产品结构设计准则支柱Boss
产品结构设计标准

产品结构设计标准第一章 塑胶部份结构设计 一、 自攻螺丝BOSS 柱2、BOSS 柱设计注意事项:2.1、BOSS 柱内孔倒0.3直角用于退胶。
2.2、打导电胶条处的螺丝柱在模具设计上不要使用丝铜,丝铜在注塑过程中由于多种原因,如模具制作不良,注塑压力等容易让柱变高会导至LCD 显示少划。
3、BOSS 柱与沉孔的装配尺寸:二、电池门及其防水设计 1、旋扭式电池门1.1、旋扭式电池门使用三个扣位,须平均分布。
1.2、扣位在模具设计上使用行位,夹线要尽量靠近扣位,夹线离扣位越远,防水性能越差。
1.3、防水圈使用O-RING 即横截面为圆的,线径1.0mm.1.4、预压值不能太大,取0.2-0.25 mm ,由于预压过大,无法通过开合100次的测试。
(全面请参考客户电池门开合力度及次数测试标准) 1.5、图示:2、锁螺丝式电池门2.1、因客人对外观之要求多数只准锁一个螺丝,因此这种设计通常电池门上要做一整圈椎台形的围骨来压防水圈。
2.2、防水圈要设计成方形的,可预压0.35 mm 左右,具体要看电池门的变形度来设计。
2.3、图示:三、底面壳防水设计 1、注意事项1.1、在底壳打螺丝的产品;空间许可的情况下防水槽要设计在面壳上,这样生产时可减少一个动作(即假如设计在底壳生产工人为了防止防水圈掉出要先合面壳才能翻转过来打螺丝。
)1.2、横截面多设计为圆形,直径取1.0 mm,正0.1负0.1.3、防水圈的路径尽量避免有落差,假如由于外形及结构等限制无法避免要倒大R过渡。
1.4、防水圈预压值取0.25 mm。
1.5、装配图示:四. LENS 设计1、装配关系及基本设计要点1.1、LCD &LENS装配关系及尺寸设计要点A:LCD V.Aθ:人眼看LCD的视角B=T*tgθ,通常用经验值:B=0.5mm.C:Lens 可视区, C=A+2BD:LENS 与外壳X。
Y方向间隙, D=0.05mm.E:双面胶厚度, E=0.2mm.F:双面胶与外壳外圈间隙 F=0.2mm.G:双面胶宽度,由于模切要求大于1.3 mm。
产品结构设计的四大原则总结

产品结构设计的四大原则总结产品结构设计原则就是在产品结构设计时遵循的基本思路及规则,这些基本规则让产品结构设计更合理,无论塑胶产品还是五金产品,产品结构设计的原则包含合理选用材料、选用合理的结构、尽量简化模具结构及成本控制等。
合理的选用材料所有的产品都是有材料构成的,在设计产品的时,首先要考虑的是材料的选用,材料不仅决定了产品的功能,还决定了产品的价格,如何合理的选用材料呢?(1)根据产品的应用场所来选择。
不同的应用场所对产品的材料需求是不一样的,举几个例子来说明。
如果为日常消费类电子产品,产品材料就应选用强度好、表面容易处理、不容易样生锈、不容易磨伤、易成型的材料,如塑胶材料选用PC、ABS、PC+ABS等,金属材料选用不锈钢、铝、锌合金等。
如果应用于食品行业,产品材料就应该选用无毒无味、耐低温、耐高温,甚至无添加色的材料,如果饮料瓶子选用PET,食品包装袋选用PPPE等,饮水用的杯子材料选用PP、PC等。
(2)根据产品的市场定位来选择。
在设计产品之前,产品的市场定位也会对材料的选用产生影响。
产品质量分高档、中档及低档,不同档次的产品对应不同的市场。
高档的产品在材料选用上优中选优,中档的产品材料性能尚可,低档产品在材料选用上就尽可能降低成本。
(3)根据产品的功能能来选择。
产品功能不同,材料选用也不一样。
有些产品带有运动功能,运动就必定带来磨损,所以在材料选用上就要考虑耐磨,耐磨材料由很多,如大部分金属材料一般都耐磨,耐磨的塑料材料如PA(尼龙料)、POM(赛钢料),橡胶材料如天然橡胶等。
(4)根据公司的要求来选择。
每个公司都有自己的供应商,包含材料供应商。
同一种产品,满足产品设计要求的材料由好几种,价格也不一样,而选用哪一种材料就要结合公司的实际情况来考虑。
产品结构设计不是越复杂越好,相反,在满足产品功能的前提下,结构越简单越好,越简单的结构在模具制作上就越容易,越简单的结构在生产装配上就越轻松,出现的问题也就越少。
塑胶产品结构--BOSS柱(螺丝柱)较全
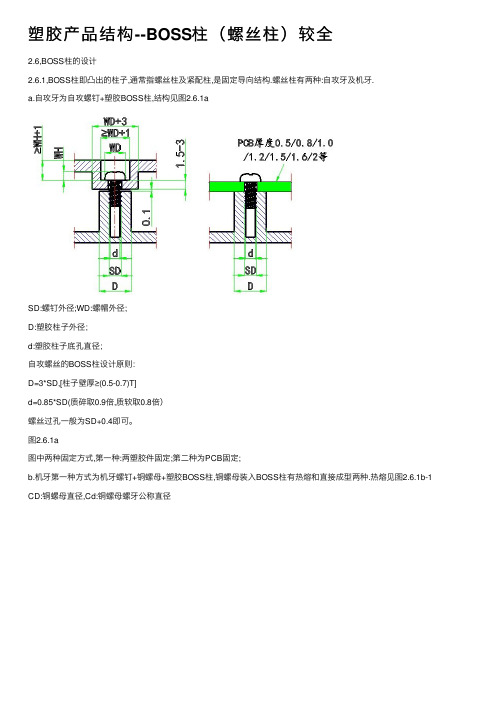
塑胶产品结构--BOSS柱(螺丝柱)较全2.6,BOSS柱的设计2.6.1,BOSS柱即凸出的柱⼦,通常指螺丝柱及紧配柱,是固定导向结构.螺丝柱有两种:⾃攻⽛及机⽛.a.⾃攻⽛为⾃攻螺钉+塑胶BOSS柱,结构见图2.6.1aSD:螺钉外径;WD:螺帽外径;D:塑胶柱⼦外径;d:塑胶柱⼦底孔直径;⾃攻螺丝的BOSS柱设计原则:D=3*SD,[柱⼦壁厚≥(0.5-0.7)T]d=0.85*SD(质碎取0.9倍,质软取0.8倍)螺丝过孔⼀般为SD+0.4即可。
图2.6.1a图中两种固定⽅式,第⼀种:两塑胶件固定;第⼆种为PCB固定;b.机⽛第⼀种⽅式为机⽛螺钉+铜螺母+塑胶BOSS柱,铜螺母装⼊BOSS柱有热熔和直接成型两种.热熔见图2.6.1b-1 CD:铜螺母直径,Cd:铜螺母螺⽛公称直径D:塑胶柱⼦外径;d:塑胶柱⼦底孔直径;热压铜螺母的BOSS柱设计原则:D=CD+1.5(质硬+1,质软+2)d=CD-0.6(质硬-0.5,质软-0.8)螺钉及安装⽅式2.6.1a中有说明如为直接成型结构,取消热压空隙及溢胶槽深图2.6.1b-1图2.6.1b-2图2.6.1b-2中为铜螺母常见样式及热压加⼯⽅式,热压⽅式是⽤熔压铜棒装⼊铜螺母,电加热压⼊塑胶柱中;直接成型是将其作为镶件装⼊模具中注塑成型,通过模具螺丝机定位.这两种⽅式成本类似,但热熔增加了周转加⼯成本,且加⼯后容易造成溢胶,铜螺母歪斜等异常;直接成型则增加了单壳体成型周期(增加安装铜螺母时间,⼀般为⼿⼯安装),但结构牢固,设计上优选.铜螺母设计原则:防脱落,防转动,锁⽛牢靠.常见铜螺母有直纹滚花+凹槽,⽹纹滚花,斜纹滚花+凹槽. c.机⽛第⼆种⽅式为机⽛螺钉+标准螺母.这种⽅式常见机械锁紧,在塑胶制品中⽤于⾼受⼒强度壳体,如电池固定,结构⼿臂,灯具,电机底座,吹风机⼿臂固定等等.螺母采⽤标准螺母,采⽤套筒或扳⼿夹紧,⽤螺丝⼑锁紧.在结构上为了⽅便,常会在胶壳上开槽,将螺母放置其中管住锁紧.d.紧配柱为柱孔配合结构,可做紧配拉紧及导向结构.常⽤在⼩壳件配合(U盘,读卡器,蓝⽛等零件);PCB 定位,壳体防翘曲拉紧等.常见为圆形,⼀般紧配直径有1.0,1.2,1.5,1.8,2.0,2.5,3.0等等,值⾃定义.还有⽅形,椭圆形等其他异形结构.导向柱则需要单边留0.1-0.3mm间隙即可.H≥3mm(直径⼩于3)C≥R避空2.6.2,螺钉的选⽤:螺钉选⽤根据所使⽤的安装⽅式,2.6.1a/b/c中有介绍⾃攻及机⽛安装结构,螺钉分⾃攻和机⽛,⾃攻即螺距较⼤的螺钉在材料预留孔中挤压推进的固定咬合⽅式;机⽛即按标准公制或英制⽛加⼯处理的内外螺丝(同规格)相配合固定咬合⽅式.常⽤⾃攻螺钉尾部有平头,尖头等,螺帽有扁圆头,圆头,P盘头,C平头,K沉头.槽型可⾃定义,常⽤⼗字. BOSS柱锁⽛达到3圈以上即可.尖头⽛在BOSS柱锁⽛⾜够情况下选⽤,具有导正⽛的作⽤;平头⽛在BOSS柱锁⽛不够,⾼度偏低情况下选⽤,容易⽛偏;C平头帽在压缩厚度情况下⽤,最薄可以做到1.0厚;P圆头:对厚度没要求常⽤的标准螺丝螺头;K沉头:常⽤在不超过平⾯的板件固定.机⽛的⽛距较⼩,不做挤压推进,所以仅有平头;螺帽除了⾃攻常⽤螺帽,还有内/外六⾓头,⽅头等,机⽛锁⽛达到2圈以上即可.因为机⽛⽛距较⼩,锁的圈数越多牢固.通常相同的长度,⽛距越⼩锁⽛越紧,强度越强.因此⽛也有粗⽛和细⽛之分.粗⽛即普通螺⽛,细⽛常见管螺纹.机⽛的规格型号,请参考标准.2.6.3,塑胶预留⾃攻螺丝底孔设计参考值如下表所⽰.常⽤⾃攻螺丝装配及测试(10次)时所要⽤的扭⼒参考值,如下表所⽰.。
HOOK&RIB&BOSS Design Guide

