高速切削发展的瓶颈——刀具
超高速切削技术对刀具设计的挑战与机遇
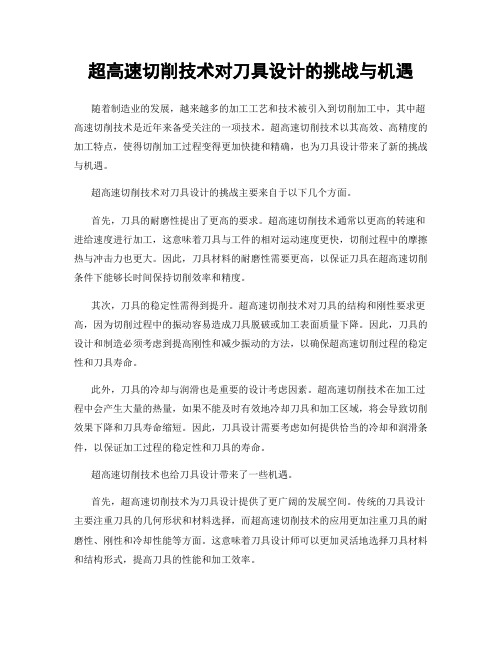
超高速切削技术对刀具设计的挑战与机遇随着制造业的发展,越来越多的加工工艺和技术被引入到切削加工中,其中超高速切削技术是近年来备受关注的一项技术。
超高速切削技术以其高效、高精度的加工特点,使得切削加工过程变得更加快捷和精确,也为刀具设计带来了新的挑战与机遇。
超高速切削技术对刀具设计的挑战主要来自于以下几个方面。
首先,刀具的耐磨性提出了更高的要求。
超高速切削技术通常以更高的转速和进给速度进行加工,这意味着刀具与工件的相对运动速度更快,切削过程中的摩擦热与冲击力也更大。
因此,刀具材料的耐磨性需要更高,以保证刀具在超高速切削条件下能够长时间保持切削效率和精度。
其次,刀具的稳定性需得到提升。
超高速切削技术对刀具的结构和刚性要求更高,因为切削过程中的振动容易造成刀具脱破或加工表面质量下降。
因此,刀具的设计和制造必须考虑到提高刚性和减少振动的方法,以确保超高速切削过程的稳定性和刀具寿命。
此外,刀具的冷却与润滑也是重要的设计考虑因素。
超高速切削技术在加工过程中会产生大量的热量,如果不能及时有效地冷却刀具和加工区域,将会导致切削效果下降和刀具寿命缩短。
因此,刀具设计需要考虑如何提供恰当的冷却和润滑条件,以保证加工过程的稳定性和刀具的寿命。
超高速切削技术也给刀具设计带来了一些机遇。
首先,超高速切削技术为刀具设计提供了更广阔的发展空间。
传统的刀具设计主要注重刀具的几何形状和材料选择,而超高速切削技术的应用更加注重刀具的耐磨性、刚性和冷却性能等方面。
这意味着刀具设计师可以更加灵活地选择刀具材料和结构形式,提高刀具的性能和加工效率。
其次,超高速切削技术的应用需要更高的自动化和智能化水平。
刀具设计需要与加工机床的控制系统紧密配合,以实现刀具状态的实时监测和自适应控制。
这为刀具设计师提供了机会,可以通过引入传感器、控制算法和智能化软件等技术手段,提高刀具在超高速切削过程中的稳定性和加工效率。
最后,超高速切削技术也带来了刀具寿命的延长。
2022年中国五金刀具企业发展面临的五大瓶颈

中国五金刀具企业发展面临的五大瓶颈目前,中国刀具企业通过不断地学习和战略规划,已经在市场上占据了半壁江山,不过,国际模协秘书长罗百辉日前指出,企业在进展过程中还是凸显出五大致命瓶颈,假如重视不够、处理不当,将会严峻影响到企业的进展和前进。
1、产品附加价值低2022年,我国生产的1.65万吨硬质合金中,有4500吨用于切削刀具生产上,数量上和日本相当。
但制成刀具后的价值仅8亿美元,远不及日本的25亿美元,这充分说明国内硬质合金高效刀具的整体生产水平与国外仍有相当大的差距。
所以,在国内企业不能满意市场需求的前提下,制造业的需求就不得不依靠大量进口来解决。
有资料显示,主要外商在中国中高端刀具市场上的销售年增长率达30%,已超过国产刀具的年均增长水平。
2、科技技术含量低现阶段,硬质合金刀具在发达国家已占刀具类型的主导地位,比重高达70%。
而高速钢刀具却正以每年1%~2%的速度缩减,所占比例目前已降至30%以下。
同时,硬质合金切削刀具在我国也已经成为加工企业所需的主力刀具,被广泛地应用在汽车及零部件生产、模具制造、航空航天等重工业领域,但我国刀具企业却盲目地、大量地生产高速钢刀以及一些低档标准刀具,完全没有考虑到市场饱和度和企业所需,最终把具有高附加值、高科技含量的中高端刀具市场“拱手相让”给国外企业。
据罗百辉透露,我国刀具目前的年销售额大约为145亿元,其中硬质合金刀具所占的比重不足25%,但国内制造业所需的硬质合金刀具已经占据刀具的50%以上,这种盲目生产已经严峻满意不了国内制造业对硬质合金刀具日益增长的需求,从而形成了中高端市场的真空状态,最终被国外企业所占据。
3、服务与国际不接轨跨国企业,如德国雄克、日本黛杰、丹麦尤尼莫克等刀具生产企业,在漫长的历史进展中已经积累了丰富的生产阅历,这也就打算了其服务形式不再是“一锤子买卖”,而是超越了只供应给客户刀具的初级销售阶段,依据客户在生产过程中遇到的刀具方面的问题,准时地提出解决方案,这种把销售融入到企业生产过程中的高级形式已成为国外企业惯用的销售方式,这也是为什么知名刀具企业所生产的产品贵而有市,部分中国企业虽“量大面广”却不能赢得客户的青睐的缘由之一。
高速切削技术对刀具性能的挑战与改进
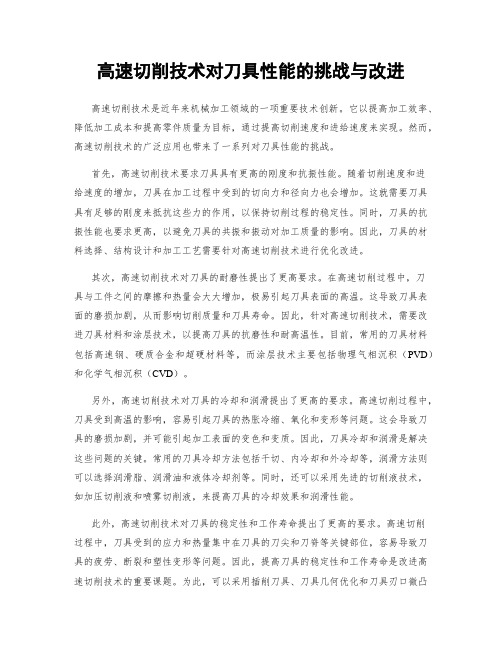
高速切削技术对刀具性能的挑战与改进高速切削技术是近年来机械加工领域的一项重要技术创新。
它以提高加工效率、降低加工成本和提高零件质量为目标,通过提高切削速度和进给速度来实现。
然而,高速切削技术的广泛应用也带来了一系列对刀具性能的挑战。
首先,高速切削技术要求刀具具有更高的刚度和抗振性能。
随着切削速度和进给速度的增加,刀具在加工过程中受到的切向力和径向力也会增加。
这就需要刀具具有足够的刚度来抵抗这些力的作用,以保持切削过程的稳定性。
同时,刀具的抗振性能也要求更高,以避免刀具的共振和振动对加工质量的影响。
