4-117连铸过程工艺优化和技术改造
改进连铸中间包工艺技术减少异常铸坯产生

一、引言面对严峻的钢铁形势,邯钢把产品转型升级作为重大战略来抓,品种钢上量、产品结构升级和生产成本的压减是提升钢铁行业竞争力必不可少的一步。
邯宝公司炼钢厂肩负着公司80%品种钢的生产任务,尤其是汽车钢的增多,呈现异常铸坯封锁控制较多,成为压减成本、产品提档升级的限制环节。
为了减少连铸异常封锁铸坯,保证合同及时兑现,压减带出品量迫在眉睫。
而邯宝炼钢厂要想压减带出品量,除了提升成分命中率外,减少连铸异常坯控制是压减带出品量最为关键一环。
二、改进措施项目(一)通过改进中间包吹氩技术,减少连铸异常坯产生中间包吹氩主要包括板间吹氩、上水口吹氩和塞棒吹氩。
SEN 滑板间氩气流形成的环形密封,隔绝了钢流与空气中氧的接触;上水口吹氩使上水口内壁形成的氩气膜,防止钢水中的Al 2O 3夹杂在上水口附着;塞棒吹氩使氩气泡进入SEN 内部钢流,可调整水口内钢水的流动状态和流速,减少了Al 2O 3在水口内壁的聚集,避免水口堵塞造成塞棒上涨,减少了大型夹杂物的生成。
发明了中间包氩气调节直观控制技术,确保了中间包动态吹氩效果。
中间包塞棒和上水口吹氩的好坏直接影响到结晶器液面波动量的大小。
中包吹氩调节的影响因素较多,如钢水过热度、钢水纯净度、拉速变化、断面等。
原来仅给操作工提供一个氩气量调节范围,实践证明该方法可操作性差,液面波动控制仍不理想。
经现场多次实践跟踪,现发明了一种根据观察结晶器液面最佳的活动状态来调节氩气量。
最佳结晶器液面活动状态为:在SEN 水口两侧200~300mm 位置及结晶器窄边部位,对称地出现“鱼吐泡”似的氩气泡为好;参考塞棒氩气量控制在4.5~10L/min ,上水口氩气量控制在3~8L/min 。
通过开发中间包离线上水口透气性检测技术及吹氩技术的优化,不仅使得SEN 水口堵塞率显著下降,由原来的16.7%降低至8%,而且结晶器液面波动量不大于5mm 比例由93%提升至97%,大大减少了异常坯产生。
炼钢过程中的连铸技术改进与优化

炼钢过程中的连铸技术改进与优化随着现代工业的快速发展,钢铁行业在全球范围内扮演着重要的角色。
炼钢是制造钢材的关键过程之一,而连铸技术在炼钢过程中的应用越来越广泛。
本文将探讨炼钢过程中连铸技术的改进与优化措施,以提高钢材质量和生产效率。
一、连铸技术的基本原理与流程连铸技术是指将炼钢炉中液态钢水直接注入连铸机中,通过结晶器的作用,使其快速凝固为连续坯料。
基本上,连铸技术分为结晶器区、中间区和加热区三个部分。
结晶器区是最重要的部分,其作用是促使钢水迅速凝固形成坯料。
中间区则起到支撑坯料并保持其形状的作用,加热区则用来提供所需的坯料温度。
二、连铸技术改进的原因尽管连铸技术已经成为钢铁生产中主要的浇铸方法,但仍然存在一些问题和潜在的改进空间。
首先,连铸坯料的质量不稳定是一个重要问题。
由于熔铸过程中的各种因素,如温度、流速、结晶器形状等,坯料的结构和性能可能会出现变化。
这导致了产品的不均匀性和不稳定性。
其次,连铸过程中易产生气孔和夹杂物的问题也需要解决。
气孔和夹杂物对钢材的力学性能和外观质量有着显著影响。
此外,传统的连铸技术在能源消耗和生产效率方面也存在一些局限。
例如,冷却设备和传输系统的耗能较高,同时生产线上的工作效率较低。
因此,为了改进钢铁行业的连铸技术,提高生产效率和产品质量,钢铁企业已经采取了一系列的措施。
三、连铸技术改进与优化措施1. 结晶器改进结晶器是连铸技术中最关键的部分,对坯料质量起到决定性的作用。
通过改进结晶器的设计和材料,可以提高坯料的凝固性能和整体质量。
现代连铸技术使用先进的结晶器涂层和陶瓷材料,以减少坯料表面张力和增加热传导率。
此外,优化结晶器的几何形状和冷却系统,可以提高坯料的结晶行为和熔体流动性。
2. 连铸过程控制技术连铸过程中的温度、流速和加热条件等参数对坯料质量有着直接的影响。
通过引入先进的控制技术,如自动化控制系统和实时监测装置,可以实现对连铸过程的精细控制和优化。
自动化系统可以实时监测和调整炉温、浇注速度和结晶器温度等参数,以确保坯料的一致性和质量。
包钢连铸生产工艺与控制现状

