电站锅炉暴管原因及对策
锅炉受热面爆管原因分析及防范措施
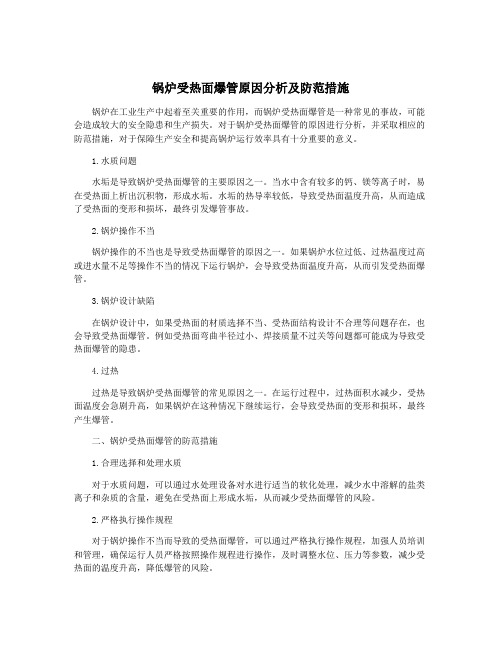
锅炉受热面爆管原因分析及防范措施锅炉在工业生产中起着至关重要的作用,而锅炉受热面爆管是一种常见的事故,可能会造成较大的安全隐患和生产损失。
对于锅炉受热面爆管的原因进行分析,并采取相应的防范措施,对于保障生产安全和提高锅炉运行效率具有十分重要的意义。
1.水质问题水垢是导致锅炉受热面爆管的主要原因之一。
当水中含有较多的钙、镁等离子时,易在受热面上析出沉积物,形成水垢。
水垢的热导率较低,导致受热面温度升高,从而造成了受热面的变形和损坏,最终引发爆管事故。
2.锅炉操作不当锅炉操作的不当也是导致受热面爆管的原因之一。
如果锅炉水位过低、过热温度过高或进水量不足等操作不当的情况下运行锅炉,会导致受热面温度升高,从而引发受热面爆管。
3.锅炉设计缺陷在锅炉设计中,如果受热面的材质选择不当、受热面结构设计不合理等问题存在,也会导致受热面爆管。
例如受热面弯曲半径过小、焊接质量不过关等问题都可能成为导致受热面爆管的隐患。
4.过热过热是导致锅炉受热面爆管的常见原因之一。
在运行过程中,过热面积水减少,受热面温度会急剧升高,如果锅炉在这种情况下继续运行,会导致受热面的变形和损坏,最终产生爆管。
二、锅炉受热面爆管的防范措施1.合理选择和处理水质对于水质问题,可以通过水处理设备对水进行适当的软化处理,减少水中溶解的盐类离子和杂质的含量,避免在受热面上形成水垢,从而减少受热面爆管的风险。
2.严格执行操作规程对于锅炉操作不当而导致的受热面爆管,可以通过严格执行操作规程,加强人员培训和管理,确保运行人员严格按照操作规程进行操作,及时调整水位、压力等参数,减少受热面的温度升高,降低爆管的风险。
3.定期进行检查和维护定期对锅炉进行检查和维护,及时发现和处理受热面的问题,确保受热面结构完好、焊接牢固等,避免因为设计缺陷而导致受热面爆管。
4.控制运行条件对于运行负荷超负荷和过热等情况,可以通过控制运行条件,避免锅炉长期超负荷运行,减少受热面受到的热应力,降低受热面爆管的风险。
锅炉受热面爆管原因分析及防范措施
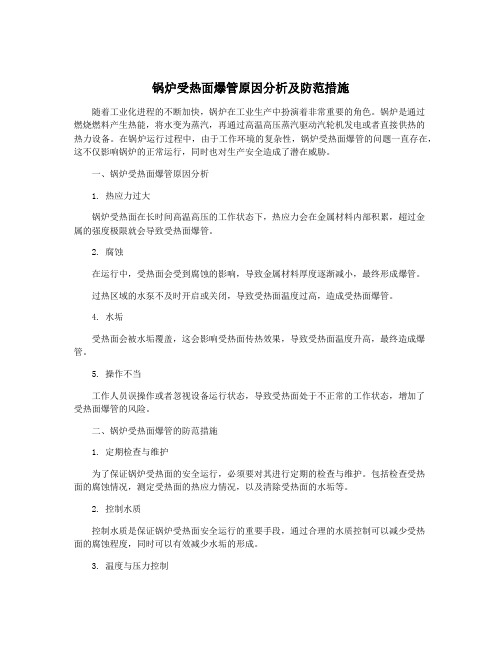
锅炉受热面爆管原因分析及防范措施随着工业化进程的不断加快,锅炉在工业生产中扮演着非常重要的角色。
锅炉是通过燃烧燃料产生热能,将水变为蒸汽,再通过高温高压蒸汽驱动汽轮机发电或者直接供热的热力设备。
在锅炉运行过程中,由于工作环境的复杂性,锅炉受热面爆管的问题一直存在,这不仅影响锅炉的正常运行,同时也对生产安全造成了潜在威胁。
一、锅炉受热面爆管原因分析1. 热应力过大锅炉受热面在长时间高温高压的工作状态下,热应力会在金属材料内部积累,超过金属的强度极限就会导致受热面爆管。
2. 腐蚀在运行中,受热面会受到腐蚀的影响,导致金属材料厚度逐渐减小,最终形成爆管。
过热区域的水泵不及时开启或关闭,导致受热面温度过高,造成受热面爆管。
4. 水垢受热面会被水垢覆盖,这会影响受热面传热效果,导致受热面温度升高,最终造成爆管。
5. 操作不当工作人员误操作或者忽视设备运行状态,导致受热面处于不正常的工作状态,增加了受热面爆管的风险。
二、锅炉受热面爆管的防范措施1. 定期检查与维护为了保证锅炉受热面的安全运行,必须要对其进行定期的检查与维护。
包括检查受热面的腐蚀情况,测定受热面的热应力情况,以及清除受热面的水垢等。
2. 控制水质控制水质是保证锅炉受热面安全运行的重要手段,通过合理的水质控制可以减少受热面的腐蚀程度,同时可以有效减少水垢的形成。
3. 温度与压力控制合理的控制过热状态的温度和压力,防止因为过热导致受热面爆管。
监测过热状态下的水泵工作情况,确保及时启停,调整工作状态。
4. 操作规程制定针对锅炉操作的相关规程,合理分工,严格执行,防止操作不当引发的事故。
5. 安全设备安装为锅炉受热面安装一些安全设备,如安全阀、超温器、低液位保护器等安全装置,以便在爆管发生时及时采取措施防范风险。
总结:锅炉受热面爆管是一个非常严重的问题,一旦发生可能导致灾难性的后果。
我们必须对锅炉受热面的原因加以分析,并且采取一系列有效的防范措施。
只有这样,才能保证工业生产的连续稳定运行,同时保障人员和设备的安全。
电站锅炉爆管事故原因分析与对策

电站锅炉爆管事故原因分析与对策
电站锅炉爆管是很严重的事故,会导致人员伤亡和财产损失。
造成这种事故的原因很多,主要包括以下几个方面:一是设计不合理或过期,二是操作不当或者维护不到位,三
是材料或者设备本身的质量问题等等。
针对不同的原因,制定不同的对策可以有效的预防
这种事故的发生。
首先,设计不合理或过期会造成安全隐患。
因此,应该定期对电站锅炉进行检查和改进。
在进行新设备的选择和设计时,应该严把质量关,选择优质的设备和环保材料。
同时,要遵循国家的安全标准,确保电站锅炉的安全使用。
其次,操作不当是另一个导致电站锅炉爆管的原因。
为此,应该加强员工的培训和技
能提高,以确保他们能熟练掌握操作技巧。
此外,定期检查设备是否处于正常工作状态,
及时解决设备故障,并对设备进行维护保养,以确保设备的正常运行和安全使用。
最后,材料或者设备本身的质量问题也会导致电站锅炉爆管。
为此,应该选择质量可
靠的材料和设备,并严格按照制造标准进行检验,以确保设备的安全使用。
如果出现故障,要及时进行维修和更换。
总之,针对这些造成电站锅炉爆管的原因,电站应该加强监督和管理,完善安全制度
和应急预案,建立健全的安全生产责任制和安全管理体系,以确保电站锅炉的安全运行和
防范事故的发生。
电站锅炉爆管事故原因分析与对策
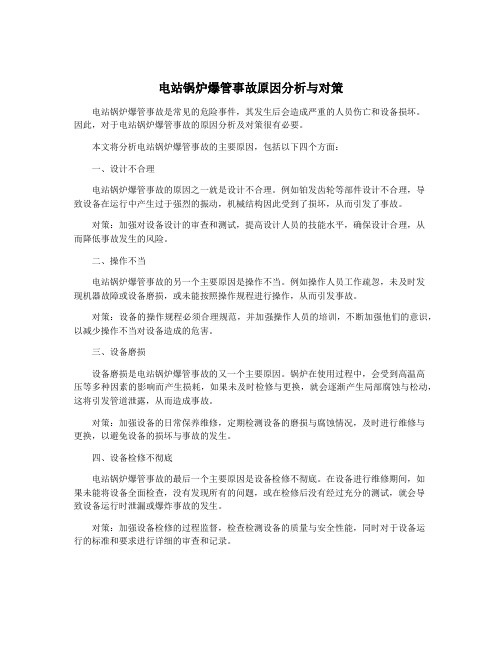
电站锅炉爆管事故原因分析与对策电站锅炉爆管事故是常见的危险事件,其发生后会造成严重的人员伤亡和设备损坏。
因此,对于电站锅炉爆管事故的原因分析及对策很有必要。
本文将分析电站锅炉爆管事故的主要原因,包括以下四个方面:一、设计不合理电站锅炉爆管事故的原因之一就是设计不合理。
例如铂发齿轮等部件设计不合理,导致设备在运行中产生过于强烈的振动,机械结构因此受到了损坏,从而引发了事故。
对策:加强对设备设计的审查和测试,提高设计人员的技能水平,确保设计合理,从而降低事故发生的风险。
二、操作不当电站锅炉爆管事故的另一个主要原因是操作不当。