3. 自攻牙Boos柱 (Mark 需要更多讲义)
H=T+L T=t+0.2mm D=d+0.4mm A=A1+0.2mm A2=A1-0.4mm D1=2A2~2.5A2 Gap=0.05~0.1mm 拔模=1.5~2° PS:A1 、L 、d按厂商提供Spec
三、防错位结构设计
3.1.防错位结构的基本设计参数
2.针对受力大的卡勾,为避免卡勾头部折断,补强Rib应支撑到卡勾头部1/2以上
RIB长在卡勾头部1/2 处,加勾强度。
4.卡勾整体布局
a.卡勾之间的间距30 mm≦ A ≦ 50mm,卡勾过近难拆卸,过远会失效. b.卡勾本身宽度按空间及功能不同,尺寸设计为3 mm≦ B ≦ 10mm
c.卡勾不可在四角圆弧位臵,不利模具加工.可放在圆弧尽头直线部位。
1-2.Boss结构设计
Hale Waihona Puke A、Boss柱外壁应做补强Rib与四周结构连接,防止Boss断裂。 厚度一般为0.7~1.0mm B、导向C角方便螺母热熔时定位,一般为0.3mm PS:为增加螺母扭拉力,可在内侧壁增加一圈半圆小Rib.
1-3.常用螺母与塑胶孔径参考
2.热熔Boss
A、热熔Boss为固定按键弹力臂,因此Boss底部需做十字Rib, 保正弹力臂能与十字Rib贴平. B、热熔Boss外径D一般取2.0~2.5mm,与弹力臂间隙T=0.05mm C、热熔柱高度H=h+1.5mm D、热熔柱内孔底部肉厚A1≦A(平均肉厚),避免外观缩水。 E、热熔柱外径拔模一般为1°
1.Rib结构要合理,不要对外观造成缩水不良
Sink Mark NG OK NG
OK
NG 1.胶位突变, 易产生应力痕 2.尖角导致模 具有尖铁,易 崩缺。
塑胶产品结构 BOSS柱 螺丝柱 较全

