高炉中有害元素的平衡分析及其脱除
炼铁原理剖析高炉内铁水中杂质的生成和去除机制
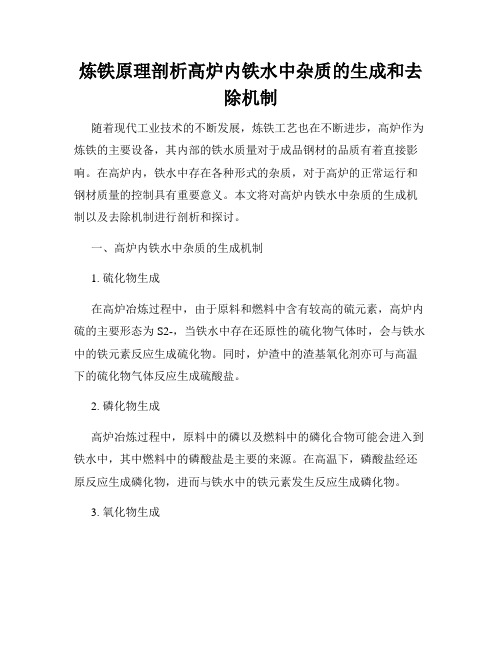
炼铁原理剖析高炉内铁水中杂质的生成和去除机制随着现代工业技术的不断发展,炼铁工艺也在不断进步,高炉作为炼铁的主要设备,其内部的铁水质量对于成品钢材的品质有着直接影响。
在高炉内,铁水中存在各种形式的杂质,对于高炉的正常运行和钢材质量的控制具有重要意义。
本文将对高炉内铁水中杂质的生成机制以及去除机制进行剖析和探讨。
一、高炉内铁水中杂质的生成机制1. 硫化物生成在高炉冶炼过程中,由于原料和燃料中含有较高的硫元素,高炉内硫的主要形态为S2-,当铁水中存在还原性的硫化物气体时,会与铁水中的铁元素反应生成硫化物。
同时,炉渣中的渣基氧化剂亦可与高温下的硫化物气体反应生成硫酸盐。
2. 磷化物生成高炉冶炼过程中,原料中的磷以及燃料中的磷化合物可能会进入到铁水中,其中燃料中的磷酸盐是主要的来源。
在高温下,磷酸盐经还原反应生成磷化物,进而与铁水中的铁元素发生反应生成磷化物。
3. 氧化物生成高炉内的氧气和含氧化物的原料在高温下会与铁水中的铁元素反应生成氧化物。
氧化物中常见的有氧化铁、二氧化硅等,它们的生成会对铁水的质量产生一定的影响。
4. 氨气生成高炉内铁水中的氨气主要来自于焦炭燃烧过程中的氨基化合物。
在高温下,氨基化合物释放出氨气,进而通过反应生成铁水中的氨气。
二、高炉内铁水中杂质的去除机制1. 物理去除对于某些密度较大的杂质,可以采用物理方法进行去除。
例如,采用沉淀、过滤等方式将密度较大的杂质从铁水中分离出来,提高铁水的纯度。
2. 矿物质添加剂在高炉冶炼过程中,可以添加一些矿物质来吸附和脱除铁水中的杂质。
例如,通过添加含氧化钠、氧化镁等矿物质来吸附和捕捉铁水中的氧化物、硫化物等杂质。
3. 化学反应去除通过化学反应使铁水中的杂质发生转化,然后以其他形式被捕获和去除。
例如,通过向铁水中加入一定量的石灰或石灰石,使铁水中的硫酸盐反应生成硫化钙沉淀,从而将硫酸盐去除。
4. 渣化作用高炉内的炉渣可以起到吸附和分离杂质的作用。
高炉有害元素调查分析

高炉有害元素调查分析摘要:鉴于1#高炉(580m3)高炉生产出现放铁期间白烟大、铁水物理热严重不足、炉况不顺、悬料、结瘤等问题,调研了高炉有害金属的分布情况。
通过现场取样,测定试样中有害金属含量,计算分析了高炉有害金属的分布与平衡。
结果表明:烧结矿及球团矿中有害金属含量是影响高炉有害金属负荷的主要因素,排有害金属主要由高炉渣、除尘灰完成。
结合实际生产情况,提出了防治高炉有害金属的途径。
关键词:有害金属;分布;有害金属负荷;平衡由于受到铁矿石资源的限制,加上矿源复杂,新疆金特钢铁公司炼铁高炉原燃料中有害金属含量较高。
在不断寻求新资源的过程中,忽略了对有害金属元素的控制,使得有害金属对高炉冶炼的危害逐渐暴露出来。
Zn、Pb、Na2O等元素入炉以后一方面破坏原燃料的冶炼性能,影响高炉技术经济指标的提升,高炉出现悬料、结瘤、炉况不顺、消耗升高,其危害随着生产进行而日益严重。
另一方面则对高炉砖衬进行侵蚀,给高炉长寿和组织安全稳定经济生产造成极大危害。
因此非常有必要对高炉Zn、Pb、Na2O等有害元素的入炉及排出情况进行长期监控,以便为高炉长寿、正常生产组织提供参考。
在本文中“碱负荷”是指每吨铁由炉料带入高炉的碱金属总量;“碱平衡”是指高炉冶炼过程中碱金属的收支明细表,反应了高炉在冶炼过程中碱金属的去留情况。
锌危害:(1)影响铁矿石和焦炭的冶金性能。
渗入铁矿石和焦炭孔隙中的锌蒸气沉积氧化成氧化锌后,一方面由于体积的膨胀会增加铁矿石和焦炭的热应力,破坏铁矿石和焦炭的热态强度,并导致烧结矿和球团矿的低温还原粉化指数有所提高,焦炭的反应性增加,反应后强度降低;另一方面,锌蒸气也会堵塞铁矿石和焦炭的孔隙,恶化高炉料柱的透气性,给高炉冶炼带来不利的影响。
(2)影响高炉的操作。
锌蒸气在上升过程中被氧化,氧化锌会冷凝黏结在上升管、下降管、炉喉及炉身上部砖衬上或大钟内表面,并形成高锌尘垢,并逐渐转变为高锌炉瘤。
炉喉及炉身上部砖衬上的锌瘤破坏炉料的下降和煤气流的上升,破坏炉料和煤气的正常分布,导致炉况失常。
衡钢1号高炉锌平衡研究及减轻锌负荷的措施

衡钢1号高炉锌平衡研究及减轻锌负荷的措施收藏本文分享锌在高炉炼铁过程中是一种微量的有害元素,不仅影响高炉的冶炼,对高炉长寿也至关重要。
衡钢1号高炉自2009年5月开炉以来,生产顺行稳定,但一直未对锌负荷作仔细研究。
为了详细了解衡钢高炉锌的分布情况,避免过重的锌负荷对高炉操作及生产带来不利影响,有必要对锌负荷和锌平衡进行分析,弄清锌的来源、去向,同时也为布袋灰、瓦斯灰等的再回收利用提供有效数据。
1锌对高炉的影响锌是与铁矿石共存的一种元素,它在铁矿石中常以闪锌矿(ZnS)的形式存在,有时也以碳酸盐或硅酸盐状态存在。
在天然铁矿中锌的质量分数是微量的,但由于其还原温度低、液态锌的沸点低,几乎不能被渣铁吸收。
锌对高炉的影响主要体现在以下2方面。
1)对高炉冶炼的影响。
锌在高炉炉内的循环会使热量发生转移,热量从高温区转移到了低温区,导致渣铁温度降低,渣的黏度升高,从而不利于高炉顺行和脱硫;另外,锌蒸气在高炉中上部冷凝后,黏附在炉墙和炉料上,易形成炉瘤,堵塞炉料气孔,恶化料柱透气性;除此以外,锌蒸气还会在料块表面冷凝,形成锌的金属或氧化物的薄膜,会弱化焦炭和矿石的冶金性能,降低料块的强度和还原性。
