乙醇-水精馏塔顶产品全凝器的设计
第4组(乙醇-水精馏塔顶产品全凝器的设计)

第4组(乙醇-水精馏塔顶产品全凝器的设计)乙醇-水精馏是一种重要的分离技术,在乙醇生产过程中得到广泛应用。
在乙醇-水混合物的精馏过程中,塔顶的产品通常需要通过全凝器进行冷却和凝结,以便得到高纯度的乙醇产品。
因此,全凝器的设计对于乙醇生产的质量和效率具有重要的影响。
为了设计一个高效的全凝器,需要考虑以下因素:1. 填料的选择和布置填料的选择和布置对于全凝器的效率和压降有很大的影响。
常见的填料类型有网状填料、环形填料和泡沫塑料填料等。
其中,泡沫塑料填料具有较低的压降和大的表面积,因此在全凝器中的应用较为广泛。
填料的布置方式也会影响全凝器的效率。
一般来说,填料的布置应足够紧密,以便使气体和液体充分接触,从而加速凝结和冷却过程。
2. 气液分布器的设计气液分布器是一种用于将液体均匀分布到整个填料层的设备。
在全凝器中,气液分布器通常位于填料层的下部,并负责将待处理的气体和液体分别送入填料层。
为了提高全凝器的效率,气液分布器的设计应足够合理。
一般来说,气液分布器应具有足够的流量和压降,以便将气体和液体均匀地输送到填料层中,并充分接触。
此外,气液分布器的设计应考虑到易维护和清洁等因素,以方便全凝器的日常维护和保养。
3. 风机和冷却器的选型风机和冷却器对于全凝器的效率和功能也有重要的影响。
一般来说,全凝器的顶端需要安装一个风机,以便将凝结的乙醇和水蒸汽吸入全凝器中;同时,还需要选择一个合适的冷却器,以便将吸入的乙醇和水蒸汽冷却并凝结。
为了保证全凝器的效率,风机和冷却器的选型应足够科学合理。
一般来说,需要选择具备足够的风量和冷却能力的设备,并结合实际工艺要求进行选型。
此外,为了保证全凝器的可靠性和稳定性,也需要注意设备的质量和耐久性等因素。
4. 其他因素除了上述因素外,全凝器的设计还需要考虑到其他诸如安全、易操作、易清洗等因素。
例如,全凝器的设计应考虑到易于清洗和保养,以便方便操作和维护;同时,全凝器的设计也应兼顾安全性,例如应使用具备耐腐蚀和防爆等性能的材料,以防止发生意外事故。
乙醇_水精馏塔设计说明

乙醇_水精馏塔设计说明
1.设备选型
2.工艺流程
(1)加热阶段:将乙醇_水混合物加热到沸点,使其部分汽化,进入下一个阶段。
(2)蒸馏阶段:乙醇和水在塔内进行汽液两相的分离,高纯度的乙醇向上升腾,低纯度的水向下流动。
(3)冷凝阶段:将高纯度的乙醇气体冷凝成液体,便于收集和储存。
(4)分离阶段:将冷凝后的液体进一步分离,得到纯度较高的乙醇和水。
3.操作参数
(1)温度控制:加热阶段需要将混合物加热到适当的沸点,通常控制在80-100摄氏度。
而在蒸馏阶段,控制塔顶和塔底的温度差异,有助于提高分离效果。
(2)压力控制:塔的进料和出料口通常需要控制一定的压力,以保证流量的稳定。
(3)流量控制:塔内液体的流速对塔的操作效果有较大影响,需保持适当的流速,通常通过调节塔顶和塔底的流量或液位来实现。
4.塔的结构及内件设计
乙醇_水精馏塔的结构包括塔壳、进料装置、分离器、冷凝器、再沸器、集液器等。
其中,塔内需要配置一些内件,如填料和板式塔板等,以
提高传质和传热效果。
填料可采用金属或塑料材料,板式塔板可选用槽式、波纹式等不同形式。
通过合理配置和设计这些内件,提高乙醇_水分离效果。
综上,乙醇_水精馏塔的设计需要综合考虑设备选型、工艺流程、操
作参数以及塔的内部结构等因素。
通过合理的设计和选择,可以实现高效
分离乙醇和水的目的。
乙醇和水的精馏塔设计
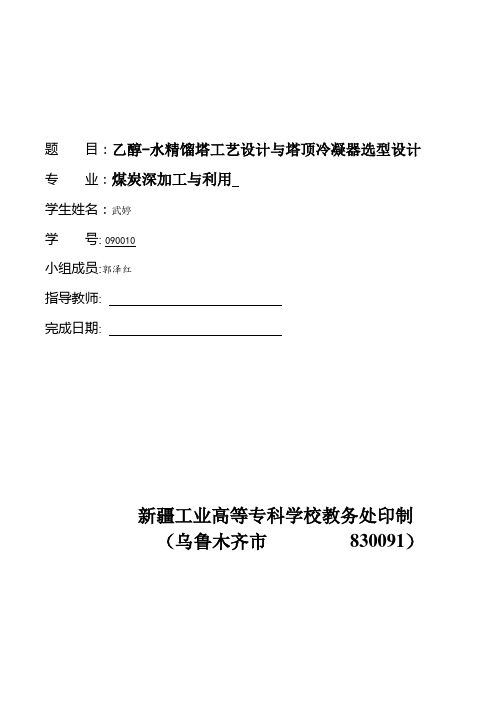
题目:乙醇-水精馏塔工艺设计与塔顶冷凝器选型设计专业:煤炭深加工与利用学生姓名:武婷学号: 090010小组成员:郭泽红指导教师:完成日期:新疆工业高等专科学校教务处印制(乌鲁木齐市830091)化工原理课程设计任务书设计题目:乙醇——水连续精馏塔的设计设计人员所在班级成绩指导教师日期一、设计题目:乙醇-水连续精馏塔的设计二、设计任务及操作条件(1)进精馏塔的料液含乙醇35%(质量分数,下同),其余为水;(2)产品的乙醇含量不得低于94;(3)塔顶易挥发组分回收率为99.5%;(4)生产能力为25000吨/年94%的乙醇产品;(5)每年按330天计,每天24h连续运行。
(6)操作条件a) 塔顶压强 4kPa(表压)b) 进料热状态自选c) 回流比自选d)加热蒸汽压力低压蒸汽(或自选)e) 单板压降小于等于0.7kPa三、设备形式:筛板塔或浮阀塔四、设计内容:1、设计说明书的内容1) 精馏塔的物料衡算;2) 塔板数的确定;3) 精馏塔的工艺条件及有关物性数据的计算;4)精馏塔的塔体工艺尺寸计算;5) 塔板主要工艺尺寸的计算;6) 塔板的流体力学验算;7) 塔板负荷性能图;8) 精馏塔接管尺寸计算;9)对设计过程的评述和有关问题的讨论。
2、设计图纸要求:1) 绘制生产工艺流程图(A2号图纸);2) 绘制精馏塔设计条件图(A2号图纸)。
五、设计基础数据:1. 常压下乙醇——水体系的t-x-y数据;2. 乙醇的密度、粘度、表面张力等物性参数。
第一章前言化工生产中所处理的原料中间产品几乎都是由若干组分组成的混合物。
其中大部分是均相混合物。
生产中为满足要求需将混合物分离成较纯的物质。
精馏是分离液体混合物(含可液化的气体混合物)最常用的一种单元操作。
在化工、炼油、石油化工等工业中得到广泛应用。
精馏过程在能量剂的驱动下(有时加质量剂)。
使气、液两相多次直接接触和分离。
利用液相混合物中各组分挥发度的不同。
使易挥发组分由液相向气相转移。
