压脱机夹板夹伤手指调查报告.docx
压面机夹伤事故报告

压面机夹伤事故报告压面机是一种把面粉和水搅拌均匀后,代替传统手工揉面的食品机械,可用于制作面条、面点等。
但这种机器如果操作不当或一时走了神,很容易发生意外!4月11日4时18分,通化市消防救援支队指挥中心接到报警:位于通化市东昌区市医院食堂发生意外事故,一女职工手指被卷入压面机内,接到报警后救援人员立即抵达现场。
救援人员到达现场后,发现现场一名女职工右手被压面机的压轴搅片死死“咬”住,表情痛苦不堪。
经询问得知,该伤员在使用压面机时,因操作不慎手指被毛巾裹缠陷进压面机内被滚轮卡住,手指受到严重挤压并皮肤损伤严重,情况十分紧急,若不及时处理,后果不堪设想。
指挥员立即展开救援:消防指战员首先对被困人员进行话语安抚,转移其注意力;同时利用小型破拆工具对压面机进行拆卸,经过20分钟的紧张救援,在被困人员不受二次伤害的情况下,成功将被困人员手部成功取出,消防救援人员反复叮嘱受伤人员手指切勿弯曲,并立即被同事送到本医院急救室进行救治。
每当因操作不当被压面机压伤手的事故并不少见看着着实让人揪心4月4日11时许,上海市金山区某单位食堂内,一名女性员工因操作搅面机不慎,在操作时,右手不慎被卷了进去,手指被卡,疼得嚎啕大哭。
接到报警后,金山消防救援站立即赶赴现场救援。
到场后,被困人员意识清醒,消防指战员,使用无齿锯锯断轴承,顺利将被困人员救出。
4月9日清晨5时20分许,湖北省宜昌市一面馆内,一女子手卡压面机。
据了解,该女子在使用压面机时,准备将最后一点余面放进机器内,没想到左手被卷进机器内,此时由于离电源有一定的距离,女子无法自行断电,同事发现后迅速将压面机电源断开,并立即报警。
待医护人员为女子止血后,消防员立即利用撬棍对压面机铁柱和铁板进行扩张,3分钟后女子左手被取出。
压脱机夹板夹伤手指调查报告.docx
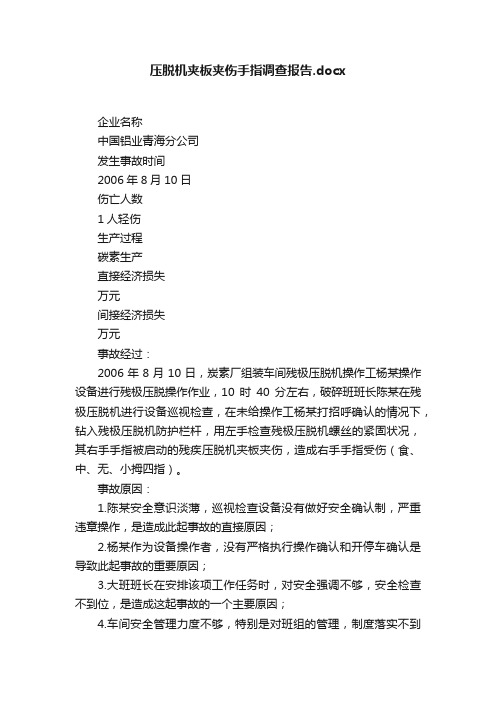
压脱机夹板夹伤手指调查报告.docx企业名称中国铝业青海分公司发生事故时间2006年8月10日伤亡人数1人轻伤生产过程碳素生产直接经济损失万元间接经济损失万元事故经过:2006年8月10日,炭素厂组装车间残极压脱机操作工杨某操作设备进行残极压脱操作作业,10时40分左右,破碎班班长陈某在残极压脱机进行设备巡视检查,在未给操作工杨某打招呼确认的情况下,钻入残极压脱机防护栏杆,用左手检查残极压脱机螺丝的紧固状况,其右手手指被启动的残疾压脱机夹板夹伤,造成右手手指受伤(食、中、无、小拇四指)。
事故原因:1.陈某安全意识淡薄,巡视检查设备没有做好安全确认制,严重违章操作,是造成此起事故的直接原因;2.杨某作为设备操作者,没有严格执行操作确认和开停车确认是导致此起事故的重要原因;3.大班班长在安排该项工作任务时,对安全强调不够,安全检查不到位,是造成这起事故的一个主要原因;4.车间安全管理力度不够,特别是对班组的管理,制度落实不到位,安全确认制未严格执行,也是造成这起事故的一个主要原因;5.在分公司和分厂强化安全管理的形式下,仍有此类违章行为的发生,说明分厂在安全管理上存在一定漏洞,分厂有一定的管理责任。
事故责任及处理情况:一、事故责任分析1.陈某做为组装车间车间一名班长,不严格遵守《公司安全生产管理规定》,在巡视设备时不认真履行安全确认,对此起事故负主要责任。
2.杨某没有严格执行操作确认和开停车确认,对此起事故负直接责任。
3.大班班长对安全强调不够,安全检查不到位,对此起事故负一定责任。
4.车间安全管理存在疏漏,安全确认制未严格执行,车间主任对此起事故负管理责任。
二、事故处理1.扣罚事故责任人陈某3个月奖金。
2.扣罚操作工杨某1个月奖金。
3.扣罚组装车间生产二班大班长贺某、副大班长田某各1个月奖金。
4.扣罚组装车间主任王某、生产副主任高某、安全员于某各1个月奖金。
5.扣罚组装车间当月奖金的10%。
防范措施:1.进一步加强班组长、职工安全教育培训工作,认真开展安全确认制学习和落实工作,提高职工的安全意识和安全操作技能,提高班组长的安全责任心;2.进一步规范作业行为,严格执行安全技术操作规程,进一步强化安全操作的程序化、制度化,严格安全确认制的执行力度,做到令行禁止,有章可循;3.举一反三,认真开展安全专项整治活动。
090211手指压伤事故检讨报告
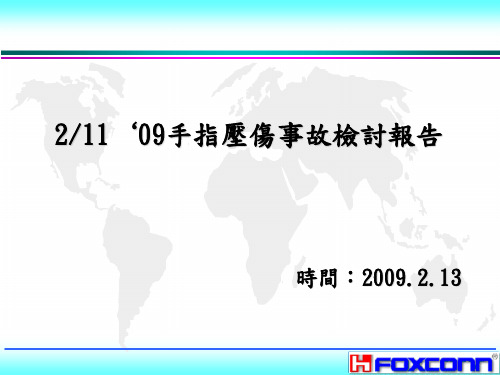
二.事故原因分析
3.經與自動化電控主管共同確認后,認為有可能是單片機性能不穩定, 易受到外部雜波信號干擾,發生死機現象,誤輸出信號給電磁閥,造成 氣缸誤動作.