因此,刀具的材料选择、结构设计和加工工艺需要针对高速切削技术进行优化改进。
其次,高速切削技术对刀具的耐磨性提出了更高要求。
在高速切削过程中,刀具与工件之间的摩擦和热量会大大增加,极易引起刀具表面的高温。
这导致刀具表面的磨损加剧,从而影响切削质量和刀具寿命。
因此,针对高速切削技术,需要改进刀具材料和涂层技术,以提高刀具的抗磨性和耐高温性。
目前,常用的刀具材料包括高速钢、硬质合金和超硬材料等,而涂层技术主要包括物理气相沉积(PVD)和化学气相沉积(CVD)。
另外,高速切削技术对刀具的冷却和润滑提出了更高的要求。
高速切削过程中,刀具受到高温的影响,容易引起刀具的热胀冷缩、氧化和变形等问题。
这会导致刀具的磨损加剧,并可能引起加工表面的变色和变质。
因此,刀具冷却和润滑是解决这些问题的关键。
常用的刀具冷却方法包括干切、内冷却和外冷却等,润滑方法则可以选择润滑脂、润滑油和液体冷却剂等。
同时,还可以采用先进的切削液技术,如加压切削液和喷雾切削液,来提高刀具的冷却效果和润滑性能。
此外,高速切削技术对刀具的稳定性和工作寿命提出了更高的要求。
高速切削过程中,刀具受到的应力和热量集中在刀具的刀尖和刀脊等关键部位,容易导致刀具的疲劳、断裂和塑性变形等问题。
因此,提高刀具的稳定性和工作寿命是改进高速切削技术的重要课题。
为此,可以采用插削刀具、刀具几何优化和刀具刃口微凸等工艺,来改善刀具的加工能力和稳定性。
高速切削技术对金属切削效果的提升及挑战

高速切削技术对金属切削效果的提升及挑战随着现代制造业的迅速发展,对金属切削工艺的要求也越来越高。
高速切削技术作为一种先进的金属切削加工方式,极大地提升了金属切削的效果和效率。
然而,高速切削技术也面临着一些挑战。
本文将就高速切削技术对金属切削效果的提升及面临的挑战进行探讨。
高速切削技术通过增加切削速度,缩短了切削时间,提高了金属切削的效率。
其核心思想是在提高切削速度的同时,保持刀具与工件之间的切割力和摩擦力在较低的水平上,以减少切削时产生的热量和切削力。
这一技术的应用使得金属切削中的切削时间大幅缩短,生产效率大大提高。
高速切削技术对金属切削效果的提升主要表现在以下几个方面:首先,高速切削技术能够实现更高的表面质量。
传统的切削加工会在切削过程中留下很多痕迹和划痕,导致工件表面质量较低。
而高速切削技术通过提高切削速度和合理选择刀具材料,可以有效减少划痕和痕迹的产生,从而提高金属表面的质量。
其次,高速切削技术可以实现更高的切削精度。
传统切削加工通常需要进行二次加工或者精修来达到所需的尺寸精度。
而高速切削技术通过控制刀具的运动速度和切削参数,能够在一次加工中达到更高的切削精度,从而减少了加工的工序,提高了生产效率。
此外,高速切削技术还可以实现更高的加工精度。
高速切削技术在切削过程中,由于切削速度高,所以切削时产生的切削力相对较小,这就减少了工件的变形和热膨胀,提高了加工精度。
同时,高速切削技术可通过调整切削参数提高切削的稳定性和一致性,从而减少加工误差,提高了加工的精度。
然而,高速切削技术也面临着一些挑战。
首先是刀具磨损问题。
高速切削技术要求刀具在高速运动下具有较长的工作寿命和较高的耐磨性。
然而,由于切削速度高,切削时的温度和切削力也较大,这会导致刀具磨损更快。
因此,选择合适的刀具材料和涂层技术,以及合理的冷却和润滑措施,对于提高刀具的耐磨性非常重要。
其次是加工精度和稳定性问题。
高速切削技术对刀具的刚性和动态平衡性要求较高,要保证加工的精度和稳定性。
高速切削刀具材料的进展和未来

高速切削刀具材料的进展和未来Progress and Prospect of High_speed Cutting Tool Material艾 兴 刘战强 赵 军 邓建新 宋世学(山东大学机械工程学院)摘 要:文章结合高速切削技术和刀具材料的研究,综述了高速切削刀具材料的进展和应用,阐明了我国高速切削刀具材料面临的机遇和挑战,指出了高速切削刀具材料的未来。
关键词:高速切削 刀具材料1 概况机械加工发展的总趋势是高效率、高精度、高柔性和强化环境意识。
在机械加工领域,切(磨)削加工是应用最广泛的加工方法。
高速切削是切削加工的发展方向,已成为切削加工的主流。
它是先进制造技术的重要共性关键技术。
推广应用高速切削技术将大幅度提高生产效率和加工质量并降低成本。
高速切削技术的发展和应用决定于机床和刀具技术的进步,其中刀具材料的进步起决定性的作用[1]。
研究表明[2、9],高速切削时,随着切削速度的提高,切削力减小,切削温度上升很高,达到一定值后上升逐渐趋缓[2]。
造成刀具损坏最主要的原因是切削力和切削温度作用下的机械摩擦、粘结、化学磨损、崩刃、破碎以及塑性变形等磨损和破损,因此高速切削刀具材料最主要的要求是高温时的力学性能、热物理性能、抗粘结性能、化学稳定性(氧化性、扩散性、溶解度等)和抗热震性能以及抗涂层破裂性能等。
基于这一要求,近20多年来,发展了一批适于高速切削的刀具材料,可在不同切削条件下,切削加工各种工件材料[3、4、7]。