乙醇_水精馏塔设计说明

符号说明:英文字母Aa---- 塔板的开孔区面积,m2A f---- 降液管的截面积, m2A T----塔的截面积 mC----负荷因子无因次C20----表面力为20mN/m的负荷因子d o----阀孔直径D----塔径e v----液沫夹带量 kg液/kg气E T----总板效率R----回流比R min----最小回流比M----平均摩尔质量 kg/kmolt m----平均温度℃g----重力加速度 9.81m/s2F----阀孔气相动能因子 kg1/2/(s.m1/2)h l----进口堰与降液管间的水平距离 mh c----与干板压降相当的液柱高度 mh f----塔板上鼓层高度 mh L----板上清液层高度 mh1----与板上液层阻力相当的液注高度 m ho----降液管底隙高度 mh ow----堰上液层高度 mh W----溢流堰高度 mh P----与克服表面力的压降相当的液注高度mH-----浮阀塔高度 mH B----塔底空间高度 mH d----降液管清液层高度 mH D----塔顶空间高度 mH F----进料板处塔板间距 m H T·----人孔处塔板间距 mH T----塔板间距 ml W----堰长 mLs----液体体积流量 m3/sN----阀孔数目P----操作压力 KPa△P---压力降 KPa△Pp---气体通过每层筛的压降 KPa N T----理论板层数u----空塔气速 m/sV s----气体体积流量 m3/sW c----边缘无效区宽度 mW d----弓形降液管宽度 mW s ----破沫区宽度 m希腊字母θ----液体在降液管停留的时间 s υ----粘度 mPa.sρ----密度 kg/m3σ----表面力N/mφ----开孔率无因次X`----质量分率无因次下标Max---- 最大的Min ---- 最小的L---- 液相的V---- 气相的m----精馏段n-----提馏段D----塔顶F-----进料板W----塔釜一、概述乙醇~水是工业上最常见的溶剂,也是非常重要的化工原料之一,是无色、无毒、无致癌性、污染性和腐蚀性小的液体混合物。
食品工程原理课程设计乙醇水精馏塔
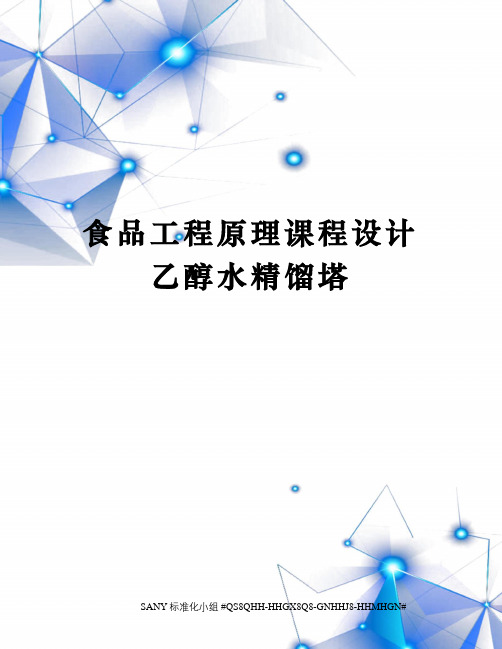
食品工程原理课程设计乙醇水精馏塔SANY标准化小组 #QS8QHH-HHGX8Q8-GNHHJ8-HHMHGN#食品工程原理课程设计题目乙醇-水精馏塔的设计课程名称食品工程原理课程设计学号学生姓名所在专业食品科学与工程所在班级指导老师目录任务书乙醇—水精馏搭的设计(一)设计任务1、生产能力:日产(24h)40吨93%乙醇产品。
2、产品要求:塔釜排出的残液中要求乙醇的浓度不大于%(质量分率)。
3、设备型式:筛板塔(二)操作条件1、精馏塔顶压强:P=1 atm(绝压)2、进料热状况:原料来至上游的粗馏塔,为95-96℃的饱和蒸气R3、回流比:操作回流比R=—min4、加热蒸汽:接蒸汽加热5、单板压降:不大于(三)设计内容1、方案确定流程说明2、塔的工艺计算3、塔和塔板主要工艺尺寸的设计4、辅助设备选型(四)设计成果1、设计说明书一份2、设计图纸,包括流程图,负荷性能图,塔盘布置图,浮阀塔工艺条件图。
一、方案确定流程说明1、生产时日设计要求塔日产40吨93%乙醇,工厂实行三班制,每班工作8小时,每天24小时连续正常工作。
2、选择塔型精馏塔属气—液传质设备。
气—液传质设备主要分为板式塔和填料塔两大类。
该塔设计生产时日要求较大,由板式塔与填料塔比较知:板式塔直径放大时,塔板效率较稳定,且持液量较大,液气比适应范围大,因此本次精馏塔设备选择板式塔。
筛板塔是降液管塔板中结构最简单的,它与泡罩塔相比较具有下列优点:生产能力大10-15%,板效率提高15%左右,而压降可降低30%左右,另外筛板塔结构简单,消耗金属少,塔板的造价可减少40%左右,安装容易,也便于清洗检修。
因此,本设计采用筛板塔比较合适。
3、精馏方式由设计要求知,本精馏塔为连续精馏方式。
4、操作压力常压操作可减少因加压或减压操作所增加的增、减压设备费用和操作费用,提高经济效益, 在条件允许下常采用常压操作,因此本精馏设计选择在常压下操作。
5、加热方式在本物系中,水为难挥发液体,选用直接蒸汽加热,可节省再沸器。
年产1.5万吨乙醇——水精馏塔塔顶全凝器的工艺设计
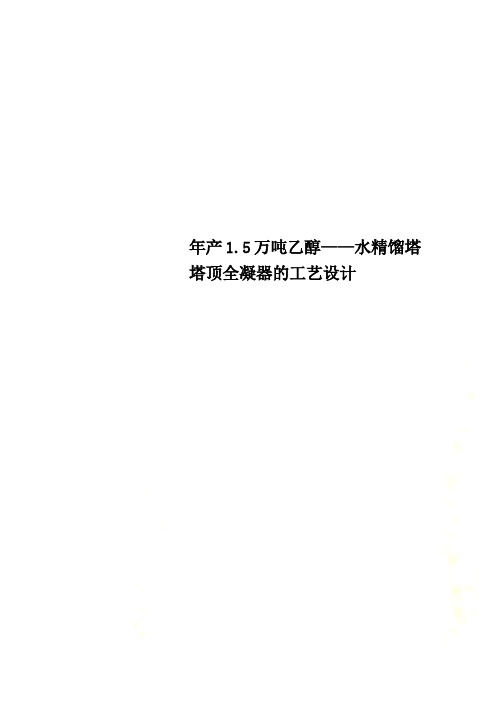
年产1.5万吨乙醇——水精馏塔塔顶全凝器的工艺设计年产1.5万吨乙醇--水精馏塔塔顶全凝器的工艺设计目录摘要 (4)化工原理课程设计任务书 (5)1. 确定设计方案 (7)1.1 选择列管换热器的类型 (7)1.2 选择冷却剂的类型和进出口温度 (7)1.2.1冷却剂的类型 (7)1.2.2进出口温度: (7)1.3 查阅介质的物性数据 (8)1.3.1 水的物性数据 (8)1.3.2 乙醇的物性数据 (8)1.4 选择冷热流体流动的空间及流速 (9)1.4.1 冷热流体流动空间的选择: (9)1.4.2冷热流体流动的流速: (10)2. 估算换热器的传热面积S (11)2.1 计算热负荷Q (11)2.2 计算平均温度 (11)2.3 估算换热面积 (12)3. 初选换热器规格 (12)4. 校核换热器的传热面积 (12)4.1 换热器的实际换热面积 (12)4.2 校核总传热系数 (13)α (13)4.2.1计算管程对流传热系数iα (13)4.2.2计算壳程对流传热系数4.2.3确定污垢热阻 (14)4.2.4总传热系数K0 (14)4.2.5核算壁温与冷凝器流型 (14)5. 计算压降 (15)5.1 计算管程压降 (15)6. 管程和壳程的管口设计 (16)6.1 冷流体进出口接管直径计算 (16)6.2 热流体进出口管直径计算 (17)6.2.1进口直径计算 (17)6.2.2出口直径计算 (17)7. 其他主要附件 (17)7.1 折流挡板 (17)7.2 拉杆、定距管 (18)7.3 防冲挡板 (19)7.4 换热管 (19)7.5 法兰和管板 (20)7.6 垫片 (20)8. 换热器主要工艺结构尺寸和计算结果一览表 (20)9. 结束语 (21)符号说明 (22)参考文献 (25)摘要全凝器是工业生产过程热量传递中应用较为广泛的一种换热器,在精馏塔塔顶的工艺设计中尤为常见。