單片機價格便宜,但穩定性較差,易受外 部干擾,造成程序紊亂死機現象.
三.改善對策檢討
短期對策:
1.早會時加強安全防範意識宣導,培養全員安全意識.宣導 全員出現異常狀況及時報告. 完成時間:2/12‘09
處理結果: 事發後及時送到觀瀾人民醫院治療,醫生經過拍片檢查左
手食指遠節末端壓傷,醫院對其進行縫針及包扎手術.其它未有 任何異常.
二.事故左手食指進入危險區氣缸突然 動作造成手指壓傷
經過現場模擬測試,電控箱無再發生故障,未發現氣缸自行壓入下來的現象.
二.事故原因分析
2/11‘09手指壓傷事故檢討報告
時間:2009.2.13
報告大綱
➢ 事故發生經過 ➢ 事故原因分析 ➢ 改善對策檢討 ➢ 案例省思
一.事故發生經過
時 間:2009年2月11號 19:10 地 點:HSDI裝配 案發經過:
作業員張某在HS2505V生產流水線作業.操作二道散PIN壓 入機,左手在往HSG流道里放入HSG時,電控箱出現故障,氣缸自行 壓入下來,此時張某的手正在流道中放HSG,未及時拿出,造成左 手食指壓傷
增加系統穩定性.
完成時間: 3/7‘09
四.案例省思
危險無處不在﹐切不可報僥幸心態 強化安全意識,杜絕安全事故再發
安全永遠第一
-----END------
單片機死機
受外部干擾程序 陷入死循環
備註
現場確認無IC故障現象,否 則會連續發生異常
由原有的單動模式改為雙 動模式,需雙手同時作業有 效且程序上已防呆用邊料 塞住一邊開關無法啟動,開 關有防護罩,無法意外接觸
工伤事故调查报告

工伤事故调查报告工伤事故调查报告1. 事故发生时间和地点:- 时间:XXXX年XX月XX日XX时- 地点:XX工厂X车间2. 事故经过:- 事故发生时,工人X正在进行机器操作,不慎将手指夹入机器中。
- 工人X立即向附近同事求救,并马上停机。
- 其他工人迅速将机器断电,并联系了医务室进行紧急救治。
- 工人X随后被送往医院进行进一步治疗。
3. 事故原因分析:- 机器操作不当:工人X在操作机器时,没有遵循正确的操作流程和安全规范,导致手指被夹伤。
- 缺乏安全培训:工人X没有接受到充分的安全培训,对机器操作的风险和安全措施缺乏了解。
- 机器安全保护装置失效:机器的安全保护装置可能存在缺陷或正常使用后出现故障,未能及时阻止事故的发生。
4. 事故影响和损失:- 工人X手指被夹伤,造成严重的切割伤,需要接受手术治疗。
- 工人X的伤势严重影响了工作效率,并可能导致一段时间的工作中断。
- 公司面临的法律诉讼和赔偿责任。
- 公司形象受到负面影响,员工安全意识和满意度下降。
5. 整改和预防措施:- 加强安全培训:全面培训所有员工关于机器操作的安全规范和流程,确保每位员工都具备安全意识和技能。
- 定期维护和检查机器:加强对机器的定期维护和检查,确保安全保护装置的正常运作。
- 设立安全监控和检查机制:建立安全监控和检查机制,定期检查和记录机器操作的安全情况,防止类似事故再次发生。
- 加强管理和领导:公司管理层和领导应加强对安全管理的重视,倡导安全文化,为员工提供更安全的工作环境。
6. 总结:- 该工伤事故是由于工人操作不当和机器安全保护装置失效所造成。
公司应加强安全培训、定期维护机器、设立安全监控和检查机制,并加强管理和领导,提升员工的安全意识和工作环境的安全性。
这样可以有效预防类似事故的再次发生,并保障员工的健康和安全。
压力机工厂压断手指事故报告
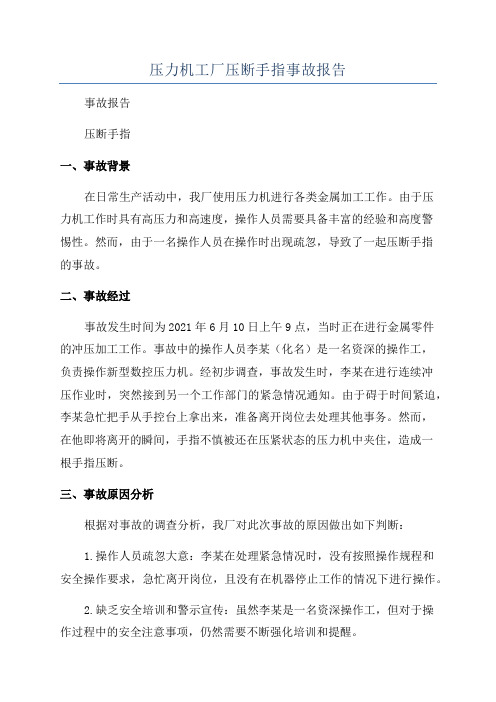
压力机工厂压断手指事故报告事故报告压断手指一、事故背景在日常生产活动中,我厂使用压力机进行各类金属加工工作。
由于压力机工作时具有高压力和高速度,操作人员需要具备丰富的经验和高度警惕性。
然而,由于一名操作人员在操作时出现疏忽,导致了一起压断手指的事故。
二、事故经过事故发生时间为2021年6月10日上午9点,当时正在进行金属零件的冲压加工工作。