锌负荷的升高,还会引起焦比的上升。
还原1 kg锌需11 (本文共计3页)......[继续阅读本文]高炉内锌平衡与结瘤的分析锌是高炉有害元素之一,其在高炉内的循环富集会对高炉生产带来极大的危害,富集过剩严重影响高炉的热制度、煤气流的分布、高炉消耗等,在一定条件下还会造成炉内结瘤,严重影响正常生产。
为明确湘钢高炉的高炉内锌负荷及其平衡状况对内部结瘤的影响,本文通过现场取样检测,并计算分析了湘钢3、4号高炉的锌负荷和锌平衡状况,同时对结瘤瘤体进行了取样分析。
一、试验方法与数据采集分别对湘钢3BF、4BF原燃料进行取样,每座高炉取6组样,第1天取入炉的原、燃料样,包括烧结矿、球团矿、澳矿(3BF)、南非矿(4BF)、焦炭和煤粉,第2天取对应的高炉产物试样,包括铁水、高炉渣、瓦斯灰和除尘灰等。
高炉铁水有害元素分析与控制
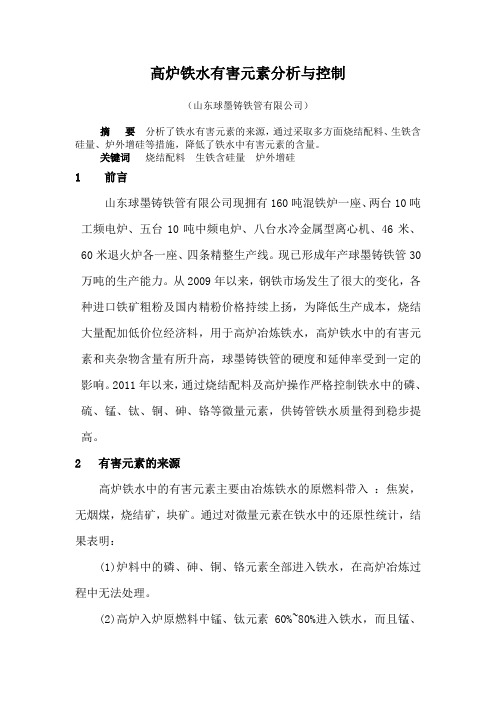
高炉铁水有害元素分析与控制(山东球墨铸铁管有限公司)摘要分析了铁水有害元素的来源,通过采取多方面烧结配料、生铁含硅量、炉外增硅等措施,降低了铁水中有害元素的含量。
关键词烧结配料生铁含硅量炉外增硅1 前言山东球墨铸铁管有限公司现拥有160吨混铁炉一座、两台10吨工频电炉、五台10吨中频电炉、八台水冷金属型离心机、46米、60米退火炉各一座、四条精整生产线。
现已形成年产球墨铸铁管30万吨的生产能力。
从2009年以来,钢铁市场发生了很大的变化,各种进口铁矿粗粉及国内精粉价格持续上扬,为降低生产成本,烧结大量配加低价位经济料,用于高炉冶炼铁水,高炉铁水中的有害元素和夹杂物含量有所升高,球墨铸铁管的硬度和延伸率受到一定的影响。
2011年以来,通过烧结配料及高炉操作严格控制铁水中的磷、硫、锰、钛、铜、砷、铬等微量元素,供铸管铁水质量得到稳步提高。
2 有害元素的来源高炉铁水中的有害元素主要由冶炼铁水的原燃料带入:焦炭,无烟煤,烧结矿,块矿。
通过对微量元素在铁水中的还原性统计,结果表明:(1)炉料中的磷、砷、铜、铬元素全部进入铁水,在高炉冶炼过程中无法处理。
(2)高炉入炉原燃料中锰、钛元素60%~80%进入铁水,而且锰、钛元素在铁水中含量与高炉铁水含硅量呈正相关性关系。
原始生铁含硅量的提高有助于有害元素含量的升高。
3 不同元素对铸铁管的危害供铸管铁水中一些元素达到一定值会对铸铁管的退火产生一定的影响,进而降低对铸铁管的产品质量:磷是铸铁中的常存元素,它对球墨铸铁的机械性能,尤其是冲击韧性和塑性有明显的不良影响,因此总是作为有害元素对待。
其主要原因是共晶团晶界产生的磷共晶脆相,磷共晶呈多角状分布于共晶团边界,急剧恶化球墨铸铁的力学性能,使球墨铸铁韧性下降;其次是磷阻碍珠光体的分解,又能固溶于铁素体中,这些都能降低韧性。
磷的质量分数每增加0.01%时,脆性转变温度升高4.0~4.5℃。
当磷的质量分数超过0.16%时,脆性转变温度已在室温以上,冲击断口出现脆性断裂。
有害元素对高炉冶炼的影响

立志当早,存高远有害元素对高炉冶炼的影响有害元素通常指硫(S)、磷(P)、钾(K)、钠(Na)、铅(Pb)、Zn(锌)、As(砷)、Cu。
通常高炉冶炼对铁矿石要求如下:Pb 小于0.1%、Zn 小于0.1%、As 小于0.07%、Cu 小于0.2%、K2O+Na2O≤0.25%。
硫(S):硫对钢材是最为有害的成份,它使钢材产生热脆性。
铁矿石中硫含量高,高炉脱硫成本增大,所以入炉铁矿石含硫愈少愈好。
磷(P):磷对钢材来说也是常见有害元素之一,它使钢材产生冷脆性。
铁矿石中的磷,在高炉冶炼时100%进入生铁,烧结也不能脱磷,控制生铁含磷量主要是靠控制铁矿石含磷量。
脱磷只能通过炼钢来进行,增加了炼钢的脱磷成本。
因此,铁矿石含磷越低越好。
碱金属:碱金属主要有钾和钠。
钾、钠对高炉的影响不是正比例性质,高炉本身有一定的排碱能力,碱金属在控制范围内对高炉影响不大。
但是入炉铁矿石碱金属含量太多,超过高炉排碱能力,就会形成碱金属富集,导致高炉中上部炉料碱金属含量大大超过入炉料原始水平。
铁矿石含有较多的碱金属极易造成软化温度降低,软熔带上移,不利于发展间接还原,造成焦比升高。
球团含有碱金属会造成球团异常膨胀引起严重粉化,恶化料柱透气性。
碱金属对焦炭性能破坏也很严重。
另外,高炉中上部碱金属化合物黏附在炉墙上,促使炉墙结厚、结瘤并破坏砖衬。
因此,铁矿石含碱金属越低越好。
铅(Pb):铅在高炉中几乎全部被还原,由于密度高达11.34t∕m³,故沉于死铁层之下,易破坏炉底砖缝,有可能会造成炉底烧穿。
锌(Zn):锌很容易气化,锌蒸汽容易进入砖缝,氧化成为ZnO 后膨胀,破坏炉身上部耐火砖衬。
有害元素对高炉操作的影响
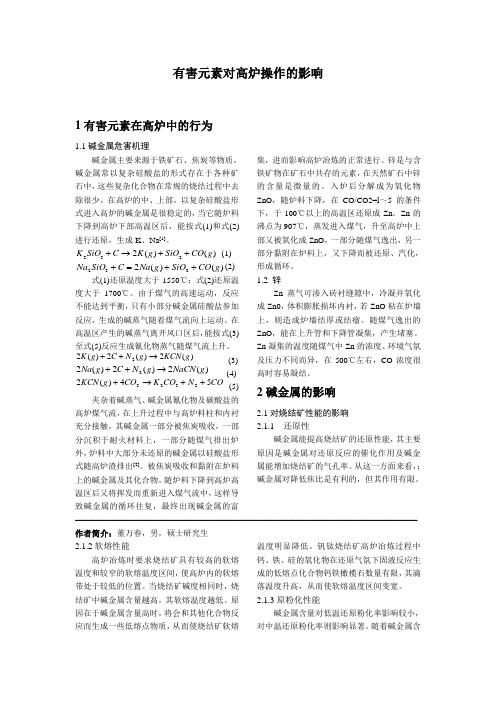
有害元素对高炉操作的影响1有害元素在高炉中的行为1.1碱金属危害机理碱金属主要来源于铁矿石、焦炭等物质,碱金属常以复杂硅酸盐的形式存在于各种矿石中,这些复杂化合物在常规的烧结过程中去除很少。
在高炉的中、上部,以复杂硅酸盐形式进入高炉的碱金属是很稳定的,当它随炉料下降到高炉下部高温区后,能按式(1)和式(2)进行还原,生成K 、Na [1]。
)()(2232g CO SiO g K C SiO K ++→+ (1))()(2232g CO SiO g Na C SiO Na ++=+(2)式(1)还原温度大于1550℃;式(2)还原温度大于1700℃。