例如操作人员工作疏忽,未及时发现机器故障或设备磨损,或未能按照操作规程进行操作,从而引发事故。
对策:设备的操作规程必须合理规范,并加强操作人员的培训,不断加强他们的意识,以减少操作不当对设备造成的危害。
三、设备磨损设备磨损是电站锅炉爆管事故的又一个主要原因。
锅炉在使用过程中,会受到高温高压等多种因素的影响而产生损耗,如果未及时检修与更换,就会逐渐产生局部腐蚀与松动,这将引发管道泄露,从而造成事故。
对策:加强设备的日常保养维修,定期检测设备的磨损与腐蚀情况,及时进行维修与更换,以避免设备的损坏与事故的发生。
四、设备检修不彻底电站锅炉爆管事故的最后一个主要原因是设备检修不彻底。
在设备进行维修期间,如果未能将设备全面检查,没有发现所有的问题,或在检修后没有经过充分的测试,就会导致设备运行时泄漏或爆炸事故的发生。
对策:加强设备检修的过程监督,检查检测设备的质量与安全性能,同时对于设备运行的标准和要求进行详细的审查和记录。
综上所述,电站锅炉爆管事故的发生是多种原因交织的,对于这样的事件,我们必须加强对设备的维修保养和操作管理、改进设备结构与设计并提高相关工作人员的专业素质。
只有这样,才能有效地减少电站锅炉爆管事故的发生,保障电站的安全稳定运行。
锅炉管道爆管-原因分析

锅炉爆管的根本原因是什么水冷壁、过热器、再热器、省煤器的管子,在承受压力条件下的破损,均称为爆管。
发生爆管的根本原因,归纳起来有以下各点:1、升火、停炉操作程序不当,使管子的加热或冷却不均匀,产生较大的热应力。
2、运行过程中,汽压、汽温超限,或热偏差过大,使管子蠕胀速度加快.3、运行调节不发,如使火焰偏斜、局部结渣、尾部再燃烧等,都会导致局部管子过热。
4、负荷变动率过大,引起汽压突变,使水循环不正常(变慢、停滞),使管子过热或出现交变应力而疲劳破坏。
5、飞灰磨损是导致省煤器爆管的主要原因。
燃烧器出口气流偏斜,出现“飞边”、“贴壁”现象,使水冷管磨损,是引起水冷壁爆管的原因之一。
6、管壁腐蚀或管内积盐。
当给水含氧量较高,或水速过低,常引起省煤器内壁点状腐蚀而爆管;锅水品质不合格、饱和蒸汽带水,造成过热器管内积盐,导致管壁过热而爆管;高温腐蚀是引起过热器和水冷壁爆管的原因之一.7、制造、安装、检修质量不良。
如管材质量不良或管子钢号用错;管子焊口质量不合格;弯头处壁厚减薄严重;管内有异物使通道面积减小或堵塞;检修时对已蠕胀超限的管子漏检,已经磨薄的管子没有发现等。
0 前言随着我国电力工业建设的迅猛发展,各种类型的大容量火力发电机组不断涌现,锅炉结构及运行更加趋于复杂,不可避免地导致并联各管内的流量与吸热量发生差异。
当工作在恶劣条件下的承压受热部件的工作条件与设计工况偏离时,就容易造成锅炉爆管。
事实上,当爆管发生时常采用所谓快速维修的方法,如喷涂或衬垫焊接来修复,一段时间后又再爆管。
爆管在同一根管子、同一种材料或锅炉的同一区域的相同断面上反复发生,这一现象说明锅炉爆管的根本问题还未被解决.因此,了解过热器爆管事故的直接原因和根本原因,搞清管子失效的机理,并提出预防措施,减少过热器爆管的发生是当前的首要问题。
1过热器爆管的直接原因造成过热器、再热器爆管的直接原因有很多,主要可以从以下几个方面来进行分析。
1.1设计因素1.热力计算结果与实际不符热力计算不准的焦点在于炉膛的传热计算,即如何从理论计算上较合理的确定炉膛出口烟温和屏式过热器的传热系数缺乏经验,致使过热器受热面的面积布置不够恰当,造成一、二次汽温偏离设计值或受热面超温。
锅炉爆管的十四种原因与六种防止措施、安全要求及规定
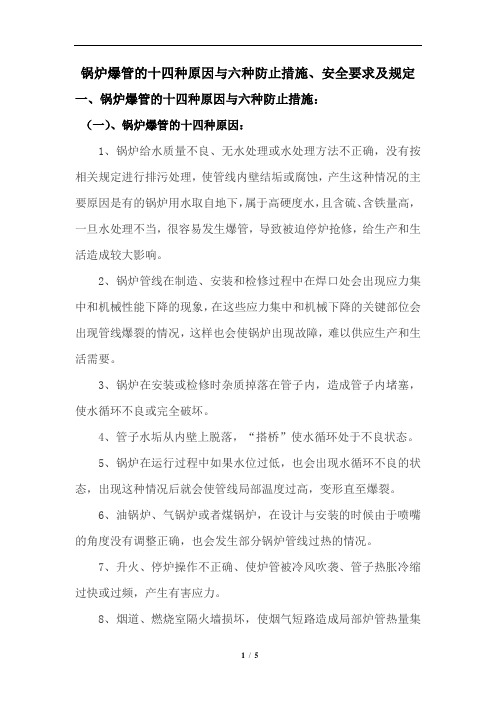
锅炉爆管的十四种原因与六种防止措施、安全要求及规定一、锅炉爆管的十四种原因与六种防止措施:(一)、锅炉爆管的十四种原因:1、锅炉给水质量不良、无水处理或水处理方法不正确,没有按相关规定进行排污处理,使管线内壁结垢或腐蚀,产生这种情况的主要原因是有的锅炉用水取自地下,属于高硬度水,且含硫、含铁量高,一旦水处理不当,很容易发生爆管,导致被迫停炉抢修,给生产和生活造成较大影响。
2、锅炉管线在制造、安装和检修过程中在焊口处会出现应力集中和机械性能下降的现象,在这些应力集中和机械下降的关键部位会出现管线爆裂的情况,这样也会使锅炉出现故障,难以供应生产和生活需要。
3、锅炉在安装或检修时杂质掉落在管子内,造成管子内堵塞,使水循环不良或完全破坏。
4、管子水垢从内壁上脱落,“搭桥”使水循环处于不良状态。
5、锅炉在运行过程中如果水位过低,也会出现水循环不良的状态,出现这种情况后就会使管线局部温度过高,变形直至爆裂。
6、油锅炉、气锅炉或者煤锅炉,在设计与安装的时候由于喷嘴的角度没有调整正确,也会发生部分锅炉管线过热的情况。
7、升火、停炉操作不正确、使炉管被冷风吹袭、管子热胀冷缩过快或过频,产生有害应力。
8、烟道、燃烧室隔火墙损坏,使烟气短路造成局部炉管热量集中而烧坏炉管。
9、腐蚀爆管和设备老化爆管,一般发生在尾部受热面的省煤器管,原因是排烟温度过低或给水温度过低而造成的酸性腐蚀。
10、局部烟速过快,在安装和检修受热面排管时,受热面管子的节距以及受热面的管排与炉墙之间的距离不符合设计要求,在管排与管排之间或管排与炉墙之间形成局部烟气走廊,或局部管子出列造成受热面管子积灰搭桥,引起局部烟速过高从而加大该部位管子磨损和过热。
11、由于施工不仔细,炉墙密封处没有按照施工要求进行严格密封,使漏风处形成涡流,这种情况也会出现管线局部过热,或者是受热不均匀,而漏风也使后面的烟气流速增加,危害尾部受热面。
12、管子高温运行也是锅炉爆管的重要原因,过热超温爆管是由于管子在超温的情况下力学性能下降,管子在压力的作用下发生塑性变形即蠕变裂纹以致爆管。
浅析260t锅炉爆管原因及预防措施

浅析260t锅炉爆管原因及预防措施锅炉爆管是指在使用过程中发生的管道爆裂现象,这种情况不仅会对设备造成严重损坏,还可能引发安全事故,危害人身和财产安全。
了解锅炉爆管的原因,并采取相应的预防措施是非常重要的。
本文将从锅炉爆管的原因和预防措施两个方面进行浅析,以期帮助广大读者更好地防范和处理锅炉爆管的问题。
一、锅炉爆管的原因1. 设计问题锅炉爆管的原因之一是由于设计上的问题所致。
包括管道的材质选择不当,设计厚度不够,结构设计不合理等等,这些问题都可能导致锅炉爆管的发生。
2. 运行问题在锅炉运行过程中,由于燃烧不完全或者燃烧过程不稳定,导致烟气温度过高,管道内的污垢积聚严重,水质不合格等问题都可能引发锅炉爆管。