事故中的操作人员李某(化名)是一名资深的操作工,负责操作新型数控压力机。
经初步调查,事故发生时,李某在进行连续冲压作业时,突然接到另一个工作部门的紧急情况通知。
由于碍于时间紧迫,李某急忙把手从手控台上拿出来,准备离开岗位去处理其他事务。
然而,在他即将离开的瞬间,手指不慎被还在压紧状态的压力机中夹住,造成一根手指压断。
三、事故原因分析根据对事故的调查分析,我厂对此次事故的原因做出如下判断:1.操作人员疏忽大意:李某在处理紧急情况时,没有按照操作规程和安全操作要求,急忙离开岗位,且没有在机器停止工作的情况下进行操作。
2.缺乏安全培训和警示宣传:虽然李某是一名资深操作工,但对于操作过程中的安全注意事项,仍然需要不断强化培训和提醒。
3.设备安全保障措施不到位:压力机在停止工作后需要进行安全保护措施,如断电、上锁等,以避免操作人员因疏忽而发生事故。
然而,在此次事故中,这些安全保障措施没有被有效执行。
四、事故教训及改进措施鉴于此次事故给企业生产秩序和员工的身体健康带来了不良影响,我们深刻吸取教训,并制定了以下改进措施:1.加强安全培训:加大对员工的安全意识教育和安全操作技能培训力度,确保每位员工具备必要的安全知识和技能,提高他们对操作风险的警惕性。
2.安全操作规程修订:修订并完善压力机的安全操作规程,明确操作人员在冲压加工工作中的操作要求,从技术层面规范操作流程,防止疏忽操作。
3.设备安全保障强化:加强压力机设备的安全保障工作,确保在停止工作时进行相应的安全保护措施,如断电、上锁等操作,防止类似事故再次发生。
安全事故调查报告书范例(使用5Why分析法)

安全事故调查报告书范例(使用5Why分析法)1. 事件背景在XX公司的某个生产车间发生了一起安全事故,工人小张在操作机器时发生了手指被夹伤的事故。
2. 事故经过2.1 小张在XX年XX月XX日的XX时XX分,操作XXXX 机器进行生产工作。
2.2 当小张将手放入机器中进行操作时,突然机器的夹紧装置启动,导致小张的手指被夹伤。
2.3 其他员工注意到小张的情况后,立即停机并呼叫急救人员前来处理伤情。
3. 事故调查过程3.1 初步调查- 调查人员对事故现场进行了勘察,取证并进行了拍照记录。
- 调查人员采访了目击者并询问小张事发前的操作情况。
3.2 5Why分析法- 第一Why: 为什么小张的手指被夹伤?因为他将手放入机器中进行操作。
- 第二Why: 为什么小张将手放入机器中进行操作?因为机器运行不稳定,需要通过手动调整来保持正常运作。
- 第三Why: 为什么机器运行不稳定?因为机器的维护保养工作不到位。
- 第四Why: 为什么机器的维护保养工作不到位?因为公司对机器维护保养的重要性意识不足。
- 第五Why: 为什么公司对机器维护保养的重要性意识不足?因为公司缺乏相关的培训和教育。
4. 整改措施4.1 针对事故原因,提出以下整改措施:- 完善机器维护保养制度,明确责任人和工作内容,确保机器的正常运行。
- 加强员工培训和教育,提高员工的安全意识和操作技能。
- 建立安全监测和检查机制,定期对机器进行检查保养,发现问题及时处理。
4.2 实施计划- 确定责任人,并明确实施各项整改措施的时间节点。
- 定期进行整改措施的检查和评估,确保整改工作的落实。
5. 总结和建议通过对该安全事故的调查分析,我们发现公司在机器维护保养和员工培训方面存在不足,导致了该事故的发生。
因此,建议公司加强对机器维护保养工作的重视,提高员工的安全意识和操作技能,确保生产过程中的安全性。
此外,定期进行安全检查和评估,及时发现问题并采取措施加以解决,以避免类似事故再次发生。
090226手指压伤事故检讨报告
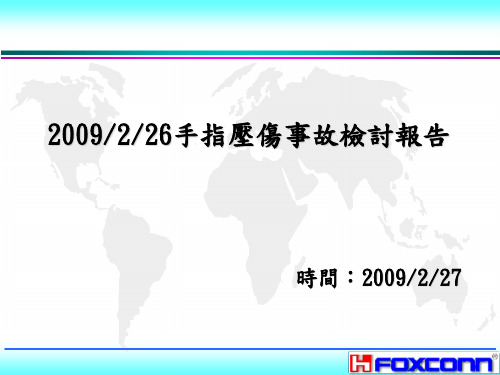
完成時間: 已完 成
2.站腳處未增加防護罩之機台,設計增加防護罩.