生产效率与成本控制
总结词
生产效率与成本控制是包钢连铸生产中的重要经济指标,直接影响到企业的市场竞争力 和经济效益。
详细描述
切割过程中,需要采用高精度的切割设备,确保铸坯的尺寸精度和表面质量。入库时,需要按照不同的钢种和规 格进行分类存放,并进行质量检验和标识。此外,还需要对库存进行有效的管理,确保铸坯的质量和数量的可追 溯性。
03
包钢连铸生产工艺控制现 状
温度控制
总结词
温度控制是包钢连铸生产中的重要环节 ,直接影响到铸坯的质量和生产效率。
详细描述
钢包管理包括控制钢包的温度、清洁度和耐火材料的使用寿 命。为了确保连铸过程的稳定,需要定期检测和维修钢包, 并对其进行严格的质量控制。
浇注与凝固
总结词
浇注与凝固是包钢连铸过程中的核心环节,涉及到液态钢水转变为固态铸坯的过 程。
详细描述
浇注与凝固过程中,需要精确控制浇注速度、温度和冷却强度,以确保铸坯的凝 固组织和内部质量。此外,还需要根据不同的钢种和规格,选择合适的浇注工艺 和保护气氛。
支持和技术储备。
感谢您的观看
THANKS
拉坯矫直
总结词
拉坯矫直是连铸过程中对铸坯进行初 步加工的环节,目的是消除铸坯的弯 曲和扭曲。
详细描述
拉坯矫直包括通过拉坯机对铸坯进行拉 伸,并在需要时进行矫直。这一过程需 要精确控制拉坯速度和矫直压力,以确 保铸坯的尺寸精度和表面质量。
解决连铸工艺难题提高产品质量
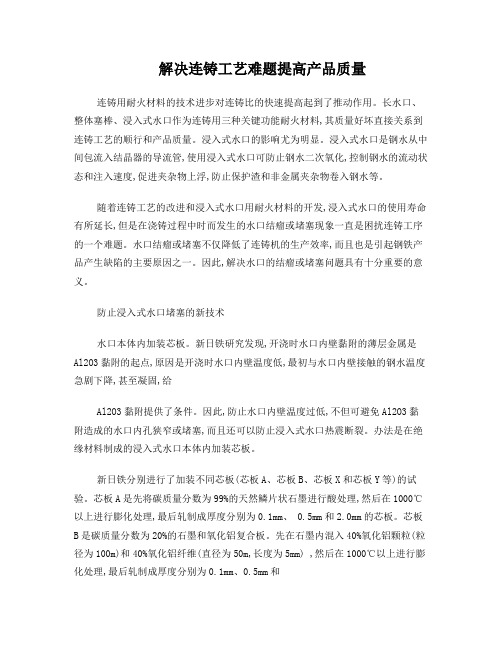
解决连铸工艺难题提高产品质量连铸用耐火材料的技术进步对连铸比的快速提高起到了推动作用。
长水口、整体塞棒、浸入式水口作为连铸用三种关键功能耐火材料,其质量好坏直接关系到连铸工艺的顺行和产品质量。
浸入式水口的影响尤为明显。
浸入式水口是钢水从中间包流入结晶器的导流管,使用浸入式水口可防止钢水二次氧化,控制钢水的流动状态和注入速度,促进夹杂物上浮,防止保护渣和非金属夹杂物卷入钢水等。
随着连铸工艺的改进和浸入式水口用耐火材料的开发,浸入式水口的使用寿命有所延长,但是在浇铸过程中时而发生的水口结瘤或堵塞现象一直是困扰连铸工序的一个难题。
水口结瘤或堵塞不仅降低了连铸机的生产效率,而且也是引起钢铁产品产生缺陷的主要原因之一。
因此,解决水口的结瘤或堵塞问题具有十分重要的意义。
防止浸入式水口堵塞的新技术水口本体内加装芯板。
新日铁研究发现,开浇时水口内壁黏附的薄层金属是Al2O3黏附的起点,原因是开浇时水口内壁温度低,最初与水口内壁接触的钢水温度急剧下降,甚至凝固,给Al2O3黏附提供了条件。
因此,防止水口内壁温度过低,不但可避免Al2O3黏附造成的水口内孔狭窄或堵塞,而且还可以防止浸入式水口热震断裂。
办法是在绝缘材料制成的浸入式水口本体内加装芯板。
新日铁分别进行了加装不同芯板(芯板A、芯板B、芯板X和芯板Y等)的试验。
芯板A是先将碳质量分数为99%的天然鳞片状石墨进行酸处理,然后在1000℃以上进行膨化处理,最后轧制成厚度分别为0.1mm、 0.5mm和2.0mm的芯板。
芯板B是碳质量分数为20%的石墨和氧化铝复合板。
先在石墨内混入40%氧化铝颗粒(粒径为100m)和40%氧化铝纤维(直径为50m,长度为5mm) ,然后在1000℃以上进行膨化处理,最后轧制成厚度分别为0.1mm、0.5mm和2.0mm的芯板。
将芯板A和B用高耐热绝缘陶瓷板包裹后,分别装入浸入式水口本体内。
浇铸之前,将芯板A或B通电加热,提高水口内壁温度,从而避免因钢水接触水口内壁,温度急剧下降而凝固,引起Al2O3黏附的现象,还可以防止浇铸初期的水口热震断裂。
连铸工艺流程

连铸工艺流程
《连铸工艺流程》
连铸工艺是一种现代金属材料生产工艺,它利用连续铸造设备,将熔化的金属直接连续铸造成坯料或板材,省去了传统铸造工艺中的铸型、浇注、凝固和脱模等环节,大大提高了生产效率和质量。
具体来说,连铸工艺流程包括以下几个关键步骤:
1. 熔炼:将原料金属经过熔炼炉的高温熔化,形成熔融金属。
2. 连铸机:熔融金属通过连铸机器,经过喷水冷却,以得到坯料或板材。
连铸机在正常情况下可连续工作数周甚至数月。
3. 切割:将冷却后的坯料或板材进行切割成所需长度。
4. 表面处理:对坯料或板材进行表面处理,以去除氧化层、锈蚀和杂质,得到光洁的表面。
5. 加工:对坯料或板材进行进一步的热处理、冷加工等工艺,以获得所需的最终产品。
连铸工艺流程的优点在于,它能够大幅提高金属材料的生产效率,减少人工干预,降低能源消耗,减少生产废料,提高产品质量和一致性。
因此,在诸如钢铁、铝合金等金属材料的生产中,连铸工艺已成为重要的生产方式。
总的来说,《连铸工艺流程》的不断改进和创新,将为金属材料生产带来更高效、更绿色、更经济的生产方式,对于促进工业制造业的可持续发展具有重要的意义。
连铸轻压下工艺优化与实践

连铸轻压下工艺优化与实践杨文清,陈迪庆,白静,潘金保(武钢股份条材总厂,武汉,430083)摘要:本文介绍了轻压下对改善铸坯中心偏析和中心疏松的作用,通过对液芯长度计算,确定压下位置,进行多次试验,并对试验结果进行分析对比,选择最适合的压下方式。
关键字:轻压下;中心偏析;中心疏松1 前言连铸钢水在冷凝过程中,低熔点的物质被推向铸坯中心部位,形成了C、S、P、Mn 等元素的偏析带,该偏析带在液相穴终端存在于底部,形成了中心偏析和中心疏松缺陷。
轻压下技术是连铸坯拉矫时,对带液芯的铸坯施加小的压力的工艺方法。
即在铸坯凝固终端附近,对铸坯施加一定的压下量,使铸坯凝固终端形成的液相穴被破坏,以打断枝晶搭桥。
轻压下工艺能够改善中心偏析和中心疏松,但如果工艺不当,会产生压下裂纹,严重影响连铸坯质量。
武钢条材总厂一炼钢分厂(以下简称“一炼钢”)1#连铸机主要生产高碳钢。
对高碳钢来说,由于碳含量较高造成导热性差、凝固区间大,连铸坯本身容易产生偏析、疏松和缩孔等缺陷,在拉丝和扭转过程中容易引起断裂 [1] 。
受铸机断面大小等条件的制约,铸坯中心碳偏析一直是一炼钢控制难点。
该厂通过对拉矫机设备进行改造,使设备具备更大压下功能,并通过计算液芯长度,调整压下方式,找出最适合的压下量及压下方式。
2 浇注工艺现状一炼钢1#连铸机是五机五流弧形连铸机,主要生产高碳钢,铸机主要工艺参数见下表:目前,高碳钢轻压下压下量为 9mm,从低倍检验看,铸坯存在一定程度中心疏松,铸坯中心碳偏析也一直徘徊在 1.15 左右,与其他炼钢厂相比有很大差距,难以满足日益增长的客户需求。
3 凝固末端计算对高碳钢发生纵裂漏钢的坯壳进行分析,将漏钢坯壳横向切开,测量切开点的坯壳厚度,根据坯壳厚度计算凝固系数,漏钢时浇注工艺如下:漏钢坯壳示意图如下:坯壳厚度测量结果及凝固系数计算如下:注:凝固系数:K=D*(V/L) 1/2 D 为凝固坯壳厚度,V 为拉速,L 为到液面距离取两点的平均凝固系数作为综合凝固系数K,则可计算出液芯长度 L。
连铸坯热装热送攻关方案的工艺改进与优化方案

