研磨具
用于研磨加工,根据不同的研磨需求选择不同类型和粒度的研磨剂和研磨具。
04
外圆内圆和平面加工的工 艺流程
研磨加工
通过研磨剂和研磨工具对工件表面进行研磨, 实现高精度的平面加工。
平面加工机床
铣床
主要用于铣削加工,可加工各种平面、 沟槽等。
刨床
主要用于刨削加工,适合于大批量生 产中加工平面、斜面等。
平面磨床
主要用于磨削加工,可实现高精度平 面加工。
研磨机
主要用于研磨加工,适用于高精度、 超光滑平面的加工。
镗床
主要用于加工较大孔的 内圆,如卧式镗床和坐
标镗床等。
拉床
主要用于加工高质量的 内圆,如平面拉床和内
圆拉床等。
内圆加工刀具
钻头
主要用于钻孔,有不同的规格和材料,如高 速钢钻头和硬质合金钻头等。
铰刀
用于铰孔,有不同的规格和材料,如高速钢 铰刀和硬质合金铰刀等。
扩孔钻
用于扩孔,有不同的规格和材料,如高速钢 扩孔钻和硬质合金扩孔钻等。
机械制造工程学(卓越)第一章 金属切削的基本要素
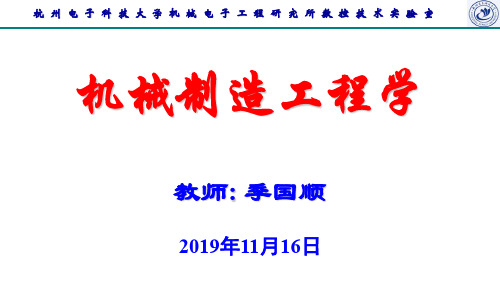
机械制造工程学
教师: 季国顺
2019年11月16日
杭州电子科技大学机械电子工程研究所数控技术实验室
第一章 金属切削的基本要素
1.1 工件表面的形成方法和成形运动 1.2 加工表面和切削用量三要素 1.3 刀具角度 1.4 切削层参数 1.5 刀具材料
杭州电子科技大学机械电子工程研究所数控技术实验室
一、刀具切削部分的结构要素
归结起来: “三面两刃一尖”
后刀面Aα 前刀面Ar 副后刀面Aα’
交线
主切削刃s
连接部分
刀尖
交线
副切削刃s’
杭州电子科技大学机械电子工程研究所数控技术实验室
1. 刀具标注角度参考坐标系
前提条件: 不考虑进给运动; 车刀刀尖与工件中心等高; 刀杆中心线与进给方向垂直; 刀具的安装面与基面 Pr 平行;
杭州电子科技大学机械电子工程研究所数控技术实验室
例1-5 螺旋槽铣刀铣削加工螺杆,如图1-8d所示。 母线:空间曲线,铣刀刀齿回转面与螺旋槽面相切形成,分解为:刀盘 的回转运动B1和铣刀轴线沿螺杆轴线的螺旋复合运动B21A22 导线:螺旋线,由螺旋复合运动B21A22形成,与母线形成运动的一部 分重合。
3. 切削深度 外圆车削切削深度
钻削切削深度
ap
dw
dm 2
mm
ap
dm 2
mm
(1-3) (1-4)
杭州电子科技大学机械电子工程研究所数控技术实验室
1.3 刀具角度
1.3 .1刀具切削部分的结构要素
前刀面 A 加工时,切屑流经的表面。 后刀面 A 与主切削刃毗邻,且与工件过渡表面相对的刀具表面。 副后刀面 A 与副切削刃毗邻,且与工件已加工表面相对的刀具表面。 切削刃 S 前刀面上直接进行切削的边锋。有主切削刃 S 和副切削刃 S 。 刀尖 主、副切削刃相衔接处很短的一段切削刃,通常也称为过渡刃。 有点刀尖、圆弧刀尖和倒角刀尖三种。
一现代制造技术的发展及体系结构PPT课件

(2)一些重要产品的年生产能力已跃居世界前列,如汽车年产
1000万辆以上,数控机床年产15万台以上。
(3)我国已成为世界最大的服装纺织品出口国;与日本、马来西
亚和韩国并称世界消费类电子产品四大生产国。
(4)成功开发生产了多种运输机和新舟60、AR21等支线飞机,大
飞机研发正在进行;神州七号发射后,中国载人航天将转向第
.
