PCB设计的可制造性-PPT精品文档
PCB设计的可制造性ppt
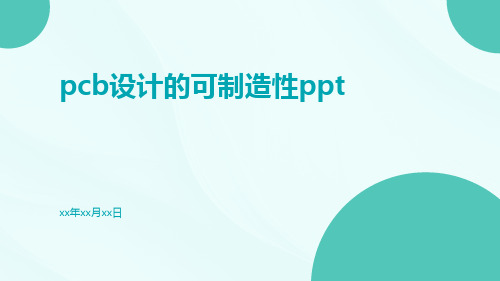
为了提高PCB设计的可制造性,需要进行一系列的优化设计和技术处理,这会增加制造成 本和生产成本。
环保要求提高
随着全球环保意识的提高,对PCB生产过程中的环保要求也越来越高,需要在设计阶段考 虑环保因素,提高PCB设计的可回收性和可降解性。
未来发展趋势与展望
01
智能化设计
利用人工智能、大数据等信息技术,实现PCB设计的智能化和自动化
设计与制程能力
总结词
PCB设计的可制造性要求充分考虑设计与制程能力,确保设 计符合制程规范。
详细描述
设计过程中应考虑制造过程中的各项因素,如加工精度、层 数、线宽和间距等。此外,还应注意PCB尺寸、形状和结构 的设计,以使其符合生产设备和工艺流程的要求。
表面处理与防护
总结词
表面处理和防护对于PCB的可制造性具有重要影响。
自动化设计与制程技术
PCB设计软件
使用具备自动化功能的PCB设计软件,可提高设 计效率和准确性。
CAM软件
通过CAM(计算机辅助制造)软件实现自动化 生产编程,减少人工操作失误。
PCB质量检测
采用自动化检测设备进行质量检测,提高检测效 率和准确性,降低漏检率。
可测试性与可维修性
制定测试计划
在设计初期考虑测试需求,制定合理的测试计划,确保可测试性 。
05
pcb度互联(hdi)板的设计
HDI板特点
高密度、多层、微型化、复杂 化。
设计难点
信号完整性、电源完整性、电 磁屏蔽、散热等问题。
解决策略
采用压合式连接、微孔定位、 精确对位等技术。
案例二:柔性板的设计与制造
01
02
03
柔性板特点
轻、薄、可弯曲、可折叠 。
PCBA可制造性设计

PCBA可制造性设计目录1.目的 (3)2.名词定义 (3)3.PCB设计要求 (3)4.元器件选用 (8)5.器件布局设计要求 (9)6.阻焊、丝印 (17)7.焊盘、焊孔及阻焊层的设计 (19)8.布线、焊盘与印制导线连接 (23)9.测试点的相关规定 (24)10.基准点(Fiducial Mark点) (24)11.拼板设计 (26)12.可装配性设计 (29)1. 目的从可制造性角度对PCB 的设计提出要求,供PCB layout 参考,同时用于指导新产品DFM (Design for manufacturability )评审。
设计无法满足此文档要求时,需经过生产工艺相关同事评估确认。
2. 名词定义Pcb layout :pcb 布局Solder mask :防焊膜面、防焊漆、防焊绿漆 Fiducial Mark :光学定位点或基准点 Via hole :导通孔 SMD :表面贴装器件 THC/THD :通孔插装器件 Mil :长度单位,1mil=0.0254mm3. PCB 设计要求3.1 PCB 外形PCB 外形(含工艺边)为矩形,单板或拼板的工艺边的四角须按半径R=2mm 圆形倒角。
应尽可能使板形长与宽之比为3:2或4:3,以便夹具夹持印制板。
3.2 印制板的可加工尺寸范围适用于全自动生产线的PCB 尺寸为最小长×宽:50mm ×50mm 、最大长×宽:610mm ×460mm 。
设计单板或拼板时,SMT 阶段允许使用最大拼板尺寸为610mm ×460mm ,PCB 单板尺寸较小时,建议拼板尺寸不大于210mm×210mm 。
3.3 传送方向的选择R=2mmPCB 传送方向工艺边为减少焊接时PCB 的变形,对不作拼板的PCB ,一般将其长边方向作为传送方向;对于拼板也应将拼板的长边方向作为传送方向。
但是对于短边与长边之比大于80%的PCB ,可以用短边传送。
PCB设计的可制造性原则

PCB设计的可制造性原那么1. 引言在电子产品制造过程中,PCB〔Printed Circuit Board,印制电路板〕的设计是非常关键的一步。