2.6,BOSS柱的设计2.6.1,BOSS柱即凸出的柱子,通常指螺丝柱及紧配柱,是固定导向结构.螺丝柱有两种:自攻牙及机牙.a.自攻牙为自攻螺钉+塑胶BOSS柱,结构见图2.6.1aSD:螺钉外径;WD:螺帽外径;D:塑胶柱子外径;d:塑胶柱子底孔直径;自攻螺丝的BOSS柱设计原则:D=3*SD,[柱子壁厚≥(0.5-0.7)T]d=0.85*SD(质碎取0.9倍,质软取0.8倍)螺丝过孔一般为SD+0.4即可。
图2.6.1a图中两种固定方式,第一种:两塑胶件固定;第二种为PCB固定;b.机牙第一种方式为机牙螺钉+铜螺母+塑胶BOSS柱,铜螺母装入BOSS柱有热熔和直接成型两种.热熔见图2.6.1b-1CD:铜螺母直径,Cd:铜螺母螺牙公称直径D:塑胶柱子外径;d:塑胶柱子底孔直径;热压铜螺母的BOSS柱设计原则:D=CD+1.5(质硬+1,质软+2)d=CD-0.6(质硬-0.5,质软-0.8)螺钉及安装方式2.6.1a中有说明如为直接成型结构,取消热压空隙及溢胶槽深图2.6.1b-1图2.6.1b-2图2.6.1b-2中为铜螺母常见样式及热压加工方式,热压方式是用熔压铜棒装入铜螺母,电加热压入塑胶柱中;直接成型是将其作为镶件装入模具中注塑成型,通过模具螺丝机定位.这两种方式成本类似,但热熔增加了周转加工成本,且加工后容易造成溢胶,铜螺母歪斜等异常;直接成型则增加了单壳体成型周期(增加安装铜螺母时间,一般为手工安装),但结构牢固,设计上优选.铜螺母设计原则:防脱落,防转动,锁牙牢靠.常见铜螺母有直纹滚花+凹槽,网纹滚花,斜纹滚花+凹槽. c.机牙第二种方式为机牙螺钉+标准螺母.这种方式常见机械锁紧,在塑胶制品中用于高受力强度壳体,如电池固定,结构手臂,灯具,电机底座,吹风机手臂固定等等.螺母采用标准螺母,采用套筒或扳手夹紧,用螺丝刀锁紧.在结构上为了方便,常会在胶壳上开槽,将螺母放置其中管住锁紧.d.紧配柱为柱孔配合结构,可做紧配拉紧及导向结构.常用在小壳件配合(U盘,读卡器,蓝牙等零件);PCB 定位,壳体防翘曲拉紧等.常见为圆形,一般紧配直径有1.0,1.2,1.5,1.8,2.0,2.5,3.0等等,值自定义.还有方形,椭圆形等其他异形结构.导向柱则需要单边留0.1-0.3mm间隙即可.H≥3mm(直径小于3)C≥R避空2.6.2,螺钉的选用:螺钉选用根据所使用的安装方式,2.6.1a/b/c中有介绍自攻及机牙安装结构,螺钉分自攻和机牙,自攻即螺距较大的螺钉在材料预留孔中挤压推进的固定咬合方式;机牙即按标准公制或英制牙加工处理的内外螺丝(同规格)相配合固定咬合方式.常用自攻螺钉尾部有平头,尖头等,螺帽有扁圆头,圆头,P盘头,C平头,K沉头.槽型可自定义,常用十字. BOSS柱锁牙达到3圈以上即可.尖头牙在BOSS柱锁牙足够情况下选用,具有导正牙的作用;平头牙在BOSS柱锁牙不够,高度偏低情况下选用,容易牙偏;C平头帽在压缩厚度情况下用,最薄可以做到1.0厚;P圆头:对厚度没要求常用的标准螺丝螺头;K沉头:常用在不超过平面的板件固定.机牙的牙距较小,不做挤压推进,所以仅有平头;螺帽除了自攻常用螺帽,还有内/外六角头,方头等,机牙锁牙达到2圈以上即可.因为机牙牙距较小,锁的圈数越多牢固.通常相同的长度,牙距越小锁牙越紧,强度越强.因此牙也有粗牙和细牙之分.粗牙即普通螺牙,细牙常见管螺纹.机牙的规格型号,请参考标准.2.6.3,塑胶预留自攻螺丝底孔设计参考值如下表所示.常用自攻螺丝装配及测试(10次)时所要用的扭力参考值,如下表所示.。
塑胶产品结构设计常用术语

塑胶产品结构设计常用术语及解释如下:
1.PL面:即Parting Panel的简称,也称分型面,是指模具在闭合时公模和母模相接触的部分。
2.枕位:外壳类塑件的边缘常开有缺口,用于安装各类配件,此处形成的枕状部分称为枕位。
3.火山口:BOOS柱根部减胶部分反映在模具上的类似于火山爆发后的形状叫做模具火山口。
4.呵(音hā):指的是模仁,香港习惯用语。
5.老虎口:又称为管位,即用来限位的部分。
6.柱位:产品上的BOSS的柱称为柱位。
7.虚位:模具上的间隙称为虚位。
8.扣位:产品联接用的钩称为扣位。
9.火花纹:电火花加工后留下的纹称为火花纹。
10.料位:塑胶产品的避厚,也称肉厚。
以上信息仅供参考,如需了解更多信息,建议咨询专业人士。
塑胶产品结构BOSS柱螺丝柱较全.pdf
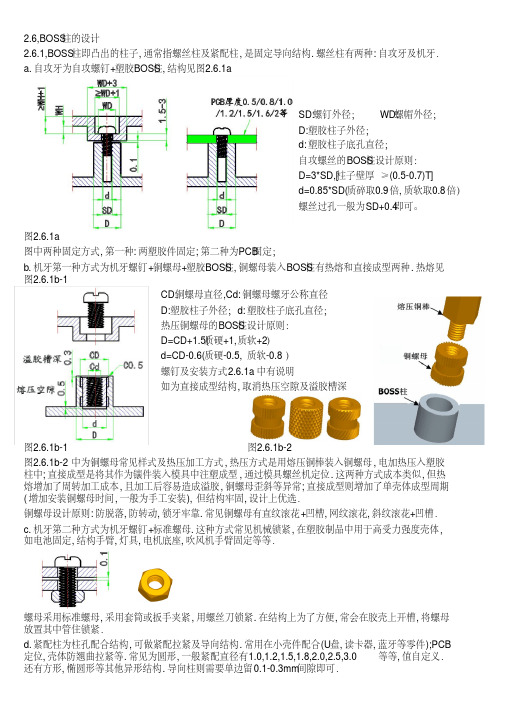
2.6,BOSS柱的设计2.6.1,BOSS柱即凸出的柱子,通常指螺丝柱及紧配柱,是固定导向结构.螺丝柱有两种:自攻牙及机牙.a.自攻牙为自攻螺钉+塑胶BOSS柱,结构见图2.6.1aSD:螺钉外径;WD:螺帽外径;D:塑胶柱子外径;d:塑胶柱子底孔直径;自攻螺丝的BOSS柱设计原则:D=3*SD,[柱子壁厚≥(0.5-0.7)T]d=0.85*SD(质碎取0.9倍,质软取0.8倍)螺丝过孔一般为SD+0.4即可。
图2.6.1a图中两种固定方式,第一种:两塑胶件固定;第二种为PCB固定;b.机牙第一种方式为机牙螺钉+铜螺母+塑胶BOSS柱,铜螺母装入BOSS柱有热熔和直接成型两种.热熔见图2.6.1b-1CD:铜螺母直径,Cd:铜螺母螺牙公称直径D:塑胶柱子外径;d:塑胶柱子底孔直径;热压铜螺母的BOSS柱设计原则:D=CD+1.5(质硬+1,质软+2)d=CD-0.6(质硬-0.5,质软-0.8)螺钉及安装方式2.6.1a中有说明如为直接成型结构,取消热压空隙及溢胶槽深图2.6.1b-1图2.6.1b-2图2.6.1b-2中为铜螺母常见样式及热压加工方式,热压方式是用熔压铜棒装入铜螺母,电加热压入塑胶柱中;直接成型是将其作为镶件装入模具中注塑成型,通过模具螺丝机定位.这两种方式成本类似,但热熔增加了周转加工成本,且加工后容易造成溢胶,铜螺母歪斜等异常;直接成型则增加了单壳体成型周期(增加安装铜螺母时间,一般为手工安装),但结构牢固,设计上优选.铜螺母设计原则:防脱落,防转动,锁牙牢靠.常见铜螺母有直纹滚花+凹槽,网纹滚花,斜纹滚花+凹槽.c.机牙第二种方式为机牙螺钉+标准螺母.这种方式常见机械锁紧,在塑胶制品中用于高受力强度壳体,如电池固定,结构手臂,灯具,电机底座,吹风机手臂固定等等.螺母采用标准螺母,采用套筒或扳手夹紧,用螺丝刀锁紧.在结构上为了方便,常会在胶壳上开槽,将螺母放置其中管住锁紧.d.紧配柱为柱孔配合结构,可做紧配拉紧及导向结构.常用在小壳件配合(U盘,读卡器,蓝牙等零件);PCB定位,壳体防翘曲拉紧等.常见为圆形,一般紧配直径有1.0,1.2,1.5,1.8,2.0,2.5,3.0等等,值自定义.还有方形,椭圆形等其他异形结构.导向柱则需要单边留0.1-0.3mm间隙即可.H≥3mm(直径小于3)C≥R避空2.6.2,螺钉的选用:螺钉选用根据所使用的安装方式,2.6.1a/b/c中有介绍自攻及机牙安装结构,螺钉分自攻和机牙,自攻即螺距较大的螺钉在材料预留孔中挤压推进的固定咬合方式;机牙即按标准公制或英制牙加工处理的内外螺丝(同规格)相配合固定咬合方式.常用自攻螺钉尾部有平头,尖头等,螺帽有扁圆头,圆头,P盘头,C平头,K沉头.槽型可自定义,常用十字.BOSS柱锁牙达到3圈以上即可.尖头牙在BOSS柱锁牙足够情况下选用,具有导正牙的作用;平头牙在BOSS柱锁牙不够,高度偏低情况下选用,容易牙偏;C平头帽在压缩厚度情况下用,最薄可以做到1.0厚;P圆头:对厚度没要求常用的标准螺丝螺头;K沉头:常用在不超过平面的板件固定.机牙的牙距较小,不做挤压推进,所以仅有平头;螺帽除了自攻常用螺帽,还有内/外六角头,方头等,机牙锁牙达到2圈以上即可.因为机牙牙距较小,锁的圈数越多牢固.通常相同的长度,牙距越小锁牙越紧,强度越强.因此牙也有粗牙和细牙之分.粗牙即普通螺牙,细牙常见管螺纹.机牙的规格型号,请参考标准.2.6.3,塑胶预留自攻螺丝底孔设计参考值如下表所示.常用自攻螺丝装配及测试(10次)时所要用的扭力参考值,如下表所示.。
产品结构设计准则--boss篇
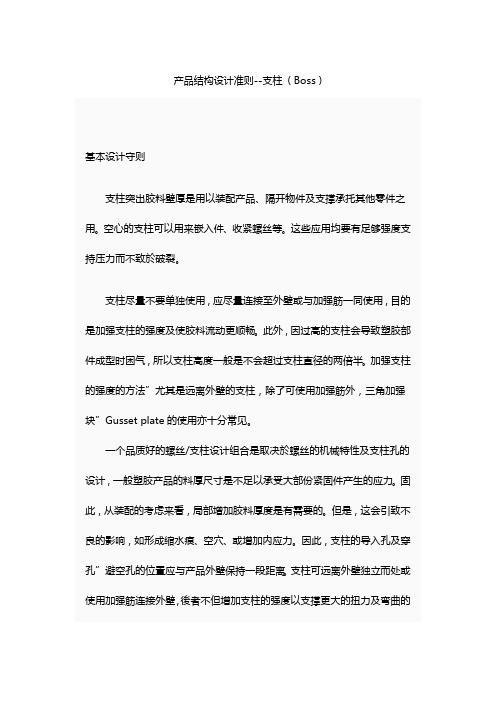
产品结构设计准则--支柱 ( Boss )基本设计守则支柱突出胶料壁厚是用以装配产品、隔开物件及支撑承托其他零件之用。
空心的支柱可以用来嵌入件、收紧螺丝等。
这些应用均要有足够强度支持压力而不致於破裂。
支柱尽量不要单独使用,应尽量连接至外壁或与加强筋一同使用,目的是加强支柱的强度及使胶料流动更顺畅。
此外,因过高的支柱会导致塑胶部件成型时困气,所以支柱高度一般是不会超过支柱直径的两倍半。
加强支柱的强度的方法”尤其是远离外壁的支柱,除了可使用加强筋外,三角加强块”Gusset plate的使用亦十分常见。
一个品质好的螺丝/支柱设计组合是取决於螺丝的机械特性及支柱孔的设计,一般塑胶产品的料厚尺寸是不足以承受大部份紧固件产生的应力。
固此,从装配的考虑来看,局部增加胶料厚度是有需要的。
但是,这会引致不良的影响,如形成缩水痕、空穴、或增加内应力。
因此,支柱的导入孔及穿孔”避空孔的位臵应与产品外壁保持一段距离。
支柱可远离外壁独立而处或使用加强筋连接外壁,後者不但增加支柱的强度以支撑更大的扭力及弯曲的外力,更有助胶料填充及减少因困气而出现烧焦的情况。
同样理由,远离外壁的支柱亦应辅以三角加强块,三角加强块对改善薄壁支柱的胶料流动特别适用。
收缩痕的大小取决於胶料的收缩率、成型工序的叁数控制、模具设计及产品设计。
使用过短的哥针、增加底部弧度尺寸、加厚的支柱壁或外壁尺寸均不利於收缩痕的减少;不幸地,支柱的强度及抵受外力的能力却随着增加底部弧度尺寸或壁厚尺寸而增加。
因此,支柱的设计须要从这两方面取得平衡。
1)支柱位臵2)支柱设计不同材料的设计要点ABS一般来说,支柱的外径是内径的两倍已足够。
有时这种方式结果支柱壁厚等於或超过胶料厚度而增加物料重量和在表面产生缩水纹及高成型应力。
严格的来说支柱的厚度应为胶料厚度的50-70%。
如因此种设计方式而支柱不能提供足够强度,但已改善了表面缩水。
斜骨是可以加强支柱的强度,可由最小的尺寸伸延至支柱高的90%。
塑胶产品结构设计准则