3/16‘09
完成時間:
3.自動機工傷事件較少,未引起重視.利用早會時間宣導
個人安全意識,加強稽查力度,對違規操作加強宣導.
完成時間: 持續
4.新人上崗前進行安全教育訓練
完成時間:持續
四.案例省思
危險無處不在﹐切不可抱僥幸心態 強化安全意識,杜絕安全事故再發
2009/2/26手指壓傷事故檢討報告
時間:2009/2/27
報告大綱
➢ 事故發生經過 ➢ 事故原因分析 ➢ 改善對策檢討 ➢ 案例省思
ห้องสมุดไป่ตู้
一.事故發生經過
時 間:2009年2月26號 16:10 地 點:HSDI裝配二期無塵室 案發經過:
自動化工程師喬某在LD5633H-A03LH自動機生產線調試.在 SAS導通不良排除工站處,在機台正常運轉狀態下,撿拾掉落在機 台上的產品,被送料氣缸與站腳夾到中指與食指,造成左手中指 與食指壓傷.
處理結果: 事發後及時送到公司社康中心治療,醫生建議到觀瀾人民醫
院拍片檢查.左手中指與食指中關節處皮膚刮傷,未傷及骨頭及 經脈,醫院對其進行縫針及包扎手術.其它未有任何異常.
二.事故原因分析
1.事故再現過程
機台正常運轉
造成手指壓傷 站腳處未安裝防護罩
經過現場分析,機台在有安全隱患處,未安裝防護罩.
安全永遠第一
-----END------
2.原因分析:
二.事故原因分析
W
W1
W2
W3
機台未加防護 工安防護不完全 罩
手指壓傷
未考慮工安措施
設計考量面不足 工站難與安裝 防護安裝遺漏 設計工程師經驗不足
下地干活手指压伤事故报告范文
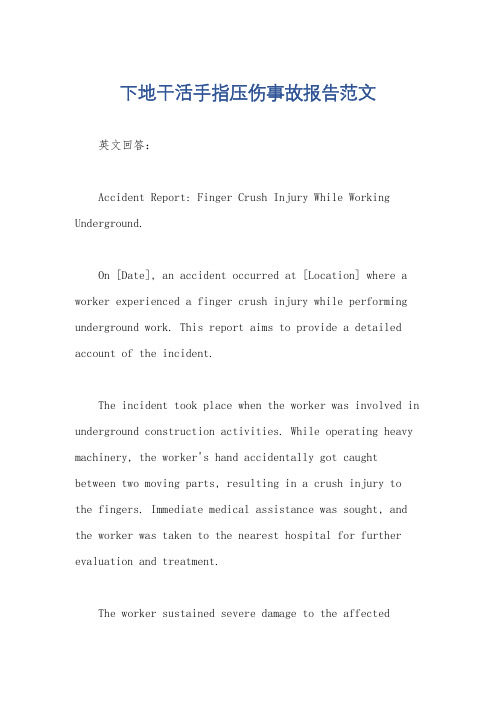
下地干活手指压伤事故报告范文英文回答:Accident Report: Finger Crush Injury While Working Underground.On [Date], an accident occurred at [Location] where a worker experienced a finger crush injury while performing underground work. This report aims to provide a detailed account of the incident.The incident took place when the worker was involved in underground construction activities. While operating heavy machinery, the worker's hand accidentally got caught between two moving parts, resulting in a crush injury to the fingers. Immediate medical assistance was sought, and the worker was taken to the nearest hospital for further evaluation and treatment.The worker sustained severe damage to the affectedfingers, including fractures and soft tissue injuries. The medical team performed emergency surgery to repair the fractures and restore the functionality of the fingers. The worker is currently undergoing a rehabilitation program to regain strength and mobility in the injured hand.Upon investigation, it was found that the accident occurred due to a combination of factors, including inadequate training on machinery operation and insufficient safety measures in place. The worker did not receive proper training on the safe operation of the specific machinery involved in the incident. Additionally, there were no adequate