一个好的PCB设计不仅可以提高产品的性能和可靠性,还可以降低制造本钱和生产周期。
为了确保PCB设计的可制造性,设计人员需要遵循一些根本原那么和最正确实践。
本文将介绍一些常用的PCB设计的可制造性原那么。
2. 原那么一:保持布局简单和紧凑在进行PCB设计时,保持布局简单和紧凑是非常重要的原那么。
简单的布局可以降低PCB的复杂性,减少错误的可能性。
紧凑的布局可以缩短信号传输路径,减少电磁干扰,提高信号完整性。
3. 原那么二:考虑耦合和信号完整性PCB上的不同电路和组件之间存在着耦合作用。
在设计PCB时,需要考虑不同信号之间的干扰和交叉耦合。
通过合理的布局和地线规划,可以减少电磁干扰的影响,并提高信号的完整性。
4. 原那么三:合理设置电源和地线电源和地线的布局在PCB设计中扮演着重要的角色。
良好的电源和地线布局可以确保良好的电源分配和地线回流,减少电源噪声和干扰。
在设计中,应尽量将电源和地线别离,并使用适宜的地引脚和电源引脚进行连接。
5. 原那么四:防止过于密集的布线在PCB设计中,过于密集的布线可能导致信号干扰和短路等问题。
因此,应尽量防止过于密集的布线,合理规划和安排信号线和电源线的路径。
同时,应留出足够的空白区域,方便焊接和维修工作。
6. 原那么五:合理选择元件和材料在PCB设计中,选择适宜的元件和材料也是非常重要的。
适宜的元件和材料可以提供更好的性能和可靠性。
应选择具有良好可焊性和耐高温的元件,并防止使用过时或质量不佳的元件和材料。
7. 原那么六:考虑制造和组装过程在PCB设计中,要考虑制造和组装过程。
例如,要确保元件的放置和布线不会影响到焊接和组装的顺利进行。
同时,要尽量减少PCB板的层数和复杂性,以降低制造和组装的本钱。
8. 原那么七:进行设计验证和测试PCB设计完成后,应进行设计验证和测试。
PCBA工艺可制造性的基本概念介绍ppt

《PCBA设计及可靠性》
THANK YOU.
静电防护
在PCBA制造过程中,静电是一个潜在的危害因素,可能导致元器件损坏或性能下降。
洁净度要求
PCBA制造过程中,对环境中的尘埃、颗粒物等污染物有严格的要求,以确保焊接质量和 可靠性。
05
总结
总结本次介绍的要点
01
PCBA工艺可制造性是指在不同环境和条件下,通过选择合适的材料、设计合理 的电路板结构、制定规范的制板流程和严格的质量控制体系,实现高效率、低 成本、高质量的PCBA制作。
背景
近年来,随着电子产品的不断升级换代和技术进步, 电子制造企业面临着日益激烈的市场竞争。为了提高 生产效率和产品质量,降低制造成本,电子制造企业 需要关注PCBA工艺的可制造性问题。通过对PCBA工 艺可制造性的研究和改进,可以有效地解决生产过程 中的瓶颈问题,提高生产效率和产品质量,增强企业 的市场竞争力。
采用专业的EDA(电子设计自动化)软件,如Cadence、 Synopsys等。
设计优化
通过软件工具进行布局优化、布线优化、信号完整性仿真等,提 高PCBA的可制造性。
数据分析
利用软件工具进行数据分析,识别出可能的制造问题和风险,提 前进行规避和优化。
案例三:环境因素对可制造性的影响
温度和湿度
对于PCBA制造来说,温度和湿度是两个重要的环境因素,对制造过程中的元器件性能和 焊接质量产生影响。
率。
软件模块化
02
将软件程序划分为多个模块,以提高代码的可读性和可维护性
。
软件测试和验证
03
对软件进行全面、细致的测试和验证,以确保其正确性和可靠
性。
环境优化
生产环境设置
PCB---可制造性

PCB可制造性一、PCB可制造性概念1、PCB可制造性设计:从广义上讲,包括了产品的制造、测试、返工、维修等产品形成全过程的可行性;狭义上讲是指产品制造的可行性。
