转炉炼钢脱氧和硅锰成分控制的研究
转炉炼钢脱氧工艺分析

转炉炼钢脱氧工艺分析发布时间:2021-05-19T09:05:28.921Z 来源:《中国科技人才》2021年第8期作者:李涛[导读] 转炉根据炉衬耐火材料的性质可分为酸性转炉和碱性转炉两种;根据气体吹入炉内的部位,可分为底吹、顶吹、侧吹和顶底复合吹炼转炉;按气体种类可分为空气转炉和氧气转炉。
石横特钢集团有限公司山东省肥城市 271600摘要:随着社会经济发展的转型,钢铁行业也需要实现创新,引入一些新工艺,控制产品的生产成本,促进产品质量的本质提高。
从转炉炼钢的角度来看,脱氧技术一直存在问题。
因此,如果想真正实现整体优化的过程中,应该采取有效的钢液脱氧处理措施, 让炼钢成本中的脱氧成本得到全面控制,确保钢铁产品的质量不断提高,在对相关企业的发展创造有利条件。
关键词:转炉;炼钢脱氧工艺;沉淀脱氧1、炼钢转炉的主要类型和冶炼工艺转炉根据炉衬耐火材料的性质可分为酸性转炉和碱性转炉两种;根据气体吹入炉内的部位,可分为底吹、顶吹、侧吹和顶底复合吹炼转炉;按气体种类可分为空气转炉和氧气转炉。
碱性氧气顶吹和顶底复吹转炉由于其生产速度快、产量大,单炉产量高、成本低、投资少,成为使用最普遍的炼钢设备。
转炉主要用于生产碳钢、合金钢等。
转炉炼钢是以铁水、废钢、铁合金为主要原料,加入少量生石灰,鼓入空气或氧气,使硅、锰、磷、硫、碳等杂质氧化,在氧化过程中放出大量的热量(含1%的硅可使生铁的温度升高200℃),使炉内达到足够高的温度(不需借助外加能源),靠铁水本身的物理热和铁水组分间化学反应产生热量而在转炉中完成炼钢过程。
2、转炉炼钢脱氧工艺问题和氧的产生和危害钢液中的氧通常以非金属夹杂物或溶解氧的形式出现。
在炼钢和吹氧过程中可能会出现氧。
但是,无论用哪种方法来扩大炼钢,这种方法都可以用来去除钢中的其他材料,物质会被分解,特别是在锰、硅、磷和碳的加工过程中。
基本上,氧气会被使用,与氧气发生化学反应,导致其他物质与氧气融合形成新的物质,同时分解其他物质。
对炼钢生产中转炉炼钢脱氧工艺的分析

对炼钢生产中转炉炼钢脱氧工艺的分析摘要:随着我国经济的发展和社会的进步,我国的各行各业均均取得了令人瞩目的成就。
在目前的炼钢过程当中,转炉炼钢脱氧方式的应用越来越广泛,作为炼钢过程当中一项重要的内容,钢液脱氧效果控制能够最大限度地保证整个钢产品的质量。
本文主要是分析了炼钢生产中转炉炼钢脱氧工艺,以此为炼钢行业的发展提供些许的借鉴。
关键词:炼钢生产转炉炼钢脱氧工艺分析引言脱氧合金化是在炼钢生产中转炉炼钢过程当中非常重要的一个过程,其能够直接影响到钢产品的质量、产能以及生产成本等重要环节。
同时,脱氧合金化也是冶炼过程最后的一个步骤,通常来讲,脱氧与合金化过程是同步进行的。
一旦出现操作失误的情况,不仅对合金回收率会造成负面影响,还会提高精炼处理的难度,致使钢水混入较多的杂物,影响其可浇性,从而对铸坯的质量造成不利影响,更为严重的情况会产生废品甚至是铸机断浇。
所以,炼钢生产中转炉炼钢脱氧工艺水平的提升是炼钢生产最为关键的环节之一。
1转炉炼钢相关概述1.1转炉炼钢的原理转炉是转炉炼钢操作最为主要的设备。
其形状与鸭梨类似,内部的炉壁是由耐火砖制成,能够实现360°全方位任何角度旋转。
铁水和废钢是炼钢所需要的原材料,整个吹炼过程中的转炉炼钢是氧化反应,脱碳、脱磷、脱硫、脱氧去除有害气体和杂质,提高温度和调整成分是炼钢最基本的任务。
相关操作人员根据铁水的温度和成分和热平衡公式,再加上白灰和轻烧公式等促使炼钢渣的碱度适中,同时有效地去除氧化镁中的碳磷硫等杂物,并且确保在冶炼过程完成之后使得钢温度和成分符合要求。
吹炼过程所产出的钢水含氧量很难达到钢种质量的要求,主要是由于顶吹氧气与铁水、废钢等发生了氧化反应。
因此,在钢产出的过程中必须要加之脱氧工艺,以确保其能够达到钢种质量的要求。
1.2转炉炼钢中氧的产生及其危害钢液当中的氧气主要是以包括非金属杂物和溶解氧气两种形式存在的,而氧气主要产生自炼钢的原材料和吹氧炼钢的工序。
浅析炼钢生产的转炉炼钢脱氧工艺
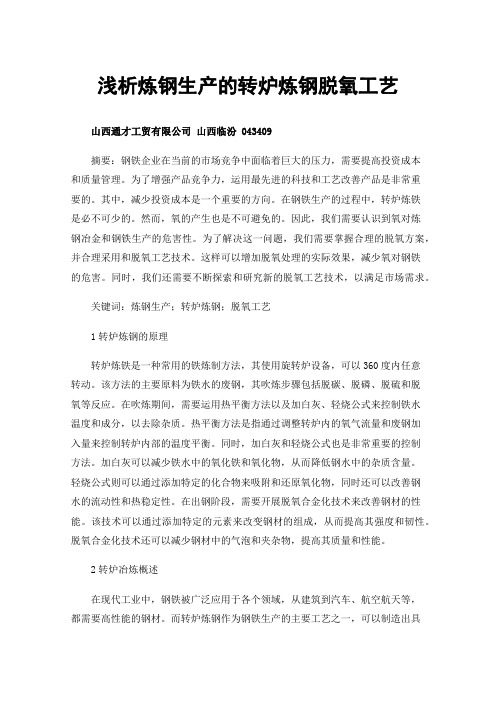
浅析炼钢生产的转炉炼钢脱氧工艺山西通才工贸有限公司山西临汾 043409摘要:钢铁企业在当前的市场竞争中面临着巨大的压力,需要提高投资成本和质量管理。
为了增强产品竞争力,运用最先进的科技和工艺改善产品是非常重要的。
其中,减少投资成本是一个重要的方向。
在钢铁生产的过程中,转炉炼铁是必不可少的。
然而,氧的产生也是不可避免的。
因此,我们需要认识到氧对炼钢冶金和钢铁生产的危害性。
为了解决这一问题,我们需要掌握合理的脱氧方案,并合理采用和脱氧工艺技术。
这样可以增加脱氧处理的实际效果,减少氧对钢铁的危害。
同时,我们还需要不断探索和研究新的脱氧工艺技术,以满足市场需求。
关键词:炼钢生产;转炉炼钢;脱氧工艺1转炉炼钢的原理转炉炼铁是一种常用的铁炼制方法,其使用旋转炉设备,可以360度内任意转动。
该方法的主要原料为铁水的废钢,其吹炼步骤包括脱碳、脱磷、脱硫和脱氧等反应。
在吹炼期间,需要运用热平衡方法以及加白灰、轻烧公式来控制铁水温度和成分,以去除杂质。
热平衡方法是指通过调整转炉内的氧气流量和废钢加入量来控制转炉内部的温度平衡。
同时,加白灰和轻烧公式也是非常重要的控制方法。
加白灰可以减少铁水中的氧化铁和氧化物,从而降低钢水中的杂质含量。
轻烧公式则可以通过添加特定的化合物来吸附和还原氧化物,同时还可以改善钢水的流动性和热稳定性。
在出钢阶段,需要开展脱氧合金化技术来改善钢材的性能。
该技术可以通过添加特定的元素来改变钢材的组成,从而提高其强度和韧性。
脱氧合金化技术还可以减少钢材中的气泡和夹杂物,提高其质量和性能。
2转炉冶炼概述在现代工业中,钢铁被广泛应用于各个领域,从建筑到汽车、航空航天等,都需要高性能的钢材。
而转炉炼钢作为钢铁生产的主要工艺之一,可以制造出具备优良物理性能和化学性能的高性能钢铁,备受业界青睐。
转炉炼钢通过氧化生铁中的碳,制造出高性能钢铁。
其中,碳含量在2.1%范围内可以产生钢铁。