由于煤气的高速运动,反应不能达到平衡,只有小部分碱金属硅酸盐参加反应,生成的碱蒸气随着煤气流向上运动。
在高温区产生的碱蒸气离开风口区后,能按式(3)至式(5)反应生成氰化物蒸气随煤气流上升。
)(2)(2)(22g KCN g N C g K →++ (3))(2)(2)(22g NaCN g N C g Na →++ (4) CON CO K COg KCN 54)(22322++→+ (5)夹杂着碱蒸气、碱金属氰化物及碳酸盐的高炉煤气流,在上升过程中与高炉料柱和内衬充分接触,其碱金属一部分被焦炭吸收,一部分沉积于耐火材料上,一部分随煤气排出炉外,炉料中大部分未还原的碱金属以硅酸盐形式随高炉渣排出[2]。
被焦炭吸收和黏附在炉料上的碱金属及其化合物,随炉料下降到高炉高温区后又将挥发而重新进入煤气流中,这样导致碱金属的循环往复,最终出现碱金属的富集,进而影响高炉冶炼的正常进行。
锌是与含铁矿物在矿石中共存的元素,在天然矿石中锌的含量是微量的。
入炉后分解成为氧化物ZnO ,随炉料下降,在CO/CO2=l ~5的条件下,于100℃以上的高温区还原成Zn 。
Zn 的沸点为907℃,蒸发进入煤气,升至高炉中上部又被氧化成ZnO ,一部分随煤气逸出,另一部分黏附在炉料上,又下降而被还原、汽化,形成循环。
炼铁高炉入炉原料中有害微量元素分析解决方案工作报告
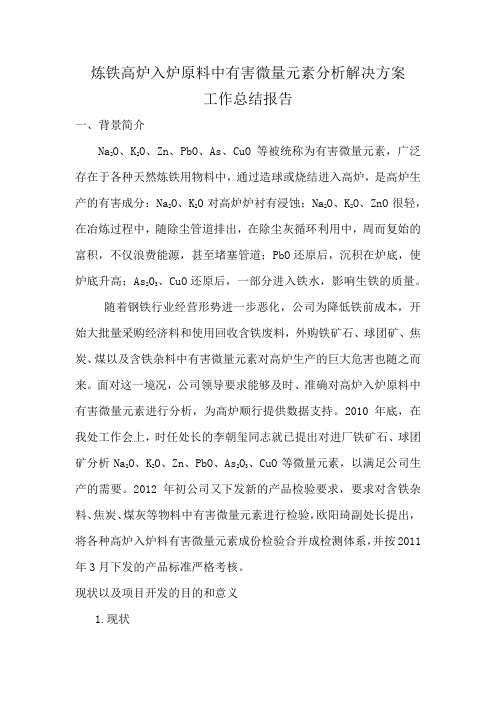
炼铁高炉入炉原料中有害微量元素分析解决方案工作总结报告一、背景简介Na2O、K2O、Zn、PbO、As、CuO等被统称为有害微量元素,广泛存在于各种天然炼铁用物料中,通过造球或烧结进入高炉,是高炉生产的有害成分:Na2O、K2O对高炉炉衬有浸蚀;Na2O、K2O、ZnO很轻,在冶炼过程中,随除尘管道排出,在除尘灰循环利用中,周而复始的富积,不仅浪费能源,甚至堵塞管道;PbO还原后,沉积在炉底,使炉底升高;As2O3、CuO还原后,一部分进入铁水,影响生铁的质量。
随着钢铁行业经营形势进一步恶化,公司为降低铁前成本,开始大批量采购经济料和使用回收含铁废料,外购铁矿石、球团矿、焦炭、煤以及含铁杂料中有害微量元素对高炉生产的巨大危害也随之而来。
面对这一境况,公司领导要求能够及时、准确对高炉入炉原料中有害微量元素进行分析,为高炉顺行提供数据支持。
2010年底,在我处工作会上,时任处长的李朝玺同志就已提出对进厂铁矿石、球团矿分析Na2O、K2O、Zn、PbO、As2O3、CuO等微量元素,以满足公司生产的需要。
2012年初公司又下发新的产品检验要求,要求对含铁杂料、焦炭、煤灰等物料中有害微量元素进行检验,欧阳琦副处长提出,将各种高炉入炉料有害微量元素成份检验合并成检测体系,并按2011年3月下发的产品标准严格考核。
现状以及项目开发的目的和意义1.现状(1)Na2O、K2O、Zn、PbO、As、CuO等检验项目在各种物料中的含量都很微少,想要准确测定微量或痕量的元素,一般都采用ICP分析或原子吸收分析方法。
这两种方法首先都需对待分析样品进行溶解,溶解的过程比较漫长,分析过程稍有差池就会造成分析失败,检验周期长、操作复杂也是这两种方法不可避免的缺点,对于大批量的进厂铁矿石、球团矿、焦炭、煤灰、含铁废料检验,已很难适应快速生产节奏的需要。
(2)X荧光仪分析速度快、对样品要求相对简单,在2011年已成功开发出铁矿石、球团矿微量元素快速分析方法,但该方法只适用于物质成份含量简单且相对稳定的铁矿石品种,焦炭、煤灰、含铁杂料等新品种因物相组成不同、成份结构复杂,不能简单用一种方法分析检验,需要一整套的系列分析解决方案,有针对性的对各种物料使用最为合适的分析方法。
高炉有害元素分析及控制

高炉有害元素分析及控制摘要:由于成矿原因和炼铁原料来源复杂,炼铁原料中含有锌杂质,因锌有害于高炉炼铁,要求入炉原料中锌含量应分别小于0.15 kg/t,而我国很多钢厂入炉原料中锌含量高于此标准。
近年来,国内钢铁产能过剩,钢铁价格持续低迷,钢企为节省成本少用国外铁矿石,多用周边品质差、价格低廉的国产矿石替代,使得有些高炉锌危害更加突出。
基于此,本文主要分析高炉内锌的主要来源以及对高炉的危害,提出了控制有害元素的措施和建议。
关键词:高炉炼铁;有害元素;锌元素;分析控制1锌在高炉中的行为机理1.1高炉内的循环铁矿石中的锌少量主要以铁酸盐(ZnO•Fe2O3)硅酸盐(2ZnO•SiO2)及硫化物(ZnS)的形式存在。
其锌硫化物先转化为复杂的氧化物,然后再在大于1000℃的高温区被CO还原为气态。
沸点为907℃时,加热为蒸汽,随煤气上升,到达温度较低的区域(580℃)时冷凝而再氧化。
再氧化形成的锌氧化细粒附着于上升煤气的粉尘时就被带出炉外,附着于下降的炉料时就再次进入高温区。
如此周而复始,就形成了在高炉内的富集现象。
1.2高炉内部的富集含矿物进入高炉后生成,固态ZnO,随炉料下降过程中被C、CO和Fe还原。
在高炉下部1000℃以上的高温区,ZnO还原出来的Zn全部被汽化为蒸汽分散于煤气中并随之上升,蒸汽到达高炉上部低温区时冷凝而再被氧化形成ZnO细粒,一部分随煤气从炉顶逸出炉外,一部分附着于下降的炉料再次进入高温区重新被还原和汽化,周而复始,形成了在高炉内的锌循环富集现象。
在高炉内的循环富集量可达到入炉料含量的10~30倍。
1.3在烧结、高炉系统间的循环富含锌元素的高炉煤气除尘灰被回收,用于烧结配料,含锌的烧结作为炼铁主原料重新进入高炉,形成了锌在烧结、高炉系统间的循环。