2、针对PCB可制造性设计包括两方面:(1)PCB的可制造性 ( DFM:Design for Manufacture );(2)PCB贴装、组装的可制造性( DFA:Design for Assembly ) ;在设计时需要考虑周全,比如:BGA周围3MM内不要放置元器件,其目的就是为了利于返修BGA。
3、可制造性设计的目的:可制造性设计DFM(Design For Manufacture)就是从产品开发设计时起,就考虑到可制造性和可测试性,使设计和制造之间紧密联系,实现从设计到制造一次成功的目的。
DFM是保证PCB设计质量的最有效的方法。
DFM具有缩短开发周期、降低成本、提高产品质量等优点,是企业产品取得成功的途径。
4、PCB可制造性设计包括以下几个方面:(1)板材的选择;(2)多层板的叠层结构设计;(3)电路图形设计:孔和焊盘的设计要求、线路设计、阻焊设计、字符设计;(4)表面处理工艺的选择。
下面将对PCB可制造性设计的以上四个方面逐一讲解:5、板材的种类:(a)覆铜箔基板(Copper-clad Laminate)简称CCL,由铜箔(皮)、树脂(肉)、增强材料(骨)、功能性添加物(组织)组成,是PCB加工的主要基础物料。
上图所示即经常讲到的芯板,也就是Core。
其上下是有铜箔,中间层是介质材料。
生益FR-4,其中间层是介质材料也是PP片。
(b)树脂类板材:环氧树脂( epoxy )、聚亚酰胺树脂( Polyimide )、聚四氟乙烯(Polytetrafluorethylene,简称PTFE 或TEFLON)、B一三氮树脂(Bismaleimide Triazine 简称BT、二亚苯基醚树脂(PPO)等6、板材的主要性能指标:(i)Er --- 介电常数:介电常数会随温度变化,在0-70度的温度范围内,其最大变化范围可以达到20%。
PCBA可制造性设计规范pptx
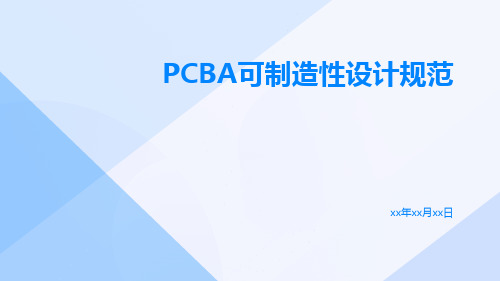
改进措施
根据故障分析结果,制定改进措施,优化电路板设计、制造 工艺、装配流程等,提高电路板的可制造性和可靠性。
05
PCBA设计优化
自动化设计和智能化设计
1 2
CAD软件应用
采用自动化CAD软件进行PCB设计,提高设计 效率和准确性。
智能化设计工具
利用智能算法和机器学习技术,实现PCB设计 的自动化布线、元件布局优化等。
多层板和高层板设计
多层板设计
采用多层板设计技术,优化空 间利用和提高电路性能。
高层板设计
采用高层板设计技术,提高电路 板设计的灵活性和可维护性。
电源完整性设计
在多层板和高层板设计中,注重电 源完整性设计,保证电源的稳定性 和可靠性。
06
PCBA可制造性最佳实践
PCBA设计审查
总结词
设计审查流程
可靠性测试计划
建立全面的可靠性测试计划,包括温度测试、湿度测试、振动测试、耐久性测试等,确保 PCB板在各种环境下能够可靠运行。
失效分析
对失效的PCB板进行失效分析,找出失效原因并采取相应的措施进行改进,不断提升PCB 板的可靠性。
THANKS
随着电子产品不断向轻薄短小、高密度、高性能方向发展, 对PCBA的可制造性设计规范的要求也越来越高。
定义和术语
PCBA(Printed Circuit Board Assembly)是指将电子元 器件与连接电路印制在电路板上的组装体。
可制造性设计规范(Design for Manufacturability, DfM)是指在设计产品时,充分考虑制造过程中可能出现 的问题,以提高产品的可制造性。
合理、安全
散热方案
根据电路板功耗和热流密度,选用合适的散热方 案,如自然散热、风扇散热等。
pcb设计的可制造性
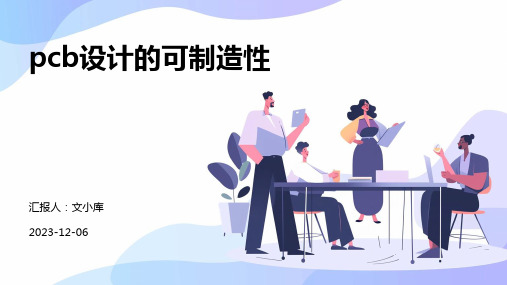