生钢铁中的铁元素和碳元素形成过饱和的固溶体,提高铁、碳含量可以提升钢的韧性和可塑性。
关于转炉炼钢脱氧工艺研究

关于转炉炼钢脱氧工艺研究摘要:随着我国社会经济的逐步发展,对高精度钢材的需求增加,钢材的生产标准也越来越高。
在此基础上,有必要加强对钢铁技术的深入研究,加强脱氧工艺,提高钢的纯度,满足现代社会经济发展的需要。
为了进一步提高加工钢材的质量和技术水平,有必要对加工钢材的制氧工艺和危害进行深入分析,并在此基础上对不同类型的脱氧工艺的不同特点等要素进行精细分析,以便为以下方面提供动态支持。
关键词:炼钢生产;转炉炼钢;脱氧工艺引言在生产过程中对钢厂的控制主要侧重于钢的水质,但随着经济的发展,市场竞争加剧和社会对环境保护的需求使得钢铁能够在生产过程中节约能源和减少能源消耗。
通过对钢加工过程的控制采取优化措施,对节能减排产生了良好影响,提高了市场竞争力。
1转炉炼钢概述转炉炼钢主要包括:建立转炉,将铁水及废钢加入其中,结合具体情况添加其他材料,促进氧和铁水等物质的氧化反应,主要任务是脱硅、脱磷、脱碳、升温,钢的熔点较高,碳含量较低,因此其综合性能明显高于生铁。
采用转炉炼钢生产的主要钢类型是低碳、强度较低、但强度较高和耐用度较高的钢。
因此,转炉炼钢生产的钢材用途比较广泛。
2氧在炼钢中的产生以及危害分析需要大量氧气吹氧,去除钢混合物,通过氧化反应有效氧化氧和杂质,提取氧,获得高纯钢。
钢液中一定有氧气,钢液中杂质含量越大,氧气呼出和硬化时所需氧气量就越大。
如果液体中的氧未得到有效处理,且液体中的氧含量过高,则液体中的氧会在液体凝固时引起氧化反应,形成氧化铁晶体沉积。
铁液中的氧化铁对熔化的原油造成了巨大损害,产品的断裂就证明了这一点,从而使熔化的原油的白色背景发生变形。
铁水含氧量越大,损害就越大。
同时,铁水还含有硫元素,硫与氧之间的化学反应产生了含硫氧化物等污染物,当液态钢含量较高时,这些污染物更难分离。
考虑到钢的力学性能,有必要确保钢水中的氧元素也用于与碳反应,钢溶液中氧含量越高,一氧化碳气泡越多,液体中一氧化碳含量越高,导致钢液沸腾。
【优化】转炉炼钢脱氧冶金化的优化改进

【关键字】优化转炉炼钢脱氧冶金化的优化改进(贾卫国)陕西略阳钢铁有限责任公司炼钢分厂摘要:论述了转炉炼钢脱氧工艺优化;硅钙钡脱氧净化剂的脱氧原理,对合金化过程的问题进行探索解决;V-N合金在HRB400中的作用原理,强调N元素的作用。
关键词:钢中的氧脱氧合金结块V-N合金作用机理一、前言略阳钢铁有限责任公司二炼钢自投产以来,通常采用硅钡钙、增碳剂、硅铁、锰硅铁、钒氮等作为脱氧合金化材料。
在冶炼HRB335钢时,合金量大,易结块,造成[Si]、[Mn]成分波动大;冶炼HRB400钢时,钒氮合金回收率不稳定,易出现废品等问题同,对原有的脱氧剂,合金的作用进行了解,改进合金加入量,加入方法,有效解决上述问题。
二、脱氧(一)终点钢中的氧冶炼低碳钢时,终点钢水的氧含量:冶炼正常的钢水,大中型转炉终点钢水氧含量200~300ppm(0.020%~0.030%),一般过氧钢水终点的氧含量在500~600 ppm,拉碳次数越多,钢水的氧活度、渣中TFe含量越高。
当终点[C]含量和温度相同时,拉碳次数每增加一次,钢中氧活度将增加100~200 ppm,而渣中TFe含量将增加2%~3%。
(二)炉渣中的氧转炉出钢过程中,会不同程度的有一批氧化性炉渣进入钢包,增加脱氧任务。
到目前为止,还不能完全杜绝炉渣进入钢包,进入钢包的炉渣可分为一次下渣,二次下渣。
一次下渣:转炉出钢时,首先进入钢包的不是转炉钢水,而是浮在钢水表面的炉渣,一次下渣数量一般不大,但危害不小。
一次下渣的危害:在出钢初期,先于钢水进入钢包的炉渣在钢水的强烈搅拌作用,自己本身则呈乳化泡沫状,向钢水卷入大量空气,向钢水中增氧。
二次下渣:出现尾期钢水出完之前,钢水表面的炉渣被卷入钢水,随钢水一起进入钢包。
(三)减少钢中氧含量的措施减少一次下渣卷入的氧含量:倒炉时倾动迅速,钢水表面炉渣越过出钢口位置后,再降低倾炉速度,缩短出渣的时间,可减少一次下渣量,出钢初期不加脱氧剂,让钢渣分离,泡沫消失后再加脱氧剂,一般钢包中钢水300mm深以后泡沫基本上完全消失。
探讨炼钢生产中转炉炼钢脱氧工艺
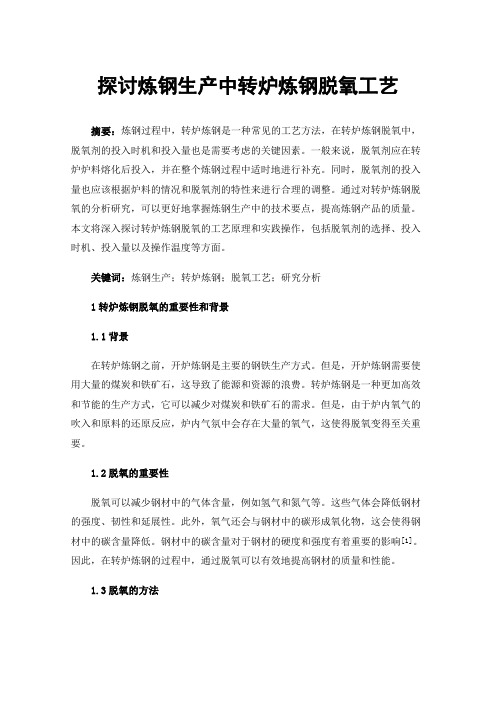
探讨炼钢生产中转炉炼钢脱氧工艺摘要:炼钢过程中,转炉炼钢是一种常见的工艺方法,在转炉炼钢脱氧中,脱氧剂的投入时机和投入量也是需要考虑的关键因素。
一般来说,脱氧剂应在转炉炉料熔化后投入,并在整个炼钢过程中适时地进行补充。
同时,脱氧剂的投入量也应该根据炉料的情况和脱氧剂的特性来进行合理的调整。
通过对转炉炼钢脱氧的分析研究,可以更好地掌握炼钢生产中的技术要点,提高炼钢产品的质量。
本文将深入探讨转炉炼钢脱氧的工艺原理和实践操作,包括脱氧剂的选择、投入时机、投入量以及操作温度等方面。
关键词:炼钢生产;转炉炼钢;脱氧工艺;研究分析1转炉炼钢脱氧的重要性和背景1.1背景在转炉炼钢之前,开炉炼钢是主要的钢铁生产方式。
但是,开炉炼钢需要使用大量的煤炭和铁矿石,这导致了能源和资源的浪费。
转炉炼钢是一种更加高效和节能的生产方式,它可以减少对煤炭和铁矿石的需求。
但是,由于炉内氧气的吹入和原料的还原反应,炉内气氛中会存在大量的氧气,这使得脱氧变得至关重要。
1.2脱氧的重要性脱氧可以减少钢材中的气体含量,例如氢气和氮气等。
这些气体会降低钢材的强度、韧性和延展性。
此外,氧气还会与钢材中的碳形成氧化物,这会使得钢材中的碳含量降低。
钢材中的碳含量对于钢材的硬度和强度有着重要的影响[1]。
因此,在转炉炼钢的过程中,通过脱氧可以有效地提高钢材的质量和性能。
1.3脱氧的方法转炉炼钢中有两种主要的脱氧方法,即硅脱氧和铝脱氧。
硅脱氧是最常用的方法,它通过在炉内加入硅来将氧气与硅反应,从而减少炉内氧气含量。
硅脱氧可以有效地减少氧气含量,但同时也会增加钢材中硅的含量。
铝脱氧则是一种更加高效的脱氧方法,它可以将氧气与铝反应,从而减少氧气含量,同时不会增加钢材中其他元素的含量。
铝脱氧可以生产出更加纯净的钢材。