乙醇和水的精馏塔设计
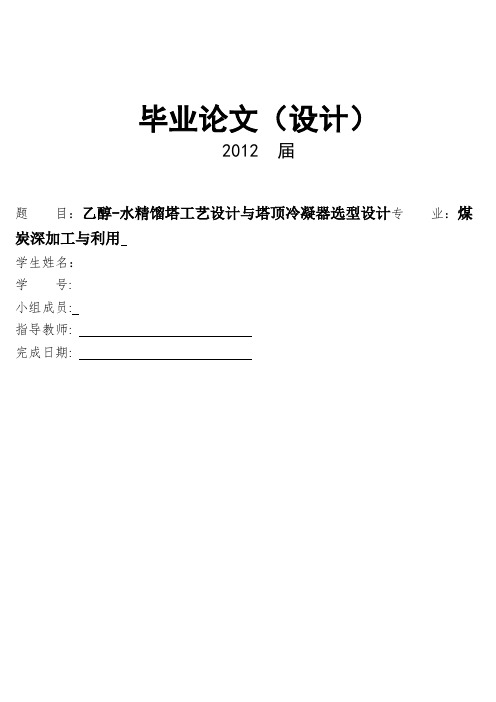
毕业论文(设计)2012 届题目:乙醇-水精馏塔工艺设计与塔顶冷凝器选型设计专业:煤炭深加工与利用学生姓名:学号:小组成员:指导教师:完成日期:前言1.1精馏原理及其在化工生产上的应用实际生产中,在精馏柱及精馏塔中精馏时,上述部分气化和部分冷凝是同时进行的。
对理想液态混合物精馏时,最后得到的馏液(气相冷却而成)是沸点低的B物质,而残液是沸点高的A物质,精馏是多次简单蒸馏的组合。
精馏塔底部是加热区,温度最高;塔顶温度最低。
精馏结果,塔顶冷凝收集的是纯低沸点组分,纯高沸点组分则留在塔底。
1.2精馏塔对塔设备的要求精馏设备所用的设备及其相互联系,总称为精馏装置,其核心为精馏塔。
常用的精馏塔有板式塔和填料塔两类,通称塔设备,和其他传质过程一样,精馏塔对塔设备的要求大致如下:一:生产能力大:即单位塔截面大的气液相流率,不会产生液泛等不正常流动。
二:效率高:气液两相在塔内保持充分的密切接触,具有较高的塔板效率或传质效率。
三:流体阻力小:流体通过塔设备时阻力降小,可以节省动力费用,在减压操作是时,易于达到所要求的真空度。
四:有一定的操作弹性:当气液相流率有一定波动时,两相均能维持正常的流动,而且不会使效率发生较大的变化。
五:结构简单,造价低,安装检修方便。
六:能满足某些工艺的特性:腐蚀性,热敏性,起泡性等。
1.4常用板式塔类型及本设计的选型常用板式塔类型有很多,如:筛板塔、泡罩塔、舌型塔、浮阀塔等。
而浮阀塔具有很多优点,且加工方便,故有关浮阀塔板的研究开发远较其他形式的塔板广泛,是目前新型塔板研开发的主要方向。
近年来与浮阀塔一直成为化工生中主要的传质设备,浮阀塔多用不锈钢板或合金。
实际操作表明,浮阀在一定程度的漏夜状态下,使其操作板效率明显下降,其操作的负荷范围较泡罩塔窄,但设计良好的塔其操作弹性仍可达到满意的程度。
浮阀塔塔板是在泡罩塔板和筛孔塔板的基础上发展起来的,它吸收了两者的优点。
所以在此我们使用浮阀塔,浮阀塔的突出优点是结构简单,造价低,制造方便;塔板开孔率大,生产能力大等。
10万吨乙醇水精馏塔顶产品冷凝器的工艺设计
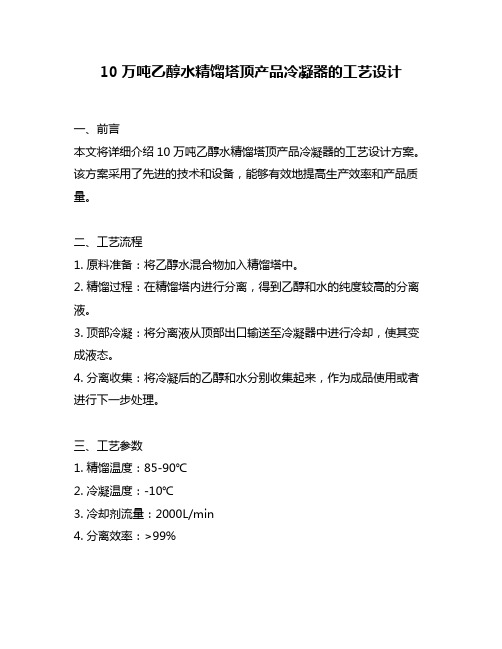
10万吨乙醇水精馏塔顶产品冷凝器的工艺设计一、前言本文将详细介绍10万吨乙醇水精馏塔顶产品冷凝器的工艺设计方案。
该方案采用了先进的技术和设备,能够有效地提高生产效率和产品质量。
二、工艺流程1. 原料准备:将乙醇水混合物加入精馏塔中。
2. 精馏过程:在精馏塔内进行分离,得到乙醇和水的纯度较高的分离液。
3. 顶部冷凝:将分离液从顶部出口输送至冷凝器中进行冷却,使其变成液态。
4. 分离收集:将冷凝后的乙醇和水分别收集起来,作为成品使用或者进行下一步处理。
三、工艺参数1. 精馏温度:85-90℃2. 冷凝温度:-10℃3. 冷却剂流量:2000L/min4. 分离效率:>99%四、设备选型1. 精馏塔:采用不锈钢材质,容积为100m³。
2. 冷凝器:采用管壳式结构,冷却面积为200m²。
3. 冷却剂循环泵:采用自吸式离心泵,流量为2000L/min。
4. 收集罐:采用不锈钢材质,容积为50m³。
五、工艺优化1. 采用先进的精馏塔设计,增加分离效率。
2. 选用高效的冷凝器,提高冷却效果。
3. 优化冷却剂循环系统,确保稳定的流量和温度。
4. 增加收集罐容积,避免过多的停机时间。
六、安全措施1. 精馏塔内部设置压力传感器和温度传感器,确保设备运行安全。
2. 冷凝器内部设置液位传感器和温度传感器,及时监测液位和温度变化。
3. 安装防爆门和防爆灯等设备,确保生产过程中的安全性。
七、结论本文详细介绍了10万吨乙醇水精馏塔顶产品冷凝器的工艺设计方案。
该方案采用了先进的技术和设备,并做出了相应的优化措施,能够有效地提高生产效率和产品质量。
同时,本文还阐述了相关的安全措施,确保生产过程中的安全性。
全凝器的设计
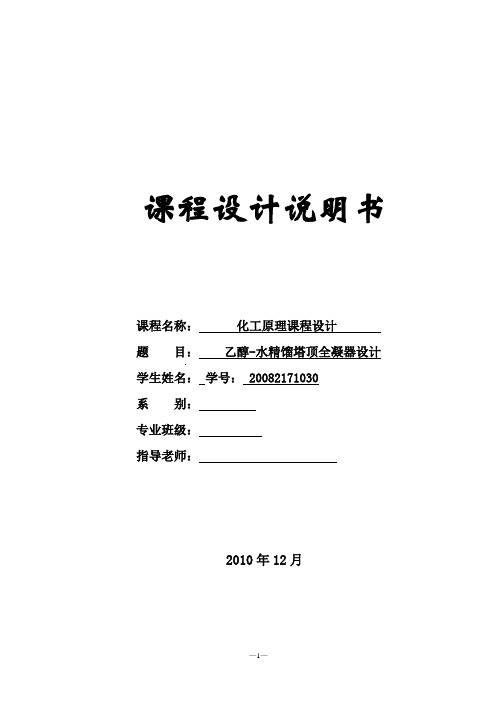
课程设计说明书课程名称:化工原理课程设计题目:乙醇-水精馏塔顶全凝器设计学生姓名:学号: 20082171030系别:专业班级:指导老师:2010年12月换热器设计任务书班级姓名学号20082171030一、设计题目乙醇——水精馏塔顶全凝器的设计二、设计任务及操作条件1、处理能力28800吨/年2.、单位产量4000kg/h3、设备型式列管式换热器4、操作条件(1)乙醇蒸汽:入口温度75℃,出口温度65℃。
(2)冷却介质:循环水,入口温度25 ℃,出口温度45 ℃。
(3)允许压降:不大于101.3kpa。