41
第二节 现代制造技术的发展
5.现代制造管理模式发生重大变化 随着制造技术从传统的福特生产模式向精益生产、并 行工程、敏捷制造、虚拟制造等新型生产模式转变, 制造管理模式也在不断发生变革。
.
42
第二节 现代制造技术的发展
.
43
第二节 现代制造技术的发展
.
44
第二节 现代制造技术的发展
.
45
返回目录
.
50
第三节 现代制造技术的体系结构
一、现代制造技术的分类 现代制造技术是一个涉及范围非常广泛、技术领域非 常繁多的复杂系统。从制造技术的功能性角度,可将 现代制造技术分为五大类型。
.
51
第三节 现代制造技术的体系结构
1.现代设计技术 现代设计技术就是以满足产品的质量、性能、时间、 成本/价格综合效益最优为目的,以计算机辅助设计 技术为主体,以知识为依托,以多种科学方法及技术 为手段,研究、改进、创造产品活动过程所用到的技 术群体的总称。
39
第二节 现代制造技术的发展
3.柔性化程度不断提高 柔性化是制造企业对市场需求多样化的快速响应的能 力,即制造系统能够根据用户的需求快速生产多样化 的产品。
.
40
第二节 现代制造技术的发展
4.集成化成为现代制造系统的重要特征 自20世纪70年代微处理器诞生以来,集成化问题一直 是制造技术的研究重点。目前,制造系统集成化正在 向深度和广度两个方向发展。
- 1、下载文档前请自行甄别文档内容的完整性,平台不提供额外的编辑、内容补充、找答案等附加服务。
- 2、"仅部分预览"的文档,不可在线预览部分如存在完整性等问题,可反馈申请退款(可完整预览的文档不适用该条件!)。
- 3、如文档侵犯您的权益,请联系客服反馈,我们会尽快为您处理(人工客服工作时间:9:00-18:30)。
2. 型壳制造
型壳制造工艺过程 模组的除油和脱脂 在模组上涂挂涂料和撒砂 型壳干燥和硬化 自型壳中熔失熔模 焙烧型壳 型壳
型壳种类:实体型和多层型壳,目前普遍采用的是多层型壳。 型壳工艺要求:在熔失熔模时,型壳会受到体积正在增大的熔融模料 的压力;在焙烧和注时,型壳各部分会产生相互牵制而又不均的膨胀的 收缩,金属还可能与型壳材料发生高温化学反应。要求型壳有小的膨胀 率和收缩率;高的机械强度、抗热震性、而火度和高温下的化学稳定性; 型壳还应有一定的透气性,以便浇注时型壳内的气体能顺利外逸。 两类型壳用材料:用来直接形成型壳的,如耐火材料、粘结剂等;为 了获得优质的型壳,简化操作、改善工艺用的材料,如熔剂、硬化剂、 表面活性剂等。 1)耐火材料:主要为石英和刚玉,以及硅酸铝耐火材料 2)粘结剂:用得最普遍的粘结剂是硅酸胶体溶液
圆盘、环类铸件。
第四章
金属的铸造成形
§4-2-5 离心铸造
离心铸造工艺
铸型转速选择 特点与应用
将液体金属浇入高速旋转(250rpm-1500rpm)的铸型中,使 其在离心力作用下充填铸型和凝固形成铸件。按铸型旋转轴线的 方向分为立式离心铸造和卧式离心铸造。
卧 式 离 心 铸 造
铸件壁厚均匀,适于长度较大的套筒及管类铸件。
r0
转速太高,外层金属壳可能产生裂纹,液体金属离心力对铸型 壁压力太大。
第四章
金属的铸造成形
§4-2-5 离心铸造
离心铸造工艺 铸型转速选择
特点与应用
优点: 省去型芯、浇注系统及冒口;
铸件组织致密,力学性能高; 方便实现双金属轴套和轴瓦类铸件生产。
缺点: 铸件内表面质量差,尺寸不易控制;
硫:硫是强烈的反石墨化元素;导致热
脆性。含量要限制在0.1%-0.15%以下。
锰:锰阻碍珠光体中的碳石墨化,提高强度和硬度;具有脱硫作用
(生成MnS)。含量0.6%-1.2%。
磷:对石墨化影响不大;增强耐磨性;增强冷脆性。含量0.5%以下。
3. 铸铁石墨化过程的控制
(1)影响铸铁石墨化过程的主要因素 冷却速度 冷却速度慢,则碳原子析出充分; 冷却速度快,则易形成白口组织。 • §4.3.1 铸铁——铸铁石墨化过程控制
第四章
金属的铸造成形
§4-2-3 压力铸造(压铸)
压铸工艺 特点与应用