2氧化铝脱氧法在转炉炼钢中的应用2.1背景在传统的转炉炼钢过程中,气氛中存在大量的氧气,这会使钢中存在过多的气体,如氮气、氧气和氢气等。
这些气体会导致钢中的气孔和夹杂物增多,从而降低钢的质量和性能。
关于转炉炼钢脱氧工艺研究
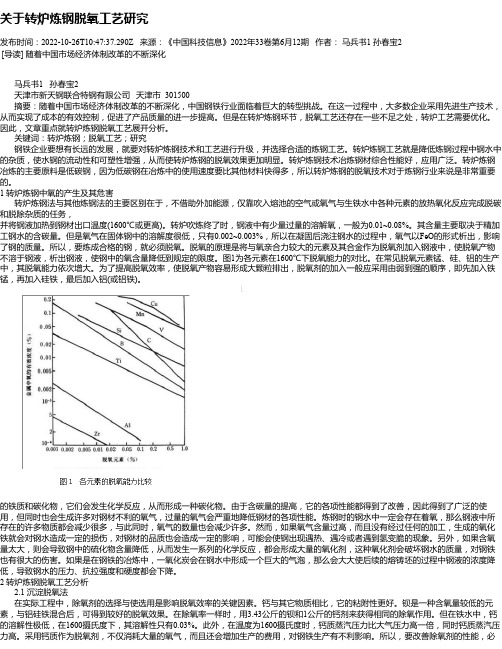
关于转炉炼钢脱氧工艺研究发布时间:2022-10-26T10:47:37.290Z 来源:《中国科技信息》2022年33卷第6月12期作者:马兵书1 孙春宝2[导读] 随着中国市场经济体制改革的不断深化马兵书1 孙春宝2天津市新天钢联合特钢有限公司天津市 301500摘要:随着中国市场经济体制改革的不断深化,中国钢铁行业面临着巨大的转型挑战。
在这一过程中,大多数企业采用先进生产技术,从而实现了成本的有效控制,促进了产品质量的进一步提高。
但是在转炉炼钢环节,脱氧工艺还存在一些不足之处,转炉工艺需要优化。
因此,文章重点就转炉炼钢脱氧工艺展开分析。
关键词:转炉炼钢;脱氧工艺;研究钢铁企业要想有长远的发展,就要对转炉炼钢技术和工艺进行升级,并选择合适的炼钢工艺。
转炉炼钢工艺就是降低炼钢过程中钢水中的杂质,使水钢的流动性和可塑性增强,从而使转炉炼钢的脱氧效果更加明显。
转炉炼钢技术冶炼钢材综合性能好,应用广泛。
转炉炼钢冶炼的主要原料是低碳钢,因为低碳钢在冶炼中的使用速度要比其他材料快得多,所以转炉炼钢的脱氧技术对于炼钢行业来说是非常重要的。
1 转炉炼钢中氧的产生及其危害转炉炼钢法与其他炼钢法的主要区别在于,不借助外加能源,仅靠吹入熔池的空气或氧气与生铁水中各种元素的放热氧化反应完成脱碳和脱除杂质的任务,并将钢液加热到钢材出口温度(1600℃或更高)。
转炉吹炼终了时,钢液中有少量过量的溶解氧,一般为0.01~0.08%。
其含量主要取决于精加工钢水的含碳量。
但是氧气在固体钢中的溶解度很低,只有0.002~0.003%,所以在凝固后浇注钢水的过程中,氧气以FeO的形式析出,影响了钢的质量。
所以,要炼成合格的钢,就必须脱氧。
脱氧的原理是将与氧亲合力较大的元素及其合金作为脱氧剂加入钢液中,使脱氧产物不溶于钢液,析出钢液,使钢中的氧含量降低到规定的限度。
图1为各元素在1600℃下脱氧能力的对比。
在常见脱氧元素锰、硅、铝的生产中,其脱氧能力依次增大。
炼钢生产中转炉炼钢脱氧工艺的分析

23
I 行业发展 ndustry development
进一步是钢液中碳、氧发生反应,生成一氧化碳气泡。在真空环 境下,脱氧法产生的 CO 不会对钢液形成污染,并且 CO 气泡逸 出,加强钢液搅拌,让脱氧反应更加充分、彻底,大大节约了脱 氧剂与石灰使用成本。真空脱氧法具备脱氧效果明显,以及投入 成本低的优势在转炉炼钢脱氧过程中获得了较为普遍的使用。3 脱氧工艺的优化 3.1 普碳钢脱氧工艺的优化
解氧气形式两种,炼钢原料与吹氧炼钢环节是产生氧的主要来 源。在实际炼钢过程中,碳、锰、磷、硅等元素以及其他一些化 ห้องสมุดไป่ตู้杂质的去除,都离不开对大量氧气的使用,借助氧化反应使氧 气与杂质有效结合形成氧化物析出,进而获得高纯度的钢。
可见,氧在钢液中存在是必然的,实际吹氧炼钢时,钢液中 需要氧化的杂质含量越大,所需的氧气量也就越大,同时钢液中 的氧含量也会有所增加。若是没有对钢液中的氧进行有效处理, 导致钢液中的氧含量过高,就会在钢液凝固时有充足的氧气与 钢液中的铁发生氧化反应。形成氧化亚铁结晶析出。钢液中的 氧化亚铁会对铸坯造成极大破坏,直接影响钢产品质量响,甚至 还会导致铸坯变形,严重时产生热脆反应进一步催生钢铁的氧 化现象,导致钢液报废。
文章编号 :11-5004(2019)09-0023-2
由于在固态铁中氧的溶解度非常低,最后形成的氧化物夹 杂会导致钢材的机械性能降低,尤其是会导致钢材的冲击韧性 以及疲劳强度下降,所以必须要采取有效的工艺方法来进行转 炉炼钢的脱氧。
对炼钢生产中转炉炼钢脱氧工艺的探讨

对炼钢生产中转炉炼钢脱氧工艺的探讨摘要:随着中国钢铁企业竞争的加剧,钢铁企业加强了成本和质量管理。
因此,如何利用新技术提高产品质量,降低投资成本,已成为现阶段中国钢铁企业提高产品竞争力的关键。
在转炉炼钢的实际制造过程中,氧气的大量存在是不可避免的,因此企业必须首先了解氧气对炼钢产品和钢铁生产的影响,同时了解有效的除氧方法,进而合理利用和改进除氧技术,在保证钢铁质量的前提下,进一步降低投资成本,更加安全有效地实现炼钢生产。
转炉炼钢脱氧工艺广泛应用于炼钢生产中,能有效提高钢材质量。
同时,为了保证应用效果,必须加强对该工艺的应用研究,特别是加强对转炉氧含量的控制。
关键词:炼钢生产;转炉炼钢;脱氧工艺;氧化处理引言:中国工业发展比较快,在冶炼钢铁材料时,对各种工艺和技术的应用有很高的要求。
转炉炼钢的脱氧处理是生产转炉炼钢产品过程中的关键环节,因为钢水脱氧的效率直接关系到炼铁生产和炼钢产品的质量。
如果钢液含氧量高,钢材的热成型性会减弱,内部气孔会扩大,组织疏松,容易形成热脆性,影响钢材的生产质量。
在转炉炼钢过程中,需要结合实际生产情况,提高对氧的危害性的认识。
通过脱氧技术的合理使用,可以有效提高钢材质量,有效提高钢厂生产能力,为钢厂持续稳定发展奠定坚实基础,加强转炉炼钢的脱氧管理已成为提高炼钢生产质量的关键原因。
目前,转炉炼钢脱氧工艺是我国最重要的炼钢技术,在应用中取得了良好的效果。
因为转炉炼钢形成的氧气会在一定程度上影响钢材质量,进而降低生产效率,制约和阻碍钢厂的经营和发展。
与其他炼钢技术相比,转炉炼钢自动化生产水平相对较高,可以提高生产质量和效率,因此,该技术在钢铁企业生产中得到了广泛应用。
但在工艺应用中仍存在一些不足,需要在现有工艺的基础上进行创新和优化,以提高综合生产水平。
1氧气在炼钢生产中的影响及危害分析在转炉炼钢中,需要分离生铁中的碳和杂质,通过氧化处理可以生产出强度更高、性能更好的材料。
在生产过程中,生铁中的碳和铁元素会反应生成碳化铁。
对炼钢生产中转炉炼钢脱氧工艺的分析