面向制造约束的优化策略
总结词
根据制造工艺和制造成本等因素进行优化, 提高制造效率和产品质量。
详细描述
在PCB设计中,应考虑制造工艺和制造成本 等因素。不同的制造工艺和材料选择会影响 制造成本和产品质量。在面向制造约束的优 化时,应考虑制造流程、材料选择、加工精 度等因素,以实现高效、稳定的PCB制造。 同时,应尽量减少制造过程中的废料和不良
流程优化
对流程中可能存在的瓶颈和问题进行分析和优化,提高生产效率。
流程监控
对制造流程进行实时监控,确保产品质量和生产计划的执行。
制造约束分析
尺寸限制
01
分析PCB板材的尺寸、厚度、孔径等参数,以满足产品的规格
要求。
制造能力限制
02
根据供应商的制造能力,分析产品的可制造性,避免制造过程
中的问题。
材料限制
选择符合制造要求的元件封装, 以确保PCB制造的可行性和可靠
性。
PCB尺寸和形状
根据产品需求和制造能力,确定 PCB的尺寸和形状,以提高制造
效率和降低成本。
定位孔和标识
在PCB上设置合适的定位孔和标 识,以确保PCB在制造过程中的
准确定位和识别。
03
pcb设计的可制造性分析
制造可行性分析
板材选择
THANKS
感谢观看
案例二:高速数字电路pcb的可制造性设计
要点一
总结词
要点二
详细描述
高速数字电路pcb的可制造性设计需要考虑信号的完整性和 时序性,以及如何优化布线和元件布局。
高速数字电路pcb设计需要关注信号的完整性和时序性, 以确保信号在传输过程中不失真或畸变。为了优化信号的 完整性和时序性,需要考虑布线和元件布局的优化。例如 ,合理安排信号线的长度和走向,以减少信号反射和延迟 ;合理安排元件的排列和连接方式,以减少信号干扰和噪 声。
PCB可制造性设计

第13页
1 材料
1.5.1 介电常数的范围及应用
PTFE 3.0 3.8 PTFE + Ceramic 4.8 FR-4 Ceramic 10.2 介电常数范围:2.2 选用板材类型: 应用范围:
微带、高频 300MHz~40GHz
正常 高压、高频 1MHz~1GHz 800MHz~12GHz
Rt5880
体积 电阻 MΩ*cm 2×107 2×107 抗剥 强度 lbs/in 22.8 20.8
厂 商 罗 杰 斯
型号
Rt5880 Rt5870
>260 >260
0.015 0.015
第9页
1 材料
1.3 热塑陶瓷 基材特性 • 耐热性好 • 机械加工性能好 • 介电常数随温度变化较小、介质损耗低 应用范围 • 高速、射频、微波电路 • 军事、航天航空
第2页
大纲
印 制 板 各 项 要 素 的 含 义 我 司 工 艺 能 力 及 设 计 实 例
分 类 及 相 关 参 数
标 准 要 求
第3页
印制电路板设计原则
电气连接准确性
印制板上布设的印制导线的电气连接关系必须符合电原 理图。 设计印制板时,应考虑印制板的制造工艺要求和装联工 艺要求,尽可能有利于制造和装配。 印制板的可靠性,是影响电子设备和仪器可靠性的重要 因素。 印制板的经济性与印制板的类型、基材选择和制造工艺 方法、技术要求的内容密切相关。 印制板的结构决定了印制板在各种环境下使用的性能和 寿命。
第17页
1 材料
2.1 粘结片介绍 粘结片是由树脂和增强材料构成的一种预浸材料。在高温和压力的作用 下,具有流动性并能很快地固化和完成粘结过程。它与增强材料一起构成绝 缘层,是多层印制板制造中不可缺少的层压材料。
浅谈PCB设计的可制造性

01 7 . 2
() 5
B 面 主 要 放 置 10 (6 3 封 装 尺 寸 以上 贴 片 电 阻 、 片 电容 68 00 ) 贴
( 不含 立 式铝 电解 电容 ) 高度 小 于 6 u , Ⅱ n的 S T S P 为 防止 拉 尖 O 、O 。
02 .5
( 0 1)
02 .