2锌对高炉危害2.1锌对高炉耐材及风口的破坏Zn被还原后,在>907℃时成为锌蒸汽,进入煤气中,渗入高炉上部耐材的缝隙,氧化后使其体积膨胀,破坏高炉上部的炉墙结构,严重时甚至可以导致炉壳胀裂,使煤气泄漏,造成一系列恶性事故。
有害元素对高炉炼铁的影响及控制措施
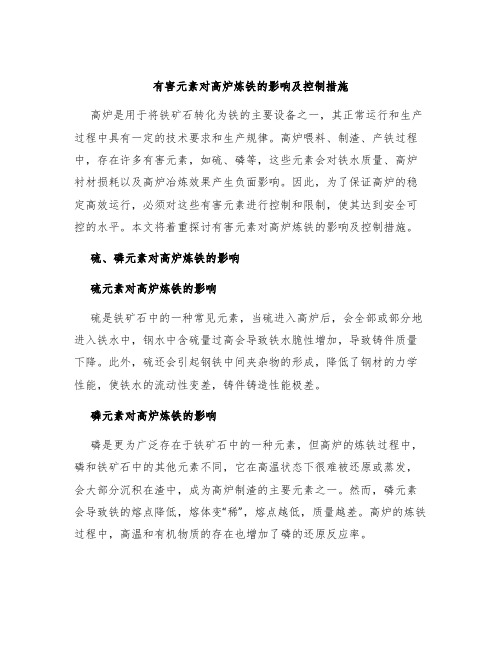
有害元素对高炉炼铁的影响及控制措施高炉是用于将铁矿石转化为铁的主要设备之一,其正常运行和生产过程中具有一定的技术要求和生产规律。
高炉喂料、制渣、产铁过程中,存在许多有害元素,如硫、磷等,这些元素会对铁水质量、高炉衬材损耗以及高炉冶炼效果产生负面影响。
因此,为了保证高炉的稳定高效运行,必须对这些有害元素进行控制和限制,使其达到安全可控的水平。
本文将着重探讨有害元素对高炉炼铁的影响及控制措施。
硫、磷元素对高炉炼铁的影响硫元素对高炉炼铁的影响硫是铁矿石中的一种常见元素,当硫进入高炉后,会全部或部分地进入铁水中,钢水中含硫量过高会导致铁水脆性增加,导致铸件质量下降。
此外,硫还会引起钢铁中间夹杂物的形成,降低了钢材的力学性能,使铁水的流动性变差,铸件铸造性能极差。
磷元素对高炉炼铁的影响磷是更为广泛存在于铁矿石中的一种元素,但高炉的炼铁过程中,磷和铁矿石中的其他元素不同,它在高温状态下很难被还原或蒸发,会大部分沉积在渣中,成为高炉制渣的主要元素之一。
然而,磷元素会导致铁的熔点降低,熔体变“稀”,熔点越低,质量越差。
高炉的炼铁过程中,高温和有机物质的存在也增加了磷的还原反应率。
控制措施在高炉炼铁的生产过程中,有害元素的控制是必不可少的一环。
下面将介绍一些常用的控制措施。
调整原料成分高炉熟料中的有害元素主要来源于铁矿石中,而铁矿石的含硫、含磷量的高低对高炉冶炼过程有很大的影响。
因此,一个有效的控制措施就是调整原料成分。
可以根据熟料化验分析结果预先掌握熟料成分,对成分含有过高有害元素的铁矿石进行挑选和筛选,或者采用掺混矿的方法控制高炉熟料的含硫、含磷量。
清洗高炉和加入流化剂在高炉生产过程中,很多有害元素都会在炉壁上结合和析出。
为了保证高炉正常运行和生产,必须定期对高炉进行清洗。
此外,加入流化剂,可以起到一定的促进还原反应和控制有害元素的效果。
在加入流化剂的过程中,可以调整流化剂的配比和添加时间,以达到较好的控制效果。
高炉有害元素利用分析

高炉有害元素的分析一、有害元素的来源通过对原燃料检测成份分析可以看出:1、碱金属来源主要来焦炭,其次是烧结矿和球团矿;2、Pb、Zn的来源,主要是球团矿和烧结矿。
Pb、Zn的主要来源是生产烧结矿、球团矿的精矿粉。
二、对高炉的影响1、有害元素破坏砖衬及炉体。
原料中的Zn如果长期超标,就会使高炉中Zn富集大量,随着生产的持续进行,Pb、Zn等在高温下就会渗透进入炉缸耐材砖缝,严重时会使风口中套变形,甚至会出现大套法兰上翘开裂冒煤气现象,并伴随煤气泄漏明显发展最终造成炉缸炉皮开裂。
2、造成炉皮开裂,冷却板损坏。
由于有害元素在炉内富集,在炉身中下部软融带附近,有害元素吸附或渗透进入砖缝,造成砖衬被侵蚀和异常膨胀,使冷却板暴露在高温气流中易受冲击而损坏。
随着原燃质量下降,有害元素入炉增加,在内的富集增加,对砖衬的破坏力度加大。
造成炉皮开裂的主要原因是使用含Zn高的原料的结果,从风口粘结物取样分析可知,zn在炉知富集是造成炉缸炉皮开裂的主要原因。
3、造成炉缸,炉底侵蚀速度加快。
碱金属,Zn等有害元素易在炉内循环富集,K、Na以液态或固态粉状化合物粘附在炉衬上破坏砖衬,Zn则以蒸汽形式渗入砖衬缝隙中,冷凝氧化成ZnO后体积膨胀损坏内衬,使高温铁水能够顺利渗入砖缝,造成水温差上升。
4、破坏焦炭强度,炉况顺行度下降。
碱金属的吸附首先从焦炭的气孔开始,而后逐步向焦炭内部扩散随着焦炭在碱金属蒸汽内暴露的时间延长,碱金属的吸附量逐渐增多,焦炭基质部分扩散的碱金属会侵蚀到石墨晶体内部,破坏原有的结构,使焦炭产生较大的体积膨胀,导致焦炭破碎,焦炭反应性增加,反应后强度降低。
5、致使高炉结瘤,严重影响高炉的生产。
大量研究表明,碱金属是高炉炉瘤形成的主要原因。
碱金属氧化物在高炉下部被还原为K、Na蒸气或生成K(Na)CN,随煤气上升到高炉上部,同炉衬发生反应,使砖衬软化和熔融,黏结粉料。
不断进行,就会逐渐形成炉瘤或结厚。
原料中含有较多碱金属,加上操作制度不合适,原料粉末多,炉渣排碱能力差,高炉便会出现频繁结瘤现象。
八钢高炉有害元素锌的分析与控制

后废 物 的再利 用 , 高炉 内 的锌 元 素增 加 , 高 炉 造 对
成影 响 , 尤其是 2 0 0 9年 度 八 钢老 区高 炉 的风 口熔 损及 炉 凉事故 。在 总结 恢 复 炉 况经 验 中发 现有 害
K e W o d b a tf r c Zi y r s: l s u na e; nc
新疆 八钢 高炉炼 铁 原 料 中锌 等 有 害元 素 的含 量相 对偏 高 。近几 年 , 炉计 划 休 风期 间 , 更 换 高 在
坏风 口时 , 口流 出金属 锌 。2 0 风 0 8年 后 , 后及 钢 铁
温度逐 渐上 升 , 缸 容 易 粘 结 , 缸 砖 衬 上 涨 , 炉 炉 砖 衬与冷却壁之 间产生气 隙, 容易出现铁 口浅和 冒
煤 气现 象 。
3 高 炉 锌 危 害 处 理 方 法
3 1 切 断高炉 内锌 的根 源 .