连铸坯热装热送攻关方案的工艺改进与优化方案近年来,连铸坯热装热送技术在钢铁行业中得到了广泛应用。
然而,由于原有的工艺存在一些问题,如产能低、能耗高等,需要进行进一步的工艺改进与优化。
本文将对连铸坯热装热送攻关方案的工艺改进与优化方案进行探讨。
一、工艺改进方案1. 提高炉冶炼效率为了提高连铸坯热装热送的生产效率,可以从炉冶炼环节入手进行工艺改进。
首先,优化炉冶炼条件,确保炉温、氧含量等参数控制在合适的范围内。
其次,选择适当的冶炼配方,减少次级铁水的含量,提高炉内熔化效率。
最后,加强对炉料的预热处理,提高能源利用率。
2. 优化连铸工艺连铸工艺是影响连铸坯热装热送效率的关键因素之一。
为了提高连铸坯的质量和产能,可以采取以下工艺改进方案:(1) 提高结晶器的冷却效果,降低结晶器温度,防止结晶器冷却水温度过高导致坯料表面温度不均匀。
(2) 优化拉矫连铸工艺,提高拉伸速度,降低结晶器出铸温度。
(3) 引进先进的连铸技术,例如双流连铸、弯曲连铸等,提高连铸坯的成形质量。
3. 建立坯料热装热送过程的模型通过建立连铸坯热装热送过程的模型,可以更好地掌握各工艺参数对坯料质量的影响,并优化相关工艺。
模型可以包括温度分布、温度控制、传热过程等,通过合理的模拟和优化,实现连铸坯质量和产能的提升。
二、优化方案1. 提高设备的自动化水平在连铸坯热装热送过程中,设备的自动化水平直接影响生产效率和产品质量。
通过提高设备自动控制系统的精度和可靠性,实现对温度、流量、压力等参数的实时监测和调节。
此外,引入智能化的技术手段,如人工智能、大数据分析等,对生产过程进行实时优化和预测,提高连铸坯热装热送的整体运行效率。
2. 强化质量管理质量管理是确保连铸坯热装热送产品质量的重要环节。
通过建立完善的质量管理体系,严格控制每个环节的工艺参数,加强对设备的维护和保养,及时发现和解决生产中出现的问题,确保连铸坯热装热送产品的一致性和稳定性。
3. 节约能源、降低排放连铸坯热装热送过程中,能源消耗和环境污染是亟待解决的问题。
连铸坯热装热送攻关方案的工艺创新与效果评估

连铸坯热装热送攻关方案的工艺创新与效果评估随着工业发展的推进,连铸坯的生产对于钢铁行业至关重要。
连铸坯热装热送是一种高效、低能耗的工艺方式,对于提高生产效率和节约能源具有重要意义。
本文将探讨连铸坯热装热送攻关方案的工艺创新及其效果评估。
一、工艺创新连铸坯热装热送的工艺创新主要包括以下几个方面:1. 采用先进的连铸技术传统的连铸技术存在能源浪费、坯料质量不稳定等问题。
为此,采用先进的连铸技术是提高连铸坯质量和生产效率的关键。
例如,采用微量合金、超细晶、超声波去气等技术手段,可以提高连铸坯的纯净度和坯面质量。
2. 优化装热设备连铸坯热装热送过程中,装热设备的优化对于提高工艺效果至关重要。
通过改进加热炉的结构和燃烧装置,增加加热面积和改善温度分布均匀性,可以提高装热效率和坯料的热均匀性。
3. 优化热送工艺连铸坯热送工艺中,通过优化热送方式,可以实现能源的有效利用和生产效率的提高。
例如,采用高效热送工具,控制热送速度和温度,避免能量的散失和过热等问题,可以有效提高坯料的温度和质量稳定性。
二、效果评估连铸坯热装热送攻关方案的工艺创新带来了许多显著的效果。
1. 提高坯料质量工艺创新可以提高连铸坯的纯净度、结晶度和坯面质量,减少坯料表面缺陷和内部夹杂物的数量。
同时,通过优化装热设备和热送工艺,坯料的温度和质量稳定性得到有效控制,提高了坯料的整体质量。
2. 提高生产效率优化装热设备和热送工艺可以提高装热效率和热均匀性,减少了能源消耗。
同时,采用先进的连铸技术可以提高连铸坯的产出率和坯料利用率,增加了生产效益。
3. 降低能耗采用工艺创新的连铸坯热装热送方案可降低能源消耗,实现节能减排。
通过优化装热设备和热送工艺,减少了能量的散失和过热现象,提高了能源的利用效率,减少了能源资源的浪费。
4. 减少环境污染连铸坯热装热送方案的工艺创新减少了产生废气和废水的数量,降低了环境污染。
通过采用微量合金和超声波去气等技术手段,减少了废气中的有害物质排放,保护了环境的安全和健康。
连铸质量保障措施