在塑胶件上开孔使其和其它部件相接合或增加产品功能上的组合是常用的手法,洞 孔的大小及位置应尽量不会对产品的强度构成影响或增加生产的复杂性, 常见孔的 类型如下:
孔离边位或内壁边之要点 :
confidential
16
四、塑胶产品结构设计准则-洞孔 (Hole)
盲孔设计要点: 盲孔是靠模具上的镶针形成,而镶针的设计只能单边支撑在模具上,因此很容易 被溶融的塑料使其弯曲变形,造成盲孔出现椭圆的形状,所以镶针的长度不能过长。 盲孔深度最大是直径的3倍,考虑模具镶针强度要求直径最小0.8mm。 外观件上的各种凹槽,如雕刻文字等,要求棱线分明,导致过渡太急,易产生气
confidential
12
三、塑胶产品结构设计准则-支柱 ( Boss )
对于外观件,当有螺丝柱子,需要进行缩水验证,依照上页图示意,塑胶壁厚 1.5 ,螺丝柱子外径3.4,验证结果 NG:(1.8-1.5)/1.5*100%=20% >8%。 外观面有可能会有缩水痕迹。
改善方案如下图:
当缩水验证NG时,可在增加火山口及加深螺丝孔深度来改善。 外观部品综合考虑缩水与螺丝柱子强度,塑胶壁厚要求大于1.3。 适当的辅以三角或十字加强筋方式,可大幅度提高强度和改善料流填充。
confidential
4
一、塑胶产品结构设计准则-壁厚
B. 转角位的设计准则亦适用於悬梁式扣位。因这种扣紧方式是需要将悬梁臂弯 曲嵌入,转角位置的设计图说明如果转角弧位R太小时会引致其应力集中系数 (Stress Concentration Factor)过大,因此,产品弯曲时容易折断,弧位R太大 的话则容易出现收缩纹和空洞。因此,圆弧位和壁厚是有一定的比例。一般 介乎0.2至0.6T之间,理想数值是在0.5T左右。
产品结构设计准则-支柱(Boss)