和尖 晶石 ( n . I , 们 都 是 难 溶 物 质 。 因 Z O A: ) 他 0 此 , 炉衬 表 面上容 易生 成 附 着 物 , 在 如果 原 料 条件
过 程 中部分 锌 蒸 气 被 冷 凝 或 被 C 氧 化 为 Z O O n。
又随炉 料 下降到 炉缸 中。炉 缸 热 严重 不 足 造 成煤
止边 缘煤 气流 过分 发展 , 持 较低 的炉 顶 温度 , 保 防 止 出现高 炉 上 部 结 瘤 。改 善 炉 渣 流 动 性 , 持 较 保
差 , 温又 频 繁 波 动 , 附着 物 层 层 相 粘 , 长 越 炉 则 越 大, 最后 导致 结瘤 。
2 3 锌 在炉 衬 内部沉 积 , 成炉 衬膨 胀 、 坏 . 造 破
八钢A高炉有害元素分析及对策

2008年第3期新疆钢铁总107期)kf压l A高炉有害元素分析及对策张永旺李涛(宝钢集团八钢公司炼铁分公司)摘要:介绍了对八钢A高炉开炉以来不同时期的有害元素负荷的跟踪调查.对A高炉有害元素负荷的变化趋势、分布特点、富集原因以及有害元素对高炉冶炼的影响进行了分析。
提出了八钢A高炉控制有害元素负荷的措施及建议。
关键词:高炉;碱金属f锌负荷中图分类号:T F549文献标识码:A文章编号:1672一d22^(2008)03--0018一01l前言近些年,随着八钢炼铁生产规模的迅速扩大,八钢的炼铁技术也逐步向精细化的道路发展。
特别是大型高炉投产后.对原燃料的质量要求也更加严格,除了对原料的品位、杂质含量、机械强度等有更高的要求外.原料中有害元素的含量和有害元素对高炉生产的负面影响也越来越引起广泛地重视。
八钢在A高炉(2500m3)投产前,就对原燃料中对应炉生产有危害的元素进行了跟踪和分析,为大型高炉的稳定顺行打下了基础。
2有害元素对炼铁生产的影响对炼铁生产有危害元素主要是指碱金属(K:O、N a:O)、Pb、Z n等。
这些元素在高炉内具有易形成低熔点物质、发生膨胀、吸收热量和改变原料属性的特性。
炼铁原燃料中有害元素负荷的增加。
给高炉生产的稳定顺行带来了很大的不确定性和操作难度,主要集中表现在两个方面。
2.1对炉内冶炼的影响(1)有害元素易在炉内形成低熔点物质.导致高炉软熔带上移、变宽.透气性减弱.高炉顺行恶化;(2)有害元素在炉缸高温区发生的还原反应和气化反应,都将吸收大量的热能,从而降低了炉缸温度.引起炉况波动.同时增加了燃料消耗;(3)有害元素易在炉墙处结瘤.破坏了煤气流的合理分布。
同时.有害元素气体在炉内的反复膨胀.也降低了炉衬的使用寿命。
2.2对原燃料质量属性的影响(1)随着碱金属在炉内的循环.使矿石的软化温度降低,烧结矿的低温还原粉化性能变差,同时也引起球团矿的异常膨胀、粉化;(2)碱金属对焦炭的气化反应起到催化作用,引起焦炭气孔壁迅速变薄,焦炭反应后强度随吸附碱金属含量的增加而下降。
[教育]有害元素对高炉的危害含量和有效预防措施
![[教育]有害元素对高炉的危害含量和有效预防措施](https://img.taocdn.com/s3/m/3a049b3bd0d233d4b04e6946.png)
高炉碱金属对铁矿石冶金性能的影响
1. 1)碱金属能明显促进烧结矿的还原,对降低焦比有利。 2. 2)少量碱金属能够提高烧结矿的软熔温度,使得高炉软
高炉中碱金属分布状况
•焦炭中碱金属分布状况
•焦炭中K含量分布曲线
•焦炭中Na含量分布曲线
•焦炭中的K2O和Na2O沿高度变化的规律基本相同。到风口回旋区上沿时,达到最 大值,可见此区域为碱金属富集量最大区域,此区域炉墙耐火材料受碱金属的破 坏极为严重,建议砌筑高炉是将风口上部炉腹区域的耐材重点考虑其抗碱金属侵 蚀的性能。
耐火材料中有害元素的分布研究
•炉喉部分取样点————
•炉身中上部取样点— —
•炉身下部取样点————
• 炉腰与炉腹取样点1— —
• 炉腰与炉腹取样点2— —
•1#
•5#
•取样位置及高炉内部温度分布
•热面
•耐火砖
•冷面
•取样点-内部 •取样点-中部 •取样点-外部
•耐火砖试样取样图
Na2O K2O Zn Pb
有害元素 百分含量 %
吨铁含量 Kg/tHM 百分含量 %
[教育]有害元素对高炉的危 害含量和有效预防措施
提纲
1. 有害元素在高炉中的影响 2. 碱金属在高炉中的分布-高炉解剖 3. 有害元素的来源-碱金属平衡计算 4. 排减措施
•1碱金属对高炉的危害主要表现
1)提前并加剧CO2对焦炭的气化反应,缩小了间接还原区,扩大了 直接还原区,进而引起焦比升高;降低焦炭的粒度和强度,从而降 低料柱特别是软熔带气窗的透气性,引起风口破损。
高炉有害元素研究
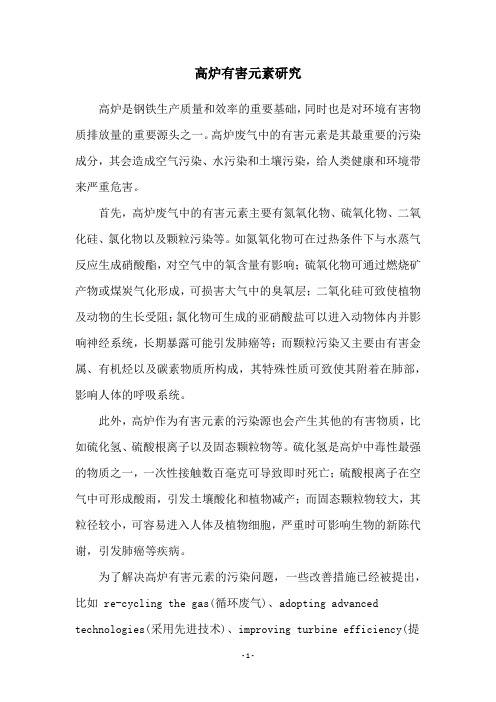
高炉有害元素研究高炉是钢铁生产质量和效率的重要基础,同时也是对环境有害物质排放量的重要源头之一。
高炉废气中的有害元素是其最重要的污染成分,其会造成空气污染、水污染和土壤污染,给人类健康和环境带来严重危害。
首先,高炉废气中的有害元素主要有氮氧化物、硫氧化物、二氧化硅、氯化物以及颗粒污染等。
如氮氧化物可在过热条件下与水蒸气反应生成硝酸酯,对空气中的氧含量有影响;硫氧化物可通过燃烧矿产物或煤炭气化形成,可损害大气中的臭氧层;二氧化硅可致使植物及动物的生长受阻;氯化物可生成的亚硝酸盐可以进入动物体内并影响神经系统,长期暴露可能引发肺癌等;而颗粒污染又主要由有害金属、有机烃以及碳素物质所构成,其特殊性质可致使其附着在肺部,影响人体的呼吸系统。
此外,高炉作为有害元素的污染源也会产生其他的有害物质,比如硫化氢、硫酸根离子以及固态颗粒物等。
硫化氢是高炉中毒性最强的物质之一,一次性接触数百毫克可导致即时死亡;硫酸根离子在空气中可形成酸雨,引发土壤酸化和植物减产;而固态颗粒物较大,其粒径较小,可容易进入人体及植物细胞,严重时可影响生物的新陈代谢,引发肺癌等疾病。
为了解决高炉有害元素的污染问题,一些改善措施已经被提出,比如 re-cycling the gas(循环废气)、adopting advanced technologies(采用先进技术)、improving turbine efficiency(提高汽轮机效率)、heat recovery(热回收)以及 using heat-resistant materials(使用耐热材料)等。