目前,可以2500~5000m/min的高速切削铝合金(Si含量 12%,大于12%的为500~1500m/min);以500~1500m/min切削铸铁;300~1000m/min切削钢;100~400m/min切削淬硬钢、耐热合金;90~200m/min切削钛合金等。
当然人们还期待着以超高切削速度进行加工而获得更好的效果。
2 国外高速切削刀具材料的进展和应用高速切削时,对不同的工件材料选用与其合理匹配的刀具材料和允许的切削条件,才能获得最佳的切削效果。
高速切削技术与刀具设计优化的研究进展
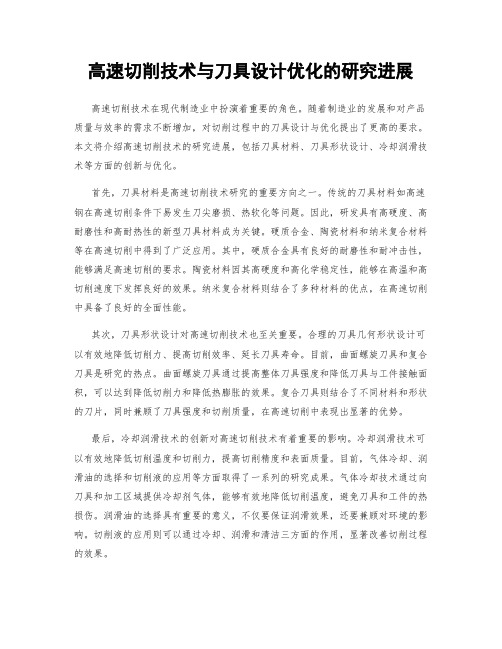
高速切削技术与刀具设计优化的研究进展高速切削技术在现代制造业中扮演着重要的角色。
随着制造业的发展和对产品质量与效率的需求不断增加,对切削过程中的刀具设计与优化提出了更高的要求。
本文将介绍高速切削技术的研究进展,包括刀具材料、刀具形状设计、冷却润滑技术等方面的创新与优化。
首先,刀具材料是高速切削技术研究的重要方向之一。
传统的刀具材料如高速钢在高速切削条件下易发生刀尖磨损、热软化等问题。
因此,研发具有高硬度、高耐磨性和高耐热性的新型刀具材料成为关键。
硬质合金、陶瓷材料和纳米复合材料等在高速切削中得到了广泛应用。
其中,硬质合金具有良好的耐磨性和耐冲击性,能够满足高速切削的要求。
陶瓷材料因其高硬度和高化学稳定性,能够在高温和高切削速度下发挥良好的效果。
纳米复合材料则结合了多种材料的优点,在高速切削中具备了良好的全面性能。
其次,刀具形状设计对高速切削技术也至关重要。
合理的刀具几何形状设计可以有效地降低切削力、提高切削效率、延长刀具寿命。
目前,曲面螺旋刀具和复合刀具是研究的热点。
曲面螺旋刀具通过提高整体刀具强度和降低刀具与工件接触面积,可以达到降低切削力和降低热膨胀的效果。
复合刀具则结合了不同材料和形状的刀片,同时兼顾了刀具强度和切削质量,在高速切削中表现出显著的优势。
最后,冷却润滑技术的创新对高速切削技术有着重要的影响。
冷却润滑技术可以有效地降低切削温度和切削力,提高切削精度和表面质量。
目前,气体冷却、润滑油的选择和切削液的应用等方面取得了一系列的研究成果。
气体冷却技术通过向刀具和加工区域提供冷却剂气体,能够有效地降低切削温度,避免刀具和工件的热损伤。
润滑油的选择具有重要的意义,不仅要保证润滑效果,还要兼顾对环境的影响。
切削液的应用则可以通过冷却、润滑和清洁三方面的作用,显著改善切削过程的效果。
综上所述,高速切削技术与刀具设计优化的研究进展主要包括刀具材料、刀具形状设计和冷却润滑技术等方面的创新与优化。
从传统的高速钢到硬质合金、陶瓷材料和纳米复合材料的应用,从常规的刀具形状到曲面螺旋刀具和复合刀具的设计,再到气体冷却和切削液的应用,各个方面的进展都为高速切削技术的发展提供了坚实的支撑。
高速切削刀具的发展现状

质合金焊接刀具的应用仍十分普遍;铝高速钢、粉末冶金高速钢的使用很少;由于市场供应的国产高速钢质量下滑,使含钴高速钢刀具品质较差;高性能硬质合金及细(超细)颗粒硬质合金较少,几乎无专用牌号。
我国的刀具涂层技术与国外相比差距较大,金刚石膜涂层技术尚处于研发阶段;尚无商品化TiCN涂层产品;TiAIN、MoS2涂层、纳米涂层等新技术尚待研究;具有优良耐磨性、抗高温、抗热震性的高速切削刀具材料也函待开发。
国内对于陶瓷刀具的研究较为充分,已基本建立了融切削学和陶瓷学为一体的、基于切削可靠性的陶瓷刀具材料设计、研究理论新体系。
国产氧化铝基陶瓷刀具已有近20个品种(部分产品性能及用途见表3) ,氮化硅基陶瓷刀具已有近10 个品种,陶瓷刀具的生产能力也较大。
目前陶瓷刀具的研发水平已达到国际先进水平,陶瓷刀具的性能水平也不低于国外同类产品。
已开发成功陶瓷—硬质合金复合刀片、梯度功能陶瓷刀片、多种采用协同增韧机理的陶瓷刀具等国外尚未见报道的新产品。
目前与国外的差距主要表现在制造工艺水平较低,高精度陶瓷刀片和某些品种的陶瓷刀具(如加入氮化物的陶瓷刀具)质量欠佳,陶瓷刀具的推广应用也不如发达国家普遍。
国内已开发出可分别用于车削、镗削、铣削等加工领域的多种不同CBN含量的CBN刀具和不同颗粒尺寸的PCD刀具,其中CBN刀具主要用于高速加工淬硬钢、高硬铸铁及某些难加工材料,PCD刀具则用于加工铝合金。
不足之处是品种规格不够齐全,某些产品质量欠佳,推广应用尚不普遍。
高速切削的技术装备作者:佚名文章来源:网络转载点击数: 112 更新时间:2006-4-24内容摘要: 高速切削(High Speed Cutting-HSC)概念起源于德国切削物理学家Carl Salomn的著名切削实验及其物理引伸。
他认为一定的工作材料对应有一个临界切削速度,其切削温度最高。
在常规切削范围内切削温度Tv随着切削速度Vc的增大而提高,当切削速度到达临界切削速度后,切削速度再增大,切削温度反而下降(见图1C区),所以越过B区,在高速区C区进行切削,则可用现有的刀具进行高速切削,从而大大地减少切削工时,成倍提高机床的生产率,同时提高加工质量管理,并可用于切削各种硬、韧性、难加工材料的工件。
我国超硬刀具高速切削技术发展现状、问题及前景