采用 拼 板 方式 。传 送 边 的两 边应 分 别 留 出不 小于 3 II18 d .II(3 5TT mi
2
布 线
在组装 密度许 可 的情 况下 , 尽量选 用较 低密度 布线 设计 , 以提高
元器 件 要尽 可 能 均匀 、 则地 分 布排 列 。均匀 分 布有 利 于 散热 规 . mm( mi / . 7 / ( m d 2 5 l 01 I 5 i 。常用布 线密度 设计如表 1 ) 2 i a r 所示 。 和 焊 接 工 艺 的 优 化 ; 规 则 地排 列 方 便 检 查 , 于 提 高 贴片 / 件 01 7 有 利 插 表 1 布线 密度说明 mm( d mi 速度 。考 虑到 焊 接 、 查 、 试 、 装 的需 要 , 检 测 安 A面 元 件 之 间 的 问隔 不 能太 近 , 体根 据 公 司的 工艺 生产 能 力而 定 。 具
测 试 点 。 2 对 于 A / A 器件 、 隔离 器件 等 注意 数字 信号 和模 拟 () DD 光 信 号 、 入输 出信 号 的 隔离 , 输 使其 能划 分 出隔 离 区域 。() 于 测试 3对 板和 背 板等 有 连接 两 板 的连 接器 时 ,注 意 端 子位 置 的正 确 摆放 和 焊 盘 序 号的 对应 关 系 。( ) 4 从减 少 工序 、 高效 率角 度 考虑 , 一面 提 能 放 完 的器 件尽 量 放在 同 一面 , 免 B面 仅 有几 个 表贴 器件 的情 况 。 避 () 电路 板 布 局 时各 去 耦 , 路 电容 靠近 芯片 的管 脚 放 置 , 5在 旁 以达
PCB设计的可制造性知识

PCB设计的可制造性知识PCB(Printed Circuit Board)是现代电子设备中不可或缺的一部分,其设计的好坏直接影响着整个产品的性能和可靠性。
在进行PCB设计时,了解和掌握可制造性知识是非常重要的,可以提高设计的效率和减少制造过程中的问题。
本文将介绍一些与PCB设计相关的可制造性知识和建议。
1. PCB板材选择在PCB设计中,选择合适的板材对于保证电路板的性能和可制造性非常重要。
常见的PCB板材有FR-4、高频板材、金属基板等。
1.1 FR-4板材FR-4是一种常见的玻璃纤维增强热固性树脂,具有良好的电气性能和机械性能。
由于其价格适中,成型工艺相对简单,所以在大多数普通应用中广泛使用。
在选择FR-4板材时,应根据电路的特性和要求来确定板材的层数、厚度和铜箔厚度等参数,以达到最佳的电气性能和机械强度。
1.2 高频板材高频板材主要应用于高频电路设计,如无线通信、雷达、卫星通信等领域。
与FR-4板材相比,高频板材具有更低的介电常数和介质损耗,以及更好的高频特性。
在使用高频板材进行设计时,应注意板材的层数和铜箔厚度,以确保电路的传输特性和匹配性能。
1.3 金属基板金属基板通常用于高功率、高散热的电路设计,如功放、LED照明等。
金属基板具有良好的散热性能和机械强度,可以有效地降低电路温度,提高整体可靠性。
在选择金属基板时,应根据电路功率和散热要求来确定基板的厚度和金属材料,以确保良好的散热效果。
2. 元件布局与走线规则良好的元件布局和走线规则对于保证电路的稳定性和可制造性至关重要。
以下是一些常见的布局和走线规则:2.1 元件布局•尽量将相互关联的元件放置在靠近一起的位置,以缩短连线长度,减小电磁干扰。
•避免元件之间的相互遮挡,以便进行后续的组装和维修。
•根据信号的传输特性和敏感性,合理地进行电路分区,以降低噪声和串扰。
2.2 走线规则•充分利用电路板的空间,合理布局走线,减小走线长度和阻抗。
电路板(PCB)设计与可制造性(DFM)

30%
理想状态
功能无缺点,达设计 要求
3..3板边缘设计要求
图形到板边 缘的距离最 小0.4.冲切 加工的板最 好与板厚尺 寸一样
3.4板面线路布局隐忧
PCB
两面的线路
尽量不要平 行,否则,图形 腐蚀后,因两 面铜箔应力 释放,易产生 板翘
3.8整板厚度结构
流程
沉电 铜
电路电 镀
防焊制 作
文字
合计
板料最大上 偏差
加成 0.005 0.05 0.02 0.03 0.105 0.13
总厚度 0.235
成品厚度:板厚T+加成总厚度 结论:成品板厚易超规格
3.9孔到板边的距离
可靠性疑问:
1)板边的机械强度降低
2)孔环一旦受到损伤,锡垫不 完整
显影后的结果,图 形转移时,网格未 形成
3.PCB设计的一般要求
• 3.1导体外观 • 3.2金手指外观 • 3.3板边缘设计要求 • 3.4板面线路布局隐忧 • 3.5V槽板外形尺寸结构 • 3.6冲切板外形尺寸结
构
• 3.7板厚标准 • 3.8整板厚度结构
3.9孔到板边的距离 3.10孔尺寸结构 3.11图形尺寸 3.12-15导体断面积,铜厚, 电压与电流等之间关系
槽深度偏差
B 板厚度方向中心到板面 ±0.08
的距离
C 上下V槽刀的偏移距离 ±0.08
D V槽线的宽度偏差
±0.08
E V槽刀角度偏差
±2°
F V槽位置偏差
D/2+累积
G 板厚
H 连片V槽线中心距
±0.08加
累积偏差
按上表和图说明 测量: V槽板的测量以V 槽线中心为基准 建议:外形公差±0.25mm
PCBA可制造性设计规范ppt课件

PCB V-CUT PCB
25mm 5c mm
PCB layout rules
V-Cut layout rules :
PCB trace to V-Cut should be more then S=0.5mm safety buffer, otherwise will have the risk to damage the trace.