连铸质量保障措施连铸质量保障措施引言:连铸是现代钢铁工业中重要的生产工艺,它能够高效地将熔化的钢水通过连续浇注,快速形成连续的铸坯。
然而,连铸过程中存在着各种各样的问题,如铸坯表面缺陷、内部结构不均匀等,这些问题会直接影响到最终的产品质量。
因此,为了保证连铸的质量,需要采取一系列的保障措施。
一、钢水质量控制钢水是连铸的原料,其质量直接关系到最终产品的质量。
因此,需要严格控制钢水的质量。
首先,在钢水的炼制过程中加入合适的合金元素,调整钢水的成分,保证其合金元素含量符合要求。
其次,要控制钢水的温度,以确保其在连铸过程中能够适当地流动和凝固。
最后,还需要对钢水进行连铸前的化学分析,判断其质量是否符合要求。
二、连铸机的控制系统连铸机是进行连铸的关键设备,其控制系统的稳定性和准确性对于连铸质量的保障至关重要。
为了保证连铸机的正常运行,需要采取一系列的措施。
首先,连铸机的控制系统需要精确地控制钢水的流量和速度,以确保连铸坯的形状和尺寸符合要求。
其次,需要及时检测和调整连铸机的温度,使其保持在适宜的范围内。
此外,还需要对连铸机的压力、振动等工艺参数进行监控,及时发现和解决问题。
三、结晶器的设计和改进结晶器是连铸过程中钢水凝固的关键部位,其设计和改进直接影响到连铸质量。
为了提高连铸的质量,需要采取以下的措施。
首先,结晶器的几何形状需要合理设计,以确保钢水在结晶器内的流动和凝固过程稳定和均匀。
其次,需要对结晶器进行定期的清理和维护,以保证其表面的光滑和无污染,减少对连铸坯表面缺陷的影响。
另外,还可以通过改变结晶器的冷却方式和参数,来控制钢水的凝固速率和晶粒尺寸,进一步提高连铸的质量。
四、连铸坯的在线检测和质量控制在连铸过程中,需要对连铸坯的质量进行在线检测和控制,以及时发现和解决问题。
首先,可以通过超声波检测仪器,对连铸坯进行超声波探伤,判断其内部是否存在缺陷和杂质。
其次,可以利用热像仪等仪器,对连铸坯的温度分布进行监控,以及时发现凝固不均匀等问题。
连铸机铸流控制系统升级及功能优化的方法

连铸机铸流控制系统升级及功能优化的方法苏钢1#连铸机铸流PLC控制系统采用德国西门子公司生产的S5系列产品,经过十几年的运行,设备趋于老化。
随着S5系统逐渐被淘汰,大多CPU和信号模块已经不再生产,不可避免地遇到了备件价格昂贵、供货时间长、维修成本高等问题,为此公司决定于2015年5月对该连铸机铸流PLC系统进行升级改造。
标签:S7控制系统;电动调节阀;变频器1 概述1#连铸机铸流控制系统中,主站原采用双机架结构:主机架由S5 CPU 928、CP143通讯模块、WF706计数模块、4块AI 466模拟量输入模块、3块AO 470模拟量输出模块、7块DI 430数字量输入模块、以及EG300扩展模块构成;扩展机架由4块DO 451数字量输出模块、3块DO 454数字量输出模块、以及ZG-AS 312扩展模块构成。
升级改造后的新硬件系统,主机架由S7 CPU 416、CP443通讯模块、FM450计数模块、4块A0 431模拟量输出模块、7块DI 421数字量输入模块、以及IM460扩展模块构成;扩展机架由4块DO 422数字量输出模块、2块AI 432模拟量输入模块、以及IM461扩展模块构成。
现上位机采用Wincc 监控软件,上位机与PLC之间通过以太网进行通讯。
2 系统中一些主要的功能优化2.1 二次冷却水控制调节阀优化连铸热坯采用气水雾化冷却,这种冷却方式,需要对冷却水的流量进行精确调节。
原S5系统采用萨姆森电液调节阀结合ABB电磁流量计实现闭环控制。
基本工作原理是:ABB电磁流量计测量实际水流量,S5程序中将实际流量与目标流量进行比较,若在死区范围外,则根据实际流量是大于或是小于目标值,输出关闭或是打开的脉冲信号给中间继电器,从而再控制调节阀的动作,直至实际流量值进入死区范围内。
但是使用经验证明,此套调节系统存在以下这些问题:控制设备都是进口产品,且连铸二冷区共有45套,维护更换成本高;控制存在死区,精度不高;存在中间继电器,线路较多,增多了故障点;缺少现场手动功能,紧急情况只能通过程序中手动模式控制动作。
连铸高效化生产中的水系统改造

连铸高效化生产中的水系统改造引言在连铸过程中,水系统是关键的组成部分,直接关系到连铸生产的效率和质量。
然而,随着生产工艺的不断发展和技术的进步,传统的水系统往往无法满足连铸高效化生产的要求。
因此,对水系统进行改造和优化是非常必要的。
本文将针对连铸高效化生产中的水系统进行改造,提出一些改进的措施和建议,并阐述改造后水系统所带来的优势和效益。
1. 分析现有水系统存在的问题在连铸过程中,水系统常常面临以下问题:1.流量不均衡:传统水系统中,水流的分配往往不均匀,导致部分区域出现冷却不足或过度冷却的情况,影响连铸质量。
2.能耗高:传统水系统中,水的供应和循环需要大量的能源支持,造成能耗较高。
3.操作繁琐:传统水系统的操作复杂,需要人工介入调整,维护工作量大。
4.水质难保证:连铸过程对水质有较高的要求,传统水系统无法保证水质的稳定性和可靠性。
2. 水系统改造的措施和建议为了解决现有水系统存在的问题,以下是针对连铸高效化生产的水系统改造的一些建议和措施:2.1. 优化水流分配通过分析连铸过程中的温度分布和冷却需求,采取合理的水流分配方案。
可以借助流体模拟软件进行模拟计算,以确保水的均匀分配,并减少冷却死区的产生。
2.2. 引入智能控制系统引入智能控制系统,对水系统的供水和循环进行自动控制,实时监测温度和流量等参数,自动调整水流量和水温,提高水系统工作效率,并减少能耗和操作人工。
2.3. 采用节能型设备选用高效节能的水泵和水循环设备,降低能耗,提高连铸生产的能源利用效率。
2.4. 强化水质控制引入水质监测装置,实时监测水质指标,通过逆渗透、过滤等技术手段对水质进行处理,保证水质的稳定性和可靠性。
同时,定期进行水质检测和维护工作,保证水系统的正常运行。
2.5. 加强维护管理建立完善的水系统维护管理制度,制定操作规范和维护计划,定期进行设备检修和清洗,保证水系统的运行稳定性和可靠性。
3. 改造后水系统的优势和效益通过对连铸高效化生产中的水系统进行改造和优化,可以实现以下优势和效益:1.提高连铸质量:优化的水流分配和水温控制,保证了连铸过程中的均匀冷却,提高连铸板坯的质量和表面光洁度。
连铸改造完成情况汇报