对炼钢生产中转炉炼钢脱氧工艺的分析发布时间:2023-01-15T06:45:19.858Z 来源:《中国科技信息》2023年第17期作者:田涛[导读] 随着钢铁行业竞争的日趋激烈,各钢铁企业开始加强对产品质量和生产成本的控制,如何改进和利用先进的生产工艺,田涛陕西钢铁集团有限公司龙钢公司炼钢厂陕西韩城 715405摘要:随着钢铁行业竞争的日趋激烈,各钢铁企业开始加强对产品质量和生产成本的控制,如何改进和利用先进的生产工艺,提高产品质量,降低生产成本,已成为目前钢铁企业保持竞争力,获得生存与发展的关键。
在转炉炼钢生产中,氧的产生是不可避免的,因此掌握各种脱氧方法,在此基础上加强对脱氧处理工艺的改进和利用,才能有效提高对钢液脱氧处理的效果。
在保证钢产品质量的同时,降低生产成本,使炼钢生产可以有序、高效地进行。
文章正是基于这个角度,重点就炼钢生产中转炉炼钢脱氧工艺展开探讨。
关键词:炼钢生产;转炉炼钢;脱氧工艺;探讨1 引言转炉炼钢生产中时常会产生一些氧气,这些氧气的存在会对钢产品质量造成一定影响,更会影响钢厂生产效益,阻碍钢厂持续健康发展。
为此,了解和掌握转炉冶炼以及炼钢生产中氧气产生的危害,并采用科学合理的脱氧工艺,来提高钢产品质量,提高钢厂生产产能,从而推动钢厂持续健康发展。
2 转炉冶炼概述转炉冶炼是在高炉高温条件下将生铁进行相应的氧化处理,来控制和降低生铁内碳元素含量,从而有效保证钢材质量。
在熔点上生铁和钢材有所不同,同时含碳量也存在很大差异,钢材含碳量在2%以下,同时相较于生铁熔点更高,大约为1450℃~1500℃。
转炉炼钢生产的钢材属于低碳钢,这种钢材强度和硬度相对不高,但在可塑性以及韧性方面具有较好的优越性,在焊接、锻造、加工各种构件中应用广泛。
3 转炉炼钢与脱氧工艺3.1转炉炼钢的原理转炉炼钢操作的设备为转炉。
转炉的形态类似于鸭梨,内部是由耐火砖形成的炉壁,炉体能够360度任意角度旋转。
龙钢转炉用硅锰和碳化硅脱氧合金化试验

本一致。
5.1 关于合金收得率由表3可知,新旧工艺相比,ηMn提高了0.70%~8.27%,ηSi基本接近,ηC有所下降。
这是由于使用了SiMn复合合金后,极大地改善了脱氧的热力学条件,同时使脱氧产物的形核、长大和排除都具有比较有利的动力学条件。
使SiMn中Mn和Si的收得率均有不同程度的提高。
这一点与复合合金剂对钢中[O]的影响也是一致的(见图1)。
图1 复合合金剂对钢中[O]的影响另外,硅锰合金中硅元素比锰元素的还原性强,会优先氧化,从而降低了钢中氧位,改善了锰元素的合金化条件,提高了ηMn。
加之由于使用了SiC粉,因其与氧的亲和力大于硅铁与氧的亲和力(见图2),其脱氧反应剧烈,导致消耗于脱氧的SiMn相对减少,也相应提高了SiMn合金中Mn和Si的收得率。
图2 脱氧反应标准自由能变化与温度关系图SiC(s)+3(FeO)=SiO2(s)+{CO}+3Fe(l)ΔG01=-260999-52.8777T KJ/mol(1)SiC(s)+3〔O〕=SiO2(s)+{O}ΔG02=-607354+91.58T KJ/mol(2)Si(s)+2(FeO)=SiO2(s)+2Fe(l)ΔG03=-486802.8+113.03T KJ/mol (3)Si(s)+2〔O〕=SiO2(s)ΔG04=-717706+209.3T KJ/mol (4)C(s)+(FeO)=Fe(l)+{CO}ΔG05=120885.6-132.84T KJ/mol (5)C(s)+〔O〕={CO}ΔG06=5434-84.68TKJ/mol (6)另一方面,SiC的密度只有3.2g/cm3,且试验时用的碳化硅中SiC含量偏低,又多呈粉状,加入钢包后,部分飘浮在钢液面上,由于烧损(即消耗于氧化性渣和气氛中)和机械损失(即损失于钢液面的渣中)以及用于脱氧的SiC量增加,导致SiC中Si和C 的收得率偏低。
而SiMn和SiC综合脱氧合金化的结果使得ηSi基本不变。
炼钢生产中转炉炼钢脱氧工艺的探讨

安全与生产2019年第4期中国机械MACHINE CHINA0引言在当今的时代里,对于钢铁企业而言,如果想要切实的提升自身在市场中的核心竞争力,就要通过现代化的生产工艺来不断的提升钢产品的品质,不断的降低生产的成本。
在转炉炼钢的过程中,会产生大量的氧气。
如果在钢液中含有过多的氧气,必然会对钢产品的品质和质量产生直接的影响。
因此,转炉炼钢脱氧工艺在转炉炼钢的过程中得到了越来越广泛的应用。
1转炉炼钢概述转炉是炼钢生产中的重要炼钢设备,不但能够用于生产碳钢与合金钢,还能够用于冶炼铜和镍。
所谓的转炉炼钢就是指以铁水、废钢以及铁合金作为主要的原料,不借助外加能源,靠铁液本身的物理热和铁液组分间化学反应产生热量而在转炉中完成炼钢过程。
转炉炼钢的原材料主要有三个种类:金属料、非金属料以及气体。
其中的金属料主要包括铁水、废钢以及铁合金;非金属料主要包括造渣料、熔剂以及冷却剂;气体主要包括氧气、氮气以及二氧化碳等。
目前,碱性氧气顶吹转炉和顶底复吹转炉是炼钢生产中应用最为广泛的炼钢设备。
2转炉炼钢中氧的产生与危害在转炉炼钢的过程中,钢液中的氧主要有两种存在形式,一种是溶解氧,另一种是非金属杂物,其主要产生于吹氧炼钢以及原料等生产环节中。
在炼钢生产的过程中,无论采用哪一种炼钢方式,都需要让钢中所含的杂质元素与氧进行氧化反应,只有这样,才能够有效的将钢中所含的杂质去除。
因此,钢液中存在氧是无可避免的。
对于吹氧炼钢而言,随着钢液中杂质含量的逐渐降低,钢液中的氧含量会逐渐的上升。
在这种情况之下,如果不及时的对钢液进行脱氧处理,在钢液冷凝的过程中,钢液就会与氧发生化学反应,从而导致钢液中产生氧化亚铁,进而对钢产品的品质和质量产生严重的影响。
首先,如果钢液中的氧含量过高,不但会降低钢产品的形状塑造效率,还会使钢产品产生热脆的现象。
其次,如果钢液中的氧含量过高,在钢液冷凝的过程中,钢液中的碳和氧就会发生化学反应,从而产生一氧化碳气泡,进而使钢液出现沸腾的现象。
炼钢生产中转炉炼钢脱氧工艺综述
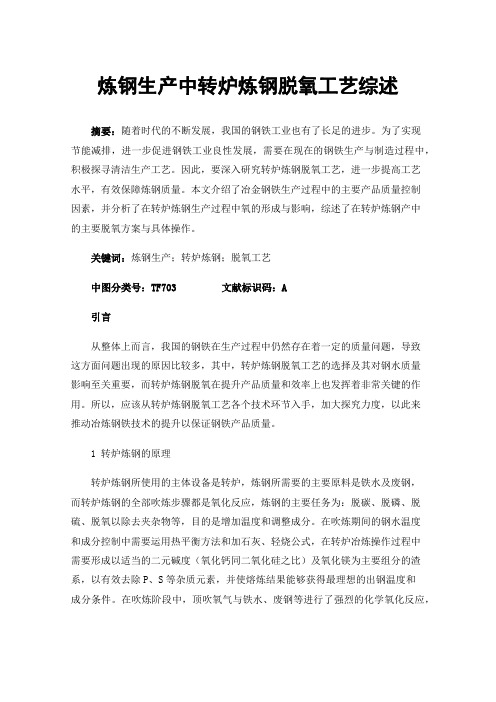
炼钢生产中转炉炼钢脱氧工艺综述摘要:随着时代的不断发展,我国的钢铁工业也有了长足的进步。
为了实现节能减排,进一步促进钢铁工业良性发展,需要在现在的钢铁生产与制造过程中,积极探寻清洁生产工艺。