产品结构设计准则-支柱(Boss )基本设计守则支柱突出胶料壁厚是用以装配产品、隔开对象及支撑承托其他零件之用。
空心的支柱可以用来嵌入件、收紧螺丝等。
这些应用均要有足够强度支持压力而不致于破裂。
支柱尽量不要单独使用,应尽量连接至外壁或与加强筋一同使用,目的是加强支柱的强度及使胶料流动更顺畅。
此外,因过高的支柱会导致塑胶部件成型时困气,所以支柱高度一般是不会超过支柱直径的两倍半。
加强支柱的强度的方法:尤其是远离外壁的支柱,除了可使用加强筋外,三角加强块Gusset plate的使用亦十分常见。
一个品质好的螺丝/支柱设计组合是取决于螺丝的机械特性及支柱孔的设计,一般塑胶产品的料厚尺寸是不足以承受大部份紧固件产生的应力。
固此,从装配的考虑来看,局部增加胶料厚度是有必要的。
但是,这会引致不良的影响,如形成缩水痕、空穴、或增加内应力。
因此,支柱的导入孔及穿孔、避空孔的位置应与产品外壁保持一段距离。
支柱可远离外壁独立而处或使用加强筋连接外壁,后者不但增加支柱的强度以支撑更大的扭力及弯曲的外力,更有助胶料填充及减少因困气而出现烧焦的情况。
同样理由,远离外壁的支柱亦应辅以三角加强块,三角加强块对改善薄壁支柱的胶料流动特别适用。
收缩痕的大小取决于胶料的收缩率、成型工序的叁数控制、模具设计及产品设计。
使用过短的哥针、增加底部弧度尺寸、加厚的支柱壁或外壁尺寸均不利于收缩痕的减少;不幸地,支柱的强度及抵受外力的能力却随着增加底部弧度尺寸或壁厚尺寸而增加。
因此,支柱的设计须要从这两方面取得平衡。
1) 支柱位置2)支柱设计不同材料的设计要点ABS丙烯腈-丁二烯-苯乙烯共聚物一般来说,支柱的外径是内径的两倍已足够。
有时这种方式结果支柱壁厚等于或超过胶料厚度而增加物料重量和在表面产生缩水纹及高成型应力。
严格的来说支柱的厚度应为胶料厚度的50-70%。
如因此种设计方式而支柱不能提供足够强度,但已改善了表面缩水。
斜骨是可以加强支柱的强度,可由最小的尺寸伸延至支柱高的90%。
塑胶产品结构设计准则

confidential
13
三、塑胶产品结构设计准则-支柱 ( Boss )
对于外观件,当有螺丝柱子,需要进行缩水验证,依照上页图示意,塑胶壁厚 1.5 ,螺丝柱子外径3.4,验证结果 NG:(1.8-1.5)/1.5*100%=20% >8%。 外观面有可能会有缩水痕迹。
改善方案如下图:
当缩水验证NG时,可在增加火山口及加深螺丝孔深度来改善。 外观部品综合考虑缩水与螺丝柱子强度,塑胶壁厚要求大于1.3。 适当的辅以三角或十字加强筋方式,可大幅度提高强度和改善料流填充。
confidential
18
四、塑胶产品结构设计准则-洞孔 (Hole)
对于塑胶部品,结合线处强度较弱,受力容易破裂。当通孔处于产品边部,同 时有配合力量要求时,要求孔壁距离外侧壁1.5mm(如因结构原因无法保证 1.5mm, 采用模具设置冷料槽成型后再剪除,但最小要1.0mm),对于卡勾槽尽 量采用盲孔。
10
三、塑胶产品结构设计准则-支柱 ( Boss )
支柱 ( Boss )基本设计守则:
A. 支柱尽量不要单独使用,应尽量连接至外壁或与加强筋一同使用,目的是加 强支柱的强度及使胶料流动更顺畅。
B. 实心支柱的直径大小取壁厚的0.5~0.7倍,当有缩水管理要求时,需使用使用 缩水公式验证。
C. 过高的支柱会导致塑胶部件成型时困气,所以支柱高度一般是不会超过支柱 直径的3倍。过高的支柱要考虑其强度及逃气问题。
塑胶产品结构设计准则
Paul ren
confidential
1
塑胶产品结构设计准则
一. 壁厚 (Thickness) 二. 加强筋(Rib) 三. 支柱 (Boss) 四. 洞孔 (Hole) 五. 扣位(Snap Joint) 六. 出模角(Draft Angle) 七. 螺紋(Screw) 八. 文字(Text) 九. 咬花(Texture)
产品结构设计准则支柱

产品结构设计准则支柱产品结构设计在产品开发过程中起着至关重要的作用,是产品成功的关键之一。
合理的产品结构设计可以提高产品的性能、降低生产成本、增加用户体验等方面带来诸多好处。
本文将介绍产品结构设计的准则支柱,帮助产品设计师更好地进行产品结构设计。
1. 产品结构设计概述产品结构设计是指在产品设计阶段对产品的组成结构进行规划和设计,包括产品的各个部件、连接方式、组装方式等方面。
一个好的产品结构设计应该具备稳定性强、易于生产、方便维修等特点。
2. 产品结构设计准则支柱2.1 结构合理性产品的结构设计应该合理,能够满足产品的功能需求,并且能够简化生产工艺,提高产品的可靠性和稳定性。
结构合理性是产品结构设计的首要准则。
2.2 易于生产产品结构设计应考虑到生产过程中的各个环节,保证产品的各个部件能够顺利生产,并能够通过自动化设备进行组装。
设计师需要考虑到加工工艺、材料选择等因素,以确保产品的生产效率和质量。
2.3 维修便捷性产品在使用过程中难免会出现故障或需要更换部件的情况,因此产品结构设计应考虑到维修的便捷性。
设计师可以通过模块化设计、标准化部件等方式来提高产品的维修效率,降低维修成本。
2.4 成本控制产品的结构设计应该考虑到成本因素,确保在具备功能需求的前提下尽量降低生产成本。
设计师需要在材料选择、加工工艺等方面进行合理折衷,以确保产品的性价比。
3. 结语产品结构设计是产品设计中至关重要的环节,在设计过程中需要充分考虑产品的功能需求、生产和维修便捷性、成本等方面因素。
通过本文介绍的产品结构设计准则支柱,希望能够帮助产品设计师更好地进行产品结构设计,提高产品的质量和竞争力。
产品结构设计的四大原则总结