(4)进料液中含乙醇70%;塔顶产品中乙醇的含量不低于99.6%;塔底产品中乙醇的含量不高于0.01%;(5)乙醇蒸汽定性温度下的物性数据:=754.2kg/m3ρh=0.523mPa·Sμhc=2.64KJ/(Kg·℃)pcλ=0.46w/(m·℃)(5)每年按300天计,每天24小时连续运行。
三、完成设备图一张。
(A3,CAD)目录1.设计方案简介 (4)1.1确定设计方案 (4)1.1.1换热器的选型 (4)1.1.2流动空间安排、管径及流速的确定 (4)1.2确定流体的定性温度、物性数据 (4)2.工艺流程草图及其说明 (6)3.工艺计算及主体设备设计 (6)3.1计算总传热系数 (6)3.1.1计算热负荷Q (6)3.1.2平均传热温差先按纯逆流算 (7)3.1.3 冷却水用量 (7)3.1.4 计算总传热系数K (7)3.2计算传热面积 (8)3.3工艺结构尺寸 (8)3.3.1管程数和传热管数 (8)3.3.2传热管排列和分程方法 (9)3.3.3壳体内径 (9)3.3.4折流板 (9)3.4换热器核算 (9)3.4.1热量核算 (9)3.4.2计算流动阻力 (11)4.辅助设备的计算及选型 (13)接管 (13)5.换热器主要结构尺寸和计算结果 (13)表3换热器主要结构尺寸和计算结果 (14)6. CAD绘制设备附属图(见附图) (15)结论 (16)符号说明 (17)参考文献 (18)1.设计方案简介1.1确定设计方案1.1.1换热器的选型两流体温度变化情况:塔顶热流体(乙醇蒸汽)进口温度75o C,出口温度65o C。
化工原理课程设计乙醇水精馏塔设计doc
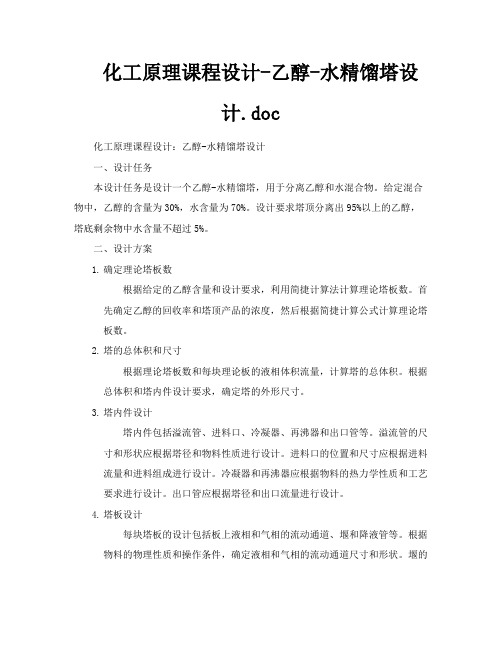
化工原理课程设计-乙醇-水精馏塔设计.doc化工原理课程设计:乙醇-水精馏塔设计一、设计任务本设计任务是设计一个乙醇-水精馏塔,用于分离乙醇和水混合物。
给定混合物中,乙醇的含量为30%,水含量为70%。
设计要求塔顶分离出95%以上的乙醇,塔底剩余物中水含量不超过5%。
二、设计方案1.确定理论塔板数根据给定的乙醇含量和设计要求,利用简捷计算法计算理论塔板数。
首先确定乙醇的回收率和塔顶产品的浓度,然后根据简捷计算公式计算理论塔板数。
2.塔的总体积和尺寸根据理论塔板数和每块理论板的液相体积流量,计算塔的总体积。
根据总体积和塔内件设计要求,确定塔的外形尺寸。
3.塔内件设计塔内件包括溢流管、进料口、冷凝器、再沸器和出口管等。
溢流管的尺寸和形状应根据塔径和物料性质进行设计。
进料口的位置和尺寸应根据进料流量和进料组成进行设计。
冷凝器和再沸器应根据物料的热力学性质和工艺要求进行设计。
出口管应根据塔径和出口流量进行设计。
4.塔板设计每块塔板的设计包括板上液相和气相的流动通道、堰和降液管等。
根据物料的物理性质和操作条件,确定液相和气相的流动通道尺寸和形状。
堰的高度和形状应根据液相流量和操作条件进行设计。
降液管的设计应保证液相流动顺畅且无滞留区。
5.塔的支撑结构和保温根据塔的外形尺寸和操作条件,设计支撑结构的形状和尺寸。
考虑保温层的设置,以减小热量损失。
三、设计计算1.确定理论塔板数根据简捷计算法,乙醇的回收率为95%,塔顶产品的乙醇浓度为95%。
通过简捷计算公式,得到理论塔板数为13块。
2.塔的总体积和尺寸每块理论板的液相体积流量为0.01m3/min,因此总体积为0.013m3/min。
考虑一定裕度,确定塔的外径为0.6m,高度为10m。
3.塔内件设计溢流管的尺寸为Φ10mm,形状为直管上升式。
进料口的位置位于第3块理论板处,尺寸为Φ20mm。
冷凝器采用列管式换热器,再沸器采用釜式再沸器。
出口管采用标准出口管,直径为Φ20mm。
乙醇—水精馏塔顶产品冷凝器的设计.

-目录一.设计任务书 (2)二.计算1.工艺流程及草图 (3)2.精馏塔的物料衡算 (3)3.塔顶温度的计算 (4)4.塔板数的确定 (6)三.换热器的设计1.初选换热器的选型 (8)2.工艺流程及草图说明 (9)3.工艺计算及主体设备设计 (9)4.初选换热器的规格 (10)5.换热器的核算 (11)6.传热管排列和分程方法 (13)7.辅助设备的设计 (17)四.换热器这要结构及尺寸和计算结果表1.计算结果表2.CAD绘制设备辅助图五.结论六.符号说明七.参考文献第一章任务书1.1 化工原理课程设计任务书一、设计题目:A:乙醇—水精馏塔顶产品冷凝器的设计二、原始数据:1、年处理产量:9万吨2、原料液温度:30℃3、原料液浓度(乙醇质量百分数):38%4、产品浓度:塔顶乙醇含量不小于95%;塔底乙醇含量不大于0.5%(乙醇质量百分数)5、精馏塔顶压强:4kpa(表压)6、塔顶采用全凝器,泡点回流。
7、冷却水温度:入口温度25℃8、饱和水蒸汽压力:3kgf/cm2(表压)9、塔:单板压降≤0.7 kPa;换热器:允许压降≤105Pa10、设备形式:换热器——列管式换热器11、厂址:12:每年按320天运行,每天按24小时计三、设计内容A:1、设计方案简介:对确定的工艺流程及换热器型式进行简要论述;2、换热器的工艺计算:确定换热器的传热面积;3、换热器的主要结构尺寸设计;4、主要辅助设备选型;四、设计成果1、设计说明书一份。
内容包括:①目录;②设计题目及原始数据(任务书);③设计方案的说明和论证;④设计过程的有关计算和数据汇总;⑤主体设备设计计算及说明;⑥附属设备的选择⑦参考文献;⑧后记及其它。
对设计过程的评述和有关问题讨论。
2、设计图及其他B:①工艺流程图、冷凝器装备图各一张。
五、设计时间安排:2周六、班级与分组说明:1、人数:2011化工共16人。
分组:每2人为一小组,共8个小组。