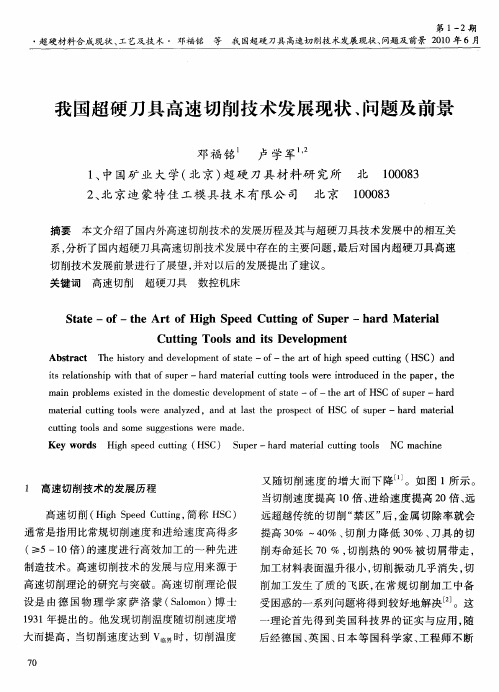
・
超 硬材料合 成现状 、 艺及技 术 ・ 邓福铭 工
等
我 国超硬 刀具 高速切 削技术发展现状 、 问题及前景 2 1 6月 0 0年
我国超硬刀具高速切 削技术发 展现状 、 问题及前景
邓 福铭 卢 学军 ’
1 中国矿 业 大学 ( 、 北京 ) 硬 刀 具材 料研 究 所 北 10 8 超 003 2 北 京迪 蒙特 佳 工模 具技 术 有 限公 司 北京 10 8 、 003
又 随切 削 速 度 的增 大 而 下 降 j 。如 图 1所 示 。
当切削速度提高 1 、 O倍 进给速度提高 2 O倍 、 远
高速切 削 ( ihSedC tn , Hg pe ut g 简称 H C) i S
通 常是 指 用 比常规 切 削 速 度 和 进 给 速 度 高 得 多
摘要 本文介绍 了国内外高速切削技术 的发展历程及其与超硬刀具 技术发展 中的相互关
系, 分析了国内超硬刀具高速切削技术发展 中存在 的主要问题 , 最后对 国内超硬刀具高速
切削技术发展前景进行 了展望 , 并对 以后的发展提出了建议 。 关键词 高速切削 超硬刀具 数控机床
St t 一 0 ae f— t e Ar fH ih e d Cuti f S pe —ha d M a e i l h to g Sp e tng o u r r t ra
提高切削效率 、 降低 生产成本 。因此 , 改进刀具
材料对于降低切削成本 比其它任何单一 过程 的
礴
疆 签
改变更具 潜力 , 如何 合理 地选 择 与应用 现代 刀
具材料是降低加工成本 、 获得经济效益 的关键 。
无独有偶 的是 , 上世 纪七十年代 中期 , 在美
高速高效切削加工技术的现状及发展趋势

高速高效切削加工技术的现状及发展趋势一、前言目前,我国已成为世界飞机零部件的重要转包生产国,波音、麦道、空客等世界著名飞机制造公司都在我国转包生产从尾翼、机身、舱门到发动机等各种零部件,这些飞机零部件的加工生产必须采用先进的加工装备和加工工艺。
为此,国内各飞机制造公司均进行了大规模的技术改造,引进了大量国外先进的加工装备,使我国的飞机制造业设备的数控化率越来越高。
与此同时,大量高速、高效、柔性、复合、环保的国外切削加工新技术不断涌现,使切削加工技术发生了根本的变化。
刀具在航空航天加工领域的应用技术进入了以发展高速切削、开发新的切削工艺和加工方法、提供成套技术为特征的新阶段。
与此形成鲜明对比的是,我国的装备制造业和以制造业为主要服务对象的传统的工具工业却无法满足航空航天工业对现代制造装备和先进加工工艺的要求。
下面结合我国航空航天工业加工技术的现状及发展趋势,着重介绍我国高效、高速切削刀具的生产应用情况,对我国工具工业的发展现状和存在的问题提出自己的看法。
二、航空航天工业加工技术的现状及发展趋势1.航空结构件材料的发展趋势及其特点①以整体件为代表的铝合金结构件为了提高零件的可靠性、降低成本和减轻重量,传统的铆接结构逐步被整体薄壁的机加工结构件所代替。
这类零件由于大部分是用整体实心铝合金材料制成的薄壁、细筋结构件,70%~95%的材料要在加工中去除掉,而高速切削产生的热量少、切削力小、零件变形小,因此提高生产效率的唯一途径是采用四轴或五轴联动机床进行高速铣削加工。
②以钛基和镍基合金零件为代表的难切削材料零件由于钛(镍)合金具有比强度高、热强度好、化学活性大等特点,目前飞机发动机重要部件采用钛基和镍基合金材料的逐渐增多。
采用高速切削后,其切削速度可提高到100m/min以上,为常规切削速度的10倍。
这类材料的加工特点是:切削力大、切削温度高、加工硬化和粘刀现象严重、刀具易磨损。
③以碳纤维复合材料零件为代表的复合材料结构件复合材料现已成为新一代飞机机体结构主要材料之一,如飞机上的大型整体成形的翼面壁板、带纵墙的整体下翼面等。
浅谈高速切削中刀具的选择

浅谈高速切削中刀具的选择【摘要】高速切削技术目前在机械加工领域占有十分重要的地位,在高速切削中刀具的选择直接关系到机械加工的质量,本文对高速切削中刀具的发展现状以及刀具材料的选择,和在数控加工中的应用情况进行了简要探讨。
【关键词】高速切削;刀具;材料选择1 高速切削技术的优势高速切削技术具有加工效率高、精准度高、成本低等特点,目前在机械加工领域有着广泛的应用。
高速切削加工的具体优势如下:1.1 在生产效率上有很大的提高。
1.2 切削力有一定程度的降低。
尤其是径向切削分力大幅度减少,特别有利于提高薄壁件、细长件等刚性差的零件的加工精度。
1.3 由于95%-98%以上的切削热来不及传给工件而被切屑带走,故特别适合于加工容易热变形的零件;1.4 高速切削时,机床的激振频率特别高,远离了工艺系统的固有频率,因而工作平稳,振动小,加工的零件表面质量高。
1.5 适用于很多难加工的材料。
1.6 加工成本降低。
2 高速切削刀具选择的重要性高速切削加工中刀具的选择时基础,是保证机械加工质量的关键。
在加工中尤其要注意刀具的选择,如果选择了不适合的刀具,会导致机械加工的效率和质量都有所降低。