3. 检修问题锅炉在使用过程中需要不定期进行检修和维护,如果使用人员在检修和维护过程中不规范,操作不当,也有可能导致锅炉爆管的发生。
4. 冷热循环锅炉在长期的冷热循环中,由于管道材质的膨胀和收缩不均匀,会导致管道内部产生应力集中,从而引发管道的破裂。
5. 疲劳损伤锅炉长期工作后,管道内部可能积累了许多微小的裂纹,而在运行时产生的振动、冲击等因素会加剧这些裂纹的扩展,最终导致爆管事故的发生。
二、锅炉爆管的预防措施1. 加强设计与选择在锅炉的设计和选择时,应该充分考虑管道的具体使用情况,选择合适的材质以及合理的设计厚度,尽量避免设计上的问题。
2. 严格控制运行过程在锅炉运行过程中,应该注意加强对燃烧过程的监控,保证燃烧的充分和稳定,尽量避免因燃烧不完全导致的烟气温度过高。
还应加强对水质的控制,定期清洗管道内的污垢,保证水质符合标准。
3. 规范检修与维护在锅炉的检修和维护过程中,使用人员应该严格按照操作规程进行操作,严格遵守操作规程,做好检修和维护记录,确保检修过程安全可靠。
4. 控制冷热循环在锅炉的运行过程中,应尽量避免频繁地进行冷热循环,平稳地进行温度变化,减小管道的膨胀和收缩,避免因温度变化而引发应力集中。
电站锅炉爆管事故原因分析与对策

电站锅炉爆管事故原因分析与对策一、引言在电站锅炉运行过程中,爆管事故是一种十分严重的安全事故,给人民生命财产造成了极大的危害。
爆管事故不仅给电站运营带来了严重的影响,同时也会对周围环境和居民生活造成不可逆转的损害。
对电站锅炉爆管事故进行原因分析并提出相应的对策措施,对于保障人民生命财产安全,维护社会稳定具有重要的意义。
二、电站锅炉爆管事故的常见原因1. 设计问题电站锅炉在设计阶段存在一些缺陷或者问题,比如管道连接处焊接强度不足、管道弯曲处弯角设计不当等,这些都可能造成爆管事故的发生。
2. 操作管理不当电站锅炉在运行时需要进行定期检查和维护,如果操作人员对于锅炉设备的工作原理不了解或者忽视了一些维护细节,那么就会增加爆管事故的发生概率。
3. 水质问题水质是影响锅炉运行的重要因素,如果水质不符合要求,其中可能含有大量腐蚀物质或者杂质,这些都会对锅炉管道造成腐蚀,从而导致爆管事故的发生。
4. 过热电站锅炉在运行过程中,如果受到过高温度的影响,就会导致管道金属材料发生热膨胀,当金属材料的强度达到极限时就会发生爆管事故。
5. 设备老化电站锅炉设备使用时间过长,金属材料由于长期的弯曲和拉伸,使得强度逐渐减弱,从而导致管道发生破裂。
1. 加强设计阶段的质量检查在电站锅炉的设计阶段,要加强对各个部件的质量检查,特别是管道连接处的焊接强度和弯曲处的设计要符合国家相关标准和要求,确保设计的合理性和稳定性。
2. 做好操作人员的培训和管理电站锅炉的操作管理是非常重要的,必须对操作人员进行专业的培训和集中管理,确保他们能够熟练掌握锅炉设备的操作原理和维护方法,降低因操作不当引起爆管事故的风险。
3. 加强水质管理对电站锅炉的供水水质进行严格管理,定期对水质进行化学分析,发现异常情况及时调整水质,避免因水质问题引起的爆管事故。
5. 定期检查和维护定期对电站锅炉设备进行检查和维护,可以及时发现设备的老化情况,采取相应的修复措施,保障设备的正常运行。
锅炉受热面爆管原因分析及防范措施

锅炉受热面爆管原因分析及防范措施锅炉是工业生产中常用的设备,它主要用于将水加热蒸发,产生蒸汽供应给生产设备或者发电机。
而锅炉受热面爆管是一个常见的问题,如果出现爆管,不仅会造成设备损坏,还可能导致人员伤亡和环境污染。
我们有必要对锅炉受热面爆管的原因进行分析,并提出相应的防范措施,以确保设备的安全运行。
一、锅炉受热面爆管原因分析1. 腐蚀腐蚀是造成锅炉受热面爆管的主要原因之一。
锅炉在长期运行过程中,受到高温和高压的影响,其受热面容易发生腐蚀。
特别是水壁受热面,由于长时间受到水的冲刷和腐蚀,容易形成腐蚀坑并逐渐扩大,最终导致爆管。
2. 热应力受热面在长时间高温高压工作状态下,会产生热应力。
当锅炉频繁启停或者受热面温度变化较大时,受热面会因热应力而发生变形和裂纹,最终导致爆管。
3. 疏松受热面焊缝和管壁上的疏松部分,容易成为裂纹的发源地。
当锅炉在高温高压下运行时,这些疏松部分会逐渐扩大地变为裂纹,从而导致爆管。
4. 过热当锅炉运行过程中,燃烧不充分或者受热面积灰,造成部分受热面温度过高,超过了其设计温度,将会导致受热面局部过热,最终导致爆管。
5. 运行控制不当锅炉的运行控制不当也是容易导致受热面爆管的原因之一。
如超压、超温、超载等运行状态下,锅炉受热面容易发生问题,进而引发爆管。
1. 定期检查和维护为了防范锅炉受热面爆管的发生,首先要进行定期的检查和维护工作。
定期对受热面进行检查,发现问题要及时修补。
2. 加强腐蚀防护加强对受热面的腐蚀防护措施,选用耐腐蚀性能好的材料进行受热面的制造或者进行防腐蚀处理。
3. 强化焊接质量管理焊接是锅炉受热面的重要组成部分,焊接质量良好与否直接影响到受热面的安全运行。
要加强焊接质量管理,确保焊接部分无裂纹和疏松。
4. 控制运行状态要合理控制锅炉的运行状态,避免过热、超压、超温等情况的发生。
特别是在启停过程中,要避免频繁的启停,以减少热应力对受热面的影响。
5. 加强运行管理和监控加强对锅炉运行过程的管理和监控,及时发现问题并采取应对措施。
锅炉爆管的原因及处理方法
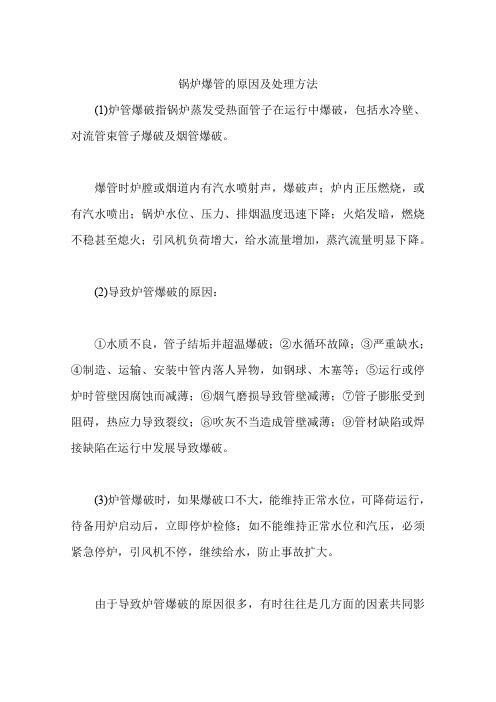
锅炉爆管的原因及处理方法
(1)炉管爆破指锅炉蒸发受热面管子在运行中爆破,包括水冷壁、对流管束管子爆破及烟管爆破。
爆管时炉膛或烟道内有汽水喷射声,爆破声;炉内正压燃烧,或有汽水喷出;锅炉水位、压力、排烟温度迅速下降;火焰发暗,燃烧不稳甚至熄火;引风机负荷增大,给水流量增加,蒸汽流量明显下降。
(2)导致炉管爆破的原因:
①水质不良,管子结垢并超温爆破;②水循环故障;③严重缺水;
④制造、运输、安装中管内落人异物,如钢球、木塞等;⑤运行或停炉时管壁因腐蚀而减薄;⑥烟气磨损导致管壁减薄;⑦管子膨胀受到阻碍,热应力导致裂纹;⑧吹灰不当造成管壁减薄;⑨管材缺陷或焊接缺陷在运行中发展导致爆破。
(3)炉管爆破时,如果爆破口不大,能维持正常水位,可降荷运行,待备用炉启动后,立即停炉检修;如不能维持正常水位和汽压,必须紧急停炉,引风机不停,继续给水,防止事故扩大。
由于导致炉管爆破的原因很多,有时往往是几方面的因素共同影