连铸改造完成情况汇报尊敬的领导:我向您汇报连铸改造完成情况如下:一、项目背景。
公司连铸设备已运行多年,存在一定的老化和磨损,为提高生产效率和产品质量,公司决定进行连铸改造项目。
二、改造内容。
1. 设备更新,更换老化设备,引进先进的连铸设备,提高生产效率和产品质量。
2. 工艺优化,优化连铸工艺,提高产品成形率,减少废品率。
3. 自动化控制,引入自动化控制系统,提高生产线的智能化水平,减少人为操作对产品质量的影响。
三、改造进展。
1. 设备更新,目前已完成设备更新的采购工作,新设备已陆续到货并开始安装调试。
2. 工艺优化,优化工艺方案已经制定完成,正在进行试验验证,初步效果良好。
3. 自动化控制,自动化控制系统已经完成采购和安装,正在进行联调测试,预计很快可以投入使用。
四、改造效果。
1. 设备更新,新设备的安装调试工作进展顺利,预计可以在规定时间内完成,提高了生产线的稳定性和可靠性。
2. 工艺优化,优化后的工艺方案有效提高了产品成形率,减少了废品率,产品质量得到了明显提升。
3. 自动化控制,自动化控制系统的引入大大减少了人为操作,提高了生产线的智能化水平,降低了人力成本,提高了生产效率。
五、下一步工作。
1. 完成设备更新的安装调试工作,确保新设备的正常运行。
2. 进一步优化工艺方案,提高产品质量和生产效率。
3. 完成自动化控制系统的联调测试,确保系统稳定可靠,投入正常生产使用。
六、结语。
连铸改造项目是公司生产线升级的重要举措,经过各部门的通力合作,项目进展顺利,效果显著。
我们将继续努力,确保项目顺利完成,为公司的发展贡献力量。
谢谢!。
连铸改造完成情况汇报

连铸改造完成情况汇报尊敬的领导:根据公司安排,我对连铸改造项目的完成情况进行了汇报。
自项目启动以来,我们团队克服了种种困难,取得了一定的成绩,现将具体情况如实汇报如下:首先,项目启动阶段我们进行了充分的前期调研和准备工作,明确了改造目标和方向。
我们对设备进行了全面的评估和分析,制定了详细的改造方案,并与相关部门进行了充分的沟通和协调。
在这一阶段,我们的工作重点是明确目标、规划路线、准备资源,确保项目能够顺利进行。
接着,我们开始了设备改造和升级工作。
我们对连铸设备进行了全面的检修和更新,更新了部分老化设备,并增加了一些先进的控制系统和技术装备。
在这一阶段,我们的工作重点是确保设备的安全稳定运行,提高生产效率,提升产品质量。
随后,我们进行了设备调试和试生产阶段。
我们对改造后的设备进行了严格的调试和测试,确保设备的各项指标符合要求,同时进行了小范围的试生产,验证了设备改造的效果。
在这一阶段,我们的工作重点是保证设备的稳定性和可靠性,为正式投产做好准备。
最后,我们顺利完成了连铸改造项目的投产和生产。
经过前期的准备工作和设备改造升级,我们顺利实现了设备的正式投产,生产效率得到了明显提升,产品质量得到了有效保障。
在这一阶段,我们的工作重点是保证生产的稳定性和连续性,确保项目的长期效益。
总体而言,连铸改造项目的完成情况较为理想。
我们克服了诸多困难,取得了一定的成绩。
但同时也存在着一些不足和问题,比如改造过程中出现了一些技术难题和设备故障,需要进一步完善和改进。
我们将继续努力,不断提升设备的稳定性和生产效率,为公司的发展贡献更大的力量。
感谢领导对我们工作的支持和关怀,我们将以更加饱满的热情和更加务实的作风,不断提高自身的素质和能力,为公司的发展做出更大的贡献。
谨此汇报。
此致。
敬礼。
连铸工艺流程介绍

连铸工艺流程介绍第一篇:连铸工艺流程介绍连铸工艺流程介绍(2010-09-11 15:38:59)标签:分类:我的大学和静中间包结晶器钢水铸坯【导读】:转炉生产出来的钢水经过精炼炉精炼以后,需要将钢水铸造成不同类型、不同规格的钢坯。
连铸工段就是将精炼后的钢水连续铸造成钢坯的生产工序,主要设备包括回转台、中间包,结晶器、拉矫机等。
本专题将详细介绍转炉(以及电炉)炼钢生产的工艺流程,主要工艺设备的工作原理以及控制要求等信息。
由于时间的仓促和编辑水平有限,专题中难免出现遗漏或错误的地方,欢迎大家补充指正。
连铸的目的: 将钢水铸造成钢坯。
将装有精炼好钢水的钢包运至回转台,回转台转动到浇注位置后,将钢水注入中间包,中间包再由水口将钢水分配到各个结晶器中去。
结晶器是连铸机的核心设备之一,它使铸件成形并迅速凝固结晶。
拉矫机与结晶振动装置共同作用,将结晶器内的铸件拉出,经冷却、电磁搅拌后,切割成一定长度的板坯。
{连铸工艺详解连铸的生产工艺流程:将装有精炼好钢水的钢包运至回转台,回转台转动到浇注位置后,将钢水注入中间包,中间包再由水口将钢水分配到各个结晶器中去。
结晶器是连铸机的核心设备之一,它使铸件成形并迅速凝固结晶。
拉矫机与结晶振动装置共同作用,将结晶器内的铸件拉出,经冷却、电磁搅拌后,切割成一定长度的板坯。
连铸钢水的准备一、连铸钢水的温度要求:钢水温度过高的危害:①出结晶器坯壳薄,容易漏钢;②耐火材料侵蚀加快,易导致铸流失控,降低浇铸安全性;③增加非金属夹杂,影响板坯内在质量;④铸坯柱状晶发达;⑤中心偏析加重,易产生中心线裂纹。
钢水温度过低的危害:①容易发生水口堵塞,浇铸中断;②连铸表面容易产生结疱、夹渣、裂纹等缺陷;③非金属夹杂不易上浮,影响铸坯内在质量。
二、钢水在钢包中的温度控制:根据冶炼钢种严格控制出钢温度,使其在较窄的范围内变化;其次,要最大限度地减少从出钢、钢包中、钢包运送途中及进入中间包的整个过程中的温降。
连铸全保护浇注工艺优化的工业实践