第四章
金属的铸造成形
§4-2-3 压力铸造(压铸)
压铸工艺
特点与应用
在高压(30MPa-100Mpa)、高速(0.5m/s-80m/s)下充填铸型。 根据压室的工作条件不同分为热压室压铸和冷压室压铸。
热 压 室 压 铸
适于压铸低熔点合金
通气塞
第四章
金属的铸造成形
§4-2-1 金属型铸造
金属铸型结构 铸造工艺
特点与应用
优点: 铸件尺寸精度和表面质量优于砂型铸造;
铸件具有较高的力学性能; 工序简化,节约造型材料和生产场地,易于实现机械化 和自动化。
缺点:
金属型制造成本高,加工周期长; 金属型不透气,而且无退让性,易造成铸件浇不足、开裂或铸 铁件白口等缺陷; 金属型铸造时,铸型的工作温度、合金的浇注温度和浇注速度, 铸件在铸型中停留的时间,以及所用的涂料等,对铸件的质量 的影响甚为敏感,需要严格控制。 金属型制造成本高,不适合单件、小批生产; 不适宜薄壁复杂及大型铸件; 主要用于铝、铜、镁等非铁合金中小型铸件的大批量生产。
应用:
第四章
金属的铸造成形
§4-2-2 熔模精密铸造
熔模铸造工艺过程 特点与应用
第四章
金属的铸造成形
§4-2-2 熔模精密铸造
熔模铸造工艺过程
特点与应用
1. 熔模制造
制造熔模的专用模具(压型)的制造
★ 机械加工 ★ 易熔合金直接浇入母模 ★ 石膏、塑料、硅橡胶压型
浇注模料,制造单个熔模 制模材料:蜡基模料、树脂基模料,常用的材料有石蜡、硬脂酸、松香、川蜡
缺点: 压铸件中存在高度弥散的气孔,不易进行切削加工、热处理或在高
温下工作; 技术改进 难于压铸高熔点金属(钢、铸铁等); 压铸型制造成本高。
应用: 低熔点有色金属精密复杂铸件的大批量生产。
第四章
金属的铸造成形 压铸工艺技术改进:半固态压铸技术
降低了工作温度,减少了压铸件中的气孔和缩孔。
3.熔模铸件的浇注和清理
熔模铸件的浇注
热型重力浇注方法 型壳从焙烧炉中取出后,在高温下进行浇注。此时金属在型壳中冷却较慢,能在流 动性较高的情况下充填铸型,故铸件能很好复制型腔的形状,提高了铸件的精度。但铸 件在热型中的缓慢冷却会使晶粒粗大,这就降低了铸件的机械性能。在浇注碳钢铸件时, 冷却较慢的铸件表面还易氧化和脱碳,从而降低了铸件的表面硬度、光洁度和尺寸精度。 真空吸气浇注 将型壳放在真空浇注箱中,通过型壳中的微小孔隙吸走型腔中的气体,使液态金 属能更好地充填型腔,复制型腔的形状,提高铸件精度,防止气孔、浇不足的缺陷。 压力下结晶 将型壳放在压力罐内进行浇注,结束后,立 即封闭压力罐,向罐内通入高压空气或惰性气体, 使铸件在压力下凝固,以增大铸件的致密度。在 国外最大压力已达150atm。 定向结晶(定向凝固) 一些熔模铸件如涡轮机叶片、磁钢等,如果 它们的结晶组织是按一定方向排列的柱状晶,它 们的工作性能便可提高很多,所以熔模铸造定向 结晶技术正迅速地得到发展。
第四章
金属的铸造成形
§4-2-3 压力铸造(压铸)
压铸工艺
特点与应用
在高压(30MPa-100Mpa)、高速(0.5m/s-80m/s)下充填铸型。 根据压室的工作条件不同分为热压室压铸和冷压室压铸。
冷 压 室 压 铸
适于压铸较高熔点合金
第四章
金属的铸造成形
§4-2-3 压力铸造(压铸)
压铸工艺
第四章
金属的铸造成形
§4-2-4 低压铸造
低压铸造工艺过程 特点与应用
第四章
金属的铸造成形
§4-2-4 低压铸造
低压铸造工艺过程
特点与应用
在低压下(0.02MPa-0.07MPa)将液态金属注入型腔, 并在压力下凝固成形。
第四章
金属的铸造成形
§4-2-4 低压铸造
低压铸造工艺过程
充型能力强,铸件轮廓清晰,表面光洁; 补缩效果较好,铸件组织致密,性能优异。拉伸强度比重力铸造 提高10%; 简化浇注系统结构;
制造工程基础
砂型铸造特点: 优点:生产率高,成本低,灵活性大,适应面广,技术 成熟。 缺点:铸件的内部质量、尺寸精度、表面粗糙度较差; 不易实现机械化、自动化。
如何克服这些缺点?