产品结构设计的四大原则总结产品结构设计原则就是在产品结构设计时遵循的基本思路及规则,这些基本规则让产品结构设计更合理,无论塑胶产品还是五金产品,产品结构设计的原则包含合理选用材料、选用合理的结构、尽量简化模具结构及成本控制等。
01合理的选用材料所有的产品都是有材料构成的,在设计产品的时,首先要考虑的是材料的选用,材料不仅决定了产品的功能,还决定了产品的价格,如何合理的选用材料呢?(1)根据产品的应用场所来选择。
不同的应用场所对产品的材料需求是不一样的,举几个例子来说明。
如果为日常消费类电子产品,产品材料就应选用强度好、表面容易处理、不容易样生锈、不容易磨伤、易成型的材料,如塑胶材料选用PC、ABS、PC+ABS等,金属材料选用不锈钢、铝、锌合金等。
如果应用于食品行业,产品材料就应该选用无毒无味、耐低温、耐高温,甚至无添加色的材料,如果饮料瓶子选用PET,食品包装袋选用PPPE等,饮水用的杯子材料选用PP、PC等。
(2)根据产品的市场定位来选择。
在设计产品之前,产品的市场定位也会对材料的选用产生影响。
产品质量分高档、中档及低档,不同档次的产品对应不同的市场。
高档的产品在材料选用上优中选优,中档的产品材料性能尚可,低档产品在材料选用上就尽可能降低成本。
(3)根据产品的功能能来选择。
产品功能不同,材料选用也不一样。
有些产品带有运动功能,运动就必定带来磨损,所以在材料选用上就要考虑耐磨,耐磨材料由很多,如大部分金属材料一般都耐磨,耐磨的塑料材料如PA(尼龙料)、POM(赛钢料),橡胶材料如天然橡胶等。
(4)根据公司的要求来选择。
每个公司都有自己的供应商,包含材料供应商。
同一种产品,满足产品设计要求的材料由好几种,价格也不一样,而选用哪一种材料就要结合公司的实际情况来考虑。
选用合理的结构02产品结构设计不是越复杂越好,相反,在满足产品功能的前提下,结构越简单越好,越简单的结构在模具制作上就越容易,越简单的结构在生产装配上就越轻松,出现的问题也就越少。
【产品结构设计】玩具结构设计常见结构设计方法系列教程之一
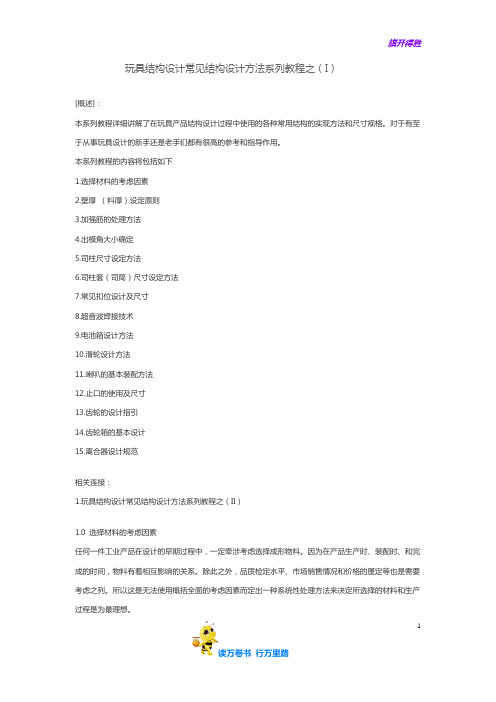
玩具结构设计常见结构设计方法系列教程之(I)[概述]:本系列教程详细讲解了在玩具产品结构设计过程中使用的各种常用结构的实现方法和尺寸规格。
对于有至于从事玩具设计的新手还是老手们都有很高的参考和指导作用。
本系列教程的内容将包括如下1.选择材料的考虑因素2.壁厚(料厚)设定原则3.加强筋的处理方法4.出模角大小确定5.司柱尺寸设定方法6.司柱套(司筒)尺寸设定方法7.常见扣位设计及尺寸8.超音波焊接技术9.电池箱设计方法10.滑轮设计方法11.喇叭的基本装配方法12.止口的使用及尺寸13.齿轮的设计指引14.齿轮箱的基本设计15.离合器设计规范相关连接:1.玩具结构设计常见结构设计方法系列教程之(II)1.0 选择材料的考虑因素任何一件工业产品在设计的早期过程中,一定牵涉考虑选择成形物料。
因为在产品生产时、装配时、和完成的时间,物料有着相互影响的关系。
除此之外,品质检定水平、市场销售情况和价格的厘定等也是需要考虑之列。
所以这是无法使用概括全面的考虑因素而定出一种系统性处理方法来决定所选择的材料和生产过程是为最理想。
11.1 不同材料的特性A。
ABS用途: 玩具、机壳、日常用品特性: 坚硬、不易碎、可涂胶水,但损坏时可能有利边出现。
(Fig. 1.1.2)设计上的应用: 多数应用于玩具外壳或不用受力的零件。
B.PP用途: 玩具、日常用品、包装胶袋、瓶子特性: 有弹性、韧度强、延伸性大、但不可涂胶水。
设计上的应用: 多数应用于一些因要接受跌落试验而拆件的地方。
2旗开得胜c.PVC用途: 软喉管、硬喉管、软板、硬板、电线、玩具Fig. 1.1.4(PVC)特性: 柔软、坚韧而有弹性。
设计上的应用: 多数用于玩具卡通公仔,或一些需要避震或吸震的地方D.POM (赛钢)用途: 机械零件、齿轮、家电外壳特性: 耐磨、坚硬但脆弱,损坏时容易有利边出现(Fig. 1.1.6)。
设计上的应用: 多数用于胶齿轮、滑轮、一些需要传动,承受大扭力或应力的地方E.Nylon (尼龙)用途: 齿轮、滑轮特性: 坚韧、吸水、但当水份完全挥发后会变得脆弱。
塑胶产品结构设计准则--支柱 ( Boss )

产品结构设计准则--支柱( Boss )基本设计守则支柱突出胶料壁厚是用以装配产品、隔开物件及支撑承托其他零件之用。
空心的支柱可以用来嵌入件、收紧螺丝等。
这些应用均要有足够强度支持压力而不致於破裂。
支柱尽量不要单独使用,应尽量连接至外壁或与加强筋一同使用,目的是加强支柱的强度及使胶料流动更顺畅。
此外,因过高的支柱会导致塑胶部件成型时困气,所以支柱高度一般是不会超过支柱直径的两倍半。
加强支柱的强度的方法”尤其是远离外壁的支柱,除了可使用加强筋外,三角加强块”Gusset plate的使用亦十分常见。
一个品质好的螺丝/支柱设计组合是取决於螺丝的机械特性及支柱孔的设计,一般塑胶产品的料厚尺寸是不足以承受大部份紧固件产生的应力。
固此,从装配的考虑来看,局部增加胶料厚度是有需要的。
但是,这会引致不良的影响,如形成缩水痕、空穴、或增加内应力。
因此,支柱的导入孔及穿孔”避空孔的位置应与产品外壁保持一段距离。
支柱可远离外壁独立而处或使用加强筋连接外壁,後者不但增加支柱的强度以支撑更大的扭力及弯曲的外力,更有助胶料填充及减少因困气而出现烧焦的情况。
同样理由,远离外壁的支柱亦应辅以三角加强块,三角加强块对改善薄壁支柱的胶料流动特别适用。
收缩痕的大小取决於胶料的收缩率、成型工序的叁数控制、模具设计及产品设计。
使用过短的哥针、增加底部弧度尺寸、加厚的支柱壁或外壁尺寸均不利於收缩痕的减少;不幸地,支柱的强度及抵受外力的能力却随着增加底部弧度尺寸或壁厚尺寸而增加。
因此,支柱的设计须要从这两方面取得平衡。
1) 支柱位置2) 支柱设计不同材料的设计要点ABS一般来说,支柱的外径是内径的两倍已足够。
有时这种方式结果支柱壁厚等於或超过胶料厚度而增加物料重量和在表面产生缩水纹及高成型应力。
严格的来说支柱的厚度应为胶料厚度的50-70%。
如因此种设计方式而支柱不能提供足够强度,但已改善了表面缩水。
斜骨是可以加强支柱的强度,可由最小的尺寸伸延至支柱高的90%。
树脂boss 柱加强筋设计

树脂boss 柱加强筋设计
树脂boss柱加强筋设计是指在树脂boss柱的结构设计中,通
过添加加强筋来增强其承载能力和稳定性。
这种设计通常用于工程
结构中,特别是在需要承受较大荷载或者受到外部力作用较大的情
况下。
首先,树脂boss柱是一种常见的结构支撑元素,通常用于建筑
物或其他工程结构中的支撑和连接。
而加强筋是指在柱的设计中添
加钢筋或其他材料来增加其强度和稳定性。
这种设计可以有效地提
高柱的承载能力和抗震性能,从而保证工程结构的安全可靠。
在进行树脂boss柱加强筋设计时,需要考虑多个方面。
首先是
结构的荷载特性,包括柱所承受的静载荷、动载荷以及可能的地震
荷载等。
其次是材料的选择,包括树脂的类型和强度等参数,以及
加强筋的材料和尺寸。
此外,还需要考虑柱的几何形状和尺寸,以
及加强筋的布置方式和数量等因素。
在实际设计中,需要进行结构分析和计算,确定加强筋的位置、数量和尺寸,以保证柱在各种荷载条件下的稳定性和安全性。
同时,还需要考虑施工工艺和成本等因素,选择合适的加强筋设计方案。
总的来说,树脂boss柱加强筋设计是一项复杂的工程设计任务,需要综合考虑结构特性、材料性能、荷载条件和施工工艺等多个方
面的因素。
通过合理的设计和施工,可以有效地提高树脂boss柱的
承载能力和稳定性,保证工程结构的安全可靠。
塑胶产品结构设计要点