safety guards or mechanisms to prevent such accidents from happening.To prevent similar accidents in the future, it is recommended that comprehensive training programs be implemented to ensure all workers are familiar with the safe operation of machinery. Regular safety inspections should be conducted to identify and rectify any potential hazards. Furthermore, the installation of safety guards and mechanisms on machinery should be mandatory to minimize therisk of crush injuries.中文回答:事故报告,地下作业中手指被压伤。
工伤调查报告

工伤调查报告根据相关法律要求,本报告对某工厂发生的一起工伤事故进行调查分析,以期找出事故原因并提出相应的解决方案,以预防类似事故再次发生。
事故发生时间为2021年1月10日上午9点30分,地点位于某工厂生产车间,事故对象为工人李某。
下面将详细介绍事故的过程及分析原因。
一、事故经过:李某在操作机械时不慎将手指夹入机械设备中,造成手指严重受伤。
事故发生后,他立即被同事送往附近医院进行治疗,经医生诊断确认为手指骨折,需要进行手术治疗。
经全面救治,伤情得到一定缓解,但由于骨骼严重受损,恢复时间较长,预计需要2个月以上的休养和康复。
二、事故原因分析:1. 李某工作疏忽:事故发生时,李某没有严格按照操作规程进行作业,缺乏工作的细心和耐心,轻视安全隐患。
2. 机械设备存在安全隐患:机械设备未进行定期检修和维护,导致安全隐患,同时缺乏明确的安全警示标识和安全操作指南。
三、解决方案:1. 加强安全培训:对所有工人进行安全生产知识培训,加强他们的安全意识和责任心,确保能够正确操作设备并遵守操作规程。
2. 定期检修和维护设备:加强对机械设备的定期检修和维护,确保其安全运行,减少安全风险。
3. 安全警示标识和操作指南:设立明确可见的安全警示标识和操作指南,指导工人按照规程进行操作,减少工作疏忽可能性。
4. 建立安全管理制度:制定和执行全面的安全管理制度,明确责任分工和安全责任人,确保安全生产的持续进行。
综上所述,通过对该工伤事故的调查分析,我们发现事故原因主要是工人的疏忽和机械设备的安全隐患。
为了避免类似的工伤事故再次发生,我们提出了加强安全培训、定期检修和维护设备、设置安全警示标识和操作指南、建立安全管理制度等解决方案。
希望该工厂能够按照上述方案,加强安全生产管理,确保工人的生命安全和身体健康。
同时,对于发生事故的工人李某,应及时给予精神和物质上的支持,为他尽快康复提供帮助。
指导有误 造成趾骨骨折调查报告.docx

企业名称西北铝加工分公司发生事故时间2004 年 8 月 4日伤亡人数重伤1人生产过程铝加工直接经济损失2万元间接经济损失万元事故经过:2004年8月4日下午,压延厂机电车间电工陈某、黄某按月检修计划检修板1#退火炉装料小车。
3点15分左右检修完成,通知退火工汪某试车,汪某对现场确认后上操作台开始试车。
试车过程中发现小车进退无动作,故障排除后,陈某站在小车轨道上打手势示意汪某再试,汪某确认指挥手势后,启动“小车前进”按钮。
小车向前移动过程中从陈某左足趾骨处碾过,造成其左足第1—5趾骨多发性粉碎性骨折,左趾骨端皮肤撕脱伤。
事故原因:1.陈某在没有确认自身安全的情况下指导有错误。
2.汪某对现场工作缺乏检查确认。
事故责任及处理情况:扣罚事故责任单位压延厂8000元,由压延厂落实到相关责任人。
防范措施:1.加强职工的安全教育,提高职工自我保护的安全意识,牢固树立“安全第一”的思想,正确处理安全与生产的关系。
2.加强安全监查,对三违行为要坚决制止。
多工种作业要相互协助配合。
3.消除安全隐患,在二级厂范围内进行一次全方位的安全大检查。
4.吸取事故教训。
“举一反三”做好安全保护工作。
对装料车,过跨车加装安全防护装置,制定相应的安全操作规定。
企业名称西北铝加工分公司发生事故时间2004 年11月2日伤亡人数轻伤1人生产过程铝加工直接经济损失0.8万元间接经济损失万元事故经过:11月2日上午,综合厂合金车间打灰班职工苟某在卸铝灰时,为了能将灰箱内剩余铝灰扒干净,违反操作规程,让班组其他职工把砖头夹在灰箱合缝处,当其用铁锹进行扒灰时,由于产生振动,致使夹放在灰箱合缝处的砖头脱落,被合拢的灰箱将其左手食指夹伤。