连铸全保护浇注工艺优化的工业实践发布时间:2022-02-17T08:36:56.438Z 来源:《防护工程》2021年29期作者:包春海[导读] 近些年,随着行业对深冲板品质的要求不断提高,对钢中成分以及夹杂物的要求也越来越严。
北营钢铁(集团)股份有限公司辽宁省本溪市 117000摘要:随着经济的发展,钢铁冶炼技术在不断创新,钢铁连铸产量提升速度加快,增加技术含量。
提升连铸机的智能化水平,有助于降低生产工人劳动强度,提升产品质量,对于钢铁企业实施连铸生产线智能化建设提供了参考。
汽车用钢是卷板质量要求较高的钢种类型之一,钢中的夹杂物往往是导致产品降级和报废的主要原因,铸坯中70%的氧化物夹杂来源于连铸过程中的钢液二次氧化。
结合现场连铸生产实际,围绕连铸全保护浇注技术展开了系列研究,不断完善优化连铸全保护浇注工艺,减少汽车钢中的夹杂物降级比例,取得了显著效果,经济效益明显提升。
关键词:连铸全保护;浇注工艺;优化引言近些年,随着行业对深冲板品质的要求不断提高,对钢中成分以及夹杂物的要求也越来越严。
洁净钢冶炼技术得到了迅速发展,钢水中的杂质元素含量已能降至很低水平,在此背景下,洁净化连铸技术已演变为洁净钢生产平台的一项非常重要、不可或缺的支撑技术。
连铸过程的二次氧化已然成为高品质钢生产的关键限制性环节。
为更好地体现洁净钢冶炼平台和连铸工艺的优越性,无氧化浇注技术的开发和应用已成为现代连铸技术的重要内容之一。
1铸机保护浇注现状中间包铝损和铝比反映了钢水在浇注过程中的纯净度。
中间包铝损和铝比越低,意味着钢水在浇注过程中受到二次氧化的概率越低,表明铸机保护浇注效果越好。
铸机中间包铝损和铝比超出范围的不合格炉次较多,数据中心线未呈现标准的正态分布,而是整体发生了偏移。
中间包铝损和铝比不合格炉数分别为22炉和65炉,合格率分别为96.8%和90.8%,且中间包铝损低的炉次中间包铝比普遍低,这在铸机开浇的第一炉尤其明显。
连铸坯热装热送攻关方案的工艺改进与效果验证

连铸坯热装热送攻关方案的工艺改进与效果验证随着钢铁行业的不断发展,连铸技术在钢铁生产中扮演着重要的角色。
连铸坯热装热送是一项关键的工艺环节,其质量直接关系到后续工艺的稳定进行。
本文将针对连铸坯热装热送的工艺进行改进,并对改进后的工艺进行效果验证。
一、工艺改进在传统的连铸坯热装热送工艺中,存在一些问题,如温度控制不准确、能耗高等。
为了解决这些问题,我们提出了以下改进措施:1. 温度控制优化:通过引入先进的温度控制系统,实时监测和调节连铸坯的温度,确保其在合理范围内。
同时,结合数据分析和模型预测等技术,优化温度控制参数,提高温度控制的准确性和稳定性。
2. 能源利用改进:采用余热回收和能量循环利用等措施,减少能源的浪费和排放,提高能源利用效率。
同时,优化传热系统,降低传热损失,进一步降低能耗。
3. 工艺流程优化:通过改善连铸坯热装热送的工艺流程,减少工艺中的倒炉次数和工序,缩短生产周期,提高生产效率。
同时,合理设计连铸坯的尺寸和形状,减少废品率,提高产品质量。
二、效果验证为了验证改进后的连铸坯热装热送工艺的效果,我们进行了一系列实验和现场应用。
首先,我们在实验室中搭建了连铸坯热装热送的小型试验台。
通过在不同工艺参数下进行试验,测量和分析连铸坯的温度变化和质量指标,验证了改进工艺的优势。
实验结果显示,改进后的工艺可以在更短的时间内实现连铸坯的热装热送,且温度控制更加准确,质量指标达到了预期要求。
随后,我们将改进后的工艺应用到实际生产中的连铸坯热装热送过程中。
通过与传统工艺进行对比,我们对比分析了工艺改进前后的能耗、生产效率和产品质量等方面的差异。
实际应用结果表明,改进后的工艺在降低能耗、提高生产效率和产品质量等方面均取得了显著的改善。
三、总结通过对连铸坯热装热送工艺的改进和效果验证,我们成功地解决了传统工艺中存在的问题,提高了连铸坯热装热送的温度控制精度、能耗利用效率和生产效率。
改进后的工艺在实际生产中取得了良好的效果,具有较高的推广应用价值。
炼钢厂连铸机优化提速改造

炼钢厂连铸机优化提速改造发布时间:2022-02-25T09:46:34.872Z 来源:《中国科技信息》2021年11月中32期作者:袁志权张爱爽陈庆国[导读] 针对炼钢一厂方坯连铸机由于设备性能老化,设计能力制约分厂进一步提升产能及产品质量的目标,通过对拉矫机、自动液面控制系统、振动台、引锭杆、切割系统、二冷区配水等关键设备进行升级改造,是的拉速得到了明显的提高,产品质量也得到了有效保证,本文论述了改造的具体过程及调试方法。
江苏永钢集团有限公司袁志权张爱爽陈庆国摘要:针对炼钢一厂方坯连铸机由于设备性能老化,设计能力制约分厂进一步提升产能及产品质量的目标,通过对拉矫机、自动液面控制系统、振动台、引锭杆、切割系统、二冷区配水等关键设备进行升级改造,是的拉速得到了明显的提高,产品质量也得到了有效保证,本文论述了改造的具体过程及调试方法。
关键字:连铸机;关键设备;调试方法1引言炼钢一厂从2003年建成投产至今,已经经历了17个年头,由于原始设备设计能力有限逐步凸显出生产能力达不到预期要求的矛盾,2018年产量目标290万吨截止到1-11月份实际完成230.67万吨,与目标238.86万吨相比欠产8.18万吨,在目前三台6米弧连铸机不更新改造的情况下,连铸机拉速较慢是产能提升的瓶颈。
目前1#-3#连铸机拉速160方超过2.79m/min、150方超过3.11m/min就会增加铸坯脱方、漏钢风险。
由于弧半径小、二冷区冷却距离短,拉速快钢坯液芯长,火切后容易导致钢坯芯部冒钢水或出现大缩孔现象,且现阶段拉矫机、火焰切割机已使用多年,不能满足拉速提升后的工况要求,设备问题也是制约拉速提升的一方面原因。
另外连铸机结晶器液面自动控制系统由于投用年份较早,存在射源发射方向是朝向操作人员不符合职业健康要求、自动液面控制故障率较高、日常维护成本高等缺陷急需整改。
2连铸机提速改造总体方案设计连铸机电气部分提速改造主要从以下几个方面入手1.自动液面控制系统改造、2.拉矫机和引锭杆更换、3.切割系统改造、4.红外定尺装置优化、5.冷却系统优化改造、6.振动参数改造。
连铸改造项目保障措施