响而造成事故,所以,防止炉管爆破也必须从搞好锅炉设计、制造、安装、运行管理、检验等各个环节人手。
电站锅炉爆管事故原因分析与对策
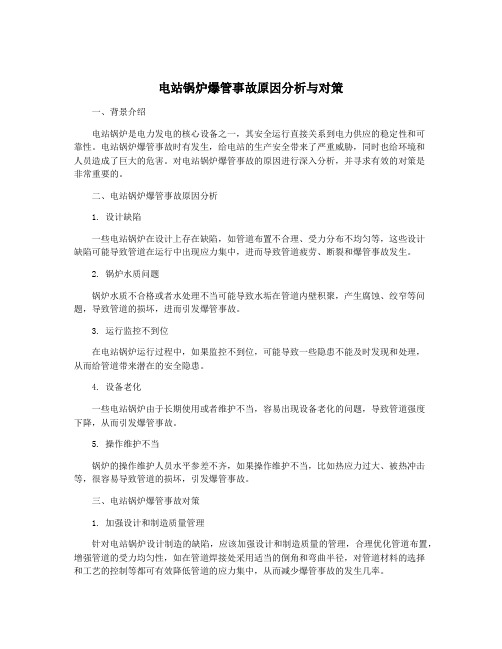
电站锅炉爆管事故原因分析与对策一、背景介绍电站锅炉是电力发电的核心设备之一,其安全运行直接关系到电力供应的稳定性和可靠性。
电站锅炉爆管事故时有发生,给电站的生产安全带来了严重威胁,同时也给环境和人员造成了巨大的危害。
对电站锅炉爆管事故的原因进行深入分析,并寻求有效的对策是非常重要的。
二、电站锅炉爆管事故原因分析1. 设计缺陷一些电站锅炉在设计上存在缺陷,如管道布置不合理、受力分布不均匀等,这些设计缺陷可能导致管道在运行中出现应力集中,进而导致管道疲劳、断裂和爆管事故发生。
2. 锅炉水质问题锅炉水质不合格或者水处理不当可能导致水垢在管道内壁积聚,产生腐蚀、绞窄等问题,导致管道的损坏,进而引发爆管事故。
3. 运行监控不到位在电站锅炉运行过程中,如果监控不到位,可能导致一些隐患不能及时发现和处理,从而给管道带来潜在的安全隐患。
4. 设备老化一些电站锅炉由于长期使用或者维护不当,容易出现设备老化的问题,导致管道强度下降,从而引发爆管事故。
5. 操作维护不当锅炉的操作维护人员水平参差不齐,如果操作维护不当,比如热应力过大、被热冲击等,很容易导致管道的损坏,引发爆管事故。
三、电站锅炉爆管事故对策1. 加强设计和制造质量管理针对电站锅炉设计制造的缺陷,应该加强设计和制造质量的管理,合理优化管道布置,增强管道的受力均匀性,如在管道焊接处采用适当的倒角和弯曲半径,对管道材料的选择和工艺的控制等都可有效降低管道的应力集中,从而减少爆管事故的发生几率。
2. 定期检测和维护锅炉水质加强对锅炉水质的监测和管理,定期对水质进行化验分析,及时清洗管道和换热设备,控制水质合格,避免管道内壁水垢的积聚,以减少管道的腐蚀、绞窄等风险,为管道的安全使用提供保障。
3. 完善运行监控体系建立完善的运行监控体系,引入智能化监测设备,实时监控设备运行状态和管道的状况,及时发现和处理潜在的安全隐患,保障管道的安全运行。
4. 加强设备维护和更新加强设备的定期维护和保养,延长设备的使用寿命,及时更新老化的设备,减少老化设备对管道的影响,降低爆管事故的发生几率。
电站锅炉爆管事故原因分析与对策
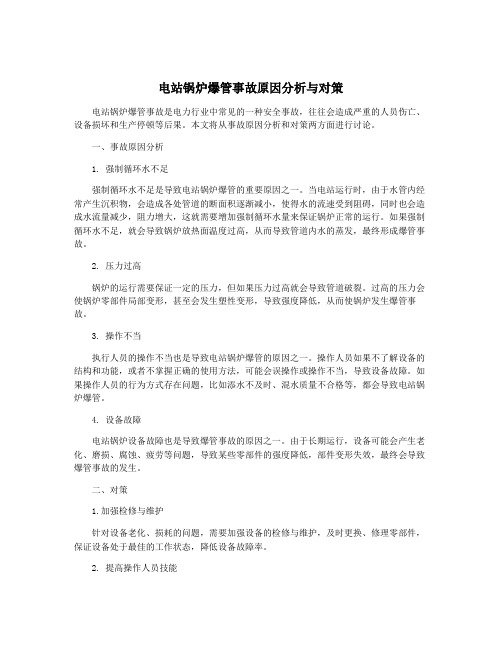
电站锅炉爆管事故原因分析与对策电站锅炉爆管事故是电力行业中常见的一种安全事故,往往会造成严重的人员伤亡、设备损坏和生产停顿等后果。
本文将从事故原因分析和对策两方面进行讨论。
一、事故原因分析1. 强制循环水不足强制循环水不足是导致电站锅炉爆管的重要原因之一。
当电站运行时,由于水管内经常产生沉积物,会造成各处管道的断面积逐渐减小,使得水的流速受到阻碍,同时也会造成水流量减少,阻力增大,这就需要增加强制循环水量来保证锅炉正常的运行。
如果强制循环水不足,就会导致锅炉放热面温度过高,从而导致管道内水的蒸发,最终形成爆管事故。
2. 压力过高锅炉的运行需要保证一定的压力,但如果压力过高就会导致管道破裂。
过高的压力会使锅炉零部件局部变形,甚至会发生塑性变形,导致强度降低,从而使锅炉发生爆管事故。
3. 操作不当执行人员的操作不当也是导致电站锅炉爆管的原因之一。
操作人员如果不了解设备的结构和功能,或者不掌握正确的使用方法,可能会误操作或操作不当,导致设备故障。
如果操作人员的行为方式存在问题,比如添水不及时、混水质量不合格等,都会导致电站锅炉爆管。
4. 设备故障电站锅炉设备故障也是导致爆管事故的原因之一。
由于长期运行,设备可能会产生老化、磨损、腐蚀、疲劳等问题,导致某些零部件的强度降低,部件变形失效,最终会导致爆管事故的发生。
二、对策1.加强检修与维护针对设备老化、损耗的问题,需要加强设备的检修与维护,及时更换、修理零部件,保证设备处于最佳的工作状态,降低设备故障率。
2. 提高操作人员技能操作人员是锅炉运行的关键环节,需要培养技术素质高、操作技能过硬的专业人员,对操作规程、安全手册等文件进行心中学习,提高操作人员对设备的认识和理解。
3.优化水处理技术通过对水质的检测,优化水处理技术,预防管道内沉积物的形成,并加大水质检测力度,减少混水的可能性,降低爆管事故的发生率。
4.保证设备安全加强设备的安全监测与保护,提高系统自动控制的精度和可靠性,并根据不同的工作状态,设置不同的预警带,及时发现问题,保证设备安全运行。
锅炉受热面爆管原因分析及防范措施
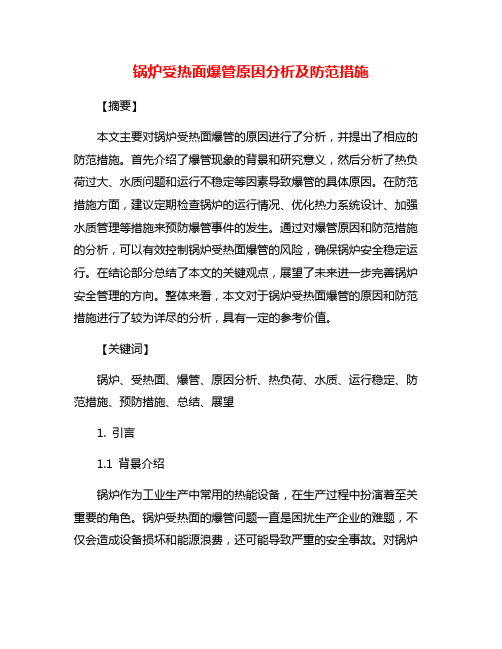
锅炉受热面爆管原因分析及防范措施【摘要】本文主要对锅炉受热面爆管的原因进行了分析,并提出了相应的防范措施。
首先介绍了爆管现象的背景和研究意义,然后分析了热负荷过大、水质问题和运行不稳定等因素导致爆管的具体原因。
在防范措施方面,建议定期检查锅炉的运行情况、优化热力系统设计、加强水质管理等措施来预防爆管事件的发生。
通过对爆管原因和防范措施的分析,可以有效控制锅炉受热面爆管的风险,确保锅炉安全稳定运行。
在结论部分总结了本文的关键观点,展望了未来进一步完善锅炉安全管理的方向。
整体来看,本文对于锅炉受热面爆管的原因和防范措施进行了较为详尽的分析,具有一定的参考价值。
【关键词】锅炉、受热面、爆管、原因分析、热负荷、水质、运行稳定、防范措施、预防措施、总结、展望1. 引言1.1 背景介绍锅炉作为工业生产中常用的热能设备,在生产过程中扮演着至关重要的角色。
锅炉受热面的爆管问题一直是困扰生产企业的难题,不仅会造成设备损坏和能源浪费,还可能导致严重的安全事故。
对锅炉受热面爆管原因进行分析,并制定相应的防范措施,对于提高生产效率、保障人员安全具有重要意义。
锅炉受热面爆管问题的出现往往与多种因素有关,如热负荷过大、水质问题、运行不稳定等。
研究这些爆管原因,可以为企业避免类似问题的发生提供重要参考,同时为锅炉的维护和管理提供方向。
通过本文对锅炉受热面爆管原因分析及防范措施的探讨,旨在帮助生产企业更好地理解该问题,防患于未然,保障设备的正常运转。
为今后的相关研究提供基础和思路,共同推动锅炉设备技术的发展和改进。
1.2 研究意义锅炉是工业生产中常见的重要设备,其受热面爆管问题一直是工程技术领域关注的热点之一。
研究锅炉受热面爆管的原因分析及防范措施,对于提高锅炉运行安全性和稳定性具有重要意义。