事故原因:主要原因是苟某违反操作规程。
事故责任及处理情况:扣罚事故责任单位综合厂1000元,由综合厂落实到相关责任人。
防范措施:1.在打灰现场标识警示牌,杜绝习惯性违章;2.加强岗位安全培训,提高职工自我保护和防护意识;3.完善装、拉、卸灰规程,对现场卸灰工作进行规范和改进;4.加快对打灰工作现场改进和扩建的施工进度。
违章操作 手被夹住调查报告.docx
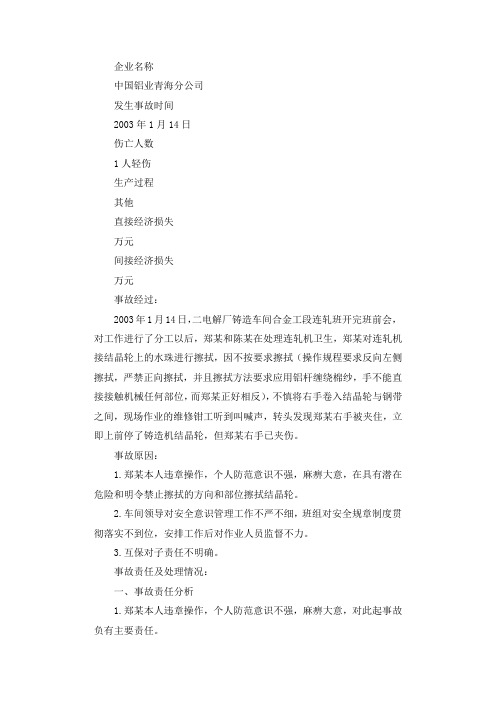
企业名称
中国铝业青海分公司
发生事故时间
2003年1月14日
伤亡人数
1人轻伤
生产过程
其他
直接经济损失
万元
间接经济损失
万元
事故经过:
2003年1月14日,二电解厂铸造车间合金工段连轧班开完班前会,对工作进行了分工以后,郑某和陈某在处理连轧机卫生,郑某对连轧机接结晶轮上的水珠进行擦拭,因不按要求擦拭(操作规程要求反向左侧擦拭,严禁正向擦拭,并且擦拭方法要求应用铝杆缠绕棉纱,手不能直接接触机械任何部位,而郑某正好相反),不慎将右手卷入结晶轮与钢带之间,现场作业的维修钳工听到叫喊声,转头发现郑某右手被夹住,立即上前停了铸造机结晶轮,但郑某右手已夹伤。
事故原因:
1.郑某本人违章操作,个人防范意识不强,麻痹大意,在具有潜在危险和明令禁止擦拭的方向和部位擦拭结晶轮。
2.车间领导对安全意识管理工作不严不细,班组对安全规章制度贯彻落实不到位,安排工作后对作业人员监督不力。
3.互保对子责任不明确。
事故责任及处理情况:
一、事故责任分析
1.郑某本人违章操作,个人防范意识不强,麻痹大意,对此起事故负有主要责任。
2.车间领导对安全意识管理工作不严不细,对此起事故负有领导责任。
二、事故处理
1.扣发事故责任人郑某四个月奖金。
2.扣发车间当月全部奖金的10%。
3.扣发分厂领导、安全员各200元奖金。
防范措施:
1.对连轧班职工进行操作规程和责任制全面考试。
2.以后擦拭结晶轮必须用铝杆缠绕上棉纱擦拭,严禁用手直接拿棉纱正向右侧擦拭。
3.铸造机控制台非经当班班长和控制台负责人外,其他人不得私自操作。
机械压伤体验报告模板

机械压伤体验报告模板概述本报告旨在描述机械压伤的体验过程,以便对该类事故进行更深入的了解和预防。
机械压伤是指人体在机械设备或工具下遭受的挤压和压迫,常见于工业生产和日常生活中。
通过本报告,我们将详细讨论机械压伤的过程和教训。
事件经过在我进行一项机械操作时,不小心被机器零件压伤。
下面是事件经过的具体描述:1. 事发时间:2021年10月15日,周三,下午2点30分。
2. 地点:位于某工厂生产车间C区。
3. 操作环境:车间内噪音较大,人员密集,设备和零件复杂多样。
4. 事件描述:- 我负责对机器A进行维护保养。
- 由于时间紧迫以及操作不慎,在清理零件时,我的手部不小心被一个旋转的齿轮夹住。
- 我立即尖叫求救,周围的同事闻声后迅速停下手头工作,赶来救助我。
- 被困期间,我非常焦虑和痛苦,感觉呼吸困难,并出现晕眩症状。
- 最终,经同事帮助,我脱离险境并得到院方的及时治疗。
伤害程度与影响1. 伤害情况:- 因机械压伤,我的手指右中指第一关节严重受伤,骨折且多处皮肤破裂。
- 伤口出血较多,被送往医院进行紧急处理。
2. 影响范围:- 由于受伤,我失去了术后工作能力,需要休息和康复一段时间。
- 需要家人和朋友的照顾,承担一些生活琐事。
- 对工作产生了一定影响,影响了项目进度。
思考与教训1. 思考问题:- 事故发生时,我认识到自己操作不慎,没有遵循操作规程。
- 工作压力较大,容易出现疏忽和马虎。
- 是否能在事故发生前意识到潜在风险并采取相应措施进行防范?2. 教训总结:- 安全至上:无论工作有多紧迫和重要,安全永远是第一位的。
- 严格遵守操作规程:在操作中,要仔细阅读和理解操作指南,并按照规程进行操作,确保自己和他人的安全。
- 加强风险意识:在工作中应始终保持高度警觉,意识到潜在的危险并采取预防措施。
- 配备个人防护装备:根据工作环境的特点,穿戴适当的安全帽、手套、护目镜等个人防护装备。
预防措施为了防止机械压伤事故的再次发生,制定以下预防措施:1. 安全意识宣传:加强员工对机械压伤事故的认知和意识,通过会议、培训和安全宣传册等方式进行宣传教育。
关于xx手指受伤事故调查报告.docx
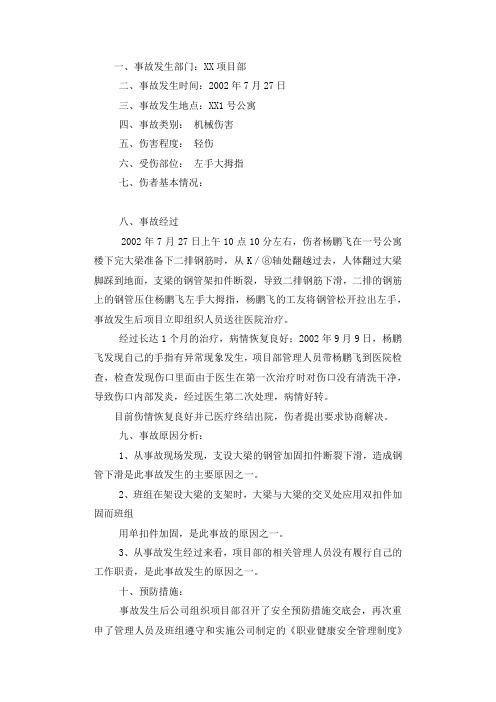