由于高速切削的切削速度快,而高速加工线速度主要受刀具限制,因为在目前机床所能达到的高速范围内,速度越高,刀具的磨损越快。
因此,高速切削对刀具材料提出了更高的要求,除了具备普通刀具材料的一些基本性能之外,还应突出要求高速切削刀具具备高的耐热性、抗热冲击性、良好的高温力学性能及高的可靠性。
高速切削技术的发展在很大程度上得益于超硬刀具材料的出现及发展。
目前常用的高速切削刀具材料有:聚晶金刚石(pcd)、立方氮化硼(cbn)、陶瓷、涂层刀具、超细晶粒硬质合金等刀具材料。
3 高速切削刀具材料的要求3.1 刀具材料的基本性能要求刀具的选择是加工的基础,而材料的选择是刀具的基础。
刀具材料对机械加工的质量有着直接的影响,而且对刀具本身的寿命也有很大作用。
高速切削技术及刀具的发展现状综述

在传统 的机械加工中, 刀具材料、 刀具 结构 和 刀具几何形状是决 定刀具切削性能的三大要求 , 其
中刀具材料起着关键作用 。近年来 , 各种难加工材 料的出现和应用 , 先进制造系统 、 高速切削的发展
夹持系统 , 高效高精 度测试测量技术 , 高性能刀具
产品及先进的切削技术等等。只有在这些技术充
Vno J 2 02 a0 1N .0 8. .8
高速切削技术及刀具的发展现状综述
张士孝
( 西安航空职业技术 学院 ,陕西 西安 7 0 8 ) 109
摘要 :切 削刀具在航空加 工领域的应用技 术进 入了以发 展高速切 削 、 开发新 的切削工艺和加工方法 、 提供成 套技术为特征的新阶段。本文介绍高速切削的刀具材料 、 涂层技术 、 创新刀具 结构 、 削加工 配套技术 等先进 的 切 切削技术及刀具的发展现状 。 关键词 : 切削技术 ; 高速 切削 ; 刀具 ; 材料 ; 涂层
分发展的基础上 , 建立起来的高速切削技术才具有
与付诸实用 , 都对刀具材料提出了更高、 更新的要 求。刀具材料通常被分为五大类 : 高速钢、 硬质合
金、 金属陶瓷、 陶瓷和超硬材料。
真正的意义。所 以要发挥 出高速切削 的优越性必
须是各方面技术的完美组合 。同时, 刀具在航空加
收稿 日 : 0 — 3— 0 期 2 8 0 2 0 作 者简介 : 士孝 (9 9 , , 张 15 一) 男 陕西西安人 , 经济师 , 研究方 向为校 办企业 的建设及产品开发。
1 刀具 材 料 、
示出独特的优越性。首先 , 切削效率成倍提高 ; 其 次, 高速切削有利于提高产品质量、 降低制造成本、 缩短交货周期 l 。事实上 , 1 】 高速切 削技术 是一个 非常庞大而复杂的系统工程 , 它涵盖了机床结构设 计和制造技术 , 高精度快速进给系统 , 高性能 刀具
高速切削加工技术和刀具技术的发展探讨

成本 1 %~1%。高速加 工普 通钢 和铸铁 的切削速度 为 5 0~ 0 5 0 2 0 mmi 钻 、 为 10~ 0 m m n 攻 丝 为 10 / i, 齿 0 0 / n( 铰 0 4 0 / i, 0 m mn 滚
为 3 0~6 0 / i)淬 硬钢(5~6 H C为 1 0 0 m mn 结 0 0 m m n, 3 5 R ) ~4 0 / l, 0 构 铝 合 金 为 30 0 0~4 0 m m n 高 硅 铝 合 金 为 5 0~ 0 0 / i, 0
广有现实的意义 。 近年 中国在刀具材料开发方面已有长足 进步 , 并开发包括 C D金刚石薄膜在 内的涂层 刀具 和厚膜金 刚石刀片 、i(, ) V T C N
切削加工用干式加工 , 的制造成本可 降低 1 %。因此 , 总 . 6 干切 削是未来切削加工 的主要方 向。 但是 当前倡导 的干切削并不是 简单地把原有工艺 中的切削液去掉 , 也不是 消极地靠降低切削 参数来保证刀具的使用寿命 , 而是用全新耐热性更好 的刀具材 料及涂层 , 设计合理 的刀具结构及 几何参数 , 选择最佳 的切削
10 m mi,镍基 、钴基 、铁基 和钛合金 等超 级合金 为 9 50 / n 0~
50rm n 0 r i。高速加工追求 的切削速度 目标是 : d 铣削一加 工铝及 其 合 金 为 10 0 / i, 铸 铁 为 50 m mn 普 通 钢 为 00 m mn 0 0 / i, 20 m mi;钻 削一 加 工 铝 及 其 合 金 的机 床 主 轴 转 速 为 50 / n 30 0/i , 铁为 2 0 O/ i, 00r n铸 m 0 0 f n 普通钢 为 1 00/ n a r 0 0 r 。大进 给 mi 目标 :进 给 速 度 V = 0~ 0m mi,每 齿 进 给 量 f=1 f2 5 / n z . 0~
高速切削刀具的发展现状与技术研究

高速切削刀具的发展现状与技术研究作者:冯剑来源:《科学与财富》2020年第09期摘要:本文将通过告诉切削刀具在工业制造业的实际应用、刀具材料、刀具结构等方面对高速切削刀具的现状进行分析,并对高速切削刀具的动平衡技术进行重点介绍。
关键词:高速切削刀具;现状分析;技术研究引言:当前工业机械零件的主要是通过切削、磨削等技术手段完成的,而高速切削刀具技术凭借其自身的优势必将成为切削加工的主要发展方向——在对零件高速切削加工中,能够有效的降低刀具切削的力度,控制刀具切削温度上升速度,提高加工零件的表面质量,实现零件加工成本控制。