深入分析锅炉受热面爆管的原因,可以帮助工程技术人员更好地了解爆管问题的根源。
通过研究不同原因导致的爆管现象,可以为进一步的防范措施提供理论依据。
电站锅炉过热器爆管原因及对策
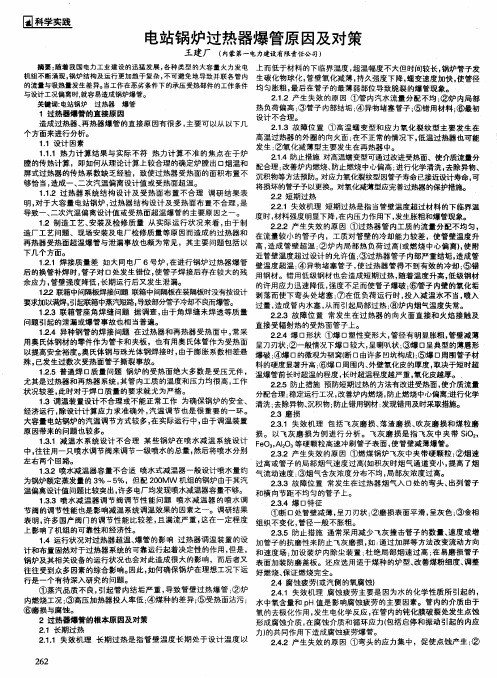
问题 引 起 的泄 漏 或爆 管事 故 也 相 当普 遍 。 直接受辐射热 的受热面管子上。 1 - 异 种 钢 管 的 焊 接 问题 在 过 热 器 和 再 热 器 受 热 面 中 , 采 .4 2 常 22 .. 口形状 ① 爆 口塑性变形大 , 4爆 管径有明显胀粗 , 管壁减 薄 用奥氏体钢材的零件作 为管卡和夹板 ,也有用奥 氏体 管作 为受热面 呈刀刃状 ; 一般情况下爆 口较大 , ② 呈喇叭状 : ③爆 口呈典型的薄唇形 以提高安全裕度。 氏体钢与珠 光体钢焊接时 , 奥 由于膨胀系数相差悬 爆破 ; 口的微观为韧窝《 ④爆 断口由许多凹坑构成) i 口周围管子材 ⑤爆 殊, 已发生过数次受热面管子撕裂事故。 料的硬度显著升高; ⑥爆 口周 围内、 外壁氧化皮的厚度, 取决于短时超 125 普 通 焊 口质 量 问 题 锅 炉 的 受热 面 绝 大 多 数 是 受 压 元 件 , 温 爆 管前 长 时超 温 的程度 , 时 超温 程 度越 严 重 , 化 皮越 厚 。 -. 长 氧 尤 其 是过 热 器 和 再 热器 系统 , 其管 内工 质 的 温度 和 压 力 均 很 高 , 工作 22 防 止措 施 预 防短 期过 热 的 方法 有改 进 受热 面 , 介质 流 量 __ 5 使 状况较 差, 此时对于焊 口质量 的要 求就尤为严格 。 分配合 理 ; 定 运行 工 况 , 稳 改善 炉 内燃烧 , 防止 燃烧 中心偏 离 : 化学 进行 13调温装置设计不合理或不能正 常工作 为确 保锅 炉的安全 、 清洗 : . 去除异物、 沉积物: 防止错用钢材 : 发现错用及时采取措施。 经济运行 , 除设计计算应力求准确外 , 汽温调 节也是很重要的一环。 23 磨 损 . 大容量电站锅炉的汽温调节 方式较多 , 在实际运行 中, 由于调温装置 231 失效机理 包括 飞灰磨 损、 .. 落渣磨 损、 吹灰磨 损和煤粒磨 原 因带来的问题也较多。 损 。 以飞灰 磨损 为例进行 分析 。飞灰磨损 是指 飞灰 中夹 带 SO i , 131减 温水系统设计 不合理 某些锅炉在 喷水减 温 系统 设计 F O , 。 硬 颗 粒 高速 冲 刷 管 子 表面 , .. e 。AI 等 0 使管 壁 减 薄 爆 管 。
电站锅炉爆管事故原因分析与对策

电站锅炉爆管事故原因分析与对策电站锅炉爆管事故是电力设施中较为严重的一种安全事故。
一旦发生,除了会造成大面积的物质损失,也会严重威胁人员的安全。
因此,对电站锅炉爆管事故的原因进行分析,并采取相应措施,减少锅炉爆管事故的发生,具有十分重要的意义。
电站锅炉爆管事故的原因较为复杂,一般可以归纳为以下几个方面:1. 压力过高锅炉操作过程中,由于各种原因,可能会导致锅炉内部压力过高。
这样的话,锅炉的材料就会受到过度的负荷,可能会引起锅炉管道或承压部件出现破损或爆裂。
2. 超温或超压3. 管道结垢锅炉管道内的水质可能会出现结垢现象,这会导致管道内部的通道变窄,使得管道内部水流量减少,从而导致管道内部的压力增大。
如果此时出现了其他问题,如超温或超压等,就很容易导致管道炸裂。
4. 材料缺陷锅炉内部的材料质量如果存在缺陷,就容易导致锅炉爆管。
例如,锅炉内部的焊缝没有焊好,或是材料内部存在裂缝等,都可能导致锅炉爆管。
此外,锅炉做工不好,也可能导致锅炉内部存在错误的焊接、不规范的受力设计等问题,从而引起爆裂。
为了解决电站锅炉爆管事故,可以采取以下对策:1. 加强安全管理针对锅炉的超压、超温等情况,需要加强安全管理。
在实际操作中,需要制定全面的安全管理计划,并建立健全的安全管理制度。
此外,还需要培训和加强工作人员的安全意识和安全技能。
2. 定期维护为了减少因管道结垢等原因引起的管道破裂,需要定期对锅炉进行维护。
例如,需要定期清理锅炉内部的管道和烟囱,清除管道内下脚料及沉淀物,对管道结垢情况进行排查。
3. 坚持科学施工在安装新锅炉或维修现有锅炉时,需要严格按照设计要求进行施工。
例如,需要严格遵守焊接规范,对焊接质量进行全面检测,避免出现漏焊、冷焊等问题。
此外,还需要在维护过程中,采用专业的工具和设备,确保锅炉的维护过程规范有效。
4. 更新设备技术为了保证锅炉的安全运行,需要采用新技术和新材料进行研发、生产和使用。
例如,可采用高强度材料来生产锅炉的承压部件,以增强承压部件的耐压性能。
电站锅炉爆管事故原因分析与对策

电站锅炉爆管事故原因分析与对策电站锅炉爆管事故是指锅炉在运行过程中发生管道爆裂、泄漏等严重事故。
这种事故会导致锅炉停产,甚至造成人员伤亡和财产损失。
对于电站而言,锅炉是其核心设备之一,一旦发生爆管事故,将对电站的正常运行和安全生产造成严重影响。
对于电站运行管理人员来说,必须高度重视锅炉爆管事故的原因分析和对策制定,以提高锅炉运行安全性和稳定性。
1. 设计原因一些锅炉爆管事故源于设计不当。
锅炉管道的强度计算不足或者管道材质选择不当等,都有可能导致管道爆裂。
设计中未充分考虑到锅炉管道的热胀冷缩和热应力等因素,也会增加爆管的风险。
2. 制造安装原因在锅炉的制造和安装过程中,如果材料选择不当、焊接质量不合格、管道连接处存在缺陷等问题,都有可能成为爆管事故的潜在隐患。
加之安装人员操作不当或者使用过程中的振动、腐蚀等因素,也会加剧管道的疲劳破坏和蠕变破坏,从而导致爆管事故。
3. 运行管理原因电站锅炉的运行管理也是爆管事故的重要原因之一。
过高的水质参数、未及时清除结垢、操作超负荷或者频繁变负荷等运行不规范的行为,都有可能对锅炉管道造成损害。
设备的维护保养工作不到位,也会加剧管道的老化和疲劳,从而增加爆管的风险。
4. 外部环境原因外部环境的影响也可能导致锅炉爆管事故。
水质差导致管道内腐蚀加剧、温度变化剧烈导致管道热应力大等因素,都可能成为爆管的隐患。
二、电站锅炉爆管事故对策1. 加强设计和制造质量管理在锅炉的设计和制造过程中,应严格按照相关标准和规范进行,确保材料的质量、焊接工艺的可靠性和管道的连接质量等。
对于现有的一些老旧设备,也应该通过技术改造或者更新换代,提高设备的安全性和稳定性。