一、事故发生部门:XX项目部二、事故发生时间:2002年7月27日三、事故发生地点:XX1号公寓四、事故类别:机械伤害五、伤害程度:轻伤六、受伤部位:左手大拇指七、伤者基本情况:八、事故经过2002年7月27日上午10点10分左右,伤者杨鹏飞在一号公寓楼下完大梁准备下二排钢筋时,从K/⑧轴处翻越过去,人体翻过大梁脚踩到地面,支梁的钢管架扣件断裂,导致二排钢筋下滑,二排的钢筋上的钢管压住杨鹏飞左手大拇指,杨鹏飞的工友将钢管松开拉出左手,事故发生后项目立即组织人员送往医院治疗。
经过长达1个月的治疗,病情恢复良好;2002年9月9日,杨鹏飞发现自己的手指有异常现象发生,项目部管理人员带杨鹏飞到医院检查,检查发现伤口里面由于医生在第一次治疗时对伤口没有清洗干净,导致伤口内部发炎,经过医生第二次处理,病情好转。
目前伤情恢复良好并已医疗终结出院,伤者提出要求协商解决。
九、事故原因分析:1、从事故现场发现,支设大梁的钢管加固扣件断裂下滑,造成钢管下滑是此事故发生的主要原因之一。
2、班组在架设大梁的支架时,大梁与大梁的交叉处应用双扣件加固而班组用单扣件加固,是此事故的原因之一。
3、从事故发生经过来看,项目部的相关管理人员没有履行自己的工作职责,是此事故发生的原因之一。
十、预防措施:事故发生后公司组织项目部召开了安全预防措施交底会,再次重申了管理人员及班组遵守和实施公司制定的《职业健康安全管理制度》的必要性和严肃性;对施工现场进行全面的安全检查,查出的安全隐患按“三定一落实”原则进行整改,对相关的管理人员按“四不放过”原则进行处理。
项目部通过认真的总结和学习,以确保类似事故的发生。
十一、事故责任分析1、项目施工员在交底时并没有对该部分说明详细的安全措施,对此事故负直接责任。
2、施工班组在操作时未按照有关安全操作规程操作,对此事故负主要直接责任。
3、项目部安全员在对支撑的钢管架的安全性,没有监督到位负监督不力的责任。
幼儿园手指压伤事件报告

幼儿园手指压伤事件报告1.引言1.1 概述幼儿园手指压伤事件是指在幼儿园教育活动中,因为儿童在玩耍、活动过程中出现手指被夹伤的事件。
这种事件给孩子和家长带来了不必要的伤害和困扰,也凸显了教育管理中存在的安全隐患和问题。
因此,本报告将对这一事件进行详细的描述和分析,并提出相应的建议和改进措施,以期减少类似事件的发生,保障幼儿园儿童的安全和健康成长。
1.2文章结构文章结构部分的内容如下:文章结构部分主要介绍了本文的排版和组织架构。
文章将分为引言、正文和结论三个部分,每个部分包含相应的子标题,以帮助读者了解整篇报告的内容和结构。
引言部分将包括概述、文章结构和目的三个小节,正文部分将包括事件描述、事件原因和教育管理问题三个小节,结论部分将包括结果总结、教训与启示和建议与改进三个小节。
通过这种结构,读者可以清楚地了解到本文将对幼儿园手指压伤事件进行全面的描述、分析和总结,同时也可以方便读者查找所需内容。
1.3 目的本报告的目的在于对幼儿园手指压伤事件进行全面而详细的分析和总结,深入挖掘事件的发生原因、背后的教育管理问题以及对幼儿园安全教育的启示和建议。
通过本报告的撰写,旨在提高幼儿园安全管理水平,保障幼儿园儿童的安全,为幼儿园教育管理工作提供借鉴和参考,促进幼儿园教育质量的不断提升。
2.正文2.1 事件描述:2019年5月15日,某幼儿园发生了一起手指压伤事件。
当天下午3点左右,一名3岁的幼儿在游戏时间中不慎被玩具椅子的折叠机构夹到手指,导致手指严重受伤,出现大量流血和剧烈疼痛。
幼儿园老师立即对伤情进行处理,并及时将幼儿送往医院就医。
医院诊断为手指压伤,需要进行手术缝合,幼儿得以及时救治,目前病情已经稳定。
此次事件引起了幼儿园师生和家长的高度关注和恐慌,同时也引起了社会各界的广泛关注和舆论热议。
事件发生后,幼儿园迅速成立了专门调查组,展开调查,以查明事件的原因,及时采取有效措施,防止类似事件再次发生。
2.2 事件原因部分:事件发生的原因主要是因为幼儿园教师在带领孩子们进行手工活动时的疏忽和不及时的监管。
车间事故报告
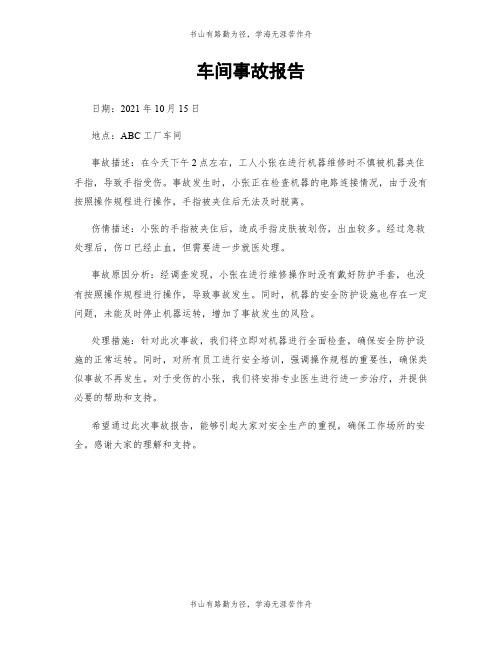
书山有路勤为径,学海无涯苦作舟
车间事故报告
日期:2021年10月15日
地点:ABC工厂车间
事故描述:在今天下午2点左右,工人小张在进行机器维修时不慎被机器夹住手指,导致手指受伤。
事故发生时,小张正在检查机器的电路连接情况,由于没有按照操作规程进行操作,手指被夹住后无法及时脱离。
伤情描述:小张的手指被夹住后,造成手指皮肤被划伤,出血较多。
经过急救处理后,伤口已经止血,但需要进一步就医处理。
事故原因分析:经调查发现,小张在进行维修操作时没有戴好防护手套,也没有按照操作规程进行操作,导致事故发生。
同时,机器的安全防护设施也存在一定问题,未能及时停止机器运转,增加了事故发生的风险。
处理措施:针对此次事故,我们将立即对机器进行全面检查,确保安全防护设施的正常运转。
同时,对所有员工进行安全培训,强调操作规程的重要性,确保类似事故不再发生。