Stamp Cut
Stamp design parameters
PCB
NPTH hole 1.0mm
2.0mm
1.5mm
2.8mm
PCB 2.0mm
1.5mm
NPTH hole1.0mm
0.4mm
5.0mm 0.4mm
PCB
5.0mm
conveyor edge
PCB layout rules
V-Cut VS Stamp layout :
Stamp Cut
irregular shape
PCB layout rules
Stamp design :
Stamp design only for irregular PCB, PCB to PCB layout distance is 2mm, V-Cut only 0.3mm
Stamp Cut
PCB layout rules
V-Cut layout rule :
Chips to V-Cut line should be more than 1mm, otherwise will damage chips or will change to use Stamp Cut design , will add the PCB cost
PCB设计的可制造性(PPT34页)

合理的元件排布 方向
桥 连
不合理的元件排布 方向
PCB设计的可制造性(PPT34页)
较轻的THT器件如二级管和1/4W电阻等,布局时应使 其轴线和波峰焊方向垂直,以防止过波峰焊时因一端 先焊接凝固而使器件产生浮高现象;
SMD元件间隔应满足设计标准,THT元件间隔应利于操 作和替换;
经常插拔器件或板边连接器周围3mm 范围内尽量不布 置SMD,以防止连接器插拔时产生的应力损坏器件;
解决连 锡
插件元件每排引脚较多时,以焊盘排列方向平行于进 板方向布置器件时,当相邻焊盘边缘间距为0.6mm~ 1.0mm 时,推荐采用椭圆形焊盘或加偷锡焊盘,受 PCB LAYOUT限制无法设置窃锡焊盘时,应将DIP后方 与焊盘邻近或相连的线路绿漆开放为裸铜,作为窃锡 焊盘用;
学习改变命运,知 识创造未来
波 峰 焊
* 如果通孔元件很少,可采用回流焊和手工焊的方式
清 洗
学习改变命运,知 识创造未来
印刷 锡膏
贴装 元件
回 流 焊
手 工 焊
PCB设计的可制造性(PPT34页)
清 洗
双面混装(一)
印刷 锡膏
贴 装 元 件
回 流 焊
翻 转
学习改变命运,知 识创造未来
贴片 胶
贴装 元件
加 热 固 化
PCB设计的可制造性(PPT34页)
•附:阴影效应
封装太高,影响焊锡 流动
引起 空焊
学习改变命运,知 识创造未来
增加焊盘长度,通过焊盘引力给引脚 上锡 PCB设计的可制造性(PPT34页)
学习改变命运,知 识创造未来
在两个互相连接的SMD元件之间﹐要避免采用单个的 大焊盘﹐因为大焊盘上的焊锡将把两元器件拉向中间 ﹐正确的做法是把两元器件的焊盘分开﹐在两个焊盘 中间用较细的导线连接﹐如果要求导线通过较大的电 流可并联几根导线﹐导线上覆盖绿油; SMT元件的焊盘上或其附近不能有通孔,否則在回流 焊过程中,焊盘上的焊锡熔化后会沿着通孔流走,会 产生虚焊﹐少錫﹐还可能流到板的另一面造成短路; 轴向器件和跳线的引脚间距(即焊盘间距)的种类应 尽量减少,以减少器件成型的调整次数,提高插件效 率;
PCB设计的可制造性(PPT34页)
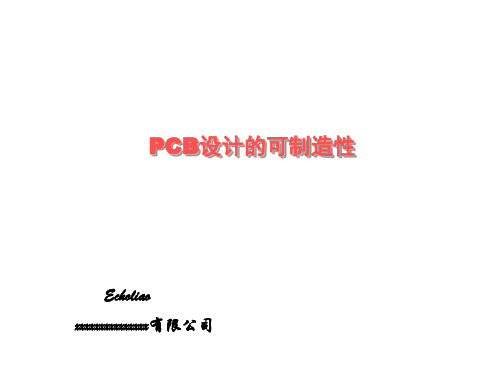
应根据系统或模块的PCBA安装布局以及可调器 件的调测方式来综合考虑可调器件的排布方向、调测 空间。
SMD元件间距(相同封装)
SMD元件间距(不同封装)
SMD元件布局图例
过板方向 BD/SMT QFP
XXX-XX-XX-XXX Vx.xx.xx
Q
发热大的元件尽量靠边
将线路铜箔开放为裸 铜作为偷锡焊盘