2. 建立健全运行管理制度电站应建立健全的锅炉运行管理制度,明确各项操作规程和注意事项,确保锅炉的正常运行和安全性。
对于水质参数、操作负荷等关键参数,应加强监测和调整,确保锅炉运行处于最佳状态。
3. 定期维护保养和检修电站锅炉的设备维护保养工作至关重要。
电站锅炉爆管事故原因分析与对策

电站锅炉爆管事故原因分析与对策1. 引言1.1 电站锅炉爆管事故简介电站锅炉爆管事故是指在电站锅炉运行过程中,由于各种原因导致锅炉管道爆裂、破裂的事故。
这种事故往往会导致严重的安全问题和损失。
电站锅炉爆管事故在电力行业中属于比较严重的事故之一,不仅会造成设备损坏和停工停产,还可能造成人员伤亡和环境污染。
电站锅炉爆管事故通常是由于多种因素的综合作用造成的。
一般来说,常见的原因包括超压、超温、金属疲劳、水垢结垢、操作不当等。
超压和超温是较为常见的原因,这可能是由于设备设计缺陷、运行参数设定不当或者操作人员误操作等导致的。
为了有效避免电站锅炉爆管事故的发生,必须对其原因进行深入分析,并提出相应的对策建议。
建立健全的防范措施也是十分必要的,只有这样,才能保障电站锅炉运行安全,保障生产和人员的安全。
2. 正文2.1 电站锅炉爆管事故原因分析电站锅炉爆管是指在锅炉运行过程中,因各种原因导致管道爆裂或破裂,造成严重的安全事故。
其主要原因包括以下几个方面:1. 设计缺陷:一些电站锅炉在设计上存在缺陷,如管道设计不合理、材料选择不当等,容易导致管道强度不够或易腐蚀。
2. 运行不当:电站锅炉在运行过程中,如加热温度过高、加压不稳定等操作不当,会导致管道温度过高或压力异常,增加爆管的风险。
3. 维护保养不到位:部分电站锅炉在维护保养上存在疏忽或不及时,导致管道腐蚀严重、积垢堵塞等问题,进而引发爆管事故。
4. 外部影响因素:如强烈震动、突然变压等外部影响因素也可能导致电站锅炉爆管,需要引起重视。
要预防电站锅炉爆管事故,必须加强设计审查、规范运行管理、定期维护保养以及加强安全监控等措施,确保电站锅炉安全运行。
2.2 电站锅炉爆管事故对策建议1. 加强设备检测和维护:定期对电站锅炉进行全面的检查和维护,及时发现问题并采取措施修复,以减少事故发生的可能性。
2. 强化员工培训:加强员工对电站锅炉操作的培训,提高他们的技能和意识,使他们能够正确操作设备,减少操纵错误导致事故的发生。
电站锅炉爆管事故原因分析与对策

电站锅炉爆管事故原因分析与对策【摘要】电站锅炉爆管事故是一种严重的安全事件,可能造成人员伤亡和财产损失。
本文通过对电站锅炉爆管事故的概述、原因分析以及对策建议等进行研究,旨在识别和解决这一问题。
爆管事故的原因主要包括设计缺陷、运行不当、设备老化等方面。
为此,本文提出了针对这些原因的预防措施和紧急处理措施,并对其进行了详细的分析和建议。
通过对这些措施的执行,可以有效减少和避免电站锅炉爆管事故的发生,保障电站设备和人员的安全。
结论总结了本文的研究成果和对未来的展望,希望可以为电站锅炉爆管事故的预防和控制提供一定的参考。
【关键词】引言:研究背景,研究意义正文:电站锅炉爆管事故概述,爆管事故原因分析,对策建议,预防措施,紧急处理措施结论:结论总结,未来展望1. 引言1.1 研究背景研究背景:电站锅炉是供给电力和热力的重要设备,由于各种原因导致的锅炉爆管事故却时有发生,给生产和生活带来了严重的危害和损失。
锅炉爆管事故不仅会造成设备损坏和人员伤亡,还会引发生产线停机、电力供应中断等连锁影响。
对电站锅炉爆管事故进行深入研究,找出原因并制订有效对策是十分必要的。
近年来,随着我国社会经济的快速发展,电力需求逐渐增加,电站锅炉的使用频率也在不断提高。
在锅炉运行过程中,各种因素如热应力、热腐蚀、水质、操作不当等都可能成为造成爆管事故的潜在因素。
研究锅炉爆管事故的原因及应对措施,对于确保电站锅炉安全运行,保障电力供应具有重要意义。
本文旨在通过对电站锅炉爆管事故进行全面分析,探讨其原因,并提出相关防范和应对措施,以期为电站锅炉安全运行提供参考和指导。
希望通过本文的研究,推动相关领域的技术进步和管理水平的提升。
1.2 研究意义电站锅炉爆管事故频发,对生产和人员安全造成严重威胁。
深入分析电站锅炉爆管事故的原因,提出有效对策和预防措施,具有非常重要的研究意义。
对爆管事故进行深入分析,能够揭示事故发生的具体原因,为今后避免类似事故提供经验教训。
电站锅炉爆管事故原因分析与对策

电站锅炉爆管事故原因分析与对策电站锅炉爆管是一种严重的安全事故,一旦发生,不仅会给电站生产和运营带来严重影响,还可能造成人员伤亡和环境污染。
对于电站锅炉爆管事故的原因分析和对策研究尤为重要。
一、电站锅炉爆管的原因分析电站锅炉爆管是由多种因素共同作用导致的,主要原因可归纳为以下几点:1. 设计缺陷:部分电站锅炉在设计上存在缺陷,例如结构不合理、材料选择不当等,容易导致管壁厚度不均匀,应力集中等问题,从而增加了爆管的风险。
2. 运行不当:电站锅炉在长期运行中,由于操作人员的疏忽大意或者缺乏必要的维护保养,导致设备的老化和劣化加速,管壁腐蚀加剧,降低了管道的承载能力。
3. 过热和缺水:电站锅炉在运行过程中,如果温度过高或者缺乏充足的水份,会导致管道的温度和压力升高,加速了管道的疲劳损伤,从而增加了爆管的风险。
4. 质量问题:部分电站锅炉的制造质量存在问题,例如材料质量不合格、焊接接头存在缺陷等,容易导致管道的蠕变和疲劳断裂,增加了爆管的风险。
5. 外部因素:电站锅炉在运行过程中,受到了外部的振动、冲击或者机械损伤,从而使管道的疲劳损伤加剧,增加了爆管的风险。
二、电站锅炉爆管的对策措施针对电站锅炉爆管的原因,可以采取以下对策措施来降低爆管事故的发生风险:1. 设备改造升级:对于存在设计缺陷的电站锅炉,可以通过对设备进行改造升级来解决问题,例如改善管道结构、优化材料选择等,提高管道的承载能力和抗爆击能力。
2. 加强运行管理:加强对电站锅炉的运行管理和维护保养工作,严格执行相关操作规程和标准,确保设备的正常运行,减少因运行不当导致的爆管风险。
3. 控制温度和水质:加强对电站锅炉的温度和水质控制,确保设备在正常的温度和压力范围内运行,避免因过热和缺水导致的爆管风险。
4. 提高质量管理水平:加强对电站锅炉制造质量的监督检验,确保材料选择合格和焊接接头质量良好,提高设备的使用寿命和安全性。
5. 安全防护设施:在电站锅炉周围设置安全防护设施,加强设备的振动和冲击的监测和保护,减少外部因素对管道的破坏。
电站锅炉过热器管爆管原因分析