因此,要深入研究转炉炼钢脱氧工艺,进一步提高工艺水平,有效保障炼钢质量。
本文介绍了冶金钢铁生产过程中的主要产品质量控制因素,并分析了在转炉炼钢生产过程中氧的形成与影响,综述了在转炉炼钢产中的主要脱氧方案与具体操作。
关键词:炼钢生产;转炉炼钢;脱氧工艺中图分类号:TF703 文献标识码:A引言从整体上而言,我国的钢铁在生产过程中仍然存在着一定的质量问题,导致这方面问题出现的原因比较多,其中,转炉炼钢脱氧工艺的选择及其对钢水质量影响至关重要,而转炉炼钢脱氧在提升产品质量和效率上也发挥着非常关键的作用。
所以,应该从转炉炼钢脱氧工艺各个技术环节入手,加大探究力度,以此来推动冶炼钢铁技术的提升以保证钢铁产品质量。
1 转炉炼钢的原理转炉炼钢所使用的主体设备是转炉,炼钢所需要的主要原料是铁水及废钢,而转炉炼钢的全部吹炼步骤都是氧化反应,炼钢的主要任务为:脱碳、脱磷、脱硫、脱氧以除去夹杂物等,目的是增加温度和调整成分。
在吹炼期间的钢水温度和成分控制中需要运用热平衡方法和加石灰、轻烧公式,在转炉冶炼操作过程中需要形成以适当的二元碱度(氧化钙同二氧化硅之比)及氧化镁为主要组分的渣系,以有效去除P、S等杂质元素,并使熔炼结果能够获得最理想的出钢温度和成分条件。
在吹炼阶段中,顶吹氧气与铁水、废钢等进行了强烈的化学氧化反应,所获得的钢水氧含量无法达到钢材的品质要求,所以在出钢阶段中必须开展脱氧合金化技术来得到质量要求合格的钢水,以满足炼钢的质量需要。
2 氧的生产和危害通常在原料和吹氧炼钢过程中产生氧。
因为炼钢过程中析出杂质时需要利用氧,在LF精炼和连铸阶段,析出杂质后将会随之减少氧的含量,且少量的氧不会影响钢的质量。
在炼钢过程中,如果没有有效处理钢液溶解的氧,将会导致氧含量超过控制标准。
关于炼钢转炉脱氧工艺研究
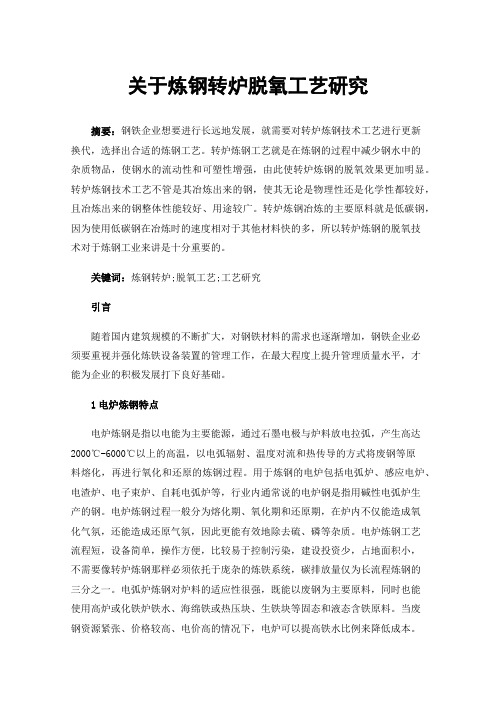
关于炼钢转炉脱氧工艺研究摘要:钢铁企业想要进行长远地发展,就需要对转炉炼钢技术工艺进行更新换代,选择出合适的炼钢工艺。
转炉炼钢工艺就是在炼钢的过程中减少钢水中的杂质物品,使钢水的流动性和可塑性增强,由此使转炉炼钢的脱氧效果更加明显。
转炉炼钢技术工艺不管是其冶炼出来的钢,使其无论是物理性还是化学性都较好,且冶炼出来的钢整体性能较好、用途较广。
转炉炼钢冶炼的主要原料就是低碳钢,因为使用低碳钢在冶炼时的速度相对于其他材料快的多,所以转炉炼钢的脱氧技术对于炼钢工业来讲是十分重要的。
关键词:炼钢转炉;脱氧工艺;工艺研究引言随着国内建筑规模的不断扩大,对钢铁材料的需求也逐渐增加,钢铁企业必须要重视并强化炼铁设备装置的管理工作,在最大程度上提升管理质量水平,才能为企业的积极发展打下良好基础。
1电炉炼钢特点电炉炼钢是指以电能为主要能源,通过石墨电极与炉料放电拉弧,产生高达2000℃-6000℃以上的高温,以电弧辐射、温度对流和热传导的方式将废钢等原料熔化,再进行氧化和还原的炼钢过程。
用于炼钢的电炉包括电弧炉、感应电炉、电渣炉、电子束炉、自耗电弧炉等,行业内通常说的电炉钢是指用碱性电弧炉生产的钢。
电炉炼钢过程一般分为熔化期、氧化期和还原期,在炉内不仅能造成氧化气氛,还能造成还原气氛,因此更能有效地除去硫、磷等杂质。
电炉炼钢工艺流程短,设备简单,操作方便,比较易于控制污染,建设投资少,占地面积小,不需要像转炉炼钢那样必须依托于庞杂的炼铁系统,碳排放量仅为长流程炼钢的三分之一。
电弧炉炼钢对炉料的适应性很强,既能以废钢为主要原料,同时也能使用高炉或化铁炉铁水、海绵铁或热压块、生铁块等固态和液态含铁原料。
当废钢资源紧张、价格较高、电价高的情况下,电炉可以提高铁水比例来降低成本。
2转炉炼钢中氧的产生及其危害转炉冶炼主要是通过将生铁中含有的大量的碳和杂质利用各种方式来进行氧化,从而冶炼出强度更高、各方面性能更好的一种钢材。
在这个过程中,生铁中含有了大量的铁元素和碳元素,而这就会相互进行反应,由此生成了一种碳化铁物质,这种物质随着碳含量的增加其各方面性能也越来越好,所以被普遍应用,但是在这个过程中,也会产生大量对钢有害的氧,氧含量过高会对钢各方面的性能都会有很大影响。
浅析炼钢生产的转炉炼钢脱氧工艺

浅析炼钢生产的转炉炼钢脱氧工艺摘要:伴随着我国生产与消费的持续增长,我国钢资源数量也呈现出了持续增加的趋势。
在转炉炼钢过程中会产生大量的氧气,影响钢的生产质量和炼钢企业的生产效率,不利于提高企业的竞争力。
因此,要深入研究转炉炼钢脱氧工艺,进一步提高工艺水平,有效保障炼钢质量。
本文主要分析了炼钢生产的转炉炼钢脱氧工艺对生产起到的参考作用,以期推动我国炼钢行业的健康发展。
关键词:炼钢生产;转炉;炼钢;脱氧工艺引言面对世界钢铁企业的剧烈竞争,各钢铁企业不断地逐步提高投资成本和质量管理。
通过运用最先进的科技和工艺改善产品,以减少投资成本,已成为现阶段钢铁企业增强产品竞争力的重点。
在转炉炼铁的实际生产过程中,氧的产生是必然的。
因此,有必要认识氧对炼钢冶金和钢铁生产的危害性,并掌握合理的脱氧方案,进而合理地采用和脱氧工艺技术,以增加脱氧处理的实际效果。
1转炉炼钢的原理及优点转炉炼铁所使用的主要机械是旋转炉设备。
旋转炉的形状近似于鸭梨,里面是由燃料气体混合物所组成的炉壁,炉体能够在360°内任何方向转动。
炼铁所需要的主要原料是铁水的废钢,而转炉炼铁的全部吹炼步骤都是抗氧化反应,主要工作应该分为:脱碳、脱磷、脱硫、脱氧以除去危险空气和杂物等,增加温度和改变成分。
在吹炼期间的铁水温度和成分作业中需要运用热平衡方法和加白灰、轻烧公式,对冶炼钢渣体系生成适当的 pH 值和氧化镁以合理的比例去除C、P、S 等,并使熔炼结果能够获得最理想的出钢温度和成分条件。
因为在吹炼阶段中,顶吹空气与高炉内铁水、废钢等进行了强烈的化学氧化反应,最后产生铁流所充氧量无法达到钢材的品质要求,所以在出钢阶段中必须开展脱氧合金化技术来改善钢材的性能,以满足炼钢的需要。
2脱氧技术的现状在熔炼的情况下,最早出来的脱氧物就是硅,即硅的制造导致镇静钢的出现。
但是,由于硅的脱氧能力降低,易产生不完全脱氧,从而在金属中产生了大量的金属泡沫。