其中,采用循环废气技术可以重复利用污染物,减少污染的产生;而采用先进技术则可有效提高锅炉的效率,减少使用能源;同时,采用热回收技术可有效恢复热能,减少热量损失;此外,选用耐热材料也可以减少有害物质的排放,达到节能减排的目的。
总之,钢铁行业中高炉有害元素的污染越来越受到重视,相关政策及法规也将持续不断的完善。
高炉本体系统危险有害因素分析
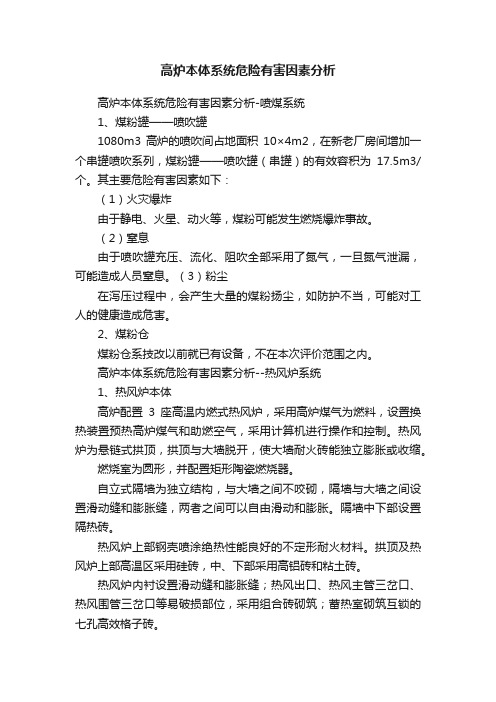
高炉本体系统危险有害因素分析高炉本体系统危险有害因素分析-喷煤系统1、煤粉罐——喷吹罐1080m3高炉的喷吹间占地面积10×4m2,在新老厂房间增加一个串罐喷吹系列,煤粉罐——喷吹罐(串罐)的有效容积为17.5m3/个。
其主要危险有害因素如下:(1)火灾爆炸由于静电、火星、动火等,煤粉可能发生燃烧爆炸事故。
(2)窒息由于喷吹罐充压、流化、阻吹全部采用了氮气,一旦氮气泄漏,可能造成人员窒息。
(3)粉尘在泻压过程中,会产生大量的煤粉扬尘,如防护不当,可能对工人的健康造成危害。
2、煤粉仓煤粉仓系技改以前就已有设备,不在本次评价范围之内。
高炉本体系统危险有害因素分析--热风炉系统1、热风炉本体高炉配置3座高温内燃式热风炉,采用高炉煤气为燃料,设置换热装置预热高炉煤气和助燃空气,采用计算机进行操作和控制。
热风炉为悬链式拱顶,拱顶与大墙脱开,使大墙耐火砖能独立膨胀或收缩。
燃烧室为圆形,并配置矩形陶瓷燃烧器。
自立式隔墙为独立结构,与大墙之间不咬砌,隔墙与大墙之间设置滑动缝和膨胀缝,两者之间可以自由滑动和膨胀。
隔墙中下部设置隔热砖。
热风炉上部钢壳喷涂绝热性能良好的不定形耐火材料。
拱顶及热风炉上部高温区采用硅砖,中、下部采用高铝砖和粘土砖。
热风炉内衬设置滑动缝和膨胀缝;热风出口、热风主管三岔口、热风围管三岔口等易破损部位,采用组合砖砌筑;蓄热室砌筑互锁的七孔高效格子砖。
其主要危险有害因素如下:(1)噪音a、混合煤气在炉内燃烧发出强大而剧烈的噪音。
b、机械动力装置在运转时所发出的噪音。
(2)触电热风炉本体内存在大量电驱动设备和装置,且部分需要通过接拉私线,加之炉体布局复杂,若检查不及时,可能存在漏电线路或装置,引发触电事故。
(3)高处坠落热风炉全高38.46m,炉壳内径为Φ7600mm/Φ7720/Φ9220mm。
整座炉体按工艺需要,设置多层工作平台。
在作业过程中,可能存在从楼梯或护栏处坠落。
(4)灼伤热风炉设计风温为1150℃,设计拱顶温度为1300℃,煤气预热温度为140℃,废气最高温度为250℃。
高炉铁合金制备中的杂质元素控制与去除
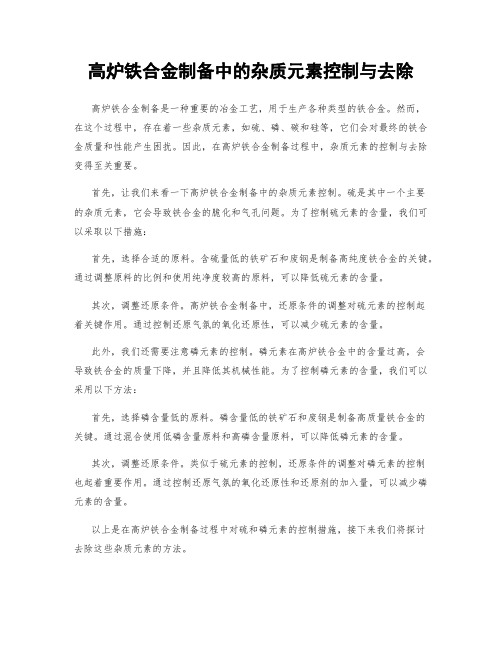
高炉铁合金制备中的杂质元素控制与去除高炉铁合金制备是一种重要的冶金工艺,用于生产各种类型的铁合金。
然而,在这个过程中,存在着一些杂质元素,如硫、磷、碳和硅等,它们会对最终的铁合金质量和性能产生困扰。
因此,在高炉铁合金制备过程中,杂质元素的控制与去除变得至关重要。
首先,让我们来看一下高炉铁合金制备中的杂质元素控制。
硫是其中一个主要的杂质元素,它会导致铁合金的脆化和气孔问题。
为了控制硫元素的含量,我们可以采取以下措施:首先,选择合适的原料。
含硫量低的铁矿石和废钢是制备高纯度铁合金的关键。
通过调整原料的比例和使用纯净度较高的原料,可以降低硫元素的含量。
其次,调整还原条件。
高炉铁合金制备中,还原条件的调整对硫元素的控制起着关键作用。
通过控制还原气氛的氧化还原性,可以减少硫元素的含量。
此外,我们还需要注意磷元素的控制。
磷元素在高炉铁合金中的含量过高,会导致铁合金的质量下降,并且降低其机械性能。
为了控制磷元素的含量,我们可以采用以下方法:首先,选择磷含量低的原料。
磷含量低的铁矿石和废钢是制备高质量铁合金的关键。
通过混合使用低磷含量原料和高磷含量原料,可以降低磷元素的含量。
其次,调整还原条件。
类似于硫元素的控制,还原条件的调整对磷元素的控制也起着重要作用。
通过控制还原气氛的氧化还原性和还原剂的加入量,可以减少磷元素的含量。
以上是在高炉铁合金制备过程中对硫和磷元素的控制措施,接下来我们将探讨去除这些杂质元素的方法。
首先,让我们关注硫元素的去除。
高炉铁合金制备中,硫元素的去除主要通过加入石灰(CaO)来实现。
石灰可以与硫元素形成硫酸钙(CaS),然后在高温条件下挥发出去。
此外,也可以通过加入氧化铝(Al2O3)来与硫反应生成硫化铝(Al2S3),从而实现硫元素的去除。
然后,我们来看磷元素的去除。
高炉铁合金制备中,磷元素的去除主要依靠加入石灰和钙质熔剂。
石灰可以与磷元素形成磷酸钙(Ca3(PO4)2),然后在高温条件下生成气体的形式逸出。
朝阳钢铁高炉有害元素的分析及控制
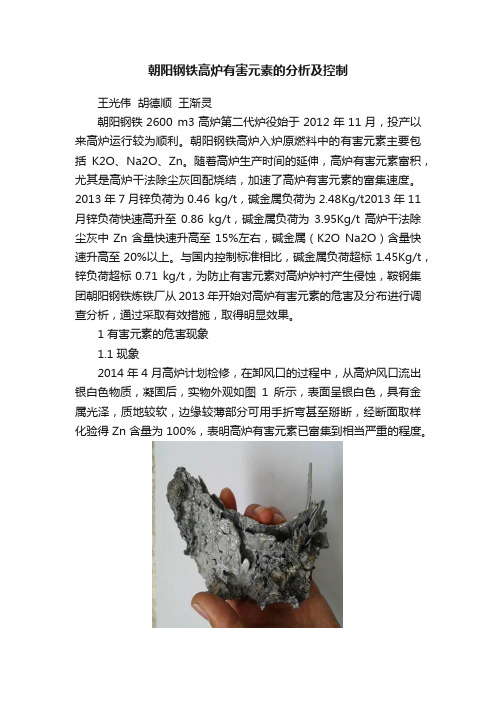
朝阳钢铁高炉有害元素的分析及控制王光伟胡德顺王渐灵朝阳钢铁2600 m3高炉第二代炉役始于2012年11月,投产以来高炉运行较为顺利。
朝阳钢铁高炉入炉原燃料中的有害元素主要包括K2O、Na2O、Zn。
随着高炉生产时间的延伸,高炉有害元素富积,尤其是高炉干法除尘灰回配烧结,加速了高炉有害元素的富集速度。
2013年7月锌负荷为0.46 kg/t,碱金属负荷为2.48Kg/t2013年11月锌负荷快速高升至0.86 kg/t,碱金属负荷为3.95Kg/t高炉干法除尘灰中Zn含量快速升高至15%左右,碱金属(K2O Na2O)含量快速升高至20%以上。
与国内控制标准相比,碱金属负荷超标1.45Kg/t,锌负荷超标0.71 kg/t,为防止有害元素对高炉炉衬产生侵蚀,鞍钢集团朝阳钢铁炼铁厂从2013年开始对高炉有害元素的危害及分布进行调查分析,通过采取有效措施,取得明显效果。
1 有害元素的危害现象1.1 现象2014年4月高炉计划检修,在卸风口的过程中,从高炉风口流出银白色物质,凝固后,实物外观如图1所示,表面呈银白色,具有金属光泽,质地较软,边缘较薄部分可用手折弯甚至掰断,经断面取样化验得Zn含量为100%,表明高炉有害元素已富集到相当严重的程度。