2、任务说明:①每小组中甲、乙两同学共同完成流程选择和物料衡算之后,再分别按照A、B设计任务完成设计,其中B组所用原始数据同A组或以A组所求相关数据作为原始数据。
10万吨乙醇水精馏塔顶产品冷凝器的工艺设计

10万吨乙醇水精馏塔顶产品冷凝器的工艺设计一、引言本文将深入探讨10万吨乙醇水精馏塔顶产品冷凝器的工艺设计。
乙醇是一种重要的化工产品,在工业中有广泛的应用。
在乙醇水精馏过程中,冷凝器是一个关键的设备,它可以使醇蒸汽冷凝为液体,从而得到高纯度的乙醇产品。
本文将从冷凝器的结构、原理、操作参数等方面进行详细的分析和讨论。
二、冷凝器的结构和原理2.1 结构乙醇水精馏塔顶冷凝器一般由管束、壳体和附件等部分组成。
管束是冷凝器的核心部件,由多根平行的管子组成。
管子可以分为乙醇进口管、乙醇出口管和冷却水管等。
壳体则是管束的外保护层,起到固定和加强管束的作用。
附件包括进口阀门、出口阀门和排污阀等。
2.2 原理冷凝器的工作原理是利用冷却水和乙醇蒸汽之间的热量传递来实现乙醇的冷凝。
乙醇蒸汽进入冷凝器后,通过管子流动,并与冷却水进行热交换,从而使乙醇蒸汽冷凝为液体。
在冷凝过程中,乙醇蒸汽释放的热量被冷却水带走,而冷却水则被加热,形成热对流,从而不断提供温度差,使得乙醇蒸汽得以冷凝。
三、操作参数的确定3.1 冷却水温度冷却水温度是冷凝器工作的重要参数之一。
一般而言,冷却水温度越低,冷凝效果越好。
但是,过低的冷却水温度也会导致冷却水和乙醇之间的温差过大,从而增加了塔顶乙醇的损失。
因此,在确定冷却水温度时,需综合考虑冷凝效果和乙醇损失的因素,经过实验和经验总结,选择合适的冷却水温度。
3.2 冷却水流量冷却水流量直接影响冷凝器的工作效果。
过大的冷却水流量会导致冷凝器压降过大,影响乙醇流动,降低冷凝效果;而过小的冷却水流量则会导致冷却效果差,无法及时将乙醇蒸汽冷凝为液体。
因此,在确定冷却水流量时,需综合考虑乙醇流量、冷却水温度和冷凝器的结构等因素,经过实验和经验总结,选择合适的冷却水流量。
3.3 乙醇进口温度和流量乙醇进口温度和流量也是冷凝器的重要操作参数。
进口温度过高会影响冷凝效果,进口流量过大或过小则会导致冷凝器的工作不稳定。
分离乙醇水的精馏塔设计

分离乙醇水的精馏塔设计乙醇和水的分离是化工过程中常见的一种操作,常用的分离方法是通过精馏塔进行分离。
精馏塔是一种经过精心设计的设备,利用液体的沸点差异进行分离。
下面是一个关于乙醇水分离的精馏塔设计的详细说明。
1.目标首先需要明确设计的目标。
在这种情况下,目标是将乙醇和水分离,获得所需浓度的乙醇产品。
这可以通过在精馏塔中提供适当的温度和压力条件来实现。
2.塔的类型根据操作需求,可以选择合适的塔类型。
在这种情况下,可以选择常见的塔类型,如板塔或填料塔。
两种类型都可以用于乙醇和水的精馏,但填料塔通常更适合操作,因为它们具有更大的表面积,有助于有效的质量传递。
3.塔的结构精馏塔的结构由塔底、塔体和塔顶组成。
塔底通常用于收集底部的饱和液和不纯物质,塔体用于分离乙醇和水的混合物,而塔顶用于收集纯净的乙醇产品。
4.塔的操作条件乙醇和水有相对较小的沸点差,因此在精馏过程中,必须要提供适当的操作条件来分离它们。
操作条件的选择将取决于所需的乙醇纯度和回收率。
一般来说,塔的顶部温度应低于乙醇的沸点,而底部温度应高于水的沸点。
5.冷却系统精馏塔需要一个冷却系统来控制温度。
这可以通过在塔顶安装冷凝器来实现。
冷凝器将气体中的乙醇蒸汽冷却成液体,并从塔顶收集纯净的乙醇产品。
6.反应器为了增加乙醇的产率,可以在塔底添加一个反应器。
在反应器中,可以将一部分乙醇和水反应生成乙醇化合物,从而增加乙醇的回收率。
这可以通过在塔底加热和加压来控制反应。
7.控制系统精馏塔的操作需要一个有效的控制系统来实现所需纯度和回收率。
这可以通过监测塔内的温度和压力,并对冷却器和加热器进行控制来实现。
8.安全防护由于精馏过程可能涉及高温和高压操作,必须采取适当的安全措施。
这包括使用安全阀和压力传感器来确保塔的安全操作。
此外,还需要对精馏塔进行定期检查和维护,以确保其在运行中的安全性。
总结:乙醇和水的精馏塔设计需要仔细考虑多个因素,包括操作条件、塔的结构和冷却系统。
乙醇_水精馏塔设计说明

符号说明:英文字母Aa---- 塔板的开孔区面积,m2A f---- 降液管的截面积, m2A T----塔的截面积 mC----负荷因子无因次C20----表面张力为20mN/m的负荷因子d o----阀孔直径D----塔径e v----液沫夹带量 kg液/kg气E T----总板效率R----回流比R min----最小回流比M----平均摩尔质量 kg/kmolt m----平均温度℃g----重力加速度 9.81m/s2F----阀孔气相动能因子 kg1/2/(s.m1/2)h l----进口堰与降液管间的水平距离 mh c----与干板压降相当的液柱高度 mh f----塔板上鼓层高度 mh L----板上清液层高度 mh1----与板上液层阻力相当的液注高度 m ho----降液管底隙高度 mh ow----堰上液层高度 mh W----溢流堰高度 mh P----与克服表面张力的压降相当的液注高度 mH-----浮阀塔高度 mH B----塔底空间高度 mH d----降液管内清液层高度 mH D----塔顶空间高度 mH F----进料板处塔板间距 m H T·----人孔处塔板间距 mH T----塔板间距 ml W----堰长 mLs----液体体积流量 m3/sN----阀孔数目P----操作压力 KPa△P---压力降 KPa△Pp---气体通过每层筛的压降 KPa N T----理论板层数u----空塔气速 m/sV s----气体体积流量 m3/sW c----边缘无效区宽度 mW d----弓形降液管宽度 mW s ----破沫区宽度 m希腊字母θ----液体在降液管内停留的时间 s υ----粘度 mPa.sρ----密度 kg/m3σ----表面张力N/mφ----开孔率无因次X`----质量分率无因次下标Max---- 最大的Min ---- 最小的L---- 液相的V---- 气相的m----精馏段n-----提馏段D----塔顶F-----进料板W----塔釜一、概述乙醇~水是工业上最常见的溶剂,也是非常重要的化工原料之一,是无色、无毒、无致癌性、污染性和腐蚀性小的液体混合物。