为更好的实现零件的高速化切削加工,还需要对高速切削刀具进行不断的研发,探求更适合高速切削刀具的新型材料,改进高速切削刀具结构,提升高速切削刀具工业应用技术。
1.高速切削刀具发展现状1.1.高速切削技术的实际应用现状“高速切削”正以无可比拟的优势逐步成为模具制造业与飞机制造业的“得力干将”。
高速切削在航空领域成功替代了焊接技术,有效降低了零件的焊缝率,提高了零件的可靠性、抗震性与零件自身强度。
高速切削技术在汽车工业的应用,在很大程度上成为了汽车产品更新换代的关键技术。
在新车型设计投产后,高速切削技术能够通过缩短模具制造周期,加快汽车新产品的上市速度,帮助汽车企业在产品更新换代中更好地满足消费者需求,提升产品的市场竞争力。
由此可见,告诉切削技术在航空、汽车生产领域的应用,可以帮助企业更好地适应市场个性化需求,产品单一、生产数量巨大的传统产业模式正在逐步向多品种、多批量转变,又过去传统的组合机床刚性生产朝着柔性生产与高速加工转变。
1.2.刀具材料现状高速钢、硬质合金是当前我国高速切削刀具最普遍的制作材料,尤其是硬质合金焊接刀具最常见,在工业生产当中几乎不会选择粉末冶金高速钢、铝高速钢等。
近年来,国产的高速钢自身品质降低,直接造成含钴高速钢刀具质量下降;高性能硬质合金、细颗粒硬质合金的产量较低,无法成为高速切削刀具的主流材料。
高速切削过程中的刀具磨损分析
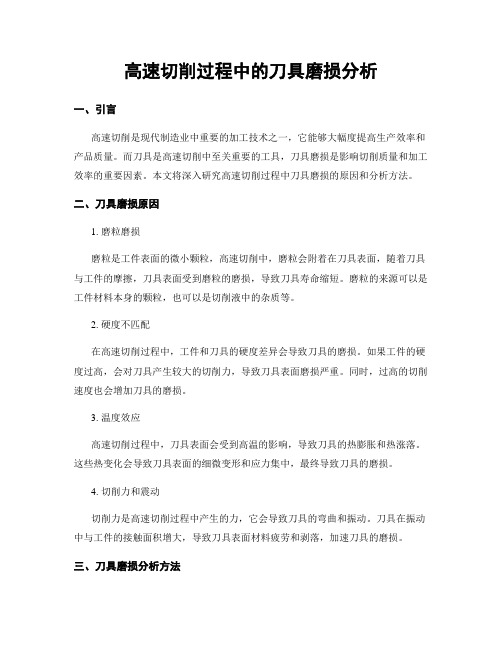
高速切削过程中的刀具磨损分析一、引言高速切削是现代制造业中重要的加工技术之一,它能够大幅度提高生产效率和产品质量。
而刀具是高速切削中至关重要的工具,刀具磨损是影响切削质量和加工效率的重要因素。
本文将深入研究高速切削过程中刀具磨损的原因和分析方法。
二、刀具磨损原因1. 磨粒磨损磨粒是工件表面的微小颗粒,高速切削中,磨粒会附着在刀具表面,随着刀具与工件的摩擦,刀具表面受到磨粒的磨损,导致刀具寿命缩短。
磨粒的来源可以是工件材料本身的颗粒,也可以是切削液中的杂质等。
2. 硬度不匹配在高速切削过程中,工件和刀具的硬度差异会导致刀具的磨损。
如果工件的硬度过高,会对刀具产生较大的切削力,导致刀具表面磨损严重。
同时,过高的切削速度也会增加刀具的磨损。
3. 温度效应高速切削过程中,刀具表面会受到高温的影响,导致刀具的热膨胀和热涨落。
这些热变化会导致刀具表面的细微变形和应力集中,最终导致刀具的磨损。
4. 切削力和震动切削力是高速切削过程中产生的力,它会导致刀具的弯曲和振动。
刀具在振动中与工件的接触面积增大,导致刀具表面材料疲劳和剥落,加速刀具的磨损。
三、刀具磨损分析方法1. 微观表面分析通过对刀具表面的显微结构分析,可以观察到刀具微观磨损的形态和特征。
可以使用光学显微镜、扫描电子显微镜等设备,观察刀具表面的磨痕、裂纹和变形等。
通过对磨损特征的分析,可以判断刀具磨损的主要原因。
2. 瑕疵检测通过对刀具表面瑕疵的检测,可以分析刀具磨损的程度和形式。
可以使用红外无损检测、超声波检测等技术,对刀具表面的微小裂纹和伤痕进行检测。
通过检测结果可以判断刀具的剩余寿命和使用情况。
3. 化学分析通过对刀具表面和切削液中主要元素和化合物的成分分析,可以了解刀具磨损的化学机理。
磨粒的成分分析可以帮助确定磨粒的来源和对刀具的磨损程度。
切削液中杂质的成分分析可以判断杂质对刀具的磨损效果。
4. 数值模拟数值模拟是一种常用的刀具磨损分析方法,通过使用有限元法等数值分析工具,对刀具和切削过程进行模拟计算。
刀具高速切削过程中强制停止的原因
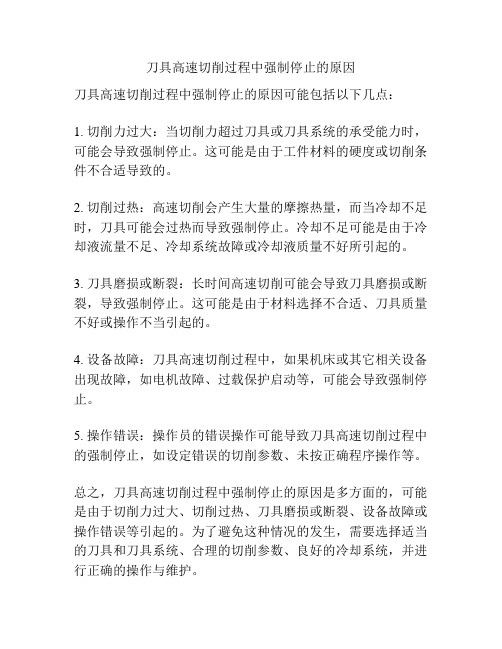
刀具高速切削过程中强制停止的原因
刀具高速切削过程中强制停止的原因可能包括以下几点:
1. 切削力过大:当切削力超过刀具或刀具系统的承受能力时,可能会导致强制停止。
这可能是由于工件材料的硬度或切削条件不合适导致的。
2. 切削过热:高速切削会产生大量的摩擦热量,而当冷却不足时,刀具可能会过热而导致强制停止。
冷却不足可能是由于冷却液流量不足、冷却系统故障或冷却液质量不好所引起的。
3. 刀具磨损或断裂:长时间高速切削可能会导致刀具磨损或断裂,导致强制停止。
这可能是由于材料选择不合适、刀具质量不好或操作不当引起的。
4. 设备故障:刀具高速切削过程中,如果机床或其它相关设备出现故障,如电机故障、过载保护启动等,可能会导致强制停止。
5. 操作错误:操作员的错误操作可能导致刀具高速切削过程中的强制停止,如设定错误的切削参数、未按正确程序操作等。
总之,刀具高速切削过程中强制停止的原因是多方面的,可能是由于切削力过大、切削过热、刀具磨损或断裂、设备故障或操作错误等引起的。
为了避免这种情况的发生,需要选择适当的刀具和刀具系统、合理的切削参数、良好的冷却系统,并进行正确的操作与维护。
高速切削刀具材料
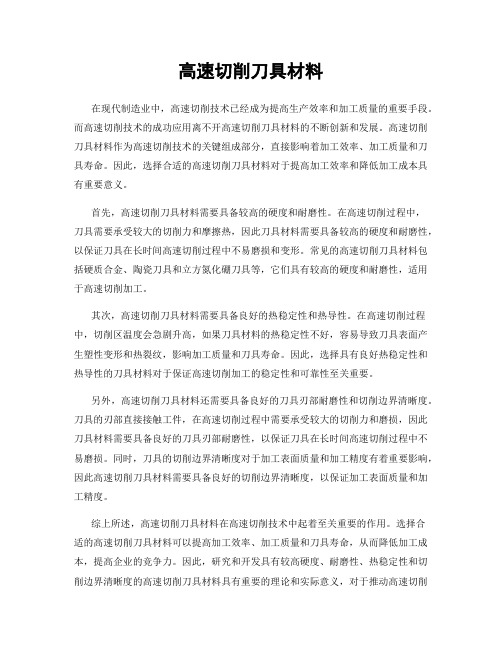