为防止过波峰时焊锡从通孔上溢到上板,导致零件对 地短路或零件脚之间短路,设计多层板时要注意,金 属外壳的元件,插件时外壳与印制板接触的,顶层的 焊盘不可开,一定要用绿油或丝印油盖住(例如两脚 的晶振、3只脚的LED)
绿油覆盖
走线要求
板面布线应疏密得当,当疏密差别太大时应以网状铜 箔填充; 为了保证PCB加工时不出现露铜的缺陷,要求所有的 走线及铜箔距离板边:V-CUT边大于0.75mm,铣槽边 大于0.3mm(铜箔离板边的距离还应满足安装要求); 考虑到PCB加工时钻孔的误差,所有走线距非安装孔 都有最小距离要求。
合理
不合理
PCB尺寸及外形要求
圆角:为方便单板加工,不拼板的单板板角应为R型 倒角,对于有工艺边和拼板的单板,工艺边应为R型 倒角,一般圆角直径为Φ5,小板可适当调整。有特 殊要求按结构图表示方法明确标出R大小,以便厂家 加工; 工艺边:板边5mm范围内有较多元器件影响PCB加工时, 可以采用加辅助边(工艺边)的方法,工艺边一般加 在长边; Mark点:基准点用于锡膏印刷和元件贴片时的光学定 位。根据基准点在PCB板上的用途,可以分为全局基 准点、单元板基准点、个别器件基准点。
SMT元件的焊盘上或其附近不能有通孔,否則在回流 焊过程中,焊盘上的焊锡熔化后会沿着通孔流走,会 产生虚焊﹐少錫﹐还可能流到板的另一面造成短路;
- 1、下载文档前请自行甄别文档内容的完整性,平台不提供额外的编辑、内容补充、找答案等附加服务。
- 2、"仅部分预览"的文档,不可在线预览部分如存在完整性等问题,可反馈申请退款(可完整预览的文档不适用该条件!)。
- 3、如文档侵犯您的权益,请联系客服反馈,我们会尽快为您处理(人工客服工作时间:9:00-18:30)。
0603以下、SOJ、PLCC、BGA、0.6mm Pitch以下的SOP、 本体托起高度(Standoff)>0.15mm的器件不能放在 波峰面;QFP器件在波峰面要成45°布局; 安装在波峰焊接面上的SMT大器件(含SOT23器件)﹐ 其长轴要和焊锡波峰流动的方向(即工艺边方向)平 行﹐这样可以减少引脚间的焊锡桥接; 波峰焊接面上的大、小SMT元器件不能排成一条直线, 要错开位置,较小的元件不应排在较大的元件之后, 这样可以防止焊接时因焊料波峰的 “阴影”效应造 成的虛焊和漏焊;
SMD元件间距(相同封装)
SMD元件间距(不同封装)
SMD元件布局图例
过板方向
XXX-XX-XX-XXX Vx.xx.xx
BD/SMT
QFP
Q
发热大的元件尽量靠边
好处:便于目视管理,方便操作,减少出错几率 !!
焊盘设计
SMT焊盘设计遵循相关标准,如IPC782标准; 波峰面上的SMT元器件,其较大元件的焊盘(如三极管 ﹑插座等)要适当加大,如SOT23之焊盘可加長0.81mm,这样可以避免因元件的 “阴影效应”而产生的 空焊; 焊盘大小要根据元器件的尺寸确定,焊盘的宽度等于 或略大于元器件引脚的宽度,焊接效果最好; 对于通孔来说,为了保证焊接效果最佳,引脚与孔径 的缝隙应在0.25mm~0.70mm之间。较大的孔径对插装 有利,而想要得到好的毛细效果则要求有较小的孔径, 因此需要在这两者之间取得一个平衡;
附:IC的合理排布方向与桥连
偷锡焊盘
桥连
合理的元件排布方向
不合理的元件排布方向
较轻的THT器件如二级管和1/4W电阻等,布局时应使 其轴线和波峰焊方向垂直,以防止过波峰焊时因一端 先焊接凝固而使器件产生浮高现象;
SMD元件间隔应满足设计标准,THT元件间隔应利于操 作和替换;
经常插拔器件或板边连接器周围3mm 范围内尽量不布 置SMD,以防止连接器插拔时产生的应力损坏器件;
设计者应考虑板形设计是否最大限度地减少组装流程的问题,
即多层板或双面板的设计能否用单面板代替?PCB每一面是否能用 一种组装流程完成?能否最大限度地不用手工焊?使用的插装元件 能否用贴片元件代替?