乙醇—水精馏塔塔顶产品冷凝器设计化工工艺学课程设计

化工工艺课程设计前言课程设计是化工原理课程教学中综合性和实际性较强的教学环节。
它要求学生利用课程理论知识,进行融会贯通的独立思考,在规定时间内完成指定的化工设计任务,是使学生体察工程实际问题复杂性的初次尝试,培养了学生分析和解决工程实际问题的能力。
同时,通过课程设计,还可以使学生树立正确的设计思想,培养实事求是,严肃认真,高度负责的工作态度。
本次课程设计为乙醇—水精馏塔塔顶产品冷凝器设计,要求设计一台冷凝器,将精馏塔顶乙醇—水气相产品全部冷凝。
设计任务包括:一、设计计算初选冷凝器结构二、传热计算(一)压降计算(二)冷凝器计算三、结构设计我们选用的冷凝器为卧式冷凝器,传热系数较高,不易积气,检修和安装方便,为减薄液膜厚度,安装时应有1/100左右坡度。
设计选用的列管换热器类型为固定管板式。
列管换热器是较典型的换热设备,在工业中应用已有悠久历史,具有易制造、成本低、处理能力大、换热表面情况较方便、可供选用的结构材料广阔、适应性强、可用于调温调压场合等优点。
在工艺计算过程中,由于选取K0不当或其他条件选取不当,造成在校核时K0不符合要求。
在重新选取K0的同时,改变了其他的条件,如:n,L等,经过二次校核达到了预期的目的。
最后在结构设计中考虑到合理经济,进行了零部件的设计与选用,使换热器完全发挥其作用。
由于缺乏实际操作经验,我们的设计的产品可能存在某些发面的不足,希望指导老师给予建议和批评。
同时感谢指导老师和参考文献作者对我们本次设计任务的支持和帮助。
第二章概述冷凝的目的在化学工业中,经常需要将气体混合物中的各个组分加以分离,其目的是:(1)回收或捕获气体混合物中的有用物质,以制取产品;(2)除去工艺气体中的有害成分,使气体净化,以便进一步加工处理,或除去工业放空尾气的有害物质,以免污大气。
气体和混合物的分离,往往是根据混合物各组分间某种物理性质和化学性质的差异来进行的。
根据不同性质上的差异,可以开发出不同的分离方法,冷凝操作仅为其中之一,它是根据混合物各组分沸点不同而达到分离的目的的。
乙醇-水冷凝器设计说明书

乙醇-水冷凝器设计说明书%乙醇-水冷凝器设计说明书————————————————————————————————作者:————————————————————————————————日期:目录1.设计方案简介 (2)2.工艺流程草图及其说明 (2)3.主要设备的计算和说明 (4)3.1初选换热器规格计算 (4)3.1.1换热器选型 (4)3.1.2确定流体的定性温度,物性数据 (4)3.1.3计算传热量Q (5)3.1.4计算有效平均温差,按逆流计算 (5)3.1.5估算K值的大小 (6)3.1.6工艺结构设计 (6)3.1.6.1管径与管内流速 (6)3.1.6.2管程数和传热管数 (6)3.1.6.3传热管排列和分程办法 (7)3.1.6.4壳体内径的计算 (7)3.1.6.5折流挡板 (7)3.1.6.6其他附件 (7)3.1.6.7计算混合气的密度 (7)3.1.6.8接管 (8)3.1.6.9核算总传热系数 (9)3.1.6.9.1计算管程对流传热系数 (9)3.1.6.9.2计算壳程对流传热系数 (9)3.1.6.9.3确定污垢热阻 (10)3.1.6.9.4总传热系数 (10)3.1.6.9.5核算壁温 (10)3.1.6.9.6计算压降 (11)3.2所选固定管板式换热器的结构说明 (12)3.2.1管程结构 (12)3.2.1.1密封形式 (12)3.2.1.2管子的排列 (12)3.2.1.3管板 (12)3.2.1.4封头和管箱 (12)3.2.2壳体结构 (12)3.2.2.1壳体 (13)3.2.2.2折流挡板 (13)3.2.2.3缓冲板 (13)3.2.3其他主要附件 (13)4. 换热器的主要结构和计算结果 (14)5.思考题 (15)2 乙醇一水精馏塔项产品冷凝器的设计任务书1、设计题目乙醇一水精馏塔顶产品全凝器的设计。
设计一冷凝器,冷凝乙醇一水系统精馏塔顶部的馏出产品。
- 1、下载文档前请自行甄别文档内容的完整性,平台不提供额外的编辑、内容补充、找答案等附加服务。
- 2、"仅部分预览"的文档,不可在线预览部分如存在完整性等问题,可反馈申请退款(可完整预览的文档不适用该条件!)。
- 3、如文档侵犯您的权益,请联系客服反馈,我们会尽快为您处理(人工客服工作时间:9:00-18:30)。