对于受伤的小张,我们将安排专业医生进行进一步治疗,并提供必要的帮助和支持。
希望通过此次事故报告,能够引起大家对安全生产的重视,确保工作场所的安全。
感谢大家的理解和支持。
书山有路勤为径,学海无涯苦作舟。
- 1、下载文档前请自行甄别文档内容的完整性,平台不提供额外的编辑、内容补充、找答案等附加服务。
- 2、"仅部分预览"的文档,不可在线预览部分如存在完整性等问题,可反馈申请退款(可完整预览的文档不适用该条件!)。
- 3、如文档侵犯您的权益,请联系客服反馈,我们会尽快为您处理(人工客服工作时间:9:00-18:30)。
企业名称
中国铝业青海分公司
发生事故时间
2006年8月10日
伤亡人数
1人轻伤
生产过程
碳素生产
直接经济损失
万元
间接经济损失
万元
事故经过:
2006年8月10日,炭素厂组装车间残极压脱机操作工杨某操作设备进行残极压脱操作作业,10时40分左右,破碎班班长陈某在残极压脱机进行设备巡视检查,在未给操作工杨某打招呼确认的情况下,钻入残极压脱机防护栏杆,用左手检查残极压脱机螺丝的紧固状况,其右手手指被启动的残疾压脱机夹板夹伤,造成右手手指受伤(食、中、无、小拇四指)。
事故原因:
1.陈某安全意识淡薄,巡视检查设备没有做好安全确认制,严重违章操作,是造成此起事故的直接原因;
2.杨某作为设备操作者,没有严格执行操作确认和开停车确认是导致此起事故的重要原因;
3.大班班长在安排该项工作任务时,对安全强调不够,安全检查不到位,是造成这起事故的一个主要原因;
4.车间安全管理力度不够,特别是对班组的管理,制度落实不到位,安全确认制未严格执行,也是造成这起事故的一个主要原因;
5.在分公司和分厂强化安全管理的形式下,仍有此类违章行为的发生,说明分厂在安全管理上存在一定漏洞,分厂有一定的管理责任。
事故责任及处理情况:
一、事故责任分析
1.陈某做为组装车间车间一名班长,不严格遵守《公司安全生产管理规定》,在巡视设备时不认真履行安全确认,对此起事故负主要责任。
2.杨某没有严格执行操作确认和开停车确认,对此起事故负直接责任。
3.大班班长对安全强调不够,安全检查不到位,对此起事故负一定责任。
4.车间安全管理存在疏漏,安全确认制未严格执行,车间主任对此起事故负管理责任。
二、事故处理
1.扣罚事故责任人陈某3个月奖金。
2.扣罚操作工杨某1个月奖金。
3.扣罚组装车间生产二班大班长贺某、副大班长田某各1个月奖金。
4.扣罚组装车间主任王某、生产副主任高某、安全员于某各1个月奖金。
5.扣罚组装车间当月奖金的10%。
防范措施:
1.进一步加强班组长、职工安全教育培训工作,认真开展安全确认制学习和落实工作,提高职工的安全意识和安全操作技能,提高班组长的安全责任心;
2.进一步规范作业行为,严格执行安全技术操作规程,进一步强化安全操作的程序化、制度化,严格安全确认制的执行力度,做到令行禁止,有章可循;
3.举一反三,认真开展安全专项整治活动。
以此为契机,在全分厂范围内组织开展隐患查找“我做哪些事会出事故”和“如何做不出事故”的安全工作大讨论反思活动,坚决杜绝此类事故再次发生。
企业名称
中铝股份矿业分公司
发生事故时间
2006 年 10 月30 日
伤亡人数
轻伤1人
生产过程
采矿
直接经济损失
0.7万元
间接经济损失
0.16万元
事故经过:
2006年10月30日,洛阳铝矿采二车间运矿车司机路某16时接班后,按要求对红岩斯太尔进行了出车前检查,未发现异常,便进行运矿作业, 晚18时左右,在破碎原矿仓卸矿过程中,使用三档起斗,突然听到一声巨响,其后粉尘飞扬,驾驶室发生强烈震动,将驾驶员路某从座位上巅起。
事故发生后,路某用电话向车间汇报,车间立即组织人员抢救,及时将路某送医院汉进行治疗,经医院检查:路某“T12椎体轻度压缩骨折、L4/5、L5/S1椎间盘变性轻度突出。
”
事故原因:
1.限位阀失灵,大箱起升过高,油顶产生扭转力矩,导致油缸爆裂。
司机路某未及时掌握新型车辆的安全技术参数、工作原理、异常处理等,操作不当。
2.红岩斯泰尔自卸运输车于7月份装备采二车间,使用单位没有按照《安全教育培训管理制度》对员工进行“四新”教育,员工对新设备还缺乏相应的了解。
事故责任及处理情况:
1.运矿司机路某违反有关法规规定,未履行员工安全义务,扣发奖金200元。
2.车间未及时落实《安全教育管理培训制度》,扣发车间主任徐某300元,车间支部书记郭某100元,安全员王某50元。
3.运矿司机路某写出书面检查,全矿通报批评。
防范措施:
1.更换新油缸,测量液压油压力是否正常,发现异常及时排除。
2.更换限位阀,由生产厂家派人调整。
3.组织人员进行培训,使驾驶员了解掌握新型车辆的安全技术参数,工作原理,异常处理等。