在用脱氧硅时,也会产生大量的硅盐酸并掺入钢材中,这对原材料钢的使用也有重要影响。
转炉炼钢脱氧工艺研究

转炉炼钢脱氧工艺研究作者:鲁川来源:《科学与财富》2020年第32期摘要:当前市场经济不断发展,企业之间的竞争日益激烈,在激烈的市场竞争环境下,必须强化钢铁企业产品质量及产品成本的把控,不断引进先进工艺技术促进钢铁产品竞争力的增强,以保障钢铁企业在激烈的市场竞争环境下立于不败之地。
转炉炼钢属于钢铁企业生产的主要形式,在生产过程中,氧气属于必不可少的物质,但是氧会对产品质量的提升产生一定的消极影响,这就需要完善脱氧工艺,合理应用脱氧工艺,促进钢水脱氧处理效果的提升,以保障钢产品质量的提升,确保钢铁企业生产的正常稳定运行。
关键词:转炉炼钢;脱氧工艺;钢铁企业钢铁企业的转炉炼钢环节中,钢水脱氧工艺属于重要环节,钢水脱氧工艺可保障钢产品质量的合格率,若是钢水中氧含量过高,将影响钢产品质量,导致钢产品内部小孔的出现,影响钢组织结构的密度,使其呈现疏松结构形态,甚至会导致热脆性现象的发生,对钢质量产生严重负面影响。
当前,转炉炼钢脱氧技术被广泛应用,必须对氧含量进行把控,以促进钢产品质量的提升,本文就转炉炼钢脱氧工艺的影响效果进行分析。
一、转炉炼钢(一)概念所谓转炉炼钢,转炉炼钢(converter steelmaking)是以铁水、废钢、铁合金为主要原料,不借助外加能源,靠铁液本身的物理热和铁液组分间化学反应产生热量而在转炉中完成炼钢过程。
由于钢材的含碳量和熔点与铁水存在较大差异性,若是钢材中的含碳量在2%以下的情况,其熔点大都维持在1500℃[1]。
转炉炼钢过程中生产低碳钢,低碳钢的强度和硬度与钢材存在相似性,但是低碳钢的可塑性和韧性均比较强,可以将其应用于部件的焊接、锻造和加工之中。
(二)危害转炉炼钢作业过程中,钢水中会存在大量的氧,氧会以溶解氧和非金属夹杂物形式存在,炼钢工作开展过程中,铁水中存在大量的硅元素、磷元素和碳元素,想要对上述元素进行脱除干预,必须采用氧化反应方式开展,依靠氧化反应将上述元素去除,满足钢材的性质。
炼钢生产中转炉炼钢脱氧工艺研究

炼钢生产中转炉炼钢脱氧工艺研究1.河北省锻造用钢技术创新中心、河北省承德市兴隆县067201摘要:转炉炼钢脱氧工艺在炼钢生产中得到广泛应用,能够使钢产品质量有效提升,同时为了确保应用成效,需要对工艺应用加大研究力度,尤其是对转炉氧气含量加强控制,由于炼钢过程中氧气产生无法避免,所以需要对生产过程中氧气对钢产品质量的造成的影响和危害进行充分了解和掌握,并对各类脱氧处理工艺进行有效利用与改进,使脱氧效果达到预期目标。
本文结合转炉冶炼特点,对炼钢生产中氧气的影响和危害进行分析,并对转炉炼钢脱氧工艺的应用策略进行探讨。
关键词:炼钢生产;转炉炼钢脱氧工艺;氧化处理引言:由于转炉炼钢生产中所形成的氧气会一定程度影响钢产品质量,进而使生产效益降低,对钢厂经营发展造成制约和阻碍。
因此转炉炼钢生产过程中,需要结合生产实际情况,对氧气的危害性提高认识,通过脱氧工艺的合理运用,使钢产品质量切实提高,钢厂生产产能有效提升,为钢厂可持续稳定发展奠定坚实的基础。
一、转炉冶炼特点分析在高炉高温状态下,转炉冶炼需要对生铁进行氧化处理,在生铁中碳元素含量加强控制,使其含量降低,钢材质量有效提高。
同时由于钢材和生铁在熔点上存在一定差异,两者的含碳量也各不相同,通常前者含碳量低于2% ,因此生铁的熔点相较于更高[1]。
另外在转炉炼钢生产过程中,所采用的钢材主要为低碳钢,钢材硬度和强度较低,但具有良好的韧性和可塑性,能够广泛应用于各种构件的锻造、焊接、加工中。
二、炼钢生产中氧气影响和危害分析在炼钢生产过程中,原料及钢液中,通常存在着溶解氧气和非金属夹杂物,因此在炼钢过程中不可避免会有一定含量的氧存在,同时还需要对生产过程中产生的化学杂质进行清除,如硅、锰、碳、磷等化学杂质,而在杂质清除过程中,氧气极容易与杂质发生化学反应,进而导致新氧化合物的形成[2]。
在吹氧炼钢过程中,随着钢液氧化和杂质含量的减少,在钢液中氧气含量不断增加,一旦钢液中氧气未得到及时、全面处理,含量过高,在钢液凝固时,会与其反应而产生结晶,以及氧化亚铁等新化学物质,此物质的存在会对铸坯造成破坏,对钢产品质量造成不利影响,甚至导致变形、热脆等,以及钢铁氧化等问题产生。
转炉的脱氧控制分类
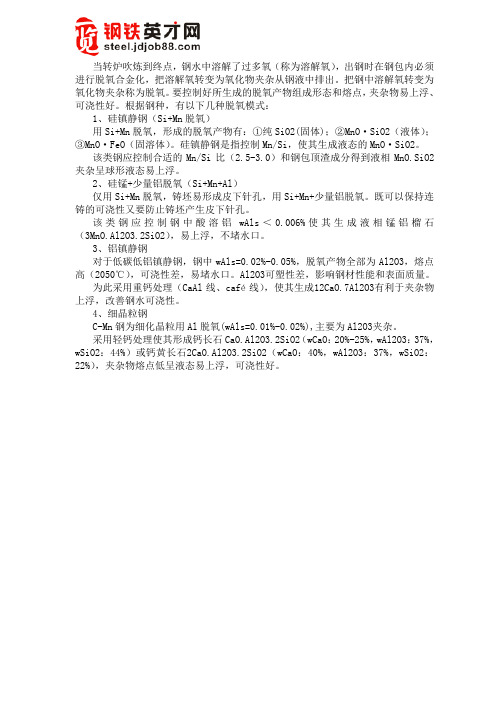
当转炉吹炼到终点,钢水中溶解了过多氧(称为溶解氧),出钢时在钢包内必须进行脱氧合金化,把溶解氧转变为氧化物夹杂从钢液中排出。
把钢中溶解氧转变为氧化物夹杂称为脱氧。
要控制好所生成的脱氧产物组成形态和熔点,夹杂物易上浮、可浇性好。
根据钢种,有以下几种脱氧模式:1、硅镇静钢(Si+Mn脱氧)用Si+Mn脱氧,形成的脱氧产物有:①纯SiO2(固体);②MnO·SiO2(液体);③MnO·Fe O(固溶体)。
硅镇静钢是指控制Mn/Si,使其生成液态的MnO·SiO2。
该类钢应控制合适的Mn/Si比(2.5-3.0)和钢包顶渣成分得到液相MnO.SiO2夹杂呈球形液态易上浮。
2、硅锰+少量铝脱氧(Si+Mn+Al)仅用Si+Mn脱氧,铸坯易形成皮下针孔,用Si+Mn+少量铝脱氧。
既可以保持连铸的可浇性又要防止铸坯产生皮下针孔。
该类钢应控制钢中酸溶铝wAls<0.006%使其生成液相锰铝榴石(3MnO.Al2O3.2SiO2),易上浮,不堵水口。
3、铝镇静钢对于低碳低铝镇静钢,钢中wAls=0.02%-0.05%,脱氧产物全部为Al2O3,熔点高(2050℃),可浇性差,易堵水口。
Al2O3可塑性差,影响钢材性能和表面质量。
为此采用重钙处理(CaAl线、café线),使其生成12CaO.7Al2O3有利于夹杂物上浮,改善钢水可浇性。
4、细晶粒钢C-Mn钢为细化晶粒用Al脱氧(wAls=0.01%-0.02%),主要为Al2O3夹杂。
采用轻钙处理使其形成钙长石CaO.Al2O3.2SiO2(wCaO:20%-25%,wAl2O3:37%,wSiO2:44%)或钙黄长石2CaO.Al2O3.2SiO2(wCaO:40%,wAl2O3:37%,wSiO2:22%),夹杂物熔点低呈液态易上浮,可浇性好。