高速切削刀具材料在现代制造业中,高速切削技术已经成为提高生产效率和加工质量的重要手段。
而高速切削技术的成功应用离不开高速切削刀具材料的不断创新和发展。
高速切削刀具材料作为高速切削技术的关键组成部分,直接影响着加工效率、加工质量和刀具寿命。
因此,选择合适的高速切削刀具材料对于提高加工效率和降低加工成本具有重要意义。
首先,高速切削刀具材料需要具备较高的硬度和耐磨性。
在高速切削过程中,刀具需要承受较大的切削力和摩擦热,因此刀具材料需要具备较高的硬度和耐磨性,以保证刀具在长时间高速切削过程中不易磨损和变形。
常见的高速切削刀具材料包括硬质合金、陶瓷刀具和立方氮化硼刀具等,它们具有较高的硬度和耐磨性,适用于高速切削加工。
其次,高速切削刀具材料需要具备良好的热稳定性和热导性。
在高速切削过程中,切削区温度会急剧升高,如果刀具材料的热稳定性不好,容易导致刀具表面产生塑性变形和热裂纹,影响加工质量和刀具寿命。
因此,选择具有良好热稳定性和热导性的刀具材料对于保证高速切削加工的稳定性和可靠性至关重要。
另外,高速切削刀具材料还需要具备良好的刀具刃部耐磨性和切削边界清晰度。
刀具的刃部直接接触工件,在高速切削过程中需要承受较大的切削力和磨损,因此刀具材料需要具备良好的刀具刃部耐磨性,以保证刀具在长时间高速切削过程中不易磨损。
同时,刀具的切削边界清晰度对于加工表面质量和加工精度有着重要影响,因此高速切削刀具材料需要具备良好的切削边界清晰度,以保证加工表面质量和加工精度。
综上所述,高速切削刀具材料在高速切削技术中起着至关重要的作用。
选择合适的高速切削刀具材料可以提高加工效率、加工质量和刀具寿命,从而降低加工成本,提高企业的竞争力。
因此,研究和开发具有较高硬度、耐磨性、热稳定性和切削边界清晰度的高速切削刀具材料具有重要的理论和实际意义,对于推动高速切削技术的发展和应用具有重要意义。
希望在未来的研究和实践中,能够不断创新和发展高速切削刀具材料,为推动高速切削技术的发展和应用做出更大的贡献。
高速切削刀具材料的应用现状和发展趋势
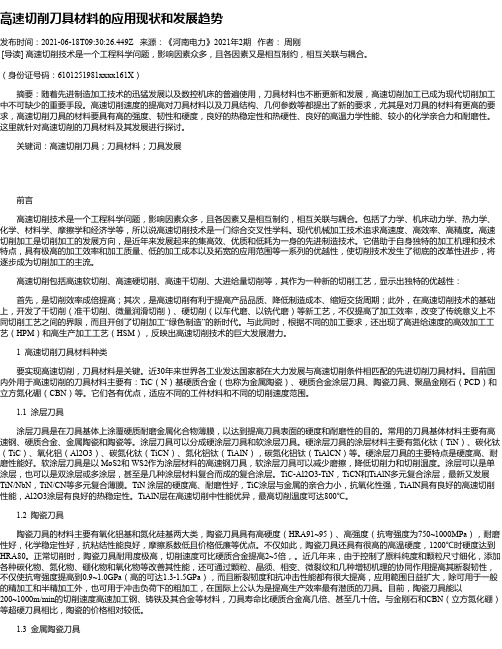
高速切削刀具材料的应用现状和发展趋势发布时间:2021-06-18T09:30:26.449Z 来源:《河南电力》2021年2期作者:周刚[导读] 高速切削技术是一个工程科学问题,影响因素众多,且各因素又是相互制约,相互关联与耦合。
(身份证号码:6101251981xxxx161X)摘要:随着先进制造加工技术的迅猛发展以及数控机床的普遍使用,刀具材料也不断更新和发展,高速切削加工已成为现代切削加工中不可缺少的重要手段。
高速切削速度的提高对刀具材料以及刀具结构、几何参数等都提出了新的要求,尤其是对刀具的材料有更高的要求,高速切削刀具的材料要具有高的强度、韧性和硬度,良好的热稳定性和热硬性、良好的高温力学性能、较小的化学亲合力和耐磨性。
这里就针对高速切削的刀具材料及其发展进行探讨。
关键词:高速切削刀具;刀具材料;刀具发展前言高速切削技术是一个工程科学问题,影响因素众多,且各因素又是相互制约,相互关联与耦合。
包括了力学、机床动力学、热力学、化学、材料学、摩擦学和经济学等,所以说高速切削技术是一门综合交叉性学科。
现代机械加工技术追求高速度、高效率、高精度。
高速切削加工是切削加工的发展方向,是近年来发展起来的集高效、优质和低耗为一身的先进制造技术。
它借助于自身独特的加工机理和技术特点,具有极高的加工效率和加工质量、低的加工成本以及拓宽的应用范围等一系列的优越性,使切削技术发生了彻底的改革性进步,将逐步成为切削加工的主流。
高速切削包括高速软切削、高速硬切削、高速干切削、大进给量切削等,其作为一种新的切削工艺,显示出独特的优越性:首先,是切削效率成倍提高;其次,是高速切削有利于提高产品品质、降低制造成本、缩短交货周期;此外,在高速切削技术的基础上,开发了干切削(准干切削、微量润滑切削)、硬切削(以车代磨、以铣代磨)等新工艺,不仅提高了加工效率,改变了传统意义上不同切削工艺之间的界限,而且开创了切削加工“绿色制造”的新时代。
- 1、下载文档前请自行甄别文档内容的完整性,平台不提供额外的编辑、内容补充、找答案等附加服务。
- 2、"仅部分预览"的文档,不可在线预览部分如存在完整性等问题,可反馈申请退款(可完整预览的文档不适用该条件!)。
- 3、如文档侵犯您的权益,请联系客服反馈,我们会尽快为您处理(人工客服工作时间:9:00-18:30)。
在 高 速情 况 下反 而 下降 。
表 1 高速切 削与 常规切 削的相关参数 比较
常规切 削
进 给 速 度 F
钛 基 硬 质 合 金 刀 具 的 硬 度 都 会 在 H 2 0 以上 。与 WC硬 V 00 质 合 金 相 比 ,强 度 、硬 度 、 韧 性 和 抗 崩 刃 性 能 得 到 明显 提 高 ,
度 下 降 。 高 速 切 削 技 术 的发 展 经 历 了 以 下 4个 阶 段 :高 速 切 削
的设 想 与理 论 探 索阶 段 索阶 段 (9 1 31~1 7 9 1年 ) ;高 速 切 削 的 应 用 探 (1 7 9 9~1 8 94