2009级化学工程与工艺专业《化工原理》课程设计说明书题目:8×104吨/年乙醇-水精馏塔顶产品全凝器的设计姓名:班级学号:指导老师:同组学生姓名:完成时间:2012年5月18日《化工原理》课程设计评分细则说明:评定成绩分为优秀(90-100),良好(80-89),中等(70-79),及格(60-69)和不及格(<60)评审单元评审要素评审内涵评审等级检查方法指导 老师 评分 检阅老师评分 设计 说明书 35%格式规范 是否符合规定的格式要求 5-4 4-3 3-2 2-1格式 标准内容完整设计任务书、评分标准、主要设备计算、作图、后记、参考文献、小组成员及 承担任务10-8 8-6 6-4 4-1设计任务书设计方案 方案是否合理及 是否有创新 10-8 8-6 6-4 4-1计算 记录工艺计算 过 程 计算过程是否正确、完整和规范10-8 8-6 6-4 4-1 计算 记录设计图纸 30%图面布置图纸幅面、比例、标题栏、明细栏是否规范 10-8 8-6 6-4 4-1图面布置标准 标注 文字、符号、代号标注是否清晰、正确 10-8 8-6 6-4 4-1 标注 标准 与设计 吻合图纸设备规格 与计算结果是否吻合10-8 8-6 6-4 4-1比较图纸与说明书 平时 成绩 20%出勤 计算、上机、手工制图 10-8 8-6 6-4 4-1 现场 考察卫生 与纪律设计室是否整洁、 卫生、文明 10-8 8-6 6-4 4-1 答辩 成绩 15%内容表述答辩表述是否清楚 5-4 4-3 3-2 2-1 现场 考察内容是否全面 5-4 4-3 3-2 2-1 回答问题回答问题是否正确5-4 4-3 3-2 2-1总 分综合成绩 成绩等级指导老师 评阅老师(签名) (签名)年 月 日 年 月 日目录1、设计任务书 (4)2、主要设备设计计算和说明 (5)3、工艺设计计算结果汇总表 (13)4、参考文献 (14)后记 (15)第一部分设计任务书1.设计题目: 乙醇-水精馏塔顶产品全凝器的设计设计课题工程背景:采用薯类与谷类原料进行发酵制乙醇。
发酵在密封的发纯度达到99-99.5%以上,其余组分为乙醇0.4-0.8%,脂酵罐进行,产生的CO2质量为基准)。
成熟发酵罐中的乙醇必类0.03-0.4%,酸类0.08-0.09%(以CO2须经过初馏.精馏..除杂等才能得到合格乙醇,初馏塔顶出来的乙醇-水溶液需要进行精馏,精馏塔顶出来的乙醇需要进行冷凝。
2.设计任务及操作条件(1)处理量:8×104吨/年(2)设备形式:卧式列管式换热器(3)冷却介质:水,压力为0.3Ma,入口温度30℃,出口温度40℃(4)冷凝器操作压力:常压(5)允许压力降:不大于105Pa(6)每年按330天计,每天24小时连续运行3.设计说明书的内容(1)封面、评分标准及目录;(2)设计题目及原始数据(任务书);(3)论述换热器总体结构(换热器模型、主要结构)的选择;(4)换热器加热过程有关计算(物料衡算、热量衡算、传热面积、换热管型号、壳体直径等);(5)设计结果概要(主要设备尺度、衡算结果等);(6)主题设备设计计算及说明;(7)附属设备的选择(选做);(8)参考文献;(9)后记及其它。
4.设计图要求A2图纸绘制换热器总装配图,两个局部放大图。
CAD图自由做2个部件。
第二部分 主要设备的计算和说明一、初选换热器规格计算1、确定流体在换热器中的流动途径:95%乙醇宜于走壳程,水走管程,因考虑泠凝效果,乙醇与水之间存在相变化,乙醇的温度较高,水的热容大,易于散热和冷凝。
2、确定流体的定性温度,物性数据,并选择列管式换热器的形式。
冷却水介质为自来水,取入口温度为30℃,出口温度为40℃. 塔顶产品:入口温度为78.2℃,出口温度为78.2℃。
水的定性温度:t m =30+402=35℃ 塔顶乙醇(95%)的定性温度:T m =78.2+78.22=78.2℃ 两流体的温度差:Tm - tm =78.2-35=43.2℃两流体的温差不大于50℃,故选用固定板管式换热器。
表1 两流体在定性温度下的物性数据3、计算热负荷Q ,按管内塔顶产品计算,即 Ms 1(乙醇的进料量)Ms 1=8×104×103/(330×24)=1.0101×104kg/h=2.8058kg/s r=r 纯乙醇×95%+r 水×5%=885.1×95%+2258.4×5%=925.265kJ/kg Q=Ms 1×r=2.80588kg/s ×925.265kJ/kg=2596.108kw 计算混合气的密度(常压下)ρ纯乙醇=5.733kg/m 3 ρ水=0.2788kg/m 3 ρ混合气=5%×0.2788+95%×5.733=5.46kg/m 3物性 流体温度T (℃) 密度ρ kg/m 3粘度μ MPa ·s 比热容C p kJ/(Kg ·℃) 热导系 数λ W/(m ·℃) 液化潜热r /(kJ/kg) 95%乙醇 78.2 738.59 0.5566 3.55 0.1647 925.265 井水35992.20.7284.1740.63382258.4若忽略换热器的热损失,水的流量可由热量恒算求得 M 2⨯Cpc ⨯(t 1-t 2)=Q∴M 2= 2596.108/(4.174×103×(40-30))=62.19kg/s 4、计算平均温度,并确定壳程数。
逆流:热流体: T 1=78.2℃ → T 2=78.2℃ 冷流体: t 1=40℃ → t 2=20℃ ∆t : 38.2℃ 48.2℃所以 ∆t m ;=12(38.2+48.2)=43.2℃温度校正:P =211140300.2178.230t t T t --==-- 12210T T R t t -==- 有P 和R 查对数平均温差校正系数图得:此时1t ϕ∆≈,大于0.8,所以选用单壳程的列管式换热器。