图1 风口流出白色物质1.2 危害1.2.1 炉体上涨有害元素富集造成高炉炉体上涨,主要表现在以下几个方面:高炉炉底板开焊,上涨约100 mm,如图2(a)所示;高炉炉体9 层平台标尺上涨约50 mm,如图2(b)所示;高炉冷却水管与平台联接处开焊,水管上移出现弯曲,如图2(c)所示;高炉上升管膨胀节发生位移,如图2(d)所示。
1.2.2 炉墙结厚2015 年9 月~2016 年2 月,由于高炉干法除尘灰无地存放及降成本需要,烧结开始回配干法除尘灰,烧结矿中Zn 含量和碱金属含量快速增加,高炉锌负荷升高至0.9 kg/t。
同时由于原料库存较低,导致入炉原燃料质量波动较大,入炉粉末增多,炉况波动大,造成2016 年3~5 月高炉炉墙结厚。
高炉项目毒性危害分析

查证要求与方法
检查结果
评价结论
备注
1、生产装置应密封化、管道化,防止有毒物质泄漏、外逸;
2、生产过程机械化、程序化和自动控制使作业人员不接触或少接触有毒物质,防止误操作造成中毒事故;
3、受技术、经济条件限制,仍然存在有毒物质逸散且自然通风不能满足要求时,应设置必要的机械通风排毒;
4、对排出的有毒气体、液体、固体应经过相应的净化装置处理,以达到环境保护排放标准;
5、对有毒物质泄漏可能造成重大事故的设备和工作场所,必须设置可靠的事故处理装置和应急防护装置;
6、根据有毒物质的性质、有毒作业的特点和防护要求,在有毒作业环境中应配置事故柜、急救箱和个体防护装置;
7、针对缺氧危险工作环境以及发生缺氧窒息和中毒窒息的原因,应配备通风换气设备和抢救器具;
8、有缺氧、窒息危险的工作场所,应在醒目处设置警示标志。
高炉项目毒性危害分析
1毒物危害分析
高炉项目涉及有毒物主要为一氧化碳,一氧化碳主要存在于热风炉作业,炉前出铁作业。一氧化பைடு நூலகம்对人体的危害如下:
一氧化碳经呼吸道吸入,属窒息性气体,主要引起人体急性中毒,一氧化碳进入人体,与血红蛋白结合,导致机体缺氧,患者出现头痛、头晕、恶心,甚至死亡。慢性危害不明显。危害级别Ⅱ级。
- 1、下载文档前请自行甄别文档内容的完整性,平台不提供额外的编辑、内容补充、找答案等附加服务。
- 2、"仅部分预览"的文档,不可在线预览部分如存在完整性等问题,可反馈申请退款(可完整预览的文档不适用该条件!)。
- 3、如文档侵犯您的权益,请联系客服反馈,我们会尽快为您处理(人工客服工作时间:9:00-18:30)。
1 750 m3 高炉 w ( K2O) / % w (Na2O) / % 物料数量/ ( kg ·t - 1) w ( K2O) / ( kg ·t - 1) w ( Na2O) / ( kg ·t - 1) 碱金属/ ( kg ·t - 1)
表 1 1 750 m3 高炉碱金属投入产出计算 Table 1 Input and output calculating of alkali metals in 1 750 m3 BF
后即气化上升 ,在不同的温度条件下又与其它物 质反应转化为氰化物 、氟化物或硅酸盐等 。当其 随炉料下降到不同温度时又被重新还原 ,从而进 行循环和富集 。 碱金属在炉内的危害表现为 : ①降低了矿石的 软化温度 ,使矿石尚未充分还原就已熔化滴落 ,增加 了高炉下部的直接还原热量消耗 ; ②引起了球团矿 的异常膨胀而严重粉化 ; ③强化了焦炭的气化反应 , 使其反应后强度急剧降低且粉化 ; ④严重恶化了料 柱透气性 ,危及生产冶炼过程的进行 ; ⑤液态或固态 碱金属粘附于炉衬上 ,既导致炉墙严重结瘤 ,又能直 接破坏砖衬 。 1. 2 铅的行为与危害 铅在炉料中主要以 PbSO4 、PbS 等形态存在 ,在 高炉中很易被碳 、铁和一氧化碳还原 。由于金属铅 质量密度 (111 34 g/ cm3 ) 比铁水 (7. 87 g/ cm3 ) 的大 得多 ,而熔点 (327 ℃) 却低 ,因此 ,铅大部分沉积在 炉底砖衬缝隙中而破坏炉底 。铅的沸点为 1 540 ℃, 在高温区部分气化进入煤气中 ,上升到低温区时又 被氧化为氧化铅再随炉料下降 ,因而在高炉中形成
(1. 济南钢铁集团总公司技术中心 ,山东 济南 250101 ;2. 济南钢铁集团总公司国贸公司 ,山东 济南 250101)
摘 要 :通过对钾 、钠 、铅 、锌等高炉中微量有害元素进行投入支出平衡计算 ,分析研究了高炉各种投入产出物中 有害元素所占比例 ,探讨了减少高炉内有害元素富集的方法和措施 ,以降低其对高炉稳定顺行的危害程度 。 关键词 :高炉 ;有害元素 ;平衡 ;富集 中图分类号 : TF5 文献标识码 :A 文章编号 :100629356 (2007) 1120035206
Abstract :Based o n t he balance calculation of inp ut and o utp ut fo r microelement imp urities such as kalium , sodium , plumbum and zinc in B F , t he ratio of t he volume of harmf ul element s in inp ut and outp ut of t he B F was st udied , and t he met hod and measure to reduce t he volume of harmf ul element s accumulatio n in B F were discussed , resul2 ting in reduce t he harm to stability of B F. Key words :B F ; harmf ul element s ;balance ;accumulation
0. 001 0 0. 502 5 0. 102 0 0. 130 0
880
566
162
408
149
1 000
270
24
10
0. 387 0. 318 0. 028 0. 257 0. 077 1. 068 0. 090 1. 341 0. 042 0. 019 1. 492