1 . 过 热 器爆 管 的原 因分 析 组 织极为粗 大 , 是不 正常组织 。 经以上分析 可知 , 爆 管是 由于管 材焊 接 在焊 缝融合 区内存在粗 大魏氏体组织 、 大量非金 属夹杂等缺 陷 般情 况下, 在 发生过 热器爆 管时 , 为尽快恢 复正常生 产, 尽量减 质量 差, 少 经济损失, 我们一般 采用快速维 修法 , 如更换新 管段、 堵 管、 补强等措 造 成的。 施, 可是往往运 行一段时 间后又发生 爆管。 并且非常巧 合的是爆 管在 同 2 . 防止 过热 器 爆管 的预 防 措旌 根 管子、 同一种材 料或锅炉 同一区域的相 同断面层次上 反复发 生, 这 从 制造 、 安装 和检修 上, 首先严把材 料 质量 关, 避 免管材本 身存 在
或烟 速偏差 , 炉内烟 气右旋 时, 右侧烟 温高 l 左旋 时左侧烟温高 。 有时, 两侧 的烟温偏差还 相当大 , 因而引起较大 的汽温偏差 。
一
焊 道融合线及 热影 响区内, 金相检验 结果表 明, 管束 的金相组织是 正常 的。 焊 道、 融合线 、 热 影响 区的金相组 织为粗 大魏 氏体组 织+ 铁素体 ,
电站锅炉过热器管爆管原因分析
于全 大庆石化公司热电厂维修 一车间 黑龙江大庆
1 6 3 7 1 4
靠运行 起着决 定性的作 用, 但是 , 锅 炉及其相关设备 的运行状况也会 对此 造成很 大的影响 , 而后者又往往 受到众多因素的综合影响。 因此 , 如何确 保锅 炉在理想工况下运行是一个有待深 入研 究的问题 。 本文对热电站锅炉
启停 曲线进行 , 控 制过热 器管壁温 度和锅 炉参数在允许 范围内, 并严格 监视 及 时调 整, 严 防超温 、 超压、 满水 、 缺 水事 故发 生 ; 其次 加 强锅炉 炉膛 、 过热 器吹 灰和吹灰 器的管理 , 防止受 热面严重积 灰, 确保 受热面
- 1、下载文档前请自行甄别文档内容的完整性,平台不提供额外的编辑、内容补充、找答案等附加服务。
- 2、"仅部分预览"的文档,不可在线预览部分如存在完整性等问题,可反馈申请退款(可完整预览的文档不适用该条件!)。
- 3、如文档侵犯您的权益,请联系客服反馈,我们会尽快为您处理(人工客服工作时间:9:00-18:30)。
前言随着我国电力工业建设的迅猛发展,各种类型的大容量火力发电机组不断涌现,锅炉结构及运行更加趋于复杂,不可避免地导致并联各管内的流量与吸热量发生差异。
当工作在恶劣条件下的承压受热部件的工作条件与设计工况偏离时,就容易造成锅炉爆管。
事实上,当爆管发生时常采用所谓快速维修的方法,如喷涂或衬垫焊接来修复,一段时间后又再爆管。
爆管在同一根管子、同一种材料或锅炉的同一区域的相同断面上反复发生,这一现象说明锅炉爆管的根本问题还未被解决。
因此,了解过热器爆管事故的直接原因和根本原因,搞清管子失效的机理,并提出预防措施,减少过热器爆管的发生是当前的首要问题。
1过热器爆管的直接原因造成过热器、再热器爆管的直接原因有很多,主要可以从以下几个方面来进行分析。
1.1设计因素1.热力计算结果与实际不符热力计算不准的焦点在于炉膛的传热计算,即如何从理论计算上较合理的确定炉膛出口烟温和屏式过热器的传热系数缺乏经验,致使过热器受热面的面积布置不够恰当,造成一、二次汽温偏离设计值或受热面超温。
2.设计时选用系数不合理如华能上安电厂由B&W公司设计、制造的“W”型锅炉,选用了不合理的受热面系数,使炉膛出口烟温实测值比设计值高80~100℃;又如富拉尔基发电总厂2号炉(HG-670/140-6型)选用的锅炉高宽比不合理,使炉膛出口实测烟温高于设计值160℃。
3.炉膛选型不当我国大容量锅炉的早期产品,除计算方法上存在问题外,缺乏根据燃料特性选择炉膛尺寸的可靠依据,使设计出的炉膛不能适应煤种多变的运行条件。
炉膛结构不合理,导致过热器超温爆管。
炉膛高度偏高,引起汽温偏低。
相反,炉膛高度偏低则引起超温。
4.过热器系统结构设计及受热面布置不合理调研结果表明,对于大容量电站锅炉,过热器结构设计及受热面布置不合理,是导致一、二次汽温偏离设计值或受热面超温爆管的主要原因之一。
过热器系统结构设计及受热面布置的不合理性体现在以下几个方面:(1)过热器管组的进出口集箱的引入、引出方式布置不当,使蒸汽在集箱中流动时静压变化过大而造成较大的流量偏差。
(2)对于蒸汽由径向引入进口集箱的并联管组,因进口集箱与引入管的三通处形成局部涡流,使得该涡流区附近管组的流量较小,从而引起较大的流量偏差。
引进美国CE公司技术设计的配300MW和600MW机组的控制循环锅炉屏再与末再之间不设中间混合集箱,屏再的各种偏差被带到末级去,导致末级再热器产生过大的热偏差。
如宝钢自备电厂、华能福州和大连电厂配350MW机组锅炉,石横电厂配300MW机组锅炉以及平坪电厂配600MW机组锅炉再热器超温均与此有关。
(3)因同屏(片)并联各管的结构(如管长、内径、弯头数)差异,引起各管的阻力系数相差较大,造成较大的同屏(片)流量偏差、结构偏差和热偏差,如陡河电厂日立850t/h锅炉高温过热器超温就是如此。
(4)过热器或再热器的前后级之间没有布置中间混合联箱而直接连接,或者未进行左右交叉,这样使得前后级的热偏差相互叠加。
在实际运行过程中,上述结构设计和布置的不合理性往往是几种方式同时存在,这样加剧了受热面超温爆管的发生。
5.壁温计算方法不完善,导致材质选用不当从原理上讲,在对过热器和再热器受热面作壁温校核时,应保证偏差管在最危险点的壁温也不超过所用材质的许用温度。
而在实际设计中,由于对各种偏差的综合影响往往未能充分计及,导致校核点计算壁温比实际运行低,或者校核点的选择不合理,这样选用的材质就可能难以满足实际运行的要求,或高等级钢材未能充分利用。
6.计算中没有充分考虑热偏差如淮北电厂5号炉过热器在后屏设计中没有将前屏造成的偏差考虑进去,影响了管材的正确使用,引起过热器爆管。
1.2制造工艺、安装及检修质量从实际运行状况来看,由于制造厂工艺问题、现场安装及电厂检修质量等原因而造成的过热器和再热器受热面超温爆管与泄漏事故也颇为常见,其主要问题包括以下几个方面。
1.焊接质量差如大同电厂6号炉,在进行锅炉过热器爆管后的换管补焊时,管子对口处发生错位,使管子焊接后存在较大的残余应力,管壁强度降低,长期运行后又发生泄漏。
2.联箱中间隔板焊接问题联箱中间隔板在装隔板时没有按设计要求加以满焊,引起联箱中蒸汽短路,导致部分管子冷却不良而爆管。