塑胶产品结构设计要点1.胶厚(胶位):塑胶产品的胶厚(整体外壳)通常在0.80-3.00左右,太厚容易缩水和产生汽泡,太薄难走满胶,大型的产品胶厚取厚一点,小的产品取薄一点,一般产品取1.0-2.0为多。
而且胶位要尽可能的均匀,在不得已的情况下,局部地方可适当的厚一点或薄一点,但需渐变不可突变,要以不缩水和能走满胶为原则,一般塑料胶厚小于0.3时就很难走胶,但软胶类和橡胶在0.2-0.3的胶厚时也能走满胶。
2.xx(骨位):塑胶产品大部分都有加强筋,因加强筋在不增加产品整体胶厚的情况下可以大大增加其整体强度,对大型和受力的产品尤其有用,同时还能防止产品变形。
加强筋的厚度通常取整体胶厚的0.5-0.7倍,如大于0.7倍则容易缩水。
加强筋的高度较大时则要做0.5-1的斜度(因其出模阻力大),高度较矮时可不做斜度。
3.脱模斜度:塑料产品都要做脱模斜度,但高度较浅的(如一块平板)和有特殊要求的除外(但当侧壁较大而又没出模斜度时需做行位)。
出模斜度通常为1-5度,常取2度左右,具体要根据产品大小、高度、形状而定,以能顺利脱模和不影响使用功能为原则。
产品的前模斜度通常要比后模的斜度大0.5度为宜,以便产品开模事时能留在后模。
通常枕位、插穿、碰穿等地方均需做斜度,其上下断差(即大端尺寸与小端尺寸之差)单边要大于0.1以上。
4.圆角(R角):塑胶产品除特殊要求指定要锐边的地方外,在棱边处通常都要做圆角,以便减小应力集中、利于塑胶的流动和容易脱模。
最小R通常大于0.3,因太小的R模具上很难做到。
5.xx:从利于模具加工方面的角度考虑,孔最好做成形状规则简单的圆孔,尽可能不要做成复杂的异型孔,孔径不宜太小,孔深与孔径比不宜太大,因细而长的模具型心容易断、变形。
孔与产品外边缘的距离最好要大于1.5倍孔径,孔与孔之间的距离最好要大于2倍的孔径,以便产品有必要的强度。
与模具开模方向平行的孔在模具上通常上是用型心(可镶、可延伸留)或碰穿、插穿成型,与模具开模方向不平行的孔通常要做行位或斜顶,在不影响产品使用和装配的前提下,产品侧壁的孔在可能的情况下也应尽量做成能用碰穿、插穿成型的孔。
产品结构

可透明,易成形
脆性,可透明
轴承齿轮 、 油管 、 容器 、 日用品 机械配件 、 齿轮 、 拉丝 、 轴套 、 工具外壳 、 电器装置薄膜 装饰品 、 太阳镜片 、 文具 、 表面 、 仪器表外壳 、 灯罩 、 广告牌 机械 、 仪器 、 医疗器械 、 电讯器 材 、 防弹玻璃 、 咖啡壶外壳
白色,延性,易成形
2mm
1.4~1.5mm
2.5mm
1.8mm
3mm
2.1mm
Suzhou Victory Precision Manufacture Co., Ltd.
三、支柱(Boss) 支柱
支柱突出胶料壁厚是用以装配产品、隔开对象及支撑承托其它零件之用。空心的支 柱可以用来嵌入镶件、收紧螺丝等。这些应用均要有足够强度支持压力而不致于破裂。 支柱尽量不要单独使用,应尽量连接至外壁或与加强筋一同使用,目的是加强支柱 的强度及使胶料流动更顺畅。此外,因过高的支柱会导致塑料部件成形时困气,所以支 柱高度一般是不会超过支柱直径的2.5倍。 加强支柱的强度的方法(尤其是远离外壁的支柱),除了可使用加强筋外,加强块 的使用亦十分常见。
简 称
软胶(花料、筒料) LDPE 硬性软胶(孖力士) HDPE 橡皮胶 EVA 百折胶 PP 软质 PVC 硬质 PVC 尼龙单6 PA-6 尼龙孖6 PA-66 亚加力 PMMA 防弹胶 PC
中英文学名
低密度聚乙烯 Low Density Polyethylene 高密度聚乙烯 High Density Polyethylene 乙烯一醋酸乙烯酯共聚物 Ethylene-Vinyl Acetate 聚丙烯 Polypropylene 聚氯乙烯(约加40%增塑剂) Polyvinyl Chloride (Plasticized) 聚氯乙烯 Polyvinyl Chloride (Rigid) 聚 胺6 Polyamide-6 聚 胺66 Polyamide-66 聚甲基丙烯酸甲酯 Polymethy Methacrylate 聚碳酸酯 Polycarbonate
产品的支柱