连铸改造项目保障措施随着钢铁生产的不断发展,传统的手工铸造方式已经无法满足工业生产的需求。
现代钢铁生产采用的是连铸技术,它可以高效、稳定地生产出高质量的钢材。
但是在连铸生产中,会出现一些问题,比如冷却不均匀、结晶不完全等,这些问题都会影响钢材的质量。
因此,为了保证连铸生产的质量和效率,需要对连铸设备进行改造和优化。
本文将介绍一些连铸改造项目保障措施,以帮助企业提高钢铁生产的效率和质量。
##1. 设备改造和优化连铸生产需要大量设备的协作,使得设备运行效率和质量十分重要。
设备改造和优化可以大大提高生产效率和质量。
具体改造和优化的措施如下:###1.1 加强设备维护设备维护是重要的环节,因为连铸设备存在较多的机械部分和液压部分,它们需要经常维护和检修,以保证设备的正常运行。
并且连铸生产需要不间断地运行,一旦设备发生故障,可能导致生产线暂停,影响生产效率。
因此,对设备的维护和保养非常重要。
###1.2 采用先进设备连铸生产需要大量使用高科技设备,比如热控系统、连铸机、结晶器等。
企业需要购买先进的设备,以提高生产效率和质量。
先进的设备能够更好地控制钢材的质量,避免出现问题。
###1.3 优化设备参数在连铸生产中,需要对设备进行优化,以提高生产效率和质量。
比如对流量、温度、压力等参数进行优化,以保证钢坯的均匀冷却,避免出现冷却不均匀的问题。
同时,还需要调节结晶器、连铸板等设备的参数,使得钢材的结晶更加完全,从而提高钢材的质量。
##2. 人员培训和管理连铸生产需要大量技能熟练的操作人员,同时也需要经验丰富的管理人员来保证生产的高效和质量。
因此,人员培训和管理是重要的保障措施。
###2.1 建立培训制度培训制度是钢铁企业为员工提升技能和知识的重要方式。
企业可以通过工程师指导、培训课程、技能竞赛等方式对员工进行培训,以提高员工的技能和知识水平。
通过培训,员工可以更好地掌握设备的操作和维护技能,从而提高生产效率和质量。
- 1、下载文档前请自行甄别文档内容的完整性,平台不提供额外的编辑、内容补充、找答案等附加服务。
- 2、"仅部分预览"的文档,不可在线预览部分如存在完整性等问题,可反馈申请退款(可完整预览的文档不适用该条件!)。
- 3、如文档侵犯您的权益,请联系客服反馈,我们会尽快为您处理(人工客服工作时间:9:00-18:30)。
连铸过程工艺优化和技术改造底根顺王宏斌翟永臻李家征门志刚王建忠(宣化钢铁公司炼钢厂,宣化075100)摘要本文介绍了宣钢炼钢厂通过对连铸机中间包流场、结晶器、二冷配水等重要工序单元进行技术改造和工艺优化,提高了铸坯质量,为开发生产品种钢提供了保证。
关键词连铸机中间包流场二冷配水结晶器电磁搅拌T echnological Optimization and Technical Innovation in Process ofContinuous CastingDi Genshun Wang Hongbin Zhai Yongzhen Li Jiazheng Men Zhigang Whang Jianzhong(Xuanhua I&S Group Co.,Ltd.,Xuanhua, 075100)Abstract This paper specifies the technical innovation and technological optimization in some important working step units, which include flow field of tundish, mold and secondary cooling water distribution etc. As the result, the quality of casting blanks have become better, which can make sure the developing and producing of new steel products.Key words continuous casting, flow field of tundish, secondary cooling water distribution, mold electromagnetic stirring1 引言宣钢炼钢厂两座公称容量为80吨的顶底复吹转炉、一座90吨LF钢包精炼炉、两台R8m的方坯连铸机于2002年5月投产,以生产普碳钢和低合金钢为主。
2004年调整产品结构,全面优化工艺及装备,12月建成单喷颗粒镁铁水脱硫站一座,以满足新开发钢种硫含量的需要。
2006年为了提高产能,同时进一步提高钢坯质量,将转炉进行了扩容改造,对LF炉进行技术改造及工艺优化;将两台六机六流连铸机扩容为国内第一家一个中包配置八流的连铸机,同时对中包流场和二冷配水进行了优化,将普通结晶器改为电磁搅拌结晶器。
连铸系统经过一系列的工艺优化及设备改造,现已经能够生产焊丝钢、高牌号优质碳素结构钢、合金结构钢、预应力钢、冷镦钢等50多个钢种,为宣钢市场定位从产品单一向多元化方向发展奠定了基础。
2 中间包优化改造中间包内研究的现象主要是内部的钢液流动、平均停留时间、注流湍流动能的研究、夹杂物上浮、成分的混合和组分的转变、钢液的传热和涡旋的产生等。
通过对这些现象的研究,可以优化中间包的结构和连铸过程的操作参数。
中间包的参数优化包括:中间包的尺寸和墙壁的倾斜度,不同的控流装置的安排,中间包注流区抑湍器的设计。
本研究以宣钢5号小方坯连铸机8流中间包为研究对象,建立中间包钢液流动的数学物理模型,通过对多流中间包内钢液的数学物理模拟,优化中间包的内部结构,改善控流装置,以减少钢液中的夹杂物含量,改善铸坯质量。
多流中间包各流出口温度及所含夹杂物的大小和数量有很大的差异,给操作和铸坯质量控制带来很大的困难。
因此,通过对中间包的数学物理模拟,来寻找合理的中间包控流装置的设置参数,均匀各个出口的钢液分布和温度,以期得到更佳的铸坯质量。
2007中国钢铁年会论文集2.1 建立数学模型2.1.1 中间包流场计算模拟方案根据宣钢5号连铸机多流中间包现状,研究了从6流改为8流中间包后,中间包内钢液的流动情况,研究合理控流装置方案[1,2]:(1)注流区抑湍器的设计:高度、位置等;(2)坝和挡墙的设计:坝和挡墙的高度、间距及合理组合;(3)大包长水口的浸入深度等。
通过以上控流装置的合理匹配,可以改变中间包中流体流动分布、延长流动距离、增加滞止时间及平均停留时间,有效去除夹杂物。