∴2.43.=∆=∆∆m t m t t ϕ℃5、初选换热器规格根据壳内为乙醇(95%),管内为水,总传热系数范围在200~700()2/W m ⋅℃ 初选:k=450w/(m 2.℃) 估算换热面积:A=Q/K △t m =2596.108×103/(450 ×43.2)=134.16m 2 6、工艺结构 6.1 管径与管内流速管径Φ25mm ×2.5mm,管内流速 u=1.0 m/s 壳程流速u=0.8 m/s 6.2 管程数和传热管数根据传热管内径和流速确定单程传热管数n sn s =V/0.785d i 2u=(62.19/992.2)/(0.785×0.022×1.0)=201(根) 按单管程计算所需换热管的长度LL=s/(n s πd o )=134.16/(201×3.14×0.025)=8.50m按单管程设计,传热管过长,根据实际情况,取传热管长L=4.5m ,则该换热器的管程数为 N p =L/4.5=8.5/4.5≈2传热管总根数N T =201×2=402(根) 6.3 传热管排列和分程方法组合排列,即每层内按正三角形排列,隔板中心侧按正方形排列,取管心距t=1.25×25=32mm 6.4 壳体内径采用两管程结构,取管板利用率η=0.7,则壳体内径 2.8057.0/4023205.1/05.1=⨯==ηN t D圆整取D=900mm (查汪镇安.化工工艺设计手册 壁厚为14mm ) 6.5 折流板采用弓形折流板,取弓形折流板圆缺高度为壳体内径的25%,则切去的圆缺高度为h=0.25×900=225mm ,取h=225mm 。
取折流板间距为B=0.3D,则B=0.3×900=270mm ,取B=270mm 。
则折流板数 161-27045001-≈==折流板间距传热管长B N (块)折流板圆缺水平面安装。
6.6 其他附件拉杆直径Φ12mm ,其数量取4~5根,壳程入口应设置防冲挡板。
6.7 接管①壳程流体(混合气体)进口接管 取接管内气体流速为20m/s(饱和蒸汽的速度范围20~40m/s),则接管内径 m V d 181.02014.346.58058.24u 4=⨯⨯==π 取标准管径为Φ194mm ×5mm出口接管取管内液体流速为0.8m/s(乙醇管内安全流速为0.8~1.5m/s),则接管内径m V d 078.08.014.359.7388058.24u 4=⨯⨯==π 取标准管径为Φ89mm ×5mm② 管程流体(循环水)进出口接管 取接管内循环水的流速为2m/s ,则接管内径m V d 20.0214.32.99219.624u 4=⨯⨯==π取标准管径为Φ219mm ×8mm 其余接管略。
6.8 则初选固定管板式换热器规格如下:公称直径 DN /mm 900 公称压力 PN /Mpa 1 管程数 Np 2 管子根数 n 402 中心管子数 n 26管子直径 d /mm φ25mm ×2.5mm. 换热管长度 L /mm 4500 换热面积 2S/m 134.16管子排列方法中心线采用正方型排列,两侧采用正三角形排列冷凝器的实际传热面积:0085.1384.4025.014.3402)1.0d m L n A =⨯⨯⨯=-=(π 该换热器所要求的总传热系数至少为:8.4344385.13810108.2596300=⨯⨯=∆=m t A Q K W/(m 2.℃)6.9 核算总传热系数①计算管程对流传热系数s m m V i si si 321262.002.044020.1=⨯⨯⨯==πρ222063.0020.0785.0)2402()4)((m d Np N A i T i =⨯⨯==π s m A V u i si i /0.2063.01262.0===(湍流)>1000048.5451610728.02.9920.2020.03=⨯⨯⨯==-iii i ei u d R μρ794.41038.6310728.010174.4233=⨯⨯⨯⨯==--iiPI pi C p λμ故管程对流传热系数5.8397794.448.54516020.01038.63023.0Re023.04.08.024.08.0=⨯⨯⨯⨯==-riii Pd a λW/(m 2.℃)②计算壳程对流传热系数0α 因为卧式管壳式换热器,壳程为95%乙醇饱和蒸气冷凝为饱和液体后离开换热器,故可按蒸气在水平管外冷凝的计算公式计算0α4/10320)(725.0td n gr s ∆=μλρα 519.0022.1Ts N n =(三角形直列) 因为95%的乙醇一直处于泡点恒温状态,则冷凝液膜平均温度为95%的乙醇泡点温度78.2o C ,故采用95%的乙醇泡点温度时的物性数据,在层流下:23402022.1022.1519.0519.0≈⨯==T s N n816)0.43025.023105566.01647.010265.92581.959.738(725.0)(725.04/133324/10320≈⨯⨯⨯⨯⨯⨯⨯⨯=∆=-t d n gr s μλραW/(m 2.℃)③确定污垢热阻41072.1-⨯=so R (m 2.℃)/W (有机液体) 4100.2-⨯=si R (m 2.℃)/W(井水) ④总传热系数K 00o s o s i 0m i ii1d d d 1b R R αλd d αd o K =++++20255.8397120250002.05.2225450025.0000172.081611⨯+⨯+⨯++=000148.000025.0000062.0000172.0001225.01++++=50.538001857.01==W/(m 2.℃) K 0=538.50W/(m 2.℃)>434.8W/(m 2.℃)所选用的换热器的安全系数为%85.23%1008.4348.43450.538=⨯-则该换热器的裕度符合生产要求。