产品的支柱基本的设计准则1.支柱一般用于装配产品、隔开物件及支撑承托其他零件之用。
空心的支柱一般用来嵌入件、收紧螺丝等。
2.支柱尽量不要单独使用,应尽量连接到外壁或与加强筋一同使用。
此外支柱高度不能超过支柱直径的两倍半。
3.支柱的位置应与产品外壁保持一段距离,可与加强筋连接外壁,可以起到增加支柱的强度作用。
4.支柱的设计如图:1).支柱的位置:2).支柱的设计:5.支柱也可以作为螺丝柱使用,主要起到零件间的紧固作用。
1. 塑胶螺丝柱参考尺寸。
A=公称直径X外径系数B=公称直径+约0.2mmC=公称直径X孔系数D=公称直径X螺纹深度系数2.螺丝柱相关的设计1).螺丝柱的拔模斜度一般在0.5°-2°如图所示:2).当螺丝柱高度远远大于螺丝长度时,螺丝的预孔也可以设计一定的拔模斜度。
3).当螺丝柱的长度过长(长度/直径>2)时,为了防止螺丝柱的断裂可以跟加强筋一起使用。
A.加强筋的典型尺寸如图所示:B.螺丝柱加强筋的几种形式:1.螺柱的四周无特殊限制时,加强筋最好如下图所示设计(模具的制造简单)。
2.结构限制时,可以如上右图所示设计。
3.当螺柱跟边壁较近时,设计可以如下图所示。
4.当几个螺柱相距很近,可以把几个螺柱用筋连接起来。
5.螺丝的预孔深度一般为壁厚的T/3-T/2,如下图所示。
6.其他说明:A.螺丝柱的经验:螺柱内径(ABS,ABS+PC)=螺丝外径-0.4mm;螺柱(PC)螺丝外径-0.3mm或0.35mm)。
B.螺柱外径=2x螺丝的外径(M2.5以下适用)。
C.螺柱的壁厚一般为塑料件壁厚的2/3。
D.在螺丝柱的顶面开孔处倒0.3X45°的倒角,起导向作用。
E.螺丝对应螺丝柱及其螺丝孔尺寸参考:不同材料的设计要点ABS:支柱的厚度一般是壁厚的50%-70%,但强度不够需要跟斜骨一起使用来增强支柱的强度。
斜骨的高度一般为支柱高度的90%。
若支柱跟边壁很近,则用加强筋跟边壁相连来达到加强支柱的强度。
BOSS柱设计之欧阳学创编
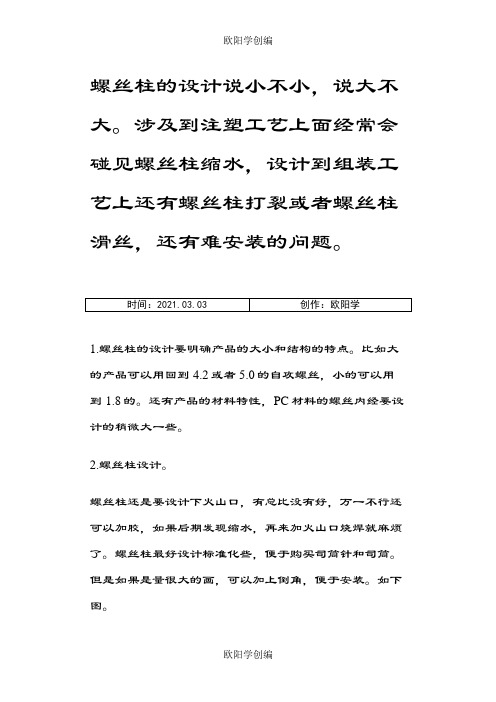
螺丝柱的设计说小不小,说大不大。
涉及到注塑工艺上面经常会碰见螺丝柱缩水,设计到组装工艺上还有螺丝柱打裂或者螺丝柱滑丝,还有难安装的问题。
1.螺丝柱的设计要明确产品的大小和结构的特点。
比如大的产品可以用回到4.2或者5.0的自攻螺丝,小的可以用到1.8的。
还有产品的材料特性,PC材料的螺丝内经要设计的稍微大一些。
2.螺丝柱设计。
螺丝柱还是要设计下火山口,有总比没有好,万一不行还可以加胶,如果后期发现缩水,再来加火山口烧焊就麻烦了。
螺丝柱最好设计标准化些,便于购买司筒针和司筒。
但是如果是量很大的画,可以加上倒角,便于安装。
如下图。
螺丝柱设计3.螺丝过孔的设计。
螺丝过孔要比螺丝大,这个大家都知道,但是有很多人设计螺丝配合的时候,不设计定位的,螺丝柱也没有倒角,生产线打螺丝打偏或者不容易定位。
建议设计一个圆形的定位筋。
如上图,C的间隙要稍微留大一些,0.2~0.3mm。
避免美工缝隙增大。
螺钉过孔最好做一个倒角,便于安装导入。
C角的作用一般可以在安装过程中起到倒入的作用。
4.螺丝柱内外径的设计,网上有很多要求,我觉得这个数据可以参考,尊重一个原则,便于加胶就行,减胶是太麻烦了,不确定的最好一个改模空间。
注:螺丝孔公称直径×系数比如ABS要设计一个ST3.0*8的螺钉,螺丝孔内径可以设计成3.0×0.8=2.4mm。
螺丝柱外径可以设计成:2.0×3.0=6mm。
这个只能作为参考,其实内径的可以作为参考,外径的就考虑螺丝柱的壁厚就行。
我们一般3.0自攻螺丝柱外径只需要5.0~5.3mm即可,太大就容易缩水了。
这样我们可以总结下就是5.2减去2.4再除以2就是螺丝柱的壁厚是1.4.壁厚太厚容易缩水,跟加强筋的设计有异曲同工之妙,不过螺丝柱要考虑强度,怕打裂。
5.螺丝柱的安规要求。
- 1、下载文档前请自行甄别文档内容的完整性,平台不提供额外的编辑、内容补充、找答案等附加服务。
- 2、"仅部分预览"的文档,不可在线预览部分如存在完整性等问题,可反馈申请退款(可完整预览的文档不适用该条件!)。
- 3、如文档侵犯您的权益,请联系客服反馈,我们会尽快为您处理(人工客服工作时间:9:00-18:30)。
产品结构设计准则--支柱( Boss )
基本设计守则
支柱突出胶料壁厚是用以装配产品、隔开物件及支撑承托其他零件之用。
空心的支柱可以用来嵌入件、收紧螺丝等。
这些应用均要有足够强度支持压力而不致於破裂。
支柱尽量不要单独使用,应尽量连接至外壁或与加强筋一同使用,目的是加强支柱的强度及使胶料流动更顺畅。
此外,因过高的支柱会导致塑胶部件成型时困气,所以支柱高度一般是不会超过支柱直径的两倍半。
加强支柱的强度的方法”尤其是远离外壁的支柱,除了可使用加强筋外,三角加强块”Gusset plate的使用亦十分常见。
一个品质好的螺丝/支柱设计组合是取决於螺丝的机械特性及支柱孔的设计,一般塑胶产品的料厚尺寸是不足以承受大部份紧固件产生的应力。
固此,从装配的考虑来看,局部增加胶料厚度是有需要的。
但是,这会引致不良的影响,如形成缩水痕、空穴、或增加内应力。
因此,支柱的导入孔及穿孔”避空孔的位置应与产品外壁保持一段距离。
支柱可远离外壁独立而处或使用加强筋连接外壁,後者不但增加支柱的强度以支撑更大的扭力及弯曲的外力,更有助胶料填充及减少因困气而出现烧焦的情况。
同样理由,远离外壁的支
柱亦应辅以三角加强块,三角加强块对改善薄壁支柱的胶料流动特别适用。
收缩痕的大小取决於胶料的收缩率、成型工序的叁数控制、模具设计及产品设计。
使用过短的哥针、增加底部弧度尺寸、加厚的支柱壁或外壁尺寸均不利於收缩痕的减少;不幸地,支柱的强度及抵受外力的能力却随着增加底部弧度尺寸或壁厚尺寸而增加。
因此,支柱的设计须要从这两方面取得平衡。
1)支柱位置
2)支柱设计
不同材料的设计要点
ABS
一般来说,支柱的外径是内径的两倍已足够。
有时这种方式结果支柱壁厚等於或超过胶料厚度而增加物料重量和
在表面产生缩水纹及高成型应力。
严格的来说支柱的厚度应为胶料厚度的50-70%。
如因此种设计方式而支柱不能提供足够强度,但已改善了表面缩水。
斜骨是可以加强支柱的强度,可由最小的尺寸伸延至支柱高的90%。
若柱位置接近边壁,则可用一条肋骨将边壁和柱相互连接来支持支柱。
PBT
支柱通常用於机构上装配,如收螺丝、紧压配合、导入装配等多数情形,支柱外径是内孔径的两倍就足够强壮。
支柱设计有如肋骨设计的观念。
太厚的切面会产生部件外缩水
和内部真空。
支柱的位置在边壁旁时可利用肋骨相连,则内孔径的尺寸可增至最大。
PC
支柱是大部份用来作装配产品用,有时用作支撑其它物件或隔开物体之用。
甚至一些很细小的支柱最终会热溶後作内部零件固定用。
一些放於边位的支柱是需耍一些肋骨作为互相依附,以增加支柱强度。
PS
支柱通常用於打入件,收螺丝,导向针,攻牙或作紧迫配合。
可能情形之下避免独立一支支柱而无任何支撑。
应加
一些肋骨以加强其强度。
若支柱离边壁不远应以肋骨将柱和边相连在一起。
PSU
支柱是用作连接两件部件的。
其外径应是内孔径的两倍,高度不应超过外径的两倍。