(1 7 9 2~1 7 9 8年 ) 高速 切 削 实 用 阶 段 ;
根 据 I O一 9 0 S 1 4 ,高 速 主 轴 的转 速 至 少 要 超 过 8 0 r n 0 0/ 。 mi
现 在 的高 速 机 床 技 术 已 经 远 远 超 过 了该 标 准 。 在 由机 床 、刀 具
随 着科 技 的 发 展 ,人 们 对 高 效 率 、高 精 度 和低 成本 的 追 求 越 来 越 高 。在 制 造 业 ,高 速 切 削 加 工 越 来 越 引起 专 业 人 士 的 重 视和青睐。
和 工 件 组 成 的切 削加 工 工 艺 系 统 中 ,刀 具 是 最活 跃 的 因 寨 。 由
于 高速 切 削加 工 所 采 用 的切 削速 度 为 常 规 切 削 的 5 O倍 ,对 ~1 刀 具 材 料 提 出 了 特 殊 的 要 求 。 刀 具 材 料 除应 具 备 硬 度 和 耐 磨
和 绝 热 剪 切 ,使 得 切 削 区 的应 变硬 化 来 不及 发 生 ,因 而 切 削 力
高童切 ■刀具 材料的曩状
现 在 一 般 用 于 高 速 切 削 的 刀 具 材 料 由钛 基 硬 质 合 金 、 陶 瓷 、聚 晶 立 方氮 化硼 、涂 层 刀 具 、金 刚 石 构 成 。
1 .钛 基 硬 质 合 金
加 工 材料 和 新型 材 料 加 工 的需 要 。 高速 切 削刀 具 的失 效 ,主 要 是 由 于 刀具 材 料 的热 性 能 ( 包 括 熔 点 、耐 热 性 、抗 氧 化 性 、 高 温 力 学 性 能 、抗 热 ; 性 能 中击 等 ) 足 所 引起 的 。研 究 表 明 ,高速 切 削 时 ,随 着 切 削 速 度 的 不 提 高 ,切 削 力 减 小 ,切 削温 度 上 升 很 高 ;达 到 一 定 值 后 上升 逐 渐 趋 缓 。 造 成 刀 具 损 坏 最 主 要 的原 因是 切 削力 和切 削温 度 作 用 下 的机 械 摩 擦 、粘 结 、 化 学 磨 损 、崩 刃 、破 碎 以及 塑 性 变形 等 磨 损 和 破 损 。 因此 高速 切 削 刀 具 材 料 最 主 要 的 要 求 是 高 温 时 的 力 学 性 能 、 热 物 理 性 能 、抗 粘 结 性 能 、化 学稳 定 性 ( 化 性 、 氧 扩 散 性 、溶 解 度 等 ) 抗 热 震 性 能 以及 抗 涂 层破 裂性 能等 。 和
年 ) ;高速 切 削成 熟 阶 段 (2 0世 纪 9 0年 代 至今 ) 。 跟 常 规 切 削 相 比 ( 1) 表 ,我 们 不 难 发 现 高 速 切 削优 势 的产 生 得 益 于 人 们 对 切 削机 理 的认 识 越 来越 成 熟 。 切 削 断 裂 发 生 在 加 工 过 程 中 不 稳 定 的 初 始 阶 段 ,导 致 初 始 剪 切 区金 属 的 热 软 化
维普资讯
高速切削发展 的瓶颈
。涂
摘 要 : 高速 切 削 刀 具技 术 是 高 速 切 削 的 关 键 技 术 之 一 。
刀具
杰
高 硬 度 的 工 件 材 料 必 须 要 用 更 高 硬 度 的 刀 具 材 料 去加 工 。
而 从 现 实 际技 术 来 看 ,高 速 切 削 刀 具 大 大 影 响 了高 速 切 削 技 术 的发展。
基 于 当今 刀 具 材 料 的 发 展 还 不 能 满 足 各 领 域 需 求 的 现 状 , 本 文
分析 了在 高速 切 削 中刀 具材 料 和 工 件 材 料 的 匹 配 问题 ,阐 述 了
如 何 合 理 选 择 高速 切 削 刀 具 ,并 对 高 速 切 削 刀 具 材 料 的 种 类 、 性 能 、发 展 和 应 用 情 况进 行 了综 合 评 述 。 关键 词 :高速 切 削 ; 刀具 ;加 工 ;探 讨
和 应 变硬 化 。 在 传 统 切 削 时 ,应 变 硬 化 、强 化 了材 料 ,而 且应 变 区 在 材 料 上 扩 散 ,使 得 切 削 力 增 加 。 如 果 切 削 速 度 足 够 快 , 使 应 变 硬 化 来 不 及 发 生 ,就 会 使 切 削 力 小 于 传 统 速 度 的 切 削 力 。 由于 高 速 切 削过 程 比 普通 切 削 过程 快 得 多 ,发 生 突 变 滑 移
高童切■的优势
高 速 切 削 加 的 概 念 源 于 德 国 的 切 削 物 理 学 家 Ca lJ・ r・
性 、强 度 和 韧 性 、耐 热 性 、 工 艺 性 能 和 经 济 性 外 ,还 对 高 速 切 削 刀 具 材 料 提 出 了如 下 更 高 的 要 求 :① 可 靠 性 ;② 高 耐 热 性 和 抗 热 冲 击 性 能 ;③ 良好 的 高温 力学 性 能 ;④ 刀具 材料 能 适应 难
S lmo 。他 认 为 ,一 定 的工 件 材 料 对 应 有 一 个 临 界 切 削速 度 , a o n 其 切 削 温 度 最 高 。也 就 是 说 ,在 常 规 切 削 范 围 内 ,切 削 温 度 随 着 切 削 速 度 的增 大 而 提 高 ; 当 切 削温 度 下 降 ,切 削 力 也 会 大 幅