0. 800 80 0. 469 78 0. 093 96 0. 359 04 0. 146 02 1. 870 00 0. 005 00 1. 357 00 0. 024 00 0. 013 00 1. 399 00
2 有害元素平衡计算与分析
多次对 1 750 m3 、350 m3 高炉的投入产出物进 行了取样化验 。高炉用原燃料 (烧结矿 、球团矿 、块
矿 、焦炭) 在槽下振动筛下料口取样 ,喷吹煤粉从取 样点取样 ,除尘灰从各自卸灰阀下取样 ,污泥从污泥 脱水机室脱水机皮带上取样 ,生铁和炉渣分别从炉 前铁渣沟中取样 。测定期间 ,根据高炉月报表所提 供的数据计算生铁产量 、炉渣量以及各种原燃料用 量 。除尘灰量采用原料厂月除尘灰进厂量的平均 值 ,污泥量采用动力厂每月污泥产出量的平均值 。 2. 1 试样的碱金属量及平衡计算 350 m3 、1 750 m3 高炉碱金属投入产出计算分 别见表 1 和表 2 ,投入产出分布见图 1 和图 2 。1 750 m3 高炉 碱 金 属 负 荷 2. 937 kg/ t , 其 绝 对 误 差 = 21 937 - 2. 891 = - 0. 046 kg/ t ,相对误差 = 0. 046/ 2. 937 = 1. 566 % ; 350 m3 高炉 碱金 属负荷 2. 615 kg/ t ,其绝对误差 = 2. 615 - 2. 748 = - 0. 133 kg/ t , 相对误差 = 0. 133/ 2. 615 = 5. 086 %。
0. 573 0. 489 0. 011 0. 359 0. 114 1. 545 0. 005 1. 374
0. 963 0. 820 0. 036 0. 621 0. 175 2. 615 0. 075 2. 516
(36. 81) (31. 36) (1. 38) (23. 76) (6. 68) (100) (2. 73) (91. 57)
1 有害元素在高炉中的行为与危害
1. 1 碱金属的行为与危害 碱 金 属 矿 物 一 般 以 铝 硅 酸 盐 和 硅 酸 盐 形 态 存 在 ,熔点较低 ,在 800~1 100 ℃即溶化 ,到高温区 时部分进 入 炉 渣 、部 分 被 碳 还 原 成 钾 和 钠 元 素 。 钾和钠的沸点只有 799 ℃和 882 ℃,故还原出来
注 :括号内数值为百分数 。
350 m3 高炉 w ( K2O) / % w (Na2O) / % 物料数量/ ( kg ·t - 1) w ( K2O) / ( kg ·t - 1) w ( Na2O) / ( kg ·t - 1) 合计/ ( kg ·t - 1)
表 2 350 m3 高炉碱金属投入产出计算 Table 2 Input and output calculating of alkali metals in 350 m3 BF
作者简介 :杨金福 (19692) ,男 ,大学本科 ,高级工程师 ; E2mail :qihuameimei @163. com ; 修订日期 :2007208210
36
中国冶金 第 17 卷
循环富集 ,使炉底沉积的铅越来越多 。在高炉内无 法控制铅的还原 ,只能控制其入炉量和定期排出沉 积的铅 。 1. 3 锌的行为与危害 锌常以硫化锌 ( ZnS) 状态存在 ,在大于 1 000 ℃ 的高温区还原成锌 。其沸点 (907 ℃) 很低 ,还原出 来的锌立即气化进入煤气 ,上升过程中部分随煤气 逸出炉外 ;但其易在管道和上部凝聚 ,大部分又被氧 化成氧化锌并被炉料吸收再度下降还原 ,形成循环 。 锌蒸气沉积在炉子上部砖衬缝隙或墙面上 ,其 氧化后的体积膨胀会损坏炉衬或造成结瘤 。
注 :括号内数值为百分数 。
除尘灰 0. 161 0. 150
16 0. 026 0. 024 0. 050 (1. 81)
污泥 0. 321 0. 239
19 0. 061 0. 045 0. 106 (3. 87)
产出
1. 299 1. 449 2. 748 (99. 98)
图 1 1 750 m3 高炉碱金属投入产出分布 Fig. 1 Input and output distributing of alkali metals in 1 750 m3 BF
烧结矿 球团 巴块 焦炭 煤粉 投入 生铁 炉渣
0. 046 0. 056 0. 017 0. 063 0. 058
0. 007 0. 423
0. 068 0. 083 0. 007 0. 086 0. 110
0. 001 0. 509
842
589
150
417
104
1 000
270
0. 390 0. 331 0. 026 0. 263 0. 060 1. 070 0. 070 1. 142
第 11 期 杨金福等 :高炉中有害元素的平衡分析及其脱除
37
图 2 350 m3 高炉碱金属投入产出分布 Fig. 2 Input and output distributing of alkali metals in 350 m3 BF
从以上图表看出 : ①碱金属投入支出的相对误 差 ,1 750 m3 、350 m3 高炉分别是 11 566 %、51 086 % , 均较低 ,这说明高炉中碱金属投入产出基本平衡 ;入 炉碱金属负荷分别为 21 937 、21 615 kg/ t , 1 750 m3 高炉比 350 m3 高炉多 01 322 kg/ t ,这主要与济钢高 炉入炉料结构有关 。350 m3 高炉进口球团比例高 , 其带入量略低一些 ,另外支出略高于带入 ; 而 1 750 m3 高炉支出略低于带入 ,主要是新高炉 ,有部分富 积在炉内 。通常认为碱负荷不超过 5 kg/ t ,而目前 济钢高炉均不超过 3 kg/ t ,总体处中等偏低水平 。 ②烧结矿带入碱金属最高 ,分别占 1 750 m3 、350 m3 高炉全部碱负荷的 401 45 %、361 81 % ,其次是球团 矿 261 84 %、311 36 % , 再 次 是 焦 炭 占 201 98 %、 231 76 % ,煤粉和进口块带入分别占 71 61 %、61 68 %