特种铸造工艺方法
第四章
金属的铸造成形
第二节
特种铸造工艺方法
第四章
金属的铸造成形
常见的特种铸造工艺 金属型铸造 熔模精密铸造 压力铸造(压铸) 低压铸造 离心铸造
第四章
金属的铸造成形
§4-2-5 离心铸造
离心铸造工艺
铸型转速选择 特点与应用
将液体金属浇入高速旋转(250rpm-1500rpm)的铸型中,使 其在离心力作用下充填铸型和凝固形成铸件。按铸型旋转轴线的 方向分为立式离心铸造和卧式离心铸造。
立 式 离 心 铸 造
铸件沿高度方向 壁厚不均匀,适用
于高度小于直径的
特点
硬而脆,难以切削加工 良好的 减震性、 减磨性 及低的 缺口敏 感性, 易于铸 造和切 削加工。
牌号示例
KmTB
应用
高耐磨性机件或工具 (轧辊、犁铧) 静载下的承压件及滑 动副零件(箱体、导 轨)
承受冲击和振动载荷的零 件(减速器壳体、曲轴) 可改善、调整强度与韧性 的组合,应用广泛。 高温及高温度梯度下工作 零件(气缸盖)
特点与应用
优点: 铸件可达到很高的尺寸精度和表面质量(Ra 3.2-0.8);
压铸薄壁件,表层晶粒细小,组织致密,铸件强度和表面硬度高。 抗拉强度比砂型铸件提高25-30%; 可以压铸形状复杂的薄壁铸件。铝合金铸件最小壁厚3mm-0.5mm; 可以实现嵌铸技术;
易于实现机械化、自动化,生产率高。
第四章
金属的铸造成形
§4-2-2 熔模精密铸造
熔模铸造工艺过程 优点: 铸件尺寸精度高、表面光洁;
可以铸出形状复杂的薄壁铸件; 对铸造合金的种类、生产批量无限制。
特点与应用
缺点: 工序复杂,生产周期长;
原材料价格及铸件成本高;
铸件尺寸及重量受限制。
应用: 高熔点、难切削加工合金、小型精密铸件。
蜡、褐煤蜡 、聚乙烯等
、地
模料回收 熔模的制造:采用压力把糊状模料压入压型的方法制造熔模:柱塞加压法、气压法
和活塞加压法。压制前需在压型表面涂薄层分型剂,以便从压型中取出熔模。压制蜡基 模料时,分型剂可为机油、松节油等;压制树脂基模料时,常用麻油和酒精的混合液或 硅油作分型剂。分型剂层越薄越好,使熔模能更好地复制压型的表面,提高熔模的表面 光洁度。
铸造非铁合金
铸造铝合金 铸造铜合金
铸造特点
铸造合金的熔炼
铸造工艺特点
铸件的热处理
§4.3.1 铸铁——碳在铸铁中的存在形式
• 铸铁是一系列主要由铁、碳(2.5%-4.0%)和硅(1.0%-2.5%)组 成的接近共晶成分的合金总称。 • 铸铁的组织由基体(铁素体、珠光体、铁素体+珠光体)和石墨组成。 • 铸铁铸造性能良好,加工性能好,减摩性能好,成本低廉;与钢相比, 强度与韧性较低。 • 碳在铸铁中的存在形式:
白 口 铸 铁
灰 口 铸 铁
可 锻 铸 铁
球 的控制
(1)影响铸铁石墨化过程的主要因素 化学成分 碳和硅:硅是强烈促进石墨化元素。
不同碳硅配比,得到不同组织和 • §4.3.1 铸铁——铸铁石墨化过程控制 性能的铸铁:白口(麻口)铸铁,铁 素体基体灰铸铁,珠光体(或珠光体 +铁素体)基体灰铸铁。