对炼钢生产中转炉炼钢脱氧工艺的探讨
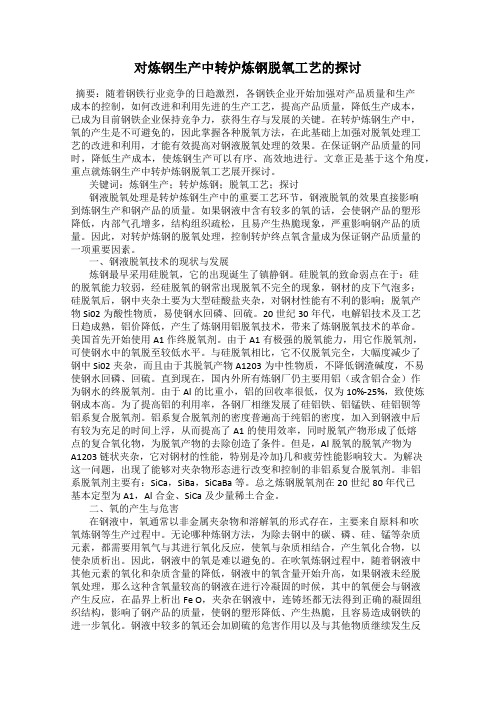
对炼钢生产中转炉炼钢脱氧工艺的探讨摘要:随着钢铁行业竞争的日趋激烈,各钢铁企业开始加强对产品质量和生产成本的控制,如何改进和利用先进的生产工艺,提高产品质量,降低生产成本,已成为目前钢铁企业保持竞争力,获得生存与发展的关键。
在转炉炼钢生产中,氧的产生是不可避免的,因此掌握各种脱氧方法,在此基础上加强对脱氧处理工艺的改进和利用,才能有效提高对钢液脱氧处理的效果。
在保证钢产品质量的同时,降低生产成本,使炼钢生产可以有序、高效地进行。
文章正是基于这个角度,重点就炼钢生产中转炉炼钢脱氧工艺展开探讨。
关键词:炼钢生产;转炉炼钢;脱氧工艺;探讨钢液脱氧处理是转炉炼钢生产中的重要工艺环节,钢液脱氧的效果直接影响到炼钢生产和钢产品的质量。
如果钢液中含有较多的氧的话,会使钢产品的塑形降低,内部气孔增多,结构组织疏松,且易产生热脆现象,严重影响钢产品的质量。
因此,对转炉炼钢的脱氧处理,控制转炉终点氧含量成为保证钢产品质量的一项重要因素。
一、钢液脱氧技术的现状与发展炼钢最早采用硅脱氧,它的出现诞生了镇静钢。
硅脱氧的致命弱点在于:硅的脱氧能力较弱,经硅脱氧的钢常出现脱氧不完全的现象,钢材的皮下气泡多;硅脱氧后,钢中夹杂土要为大型硅酸盐夹杂,对钢材性能有不利的影响;脱氧产物Si02为酸性物质,易使钢水回磷、回硫。
20世纪30年代,电解铝技术及工艺日趋成熟,铝价降低,产生了炼钢用铝脱氧技术,带来了炼钢脱氧技术的革命。
美国首先开始使用A1作终脱氧剂。
由于A1有极强的脱氧能力,用它作脱氧剂,可使钢水中的氧脱至较低水平。
与硅脱氧相比,它不仅脱氧完全,大幅度减少了钢中Si02夹杂,而且由于其脱氧产物A1203为中性物质,不降低钢渣碱度,不易使钢水回磷、回硫。
直到现在,国内外所有炼钢厂仍主要用铝(或含铝合金)作为钢水的终脱氧剂。
由于Al的比重小,铝的回收率很低,仅为10%-25%,致使炼钢成本高。
为了提高铝的利用率,各钢厂相继发展了硅铝铁、铝锰铁、硅铝钡等铝系复合脱氧剂。
- 1、下载文档前请自行甄别文档内容的完整性,平台不提供额外的编辑、内容补充、找答案等附加服务。
- 2、"仅部分预览"的文档,不可在线预览部分如存在完整性等问题,可反馈申请退款(可完整预览的文档不适用该条件!)。
- 3、如文档侵犯您的权益,请联系客服反馈,我们会尽快为您处理(人工客服工作时间:9:00-18:30)。
表4硅、锰元素收得牢
Tal)le 4 Yield rallo of Si,Mn
蟛
脱氧制度和成分控制的新设计
基于以I:的分析.对脱氧和成晶含量的控制提 出一种新的设想和确定日标值。
出钢过程中,当出钢量达I 5%~20%时加入 硅铁,然后再加入铝饼,让硅铁充分熔化和脱氧。
出钢量达80%~90,;再加入锰铁。锰铁的密 度为7.2 g/cm。,熔点为l 250~l 300℃t钢水密度 为7.0 g/cm’,温度在1 600(:以上;渣f密度为2.2 ~2.8 g/cm3。锰铁能很快穿过渣层进入钢水中,在 钢水中下沉、吸热、熔化和扩散。锰铁的密度略大于 钢水.在钢水巾的沉降速度不会很快,加上钢水的搅 动和对流作』H,在锰铁到达钢包底之前能先全熔化。 另外还nr以控制锰铁的块度。使之在较短的时间内 熔|匕完毕。
shortcomings.Especially,for SONIC lOW alloy steel,then Mn often goes beyond contr01.By changing the addition order into the following one Si—Fe,the AI,then Mn—Fe,which is
本文链接:/Conference_300153.aspx
第34卷增刊 1 9 9}年l 0月
钢铁
JR()N AND STEEL
V01.34.Suppl. 0ctober.1999
转炉炼钢脱氧和硅锰成分控制的研究
刘文辉
(韶关钢铁集团有限公司)
摘要转炉炼钢的t要钢种为普碳钢和低台金钢,传统的脱氧方法是先加入锰铁,再加入硅铁,最后加入铝 或者硅铝钡等。这利r先弱后强的fJu入方法,存在很大的不足,特别是含锰较高的低合金钢,常出现锰含量出 格。改为先加入硅铁.再加入铝.最后加入锰铁,锰只作为纯合金元素加入钢中,在热力学和反应动力学上是 口r行的,经济上合算。r艺上容易作副,并且减少废品和回炉。 关键词脱氧台金化收得牢
从表2可知,低碳钢和低合金钢中锰含量远没 有达到与硅含量相平衡的数值。
钢中元素作用系数如表3所示。
表3钢水中各种元素对Si、Mn元素作用系数el
fable 3 el in liquid steel
从表3可知,钢中溶解五大元素,使硅元素的活 度提高,而锰元素的活度略有下降。 4常炼钢种硅、锰元素含量的特点
不同的钢种含Si、Mn有一定的范围,有些钢种 锰含量的绝对范围大F或等于硅含量的绝对范围。
以20MnSi为例,两元素的绝对范围同是0.4%,但
相对于各自规格中限的相对范围印相差很大,si为
66.7%,Mn为28.6%,也就是说硅铁多加或少加 卡日当于甘标值的33.5%便会产生出格;锰铁多加或 少加相当1二日标值的14.3%便产生出格,这样锰含 量容易出格是理所当然的。原有的工艺硅、锰元素收 得率见表4
deoxidizing method used in usual practice is adding Fe—Mn firstly,then Fe—Si and lastly AI or
Sl-Al—Ba etc..This method using weak deoxidizer before stronger one has many
reasonable in terms of thermodynamics and kinetics.The scrap and re blow is reduced and the method is easy in operation.