通过本实验,可得到最优的挡墙设置,并有效减少流体中的非金属夹杂物。
2.1.2 中间包流场计算2.1.2.1 中间包内流体流动模型的基本假设 (1)中间包内钢水流动是湍流流动;(2)中间包内钢水流动为稳定态;(3)忽略表面渣层的影响;(4)中间包内钢水液面为自由液面。
2.1.2.2 基本方程流体在中间包内的流动是一个复杂的湍流流动过程,描述流体在中间包内流动的方程有连续性方程、动量方程(Navier —Stokes 方程)以及描述湍流的K —ε方程。
假设中间包内的流体的流动是稳态的并且密度ρ为常数,各方程表示如下:连续性方程0=∂∂iix u ρ (1)式中,ρ为流体密度,kg/m 3 ; u i 为张量表示的时均速度,m/s 。
动量方程(Navier —Stokes 方程)()i j j i eff ji jj i u u u u P x x x x x ρµ∂ ∂∂∂∂=−++ ∂∂∂∂∂(2) 式中,u i 为i 方向的速度(m/s );u j 为j 方向的速度(m/s );x i 为i 方向的坐标值(m ); x j 为j 方向的坐标值(m );ρ为流体密度(kg/m 3); P 为压力(Pa )μeff 为有效黏度系数(Pa ·s )。
湍动能方程ρεσµρ−= ∂∂−∂∂k i k eff iiG x k k u x (3)式中,k 为湍流动能(m 2/s 2); ε为湍流动能耗散率(m 2/s 2)。
在壁面附近的黏性支层中的流体计算,采用壁面函数法。
根据中间包入口流量与中间包出口流量相等,也与结晶器底部流出的流量相等,从而推算出中间包的入口速度w 0(m/s),即w ba cast S l l v w =式中,v cast 为铸坯拉速(m/s);S w 为中间包出口截面面积(m 2) ;l a 为铸坯断面宽度(m);l b 为铸坯断面高度(m)。
2.2 中间包流场计算模拟结果通过计算,对比了改造前后六流与八流中间包的流场情况。
在六流改八流的过程中,虽然中间包每端加长了近2米,但中间包内钢水流动更加平稳,端部没有出现死角和冻钢现象,钢水在中间包内的平均停留时间有所延长,更加有利于钢水中非金属夹杂物的上浮,使进入结晶器的钢水更加纯净。
连铸过程工艺优化和技术改造3 二冷配水优化连铸过程实质是一个传热和相变的过程。
冷却水量大,铸坯断面温度梯度大,有利于柱状晶的生长,柱状晶区就宽,这使得铸坯表面组织中成分偏析严重,表层和次表层温差较大,产生很大的组织应力和热应力,易产生表面和内部裂纹。
降低水量可使柱状区宽度减少,等轴晶区增宽。
因此,二冷水量的多少和合理分配是影响铸坯质量的关键因素之一[3]。
连铸坯二冷区配水应遵循的原则是:(1)尽量减少热应力和组织应力;(2)由强冷变弱冷来控制柱状晶的生长(小的冷速有助于减小偏析)。
为满足以上二冷配水的基本要求,建立了数学模型,计算了连铸坯在凝固过程中温度场的变化情况,制定出科学合理的二冷配水。
3.1 建立数学模型3.1.1 二冷区温度场模拟计算基本假设与简化根据目前二冷配水现状及计算的需要,制定的方案主要考虑以下三个方面:(1)在模型的模拟计算中主要考虑连铸坯在凝固过程中内部存在固相区、液相区和固液糊状区三个区域;(2)计算中不考虑偏析的影响;(3)忽略沿浇铸方向的传热。
3.1.2 二冷区温度场模拟计算的基本方程[4]温度场的计算可以在铸坯的横截面的二维平面上进行[5]。
连铸坯传热为二维非稳态传热,传热方程为:0x yT T Tk k Q C x x y y t∂∂∂∂∂ ++−= ∂∂∂∂∂ (4) 式中,C 为钢的比热容;T 为温度;k x k y 为连铸坯在X 方向和Y 方向上的导热系数;t 为时间;Q 为单位时间单位体积内的内热源强度。
边界条件和初始条件为:),()(),,(10y x T T T T h q n y Tk n x T k t y x T T y y x x =−+=∂∂+∂∂= Ω∈∈∈),(),(),(21y x S y x S y x 000t t t >>= (5) 式中,T (x,y,t )为边界上的S 1上的温度分布(℃) ;H 为热交换系数(W/(m 2·K));S 2为具有热交换的边界; q为热传导引起的边界上的热量散逸(J) ;n x 和x y 为边界外法线方向与X ,Y 轴的夹角余弦;h (T −T 0)为由于物体与温度为T 0的周围介质的热交换所损失的热量(J)铸坯中心边界条件的处理:0T T x yλλ∂∂−=−=∂∂ (6) 铸坯在空冷区的冷却是靠辐射散热:44()b w T T T T x yλλεσ∂∂−=−=−∂∂ (7) 式中,λ为钢的导热系数;h 为连铸坯喷水侧的换热系数;ε为连铸坯的黑度系数;σ为玻耳兹曼常数。
3.1.3 对20钢计算结果利用上述数学模型对20钢在不同的拉速和不同配水条件下温度场的变化情况及坯壳的生长情况进行了计算,并且与原配水进行了对比,从而确定了20钢最佳的二冷配水方案,即20钢的拉速2.2~3.0m/min 为最佳拉速范围,最大拉速不宜超过3.2m/min 。
以下为20钢拉速为2.6m/min 时连铸坯在原配水和新配水下温度场、坯壳生长及液芯长度的变化情况,如图1所示,从图1和表1中可以看出,液芯长度由原来的13.56m 变为16.46m 。
在足辊区,新旧水量虽然相差5.8倍,但坯壳厚度仅相差1.3mm ,二冷区末端表面中央温度却相差110.3℃,在整个二冷区,新的配水制度下铸坯表面温度的波动上下100℃左右,而原配水波动在300℃左右。
2007中国钢铁年会论文集图1 温度场、坯壳生长及液心长度的曲线3.2 工业试验将研究结果应用于4号铸机,在不同流上进行了对比实验。
在4号连铸机共实验取试样29块,其中对比流12块。
实验热酸检验评级结果如下:(1)原配水中间裂纹评级(对比流):Q215:≥2级比例为100%,Q235:≥2级比例为100%,20MnSi:≥2级比例为25%,Q195:≥2级比例为0%。
(2)新配水中间裂纹评级(试验流):Q215:≥2级比例为25%,Q235:0、1级比例为50%,2级比例为50%,20MnSi:≥2级的比例为0%,Q195:≥2级比例为0%。
(3)原配水与新配水生产的连铸坯评级的对比:原配水方案生产的连铸坯,Q235优质坯约为30%左右,20MnSi优质坯约为25%左右;新配水方案生产的连铸坯,Q235优质坯约为50%左右(其余50%为2级),20MnSi 优质坯为100%(Q235和20MnSi取样数较多,数据的数量符合统计规律要求)。