3.联箱管座角焊缝问题据调查,由于角焊缝未焊透等质量问题引起的泄漏或爆管事故也相当普遍。
如神头电厂5号炉(捷克650t/h亚临界直流锅炉)包墙过热器出口联箱至混合联箱之间导汽管曾在水压试验突然断裂飞脱,主要原因是导汽管与联箱连接的管角焊缝存在焊接冷裂纹。
4.异种钢管的焊接间题在过热器和再热器受热面中,常采用奥氏体钢材的零件作为管卡和夹板,也有用奥氏体管作为受热面以提高安全裕度。
奥氏体钢与珠光体钢焊接时,由于膨胀系数相差悬殊,已发生过数次受热面管子撕裂事故。
此外,一种钢管焊接时往往有接头两边壁厚不等的问题,不同壁厚主蒸汽管的焊接接头损坏事故也多次发生。
一些厂家认为,在这种情况下应考虑采用短节,以保证焊接接头两侧及其热影响区范围内壁厚不变。
5.普通焊口质量问题锅炉的受热面绝大多数是受压元件,尤其是过热器和再热器系统,其管内工质的温度和压力均很高,工作状况较差,此时对于焊口质量的要求就尤为严格。
但在实际运行中,由于制造厂焊口、安装焊口和电厂检修焊口质量不合格(如焊口毛刺、砂眼等)而引起的爆管、泄漏事故相当普遍,其后果也相当严重。
6.管子弯头椭圆度和管壁减薄问题GB9222-88水管锅炉受压无件强度计算标准规定了弯头的椭圆度,同时考虑了弯管减薄所需的附加厚度。
该标准规定,对弯管半径R>4D的弯头,弯管椭圆度不大于8%。
但实测数据往往大于此值,最大达21%,有相当一部分弯头的椭圆度在9%~12%之间。
另外,实测数据表明,有不少管子弯头的减薄量达23%~28%,小于直管的最小需要壁厚。
因此,希望对弯管工艺加以适当的改进,以降低椭圆度和弯管减薄量,或者增加弯头的壁厚。
7.异物堵塞管路锅炉在长期运行中,锈蚀量较大,但因管径小,无法彻底清除,管内锈蚀物沉积在管子底部水平段或弯头处,造成过热而爆管。
在过热器的爆管事故中,由干管内存在制造、安装或检修遗留物引起的事故也占相当的比例。
如长春热电二厂1号炉因管路堵塞造成短时超温爆管。
8.管材质量问题钢材质量差。
管子本身存在分层、夹渣等缺陷,运行时受温度和应力影响缺陷扩大而爆管。
由于管材本身的质量不合格造成的爆破事故不像前述几个问题那么普遍,但在运行中也确实存在。
9.错用钢材如靖远电厂4号炉的制造、维修过程中,应该用合金钢的高温过热器出口联箱管座错用碳钢,使碳钢管座长期过热爆破。
为此,在制造厂制造加工和电厂检修时应注意严格检查管材的质量,加以避免。
10.安装质量问题如扬州发电厂DG-670/140-8型固态排渣煤粉炉的包墙过热器未按照图纸要求施工,使管子排列、固定和膨胀间隙出现问题,从而导致爆管。
这类问题在机组试运行期间更为多见。
1.3调温装置设计不合理或不能正常工作为确保锅炉的安全、经济运行,除设计计算应力求准确外,汽温调节也是很重要的一环。
大容量电站锅炉的汽温调节方式较多,在实际运行中,由于调温装置原因带来的问题也较多,据有关部门调查,配200MW机组的锅炉80%以上的再热蒸汽调温装置不能正常使用。
1.减温水系统设计不合理某些锅炉在喷水减温系统设计中,往往用一只喷水调节阀来调节一级喷水的总量,然后将喷水分别左右两个回路。
这时,当左右侧的燃烧工况或汽温有较大偏差时,就无法用调整左右侧喷水量来平衡两侧的汽温。
2.喷水减温器容量不合适喷水式减温器一般设计喷水量约为锅炉额定蒸发量的3%~5%,但配200MW 机组的锅炉由于其汽温偏离设计值问题比较突出,许多电厂均发现喷水减温器容量不够。
如:邢台电厂、沙角A电厂和通辽电厂等都将原减温水管口放大,以满足调温需要;对再热蒸汽,由于大量喷水对机组运行的经济性影响较大,故设计时再热蒸汽的微量喷水一般都很小,或不用喷水。
然而,在实际运行中,因再热器超温,有些电厂不得不用加大喷水量来解决。
3.喷水减温器调节阀调节性能问题喷水减温器的喷水调节阀的调节性能也是影响减温系统调温效果的因素之一。
调研结果表明,许多国产阀门的调节性能比较差,且漏流严重,这在一定程度上影响了机组的可靠性和经济性。
4.减温器发生故障如巴陵石化公司动力厂5号炉,将减温器I级调节阀固定,用II级调节阀调节。
因起主调作用的I级减温器减温水投入少,冷却屏式过热器、高温过热器的效果差,增加过热器超温的可能。
5.再热器调节受热面所谓再热器调节受热面是指用改变通过的蒸汽量来改变再热蒸汽的吸热量,从而达到调节再热汽温的一种附加受热面。
苏制Efl670 / 140型锅炉的再热汽温的调节就是利用这一装置实现的。
但是由于运行时蒸汽的重量流速低于设计值,而锅炉负荷则高于设计值,因而马头电厂5, 6号炉都曾发生再热器调节受热面管子过热超温事故,后经减少调节受热面面积和流通截面积,才解决了过热问题。
6.挡板调温装置采用烟气挡板调温装置的锅炉再热蒸汽温度问题要好于采用汽——汽热交换器的锅炉。
挡板调温可改变烟气量的分配,较适合纯对流传热的再热蒸汽调温,但在烟气挡板的实际应用中也存在一些问题:(1)挡板开启不太灵活,有的电厂出现锈死现象;(2)再热器侧和过热器侧挡板开度较难匹配,挡板的最佳工作点也不易控制,运行人员操作不便,往往只要主蒸汽温度满足就不再调节。
有些电厂还反映用调节挡板时,汽温变化滞后较为严重。
7.烟气再循环烟气再循环是将省煤器后温度为250~350℃的一部分烟气,通过再循环风机送入炉膛,改变辐射受热面与对流受热面的吸热量比例,以调节汽温。
采用这种调温方式能够降低和均匀炉膛出口烟温,防止对流过热器结渣及减小热偏差,保护屏式过热器及高温对流过热器的安全。
一般在锅炉低负荷时,从炉膛下部送入,起调温作用;在高负荷时,从炉膛上部送入,起保护高温对流受热面的作用。
此外,还可利用烟气再循环降低炉膛的热负荷,防止管内沸腾传热恶化的发生,并能抑制烟气中NOx的形成,减轻对大气的污染。
但是,由于这种方式需要增加工作于高烟温的再循环风机,要消耗一定的能量,且因目前再循环风机的防腐和防磨问题远未得到解决,因而限制了烟气再循环的应用。
此外,采用烟气再循环后,对炉膛内烟气动力场及燃烧的影响究竟如何也有待于进一步研究。
因此,从原理上将烟气再循环是一种较理想的调温手段,对于大型电站锅炉的运行是十分有利的。
但因种种原因,实际运行时极少有电厂采用。
8.火焰中心的调节改变炉膛火焰中心位置可以增加或减少炉膛受热面的吸热量和改变炉膛出口烟气温度,因而可以调节过热器汽温和再热器汽温。
但要在运行中控制炉膛出口烟温,必须组织好炉内空气动力场,根据锅炉负荷和燃料的变化,合理选择燃烧器的运行方式。