选用元件的封装应与实物统一,焊盘间距、大小满足 设计要求;
元器件均匀分布﹐特别要把大功率的器件分散开﹐避 免电路工作时PCB上局部过热产生应力﹐影响焊点的 可靠性; 考虑大功率器件的散热设计; 在设计许可的条件下,元器件的布局尽可能做到同类 元器件按相同的方向排列,相同功能的模块集中在一 起布置;相同封装的元器件等距离放置,以便元件贴 装、焊接和检测;
双面贴装
B面 印刷锡膏 贴装元件 回流焊 翻转
A面
印刷锡膏
贴装元件
回流焊
翻转
A面布有大型IC器件,B面以片式元件为主 充分利用 PCB空间,实现安装面积最小化,效率高
清洗
单面混装
印刷锡膏
贴装元件
回流焊 插通孔元件
波峰焊
清洗
PCB组装二次加热,效率较高 * 如果通孔元件很少,可采用回流焊和手工焊的方式
双面混装(二)
B面 印刷锡膏 贴装元件 回流焊 翻转
A面
印刷锡膏
贴装元件
回流焊
手工焊接
清洗
适用于双面SMD元件较多,THT元件很少的情况,效率低
DFM设计(PCB)一般原则
PCB外形和尺寸应与结构设计一致,器件选型应满足 结构件的限高要求,元器件布局不应导致装配干涉; PCB外形以及定位孔、安装孔等的设计应考虑PCB制造 的加工误差以及结构件的加工误差 PCB布局选用的组装流程应使生产效率最高;
附:阴影效应
封装太高,影响焊锡流动
引起空焊
增加焊盘长度,通过焊盘引力给引脚上锡
在两个互相连接的SMD元件之间﹐要避免采用单个的 大焊盘﹐因为大焊盘上的焊锡将把两元器件拉向中间 ﹐正确的做法是把两元器件的焊盘分开﹐在两个焊盘 中间用较细的导线连接﹐如果要求导线通过较大的电 流可并联几根导线﹐导线上覆盖绿油; SMT元件的焊盘上或其附近不能有通孔,否則在回流 焊过程中,焊盘上的焊锡熔化后会沿着通孔流走,会 产生虚焊﹐少錫﹐还可能流到板的另一面造成短路; 轴向器件和跳线的引脚间距(即焊盘间距)的种类应 尽量减少,以减少器件成型的调整次数,提高插件效 率;
需波峰焊的贴片IC各脚焊盘之间要加阻焊漆,在最后 一脚要设计偷锡焊盘;
一面贴装、另一面插装
印贴片胶
贴装元件
固化 翻转 插件
PCB组装二次加热,效率较高
波峰焊
清洗
* 如果通孔元件很少,可采用回流焊和手工焊的方式
手工焊 印刷锡膏 贴装元件 回流焊
清洗
双面混装(一)
印刷锡膏 贴装元件 回流焊 翻插通孔元件 波峰焊 清洗
PCB组装三次加热,效率低
丝印清晰可辨,极性、方向指示明确,且不被组装好 后的器件遮挡住。
元件分布
均匀,方向尽量统一; 采用回流焊工艺时,元器件的长轴应与工艺边方向 (即板传送方向)垂直﹐这样可以防止在焊接过程中 出现元器件在板上漂移或 “立碑”的现象; 采用波峰焊工艺时,无源元件的长轴应垂直于工艺边 方向,这样可以防止PCB受热产生变形时导致元件破 裂,尤其片式陶瓷电容的抗拉能力比较差; 双面贴装的元器件﹐两面上体积较大的器件要错开安 裝位置﹐否則在焊接过程中会因为局部热容量增大而 影响焊接效果; 小、低元件不要埋在大、高元件群中,影响检、修;
2005年12月(中国•上海)
PCB设计的可制造性
Echoliao
xxxxxxxxxxxxxxx有限公司
工艺流程
单面贴装
印刷锡膏 贴装元件 回流焊
锡膏——回流焊工艺 简单,快捷
清洗
单面插装
成型、堵孔 插件 波峰焊
波峰焊工艺 简单,快捷
清洗
波峰焊中的成型工作,是生产过程中效率最低的部分之一,相应 带来了静电损坏风险并使交货期延长,还增加了出错的机会。
为了保证可维修性,BGA 器件周围需留有3mm 禁布区, 最佳为5mm 禁布区。一般情况下BGA 不允许放置在背 面;当背面有BGA 器件时,不能在正面BGA 5mm 禁布 区的投影范围内布器件; 可调器件周围留有足够的空间供调试和维修; 应根据系统或模块的PCBA安装布局以及可调器 件的调测方式来综合考虑可调器件的排布方向、调测 空间。