KEY WORDS deoxidatlon.a1[oying.recovery rate
1前言
转炉炼钢脱氧合金加入的顺序,传统的做法是 先加入锰铁,再加入硅铁,最后加入铝。残存在钢中 的硅、锰含量,符合所炼钢种相对应的含量范围即为 合格。辞、锰含量控制不当,超出钢种规定要求的范 围便成为废品或回炉。
锰铁、硅铁、铝这种顺序的加入方法,是按元素 的脱氧能力由弱到强的顺序先后加入钢中进行脱 氧,对充分发挥各种脱氧剂的脱氧能力物尽其用,是 有其优越性的,工艺方法也是出于这一认UI而没计
联系^:刘文辉.高级1‘程师,韶关(51 20001韶关钢铁集囤有限公司
增刊
刘文辉.车}炉炼钢脱氧和硅锰成分控制的研究
单一元素脱氧,去除钢水中1.0 kg[O],各种台 金的消耗量不同。
脱去1.0 kg[o]需消耗锰铁5.3 kg,或消耗硅 铁I.2 kg.或消耗铝饼1.13 kg。I.0 kg的硅铁相当 于4.5 kg锰铁的脱氧量。 3有关的热力学数据.
采用这一脱氧和合金化的丁=艺,能起到耗硅保 锰、稳定和提高锰元素牧得率的作用,从而解决 20MnSi钢种锰含量出格的难题。
颁期的目标,采取耗硅保锰的做法,硅的收得率 降低,硅铁加入量相应增加,锰的收得率提高.锰铁 的加入量相应减少。有关日标值的数据见表5。
下均每吨钢多消耗0.5 kg硅铁,少消耗2.25 kg锰铁,按公司结臂价格,硅铁3.891元/kg,锰铁 2.96;g/kg.吨钢成本下降4.71元。
的。
先弱后慢的加入方法存在很大的小足,特别是 当锰硅比大于2.0的低台金钢种更暴嚣fH它的弱 点。生产现场的统汁数据,低合垒钢种成分出格的炉 号90%以上是锰含量不符合钢种要求而导致废品
或回炉。同时从自然资源、工艺特点、常炼钢种对硅、 锰含量要求、经济效益等方面考虑,先弱后强顺序的 加入方法也是低效的。F面由浅入深加以论述,并从 理论上沦证另一种新的加入方法,力求达到更高效
益。Βιβλιοθήκη 2脱氧反应 脱氧剂加入钢水后,经升温、熔化,与钢水中的
氧反应,反应式如下:
EMn]-r[03
(1)
ESi]+2[()]
(2)
眦姚蛳 2[AI]十3[()]
”,U
(3)
各元素的原子量:Mn 55;Si 28;O 16;Al 27。 各种合金的合金元素含量:锰铁含锰65%;硅 铁含硅75%;铝饼含铝99.5%。
硅和锰脱氧反应的综台算式为: [si]+2(MnO)一2[Mn]十(SiO:) (4)
在炼钢温度下,钢水中的平衡含苣如表l、2所 示。
表l炼钢温度卜K。。。数据表 ,Iable 1 KM啪I data at steelmaking lemperature
袁2炼钢温度l、与硅含量相平衡的锰含量 Fable 2[Mn]contem at steelmaking temperaluYe蹦
(下转第j77蚝)
转炉炼钢脱氧和硅锰成分控制的研究
作者: 作者单位:
刘文辉 韶关钢铁集团有限公司
本文读者也读过(10条) 1. 赖云.邹锦忠.LAI Yun.ZOU Jin-zhong 硅锰和铝锰脱氧合金化实践[期刊论文]-江西冶金2005,25(4) 2. 李忠华 铝硅铁复合脱氧剂在炼钢生产中的应用[期刊论文]-铸造2000,49 (4) 3. 闫晓平.潘素英.段永卿.师艳秋.翟晓毅 转炉用低硅铁脱氧合金化的实验[期刊论文]-河北冶金2003(2) 4. 汤天宇.栾秋生.文永才.王胜.张槐.陈守俊.TANG Tian-yu.LUAN Qiu-sheng.WEN Yong-cai.WANG Sheng.ZHANG Huai.CHEN Shou-jun 低碳铝镇静钢铝锰铁脱氧合金化试验[期刊论文]-钢铁钒钛2000,21(4) 5. 刘守林.陈东宁.安君辉.赵小雷.潘素英 转炉用合金料生产工艺优化[会议论文]-2005 6. 迟沁芳.尹卫平.李洪春.刘广 转炉炼钢钢水氧含量变化规律的研究[会议论文]-2002 7. 徐金瑜.游敏.苏国亮.王飞.张康.邱会东.XU Jin-yu.YOU Min.SU Guo-liang.WANG Fei.ZHANG Kang.QIU Hui-dong 炼钢脱氧剂的研究进展[期刊论文]-重庆科技学院学报(自然科学版)2011,13(3) 8. 李忠思.董方.王玉莲.王玉刚 含钡铁合金生产与使用对环境的污染[会议论文]-2004 9. 耿志军 转炉采用热补偿工艺提高终点命中率的研究[期刊论文]-钢铁2004,39(9) 10. 贾建辉.田焱君.JIA Jian-hui.TIAN Yan-jun 铝锰钛合金用于钢水脱氧的研究与应用[期刊论文]-河北冶金2005(4)
RESEARCH oN DEoXIDATIoN AND SILICoN AND MANGANESE CoNTRoL oF CoNVERTER STEELMAKING
I,IU Wenhui
(Shaoguan Iron and Steel Group Co.,I.td.)
ABSTRACT Thc main grades of convefter steel are carbon steel and low alloy steel.The
巾于在钢水脱氧比较好的情况下才加入锰铁,
锰的收得率旨定会提高,更为重要的是稳定锰的收 得率。对锰含量较高的钢种.锰元素的命中率也相应
提高。 对锰含量较高的钢种可按L述的新顺序加入目
标值80%~90%的锰铁,留下10%~20%的锰铁 在钢包吹氩时酌量补加。对出钢量波动、钢水氧化性 强弱、r渣量不同等有相当程度的调节作Hj。